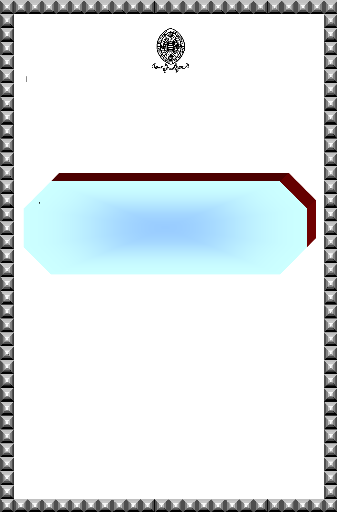
p
UNIVERSITÉ DE YAOUNDÉ
I THE UNIVERSITY OF YAOUNDE I
REPUBLIQUE DU CAMEROUN REPUBLIC OF
CAMEROON
Paix - Travail - Patrie Peace - Work -
Fatherland
FACULTÉ DES SCIENCES FACULTY OF
SCIENCE
DÉPARTEMENT DE
CHIMIE INORGANIQUE DEPARTMENT OF INORGANIC CHEMISTRY
CON TRIBUTION A LA DIMINUTION DES
CASSES DANS LA PRODUCTION DES
BRIQUES DE TERRE CUITE A LA
PROMOBAT
MÉMOIRE Présenté et soutenu en
vue de l'obtention du Diplôme d'Études Supérieures
Spécialisées (D.E.S.S.) en Chimie Industrielle
Option : Céramique et Verre
Par
LEMOUGNA NINLA Patrick Licencié en
Chimie Mat : 01U481
Sous
la direction de : Antoine
ELIMBI Chargé de Cours
la supervision de : Daniel
NJOPWOUO Professeur
l'encadrement professionnel de : Elie
NDOUM Chef de production
Année académique 2002-2003
TABLE DES MATIERES
DEDICACES iii
REMERCIEMENTS iv
LISTES DES FIGURES vi
LISTE DES TABLEAUX vii
RESUME viii
ABSTRACT ix
INTRODUCTION ..1
CHAPITRE I : PRESENTATION DE LA SOCIETE DE PROMOTION DE
BATIMENTS EN TERRE CUITE (PROMOBAT) 3
I-1- PARTENAIRES ET ACTIVITÉS 4
I-2 : LOCALISATION 4
I-3 : PROTOCOLE DE PRODUCTION 4
1-3-1 Organigramme 4
1-3-2 Matiere premiere et mise en forme du produit cru 5
1-3-3 Le sechage 5
1-3-4 : Les fours et l'enfournement 5
1-3- 5 : La cuisson 6
1-3-6 : Le defournement 6
CHAPITRE II : GENERALITES SUR LA TECHNOLOGIE DE
FABRICATION DES PRODUITS DE TERRE CUITE 7
II-1 : MATIÈRES PREMIÈRES ET PARAMÈTRES DE
FAÇONNAGE 8
11-1-1 : Matieres premieres 8
11-1-2 : Granulometrie et composition mineralogique 8
11-1-3 : 1nfluence de la temperature d'eau de faconnage 10
11-1-4 : 1nfluence du pH 10
11-1-5 : 1nfluence du faconnage sous vide 11
II-2 : LE SÉCHAGE 11
11-2-1 : La liaison argile -- eau 12
11-2-2 : Mecanisme du sechage 13
11-2-3 : le sechage naturel 13
11-2-4 : Le sechage artificiel 13
11-2- 5 : Moyens pratiques pour accelerer la vitesse de sechage
14
II-3 : LA CUISSON 14
11-3-1 Le processus de transformation thermique d'une argile
14
11- 3-2 Vitesse de cuisson -- Economie d'energie 16
CHAPITRE III : MATERIAUX ET METHODES EXPERIMENTALES
17
III-1 : LES MATÉRIAUX 18
111-1-1 : Les materiaux argileux 18
III-1-1-1 : L'argile fusible d'Etoa 18
i
III-1-1-2 : L'argile sableuse de Nkolbisson 18
III-1-2 : Le sable fin de riviere 18
III-2 : LES MÉTHODES EXPÉRIMENTALES 19
III-2-1 : Caracterisation des materiaux argileux 19
III-2-1-1 : Analyse granulométrique par tamisage humide
19
III-2-1-2 : Analyse granulométrique par
sédimentométrie 19
III-2-1-3 : La plasticité 21
III-2-1-4 : Mesure du pH 22
III-2-2 : Formulations elaborees 22
III-2-3 : Fagonnage des eprouvettes 23
III-2-4 : Le sechage 23
III-2-4-1 : Le séchage naturel 24
III-2-4-2 : Le séchage à l'étuve 24
III-2- 5 : Cuisson des produits 24
III.2.6- Proprietes physiques des produits 24
III-2-7 : Dispositif utilise pour mesurer les temperatures a
PROMOBAT 26
CHAPITRE IV : RESULTATS, INTERPRETATIONS ET SUGGESTIONS
27
IV.1- CARACTÉRISATION DES MATIÈRES
PREMIÈRES 28
IV.1.1- Analyse granulométrique 28
IV-1-2 La plasticité 30
IV.1.3- Le pH 31
IV.2- LE SÉCHAGE 31
IV.3- PROPRIÉTÉS PHYSIQUES ET MÉCANIQUES
DES PRODUITS DE
CUISSON 36
IV.3.1- La couleur 36
IV.3.2- Le retrait lineaire (Rc) 37
IV.3.3- La perte au feu (PF) 39
IV.3.4- Le pourcentage d'absorption d'eau 40
IV-3- 5 : La masse volumique apparente 42
IV.3.6- La resistance a la flexion (S) 43
IV-4 : PROGRAMME THERMIQUE UTILISE A PROMOBAT 45
IV.5- SUGGESTIONS 46
CONCLUSION 48
REFERENCES 50
ANNEXES 53
ii
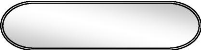
DEDICACES
Jcents dcentsdicents ccents n-2moir
fl mon p0, Mr bemoueNiti Pascal,
iii
Ma mO, mmo bemoueNiti ncentscents
MVECIelsOUNG bouisft, en tOnoignag dcents toutcents mon off~etio
n,* ous suis tr0 meonnaissant pour W saerifies qn ous a a eonnntis pour
moi.
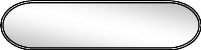
REMERCIEMENTS
Ce travail est le fruit d'une collaboration fructueuse entre
les hommes. Je remercie le tout puissant, le très miséricordieux
de sa grâce, sa protection sans lesquelles je n'aurais jamais pu
réaliser ce travail. Nous remercions aussi tous ceux qui de près
ou de loin y ont contribué. Il s'agit notamment de :
- Dr Antoine ELIMBI, chargé de cours, pour sa
disponibilité, ses conseils ; ma profonde gratitude lui est acquise pour
avoir dirigé ce travail ;
- Pr Daniel NJOPWOUO, chef du département de chimie
inorganique et responsable de la filière chimie industrielle, toujours
présent comme un père pour ses conseils, ses multiples
encouragements durant notre formation et pour avoir supervisé ce
travail;
- Pr GILLES LECOMTE, Pr ABELARD, Pr GAILLARD, Pr JAWORSKI,
tous enseignants à l'École Nationale de Céramique
Industrielle de Limoge (France), pour leurs conseils et la formation qu'ils
nous ont donnée ;
- Dr UPHIE CHINDJE MELO, Directeur de la MIPROMALO, pour tout
l'aide et la participation de la MIPROMALO à la formation des
étudiants de la filière chimie industrielle option
Céramique et Verre ;
- Dr LIBOUM, coordinateur de la filière chimie
industrielle, pour ses conseils, sa disponibilité et ses encouragements
;
- Tous les enseignants de la filière chimie industrielle,
pour la formation qu'ils nous ont donnée.
Nos remerciements vont également à :
- Mr Elie NDOUM, chef de production à PROMOBAT, pour ses
conseils, sa disponibilité et pour m'avoir encadré en
industrie;
- Dr STAN BELL, Directeur Général de PROMOBAT, pour
nous avoir accueilli dans son entreprise ;
- Mr ISAÏ, chef de production adjoint à PROMOBAT,
pour ses conseils ;
- Mlle Yvette MAKON, secrétaire à PROMOBAT pour
l'aide à la finalisation de ce manuscrit ;
- Tout le personnel de PROMOBAT, pour leur
disponibilité.
Nos remerciements vont enfin à :
iv
- Mr KAMSEU, Mr BILONG, Mr LOWE, tous en service à la
MIPROMALO, pour leur aide et leurs conseils ;
- Mr NGNITEDEM Paul, en service au laboratoire de
géotechnique et matériaux de l'École Nationale
Supérieure Polytechnique, pour sa disponibilité ;
- Mr FOTIO et Mr NJOYA, étudiants en thèse, pour
leur aide et leurs conseils ;
- Mes camarades de promotion ( NGANTU Victor, FEUZING Henri,
SIEWE Alain, ESSOME Alain et PONKAM Bertille), pour leur soutient moral ;
- Mes frères et amis ( GUEMETA Jean Bernard, TCHIFFO
Stéphane, HAROUNA MASSAï, BODJOLBO Roger, GAYE Samuel, LOMPA
Dieudonné, TUEM Bénédicte, SOHOUNG Yolande et DJIEUTEDJEU
Honoré ), pour leur soutien moral ;
v
Toute ma famille, les membres du jury, pour leur contribution
à l'amélioration de ce travail.

LISTES DES FIGURES
Figure 1 : Organigramme de production à
PROMOBAT 4
Figure 2 : Schéma d'un four à
PROMOBAT ...5
Figure 3 : Courbe de répartition
granulométrique des matériaux AE et AN...30 Figure
4a : Perte de masse des éprouvettes de matériau en
fonction du temps
(séchage naturel) 34 Figure 4b :
Retrait linéaire de séchage des éprouvettes de
matériau en fonction
du temps (séchage naturel ) 34 Figure
5a : Perte de masse des éprouvettes de matériau en
fonction du temps
(séchage à l'étuve) ..35 Figure
5b : Retrait linéaire de séchage des éprouvettes
de matériau en fonction
du temps (séchage à l'étuve )
.35 Figure 6a : Retrait linéaire de cuisson des
céramiques de coupures AE-AN en
fonction de la température .38 Figure
6b : Retrait linéaire de cuisson des céramiques de
mélange AE-SF en
fonction de la température .....38 Figure
7a : Perte au feu des céramiques de coupures AE-AN en fonction
de la
température .39 Figure 7b : Perte au
feu des céramiques de mélange AE-SF en fonction de la
température .40 Figure 8a :
Pourcentage d'absorption d'eau des céramiques de coupures AE-AN
en fonction de la température .42 Figure
8b: Pourcentage d'absorption d'eau des céramiques de
mélange AE-SF
en fonction de la température 42 Figure
9a : Masse volumique apparente des céramiques de coupures AE-AN
en
fonction de la température .42 Figure
9b : Masse volumique apparente des céramiques de mélange
AE-SF en
fonction de la température .43 Figure
10a : Résistance à la flexion des céramiques de
coupures AE-AN en
fonction de la température .44 Figure
10b : Résistance à la flexion des céramiques de
mélange AE-SF en
fonction de la température .44 Figure
11 : Variations de la température en fonction du temps de
chauffe à
PROMOBAT ..45
Figure 12 : Organigramme de production
proposé à PROMOBAT 46
vi
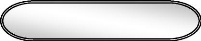
LISTE DES TABLEAUX
Tableau I: Différentes fractions
granulométriques dans une terre pour brique de terre cuite ... .9
Tableau II : Tamisage humide de AE et de AN .
28
Tableau III: Sédimentométrie de AN
.29
Tableau IV: Sédimentométrie de AE
29
Tableau V: Résultats du test de
plasticité des matériaux AE et AN comparés à ceux
des terres argileuses pour brique de référence . 30
Tableau VI: Résultats sur le
séchage naturel ...33
Tableau VII : Résultats sur le
séchage isotherme à l'étuve ..33
Tableau VIII : Coloration des produits de
cuisson en fonction de la température .36
Tableau IX : Retrait linéaire de cuisson
(en %) des produits en fonction de la température .
.37 Tableau X: Perte au feu (en % ) des produits de cuisson
en fonction de la température ...40
Tableau XI : Pourcentage d'absorption d'eau des
produits de cuisson en fonction de la température .42
Tableau XII : Masses volumiques apparentes (en
g/cm3 ) des produits de cuisson en fonction de la température
42
Tableau XIII : Résistance à la
flexion (en Mpa ) des produits de cuisson en fonction de la température
.44
Tableau XIV: Résultats des mesures de
température effectuées à PROMOBAT ..45
vii
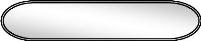
RESUME
Le but de ce travail est de contribuer à la diminution
des casses dans la production des briques de terre cuite à la
Société de Promotion de Bâtiments en Terre Cuite
(PROMOBAT). Après une descente dans cette société et une
analyse des faits, nous avons cerné les principales causes des casses
(préparation inadéquate de la matière première,
enfournement des produits humides, manque de programme de cuisson...) et avons
suggéré des solutions pour pallier ces dernières. Dans le
souci d'améliorer l'aptitude au séchage du matériau
argileux utilisé à PROMOBAT (argile AE), nous avons
envisagé des ajouts de dégraissant (matériaux argileux
(AN) d'une part et sable quartzeux (SF) d'autre part). Une étude
préliminaire (analyses granulométrique et plasticité) a
montré que les matériaux AE et AN contiennent 25 et 12% de
fraction argileuse respectivement.
Six formulations ont été étudiées
: E0, E20 et E30 obtenus par ajout de 0, 20 et 30% de AN dans AE respectivement
, AS9 et AS15 obtenus par ajout de 9 et 15% de sable dans AE respectivement et
En, constitué de 100% de AN. Ces formulations ont
été traitées thermiquement entre 850 et 1100°C au
four électrique pendant des intervalles réguliers de 50°C et
un palier de 2h pour chaque température. Les propriétés
céramiques suivantes ont été déterminées:
retrait linéaire de cuisson, perte au feu, masse volumique apparente,
pourcentage d'absorption d'eau et résistance à la flexion.
Les résultats obtenus montrent que :
- le retrait linéaire, la perte au feu, la masse volumique
apparente et la
résistance à la flexion augmente avec
l'élévation de la température, tandis que le pourcentage
d'absorption d'eau diminue ;
- les ajouts de dégraissant améliorent l'aptitude
au séchage de AE, mais
diminuent ses propriétés mécaniques à
la cuisson.
Mots clés : Brique de terre cuite,
casses, séchage, matériaux argileux, température,
propriétés
céramiques, cuisson.
viii
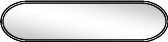
ABSTRACT
The aim of this work is to contribute to the reduction of
breakages in the production of fired earth bricks at PROMOBAT
(Société de Promotion des Bâtiments en Terre cuite ). After
an analysis of the situation at the site, we came out with the principal causes
of breakages and suggestions have been made to remedy the situation. In order
to ameliorate the aptitude to drying of clayey material used at PROMOBAT (clay
AE), we envisaged the addition of degreasing materials (clayey material AN of
one part and quartzeous sand (SF) on the other). A preliminary study (particle
size distribution analysis and plasticity) revealed that materials AE and AN
contain 25 and 12% of clay fraction respectively.
Six formulations were studied: E0, E20, and E30 obtained by
addition of 0, 20 and 30% of AN in AE respectively, AS9 and AS15 obtained by
addition of 9 and 15% of sand in AE respectively and En, constituted
of 100% AN. The formulations were thermally treated between 850 and 1100°C
in an electric kiln at a regular interval of 50°C and a soak of 2 hours
for each temperature. The following ceramic properties have been determined:
linear shrinkage, loss on ignition, bulk density, percentage of water
absorption, and mechanical resistance to bending.
The results show that:
the linear shrinkage, loss on ignition, bulk density and
mechanical resistance to bending increases with increase in temperature while
the percentage of water absorption decreases;
the addition of degreasing material ameliorates the aptitude
to drying of AE, but decreases the mechanical properties at firing.
Key words: Fired earth bricks, breakages,
drying, clayey materials, temperature, ceramic
properties, firing.
ix
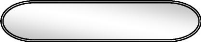
INTRODUCTION
Dans le passé, la notion de céramique faisait
allusion aux terres cuites et aux poteries, la matière première
étant alors l'argile [1]. L'argile a la propriété de
retenir l'eau entre ses feuillets et d'augmenter de volume. Ce matériau
a aussi le pouvoir d'être façonné, de subir des retraits,
de durcir après séchage et de se consolider grâce à
une cuisson qui permet la formation d'une phase vitreuse plus ou moins
importante.
La découverte de cette dernière
propriété ( consolidation de l'argile par le feu ) est l'une des
premières inventions essentielles de l'homme [2]. Pendant la
préhistoire, la vie de l'homme s'est trouvée extraordinairement
enrichie par la fabrication des récipients en argile cuite pour
conserver les grains, transporter l'eau, faire cuire et conserver la
nourriture. Il en est de même des objets en argile cuite pour des usages
purement esthétiques [2,1].
Cette conception de la céramique a beaucoup
changé avec l'évolution de la technologie. D'après Kingery
et al dans [3], la céramique se situe dans la production d'objets
formés de solides dont les constituants essentiels sont des
matériaux inorganiques et non métalliques. Cette
définition inclut non seulement les poteries, les porcelaines, les
matériaux réfractaires, les abrasifs, les émaux sur
tôles, les ciments, les verres, etc. Les produits céramiques sont
donc des matériaux complexes dont les propriétés
résultent des transformations physico-chimiques que subissent les
matières premières inorganiques (argiles, calcaires,
feldspaths...) pendant la cuisson [2,3].
Pour ce qui est des produits céramiques utilisés
dans le bâtiment, il s'agit de rechercher des propriétés
telles que la résistance à la compression, à l'usure,
l'esthétique architectural, la résistance aux agents chimiques et
aux sollicitations physiques, en plus des propriétés qui assurent
aux maisons le climat d'habitation recherché [4].
Seulement, au Cameroun, les jeunes entreprises qui se lancent
dans la fabrication des produits céramiques se heurtent aux
problèmes technologiques (équipements insuffisants, pas de
maîtrise des procédés de fabrication...), ce qui non
seulement affecte la qualité des produits, mais élève
aussi le coût de production. La maîtrise de ces
procédés constitue à l'heure actuelle un des axes
prioritaires de recherche dans plusieurs laboratoires dont celui de
physico-chimie des matériaux minéraux de la Faculté des
Sciences de l'Université de Yaoundé I.
L'objet de cette étude est non seulement de palier aux
casses constatées dans la production des briques de terre à la
Société de Promotion des Bâtiments en Terre cuite
1
(PROMOBAT ), mais aussi de contribuer à la formulation des
produits de qualité dans la dite société à travers
le partenariat Université-Industrie.
Notre étude porte sur quatre chapitres :
- le chapitre I présente la Société de
Promotion des Bâtiments en Terre cuite (PROMOBAT) et son produit ;
- le chapitre II concerne les généralités
sur les paramètres et étapes importantes du processus de
fabrication ainsi que leur influence sur l'apparition des craquelures et les
casses des produits de terre cuite ;
- quelques caractéristiques sur les matériaux
étudiés ainsi que les méthodes expérimentales
utilisées en constituent le chapitre III ;
- dans le quatrième chapitre, nous présenterons les
résultats obtenus et proposerons une interprétation.
2
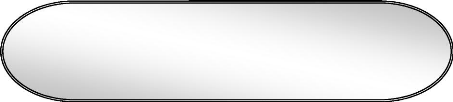
CHAPITRE I :
PRESENTATION DE LA SOCIETE DE PROMOTION DE
BATIMENTS EN TERRE CUITE (PROMOBAT)
3
I-1- PARTENAIRES ET ACTIVITÉS
La société de promotion des bâtiments en
brique de terre cuite (PROMOBAT) est une filiale du groupe GERTAU (Groupement
d'Étude et de Recherche pour les Travaux en Aménagement Urbain).
Cette société est née de la volonté de rendre le
logement accessible au plus grand nombre de camerounais à revenus
divers, et de promouvoir l'utilisation des matériaux locaux dans la
construction.
Créée en 1995, PROMOBAT est une SARL au capital
de 6 millions de Francs CFA, repartis entre le Groupe GERTAU
représenté par Maurice TEGUEL (65% du capital), la
société Terres cuites de Rougeoles en France
représenté par Claude RIVIERE (25% du capital) et par le
Général MPAY Philippe (10% du capital).
A ce jour, PROMOBAT produit essentiellement les briques de
terre cuite (briquettes, briques creuses, blocs perforés ...) qui ont
des formes et des dimensions variées selon le type de filière de
production.
I-2 : LOCALISATION
La Société de Promotion de Bâtiments en
Brique de Terre cuite est située dans l'arrondissement de Yaoundé
III (quartier Mvan), une parmi les zones industrielles de la capitale politique
du Cameroun.
I-3 : PROTOCOLE DE PRODUCTION 1-3-1
Organigramme
Argile d'Etoa (brut de carrière)


Mélangeur - Mouilleur

Chambre à vide

Extrudeuse

séchage

Cuisson

Sortie four et tris

Expédition
Figure 1 : Organigramme de production à
PROMOBAT
4
1-3-2 Matiere premiere et mise en forme du produit
cru
La matière première utilisée à
PROMOBAT est l'argile fusible d'Etoa. C'est un matériau plastique, de
couleur brune et à bariolage gris. Dans le processus de fabrication,
cette argile est utilisée sans ajout d'autres matériaux
d'addition et le façonnage est fait par extrusion.
1-3-3 Le sechage
Le séchage est naturel (air atmosphérique ),
mais un séchoir électrique est actuellement en cours
d'expérimentation. L'espace de séchage réduit ainsi que
les paramètres climatiques difficiles à maîtriser rendent
cette opération délicate. Les produits séchés
présentent régulièrement les fentes et des craquelures qui
peuvent être attribuées soit à un séchage
inapproprié, soit à une préparation inadéquate de
la matière première.
1-3-4 : Les fours et I'enfournement
PROMOBAT dispose de deux fours artisanaux à
voûtes cintrées de capacité 20 m3 chacun. Les
fours sont encastrés dans du béton afin de minimiser les effets
néfastes de la pression au cours de la cuisson. De la pouzzolane sous
forme d'agrégats est déversée sur les voûtes, ce qui
limite les pertes de chaleur et permet ainsi aux ouvriers d'introduire
aisément du bois à travers les regards pendant la cuisson.
L'enfournement est manuel et parfois les produits sont enfournés
à l'état humide.
Canal pour fumées
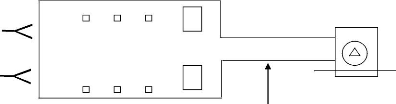
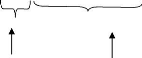
Zone d'alimentation du bois
Zone de disposition des briques
|
|
Regard
Cheminée
Brûleur électromécanique pour combustible
liquide
|
|
|
|

Aspirateur / Ventilateur
5
Figure 2: Schéma d'un four à
PROMOBAT
1-3- 5 : La cuisson
Elle dure environ 48 heures (24h de préchauffe et 24 h
pour la cuisson proprement dite) et est réalisée sans programme
de montée en température définie. Les ouvriers qui cuisent
se servent de leur expérience et de leurs sens pour mener à bien
leurs tâches. Par ailleurs, le taux d'humidité varie
considérablement d'un enfournement à l'autre.
Ce manque de rigueur à la cuisson est malheureusement
source de fluctuations aussi bien au niveau de la qualité des produits
que du taux de casse sur cuit.
1-3-6 Le défournement
A la fin de la cuisson, le four reste fermé pendant 15
h environ et le défournement est effectué 24 h après. Les
produits défectueux sont mis de côté et les bons produits
rangés à l'air libre, prêts à être
expédiés.
6
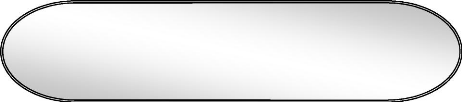
CHAPITRE II :
GENERALITES SUR LA TECHNOLOGIE DE
FABRICATION
DES PRODUITS DE TERRE CUITE
7
II-1 : MATIÈRES PREMIÈRES ET
PARAMÈTRES DE FAÇONNAGE
11-1-1 : Matieres premieres
Les terres utilisées à la fabrication des
briques de terre cuite sont généralement constituées
d'argiles ayant des proportions variables de kaolinite, illite, chlorite,
quartz, matières organique, oxydes de fer et oxydes de calcium. Ces
matériaux présentent une tendance à la vitrification entre
900 et 1160 °C [2 ].A l'état naturel, ces terres sont grises,
verdâtres, rouges ou brunes, en fonction des oxydes qu'elles
contiennent.
11-1-2 : Granulométrie et composition
mineralogique
Les compositions minéralogiques et
granulométriques des matières premières sont des facteurs
déterminants dans le processus de fabrication [5,6]. Les
quantités d'eau de façonnage en dépendent, et donc aussi
les retraits. Le pourcentage de minéraux à trois couches est
particulièrement significatif, surtout celui de la montmorillonite [5].
En effet, la structure et la finesse des particules de ce minéral
confèrent au produit cru une forte rétention capillaire en
présence d'eau, ce qui rend difficile le séchage [5,6].
L'importance de la phase inerte (dégraissante)
généralement constituée de quartz, calcaire, reliquats de
roches primaires ou même de chamotte est considérable. En effet,
pour une même consistance du produit cru, si la teneur en eau
d'imbibition diminue, le retrait est faible. Toute fois, pour une même
perte en eau colloïdale (eau éliminée pendant le retrait),
le retrait peut varier selon la proportion et la granulométrie du
dégraissant. En effet, la diffusion est améliorée, car
pour un même poids de la phase argileuse, la phase inerte a une surface
spécifique beaucoup moins importante, tandis que les forces capillaires
ont tendance à redistribuer les particules argileuses autour des grains
inertes avec formation de plus gros pores [5]. Par ailleurs, les grains qui
constituent la phase inerte étant sans retrait, une certaine
hétérogénéité de la texture s'ajoute
à l'influence de la porosité spécifique [5]. En somme, la
migration capillaire qui se traduit par la plus ou moins grande facilité
à pouvoir sécher les produits de différentes formes et
dimensions apparaît comme une caractéristique
particulièrement significative. Les facteurs qui influent sur la
diffusion sont donc déterminants, compte tenu de leur tendance à
agir sur la formation des fissures au cours du séchage [5,6] .
En résumé, la matière première
utilisée pour la fabrication des briques de terre cuite doit contenir
les éléments suivants :
8
- une fraction d'argile suffisante pour assurer une bonne
plasticité nécessaire au façonnage. Cette fraction ne doit
pas dépasser une certaine limite, au risque de rendre la pâte trop
collante pour être façonner. D'autre part, une grande proportion
de particules fines augmente le retrait lors du séchage, ce qui est
souvent cause des fissures et des casses ;
- une quantité suffisante de matière non
réactive (dégraissant), pour atténuer les retraits ;
- des fondants tels que les oxydes ferreux et alcalins pour
faciliter la formation de la phase vitreuse ;
- pas d'impuretés ou d'inclusions susceptibles de rompre
la structure des briques au séchage ou à la cuisson.[6].
Les différentes fractions granulométriques de
particules dans les terres pour briques de terre cuite se répartissent
généralement selon les valeurs consignées dans le tableau
I.
Tableau I: Différentes fractions
granulométriques dans une terre pour brique de terre cuite [6]
Fractions
|
|
Taille (mm)
|
-
Sable -
-
|
Grossier Moyen fm
|
2 - 0,6
0,6 - 0,2
0,2 -- 0,06
|
-
Limons -
-
|
Grossier Moyen
fin
|
0,06 - 0,02
0,02 - 0,006
0,006 -- 0,002
|
Argile
|
|
< 0,002
|
Dans la pratique, les terres pour briques de terre cuite
doivent contenir 10 à 50% de la fraction argileuse,
mélangée à un peu de limon et du sable. La présence
simultanée de sable, de limons, ainsi qu'une granulométrie
étalée a des effets bénéfiques [6].
9
II-1-3 : Influence de la temperature d'eau de
fagonnage
Une élévation de la température d'eau de
façonnage a une action positive [5,8]. En effet, au sein d'un corps
poreux, l'eau à tendance à migrer du côté chaud vers
le côté froid. Pour faciliter la diffusion dans le produit cru, il
faut agir sur le gradient de température. En effet, il faut compenser
l'eau évaporée à la surface par celle qui provient des
pores et qui migre sous l'effet des forces capillaires. Or, au début
d'un processus de séchage ordinaire, pour éviter de «
croûter» en surface, c'est au chauffage de la pièce à
sécher qu'il faut d'abord consacrer du temps. Tout le processus est
ralenti avec danger accru de fissuration, si la pâte est relativement
dense, la pièce massive, ou si son rapport volume-surface est
défavorable [5,6]. Au contraire, avec le préchauffage à la
vapeur, dès la sortie de filière, le gradient thermique ne
s'oppose plus à la migration capillaire, puisque le coeur de la
pièce peut être plus chaud que la surface d'évaporation
[5].
II-1-4 : Influence du pH
Le façonnement et d'autres propriétés
(résistance mécanique et couleur ) des argiles employées
à la fabrication des briques de terre cuite et des tuiles peuvent
être améliorées en ajustant la valeur de leur pH dans des
limites déterminées et assez étroites avant leur
traitement [7].
Pour obtenir une brique ou une tuile possédant un
tesson homogène, compact et imperméable, il est nécessaire
que dans le mélange des matières premières, les petits
grumeaux cohérents et agglomérés soient
complètement désagrégés. D'autre part, les
particules élémentaires doivent être finement
réparties dans la masse afin que la pâte soit travaillée
à fond et prenne une texture parfaitement homogène. Dans le cas
d'une argile riche en chaux, il est difficile d'obtenir cette fine dispersion
si la quantité de matière à mélanger est
importante. Les essais de laboratoire et le travail en usine montrent qu'en
maintenant le pH entre certaines valeurs, un maximum favorable du comportement
des argiles au filage peut être obtenu [7]. Pour ajuster le pH, on peut
recourir aux carbonates ou aux hydroxydes de sodium, de potassium ou
d'ammonium. La quantité de produit à ajouter correspond à
la neutralisation de l'acide argilique. Au delà de cette
quantité, l'excès de carbonate soluble dans l'eau, provoque une
granulation indésirable [7]. Des essais montrent que le traitement qui
assure d'une façon générale, de meilleurs résultats
est celui pour lequel le pH des argiles acides est ramené entre 6 et 8,5
et celui des argiles neutres ou basiques entre 7,3 et 10,5 [7]. Toutefois, ce
résultat ne doit pas être interprété ipso facto
comme la plus grande amélioration, mais seulement comme un fait.
L'intérêt d'ajouts de carbonate de sodium réside au prix de
revient peu élevé d'une telle opération : En effet, au
Cameroun le prix du kilogramme de Na2C03 est sensiblement 1500Fcfa. Un ajout de
0,5% de ce produit par
10
rapport au poids sec de terre conduit à une
dépense de 7500F cfa à la tonne, ce qui est minime compte tenu
des résultats qu'on peut en attendre. La solubilité du carbonate
étant de 150g au litre environ, son ajout à la terre ne
présente aucune difficulté : Il réagira mieux et son
action sera plus efficace que s'il est ajouté sec à la terre
[7].Les améliorations obtenues par cet ajustement du pH peuvent se
résumer ainsi :
- l'argile est plus plastique : Il suffit d'une faible pression
pour assurer son écoulement à travers une filière ;
- la quantité d'eau de façonnage se trouve
diminuée et la texture physique du produit filé est
améliorée ;
- le feuilletage disparaît, la surface est lisse et il
apparaît moins de fentes et de défauts d'arêtes ;
- un bon ajustage du PH permet l'étirage de
produits creux sans arrachement de cloisons avec des argiles brutes impropres
à ce mode de fabrication ;
- pour certaines argiles, le séchage est facilité,
mais pour d'autres au contraire, ceci peut paraître plus délicat
;
- la température de cuisson peut être
abaissée, car le tesson est plus compact, de porosité plus faible
et de résistance à la compression et à la flexion plus
élevée ;
- la couleur est généralement
améliorée et il est possible d'obtenir des produits rouges avec
des argiles calcaires cuisant jaune clair [7].
11-1-5 : Influence du fagonnage sous vide
L'air existant dans le système poreux des pièces
céramiques humides peut fortement entraver le séchage. En effet,
il provoque localement la rupture des courants capillaires. En outre, l'air
emprisonné se dilate au chauffage dans le séchoir et peut
même entraîner la rupture des pièces, raison pour laquelle
le façonnage sous vide est avantageux [8].
II-2 : LE SÉCHAGE
Le séchage consiste à l'élimination de l'eau
contenue dans les produits façonnés ou dans les matières
premières [6,8].Cette extraction peut se faire de deux façons
:
1) Le séchage mécanique: l'élimination
d'eau est effectuée à l'aide de forces purement mécaniques
(centrifugation, pressage, application d'un vide, traitement par secousses
etc).
2) Le séchage thermique. Dans ce cas, deux processus
successifs apparaissent :
- l'eau liquide est transformée en vapeur grâce
à l'apport de chaleur ;
11
- la vapeur d'eau formée est évacuée.
Pour sécher des matières premières ou
produits céramiques façonnés, le séchage thermique
est presque toujours utilisé [8].
11-2-1 : La liaison argile -- eau
Le mode de liaison d'eau d'humidité dans les argiles
peut être de différentes natures. En considérant que cette
eau s'échappe du produit par suite de la destruction de la liaison
argile-eau, et que celle - ci consomme de l'énergie, il semble plus
logique de ne se baser que sur l'énergie de liaison du produit à
sécher pour comparer les différents types d'eau.
On peut ainsi distinguer :
a) la liaison physique,
b) la liaison physico - chimique,
c) la liaison chimique.
Dans le cas du séchage thermique, l'eau liée
chimiquement (eau de cristallisation) subsiste dans les produits, et ne sera
donc pas abordée ici.
L'absorption de liquide par un gel est
généralement accompagnée d'un gonflement. Pour cette
raison, l'eau liée est appelée eau de gonflement ( l'eau de
gonflement dans les minéraux tels que ceux de la montmorillonite,
appartient également à cette catégorie)[8]. Ainsi,
abstraction faite à celle liée chimiquement, l'eau de gonflement
est la plus difficile à éliminer.
L'eau liée physiquement apparaît essentiellement
sous deux formes : l'eau capillaire et l'eau superficielle. L'eau capillaire
présente la liaison la moins solide. Elle remplit les cavités et
canaux qui forment un système cohérent de capillaires entre les
particules d'argile. Cette eau est aussi appelée eau des pores.
L'eau superficielle entoure les particules solides comme une
enveloppe.
En résumé, il existe trois types essentiels d'eau :
l'eau des pores, l'eau des enveloppes et l'eau de gonflement [8].
Selon la nature de la matière première, la
proportion de ces types d'eau, rapportée à la totalité
d'eau existant dans une pâte, peut être différente. Il
ressort de ces constatations que la vitesse et la sensibilité au
séchage des pâtes dépendent dans une large mesure de la
nature de la matière première [5,8].
12
11-2-2 : Mecanisme du sechage
L'eau contenue dans les produits ne peut s'échapper
qu'à la surface de ce dernier ou plus précisément à
l'interface produit-air ambiant.
En s'évaporant, l'eau peut s'échapper par
diffusion dans l'air. Ce phénomène dépend de la
température, de l'humidité relative et de la pression de l'air.
Un air complètement saturé de vapeur n'absorbe plus d'eau
provenant du produit : Il n'y a pas de séchage.
Dès que le processus de séchage commence par la
migration de molécules d'eau en direction de l'air, il se forme un
gradient d'humidité entre la surface des pièces où
débute le séchage et l'intérieur encore
complètement humide. Le séchage débutant en surface
s'accompagne d'un retrait, caractérisé par le fait que les
capillaires de la surface, et au fur et à mesure que le séchage
progresse, ceux d'une couche superficielle plus épaisse
rétrécissent. Des études physico-chimiques montrent que le
rétrécissement des pores capillaires, loin de freiner le
mouvement d'eau de l'intérieur vers l'extérieur, favorise cette
migration conjointement avec le gradient d'humidité [8]. En effet,
lorsque deux capillaires de diamètres différents et remplis d'eau
se rejoignent, l'eau passe automatiquement du capillaire le plus gros vers le
petit. Ceci veut dire que l'eau migre de l'intérieur vers la surface de
la pièce d'où elle passe par diffusion dans l'air
atmosphérique [8].
11-2-3 : le sechage naturel
L'une des principales causes d'apparition des fissures ou de
l'existence des casses dans les briques est une grande vitesse de
séchage. Celle-ci est difficile à contrôler lorsque les
briques sont exposées dans l'air atmosphérique. Une grande
vitesse de séchage peut être due à l'action du soleil, ou
à une faible humidité relative de l'air. Celle- ci peut
être atténuée en protégeant les briques du contact
direct des rayons du soleil [6 ].
Néanmoins, le séchage naturel conserve un avantage
par rapport au séchage artificiel : l'économie
d'énergie.
11-2-4 : Le sechage artificiel
Ce type de séchage doit limiter les pertes de briques
dues aux fissurations et aux gauchissements. La vitesse avec laquelle l'eau
s'évapore à la surface de la brique ne doit pas être plus
grande que celle de diffusion à travers les fins pores de la brique.
Ainsi, il n'y a pas de raison d'accélérer le séchage
à la surface du matériau ou de chauffer ce dernier au-delà
d'une certaine température. En effet, des dispositions contraires
à ce qui précède causeront un retrait rapide de la surface
vers l'intérieur de la brique, avec apparition des fissures ou
simplement la présence des fentes [5,6,8].
13
Une fois que l'eau colloïdale est éliminée, la
vitesse de séchage peut être élevée pour
évacuer l'eau qui remplit les pores [5].
Un séchoir moderne, prototype de séchoir
artificiel, fonctionne sur des bases rationnelles. Dans ce cadre, le
système de régulation automatique trouve des applications
précieuses. Le contrôle de la régulation nécessite
les instruments et appareils ci-après :
1.Thermomètres et thermographes, pour mesurer et
enregistrer la température à divers emplacements du
séchoir.
2. Psychomètres et hypographes, pour mesurer et
enregistrer l'humidité relative d'air.
3. Balances et instruments de mesure des dimensions, pour
mesurer la progression du séchage et notamment déterminer le
retrait et la teneur en eau.
4. Anémomètres et tube de Pitot, pour mesurer la
quantité effective et le tirage d'air [8].
11-2- 5 : Moyens pratiques pour accelerer la vitesse de
sechage
Il est possible d'améliorer le séchage grâce
aux méthodes de préparation de la matière première.
En effet :
- elles créent un réseau complexe de pores qui
offre à l'eau un nombre élevé de voies pour quitter
l'intérieur des produits. De plus, si le mélange est
homogène, les conditions de séchage plus uniformes
s'établissent dans les pièces. Les différences de retrait
aux divers points des produits ne sont alors pas trop importantes et les fentes
de séchage peuvent être évitées.
- si le retrait au séchage est trop grand (> 7%), il
faut s'attendre à des dommages, même si la conduite du
séchoir est parfaite. Dans ce cas, le résultat peut être
amélioré par le dégraissage de la pâte. L'emploi de
dégraissants à faible porosité permet en outre de
réduire la teneur en eau de la pâte [4,8].
- le troisième moyen pour accélérer la
vitesse de séchage est la préparation à chaud. Grâce
au chauffage, l'eau est plus fluide et facile à être
expulsée. Une pâte préparée à chaud contient
moins d'eau et la quantité de cette dernière à
éliminer est faible [5,6].
II-3 : LA CUISSON
11-3-1 Le processus de transformation thermique d'une
argile
La cuisson est l'opération finale et décisive de
la fabrication des produits céramiques préalablement
façonnés. Pendant ce processus, il se développe un fluide
visqueux, qui au refroidissement conduit à la consolidation et à
la diminution de la porosité [9].
14
Quelque soit le système de chauffage utilisé, il
est recommandé que le début de cuisson commence par une faible
vitesse de montée en température (préchauffe),
jusqu'à ce que toute l'eau résiduelle de façonnage soit
éliminée. Dans le cas contraire, la formation de vapeur à
l'intérieur de la masse du produit pourrait la faire éclater
[2,6]. Dans les fours traditionnels à combustible, une fois que les
fumées ne contiennent plus de la vapeur d'eau, une montée en
température de 50°C par heure donne des résultats
satisfaisants [6]. Au cours de la cuisson d'une terre argileuse, les
importantes étapes de transformation sont :
* L'oxydation et la d6composition de certains mineraux
associ6s
A partir de 450°C et au-delà, certains
minéraux se décomposent. Les minéraux argileux perdent
leur eau de constitution et se déstructurent complètement. Pour
le cas de la kaolinite, la transformation en métakaolinite se fait
suivant la réaction :
Si2 O5 Al2 (OH)4 2 SiO2 , Al2 O3 + 2H2O
400 - 600°C
D'autre part, c'est le début de la décomposition
de certains minéraux comme le calcaire, la dolomite ... La
matière organique s'oxyde en formant du CO2 si le four est bien
aéré. Les gaz issus de ces réactions doivent être
évacués par un tirage suffisant, car trop de CO2 issu de la
combustion dans un four qui tire mal inhibe la pyrolyse des carbonates [10].
* La transformation allotropique du quartz
Toutes les argiles naturelles contiennent une quantité
appréciable de quartz [11]. Le réseau cristallin de ce
minéral dépend de la température à laquelle se
trouve le produit. A la température ambiante, le quartz est sous la
forme a . Lors de la montée en température, les cristaux
du minéral se redisposent dans un ordre peu différent. En effet,
à 573°C le quartz a passe sous la forme de quartz 5. Cette
transformation réversible s'accompagne d'un accroissement de volume
d'environ 2% [2,10]. Ce changement de volume, bien qu'assez faible doit
s'accomplir lentement pour éviter des dégâts
éventuels (fissures ou rupture des produits). La vitesse de chauffe
à ce niveau doit donc être assez lente. Les mêmes
précautions doivent être prises lors du refroidissement.
* La reorganisation de la metakaolinite et la
vitrification
Autour de 980°C, la métakaolinite est
transformée en spinelle alumineuse suivant la réaction [12 ] :
15

2(2SiO2, Al2O3) Si3 Al4O12 + SiO2
Métakaolinite Spinelle Silice
alumineuse amorphe
D' autre part, les impuretés fusibles commencent
à fondre et la masse vitreuse qui en résulte cimente les cristaux
de minéraux stables (mullite, cristobalite) en formation, ce qui diminue
grandement la porosité [2,9].
II- 3-2 Vitesse de cuisson -- Economie d'energie
Dans plusieurs types de fours artisanaux, la vitesse de
montée en température est assez lente. Cela peut être
dû au manque de contrôle précis de la température ou
à une capacité d'alimentation en énergie faible. Toute
fois, il est important de signaler que, les faibles vitesses de montée
en température engendrent beaucoup de pertes d'énergie,
malgré leur aspect sécurisant. Par contre, les vitesses plus
grandes font gagner en temps, en énergie et par conséquent,
baissent le coût de production si la cuisson est bien conduite (sans
casses dues aux variations dimensionnelles brutales).
La vitesse de montée en température optimale est
donc celle qui conduit à un temps de cuisson minimale avec le meilleur
rendement de brique de bonne qualité [6].
16
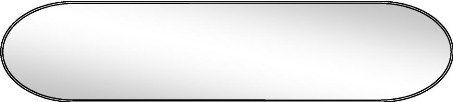
CHAPITRE III :
MATERIAUX ET METHODES EXPERIMENTALES
17
III-1 : LES MATÉRIAUX III-1-1 : Les
matériaux argileux
Notre étude a porté sur le matériau d'Etoa (
utilisé à PROMOBAT) et l'argile sableuse de Nkolbisson,
matériau pouvant améliorer l'aptitude au séchage de la
première.
III-1-1-1 : L'argile fusible d'Etoa
Le gisement d'argile d'Etoa (AE), situé sur
l'interfluve des cours d'eau Mefou et Mfoundi et son affluent Ezala a fait
l'objet de recherche et d'étude des argiles alluviales par BRGM [13].
Les sondages effectués par NGON NGON [13] montrent que
la nature des alluvions dans cette région est très variée
d'un point à l'autre d'une même terrasse alluviale et suivant la
profondeur. Les résultats de ces travaux mettent en évidence
trois profils :
- un profil stérile, essentiellement constitué des
matériaux peu argileux ou argiles indésirables pour la
céramique ;
- un profil moyennement sableux, constitué d'argiles
sableuses et dont l'épaisseur est variable (0,8 à 1m) ;
- un profil argileux, constitué d'une couche
humifère argilo - organique, gris sombre de 40 cm d'épaisseur et
une couche argileuse d'épaisseur 3,5 m par endroit.
III-1-1-2 : L'argile sableuse de Nkolbisson
Le gisement est situé dans le flanc de la
rivière Amga, à environ 2 Km de l'usine SNEC de Nkolbisson. Les
populations de la région affirment que dans le passé, cette
argile était utilisée pour la production des objets de poterie
[14]. Selon les travaux de AMOUGOU,[14] les épaisseurs mises en
évidence varient entre 1,10 à 2,70 m. Cette argile est
très sableuse, de couleur variable et à granules
ferrugineuses.
III-1-2 : Le sable fin de rivière
Le sable utilisé est de couleur grise. Il provient de
la décomposition des roches granitiques et est souvent transporté
par la pluie et le vent pour s'accumuler au fond des cours d'eau.
18
III-2 : LES MÉTHODES EXPÉRIMENTALES
111-2-1 : Caractérisation des matériaux
argileux
Les matériaux argileux AE et AN ont fait l'objet d'une
caractérisation préliminaire : l'analyse granulométrique
(tamisage humide et sédimentométrie), et la détermination
des limites d'Atterberg.
III-2-1-1 : Analyse granulométrique par tamisage
humide
Elle consiste à séparer les différentes
fractions et à les évaluer en pourcentage pondéraux de
l'ensemble de l'échantillon [15].Chaque matériau argileux est
d'abord séché dans l'air atmosphérique, puis
étuvé à 105°C pendant 24h. Par la suite, 500g de
matériau sont pesés, trempés dans l'eau pendant 24h, puis
passés à travers une colonne de tamis : 2 et 1,6 mm, puis
500,400,200,125,et 100 um. Après plusieurs lavages, les tamis, contenant
les refus sont séchés à l'étuve pendant 24h
à 105°C. Les différentes fractions sont calculées par
pesée. Pour finir, la proportion de particules inférieures
à 100 um est retenue pour effectuer l'analyse granulométrique par
sédimentométrie.
III-2-1-2 : Analyse granulométrique par
sédimentométrie
Cette analyse permet de déterminer le pourcentage de
particules argileuses dans un matériau. Dans l'étude des sols, on
désigne par argile la fraction de matériau comprenant des
éléments de diamètres inférieurs à 2 um, et
séparés au cours de l'analyse mécanique [16].
a) Principe
Le principe de la sédimentométrie est
basé sur la loi de Stockes qui mesure la vitesse (v) de
décantation des particules sphériques dans un milieu visqueux
sous l'influence de la force de gravitation et de la résistance du
milieu [17,18]. Cette vitesse est donnée par la relation :
V =
d 2(ñ
s-ñL)
n
18
d = diamètre des particules(um),
Ps= masse volumique des particules (g/cm3),
PL= masse volumique du milieu visqueux (g/cm3), n =
viscosité (poise),
19
v = vitesse (m/s).
Si pendant un temps t(seconde) les particules ont
sédimenté d'une hauteur Ht(cm), la vitesse de ce mouvement est
égale à Ht/t
b) Mode opératoire
20,0g de matériau sec sont pesés et introduits
dans une éprouvette A. Par la suite, 30cm3 de solution
d'hexamétaphosphate de sodium à 5% et 200 cm3 d'eau
déminéralisée sont ajoutés, puis le tout est
agité manuellement. Après un repos de 24 h, on agite à
nouveau pendant 10 minutes et le volume de la solution de l'éprouvette A
est complété à 1000 cm3 avec l'eau
déminéralisée. De la même manière, on
prépare une autre solution dans l'éprouvette B : 30
cm3 de solution d'hexamétaphosphate de sodium à 5%,
complété à 1000 cm3 avec l'eau
déminéralisée. Les éprouvettes A et B sont
placées dans un bain d'eau froide afin d'uniformiser la
température. Le densimètre est d'abord introduit dans
l'éprouvette B, et, concomitamment on agite vigoureusement la solution
de l'éprouvette A. Aux différents instants, après avoir
effectué la lecture de B, le densimètre est enlevé et
introduit doucement dans l'éprouvette A et la lecture est à
nouveau effectuée. A chaque lecture du densimètre, la
température est aussi mesurée dans le bain d'eau froide.
c) Calculs · Calcul des
diamètres équivalents (dy)
La loi de Stockes étant établie pour les grains
sphériques, le résultat de la mesure ne peut correspondre qu'aux
diamètres équivalents. En prenant le temps en minutes, dy en
micromètre et ñs en g/cm3, nous avons :
2
) dy
d'où dy=

108
3 . 1 0 7nHt
g( ñ s -1)t
H t = g(
ñs -1
60 t 18nx
La masse volumique du matériau n'étant pas connue,
nous avons pris ñs = 2,65 g/cm3 qui est celle du quartz [
17,18].
A 25°C n = 0,0090 poises g=981 cm/s2

H t = H 0 - D(A +
Cm)-1 ,C
L e
H0 = distance du centre de gravité du volume du bulbe du
densimètre à la division 1000 ;
20
D = longueur d'une division,
Cm = hauteur du ménisque en fraction de
division, mesurée sur l'éprouvette due à l'introduction du
densimètre.
· Calcul des pourcentages cumulés (Y%)
A l'instant t(min) et à la profondeur Ht(cm), on ne
trouve que des particules de dimensions inférieures ou égales
à dy. Le pourcentage de ces particules s'obtient suivant la formule
0 _Vñs × R
0-- -1 1 0
Pñs
Y


R = lecture de A -lecture de B (en nombre de divisions),
V = volume de la suspension (cm3),
P = masse sèche des grains contenus dans la suspension
(g).
La lecture dans A ou B est effectuée après 0.5,
2,5,10,30 minutes et 1,2,3,5, 24 heures.
III-2-1-3 : La plasticité
a) La limite de liquidité
La limite de liquidité est la teneur en eau qui
correspond à la fermeture de la rainure sur un centimètre de
longueur après environ vingt cinq chocs (appareil de Casagrande). Le
matériau argileux est au préalable lavé au tamis de maille
de 400um puis conservé pendant 24 heures dans l'eau. Après
décantation, il est répandu sur une plaque de plâtre pour
séchage et homogénéisation avant d'être placé
dans l'appareil de Casagrande où une rainure est creusée dans la
coupelle comportant l'échantillon. La manivelle est tournée
à une vitesse de 2 chocs par seconde jusqu'à ce que la rainure se
ferme sur un centimètre.
Des essais successifs sont effectués en laissant
évaporer l'eau progressivement. Le procédé est tel que le
nombre de chocs soit compris entre 15et 35 pendant cinq essais. La limite de
liquidité est donnée par la formule :
W
L
|
Ph - Ps
|
× 100
|
Ps -Tare
|
Ph = poids total humide, Ps = poids total sec.
21
b) La limite de plasticité
La pâte argileuse du dernier essai de la limite de
liquidité est utilisée pour déterminer la limite de
plasticité : après un léger séchage, on forme une
boule de 12 mm de diamètre environ que l'on utilise pour faire un
cylindre de 10 à 15cm environ avec 3mm de diamètre en roulant sur
une surface plane, sèche, propre et non absorbante. La limite de
plasticité est la teneur en eau du cylindre qui se brise lorsqu'on le
soulève de 1à 2cm. Elle est donnée par la formule :
W
P
|
=
|
Ph -Ps
|
×100
|
Ps -Tare
|
c) L'indice de plasticité

Elle est obtenue en faisant la différence entre la
limite de liquidité et celle de plasticité. L'indice de
plasticité indique l'intervalle dans lequel le matériau argileux
est façonnable. Sa formule est donnée par l'équation :
= w - W p L P
III-2-1-4 : Mesure du pH
Compte tenu de l'influence du pH sur l'aptitude au filage des
pâtes nous avons jugé intéressant de mesurer le pH d'une
solution saturée en argile AE.
Après avoir étalonné le pH-mètre
dans une solution étalon de pH = 6,86 , son électrode est
nettoyée et introduit dans un bêcher contenant 30ml d'eau
distillée placé sur un agitateur magnétique. La poudre
d'argile (diamètre inférieur à 400um) est par la suite
introduite dans le bêcher jusqu'à l'obtention d'une solution
saturée. La lecture du pH est effectuée une fois que l'on
n'observe plus des variations sur l'écran.
III-2-2 : Formulations élaborées
L'adjuvant minéral le plus fréquemment
utilisé dans la fabrication des briques de terre cuite est le sable
quartzeux. Il est utilisé comme dégraissant dans les argiles
plastiques dites grasses, de préférence à d'autres agents
dégraissants [19,20].
Compte tenu du fait que AE est assez grasse, (retrait sur sec
de 7%) ce matériau se trouve dans les limites maximales acceptables pour
les produits de terre cuite,[6,8]. Dans le
I
22
souci d'améliorer l'aptitude au séchage de cette
argile, nous avons effectué des ajouts de 0 , 20, 30 % d'argile AN d'une
part, et 9, 15% de sable quartzeux d'autre part.
111-2-3 : Fagonnage des eprouvettes
Les matériaux argileux (AE et AN) sont
prélevés, séchés, broyés dans un mortier en
porcelaine puis tamisés jusqu'à passage intégrale au tamis
d'ouverture de mailles 400um. Le sable (SF) est tamisé à 200um.
Pour la suite, les matériaux sont étuvés à
105°C pendant 24h et, conservés dans des sachets en plastique afin
d'éviter la fixation d'eau atmosphérique. Le façonnage des
produits de brique de terre cuite se fait généralement par
extrusion [21]. Mais, suite au manque d'extrudeuse, nous avons utilisé
les moyens compatibles avec les conditions expérimentales du
laboratoire. Les éprouvettes de formulation argile d'Etoa (AE)-argile de
Nkolbisson (AN), désignées E0, E20, E30, sont obtenues avec les
pourcentages d'argile AN ciaprès : 0, 20 et 30% .
Les éprouvettes de formulation argile d'Etoa-sable fin
(SF) dénommés AS9, AS15, sont obtenues avec les pourcentages de 9
et 15% de SF.
Pour une étude comparative, des éprouvettes (En )
ne contenant que l'argile de Nkolbisson (AN) étaient aussi
façonnées.
Pour l'étude du séchage, de la poudre de
matériau est humidifiée à 25% (eau
déminéralisée), et malaxée manuellement
jusqu'à l'obtention d'une pâte homogène. Le
façonnage a consisté à mettre la pâte plastique en
forme dans un moule en acier, puis à presser faiblement avec une presse
hydraulique. A la fin du pressage, il en ressort des éprouvettes
parallélépipédiques ( 7,9x3,9x1,8 cm ).
111-2-4 : Le sechage
L'étude du séchage a été
effectuée à l'aide des mesures des variations du retrait
linéaire de séchage et de la perte de masse des
éprouvettes de matériau en fonction du temps. Après le
façonnage d'une éprouvette de matériau, sa masse est prise
et une rainure de longueur déterminée est effectuée sur sa
surface
Soient L0 et M0 ,respectivement, la longueur et la masse de
l'éprouvette juste après façonnage, Lt et Mt , la longueur
et la masse de l'éprouvette après un temps t de séchage .
Le retrait linéaire de séchage à l'instant t est
donné par la relation :
R--
x100
L 0-Lt
23
L0
La perte de masse à l'instant t est donné par la
relation
ÄM= M 0- MT
x100 M0
III-2-4-1 : Le séchage naturel
Ce mode de séchage consiste à étaler les
éprouvettes de matériau sur un contre plaquet, dans l'air
atmosphérique du laboratoire, à la température de
26°C #177; 1°C. Pour chaque composition de formulation, trois
éprouvettes sont expérimentées et les mesures ( retrait
linéaire de séchage et perte de masse ) sont effectuées
toutes les 24h.
III-2-4-2 : Le séchage à
l'étuve
Parallèlement au séchage naturel, le
séchage iso thermique (50°C) à l'étuve a
été effectué pour les autres éprouvettes de
matériau. A cet effet, les mesures de variation de masse et de retrait
linéaire de séchage ont aussi été effectuées
toutes les 24h sur les éprouvettes de matériau. Toutefois, au
cours de cette étude, les éprouvettes façonnées
séjournent d'abord 24h dans l'air atmosphérique du laboratoire
(température de 26°C #177; 1°C) avant d'être
étuvées.
111-2- 5 : Cuisson des produits
Les produits sont cuits dans un four électrique de
marque FP34G et de capacité 0,02 m3.. C'est un four
programmable de température maximale 1280°C. La montée en
température est de 2°C /minute et le traitement a porté sur
la plage 850 -1100°C, avec un intervalle régulier de 50°C. La
durée du traitement à une température donnée est de
2 heures.
111.2.6- Propriétés physiques des
produits
Afin d'évaluer les performances des céramiques
des formulations élaborées, les propriétés
physiques suivantes ont été déterminées : la
couleur, le retrait linéaire de cuisson, le pourcentage d'eau
absorbée, la masse volumique apparente ainsi que la résistance
à la flexion.
a) La couleur
La couleur se définie comme l'impression que la
lumière diffusée par les corps produit sur l'oeil [22]. Pour
étudier la couleur des produits cuits, nous avons utilisé
l'appréciation visuelle.
24
b) Le retrait linéaire de cuisson
Le retrait linéaire de cuisson est le pourcentage de la
variation de longueur de l'éprouvette de matériau après le
traitement thermique [23].
En désignant par Lo et Lc les longueurs de
l'éprouvette de matériau avant et après la cuisson, le
retrait linéaire de cuisson Rc est donné par l'équation
:
=
Lo-Lc
× 100
Rc
Lo
c) Le pourcentage d'eau absorbée
Cette grandeur est définie comme étant le
rapport de l'augmentation de masse de l'échantillon
entraînée par une imbibition partielle en eau à la masse
sèche de l'échantillon. Cette imbibition est obtenue par
immersion de l'échantillon dans l'eau à 20°C et à la
pression atmosphérique pendant 24h [24]. Ces essais sont
effectués selon le protocole P18-554 des normes Françaises, AFNOR
[24]. Pour effectuer la mesure sur une éprouvette de matériau, sa
masse Ms est d'abord déterminée à l'air libre après
son étuvage à 105°C pendant au moins 24h. Elle est ensuite
immergée dans l'eau distillée pendant 24h à la
température de (20 #177;1)°C. L'éprouvette de
matériau est ensuite soigneusement épongée avec du papier
absorbant et sa masse Ma est déterminée. Le pourcentage d'eau
absorbée, ab, est donné par l'équation :
d) La masse volumique apparente
La masse volumique apparente est définie comme
étant le quotient de la masse sèche de l'échantillon par
le volume occupé par la matière solide, y compris les vides
contenus dans les grains (volume apparent) [24]. Les essais effectués
respectent le protocole P.18-554 des normes Françaises [24]. La mesure
de la masse volumique apparente est consécutive à la
détermination du pourcentage d'eau absorbée. Ainsi,
l'éprouvette de matériau imbibée d'eau (20°C) et de
masse Ma est introduite dans une nacelle métallique. Le tout est
plongé dans l'eau distillée d'un bêcher et la masse Ma' de
l'éprouvette de matériau est mesurée. Si Ms désigne
la masse de l'éprouvette étuvée à 105°C
pendant 24h, la masse volumique apparente ña est
donnée par l'équation :
ña = Ms e ' ñ
-
ñe=0,99823g /cm3 = masse volumique
de l'eau à 20°C [24 ]
25
e) La résistance à la flexion
Elle est obtenue par calcul après mesure de la charge
qu'un matériau peut supporter avant sa rupture. Les essais sont
effectués à l'aide d'un appareil à flexion qui utilise la
méthode des trois points. Ces essais sont basés sur le protocole
P.61-503 des normes Françaises [25]. L'éprouvette est
séchée à l'étuve à 105°C jusqu'à
poids constant. Après refroidissement, elle est placée sur deux
appuis cylindriques et horizontaux fixés sur un socle de mouvement
vertical. Un troisième cylindre immobile est placé au-dessus,
parallèlement et symétrique aux deux précédents. Le
socle des deux cylindres à une vitesse ascensionnelle de 2,5mm /min
jusqu'à la rupture de l'éprouvette de matériau. La lecture
sur un écran permet de déterminer la charge produisant cette
rupture. La résistance à la flexion est donnée par la
relation

3 FL
2 bh 2
où
F = force à la rupture de l'éprouvette (en N ),
L = écart entre les cylindres horizontaux (en mm), b =
largeur de l'éprouvette ( en mm),
h= épaisseur de l'éprouvette (en mm).
III-2-7 : Dispositif utilisé pour mesurer les
temperatures a PROMOBAT
Les mesures de températures à PROMOBAT ont
été faites à l'aide des thermocouple et multimètre.
Le thermocouple utilisé est du type Chromel / Alumel, avec une force
électromotrice qui croît de -9 à 50 mv quand la
température évolue de -200 à 1200°C [26]. Le point de
soudure des fils est réalisé grâce au
chalumeau-oxyacéthylénique.
Le multimètre est digital, de marque UNILAB type
513.021\3.
Les connections sont effectuées de façon à
avoir une force électromotrice positive lorsque la température
s'élève.
26
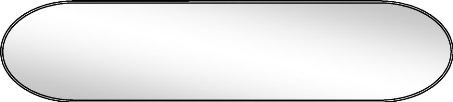
CHAPITRE IV :
RESULTATS, INTERPRETATIONS ET SUGGESTIONS
27
IV.1- CARACTÉRISATION DES MATIÈRES
PREMIÈRES
IV.1.1- Analyse granulométrique
Les résultats de l'analyse granulométrique des
matériaux argileux d'Etoa (AE) et de Nkolbisson (AN) sont
regroupés dans les tableaux II, III et IV , puis
représentés sur la figure 3.
Ces résultats montrent que l'argile d'ETOA est
constituée d'environ 40% de sable, 35% de limon et 25% d'argile
minéralogique tandis que l'argile de Nkolbinsson est constituée
de 66% de sable, 22% de limons et 12% d'argiles minéralogiques. Ces
différences de proportion en fractions granulométriques de
sables, limons et argiles minéralogiques ont une influence significative
sur les propriétés rhéologiques et céramiques des
matériaux. En effet, d'après la littérature, il est
souhaitable que la granulométrie d'une terre argileuse pour brique soit
étalée [6]. La granulométrie du matériau AE est
donc compatible avec celle des terres argileuses pour brique, ce qui n'est pas
le cas pour AN.
Tableau II : Tamisage humide de AE et AN
Masse sèche :500g
|
|
AE
|
AN
|
(I) (mm)
|
Poids Refus cumulés (g)
|
Tamisat (%)
|
Poids Refus cumulés (g)
|
Tamisat (%)
|
1,6
|
5
|
99,0
|
12
|
97,6
|
0,5
|
29
|
94,2
|
92
|
81,6
|
0,4
|
35
|
93,0
|
121
|
75,8
|
0,2
|
69
|
86,2
|
200
|
60
|
0,125
|
103
|
79,4
|
258
|
48,4
|
0,1
|
131
|
73,8
|
290
|
42,2
|
28
Tableau III: Sédimentométrie de
AN
% < 100um = 12,38 Température 25 #177; 1°C
prise d'essai P = 20,0g
volume de la suspension V = 1000 cm3
|
Densimètre : Ho = 19,5 d = 0,21 Cm = 0,5 Co = 1,7
|
Temps (1)
|
Lecture
|
R= A - B
|
Y %
|
Ht (cm)
|
dy (um)
|
% < dy
|
A
|
B
|
30
|
11
|
0,25
|
10,5
|
84,32
|
16,23
|
73,58
|
35,41
|
60
|
10
|
0,25
|
9,75
|
78,29
|
16,39
|
52,28
|
32,88
|
120
|
9,5
|
0,25
|
9,5
|
76,28
|
16,45
|
27,04
|
32,03
|
300
|
8,5
|
0,25
|
9
|
72,27
|
16,55
|
23,49
|
30,35
|
600
|
8,25
|
0,25
|
8
|
64,24
|
16,81
|
16,75
|
26,98
|
1800
|
7,5
|
0,25
|
7,75
|
62,23
|
16,81
|
9,68
|
26,14
|
3600
|
7
|
0,25
|
6,75
|
54,20
|
17,08
|
6,89
|
22,76
|
7200
|
6,25
|
0,25
|
6,25
|
50,19
|
17,18
|
4,89
|
21,08
|
10800
|
6
|
0,25
|
5,75
|
46,17
|
17,29
|
4,03
|
19,39
|
18000
|
5
|
0,25
|
5
|
40,15
|
17,44
|
3,11
|
16,86
|
86400
|
3,5
|
- 0,5
|
3
|
24,10
|
18,02
|
1,44
|
10,12
|
Tableau IV: Sédimentométrie de
AE
% < 100um = 13,80 Température 25 #177; 1°C
prise d'essai P = 20,0g
volume de la suspension V = 1000 cm3
|
Densimètre : Ho = 19,5 d = 0,21 Cm = 0,5 Co = 1,7
|
Temps (1)
|
Lecture
|
R= A - B
|
Y %
|
Ht (cm)
|
dy (um)
|
% < dy
|
A
|
B
|
30
|
11
|
0,25
|
10,75
|
86,33
|
16,24
|
79,60
|
63,88
|
60
|
10
|
0,25
|
9,75
|
78,29
|
16,45
|
52,38
|
57,93
|
120
|
9,5
|
0,25
|
9,25
|
74,28
|
16,55
|
37,15
|
54,96
|
300
|
8,5
|
0,25
|
8,25
|
66,25
|
16,76
|
23,64
|
49,02
|
600
|
8,25
|
0,25
|
8,00
|
64,24
|
16,81
|
16,74
|
47,53
|
1800
|
7,5
|
0,25
|
7,25
|
58,21
|
16,97
|
9,91
|
43,08
|
3600
|
7
|
0,25
|
6,75
|
54,20
|
17,07
|
6,88
|
40,11
|
7200
|
6,25
|
0,25
|
6,00
|
48,18
|
17,23
|
4,89
|
35,65
|
10800
|
6
|
0,25
|
5,75
|
46,17
|
17,28
|
4,00
|
34,16
|
18000
|
5
|
0,25
|
4,75
|
38,14
|
17,49
|
3,11
|
28,22
|
86400
|
3,5
|
- 0,5
|
4,00
|
32,12
|
17,81
|
1,43
|
23,76
|
29
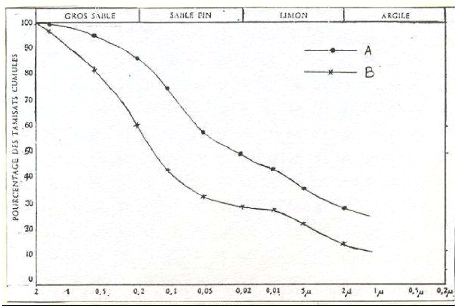
Figure 3 : Courbe de répartition
granulométrique des matériaux AE et AN
IV-1-2 La plasticité
La rhéologie étudie l'écoulement et la
déformation de la matière [9]. Ainsi, l'étude de la
rhéologie des pâtes peut conduire à la connaissance de la
plasticité. Une masse semi-solide comme l'argile humide peut être
plus ou moins déformée par une force mécanique sans perdre
sa cohésion et sans que la masse montre une tendance à reprendre
sa forme initiale. C'est dans ce sens qu'on emploie le terme «
plasticité » en céramique [9].
Les résultats des limites de liquidité et de
plasticité sont donnés dans le tableau V.
Tableau V : Résultats du test de
plasticité des matériaux AE et AN comparés à
ceux
des terres argileuses pour brique de référence
[6].
Échantillon
|
Limite de liquidité (%)
|
Limite de plasticité (%)
|
Indice de plasticité (%)
|
AE
|
41
|
26
|
15
|
AN
|
29
|
19
|
10
|
Argile de référence pour terre cuite
|
30 - 35
|
12 - 22
|
7 - 18
|
30
De ces résultats, il en ressort que les
matériaux AE et AN peuvent contenir 41 et 19% d'eau respectivement sans
couler sous leur propre poids. Par contre, ils ne peuvent se déformer de
manière plastique quand ils ont moins de 26 et 19% d'eau respectivement.
Plus une argile est plastique, plus elle nécessitera d'eau pour former
une pâte de consistance dite « normale » (c'est-à-dire
ne collant pas aux doigts et pouvant supporter des corps inertes
(dégraissant) tout en conservant une aptitude au façonnage
appréciable et une résistance mécanique à sec
suffisante pour assurer la fabrication ) [8,9].
La teneur en fraction fine du matériau AE
supérieure à celle du matériau AN est l'une des raisons
pour laquelle AE est plus plastique que AN
Ces résultats montrent donc qu'il est nécessaire
d'envisager des ajouts de corps inertes dans le matériau AE pour
améliorer son aptitude au séchage.
IV.1.3- Le pH
La mesure du pH d'une solution saturée d'argile AE a
donné 5,70 . Ce résultat montre donc le caractère acide de
ce matériau et laisse entrevoir la possibilité d'améliorer
les propriétés rhéologiques de cette argile par le
carbonate de sodium (si l'on s'en tient au fait expérimental qu'une
argile acide convenablement traitée et dont les propriétés
sont améliorées au maximum a un pH compris entre 6 et 8,5)
[7].
IV.2- LE SÉCHAGE
Les études sur le séchage des formulations
élaborées montrent que l'aptitude au séchage du
matériau AE est améliorée par ajout d'argile AN ou du
sable (figure 4a et 5a ). Le sable étant un dégraissant à
faible porosité [8], pour une même teneur en eau d'imbibition,
l'ajout de dégraissant a pour effet de diminuer la consistance de la
pâte. Ce qui inhibe la tendance du sable à réduire le
retrait linéaire de séchage. Dans la pratique industrielle, c'est
plutôt la consistance de la pâte qui intervient au cours du
façonnage, de sorte que l'ajout du sable a pour rôle la diminution
de la quantité d'eau d'imbibition, la facilitation du séchage et
la réduction du retrait linéaire de séchage [7,8]. La
diminution des variations dimensionnelles entraînant alors la diminution
du risque d'apparition de fentes de séchage.
a) Le séchage naturel
Les résultats obtenus sur le séchage naturel
sont consignés dans le tableau VI. Les figures 4a et 4b montrent
l'évolution de la perte de masse et du retrait linéaire de
séchage des éprouvettes de matériau pendant le
séchage (air atmosphérique).
31
Au cours du premier jour, la surface des produits est assez
humide et la vitesse de séchage reste dans une large mesure fonction de
la vitesse d'évaporation d'eau à la surface des
éprouvettes de matériau, ce qui justifie les pertes de masse
assez voisines pour 24 heures de séchage (figure 4a). A partir du
2e jour, l'humidité de la surface commence à
être conditionnée par le phénomène de diffusion
capillaire : l'influence des dégraissants (qui améliore la
diffusion capillaire) commence à devenir perceptible. Au 5e
jour, on observe une perte de masse de 16,9% pour E0 contre 18,1 , 18,6 , 18,8
,et 19,4% pour E20,E30, AS9, et AS15 respectivement. A partir du 7e
jour, la diffusion d'eau dans les échantillons amaigris
(E20,E30,AS9,AS15) est limitée par le gradient d'humidité. La
différence de vitesse de séchage entre les éprouvettes de
matériau non amaigris (E0), et amaigris (E20,E30,AS9,AS15) devient de
plus en plus faible et il apparaît une perte de masse voisine de 22%
après 10 jours de séchage pour toutes les formulations
étudiées.
La figure 4b montre l'évolution du retrait
linéaire en fonction du temps pour le séchage à l'air
atmosphérique. De cette figure, il en ressort que les
dégraissants diminuent le retrait linéaire de séchage.
Cependant, la teneur en eau étant la même pour toutes les
formulations élaborées, au-delà d'une certaine valeur de
dégraissant incorporé, la pâte devient si molle que le
retrait de séchage s'en trouve augmenté. Ce qui justifie le fait
que AS9 présente un retrait linéaire de séchage
inférieur à E0 , contrairement à E30 et AS15.
b) Le séchage par étuvage
Les résultats sur le séchage à
l'étuve sont regroupés dans le tableau VII. Les figures 5a et 5b
présentent les variations de la perte de masse et du retrait
linéaire de séchage en fonction du temps. Ces résultats
montrent que les variations observées pour le séchage à
l'étuve restent semblables à celles du séchage dans l'air
atmosphérique.
Toute fois, en industrie, le coût
énergétique du séchage artificiel nous amène
à ressortir l'influence des dégraissants. La figure 5a
présente l'évolution de la perte de masse en fonction du temps de
séchage. D'après cette figure, après un jour
d'étuvage, il apparaît une perte de masse de 12,6% pour E0 contre
14,4 , 15,1 , 14,4 , 15,2% respectivement pour E20,E30 , AS9 , AS15. En
considérant un séchoir industriel qui contient 10 tonnes de
produit à sécher, si l'apport de dégraissant
entraîne le départ supplémentaire de 2% d'eau par rapport
au matériau non dégraissé, pendant un même temps de
séchage, cela revient à économiser une énergie
nécessaire pour le départ de 200 kg d'eau des produits, ce qui
n'est pas négligeable.
Pour toutes les formulations élaborées, les
éprouvettes séchées aussi bien à l'air
atmosphérique qu'à l'étuve n'ont présenté
aucune fissuration. Les résultats obtenus montrent que la plus grande
partie des fentes de séchage observées à la PROMOBAT
seraient due à une préparation inadéquate de la
matière première. En effet, beaucoup d'impuretés
grossières se retrouvent dans la pâte suite au manque de broyeur
en début de chaîne de production.
32
|
1er jour
|
2e jour
|
3e jour
|
4e jour
|
5e jour
|
6e jour
|
7e jour
|
8e jour
|
9e jour
|
10e jour
|
AM
(%)
|
R
(%)
|
AM
(%)
|
R
(%)
|
AM
(%)
|
R
(%)
|
AM
(%)
|
R
(%)
|
AM
(%)
|
R
(%)
|
AM
(%)
|
R
(%)
|
AM
(%)
|
R
(%)
|
AM
(%)
|
R
(%)
|
AM
(%)
|
R
(%)
|
AM
(%)
|
R(%)
|
E1
|
4,9
|
4,28
|
8,95
|
6,9
|
11,97
|
7,14
|
14,45
|
7,14
|
16,92
|
7,14
|
19,05
|
7,14
|
20,84
|
7,14
|
21,13
|
7,14
|
21,65
|
7,14
|
21,94
|
7,14
|
E3
|
5,48
|
3,09
|
9,22
|
5,71
|
12,98
|
6,9
|
15,32
|
7,14
|
18,10
|
7,14
|
20,30
|
7,14
|
21,5
|
7,14
|
21,79
|
7,14
|
22,23
|
7,14
|
22,41
|
7,14
|
E4
|
5,55
|
4,04
|
10,24
|
6,9
|
14,25
|
7,38
|
16,28
|
7,38
|
18,68
|
7,38
|
20,71
|
7,38
|
21,60
|
7,38
|
21,96
|
7,38
|
22,34
|
7,38
|
22,52
|
7,38
|
E9
|
5,67
|
3,09
|
9,51
|
5,23
|
12,43
|
5,95
|
15,68
|
6,66
|
18,8
|
6,66
|
21,00
|
6,66
|
21,68
|
6,66
|
21,99
|
6,66
|
22,67
|
6,66
|
22,82
|
6,66
|
E11
|
5,93
|
4,93
|
9,86
|
6,9
|
12,95
|
7,61
|
16,34
|
7,85
|
19,46
|
7,85
|
21,21
|
7,85
|
21,88
|
7,85
|
22,42
|
7,85
|
22,67
|
7,85
|
22,76
|
7,85
|
Tableau VII : Résultats sur le
séchage isotherme à l'étuve (t° = 50°C, Eau de
façonnage : 25% )
33
|
1er jour (air libre)
|
2e jour
|
3e jour
|
4e jour
|
AM (%)
|
R (%)
|
AM (%)
|
R (%)
|
AM (%)
|
R (%)
|
AM (%)
|
R (%)
|
E1
|
6,44
|
3,80
|
12,67
|
7,14
|
24,34
|
7,14
|
24,66
|
7,14
|
E3
|
6,46
|
3,09
|
14,43
|
7,14
|
24,56
|
7,14
|
24,72
|
7,14
|
E4
|
6,30
|
4,04
|
15,06
|
7,38
|
24,54
|
7,38
|
24,69
|
7,38
|
E9
|
6,66
|
3,09
|
14,38
|
6,66
|
24,48
|
6,66
|
24,75
|
6,66
|
E11
|
7,05
|
4,93
|
15,15
|
7,85
|
24,52
|
7,85
|
24,76
|
7,85
|
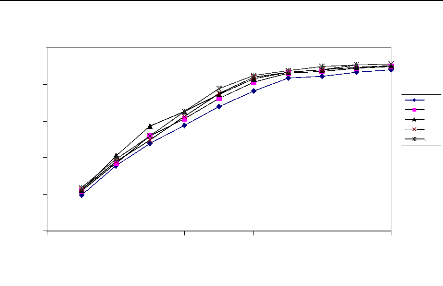
Perte de masse (%)
25
20
15
10
5
0
0 2 4 6 8 10
Jours
E0 E20 E30 E1 AS9
E3 AS15
E4
Figure 4a : Perte de masse des
éprouvettes de matériau
en fonction du temps de séchage (séchage
naturel)
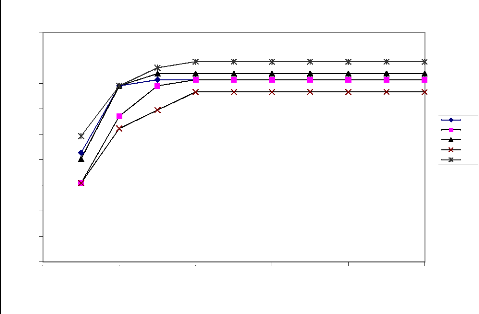
Retrait lineaire (%)
4
6
2
9
8
7
5
3
0
1
0 2 4 6 8 10
Jours
E0 E20 E30 AS9 AS15
Figure 4b : Retrait linéaire de
séchage des éprouvettes de matériau en fonction du temps
(séchage naturel )
34
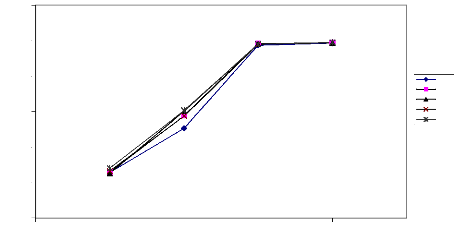
0 1 2 3 4 5
Perte de masse (%)
25
20
30
15
10
5
0
E0 E20 E30 AS9 AS15
Jours
Figure 5a : Perte de masse des
éprouvettes de matériau en fonction du temps (séchage
à l'étuve)
Jours
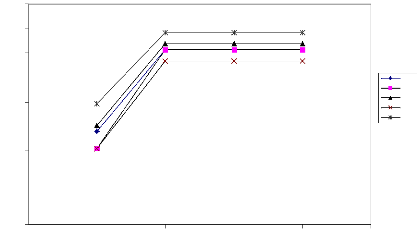
Retrait lineaire (%)
4
9
8
6
5
3
2
0
7
1
0 1 2 3 4 5
E0 E20 E30 AS9 AS15
Figure 5b : Retrait linéaire de
séchage des éprouvettes de matériau
en fonction du temps (séchage à l'étuve)
35
IV.3- PROPRIÉTÉS PHYSIQUES ET
MÉCANIQUES DES PRODUITS DE CUISSON
L'étude des propriétés physiques et
mécaniques a porté sur la couleur, le retrait linéaire de
cuisson, la perte au feu, le pourcentage d'absorption d'eau, la masse volumique
apparente et la résistance à flexion.
IV.3.1- La couleur
Les résultats obtenus sont regroupés dans le
tableau VIII. Ces résultats montrent que la couleur des
céramiques de AE varient du rouge brique-clair (850°C) au rouge
brique-foncé (1100°C). Les céramiques de AN sont brun-sombre
à 850°C et deviennent brun-clair entre 900 et 1100°C.
L'incorporation du matériau AN dans l'argile AE conduit
aux céramiques ayant un ton clair tandis que l'ajout de sable dans cette
dernière argile est sans effet notable sur la coloration. La couleur
rouge des produits de cuisson est probablement due à la présence
des oxydes de fer. D'autre part, la couleur d'un tesson peut être
modifiée par la présence des impuretés contenues dans le
cru et par les conditions de cuisson (atmosphère plus ou moins oxydante
et température maximale atteinte ) [3,27]. Ainsi, le changement de ton
obtenu pour les céramiques de coupures AE-AN est dû à
l'interaction entre les minéraux et les impuretés que l'argile de
Nkolbisson produit avec les composants chimiques et minéralogiques du
matériau AE .
Tableau VIII : Coloration des produits de
cuisson en fonction de la température
Températures Formulations
|
850°C
|
900°C
|
950°C
|
1000°C
|
1050°C
|
1100°C
|
E0
|
Rouge brique claire
|
Rouge brique claire
|
Rouge brique claire
|
Rouge brique
|
Rouge brique
|
Rouge brique sombre
|
E20
|
Rouge brique claire
|
Rouge brique claire
|
Rouge brique claire
|
Rouge brique
|
Rouge brique
|
Rouge brique
|
E30
|
Rouge brique claire
|
Rouge brique claire
|
Rouge brique claire
|
Rouge brique
|
Rouge brique
|
Rouge brique
|
En
|
Brun sombre
|
Brun sombre
|
Brun clair
|
Brun clair
|
Brun clair
|
Brun clair
|
AS9
|
Rouge brique claire
|
Rouge brique claire
|
Rouge brique claire
|
Rouge brique
|
Rouge brique
|
Rouge brique sombre
|
AS15
|
Rouge brique claire
|
Rouge brique claire
|
Rouge brique claire
|
Rouge brique
|
Rouge brique
|
Rouge brique
|
36
IV.3.2- Le retrait lineaire (Re)
Le retrait linéaire de cuisson est un paramètre
qui traduit la réactivité d'un matériau au cours de la
cuisson [28]. Ainsi, l'augmentation de Rc dans les figures 6a et 6b
est une conséquence des transformations chimiques qui se produisent dans
ces matériaux. Par ailleurs, la figure 6a montre que le matériau
AN (matériau argileux de Nkolbisson ) ne donne aucun retrait entre 850et
1050°C. En effet, ce matériau est très riche en quartz, de
sorte que les réactions chimiques qui se produisent sont inhibées
par la présence d'un excès de minéral quartzeux. Ce qui
montre que ce dernier matériau est un bon adjuvant pour la diminution du
retrait linéaire de cuisson. Ce qui précède explique donc
la diminution du retrait pour les formulations E20 et E30, comparé aux
céramiques obtenues avec la seule argile AE (E0). Pour ce qui est des
valeurs de Rc pour les formulations AS9 et AS15 entre 850 et
1000°C, les résultats obtenus sont normaux, car le quartz est bien
un adjuvant dégraissant sur cet intervalle de température.
Toutefois, au delà de 1000°C les valeurs de
Rc augmentent fortement pour toutes les formulations, car,
d'après certains auteurs [29,30], il se produit une réaction de
réarrangement au sein du produit (passage de la métakaolinite
à la mullite ou à la formation d'une phase spinelle et
éventuellement apparition de l'alumine y .
Tableau IX : Retrait linéaire de cuisson
(en %) des produits en fonction de la température
37
Températures Formulations
|
850°C
|
900°C
|
950°C
|
1000°C
|
1050°C
|
1100°C
|
E0
|
0,77
|
1,54
|
1,78
|
2,3
|
3,32
|
6,92
|
E20
|
0
|
1,28
|
1,53
|
1,54
|
2,3
|
4,35
|
E30
|
0
|
0,25
|
0,77
|
1,28
|
1,53
|
4,29
|
En
|
0
|
0
|
0
|
0
|
0
|
1,49
|
AS9
|
0,76
|
0,76
|
0,76
|
0,76
|
3,05
|
5,37
|
AS15
|
0
|
0,76
|
0,76
|
0,76
|
2,34
|
4,07
|
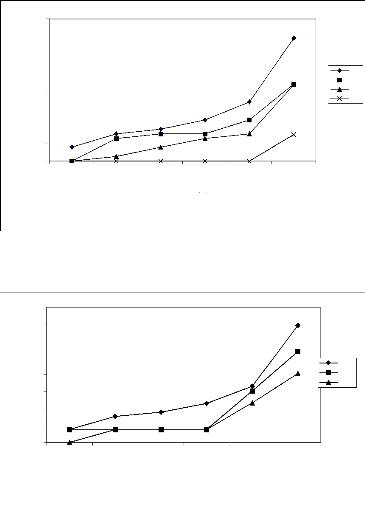
8
7
6
Retrait lineaire (%)
E0 E20 E30 En
5
4
3
2
1
0
Figure 6a : Retrait linéaire de cuisson des
céramiques de coupures AE-AN en fonction de la
température
850 900 950 1000 1050 1100
Température (°C)
8
7
6
Retrait lineaire (%)
5
E0 AS9 AS15
4
3
2
1
0
Figure 6b : Retrait linéaire de cuisson des
céramiques de mélange AE-SF en fonction de la
température
850 900 950 1000 1050 1100
Température(°C)
38
IV.3.3- La perte au feu (PF)
Les résultats de perte au feu des matériaux
étudiés sont regroupés dans le tableau X et les figures 7a
et 7b donnent les variations de PF avec la température. Ces
résultats montrent que la perte au feu de E 0
(matériau AE ) varie de 8,44 à 10,19% entre 850°C et
1100°C, ce qui montre que les plus grandes pertes de masse se sont
effectuées en dessous de 850°C. Ceci est normal, car en dessous de
cette température, le matériau est sujet au départ d'eau
de cristallisation, de la décomposition de la matière
organique...Il apparaît également que la perte au feu diminue avec
l'augmentation d'adjuvant. Ceci peut s'expliquer d'une part par le fait que les
dégraissants quartzeux ne contiennent pas d'eau liée chimiquement
et d'autre part, l'argile AN titre fortement en sable (tableau II )
Tableau X: Perte au feu (en % ) des produits
de cuisson en fonction de la température
850 900 950 1000 1050 1100
Température (°C)
Figure 7a : Perte au feu des céramiques de
coupures AE-AN en fonction de la température
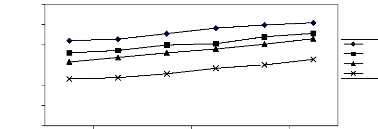
12
10
Perte au feu (%)
8
6
4
2
0
E0 E20 E30 En
39
Températures Formulations
|
850°C
|
900°C
|
950°C
|
1000°C
|
1050°C
|
1100°C
|
E0
|
8,44
|
8,59
|
9,12
|
9,66
|
9,98
|
10,19
|
E20
|
7,22
|
7,46
|
8,01
|
8,13
|
8,82
|
9,16
|
E30
|
6,33
|
6,77
|
7,23
|
7,61
|
8,09
|
8,63
|
En
|
4,64
|
4,76
|
5,13
|
5,67
|
6,04
|
6,58
|
AS9
|
7,36
|
7,45
|
7,99
|
8,44
|
8,93
|
9,27
|
AS15
|
6,81
|
6,83
|
7,35
|
7,83
|
8,26
|
8,88
|
Température(°C)
Figure 7b : Perte au feu des céramiques de
mélange AE-SF en fonction de la température
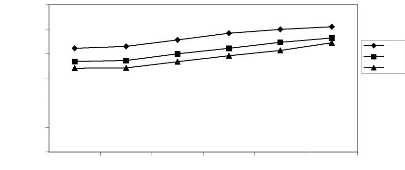
Perte au feu (%)
850 900 950 1000 1050 1100
12
10
8
6
4
2
0
E0 AS9 AS15
IV.3.4- Le pourcentage d'absorption d'eau
Le pourcentage d'absorption d'eau est une
propriété très importante en céramique. Elle permet
d'avoir une idée sur le taux de grésification du tesson [31-34].
Les figures 8a et 8b montrent la variation du pourcentage d'absorption d'eau du
matériau AE en fonction de la température, du pourcentage d'ajout
de sable et du pourcentage d'ajout du matériau AN. Ces résultats
montrent que pour une formulation donnée, le pourcentage d'absorption
d'eau diminue avec l'augmentation de la température. Ceci serait
dû à l'augmentation du taux de grésification avec la
température. Nous notons également que l'introduction du sable a
pour effet d'abaisser légèrement le pourcentage d'absorption
d'eau à basse température (850°C - 900°C), tandis qu'a
haute température (1050- 1100°C ), cette introduction a des effets
contraires. Ceci peut s'expliquer par le fait qu'à basse
température, le taux de grésification de notre matériau
étant très faible, la présence de sable dans le tesson
entraîne la rupture des courants capillaires ; Ce qui entraîne la
diminution du pourcentage d'absorption d'eau. Par contre, à haute
température, sa présence inhiberait les réactions de
consolidations qui conduisent à la réduction de la
porosité.
D'après Melo et al[35], le pourcentage d'absorption
d'eau des briques de terre cuite ne devrait pas dépasser 20%. Si l'on
s'en tient à cela, on pourrait dire que la température
idéale de cuisson de nos produits se situerait entre 1050 et
1100°C. Ce pourcentage ne doit non plus être trop faible. En effet,
la texture d'une terre cuite joue un rôle essentiel sur
l'adhérence du produit à un mortier de ciment [7].
40
Mémoire de D.E. S. S en Chimie
bidustrielle
Tableau XI : Pourcentage d'absorption d'eau des
produits de cuisson en fonction de la température
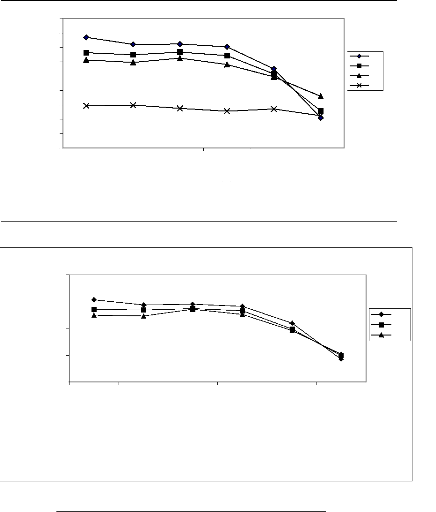
850 900 950 1000 1050 1100
Température (°C)
Figure 8a : Pourcentage d'adsorption d'eau des
céramiques de coupures AE-AN en fonction de la
température
28
Pourcentage d'absorption d'eau (%)
26
24
22
20
18
16
14
12
10
E0 E20 E30 En
Température(°C)
Figure 8b: Pourcentage d'adsorption d'eau des
céramiques de mélange AE-SF en fonction de la
température
Pourcentage d'absorption d'eau (%)
850 900 950 1000 1050 1100
E0 AS9 AS15
30
25
20
15
10
41
Températures
|
|
|
|
|
|
|
Formulations
|
850°C
|
900°C
|
950°C
|
1000°C
|
1050°C
|
1100°C
|
E0
|
25,41
|
24,43
|
24,47
|
24,09
|
21,02
|
14,23
|
E20
|
23,27
|
22,98
|
23,35
|
22,86
|
20,31
|
15,17
|
E30
|
22,25
|
21,91
|
22,52
|
21,62
|
19,91
|
17,2
|
En
|
15,88
|
15,98
|
15,52
|
15,13
|
15,44
|
14,49
|
AS9
|
23,62
|
23,39
|
23,73
|
23,29
|
19,81
|
14,94
|
AS15
|
22,5
|
22,31
|
23,53
|
22,61
|
19,62
|
15,26
|
IV-3- 5 : La masse volumique apparente
Les résultats des masses volumiques apparentes sont
regroupés dans le tableau XII. Les figures 8a et 8b montrent les masses
volumiques apparentes des différentes formulations en fonction de
l'évolution de la température. Les masses volumiques du
matériau AE croissent de 1,61g/cm3 à
1,94g/cm3 quand la température évolue de 850°C
à 1100°C. A basse température (850°- 900°C), les
ajouts de sable élèvent légèrement la masse
volumique, tandis qu'à haute température (1050°,
1100°C), on observe le phénomène contraire. Ceci peut
s'expliquer par le fait qu'à basse température, les
réactions de densification étant faibles, le sable est encore
plus dense que la matrice céramique dans laquelle il est noyé ;
tandis qu'à haute température, les réactions de
consolidations entraînent une augmentation de la densité de la
matrice. Ce qui a pour effet d'inverser le phénomène
observé aux plus basses températures.
Tableau XII : Masses volumiques apparentes (en
g/cm3 ) des produits de cuisson en fonction
de la température
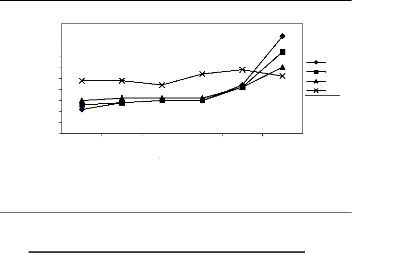
Température (°C)
Figure 9a : Masse volumique apparente des
céramiques de coupures AE- AN en fonction de la
température
Masse volumique apparente(g/cm3)
2
1,95
1,9
1,85
1,8
1,75
1,7
1,65
1,6
1,55
1,5
850 900 950 1000 1050 1100
E0 E20 E30 En
Températures Formulations
|
850°C
|
900°C
|
950°C
|
1000°C
|
1050°C
|
1100°C
|
E0
|
1,61
|
1,64
|
1,65
|
1,65
|
1,72
|
1,94
|
E20
|
1,63
|
1,64
|
1,65
|
1,65
|
1,71
|
1,87
|
E30
|
1,65
|
1,66
|
1,66
|
1,66
|
1,71
|
1,8
|
En
|
1,74
|
1,74
|
1,72
|
1,77
|
1,79
|
1,76
|
AS9
|
1,63
|
1,65
|
1,66
|
1,65
|
1,74
|
1,91
|
AS15
|
1,65
|
1,67
|
1,65
|
1,64
|
1,75
|
1,82
|
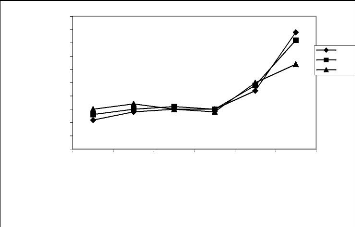
Masse volumique apparente (g/cm3)
Figure 9b : Masse volumique apparente des
céramiques de mélange AE- SF en fonction de
la température
1,95
1,85
1,75
1,65
1,55
1,9
1,8
1,7
1,6
1,5
2
850 900 950 1000 1050 1100
Température(°C)
E0 AS9 AS15
IV.3.6- La resistance a la flexion (8 )
Les résultats de la résistance à la
flexion sont regroupés dans le tableau XIII. Les figures 9a et 9b
présentent les variations de ö des différentes formulations
en fonction de la température. Ces résultats montrent qu'entre
850 et 1100°C, la résistance mécanique des céramiques
des formulations élaborées augmente avec
l'élévation de la température et diminue avec la
proportion de dégraissant incorporée. Entre 850 et 1100°C la
résistance à la flexion du matériau AE varie de 1,78
à 7,30 Mpa tandis que celle de AS15 varie de 1,04 à 3,13 Mpa.
Ceci nous montre l'aspect négatif de l'ajout de dégraissant sur
les propriétés mécaniques de l'argile d'Etoa. En effet,
bien que le dégraissant induise certains avantages au cours du
séchage de l'argile d'Etoa, son apport ne doit pas dépasser 10%
(en masse) si nous voulons atteindre une résistance à la flexion
supérieure à 4Mpa à 1100°C.
Généralement pour les produits céramiques, les
propriétés mécaniques augmentent avec la
température de cuisson jusqu'à ce que la phase vitreuse atteigne
une proportion optimale. Au-delà de cette proportion, toute augmentation
de la température entraîne leur diminution [33,34]. Ceci nous
amène à croire que la résistance à la flexion de
nos formulations peut encore augmenter si nous élevons la
température de cuisson.
Les briques de terre cuite étant des matériaux
fragiles, la rupture s'effectue au cours du chargement élastique
dès que la contrainte atteint localement le seuil critique de
décohésion inter atomique. Cette séparation se produit par
propagation de fissures existant dans le matériau. La rupture est donc
fortement influencée par la présence d'entaille (macro fissures)
résultant de défauts de fabrication ou de conception [36,37]. Il
est donc nécessaire de procéder à un broyage des
matières premières et d'effectuer une bonne
homogénéisation de la pâte avant le façonnage.
43
Mémoire de D.E. S. S en Chimie
bidustrielle
Tableau XIII: Résistance à la
flexion (en Mpa ) des produits de cuisson en fonction de la
température
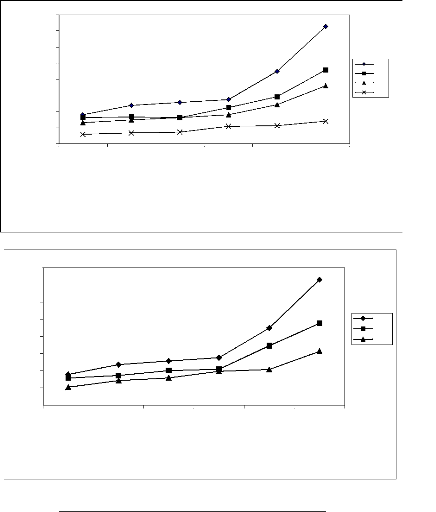
Température (°C)
Figure 10a : Résistance à la flexion des
céramiques de coupures AE-AN en fonction de la
température
Resistance a la flexion (Mpa)
850 900 950 1000 1050 1100
E0 E20 E30 En
8
7
6
5
4
3
2
1
0
Température(°C)
Figure 10b : Résistance à la flexion des
céramiques de mélange AE-SF en fonction de la
température
Resistance a la flexion (Mpa)
850 900 950 1000 1050 1100
E0 AS9 AS15
8
7
6
5
4
3
2
1
0
44
Températures Formulations
|
850°C
|
900°C
|
950°C
|
1000°C
|
1050°C
|
1100°C
|
E0
|
1,78
|
2,36
|
2,57
|
2,76
|
4,49
|
7,3
|
E20
|
1,6
|
1,66
|
1,61
|
2,23
|
2,93
|
4,6
|
E30
|
1,29
|
1,49
|
1,62
|
1,79
|
2,42
|
3,59
|
En
|
0,58
|
0,67
|
0,72
|
1,06
|
1,14
|
1,41
|
AS9
|
1,57
|
1,72
|
2
|
2,08
|
3,46
|
4,76
|
AS15
|
1,04
|
1,42
|
1,58
|
1,96
|
2,07
|
3,13
|
IV-4 : PROGRAMME THERMIQUE UTILISÉ À
PROMOBAT
Les résultats des mesures de températures
effectuées à PROMOBAT sont regroupés dans le tableau XIV.
Étant donné que nous avons utilisé un thermocouple
à une soudure, à la température correspondante à la
force électromotrice lue sur le multimètre, nous ajoutons la
valeur de la température ambiante (26°C) pour obtenir la
température mesurée. La figure 11 montre l'évolution de la
température en fonction du temps pour une cuisson réalisée
au cours du mois de décembre 2003. Cette courbe représente un
programme de cuisson dont la vitesse de chauffe ne constitue aucun danger pour
la qualité des produits. Malheureusement, suite à l'absence de
capteurs et d'enregistreurs de températures à PROMOBAT, les
programmes de cuisson varient en fonction de la nature et de l'humeur de ceux
qui cuisent. C'est l'une des raisons pour laquelle on observe parfois des taux
de casse très élevés (supérieure à 50%) sur
cuit. D'après la figure 11, il ressort que la température
maximale à l'endroit où est placé le thermocouple est de
836°C. Par ailleurs, nous avons noté des écarts de
température supérieure à 300°C dans le four au cours
de la cuisson ; ce qui justifie quelques différences observées
quant à l'aspect des produits cuits.
Tableau XIV : Résultats des mesures de
température effectuées à PROMOBAT
Temps (heures)
|
0,5
|
1
|
1,5
|
2
|
2,5
|
3
|
3,5
|
4
|
4,5
|
5
|
5,5
|
6
|
6,5
|
7
|
7,5
|
8
|
8,5
|
9
|
9,5
|
10
|
f.e.m (mv)
|
0,8
|
1,2
|
1,8
|
2,3
|
3,1
|
3,9
|
4,5
|
4,8
|
5,1
|
5,5
|
6,5
|
8,3
|
9,6
|
10,4
|
10,9
|
12,5
|
14,0
|
15,3
|
16,7
|
17,5
|
Températures (°C)
|
46
|
56
|
71
|
83
|
102
|
121
|
136
|
143
|
150
|
160
|
185
|
230
|
262
|
282
|
294
|
333
|
371
|
396
|
433
|
452
|
Temps (heures)
|
10,5
|
11
|
11,5
|
12
|
12,5
|
13
|
13,5
|
14
|
14,5
|
15
|
15,5
|
16
|
16,5
|
17
|
17,5
|
18
|
f.e.m (mv)
|
18,2
|
19,3
|
22,5
|
23,6
|
24,7
|
25,1
|
26,8
|
27,9
|
28,1
|
29,0
|
29,5
|
30,7
|
31,7
|
32,8
|
33,7
|
33,6
|
Températures (°C)
|
469
|
495
|
570
|
595
|
621
|
631
|
671
|
697
|
702
|
716
|
735
|
763
|
788
|
814
|
836
|
833
|
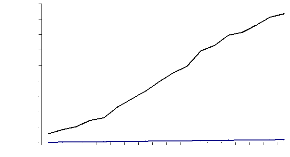
1 2 3 4 5 6 7 8 9 10 11 12 13 14 15 16 17 18
Temperatures (V)
400
900
800
700
600
500
300
200
100
0
Temps (en heure)
45
Figure 11 : Variations de la température
en fonction du temps de chauffe à PROMOBAT
IV.5- SUGGESTIONS
La qualité des briques produites à PROMOBAT peut
être améliorée par l'installation d'un broyeur en
début de chaîne de production. Cela limitera les fentes de
séchage et pourra permettre le cas échéant l'utilisation
de chamotte (casses sur cuit) comme dégraissant. Ceci nous donne
l'organigramme de production suivant :
Argile d'ETOA (Brut de carrière)

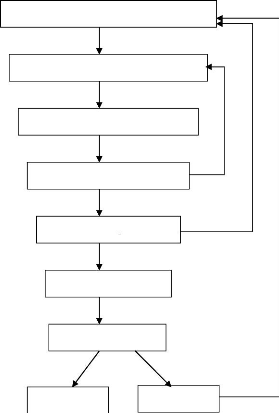
Expédition
Mélangeur mouilleur
Broyeur à cylindre
Sortie four et tris
Chambre à vide
Extrudeuse
Séchage
Cuisson
Casses
46
Figure 12 : Organigramme de production
proposé à PROMOBAT
PROMOBAT gagnerait également en augmentant l'espace de
séchage. Cela pourra permettre entre autre le stockage d`une
quantité plus importante de briques sèches, le maintien d'un
travail constant au niveau de la fabrication, et une limitation de
l'utilisation du séchoir électrique. En effet, l'espace de
séchage actuel permet le stockage de 40.000 à 50.000 briques
(10,5x15x30cm ). Pour une production moyenne de 6000 briques par jour, il faut
environ une semaine pour remplir l'espace de séchage et de stockage. Si
entre temps les cuissons ne sont pas faites, la fabrication est
paralysée à cause de la non disponibilité d'espace
à sécher et à stocker les produits façonnés.
D'autre part, lorsque la demande est forte et que PROMOBAT se trouve
obligée de réaliser deux à trois cuissons par semaine, les
briques sèches disponibles sont parfois insuffisantes. Si au contraire
PROMOBAT augmente l'espace de séchage de façon à pouvoir
sécher et stocker 100.000 à 200.000 briques à la fois,
elle pourra se passer de l'utilisation du séchoir électrique dont
la consommation énergétique est assez significative.
En effet, le temps moyen de séchage naturel d'une
brique (environ 10 jours) et la vitesse de façonnage de 6000 briques par
jour pourront être suffisant pour alimenter les deux fours en briques
sèches pour des cuissons de 10 à 20000 briques par semaine, ce
qui représente à peu près la capacité de production
actuelle de PROMOBAT.
L'énergie pour le séchage naturel étant
gratuite, le séchoir électrique ne serait alors utilisé
qu'en cas de nécessité (demande de briques de format non
disponible, conditions climatiques très défavorables,
augmentation de la production suite à la construction de nouveaux
fours...).
Pour ce qui est de la cuisson, l'une des astuces qui pourrait
rendre le processus efficient serait de s'assurer que toutes les briques
entrant dans le four sont totalement sèches. Ainsi, on ne gaspillera pas
de combustible pour achever un processus qui aurait pu être fait
naturellement [38]. Ceci anéantirait d'autre part le risque de casse
dû à l'élévation de la pression de vapeur d'eau dans
les pores des produits lorsqu'ils sont enfournés humides.
Concernant le combustible bois, il serait
bénéfique pour PROMOBAT lors des achats de rechercher les
matériaux les plus massifs et de les entreposer à l'abri des
pluies : en effet, le bois massif sec montre des propriétés
calorifiques plus élevées que le bois humide [39].
47
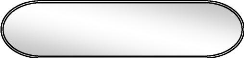
CONCLUSION
48
Il ressort de ce travail que les propriétés
céramiques de nos différents produits de cuisson (masse volumique
apparente, la résistance à la flexion, la perte au feu et le
retrait linéaire de cuisson) croissent avec l'évolution de la
température pendant que le pourcentage d'absorption d'eau
décroît.
Nous avons également observé que les ajouts de
dégraissants diminuent les propriétés mécaniques de
l'argile d'Etoa, malgré le fait qu'ils améliorent son aptitude au
séchage. Les résultats de résistance à la flexion
de nos échantillons cuits à basse température (850 -
1050°C) sont relativement faibles par rapport aux normes Françaises
(7Mpa pour les briques normales) [5] ; Cependant, étant donné la
difficulté et le coût énergétique qu'une entreprise
supporterait en cuisant ses briques à haute température (
1100°C ), il serait sans doute plus sensé, si l'on veut
améliorer les propriétés mécaniques des produits de
cuisson, de rechercher plutôt une matière première fusible,
qui pourrait développer des propriétés optimums autour de
950°C. Malheureusement, dans la pratique, cette hypothèse est le
plus souvent écartée à cause du coût
économique du transport quand le gisement et l'usine sont assez
distants.
L'insensibilité de l'argile de Nkolbisson entre 850 et
1100°C (retrait linéaire et perte de masse qui croissent de 0
à 1,49% et 4,64 à 6,58% respectivement) laisse envisager la
possibilité de son utilisation dans l'industrie des réfractaires
alumino-silicatés.
En somme, PROMOBAT devrait prendre un certain nombre de
disposition pour pouvoir pallier aux casses.
Au niveau de la fabrication, l'installation d'un broyeur en
début de chaîne contribuerait beaucoup à diminuer les
fentes de séchage. PROMOBAT devrait également veiller à ce
que les produits se sèchent sans brutalité et s'assurer au moment
de leur enfournement que le processus de séchage est terminé.
Pour ce qui est de la cuisson, un équipement en capteur de
température pourra alléger la tâche des cuiseurs tout en
leur permettant de rechercher le cycle de cuisson optimum.
Il serait enfin bénéfique pour PROMOBAT
d'effectuer des tests tels que la résistance à la flexion et le
taux d'absorption d'eau sur un échantillonnage de brique
prélevé après chaque cuisson. Cela pourra leur permettre
de s'assurer au moins de la constance de la qualité de leurs
produits.
Les analyses chimiques et minéralogiques de nos
échantillons pourraient rendre plus aisé l'interprétation
des résultats.
49
[1]

REFERENCES BIBLIOGRAPHIQUES
A. BOUQUILLON (2001)- Histoire des céramiques,
Matériaux et processus céramiques, Hermes Sciences, Paris,
47-72.
[2] D.RHODE (1986)- Terres et glaçures, DESSAIN
et TOLRA , Paris, 22- 31.
[3] P.BOCH (2001)- Composés céramiques,
Matériaux et processus céramiques, Hermes Science, Paris,
19- 46.
[4] E. KRAUSE (1973)- Principes et techniques de cuisson et
de construction de fours céramiques. Septima, Paris.
[5] J. SIGG (1991)- Les produits de terre cuites,
Septima, Paris.
[6] International Labour Office (1986)- Small-Scale
Brickmaking, Technology series, Geneva.
[7] C.A. JOUENNE (1984)- Traité de céramique
et matériaux, Septima, Paris.
[8] E. KRAUSE (1977)- Le séchage en céramique,
principes et techniques, Septima, Paris.
[9] G. ALIPRANDI (1979)- Matériaux
réfractaires et céramiques technique, Septima, Paris.
[10] E. LAMBERCY (1993)- Les matières
céramiques et leur transformation par le feu, Granit 1. Des
dossiers argiles.
[11] W.E. WORRALL (1986)- Clays and ceramic raw materials,
Second edition, Elsevier Applied Science Publishers, London and New York.
[12] A.K. CHAKRABORTY, K. GHOSHD (1978)- Reexamination of the
kaolinite- mullite reaction series, J. Am. Ceram. Soc.,61[3-4], 170-13.
[13] NGON NGON (2001)- Prospection et caractérisation
macroscopique des argiles alluviales pour l'industrie céramique à
Etoa, Actes 1ère conférence GCA, 123-128.
[14] E. KAMSEU (2002)- Projet de dimensionnement des
briques cuites: étude de la relation dimension des moules - retrait -
dimension des produits, MIPROMALO/PROG. CER et BTC.
[15] H. CHAMAYOU, J.P. LEGROS (1989)- Les bases physiques,
chimiques et minéralogiques de la science du sol, Presse
universitaire de France.
[16] A. DEMOLON, D. LEROUX (1952)- Guide pour l'étude
expérimentale du sol. 2e édition,
Gauthier-Villars - Paris.
50
[17] ENSP YAOUNDE (1999)- Analyse granulométrique
d'un sol fin, Travaux pratiques de géotechniques.
[18] LCPC (1970)- Analyse granulométrique par
sédimentométrie, Dunod, Paris.
[19] J. KARSTEN (2001)- additifs pour l'industrie des tuiles
et des brique, Industrie céramique et verrière - N°
970, 268 - 271.
[20] J. KARSTEN (2000)- Additive in the brick and tile
industry, NOVOKERAM, 25-39.
[21] M. VOUILLEMET (2001)- Maîtriser les produits
grâce à la modélisation des comportements des
mélanges, Industrie céramique et verrière , 964[11],
686 - 689.
[22] Dictionnaire Larousse de poche (1987).
[23] J. RIGAUD (1978)- La céramique de A à
Z, Septima, Paris.
[24] N F P18-554 (1979)- Mesures des masses volumiques,
porosités, coefficient d'absorption et teneur en eau des gravillons et
cailloux., AFNOR.
[25] N F P61-503 (1982)- Carreaux et dalles
céramiques - Détermination de la résistance à la
flexion., AFNOR.
[26] Handbook of Chemistry and Physics ,55TH ,
Edition 1974- 1975 CRC PRESS, E-106- E107.
[27] J.P BONNET, J.M GAILLARD (2001)- Céramique
silicatées, Matériaux et processus céramiques, Hermes
Science , Paris, 113- 140.
[28] A ELIMBI ,D NJOPWOUO , P PIALY, R WANDJI (2001)-
Propriétés des produits de cuisson de deux argiles
kaolinitiques de l'ouest Cameroun, Sil. Ind., 66 [11-12],121- 125.
[29] Y TSUZUKI , K NAGASAWA (1969)- Transitional stage to
the 980°C exotherm of kaolin minerals, Clays Sciences Japan,
3,8-102.
[30] J LEMAITRE, A.J LEONARD,B DELMON (1977)- The sequence
of phases in the 900- 1050°C tranformation of metakaolinite, Proc.
Int. Clay Conf. ,60 [1-2] 37-43
[31] B.A. SABRAH, H. El - DIDAMONY, M. M. El.- RABIECHI
(1989)- Ceramic studies of the clay / Rice composition and physical
properties of high dam lake sediments, Tile & Brick Int. Vol.12
N°1, 16-19.
[32] ] A. A. KHALIL, E. M. HAMAD, I. MOHAMED (1996)-
Effect of firing temperature on the phase composition and physical
properties of high dam lake sediments, Tile & Brick Int. 12 [1],
12-19.
[33] K. PIMPAKA, M WILHELM, W. WRUSS (2000)- A new Approach
to the production of bricks made of 100% fly ash, Tile & Brick Int, 16
[6], 428-433.
51
[34] V.T.L BOGAHAWATTA , A. B POOLE (1991)- Estimation of
the optimum firing condition for kaolinic clay bodies, Br Ceram Trans. J.
90, 52-96.
[35] C. MELO et al. (2001)- Effcet of fluxes on the fired
properties between 950 - 1050°C of some cameroonian clays. Actes
1ère conférence GCA, 57-69.
[36] T ROUXEL (2001)- Propriétés
mécaniques, Matériaux et processus céramiques, Hermes
Science, Paris, 19-74.
[37] W KURZ , J.P MERCIER , G ZAMBELLI (1991)- Introduction
à la science des matériaux, Presse polytechnique et
universitaire Romande.
[38] J.P.M Pavoy MBE, B.A, MICT (1979)- Brick making in
developing countries, Building research establishment, Garston, Waford.
[39] C. MELO, S. MONGET (2001)- Brick firing in a
Down-Draught wood fired kiln. Actes 1ère conference GCA, 49-56.
52
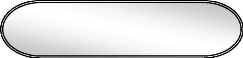
ANNEXES
53
CALCUL D'ERREURS
a) Limite de liquidité

WL = × 1 00
P P
h - s
P Tare
s -
ln(WL) = ln(Ph - Ps) - ln (Ps - Tare)
dWL =
|
d P P
( )
h S
- d P Tare
( S - )
-
|
WL ( P P
h S
-
|
(PS- Tare)
|
ÄWL = WL
ÄPh
Ph-PS
Ph-PS
Ph-PS
+ ÄPS + ÄPS +
ÄTare ÄPh Tare

Ph = ÄPs = ÄTare = ÄP
ÄWL = WL
|
3 ÄP
|
+ ÄP
|
P P
h S
-
|
|
|
|
P Tare
S -
|
Exemple de calcul:
WL = 40,08; Ph = 32,97g ; Tare = 1,25g ; Ps = 18,82g ; ÄP =
0,01g
ÄWL = 40,08 [ 3 2 1,

97-1
82-1
3 × 0,0 125 + 8 0,0 125 0 6
WL = 0,6 WL = 40,8 #177;0,6 b) Limite de
plasticité
ÄP
Wp
3 ÄP +
Ph-Ps

ÄWP = Ph--Ps
×1 00.
Ps-Tare
Ps-Tare
3 0,0 1
× 0,0 1
Exemple de calcul : ÄWP = 26,4 + = 0,49


9 ,67 7 ,9 1
- 7 ,9 1 1 ,25
-
WP = 26,4 #177; 0,5
c) Indice deplasticitéeIPp = WL---
WPdI P dW L dW P Ä I P Ä W
L Ä W P
ln IP = ln (WL - WP) = - = -pIPpW
W
L - P pWL-WP p IPpW W
L - P pWL-WPp
ÄIPp =IPp (L
Ä W L Ä W P
+ P )
54
W W
L - P W W
- pExemple de calcul: ÄIP = 14,4
40,06 6+ #177;0,499
=(40,08 - 26,4440,08 -26,40,44
IP = 14,4 #177; 0,4
d) Retrait linéaire
R = × 1 00
L L
o -
Lo
ln R = ln (Lo - L) -ln(Lo) + ln100
dL0 dL0 dL
R Lo- L L0 Lo-L Lo-L
L0
d( L o - L) dL0
dR = -
=
dR [ ] [ ]dL
1 1 1
= - dL 0 +
R L L L
o - 0 L L
ÄR
R
|
1 1
Lo - L L0
|
ÄL0
|
+
|
1
L0-L
|
ÄL
|
|
|
|
|
|
|
0 -
Exemple de calcul : ÄL0 = ÄL = 0,05cm ; L0 =
6,55cm ; L = 6,30cm ; R=3,81%
1
1
1
ÄR = 3,81
× 0,05+
0,05
×
6,5 5
6,5 5 -6,3 0
6,5 5 -6,3 0
R = 3,8 #177; 0,4% e) Perte au feu PF =
100
m m
0 ×
-
m0
Ln(PF) = ln (m0 - m) - ln(m0) + ln100
dPF
PF m0- m m0 m0- m m0- m
m0
d(m 0 - m)
dm 0 = dm0 dm
dm0
- -
dPF PF
|
[ 1 1 -
m0- m m0
|
] [ ]dm
1
dm 0 +
m m
0 -
|
1 1
1
ÄP F =
+ m0
Äm0
Äm
-
m 0- m m0
PF
m
Exemple de calcul: Äm0 = Äm = 0,1g m0 = 84,4 m =
76,9 PF = 8,9
ÄPF = 8,91
|
|
1
|
|
|
|
1
|
×
|
0, 1 +
|
|
1
|
|
|
|
×
|
0, 1
|
|
84,4 -7 6
|
,
|
9
|
|
84,4
|
|
84,4 -76
|
,
|
9
|
|
|
|
|
|
|
|
|
|
|
|
|
|
|
|
|
|
PF = 8,9 #177; 0,2%
f) Pourcentage d'absorption d'eau
ab = × 1 00
Ma Ms lnab = ln (Ma - Ms) - lnMs + ln100
-
Ms
Ä ab = ÄMa +
ÄMs + ÄMs or
ÄMa = ÄMS = ÄM
55
ab Ma- Ms Ma- Ms Ms
Äab = ab ( Ms )
2Ä M Ä M
+
Ma Ms
-
Exemple de calcul : Ms = 10,4932g Ma = 12,6957g M'a =
6,6325g
ab = 20,9897 ÄM = #177; 0,0001g
0, 0001 2
× 0, 0001
Äab = 20,9897 (1 2, 6957-1 0, 4932+ 1
0, 4932 0, 0021
ab = 20,989 #177; 0,002%
g) Masse volumique apparente
ñ = Ma-

s ñe = lnñ = lnMs -
ln(Ma - M'a) + lnñe
M
a
dñ = dMs dMa dMa
+ +0 car ñe = cste
ñ Ms Ma
-Ma Ma-Ma
dñ = dMs dMa +
dMa or, ÄM'a = 2ÄMa = 2ÄMs
= 2ÄM
D'où
ñ
M
s
M
a
-
M'
a
M a-Ma
ñ = ñ ( 1 + 3
Ms Ma-Ma
Exemple de calcul : ñ = 1,7306
Äñ = 1,7306 3 )
(1 0, 4932+ 1 2, 6957-6, 6325 <0, 0001=0, 0004
ñ = 1,7306 #177; 0,0004g/cm3
h) Résistance à la flexion
ä
3 FL 2 bh2
lnä = lnF + lnL - ln - 2lnh + ln 23
d ä = Ä F
+ÄL db 2dh

h
äF Lb
b
Ää = ä ( Ä F L Ä
2
h )
h
+ + Ä Ä +
F L b Exemple de calcul
ÄF = 5N Äb = Äh = ÄL = 0,002mm F = 922N
ä = 7,40Mpa h = 16,80mm
5 0,0 1 0,0 1 0,02
Ää = 7,40 + + + =0,052
56
922 55 3 6,40 1 6, 80 ä = 7,40 #177; 0,05 Mpa
|
|