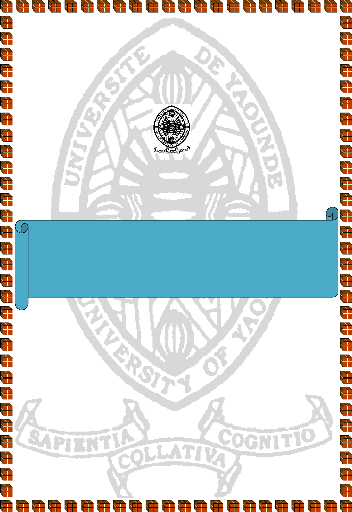
REPUBLIQUE DU CAMEROUN Paix - Travail -
Patrie REPUBLIC OF CAMEROON Peace - Work -
Fatherland
UNIVERSITE DE YAOUNDE I
THE UNIVERSITY OF YAOUNDE I
FACULTE DES SCIENCES
DEPARTEMENT DE CHIMIE INORGANIQUE
FACULTY OF SCIENCE
DEPARTMENT OF INORGANIC CHEMISTRY
LABORATOIRE DE PHYSICO-CHIMIE DES MATERIAUX
MINERAUX PHYSICO-CHEMISTRY OF MINERAL MATERIALS LABORATORY
RETICULATION GEOPOLYMERIQUE A BASSE
TEMPERATURE DE QUELQUES
ALUMINOSILICATES
MEMOIRE Présenté et soutenu en vue de
l'obtention du Diplôme d'Etudes Approfondies (D.E.A) en Chimie
Inorganique
Par LEMOUGNA NINLA Patrick
Maître en Chimie Mat :
01U481
Sous la Direction de : Dr. UPHIE CHINJE
MELO Chargée de Cours
Année académique 2007-2008

TABLE DES MATIERES
DEDICACES IV
REMERCIEMENTS V
LISTE DES FIGURES VII
LISTE DES TABLEAUX IX
LISTE DES ABREVIATIONS X
RESUME XI
ABSTRACT XII
INTRODUCTION 1
CHAPITRE I : GENERALITES SUR QUELQUES SILICATES NATURELS
ET LA GEOPOLYMERISATION 3
I-1 : LE SOL 4
I-1-1 : Les minéraux argileux, les latérites et
les pouzzolanes 5
I-1-1-1 : Les minéraux argileux 5
I-1-1-2 : Les latérites 7
I-1-1-3 : Les pouzzolanes 7
I-2 : LA STABILISATION DES SOLS 7
I-2-1 : La stabilisation mécanique 8
I-2-2 : La stabilisation physique 9
I-2-3 : La stabilisation chimique 9
I-2-3-1 : La stabilisation à la chaux 9
I-2-3-2 : La stabilisation au ciment 10
I-3 : LA GEOPOLYMERISATION 10
I-3-1 : Les Zéolites 11
I-3-2 : Les terminologies et l'historique des
géopolymères 12
I-3-3 : La réticulation géopolymérique
à basse température (L.T.G.S) 13
I-3-3-1 : La L.T.G.S et les matériaux de construction
15
I-3-3-2 : Le temps et l'énergie dans les
procédés L.T.G.S 15
I -3-4 : Les réactions de polycondensation 16
I-3-5 : l'influence de la nature des matières
premières sur le processus de géopolymérisation
18
I -3-5-1: L'influence de la nature des ions alcalins dans le
processus de géopolymérisation 19
I-3-5-2 : l'influence des ions calciums 20
I-3-5-3 : Les facteurs influençant la résistance
à la compression 20
I-4 : LES CIMENTS GEOPOLYMERES 21
CHAPITRE II : MATERIAUX ET METHODES EXPERIMENTALES
23
II-1 : LES MATERIAUX 24
II-1-1 : Les Matériaux Naturels 24
II-1-1-1 : L'argile sableuse de Nkolbisson 24
II-1-1-2 : La latérite d'Ekoumdoum 24
II-1-1-3 : La pouzzolane de Djoungo 24
II-1-2 : Les matériaux synthétiques 26
II-2 : LES METHODES DE CARACTERISATION DES MATIERES PREMIERES
27
II-2-1 : La caractérisation physique des
matériaux argileux 27
II-2-1-1 : L'analyse granulométrique par tamisage humide
27
II-2-1-2 : L'analyse granulométrique par
sédimentométrie 27
II-2-1-3 : La plasticité 29
II-2-2 : La composition chimique des matériaux
naturels 30
II-2-3 : L'analyse minéralogique des matériaux
31
II-2-4 : La granulométrie laser et la surface
spécifique des poudres d'aluminosilicates 31
II-3 : LA METHODE EXPERIMENTALE D'ELABORATION DES MATERIAUX
GEOPOLYMERES 31
II-3-1 : La préparation des matières
premières 31
II-3-2 : L'élaboration des formulations et le
façonnage des éprouvettes 32
II-3-3 : Le traitement thermique des différentes
formulations 32
II-4 : LA CARACTERISATION PHYSICO-CHIMIQUE DES PRODUITS OBTENUS
32
II-4-1 : Le pourcentage d'absorption d'eau et la masse
volumique apparente 32
II-4-2 : La résistance à la compression
33
II-4-3 : La Microstructure 34
CHAPITRE III : RESULTATS ET INTERPRETATION 35
III-1 : LA CARACTERISATION PHYSIQUE DES MATERIAUX ARGILEUX
36
III-1-1 : L'analyse granulométrique 36
III-1-2 : La plasticité 36
III-2: LA COMPOSITION CHIMIQUE DES MATERIAUX 37
III-3: L'ANALYSE MINERALOGIQUE DES MATERIAUX 38
III-4 : LA CARACTERISATION GRANULOMETRIQUE DES POUDRES
BROYEES 43
III-4-1 : Les surfaces spécifiques des poudres
utilisées 43
III-4-2 : La granulométrie laser des poudres
utilisées 43
III-5 : LES PROPRIETES PHYSIQUES DES PRODUITS OBTENUS
46
III-5-1 : Le pourcentage d'absorption d'eau et la masse volumique
apparente 47
III-5-2 : La résistance à la compression 53
III-5-3 : La Microstructure (MEB) 57
III-6 : DISCUSSION GENERALE 58
CONCLUSION ET PERSPECTIVES 61
ANNEXES 68

DEDICACES
Jcents dcentsdicents ccents n2moim fl mon IDO., Mr
isemoueNiti Pascal, Ma mO, mmo isemouelliti
ncentscents mitieuebourie J.DOLIiSrl, en tmoignag dcents
toutcents mon of fcentsction, Jcents vous suis tr0 meonnaissant pour W
saerifies n vous ava eonnntis pour moi.
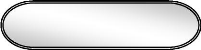
REMERCIEMENTS
Ce travail est le fruit d'une collaboration fructueuse entre
les hommes. Je remercie le tout puissant, le très miséricordieux
de sa grâce, sa protection sans lesquelles je n'aurais jamais pu
réaliser ce travail. Nous remercions aussi tous ceux qui de près
ou de loin y ont contribué. Il s'agit notamment de :
- Dr UPHIE CHINJE MELO, chargée de cours à
l'Université de Yaoundé 1 et Directeur de la Mission de Promotion
des Matériaux Locaux (MIPROMALO), pour le financement de ce travail par
la MIPROMALO. Son dynamisme et sa rigueur ont été pour moi une
source permanente d'encouragement. Ma profonde gratitude lui est
également acquise pour avoir dirigé ce travail;
- Pr Daniel NJOPWOUO, Chef du Département de Chimie
Inorganique et Chef du laboratoire de physico-chimie des matériaux
minéraux, pour m'avoir accepté dans son laboratoire, pour ses
conseils et ses encouragements;
- Pr BELOMBE, pour ses conseils, et ses multiples encouragements
;
- Dr Antoine ELIMBI pour ses conseils, sa disponibilité et
ses encouragements ; - Dr DJOUFACK, pour ses conseils, et ses encouragements
;
- Tous les enseignants du Département de Chimie
Inorganique, pour la formation qu'ils nous ont donnée.
Nos remerciements vont également à :
- Mr KAMSEU, pour l'aide à la réalisation des
analyses, la facilitation de l'accès à la documentation et ses
multiples encouragements.
- Mr BILLONG, pour la facilitation de l'accès à la
documentation et ses multiples encouragements.
- Mr BALO, pour la facilitation de l'accès à la
documentation et ses encouragements. - Dr NJOYA André, pour ses conseils
et la facilitation de l'accès à la documentation.
Nos remerciements vont enfin à :
- Mr TCHAPTCHET, Mr NZEUKOU, Mr TENE, Mr TCHAMBA, Mr SUILABAYU,
Mr KEMMEUGNI pour leur soutien moral ;
- Mes aînés de laboratoire, Dr FOTIO et Dr NJOYA
DAÚROU, pour leur soutien moral; - Mes camarades de
promotion, pour l'ambiance conviviale et fraternelle;
- Toute ma famille, mes frères et amis (GUEMETA Jean
Bernard, TCHIFFO Stéphane, HAROUNA MASSAï, ABDOUL RAHMAN, AMOUD
Jean- Jacques), pour leur soutien moral ;
- Les membres du jury, pour leur contribution à
l'amélioration de ce travail.
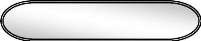
LISTE DES FIGURES
Figure 1 : Eléments structuraux des minéraux
argileux [6]. 5
Figure 2: Structure de la kaolinite (minéral argileux type
1/1) 6
Figure 3: Structure du réseau de Na-poly(sialate) et du
zéolite A [3] 11
Figure 4: Types de poly(sialates) [21]. 12
Figure 5 : Polycondensation du quartz silanol Si-OH avec les
poly(sialates) [21]. 14
Figure 6: Résistance à la compression en MPa d'un
sol kaolinitique non traité et traité par L.T.G.S 14
Figure 7 : Energies et temps de production des céramiques
traditionnelles et céramiques L.T.G.S [24].
15
Figure 8: Modèle conceptuel explicitant la structure des
géopolymères [27]. 18
Figure 9: Processus de prise du ciment géopolymère
potassium poly(sialate-siloxo)[23] 21
Figure 10 : Carte de localisation des zones de
prélèvement des échantillons de la ville de Yaoundé
25
Figure 11 : Courbes granulométriques des matériaux
LE et AN. 36
Figure 12: Diffractogramme de rayons X de l'argile Nkolbisson,
calcinéé et non calcinéé 39
Figure 13: Diffractogramme de rayons X de la latérite
d'Ekoumdoum, calcinée et non calcinée 40
Figure 14: Diffractogramme de rayons X de la pouzzolane de
Djoungo, calcinée et non calcinée 41
Figure 15 : Granulométrie laser du matériau AN
43
Figure 16 : Granulométrie laser du matériau AN
calciné à 700 °C 44
Figure 17 : Granulométrie laser du matériau LE
44
Figure 18: Granulométrie laser du matériau LE
calciné à 700 °C 44
Figure 19: Granulométrie laser du matériau PD 45
Figure 20: Granulométrie laser du matériau PD
calciné à 700 °C 45
Figure 21 : Efflorescences observées sur les
matériaux AN à 10% de R, juste avant traitement 47
Figure 22 : Pourcentage d'absorption d'eau des
géopolymères obtenus à base de AN 48
Figure 23 : Masse volumique apparente des
géopolymères obtenus à base de AN 48
Figure 24: Pourcentage d'absorption d'eau des
géopolymères obtenus à base de LE 49
Figure 25 : Masse volumique apparente des
géopolymères obtenus à base de LE 50
Figure 26 : Pourcentage d'absorption d'eau des
géopolymères obtenus à base de PD 51
Figure 27 : Masse volumique apparente des
géopolymères obtenus à base de PD 51
Figure 28 : Pourcentage d'absorption d'eau des
géopolymères obtenus à base de PD 700°C 52
Figure 29 : Masse volumique apparente des
géopolymères obtenus à base de PD 700°C 52
Figure 30: Résistance à la compression des
géopolymères obtenus à base de AN 53
Figure 31: Résistance à la compression des
géopolymères obtenus à base de LE 54
Figure 32: Résistance à la compression des
géopolymères obtenus à base de PD 55
Figure 33: Résistance à la compression des
géopolymères obtenus à base de PD 700°C 56
Figure 34 : Microstructure des géopolymères obtenus
à partir de AN à 10% R et traité à 450°C 57
Figure 35 : Microstructure des géopolymères obtenus
à partir de LE à 10% R et traité à 450°C 57
Figure 36: Microstructure des géopolymères obtenus
à partir de PD 700 °C à 10% R et traité 450°C
57
Figure 37: Schéma de la polycondensation hydrothermale de
Na- poly(syalate)[3]. 59
Figure 38 : Structure de l'anorthite 59
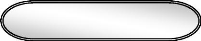
LISTE DES TABLEAUX
Tableau 1 : Pourcentages comparatifs en poids et volume des
éléments présents dans les 20 premiers
Km de l'épaisseur terrestre 4
Tableau 2: Classification des minéraux argileux 6
Tableau 3: Localisation géographique des sites de
prélèvement des matériaux étudiés 25
Tableau 4: Caractéristiques physicochimiques du silicate
de sodium utilisé 26
Tableau 5 : Résultats du test de plasticité des
matériaux LE et AN. 37
Tableau 6 : Analyse chimique des matériaux LE, AN et PD.
37
Tableau 7 : Surface spécifique des matériaux LE, AN
et PD. 43
Tableau 8 : Analyse granulométrique par tamisage humide de
AN 69
Tableau 9 : Analyse granulométrique par tamisage humide de
LE 69
Tableau 10 : Analyse granulométrique par
sédimentométrie de AN 69
Tableau 11 : Analyse granulométrique par
sédimentométrie de LE 70
Tableau 12 : Pourcentage d'absorption d'eau des
géopolymères obtenus à base de AN 70
Tableau 13 : Masses volumiques apparentes des
géopolymères obtenus à base de AN 70
Tableau 14 : Résistances à la compression des
géopolymères obtenus à base de AN 71
Tableau 15 : Pourcentage d'absorption d'eau des
géopolymères obtenus à base de LE 71
Tableau 16 : Masses volumiques apparentes des
géopolymères obtenus à base de LE 71
Tableau 17 : Résistances à la compression des
géopolymères obtenus à base de LE 71
Tableau 18 : Pourcentage d'absorption d'eau des
géopolymères obtenus à base de PD 72
Tableau 19 : Masses volumiques apparentes des
géopolymères obtenus à base de PD 72
Tableau 20 : Résistances à la compression des
géopolymères obtenus à base de PD 72
Tableau 21 : Pourcentage d'absorption d'eau des
géopolymères obtenus à base de PD 700 °C 72
Tableau 22 : Masses volumiques apparentes des
géopolymères obtenus à base de PD 700°C 72
Tableau 23 : Résistances à la compression des
géopolymères obtenus à base de PD 700 °C 73
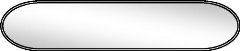
LISTE DES ABREVIATIONS
AN: Argile de Nkolbisson
AN 700°C: Argile de Nkolbisson calcinée à
700°C
A.S.T.M: American Society for Testing Materials
CAH : Calcium Alumino Hydrate
CASH: Calcium Alumino Silicate Hydrate
CSH: Calcium Silicate Hydrate
ICP-AES: Inductive Coupled Plasma by Atomic Emission Spectrometry
LE: Latérite d'Ekoumdoum
LE 700°C: Latérite d'Ekoumdoum calcinée
à 700°C
LFP: lime fixation point
L.T.G.S: Low Temperature Geopolymeric Setting
MPa: Mega Pascal
PCDS: Polycyclodisialate PD: Pouzzolane de Djoungo
PD 700°C: Pouzzolane de Djoungo calcinée à
700°C
PS: Poly(sialate)
PSDS: Poly(sialate-disiloxo) PSS: Poly(sialate-siloxo) PVC:
Polyvinyl Chloride
R : Réactif géopolymère

RESUME
Le but de ce travail est de pouvoir explorer les
possibilités de synthèse des matériaux de construction
géopolymères à partir de certaines matières
premières aluminosilicates disponibles au Cameroun. L'analyse chimique
des trois types de matières premières aluminosilicates (argile de
Nkolbisson (AN), latérite d'Ekoumdoum (LE) et pouzzolane de Djoungo
(PD)) ayant fait l'objet de notre étude a montré que leurs
rapports SiO2 /Al2O3 sont égales à 5,25 ; 2,54 ; et 5,52
respectivement. Les minéraux aluminosilicates sont respectivement la
kaolinite dans AN et LE, l'anorthite et le plagioclase dans PD.
Afin d'évaluer l'influence de l'amorphisation sur le
degré de réactivité de nos matières
premières aluminosilicates, des échantillons de matériaux
AN, LE, et PD a été calcinée à 700 °C pendant
6 heures. Les différentes formulations pour la synthèse des
matériaux géopolymères ont été
réalisées en faisant varier la teneur en réactif
géopolymère de 0 à 10%, à intervalle de 2%, par
rapport aux masses de poudres sèches pour les matériaux AN et LE.
Pour le matériau PD, les teneurs en réactif
géopolymère ont été respectivement 0, 2, 6 et
10%.
Les éprouvettes façonnées de chaque
formulation ont ensuite été traitées thermiquement
à 250°C, 350°C, et 450°C pendant 5 heures pour chaque
température d'étude.
Les résultats obtenues montrent que les
matériaux AN et LE calcinés ne se consolident pas dans nos
conditions de travail (plage de température de traitement thermique et
plage de concentration du réactif géopolymère). Les
matériaux AN, LE, (non calcinés), et PD (calciné ou non),
réagissent bien dans nos conditions de travail et pourraient être
utilisés comme matériaux de construction. La détermination
de leurs propriétés physiques montre les masses volumiques
apparentes sont comprises entre 1,59 et 1,9 g/cm3 ; les pourcentages
d'absorption d'eau sont compris entre 9 et 26,6% ; les résistances
maximales à la compression sont comprises entre 9,55 et 29,7 MPa.
Les masses volumiques apparentes et les résistances
à la compression croissent avec l'augmentation de la teneur en
réactif géopolymère alors que le pourcentage d'absorption
d'eau décroit. La résistance à la compression croît
avec l'augmentation du rapport SiO2/Al2O3 de nos matières
premières aluminosilicates.
La microstructure des matériaux fait état d'une
phase homogène pour les géopolymères à base de AN
et LE, et d'une phase hétérogène, plus microporeuse, pour
les géopolymères à base de PD.
Mots clés : aluminosilicates,
géopolymères, matériaux, traitement thermique,
propriétés physiques.
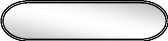
ABSTRACT
The aim of this study is to explore possibilities of the
synthesis of geopolymer construction materials from some aluminosilicate raw
materials available in Cameroon. The chemical analyses of the three samples
under study (clay from Nkolbisson (AN), laterite from Ekoumdoum (LE) and
Pouzzolana from Djoungo (PD)) have revealed that the ratio of SiO2/Al2O3 are
respectively 5.25, 2.54, and 5.52. The aluminosilicates compounds are
respectively kaolinite in AN and LE, anorthite and plagioclase in PD.
Samples (AN, LE and PD) was calcinated at 700°C for 6
hours in order to study the influence of amorphisation on the raw materials'
reactivity. The various formulations were realised by varying the geopolymer
reagent between 0 to 10%, at 2% interval, with respect to the powders' dry
masses for samples AN and LE. For sample PD, the proportions of the geopolymer
reagent were 0, 2, 6 and 10%.
The moulded samples for each formulation were later on
subjected to a thermal treatment at 250, 350 and 450°C for 5 hours.
The obtained results reveal that calcinated samples AN and LE
do not consolidate in our working conditions (thermal treatment temperature
range and geopolymer reagent concentration range). Samples AN, LE and PD
(calcinated or not) react well in our working conditions and can be used for
construction purposes. The investigation of their physical properties shows
that values of bulk density vary between 1.59 and 1.90 g/cm3, those
of water absorption between 9 and 26,6%, and the maximum values of compressive
strength between 9,55 and 29,7 MPa. The bulk density and compressive strength
increase with an increase in geopolymer reagent content meanwhile water
absorption decreases. The compressive strength increases with an increase in
the SiO2/Al2O3 ratio of the raw materials.
The microstructure of the geopolymers reveals a homogenous
phase in AN and LE, and a heterogenous and more porous (micro) phase for PD.
Key words: aluminosilicates, geopolymers,
materials, thermal treatment, physical properties.
INTRODUCTION
Depuis plus de cent cinquante ans, l'objectif de la science
chimique était la compréhension et la réplication des
différents matériaux caractérisant le règne animal
et le règne végétal. Cette recherche biochimique a abouti
à la création des matières plastiques, des fibres
synthétiques, de la biochimie, et de la médecine moderne [1].
Cependant, ce n'est que depuis 1970 que les sciences chimiques,
minéralogiques, géologiques sont parvenues à
élaborer des matériaux pouvant répliquer le règne
minéral. Il est actuellement possible de synthétiser en
laboratoire pratiquement tous les types de matériaux
minéralogiques, mais les résultats les plus spectaculaires sont
obtenus avec les géopolymères de type aluminosilicate ou
polysialate [1,2]. Introduit pour la première fois en 1978 par le
professeur Joseph Davidovits [3], le terme géopolymère
désigne les polymères inorganiques de structure
tridimensionnelle formés à basse
température par polycondensation des aluminosilicates [2-5]. Dès
lors, les propriétés chimiques et physiques intéressantes
de ces matériaux suscitèrent l'intérêt de la
communauté scientifique, et les activités de recherche y
afférentes permirent de développer de nombreuses applications. A
nos jours, les géopolymères sont utilisés dans
l'ingénierie aéronautique, l'industrie nucléaire, la
reproduction d'objets d'art, les matériaux de construction, l'isolation
thermique des fours, etc. [2-4]. Les matériaux
géopolymères utilisés dans la construction
présentent d'excellentes propriétés mécaniques et
thermiques.
Au Cameroun, malgré la grande disponibilité des
matières premières adéquates pour la synthèse des
matériaux géopolymères, les avantages de cette technologie
demeurent encore très peu exploités. Le secteur des
matériaux de construction reste dominé par des matériaux
importés dont les prix ne cessent de croître. Si nous prenons
l'exemple du ciment, son prix s'est accru de près de 51% ces onze
dernières années. Cette évolution vertigineuse des prix,
entretenue par une pauvreté du tissu industriel d'entreprises produisant
les matériaux de construction, rend difficile l'accès à
l'habitat à une grande fraction de la population à revenus
limités. Le développement des matériaux de construction
géopolymères, dont les procédés de synthèse
ont l'avantage d'être écologiques, avec une faible production des
gaz à effet de serre par rapport aux matériaux de construction
conventionnels localement produits, pourrait contribuer de façon
significative à l'accroissement d'offre en matériaux de
construction sur le marché camerounais. Ces matériaux, moins
énergétivores que les briques cuites et les
ciments pouzzolaniques, pourraient se synthétiser par
des procédés chimiques à partir des terres d'argiles
latéritiques très disponibles sur l'étendue du
territoire.
La maîtrise de ces procédés constitue
à l'heure actuelle un des axes prioritaires de recherche dans plusieurs
laboratoires dont celui de physico-chimie des matériaux minéraux
de la Faculté des Sciences de l'Université de Yaoundé I et
celui d'analyse des matériaux de la Mission de Promotion des
Matériaux Locaux (MIPROMALO).
L'objectif de cette étude est de pouvoir étudier
les paramètres de formulation des produits de construction
géopolymères à base de matières premières
aluminosilicates disponibles.
Notre rapport d'étude s'articule en trois chapitres :
- le chapitre I présente les
généralités sur quelques silicates naturels, la
géopolymérisation, et les paramètres pouvant influencer
les propriétés physiques et mécaniques des produits
géopolymères;
- les caractéristiques sur les matériaux
étudiés ainsi que les méthodes expérimentales
utilisées constituent le chapitre II ;
- dans le troisième chapitre, nous présenterons les
résultats obtenus et proposerons une interprétation.
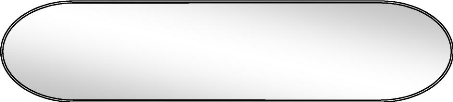
GENERALITES SUR QUELQUES SILICATES NATURELS ET
LA GEOPOLYMERISATION
CHAPITRE I :
I-1 : LE SOL
Le sol est la fraction solide de la sphère terrestre. A la
surface du sol, la terre est un matériau meuble, d'épaisseur
variable, qui supporte les êtres vivants, leurs ouvrages, et
oüpoussent les végétaux. Elle résulte de
la transformation de la roche mère sous-jacente sous
l'influence de divers processus physiques, chimiques,
biologiques, liés aux conditions bioclimatiques et à la vie
animale et végétale [6]. Le matériau terre est
constitué de plusieurs éléments :
- les constituants gazeux : principalement l'air ;
- les constituants liquides : principalement l'eau ;
- les constituants solides : la matière minérale et
organique.
La composition chimique moyenne ainsi que les pourcentages
comparatifs en poids et en volume des éléments présents
dans les 20 premiers km d'épaisseur de la croûte terrestre sont
consignés dans le tableau 1.
Tableau 1 : Pourcentages comparatifs en
poids et volume des éléments présents dans les 20 premiers
km de l'épaisseur terrestre [6].
Oxydes
|
% en poids
|
Eléments
|
% en poids
|
% en volume
|
Rayon
|
|
des oxydes
|
|
des éléments
|
des éléments
|
ionique en ?
|
|
|
O
|
46,7
|
92
|
1,3
|
SiO2
|
59,0
|
Si
|
27,7
|
0,8
|
0,4
|
Al2O3
|
15,5
|
Al
|
8,1
|
0,8
|
0,6
|
Fe2O3
|
7,0
|
Fe
|
5,1
|
0,7
|
0,7
|
CaO
|
5,0
|
Ca
|
3,6
|
1,6
|
1,0
|
Na2O
|
4,0
|
Na
|
2,7
|
1,5
|
1,0
|
K2O
|
3,0
|
K
|
2,6
|
2,1
|
1,3
|
MgO
|
3,5
|
Mg
|
2,1
|
0,6
|
0,8
|
TiO2
|
1,0
|
Ti
|
0,5
|
0,1
|
0,6
|
L'écorce terrestre, de composition chimique riche en
silice et alumine, constitue par conséquent une source importante de
matières premières aluminosilicates disponibles pour les
réactions de géopolymérisation.
I-1-1 : Les minéraux argileux, les
latérites et les pouzzolanes I-1-1-1 : Les minéraux
argileux
Les minéraux argileux sont les silicates
hydratés d'aluminium plus ou moins complexes, principalement sous forme
de fines lamelles (phyllosilicates) [6,7]. Pour la construction de ces
minéraux, la nature a fait appel à deux types de moellons : le
tétraèdre, constitué d'un silicium entouré de
quatre oxygènes (coordination 4), et l'octaèdre, ayant un atome
d'aluminium (de magnésium ou de fer) entouré de six
oxygènes (coordination 6) [6].
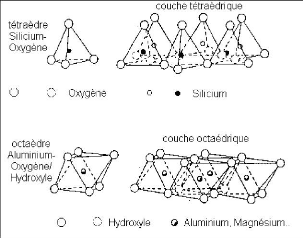
Figure 1 : Eléments structuraux des
minéraux argileux [6].
La distance inter-réticulaire (d) sépare 2
feuillets successifs. Les substitutions d'atomes sont fréquentes dans
les feuillets et l'édifice cristallin peut être
désorganisé. D'après la structure du feuillet, on
distingue principalement les argiles 1/1 (1 couche tétraédrique
et 1 couche octaédrique), les argiles 2/1 (2 couches
tétraédriques et 1 couche octaédrique), et les argiles
2/1/1 (deux couches tétraédriques et deux couches
octaédriques) [7,8]. Le sol camerounais regorge de nombreux gisements
d'argiles non exploités. L'on note toutefois quelques utilisations des
matériaux argileux camerounais dans la production des briques cuites et
poteries. La figure 2 et le tableau 2 présentent respectivement la
structure d'un minéral argileux de type 1/1 et la classification des
minéraux argileux.
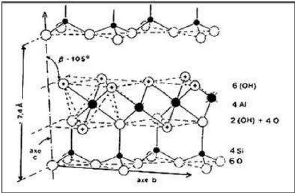
Figure 2: Structure de la kaolinite
(minéral argileux type 1/1)
Tableau 2: Classification des
minéraux argileux (le premier chiffre désignant le nombre de
couches tétraédriques, le second et le troisième, celui
des couches octaédriques (dioctaédrique ou trioctaédrique)
[8].
Type Groupe Sous-groupe Especes
Formules
1/1
|
Kaolinite
|
Kaolinite Dickite
Nacrite Kaolinite Métahalloysite Halloysite
|
Si2O5Al2(OH)4 Si2O5Al2(OH)4 Si2O5Al2(OH)4 Si2O5Al2(OH)4
Si2O5Al2(OH)4 4H2O
|
Serpentine Anti gorite Si2O5M g3(OH)4
Talc Pyrophyllite Pyrophyllite Si4O10Al2(OH)2
Talc Talc Si4O1oM g3(OH)2
2/1
|
Smectite Smectite
dioctaedrique
|
Montmorillonite Si4O1o(Al1,67M go,33)(OH)2
|
|
|
Smectite trioctaedrique
|
Saponite (Si3,67Alo,33)O10M g3 (OH)2
|
Vermi Vermiculite Vermiculite
(Si,Al)4O1o(Al,Fe · · ·)2(OH)2
culite dioctaédrique dioctaèdrique
Vermiculite Vermiculite (Si,Al)4O10(M
g,Fe · · ·)2(OH)2
trioctaedrique
Micas Micas Muscovite K(Si3Al)O10Al2(OH)2
dioctaedrique
Micas Phlo gopite K(Si3Al)O1oM g3(OH)2
trioctaedrique
2/1/1 Chlorite Chlorite dioctaedrique Sudoite
(Si,Al)4O10Al4(OH)8
Chlorite trioctaedrique Espèces différentes
(Si,Al)4O10(M g,Fe · · ·)6(OH)8
I-1-1-2 : Les latérites
Les latérites sont des terres très
altérées, qui contiennent des proportions importantes mais
très variables d'oxydes de fer et d'aluminium, ainsi que du quartz et
d'autres minéraux. On les trouve abondamment dans la ceinture tropicale
et subtropicale, généralement juste en dessous de la surface des
immenses plaines ou clairières, dans des régions à
précipitation importante. Leur caractéristique d'ameublissement
naturel varie du conglomérat compact à la terre friable. La
couleur est très variable : ocre, rouge, brune, violette et noire. Le
matériau est facile à découper, et il durcit très
vite à l'air et devient assez résistant aux agents
météorologiques [9]. Le sol Camerounais est très riche en
cuirasses latéritiques. Ces latérites sont fréquemment
utilisées dans les travaux routiers ou dans la production des
matériaux de construction (adobes, brique de terre
comprimée...).
I-1-1-3 : Les pouzzolanes
Les pouzzolanes sont des matériaux naturels ou
artificiels riches en silice et en alumine, pouvant réagir avec la chaux
en présence de l'eau pour former des produits manifestant des
propriétés liantes [10,11]. Elles sont employées en
cimenterie pour leurs propriétés pouzzolaniques (aptitude
à fixer la chaux à la température ambiante et à
former des composés ayant des propriétés hydrauliques)
[10]. Les principales pouzzolanes sont les matériaux volcaniques
(cendres, scories...), les cendres des centrales thermiques, les laitiers de
hauts fourneaux, les cendres des balles de riz, la bagasse des cannes à
sucre, et l'argile calcinée [11]. Il existe au Cameroun plusieurs
gisements de pouzzolanes volcaniques, notamment autour du Mont Manengouba, du
Mont Cameroun, dans les régions de Foumbot, Djoungo, Kumba, et les
plateaux de l'Adamaoua [12]. Une partie de cette pouzzolane est parfois
utilisée dans les travaux d'aménagements routiers, ou comme
additif dans la production du ciment et les mortiers de béton.
I-2 : LA STABILISATION DES SOLS
Stabiliser la terre c'est modifier les
propriétés d'un système terre-eau-air pour obtenir des
propriétés permanentes compatibles avec une application
particulière [9]. Cela implique des changements affectant directement
les interactions terre, eau et air dans le sol et
permettant d'obtenir des propriétés permanentes qui
rendent le sol apte à diverses sollicitations telles que la construction
[13-17].
Il est possible de modifier deux principales
caractéristiques d'un sol : la texture et la structure. Ces changements
affectent les propriétés du sol telles que la porosité, la
perméabilité et la résistance mécanique [9,13]. Les
objectifs visés par ces modifications sont :
· la réduction de la porosité et la tendance
du sol au gonflement et à la fissuration ;
· l'obtention d'une meilleure cohésion ;
· l'amélioration de la résistance à
l'érosion (création des liens ou amélioration des liaisons
existantes entre les particules afin d'obtenir une résistance
mécanique plus importante) ;
· l'amélioration de la force de compression humide
et sèche, la force de traction et de cisaillement.
La stabilisation est un processus très complexe
à cause de nombreux paramètres qui entrent en jeu. Une
connaissance des propriétés du sol permet de mieux envisager les
modifications, les études économiques (coût et
délais), ainsi que les techniques de production et de construction
à utiliser.
On dénombre trois procédés de
stabilisation : mécanique, physique et chimique.
I-2-1 : La stabilisation mécanique
Elle consiste au compactage de la terre qui modifie sa
résistance mécanique, sa compressibilité, sa
perméabilité et sa porosité. Le sol est
mécaniquement traité de sorte qu'un maximum d'air puisse
être éliminé, ce qui contribue à une augmentation de
sa densité. Dans la stabilisation mécanique, la distribution
granulométrique des particules constitutives du matériau n'est
pas affectée, mais sa structure est changée, car les particules
sont redistribuées [9,13]. La stabilisation mécanique est
très utilisée en construction routière et nécessite
une analyse préalable du sol afin de déterminer la teneur optimal
en eau pour une meilleure compressibilité du sol.
I-2-2 : La stabilisation physique
Elle consiste à modifier les propriétés
d'une terre en intervenant sur sa texture : mélange
contrôlé de la fraction de grains différents, traitement
thermique (déshydratation ou gel), traitement électrique
(électro-osmose qui favorise un drainage de la terre), etc. [9,13]. La
stabilisation physique peut également consister à l'introduction
des fibres végétales, animales, minérales ou
synthétiques dans une terre. Ce procédé est utilisé
lorsqu'il y a des raisons de ne pas agir sur la distribution
granulométrique, ou si le matériau est sensible aux mouvements
induits par des causes telles que l'action de l'eau, l'expansion thermique,
etc. Ces mouvements peuvent alors être contrecarrés par une
armature faite de fibres. L'armature agit au niveau macroscopique (sur
l'agrégation des grains), et non au niveau des grains individuels
[9].
I-2-3 : La stabilisation chimique
Elle consiste à ajouter à la terre d'autres
matériaux ou produits chimiques qui modifient ses
propriétés, soit du fait d'une réaction physico-chimique
entre les particules et le matériau ou le produit ajouté, soit en
créant une matrice qui lie ou enrobe les particules. La réaction
physico-chimique peut entraîner la formation d'un nouveau matériau
: composé pouzzolanique issu d'une réaction entre l'argile et la
chaux par exemple [9]. Les ajouts les plus utilisés pour la
stabilisation des sols sont le ciment, la chaux et le mélange
ciment/chaux [14].
I-2-3-1 : La stabilisation à la chaux
Suite à l'introduction de la chaux dans une terre pour
stabilisation, les ions Ca2+ sont en partie adsorbés à
la surface des particules argileuses en remplacement des cations monovalents
comme Na+ et K+ [14]. La quantité de
Ca2+ adsorbée dépend de la capacité
d'échange cationique du sol traité. Plus la capacité
d'échange est élevée, plus le sol adsorbe de
Ca2+. En fait, tous les cations adsorbés ne sont plus
disponibles pour les réactions pouzzolaniques. La quantité de
chaux nécessaire pour satisfaire l'affinité du sol pour la chaux
est appelée "lime fixation point" (LFP). La chaux en excès du LFP
est celle qui participe au processus de cimentation. Les réactions entre
cette chaux, la silice et l'alumine libres, concourant à la formation de
nouveaux minéraux comme des CSH (silicates de calcium
hydratés), des CAH (aluminates de calcium
hydratés) et des CASH (alumino-silicates de calcium hydratés)
sont principalement responsables de la consolidation. Ces réactions sont
plus ou moins lentes, et sont fonction de divers facteurs comme la
minéralogie, la granulométrie du sol traité, ainsi que le
temps et la température de curage [14].
I-2-3-2 : La stabilisation au ciment
La principale réaction dans un mélange sol
/ciment provient de l'hydratation des deux silicates anhydres de calcium, 3CaO.
SiO2 (C3S) et 2CaO. Si02 (C2S), constituants majeurs du ciment, qui forment
deux nouveaux composés : l'hydroxyde de calcium (chaux hydratée
appelée Portlandite) et le silicate de calcium hydraté (CSH)
principal agent liant du béton [14, 18].
La réaction est la suivante (équation I.1):
ciment + H20 ? CSH + Ca(OH)2 ( I.1)
Contrairement à la chaux, la minéralogie et la
granulométrie des sols traités au ciment influencent peu les
réactions puisque la poudre de ciment contient en elle-même tout
ce dont elle a besoin pour réagir et former des produits cimentaires. Le
ciment va créer des liens physiques entre les particules augmentant
ainsi la résistance des sols comparativement à la chaux qui a
besoin de silice et d'alumine provenant des particules argileuses pour
développer les réactions pouzzolaniques [14, 15].
Généralement, les réactions d'hydratation
des ciments sont plus rapides que celles de la chaux, mais dans les deux cas,
la résistance finale résulte de la formation de silicates de
calcium hydratés (CSH) [15].
I-3 : LA GEOPOLYMERISATION
Avant de parler des géopolymères, il est
nécessaire de présenter brièvement les zéolites,
étant donné que ces derniers sont synthétisés par
un procédé analogue à celui de la
géopolymérisation. Certains auteurs [19] ont
suggéré que les gels de géopolymère soient les
précurseurs amorphes de cristaux de zéolite. Bien que les
géopolymères soient des gels d'aluminosilicate par
définition, la structure macromoléculaire des
géopolymères ressemble au réseau cristallin de divers
zéolites [19].
I-3-1 : Les Zéolites
Les zéolites sont des aluminosilicates de structure
tridimensionnelle formés de polymères inorganiques
constitués de (Si, Al)O4 tétra coordonnés par le partage
de tous leurs atomes d'oxygène dans le réseau. La
stoechiométrie des zéolites peut être
représentée par la formule générale [20]:
M
n + 1 n [(AlO2)(SiO2)x]-
z H2O, où x représente le rapport molaire Si/Al, z le nombre de
molécules d'eau liées
physiquement. Les cations tels que H+,
Na+, K+, Cu+ et Fe(OH)+, (ici de
valence n=1) sont nécessaires pour la compensation des charges. Les
zéolites existent à l'état naturel, mais peuvent aussi
être synthétisés par voie hydrothermale à partir des
solutions alcalines de silicate de sodium, hydroxyde d'aluminium.
La synthèse des zéolites de type A par exemple est
obtenue par traitement hydrothermal de la kaolinite en solution alcaline
à 100°C suivant la réaction [20] :
100°C
Al2O3.2SiO2.2H2O + 2NaOH Na2O.Al2O3.2SiO2 + 3H2O (I.2)
Kaolinite Zéolite A
Cette méthodologie de synthèse peut
également être utilisé dans la synthèse des
géopolymères, cependant, pour la géopolymerisation le
rapport liquide/ phase solide est plus petit [20]. L'unité structurale
des zéolites A est identique à celle du Na-poly(sialate). Mais,
le zéolite A provient de la polycondensation d'un
cyclo-tétrasialate alors que le Na-poly(sialate) provient de la
polycondensation d'un cyclo-disialate [3].
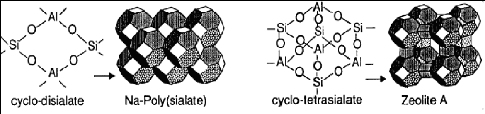
Figure 3: Structure du réseau de
Na-poly(sialate) et du zéolite A [3]
I-3-2 : Les terminologies et l'historique des
géopolymères
Les géopolymères, selon J. Davidovits [21] ont
été développés dans la recherche des
polymères inorganiques résistants à la chaleur et non
combustibles, après de nombreux incendies favorisés par
l'inflammabilité des matériaux plastiques en France entre 1970 et
1973.
La famille des géopolymères
synthétisés à partir d'aluminosilicates est appelée
poly(sialate). Elle est constituée d'un réseau amorphe de SiO4 et
AlO4, où le silicium et l'aluminium ont une coordinance IV, avec le
partage de tous leurs oxygènes [22 ,23]. Sialate est
l'abréviation de silico-oxo-aluminate (-Si-O-Al-O-). La présence
de cations tels que Na+, K+, Li+,
Ca2+... dans le réseau est nécessaire pour
l'équilibration des charges négatives de Al3+ en
coordination IV avec les oxygènes [21]. La formule empirique des
poly(sialates) est la suivante [22 ,23] :
Mn[(-SiO2)z-AlO2]n w H2O
où z=1, 2, ou 3. M est un cation monovalent tel que
K+ ou Na+, n le degré de polycondensation et w le
nombre de molécules d'eau liées physiquement.
Les géopolymères comprennent trois classes de
polymères inorganiques, selon le ratio (R) SiO2/Al2O3 dans
l'unité monomère [22 ,23] :
- poly(sialate), PS, dont l'unité monomère est
(-Si-O-Al-O-), avec R=2 ;
- poly(sialate-siloxo), PSS, dont l'unité monomère
est (-Si-O-Al-O-Si-O-), avec R=4 ;
- poly(sialate-disiloxo), PSDS, dont l'unité
monomère est (-Si-O-Al-O-Si-O-Si-O-), avec R=6.
Les structures des différents types de poly(sialates)
selon Davidovits [21] sont présentées sur la figure 4.
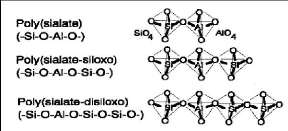
Figure 4: Types de poly(sialates)
[21].
Les poly(sialates) et poly(sialates-siloxo)
cristallisés peuvent s'obtenir dans les conditions hydrothermales de
curage, alors que le curage à température ambiante induit des
matrices amorphes ou vitreuses [21]. En utilisant la kaolinite comme
précurseur géopolymérique, la polycondensation
hydrothermale à 150°C aboutirait à une sodalite bien
cristallisée [3].
I-3-3 : La réticulation
géopolymérique à basse température (L.T.G.S)
La réticulation géopolymérique à
basse température encore appelé « Low Temperature
Geopolymeric Setting » (L.T.G.S), est un procédé de
géopolymérisation qui utilise généralement des
faibles teneurs en catalyseurs alcalins (0,5 à 6% du poids des
matières premières aluminosilicates). La L.T.G.S permet de
transformer tout matériau aluminosilicate en un ensemble de produits
minéraux qui possèdent les caractéristiques des roches
(insensibilité à l'eau, tenue en température,
dureté, etc.) [24]. Ce procédé de
géopolymérisation assure la cohésion de la matière
terre selon un principe totalement différent de la stabilisation aux
liants hydrauliques. Il n'y a pas d'ajout de liant mais de catalyseurs
permettant aux constituants minéralogiques de réagir entre eux.
C'est l'aluminosilicate luimême qui fabrique, in situ, le liant
d'agglomération. Il s'agit d'un processus comparable à celui qui
a lieu pendant la cuisson céramique à 900°C-1100°C,
à la différence que, dans le cas de la L.T.G.S, la
réticulation peut commencer déjà à
température ambiante [24].
Lors de la fabrication des produits par L.T.G.S, Davidovits
[21] a utilisé des fins cristaux de quartz pour produire des blocs
composites Na-PS-quartz. Dans ces composites, les grains de quartz
entourés de micelles de kaolinite ont une séquence
-(Na-PS)-(SiO2)n-(NaPS)-(SiO2)n, qu'il a appelé SILIFACE Q. La structure
géopolymère résulte ici de la polycondensation des
sialates ou des poly(sialates) des micelles de kaolinite avec les liaisons du
siloxane (Si-O-Si) hydrolysées à la surface du quartz en silanol
(Si-OH). La réaction est la suivante (figure 5) [21]:
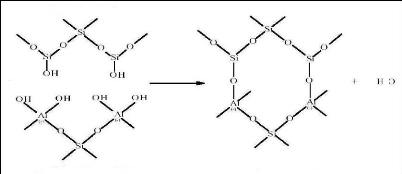
Quartz
Sialate
Structure géopolymère en formation
2
Figure 5 : Polycondensation du quartz
silanol Si-OH avec les poly(sialates) [21].
Les températures de travail dans les
procédés L.T.G.S varient généralement entre 50 et
500°C. La masse volumique des céramiques obtenues est voisine de
1.9 g/cm3. Leur porosité apparente se situe autour de 30% et
les résistances mécaniques à la compression peuvent
atteindre 40 MPa [20]. La figure 6 présente l'évolution de la
résistance à la compression en fonction de la température
de traitement pour un sol kaolinitique traité par le
procédé L.T.G.S.
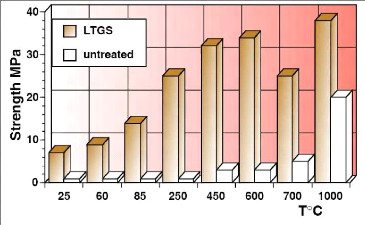
Figure 6: Résistance à la
compression en MPa d'un sol kaolinitique non traité et traité par
L.T.G.S (3 % d'équivalent Na2O), température de traitement
20°C- 1000°C [3]
I-3-3-1 : La L.T.G.S et les matériaux de
construction
La L.T.G.S est une innovation dans l'utilisation du
matériau terre. Dans chaque pays, en changeant seulement certains
paramètres, il est possible de fabriquer pratiquement tous les
matériaux utilisés dans le bâtiment (pisé
résistant à l'eau, adobes, briques, linteaux, fondations,
revêtements de sol, pavements, toitures, enduits, revêtements de
mur, et même des liants hydrauliques) [1] .
Lorsqu'ils sont élaborés convenablement, les
matériaux obtenus par L.T.G.S gardent la qualité de confort
propre aux matériaux terres [1]. Cette qualité de confort demeure
et n'est pas perturbée par les traitements à température
moyenne (85°C- 450°C) [1, 24].
Au Cameroun, très peu d'études ont
été effectuées sur l'utilisation des techniques L.T.G.S
pour la production des matériaux de construction. Ndofor [25] a pu
obtenir des résistances mécaniques à la compression de
l'ordre de 25 MPa pour une teneur en NaOH de 12% par rapport à la terre
argileuse. Par la suite, il conclut qu'une optimisation des proportions en
silice, eau et NaOH dans le mélange pour
géopolymérisation, conduirait aux produits de qualité
optimale.
I-3-3-2 : Le temps et l'énergie dans les
procédés L.T.G.S
Davidovit [24], lors de la production de divers produits
(tuiles, briques objets d'arts...) par L.T.G.S, a utilisé
différents procédés de préparation, de mise en
forme, et de traitements thermiques des pâtes. Il a
démontré que le procédé L.T.G.S permettait
d'obtenir des produits synthétiques aux propriétés
semblables à celles des produits céramiques traditionnelles,
mais, avec des gains de temps et d'énergies.
La figure 7 présente en a) la consommation
d'énergie pour la fabrication des tuiles selon les
procédés traditionnels de cuisson des produits céramiques
(classique et rapide), par procédé L.T.G.S (Géop-A),
L.T.G.S optimisé (Géop-B), et en b), les temps de production des
céramiques traditionnelles et des céramiques obtenues par
L.T.G.S.
Figure 7 : Energies et temps de production
des céramiques traditionnelles et céramiques L.T.G.S
[24].
Selon Davidovits [24], l'exploitation des techniques L.T.G.S
pour la production de « céramiques géopolymères
» offrirait des perspectives économiques intéressantes pour
l'industrie céramique, grâce aux gains d'énergie et de
temps qui pourraient conduire à une multiplication de la
productivité par un facteur de 2 à 5.
I -3-4 : Les réactions de polycondensation
La géopolymérisation est une réaction
exothermique qui consiste à la polycondensation des monomères
pour former une macromolécule de structure tridimensionnelle. Les
réactions chimiques suivent le schéma réactionnel suivant
(équations I.3 et I.4) [26, 27] :
n (Si2O5, Al2O2) + 2n SiO2 + 4n H2O + NaOH ou (KOH) Na+,
K+ + n (OH)3-Si-O-Al--O-Si-(OH)3 (I.3)
Aluminosilicate (OH)2
Précurseur géopolymérique

(I.4)
n (OH)3-Si-O-Al--O- Si-(OH)3 + NaOH ou (KOH)
(Na+, K+)-(-Si-O-Al--O-Si-O-) + 4n H2O


(OH)2 O O O
Réseau géopolymérique
Xu et van Deventer [26] ont proposé une théorie
de paires d'ions pour expliciter le mécanisme de dissolution des
minéraux aluminosilicates ainsi que le mécanisme de
géopolymérisation. Le processus chimique possible de dissolution
des minéraux aluminosilicates et des silicates en milieu alcalin est
présenté dans les trois équations suivantes (I.5 - I.7)
[26].
Al-Si (particule solide) + OH- (aqueux) Al
(OH)-4 + -OSi(OH)3 (I.5)
Monomère Monomère

-OSi (OH)3 + OH- -OSi (OH)2O-
+ H2O (I.6)

O-
-OSi (OH)2O- + OH - -OSi
(OH)O- + H2O (I.7)
Les réactions entre le métal alcalin
M+ et les acides ortho siliciques trivalents et divalents en vue de
compenser les charges électrostatiques de répulsion sont
présentées par les équations suivantes (I.8 - I.11)
[26]:
M+ + -OSi (OH)3 M+ -OSi (OH)3 (I.8)
Monomère Monomère
2M+ + -OSi (OH)2O- M+ -OSi
(OH)2O- M+ (I.9)
Monomère Monomère
O- O- M+
3M+ + -OSi (OH)O- M+ -OSi (OH)O-
M+ (I.10)
Monomère Monomère
M+ + Al (OH) - 4 + OH- M+ -OAl (OH) - 3 + H2O
(I.11)
Monomère Monomère
Les réactions de condensation cations - anions sont
présentées dans les équations suivantes (I.12 - I.15) [26,
27]:
-OSi (OH)3 + M+ -OSi (OH)3+ M+
M+ -OSi (OH)2-O-Si (OH)3 + MOH (I.12)
Monomère Monomère Dimère

-OSi (OH)2O- + M+ -OSi (OH)3+
M+ M+ -OSi (OH)2-O-Si (OH)2-O- + MOH (I.13)
Monomère Monomère Dimère

O- O-
-OSi (OH)O- + M+ -OSi (OH)3+
M+ M+-OSi (OH)-O-Si (OH)2-O- + MOH (I.14)
Monomère Monomère Dimère
2 silicates monomères- + 2 silicates
dimères- + 2M+ M++ trimère
cyclique- + M+ trimère linéaire-
+ 2OH- (I.15)
Barbosa dans [28] a proposé un modèle
explicitant la structure des géopolymères. Les atomes de silicium
et d'aluminium sont arbitrairement distribués dans une structure
tridimensionnelle en laissant des cavités où les cations
compensateurs Na+ peuvent se loger (figure 8).
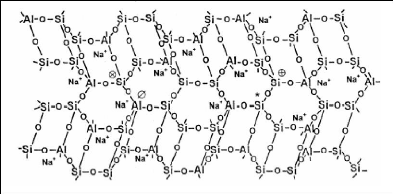
Figure 8: Modèle conceptuel
explicitant la structure des géopolymères [27].
I-3-5 : l'influence de la nature des matières
premières sur le processus de
géopolymérisation
Les compositions chimiques, minéralogiques des
matières premières, leur distribution granulométriques, et
les concentrations des éléments activateurs ont une grande
influence sur les propriétés des géopolymères [2].
La kaolinite et d'autres argiles furent initialement utilisées en 1974
et 1975 comme source d'aluminosilicates pour la fabrication des
géopolymères devant servir à l'encapsulation des
déchets radioactifs [2]. La kaolinite a une structure appropriée
à tout type de procédé de géopolymérisation.
Toutefois, lors des synthèses, une bonne partie de ce minéral ne
participe pas aux réactions de géopolymérisation [29]. Les
matériaux calcinés réagissent généralement
mieux que les matériaux non calcinés, et les impuretés
présentent dans les matières premières peuvent subir des
réactions secondaires affectant aussi bien la cinétique des
réactions que les propriétés mécaniques des
produits obtenus [2]. Les géopolymères issus du métakaolin
nécessitent plus d'eau due à une augmentation de la
porosité et deviennent alors peu résistant pour être
utilisés comme matériau de construction [2]. Toutefois, le
métakaolin est bénéfique comme additif minéral dans
les ciments géopolymères, car il améliore les
résistances mécaniques et réduit le
transport des sels et de l'eau. Il est également
utilisé dans la fabrication des géopolymères pour
application comme adhésifs [2].
Xu et van Deventer [26] ont effectué en 2000 des
recherches étendues sur l'utilisation de 16 minéraux
aluminosilicates différents, avec addition de la kaolinite pour la
fabrication des géopolymères. Ils observèrent que pour la
plupart des minéraux aluminosilicates, l'addition de la kaolinite
était nécessaire pour la formation des gels, et lorsque la
kaolinite était utilisée seul, les propriétés
mécaniques étaient médiocres. Ce résultat signifie
qu'une synergie entre les différents minéraux aluminosilicates
pourrait avoir des effets bénéfiques lors des réactions de
gépolymérisation.
I -3-5-1: L'influence de la nature des ions alcalins
dans le processus de géopolymérisation
Théoriquement, n'importe quelle alcalin ou
alcalinoterreux pourrait être utilisé pour les réactions de
géopolymérisation. Toutefois, la plupart des études ont
été centrées sur les effets des ions sodium et potassium.
Le choix du type d'ion alcalin à utiliser pour les synthèses
géopolymériques dépend de plusieurs facteurs dont les plus
importants sont l'origine, les sources de matières premières
aluminosilicates, et les applications des futurs géopolymères
[2]. La présence de cations dans les matières premières de
base ou ajoutés comme hydroxydes alcalins est considérée
comme importante à cause de leur rôle catalytique. Les
propriétés optimales des géopolymères sont obtenues
quand la concentration de sodium est suffisante pour l'équilibration des
charges lors de la substitution du silicium par l'aluminium dans les
tétraèdres, mais pas en excès pour former le carbonate de
sodium en présence du CO2 atmosphérique [2]. La grande taille de
K+ favorise la formation des oligomères silicates avec qui
Al(OH)4 - préfère se lier. Par conséquent, lorsque la
solution de KOH est utilisée, il se forme plus de précurseur
géopolymérique, facilitant une meilleure polymérisation et
des meilleures résistances en compression que les
géopolymères synthétisés dans les solutions de NaOH
[2, 31].
Les ions potassium semblent être responsables d'un
meilleur degré de condensation par rapport aux ions sodium dans les
mêmes conditions. Puisque K+ est plus basique, il permet des
grandes vitesses de dissolution des silicates. En plus, le fait que
K+ ait une sphère d'hydratation plus petite que
Na+ permet des réactions de polycondensation plus denses et
plus intimes. L'addition de KOH tendrait à améliorer le
degré de polycondensation dans la solution de silicate d'ion alcalin
alors que l'addition de NaOH augmenterait la quantité de silicates
monomères [2, 31].
I-3-5-2 : l'influence des ions calciums
La présence des ions calcium dans les matières
premières améliorerait les propriétés
mécaniques des géopolymères en formant un gel amorphe
structuré Ca-Al-Si. Lorsque les teneurs en CaO sont
élevées, la porosité microstructurale diminue avec comme
résultante la formation des gels [2].
L'addition des grandes quantités d'hydroxyde de calcium
dans la fabrication des géopolomères à base de cendre
volcanique améliore rapidement les résistances mécaniques,
alors que l'addition des petites quantités le fait plus tardivement. Que
ce soit pour les géopolymères à base de cendre volcanique
ou de métakaolin, une substitution de 10% d'aluminosilicate par
l'hydroxyde de calcium semble avoir des effets bénéfiques.
Lorsque les matières premières solides sont déficientes en
calcium, le carbonate de calcium pourrait être introduit sous forme de
suspension aqueuse pour améliorer les propriétés
mécaniques des géopolymères [2, 32].
I-3-5-3 : Les facteurs influençant la
résistance à la compression
La résistance à la compression a
été utilisée par plusieurs chercheurs comme outils pour
l'affirmation du « succès » de la
géopolymérisation [2]. La résistance à la
compression dépend de nombreux facteurs dont la solidité de la
phase gel, le rapport de la phase gel à la phase non dissoute de
particule Al-Si, la distribution et la dureté des particules Al-Si non
dissoutes. Elle dépend également de la nature de la phase amorphe
du géopolymère, du degré de cristallinité, et de la
surface de réaction entre la phase gel et les particules Al-Si non
dissoutes [2, 32]. Toutefois les facteurs tels que le pourcentage de CaO, K2O,
et le type d'alcalin ont une forte corrélation avec la résistance
à la compression [2]. Après géopolymérisation, les
particules non dissoutes restent liées dans la matrice, ce qui signifie
que la dureté des minéraux a une corrélation positive avec
la résistance à la compression. Pendant la
géopolymérisation des minéraux naturels, il est connu que
lorsque des agrégats tels que la poudre de sable sont ajoutés au
mélange géopolymère, la résistance à la
compression s'accroît [2, 26]. L'activation alcaline du metakaolin
utilisant une solution contenant le silicate de sodium et l'hydroxyde de sodium
donne des propriétés mécaniques meilleures à celui
activé avec uniquement l'hydroxyde de sodium [2]. Les meilleures
résistances sont obtenues lorsque les rapports molaires SiO2/Al2O3 et
Na2O/Al2O3 sont 3.0-3.8 et environ 1 respectivement [33]. Toutefois, ces ratios
pourraient changer selon le type de matière première
utilisée comme source de Al2O3 et SiO2 [32].
I-4 : LES CIMENTS GEOPOLYMERES
Les ciments geopolymères sont des composés
synthétiques de structure analogue aux tecto-alumino-silicates. La
chimie de leur géopolymérisation met en jeu des oxydes
aluminosilicates (Al3+ en coordination IV) avec des disilicates
alcalins ou calciques. L'équation de réaction est la suivante
[34]:
2(Si2O5,Al2O2) + K2 (H3SiO4)2 + Ca(H3SiO4)2 (K2O,CaO)
(8SiO2,2Al2O3, nH2O) (I.16)
Aluminosilicate Ciment géopolymère
Contrairement aux Ciments Portland, les ciments
géopolymères sont des matériaux résistants aux
acides, avec des propriétés zéolitiques qui leur
permettent d'encapsuler les déchets toxiques tels que les métaux
lourds. La consolidation de ce ciment s'effectue à travers un processus
de polycondensation du potassium-oligo-(sialate-siloxo) en potassium
poly(syalate-siloxo) (figure 9 ).
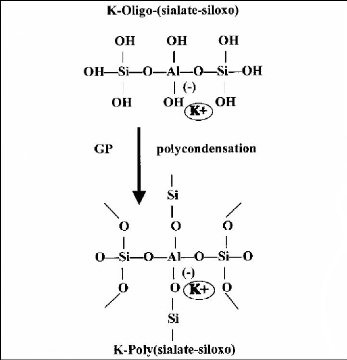
Figure 9: Processus de prise du ciment
géopolymère potassium poly(sialate-siloxo)[23]
Le ciment géopolymère fabriqué par PZ-
Geopoly [35] comprend les éléments majeurs suivants:
- les aluminosilicates spécifiques des espèces
argileuses kaolinitiques calcinées à 750°C ;
- le disilicate alcalin (Na2,K2) (H3SiO4)2;
- le disilicate de calcium (Ca(H3SiO4)2), fabriqué par
réaction alcaline avec les laitiers de hauts fourneaux ;
- la fumée de silice.
Ces ciments sont caractérisés par une prise
rapide à température ambiante et donnent des résistances
à la compression de l'ordre de 20 MPa après 4 h. La
résistance finale après 28 jours est de l'ordre de 70 à
100 MPa [34, 35].
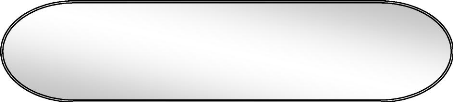
MATERIAUX ET METHODES EXPERIMENTALES
CHAPITRE II :
II-1 : LES MATERIAUX
II-1-1 : Les Matériaux Naturels
Notre étude a porté sur l'argile de Nkolbisson
(AN), la latérite d'Ekoumdoum (LE), et la pouzzolane noire de Djoungo
(PD). Ces matériaux ont été choisis à cause de
leurs teneurs en silice et alumine suffisantes pour leur utilisation comme
source d'aluminosilicates aux réactions de
géopolymérisation.
II-1-1-1 : L'argile sableuse de Nkolbisson
Le gisement est situé dans le flanc de la
rivière Amga, à environ 2 km de l'usine SNEC de Nkolbisson
à Yaoundé. Les populations de la région affirment que dans
le passé, cette argile était utilisée pour la production
des objets de poterie. Selon les travaux de Amougou, les épaisseurs
mises en évidence varient entre 1,10 à 2,70 m [36]. Cette argile
est très sableuse, de couleur variable et à granules
ferrugineuses.
II-1-1-2 : La latérite d'Ekoumdoum
Le gisement est situé sur la route d'Awae, au niveau du
carrefour dit « 3 lions », dans la ville de Yaoundé. Les
latérites de ce gisement présentent une texture gravelo argileuse
et sont actuellement en cours d'exploitation par des artisans, pour la
production des briques de terre comprimée.
II-1-1-3 : La pouzzolane de Djoungo
Le gisement de pouzzolane de Djoungo est situé dans la
province du littorale, et constitue actuellement au Cameroun le gisement le
plus sollicité par la cimenterie locale. Les principales raisons en sont
l'importance quantitative du gisement, ainsi que sa situation
privilégiée à proximité de la voie ferrée
joignant la plus grande ville industrielle du Cameroun [37].
Les coordonnées géographiques et la localisation
des sites des matériaux utilisés sont présentées
dans le tableau 3 et la figure 10.
Tableau 3: Localisation géographique
des sites de prélèvement des matériaux
étudiés
Matériaux
|
Symboles
|
Coordonnées géographiques
|
Ville
|
Latérite d'Ekoumdoum Argile de
Nkolbisson Pouzzolane de Djoungo
|
LE AN PD
|
11°32,222 E et 03°49,511 N 11°25,197 E et
03°52,597 N 09°37,48 E et 04°35,18 N
|
Yaoundé Yaoundé Djoungo
|
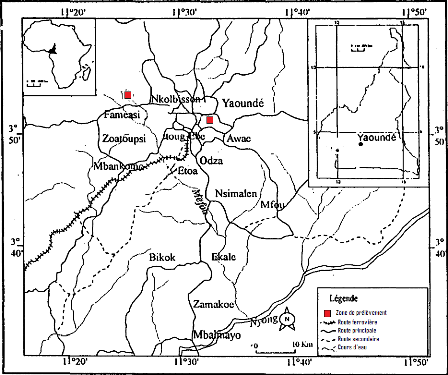
Djoungo
Figure 10 : Carte de localisation
des zones de prélèvement des échantillons de la ville de
Yaoundé [38]
II-1-2 : Les matériaux synthétiques
Le réactif géopolymère utilisé est
constitué d'un mélange de 50% en masse d'hydroxyde de sodium en
pastille et de 50% en masse de silicate de sodium liquide.
Le silicate de sodium provient de la société ACO
SIL S.r.l de Montorio (Italie). Ses caractéristiques physicochimiques
sont consignées dans le tableau 4.
Tableau 4: Caractéristiques
physicochimiques du silicate de sodium utilisé
Caractéristiques physico Unité de mesure
Valeurs
chimiques
Apparence / Liquide légèrement opalescent
Concentration % 45#177;1
Gravité spécifique g/mL 1,37#177;0,01
pH -lg[H+] 11,6#177;0,5
Viscosité (20°C) mPa.s 100#177;50
Point de fusion °C En dessous de 0
Point d'ébullition °C Au dessus de 100
L'hydroxyde de sodium provient de la société
PROLABO de Paris (France). Sa composition chimique est la suivante:
NaOH : 97%
Pourcentage maximale en impuretés :
Na2CO3 : 1,5%
Métaux lourds (Pb) : 0,002%
Fe : 0,002% Cl : 0,010% SO4 : 0,005%
II-2 : LES METHODES DE CARACTERISATION DES MATIERES
PREMIERES II-2-1 : La caractérisation physique des matériaux
argileux
Les matériaux AN et LE ont fait l'objet d'une
caractérisation préliminaire : l'analyse granulométrique
(tamisage humide et sédimentométrie), et la détermination
des limites d'Atterberg. Ces essais ont été effectués dans
le laboratoire d'analyse des matériaux de la MIPROMALO.
II-2-1-1 : L'analyse granulométrique par
tamisage humide
Elle consiste à séparer les différentes
fractions et à les évaluer en pourcentage pondéraux de
l'ensemble de l'échantillon [39]. Chaque matériau est d'abord
séché à l'air atmosphérique, puis
étuvé à 105°C pendant 24 h. Par la suite, 500 g de
matériau sont pesés, trempés dans l'eau pendant 24h, puis
passés à travers une colonne de tamis : 2 et 0,8 mm, puis 500,
400, 200, et 100 um. Après plusieurs lavages, les tamis contenant les
résidus sont séchés à l'étuve pendant 24 h
à 105°C. Les différentes fractions sont calculées par
pesée. Pour finir, la proportion de particules inférieures
à 100 um est retenue pour effectuer l'analyse granulométrique par
sédimentométrie.
II-2-1-2 : L'analyse granulométrique par
sédimentométrie
Cette analyse permet de déterminer le pourcentage de
particules argileuses dans un matériau. Dans l'étude des sols, on
désigne par argile la fraction de matériau comprenant des
éléments de diamètres inférieurs à 2 um, et
séparés au cours de l'analyse mécanique [40].
a) Principe
Le principe de la sédimentométrie est
basé sur la loi de Stockes qui mesure la vitesse (v) de
décantation des particules sphériques dans un milieu visqueux
sous l'influence de la force de gravitation et de la résistance du
milieu [41, 42]. Cette vitesse est donnée par la relation :
V =
|
d s
2( ñ - ñ )
L
18n
|
, où
|
d est le diamètre des particules (um),
ñs est la masse volumique des particules
(g/cm3),
ñL est la masse volumique du milieu visqueux
(g/cm3), n est la viscosité (poise), et
v est la vitesse (m/s) de chute.
Si pendant un temps t (seconde) les particules ont
sédimenté d'une hauteur Ht (cm), la vitesse de ce mouvement est
égale à Ht/t.
b) Mode opératoire
20,0 g de matériau sec sont pesés et introduits
dans une éprouvette A. Par la suite, 30 cm3 de solution
d'hexamétaphosphate de sodium à 5% et 200 cm3 d'eau
déminéralisée sont ajoutés, puis le tout est
agité manuellement. Après un repos de 24 h, on agite à
nouveau pendant 10 minutes et le volume de la solution de l'éprouvette A
est complété à 1000 cm3 avec l'eau
déminéralisée. De la même manière, on
prépare une autre solution dans l'éprouvette B : 30
cm3 de solution d'hexamétaphosphate de sodium à 5%,
complétée à 1000 cm3 avec l'eau
déminéralisée. Les éprouvettes A et B sont
placées dans un bain d'eau froide afin d'uniformiser la
température. Le densimètre est d'abord introduit dans
l'éprouvette B, et, concomitamment on agite vigoureusement la solution
de l'éprouvette A. Aux différents instants, après avoir
effectué la lecture de B, le densimètre est enlevé et
introduit doucement dans l'éprouvette A et la lecture est à
nouveau effectuée. A chaque lecture du densimètre, la
température est aussi mesurée dans le bain d'eau froide.
c) Calculs · Calcul des
diamètres équivalents (dy)
La loi de Stockes étant établie pour les grains
sphériques, le résultat de la mesure ne peut correspondre qu'aux
diamètres équivalents. En prenant le temps en minutes, dy en
micromètre et ñs en g/cm3, nous avons :
g ( 1 )
ñ dy 2 H -
s
t =
|
d'où dy=
|
|
|
3 . 1 0 7nHt
|
|
60 t 18 10
nx 8
|
|
|
g ( 1 )
ñ -
s t
|
|
|
|
|
|
|
La masse volumique du matériau n'étant pas connue,
nous avons pris ñs = 2,65 g/cm3 qui est celle du
quartz [41, 42].
A 25°C, n = 0,0090 poises, g=981 cm/s2.

H H D A C
= 0 - ( + ) - 1 2 C
t ,
m e
où H0 est la distance du centre de gravité du
volume du bulbe du densimètre à la division 1000,
D est la longueur d'une division, et
Cm est la hauteur du ménisque en fraction de
division, mesurée sur l'éprouvette due à l'introduction du
densimètre.
· Calcul des pourcentages cumulés (Y%)
A l'instant t (min) et à la profondeur Ht (cm), on ne
trouve que des particules de dimensions inférieures ou égales
à dy. Le pourcentage de ces particules s'obtient suivant la formule :
V ñ s
Y

0 × R
0 = P ñ s - 1 1 0
R = lecture de A -lecture de B (en nombre de divisions),
V = volume de la suspension (cm3),
P = masse sèche des grains contenus dans la suspension
(g).
La lecture dans A ou B est effectuée après 0.5, 2,
5, 10, 30 minutes et 1, 2, 3, 5, 24 heures.
II-2-1-3 : La plasticitéa) La limite de
liquidité
La limite de liquidité est la teneur en eau qui
correspond à la fermeture de la rainure sur un centimètre de
longueur après environ vingt cinq chocs (appareil de Casagrande). Le
matériau argileux est au préalable lavé au tamis de maille
de 400um puis conservé pendant 24 heures dans l'eau. Après
décantation, il est répandu sur une plaque de plâtre pour
séchage et homogénéisation avant d'être placé
dans l'appareil de Casagrande où une rainure est creusée dans la
coupelle comportant l'échantillon. La manivelle est tournée
à une vitesse de 2 chocs par seconde jusqu'à ce que la rainure se
ferme sur un centimètre.
Des essais successifs sont effectués en laissant
évaporer l'eau progressivement. Le procédé est tel que le
nombre de chocs soit compris entre 15 et 35 pendant cinq essais. La limite de
liquidité est donnée par la formule :
W
L
|
P P
h - s
|
× 100
|
P Tare
s -
|
Où Ph est le poids total humide, et Ps, le poids total
sec.
b) La limite de plasticité
La pâte argileuse du dernier essai de la limite de
liquidité est utilisée pour déterminer la limite de
plasticité : après un léger séchage, on forme une
boule de 12 mm de diamètre environ que l'on utilise pour faire un
cylindre de 10 à 15 cm environ avec 3 mm de diamètre en roulant
sur une surface plane, sèche, propre et non absorbante. La limite de
plasticité est la teneur en eau du cylindre qui se brise lorsqu'on le
soulève de 1 à 2 cm. Elle est donnée par la formule :
W
P
|
=
|
P P
h - s
|
× 100
|
P Tare
s -
|
c) L'indice de plasticité
Elle est obtenue en faisant la différence entre la
limite de liquidité et celle de plasticité. L'indice de
plasticité indique l'intervalle dans lequel le matériau argileux
est façonnable. Sa formule est donnée par l'équation :
I p = wL - WP
II-2-2 : La composition chimique des matériaux
naturels
Les analyses chimiques des matériaux AN, LE, et PD ont
été effectués. Ces analyses permettent de
déterminer les pourcentages pondéraux des éléments
constitutifs du matériau sous forme de leurs oxydes stables. Elles ont
été réalisées au laboratoire d'analyse et de
caractérisation des matériaux de DEMO-CENTER à
Modéna (Italie), par fusion de l'échantillon au métaborate
de lithium (LiBO2), suivie de sa dissolution à l'acide nitrique (HNO3).
Les éléments mis en solution sont dosés par ICP-AES
(Inductive coupled plasma by Atomic emission spectrometry).
II-2-3 : L'analyse minéralogique des
matériaux
Ces analyses ont été effectuées au
laboratoire d'analyse des matériaux de DEMO-CENTER à
Modéna (Italie). La composition des phases est déterminée
par diffraction des rayons X avec une anticathode de
cuivre.
II-2-4 : La granulométrie laser et la surface
spécifique des poudres d'aluminosilicates
La granulométrie laser permet de mesurer les rayons de
particules ou de grains (farines, poudres, sables,...) entre 0,05 et 900 um.
Cette technique est basée sur la diffraction de la lumière d'un
laser. La poudre est convoyée par de l'eau ou par de l'air et passe dans
un faisceau laser. Lorsque le faisceau laser éclaire une particule, on
peut observer des franges de diffraction. L'intensité du rayonnement
diffracté et l'angle de diffraction dépendent de la taille des
particules (plus la particule est petite, plus l'angle de diffraction est
grand). Cet essai a été réalisé dans le laboratoire
de DEMO-CENTER à Modéna (Italie).
La mesure de la surface spécifique permet la
détermination de l'aire de la totalité de la surface des
particules de poudre, y compris la surface des pores ouverts ou criques en
cul-de-sac, accessible aux molécules de gaz extérieures. La
détermination de la surface spécifique est basée sur la
mesure de la quantité de gaz adsorbé par un échantillon de
poudre. Elle a été réalisée par méthode BET
au laboratoire de DEMO-CENTER à Modéna (Italie).
II-3 : LA METHODE EXPERIMENTALE D'ELABORATION DES
MATERIAUX GEOPOLYMERES
II-3-1 : La préparation des matières
premières
La préparation des matières premières
s'est effectuée dans le laboratoire d'analyse des matériaux de la
MIPROMALO. Les matériaux (LE, AN et PD) devant servir à la
synthèse des produits géopolymères sont
prélevés, séchés, broyés dans un broyeur
à boulet jusqu'à passage intégrale au tamis d'ouverture de
mailles 400 um. Par la suite, la moitié des poudres issues du broyage de
chaque type de matériau est traité thermiquement (vitesse de
chauffe de 5°/min jusqu'à 700°C, suivi d'un palier de six
heures). Leur surface spécifique et leur granulométrie (par
méthode laser) est ensuite déterminée afin d'avoir une
idée sur la finesse de leurs particules après broyage. Les six
types de poudre de matériau obtenus (dont trois traités
thermiquement et trois non traités thermiquement), près pour
synthèse géopolymérique, sont ensuite conservés
dans des sachets en plastique afin d'éviter la fixation d'eau
atmosphérique.
II-3-2 : L'élaboration des formulations et le
façonnage des éprouvettes
Les différentes formulations pour la synthèse
des matériaux géopolymères ont été
réalisées en faisant varier la teneur en réactif
géopolymère (mélange constitué en masse de 50% de
NaOH et 50% de silicate de sodium liquide) de 0 à 10%, à
intervalle de 2%, par rapport aux masses de poudres sèches pour les
matériaux AN et LE. Pour les matériaux PD, les teneurs en
réactif géopolymère ont été respectivement
0, 2, 6 et 10%. Les différents mélanges sont ensuite
humidifiés avec de l'eau distillée jusqu'a la limite de
plasticité, et la mise en forme est réalisée dans des
moules cylindriques en PVC (2,1 cm de diamètre et 4,2 cm de hauteur).
Les teneurs en réactif géopolymères et en eau de
façonnage sont calculées par rapport à 100 parts de
poudres sèches.
II-3-3 : Le traitement thermique des différentes
formulations
Les éprouvettes de chaque formulation
façonnées sont laissés sécher à l'air
atmosphérique du laboratoire (à 25°C), puis traité
thermiquement dans un four programmable (type MNI 51 A de marque Multimat) aux
trois températures de curage : 250°C, 350°C, et 450°C. La
vitesse de montée en température est de 5°C/min et le palier
est de 5 heures pour chaque température d'étude. Cet essai
à été réalisé dans le laboratoire d'analyse
des matériaux de la MIPROMALO.
II-4 : LA CARACTERISATION PHYSICO-CHIMIQUE DES
PRODUITS OBTENUS
Afin d'évaluer les performances des produits obtenus,
les propriétés physiques suivantes ont été
déterminées : le pourcentage d'eau absorbée, la masse
volumique apparente la résistance à la compression, et la
microstructure.
II-4-1 : Le pourcentage d'absorption d'eau et la masse
volumique apparente
La détermination de ces paramètres a
été faite suivant la norme ASTM C 20 - 74 [44]. Ces essais ont
été réalisés dans le laboratoire de physicochimie
des matériaux minéraux de l'Université de Yaoundé
I. Les éprouvettes de matériaux obtenues après traitement
thermique sont conservées dans des sachets en plastique afin
d'éviter la fixation d'air
atmosphérique. Par la suite, leur masse Md est
déterminée et elles sont introduites dans un bécher
contenant l'eau distillée. Le mélange est porté à
ébullition pendant 2 heures en s'assurant que les éprouvettes
restent immergées. Après avoir laisser le mélange
refroidir pendant 24 heures, leur masse humide Mw et leur masse suspendue dans
l'eau Ms sont déterminées.
i) Le pourcentage d'absorption d'eau ab (%) est le rapport de
l'augmentation de masse
de l'échantillon entraînée par une imbibition
en eau à la masse sèche de l'échantillon [44]. Il est
donné par la relation :
Md
ii) La masse volumique apparente ñ
(g/cm3) est définie comme étant le quotient de la
masse sèche de l'échantillon par le volume
occupé par la matière solide, y compris les vides contenus dans
les grains (volume apparent). Elle est donnée par la relation :
Md
II-4-2 : La résistance à la
compression
Elle est obtenue par calcul après mesure de la charge
en compression qu'un matériau peut supporter avant sa rupture. Cet
essai, conforme au protocole D 695 des Normes ASTM, à été
réalisé dans le laboratoire de physicochimie des matériaux
minéraux de l'université de Yaoundé 1. Les
éprouvettes de matériau sont placées entre les deux
surfaces planes de l'appareil de compression, et sont comprimées avec
une vitesse uniforme. La lecture de la charge maximale supportée par le
matériau avant sa rupture permet de déterminer sa
résistance à la compression [45]. En désignant par d le
diamètre de l'éprouvette en millimètre, F, la charge
à la rupture en Newton, la résistance à la compression
ä (MPa) est donnée par la relation :
ðd 2
II-4-3 : La Microstructure
La microstructure des produits a été
déterminée par un microscope électronique à
balayage au laboratoire d'analyse et de caractérisation des
matériaux de DEMO-CENTER à Modéna (Italie). Une sonde
électronique fine (faisceau d'électrons) est projetée sur
l'échantillon à analyser. L'interaction entre la sonde
électronique et l'échantillon génère des
électrons secondaires, de basse énergie qui sont
accélérés vers un détecteur d'électrons
secondaires qui amplifie le signal. À chaque point d'impact correspond
un signal électrique. L'intensité de ce signal électrique
dépend à la fois de la nature de l'échantillon au point
d'impact qui détermine le rendement en électrons secondaires et
de la topographie de l'échantillon au point considéré. Il
est ainsi possible, en balayant le faisceau sur l'échantillon, d'obtenir
une cartographie de la zone balayée. Les agrandissements x 35, x50 et
x500 ont ainsi été réalisés.
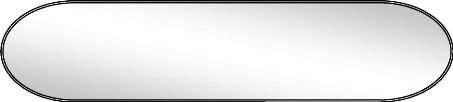
RESULTATS ET INTERPRETATION
CHAPITRE III :
III-1 : LA CARACTERISATION PHYSIQUE DES MATERIAUX
ARGILEUX III-1-1 : L'analyse granulométrique
Les résultats de l'analyse granulométrique de
l'argile Nkolbisson (AN) et de la latérite d'Ekoundoum (LE) sont
représentés sur la figure 11.
Ces résultats montrent que le matériau AN est
constitué d'environ 68% de sable (2 mm > Ô
>0,006 mm), 10% de limon (0,006 >
Ô>0,002 mm et 12% d'argile minéralogique
(Ô <0,002 mm) tandis que LE est constituée de
47% de sable, 22% de limons et 25% d'argiles minéralogiques. Le
matériau LE est donc plus riche en fraction fine que AN.
Généralement, plus un matériau est riche en fraction fine,
plus il nécessite l'eau pour la réalisation d'une pâte
plastique ou une barbotine de coulage.
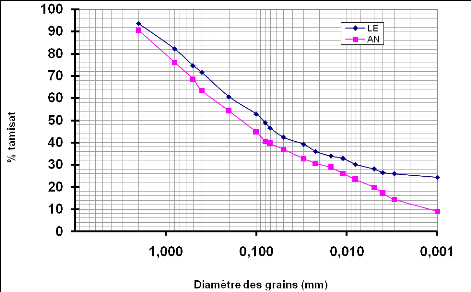
Figure 11 : Courbes granulométriques
des matériaux LE et AN. III-1-2 : La
plasticité
La rhéologie étudie l'écoulement et la
déformation de la matière [8]. Ainsi, l'étude de la
rhéologie des pâtes peut conduire à la connaissance de la
plasticité. Une masse semisolide comme l'argile humide peut être
plus ou moins déformée par une force mécanique
sans perdre sa cohésion et sans que la masse montre une
tendance à reprendre sa forme initiale. C'est dans ce sens qu'on emploie
le terme « plasticité » en céramique [8].
Les résultats des limites de liquidité et de
plasticité des matériaux LE et AN sont consignés dans le
tableau IV.
Tableau 5 : Résultats du test de
plasticité des matériaux LE et AN.
Échantillon Limite de Limite de Indice de
liquidité (%) plasticité (%) plasticité
(%)
AN
|
33
|
19,8
|
13,2
|
LE
|
43,5
|
29,2
|
14,3
|
De ces résultats, il en ressort que les
matériaux AN et LE peuvent contenir 33 et 43% d'eau respectivement sans
couler sous leur propre poids. Par contre, ils ne peuvent se déformer de
manière plastique quand ils ont moins de 19 et 29% d'eau respectivement.
Plus une argile est plastique, plus elle nécessitera d'eau pour former
une pâte de consistance dite « normale » (c'est-à-dire
ne collant pas aux doigts et pouvant supporter des corps inertes
(dégraissant) tout en conservant une aptitude au façonnage
appréciable et une résistance mécanique à sec
suffisante pour assurer la fabrication [8,46].
III-2: LA COMPOSITION CHIMIQUE DES MATERIAUX
Les résultats des analyses chimiques des matériaux
LE, AN et PD sont consignés dans le tableau V.

Tableau 6 : Analyse chimique des
matériaux LE, AN et PD.
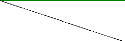
Echantillons
Argile NKolbisson (AN)
Latérite Ekoumdoum (LE)
Pouzzolan Djoungo (PD)
Oxydes
SiO2
|
63.11
|
40.60
|
46.61
|
Al2O3
|
21.20
|
27.14
|
14.33
|
CaO
|
0.32
|
0.04
|
7.59
|
MgO
|
0.43
|
0.05
|
5.95
|
Na2O
|
0.14
|
0,00
|
2.76
|
K2O
|
0.68
|
0.06
|
1.41
|
Fe2O3
|
4.05
|
17.73
|
13.95
|
TiO2
|
1.99
|
1.81
|
2.31
|
Cr2O3
|
0.22
|
0.19
|
0,00
|
L.O.I
|
5.60
|
11.20
|
0.90
|
De ces résultats, il ressort que les matériaux
AN, LE, et PD contiennent tous la silice et l'alumine. Les teneurs en silice
sont respectivement 40,60%, 46,61%, et 63,11% pour les matériaux LE, PD
et AN. Les teneurs en alumine quant à elles sont de 14,33% pour PD,
21,20% pour AN et 27,14% pour LE. Le rapport molaire SiO2 /Al2O3 est
égale à 5,25 pour AN, 2,54 pour LE, et 5,52 pour PD. Ce rapport,
avoisinant 5 pour AN et inférieur à 3 pour LE traduit une faible
proportion en fraction argileuse dans le matériau AN, par rapport au
matériau LE. Pour tous ces matériaux, les teneurs en (SiO2
+Al2O3) sont supérieures à 60 % (84,31% pour AN, 67,74% pour LE,
et 60,94% pour PD).
Les teneurs en oxyde de fer sont de 17,73% pour LE, 13,95 %
pour PD et 4,05% pour AN. L'oxyde de calcium est à l'état de
trace dans les matériaux AN et LE. Par contre, sa teneur est de 7,59 %
dans le matériau PD. Il en est de même pour les oxydes de sodium
et de potassium qui sont à l'état de trace dans les
matériaux AN et LE et dont les teneurs sont respectivement de 2,76% et
4,81% dans le matériau PD. Les rapports molaires Na2O/Al2O3 sont de 0
pour LE, 0,011 pour AN et 0,31 pour PD. Tous ces matériaux ont une
teneur en oxyde de titane TiO2 voisine 2%.
L'oxyde de chrome quasi inexistant dans le matériau PD,
se trouve à l'état de trace dans les matériaux AN et LE.
La perte au feu très faible pour PD (0,9%), se situe autour de 5,60%
pour AN et 11,20% pour LE. LE contient plus de kaolinite que AN selon l'analyse
aux rayons X.
III-3: L'ANALYSE MINERALOGIQUE DES MATERIAUX
Les diffractogrammes de rayons X de nos matières
premières calcinées (AN 700°C, LE 700°C, et PD
700°C), et non calcinées (AN, LE, et PD) sont
présentés sur les figures 12 à 14.
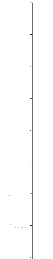
80000
70000
60000
50000
40000
Intensite (cps)
30000
20000
10000
0
Q
K= Kaolinite
Q = Quartz
R = Rutile
G =Goethite
R
Q
Q
Q
R

Q+R Q
K
K
Q-FG
K
R
Q+R+G
Q+R
K#177;Q
Q
K#177;Q
Q
K#177;Q
Q Q+R
Q+R
AN 700°C
AN
Q
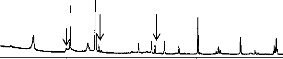
0 10 20 30 40 50 60 70 80
Angle deux théta (°)
Figure 12: Diffractogramme de rayons X de
l'argile Nkolbisson, calcinéé et non calcinéé (AN
et AN 700°C)
Q
Q
H
H+R
Intensit6 (cps)
3000
2000
H= Hématite I=Ilménite K=Kaolinite
Q = Quartz
R = Rutile
|
Q
Q+R
R
Q
H+R
Q R R
R
K
K
R
Hd-G
G
K
K
R K#177;Q
K#177;Q
R +H
K
K+R K+R
R
LE 700°C
LE
Q
K
R+H
Q-FG
K#177;Q


1000
0
0 10 20 30 40 50 60 70 80
Angle deux Théta (°)
Figure 13: Diffractogramme de rayons X de la
latérite d'Ekoumdoum calcinée et non calcinée (LE et LE
700°C)
7000
6000
5000
Intensite (cps)
4000
3000
2000
1000
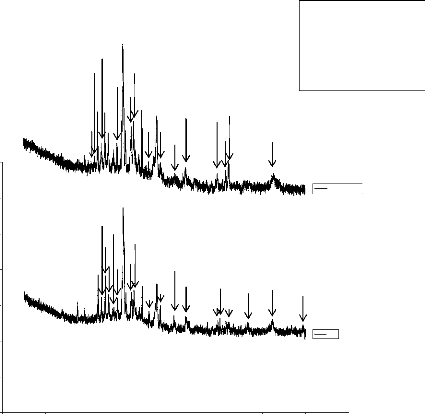
PD 700 °C
PD
A = Anorthite
D = Diopside
E = Enstatite I= Ilménite
P= Plagioclase Q = Quartz
E+I
P+I
P
E+I
D
D
P
I
E
A
A+E+P
P
D
E+I+D
D+I
P
A
P
D
E
13+E
D+I
E
I
P
D
Q+A
Q
Q
D+Q
A+Q
A+p
D+A+Q
A+E+P
P IP
E A
A+P P
Q
Q
1
0
0 10 20 30 40 50 60 70 80
Angle deux théta (°)
Figure 14: Diffractogramme de rayons X de la
pouzzolane de Djoungo, calcinée et non calcinée (PD et PD
700°C)
De ces résultats, il ressort que nos matières
premières aluminosilicates contiennent :
- L'anorthite de formule CaAl2Si2O8, (fichier A.S.T.M 12-301),
avec les raies principales à 3.20 Å, 4.18 Å, et 4.04 Å
;
- le diopside de formule CaMg(SiO3)2, (fichier A.S.T.M 11-654),
dont les raies principales se situent à 2.99 Å, 2.53 Å et
2.89 Å ;
- l'enstatite de formule MgSiO3, (fichier A.S.T.M 7-216), dont
les principales raies se situent à 3.17Å, 2.87 Å, et 2.49
Å ;
- la goethite de formule FeO(OH), (fichier A.S.T.M 17-536), dont
les principales raies se situent à 4.18 Å, 2.69 Å, et 2.45
Å ;
- l'ilménite de formule FeTiO3, (fichier A.S.T.M 3-781),
dont les principales raies se situent à 2.74 Å, 1.72 Å, et
2.54 Å ;
- la kaolinite (Si2O5Al2(OH)4, fichier A.S.T.M. 14-164), dont les
principales raies se situent à 7.17, 3.58 Å, 1.49 Å;
- le plagioclase de formule 0.4 NaAlSi2O8, 0.6 CaAl2Si2O8
(fichier A.S.T.M 10-360) dont les principales raies se situent à 3.20
Å, 4.03 Å et 3.75 Å ;
- le quartz alpha de formule SiO2 (fichier ASTM 5-490) dont les
raies principales se situent à 3.34 Å, 4.26 Å et 1.82
Å ;
- le rutile de formule TiO2, (fichier A.S.T.M. 4-551) dont les
principales raies se situent à 3.25 Å, 1.69 Å et 2.49
Å;
L'on constate que les matériaux AN 700°C et LE
700°C ne contiennent plus la kaolinite. Ceci est dû à leur
décomposition pendant le traitement thermique suivant l'équation
(III. 1) [30]:
400 - 600°C
Si2 O5 Al2 (OH)4 2 SiO2, Al2 O3 + 2H2O (III. 1)
Kaolinite Métakaolinite
III-4 : LA CARACTERISATION GRANULOMETRIQUE DES POUDRES
BROYEES III-4-1 : Les surfaces spécifiques des poudres
utilisées
Les surfaces spécifiques déterminées par
méthode BET, des matériaux broyés AN, LE et PD,
calcinés et non calcinés, sont consignés dans le tableau
V. La surface spécifique d'un matériau est un paramètre
caractéristique du matériau qui peut avoir une grande influence
sur son degré de réactivité lors d'une réaction de
synthèse. Il ressort de ces résultats que le matériau LE
possède une grande proportion en particules fines par rapport à
au matériau AN, dont la proportion en particules fines est
également supérieure à celle du matériau PD. Dans
les procédés de géopolymérisation, l'étape
de formation du précurseur géopolymérique est
favorisée par la finesse des particules d'aluminosilicates [2] ; ce qui
signifie que la vitesse initiale de réaction du matériau LE
serait supérieur à celles des matériaux AN et PD.
Tableau 7 : Surface spécifique des
matériaux LE, AN et PD.
Matériaux AN AN 700°C LE LE
700°C PD PD 700°C
Surfaces spécifiques BET 12,39 11,01
31,73 31,40 0,79 0,41
(m2 /g)
III-4-2 : La granulométrie laser des poudres
utilisées
Les informations obtenus par analyse granulométrique
laser sur la taille des grains de poudres d'aluminosilicates utilisées
pour synthèse géopolymérique sont présentées
sur les figures 15 à 20.
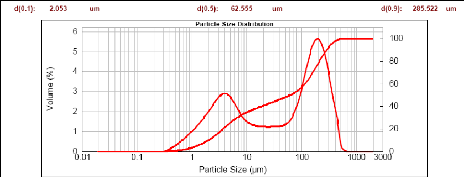
Figure 15 : Granulométrie laser du
matériau AN
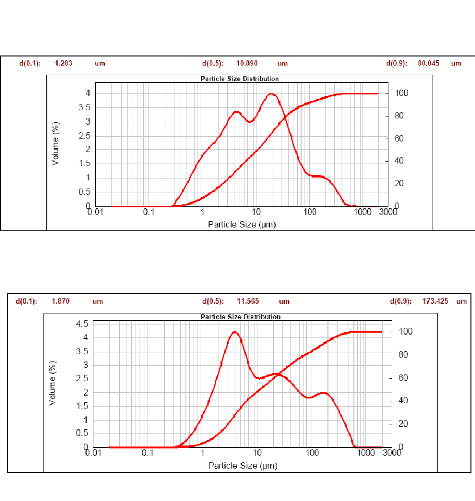
Figure 16 : Granulométrie laser du
matériau AN calciné à 700 °C
Figure 17 : Granulométrie laser du
matériau LE
Figure 18: Granulométrie laser du
matériau LE calciné à 700 °C
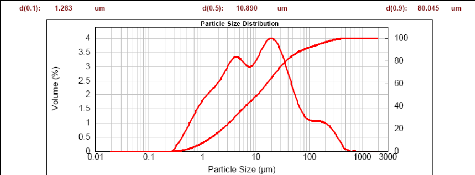

Figure 19: Granulométrie laser du
matériau PD
Figure 20: Granulométrie laser du
matériau PD calciné à 700 °C
De ces résultats, il ressort les informations suivantes
:
· les poudres des matériaux AN et AN
calciné à 700°C contiennent chacune :
- 10% de particules de diamètres inférieurs ou
égales à 2,05 um et 1,28 um respectivement ;
- 50% des particules de diamètres inférieurs ou
égales à 62,55 um et 10,89 um respectivement ;
- 90% de particules de diamètres inférieurs ou
égales à 285,52 um et 80,04 um respectivement.
· les poudres des matériaux LE et LE
calciné à 700°C contiennent chacune :
- 10% de particules de diamètres inférieures ou
égales à 1,28 um et 1,87 um respectivement ;
- 50% des particules de diamètres inférieurs ou
égales à 10,89 um et 11,56 um respectivement ;
- 90% de particules de diamètres inférieurs ou
égales à 80,04 um et 173,42 um respectivement.
· les poudres des matériaux PD et PD
calciné à 700°C contiennent chacune :
- 10% de particules de diamètres inférieurs ou
égales à 4,03 um et 3,25 um respectivement ;
- 50% des particules de diamètres inférieurs ou
égales à 43,09 um et 19,11 um respectivement ;
- 90% de particules de diamètres inférieurs ou
égales à 141,93 um et 87,68 um respectivement.
La granulométrie des particules influence
généralement la réactivité des matières
premières aluminosilicates lors des synthèses
géopolymériques. Si l'on ne s'en tient qu'aux valeurs de la
granulométrie, les latérites seraient plus susceptibles de
réagir, suivi de l'argile Nkolbisson et enfin des pouzzolanes. Mais la
réactivité dépend surtout de la nature chimique et
minéralogique du matériau [2], ce qui signifie qu'il est possible
que l'on observe une réactivité indifférente de la
granulométrie pour nos différents matériaux.
III-5 : LES PROPRIETES PHYSIQUES DES PRODUITS
OBTENUS
Après réalisation des différentes
formulations et traitement thermique, les matériaux AN 700°C et LE
700°C, ne se sont pas consolidés, d'où la non
détermination de leur propriétés physiques. Par ailleurs,
le degré de réactivité de LE, PD, et PD 700°C
à 0 et 2% de réactif géopolymère (R), était
insuffisant pour la détermination des valeurs de leurs pourcentages
d'absorption d'eau et de leurs masses volumiques apparentes. Il en est de
même pour AN à 0% de R.
Les matériaux AN à 10% de R ont
présenté des efflorescences à partir de 3 jours de
séchage dans l'atmosphère du laboratoire avant leur traitement
aux différentes températures
d'études (250°C, 350°C, et 450°C).
Après traitement thermique aucune formulation n'a présenté
des efflorescences. La figure 21 montre les efflorescences observées sur
les matériaux AN à 10% de R juste avant le traitement
thermique.
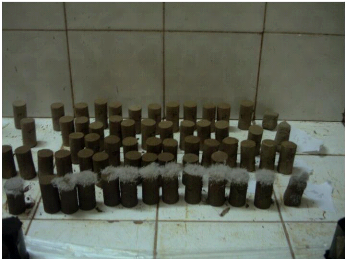
Figure 21 : Efflorescences observées
sur les matériaux AN à 10% de R, juste avant traitement
thermique
Ces efflorescences ne sont en principe pas souhaitables et
contribuent généralement à la dégradation des
propriétés mécaniques des produits. Elles sont
causées par la formation du carbonate de sodium par réaction
chimique entre l'excès de sodium dans le matériau et le CO2
atmosphérique [2]. Elles peuvent être évitées dans
certains cas par optimisation des conditions de curage.
III-5-1 : Le pourcentage d'absorption d'eau et la masse
volumique apparente
Les résultats des pourcentages d'absorption d'eau et des
masses volumiques apparentes des matériaux synthétisés
sont présentés sur les figures 22 à 29.
a) Matériau AN
Les résultats du pourcentage d'absorption d'eau et des
masses volumiques apparentes des géopolymères obtenus à
partir du matériau AN sont présentés sur les figures 22 et
23.
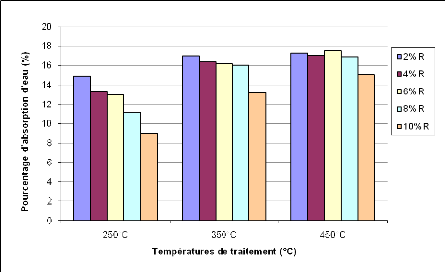
Figure 22 : Pourcentage d'absorption d'eau
des géopolymères obtenus à base de l'argile Nkolbisson
(AN)
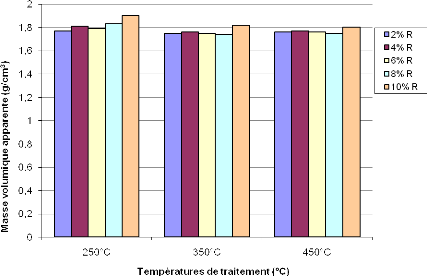
Figure 23 : Masse volumique apparente des
géopolymères obtenus à base de l'argile Nkolbisson
(AN)
Les valeurs du pourcentage d'absorption d'eau des
géopolymères obtenus à partir du matériau AN
varient de 9,00 à 14,88% pour ceux traités à 250°C,
13,19 à 17,00% pour ceux traités à 350°C, et de 15,07
à 17,28% pour ceux traités à 450°C. D'une
manière générale, ces pourcentages d'absorption d'eau
diminuent avec l'augmentation du pourcentage de réactif
géopolymère, et augmentent avec la température de curage.
Ceci pourrait s'expliquer par le fait que l'augmentation du pourcentage de
réactif géopolymère accroitrait le taux de
réactivité du matériau, ce qui conduirait à une
réduction de la porosité. Cependant, l'élévation de
la température de traitement thermique (de 250°C à
450°C) conduirait à une meilleure élimination des
matières organiques contenues dans le matériau. Les vides
laissés par la combustion des matières organiques contribueraient
alors à une augmentation de la porosité, d'où une
augmentation du pourcentage d'absorption d'eau. Par ailleurs, les valeurs des
masses volumiques apparentes sont comprises entre 1.74 et 1.90
g/cm3. Ces valeurs croissent légèrement avec
l'augmentation de la teneur en réactif géopolymère et
décroissent avec la l'augmentation de la température de
traitement thermique ; ce qui est tout à fait normale. En effet, la
masse volumique apparente et le pourcentage d'absorption d'eau des
matériaux évoluent généralement de façons
inverses [47].
b) Matériau LE
Les résultats du pourcentage d'absorption d'eau et des
masses volumiques apparentes des géopolymères obtenus à
partir du matériau LE sont présentés sur les figures 24 et
25.
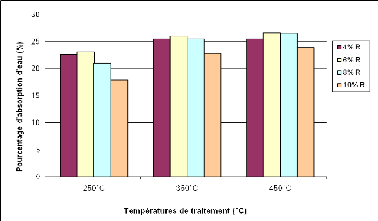
Figure 24: Pourcentage d'absorption d'eau
des géopolymères obtenus à base de la latérite
d'Ekoumdoum (LE)
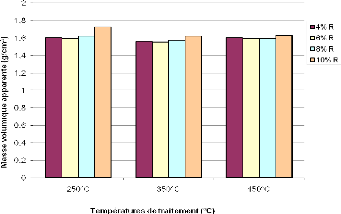
Figure 25 : Masse volumique apparente des
géopolymères obtenus à base de la latérite
d'Ekoumdoum (LE)
Les valeurs du pourcentage d'absorption d'eau des
géopolymères obtenus à partir du matériau LE
varient de 17,87 à 22,6% pour ceux traités à 250°C,
22,8 à 25,5% pour ceux traités à 350°C, et 23,85
à 26,6% pour ceux traités à 450°C. D'une
manière générale ces valeurs varient de manière
similaire à ceux des géopolymères obtenus avec AN,
néanmoins elles sont plus élevées que celles-ci. Certaines
de ces valeurs sont supérieures à celle du pourcentage
d'absorption d'eau maximale recommandée pour briques cuites
exposées aux intempéries (20%) [48].
L'on n'observe pas de grandes différences entre les
valeurs des masses volumiques quisont comprises entre 1.56 et 1.72
g/cm3. Toutefois l'on note une légère augmentation
des
valeurs des masses volumiques lorsque le pourcentage de
réactif géopolymère augmente, surtout avec 10% de R.
c) Matériau PD
Les résultats du pourcentage d'absorption d'eau et des
masses volumiques apparentes des géopolymères obtenus à
partir des matériaux PD et PD700°C sont présentés sur
les figures 26 à 29.
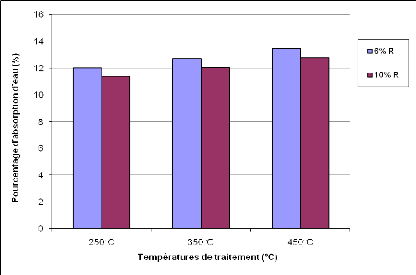
Figure 26 : Pourcentage d'absorption d'eau
des géopolymères obtenus à base de la pouzzolane de
Djoungo (PD)
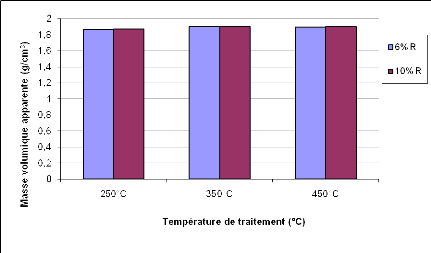
Figure 27 : Masse volumique apparente des
géopolymères obtenus à base de la pouzzolane de Djoungo
(PD)
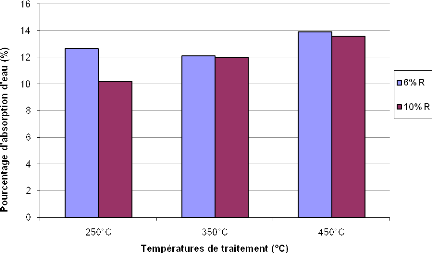
Figure 28 : Pourcentage d'absorption d'eau
des géopolymères obtenus à base de la pouzzolane de
Djoungo calcinée à 700 °C (PD 700°C)
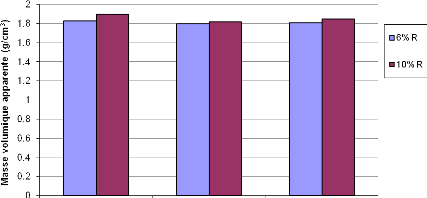

Figure 29 : Masse volumique apparente des
géopolymères obtenus à base de la pouzzolane de Djoungo
calcinée à 700 °C (PD 700°C)
Les valeurs du pourcentage d'absorption d'eau des
géopolymères obtenus à partir des matériaux PD et
PD 700°C varient de 10.02 à 12,66 % pour ceux traités
à 250°C, 12 à 12.72 % pour ceux traités à
350°C, et 12.69 à 13,9 % pour ceux traités à
450°C. L'on observe ici une diminution des valeurs du pourcentage
d'absorption d'eau lorsque la teneur en R passe de 6 à 10%, ce qui
pourrait s'expliquer par le fait que plus il ya de réactif
géopolymère, plus les réactions de consolidation
géopolymériques sont importantes, conduisant ainsi à une
réduction de la porosité. Les valeurs des masses volumiques
apparentes sont quant à elles comprises entre 1,81 et 1.90
g/cm3, ce qui est proche de certaines valeurs de masse volumique des
matériaux L.T.G.S observées dans la littérature [20].
III-5-2 : La résistance à la
compression
Les résultats des résistances à la
compression des matériaux synthétisés sont
présentés sur les figures 30 à 33.
a) Matériau AN
Les valeurs des résistances à la compression des
géopolymères obtenus à partir du matériau AN sont
présentées sur la figure 30.
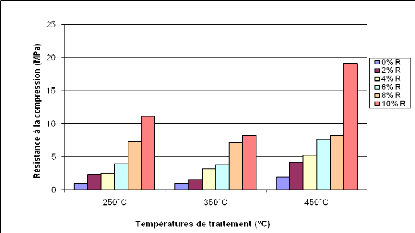
Figure 30: Résistance à la
compression des géopolymères obtenus à base de l'argile
Nkolbisson (AN)
Les valeurs des résistances à la compression des
géopolymères obtenus à partir du matériau AN
varient de 1 à 11,14 MPa pour ceux traités à 250°C, 1
à 8,28 MPa pour ceux traités à 350°C, et 1,9 à
19.10 MPa pour ceux traités à 450°C. D'une manière
générale, la résistance à la compression augmente
avec la teneur en réactif géopolymère pour nos
températures d'étude. A 350 °C, l'on observe une
légère baisse des résistances à la compression des
différentes formulations. Cette baisse pourrait s'expliquer par la
présence des réactions secondaires telles que la
décomposition des matières organiques et les changements
d'état d'oxydation du fer qui se produirait à cette
température ; en effet, d'après Mackenzie [49], la
décomposition des matières organiques constituées
principalement de carbone se produirait entre 200 et 400°C (avec une
réaction exothermique autour de 300°C), et celle de la goethite en
hématite se produirait autour de 380°C suivant la réaction
:

380°C
2 á-FeO.OH á-
Fe2O3 + H2O (III. 2)
Goethite Hématite
b) Matériau LE
Les valeurs des résistances à la compression des
géopolymères obtenus à partir du matériau LE sont
présentées sur la figure 31.
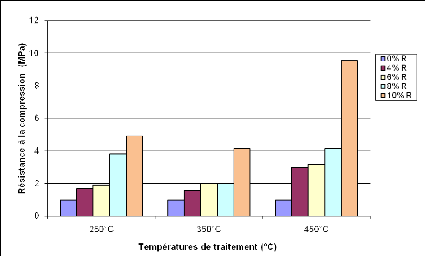
Figure 31: Résistance à la
compression des géopolymères obtenus à base de la
latérite d'Ekoumdoum (LE)
Les valeurs des résistances à la compression des
géopolymères obtenus à partir du matériau LE
varient de 1 à 4,93 MPa pour ceux traités à 250°C, 1
à 4,14 MPa pour ceux traités à 350°C, et 1 à
9,55 MPa pour ceux traités à 450°C. D'une manière
générale, la résistance à la compression augmente
avec l'augmentation de la teneur en réactif géopolymère
pour chaque température d'étude. A 350 °C, la baisse des
résistances à la compression des différentes formulations
pourrait avoir les mêmes origines que pour le matériau AN. La
différence du rapport SiO2/Al2O3 entre les matériaux AN et LE
pourrait être à l'origine des écarts observés entre
les résistances mécaniques des géopolymères
synthétisés à partir de ces matériaux.
c) Matériau PD
Les valeurs des résistances à la compression des
géopolymères obtenus à partir des matériaux PD et
PD 700°C sont présentées sur les figures 32 et 33.
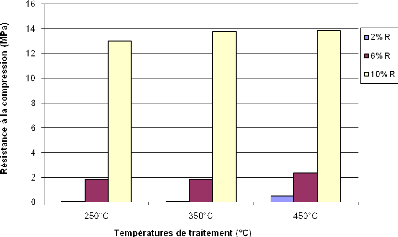
Figure 32: Résistance à la
compression des géopolymères obtenus à base de la
pouzzolane de Djoungo (PD)
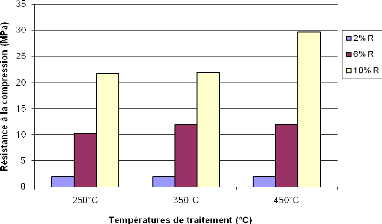
Figure 33: Résistance à la
compression des géopolymères obtenus à base de la
pouzzolane de Djoungo calcinée à 700 °C (PD
700°C)
De ces résultats, il ressort que la résistance
à la compression des différentes formulations augmente avec
l'augmentation de la teneur en réactif géopolymère. Ces
valeurs sont comprises entre 0,1 et 13, 88% pour les matériaux obtenus
à partir de PD et entre 1,9 et 29,7 MPa pour les matériaux
obtenues à base de PD 700°C. L'on n'observe pas de
différence significative entre les résistances à la
compression des matériaux obtenus après traitement à
250°C et 350° C. Par ailleurs, à 450°C, l'on observe une
bonne monté de la résistance à la compression avec
PD700°C à 10 % R qui avoisine 30 MPa. Pour toutes les
températures, les résistances à la compression de PD
700°C sont supérieures à celle de PD ; ce qui signifie ici
que le fait de calciner aurait augmenté la réactivité de
PD.
III-5-3 : La Microstructure (MEB)
Les microstructures des produits obtenus sont
présentées sur les figures 34 à 36.
Figure 34 : Microstructure des
géopolymères obtenus à partir de AN à 10% R et
traité à 450°C (agrandissement x 35 (a) et x500
(b)).
Figure 35 : Microstructure des
géopolymères obtenus à partir de LE à 10% R et
traité à 450°C (agrandissement x 35 (a) et x 500
(b)).
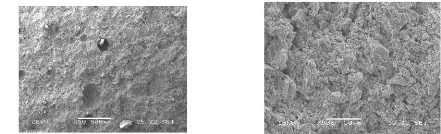
a) b)
Figure 36: Microstructure des
géopolymères obtenus à partir de PD 700 °C à
10% R et traité à 450°C (agrandissement x 50 (a) et x 500
(b)).
Ces microstructures font états de la présence
d'une porosité visible sur les agrandissements x 35, mais non visible
sur les agrandissements x500 pour les matériaux AN et LE. Pour le
matériau PD 700°C, l'on observe la présence d'une faible
porosité visible sur l'agrandissement x 50 et d'une porosité
visible sur l'agrandissement x 500. L'on observe également une phase
homogène pour les géopolymères à base de AN et LE,
et une phase hétérogène, plus microporeuse, pour les
géopolymères à base de PD.
III-6 : DISCUSSION GENERALE
Les rapports molaires SiO2/ Al2O3 des
matériaux AN, LE, et PD sont respectivement 5,25 ; 2,54 ; et 5,52. Les
résistances maximales à la compression de ces matériaux
sont respectivement de 19,1 MPa, 9,55 MPa, et 29,7 MPa. Au vu de ces
résultats, nous pouvons dire que la résistance à la
compression augmente avec le rapport SiO2/Al2O3 de nos différentes
matières premières aluminosilicates ; ce qui est normale, car
d'après la littérature [33], la résistance à la
compression croit avec l'augmentation du rapport SiO2/Al2O3 jusqu'à
atteindre un optimum où ce rapport se situe autour de 3,76, mais qui
pourrait varier en fonction de la nature des matières premières
aluminosilicates. Les résistances mécaniques faibles du
matériau LE par rapport aux matériaux AN et PD pourraient
s'expliquer d'une part par son rapport SiO2/Al2O3 faible (2,54) contre 5,25 et
5,52 pour AN et PD respectivement, et d'autre part par ses teneurs de
pourcentage d'absorption d'eau élevées par rapport à ceux
des matériaux PD et AN. Ces résultats sont en accord avec ceux
observés dans la littérature ; en effet il à
été démontré que la formation des pores au cours du
traitement thermique des matériaux argileux réduit les
résistances mécaniques [47]. Par ailleurs, De Silva et al [33]
ont prouvé que l'augmentation de la proportion en alumine dans les
matières premières aluminosilicates contribuait à
réduire les résistances mécaniques des produits
géopolymères. L'on pourrait également établir une
corrélation entre les rapports molaires Na2O/Al2O3 de nos
matières premières (0 pour LE, 0.011 pour AN et 0.31 pour PD)
avec les résistances à la compression. En effet, les
résistances à la compression croissent avec ces rapports
jusqu'à atteindre un optimum ou ce rapport se situe autour de 1 [33,
50].
Les résistances mécaniques obtenues avec les
matériaux PD 700°C sont supérieures à celles obtenues
avec PD. En effet, d'après Komnitsas, et Zaharaki [2], le fait de
calciner les matières premières aluminosilicates pour la
réalisation des matériaux géopolymères
contribuerait à libérer les silicates et aluminates, ce qui
augmenterait alors leur degré de
réactivité. Toutefois les matériaux
L.T.G.S sont un cas particulier de matériaux géopolymères
dont les méthodes de synthèses proposés par Davidovits [1,
24, 51] ne font pas allusion à la nécessité de calcination
préalable des matières premières aluminosilicates lors du
procédé de synthèse ; la consolidation des
matériaux L.T.G.S se produirait par polycondensation des micelles de
kaolinite en milieu basique suivant la réaction :
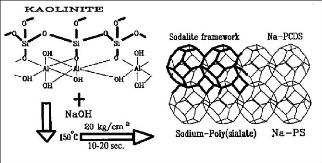
Figure 37: Schéma de la
polycondensation hydrothermale de Na- poly(syalate)[3].
Cette équation pourrait justifier la non
réactivité observée sur les matériaux AN 700°C
et LE 700°C (contenant la métakaolinite), par rapport aux
matériaux AN et LE (contenant la kaolinite). Pour ce qui est du
matériau PD la présence des minéraux tel que l'anorthite,
dans les phases calcinées et non aurait fortement contribué
à la formation des structures consolidées. En effet la structure
en réseau de ce minérale (figure 41) participerait à la
formation de la structure géopolymère [24].
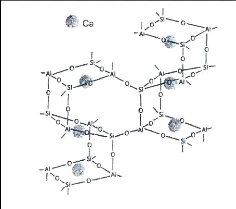
Figure 38 : Structure de l'anorthite
La teneur élevée (7,59 %) en oxyde de calcium
dans le matériau PD par rapport au matériau LE (0,04 %), et AN
(0,32 %) est également l'une des causes des bonnes résistances
à la compression de ce matériau. En effet, il à
été démontré [2, 32] qu'une substitution de 10%
d'aluminosilicate par l'hydroxyde de calcium lors de la synthèse des
matériaux géopolymères avait des effets
bénéfiques sur les propriétés mécaniques.
Malgré sa grande proportion en particules fines par
rapport aux matériaux AN et PD,
le matériau LE a présenté des
résistances à la compression relativement faibles ; ce
quisignifie que la réactivité comparative de nos
différentes matières premières aluminosilicates a
été beaucoup plus liée à leur nature
chimique et minéralogique qu'a la taille de leurs particules
constitutives.
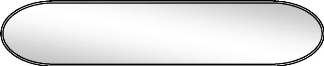
CONCLUSION ET PERSPECTIVES
Au terme de notre étude, il ressort que la calcination
des matériaux AN et LE ne permet pas d'obtenir des produits
consolidés dans nos conditions de travail (granulométrie des
matières premières, plages de températures de traitement
thermique et concentrations de réactifs géopolymères). Les
matériaux AN, LE, (non calcinés), et PD (calciné ou non),
se consolident bien dans nos conditions de travail.
L'analyse chimique de nos matières premières a
montré que les rapports molaires SiO2/ Al2O3 sont
respectivement 5,25; 2,54 ; et 5,52 pour les matériaux AN, LE et PD.
La détermination des propriétés physiques
des produits obtenus après synthèse montre
que :
- la masse volumique apparente et la résistance
à la compression croissent légèrement avec l'augmentation
de la teneur en réactif géopolymère alors que le
pourcentage d'absorption d'eau décroit ;
- la résistance à la compression croît avec
l'augmentation du rapport SiO2/Al2O3 de nos matières premières
aluminosilicates ;
- la microstructure des matériaux fait état
d'une phase homogène pour les géopolymères à base
de AN et LE, et d'une phase hétérogène, plus microporeuse,
pour les géopolymères à base de PD.
Nous avons également observé qu'il est difficile
d'établir une corrélation entre la taille des particules et le
degré de consolidation des produits géopolymères pour des
matières premières aluminosilicates de nature différente.
Les résistances maximales à la compression sont respectivement de
11,14 MPa, 4,93 MPa, 13 MPa, et 21,8MPa pour les matériaux AN, LE, PD,
et PD 700°C, traités à 250°C. A 350°C, elles sont
respectivement de 8,28 MPa, 4,14 MPa, 13,8 MPa, et 21,9 MPa. Les plus grandes
résistances à la compression observées sur nos
matériaux ont été obtenues sur les produits traités
à 450°C. Elles sont respectivement de 19,1MPa, 9,55 MPa, 13,88 MPa,
et 29,7 MPa pour les matériaux AN, LE, PD, et PD 700°C. Ces
résistances correspondent tous aux formulations à 10% de R, ce
qui laisse présager qu'elles pourraient encore croitre si l'on
augmentait la teneur en réactif géopolymère. Malgré
les efflorescences observées sur AN à 10% de R avant traitement
thermique, cette formulation présente les meilleures résistances
à la compression des matériaux obtenus à partir de AN aux
différentes températures d'études ; ce qui signifie qu'une
optimisation des conditions de curage pourrait accroitre les
propriétés mécaniques de nos matériaux. Les valeurs
de résistances à la compression obtenues à partir des
géopolymères à base de LE sont faibles pour certaines
applications dans le domaine de la
construction, qui nécessitent parfois des
résistances en compression supérieures ou égales à
10 MPa. Les matériaux AN et PD par contre pourraient bien être
utilisés dans la production des matériaux de construction
géopolymères (briques, tuiles, pavés...). Toutefois il est
possible que l'incorporation des poudres de silice dans le matériau LE
puisse contribuer à l'amélioration de ces résistances en
compression.
Comme perspective, nous nous proposons d'améliorer les
propriétés mécaniques des produits en étudiant les
paramètres de curage (humidité relative de l'enceinte de curage,
temps et températures de traitement thermique), et en optimisant la
préparation des matières premières (granulométrie
des particules, teneurs en eau et méthode
d'homogénéisation des formulations avant la mise en forme). Nous
comptons ensuite réaliser des essais de durabilité et de
résistances aux acides sur les produits synthétisés, puis,
les comparer avec ceux obtenus par le réactif géopolymère
commercialisé par l'Institut CORDI-GEOPOLYMERE. Nous comptons enfin
réaliser des essais de synthèse d'activateurs alcalins avec les
matières premières locales (calcaire et trona), puis des essais
de synthèse des matériaux géopolymères
optimisés a base d'activateurs alcalins locaux, et proposer un protocole
de synthèses a petite échelle des briques
géopolymères à partir des matières premières
essentiellement locales.
[1]

REFERENCES BIBLIOGRAPHIQUES
C. Boutterin, J. Davidovits (2003)- Réticulation
Géopolymérique (LTGS) et Matériaux de Construction,
géopolymère, vol.1, pp 79-88.
[2] K. Komnitsas, D. Zaharaki (2007)- Geopolymereisation: a
review and prospects for minerals industry, Minerals engineering,
vol 20, pp 1261-1277.
[3] J. Davidovits (1991)- Geopolymer : inorganic polymeric
new materials, journal of thermal analysis- vol.37, pp
1633-1656.
[4] S. Andini, R. Cioffi, F. Colangelo, T. Grieco, F.
Montagnaro, L. Santoro (2007)- Coal fly as raw material for the manufacture
of geopolymer-based products, Waste Management,
doi:10.16/j.wasman.2007.02.001.
[5] P. Duxson, A. Fernandez-Jimérez, J. L. Provis,
G.C. Lukey, A. Palomo, J. S. J van Deventer (2007)- Geopolymer technology:
the current state of the art, Advances in geopolymer science and
technology, vol 42, pp 2917- 2933.
[6] J. Sigg (1991)- Les produits de terre cuites,
Septima, Paris, 494 P.
[7] C.A. Jouenne (2001)- Traité de
céramique et matériaux, Septima, Paris, 657 p.
[8] G. Aliprandi (1979)- Matériaux
réfractaires et céramiques technique, Septima, Paris 612
p.
[9] H. Houben and H. Guillaud (1994)- earth construction, A
comprehensive guide, Intermediate Technology Publications, pp 73.
[10] J. Davidovits (1994)- Global Warming Impact on cement
and Aggregates Industries, World Ressource Review, vol.6 N° 2, pp
263-276.
[11] U. C. Melo and B. Ndigui (2004)- Activité
pouzzolanique des déchets de briques et tuiles cuites, Silicate
Industriel, vol 70, N° 1-2, pp 11-18.
[12] C. Leonelli, E. Kamseu, D.N. Boccaccini, U.C. Melo, A.
Rizzuti, N. Billong, P. Misselli (2007)- Volcanic ash as alternative raw
materials for traditional vitrified ceramic products, Advances in
Applied Ceramics, vol 106 , NO 1.
[13] R. Stulz, K. Mukerji (1993)- Appropriate building
materials, catalogue of potential solution third revised edition, pp
29.
[14] H. Tremblay (1998)- AMELIORATION MECANIQUE ET
PREDICTION DE COMPRESSIBILITE DES SOLS FINS DU QUEBEC, thèse Ph.D,
Université LAVAL, Québec.
[15] A. Geoffrey Kerali (2001)- DURABILITY OF COMPRESSED AND
CEMENT-STABILISED BUILDING BLOCKS, Ph.D engineering Thesis, University of
Warwick, School of Engineering.
[16] E. A. Basha, R. Hashim, H. B. Mahmud, A. S. Muntohar
(2005)- Stabilisation of residual soil with rice husk ash and cement,
Construction and Building Materials, vol 19, pp 448- 453.
[17] K.M.A. Hossain, M. Lachemi, S. Easa (2007)-
Stabilized soils for construction applications incorporating natural
resources of Papua New Guinea, Resources, Conservation and Recycling,
vol.51, pp 711-731.
[18] Ndigui Billong, U. Chinje Melo, M. K. Ndikontar (2008)-
Effet du Trona sur les Proprietés Hydrauliques d'un Ciment Portland
Composé, Silicate Industriel, vol 73, N° 1-2, pp
17-23.
[19] J.G.S. Van Jaarsveld, J.S.J. Van Deventer, G.C. Lukey
(2002)- The effect of composition and temperature on the properties of fly
ash-and kaolinite-based géopolymers, Chemical Engineering
journal, vol 89, pp 63-73.
[20] Subaer (2004)- INFLUENCE OF AGGREGATE ON THE
MICROSTRUCTURE OF GEOPOLYMER, Ph.D Thesis, Curtin University of
Technology, Western Australia.
[21] J. Davidovits (1994)- GEOPOLYMERS: Man-Made Rock
Geosynthesis and the Resulting Development of Very Early High Strength
Cement, Materials Education, vol.16 pp 91-139.
[22] J.C.Swanepoel, C.A. Strydom (2002)- Utilisation of fly
ash in a geopolymeric material, Applied Geochemistry, vol. 17, pp
1143-1148.
[23] J. Davidovits (2002)- 30 Years of Successes and
Failures in Geopolymer Application. Market Trends and Potential
Breakthroughs, Geopolymer Conference, October 28-29, Melbourne,
Australia.
[24] J. Davidovits (2008)- Geopolymer Chemistry and Application,
2nd edition, Institut Géopolymère, 586 p.
[25] Ndofor Akongnui Fai (2006)- Stabilization of soils from
Cameroon for construction purposes, Dissertation in Physical Land
Resources', Universiteit GentVrije Universiteit Brussel, Belgium.
[26] Hua Xu, J.S.J. Van Deventer (2000)- The
geopolymerisation of alumino-silicate minerals, International journal
of mineral processing, vol 59, pp 247-266.
[27] Hua Xu (2002)- GEOPOLYMERISATION OF ALUMINOSILICATE
MINERALS, Ph.D engineering Thesis, University of Melbourne, Australia.
[28] P. Duxson (2006)- THE STRUCTURE AND THERMAL EVOLUTION
OF METAKAOLIN GEOPOLYMERS, Ph.D engineering Thesis, University of
Melbourne, Australia.
[29] M. Schüker, J.D. Kenneth Mackenzie (2005)-
Microstructure of sodium polysialate siloxo géopolymère,
Ceramics International, vol. 31, PP 433-437.
[30] E. Lambercy (1993)- Les matières
céramiques et leur transformation par le feu, Granit 1. Des
dossiers argiles.
[31] R. Cioffi, L. Maffucci, L. Santoro (2003)-
Optimization of geopolymer synthesis by calcination and polycondensation of
a kaolinitic residue, Resources Conservation and Recycling, vol.
40, pp 27-28.
[32] J.G.S. Van Jaarsveld, J.S.J. Van Deventer, G.C. Lukey
(2003)- The characterization of source materials in fly ash-based
geopolymers, Materials Letters, vol. 57, pp 1272-1280.
[33] P. De Silva, K. Sagoe-Crenstil, V. Sirivivatnanon (2007)-
Kinetics of geopolymerization : Role of Al2O3 and SiO2,,
Cement and Concrete Research, vol. 37, pp 512-518.
[34] J. Davidovits (1994)- PROPERTIES OF GEOPOLYMER
CEMENTS, proceedings First International Conference on Alkaline Cement and
Concretes, Scientific Research Institute on Binders and Material, Kiev
State Technical University, Ukraine PP. 131-149.
[35] M. Sofi, J. S. J. van Deventer, P. A. Mendis, G.C. Lukey
(2007)- Engineering properties of inorganic polymer concretes,
Cement and Concrete Research, Vol 37, PP 251-257.
[36] E. Kamseu (2002)- Projet de dimensionnement des briques
cuites: étude de la relation dimension des moules - retrait - dimension
des produits, MIPROMALO/PROG. CER et BTC.
[37] C. Bidjoka, J. Tuset, A. Messi , J. Pera (1993)-
Etude et évaluation de l'activité pouzzolanique des
pouzzolanes de Djoungo (Cameroun), Ann. Fac. Sci, HSI, Chimie Sciences
de la Terre, pp133-145.
[38] G. F. Ngon Ngon (2007)- ETUDE MORPHOLOGIQUE,
GEOLOGIQUE ET CRISTALLOGRAPHIQUE DES ARGILES LATERITIQUES ET DES ARGILES
HYDROMORPHES DE LA REGION DE YAOUNDE EN ZONE TROPICALE HUMIDE. ESSAIS
INDUSTRIELS ET EVALUATION DE LEURS POTENTIELS COMME MATERIAUX DE CONSTRUCTION,
Thèse de Doctorat/ Ph.D en Science de la Terre, Université
de Yaoundé1, Cameroun.
[39] H. Chamayou, J.P. Legros (1989)- Les bases physiques,
chimiques et minéralogiques de la science du sol, Presse
Universitaire de France.
[40] A. Demolon, D. Leroux (1952)- Guide pour l'étude
expérimentale du sol. 2e édition, GauthierVillars
- Paris.
[41] ENSP Yaoundé (1999)- Analyse
granulométrique d'un sol fin, Travaux pratiques de
géotechniques.
[42] LCPC (1970)- Analyse granulométrique par
sédimentométrie, Dunod, Paris.
[43] ASTM C 20 - 74-(1979) Stadard Test Methods for apparent
porosity, water absorption, apparent specific gravity, and bulk density of
burned refractory brick by boiling water .
[44 ] J. Rigaud (1978)- La céramique de A à
Z, Septima, Paris, 56 p.
[45] ASTM D 695 (1996)- Compressive Properties.
[46] E. KRAUSE (1977)- Le séchage en
céramique, principes et techniques, Septima, Paris, 265 p.
[47] J. KARSTEN (2000)- Additive in the brick and tile
industry, novokeram, pp 25-39.
[48] U.C. Melo, E. Kamseu, C. Djangang (2001)- Effcet of
fluxes on the fired properties between 950 - 1050°C of some cameroonian
clays. Actes 1ère conférence GCA, pp 57-69.
[49] C. MACKENZIE R. (1957)- The differential thermal
investigation of clays, Mineralogical society, London 456 p.
[50] P. Duxsona, S.W. Mallicoat , G.C. Lukey , W.M. Kriven ,
J.S.J. van Deventer (2006)- The effect of alkali and Si/Al ratio on the
development of mechanical properties of metakaolin-based geopolymers,
colloids and surfaces, vol 292, pp 8-20.
[51] J.Davidovits and C.James (1984)- Low Temperature
Geopolymeric Setting of Ceramics (LTGS)(IV): Dolomite presence is proof of LTGS
in Cyprus Amphorae, Symposium on Archaeometry, Smithsonian Institution,
Washington D.C, USA, Abstracts pp. 24-25.
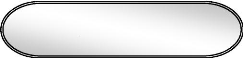
ANNEXES
Tableau 8 : Analyse granulométrique
par tamisage humide de AN
|
Ouvertures tamis (mm)
|
% tamisat
|
2,000
|
90,6
|
0,800
|
76,2
|
0,500
|
68,6
|
0,400
|
63,4
|
0,200
|
54,2
|
0,100
|
44,8
|
Tableau 9 : Analyse granulométrique
par tamisage humide de LE
|
Ouvertures tamis (mm)
|
% tamisat
|
2,000
|
93,6
|
0,800
|
82,2
|
0,500
|
74,6
|
0,400
|
71,6
|
0,200
|
60,6
|
0,100
|
52,8
|
Tableau 10 : Analyse granulométrique
par sédimentométrie de AN
% < 100um = 44,80
prise d'essai P = 20,0g
volume de la suspension V = 1000 cm3
|
|
Température 25
|
#177; 1°C
|
t(s)
|
A
|
B
|
R=A-B
|
Hr(10-2m)
|
D(pm)
|
% D(P)
|
% des passants
|
30
|
19,5
|
-2,5
|
22
|
14,45
|
69,19
|
88,33
|
39,57
|
60
|
18
|
-2,5
|
20,5
|
14,765
|
49,46
|
82,31
|
36,88
|
120
|
15,7
|
-2,5
|
18,2
|
15,248
|
35,54
|
73,08
|
32,74
|
300
|
14,5
|
-2,5
|
17
|
15,5
|
22,66
|
68,26
|
30,58
|
600
|
13,5
|
-2,5
|
16
|
15,71
|
16,13
|
64,24
|
28,78
|
1200
|
12
|
-2,5
|
14,5
|
16,025
|
11,52
|
58,22
|
26,08
|
2400
|
10,5
|
-2,5
|
13
|
16,34
|
8,23
|
52,20
|
23,38
|
4800
|
8,5
|
-2,5
|
11
|
16,76
|
5,89
|
44,17
|
19,79
|
7200
|
7
|
-2,5
|
9,5
|
17,075
|
4,86
|
38,14
|
17,09
|
14400
|
5,5
|
-2,5
|
8
|
17,39
|
3,46
|
32,12
|
14,39
|
86400
|
2,5
|
-2,5
|
5
|
18,02
|
1,44
|
20,08
|
8,99
|
Tableau 11 : Analyse granulométrique par
sédimentométrie de LE
% < 100um = 52,80
prise d'essai P = 20,0g
volume de la suspension V = 1000 cm3
|
|
Température 25
|
#177; 1°C
|
t(s)
|
A
|
B
|
R=A-B
|
Hr(10-2m)
|
D(pm)
|
% D(P)
|
% des passants
|
30
|
19,5
|
-2,5
|
22,00
|
14,45
|
69,19
|
88,33
|
46,64
|
60
|
17,5
|
-2,5
|
20,00
|
14,87
|
49,63
|
80,30
|
42,4
|
120
|
16
|
-2,5
|
18,50
|
15,19
|
35,46
|
74,28
|
39,22
|
300
|
14,5
|
-2,5
|
17,00
|
15,50
|
22,66
|
68,26
|
36,04
|
600
|
13,5
|
-2,5
|
16,00
|
15,71
|
16,13
|
64,24
|
33,92
|
1200
|
13
|
-2,5
|
15,50
|
15,82
|
11,45
|
62,23
|
32,86
|
2400
|
11,75
|
-2,5
|
14,25
|
16,08
|
8,16
|
57,22
|
30,21
|
4800
|
10,75
|
-2,5
|
13,25
|
16,29
|
5,81
|
53,20
|
28,09
|
7200
|
10
|
-2,5
|
12,50
|
16,45
|
4,76
|
50,19
|
26,5
|
14400
|
9,75
|
-2,5
|
12,25
|
16,50
|
3,37
|
49,19
|
25,97
|
86400
|
9
|
-2,5
|
11,50
|
16,66
|
1,38
|
46,17
|
24,38
|
Tableau 12 : Pourcentage d'absorption d'eau
des géopolymères obtenus à base de AN
% de R
|
250 °C 350 °C 450 °C
|
Pourcentage d'absorption d'eau (%)
|
2
|
14,88
|
17
|
17,28
|
4
|
13,3
|
16,34
|
17,01
|
6
|
13
|
16,16
|
17,49
|
8
|
11,18
|
16
|
16,88
|
10
|
9
|
13,19
|
15,07
|
Tableau 13 : Masses volumiques apparentes
des géopolymères obtenus à base de AN
% de R
|
250 °C 350 °C 450 °C
|
Masse volumique apparente (g/cm3)
|
2
|
1,77 1,75 1,76
|
4
|
1,81
|
1,76
|
1,77
|
6
|
1,79
|
1,75
|
1,76
|
8
|
1,83
|
1,74
|
1,75
|
10
|
1,9
|
1,82
|
1,8
|
Tableau 14 : Résistances à la
compression des géopolymères obtenus à base de AN
% de R
|
250 °C 350 °C 450 °C
|
Résistance à la compression (MPa)
|
0
|
1
|
1
|
1,9
|
2
|
2,29
|
1,59
|
4,14
|
4
|
2,54
|
3,18
|
5,25
|
6
|
3,98
|
3,82
|
7,64
|
8
|
7,32
|
7,16
|
8,28
|
10
|
11,14
|
8,28
|
19,1
|
Tableau 15 : Pourcentage d'absorption d'eau
des géopolymères obtenus à base de LE
% de R
|
250 °C 350 °C 450 °C
|
Pourcentage d'absorption d'eau (%)
|
4
|
22,6
|
25,5
|
25,5
|
6
|
23,09
|
26
|
26,6
|
8
|
21
|
25,5
|
26,5
|
10
|
17,87
|
22,8
|
23,85
|
Tableau 16 : Masses volumiques apparentes
des géopolymères obtenus à base de LE
% de R
|
250 °C 350 °C 450 °C
|
Masse volumique apparente (g/cm3)
|
4
|
1,6 1,56 1,6
|
6
|
1,59
|
1,55
|
1,59
|
8
|
1,62
|
1,57
|
1,59
|
10
|
1,72
|
1,62
|
1,63
|
Tableau 17 : Résistances à la
compression des géopolymères obtenus à base de LE
% de R
|
250 °C 350 °C 450 °C
|
Résistance à la compression (MPa)
|
0
|
1
|
1
|
1
|
4
|
1,7
|
1,59
|
3
|
6
|
1,9
|
2
|
3,18
|
8
|
3,82
|
2
|
4,14
|
10
|
4,93
|
4,14
|
9,55
|
Tableau 18 : Pourcentage d'absorption d'eau
des géopolymères obtenus à base de PD
% de R 250 °C 350 °C 450 °C
Pourcentage d'absorption d'eau (%)
6
|
12,03
|
12,72
|
13,46
|
10
|
11,39
|
12,05
|
12,79
|
Tableau 19 : Masses volumiques apparentes
des géopolymères obtenus à base de PD
% de R 250 °C 350 °C 450 °C
Masse volumique apparente (g/cm3)
6
|
1,86
|
1,9
|
1,89
|
10
|
1,87
|
1,9
|
1,9
|
Tableau 20 : Résistances à la
compression des géopolymères obtenus à base de PD
% de R 250 °C 350 °C 450 °C
|
Résistance à la compression
|
(MPa)
|
2
|
0,1
|
0,1
|
0,5
|
6
|
1,9
|
1,9
|
2,38
|
10
|
13
|
13,8
|
13,88
|
Tableau 21 : Pourcentage d'absorption d'eau
des géopolymères obtenus à base de PD 700 °C
% de R 250 °C 350 °C 450 °C
Pourcentage d'absorption d'eau (%)
6
|
12,66
|
12,1
|
13,9
|
10
|
10,2
|
12
|
13,6
|
Tableau 22 : Masses volumiques apparentes
des géopolymères obtenus à base de PD 700°C
% de R 250 °C 350 °C 450 °C
Masse volumique apparente (g/cm3)
6
|
1,83
|
1,8
|
1,81
|
10
|
1,9
|
1,82
|
1,85
|
Tableau 23 : Résistances à la
compression des géopolymères obtenus à base de PD 700
°C
% de R 250 °C 350 °C 450 °C
|
Résistance à la compression
|
(MPa)
|
2
|
1,9
|
1,9
|
1,9
|
6
|
10,3
|
11,9
|
12
|
10
|
21,8
|
21,9
|
29,7
|
|