1
EPIGRAPHE
Que tes bien-aimés jouissent du
bonheur!
2Ch.6:41
Que ce travail soit le vôtre.
2
DEDICACE
Je dédie ce travail à mon père Albert
KASHIKI MANDAZAZI ainsi qu'à ma mère Vicky TSHILEMBA TSHIZAMBALA
pour tout l'amour et le soutien qu'ils n'ont jamais cessé de manifester
à ma personne.
Je dédie également ce travail :
- A vous mes frères et soeurs Franck KATOBO, Laora
TSHIBANGU Gloire MBAYA, Nadège MUYAMBO, Cynthia KISIMBA, Demaman
TSHILEMBA, Miradi TSHILEMBA.
- A vous mes grand parents, oncles et tantes Michel TSHINISH,
Marthe KISIMBA, Jonas MWAMBA, Job MULAJI, Bernadette KAPEMBA, MUTOMBO, KAFAT,
Madeleine MWIKA, Jolie MAHEBA, Louis MANDA, John BAITA.
- A vous mes amis et frère en christ FINYA, MBAKA,
Trésor KAJ, KABOLESHA, MBUYA, MUTAZA, MATONDO, KASONGO Alain KALONJI,
KIPILI, HOLESA, KAZEMBE, LOMINGO, MPANGA, BUFUKO, DIKULO, PAMI , MUSHID,
LUMINGU, ISULA, CINYEMBA.
+243 99 279 66 72 / +243 81 721 31 56
3
AVANT -PROPOS
Ce travail, étant le couronnement de mes études
d'ingénieur technicien est le fruit d'une longue recherche personnelle
mais aussi l'aboutissement d'une collaboration entre plusieurs personnes qui
m'ont aidé à sa réalisation.
Je tiens ainsi par cette occasion à remercier tout
d'abord le TRES-HAUT pour sa grâce qu'il ne cesse de m'accorder.
Je tiens aussi à remercier l'Ingénieur KANYEMBO
ELISHA pour ces conseils, sa disponibilité et surtout pour sa guidance
utile dans le cadre du présent travail.
Je ne pourrai finir ici sans mentionner les personnels de la
Société Tenke Fungurume Mining pour leur collaboration, plus
particulièrement Messieurs Mamadou DIA, Reginald MWILA, Alexandre AZAMA,
Alex KIBUTA, Hénoch Ongendja, Félie KAWAMA, Dieudonné
LUKWESA, KASADIMA, Trésor KASONGO, Matias. Je remercie également
le Comité de Gestion, tous les enseignants, professeurs et
différents encadreurs de l'ISTA qui ont fait de nous ce que nous sommes
aujourd'hui.
Mes pensées vont également à mes amis et
connaissances pour leur soutien moral, encouragements et suggestions: Rosie
MAFO, Solenne LUPANDA, Freddy LOMINGO, KUTEMBA, Bibiche, Erick KAUND.
Mais aussi à tous ceux que je n'ai guère
cité ici, trouvent dans ces lignes l'expression de ma reconnaissance la
plus distinguée.
Guillaume KATOBO ILUNGA
4
INTRODUCTION
Tenke Fungurume Mining, l'une des ressources minières
en cuivre et cobalt les plus importantes et à plus haute teneur au
monde. Les concessions minières de Tenke Fungurume Mining sont
situées dans la province du Katanga, ville de Kolwezi, en
République Démocratique du Congo à environ 135
Kilomètres de la ville minière de Kolwezi. Elles couvrent une
superficie d'environ 1600 Km2 et sont situées entre deux
grandes cités à savoir Tenke et Fungurume. Les concessions sont
accessibles par des routes non pavées, par rail et par voie
aérienne. Les températures y sont toutefois
modérées par l'altitude. Le climat de cette région est
caractérisé par une saison sèche et une saison des pluies,
d'environ six mois chacune, avec des précipitations moyennes de
119cm.
Elle est un projet de classe mondiale et constitue le plus
important projet d'investissement étranger en République
Démocratique du Congo (RDC).
Afin de produire le cobalt, l'entreprise dispose d'un
concasseur pilote qui produit les limes stones, graviers, congreds et
ballastes.
Il est question dans notre travail de fin de cycle, de
prévoir un système de graissage automatique des organes mobiles,
cas de notre sujet <<conception d'un
système de graissage centralisé sur la chaine de production d'un
concasseur pilote (cas du pilote crusher Mbeba à
TFM)>> , partant des principes et
propriétés de l'hydraulique industrielle et en vue de satisfaire
aux besoins des employés travaillant sur cette chaine de production.
Le but de ce travail se justifie par le fait que depuis
l'implantation de cette machine jusqu'alors, les travailleurs connaissent des
problèmes de suivi de la maintenance et des pressions en provenance de
l'usine cobalt, qui sont dus aux difficultés de graissage, auxquels nous
voulons remédier au moyen d'un système de graissage
centralisé.
En effet, l'intérêt sera la réalisation
des conditions de travail beaucoup plus satisfaisantes, pour le bien-être
physique et sanitaire de travailleurs ainsi que l'accroissement de la
production.
5
L'apport de ce travail fait recours à la technologie
moderne qui n'existe pas sur ce genre de chaines de production.
Le problème est donc de savoir : que faire pour
améliorer les conditions de travail de cette chaine de production, et
des travailleurs en évitant des difficultés telles que :
+ L'inaccessibilité de certains endroits à graisser
;
+ Le temps de la maintenance journalière prolongé
;
+ Le colmatage des graisseurs sur les paliers ;
+ Négligence ou oubli de graisser certaines parties par
suite de la
fatigue des travailleurs et du nombre des graisseurs
élevé ;
+ Insuffisance de la graisse sur des endroits où
l'exigence est très
importante.
Pour que le but de notre travail soit atteint, il faut supposer
que :
> Les positions et les mouvements des endroits
inaccessibles au graissage manuel sont restés inchangés ;
> La pression du nouveau mode de graissage parviendra
à
atteindre tous les points à graisser en quantité
suffisante ; > Que le temps de la maintenance journalière sera
réduit au
bénéfice de la production ;
> Que les travailleurs aient moins de problème avec
cette nouvelle méthode ;
> Que les graisseurs soient protégés.
Pour résoudre correctement les problèmes
posés, deux grands objectifs sont fixés dans nos recherches
à savoir:
V' Analyser et évaluer les équipements de
l'installation hydraulique ;
V' Choisir une pompe hydraulique capable de fournir une bonne
pression et de réaliser le nouveau système de graissage.
Compte tenu des hypothèses précitées, au
cours de ce travail, nous nous limiterons aux choix des éléments
et conception du système de graissage centralisé.
6
Le présent travail renferme, outre l'introduction et la
conclusion, quatre grands chapitres qui sont :
CHAP I : Généralités ;
CHAP II : Hydraulique industrielle
CHAPIII : Présentation de la chaine de production du
concasseur pilote ;
CHAP IV : Systèmes de Graissage.
7
CHAPITRE I. GENERALITES
Sur la chaine de production du concasseur pilote, les
éléments à graisser sont les roulements excepté le
graissage du concasseur à cône sur lequel on envoie de la graisse
sur une vis trapézoïdale.
I.1 Roulements à billes
Les avantages du graissage des roulements sont les suivants :
1) Réduire la friction et l'usure
2) Dissiper la chaleur
3) Éviter la corrosion
4) Empêcher les contaminants d'entrer en contact avec les
pièces
5) Augmenter la durée de vie du roulement
Graisseur d'arrivée de la graisse
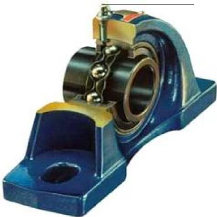
Figure 1.1
Un graissage insuffisant causera donc un ou plusieurs
problèmes à ces niveaux alors qu'un graissage excessif risque
d'augmenter la température de roulement et amener à l'usure
prématurée autant qu'un graissage insuffisant. De plus, le
graissage excessif peut abimer les joints ou les déflecteurs des
roulements s'ils en possèdent.
1 Catalogue lubrification SNR, p23
8
La plupart des roulements requièrent un graissage avec
de la graisse au lithium. Pour le calcul des quantités de graisse et des
intervalles de graissage, il existe plusieurs façons de faire,
dépendant des fabricants, des fournisseurs et des spécialistes du
domaine. Il ne semble exister aucune méthode de calcul officielle et il
devient très difficile de s'y retrouver. Nous avons donc monté
quelques formules à partir de différentes données et
formules trouvées. Les résultats ainsi obtenus donnent un
approximatif et permettent un point de départ pouvant nous aider
à déterminer les besoins en graissage des roulements de type
à billes (ball bearings).
Toujours se référer aux exigences des fabricants
pour obtenir les données exactes puisque les formules suivantes n'ont
que pour seul but de donner une idée.
I.2 Méthodes de graissage
1) Toujours nettoyer le raccord de graissage avant de
procéder ;
2) Faire le graissage pendant que le roulement tourne ;
3) Utiliser une graisse répondant aux
spécifications du roulement.
I.3 Aperçus des Formules
1) Graissage initial selon le type de roulement ;
2) Graissage d'appoint selon le type de roulement ; ---
Quantité de graisse à ajouter
--- Fréquence de graissage
? Graissage initial1
Pour le graissage initial des roulements, la quantité
de graisse est établie en calculant l'espace libre contenu dans le
roulement. On doit remplir cet espace libre entre 30-40 % avec la graisse.
QTÉ (g) = B x D x 0.005 (1.1)
9
B= Largeur du roulement (mm)
D= Diamètre extérieur du roulement (mm) g =
Gramme
? Graissage d'appoint
L'appoint en graisse doit se faire selon un intervalle et une
quantité déterminée. Il n'existe aucune donnée
officielle sur les intervalles de lubrification et les quantités
à ajouter. Les formules suivantes donnent un aperçu de ces
intervalles et quantités afin d'avoir un chiffre approximatif pour les
roulements dont nous n'avons pas de données.
En règle générale, le graissage d'appoint
utilise entre 30-45 % de la quantité de graisse initial.
Se rappeler qu'il vaut mieux graisser plus souvent avec une
quantité plus petite. On peut donc diviser les résultats obtenus
pour faire le graissage plus souvent. Ex : 21 grammes aux 3 mois pourrait
devenir 7 grammes par mois.
10
I.4 Fréquence de regraissage2
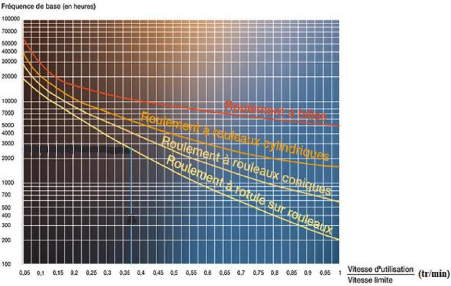
Figure 1.2
La fréquence de base (Fb) de graissage dépend du
type de roulement et du rapport de la vitesse d'utilisation, sur la vitesse
limite donnée dans les caractéristiques du roulement. Cette
fréquence de base doit être corrigée par les coefficients
ci-dessous en fonction des conditions d'environnement particulières du
mécanisme (poussière, humidité, chocs, vibrations, axe
vertical, température de fonctionnement...) selon la relation :
Fc = Fb x Te x Ta x Tt (1.2)
|
Environnement
|
Application
|
Température
|
Conditions
|
-Poussière -Humidité -Condensation
|
-Avec chocs -Vibrations -Axe
vertical
|
Niveau (°c)
|
Pour graisse standard
|
Pour graisse haute températ ure
|
Coefficients
|
Te
|
Ta
|
Tt
|
Tt
|
2 Catalogue lubrification SNR, Op.cit.
11
Moyenne
|
0.7 à .09
|
0.7 à 0.9
|
75
|
0.7 à 0.9
|
-
|
Forte
|
0.4 à 0.7
|
0.4 à 0.7
|
75 à 85
|
0.4 à 0.7
|
0.7 à 0.9
|
Très forte
|
0.1 à 0.4
|
0.1 à 0.4
|
85 à 125
|
0.1 à 0.4
|
0.4 à 0.7
|
|
-
|
-
|
130 à 170
|
-
|
0.1 à 0.4
|
I.5 Calcul de la quantité de graisse à
ajouter
QTÉ (g) = B x D x 0.002 (1.3)
B= Largeur du roulement (mm)
D= Diamètre extérieur du roulement (mm)
? Facteur Température
Ces calculs sont basés sur une température de
roulement de 70°C (Mesuré sur l'extérieur du roulement).
Pour chaque tranche de 15° C de plus, il faut diminuer
l'intervalle de moitié. Dans le cas d'une température de
roulement de moins de 50° C, on peut doubler l'intervalle de graissage.
Attention prendre toujours soins de respecter les
températures permises de la graisse et des roulements.
? Autres Facteurs
D'autres facteurs tel que les vibrations excessives, la
quantité de poussière dans l'air ambiant et le taux
d'humidité peuvent influencer l'intervalle de graissage. Graisser plus
Souvent dans de telles conditions. Faire un graissage avant et après de
longues périodes d'arrêts. Pour les roulements à billes et
les Roller Bearing (rouleaux cylindriques), diminuer l'intervalle de temps de
la moitié.
12
CHAPITRE II. HYDRAULIQUE INDUSTRIELLE
L'hydraulique industrielle est un domaine très vaste,
alors on s'intéresse d'abord aux composants essentiels participant
à la réalisation des circuits hydrauliques: (pompes,
distributeurs, répartiteurs, limiteur de pression, régulateurs de
pression, limiteur de débit...).
Ce chapitre présente les caractéristiques de ces
composants et les notions de base des systèmes hydrauliques dont on aura
besoin dans notre travail.
II.1 Fluides hydraulique3
Le pétrole brut est le produit de base pour tout
lubrifiant, indépendamment du fait qu'il soit à base d'huile
minérale ou synthétique. La figure 1.3 montre un schéma
très simplifié des différentes méthodes de
fabrication.
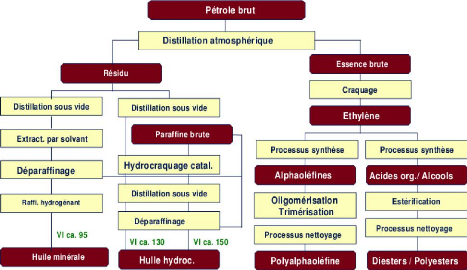
Figure 2.1
Les huiles brutes sont différentes car issues de
pétroles bruts différents. Les fabricants d'huile effectuent des
mélanges d'huiles brutes
3 Henry ClémençonL, ABC du
graissage, éd2009, Castrol, Switzerland, p12
13
appelées huiles de bases pour obtenir une huile de
meilleure qualité. Il est nécessaire d'apporter des additifs pour
en améliorer les caractéristiques physiques, chimiques, les
performances et adapter cette huile pour satisfaire des conditions de travail
particulières.
Les additifs sont très variés et chacun donne
à l'huile finie des propriétés particulières
qu'elle ne possédait pas originellement ou améliore ses
propriétés intrinsèques.
Fonction d'additifs
|
Antioxydant
|
retarder le vieillissement des huiles de base
|
Anticorrosif
|
protéger les métaux cuivreux et les
antifrictions
|
Antirouille
|
protéger les alliages ferreux
|
Anti-usure soufre, zinc, phosphore
|
limiter la dégradation mécanique des pièces
en frottement
|
Extrême pression
|
maintenir un film d'huile entre les surfaces de deux
pièces fortement pressée
|
Anti-mouse
|
éviter les problèmes dus à un moussage
excessif
|
Améliorant d'indice de viscosité
|
permettre l'utilisation de l'huile dans une plus grande plage
de température
|
Détergence
|
assurer la propreté interne des circuits, neutraliser
les acides
|
II.2 Les graisses4.
Une graisse lubrifiante est un produit de consistance
semi-fluide obtenue par dispersion d'un agent épaississant ou
gélifiant dans une huile minérale ou synthétique, avec
éventuellement divers additifs destinés à lui
conférer des propriétés spécifiques à des
applications particulières. Les agents épaississants ou
gélifiants généralement des savons métalliques
constituent la phase solide dispersée dans la graisse. Ils se
présentent soit comme un enchevêtrement des fibres soit comme une
dispersion des particules pulvérulentes. Les teneurs classiques sont de
5 à 40%.
4 RENE GRAS, Tribologie, éd 2008, Dunod,
Paris, p183
14
Savon
|
Point de goutte °C
|
Température d'utilisation °C
|
Résistance à H2O
|
Calcium
|
100
|
60
|
Bonne
|
Lithium
|
180
|
120 à 140
|
Moyenne
|
Aluminium
|
140
|
80 à 100
|
Bonne
|
Baryum
|
160
|
110 à 120
|
Excellente
|
Sodium
|
170
|
130
|
Mauvaise
|
II.3. Graisse au lithium5
Caractéristiques
|
Unité
|
Valeur
|
Masse volumique
|
[kg/m3]
|
900
|
Aspect
|
|
Graisse noire
|
Epaississant
|
|
Lithium
|
Type d'huile de base
|
|
Huile minérale
|
Plage de température
|
[°c]
|
-30 à 150
|
Viscosité de l'huile de base à 40c
|
[mm2/s]
|
150
|
II.3 Réservoir d'huile
Le réservoir en tant que tel est un
élément principal du circuit oléo hydraulique du fait
qu'il emmagasine à l'abri des poussières, la quantité des
graisses nécessaire au fonctionnement correct de l'installation.
Symboles.

5Schaeffler Technologies GmbH & Co. KG, éd
2010, FAG, p16
15
II.4 Pompe hydraulique6
1. Rôle de la pompe dans un système
hydraulique
La pompe est destinée à transformer une
énergie mécanique fournie par un moteur en énergie
hydraulique. Son rôle se limite à aspirer l'huile de
réservoir et de la refouler. La pompe fournit un débit. Elle est
donc un générateur de débit.
2. Les caractéristiques générales
d'une pompe
Une pompe se caractérise par :
- son débit
- sa cylindrée
- son rendement
- son sens de rotation
- sa vitesse de rotation
y' Débit
C'est le volume de graisse que la pompe peut fournir pendant
l'unité de temps pour une vitesse de rotation établie.
Q : débit, en m3/s
y' Cylindrée
Elle correspond au volume d'huile théorique
débitée par tour en cm3 ou en litre. Donc le
débit Q correspond à la cylindrée par la vitesse de
rotation.
Q= Cyl. N (2.1) Avec : Q: débit, en litres /minute
(l/min) ; Cyl: Cylindrée, en litres/tour (l/tr);
N : vitesse de rotation, en tours /minute (tr/min).
6 Sami Bellalah et Iset Nabeul, Hydraulique
Industrielle, p12
çg= çv .çm (2.6)
16
? Rendements
- La puissance hydraulique à la sortie
d'une pompe, traitant le débit volumique Q est :
PH (w) = P (Pa) x Q (m3/s) (2.2)
- La puissance donnée à la pompe
par le moteur dont l'axe tourne à la vitesse w
et transmet un couple C, s'écrit :
Pa= C. ù (2.3)
C : moment du couple appliqué à
l'arbre d'entraînement de la pompe (N.m), w: La vitesse
angulaire de l'arbre d'entraînement de la pompe (rad/s),
Pa : La puissance absorbée par la
pompe (W). Ces deux relations permettent d'exprimer le rendement global
d'une pompe :
çg = (2.4)
Pour affiner notre connaissance d'une pompe
volumétrique, on peut définir le rendement
Volumétrique : rapport du débit réel au
débit théorique, (qui permettra de connaître les fuites)
:
çv = (2.5)
Le rendement mécanique ; rapport du
couple théorique au couple réel (qui permettra de connaître
les pertes mécaniques : Frottement). Le produit de ces deux rendements
est évidemment le rendement global :
17
Symboles
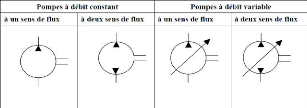
3. Classification des pompes
On classe les pompes en deux grandes familles :
- Les pompes non volumétriques ; dans lesquelles la
chambre d'admission et la chambre de refoulement où le fluide est
expulsé ne sont pas séparées l'une de l'autre par des
pièces mécaniques rigides.
- Les pompes hydrodynamiques (volumétriques), dans
lesquelles la chambre d'admission est séparée par des
pièces mécaniques rigides de la chambre de refoulement, ce qui
assure l'étanchéité entre ces deux chambres.
4. Les pompes à engrenages extérieures -
Fonctionnement
Elle est constituée de deux engrenages tournant
à l'intérieur du corps de pompe. Le principe consiste à
aspirer le liquide dans l'espace compris entre deux dents consécutives
et à le faire passer vers la section de refoulement (La rotation
d'un pignon entraîne la rotation en sens inverse de l'autre, ainsi une
chambre se trouve à l'aspiration, l'autre au refoulement).
18
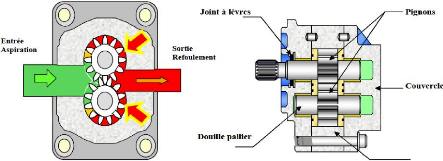
Figure 2.2
Avantages
|
Inconvénients
|
*Débit régulier ; *Pas de clapets
nécessaires ; *Marche de la pompe réversible.
|
*Nombres pièces d'usure élevée
*Pas de particules solides dans cette pompe, ni de produits
abrasifs ; la présence de traces de solide ayant pour effet
d'accélérer l'usure mécanique des pignons et de diminuer
l'étanchéité entre le corps de pompe et les dents.
|
II.5 Tubes7
Les tubes sont utilisés pour la conduction du fluide de
la pompe aux appareils et aux récepteurs. Ces tubes peuvent être
rigides ou flexibles faits à base de caoutchouc, de couches textile et
métalliques. Les caractéristiques du tube dépendent des
éléments suivants :
? le débit à transporter(en l/min) qui
détermine la section intérieur du tube ;
? la pression de service maximale qui doit être
supportée et qui détermine l'épaisseur du tube ;
? la manière de réaliser les couplages entre les
parties du tube
(soudure, bride, filetages, raccords, colliers de serrage,
etc....) ;
7 J.ROLDAN VILORIA, Aide-mémoire Hydraulique
industrielle, éd 2002, Dunod, Paris, p110
19
· la fixation des tubes aux appareils et autres
éléments. Attention au coup de bélier ;
· la connexion du tube aux appareils ;
· les formes du tracé du tube (courbes, coudes,
parties droite horizontales et verticales, réductions, couplages,
connexions, etc....) ;
· la rugosité intérieure du tube.
1. Caractéristiques des tubes flexibles en
caoutchouc, tresses textiles, tresses métalliques8
Diamètre extérieur (mm)
|
14
|
17,5
|
19
|
21,5
|
24,5
|
28
|
32
|
Diamètre intérieur (mm)
|
4
|
6
|
8
|
10
|
13
|
16
|
19
|
Epaisseur (mm)
|
5
|
5,75
|
5,5
|
5,75
|
5,75
|
6
|
6,5
|
Pression de service (bar)
|
630
|
530
|
430
|
390
|
330
|
255
|
210
|
Pression de rupture (bar)
|
1900
|
1600
|
1300
|
1170
|
1000
|
770
|
630
|
|
2. Perte de charge dans les tubes9
Tout fluide qui circule dans une conduite rencontre deux
types de difficultés ou des résistances provoquant des pertes de
charge.
Ces résistances sont :
· Des résistances localisées qui
produisent des pertes de charge locales, telles que des coudes, des tubes, des
soupapes, des fonctions...
· Des résistances réparties qui causent
des pertes de charge longitudinales et sont dues au frottement.
2.1. Calcule de pertes de charge10
Le calcul de la perte de charge linéaire, celle
correspondant à l'écoulement général dans un
conduit rectiligne, est donné par la formule générale
suivante :
8 J.ROLDAN VILORIA, op.cit, p117
9 IDEM, p122
10 IBIDEM
20
· P = perte de charge linéaire en Pa
;
· f = coefficient de perte de charge (nombre sans
dimension) ;
· = masse volumique de l'eau en kg/m3
;
· V = vitesse d'écoulement en m/s ;
· d = diamètre hydraulique du tube en m
;
· L = longueur du tube en m.
La valeur du coefficient de frottement dépend du
régime du fluide en régime laminaire.
f= (2.8)
En régime turbulent :
Avec Re le nombre de Reynolds donné par
Re = (2.10)
Où y est la viscosité cinématique du
fluide ; la viscosité du fluide est donnée par la formule :
V=
2.2. Pertes de charge singulières Dans ce
cas-là, la formule devient :
21
Où k est un coefficient dépendant de la forme
du tube
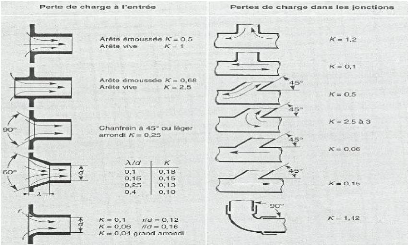
Figure 2.3
2.3. Pertes de charge totales d'un tronçon
kpv
?P = ?PR + ?PS = pv2Lf2
+ ? (2.13)
2d 2
II.6 Régulateur de pression
Contrairement au « Limiteur de pression », le
régulateur de pression peut être réglé à une
valeur de pression désirée, mais qui ne sera jamais
supérieure à celle délivrée par la centrale
hydraulique.
Symbole
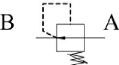
A action directe
22
II.7 Soupape de limitation de pression
Un limiteur de pression est un système de
régulation utilisé dans de nombreux domaines de l'industrie. Il
est indispensable en parallèle de la sortie d'une pompe hydraulique, et
en protection des récepteurs si ceux-ci sont soumis à un effort
extérieur non contrôlé. Il permet de limiter la pression
interne d'un circuit hydraulique ou pneumatique en dérivant
l'excès de pression vers le circuit basse pression.
Symboles
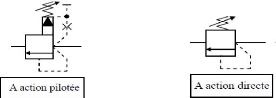
II.8 Soupape anti-retour
Les clapets anti-retour sont des valves d'obturation. Ces
valves permettent l'écoulement dans un sens et le bloquent dans le sens
contraire. Ce sont des clapets plans à rappel par ressort pouvant
être vissés dans les deux sens, pour séquences de
commutation rapides.
Symbole


23
II.9 Distributeur hydraulique
Les distributeurs hydrauliques, comme leur nom l'indique ont
pour objectif de distribuer le fluide hydraulique dans la direction qui
convient le mieux aux appareils de l'utilisation.
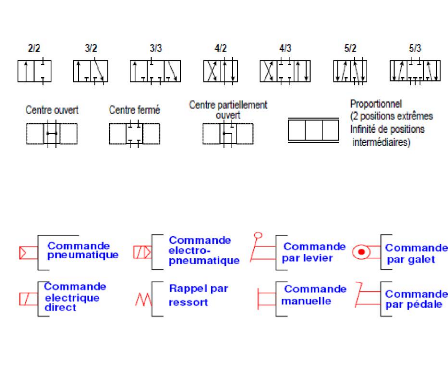
1. Symboles des distributeurs
2. Symboles de Commandes des distributeurs II.10
Manomètres
Ce sont des appareils qui indiquent la pression du fluide
à l'endroit où ils sont installés. Selon les
caractéristiques, les coups de bélier ou les impulsions brusques,
qui conduiraient à la détérioration du manomètre,
peuvent être évités.
24
Symbole
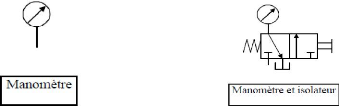
a b
II.11 Répartiteur progressif
Le répartiteur progressif est un élément
hydraulique à tiroirs. Les tiroirs sont mis en mouvement par
l'adjonction de lubrifiant qui les déplace point par point afin
d'alimenter chaque sortie. En cas de difficultés dans le mouvement du
fluide,
ex: une coquille de palier qui se
déplace ou un flexible qui se ferme, le répartiteur se bloque et
dans le cas d 'une installation équipée d'une pompe, le
lubrifiant sort par la soupape de surpression. Le répartiteur progressif
est modulable. Il a l'avantage d'être adaptable au nombre de points de
graissage groupés et que des modules de différents volumes
peuvent être rassemblés. Ces volumes sont obtenus par des
diamètres différents de tiroirs. Pour le bon fonctionnement, au
moins 3 tiroirs sont nécessaires.
Donnes techniques Nombre d'éléménts
:
Pression de service entrée :max 300bar min :3/6 (3
éléments)
Temperature de service : -35°C jusau'a+100°C max :10/20
(10 éléments) Lubrification :Huile-graisse 00-graisse
? Rôle des distributeurs progressifs
La fonction du distributeur progressif est d'acheminer
successivement aux points à graisser, par doses
prédéterminées, le lubrifiant reçu sous pression
(graisse). Le distributeur débite tant qu'il est alimenté
lui-même en lubrifiant sous pression.
25
Le dosage est effectué par le mouvement des pistons.
Chaque piston dessert deux sorties de lubrifiant raccordées à ses
deux extrémités. Le nombre de pistons du distributeur est
variable. L'arrivée sous pression du lubrifiant pousse successivement
les pistons sur leur butée. Le mouvement des pistons a pour effet de
refouler la quantité de lubrifiant se trouvant devant le piston vers la
sortie située en aval. Un piston ne peut se déplacer que lorsque
le piston placé devant lui a atteint sa butée. Les points de
graissage ont reçu la quantité prévue de lubrifiant une
fois que tous les pistons ont effectué un aller-retour entre les
butées droite et gauche. Les doses fournies par les deux sorties sont
déterminées par le diamètre et la course du piston. Le
choix du débit s'effectue au moment de la conception du distributeur, il
ne peut être modifié que par une transformation du
distributeur.
Symbol
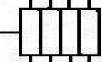
DIN ISO 5170
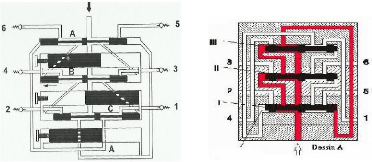
Figure2.4
26
CHAPITRE III : PRESENTATATION DU PILOTE CRUSHER
III .1 Définition du concassage
Le concassage est l'opération qui permet la
réduction granulométrique des matériaux, autrement dit la
diminution de la taille des éléments qui constituent les
matériaux en cours d'élaboration.
Il s'agit d'un procédé purement mécanique
qui consiste, le plus souvent, à placer les matériaux entre deux
plaques métalliques dont l'une est fixe et l'autre est mobile et se
rapproche de la plaque fixe. En fonction de la vitesse de rapprochement nous
parlerons d'écrasement.
III .2 Description de la chaine
La chaine d'extractions est constituée de :
> Grizzly (Alimentateur vibrant) ;
> Jaw Crusher (Concasseur à mâchoire) ;
> Convoyeur n°1 MC1000 ;
> Convoyeur n°2 MC800 ;
> Screen (Cribleur) n°1 ;
> Convoyeur n°3 MC800 ;
> Concasseur à cône ;
> Convoyeur n°4 MC800 ;
> Convoyeur n°10 MC800 ;
> Convoyeur n°5 MC800 ;
> Twister ;
> Convoyeur n°6 MC800 ;
> Screen (Cribleur) n°2 ;
> Convoyeur n°7 MC600 ;
> Convoyeur n°8 MC800 ;
> Convoyeur n°9 MC600.
27
III.2.1 Grizzly (Alimentateur Vibrant) ? Introduction
L'alimentateur vibrant est conçu pour
fonctionner sous des conditions dures dans une carrière ou une mine. Il
sert à réguler le coefficient d'alimentation du concasseur en
séparant les matériaux selon la taille, dégageant les
non-broyables, et passant les plus petits de façon à maximiser la
capacité de concassage du broyeur.
Dans le processus de production, l'alimentateur vibrant peut
alimenter l'équipement de concassage également,
régulièrement et continuellement, et d'ailleurs, il peut aussi
effectuer le criblage primaire des matériaux.
? Principe de fonctionnement
Notre alimentateur vibrant consiste en une alimentation
à travers un vibrateur, ressort, moteur, etc. La source de vibration de
l'alimentateur de matériaux est faite de deux manches (actif et passif)
et d'un engrenage. Le manche principal est actionné par le moteur
grâce au convoyeur en V, le manche passif commence à tourner
à travers la maille d'engrenage du manche actif. Ensuite le manche
contre rotatif force l'alimentateur à vibrer. Grâce à ces
vibrations, les matériaux vont glisser et s'élinguer dans la
cheminée remuant en arrière. Quand les matériaux passent
dans le tamis, les plus petites particules vont tomber complétant le
cycle.
? Caractéristiques
1. Barre de connexion sidérurgique résistante,
4 ressorts pour supporter le cadre général garantissant des
vibrations stables et des opérations fiables ;
2. Machine capable de réaliser des ajustements
variables de capacité d'alimentation grâce à la vitesse du
moteur variable;
3. La barre spécialement conçue est
utilisée pour éliminer le blocage de matériaux pour
améliorer l'effet de tamis.
28
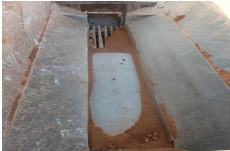
Figure 3.1
III.2.2 : Jaw Crusher (Concasseur à
mâchoire)
Un concasseur est un équipement lourd destiné
à briser la pierre en petits fragments appelés
Agrégats.
? Introduction
Le concasseur à mâchoires est le plus ancien
genre de concasseur. Grâce à sa structure simple, son bâti
solide, son fonctionnement stable et son entretien facile ainsi que son
coût faible, il est donc toujours utilisé dans l'industrie
métallurgique et chimique, les matériaux de construction, le
domaine électrique et la circulation etc.
Le concasseur à mâchoire est une machine à
broyer des roches (granite, calcaire, etc.) généralement à
des fins industrielles, vu que la roche est la matière première
par excellence de quasiment toutes les industries (métallurgie
minière, etc.). Il sert à broyer des divers minerais et roches
gros, moyens et fins avec une résistance à la compression de 147
à 245 Mpa.
? Principe de fonctionnement
Le concasseur à mâchoires fonctionne à la
manière de l'extrusion et le mouvement curviligne, son principe de
fonctionnement est le suivant:
L'appellation « à mâchoire » est due au
dispositif de broyage, qui reprend le principe de base d'une mâchoire,
avec une paroi fixe et un autre mobile, la roche étant coincée
entre les deux. Le moteur électrique entraîne la courroie et la
poulie, déplace la mâchoire mobile de haut en bas en utilisant
l'arbre
29
d'excentrique. L'angle entre la plaque à coude et la
mâchoire mobile s'augmente lorsque celle-ci monte, ceci favorise
l'approche de plaque de mâchoire mobile vers la plaque de mâchoire
fixée, et en même temps les matériaux primaires sont
concassés; l'angle diminue lorsque la mâchoire mobile descend,
sous la force du levier et du ressort, celle-ci se sépare de la plaque
de mâchoire fixée, et les matériaux broyés
s'évacuent de l'ouverture de décharge de la chambre de
concassage. La mâchoire mobile fonctionne périodiquement au fur et
à mesure que le moteur tourne continuellement, pour réaliser la
production en série.
? Caractéristiques
V' Assemblage des mâchoires mobiles est plus
avancé, composé des moulages d'acier de bonne qualité, et
entraîné par deux grands volants moulés d'acier, de plus,
l'arbre d'excentrique lourd est façonné en billette
forgée.
V' Le support de roulement est un ensemble moulé
d'acier, par rapport au support fendu, ceci peut assurer l'harmonisation
complète avec le bâti de concasseur, et aussi bien augmenter la
résistance diamétrale du support de roulement.
V' La chambre de concassage est en structure de forme
«V» symétrique, cela fait l'unanimité de largeur
réelle et nominale de l'ouverture d'alimentation.
V' Un dispositif de coin équipant dans les concasseurs,
par rapport au dispositif de coussin ancien, permet de régler
l'ouverture de décharge plus rapidement, simplement et en
sécurité.
V' Le roulement d'excentrique choisi dans tous les concasseurs
est plus grand, plus durable que celui-ci d'autres concasseurs en même
spécification, sa capacité de charge plus haute et son scellement
dédaléen plus effectif rallongent sa vie d'utilisation
énormément.
30
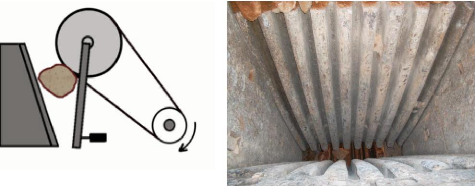
Figure 3.2
III.2.3 Convoyeurs à Bandes ? Introduction
Le convoyeur à bande est une machine
de transfert essentiel et économique dans la ligne de production
ininterrompue.
Le convoyeur à bande est une sorte d'équipement
de traitement à sable et gravier principalement utilisé pour les
équipements vibrants et usines de concassage. Il joue un rôle
important dans la connexion de chaque installation de production, ce qui
facilite la réalisation de la continuité et l'automatisation du
traitement de production, améliore la production et réduit
l'intensité de la charge de travail. C'est un appareil auxiliaire
basé sur le principe de friction.
? Principe de fonctionnement
Le système du convoyeur à bande est
constitué d'un cadre métallique avec des rouleaux à chaque
extrémité d'un lit plat en métal. La bande est
enroulée autour des rouleaux et quand l'un des rouleaux est
alimenté (par un moteur électrique) les courroies se glissent sur
le lit en métal solide, transportant les produits. Pour les applications
des produits lourds, les lits sur lesquels les courroies posent sont
remplacés par des rouleaux.
31
Les rouleaux permettent de transporter des produits lourds, car
ils réduisent la friction produite à partir de la charge plus
lourde sur les courroies.
> La taille de pierre doit être modérée,
elle ne peut pas être trop grosse > La production doit être
uniforme
> L'utilisation de la bande de convoyage différent
selon la pierre
> L'justement de la vitesse de convoyage selon l'angle
? Caractéristiques
V' convoyage stable et plus long sans mouvement relatif.
V' réduction du bruit
V' structure simple, entretien facile, économies
d'énergie et faible coût.
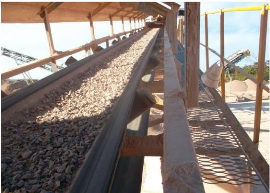
Figure 3.3
III.2.3.1 Types des convoyeurs11 III.2.3.1.1 MC1000
Le convoyeur MC 1000 pilote modulaire est un convoyeur robuste et
est conçu pour fonctionner dans des fonctions de transfert des
matières.
11
WWW.Pilotcrushtec.com
32
--
? Convoyeur
-Largeur : 1000mm
-Options de longueur : 11m
-Type de ceinture : 200/3 plis
-Suivi ceinture : type à vis réglable Vitesse :
1440/15 tr/min
-Tambour d'entraînement : caoutchouc retardé
-Grattoir : racleur auto tension sur le tambour
d'entraînement et grattoir
plough sur le tambour de queue
-Support : structure d'appui fixe
? Options d'entraînement
Commande : 15kw, 380 V et moteur électrique avec boitier
d'entraînement hélicoïdal réducteur directe.
Poids estimé
Total : 2200kg convoyeur 9m et 2500kg convoyeur 11m
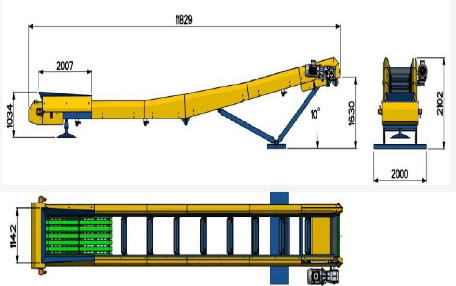
Figure 3.4
33
III.2.3.1.2 MC 800
Le convoyeur modulaire MC800 est un pilote monté sur
roues, service moyen de transport et est conçu pour fonctionner dans le
transfert des matières.
? Convoyeur
-Largeur : 800mm
-Options de longueur : 16m
-Type de ceinture : 200/3 plis
-Suivi ceinture : type à vis réglable Vitesse :
1440/14,3 tr/min
-Tambour d'entraînement : caoutchouc retardé
-Grattoir : racleur auto tension sur le tambour
d'entraînement et grattoir
plough sur le tambour de queue
-Passerelles : walkway
? Options d'entraînement
MC
|
Largeur (mm)
|
Longueur(m)
|
Angle(°)
|
Hauteur (mm)
|
Puissance (kW)
|
Poids (kg)
|
|
|
8
|
10°
|
1211
|
7.5
|
2600
|
|
|
|
20°
|
4079
|
7.5
|
2940
|
|
|
12
|
12°
|
1839
|
|
|
MC800
|
800
|
16
|
20°
|
5447
|
9.2
|
3280
|
|
|
|
12°
|
3342
|
|
|
|
|
20
|
21°
|
7279
|
9.2
|
3621
|
|
|
|
13°
|
4899
|
|
|
34
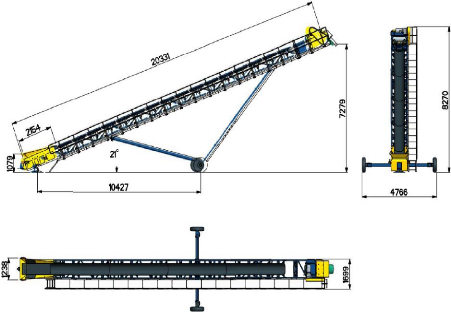
Figure 3.5
III.2.3.1.3 MC600
Le pilote modulaire MC600 convoyeur est monté sur deux
roues, service moyen de transport et est conçu pour fonctionner dans le
transfert des matières.
? Convoyeur
-Largeur : 600mm
-Options de longueur :16m - Type de ceinture : classe 200/3
plis -Suivi ceinture : Type à vis réglable -Tambour
d'entraînement : caoutchouc retardé
-Grattoir : racleur auto tension sur tambour d'entraînement
et grattoir plough sur le tambour de queue
35
? Option d'entraînement
MC
|
Largeur (mm)
|
Longueur(m)
|
Angle(°)
|
Hauteur (mm)
|
Puissance (kW)
|
Poids (kg)
|
|
|
7
|
11°
|
1701
|
3.3
|
940
|
|
|
|
20°
|
3657
|
|
|
|
|
10
|
16°
|
3047
|
3.0
|
1262
|
|
|
|
13°
|
2542
|
|
|
|
|
|
20°
|
4570
|
|
|
|
|
13
|
16°
|
3870
|
3.0
|
1460
|
MC600
|
600
|
|
13°
|
3300
|
|
|
|
|
|
20°
|
5730
|
|
|
|
|
16
|
16°
|
4575
|
4.0
|
1660
|
|
|
|
13°
|
3850
|
|
|
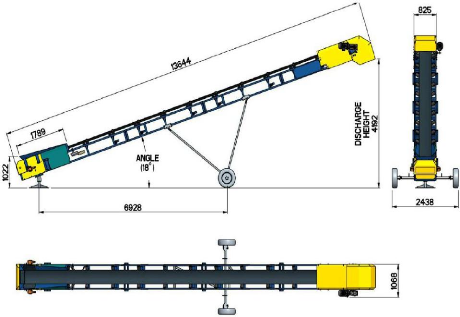
Figure 3.6
36
III.2.4 Screen (Cribleur) ? Introduction
Le crible vibrant est appelé
également le crible vibrant circulaire en raison de son mouvement
approximativement circulaire. Il est fabriqué dans une structure robuste
afin d'être installé sur le site avec un angle de 15-20°,
nécessitant moins de puissance grâce à leur pente de
15-20° et à l'effet de gravité. Il est de multicouche, le
design simple le rend particulièrement utile et économique pour
le criblage des roches et matériaux de grosse taille. L'unité
vibrante est formée d'un arbre excentrique à balourd doté
de contrepoids permettant des courses différentes qui
génèrent un mouvement circulaire. L'excitateur de vibration de
l'arbre excentrique et le bloc partiel aident à ajuster l'amplitude.
? Principe de fonctionnement du crible
vibrant
Le crible vibrant tourne. Il a de multicouches et une grande
efficacité. L'excitateur de l'arbre excentrique de vibration et le bloc
partiel aident à adapter à l'amplitude. Le matériel
descend le long de la ligne longue. Dans le classement de criblage, il est
séparé mécaniquement sur des plaques du crible. Les
roulements du crible vibrant sont principalement stressés par de hautes
charges de type de choc. En outre, les roulements, tout en tournant autour de
leur axe, effectuent un mouvement circulaire elliptique ou linéaire. Il
en résulte une forte accélération radiale qui produit
considérablement en plus de stress sur les roulements, et en particulier
sur les cages, La vitesse de fonctionnement est généralement
très élevée de l'ordre de 1440tr/min.
? Caractéristiques
V' Bloc excentrique pour produire une forte force excitante.
V' Poutre et le cadre principal connectés avec des
boulons à haute résistance.
V' Structure de faible amplitude, de fréquence
élevée, et de grande obliquité pour accorder au crible
l'efficacité élevée, la capacité de
37
gérer, une longue durée de vie, une faible
consommation avec peu de bruit.
? Le tamis vibrant utilise un rotor d'isolation vibrant pour
une amplitude stable, des hautes performances et un faible niveau sonore.
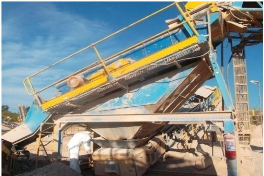
Figure 3.7
III.2.5 Concasseur à cône
? Introduction
Nous avons deux types de concasseur à cône: le
concasseur à cône hydraulique et le concasseur à cône
de ressorts. Les deux types sont destinés à un concassage
secondaire ou tertiaire que ce soit dans une installation fixe ou mobile pour
des matériaux hautement abrasifs et été largement
utilisée dans les industries de métallurgie, le bâtiment,
la construction de routes, de phosphate et de l'industrie chimique, et
principalement utilisé pour le broyage des roches, minerai de fer, le
minerai de cuivre, le calcaire, le quartz, le granit, le basalte, diabase,
etc.
? Principe de fonctionnement de Concasseur à
Cône
Un concasseur à cône à un fonctionnement
similaire au concasseur giratoire, avec moins de pente dans la chambre de
concassage et une plus grande zone parallèle entre les zones de
concassage. Un broyeur à cône brise la roche en la serrant entre
une tête excentrée tournante, qui est couverte par un blindage
résistant à l'usure (lower mantle), et le bowl, couvert par un
38
concave manganèse (bowl liner). Comme la roche entre
par le sommet du broyeur à cône, elle se coince et se comprime
entre le lower mantle et le bowl liner. De gros morceaux de minerai sont
cassés une fois, puis tombent à une position inférieure
(car ils sont maintenant plus petits), où ils sont à nouveau
cassé. Ce processus continue jusqu'à ce que les morceaux soient
assez petits pour passer à travers l'ouverture étroite dans le
bas de la chambre de cassage. Un broyeur à cône est adapté
au broyage de divers minerais et roches, pour des duretés allant de
mi-dure à dure.
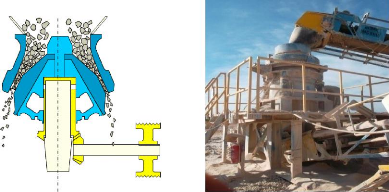
L'impact de broyage où la roche est amenées sur un
rotor de type tableau
Figure 3.8
III.2.6 Twister
? Introduction
Les Twister statiques sont souvent utilisés pour
transformer les déchets et les matières floconneuses en granulats
de qualité cubique en forme ainsi que du sable concasseur constamment
graduée pour une utilisation en tant sables bitumineux, de sable
à mortier, du plâtre ou du sable de haute qualité du sable
à béton. Le faible coût et une forte réduction de
concassage rendent les concasseurs Twister idéal pour une utilisation
dans le traitement des minéraux industriels.
? Principe de fonctionnement
Le Twister est un concasseur à axe vertical.
39
qui accélère et se décharge alors la
roche à grande vitesse contre des enclumes en acier dans la chambre de
broyage. L'impact de la roche contre les enclumes en acier induit la rupture et
brise le roc en éliminant les fissures et les coins vifs.
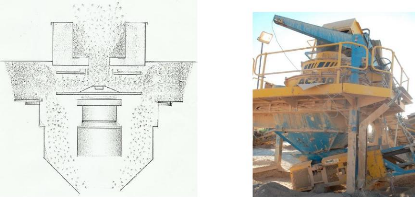
Figure 3.9
40
CHAP IV. SYSTEMES DE GRAISSAGES
IV.1 Graissage manuel
Le graissage manuel s'effectue à l'aide des pompes
à main qui sont généralement destinées à
servir comme pompe de secours ou d'épreuve.
IV.1.1 Types de pompe à main
? La figure 4.1 représente la pompe la plus classique
à deux cylindres à double effet et à clapets ;
? La figure 4.2 représente une variante de la disposition
présidente ;
? La figure 4.3 représente également une pompe
à double effet et à un seul piston, utilisant l'effet du piston
plongeur.
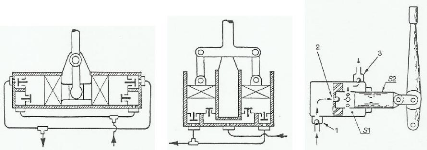
Figure 4.1 Figure 4.2 Figure 4.3
IV.1.2 Fonctionnement
Sur la figure 4.3, on remarque que pendant la course du piston
vers la droite, (2) est fermé, la pompe refoule par la section
différentielle s1, l'aspiration se produit par (1). Pendant la course
vers la gauche, (1) est ferme, (2) est ouvert, la pompe travaille comme une
pompe à piston plongeur de section s2. On remarque que l'aspiration ne
se produit qu'un temps sur deux.
41
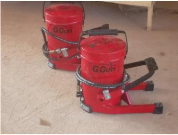
Figure 4.4
IV.1.3 Avantage et Inconvénient de la lubrification
manuelle
1. Avantages
V' Exécution simple ;
V' Pas d'encombrement du circuit hydraulique,
V' Pompe moins lourde
V' Permet aux travailleurs d'être proche de la machine
2. Inconvénients
> Lubrification insuffisante
> Lubrification excessive
> Coût de réparation importante dû à
l'usure > Intervalle de graissage très irrégulier
IV.2 Graissage centralisé
IV.2.1 Définition
Il s'agit d'un ensemble d'éléments relier entre
eux, qui ont pour but de graisser périodiquement et automatiquement les
différents organes en mouvement d'une machine ou d'une installation. Le
graissage centralisé s'effectue en général sans
récupération de l'huile.
42
IV.2.2 Graissage progressive
IV.2.2.1 Principe
Un système progressif se compose pour l'essentiel d'une
pompe, de distributeurs, doseur, raccords, tuyaux et appareils de
contrôle et d'un système de commande. Le volume de lubrifiant
débité par la pompe est envoyé aux points de graissage par
les distributeurs progressifs, en fonction du nombre de leurs pistons et de
leur débit prédéterminé.
IV.2.2.2 Caractéristiques des systèmes
progressifs
> Utilisation universelle quel que soit le type de
fonctionnement (continu/cyclique) et de lubrifiants ;
> Contrôle centralisé du fonctionnement de
tous les points de distribution réalisable facilement ;
> Nombre de cycles : 200/min maximum;
> Distribution précise, grâce à
l'action coordonnée des pistons, du lubrifiant aux points de graissage,
même en présence de contre pression ;
> Nombre maximum de points de lubrification : une centaine
;
> Pressions maximales possibles : 350 bars pour les
systèmes à graisse
IV.2.2.3 distributeurs progressifs
? Distributeurs progressifs à débit
variable12. + Principe de fonctionnement
y' Phase 1
? Le lubrifiant arrive sous pression P dans le distributeur
par le haut (flèche supérieure) et la pression est exercée
sur l'extrémité droite du piston de commande B et du piston
doseur B ;
12 LINCOLN Gmbh, Manuel d'utilisation,
éd 2005, st. Louis, p F9 de 26
43
? La section étant plus grande, la pression P du
lubrifiant fait d'abord déplacer le piston doseur B (flèche
noire) vers la gauche, ce qui amène le lubrifiant enfermé
à gauche du piston doseur B vers la sortie 6(V1).
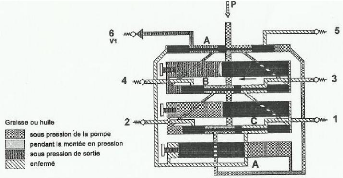
Figure 4.5
? Phase 2
? Dès que le piston doseur B a atteint sa position
finale de gauche, la pression P du lubrifiant fait déplacer le piston de
commande B (flèche noire) vers la gauche, sur quoi le lubrifiant
enfermé à gauche du piston de commande B est amène en plus
à la sortie 6 (V2) ;
? La quantité totale à la sortie 6 est la
quantité de lubrifiant du piston doseur B et du piston de commande B
(V1+V2).
44
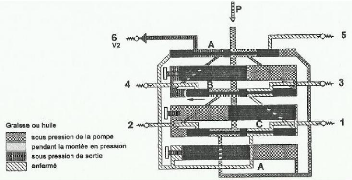
Figure 4.6
y' Phase 3
· A la phase 3, le piston de commande B a atteint sa
position finale de gauche ;
· Il ouvre en même temps le canal de liaison vers
l'extrémité droite du piston de commande C et du piston doseur C
;
· La pression P du lubrifiant est alors présente
sur l'extrémité droite du piston de commande C et du piston
doseur C ;
· La section étant plus grande, la pression P du
lubrifiant fait d'abord déplacer le piston doseur C (flèche
noire) vers la gauche, ce qui amène le lubrifiant enfermé
à gauche du piston doseur C vers la sortie 4(V1).
y' Phase 4
· Dès que le piston doseur C a atteint sa
position finale de gauche, la pression P du lubrifiant fait déplacer le
piston de commande C (flèche noire) vers la gauche, sur quoi le
lubrifiant enfermé à gauche du piston de commande C est
amené en plus à la sortie 4 (V2) ;
· La quantité totale à la sortie 4 est la
quantité de lubrifiant du piston doseur C et du piston de commande C
(V1+V2).
45
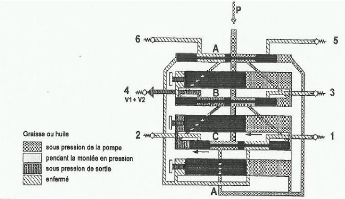
Figure 4.7
y' Phase 5
· A la phase 5, le piston de commande C a atteint sa
position finale de gauche ;
· Il ouvre en même temps le canal de liaison vers
l'extrémité gauche du piston de commande A et du piston doseuse A
;
· La pression P du lubrifiant est alors présente
sur l'extrémité gauche du piston de commande A et du piston
doseuse A ;
· La section étant plus grande, la pression P du
lubrifiant fait d'abord déplacer le piston doseur A (flèche
noire) vers la droite, ce qui amène le lubrifiant enfermé
à droite du piston doseur A vers la sortie 2 (V1).
y' Phase 6
· Dès que le piston doseur A a atteint sa
position finale de droite, le lubrifiant sous pression P fait déplacer
le piston de commande A (flèche noire) vers la droite, sur quoi le
lubrifiant enfermé à droite du piston de commande C est
amené en plus à la sortie 2(V2) ;
· La quantité totale à la sortie 2 est la
quantité de lubrifiant du piston doseur A et du piston de commande A
(V1+V2).
46
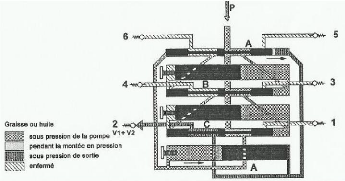
Figure 4.8
y' Phase 7
· A la phase 7, le piston de commande A a atteint sa
position finale de droite ;
· Il ouvre en même temps le canal de liaison vers
l'extrémité gauche du piston doseuse B ;
· Le lubrifiant sous pression P est alors présent
sur l'extrémité gauche du piston de commande B et du piston
doseur B ;
· La section étant plus grande, la pression P du
lubrifiant fait d'abord déplacer le piston doseur B (flèche
noire) vers la droite, ce qui amène le lubrifiant enfermé
à droite du piston doseur B vers la sortie 5 (V1).
y' Phase 8
· Dès que le piston doseur B a atteint sa
position finale de droite, la pression P du lubrifiant fait déplacer le
piston de commande B (flèche noire) vers la droite, sur quoi le
lubrifiant enfermé à droite du piston de commande B est
amené en plus à la sortie 5(V2) ;
· La quantité totale à la sortie 5 est la
quantité de lubrifiant du piston doseur B et du piston de commande B
(V1+V2).
47
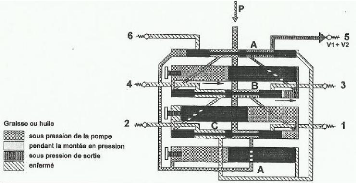
Figure 4.9
y' Phase 9
· A la sortie 9, le piston de commande B a atteint sa
position finale de droite ;
· Il ouvre en même temps le canal de liaison vers
l'extrémité gauche du piston de commande C et du piston doseur C
;
· Le lubrifiant sous pression P est alors présent
sur l'extrémité gauche du piston de commande C et du piston
doseur C ;
· La section étant plus grande, la pression P du
lubrifiant fait d'abord déplacer le piston doseur C (flèche
noire) vers la droite, ce qui amène le lubrifiant enfermé
à droite du piston doseur C vers la sortie 3(V1).
y' Phase 10
· Dès que le piston doseur C a atteint sa
position finale de droite, la pression P du lubrifiant fait déplacer le
piston de commande C (flèche noire) vers la droite, sur quoi le
lubrifiant enfermé à droite du piston de commande C est
amené en plus à la sortie 3 (V2) ;
· La quantité totale à la sortie 3 est la
quantité de lubrifiant du piston doseur C et du piston de commande C
(V1+V2).
48
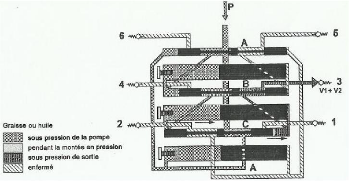
Figure 4.10
y' Phase 11
· A la phase 11, le piston de commande C a atteint sa
position finale de droite ;
· Il ouvre en même temps le canal de liaison vers
l'extrémité droit du piston de commande A et du piston doseur A
;
· Le lubrifiant sous pression P est alors présent
sur l'extrémité droite du piston de commande A et du piston
doseur A ;
· La section étant plus grande, la pression P du
lubrifiant fait d'abord déplacer le piston doseur A (flèche
noire) vers la gauche, ce qui amène le lubrifiant enferme à
gauche du piston doseur A vers la sortie 1(V1).
y' Phase 12
· Dès que le piston doseur A a atteint sa
position finale de gauche, la pression P du lubrifiant fait déplacer le
piston de commande A (flèche noire) vers la gauche, sur quoi le
lubrifiant enfermé à gauche du piston de commande A est
amené à la sortie 1(V2) ;
· La quantité totale à la sortie 1 est la
quantité de lubrifiant du piston doseur A et du piston de commande A
(V1+V2).
49
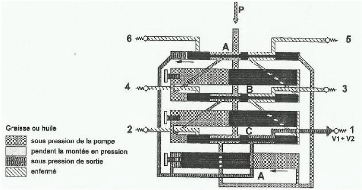
Figure 4.11
Remarque :
Les figures ci-dessus montre la transition entre la phase 3-4
; 5-6 ; 7-8 ; 9-10 ; 11-12. Les figures 5 et 6 montrent des
représentations distinctes des mouvements des pistons doseurs et des
pistons de commande.
? Regroupement interne de sortie
Dans les distributeurs ou les sortie sont regroupées de
manière interne (doseur by-pass), les orifices des sortie 1 et 2 sont
raccordés entre eux ; voir le canal de liaison représente en
pointillés entre la sortie 2 et la sotie 1 ;
Une sortie d'un côté du doseur est fermée
afin de pouvoir utiliser la quantité de lubrifiant double de l'autre
côté ;
Debit V = V1phase5+V2phase6+V1phase11+V2phase12
On a ainsi d'autre possibilités de dosage en regroupant
des sorties: Pratiquement toutes les combinaisons sont possibles, de
l'attribution d'une sortie de doseur à un pont de lubrification jusqu'au
regroupement de toute les sorties en un seul point de lubrification.
50
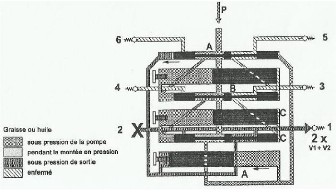
Figure 4.12
? Regroupement externe de sorties
Dans les distributeurs, il est également possible de
regrouper des sorties extérieurement et de les raccorder à un
pont de lubrification au moyen d'une pièce en T.
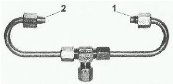
Figure 4.13
Regroupement externe de quantités de lubrifiant,
dispositif à visser
IV.2.3 Eléments à graissés
Sur la machine crusher il y a au moins 56 points a
graissé à savoir ;
? 6 graisseurs au concasseur à mâchoire ; ? 3
graisseurs au concasseur à cône ;
? 3 graisseurs au twister ;
? 4 graisseurs aux screen, dont 2 graisseurs par screen ;
51
? 40graisseurs aux convoyeurs, dont 4 par convoyeur.
IV.2.4 Calcul de la quantité de graisse
1. Jaw crusher
La quantité de la graisse au jaw crusher par jour et
après 8 heures de travail.
Taille jaw
|
Graisse pour les roulements centraux
|
Graisse pour les roulements extrêmes
|
|
Poids (g)
|
Volume (cc)
|
Poids (g)
|
Volume (cc)
|
MJ 2436
|
25
|
30
|
20
|
24
|
|
2. Concasseur à cône
La partie à graisse du concasseur à cône
est normalement fixe et elle est mise en mouvement lors du réglage du
cône. On doit veiller à graisser cette partie
régulièrement afin de pouvoir éviter le blocage du
cône lors du manoeuvre.
3. Twister
Le système de lubrification se compose de trois points
de graissage situés sous le passage de maintenance sur le bâti du
broyeur. Deux nipples extrêmes 10g de graisse doit être
pompée chaque 8heures de travail et 50g de graisse au nipple
centrale.
4. Screen
Screen
|
Description
|
Fréquence
|
Qualité
|
2
|
2 roulements par screen
|
8 heures
|
4g par roulement
|
- La quantité de graisse peut être
augmentée de 20% pour les paliers munis d'un orifice d'évacuation
de la graisse,
52
5. Convoyeurs
Sur la machine crusher nous avons 10 convoyeurs à savoir:
? 1 convoyeur cv1000 ; ? 5 convoyeurs cv 800 ; ? 4 convoyeurs cv 600.
Donc 40 paliers à roulements dont 4 par convoyeur ;
5.1 dimension des roulements
Dimension
|
MC 600
|
MC800
|
MC1000
|
D
|
85
|
100
|
110
|
B
|
22
|
25
|
27
|
darbres
|
45
|
55
|
60
|
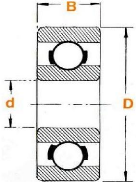
Figure 4.14
5.2 Quantité de graisse par roulement
La graisse doit occuper 20 à 30% du volume libre
à l'intérieur du roulement.
Exceptions :
53
- Un roulement tournant à très faible vitesse
tolère un plein remplissage
1. MC 600
D = 85 B = 22 darbre = 45
De 1.1;
|
g= 0,005.
|
85 .22
|
=
|
9.35g
|
De 1.3
|
gr= 0.002
|
.85.22
|
=
|
3.75g
|
|
2. MC 800
D
|
=
|
100
|
B
|
=
|
25
|
darbre =
|
55
|
|
De 1.1 ; g=0, 005.100.25 = 12.5g
De 1.3 ; gr= 0.002 .100.25 = 5g
3. MC 1000
D = 110
B = 27
darbre = 60
De 1.1;
|
g=0, 005.110. 27
|
=
|
14.85g
|
De 1.3;
|
gr= 0.002 .110. 27
|
=
|
5,94g
|
De 1.2 calculons la fréquence de regraissage
Un roulement graissé avec une graisse standard,
tournant à une vitesse N en environnement poussiéreux, à
75°C sans autres contraintes d'application.
Fréquence corrigée (Fc) = 5000. 0,3. 0,9. 0,4 = 540
heures
54
|
MC600
|
MC800
|
MC1000
|
Vitesse limite
|
1440tr/min
|
1440tr/min
|
1440tr/min
|
Vitesse utilisation
|
1440tr/min
|
1440tr/min
|
1440tr/min
|
Ratio/réducteur
|
13.6
|
14.3
|
15
|
Avec Fb=
|
=
|
|
|
|
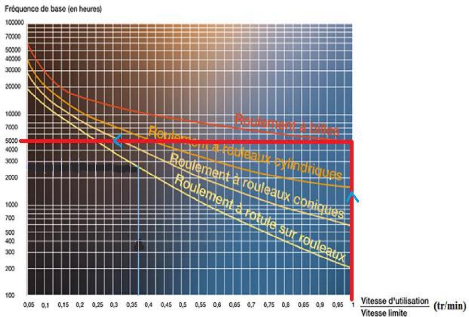
Figure 4.15
Coefficients
Fréquence de base Te = 0,3 ----> poussières
Fb= 5000H Ta = 0,7 ----> avec chocs
Tt = 0,4 ----> à 75°c
55
IV.2.5 Longueur des flexibles
Tête cv1
|
|
Pied cv1 Tête cv2
|
|
Pied cv2 Tête cv3
|
|
Pied cv3 Tête cv4
|
|
Pied cv4 Tête cv5
|
|
Pied cv5 Tête cv6
|
|
Pied cv6 Tête cv7
|
|
Pied cv7 Tête cv8
|
|
Pied cv8 Tête cv9
|
|
Pied cv9
|
Cv 10
|
Screen1
|
Screen 2 Cône
|
|
Mâchoir
|
Mâchoir
|
Twister
|
Flexibles après le répartiteur central
|
Nbre
|
1
|
1
|
1
|
1
|
1
|
1
|
1
|
1
|
1
|
1
|
1
|
1
|
1
|
1
|
1
|
1
|
1
|
1
|
1
|
1
|
1
|
1
|
(m)
|
32
|
50
|
26
|
32
|
47
|
26
|
32
|
47
|
6
|
26
|
20
|
6
|
20
|
20
|
20
|
32
|
26
|
20
|
47
|
40
|
40
|
2
|
Flexibles après le répartiteur progressif
|
Nbre
|
2
|
2
|
2
|
2
|
2
|
2
|
2
|
2
|
2
|
2
|
2
|
2
|
2
|
2
|
2
|
2
|
2
|
2
|
2
|
2
|
2
|
2
|
3
|
2
|
2
|
3
|
(m)
|
10
|
3
|
6
|
8
|
4
|
6
|
2
|
6
|
3
|
3
|
2
|
6
|
19
|
2
|
20
|
2
|
22
|
3
|
8
|
8
|
6
|
4
|
2
|
4
|
5
|
1
|
Localisation de répartiteurs progressifs
|
RP
|
8
|
12
|
5
|
8
|
6
|
5
|
8
|
6
|
3
|
5
|
2
|
3
|
1
|
1
|
2
|
2
|
1
|
1
|
7
|
7
|
1
|
2
|
9
|
10
|
11
|
4
|
Circuit de commande
|
KM
|
8
|
12
|
5
|
8
|
6
|
5
|
8
|
6
|
3
|
5
|
2
|
3
|
1
|
1
|
2
|
2
|
1
|
1
|
7
|
7
|
1
|
2
|
9
|
10
|
11
|
4
|
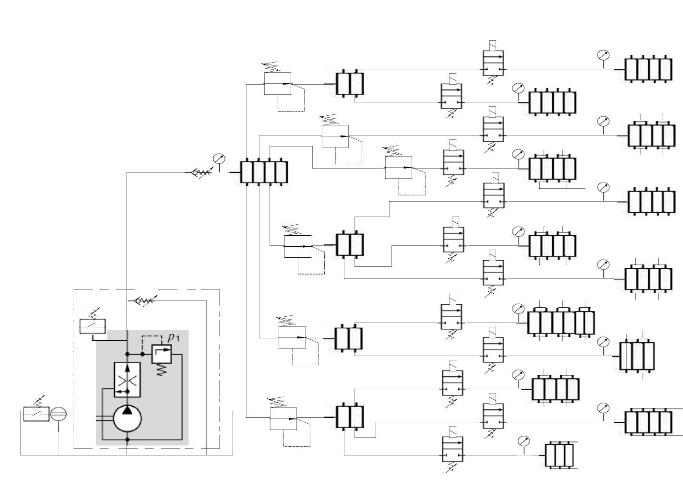
56
M1
D1 /2/2
R A /4
D2 /2/2
R P1/ 4/8
Rp1
M
M3
2
D3 /2/2
R P2 /4/8
MP
R P4 /4/8
D4 /2/2
R P3 /4/8
M5
M
CA
4
Rp3
R C /8
D5 /2/2
R A /4
Rp2
M6
R P5 /4/8
D6 /2/2
M7
Pompes à engrenage
à valves incorporées
D7/ 2/2
R P6 /4/8
CA
M8
R P7 /4/8
IF
D8 /2/2
R P9 /3/6
R A /4
Rp5
Rp4
R P8 /6/12
D9 /2/2
M
9
IO
D10 /2/2
R P9 /3/6
R A /4
D11 /2/2
R P10 /4/8
M
1
0
Rp6
R P11 /4/8
D12 /2/2
M
1
1
M
1
2
R P12 /3/6
57
IV.2.6 Dimensionnement du circuit de graissage Dans notre
circuit de graissage, nous avons :
> les tuyaux (flexibles) haute pression de diamètre
égale à 10 mm13 ;
> de débit maximal par sorties des graisseurs est de
1.8 cm3/s ;
> dans notre circuit l'effort à vaincre aux graisseurs
est de 40N ;
> la pression nécessaire pour faire déplacer les
tiroirs des répartiteurs
est de 100 bars ;
> Vitesse de rotation du moteur électrique est 1500
tr/min à ç = 0,9 ; > Le graisseur le plus
éloigné se trouve à 53m de la pompe.
cyl = 2cm3 = 2 x 10-3 l; comme cylindre de
la pompe ;
?Q=cyl x N = 2 x 10-3 x 1500 = 3 l/min = 5 x
10-5 m3/s d = 10 x 10-3m
s = = = 7, 85 x 10-5 m2
V = = 0.6369m/s
P = 509554, 1401Pa
? P = 509554, 1401+ (100 x 105) = 10509554, 14
Pa
> Détermination des pertes de charge en fonction du
graisseur le plus éloigné.
42, 46
f= 1, 5073
?P =
+ [5(1.12 2(1, 2
)]
= 1459705, 593 Pa = 14, 5971bar
13 LINCOLN Gmbh, Manuel d'utilisation,
éd 2005, st. Louis, p F6 de 26
58
? Pt = 10509554, 14 + 1459705, 593 =11969259, 73
Pa
Pour la sécurité de notre circuit on y ajoute
10% de la pression totale.
?Pt=11969259, 73 + 13166185, 71 = 131, 6619
bar.
PH = 13166185, 71 x (5 x 10-5) = 658, 3093
w
ç 731, 4548 w
La puissance mécanique normalisée est de 750 w
sur un réseau de 380 V et la vitesse de rotation est de 1380
tr/min.14
çv = = = = 0.92
IV.2.7 Avantages du graissage centralisé
V' Gains accrus grâce à une meilleure
productivité ;
V' Réduction des temps d'immobilisation improductifs et
onéreux dus à une lubrification inadéquate ;
V' Consommation de lubrifiants réduite grâce au
dosage précis ;
V' Sécurité du travail accrue, les ponts de
lubrification difficilement
accessibles sont regroupés et alimentés depuis un
pont central
d'accès aisé ;
V' Alimentation fiable de tous les points à lubrifier. Pas
d'oubli.
IV.2.8 Inconvénients du graissage centralisé
+ Vitesse de fonctionnement faible ;
+ Coût de fabrication élevé ;
+ Réduction de l'inspection de la machine ;
+ Exige beaucoup des soins ;
+ Pas de graissage en cas du blocage d'un seul tiroir.
14 J.ROLDAN VILORIA, Aide-mémoire
Hydraulique industrielle, éd 2002, Dunod, Paris, p330.
VI. Schéma de commande
59
V. Etude comparative du système de graissage
manuel et automatique
V.1. Graissage manuel
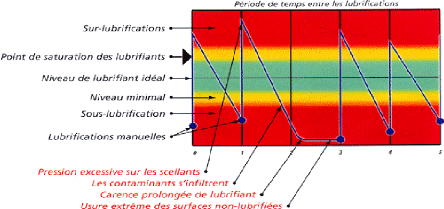
Figure 4.16
V.2. Graissage automatique
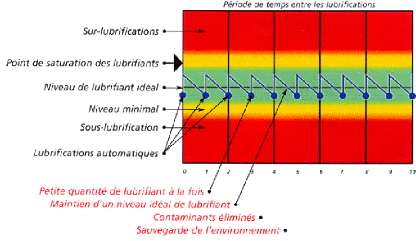
Figure 4.17
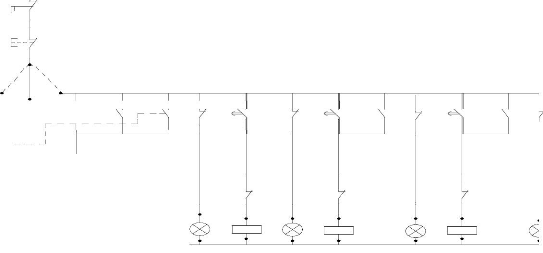
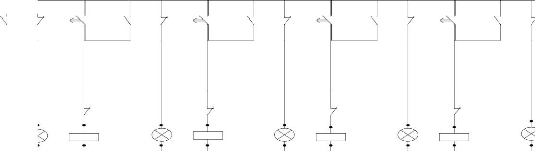
1
2
1
21
22
2
60
L
2
1
F1
F2
SO
MAN
AUT
13
27
27
21
13
21
13
13
21
13
21
27
0
95
96
11
12

KM2/1 KM2/4 KM3/1
KM1/2 KM3/3
KM2/3
KM1/1
SM
KM
KM
KM
22
22
14
14
INT
HORAIRE
14
14
28
28
14
22
28
22
21
21
21
KM12/2
KM2/2
KM3/2
KM4/2
22
22
22
A1
1
1
1
A1
A1
A1
H2
KM1
H1
KM
KM2
KM3
H4
H3
N

2
A2
2
A2
A2
2
A2
L
27
21
21
21
27
13
27
21
27
21
21
27
13
13
KM4/1
M%3/4 KM4/3 KM4/4 KM5/1 KM5/3 KM6/4
KM6/1 KM6/3 KM6/4 KM7/1 KM7/3 KM7/4 KM8/1 KM8/3
28
22
22
22
28
28
22
28
22
28
14
14
14
22
21
21
21
21
22
A1
21
KM4/2
KM7/2
KM8/2
KM6/2
KM9/2
22
22
22
22
1
1
A1
A1
A1
A1
1
1
H6
H7 H8 H9
KM7 KM8
KM6
H5
KM4
A2
KM5
N
A2
2
2
2
A2
2
A2
A2
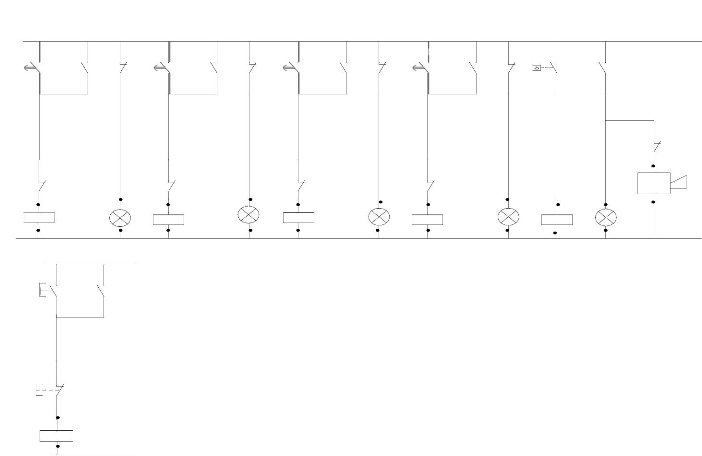
N
A2
KA2
61
N
A2
L
27
21
27
13
21
13
KM9/1
KM9/3
KM9
KM8/4
S1
28
14
14
28
27
22
14
28
14
14
22
22
21
21
21
KM12/2
KM11/2
KM13/2
22
22
22
1
1
1
A1
1
A1
A1
A1
H11
H12
KM10
KM9 H10
H 13
KM11
KM12
A2
2
A2
2
2
A2
2
A2
KM10/1 KM10/3 KM10/4 KM11/1 KM11/3 KM11/4
KM12/3 28 13 21 27
KA1/1
14
21
KA2/2
22
H1
H14
H2
1
KA1
H14
2
13
22
A1
KM10/2
21
H: Lampes signalisations
KM: Contacteurs
KA: Relaies
13
13
L
KA2/1
11
12
A1
14
SR
SQ
14
62
CONCLUSION
Eût égard à ce qui précède ;
la problématique du système de graissage manuel du pilote crusher
qui consiste à faire le graissage à l'aide d'une pompe à
graisse manuelle sur les paliers des convoyeurs, les roulements des concasseurs
et des cribleurs a été tout au long de notre étude une
préoccupation majeure.
Nous nous sommes consacré à évaluer
à priori la quantité de la graisse à envoyer dans chaque
organe à graisser et du temps de regraissage pour une bonne maintenance
préventive des organes en mouvement du pilote crusher. Alors l'analyse
des résultats nous a donné ce qui suit:
V' 25g de graisse sur les roulements centraux et 20g de
graisse
pour les roulements extrêmes du Jaw crusher ;
V' 10g de graisse aux 2 nipples extrêmes et 50g au
nipple
centrale du Twister ;
V' 4g de graisse par roulements des cribleurs ;
V' 3.75g de graisse par roulement des paliers MC600 ;
V' 5g de graisse par roulement des paliers MC 800 ;
V' 5.94g de graisse par roulement des paliers MC1000 ;
V' Fréquence corrigée est de 540 heures.
Nous avons eu par la suite à concevoir le
système de graissage automatique afin de rendre la tâche plus au
moins facile aux opérateurs et augmenter la productivité du
pilote Crusher comme nous l'avons énoncé dans les lignes qui
précèdent. Ainsi cela nous a amené à faire le choix
et le dimensionnement de certains paramètres du circuit de graissage
à savoir :
V' Diamètre des flexibles : 10mm V' cylindré:
2cm3
V' débit de la pompe : 5 x 10-5 m3/s
V' vitesse d'écoulement : 0.6369m/s
63
V' rendement volumétrique : 0.92
V' pression de la pompe : 131, 6619bar
V' puissance hydraulique : 658, 3093 w
V' rendement : 0.9
V' puissance du moteur d'entrainement : 750w
Les objectifs que nous nous sommes fixés tout au long
de nos recherches ont trouvé satisfactions dans les résultats que
nous avons obtenus malgré les multiples difficultés
rencontrées. Nous avons conçu un circuit hydraulique et un
schéma de commande électrique afin de pouvoir réaliser un
graissage automatique de notre chaine de production.
Ce travail n'est qu'une oeuvre humaine ; les critiques et
suggestions dans le sens de l'améliorer seront les bienvenus.
64
BIBLIOGRAPHIE
I. Cours
1. CHIYEY K, Mécanique de Fluides, ISTA/KZI, G2
EM, 2011-2012.
2. MADOU H,Technologie Hydropneumatique, ISTA/KZI, G2 EM,
2011-2012.
3. MUTAZ K, Combustibles et lubrifiants, ISTA/KZI, G2 EM,
2011-2012.
4. Daniel M, Dessins schémas, ISTA/KZI, G2 EM,
2011-2012.
II. Ouvrages
1. José Roldan Viloria, Aide-mémoire
Hydraulique industrielle, 2004.
2. Jacques Faisandier et coll., Mécaniques
Hydrauliques et Pneumatiques, 2006.
3. René Gras, Tribologie (principes et solutions
industrielles, 2008.
4. Sami Bellalah et Iset Nabeul, Hydraulique industrielle.
III. Catalogues
1. Lubrification SNR industry.
2. Manuel d'utilisation, Instruction de Service LINCOLN.
3. Schaeffler Groupe industrial
4. Symboles hydraulique.
III. Sites Web
1.
www.fis-services.com
2.
https://sites.google.com/site/patrickote
73/graissage.
3.
medias.
Schaeffler.com/media/fr!hp.tg.cat/tg_hr*ST4_1652077067.
4.
www.pilotcrusher.com
5.
www.rubblebuster.com
6.
www.boschrexroth.com/brm
|