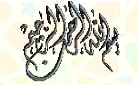
óÒÞÇ )2
òÞáóÚ äöå
ä~ó~~ö áúÇ Þá
~ÞáÎ íöÐ~Ç
ßøöÈóÑ
öäúÓ~öÈ
óÒÞÇ
~ õãóÒi
úáúÇ
ßøõÈóÑóæ
úä~ ~óå ä~ó~~ö
áúÇ óäáóÚ )4
öäá~~~öÈ óäáóÚ
í
Þ1 Ú áÇ
ÉÑæÓ
DEDICACES
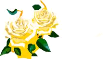
Comme symbole d'une profonde reconnaissance et d'une gratitude
égale, nous dédions ce modeste travail :
A NOS DEUX PLUS CHERS ETRES

Nos parents, qui nous ont accordé toute l'aide et le
soutien voulu, qui nous ont garanti un amour que nul n'oublie et nous ont
guidé avec leurs conseils intangibles dans la conception de notre
personnalité.
A NOS FRERES ET SOEURS

Auxquels nous devons, du fond du coeur, une profonde gratitude,
de nous avoir encouragé et nous avoir tendu mains fortes.
A TOUS NOS AMIS

Avec lesquels nous avons formé une équipe solide,
efficace et particulièrement, liée par une amitié
confiante que nous n'aurions garde d'oublier.
A TOUS NOS PROFESSEURS

A qui nous devons tout respect et hommage d'avoir
contribué à notre solide formation.
REMERCIMENTS
Il nous est agréable de nous acquitter d'une dette de
reconnaissance auprès de toutes les personnes, dont l'intervention au
cours de ce projet a favorisé son aboutissement.
Nous tenons à remercier toute personne qui a
participée de prés ou de loin à la réussite de ce
modeste travail et à la tête de ces personnes notre parrain
à la SAMIR Mr. A.REDOUEN qui nous a encadré d'une manière
permanente jusqu'à la fin de ce travail et nous a donné le temps
suffisant et les conseils favorisants afin de mener à bien ce travail,
Sa sympathie et sa modestie nous font la plus grande estime.
Nous tenons à remercier très sincèrement
notre encadrant à l'école Mr. M.FEDDAOUI qui nous a guidé
pour réaliser ce travail.
Nos plus vifs remerciements sont aussi adressés au
personnel de la Centrale Thermoélectrique II, et de la nouvelle
unité de cogénération, en particulier : Mr. JILALI, Mr.
ERRAKI et Mr. HOUACHMI
Nous tenons à remercier également Mr. FALLAH et Mr.
AZHARI qui nous ont facilité la tâche d'avoir passé notre
stage au sein de la SAMIR.
Nous remercions vivement Mr. CHAHID et Mr. FARKHANI pour l'aide
précieuse et les conseils qu'ils nous ont pas cessé de nous
prodiguer tout au long de l'élaboration de ce travail.
Que les membres de jury trouvent ici l'expression de notre
profonde estime et notre gratitude pour avoir accepté de juger notre
travail.
Résumé
Ce document constitue le rapport de notre projet de fin
d'étude effectué au sein de la Société Anonyme
Marocaine de l'Industrie du Raffinage (SAMIR) dont l'objectif est
l'optimisation de la facture énergétique de la raffinerie,
notamment électrique.
Dans un premier lieu, ce travail consiste en un diagnostic de
l'existant c'est-à-dire une analyse du système de production de
la vapeur dans la centrale thermoélectrique II, et de
l'électricité dans la nouvelle unité de
cogénération, et par conséquent la détermination,
sous forme de bilans matières et thermiques, des différents
paramètres qui caractérisent cette production
(Températures, pressions, débits, puissances,...) dans les
chaudières et la cogénération.
Ensuite, en se basant sur les résultats obtenus, on va
calculer les consommations spécifiques et les coûts de revient de
l'eau déminéralisée, de la vapeur et de
l'électricité.
Dans un deuxième lieu, ce travail va se focaliser sur
la détermination de la marche opératoire optimale de
l'unité de cogénération qui utilise la technologie de la
turbine à gaz associant une turbine à gaz de 40 MW à une
chaudière de récupération thermique des fumées
d'échappement de la turbine et pouvant générer prés
de 70 T/h de vapeur haute pression. Elle alimente en électricité
et en vapeur, les installations actuelles (ancienne raffinerie) et celles du
projet de modernisation (Up grade). Elle permet ainsi une réduction des
émissions des Gaz à Effet de Serre.
La raffinerie possède des équipements qui sont
particulièrement sensibles à la continuité absolue de leur
alimentation électrique. La SAMIR qui a un besoin absolu de s'en
prémunir contre toute coupure de l'énergie électrique
trouve dans la cogénération la sécurisation de
l'alimentation électrique de son site. En plus la SAMIR a conclu avec
l'ONE un contrat d'approvisionnement de l'électricité dont la
puissance souscrite est 17,1 MW. Faute de dépassement de cette
puissance, la SAMIR paie des pénalités qui rendent la facture
énergétique importante. L'optimisation de cette facture devient
donc indispensable.
Vers la fin on va pouvoir déterminer un optimum
économique en fonction de : - régime de marche optimale de la
cogénération.
- la nouvelle puissance souscrite.
- production optimale de la nouvelle turbine à vapeur.
Mots dles : Turbine A Gaz,
Cogénération, Chaudière, Turbine A Vapeur, Rendement,
Ratio, Facture Energétique, Puissance Souscrite, Bilan
énergétique, Cycle simple, Coût de
l'électricité
Abstract
This document is the report of our final project study carried
out in the Society Anonym Moroccan of Refining Industry (SAMIR) whose objective
is the optimization of the refinery's energy bill, including the electrical
one.
First of all, this work is a diagnosis of the existing which
means an analysis of the steam production system in thermal power plant II, and
electricity in the new cogeneration unit, and thus determining the form of
material balances and thermal parameters that characterize this production
(temperature, pressure, flow, power...) in boilers and cogeneration.
Then, based on the results obtained, we will calculate the
specific consumption and cost of dematerialized water, steam and
electricity.
Secondly, this work will focus on determining the optimal
surgical operation of a cogeneration unit that uses the combined cycle
technology combining a gas turbine of 40 MW at a heat recovery boiler flue gas
exhaust and turbine can generate almost 70 T / h high pressure steam. It
supplies electricity and steam, to the current facilities (former refinery) and
the project of modernization. It allows a reduction in emissions of Greenhouse
Gases.
The refinery has facilities that are particularly sensitive to
the absolute continuity of supply. SAMIR has an absolute need to protect them
against any interruption of electricity cogeneration is in insuring the power
of its site. In addition SAMIR concluded a convention with ONE which will
supply a 17.1 MW of electricity power. In case of exceeding this power, SAMIR
pay penalties that make the energy bill greater. The optimization of this bill
becomes crucial.
By the end we will be able to determinate an economic optimum in
terms of : - Operating conditions of cogeneration.
- The new contract power.
- Optimal production of new steam turbine.
Keywords: Gas turbine, Cogeneration, Boiler,
Steam turbine, Yield, Ratio, Energy Bill, Contract power, Energy Balance,
Simple cycle, Cost of electricity
Table des matières
Dédicace 2
Remerciements 3
Résumé - Abstract 4
Liste des figures 9
Liste des tableaux 11
Liste des annexes 12
Nomenclature 13
Introduction générale 15
Chapitre I : Présentation de la SAMIR
17
I. Localisation géographique 18
II. Historique et création 18
III Secteur d'activité 20
III-1. Activité 20
III-2. Produits 20
IV. Structure organisationnelle 21
IV-1. Conseil d'administration 21
IV-2. Organigramme 22
V. Description des projets récents 23
V-1. Projet Upgrade 23
V-2. Projet de cogénération 24
V-3. Topping 4 25
Chapitre II: Généralités sur les
chaudières et la cogénération 26
I. Généralités sur les chaudières
27
I-1. Généralités sur le combustible (fuel
n°2) 27
I-2. Généralités sur la combustion 28
I-3. Généralités sur les chaudières
30
I-3-1. Description et principe de fonctionnement des
chaudières 30
I-3-2. Caractéristiques principales des
générateurs 31
I-3-3. Appareils complémentaires 32
I-3-4. Les circuits des chaudières 34
II Généralités sur la
cogénération 36
II-1. Définition de la cogénération 36
II-2. Principe de la cogénération 36
II-3. Les types d'installations 36
II-3-1. Turbine à vapeur 37
II-3-2. Turbine à gaz 37
II-3-3. Moteur à combustion interne (gaz ou diesel) 38
II-3-4. Cycle combiné: turbine à gaz + turbine
à vapeur 39
II-3-5. La trigénération 39
II-4 Etude comparative des différentes technologies 40
Chapitre III : Fonctionnement de la CTE II et de
l'unité de cogénération 41
I. La centrale thermoélectrique II (GTE II) 42
I-1. Introduction 42
I-2. Différentes unités de la CTE II 42
I-3. Chaudières de la CTE II 44
I-3-1. Production de la vapeur haute pression 44
I-3-2. Production de la vapeur moyenne pression 45
I-3-3. Production de vapeur basse pression 45
I-3-4. Production de vapeur très basse pression 45
II. L'unité de cogénération de la SAMIR
47
II-1. Introduction 47
II-2. Architecture de l'unité 47
II-3. Fonctionnement de l'unité de
cogénération 48
II-3-1. Le groupe turboalternateur 48
II-3-2. Chaudière de récupération 50
II-3-3. Circuit (Eau /vapeur) 51
II-3-4. Circuit diesel 51
II-3-5. Le Groupe électrogène 52
Chapitre IV : Calcul des consommations spécifiques
et des Coûts de revient des utilités 53
I. Méthodologie de calcul 54
I-1. Définition 54
I-2. Coût variable et coût fixe 54
II. Goûts de revient des utilités dans la
Gentrale thermoélectrique II 54
II-1. Coüt de revient de l'eau
déminéralisée 55
II-2. Coüt de revient de l'air comprimé 56
II-3. Calcul du coût de revient de la vapeur 58
II-3-1. Modélisation du système de production 58
II-3-2. Calcul du coût variable de production 58
II-3-3. Calcul du coût fixe de production 61
II-3-4. Coût de revient de la vapeur HP 62
III Coûts de revient de l'électricité et
de la vapeur HP dans l'unité de cogénération 64
III-1. Introduction 64
III-2. Prix d'achat d'électricité 64
III-3. Coüt de revient de l'électricité et la
vapeur produite par l'unité de cogénération 65
III-3-1. Méthodologie de calcul 65
III-3-2. Calcul du coût de revient de la vapeur et de
l'électricité (méthode I) 66
III-3-3. Calcul du coût de revient
l'électricité (méthode II) 70
III-3-4. Synthèse et interprétation 73
IV. Conclusion 74
Chapitre V : Etude des différents scénarios
IHOMMEMIUnMB'pOLMIEBpC dans la raffinerie & détermination de la
nouvelle puissance souscrite 75
I Détermination de la marche opératoire
optimale de l'unité de cogénération 76
I-1. Influence de la température ambiante 76
I-2. Influence de la qualité d'air 78
I-3. Influence du facteur de puissance Cos á 79
I-4. Marche optimale de la cogénération 81
II. Différents scénarios de distribution
d'électricité dans la raffinerie 84
II-1. Consommations des unités 84
II-2. Différents scénarios de distribution
d'électricité 84
III. Détermination de la nouvelle puissance souscrite
86
III-1. Rappel du contrat ONE-SAMIR 86
III-2. Dépassement de puissance souscrite 88
III-3. Détermination de la nouvelle puissance souscrite
90
Chapitre VI : $ P pOULDiUnsASN IX WP
HCBSIUdARiUMEd'pOMI .. 92
I. Introduction 93
II. Amélioration du système de production de
la vapeur 94
II-1.Diagnostic des chaudières 94
II-2.Dimensionnement d'un échangeur de
préchauffage de l'eau de chaudières 103
III. Calcul technico-économique de la turbine
à vapeur 110
III-1.Justification du projet 110
III-2. Calcul de la turbine à vapeur 111
III-3. Estimation économique du projet 116
III-4. Implantation du projet 118
IV. Amélioration de la cogénération
119
IV-1.Changement des filtres de gazoline 119
IV-2 Lavage off-line 119
V. Mise en place du système de délestage
121
V-1. Les unités à délester en cas de
coupure d'électricité 121
V-2. Intérêt économique du délestage
124
Conclusion générale 126
Références bibliographiques 127
Annexes 128
Biographie des auteurs 140
Liste des figures
Figure 1.1 : Localisation de la SAMIR sur la carte
géographique 18
Figure 1.2 : Répartition de la production de la SAMIR 2008
21
Figure 1.3 : Organigramme de la SAMIR 2008 22
Figure 1.4 : Répartition de production avec le nouveau
projet UPGRADE 23
Figure 2.1 : Chaudières à tubes de fumées
30
Figure 2.2 : Chaudières à tubes d'eau 31
Figure 2.3 : Ballon supérieur 33
Figure 2.4: Surchauffeur 33
Figure 2.5 : Circuit Eau/Vapeur 34
Figure 2.6 : Descriptif du circuit de l'air et des fumées
35
Figure 2.7 : Principe de la cogénération 36
Figure 2.8 : Cogénération par Turbine à
vapeur 37
Figure 2.9 : Cogénération par Turbine à gaz
38
Figure 2.10 : Cogénération par Moteur à
combustion interne 38
Figure 2.11 : Cogénération par cycle combiné
39
Figure 3.1 : Schéma de la centrale thermoélectrique
II 42
Figure 3.2 : Schéma de la production d'air comprimé
43
Figure 3.3: Système de réception et de distribution
de la vapeur dans CTE II 46
Figure 3.4 : Vue général de l'unité de
cogénération 48
Figure 3.5 : Schéma d'une Turbine à gaz simple
49
Figure 3.6: Chaudière de récupération 50
Figure 3.7: Parcours de l'eau et des fumées dans la
chaudière de récupération 51
Figure 4.1: Schématisation de la station de
déminéralisation d'eau 55
Figure 4.2 : Schéma de production d'air comprimé
56
Figure 4.3: Système de production de la vapeur haute
pression dans la CTE II 58
Figure 4.4: Augmentation du coût de la vapeur HP (Dh/T)
63
Figure 4.5: Système de production dans l'unité de
cogénération 65
Figure 4.6: production de la VH dans la chaudière de
récupération 66
Figure 4.7: Coût de la vapeur HP pour les différents
régimes de cogénération 68
Figure 4.8: Système de production
d'électricité dans l'unité de cogénération
68
Figure 4.9: Coüt de l'électricité pour les
différents régimes de cogénération 70
Figure 4.10: Coût de production d'électricité
en fonction de la puissance produite 73
Figure 5.1: Variation des différentes productions en
fonction de la température ambiante 77
Figure 5.2: Détérioration des performances de la
turbine à gaz en raison d'un encrassement
des aubes du compresseur 78
Figure 5.3: Variation du facteur de puissance Cos á en
fonction de la puissance réactive 80
Figure 5.4: Variation du coüt de production
d'électricité en fonction de la puissance active 81
Figure 5.5: Evolution des charges totales
d'électricité en fonction du régime de la
cogénération 82 Figure 5.6: Facture électrique en 2009
et 2010 en fonction du régime de marche de la
cogénération 83
Figure 5.7: Principe de tarification de
l'électricité (ONE) 87
Figure 6.1 : Analyse PARETO de défaillances des
éléments de la chaudière A 95
Figure 6.2 : Analyse PARETO de défaillances des
éléments de la chaudière B 95
Figure 6.3 : Analyse PARETO de défaillances des
éléments de la chaudière C 96
Figure 6.4 : Analyse PARETO de défaillances des
éléments de la chaudière D 97
Figure 6.5 : Dégradation des éléments
concernés 98
Figure 6.6 : Suivi de pourcentage d'Oxygène pour la
chaudière A 100
Figure 6.7 : Variation du point de rosée en fonction du
pourcentage de SO3 101
Figure 6.8 : Economiseur en bon état et Economiseur
encrassé 101
Figure 6.9 : Suivi de la température entrée
économiseur pour les quatre chaudières 102
Figure 6.10 : principe de fonctionnement et bilan
énergétique de l'échangeur de chaleur avec
l'eau chaude sortant de l'économiseur 105
Figure 6.11: Répartition de la consommation de vapeur HP
112
Figure 6.12: Processus de production d'une turbine à
vapeur 113
Figure 6.13: Point d'entrée et de sortie de la turbine sur
les diagrammes (T-S) et (H-S) 115
Figure 6.14: Degré d'autonomie électrique 116
Figure 6.15: Implantation de la turbine à vapeur 118
Liste des tableaux
Tableau 1.1 : Principaux fournisseurs de la SAMIR 20
Tableau 2.1: Etude comparative des technologies de
cogénération 40
Tableau 4.1 : Matières premières consommées
dans la production de l'eau déminéralisée 55
Tableau 4.2 : Consommations spécifiques pour production de
l'eau déminéralisée 55
Tableau 4.3: Calcul du coüt de l'eau
déminéralisée 56
Tableau 4.4: Cout de l'air de service 57
Tableau 4.5: Coüt de l'air instrument 57
Tableau 4.6 : Quantités de matières
premières consommées pour la production de la vapeur 59
Tableau 4.7 : Dosage et densité du Nalco 59
Tableau 4.8: Consommation horaire de l'énergie
électrique dans les chaudières 60
Tableau 4.9: Consommation d'air comprimé dans les
chaudières 60
Tableau 4.10: Coût variable de production de vapeur HP
61
Tableau 4.11: Coût de maintenance dans le système de
production de vapeur HP (2009) 61
Tableau 4.12: Coût de production de vapeur HP (2009) 62
Tableau 4.13: Données de base pour le calcul du Coût
VH cogénération 67
Tableau 4.14: Coût de revient de la vapeur HP dans la
cogénération 68
Tableau 4.15: Consommations de matières premières
pour la génération électrique 69
Tableau 4.16: Coût de revient de
l'électricité dans la cogénération 69
Tableau 4.17: Coûts de matières premières de
la cogénération 71
Tableau 4.18: Coüts de l'électricité pour les
différents régimes de marche de cogénération 71
Tableau 5.1: Variation des paramètres
caractéristiques de la cogénération en fonction de la
température ambiante 76
Tableau 5.2: Variation du facteur de puissance Cos á en
fonction de la puissance réactive 80
Tableau 5.3: Facture électrique de la raffinerie pour
différents régimes de cogénération 82
Tableau 5.4: répartition de la consommation
électrique des unités de la SAMIR 84
Tableau 5.5: Postes horaires pour la tarification
d'électricité 88
Tableau 6.1 : défaillances des éléments dans
les quatre chaudières A 94
Tableau 6.2 : défaillance des éléments de la
chaudière B 95
Tableau 6.3 : défaillance des éléments de la
chaudière C 96
Tableau 6.4 : défaillance des éléments de la
chaudière D 96
Tableau 6.5 : suivie du rendement de la chaudière 103
Tableau 6.6 : Données des fluides chaud et fraoid 106
Tableau 6.7 : Calcul du ÄTLM et Us 106
Tableau 6.8 :.Caractéristiques des faisceaux tubulaires
107
Tableau 6.9 : Caractéristique de la calandre 107
Tableau 6.10 : Pertes de charges à l'intérieur et
l'extérieur des tubes 107
Tableau 6.11 : les résistances d'encrassement 108
Tableau 6.12 : Compléments de vapeur à fournir aux
unités Upgrade 111
Tableau 6 .13 : Estimation des charges annuelles de maintenance
117
Tableau 6.14: Unités à délester dans
l'ancienne raffinerie SAMIR 122
Tableau 6.15: Pompes à délester dans le
système de stockage (réservoirs) 122
Tableau 6.16: Ordre de priorité de délestage dans
le nouveau projet UPGRADE 123
Liste des annexes
Annexe 1 : Vue générale de l'unité de
cogénération 127
Annexe 2 : Caractéristiques des moteurs de la
cogénération 128
Annexe 3 : Les unités de la SAMIR 129
Annexe 4 : Diagnostique des chaudières A,B,C et D de la
centrale II 131
Annexe 5 : Méthodologie de dimensionnement de
l'échangeur de chaleur 132
Annexe 6 : Cycle thermodynamique de HIRN 137
Annexe 7 : Capacités de production et consommation de la
vapeur dans la raffinerie 138
Nomenclature
A : air d'échange.
AFNOR : Association française de normalisation.
BP : Basse Pression.
CTE II : Centrale Thermo-Electrique II.
CCI : Corps Cylindrique Inférieur.
CCS : Corps Cylindrique Supérieur.
Cos ö : facteur de puissance. DH: Dirham.
ED: Eau déminéralisée. EE : Energie
électrique. Ec : L'énergie cinétique.
Ep : L'énergie potentielle. É : coefficient
de correction des prix.
F : facteur de correction (échangeur).
GAT: Groupe Turboalternateur (Turbine+Alternateur).
GE : Général électrique.
h : coefficient d'échange convectif.
hp : Heures de pointe. hpl : Heures pleines.
hc : Heures creuses.
HP : Haute Pression. H : Enthalpie.
KW: Kilowatt (Puissance). KWh: Kilowatt-hour (Energie).
m2 : Mètre Carré.
m3 : Mètre Cube.
MP: Moyenne Pression. MW: Mégawatt (Puissance). MDH:
Million de dirham. MMDH : Milliard de dirham.
Ntt : nombre de tube total (échangeur).
Nu : nombre de Nusselt.
ONE : Office Nationale d'Electricité.
ppm : partie par million, unité de concentration des
composées.
Pr : nombre de Prandtl.
P : puissance électrique produite par la TAG.
PCI : pouvoir calorifique inférieur.
PCS : pouvoir calorifique supérieur.
Q: puissance thermique.
rpm : roue par minute, nombre de rotation de l'arbre d'un
moteur.
R : rendement de la chaudière.
Ra : Ratio de la chaudière.
Re : nombre de Reynolds.
SAMIR : Société Anonyme Marocaine de l'Industrie du
Raffinage.
S : Entropie.
SHT : Surchauffeur haute pression. SBT : Surchauffeur basse
pression. t : température.
TAG : turbine à gaz.
T: Tonne.
UPGRADE : projet de modernisation de la SAMIR.
U : L'énergie interne.
Us : coefficient d'échange global.
V : vitesse de fluide.
VH : Vapeur Haute Pression.
VM : Vapeur Moyenne pression. VB : Vapeur Basse pression.
VBB : Vapeur plus Basse pression.
W : puissance mécanique.
u : Rendement isentropique du groupe turboalternateur.
ô : Rendement Mécanique-électrique du groupe
turboalternateur.
€ : Euro = 11,5 DH.
$ : Dollars = 8,9 DH.
ñ : masse volumique.
ë : conductivité thermique.
ÄTLM : différence de température moyenne
logarithmique.
ÄP : perte de charge.
Introduction générale
Dans un environnement marqué
par la mondialisation, l'évolution, la concurrence, la complexité
et la rapidité des exigences du marché, les entreprises doivent
faire preuve de dynamisme pour s'adapter rapidement et en souplesse aux
nouvelles exigences et savoir saisir les opportunités. Soucieux
d'améliorer la qualité des produits, d'optimiser le potentiel de
production, de réduire les coûts, de moderniser les installations,
de conforter sa position sur le marché et de répondre aux besoins
des clients, la société SAMIR mène en continue plusieurs
projets de modernisation et de développement pour s'engager dans une
démarche d'optimisation énergétique globale dont
l'objectif est de rationaliser la consommation, maîtriser la facture
énergétique et par la suite diminuer les coûts de revient
des utilités et du produit fini et ainsi augmenter la marge de gain de
l'entreprise.
Ainsi, l'objectif de ce travail s'inscrit dans l'optique de
l'optimisation de la facture énergétique de la raffinerie et
l'amélioration de la production d'énergie notamment de la vapeur
et de l'électricité. Ce stage est effectué au sein de la
centrale thermoélectrique II qui est le coeur battant de la
société et qui alimente les différentes unités en
utilités (vapeur VH, VM, VB, VBB, électricité, eau
déminéralisée, air comprimé et air instrument,
azote...)
Le présent travail consiste en premier lieu, au calcul
des consommations spécifiques pour la production des utilités
(eau déminéralisée, vapeur HP et
électricité), ainsi l'évaluation des coûts de
revient de la vapeur haute et moyenne pression dans la centrale
thermoélectrique II, et de l'électricité dans
l'unité de cogénération. Ensuite, en se basant sur les
résultats obtenus, on va déterminer la puissance de marche
optimale de l'unité de cogénération qui permettra un
coût de revient minimal d'électricité et de vapeur produite
par la cogénération et un gain maximal sur la facture
énergétique tout en maximisant le degré d'autonomie
électrique.
En deuxième lieu ce projet vise à
déterminer la nouvelle puissance souscrite à souscrire avec
l'ONE. En effet une partie d'alimentation en énergie électrique
pour la SAMIR est assurée actuellement par l'ONE avec un contrat
d'approvisionnement dont la puissance souscrite est de 17.1
MW. C'est la puissance qui sera tenue à la disposition de la SAMIR en
permanence.
Lorsque l'on dépasse cette puissance souscrite, l'ONE
continue de fournir à la SAMIR ce surplus de puissance en la facturant
à un tarif plus élevé plus une prime fixe proportionnelle
à la puissance souscrite.
Au démarrage du projet UP GRADE (projet de
modernisation de la raffinerie SAMIR), le besoin en énergie
électrique est multiplié, actuellement, il est de l'ordre de 44
MW. Une partie (28 MW) est produite par l'unité de
cogénération, et le complément restant (16 MW) est
acheté de l'ONE. D'où la nécessité de bien
identifier la fourchette d'utilisation optimale de l'installation de
cogénération, sachant que cette dernière permet de
produire une puissance de 40 MW mais dans des conditions bien
spécifiées, ainsi déterminer la puissance souscrite
optimale à spécifier dans le nouveau contrat avec l'ONE.
En bref, les objectifs principaux de ce projet sont :
1- Déterminer la facture énergétique de
l'entreprise dans l'état présent.
2- Proposer quelques améliorations pour réduire
cette facture.
3- Evaluer l'opportunité d'ajouter une turbine à
vapeur produisant de l'électricité et de la vapeur VM.
4- La mise en place du système de délestage.
Ce mémoire est organisé selon les lignes directives
suivantes :
Chapitre I : Un aperçu
général sur la Société Anonyme Marocaine de
L'Industrie du Raffinage (SAMIR).
Chapitre II : Une étude
bibliographique sur les différents thèmes traités dans
cette mémoire, il est consacré aux connaissances de bases
nécessaires sur les chaudières et les techniques de
cogénération.
Chapitre III : Une étude du
fonctionnement de la centrale thermoélectrique II et l'unité de
cogénération. Il comprend une description des
procédés utilisés, les principes de fonctionnement ainsi
que quelques caractéristiques techniques des installations pour mettre
en évidence les éléments nécessaires au chapitre
suivant.
Chapitre IV : Calcul des consommations
spécifiques et des coûts de revient de la vapeur et de
l'électricité dans la centrale thermoélectrique II et
l'unité de cogénération, ainsi la détermination de
la marche opératoire optimale de l'unité de
cogénération.
Chapitre V : Etude des différents
scénarios de distribution de la vapeur et de l'électricité
dans la raffinerie et détermination de la nouvelle puissance souscrite
en se basant sur la production de deux cogénération, la turbine
à gaz et la turbine à vapeur, ainsi que sur la puissance fournie
par l'ONE.
Chapitre VI : propositions de solutions pour
la démarche d'optimisation, ainsi dans ce chapitre on va calculer les
caractéristiques techniques de la nouvelle turbine à vapeur, la
mise en place d'un système de délestage, et les systèmes
d'amélioration de production.
Chapitre I : Présentation de la SAMIR
- Aperçu général sur la SAMIR.
- Sa création.
- Ses activités et produits.
- Sa structure hiérarchique.
- Ses projets récents et en cours de
réalisation.
I.
Localisation géographique
La Société Anonyme Marocaine de l'Industrie du
Raffinage (SAMIR) s'étend sur une superficie de 200 hectares à la
zone ouest de la ville Mohammedia à proximité du port dans
l'objectif de faciliter la réception du pétrole brut
importé. Elle est reliée par un réseau de pipeline au port
pétrolier (distant de 5km) ainsi qu'au dépôt de stockage
des sociétés de distribution et à la centrale ONE (Office
Nationale d'électricité).
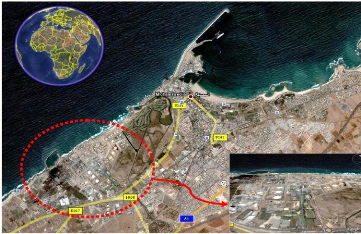
Figure 1.1: Localisation de la
SAMIR sur la carte géographique
II. Historique et création
La première raffinerie qui a été
construit au Maroc est la société chérifienne de
pétrole (SCP) en 1929 à Sidi Kacem. Après
l'indépendance, ce dernier n'a pas pu satisfait les besoins
énergétiques de plus en plus importants du pays, il a fallu donc
construire une 2ème raffinerie plus proche d'un port. C'est ainsi que
fut décidé la création de la SAMIR.
Cette dernière naquit d'une convention signée en
1959 entre l'Etat Marocain représenté par « le bureau des
études et des participations industrielles » et l'office italien
des hydrocarbures « centre national des hydrocarbures ». Cette
raffinerie nouvellement crée a pris la dénomination de «
Société Anonyme Marocaine Italienne de raffinage » qui a
changé sa raison sociale après la marocanisation de son capital
en 1973 pour devenir la « société Anonyme de l'Industrie du
Raffinage ».
1959
|
Création de la SAMIR (Société Anonyme
Marocaine et Italienne de Raffinage) par l'Etat Marocain,
représenté par le Bureau des Etudes et des Participations
Industrielles (BEPI) et l'Office Italien des Hydrocarbures (Ente Nazionale
Idrocarbur ENI) en joint venture avec la compagnie AGIP. Construction de la
première unité de distillation de pétrole brut à
Mohammedia d'une capacité de 1,25 million de tonnes par an.
|
1960
|
le souverain Feu Mohammed V pose la première pierre de la
raffinerie, le 25 juin 1960.
|
|
Projet de Fin d'Etudes
|
|
|
1973 Marocanisation de la société
qui devient une entreprise entièrement étatique
; l'Etat rachète les parts détenues par les
Italiens.
1996 Mise en bourse de 30% du capital.
1997 Privatisation et transfert de 67,27% du
capital au groupe Corral.
1999 Fusion-absorption de la SCP
(Société chérifienne des pétroles) par Samir.
2003 Création de la FONDATION SAMIR.
Fin 2004 Corral s'engage à moderniser la
SAMIR, un investissement dont l'enveloppe
global s'élève à plus de 6 milliards de
dirhams. Cette convention a fait l'objet de la signature d'une convention de
mise à niveau entre l'Etat marocain et la
Sept 2005 Démarrage officiel des travaux
de modernisation de la raffinerie de
Mohammedia. Avec un coût global de plus de 1 milliard de
dollars, ce projet permettra à la SAMIR d'introduire les technologies
les plus récentes dans le domaine du raffinage, à même de
lui permettre de satisfaire les besoins futurs du marché national en
carburants propres, respectueux de l'environnement, notamment le gasoil 10 ppm
et 50 ppm et l'essence sans plomb, globalement conformément aux normes
européennes.
Juillet 2006 Signature projet de construction de
l'unité de cogénération d'une puissance de 40 MW.
Février 2008 Signature d'un contrat de
partenariat avec Shell Global Solutions portant sur l'assistance technique et
le transfert de technologies et de savoir faire dans le domaine du
raffinage.
Juillet 2008 Signature d'un contrat de 17
millions d'euros avec la Société Espagnole Tecnicas Reunidas
portant sur les études d'ingénierie et de conception du projet de
remplacement des anciennes unités de distillation (Topping 1 et 2) de la
raffinerie de Mohammedia, par une nouvelle unité (Topping 4) d'une
capacité annuelle de 4 millions de tonnes.
2008 Création de la société
TSPP, filiale à 100% de la SAMIR, ayant pour mission
le transport et stockage des produits pétroliers.
Juin 2009 Démarrage de l'unité de
cogénération.
Mars 2010 Démarrage du projet UPGRADE de
modernisation de la SAMIR
III. Secteur d'activité III.1.
Activité
L'activité principale de la SAMIR est le raffinage du
pétrole Outre cette activité de base, la SAMIR est
présente aussi dans les domaines des GPL (Gaz de pétrole
Liquéfiés) et dans la logistique d'approvisionnement et de
distribution grace à sa participation dans le capital des
sociétés SALAM-GAZ (50%), SOMAS (38%) et TSPP (100%).
Les principaux fournisseurs sont regroupés dans le tableau
ci-dissous : Tableau 1.1 : Principaux
fournisseurs de la SAMIR
Pays
|
Société
|
Arabie Saoudite
|
Arabian light
|
Irak
|
Kirkuk
|
Iran
|
Iranien light
|
Russie
|
Ural
|
III.2. Produits
La SAMIR élabore 12 produits à partir du
pétrole brut dont les capacités de production sont variables et
relative à l'importance de produit, on trouve principalement :
Propane, Butane, Super Sans Plomb, Jet A1, Gasoil 50 ppm
(à partir de Septembre 2009), Fioul Oil, Huile de Base 150 NS, Huile de
Base 300 NS, Huile de Base 600 NS, Huile de Base BSS, Bitumes, Paraffines.
? Capacité de Raffinage : 7,75 millions
tonnes
? Capacité de Stockage: > 2 millions
de m3
v' 1 million de m3 de pétrole brut
v' 1 million de m3 de produits finis
? Effectif : près de 1200 personnes
> Exportations : 20 à 25% de la
production
> Configuration : raffinerie complexe avec un
facteur Nelson de 14.
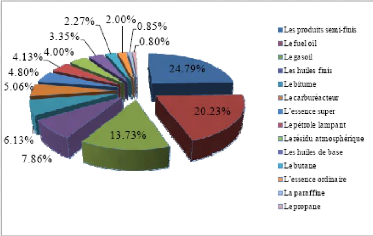
Figure 1.2: Répartition de
la production de la SAMIR 2008
IV. Structure organisationnelle IV-1. Conseil
d'administration
Président : Sheikh Mohammed Hussein
AL-AMOUDI
Membres du Conseil :
Docteur GHAZI Mahmud HABIB
M. Bassam ABURDENE M. Mustapha AMHAL
M. Jamal Mohammed BA-AMER
M. Mohammed Hassan BENSALAH
M. Lars NELSON
M. John P. OSWALD M. George SALEM
M. Lennart WIKSTRÖM
Comité de Direction Membres :
M. Jamal BA-AMER, Directeur Général
M. Rachid BENNOUNA, DGA Administration et Finance
M. Ulf JANSON, DGA Approvisionnement, Ventes et Distribution
Directeurs Relevant de la Direction
Générale :
M. AbdulkaderBahajri : - Projet Upgrade & Grands Projets
M. Youssef Belkhadir :
M. Ahmed Chakib :
M. Abdelmounim El Yaalaoui : M. Ahmed Harnouch :
M. Abdelkrim Lamssafri :
M. Sidi Mohammed Meliani :
- Achats& Contrats
- Ingénierie & Intégration Upgrade - Audit
& Systèmes de Gestion
- Stratégie & Coordination
- Hygiène & Sécurité- Infrastructures
& Affaires Générales
Direction Générale Adjoint Raffinage
:
Mme Maria Charaf :
M. Mohamed Gajjaoui : M. Abdelhafid Kodade : M. Abdellatif
M'Haïdra : M. Hmida M'Hamdi :
- Qualité- Maintenance
- Raffinerie Sidi Kacem - Production
- Services Techniques
IV-2. Organigramme
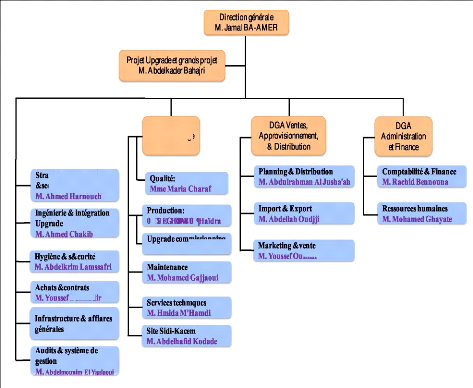
rection générale
DGA Ventes
Adm
a
Blkliaéd
Projet Upgrade et gra M Abdelkader B
Figure 1.3 : Organigramme de la
SAMIR 2009
V. Description des projets récents V-1. Projet
Upgrade
Considéré comme étant la plus grande
réalisation que l'industrie nationale du raffinage ait connu depuis la
création du complexe SAMIR des huiles lubrifiantes en 1984, le projet de
modernisation de la raffinerie de Mohammedia intègre tous les
éléments de la stratégie pétrolière
nationale, telle que définie par les Hautes Directives Royales du 4 mai
2004, et englobe les technologies les plus modernes et les
procédés les plus performants dans le domaine du raffinage.
Ce projet, qui a démarré en septembre 2005, fait
partie intégrante du programme général de modernisation de
la raffinerie de Mohammedia, ayant fait l'objet de la Convention
d'Investissement signée le 20 décembre 2004 entre le Gouvernement
Marocain et la SAMIR. Le budget global y afférent est estimé
à plus de 1 milliard de Dollars US.
Intérêt du Projet :
Compte tenu de sa taille et de sa nature, la
réalisation de ce projet aura des répercussions positives sur
l'économie nationale et sur la société. Il permettra
d'adapter la configuration de la raffinerie à la structure de la demande
nationale en augmentant la production de gasoil. Il aura aussi un impact
très positif sur la protection de l'environnement et
l'amélioration de la qualité de l'air par la production de
carburants propres, notamment : le Gasoil: 50 et 10 ppm, conforme à
l'Euro 4 et 5 ainsi que l'Essence Super sans plomb, conforme à l'Euro
3.
Le projet permettra également, à la
société, d'atteindre un niveau de compétitivité en
ligne avec celui des raffineries européennes modernes.
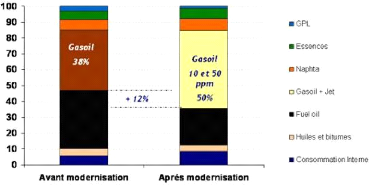
Figure 1.4 : Répartition
de la production avec le nouveau projet UPGRADE
Phases du projet
Phase1: Production gasoil 50 ppm démarrée en
Septembre 2009.
Phase2: Mise en service effective du complexe hydrocraking en
mars 2010.
Budget :
Budget initial : 6 milliards DH (à la signature de la
convention)
Budget actuel : près de 13 milliards DH
Paiements : 8.2 milliards DH
Augmentation due au coüt de l'énergie, de la
matière première et inflation, de la main d'oeuvre et à
l'appréciation de l'Euro face au US dollar et au Dirham.
V-2. Projet de cogénération
La SAMIR a conclu avec la Société LITWIN France
un contrat d'une valeur de 32 Millions d'euros (350 MDH) portant sur la
réalisation d'une unité de cogénération d'une
puissance de 40 MW dans l'enceinte de la raffinerie de Mohammedia.
La nouvelle unité utilisera la technologie des cycles
combinés associant une turbine à gaz GENERAL ELECTRIC de 40 MW
à une chaudière de récupération thermique des
fumées d'échappement de la turbine et pouvant
générer prés de 70 T/h de vapeur haute pression. Elle
permettra d'alimenter en électricité et en vapeur, les
installations actuelles et celles du projet de modernisation.
Apports du projet
Ce projet qui a démarré en 2009 et qui alimente
le réseau électrique de la raffinerie avec 28 MW et de la vapeur
VH 50 T/h permet de répondre aux exigences les plus strictes en
matière de sécurité et d'environnement et garantit
à la raffinerie une alimentation électrique fiable. La centrale
de cogénération est actuellement opérationnelle et
alimente la raffinerie en énergie éclectique.
Ce projet présente de multiples avantages :
· Coüt d'investissement et besoins en utilité
plus réduits par rapport à ceux d'une centrale classique
· Meilleur rendement énergétique
· Meilleur respect de l'environnement répondant
ainsi aux exigences de la Banque Mondiale
De plus, l'unité sera dimensionnée pour
être opérée soit au diesel, durant les premières
années de service, soit au gaz naturel, une fois ce dernier accessible.
L'utilisation du diesel contenant 1% de soufre au lieu du fuel-oil qui en
contient 3,6 %, assurera une amélioration considérable de la
qualité de l'air à l'échelle locale et régionale
à travers la réduction des émissions en SO2 d'environ 1500
tonnes par an.
V-3. Topping 4
Remplacement des anciennes unités de distillation par des
nouvelles (Topping 4) Intérêt et objectif du projet
Avec l'initiation du projet de remplacement des anciennes
unités de distillation du Topping 1 et 2 de la raffinerie de Mohammedia
par une nouvelle unité (Topping 4), la SAMIR réaffirme son
adhésion totale à la concrétisation des actions de la
Stratégie Energétique Nationale et son engagement à la
modernisation de l'industrie nationale du raffinage et au développement
de l'économie nationale exposée à Sa Majesté le Roi
Mohamed VI, que Dieu le glorifie, par la Ministre de l'Energie, des Mines, de
l'Eau et de l'Environnement le 08 juillet 2008 à Oujda.
Description du projet
La SAMIR et la société espagnole Tecnicas
Reunidas ont signé, mardi 29 juillet 2008, un contrat d'un montant de 17
millions d'Euros, portant sur les études d'ingénierie et de
conception du projet de remplacement des anciennes unités de
distillation (Topping 1 et 2) de la raffinerie de Mohammedia, par une nouvelle
unité (Topping 4) d'une capacité annuelle de 4 millions de
tonnes.
Budget du projet
La construction de cette unité nécessitera un
budget d'environ 120 millions d'Euro et sera opérationnelle en
début 2011.
Par ailleurs, la SAMIR a obtenu l'accord de principe pour le
financement de ce projet par l'Agence Espagnole de la Promotion des
Exportations, dans le cadre de la coopération Marocco-Espagnole.
Apport du Projet
Cet investissement qui s'intègre dans le programme global
de modernisation de la raffinerie de Mohammedia, vise essentiellement :
· Le maintien de la capacité annuelle nationale de
raffinage de 8,5 millions de tonnes,
· La satisfaction de la demande en fioul,
· La réduction du déficit structurel en
gasoil,
· L'amélioration de l'efficacité
énergétique,
· L'amélioration de la qualité de l'air par
l'utilisation de technologies de pointe.
Chapitre II: Généralités sur les
chaudières et la cogénération
- Généralités sur les chaudières, la
combustion et le fuel 2. - Généralités sur la
cogénération.
- Etude comparative des technologies de
cogénération.
I. Généralités sur les
chaudières
La production de la vapeur nécessite une
quantité de chaleur suffisante pour transformer l'eau d'alimentation en
vapeur. Le combustible utilisé est le fuel lourd n°2. Une
description de ses caractéristiques, de celles de la combustion et des
chaudières fera l'objet de ce chapitre.
I.1- Généralités sur le
combustible (fuel n°2) La viscosité :
La viscosité est la propriété physique
principale qui différencie les fuels, pour l'utilisateur d'une
installation de chauffage de fuel, elle a une relation direct avec les
conditions d'écoulement dans les diverses tuyauteries Elle traduit les
phénomènes de cohésion ou de frottement entre
molécules, ainsi que les conditions hydrodynamiques d'écoulement,
elle est aussi prise en compte dans la pulvérisation du fuel.
Densité
La densité est une caractéristique de fioul,
utilisée pour évaluer les possibilités calorifiques d'un
stockage ou pour établir des bilans thermiques, ainsi que pour expliquer
les anomalies de consommation.
Cette caractéristique présente l'avantage
d'être peu sensible à la variation de la température.
La chaleur massique
La connaissance de cette caractéristique du combustible
est indispensable pour mener à bien les calculs de réchauffage,
elle varie en fonction de la densité et de la température.
La teneur en soufre
Le fuel lourd se répartis en trois classes, selon leur
teneur en soufre (4, 2et 1 % en masse).
- le fioul n°2 de 3% à 4%
- le fioul n°2 de qualité dite BTS de 1% à 2%
- le fioul n°2 de qualité dite TBTS* =1%
La présence de soufre est surtout gênante en
raison des émissions d'anhydride sulfureux (SO2). Il est
également une source potentielle de corrosion, si des précautions
ne sont pas prises dans la mise en oeuvre des installations industrielles.
Inflammabilité (Point d'éclair)
L'inflammabilité ou point d'éclair correspond
à la température maximale à laquelle un combustible
liquide peut être réchauffé sans risque d'explosion ou
d'incendie. C'est un critère de sécurité lors des
opérations de stockage et de distribution pour le fuel n°2 le point
d'éclair est égal à 70°C.
Point de combustion ou point de feu
Le point de combustion exprime la température à
laquelle le fuel doit être porté pour que, après
l'inflammation, la combustion se poursuive sur toute la surface du liquide
pendant au moins cinq secondes. Il se détermine toujours en vase ouvert
et il se situe toujours au dessus du point d'éclair (différence
de l'ordre de + 10°C).
Composition chimique du fuel n°2
Le fuel n°2 provient de la distillation du
pétrole brute. Les proportions de carbone et d'hydrogène dans les
fiouls varient très peu, la valeur moyenne des composantes du fuel
utilisé au Maroc est donnée ci--après :
o Carbone.................................................
|
85,8%
|
o
Hydrogène..............................................
|
10,5%
|
oSoufre.....................................................
|
.3%
|
oAzote...........................................
|
..........0.2%
|
oOxygène...................................................
|
0.4%
|
oH2O.........................................................
|
0.1%
|
|
I.2- Généralités sur la
combustion
Une combustion est la réaction chimique complète
ou partielle du carbone et de l'hydrogène des combustibles usuels par
oxydation.
Cette réaction produit une combustion exothermique
c'est-à-dire : qui dégage de la chaleur, elle produit du CO2 mais
aussi de l'eau ainsi que d'autres composés plus ou moins agressif.
Réactions principales :
La combustion du carbone et de l'oxygène donne naissance
au gaz carbonique.
C + O2 CO2 + 394Kj/mol La combustion de l'hydrogène
et de l'oxygène donne naissance à la vapeur.
H2 + 1/2O2 H2O + 242Kj/mol
Réaction secondaires :
La combustion du soufre et de l'oxygène donne naissance
au gaz SO2.

S + O2 SO2 + 71Kj/mol
Dans le cas d'un défaut d'air, une réaction
secondaire se produit :

C + 1/2O2 CO + 111Kj/mol
La totalité de la chaleur dégagée par
l'ensemble de ces réactions s'appelle le pouvoir calorifique du
combustible.
Définition du pouvoir calorifique d'un combustible :
Le pouvoir calorifique supérieur ou inferieur [en
KJ/KG] est la quantité d'énergie dégagée lors de la
combustion complète de l'unité de masse du combustible solide ou
liquide ou de volume pour le combustible gazeux.
On distingue deux pouvoirs calorifiques lorsqu'il s'agit d'un
combustible contenant l'hydrogène :
o Le pouvoir calorifique est dit supérieur
(PCS) lorsque l'eau qui résulte de la combustion du gaz
hydrogène et des hydrocarbures sont supposée ramenés
à l'état liquide dans les produits de combustion.
o Le pouvoir calorifique est dit inférieur
(PCI) lorsque l'eau de combustion est supposée à
l'état de vapeur dans les produits de combustion.
Cependant la pratique industrielle n'utilise que le PCI pour les
raisons qu'il présente un intérét d'ordre
énergétique.
La différence entre le pouvoir calorifique
supérieur et inférieur est la chaleur de condensation de la
vapeur d'eau qui se trouve dans les fumées. Ils sont liés par la
relation suivante :
PCS = PCI + énergie d'évaporation de l'eau
Pratique de la combustion
Le réglage de la combustion n'est malheureusement pas
stable dans le temps. Un contrôle périodique et
systématique est donc nécessaire. En effet les grandeurs
essentielles à surveiller sont :
· la teneur en gaz carbonique (%CO2) ou en oxygène
(%O2) dans les fumées.
· La température des fumées
· La teneur des fumées en imbrûlés.
Parmi les méthodes de contrôle de la combustion on
peut citer :
> Contrôle visuel
Souvent négligé, il permet d'apprécier la
qualité des réglages et leur dérive en se
référant à la forme et à la couleur de la
flamme.
> Contrôle a l'aide des mesures :
· Températures de l'air comburant, et des
fumées
· La teneur en oxygène O2 ou en gaz carbonique
CO2
I.3- Généralités sur les
chaudières
I-3-1. Description et principe de fonctionnement des
chaudières a ) Définition
Une chaudière est un appareil dont le rôle est de
transmettre à un fluide thermique, les calories dégagées
par une combustion. Cette combustion peut se faire dans la chaudière
(foyer) ou bien à l'extérieur (c'est le cas des chaudières
de récupération). Cet apport de chaleur a pour effet soit
uniquement de réchauffer le fluide thermique, soit de le
réchauffer et le vaporiser.
B ) Type des chaudières
Nous distinguons plusieurs types de chaudières :
Les chaudières à tubes de fumées :
les tubes de fumée sont disposés à l'intérieur
du récipient d'eau, La vapeur est générée en
chauffant un important volume d'eau, au moyen de fumées produites par
combustion de fioul et circulant dans des tubes immergés. C'est la
technique la plus classique pour la production de vapeur saturée, d'eau
ou de vapeur
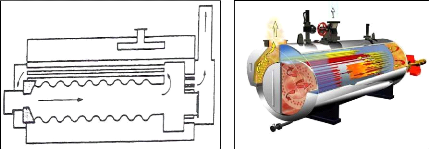
Figure 2.1 : chaudières
à tubes de fumées
Les chaudiqres à tubes d'eau : se
caractérisent par la présence de 1 ou 2 ballons supérieurs
et 1 ou 2 ballons inferieurs reliés entre eux par des tubes dans
lesquels circule l'eau. Dans le cas des chaudières auxiliaires de la
centrale thermoélectrique on à 1 ballon supérieur et 1
autre inferieur
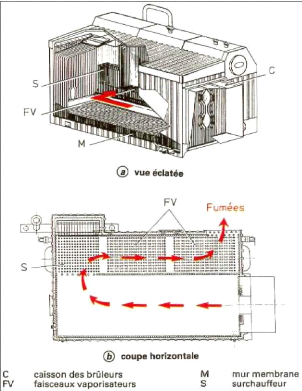
Figure 2.2 : chaudiêres
à tubes d'eau I-3-2. Caractéristiques
principales des générateurs :
a) Timbre :
Le timbre d'une chaudière est la pression maximale
d'utilisation déterminée par le constructeur. (71bars abs pour
les deux chaudières auxiliaires). Cette pression s'exprime en bars et ne
doit jamais être dépassée.
b) Pression de service ou pression de marche
:
C'est la pression que les appareils de régulation de
chauffe visent à maintenir. Cette pression ne peut être
supérieure à celle du timbre. La pression de service ou pression
de marche s'exprime encore en bar (55bars abs pour les deux chaudières
auxiliaire).
c) Surface de chauffe : C'est la surface
d'échange entre les gaz chauds et l'eau. Elle s'exprime en m2
d)
Puissance :
La puissance normalement indiquée en kcal/h (ou en
thermie) représente la puissance calorifique à fournir à
l'eau. C'est le produit du débit de vapeur produite par la
différence d'enthalpie de l'eau entre l'entrée et la sortie de la
chaudière.
P = ( hv - he ).Qm
Avec:
hv : enthalpie de la vapeur produite
he : enthalpie de l'eau alimentaire
Qm : débit de vapeur produite
NB : 1kcal/h = 1.16 . 10-6 MW
e) Taux de vaporisation :
Le taux de vaporisation d'une chaudière est le
résultat du rapport entre la puissance et la surface de chauffe .Il
s'exprime en (KW/m2).
I-3-3. Appareils complémentaires :
a) Les brûleurs :
C'est le moteur de la chaudière, il doit remplir un
rôle essentiel, c'est de crée le mélange air/combustible
aussi homogène que possible, de telle manière que la proportion
entre les deux constituants tende vers celle qui donne la meilleure combustion,
c.-à-d. le maximum « d'effet thermique » Il est indispensable
pour une chaudière à fuel.
Le brûleur est constitué des éléments
suivants :
· Un injecteur amenant le combustible.
· Une amené d'air comburant.
· Une tête de brûleur ou gicleur
Les brûleurs diffèrent selon la nature du
combustible utilisé. Le rôle des brûleurs de combustible
liquide est de :
· pulvériser le combustible dans la chambre de
combustion de manière à augmenter la surface de contact avec
l'air.
· Distribuer judicieusement le combustible
pulvérisé dans l'air comburant afin de réaliser un
meilleur mélange possible.
b) Le ballon supérieur et inférieur
:
La vapeur doit être exempte de gouttelettes d'eau pouvant
perturber la bonne marche de l'installation. Le rôle fondamental du
ballon supérieur, au niveau duquel se fait l'alimentation
en eau de la chaudière sera d'assurer une bonne
séparation du mélange eau-vapeur par l'intermédiaire des
chicanes canalisant le mélange ce dernier vers les cyclones
séparateurs.
Avant que la vapeur quitte le ballon supérieur vers le
surchauffeur, elle passe à travers des filtres de vapeurs (voire
schéma ballon supérieure).
Le ballon inférieur est équipé d'un
désurchauffeur de vapeur et d'une purge à extraction rapide. Les
deux ballons sont constitués en tôle et comportent tous les
accessoires nécessaires tels que le trou d'homme, la tubulure...
Les tubes constituants les murs de la chambre de combustion sont
assemblés par dudgeonnage aux deux ballons.
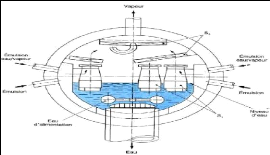
Figure 2.3 : Ballon
supérieur
c) Vaporisateur :
Ils assurent la fin de l'échauffement de l'eau (quand
l'économiseur n'est pas vaporisant) et la production de la vapeur. Les
vaporisateurs sont généralement constitués par les
écrans soudés de la chaudière mais doivent parfois
être complétés par des faisceaux, notamment dans le cas des
chaudières à faible pression.
d) Surchauffeurs :
Reçoivent extérieurement les gaz venants
directement de la chambre de combustion. Ce sont les faisceaux tubulaires du
générateur de vapeur qui sont soumis aux températures les
plus élevées voir. La vapeur saturée venant de la partie
haute de réservoir, passe dans les tubes des surchauffeurs, où sa
température est élevée à pression constante.
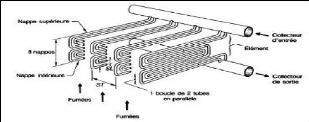
Figure 2.4: Surchauffeur
e) Economiseur :
Dans le but d'augmenter la température de l'eau
d'alimentation qui provient du dégazeur à l'aide de la
récupération d'une partie de calories restantes dans les gaz de
combustion. L'économiseur est un échangeur de chaleur à
circulation d'eau inversée par rapport à celle des gaz de
combustion.
L'échange de la chaleur se réalise par convection,
il a pour but l'augmentation du rendement thermique.
I-3-4. Les circuits des chaudières :
a) Circuit eau et vapeur
Le schéma de circuit est représenté par le
graphe suivant :
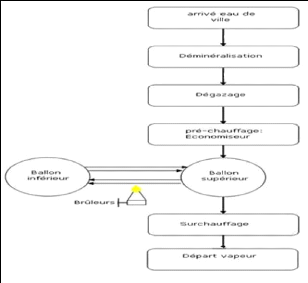
Figure 2.5 : Circuit
Eau/Vapeur
+ L'eau d'alimentation :
Elle est stockée dans une bâche, provient en partie
des condensats de vapeur en retour après utilisation, et l'eau brute
traité dans la station de polissage.
+ Passage par l'économiseur :
L'eau venant de la bâche alimentaire, s'échauffe
avant son introduction dans le réservoir ou le séparateur «
humide ». L'eau à la sortie de cet appareil est
généralement à une température d'environ 160°C
qui est inférieure à la température de saturation, mais
dans certains cas, l'économiseur peut être vaporisant.
L'économiseur, divisé parfois en
différents éléments, est généralement
constitué de tubes à ailettes (fuel ou gaz naturel). Pour des
raisons d'optimisation des échanges et pour des raisons de prix, il est
généralement situé sur le parcours des fumées entre
la dernière surchauffeur ou resurchauffeur et le réchauffeur
d'air.
+ Stockage dans le ballon supérieur :
L'eau venant de l'économiseur est stockée au
niveau du ballon supérieur en mélange avec la vapeur, ce qui
permet d'augmenter sa température d'avantage. Après, l'eau passe
à travers des tubes appelés tubes écrans qui sont
exposés directement aux flammes.
+ Passage par la surchauffeur :
Si la température désirée de la vapeur
n'est pas encore atteinte (490 °C) ou si la vapeur contient encore des
goütes d'eau, on a recoure au surchauffage. Il consiste à faire
passer la vapeur par des serpentins dans la chambre de combustion, ces derniers
seront exposés à la chaleur fournit par la fumée. Ainsi on
aura de la vapeur HP.
b) Circuit de l'air comburant et des fumées
:
L'air comburant passe par un ventilateur
protégée par un grillage et actionnée par un moteur
électrique appelé moteur de soufflage, il passe aussi par une
Volet d'air qui permet la régulation du débit d'air et finalement
par un Déflecteur: c'est un disque avec fentes, qui fait tourner l'air
pour le mélanger au fuel pulvérisé
La fumée provenant de la chambre de combustion traverse
l'économiseur après avoir cédé une partie de son
énergie aux ballons de la chaudière, puis passe par le
surchauffeur pour qu'elle soit évacuée par la cheminée.
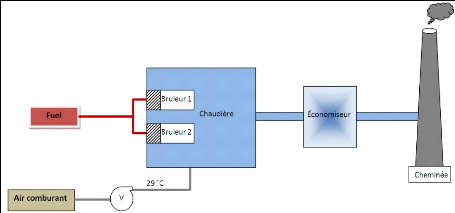
Figure 2.6 : descriptif du
circuit de l'air et des fumées
II. Généralités sur la
cogénération
Généralement, tout établissement ou
industrie produit sa chaleur avec une chaudière à combustible
fossile et achète son électricité au réseau.
Pourtant, il est possible, de produire simultanément une partie de ses
besoins de chaleur et d'électricité par une unité de
cogénération. Cette opération a l'avantage d'optimiser les
coûts d'installation, d'améliorer les rendements
énergétiques et de limiter l'impact sur l'environnement.
II-1.Définition de la
cogénération:
On appelle cogénération (ou encore
production combinée chaleur force), un système
dans lequel, en brûlant un combustible primaire, on produit
simultanément de l'énergie mécanique et de
l'énergie thermique. Le combustible primaire est
généralement un produit fossile commercialisé : charbon,
gaz naturel, GPL (gaz de pétrole liquéfié), fuel lourd ou
domestique ; il peut s'agir aussi de bois ou de biomasse, ou encore d'un
produit de récupération : biogaz, ordures
ménagères, déchets industriels, gaz fatals, etc.
L'énergie mécanique disponible
sur l'arbre de la machine motrice, est utilisée pour entraîner une
autre machine tournante (ventilateur, compresseur) ou le plus
fréquemment un alternateur qui fournit du courant électrique.
L'énergie thermique est disponible
soit directement, soit après transformation, sous la forme d'un fluide
caloporteur facilement utilisable : vapeur, eau chaude, eau surchauffée,
air chaud, etc.
II-2. Principe de la
cogénération
Le principe de la cogénération est contenu dans
son nom : elle consiste à produire, à partir d'une énergie
primaire combustible, deux énergies secondaires utilisables : une
énergie mécanique ou électrique et une énergie
thermique.
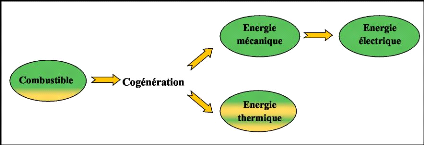
mcan qe c
Figure 2.7 : Principe de la
cogénération
II-3. Les types d'installations
Cogénération
Les principaux systèmes de cogénérations
sont classés en deux groupes :
Eergie
v' Technologies matures (Turbines à vapeur, Turbines
à gaz et Moteurs à combustion
thermique
interne).
v' Technologies nouvelles (Piles à combustible, Moteurs
Stirling, Micro turbines).
II-3-1. Turbine à vapeur:
Cette technique, réservée aux industriels
pouvant produire de grandes quantités de vapeur, permet de produire de
l'électricité lorsque de la vapeur est produite en
excédent, permettant de régulariser sa consommation, par
conversion énergétique. C'est aussi la principale technique
utilisée dans les grosses centrales électriques,
nucléaires ou à combustibles fossiles, pour convertir
l'énergie thermique du combustible en électricité.
La cogénération par turbine à vapeur
permet d'utiliser des sources d'énergie primaires variées, dont
entre autres les sources d'énergie diverses issues de la valorisation
des déchets de l'industrie, tels que les déchets de bois dans les
scieries, où les déchets végétaux de
l'agriculture.
Le cycle thermodynamique des turbines à vapeur est
basé sur le cycle de Rankine. A l'aide de la chaleur
dégagée par la combustion d'un combustible, on produit de la
vapeur à haute pression dans une chaudière. Cette vapeur
est ensuite dirigée vers une turbine, où en se détendant,
entraîne la turbine. Sortie de la turbine, la vapeur est condensée
et ramenée à la chaudière, où ce cycle recommence.
Dans ce cycle, la combustion est externe : c'est-à-dire qu'il n'y a pas
de contact direct entre le fluide process (vapeur) et le foyer. Ainsi le
combustible ne requiert pas de spécifications de qualités
précises et donc tout combustible peut être employé.
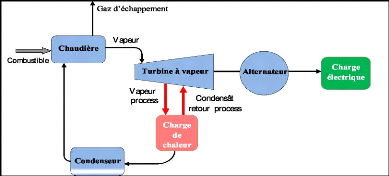
Figure 2.8 :
Cogénération par Turbine à
vapeur
t
II-3-2. Turbine à gaz :
V
C'est la technologie la plus utilisée en
général pour les moyennes et grandes puissances. Ces
ha
T
systèmes sont à démarrage rapide et
s'adaptent rapidement à une variation de la charge.
pu Alternateur
électrique
Une grande quantité d'air atmosphérique est
aspirée et comprimée dans une chambre de
etour process
combustion où a lieu une injection en continu du
combustible. Les produits de combustion,
Charge
lors de leur détente, entraînent le compresseur et
l'arbre de sortie. La turbine fonctionne au
de chaeu
gaz ou au fioul domestique. L'énergie mécanique
est soit utilisée directement en entraînement
Condenur
de machines tournantes, soit convertie en énergie
électrique via un alternateur. La température des gaz
d'échappement avoisine les 500°C, autorisant ainsi un large choix
de valorisation.
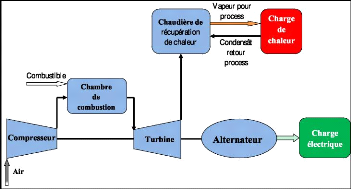
Figure 2.9 :
Cogénération par Turbine à gaz
II-3-3. Moteur à combustion interne (gaz ou
diesel)
Un moteur à pistons et à combustion interne
fournit de l'énergie mécanique, il fonctionne
généralement au fuel domestique ou au gaz. L'énergie
disponible sur l'arbre de sortie est soit utilisée directement en
entraînement de machine tournante (compresseurs, soufflantes,...), soit
convertie en énergie électrique par un alternateur couplé
au réseau. Le maintien en température du bloc moteur et de
l'huile nécessite un ou plusieurs circuits de refroidissement sur
lesquels s'effectue une première récupération à
environ 90°C.
Un complément d'énergie thermique est obtenu
à partir des gaz d'échappement comme le montre la figure suivante
:
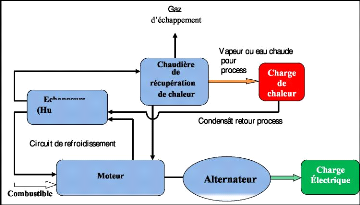
gaz
d'échappemen
Figure 2.10 :
Cogénération par Moteur à combustion
interne
II-3-4. Cycle combiné: turbine à gaz +
turbine à vapeur :
Le cycle combiné le plus utilisé est
l'association du cycle de JOULE et du cycle de RANKINE (association d'une
turbine à gaz et d'une turbine à vapeur), la turbine à gaz
peut produire de la vapeur à travers une chaudière de
récupération. Cette vapeur peut aussi entraîner une turbine
à vapeur au lieu d'être employée directement dans un
process, et avec un alternateur placé sur l'axe de la turbine à
vapeur, on peut ainsi produire un complément
d'électricité. L'intérêt ici est d'augmenter le
rendement électrique de l'installation.

Figure2.11 :
Cogénération par cycle combiné
II-3-5. Tri génération :
La trigénération est l'association de deux
techniques aujourd'hui bien connues : la cogénération et la
production de froid par absorption.
Cette technique fait généralement appel à
l'installation d'un moteur thermique ou d'une turbine à combustion, d'un
alternateur et d'un groupe frigorifique. L'énergie mécanique
produite est totalement affectée à la production
d'électricité.
Tout ou partie de l'énergie thermique produite par le
cycle de cogénération est transmise à un groupe
frigorifique à absorption.
Dans cette configuration, le rapport
électricité/chaleur est plus élevé que celui d'une
cogénération classique.
Ga
g
Le rendement global d'une installation de tri
génération peut atteindre 85%, cette optimisation
de
Chdiè d ar
des rendements, par rapport à la
cogénération classique, se double d'une grande
flexibilité
récupération Turbine à
Chb d cha
dans la répartition des énergies produites.
combustion Condensât retou
II-4. Etude comparative des différentes
technologies
Le tableau suivant représente les avantages et
inconvénients de différentes techniques de
cogénération utilisées dans l'industrie
Tableau 2.1: Etude comparative des
technologies de cogénération.
Techniques de cogénération
|
Avantages
|
Inconvénients
|
Domaines d'applications
|
Turbine à vapeur
|
Convient à tous types de combustible.
|
Très faible E/Q
|
le secteur industriel (chimie, papier,
carton agro-alimentaire, sidérurgie,...).
Une production importante de la chaleur et peu
d'électricité.
|
Très bon rendement global > 0,85.
|
Investissement élevé
|
Coüt d'entretient modique.
|
Durée de vie élevée.
|
possible d'effectuer des soutirages de vapeur à divers
stades de détente pour les usages thermiques.
|
Turbine à gaz
|
A partir de 500KWe.
|
E/Q faible pour les puissances
inférieures.
|
le secteur industriel (chimie, papier, carton,
sidérurgie,
agroalimentaire...), les réseaux de chaleur et des
applications tertiaires hôpitaux...)
|
Production aisée de vapeur.
|
Nécessite en général du gaz naturel.
|
Bon rendement global. (0,6- 0,8)
|
E/Q important
|
Moteur à gaz ou diesel
|
E/Q Très favorable surtout pour le
diesel.
|
Peu propice à la production de vapeur
|
bien adapté aux
secteurs tertiaires (hôpitaux, centres administratifs,
centres commerciaux,..) et industriels
(électronique, laboratoires, alimentaire,..).
|
Coût abordable.
|
Coût élevé de Maintenance
|
Peut s'adapter à la variation de la demande
|
Durée de vie limitée
|
Peut jouer le rôle de
secours en cas de coupure de l'électricité.
|
Entretien programmé d'atteindre une durée
de vie de 100 000 H avant le remplacement complet du moteur
|
E : Energie électrique Q : Chaleur
Chapitre III : Fonctionnement de la CTE II et de
l'unité de cogénération
- Différentes unités de la CTE II.
- Système de production de vapeur dans la CTE II.
- Production de l'électrice dans l'unité de
cogénération.
I. Fonctionnement de la centrale thermoélectrique
II
I-1. Introduction
Au niveau de la raffinerie SAMIR, le fonctionnement des
différentes unités dépend étroitement de la
production de la vapeur. Pour satisfaire le besoin en vapeur, la SAMIR a mis en
place deux centrales thermiques (CTE1 et CTE2).
La CTE2 assure la production de la vapeur et la distribution
de l'électricité ainsi que les autres utilités (air
comprimé, eau déminéralisée, eau de mer, fioul
chauffé, azote ....) nécessaire au processus de raffinage au sein
de la SAMIR.
Les besoins en vapeurs sont couverts en exploitation par
quatre chaudières, l'alimentation électrique est assurée
actuellement en majorité par l'unité de
cogénération et le complément restant par l'Office
Nationale d'Electricité (ONE).
I-2. Différentes unités de la CTE
II
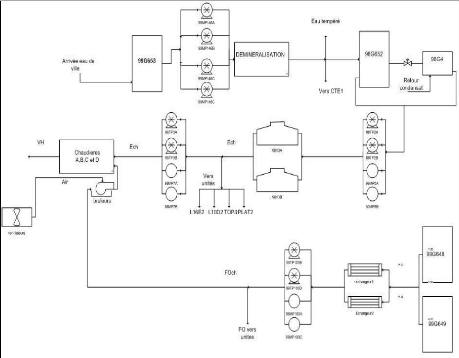
Figure 3.1 : Schéma de la
centrale thermoélectrique II.
La centrale thermoélectrique II (figure 2.1) comprend :
> Des installations destinées à assurer son
alimentation en combustible (fioul-oil ou fioul gaz), stockage, chauffage et
acheminement vers les chaudières, les fours et les bacs des groupes
diesel.
> Des installations destinées à assurer son
alimentation en eau traitée. Ces installations comportent la station de
traitement d'eau, les bacs de stockage d'eau de ville et celle
déminéralisée et le pompage d'eau de chaudière.
> Une chaufferie groupant les quatre chaudières et
leurs auxiliaires (économiseur, ventilateurs de soufflage, pompes
alimentaires,. .etc.).
> Une salle de contrôle et de commande permettant la
supervision et la commande à distance des équipements de la CTE
II.
> Des locaux des groupes diesel, des compresseurs et leurs
auxiliaires.
> La distribution d'énergie électrique
achetée se fait en 60KV vers les sous stations de toutes les
unités, à travers des postes de transformation (60KV/20KV),
(20KV/5.5KV), (5.5KV/380V), (380V/220V).
Par ailleurs la centrale thermoélectrique comprend des
installations de production d'air comprimé et de l'eau
déminéralisée :
1. L'air comprimé :
L'air comprimé est indispensable pour la mise et le
maintien en marche des équipements pneumatique, sa production est
assurée par cinq compresseurs, l'air comprimé produit est de deux
types : air de service et air instrument. La différence entre eux est
l'étape de séchage que subit l'air comprimé produite au
niveau des compresseurs pour être utilisé dans les appareils
pneumatique (Air instrument).
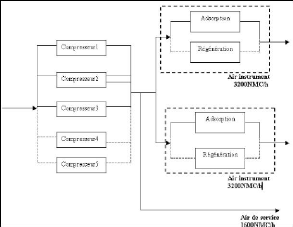
Figure 3.2 : Schéma de la
production d'air comprimé
2. L'eau déminéralisée :
L'unité de déminéralisation est
dimensionnée pour fournir la totalité des besoins de la
raffinerie en eau déminéralisée, aussi bien pour les
installations existantes que pour le nouveau projet UPGRADE.
L'unité comporte trois trains ou lignes de
déminéralisation identiques dimensionnés pour une
production nette de 150 m3/h chacune. Le concept adopté pour
l'unité est basé sur la technologie de l'échange
d'ions.
Les étapes principales du processus de
déminéralisation sont :
1 Stockage de l'eau brut.
1 Filtration à travers les filtres à charbon.
( Echange sur support cationique.
( Désorption du dioxyde de carbone.
( Echange sur support anionique.
( Traitement de finition sur support de lits
mélangés (anions + cations). 1' Stockage de l'eau
déminéralisé.
I-3. Les chaudières de la CTE II
La centrale thermoélectrique II comprend quatre
chaudières 98 H 1 (A, B, C et D) d'une capacité unitaire maximale
de 80 T/h en marche continue, elles peuvent fonctionner
séparément ou en parallèle et elles sont
équipées d'un système de régulation permettant la
marche manuelle ou automatique d'un nombre quelconque de chaudières.
Les chaudières A, B et C sont équipées de
quatre brûleurs pour la combustion au fuel-oil et fuel gaz, soit
séparément soit simultanément et en proportions variables,
La chaudière D est équipé de deux brûleurs dont la
capacité est équivalente aux quatre brûleurs des autres
chaudières.
Les chaudières de la SAMIR sont de type à tubes
d'eau (voire chapitre II paragraphe I-3). I-3-1. Production de la vapeur
haute pression (Figure 3.3)
Les chaudières sont alimentées en eau
dégazée à 127°C et équipées d'un
économiseur assurant le réchauffage de l'eau d'alimentation
à 184°C à travers la récupération des calories
des fumées sortant de la chambre de combustion. Elles sont
alimentées en air comburant par un ventilateur de soufflage
entraîné par un moteur électrique et une turbine à
vapeur. Après avoir traverser l'économiseur, l'eau arrive au
corps cylindrique supérieur de la chaudière (CCS) où se
trouve réunies les phases liquides et vapeur saturée. La phase
liquide circule entre le CCS et le corps cylindrique inférieur (CCI)
à travers un faisceau de tubes qui consomment la chaleur
dégagée par la combustion (par radiation et convection).
La vapeur saturée est ensuite envoyée dans les
tubes des surchauffeurs, où sa température augmente à
pression constante (40bars, 400°C).
La vapeur HP sèche produite est collectée dans
deux barillets (98 X 1A et 98 X 1B) chacun alimentant un barillet MP à
travers une vanne de détente (vannes réductrice de
détente). Les liaisons VH d'export vers les unités sont prises
sur les deux barillets.
I-3-2. Production de la vapeur moyenne pression (Figure
3.3)
Auparavant, les besoins en vapeur moyenne pression de la
raffinerie ont été couverts par le soutirage des
turbo-alternateurs qui sont hors service depuis 2002. Actuellement cette
fonction est assurée par deux ensembles de détente de vapeur HP
d'une capacité unitaire de 50 T/h. La vapeur MP et haute
température provenant des postes de détentes est collectée
dans les barillets (98 X 2A) et (98 X 2B).
Des barillets (98 X 2 A/B), la vapeur MP est
transférée à travers 4 ensembles de désurchauffe en
parallèle (2 par barillet) (98 DS 1 A/B) et (98 DS 2 A/B) (14 bars, 270
à 300°C) aux barillets (98 X 3A) et (98 X 3A).
La distribution aux auxiliaires propres à la CTE II et
utilisateurs extérieurs se fait à partir des barillets (98 X 3
A/B).
I-3-3. Production de vapeur basse pression (Figure 3.3)
Les collecteurs de vapeurs basse pression extérieurs
à la CTE II aboutissant aux deux barillets (98 X 4 A/B). Un appoint en
vapeur BP est possible à partir des barillets MP (98 X 3 A/B), à
travers deux ensembles détente-désurchauffe (1 par barillet) (98
DS 3 A et B) d'une capacité unitaire de 30 T/h.
Un appoint en vapeur très basse pression (VBB) est
également possible à partir des barillets VB (98 X 4 A/B) par
l'intermédiaire d'une vanne automatique de détente.
I-3-4. Production de vapeur très basse pression
(Figure 3.3)
La vapeur très basse pression (1,8 bars) est
destinée au réchauffage de l'eau de chaudière dans les
dégazeurs (98 V 3 A/B) opérant à (1,5 bars) et
(127°C). Le principe directeur est d'assurer une autonomie fonctionnelle
de la CTE, le réseau VBB est alimenté en priorité par la
vapeur d'échappement des turbines axillaires propres à la CTE
II.
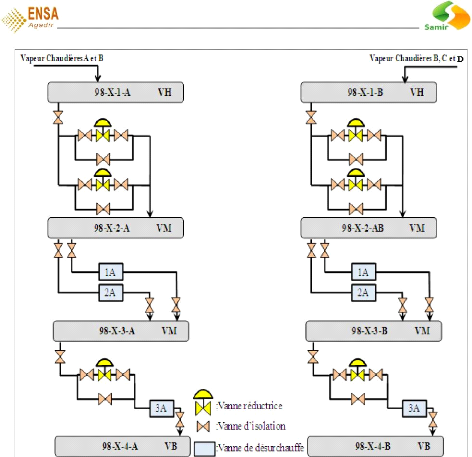
Projet de Fin d'Etudes
Figure 3.3: Système de
réception et de distribution de la vapeur dans GTE II
II. F14!\io44eP I4\ d1It'unité de
cogénération
II-1. Introduction :
La SAMIR a conclu avec la Société LITWIN France
un contrat d'une valeur de 32 Millions d'euros portant sur la
réalisation d'une unité de cogénération d'une
puissance de 40 MW dans l'enceinte de la raffinerie de Mohammedia.
La nouvelle unité utilisera la technologie des cycles
combinés associant une turbine à gaz GENERAL ELECTRIC de 40 MW
à une chaudière de récupération thermique des
fumées d'échappement de la turbine et pouvant
générer prés de 70 T/h de vapeur haute pression. Elle
permettra d'alimenter en électricité et en vapeur, les
installations actuelles et celles du projet de modernisation.
Ce projet, qui a démarré en 2009 permet de
répondre aux exigences les plus strictes en matière de
sécurité et d'environnement et garantit à la raffinerie
une alimentation électrique fiable.
Ce projet présente de multiples avantages :
1 Coût d'investissement et besoins en utilité plus
réduits par rapport a ceux d'une centrale classique ;
1 Meilleur rendement énergétique ;
( Meilleur respect de l'environnement répondant ainsi aux
exigences de la Banque Mondiale
De plus, l'unité sera dimensionnée pour être
opérée soit au diesel, durant les premières années
de service, soit au gaz naturel, une fois ce dernier accessible.
L'utilisation du diesel contenant 1% de soufre au lieu du
fuel-oil qui en contient 3,6 %, assurera une amélioration
considérable de la qualité de l'air à l'échelle
locale et régionale à travers la réduction des
émissions en SO2 d'environ 1500 tonnes par an.
II-2. Architecture de
l'unité:
L'unité de cogénération est principalement
composée de :
> Un groupe turbo alternateur comprenant essentiellement un
dispositif de démarrage, un compresseur axial multi étage, une
turbine à trois étages et d'un alternateur.
> Une chaudière de récupération
> Un bac de stockage diesel d'une capacité de 300
_L.
> Deux pompes pour l'alimentation de la turbine a combustion
en combustible.
> Deux pompes pour alimenter la chaudière de
récupération en eau déminéralisé > Deux
pompes pour aspirer l'eau de dégazeur et le refouler vers
l'économiseur
> Un package compresseur et sécheur d'air qui produit
120 NmL/h pour les besoins de l'unité.
> Un groupe électrogène
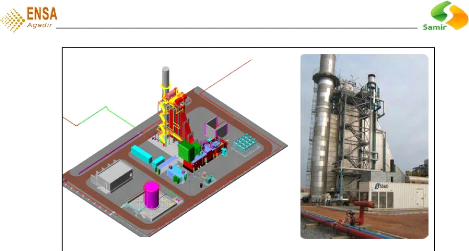
Figure 3.4 : Vue
général de l'unité de cogénération
II-3. Fonctionnement de l'unité de
cogénération
L'installation comporte une turbine à combustion
bicombustible, un alternateur délivrant une puissance de l'ordre de 40
MW et une chaudière de récupération de 70T/h.
II-3-1. Le groupe turboalternateur :
Le groupe turboalternateur de l'unité de
cogénération comprend :
· un dispositif de démarrage.
· convertisseur de couple.
· réducteur des auxiliaires.
· des équipements attelés au réducteur
des auxiliaires.
· un compresseur.
· système de combustion.
· une turbine à trois étages.
· Un réducteur.
· Un alternateur.
Le compresseur et la turbine sont reliés par un arbre
unique, supporté par deux paliers lubrifiés sous pression.
L'extrémité de l'arbre d'entrée du rotor est
couplée au réducteur des auxiliaires, équipé de ses
propres arbres destinés à entraîner la pompe à
combustible, la pompe à huile et d'autres dispositifs.
La turbine à gaz est un moteur thermique reliant les
différentes phases de son cycle thermodynamique dans une succession
d'organes traversés par un fluide moteur gazeux en écoulement
continu. Elle est composée de trois éléments essentiels
comme le montre la figure suivante :

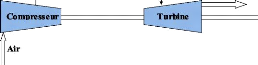
Figure 3.5 : Schéma d'une
Turbine à gaz simple
+ Un compresseur axial, compresseur axial a 17
étages, il produit l'air de comburant.
+ Une chambre de combustion, dans laquelle le
gaz oïl (injecté sous pression) est brulé avec l'air
préalablement comprimé (ce dernier en fort excès afin de
limiter la température des gaz brulés en entrée de la
turbine)
+ Une turbine axiale à trois
étages dans laquelle sont détendus les gaz à haute
température sortant de la chambre de combustion.
Principe de fonctionnement (figure 3.5):
Dès que le système de démarrage de la
turbine est activé et que l'embrayage est engagé, l'air ambiant
est aspiré, filtré puis compressé dans les 17
étages du compresseur axial. L'air comprimé en provenance du
compresseur pénètre dans l'espace annulaire à la
périphérie des dix chambres de combustion, d'où il
s'introduit entre les enveloppes intermédiaires et les tubes de
flamme.
Les injecteurs introduisent le combustible dans chacune des dix
chambres de combustion où il
Chambre de combsto
se mélange à l'air. L'allumage s'effectue grace
à deux bougies rétractables (mais une seule est suffisante
pour effectuer l'opération). Au moment où l'allumage se produit
au niveau d'une des deux bougies équipant ces chambres, la combustion
se propage dans les autres chambres à
Ecappement
ompresseur Turbine
travers des tubes d'interconnexion qui les relient entre elles
au niveau de la zone de combustion. A peu près à 50 % de la
vitesse nominale de la turbine, la pression régnant à
ir
l'intérieur des chambres de combustion est suffisante pour
provoquer le retrait des électrodes des bougies afin de le
protéger du rayonnement des flammes.
Les gaz chauds issus des chambres de combustion franchissent
les pièces de transition emboîtées à
l'extrémité arrière de chaque tube de flamme pour
traverser ensuite les trois étages de la turbine où ils se
détendent. Chaque étage se compose d'un ensemble d'aubes fixes
suivies d'une rangée d'aubes mobiles. Dans chaque rangée d'aubes
fixes, l'énergie cinétique du jet de gaz augmente, en même
temps que la pression chute. Dans la rangée
adjacente d'aubes mobiles, une partie de l'énergie
cinétique du jet est convertie en travail utile transmis au rotor de la
turbine sous la forme d'un couple mécanique.
Après leur passage dans les aubes du troisième
étage, les gaz d'échappement traversent le diffuseur, qui
comporte une série de déflecteurs ou aubes de guidage
transformant la direction axiale des gaz en direction radiale et diminuant
ainsi les pertes à l'échappement. Puis les gaz sont
envoyés dans le cadre d'échappement. La rotation
résultante de l'arbre entraîne le rotor de l'alternateur, le
compresseur et certains auxiliaires. (Voir Equipements attelés au
réducteur des auxiliaires).
II-3-2.La chaudière de
récupération
Une chaudière de récupération est une
chaudière qui utilise la chaleur des gaz d'échappement de la
turbine à gaz, elle permet de récupérer les calories
contenues dans les fumées pour produire de la vapeur.
La chaudière de récupération SECI (SECI ;
Stein Energie Chaudières Industrielles) installée dans la
l'unité de cogénération de la SAMIR est de type tube d'eau
à circulation naturelle avec un seul passage des fumées. Les
fumées de l'échappement de la turbine passent successivement
à travers une Surchauffeur Haute Température SHT, une
Surchauffeur Basse Température SBT, un évaporateur, et un
économiseur (figure 3.6).
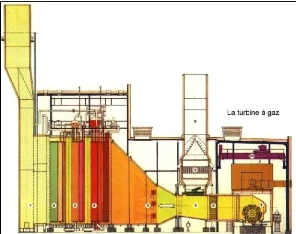
Figure 3.6: Chaudière de
récupération
La chaudière fonctionne en mode
récupération pure (sans post de combustion), elle permet de
récupérer l'énergie disponible dans les fumées
à l'échappement de la turbine à combustion, pour produire
de la vapeur surchauffée à partir d'eau
déminéralisée à température ambiante.
En fonctionnement nominal, la puissance des fumées
à l'échappement de la turbine est de 82 MW, le débit des
fumées est de l'ordre de 143 kg/s, la production de vapeur est de 71,5
T/h à 46 bars et 415 °C. La ligne à la sortie de la
chaudière fait environ 500 m de longueur et la vapeur est livrée
à 42.2 bar et 405°C au barillet (98-X-l A) dans la CTE II.
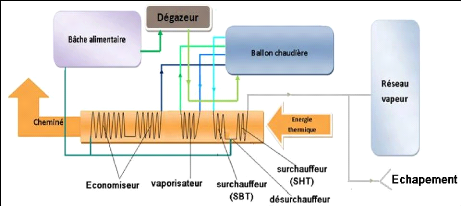
Figure 3.7: Parcours de l'eau et
des fumées dans la chaudière de
récupération.
II-3-3. Circuit (Eau /vapeur)
L'eau déminéralisée est aspiré
d'un bac de stockage vers la bâche alimentaire par un système
à deux pompes (une en marche et l'autre en secours), ensuite elle
transporté vers l'économiseur par l'intermédiaire d'une
motopompe. A la sortie de l'économiseur, une première partie
d'eau est acheminé vers le pot de détente, la vapeur extraite de
dernier est injecté au fond de la bâche alimentaire pour
dégazer l'eau d'appoint, une deuxième partie de l'eau sortant de
l'économiseur est injecté dans le désurchauffeur entre les
deux surchauffeurs SHT et SBT pour réguler la température de
sortie de la vapeur. La troisième partie sortante de
l'économiseur est stockée dans le ballon de la chaudière,
elle passe ensuite à travers les tubes du vaporisateur appelés
tubes écrans pour se transformer en vapeur saturé qui est
renvoyée vers le ballon chaudière.
La température désirée de la vapeur n'est
pas encore atteinte (500°C) et la vapeur contient encore des gouttelettes
d'eau, c'est pourquoi on a recoure au surchauffage. Il consiste à faire
passer la vapeur à travers des serpentins devisés en deux
étages (SHT et SBT), afin d'avoir une vapeur surchauffée qui va
être débité dans le réseau.
II-3-4. Circuit diesel :
Le diesel oïl fourni par SAMIR alimente un bac de
300m3 de volume utile, pour une autonomie de 24h.
Le bac diesel est en acier carbone de type cylindrique vertical
à toit fixe conique, et à fond conique.
Au point de fonctionnement nominal, la turbine à gaz
consomme environ 12 m3/h.
Deux pompes de type centrifuge fonctionnant à 2x100% (une
en service et une en secours), sont placées à côté
du bac diesel afin d'alimenter la turbine et le groupe
diesel.
II-3-5. Le groupe électrogène :
Le groupe électrogène est un dispositif autonome
capable de produire de l'électricité. Il permet d'assurer une
sécurité et une continuité de service en cas de coupure de
courant délivré par l'ONE.
Le groupe diesel est constitué de :
> Un moteur thermique diesel qui actionne un alternateur. >
Un mécanisme de refroidissement et de préchauffage.
> Une armoire de contrôle commande.
> Un transformateur élévateur.
Chapitre PV : Calcul des consommations spécifiques
et des Coûts de revient des utilités.
- Méthodologie de calcul.
- Coûts de revient des utilités dans la centrale
thermoélectrique II. - Coût de revient de
l'électricité dans l'unité de
cogénération.
I. Méthodologie de calcul
I-1. Définition
La définition du coüt est Selon l'AFNOR
«c'est la charge ou la dépense, supporté par un
intervenant économique par suite de la production ou de l'utilisation,
d'un produit ou de l'ensemble des deux.»
AFNOR : association française de normalisation
I-2. Coût variable et coût fixe
:
Les coûts fixes sont des charges
indépendantes du volume de production. Ces coûts
représentent les coûts engagés de façon permanente
pour les activités de production, tels que les coüts du personnel
d'encadrement, de l'amortissement, du loyer et de l'assurance des
bâtiments, des équipements et des machines.
Les coûts variables sont des coûts dont
le montant varie proportionnellement à l'activité. Ce sont des
charges variant corrélativement à la production de
l'élément considéré et elles sont essentiellement
constituées des coüts des matières premières, de la
main d'oeuvre dont l'utilisation est fonction des quantités produites et
de l'énergie dépensée dans l'élaboration des
produits.
II. Coûts de revient des utilités dans la
Centrale thermoélectrique II
Dans le calcul des coûts de revient des produits, la
méthode la plus utilisée et la plus significative est celle des
consommations spécifiques, c-à-d On calcul les consommations
spécifiques de chaque produit, par exemple pour produire une tonne de
vapeur HP, on a besoin de combien d'eau déminéralisée ?
C'est ce qu'on désigne par consommation spécifique en eau
déminéralisée. De même pour le fuel,
l'électricité, les additifs...., et donc on calcul d'abord les
coüts de matières premières et de l'énergie puis on
détermine le coüt de la vapeur
Mais avant de passer au calcul du coût de revient de la
vapeur haute pression, on commence par le calcul de celui de l'eau
déminéralisée et de l'air comprimé, ils seront
utilisé dans les calculs qui suivent.
II-1. Coût de revient de l'eau
déminéralisée
La figure suivante schématise les entrées-sorties
de la station de déminéralisation d'eau,

Figure 4.1: Schématisation
de la station de déminéralisation d'eau.
L'unité de déminéralisation est
dimensionnée pour fournir la totalité des besoins de la
raffinerie en eau déminéralisée, elle comporte trois
chaines de déminéralisation identiques dimensionnés pour
une production nette de 150 m3/h chacune.
Dans le cycle normal de production, deux chaines sont en
marche et la troisième est en régénération puis en
repos, la production de l'unité est alors 300 m3/h, mais une
quantité de 20 m3/h est recyclée pour utilisation en
régénération.
Donc : production horaire = 280
m3/h
En se basant sur les bilans mensuels des mois Mars, Avril et
Mai 2010 on calcule les quantités de matières premières
nécessaires à la production de cette quantité d'eau
déminéralisée.
Tableau 4.1 : Mati~res premiqres
consommées dans la production de l'eau
déminéralisée.
Matières
|
Quantité
|
Unité
|
Eau de ville
|
308
|
m3/h
|
Acide sulfurique
|
196
|
Kg
|
Soude caustique
|
448
|
Kg
|
Energie électrique
|
113
|
KWh
|
Eau déminé pour la
régénération
|
48
|
m3/h
|
Les consommations spécifiques de matières
premières de production de l'eau déminéralisée sont
présentées dans le tableau suivant :
Tableau 4.2 : Consommations
spécifiques pour production de l'eau
déminéralisée.
Matières
|
Consommation
|
Unité
|
Eau de ville
|
1,1
|
m3 /m3
|
Acide sulfurique
|
0,7
|
Kg /m3
|
Soude caustique
|
1,6
|
Kg /m3
|
Energie électrique
|
0,40357143
|
KWh /m3
|
Eau déminé pour la
régénération
|
0,17142857
|
m3/ m3
|
|
Projet de Fin d'Etudes
|
|
|
m3/m3 : mètre cube d'eau brute
consommé pour produire un mètre cube d'eau
déminéralisé
Le coüt variable de déminéralisation (en
DH/T) englobe le coüt d'eau de ville (eau potable acheté de
-Lydec-) ainsi que les coüts des matières chimiques
utilisées et l'électricité consommée (ONE) pour le
fonctionnement de l'installation de déminéralisation.
Les résultats de calcul sont présentés dans
le tableau suivant. Tableau 4.3: Calcul du
coût de l'eau déminéralisée.
Matière
|
Consommation spécifique
|
Prix unitaire
|
Coût (Dh/T)
|
Eau de ville
|
1,1 m3 /m3
|
7,41 Dh/m3
|
8,151
|
Acide sulfurique
|
0,7 Kg /m3
|
2,1 Dh/ kg
|
1,47
|
Soude caustique
|
1,6 Kg /m3
|
1,27 Dh/ kg
|
2,032
|
Energie électrique
|
0,4035714 KWh /m3
|
0,78 Dh/kWh
|
0,31478571
|
Eau déminé pour la
régénération
|
0,17142857 m3/ m3
|
1,9340 Dh/m3
|
1,93402041
|
Total
|
14,0194
|
II-2. Coût de revient de l'air comprimé
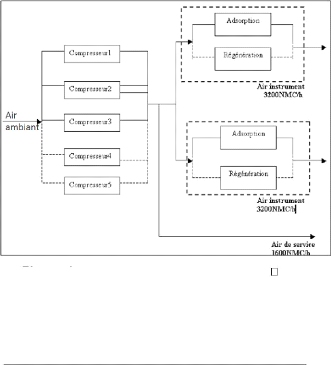
Figure 4.2 : Schéma de
production d'air comprimé
L'air comprimé est produit par passage de l'air ambiant
dans des compresseurs puis un séchage par adsorption de
l'humidité, le schéma de production est la suivante :
II-2-1. L'air de service
Les seuls éléments qui entre dans la production
de l'air comprimé de service sont l'air ambiant (gratuit),
l'énergie électrique et les lubrifiants (négligeables),
donc le coüt d'air comprimé peut être approché par la
consommation électrique des compresseurs.
Le tableau suivant présente la production d'air
comprimé, la consommation électrique des compresseurs et ainsi le
coüt de l'air de service.
Tableau 4.4: coût de l'air de
service
Nombre de compresseur en marche
|
2,5
|
Débit de chaque compresseur (Nm3)
|
1600
|
Production d'air comprimé (Nm3)
|
4000
|
Consommation électrique d'un seul compresseur (kW)
|
287
|
Consommation électrique totale des compresseurs (kW)
|
717,5
|
Prix unitaire électricité Dh/KWh
|
0,78
|
Consommation Spécifique d'électricité KWh/
Nm3
|
0,179375
|
Coût de l'air de service
DH/Nm3
|
0,1399125
|
II-2-2. Air instrument
Le coüt de l'air instrument n'est que le coüt de l'air
de service plus le coüt de séchage, le calcul est
représenté dans le tableau suivant
Tableau 4.5: coût de l'air
instrument.
Coüt de l'air de service DH/Nm3
|
0,1399125
|
Coût de séchage DH/Nm3
|
0,014
|
Coût de l'air instrument
DH/Nm3
|
0,1539125
|
|
Projet de Fin d'Etudes
|
|
|
II-3. Calcul du coût de revient de la vapeur HP
II-3-1. Modélisation du système de
production
La figure suivante représente le système de
production de la vapeur haute pression dont les entrées sont : Le fioul,
l'eau déminéralisée, les matières chimiques et
l'électricité nécessaires à la mise en marches des
circuits de pompage, de ventilation, de lubrification, etc...
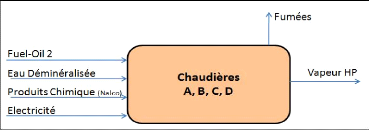
Figure 4.3: Système de
production de la vapeur haute pression dans la GTE II
La centrale thermoélectrique II contient quatre
chaudières destinées à la production de la vapeur HP, on
procédera par une démarche de calcule globale pour évaluer
le coût de revient, on modélise les chaudières de la
centrale thermoélectrique par une chaudière équivalente,
car ce qui nous intéresse c'est les quantités de vapeurs
produites et les quantités des matières premières
consommées. Ainsi, en se basant sur les bilans mensuels de production de
vapeur de la CTE II, on pourra calculer le coût de revient de la vapeur
HP.
II-3-2. Calcul du coût variable de production
Le coût variable de production de la vapeur HP est la
somme des charges relatives aux matières premières
utilisées, qui sont principalement l'eau
déminéralisée et de l'énergie nécessaire
dépensé (Le fioul et l'énergie électrique). La base
de calcul sera sur une tonne de vapeur HP, c'est-à-dire combien y-t-il
besoin d'eau déminéralisée pour produire une tonne de
vapeur HP, c'est ce qu'on désigne par consommation spécifique en
eau déminéralisée. De méme pour l'énergie
dépensée et les autres éléments.
Le calcul sera effectué sur la base de la quantité
horaire de vapeur produite par les quatre chaudières dans la centrale
thermoélectrique II qui est de l'ordre :
Production horaire = 166 T/h
En se basant sur les bilans mensuels des mois Mars, Avril et Mai
2010 on calcule les quantités de matières premières
nécessaires à la production de cette quantité de
vapeur.
Tableau 4.6 : Quantités de
matières premières consommées pour la production de la
vapeur
Elément
|
Quantité
|
Unité
|
Eau déminéralisée
|
168
|
m3
|
Fioul
|
10,1
|
Tonne
|
Nalco-1801 Dosage
|
densité ?
1,003021
|
0 kg/h
|
Nalco-72215
|
0,930841 h
/ )
|
Kg/h
|
Energie électrique
|
681
|
kwh
|
Air comprimé
|
150 arg
|
m3
|
a) Méthodologie de calcul
> L'eau qui rentre dans les chaudières est
constituée de 70 % d'eau déminéralisée et de 30%
des condensas, en effet, c'est juste le 70% d'eau qui sera comptabilisé
dans le coût.
Donc la quantité d'eau déminéralisée
produite par les chaines de déminéralisation et
alimente directement les chaudières est :
> Quantité de Nalco
Avant d'être vaporisé dans les chaudières
l'eau déminéralisée subie un traitement chimique qui
consiste à l'injection de deux types de Nalco, le Nalco-72215 pour
protéger les tubes des chaudières contre la corrosion, et le
Nalco-1801 pour éliminer l'oxygène.
Le dosage du Nalco est donné par la formule suivante :
Donc le débit de Nalco est :
Le tableau suivant représente le dosage et la
densité du Nalco Tableau 4.7 : Dosage et
densité du Nalco
Type Nalco
|
dosage
|
densité
|
Nalco 1801
|
6 ppm
|
0.993
|
Nalco 72215
|
6 ppm
|
1.07
|
> L'énergie électrique
L'énergie électrique se consomme au niveau des
turboventilateurs (98H1MMK1C) et dans les systèmes suivants :
? Le système Fioul (deux motopompes 98MP100A et C). dont
un seul est en marche à l'état normal, l'autre étant de
secours.
? L'alimentation en eau déminéralisée
(quartes Motopompes 99MP5A /99MP5B et 98MP7A / 98MP7B). dont deux seulement
sont en marche.
La consommation mensuelle et horaire d'électricité
dans les chaudières et résumé dans le tableau suivant :
Tableau 4.8: Consommation horaire
de l'énergie électrique dans les chaudières.
Equipement
|
Consommation mensuelle en KWh
|
98MP100A
|
12624,03
|
99MP7A
|
26537,79
|
98MP7B
|
230459,75
|
98H1MMK1C
|
133920
|
Energie électrique total consommée
|
490272,03
|
Consommation horaire
|
681,00
|
> L'air comprimé :
La consommation en air comprimé est
présentée dans le tableau suivant :
Tableau 4.9: Consommation d'air
comprimé dans les chaudiqres.
Consommation
|
Unité
|
Consommation mensuelle
|
Consommation horaire
|
Air comprimé pécifique en ea
|
Nm3 ralisé
|
bit d eau
432.000
|
alis
600
|
b) Calcul des consommations spécifiques
:
Les consommations spécifiques représentent les
quantités de matières premières nécessaires pour
produire une tonne de vapeur haute pression. Par exemple la consommation
spécifique en eau déminéralisé représente la
quantité d'eau traitée nécessaire pour produire une tonne
de vapeur haute pression Elle est exprimée par le rapport entre le
débit d'eau déminéralisée et le débit de
vapeur HP produite ou bien par le rapport entre la consommation et la
production mensuelles de la vapeur et de l'eau
déminéralisé.
Idem pour le fuel, l'électricité, l'air
comprimé et les matières chimiques (Nalco).Le tableau suivant
résume les valeurs des consommations spécifiques par une tonne de
vapeur et le Coût de production de vapeur HP dans la centrale
thermoélectrique II.
Tableau 4.10: Goût variable
de production de vapeur HP
Elément
|
Consommations spécifiques
|
Prix unitaire (Dh)
|
Coût Dh/Tonne
|
Eau déminéralisée (m3)
|
1,01204819
|
7,41
|
14,1883146
|
Fioul (tonne)
|
0,06084337
|
4014
|
244,225301
|
Nalco-1801 (kg)
|
0,0060423
|
60
|
0,36253776
|
Nalco-72215 (kg)
|
0,00560748
|
26
|
0,14579439
|
Energie électrique (kWh)
|
4,10240964
|
0,78
|
3,19987952
|
Air comprimé (N m3)
|
3,61445783
|
0,153
|
0,55301205
|
Coût total de vapeur HP (DH/TVH)
|
262,674
|
II-3-3. Calcul du coût fixe de production
Les coûts fixes de production de vapeur englobent les
frais de maintenance et d'entretien, y compris les pièces de rechanges,
les frais d'assurance ainsi que la main d'oeuvre.
Pour les charges relatives à l'assurance, ils sont
négligeables devant le coüt de la main d'oeuvre et de pièces
de rechange.
Avec
CM : coût de maintenance
CMO : coût de la main d'oeuvre CR : coût des
pièces de rechange
L'analyse de l'historique des charges de la maintenance du
système de production de la vapeur; de l'année 2009 donne ce qui
suit :
Tableau 4.11: Goût de
maintenance dans le système de production de vapeur HP (2009)
Elément
|
Coût De maintenance (Dh)
|
Chaudière 98H1A
|
|
223 097,86
|
Chaudière 98H1B
|
|
613 241,72
|
Chaudière 98H1C
|
|
578 327,13
|
Chaudière 98H1D
|
|
211 600,26
|
Total
|
1
|
626 266,97
|
Le coût spécifique de maintenance est donné
par la formule suivante :
Tout calcul fait, le coût de maintenance est :
Donc le coût fixe de production de la vapeur VH est :
Coût fixe de vapeur HP=1,133 Dh/TVH
II-3-4. Coût de revient de la vapeur HP
Le coût de revient de la vapeur HP est la somme des
coûts fixe et variable,
Le coût de revient de la vapeur haute pression est :
Synthèse :
Les calculs précédents ont permis
d'évaluer le coüt de revient de la vapeur HP à 264 dirham la
tonne. Ce coût varie proportionnellement avec les prix des
matières premières, notamment celui du combustible fioul et de
l'électricité
Sachant que la CTE II produit chaque mois environ 119.520 tonnes
de vapeur haute pression, les charges dépensées pour assurer la
production sont évaluées de 31.553.280 DH.
Une étude pour le calcul du coût de revient à
été élaboré en 2009 et les résultats sont :
Tableau 4.12: Goût de production de vapeur
HP (2009)
Production mensuelle de VH
|
72 000 Tonnes
|
Coût de la Tonne de VH
|
222 Dh/TVH
|
Coût mensuelle de production
|
15 984 000 Dh.
|
|
Projet de Fin d'Etudes
|
|
|
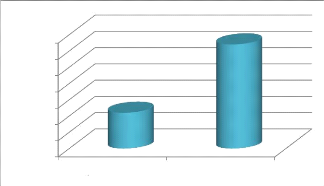
Coût (DH/T)
270
260
250
240
230
220
210
200
Année 2009 Année 2010
Année
Figure 4.4: Augmentation du
coût de la vapeur HP (Dh/T)
L'augmentation du coût de la vapeur est due
essentiellement à l'augmentation des prix des matières
premières, notamment celui du combustible fioul qui a atteint 4600 Dh/T
en fin Avril 2010 et de l'électricité avec 0,78 KWh.
Cependant, juste 19% de cette production est consommée
à l'état HP tandis que tout le reste est converti en vapeur MP
par des vannes réductrice de pression qui ne permette pas la
récupération de l'énergie de détente. Ainsi, le
coüt de production de la vapeur MP est pratiquement le même que
celui de la vapeur HP.
III. Coûts de revient de
l'électricité et de la vapeur HP dans l'unité de
cogéIératioI
III-1. Introduction
L'unité de cogénération permettra de
produire une partie des besoins thermiques de la SAMIR, auparavant
assurés par les chaudières existantes, et une partie des besoins
électriques, auparavant satisfaits par le réseau
électrique provenant de L'ONE.
Cette partie consiste à évaluer le
système de cogénération par le calcul du coût de
revient de l'énergie électrique et de la vapeur HP dans la
chaudière de récupération afin de déterminer la
capacité opératoire optimale qui permet un coût de revient
minimal et une économie dans la facture énergétique.
III-2. Prix d'achat d'électricité de
l'ONE
La SAMIR a conclut un contrat d'approvisionnement en
électricité avec l'ONE (Office Nationale d'Electricité).
Le contrat spécifie un seuil qu'on appelle puissance souscrite. C'est la
puissance que la SAMIR demande à l'ONE de lui mettre, en permanence,
à sa disposition. En contrepartie de ce service l'ONE lui facture:
> Une prime fixe proportionnelle à la puissance
souscrite.
> Un complément de prime fixe lorsque la puissance
réellement appelée, par les installations de la SAMIR,
dépasse la puissance souscrite.
Actuellement, la puissance souscrite de la SAMIR est de 17.1MW.
La tarification actuelle de l'ONE est estimé à :
Prix d'achat d'électricité ONE = 0,78
Dh/KWh
|
Le démarrage du projet UP GRADE (projet de
modernisation de la raffinerie SAMIR) a multiplié le besoin en
énergie électrique, actuellement, il est de l'ordre de 44 MW. Une
partie (28 MW) est produite par l'unité de cogénération,
et le complément restant (16 MW) est acheté de l'ONE.
En cas de trip de l'unité de
cogénération, ce complément dépasse la puissance
souscrite, et la SAMIR paie une pénalité de dépassement
qui rend la facture énergétique très importante.
d'où la nécessité de bien identifier la fourchette
d'utilisation optimale de l'installation de cogénération, sachant
que cette dernière permet de produire une puissance de 40 MW mais dans
des conditions spécifiques, ainsi déterminer la nouvelle
puissance souscrite optimale à spécifier dans le nouveau contrat
avec l'ONE.
III-3. Coût de revient de
l'électricité et de la vapeur produite par l'unité de
cogénération
III-3-1. Méthodologie de calcul
La cogénération permet de produire
l'électricité et la vapeur HP au méme temps, à fin
d'évaluer les coüts de revient on a déterminé
séparément le coüt de revient de chaque produit de
cogénération (électricité et vapeur haute pression)
et de les comparer avec le coût de la vapeur haute pression produite au
niveau de la CTEII et l'électricité acheté à
l'ONE.
Dans le processus de production de la
cogénération, on utilise comme matières premières,
le Gasoil, l'eau déminéralisée, les matières
chimiques et certainement de l'énergie électrique pour la mise en
marche des circuits de pompage, de lubrification et de ventilation.
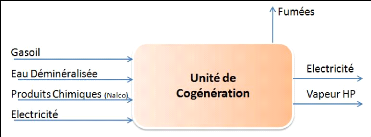
Figure 4.5: Système de
production dans l'unité de cogénération.
Pour le calcul des Coûts de revient de la vapeur HP et
de l'électricité produites par l'unité de
cogénération, on procède aux calculs des consommations
spécifiques par la méme méthode du chapitre
précédant
Le coût de revient par une tonne de vapeur haute pression
est calculé par la formule suivante basée sur les consommations
spécifiques :
VH)
|
( × Prix
D
|
Gao
|
) +
|
q
(
|
q Ecit
P ) + ( × ix
ED Ele
D
|
)
|
x Na
|
) +
|
(
|
|
Nac
|
)
|
|
|
|
i
|
|
|
|
|
|
|
|
|
Avec :
q : débit des matières premières.
DVH : débit de vapeur HP produit par la chaudière
de récupération.
Le coüt de revient par un KWh d'électricité
est calculé par la formule suivante :
|
Projet de Fin d'Etudes
q N72215
) + ( × Pi
|
|
|
Avec :
q : débit des matières premières.
P : Puissance électrique produite par l'unité de
cogénération.
Afin d'évaluer les coüts de revient on a
procédé à deux méthodes :
Méthode I : Gonsiste à
déterminer séparément le coût de revient de chaque
produit de cogénération (électricité et vapeur
haute pression).
Méthode II : on considère que
l'électricité est notre produit principal, et que la
quantité de vapeur produite en parallèle est quelque chose que
nous devions produire nécessairement dans la CTE II si elle n'est pas
produite au niveau de la cogénération. En effet, la vapeur HP
dans ce cas là, sera évaluée aux prix CTE II. Le coüt
d'électricité dans la cogénération est
égale
q q q
Goi ED Eli é
) (
alors au coût de revient total moins le coût de
revient de la vapeur au prix GTE II. × Prix ) + ( Prix ) + ( Prix
)
Gasoil ED Electricit é
P P P
Dans cette méthode le coût de revient par KWh est
calculé par la formule suivante : q q q
al
Avec :
q : débit des matières premières.
P : Puissance électrique produite par l'unité de
cogénération.
III-3-2. Galcul du coût de revient de la vapeur HP et de
l'électricité (méthode I) Calcul du
coût de revient de la vapeur HP (méthode I)
La production de la vapeur HP au niveau de la chaudière
de récupération de l'installation de cogénération
nécessite l'eau déminéralisée, les matières
chimiques, l'énergie électrique pour la mise en marche des
circuits de pompage et les calories contenues dans les fumées à
la sortie de la turbine (figure 4.6)
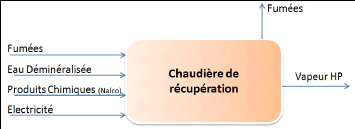
Figure 4.6: production de la VH
dans la chaudière de récupération.
L'unité de cogénération est en mode de
fonctionnement Electricity first, c'est-a-dire que la
production d'électricité est primordial et que la vapeur obtenue
est un gain de récupération d'énergie des
fumées.
La puissance chaudière donc le débit vapeur
dépend directement de la charge de la TAG qui est fixé par
l'opérateur de 0 à 100%.
Dans le calcul du Coût de revient de la vapeur HP
produite par la chaudière de récupération, on ne va pas
prendre en considération la consommation spécifique du gasoil
puisqu'elle entre dans le calcul du Coüt de revient de
l'électricité et que les fumées sont un gain de la
cogénération.
Les données de base pour le calcul sont regroupées
dans le tableau suivant : Tableau 4.13:
Données de base pour le calcul du Goût VH
cogénération.
Elément
|
Valeur
|
Coût Nalco 1801 (Dh/kg)
|
60
|
Coût Nalco 72215 (Dh/kg)
|
26
|
Consommation électrique (kW)
|
495
|
Coût énergie électrique (Dh/kWh)
|
0,78
|
Coût eau déminéralisée (Dh/T)
|
14
|
Remarque :
La consommation en électricité est au niveau
deux motopompes d'aspiration d'eau déminéralisée depuis le
bac de stockage vers la bâche alimentaire de la chaudière (pompes
d'appoint), deux motopompes de refoulement vers l'économiseur (pompes
alimentaires) ainsi qu'une motopompe d'injection de la matière chimique
(Nalco). Il y a aussi deux compresseurs d'air pour la commande des vannes
pneumatiques de la chaudière de récupération (annexe
2).
Le calcul est fait sur la base des consommations
spécifiques, la méthode est décrite
précédemment.
Le tableau suivant regroupe les quantités et les
coûts de vapeur HP produite par la chaudière de
récupération pour les différents régimes de marche
de la cogénération.
Tableau 4.14: Goût de revient
de la vapeur HP dans la cogénération.
Puissance produite (MW)
|
25
|
30
|
35
|
38
|
40
|
VH produite (T/h)
|
50
|
61,2
|
65,7
|
71,2
|
75,4
|
Nalco 1805 (kg/h)
|
0,320736
|
0,380736
|
0,3942
|
0,4272
|
0,4525
|
Nalco 72215 (kg/h)
|
0,320736
|
0,380736
|
0,3942
|
0,4272
|
0,4525
|
CS d'eau déminéralisée (T/TVH)
|
1,1
|
1,01
|
1
|
1,01
|
1,04
|
CS du Nalco (kg/TVH)
|
0,551665
|
0,535021
|
0,516
|
0,516
|
0,516114
|
CS d'électricité (kw/TVH)
|
9,9
|
8,08
|
7,53
|
6,95
|
6,56
|
Coût de revient VH (Dh/TVH)
|
22,273
|
20,837
|
20,389
|
19,937
|
19,632
|
CS : Consommation Spécifique
En représentation graphique, le Coût de la vapeur HP
est donné par la figure suivante :
Cout (DH)
22,5 22 21,5 21 20,5 20 19,5
19
18,5
18
|
|
|
|
25 30 35 38 40
|
Puissance (MW)
Figure 4.7: Goût de la vapeur
HP pour les différents régimes de
cogénération.
Le Coût de la vapeur produite par la chaudière de
récupération diminue pour des régimes de marche de la
cogénération de plus en plus élevé. Cela est
dû essentiellement aux performances de l'unité et a son rendement
qui devient meilleur pour les hauts régimes.
Calcul du coût de
l'électricité (méthode I)
La production de l'électricité au niveau du
turboalternateur de l'installation de cogénération
nécessite le gasoil et l'électricité consommée par
ses auxiliaires.
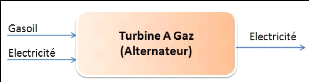
Figure 4.8: Syst~me de production
d'électricité dans l'unité de
cogénération.
De même on procède au calcul des consommations
spécifiques pour déterminer le coût de revient d'un KWh
d'électricité.
Le coüt de revient par un KWh d'électricité
est calculé par la formule suivante :
Avec :
q: Débit des matières premières.
P : Puissance électrique produite par l'unité de
cogénération.
Les consommations en gasoil, électricité et huile
de lubrification sont données dans le tableau suivant en fonction de
différents régimes de marche de la cogénération
:
Tableau 4.15: Consommations de
matières premières pour la génération
électrique.
Puissance produite (MW)
|
25
|
30
|
35
|
38
|
40
|
Débit du gasoil (T/h)
|
7,92
|
8,28
|
9
|
11,5
|
12,6
|
Consommation électricité
|
|
|
|
|
|
(kWh)
|
390
|
390
|
390
|
390
|
390
|
Consommation d'huile (g)
|
3
|
3
|
3
|
3
|
3
|
( Pour la consommation d'électricité (voire annexe
2)
( Le circuit d'huile de lubrification est un système
fermé, cependant il y a consommation d'huile d'appointe, cette
consommation est estimé par le constructeur à 3g/KWh, il est donc
négligeable par rapport au gasoil et l'électricité.
La méthodologie de calcul des consommations
spécifiques ainsi que les Coûts de revient est décrite
précédemment, les résultats sont regroupés dans le
tableau suivant sachant que le Coût du gasoil est 6000Dh/T
(en fin Avril 2010)
Prix du gasoil (Avril 2010) = 6000 Dh/T Tableau
4.16: Coût de revient de l'électricité
dans la cogénération.
Puissance (MW)
|
25
|
30
|
35
|
38
|
40
|
CS du gasoil
|
3,168.10-4
|
2,76.10-4
|
2,57.10-4
|
3,02.10-4
|
3,15.10-4
|
Prix (DH/kWh)
|
1,90
|
1,66
|
1,54
|
1,81
|
1,89
|
CS électricité
|
1,56.10-2
|
1,3.10-2
|
1,11.10-2
|
1,02.10-2
|
0,97.10-2
|
Prix (DH/kWh)
|
0,0121
|
0,01014
|
0,00865
|
0,00795
|
0,00756
|
Coût de revient d'électricité
(DH/kWh)
|
1,912
|
1,67
|
1,548
|
1,817
|
1,897
|
CS : Consommation Spécifique
Ges résultats sont schématisés dans la
figure suivante donnant le coût de l'électricité pour les
différents régimes de marche de la cogénération (la
puissance)
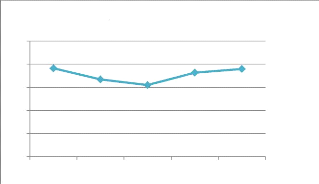
Cout (Dh/kWh)
2,5
2
1,5
1
0,5
0
Coût de revient de
l'électricité
Puissance (MW) 25 (62 %) 30 (75 %) 35 (87 %) 38
(95 %) 40 (100 %)
Figure 4.9: Coût de
l'électricité pour les différents régimes de
cogénération.
1111111111 11111111111 11
Le coût de l'électricité produite par la
cogénération varie en fonction de la puissance, cette variation
dépend de plusieurs facteurs que l'on va détailler dans le
chapitre suivant, notamment la température ambiante, le débit du
gasoil, le lavage off-line et le facteur de puissance Cos ö.
III-3-3. Galcul du coût de revient de
l'électricité (méthode II)
Gette méthode consiste à considérer que
l'électricité est notre produit principal, et que la
quantité de vapeur produite en parallèle est quelque chose que
nous devions produire nécessairement dans la CTE II si elle n'est pas
produite au niveau de la cogénération. En effet, la vapeur HP
dans ce cas là sera évaluée aux prix CTE II. Le coüt
d'électricité dans la cogénération est égale
alors au coût de revient total moins le coût de revient de la
vapeur au prix GTE II.
Dans le processus de production de la
cogénération (Figure 4.5) on utilise comme matières
premières, le Gasoil, L'eau déminéralisée, les
matières chimiques et certainement de l'énergie électrique
pour la mise en marche des circuits de pompage, de lubrification et de
ventilation.
Dans cette méthode le coût de revient par KWh est
calculé par la formule suivante : q q q
Gil ED Eltit é
uil
Avec :
q : débit des matières premières.
P : Puissance électrique produite par l'unité de
cogénération.
Les données de base pour le calcul du Coüt
d'électricité produite par la cogénération sont
regroupées dans le tableau suivant :
Tableau 4.17: Coûts de
matières premières de la cogénération.
Elément
|
Prix
|
Eau déminéralisée (Dh/m3)
|
14
|
Gasoil (Dh/T)
|
6000
|
Energie électrique (Dh/kWh)
|
0,78
|
Vapeur CTE (Dh/T)
|
264
|
Nalco 1801 (Dh/Kg)
|
60
|
Nalco 72215 (Dh/Kg)
|
26
|
Dans ce qui suit, on va calculer les consommations
spécifiques et le Coût de revient de l'électricité
pour les différents régimes de marche de la
cogénération (puissance).
Sachant que :
Tableau 4.18: Coûts de
l'électricité pour les différents régimes de marche
de cogénération.
Puissance produite = 25 MW (régime
62%)
|
|
Quantité
|
Consommation spécifiques
|
Coûts (DH/kWh)
|
Eau déminéralisée (T/h)
|
50
|
0,002
|
0,028
|
Gasoil (T/h)
|
7,92
|
0,0003168
|
1,9008
|
Energie électrique (kwh)
|
885
|
0,0354
|
0,027612
|
Nalco 1801 (kg)
|
0,3
|
0,000012
|
0,00072
|
Nalco 72215 (kg)
|
0,3
|
0,000012
|
0,000312
|
Coüt total de l'électricité (DH/kWh)
|
1,957
|
Coût net de l'électricité (DH/kWh)
|
1,429
|
Puissance produite = 30 MW (régime
75%)
|
|
Quantité
|
Consommation spécifiques
|
Coûts (DH/kWh)
|
Eau déminéralisée (T/h)
|
61,2
|
0,00204
|
0,02856
|
Gasoil (T/h)
|
8,28
|
0,000276
|
1,656
|
Energie électrique (kwh)
|
885
|
0,0295
|
0,02301
|
Nalco 1801 (kg)
|
0,3672
|
0,00001224
|
0,0007344
|
Nalco 72215 (kg)
|
0,3672
|
0,00001224
|
0,00031824
|
Coüt total de l'électricité (DH/kWh)
|
1,708
|
Coût net de l'électricité (DH/kWh)
|
1,170
|
Puissance produite = 35 MW (régime
87%)
|
|
Quantité
|
Consommation
|
Coûts
|
|
|
spécifiques
|
(DH/kWh)
|
Eau déminéralisée (T/h)
|
65,7
|
0,00187714
|
0,02440286
|
Gasoil (T/h)
|
9
|
0,00025714
|
1,54285714
|
Energie électrique (kwh)
|
523
|
0,01494286
|
0,01165543
|
Nalco 1801 (kg)
|
0,3942
|
1,1263E-05
|
0,00067577
|
Nalco 72215 (kg)
|
0,3942
|
1,1263E-05
|
0,00029283
|
Coüt total de l'électricité (DH/kWh)
|
1,579
|
Coût net de l'électricité (DH/kWh)
|
1,074
|
Puissance produite = 38 MW (régime
95%)
|
|
Quantité
|
Consommation spécifiques
|
Coûts (DH/kWh)
|
Eau déminéralisée (T/h)
|
71,2
|
0,00187368
|
0,02435789
|
Gasoil (T/h)
|
11,5
|
0,00030263
|
1,81578947
|
Energie électrique (kwh)
|
523
|
0,01376316
|
0,01073526
|
Nalco 1801 (kg)
|
0,4272
|
1,1242E-05
|
0,00067453
|
Nalco 72215 (kg)
|
0,4272
|
1,1242E-05
|
0,00029229
|
Coût total de l'électricité (DH/kWh)
|
1,851
|
Coût net de l'électricité (DH/kWh)
|
1,347
|
Puissance produite = 40 MW (régime
100%)
|
|
Quantité
|
Consommation spécifiques
|
Coûts (DH/kWh)
|
Eau déminéralisée (T/h)
|
75,4
|
0,001885
|
0,02639
|
Gasoil (T/h)
|
12,6
|
0,000315
|
1,89
|
Energie électrique (kwh)
|
885
|
0,022125
|
0,0172575
|
Nalco 1801 (kg)
|
0,4524
|
0,00001131
|
0,0006786
|
Nalco 72215 (kg)
|
0,4524
|
0,00001131
|
0,00029406
|
Coüt total de l'électricité (DH/kWh)
|
1,934
|
Coût net de l'électricité (DH/kWh)
|
1,436
|
|
Projet de Fin d'Etudes
|
|
|
N.B : Pour les puissances inférieures
à 25 MW, la vapeur produite est de mauvaise qualité
(température et pression inférieurs aux valeurs exigées
par les unités consommatrices de vapeur) En effet, la vapeur produite
dans ce cas de marche doit être évacuée vers
l'atmosphère.
Les résultats obtenus sont schématisés
dans la courbe suivante donnant l'évolution du coût de production
d'électricité en fonction de la puissance produite, donc du
régime de marche de la cogénération.
|
1,6 1,4 1,2
1 0,8 0,6 0,4 0,2
0
|
|
Coût de revient de
l'électricité
|
|
Cout en DH/kWh
|
|
|
|
|
|
|
|
|
|
|
|
|
|
|
|
|
|
|
|
|
|
|
|
|
|
|
|
|
25 30 35 38 40
Puissance en MW
|
|
|
Projet de Fin d'Etudes
|
|
|
Figure 4.10: Evolution du
coût de production d'électricité en fonction de la
puissance
11111111111
III-3-4. Synthèse et interprétation
En fonction de la puissance produite, on distingue
différents coüts de revient d'électricité.
Les puissances 25 MW et 40 MW correspondent respectivement aux
régimes 62% et à 100% de la charge opératoire de
l'unité de cogénération, c'est en fait la plage de marche
qui permet de produire de la vapeur HP de bonne qualité en
matière de pression et de température. D'après les
résultats on constate que la puissance 35MW est celle qui
représente le coût de revient minimal. Mais il reste à
vérifier est-ce-que cette puissance représente le régime
de marche le plus optimal ? Réponse au chapitre suivant.
IV. Conclusion
Il y a plusieurs méthode pour le calcul des Goûts de
revient des utilités, cependant la méthode dite des consommations
spécifiques reste la plus significative et la plus utilisée.
Le Goût de la vapeur produite par la GTE II a connu une
augmentation de 19% en 2010 (264 Dh/T) par rapport à 2009 (222 Dh/T).
Cela est dü essentiellement à l'augmentation des prix de
matières premières, notamment du fuel et donc du pétrole
brut, car la facture pétrolière du Maroc a multiplié, 8,18
MMDH en fin Avril 2010 au lieu de 3,93 MMDH une année avant.
Pour ce qui est de l'électricité achetée par
l'ONE, elle a augmentée de 0,68 Dh/kWh en 2009 à 0,78 Dh/kWh en
2010, soit une augmentation de 14,7 %.
Le coüt de l'électricité produite par
l'unité de cogénération varie en fonction du régime
de marche c.-à-d. de puissance aux bornes de l'alternateur, cette
évolution atteint un minimum pour la puissance 35 MW, soit le
régime 87%.
Le gasoil utilisé dans l'unité de
cogénération est un gasoil 50ppm qui coüte 6000Dh /T,
d'oüla raison pour laquelle le coüt de l'électricité
est élevé par rapport a son coüt en 2009 pendant le
démarrage et l'essai ou l'unité a été
fonctionnée avec du gasoil 10000ppm moins cher.
Chapitre V : Etude des différents scénarios
de distribution de l'électricité dans la raffinerie &
détermination de la nouvelle puissance souscrite
- Détermination de la marche
opératoire optimale de l'unité de cogénération.
- Différents scénarios de
distribution d'électricité dans la raffinerie.
- Détermination de la nouvelle puissance
souscrite.
I. Détermination de la marche opératoire
optimale de l'unité de cogénération
Avant de déterminer le régime de marche optimal
de l'unité de cogénération, on va étudier les
paramètres qui influence sur cette marche, à savoir la
température ambiante, le débit du gasoil, la qualité d'air
et le facteur de puissance Cosö.
I-1. Influence de la température ambiante
Pour étudier l'influence de la température
ambiante sur la marche de la cogénération, des essais ont
été faits pendant le démarrage de l'unité et les
résultats sont donnés dans le tableau suivant qui montre les
différentes entrées et sorties du système en fonction de
la température ambiante et la charge de la turbine à gaz.
Tableau 5.1: Variation des
paramètres caractéristiques de la cogénération en
fonction de la température ambiante.
Température ambiante
|
T=46°C
|
T=25°C
|
T=5°C
|
La charge de la turbine à gaz
|
60 %
|
100 %
|
60 %
|
100 %
|
60 %
|
100 %
|
Débit du gasoil (T/h)
|
6.78
|
9.65
|
7.61
|
11.12
|
8.29
|
12.35
|
Débit nominal
d'eau déminéralisée (m3/h)
|
50.14
|
71.78
|
52.59
|
89.12
|
53.61
|
84.64
|
Débit maximal
d'eau déminéralisée (m3/h)
|
57.235
|
80.84
|
64.13
|
91.224
|
60.641
|
94.32
|
Débit de la vapeur à haute pression (T/h)
|
49
|
68.6
|
48.6
|
71.5
|
48.3
|
74.7
|
Puissance électrique (MW)
|
20
|
33.29
|
23.91
|
39.84
|
27.18
|
45.30
|
Remarque :
Dans l'unité de cogénération la
température ambiante influence sur les composants suivants :
> Système de lavage ON LINE : La turbine
doit marcher à pleine vitesse et ne doit pas avoir entamée la
procédure d'arrêt. Le lavage est permis à toute charge,
mais pas à n'importe quelle température ambiante et
humidité. La température ambiante doit être
supérieure à 10°C.
> Système de lubrification : Lorsque la
température ambiante est élevée, la vanne VTR-1 (vanne
thermostatique trois voies) peut s'ouvrir entièrement, si bien que le
débit d'eau de refroidissement dans les réfrigérants et
dans les boucles de dérivation s'effectue selon des débits
constants. Si la température ambiante est suffisamment
élevée, la
température du fluide de lubrification peut
dépasser la valeur de réglage de la vanne VTR-1.
> Température d'huile de lubrification :
Pour déterminer l'adéquation des huiles, commencer par
établir la température ambiante attendue la plus basse à
laquelle la machine doit être soumise ; le point d'écoulement de
l'huile doit être au moins 10°C en dessous de ce chiffre. Si la
température ambiante est inférieure à -20°C, de
l'huile ayant un indice de viscosité élevé d'au moins 140
doit être utilisée.
Les résultats du tableau sont schématisés
dans la figure suivante :
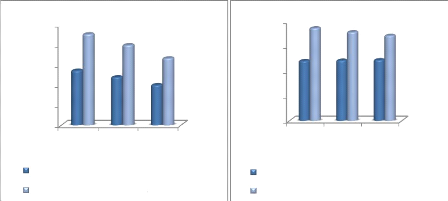
Puissance electrique (MW)
Puissance électrique à 60 % Puissance
électrique à 100 %
40
50
30
20
10
0
Température ambiante (°C)
5 25 46
Debit de la VII (T/h)
Débit de la VH à 60 % Débit de la VH
à 100 %
80
40
60
20
0
Température ambiante (°C)
5 25 46
Figure 5.1: Variation des
différentes productions en fonction de la température ambiante
Synthèse et interprétation
La raffinerie utilise de la vapeur surchauffée avec des
caractéristiques bien précises, une température
supérieure à 400°C et une pression supérieure
à 42bar.
Faute de quoi, une vapeur qui n'atteint pas ces
caractéristiques est rejetée à l'atmosphère.
L'unité de cogénération peut produire une
telle qualité de vapeur, à partir d'une charge de 60% de la
T.A.G, soit une puissance de 24 MW aux bornes de l'alternateur.
Les performances de l'unité de
cogénération sont d'autant plus meilleures que la
température ambiante est faible, car la quantité d'air
aspirée a une masse volumique importante et lors de la détente
dans la turbine à gaz on obtient un volume important d'air ce qui
augmente le rendement de la turbine à gaz.
Autrement dit en augmentant la température du milieu
extérieur, on consomme moins de combustible vu que l'échange
thermique entre le milieu réactionnel (au niveau de la chambre de
combustion) et le milieu extérieur est moins important d'où la
diminution du débit de la vapeur VH et de la puissance électrique
produite.
I-2. Influence de la qualité d'air
La bonne marche de l'unité de cogénération
dépend aussi du système de lavage du compresseur et de la
turbine.
En effet les coüts de maintenance et d'exploitation de
l'unité sont influencés par la qualité de l'air que la
turbine consomme. En plus des effets délétères des
contaminants en suspension dans l'air sur les composants des parties chaudes,
des impuretés telles que la poussière, le sel et l'huile peuvent
également entraîner l'érosion des pales du compresseur et
un encrassement. Des particules de 20ì qui pénètrent dans
le compresseur peuvent provoquer l'érosion significative des pales.
L'encrassement peut être causé par de microscopiques particules de
saleté qui pénètrent le compresseur ainsi que par
l'ingestion de vapeur d'huile, de fumée, de sel marin et de vapeurs
industrielles.
La corrosion des pales de compresseur entraîne une
piqûre de la surface des pales qui, en plus de l'augmentation de la
rugosité de surface, sert également de sites potentiels pour un
début de crique de fatigue. Ces rugosités de surface et ces
changements de contours de pale diminuent le rendement et l'écoulement
d'air du compresseur ce qui, à son tour, réduit le rendement de
la turbine à gaz et le rendement thermique global.
En général, la détérioration d'un
compresseur à débit axial peut être la cause majeure de
perte de rendement et d'efficacité de la turbine à gaz. Des
pertes récupérables, attribuables à l'encrassement des
pales du compresseur comptent en général pour 70 à 85% des
pertes de performance constatées. Comme le montre la figure suivante
:
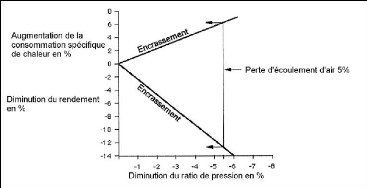
Figure 5.2:
Détérioration des performances de la turbine
à gaz en raison d'un encrassement des aubes du compresseur.
Interprétations :
L'encrassement du compresseur dans une mesure où le
flux d'air est réduit de 5%, réduira le rendement de 13% et
augmentera le taux thermique de 5,5%. Heureusement, on peut beaucoup faire en
mettant en application les procédures d'exploitation et de maintenance
adéquates pour minimiser les pertes de type encrassement. Les
systèmes de lavage de
compresseur en ligne (ON-LINE) sont
disponibles et sont utilisés pour maintenir le rendement du compresseur
en lavant le compresseur jusqu'à 95% de la charge de base (ou moins)
avant qu'un encrassement significatif n'intervienne.
Q = U.I. 3 .Sin ?
Les systèmes hors ligne (OFF-LINE)
sont utilisés pour nettoyer les compresseurs fortement encrassés.
Le nettoyage hors ligne ne peut être fait que si l'unité est
arrêtée et froide. Le lavage doit être fait à une
vitesse de compresseur de 600 rpm. Pour des questions de méthodes, le
système de nettoyage hors ligne a été conservé
comme étant la procédure la plus efficace. Une combinaison d'un
lavage de compresseur quotidien en ligne et d'un cycle de lavage hors ligne est
la méthode préférée.
Abattement des NOx
En plus de son rôle de nettoyage contre l'encrassement,
le lavage off-line a un intérêt écologique et
environnemental, il permet ainsi de réduire les rejets de la turbine en
NOx contenus dans les fumées d'échappement. Un débit d'eau
est injecté dans la chambre de combustion de la turbine. En fonction de
la charge de turbine le débit d'eau injecté dans la turbine
varie, au fonctionnement nominal le débit d'eau injecté est de
6,55 T/h
I-3. Influence du facteur de puissance Cos á
Le facteur de puissance appelé également Cosinus
á est le déphasage angulaire entre la tension et
l'intensité du courant dans un circuit alternatif.
Le facteur de puissance est une caractéristique d'un
récepteur électrique. En régime alternatif
sinusoïdal, on distingue trois puissances :
· La puissance active : qui est
transformée en énergie mécanique (moteur) et en chaleur
(éléments résistif).Elle se note P.

· La puissance réactive :
nécessaire à la magnétisation des machines
(moteurs, transformateurs, bobines de relais ...). Elle se note Q.

· La puissance apparente : qui
caractérise la puissance globale (réactive + active) que peut
Tg ?
P
fournir un réseau électrique. Elle se note S.

D'oü
Une trop grande consommation d'energie reactive pour une
installation electrique va augmenter considerablement ses courants en ligne
bien que sa puissance active n'est pas changee. Il y a donc interest
à avoir un bon Cos a (Cos a proche de 1 d'où un
angle a petit) car si le Cos a est petit (dephasage
important) il faudra fournir une puissance reactive plus grande d'où une
intensite plus grande.
Le tableau suivant donne quelques valeurs du facteur de puissance
Cos a pour le regime de marche 62%, soit une puissance active de 25 MW
de l'unité de cogénération dans la SAMIR :
Tableau 5.2: Variation du facteur
de puissance Cos a en fonction de la puissance
réactive.
Puissance active (MW)
|
25
|
25
|
25
|
25
|
25
|
25
|
25
|
puissance réactive (MVAR)
|
14,8
|
13,2
|
11,6
|
10,6
|
9,1
|
7
|
5,07
|
Cos a
|
0,86
|
0,884
|
0,907
|
0,92
|
0,94
|
0,962
|
0,98
|
La figure suivante represente la variation du facteur de
puissance en fonction de l'énergie reactive pour une energie active
donnee (25MW).
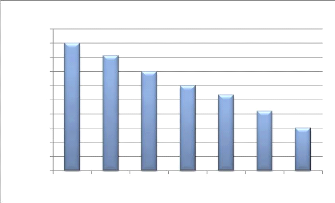
Facteur de puissance
0,98
0,96
0,94
0,92
0,88
0,86
0,84
0,82
0,9
0,8
1
5,07 7 9,1 10,6 11,6 13,2 14,8
Puissance réactive
Variation du facteur de puissance
Figure 5.3: Variation du facteur de
puissance Cos a en fonction de la puissance réactive.
Interprétation
La figure montre bien qu'à puissance active constante,
une augmentation de la puissance reactive va augmenter les courants en ligne
absorbes par l'installation electrique et par consequent il y a diminution du
facteur de puissance Cos á, qui signifie les pertes au niveau du reseau
electrique.
Les distributeurs d'electricite facturent generalement et
seulement la puissance active consommee. Les pertes dans les lignes ne sont
pas facturees. Or celles-ci dependent de
l'intensité apparente appelée par les
consommateurs (pertes par effet Joule). Si le facteur de puissance d'une
installation est faible, l'intensité appelée est grande mais la
puissance consommée est faible. G'est pourquoi, pour le cas de la SAMIR
(installations raccordées à la haute tension), la facturation ne
tient pas uniquement compte de la puissance active consommée mais aussi
du facteur de puissance appelé, en effet dans le contrat
d'approvisionnement de l'électricité signé avec l'ONE, ce
dernier a exigé une pénalité de chute du facteur de
puissance.
Remèdes
Pour limiter les courants en ligne et donc l'énergie
réactive absorbée par l'installation, la SAMIR a installée
au niveau de la GTE II des batteries de condensateurs sources d'énergie
réactive.
Il y a aussi au niveau des unités du nouveau projet
UPGRADE des compensateurs d'énergie réactive qui servent à
améliorer le facteur de puissance.
I-4. Marche optimale de la cogénération
L'unité de cogénération permettra de
produire une partie des besoins thermiques et électriques de la
raffinerie, auparavant assurés par les chaudières existantes et
par le réseau électrique ONE.
Pour déterminer la marche opératoire optimale
parmi les états de marches étudiées dans le chapitre 4, on
procède à une comparaison économique de la valeur de la
facture mensuelle d'énergie électrique pour chaque marche
opératoire.
La variation du coüt de revient de
l'électricité en fonction de la puissance produite par
l'unité de cogénération (chapitre 4) est donnée par
la figure suivante :
|
1,6 1,4 1,2
1 0,8 0,6 0,4 0,2
0
|
|
Coût de revient de
l'électricité
|
|
Cout en DH/kWh
|
|
|
|
|
|
|
|
|
|
|
|
|
|
|
|
|
|
|
|
|
|
|
|
|
|
|
|
25 30 35 38 40
Puissance en MW
|
|
Figure 5.4: Variation du
coût de production d'électricité en fonction de la
puissance produite.
Au démarrage des unités de production du projet
de modernisation de la SAMIR en Mars 2010 (Projet Upgrade), la consommation
totale en électricité de la raffinerie est évaluée
à 45 MW et la production maximale de l'unité de
cogénération est d'environ 40 MW.
Le calcul ci-après concerne en particulier la
détermination de la puissance optimale qu'on peut produire par
l'unité de cogénération et qui permet d'une part d'obtenir
un coüt de revient minimal par rapport aux autres marches
opératoire, et d'autre part un coüt de revient minimal
vis-à-vis de l'ONE.
Les valeurs de la facture énergétique pour les
différentes marches opératoires de l'unité de
cogénération sont résumées dans le tableau suivant
sachant que la raffinerie étant en marche 24H/24 et 7J/7.
Tableau 5.3: Facture
électrique de la raffinerie pour différents régimes de
cogénération.
Puissance Produite (MW)
|
|
|
25
|
|
30
|
|
35
|
|
38
|
|
40
|
Coût de production
|
(DH/KWh)
|
|
1,429
|
|
1,170
|
|
1,074
|
|
1,347
|
|
1,436
|
Charges mensuelles de production
|
(DH)
|
25
|
722
|
000
|
25
|
272
|
000
|
27
|
064
|
800
|
36
|
853
|
920
|
41
|
356 800
|
Complément à acheter de l'ONE
|
(MW)
|
|
20
|
|
|
15
|
|
|
10
|
|
|
7
|
|
|
5
|
Prix d'achat ONE
|
(DH/KWh)
|
|
0.78
|
|
|
0.78
|
|
0.78
|
|
0.78
|
|
0.78
|
Charges mensuelles d'achat ONE
|
(DH)
|
11 + 2
|
232
000
|
000
000
|
8
|
424
|
000
|
5
|
616
|
000
|
3
|
931
|
200
|
2
|
808 000
|
Facture électrique mensuelle
|
(DH)
|
38
|
954
|
000
|
33
|
696
|
000
|
32
|
680
|
800
|
40
|
785
|
120
|
44
|
164 800
|
N.B : pour le régime de 25 MW, la
puissance appelée de l'ONE (20MW) dépasse la puissance souscrite
17,1 MW, donc la SAMIR doit payer la pénalité de
dépassement qui est 2MDH.
Les résultats de calculs sont schématisés
dans la figure suivante :
Charges mensuelles d'électrcité en
DH
50 000 000 45 000 000 40 000 000 35 000 000 30 000
000 25 000 000 20 000 000 15 000 000 10 000 000 5 000
000 0
|
|
|
|
25 30 35 38 40
|
|
Charges mensuelle de production
Charges mensuelle d'achat du complèment (ONE) en DH
Facture électrique mensuelle en (DH)
|
Puissance en MW
|
Figure 5.5: Evolution des charges
totales d'électricité en fonction du régime de
la cogénération.
Synthèse et
interprétation
D'après les résultats obtenus, on déduit
que le régime de marche opératoire 87% de l'unité de
cogénération qui permet de produire la puissance 35 MW est celui
qui correspond à une facture minimale, et donc c'est le régime
optimal de fonctionnement de l'unité
Cependant le coüt de revient de
l'électricité produite par l'unité de
cogénération dépend fortement du prix de gasoil. Ce
dernier a connu une augmentation en avril 2010 (6000 DH/Tonne) un mois
après le démarrage du nouveau projet UGRADE, la figure ci-dessous
donne une comparaison entre la facture électrique en 2009 où le
prix du gasoil était 4114 DH/Tonne et celle de 2010.
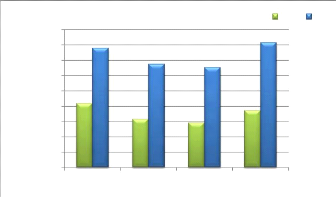
45 000 000
40 000 000
35 000 000
30 000 000
25 000 000
20 000 000
15 000 000
10 000 000
5 000 000
Facture électrique en DH
0
25 30 35 38
Puissance en MW
2009 2010
Figure 5.6: Facture
électrique en 2009 et 2010 en fonction du régime de marche de
la cogénération
Le groupe turboalternateur présente des performances
meilleures pour une puissance de 35MW tel que le prix de revient de
l'électricité produite est minimale, Cette puissance reste
Optimale.
Le coüt de l'électricité produite par
l'unité de cogénération varie en fonction du régime
de marche c.-à-d. de puissance aux bornes de l'alternateur, cette
évolution atteint un minimum pour la puissance 35 MW, soit le
régime 87%.
Le gasoil utilisé dans l'unité de
cogénération est un gasoil 50ppm qui coüte 6000Dh /T,
d'où la raison pour laquelle le coüt de l'électricité
est élevé par rapport a son coüt en 2009 pendant le
démarrage et l'essai où l'unité a été
fonctionnée avec du gasoil 10000ppm moins cher.
II. Différents scénarios de distribution
d'électricité dans la raffinerie
II-1. Consommations des
unités
La raffinerie SAMIR comporte plusieurs unités (voire
annexe 3) dont les consommations électriques varient en fonction de
leurs installations (moteurs asynchrones, compresseurs, pompes,
réacteurs, échangeurs, colonnes, extracteur, ventilateur,
aéro-réfrégérants...).
Avant la mise en service du projet (UPGRADE) de modernisation
de la SAMIR, la consommation de cette dernière en
électricité est évaluée à 18 MW. Aujourd'hui
avec le nouveau projet, cette consommation est multipliée et est devenue
45 MW
Les unités du projet UPGRADE consomment 27 MW.
L'ancienne raffinerie se divise en 3 grandes zones
industrielles (Zone I, II et III). Chaque zone englobe des unités de
fabrication ou de traitement dont la consommation électrique est
évaluée à 18 MW et repartie de la manière suivante
:
Tableau 5.4: répartition de
la consommation électrique des unités de la SAMIR.
Unité
|
Consommation en MW
|
Zone I: ATK - Merox - topping I et II - platforming
|
2,5
|
Zone II: Platforming II - Topping III - HDS - HDT.
|
4,5
|
Zone III : Complexe des huiles lubrifiantes.
|
5
|
CTE II + Cogénération
|
4,5
|
UPGRADE
|
27
|
Off site
|
1,5
|
Total
|
45
|
Remarque
Cette répartition d'électricité au niveau
de la raffinerie va nous aider à la mise en place du système de
délestage, et ainsi savoir les unités à délester en
cas de coupure de l'électricité du réseau ONE.
Le système de délestage est étudié
d'une manière détaillée dans le chapitre VI
II-2. Différents scénarios de
distribution d'électricité.
Dans l'étude des scénarios de distribution
d'électricité dans la raffinerie, on va prendre en
considération la nouvelle turbine à vapeur qui va être
installée en parallèle avec les vannes réductrice de
pression dans la CTE II, elle permettra de réduire la pression et la
température de vapeur haute pression HP afin d'assurer
l'approvisionnement de l'usine en vapeur moyenne pression ainsi que la
récupération d'une énergie mécanique sur l'arbre de
la turbine.
Cette énergie est convertie par l'intermédiaire
d'un alternateur en énergie électrique débité sur
le réseau électrique.
Cette nouvelle turbine à vapeur permet d'augmenter
l'autonomie électrique de la SAMIR
En effet, l'analyse et le dimensionnement de cette turbine
à vapeur est étudié dans le chapitre six consacré
aux solutions d'amélioration du système de production
d'énergie
Cette turbine à vapeur permettra de produire une puissance
électrique de 10 MW.
La puissance appelée par la SAMIR ne doit pas
dépasser la puissance souscrite avec l'ONE qui est fixée à
17.1 MW, faute de dépassement de cette puissance la SAMIR paye une
pénalité de 2MDH plus la surconsommation.
Le rendement de l'unité de cogénération
est meilleur quand la température ambiante est faible, donc dans la nuit
on peut fonctionner cette unité avec le régime 35 MW
préalablement justifié.
Sachant que les besoins en électricité de la
raffinerie sont évalués à 45 MW, les différents cas
de distribution et de production de l'électricité qu'on a
proposés pour un bon fonctionnement de la raffinerie, une augmentation
de son autonomie énergétique et par conséquent une
diminution de la facture électrique sont les suivants :
Cas 1 : les trois sources
d'électricité sont en fonctionnement normal
gen MW 3
V 10 MW
?
NE 7 MW
E
Cen 0 MW
d h à h
07 22
?
|
0 MW MW
|
Cas 2 : Arrét de l'unité de
cogénération (Trip de l'unité)
Cas 3 : Arrêt de la turbine à
vapeur TAV (maintenance ou trip)
MM 35 MW
CoCog
0 MW
AV 0 MM
?
NE 15 MM
E
7
h à h
|
10MW
|
|
Projet de Fin d'Etudes
|
|
|
Cas 4 : Arrét de l'unité de
cogénération et de la turbine à vapeur.
AV 10 MW NE 0 MW
g
Cas 5 : Coupure de l'électricité
du réseau l'ONE

Cas 6 : Arrét de la TAV et coupure de
l'électricité du réseau l'ONE
Dans ce dernier cas une puissance de 7MW (45-38) sera
indispensable pour assurer le fonctionnement de toutes les unités de la
raffinerie, pour compenser ce besoin on aura recours au délestage,
c-à-d. sacrifier par certaines unités de la raffinerie qui ne
représentent pas un danger (Ex : incendie) en cas d'arrêt et ne
sont pas nécessaires pour la société.
L'étude de délestage est détaillée
dans le chapitre VI consacré aux solutions d'amélioration du
système de production d'énergie.
III. Détermination de la nouvelle puissance
souscrite III-1. Rappel du contrat ONE-SAMIR
Ci-dessous un extrait d'un contrat ONE d'approvisionnement en
électricité :
Article - OBJET DU CONTRAT
L'Abonné demande à l'ONE, qui accepte, de lui
fournir aux conditions du présent contrat l'énergie
électrique nécessaire à l'alimentation de l'installation
désignée aux dispositions particulières. Sauf stipulation
expresse contraire figurant aux dispositions particulières du
présent contrat, l'abonné s'engage à n'utiliser aucune
source d'énergie électrique autre que le réseau de l'ONE
et à demander la révision du présent contrat pour
l'application, s'il y a lieu, des conditions tarifaires propres aux fournitures
d'appoint, s'il décidait d'alimenter simultanément ses
installations par un moyen quelconque de production autonome d'énergie
électrique.
Article - PUISSANCES SOUSCRITES
1) Puissance souscrite
L'abonné s'engage à limiter les puissances
appelées par son installation, aux valeurs indiquées aux
dispositions particulières.
2) Dépassement des puissances
souscrites
Le dépassement est la puissance non souscrite
appelée à titre exceptionnel par l'abonné, au cours d'un
mois, en excédent de la puissance souscrite.
L'ONE n'est pas tenue de faire face aux appels qui
dépasseraient la puissance souscrite.
3) Modification des puissances souscrites
Les puissances sont souscrites par l'Abonné, pour la
durée du présent contrat. Toutefois, pendant l'Abonné a la
faculté de les réduire à concurrence de ?°I. Ces
réductions prennent effet à dater du début du mois suivant
la demande de l'Abonné, par un avenant de modification des puissances
souscrites qui sera annexé au présent Contrat.
Les puissances souscrites pourront être
augmentées par avenant, pendant la durée du contrat, par tranches
d'au moins ?°I. La mise à disposition des nouvelles puissances
souscrites prend effet à la date fixée à l'avenant en
considération de la durée d'exécution des travaux
éventuels. Les nouvelles puissances sont souscrites pour une
durée d'un an au moins.
Dans les dispositions particulières on peut trouver :
· Caractéristiques du courant
· Mesure de la fourniture
· Conditions de la fourniture (tranches horaires,
tarification...)
· Clauses diverses
Le principe de la tarification de l'électricité est
illustré dans le schéma suivant :
CONTRAT D'ABONNEMENT
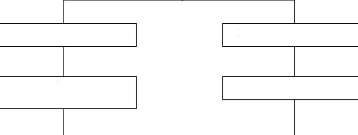
CONSOMMATION
COÛT DE LA CONSOMMATION
PUISSANCE SOUSCRITE
PRIME FIXE
MONTANT DE LA FACTURE
Figure 5.7: Principe de
tarification de l'électricité (ONE
La SAMIR a conclut un contrat d'approvisionnement en
électricité avec l'ONE (Office Nationale d'Electricité).
Le contrat spécifie un seuil qu'on appelle puissance souscrite. C'est la
puissance que la SAMIR demande à l'ONE de lui mettre, en permanence,
à sa disposition. En contrepartie de ce service l'ONE lui facture:
> Une prime fixe proportionnelle à la puissance
souscrite (1419,95 DH/kW/an hors taxes),
> Un complément de prime fixe lorsque la puissance
réellement appelée, par les installations de la SAMIR,
dépasse la puissance souscrite.
Actuellement, la puissance souscrite de la SAMIR est de 17.1MW.
La tarification actuelle de l'ONE est estimé à :
Prix d'achat d'électricité ONE = 0,78
DH/KWh/hors taxes
|
III-2. Dépassement de puissance
souscrite
Le dépassement de puissance souscrite est toujours eu lieu
en cas de trip (arrest) de l'unité de cogénération qui
permet de fournir jusqu'à 38 MW d'électricité.
Actuellement, la puissance souscrite de la SAMIR est de
17.1MW. Faute de dépassement de cette puissance, la SAMIR paye la
pénalité de dépassement plus les frais de surconsommations
selon les tranches horaires illustrées dans le tableau
ci-après.
D'après le contrat de fourniture de l'énergie
électrique en haute tension au poste 60/20 kV de la SAMIR à
Mohammedia, signé entre l'ONE et la SAMIR, les postes horaires sont
définis comme suit :
Tableau 5.5: Postes horaires pour
la tarification d'électricité.
POSTE HORAIRE
|
HIVER Du 01 Octobre au 31 Mars
|
ETE Du 01 Avril au 30 Septembre
|
Heures de pointe (hp)
|
17h00 à 22h00
|
18h00 à 23h00
|
Heures pleines (hpl)
|
07h00 à 17h00
|
07h00 à 18h00
|
Heures creuses (hc)
|
22h00 à 07h00
|
23h00 à 07h00
|
Les valeurs des redevances du Tarif Optionnel Très Longue
Utilisation (TLU) sont les suivantes :
- Redevance de puissances souscrites : 1419,95
DH/kW/an hors taxes
- Les coefficients de pondération des puissances
souscrites sont : En heures de pointe : 1
En heures pleines : 0,6
En heures creuses : 0,4
La pénalité (mensuelle) de dépassement est
alors estimée à :
|
Projet de Fin d'Etudes
c s
|
|
|
Le prix de pénalité est de l'ordre de 2 MDH
Les frais de surconsommation sont donnés par la formule
suivante :

Avec :
Pf : prime mensuelle fixe (2129,93).
Ps : puissance souscrite =17,1 MW.
Pp : puissance appelée aux heures de pointe. Ppl :
puissance appelée aux heures pleines. Pc : puissance
appelée aux heures creuses.
,
Alors la facture totale en cas de dépassement est
donnée par la formule suivante :
? ? ? ? ? ? ?
1 45 1 7,1 0,6 45 1 7,1 0,4 45 1 7,1 . 1 0
? ? 3
ti ? ? ? ? ? ?
En cas de trip (arrét) de l'unité de
cogénération, la totalité des besoins électriques
de la raffinerie sont satisfaites par le réseau ONE, la puissance
appelée (45 MW) dépasse alors la puissance souscrite.
Sachant que les besoins de la raffinerie en
électricité sont évalués à 45 MW,
Par exemple On peut calculer les frais de surconsommation pendant
un jour (tous les postes horaires) en cas d'arrêt de l'unité de
cogénération.
Ce sont les frais d'électricité pour un jour de
surconsommation, si on ajoute la pénalité de dépassement 2
MDH, le total est de l'ordre de 11 MDH sera facturé à la fin du
mois, plus la consommation usuelle.
III.3 Détermination de la nouvelle puissance
souscrite
Dans le paragraphe précédent, on a vu que le
dépassement de la puissance souscrite constitue des frais
supplémentaires qui rendent la facture électrique de la SAMIR
très importante.
Pour éviter tout risque de dépassement et de
pénalité la puissance appelée doit être inferieure
à la puissance souscrite.
Dans le cas où la puissance atteinte est
supérieure à la puissance souscrite, il faut calculer si
l'augmentation de la puissance souscrite jusqu'au niveau du dépassement
ne coûte pas moins cher que le dépassement de puissance
facturé. Si le dépassement ne se produit qu'une fois et qu'il
n'est pas très important, la pénalité est la plus
avantageuse des solutions.
Cependant pour éviter la pénalité et les
frais de surconsommations, on a proposé deux solutions :
Solution I : garder la même puissance
souscrite (17,1 MW)
Pour adopter cette solution, il faut maîtriser la marche de
l'unité de cogénération, c-à-d. éviter
l'arrêt urgent (Trip) de l'unité.
L'unité de cogénération est
récemment mise en service (2009), donc les arréts et les
problèmes de jeunesse sont de plus en plus fréquents, ce qui est
normal car la maîtrise et la bonne marche de l'unité
nécessite une période (6 à 12 mois) après la mise
en service de l'installation
Cette unité est actuellement en arrêt pour les
travaux de maintenance (changement filtre gasoil, nettoyage, réglage du
synchronoscope...), après cet arrét l'unité de
cogénération est censée assurer un bon fonctionnement pour
une puissance d'au moins 30 MW.
D'autre part la mise en place de la nouvelle turbine à
vapeur va assurer une puissance de 10 MW qui sera débitée sur le
réseau électrique de la SAMIR.
Donc avec cet état de marche, on n'aura pas besoin
d'augmenter la puissance souscrite et rajouter ainsi des charges
supplémentaires à la facture électrique de la
société, la puissance souscrite est gardée à 17,1
MW et si le dépassement ne se produit que de temps à autre et
qu'il n'est pas très important, la pénalité est la plus
avantageuse des solutions.
Solution II : augmenter la puissance
souscrite.
La puissance souscrite peut être modifiée par
avenant, pendant la durée du contrat.
Pour augmenter la puissance souscrite il faut calculer si
l'augmentation de la puissance souscrite jusqu'au niveau du dépassement
coûte moins cher que le dépassement de puissance facturé,
sinon ce n'est pas la peine d'augmenter cette puissance.
L'augmentation de la puissance souscrite dépend
étroitement du nombre d'arrêt de l'unité de
cogénération, elle est recommandée dans le cas où
le trip de l'unité est fréquent et le nombre d'arrêt
(maintenance, modification...) est élevé.
La formule suivante donne la relation entre la puissance
souscrite, la facture électrique et le nombre d'arrêt.
Avec :
Ftotale : facture électrique (DH) PS : puissance
souscrite (MW) á : nombre d'arrêt
Dans le contrat ONE-SAMIR, le dépassement est
facturé de la manière suivante : v' Pénalité de
dépassement = 2MDH
v' Surconsommation (puissance > 17,1 MW)
v' Un arrêt est équivaut à cinq arrêt
(par mois)
Donc pour calculer la nouvelle puissance souscrite, il faut
déterminer le nombre d'arrêt à partir duquel on doit
augmenter la puissance souscrite, ce nombre doit d'être supérieur
à six, mais sa détermination nécessite la connaissance de
la facture maximale à ne pas dépasser.
Sachant que l'augmentation de la puissance souscrite entraine
une augmentation de la prime fixe de souscription et de la
pénalité en cas de dépassement de la nouvelle puissance
souscrite.
Parmi ces deux solutions, la première est la plus
avantageuse de part ces charges qui sont moins que la deuxième,
cependant pour adopter la première solution, le bon fonctionnement de
l'unité de cogénération et la mise en place de la turbine
à vapeur sont nécessaires.
Chapitre VI : Améliorations du système de
production d'énergie.
- Calcul de l'échangeur de chaleur.
- Calcul de la nouvelle turbine à vapeur.
- Amélioration de la cogénération.
- Mise en place du système de
délestage.
I. Introduction
Etre lié à une seule source d'énergie
électrique, représente un risque majeur pour toutes les
unités de production d'une industrie fortement consommatrice
d'énergie comme celle du raffinage. Malgré la présence de
deux groupes de secours, la puissance fournie en cas de coupure
d'électricité (arrêt de la cogénération ou du
réseau ONE) est de l'ordre de quelques MW et reste très faible
devant la demande des installations vitales de la raffinerie.
Pour faire face à une crise électrique probable,
la SAMIR renforce sa volonté de diversifier ses sources
énergétiques et de recourir à une autonomie
électrique pour sécuriser ses besoins en énergie.
Parmi les unités de la raffinerie, il y a celles qui ne
tolèrent pas un arrêt brusque, car elles contiennent des produits
dangereux et qui peuvent avoir un impact sur le matériel et la
sécurité du personnel. Les produits pétroliers ou
hydrocarbonés (propane, butane, fioul, gasoil, kérosène,
...) sont hautement inflammables, explosibles et toxiques.
La mise en place d'une turbine à vapeur pour augmenter
l'autonomie électrique de la raffinerie est l'une des solutions qui
permet à la fois de fournir de l'électricité et de
satisfaire un grand pourcentage de ses besoins en énergie thermique
notamment en vapeur MP.
L'autonomie électrique et la sécurité sont
alors les facteurs essentiels justifiant le projet de la turbine à
vapeur.
En plus, le diagnostic du système de production de la
vapeur montre que les phénomènes de corrosion et d'encrassement
sont de plus en plus fréquents et que certains éléments
des chaudières sont non opérationnels, ainsi ce diagnostic
révèle qu'il y a une surconsommation du fuel qui engendre des
pertes économiques très importantes.
L'installation d'un échangeur avant l'économiseur
est une solution efficace pour réduire, voire annuler ces
conséquences.
Par ailleurs la mise en place du système de
délestage est fortement recommandée pour réduire la
facture d'énergie électrique et en cas de coupure brusque
d'électricité du réseau ONE, le système de
délestage permet de réduire la charge électrique de
certaines unités pour éviter l'arrêt général
de l'usine.
Dans ce chapitre on va évoquer ces différentes
solutions d'optimisation de la facture énergétique et ainsi
l'amélioration du système de production d'énergie dans la
raffinerie pour assurer un fonctionnement nominal de toutes les unités,
augmenter l'autonomie énergétique et ainsi éviter les
pertes économiques en cas d'arrêt de l'usine.
II. Amélioration du système de production
de la vapeur
II-1.Diagnostic des chaudières
Apres la mise en service des chaudières A, B, et C en
1975 et 1997 pour la chaudière D, dans la CTE2, elles ont
assurées la production de la vapeur avec une capacité de 80 T/h
chacune et la distribution de l'électricité pendant 35 ans
d'utilisation
Les quatre chaudières présentent plusieurs
problèmes liés aux matériaux des éléments
principaux et la surconsommation du fuel, Dans ce paragraphe nous allons
essayer de diagnostiquer ces problèmes avec une étude bien
détaillée sur les causes de dégradation de chaque
élément
Pour commencer le diagnostic des chaudières, il est
indispensable de se revenir à la synthèse de l'historique de
dégradation (Annexe 4).
II-1-1. Défaillances des éléments de
la chaudière
Le diagramme de PARETO constitue un outil de qualité
très efficace. Il permet de discriminer parmi toutes les sources de non
qualités (défaillance), celles qui sont les plus importantes, de
celles qui le sont moins. Il permet ainsi de dégager les actions
prioritaires.
Ce diagramme contient des colonnes indiquant le détail
des différentes parties où il y a défaillance
matérielle dans les quatre chaudières A, B, C et
D. Le nombre de défaut enregistré, (2004 à 2009)
est indiqué par ordre croissant (Pourcentage cumulé) à
l'aide de colonnes de tailles différentes. Ce diagramme sert à
identifier précisément et objectivement les problèmes les
plus importants ainsi qu'à clarifier les objectifs des activités
de résolution.
Le tableau suivant donne la fréquence de
défaillance pour chaque élément objet de l'étude
dans la chaudière A.
Tableau 6.1 : défaillances
des éléments dans les quatre chaudières A.
|
Elément défectueux
|
Fréquence
|
Pourcentage (%)
|
Pourcentage cumulé
|
A
|
Tubes (la partie ballon inférieur)
|
49
|
66,22
|
66,22
|
B
|
Tubes (Ecran)
|
14
|
18,92
|
85,14
|
C
|
Economiseur
|
9
|
12,16
|
97,30
|
D
|
Surchauffeur
|
2
|
2,70
|
100,00
|
E
|
Ballon sup
|
0
|
0
|
100,00
|
|
TOTAL
|
74
|
100
|
|
|
Projet de Fin d'Etudes
|
|
|
Les résultats obtenus sont représentés
graphiquement par la figure suivante
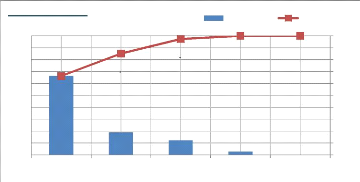
A B C D E
100
100
90
90
100,00
100,00
97,30
80
80
66,22
85,14
70
70
60
60
66,22%
50
50
40
40
30
30
20
20
12,16 %
10
10
18,92 %
0 %
2,70 %
0
0
Chaudiére 98H1A
Fréquence %cumulé
Figure 6.1 : Analyse PARETO de
défaillances des éléments de la chaudière A
Pour la chaudière B :
Tableau 6.2 : défaillance
des éléments de la chaudière B.
|
Elément défectueux
|
Fréquence
|
Pourcentage (%)
|
Pourcentage cumulé
|
A
|
Tubes (la partie ballon inférieur)
|
36
|
87,80
|
87,80
|
D
|
surchauffeur
|
3
|
7,32
|
95,12
|
C
|
Economiseur
|
2
|
4,88
|
100,00
|
B
|
Tubes (Ecran)
|
0
|
0,00
|
|
E
|
ballon sup
|
0
|
0,00
|
|
|
TOTAL
|
41
|
100
|
|
Chaudiére 98H1B
Fréquence %cumulé
87,80
|
|
|
|
|
|
|
|
95,12
|
|
|
100,00
|
|
|
|
|
87,80
|
|
|
|
|
|
|
|
|
|
|
|
|
|
|
|
|
|
|
|
|
|
|
|
|
|
|
|
|
|
|
|
|
|
|
|
|
|
|
|
|
|
|
|
|
|
|
|
|
|
|
|
|
|
|
|
|
|
|
|
|
|
7,32
|
4,88
|
|
0,00
|
|
|
0,00
|
A D C B E
100 90 80 70 60 50 40 30 20 10 0
100 90 80 70 60 50 40 30 20 10 0
Figure 6.2 : Analyse PARETO de
défaillances des éléments de la chaudière B
Pour la chaudière C :
Tableau 6.3 : défaillance
des éléments de la chaudière C.
|
Elément défectueux
|
Fréquence
|
Pourcentage (%)
|
Pourcentage cumulé
|
A
|
Tubes (la partie balloninférieur)
|
44
|
88
|
88
|
C
|
Economiseur
|
4
|
8
|
96
|
D
|
surchauffeur
|
2
|
4
|
100
|
B
|
Tubes (Ecran)
|
0
|
0
|
|
E
|
ballon sup
|
0
|
0
|
|
|
TOTAL
|
50
|
100
|
|
88
|
|
|
|
|
|
|
|
|
|
96
|
|
100
|
|
|
|
|
88
|
|
|
|
|
|
|
|
|
|
|
|
|
|
|
|
|
|
|
|
|
|
|
|
|
|
|
|
|
|
|
|
|
|
|
|
|
|
|
|
|
|
|
|
|
|
|
|
|
|
|
|
|
|
|
|
|
|
|
|
|
|
|
|
8
|
4
|
|
0
|
|
|
0
|
A C D B E
100 90 80 70 60 50 40 30 20 10 0
100 90 80 70 60 50 40 30 20 10 0

Fréquence %cumulé
Chaudiére 98H1C
Figure 6.3 : Analyse PARETO de
défaillances des éléments de la chaudière C
Pour la chaudière D :
Tableau 6.4 : défaillance
des éléments de la chaudière D.
|
Elément défectueux
|
Fréquence
|
Pourcentage (%)
|
Pourcentage cumulé
|
D
|
Economiseur
|
12
|
63,16
|
63,16
|
B
|
Tubes (Ecran)
|
5
|
26,32
|
89,47
|
C
|
surchauffeur
|
2
|
10,53
|
100,00
|
A
|
Tubes (la partie balloninférieur)
|
0
|
0,00
|
|
E
|
ballon sup
|
0
|
0,00
|
|
|
TOTAL
|
19
|
100
|
|
|
Projet de Fin d'Etudes
|
|
|
|
|
|
|
|
|
|
|
|
|
|
89,47
|
|
|
100,00
|
|
|
|
|
|
|
|
|
|
|
|
|
|
63,16
|
|
|
|
|
|
|
|
|
63,16
|
|
|
|
|
|
|
|
|
|
|
|
|
|
|
|
|
|
|
|
|
|
|
|
|
|
|
26,32
|
|
|
|
|
|
|
|
10,53
|
|
|
|
|
|
0,00
|
|
|
0,00
|
D B C A E
100 90 80 70 60 50 40 30 20 10 0
100 90 80 70 60 50 40 30 20 10 0

Chaudiére 98H1D
Fréquence %cumulé
Figure 6.4 : Analyse PARETO de
défaillances des éléments de la chaudière D
Interprétation et
synthèse
D'après les analyses de défaillances, on remarque
ce qui suit :
v' Les tubes de la partie inférieure ont un pourcentage de
défaillance très élevé pour les
quatre chaudières. Les causes de ce problème sont
détaillées dans le paragraphe suivant
v' L'économiseur a une fréquence de
défaillance moins que les tubes pour les quatre
chaudières suivie du surchauffeur et les tubes
écran.
v' La chaudière A possède une fréquence
de défaillance importante au niveau des tubes Ecran, a cause de mauvaise
orientation de la flamme du bruleur. Cependant ce problème arrive
rarement.
v' Le ballon supérieur possède une
fréquence de défaillance nulle pour les quatre chaudières
car il n'est pas touché par les suits de fumées et donc
l'accumulation des dépôts y négligeable.
Pour éliminer 80% des défauts, il faut attaquer les
problèmes liés aux tubes de la partie inférieure,
l'économiseur et les surchauffeurs des chaudières.
II-1-2. Origines et causes du phénomène
Afin de bien visualiser le problème, nous avons
profité à l'arrêt d'une chaudière pour examiner ses
éléments, et voir les conséquences de la corrosion.
Nous remarquons :
· La présence de dépôts sur les parois
des tubes à la partie inférieure
· une quantité très importante d'amas de
dépôt
· Accumulation des suies sur les parois externes du ballon
inférieur et qui mesurent un mètre en hauteur.
· Percement (fuite d'eau) du tube à la partie
inférieur.
· Tubes de la zone de passage de fumées recouverts
de dépôts, de suies.
·
Les brOleurs sont recouverts d'amas de dépôts et le
réfractaire est recouvert d'imbrulés de fuel
· Nous avons observé la dégradation de
matériau au niveau :
ü des parties inférieures cintrées des tubes
du faisceau convection.
ü Les tubes des surchauffeurs.
ü La paroi externe du ballon inférieur.
ü Les tubes et les ailettes de l'économiseur de la
chaudière.
ü Certaines parties du casing de la chaudière.
Le schéma suivant représente les différents
éléments concernés par la dégradation
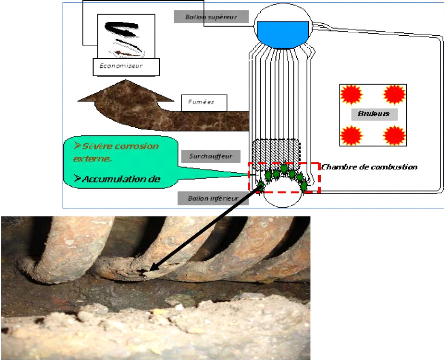
Figure 6.5 : Dégradation
des éléments concernés
D'après ces observations, on peut conclure que
l'ensemble des percements de ces tubes est localisé aux parties
cintrées inférieures au voisinage du ballon inférieur,
suite à une corrosion externe très accélérée
par cratères et qui est favorisée par :
ü Accumulation de dépôt riche en
composés soufrés à ces endroits, provenant de la
combustion du fuel à teneur élevée en soufre. Touts les
conditions favorables telles que la
température, le taux d'oxygène et
d'humidité, lors des arréts, permettant la formation d'acide
sulfurique, responsable de la corrosion.
v' Défaillance et inefficacité du nettoyage
chimique pour éliminer les dépôts persistants aux parties
inférieures.
v' Inefficacité du drainage et de neutralisation, lors
des nettoyages chimiques, favorisant la rétention des produits corrosifs
piégés entre les tubes et le réfractaire.
v' Arrêts prolongés des chaudières à
des températures inférieures au point de rosée eau/acide,
ce qui accélère la corrosion.
Les produits dus à la réaction de combustion au
niveau de la chaudière sont les principales causes de
dégradations considérées.
? formation du SO3
Les difficultés d'exploitation par encrassement et
corrosion à haute et basse température ont pour origine la
formation de SO3 à partir du soufre contenu dans le combustible.
En brûlant, le soufre du combustible (fuel lourd) donne
naissance à de l'anhydride sulfureux (SO2). Mis en présence de
l'oxygène de l'air en excès, dans le cas de combustion oxydante
ou oxydo-réductrice, et de catalyseurs de conversion tels que le
vanadium, le fer ou le nickel, une partie du SO2 formé se transforme en
anhydride sulfurique (SO3).
Dans certaines conditions de température de peau du
métal et d'hygrométrie, le SO3 se condense et forme de l'acide
sulfurique (H2SO4).
La combustion du S donne :
S + O2 ? SO2
La présence d'excès d'air donne ensuite
l'équilibre :
SO2 + 1/2 O2 ? SO3
Les quatre chaudières fonctionnent en excès
d'Oxygène.
Pour visualiser le rôle de l'excès d'air dan la
formation de SO3, on a fait un essai de la diminution de %O2 et on a
rencontré un fort dégagement de fumées noir à cause
de la combustion non complète, ces fumées noire indiquent la
présence de monoxyde de carbone. Raison pour laquelle on travail
toujours avec un excès d'aire dans les chaudières. Mais
cet excès d'air favorise la formation des éléments
corrosifs.
La figure suivante présente le Taux d'oxygène pour
la chaudière A :
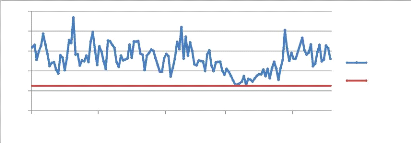
01/12/2009 01/01/2010 01/02/2010 01/03/2010 01/04/2010
10
8
4
0
6
2
%O2 L'aspect
Figure 6.6 : 6K1112O7
SRKrFIEtI:JHOP PJqgiSRKrIII: FII:KOiqUB
D'après les courbes ci-dessus on remarque que le Taux
d'O2 est très élevé, donc on est en présence d'un
excès d'air important qui influence négativement sur
l'état des matériaux des chaudières.
Cet impact est d'autant plus important que les
températures de fumées dépassent 950°C
ü une température de flamme élevée
donne de l'oxygène atomique très réactif.
ü la présence de S et O2 donne SO3 en fonction de la
température
ü la présence d'oxygène augmente la
probabilité de transformations de l'oxyde de vanadium V2O3 en pentoxyde
de vanadium V2O5 qui est plus oxydant et agit comme catalyseur de la
transformation SO2 en SO3.
tt> Formation de l'acide sulfurique
L'acide sulfurique prend naissance à partir de SO3 et de
la vapeur d'eau produite par la combustion du fuel.
111E+11E11E? SO2 111211ll EO
?HES11+
Le point de rosée des fumées varie en fonction du
pourcentage de SO3 contenant dans les fumées,
Le mélange "eau-acide" se condense sur les parties
froides dès que la température atteint le point de rosée
acide entre 100° et 150°C. Aux moments des
arrests des chaudières la température peut atteindre
des valeurs très inférieures à 100°C. Donc la
formation de H2SO4 liquide et l'ionisation par l'eau (humidité) est
fortement probable.
La figure suivante présente cette évolution
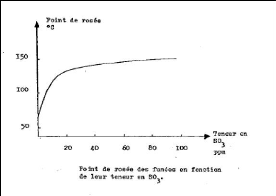
Figure 6.7 : Variation du point de
rosée en fonction du pourcentage de SO3
NB : la dégradation des surchauffeurs
suit la même procédure que les tubes partie inférieur, avec
le même mécanisme réactionnel, mêmes causes et les
mêmes conséquences.
t;. ' pJUIIINIKIIIIe l'EWV IsHr
L'économiseur est un échangeur de chaleur à
circulation d'eau inverse par rapport à celle des gaz de combustion.
L'échange de la chaleur se réalise par convection.
L'économiseur est généralement placé
avant le réchauffeur d'air, dans le circuit des fumées.
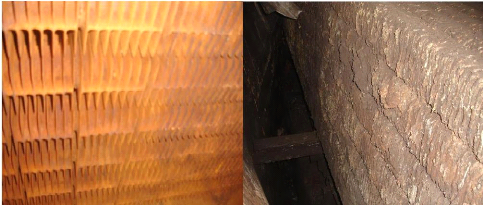
Figure 6.8 : Economiseur en bon
état et Economiseur encrassé
Les Fumées condensées à l'interface des
Tubes et les ailettes de l'économiseur sont causées par la
Température d'eau à l'entrée de l'économiseur
inférieur à la procédure définie par le
constructeur (et très bas par rapport au point de rosé des
fumées). Pour justifier ce phénomène on a fait un suivi de
la température de l'eau, à l'entrée de
l'économiseur
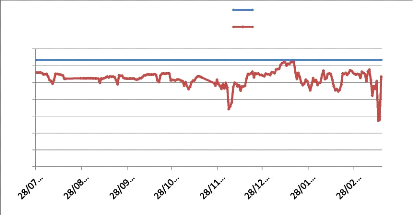
140
120
100
80
40
60
20
0
T° EAU Aspect
T°C EAU ENTREE ECONOMISEUR
Figure 6.9 : Suivi de la
température entrée économiseur pour les quatre
chaudières
D'après le suivi de la température de l'eau
d'entrée économiseur pour les quatre chaudières on
remarque que la température d'eau est très faible ce qui veut
dire qu'il y a une forte condensation des fumées à ce
niveau. la cause principale de cette
chute de Température est due à l'état de dégazeur
(partie de dégazage physique, le matériau des chicanes
dégradé) .
L'attaque de H2SO4 a le mécanisme suivant :
1 -- En se condensant l'acide sulfurique attaque
l'acier :
H2SO4 + Fe ? Fe SO4 + H2 (sulfate ferreux)
2 - En présence d'oxygène une autre réaction
se poursuit :
2Fe SO4 +O2 + H2SO4 ?Fe2(SO4)3 + H2O
3 -- Le sulfate ferrique formé peut
réagir sur le fer pour revenir à l'état ferreux :
Fe2 (SO4)3 + Fe? 3FeSO4
q> Influence de la température de fumées
sur le rendement de la chaudière f
Pour étudier l'influence de la température des
fumées sur le rendement de la chaudière, on a calculé ce
rendement pour différentes températures de sortie des
fumées ainsi que le pourcentage de CO2 dégagé, ci-dessous
les résultats obtenus :
Le rendement de la chaudière est calculé par la
formule suivante :
Avec :
Tf : Température de fumées
Ta : Température ambiante
k : coefficient dépend du type de combustible (pour le
fuel k= 0,6)
Tableau 6.5 : suivie du rendement
de la chaudière.
Mois
|
Température de fumée
|
% CO2
|
Rendement
|
08/2009
|
198°C
|
7,8%
|
86%
|
09/2009
|
250°C
|
8,7%
|
84%
|
10/2009
|
355°C
|
8%
|
75%
|
11/2009
|
355°C
|
8%
|
75%
|
12/2009
|
365°C
|
8,7%
|
75%
|
Interprétation
Un bon rendement signifie que la quantité
d'énergie consommée par la chaudière, est
utilisée de façon optimale. Il est obtenu grâce à
une isolation renforcée des parois de la chaudière qui limite
les déperditions thermiques. Le brûleur est aussi mieux
réglé pour optimiser l'énergie
de la combustion. La chaudière possède par
estimation un rendement de 80 %, 10 % ? H H H
représentent les fumées qui s'échappent
dans la cheminée. Pour obtenir un rendement
1 2
R ? ?
important il faut récupérer le maximum de
calories contenues dans les fumées et de baisser
Ra PCI
? Ra PCI
?
par la même occasion les polluants émis. Raison
pour laquelle on a pensé à installer un échangeur avant
l'économiseur, l'étude est détaillée dans le
paragraphe suivant
II-2.Dimensionnement d'un échangeur de
préchauffage de l'eau de chaudières ?
Pourquoi installer un tel échangeur ?
On prend le cas de la chaudière C, mois 09/2009
début d'encrassement de l'économiseur Le moi 10/2009 :
Température de fumée = 355°C, CO2= 8% R=
75%
Sachant que le rendement de la chaudière est liée
par son ratio par la formule suivante :
H1: Enthalpie de la vapeur à 405°C et 42 bar = 770
Kcal/Kg
H2: Enthalpie de Fuel =120 Kcal/Kg
PCI(Fuel) : pouvoir calorifique inferieur 9600
Kcal/Kg
Ra : Ratio, c'est la quantité de fuel
consommée pour produire 1 Tonne de vapeur
(Ra de constructeur = 75Kg de fuel / 1T de vapeur haut pression).
Notre cas
Ra calculé - Ra constructeur = 15 Kg
(surconsommation de fuel)
Sachant que : Production Moyenne de VH= 40T/h
1 an = 8000 heures de marche
Production annuel de VH = 320000 TVH La surconsommation de 15Kg
pour 1 TVH
Donc Surconsommation de fuel = 4800 T Fuel /an
Avec un prix de 4014 Dh /1T fuel
Au début d'encrassement la surconsommation de fuel est
monnayée à :
19.267.200,00 DH/an
Ces résultats sont obtenus d'après la
consommation du mois 10 juste trois mois après le premier
démarrage de l'économiseur après la maintenance, et
vis-à-vis les conditions de fonctionnement de l'économiseur les
pertes seront plus importantes.
? Principe
Cette solution consiste à un préchauffage de l'eau
à l'entrée économiseur avec une partie de l'eau chaude
sortie économiseur à condition que le nettoyage se fait
auparavant.
Le principe est le suivant : une partie de l'eau chaude 60%
sortant de l'économiseur est recyclée pour être
utilisé dans le préchauffage de l'eau sortant du dégazeur
et entrant à l'économiseur, les 40% (220°C) restent au
niveau de la conduite d'alimentation du ballon supérieur avant
d'être mélangé avec l'eau qui sort de l'échangeur
à une température de 155 °C. Le mélange (182°C)
alimente directement la chaudière.
Pour appliquer cette solution, le nettoyage de
l'économiseur auparavant est une condition nécessaire qui doit
être satisfaite, cela permet de bien récupérer les calories
des fumées pour le chauffage de l'eau avant sortie économiseur et
pour arriver aux températures cité ci-dessus.
Autrement dit en gardant la température d'entrée
économiseur à 150°C, c.-à-d supérieure au
point de rosé des fumées avec le bon fonctionnement du
système de ramonage, l'encrassement de l'économiseur est
réduit pour une longue durée.
II-2-1.Méthodologie de dimensionnement : voire
annexe 5
Le schéma suivant représente le principe et le
bilan énergétique de la solution proposée
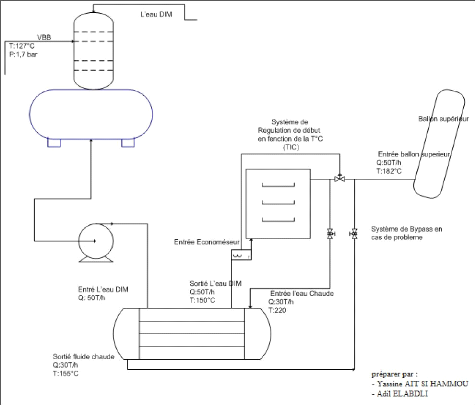
Figure 6.10 : principe de
fonctionnement et bilan énergétique de l'échangeur de
chaleur avec l'eau chaude sortant de l'économiseur
Remarque :
Calcule de la température finale d'entrée ballon
supérieur d'après l'équation de la
conservation de chaleur
La température qui alimente les chaudières est
fixée par le constructeur à 184 °C, donc avec cette solution
dont la température de l'eau alimentant la chaudière est
182°C, on est proche aux conditions du constructeur, ce qui signifie que
cette solution est faisable.
II-2-2. Résultats de dimensionnement
Le tableau suivant regroupe les données des fluides froid
et chaud : Tableau 6.6 : Données des
fluides chaud et fraoid.
paramètre
|
valeur
|
fluide froid (eau déminéralisée
entrée Eco)
|
débit massique en Kg/h
|
50 000
|
débit massique en Kg/s
|
13,888889
|
Cp de l'eau Kj/Kg.K
|
4,2052
|
Masse volumique
|
970,4
|
Température d'entrée °C
|
110
|
Température de sortie °C
|
150
|
viscosité dynamique u
|
0,000317
|
conductivité thermique ë W/m.K
|
0,68
|
fluide chaud (eau déminéralisée
sortie Eco)
|
débit massique en Kg/h
|
28 006,66
|
débit massique en Kg/s
|
7,78
|
Cp de l'eau Kj/Kg.K
|
4,62
|
Masse volumique (Kg/m3)
|
970,4
|
Température d'entrée °C
|
220
|
Température de sortie °C
|
155,00
|
viscosité dynamique u Pa.s
|
0,000317
|
conductivité thermique ë W/m.K
|
0,68
|
Les tableaux suivants regroupent les valeurs des principaux
paramètres caractéristiques de l'échangeur
dimensionné :
Tableau 6.7 : Calcul du ÄTLM
et Us .
|
Paramètres corrigés
|
?T moyenne logarithmique
|
56,5824961
|
-
|
Us en Kcal/h.m2.°C
|
1050
|
1000,89921
|
Us en Kj/s.m2.°C
|
1,21916667
|
1,1621552
|
Coefficient de correction
|
0,97
|
-
|
|
Projet de Fin d'Etudes
|
|
|
Tableau 6.8
:.Caractéristiques des faisceaux tubulaires :
Paramitres de l'échangeur
|
paramètre corrigé
|
Surface d'échange (m2)
|
34,9138092
|
36,6265645
|
longueur de l'échangeur (m)
|
1,5
|
-
|
diamètre externe (mm)
|
19,05
|
-
|
diamètre externe (m)
|
0,01905
|
-
|
nombre de tubes total
|
388,920838
|
408
|
nombre de tubes par passe
|
64,8201396
|
68
|
diamètre interne (cm)
|
1,7
|
_-
|
diamètre interne (m)
|
0,017
|
-
|
section du tube (cm2)
|
2,26865
|
-
|
section du tube (m2)
|
0,00022687
|
2,85022898
|
vitesse d'écoulement (m/s)
|
0,51967475
|
-
|
vitesse massique d'écoulement
|
504,29238
|
--
|
Tableau 6.9 :
Caractéristique de la calandre :
paramètre
|
valeur
|
Espacement entre chicanes B (m)
|
0,1
|
diamètre de la calandre Dc (m)
|
0,5
|
le pas (m)
|
0,0254
|
section de passage at (m2)
|
0,0125
|
vitesse massique transversale
|
1111,11111
|
vitesse massique longitudinale
|
693,643299
|
vitesse massique moyenne
|
877,903626
|
débit unitaire massique
|
173,480659
|
diamètre équivalent (m)
|
0,02407039
|
Tableau 6.10 : Pertes de charges
à l'intérieur et l'extérieur des tubes :
paramètre
|
valeur
|
|
2223,50854
|
Perte de charge dans les tubes en pascal
|
Dp dans les tubes (Kg/cm2)
|
0,02223509
|
la
|
63283,6826
|
perte de charge dans calandre
|
Dp dans la calandre (Kg/cm2)
|
0,63283683
|
?Pi est inférieur à la perte de charge admissible
(1 Kg/cm2).
Tableau 6.11 : les
résistances d'encrassement :
paramètre
|
valeur
|
coefficient global d'échange propre Up
|
2278,46748
|
la résistance d'encrassement R
|
0,00051349
|
La résistance d'encrassement est acceptable avec la valeur
de la résistance d'encrassement admissible
II-2-3. Etude économique
? Coût d'investissement
Le coüt d'investissement compris l'ensemble des charges
financières nécessaires à la réalisation du projet
à savoir :
1- échangeur de chaleur :
le prix de base : on a une surface d'échange égale
à 36 m2 d'où :
Le prix de base = 3,7 104 F en mi
1975
Le coefficient fd dépend du type de l'échangeur
choisit, dans ce cas c'est le AEM : fd = 0.87
S n
S ?
fp = 1,00 fl = 1,35 fnp = 1,04 fp = 1,67 ft = 1
le fm dépend du matériel utilisé est le
AO/Cu et la surface est 36 m2 d'où : fm = 1,10
Ainsi
Le prix corrigé = 83022 ,77 F en 1975
Actualisation des prix
La relation qui donne le prix actuel est : Avec :
S0 : valeur actuelle de la somme Sn Sn : la somme
à l'année n
n : nombre d'année
i : indice d'actualisation on le prend à 10 %, i = 0.1
n = 2010- 1975 = 35 S0 = 83022,77 F
D'où Sn = 2 333 142,267 F en 2010
Sachant que 1€ = 6,5 F donc Sn = 358944,96 € en 2010
et 1€ = 11,5 dh
Donc Coût de l'échangeur = 4.127.867 ,087
dh.
2- Travaux de montage
· Génie civile
· Tuyauterie
· Accessoires (vannes, tés, brides ...)
· Montage
Coût = 100.000,00 Dh
Donc le coût d'investissement global est :
? Coût de fonctionnement
C'est le coüt énergétique c'est-à-dire
la consommation de la pompe en électricité. Sachant que 1 kwatt =
0,78 Dh
La pompe alimentaire a une puissance électrique de 48
kwatt et elle travaille 8600 heures/ an. Donc
? Gain
Avec l'application de cette modification on aura une
optimisation de la facture énergétique de oût d
investisse mnt
' 4 227 . 867 087
N.B : le montant de 19.267.200
représente le coût de surconsommation du fuel à
optimiser.
? Retour d'investissement
Le retour d'investissement de ce projet est estimé
à :
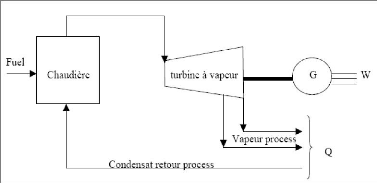
III. Calcul technico-économique de la turbine
à vapeur III-1.Justification du projet
Au démarrage du projet UP GRADE (projet de
modernisation de la raffinerie SAMIR), le besoin en énergie
électrique est multiplié, actuellement, il est de l'ordre de 44
MW. Une partie (28 MW) est produite par l'unité de
cogénération, et le complément restant (16 MW) est
acheté de l'ONE.
La raffinerie possède des équipements qui sont
particulièrement sensibles à la continuité absolue de leur
alimentation électrique. La SAMIR qui a un besoin absolu de s'en
prémunir contre toute coupure de l'énergie électrique
trouve dans la cogénération la sécurisation de
l'alimentation électrique de son site.
Cependant les arrêts fréquents (trip) de cette
unité et la dépendance envers l'ONE mettent la raffinerie dans
l'obligation de chercher des solutions pour augmenter son autonomie
électrique et être à l'abri de tout risque d'arrêt de
l'usine.
L'idée d'installer une turbine à vapeur
s'inscrit dans le cadre d'optimisation énergétique qui vise
à récupérer l'énergie de détente perdue au
niveau des vannes réductrices actuellement utilisées à CTE
II. Elle permet à la fois de réduire la pression de la vapeur
(VH-VM) et de récupérer l'énergie de détente sous
forme d'énergie mécanique converti ensuite via un alternateur en
énergie électrique débité sur le réseau
électrique de la raffinerie.
Le principe de la turbine à vapeur est illustré
dans le schéma suivant :
Q : Energie thermique W :
Energie électrique
III-2. Calcul de la turbine à vapeur
Les différentes étapes à suivre pour le
dimensionnement sont :
· L'évaluation du besoin en énergie.
· Le dimensionnement du cycle de HIRN (annexe 6) qui est
l'outil principal de notre méthode.
? Evaluation des besoins en vapeur (annexe
7)
Avec le démarrage du projet UPGRADE, La production
totale de la vapeur haute pression dans la centrale thermoélectrique II
et la nouvelle unité de cogénération est
évaluée à un débit horaire moyen de 166 T/h de
vapeur produite.
La consommation de la vapeur HP dans la raffinerie est repartie
de la manière suivante :
- Pour l'unité reforming II, sa moyenne de consommation
est 8,2 TVH/h.
- Pour l'unité de déparaffinage des huiles, sa
moyenne de consommation est 10,75 TVH/h. - Pour le nouveau projet UPGRADE sa
consommation en complément de vapeur HP par la CTE II dépend des
régimes de marche des unités en fonctionnement
Les différents cas de figure décrite par le
concepteur du projet sont résumés dans le tableau :
Tableau 6.12 : Compléments de vapeur
à fournir aux unités Upgrade:
|
Capacité opérationnelle de
l'unité
|
Unites
|
Cas 1
|
Cas 2
|
Cas 3
|
Cas 4
|
Cas 5
|
Cas 6
|
Cas 7
|
Cas 8
|
Cas 9
|
Unité 31-VDU 3
|
100%
|
100%
|
100%
|
100%
|
100%
|
100%
|
100%
|
80%
|
0%
|
Unité 33-Dist Hydrotreater
|
100%
|
100%
|
0%
|
100%
|
100%
|
75%
|
75%
|
0%
|
0%
|
Unité 34-Hydrocracker (Fiouls)
|
100%
|
0%
|
0%
|
100%
|
100%
|
95%
|
95%
|
0%
|
0%
|
Unité 36-Hydrogen Prod Unit
|
100%
|
100%
|
100%
|
100%
|
100%
|
82%
|
82%
|
0%
|
0%
|
Unité 37-Amine Regen
|
100%
|
100%
|
100%
|
100%
|
100%
|
100%
|
100%
|
40%
|
0%
|
Unité 38-SWS
|
100%
|
100%
|
100%
|
100%
|
100%
|
100%
|
100%
|
0%
|
0%
|
Unité 39-SRU
|
58%
|
58%
|
58%
|
58%
|
58%
|
55%
|
55%
|
0%
|
0%
|
Complément vapeur HP (T/h) à fournir par la CTE
II à l'UPGRADE
|
15.4
|
37.7
|
35.7
|
27
|
10.7
|
40.2
|
25.4
|
74
|
80.6
|
|
Pour le complément de vapeur HP à fournir aux
installations du projet UPGRADE, il est estimé en moyenne à 27
T/h dans l'état de marche normale où l'unité
d'hydrocrackage est en fonctionnement. C'est la valeur qu'on va
considérer par la suite dans le dimensionnement de la turbine à
vapeur.
La figure suivante représente la répartition de la
consommation de vapeur VH dans la SAMIR
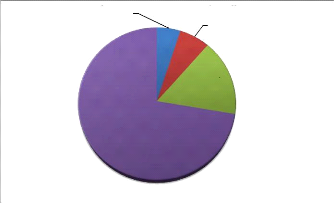
Converti en VM (72%)
Reforming (5%)
Upgrade (16%)
Déparaffinage des huiles (7%)
Figure 6.11: Répartition
de la consommation de vapeur HP
D'après la figure on constate clairement qu'une
quantité minoritaire de la vapeur HP produite est utilisé
à l'état VH (environ 28% de la production totale) dans les
unités reforming II, le déparaffinage des huiles et le projet
Upgrade tandis que la quantité majoritaire (72% de la production totale)
est convertie en vapeur moyenne pression dans les vannes réductrices.
La moyenne de la demande mensuelle en vapeur moyenne pression
est évaluée à 76270 tonnes avec un débit massique
moyen de 106 (T/h).
? Calcul de la turbine à
vapeur
Afin de faciliter le dimensionnement de la turbine à
vapeur, nous allons procéder dans à la modélisation du
système de production de la vapeur HP (Ghaudières GTE II,
platforming II et chaudière de récupération) par une
chaudière équivalente dont la production est acheminé vers
le réseau de vapeur HP puis à la turbine à vapeur.
Le débit horaire équivalent de la vapeur HP de
cette chaudière est
Q équivalent =166-8,2-10,75-27 = 120
T/h
Avec une pression de 40 bars et une température de
400°G.
Les éléments importants de notre cycle de HIRN
(annexe 6) sont: La turbine à vapeur, la chaudière, la pompe, et
le condenseur.
Les chaudières et les pompes de circulations sont des
éléments déjà existants dans l'installation et dont
les caractéristiques techniques sont déjà définies,
et pour le condenseur on a une turbine à vapeur à contre pression
donc on n'a pas besoin d'un condenseur. Il nous reste alors à
dimensionner la turbine à vapeur.
La figure suivante, représente le schéma
simplifié d'un processus de cogénération avec turbine
à vapeur.
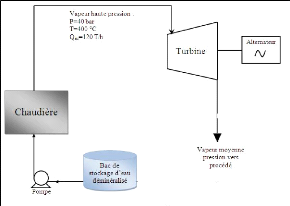
Figure 6.12: Processus de
production OfKCMKUICIV vapIKr. Hypothèse de dimensionnement
:
· Le régime est considéré stationnaire
;
· La transformation est supposé adiabatique ;
· La turbine est à réaction avec une vitesse
de la vapeur d'entrée est égale à la vitesse de sortie
;
· Les pertes de charge sont négligées.
ü Bilan massique
La conservation de la masse permet d'écrire :
mh1 = mh2
m:h Désigne le débit massique de la vapeur.
1 : entrée de la turbine.
2 : sortie de la turbine
ü Bilan énergétique
L'énergie qui entre dans la turbine est égale
à la somme de l'énergie qui sort de la turbine et de
l'énergie accumulée dans la turbine.
L'énergie qui entre dans le système est la
vapeur haute pression, et l'énergie qui sort est constitué du
travail échangé avec le milieu extérieur au moyen de
l'arbre et l'énergie thermique contenue dans la vapeur moyenne pression
sortante de la turbine.
Appliquons l'équation de conservation d'énergie
:
Enérgie Transf ert Energ ie
Accumulation} + sortante de -- à la entrante
dans
la turbine surface la turbine
Ce qui est traduit en dérivant par rapport au temps pour
passer aux puissances échangées par :
d(U + Ec + Ep)
+ m 2(u2 +
dt
2 + gz2) = Q - W + m 1 u1 +
V1 2
2 + gz1)
V22
Avec :
U : L'énergie interne.
Ec : L'énergie cinétique due au
mouvement de la vapeur.
Ep : L'énergie potentielle due au champ des forces. En
général, il s'agit du champ de force de la pesanteur.
?? : La puissance thermique échangée.
?? : La dérivée du travail échangé
lors de la transformation
Avec les hypothèses cités auparavant et selon le
bilan massique et énergétique on trouve que la puissance
mécanique échangée est donnée par :
?? = ?? (????- ????)
Avec :
?? : La puissance mécanique présente sur l'arbre de
la turbine.
?? : Le débit massique de la vapeur d'eau passant à
travers la turbine.
H1 et H2 : sont respectivement l'enthalpie de la vapeur entrant
et sortant de la turbine.
1' Rendements de la turbine à vapeur
Le rendement Isentropique : ?? = 80%
Le rendement Mécanique-électrique : ?? = 96%
Ces rendement ont été choisi selon la technologie
des turbines à vapeur actuellement disponible sur le marché,
elles présentent des rendements voisines de celui choisis ci-dessus.
1' Détermination des caractéristiques de la
vapeur MP
En se servant du diagramme de Mollier (diagramme H-S) ou du
logiciel STEAMTAB donnant les caractéristiques de l'eau à
l'état liquide et vapeur selon sa température et sa pression, on
détermine l'enthalpie et l'entropie de la vapeur HP entrant dans la
turbine :
Enthalpie de la vapeur à l'entré de la turbine :
H1=3241,47 Kj/Kg
Entropie de la vapeur à l'entré de la turbine :
S1=6771,36 J/Kg/°C.
On suppose que la transformation dans la turbine soit
isentropique, ce qui nous permettra de construire le point de sortie de la
turbine sur le diagramme (S-T) figure (6.13) :
Les caractéristiques de la vapeur à la sortie de la
turbine sont :
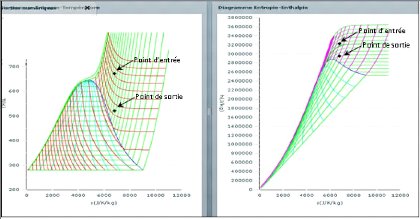
Figure 6.13: Point d'entrée
et de sortie de la turbine sur les diagrammes (T-S) et (H-S).
Détermination de la puissance électrique
du turboalternateur Apres détermination de point de sortie de
la turbine on a :
AH????éor??????e = H1 -- H2 = 337,17 KJ/Kg
Le rendement isentropique de la turbine est ì=80%
Donc : AHrée?? = II X AH????éor??????e = 269,73
Kj/Kg
Le travail de détente isentropique au niveau de la turbine
permet de calculer la puissance mécanique fournie par la turbine
à l'arbre de l'alternateur, il est donné par :
????é?? = Th X AHrée??
ril = 120 ?? /?? Le débit massique de la vapeur entrant
dans la turbine. Nous allons obtenir une puissance mécanique au niveau
de la turbine :
?? ??é?? = 8991 KW~9??W
Sachant que le rendement Mécanique-électrique est T
= 96%, la puissance électrique aux bornes de l'alternateur est
égale:
Pélectrique = T X
????é?? Pélectrique = 8, 64 ????
Synthèse :
La mise en place de la nouvelle turbine à vapeur va
permettre de produire une puissance électrique de 8,64 MW, soit 19,63 %
du besoin global en électricité (44 MW).
Cette solution augmentera l'autonomie électrique de la
raffinerie à 87%.
|
32%
Situation actuelle
|
68%
|
|
|
19%
13%
Turbine à vapeur
|
68%
en service
|
|
|
|
|
|
: Cogénération
|
|
: Turbine à vapeur : ONE
|
Figure 6.14: Degré
d'autonomie électrique III-3. Estimation économique du
projet
1' Coût d'investissement
Le cout d'investissement de ce projet comprend:
· Turbine à vapeur (groupe turbine)
· Groupe alternateur
· Raccordement au réseau électrique
· Raccordement au réseau vapeur
· Travaux de montage (Génie civil)
Pour estimer les coûts relatives aux
éléments précédents, on a transmit la liste des
équipements au service d'achat, et on se basant sur les coüts des
groupes turboalternateurs utilisés dans la raffinerie avant l'incendie
de 2002 et en contactant leurs fournisseurs, Ils ont estimés le
coüt global de l'investissement à
Sachant que 1$=8,9 Dh Soit
1' Gain net apporté par le groupe
turboalternateur (Cash-flows) : Le gain du projet (Cash-flows)
correspond à l'économie que sera réalisée sur la
facture de
l'énergie électrique et qui correspond au
montant dépensé pour acheter l'énergie
électrique
qui sera produite par le turboalternateur ; soit une puissance de
8,64MW multiplié par un temps d'utilisation continu (24/24 et 7J/7J).
Sachant que le KWh acheté de l'ONE vaut :
Le turboalternateur permettra de produire annuellement :
On a estimé 20 jours d'arrêt par an pour les
interventions de maintenance et des arrêts imprévisible.
Donc l'économie réalisée sur la facture
énergétique est :
1' Coûts d'exploitation
Les coüts d'exploitation relative à
l'installation du turboalternateur sont exprimés annuellement et
généralement constitués des frais du personnel, de
maintenance et de réparation, les frais d'amortissement et d'assurance.
Les charges du personnel sont négligeables puisque les tâches
techniques et de supervision seront attribuées aux opérateurs du
service utilités. (GTE II)
Maintenance
Pour évaluer le cout de maintenance une simplification
a été introduite en considérant que les dépenses en
entretien sont constantes et égales chaque année à un
pourcentage de l'investissement total. Pendant la première année,
ces dépenses sont nul vu que le projet sera encore en période de
garantie, après la première année, ils évoluent
graduellement d'une manière linéaire en fonction d'années
d'exploitation avant de se stabiliser à 3% à partir de la
dixième année.
L'estimation des charges de maintenance est
présentée dans le tableau suivant :
Tableau 6 .13 : Estimation des
charges annuelles de maintenance.
Année
|
1
|
2
|
3
|
4
|
5
|
6
|
7
|
8
|
9
|
10-20
|
frais de maintenance (%)
|
0
|
0,60
|
0,9
|
1,20
|
1,5
|
1,8
|
2,10
|
2,40
|
2,70
|
3
|
frais de maintenance (DH /an) ×103
|
0
|
133,5
|
200,2
|
267,0
|
333,7
|
400,5
|
415,8
|
534,0
|
600,7
|
667,5
|
|
)rTih d'ThhurTnJe
Les frais d'assurance annuel relative au projet sont
estimés à 1% de la valeur globale de l'investissement.
Soit :
v' Retour d'investissement
Le retour d'investissement du projet est donné par la
formule suivante :
Le cout d'exploitation est égale a la somme des couts de
maintenances estimé annuellement à 333000,7 DH plis les frais
d'assurance
Pour le groupe turboalternateur dont le coüt
d'investissement est de l'ordre de 22,25 MDH, l'amortissement est simulé
à 5 mois,
III-4. Implantation du projet
Généralement, il est préférable
que la mise en place du groupe turboalternateur soit le plus proche possible du
réseau vapeur (barillets) et de la station électrique, ceci afin
de réduire les coüts d'investissement relative au raccordement de
la turbine au réseau vapeur et du couplage de l'alternateur au
réseau électrique.
En termes de sécurité et
d'accessibilité, l'endroit choisi répond aux recommandations de
sécurité au sein de la SAMIR; il est largement spacieux pour
permettre aux opérateurs d'effectuer le suivi, le contrôle et la
maintenance.
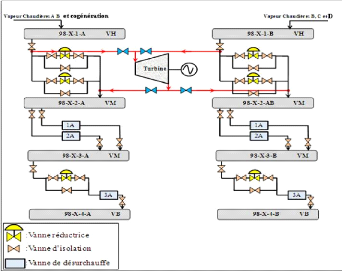
Figure 6.15: Implantation de la
turbine à vapeur
IV. Amélioration de la cogénération
IV-1.Changement des filtres de gazoline
Dans le circuit diesel de l'unité de
cogénération, le combustible à basse pression, venant du
système d'alimentation, passe par le filtre basse pression (strainer)
avant de parvenir à la pompe à combustible. Normalement, le
combustible fourni au système de la turbine est propre. Cependant, le
filtre basse pression est prévu pour éviter que toute particule
pouvant se trouver dans le système puisse passer et ainsi endommager ou
affecter le bon fonctionnement de la vanne d'admission et d'arrêt et de
la pompe à combustible.
Le filtrage est assuré par un élément en
papier plissé de 5 microns.
Au démarrage de l'unité de
cogénération le combustible était le gasoil 10000 ppm, ce
dernier avec la forte concentration du soufre et d'impuretés qu'il
contient entarte et endommage rapidement les filtres.
Aujourd'hui avec l'utilisation du gasoil 50 ppm, la
longévité des filtres est plus grande, cependant pour
éviter tout TRIP de l'unité de cogénération
dû à une pénétration des particules contaminantes
dans la pompe ou le diviseur de débit, il faut penser à un
changement des filtres.
Un filtre à gazole colmaté peut provoquer des
"trous" dans l'alimentation pouvant aller jusqu'à une coupure
complète de l'arrivée du carburant et l'arrêt de
l'unité.
? Quand changer le filtre à gazole
?
Les filtres du gasoil doivent être changés selon
les préconisations du constructeur ou
· Au moins une fois par six mois
· Quand la perte de charge atteint 1,5 bar.
IV-2 Lavage off-line
Le système de lavage hors ligne
(OFF-LINE) est utilisé pour nettoyer les compresseurs fortement
encrassés. Cependant ce lavage diminue les performances de
l'unité de cogénération en augmentant le débit du
gasoil nécessaire pour produire la même puissance active et le
même débit de vapeur en cas de non lavage et engendre des charges
supplémentaires qu'on peut optimiser en arrétant ce lavage.
Ci-après un calcul du manque à gagner en cas
d'arrêt de lavage :
Pendant le lavage, la quantité du gasoil nécessaire
augmente, soit :
Q1 2,13 Kg de gasoil / s (sans injection
d'eau)
Q2 2,15 Kg de gasoil / s (avec injection
d'eau)
La différence de ces deux quantités donne la
quantité Q du gasoil à optimiser :
Q = Q2 - Q1 = 0,02 Kg/s = 0,072 T/h
Soit Q = 51,84 T/ mois
Sachant que le prix du gasoil a atteint 6000 DH/ T en Avril 2010,
Donc la perte constatée du gasoil est :
Le lavage nécessite l'injection d'eau avec un débit
de 6,55 T/h, soit 4716 T/mois
Sachant que le prix de l'eau déminéralisée
est calculé auparavant (chapitre 4) et égal 14 DH/
m3.
Donc la perte constatée en eau
déminéralisée est :
Donc la perte totale constatée en cas de lavage sur un
bénéfice envisageable est :
Synthèse :
Sans lavage, on peut réduire la consommation du gasoil et
celle de l'eau déminéralisée, tout en gagnant
jusqu'à 377 000 DH par mois, Soit une optimisation annuelle de 4,5
MDH.
Remarque :
Malgré son coût, le lavage off-line a un
intérêt écologique et environnemental, il permet ainsi de
réduire les rejets de la turbine en NOx contenus dans les fumées
d'échappement.
Donc avant d'appliquer cette solution, il faut s'assurer qu'en
cas d'arrêt lavage, les émissions en NOx de l'unité de
cogénération respectent les normes exigées.
0 MW
V. Mise en place du système de délestage
Auparavant dans l'étude des différents
scénarios de distribution d'électricité (chapitre 5), on a
évoqué le cas où il y a un arrêt de la turbine
à vapeur et une coupure de l'électricité du réseau
ONE
Cas 6 : Arrét de la TAV et coupure de
l'électricité du réseau l'ONE
Dans ce dernier cas une puissance de 7MW (45-38) sera
indispensable pour assurer le fonctionnement de toutes les unités de la
raffinerie, pour compenser ce besoin on aura recours au délestage,
c-à-d. sacrifier par certaines unités de la raffinerie qui ne
représentent pas un risque (Ex : incendie) en cas d'arrêt et qui
ne sont pas indispensables pour le fonctionnement des unités de la
raffinerie.
Ainsi un système de délestage électrique
est un outil de gestion de l'énergie électrique (Norme NF C
61-750), dont le principe est la mise hors circuit des appareils, installations
et unités jugées non prioritaires pour permettre aux autres
unités et installations prioritaires de consommer librement
l'énergie dont ils ont besoin.
Un système de délestage joue sur l'ordre de
priorité des unités
V-1. Les unités à délester en cas de
coupure d'électricité
Pour appliquer le système de délestage, il est
nécessaire de prendre en compte trois mesures pour répondre
à l'objectif :
- les consommations effectives des
unités.
- Les risques probables (incendie, explosion...)
en cas d'arrêt brusque.
- le coût de pertes en cas de coupure
d'énergie électrique arrivant de l'ONE. La raffinerie SAMIR
comporte les entités essentielles suivantes (annexe 3) :
- Des unités de fabrications de grands
produits (zone I, II et III)
- Des installations off sites
- Les unités du projet UPGRADE
- Les utilités
Afin de mieux gérer le système de
délestage et pour identifier le fonctionnement des unités de la
SAMIR selon leurs ordres de priorités, on a fait un diagnostic des
unités à délester en collaboration avec le
département des utilités, les résultats sont
regroupés dans les tableaux suivants :
Sachant que l'ordre de priorité est désigné
par un chiffre de 1 à 5 :
Tableau 6.14: Unités
à délester dans l'ancienne raffinerie SAMIR
Unite (nombre)
|
Process unité
|
Priorité de délestage
|
15
|
|
traitement des paraffines
|
1
|
18
|
|
Unite de mélange
|
1
|
84
|
|
Mouvements produits (bitumes)
|
1
|
86
|
|
Mouvements produits (traitement des eaux)
|
1
|
99
|
|
Movements des huiles
|
1
|
|
|
Topping 1
|
1
|
|
|
Topping 2
|
1
|
|
|
Platforming I
|
1
|
10
|
|
Distillation sous vide
|
2
|
12
|
|
Extraction au furfural
|
2
|
13
|
|
Déparaffinage
|
2
|
14
|
|
Hydrofining
|
2
|
16
|
|
Oxydation des bitumes
|
2
|
|
|
Topping 3
|
2
|
93
|
|
Merox pour GPL - Amines
|
2
|
94
|
|
Merox LSR
|
2
|
97
|
|
HDS (hydrodésulfuration)
|
2
|
11
|
|
desasphaltages au propane
|
3
|
92
|
|
séparation C3/C4- récupération GPL
|
3
|
95
|
|
HDT-2
|
3
|
96
|
|
Platforming II
|
3
|
17, 98, 99,
|
41
|
utilités
|
N.A
|
Tableau 6.15: Pompes à
délester dans le système de stockage (réservoirs)
Ref pompe
|
Designation
|
Priorité de délestage
|
77-P-226 A/B
|
VDU3 (unité 31) pompe d'alimentation
|
2
|
77-P-235 A/B
|
DHTU (unite 33) pompe d'alimentation de stockage
|
4
|
77-P-220 A/B/C
|
HCU (unité 34) pompe d'alimentation à froid
|
5
|
77-P-208 99-109-A/B
|
Pompe de transfert de Naphta léger à HPU
(unité 36)
|
5
|
68-P-201 A/B
|
pompe d'alimentation GPL des HPU/SRU/syqteme fuel gaz
(unités 36/39/68)
|
5
|
|
Pompe d'alimentation fuel des unites (utilités, zone 2 et
unités 69)
|
N.A
|
1(+++), 2(++), 3(+), 4(-), 5(--) + : à
délester
- : éviter le délestage
N.A : délestage non appliqué
Tableau 6.16: Ordre de
priorité de délestage dans le nouveau projet UPGRADE
Unite (nombre)
|
Process unité
|
Priorité de délestage
|
67
|
Système Azote
|
1
|
70 A
|
Osmose inverse
|
1
|
73
|
Traitement des Effluents
|
1
|
77
|
Réservoirs (unités 12, 13, 14, 15)
|
1
|
79
|
Huile de flash
|
1
|
932
|
Amine
|
1
|
31
|
Distillation sous vide VDU
|
2
|
38
|
Stripping des Eaux Acides SWS
|
2
|
37
|
régénération d'amine ARU
|
3
|
39
|
Récupération du Soufre SRU
|
3
|
72
|
Huile de résidus de raffinage
|
3
|
33
|
Hydrotraitement Gasoil DHU
|
4
|
34
|
Hydrocracker HCU
|
5
|
36
|
production d'hydrogène HPU
|
5
|
61
|
Eau de ville
|
N.A
|
62
|
Eau déminéralisée
|
N.A
|
63
|
Eau de chaudière BFW
|
N.A
|
64
|
Système vapeur
|
N.A
|
65
|
Système condensats
|
N.A
|
66
|
Air instrument et air de service
|
N.A
|
68
|
Système fioul gaz
|
N.A
|
69
|
Système fioul oil
|
N.A
|
70
|
Eau de refroidissement
|
N.A
|
71
|
Système de torche
|
N.A
|
78
|
Systeme eau d'incendie
|
N.A
|
Par ailleurs la mise en place du système de
délestage est fortement recommandée pour réduire la
facture d'énergie électrique et en cas de coupure brusque
d'électricité du réseau ONE, le système de
délestage permet de réduire la charge électrique de
certaines unités pour éviter l'arrêt général
de l'usine et ainsi éviter tout risque d'incendie ou d'explosion dans la
raffinerie.
? Quel délesteur utiliser ?
Pour mettre en place un système de délestage qui
permet d'agir en cas de coupure ou de manque d'électricité, il
faut penser aux délesteurs ampèremétriques
Les délesteurs ampèremétriques agissent
en arrêtant la marche d'un ou plusieurs équipements ou en
réduisant leur régime de fonctionnement lorsque s'opèrent
des dépassements de la puissance appelée.
Le délestage des charges électriques s'effectue
en fonction d'un ordre de priorité
décroissant préprogrammé. Lorsque la puissance
appelée retombe en dessous de la puissance souscrite,
les équipements mis à l'arrêt, ou dont le
régime de fonctionnement a été réduit, sont alors
remis dans leur état de marche initial selon l'ordre de priorité,
inverse cette fois.
Les délesteurs électromécaniques mesurent
le courant sur chacune des phases du réseau à partir de
transformateurs d'intensité. Ils sont pourvus de relais à seuil
qui opèrent les séquences de délestage-relestage.
Il existe des délesteurs électroniques qui
prennent en compte des paramètres complémentaires sur les
caractéristiques de fonctionnement des installations comme les
durées minimales ou maximales de mise hors service admissibles.
V-2. Intérêt économique du
délestage
Pour mettre en évidence l'intérêt
économique du système de délestage et l'estimation de
pertes en cas de coupure d'énergie électrique, nous allons
présenter par la suite un calcul du manque à gagner causé
par cet arrêt.
Avec le projet de modernisation de la raffinerie, les
responsables visent une production annuelle de 8 000 000 tonnes de produits
pétroliers. La marge de bénéfice réalisée
par baril produit est quasi-constante, elle est de l'ordre de 6,5 $ (en
2009).
D'après les responsables de la SAMIR, un arrét
de la raffinerie d'une durée d'une heure provoque 5 jours d'arrêt
général de la production pour remettre l'activité en
régime normal et pour que la qualité des produits
pétroliers soit dans le cadre des normes exigées.
Dans le but d'estimer la quantité des pertes suite
à une coupure d'énergie électrique probable,
considérons le cas suivant :
Suite à un problème de la part de l'ONE (baisse
de tension, délestage,...), l'unité de cogénération
et la turbine à vapeur sont en arrêt, il y a lieu d'une coupure
d'énergie d'une durée d'une heure. La réinitialisation de
l'état de production demande 5 jours.
En se basant sur les données citées
précédemment, calculons le manque à gagner sans tenir
compte des autres dégâts :
Rappelons que :
1 baril de pétrole = 0,159 m3
La masse volumique du pétrole = 800
Kg/m3 Densité moyenne du pétrole = 0,8.
La capacité de production de la raffinerie par jour est
égale à :
CProduction/an 8.000.000
CProduction/jour= 365 = 365
CProduction/jour=21.917,8 ~
22.000,00 Tonne/jour
Ceci est équivalent à :
CProduction /Jo???? =
22 000
= n11:11:11:1
0,159 × 0,85 172.955 baril
Le manque à gagner par jour est donc :
Le manque à gagner/ jour=
Cproduction /Jour × 6,5 Le
manque à gagner/ jour= 1.124.213,8 $ Sachant que 1 $ est
équivalentà 8,9 DH
Le manque à gagner/ jour= 10,00 MDH
Sachant que s'il y a lieu d'une coupure d'énergie d'une
durée d'une heure. La réinitialisation de l'état de
production demande 5 jours.
Le manque à gagner causé par une coupure
d'énergie électrique pendant une heure Sera donc :
Le manque à gagner/ coupure éléctriquede 1
heure = 10,00 × 5 MDH
Le manque à gagner pour une coupure électrique
dune heure = 50, 00 MDH
Ce chiffre approximatif donne une idée sur la grandeur
des pertes causées par des arrêts probables qui peuvent avoir lieu
à un moment où (par exemple) l'offre de l'énergie
électrique n'arrive pas à suivre la demande ce qui peut donner
lieu au délestage.
Conclusion générale
Notre projet de fin d'étude s'inscrit dans le cadre de
l'optimisation de la facture énergétique, notamment
électrique de la raffinerie et l'amélioration du système
de production d'énergie par la mise en place de nouvelles installations
permettant une bonne gestion de l'énergie au sein de la SAMIR
Dans un premier lieu, on a calculé les consommations
spécifiques et les coûts de revient des utilités à
savoir, l'eau déminéralisée, la vapeur et
l'électricité dans la centrale thermoélectrique II et
l'unité de cogénération. Et on a trouvé que le
coût de la vapeur produite par la GTE II a connu une augmentation de 19%
en 2010 (264 Dh/T) par rapport à 2009 (222 Dh/T). Cela est dü
essentiellement à l'augmentation des prix de matières
premières, notamment du fuel et donc du pétrole brut, car la
facture pétrolière du Maroc a multipliée, 8,18 MMDH en fin
Avril 2010 au lieu de 3,93 MMDH une année avant.
Pour ce qui est de l'électricité achetée
par l'ONE, elle a augmentée de 0,68 Dh/kWh en 2009 à 0,78 Dh/kWh
en 2010, soit une augmentation de 14,7 %. Et le coüt de
l'électricité produite par l'unité de
cogénération varie en fonction du régime de marche
c.-à-d. de puissance aux bornes de l'alternateur, cette évolution
atteint un minimum pour la puissance 35 MW, soit le régime 87%.
Dans un deuxième lieu on a étudié les
différents scénarios de distribution d'électricité
dans la raffinerie en prenant en considération la nouvelle turbine
à vapeur, ces scénarios sont proposés pour assurer un bon
fonctionnement de la raffinerie, une augmentation de son autonomie
énergétique et par conséquent une diminution de la facture
électrique.
Par ailleurs les solutions proposées permettent
d'augmenter l'autonomie énergétique et ainsi éviter les
pertes économiques en cas d'arrêt de l'usine. L'installation d'un
échangeur de chaleur avant l'économiseur est une solution
efficace pour réduire les problèmes de corrosion et
d'encrassement engendrant une surconsommation du fuel monnayée à
21 MDH.
La mise en place de la nouvelle turbine à vapeur va
permettre de produire une puissance électrique de 8,64 MW, soit 19,63 %
du besoin global en électricité (44 MW) et une augmentation de
l'autonomie électrique de la raffinerie à 87%. Gette solution
réalise une économie sur la facture énergétique
annuelle de 55,8 MDH:
L'intérêt économique du système de
délestage révèle qu'un montant de 50 MDH peut être
économisé comme manque à gagner. Ge chiffre donne une
idée sur la grandeur des pertes causées par des arréts
probables qui peuvent avoir lieu à un moment où l'offre de
l'énergie électrique n'arrive pas à suivre la demande.
Références bibliographiques
[1]: Christian CHATELAIN. Optimisation des processus
énergétiques : gestion optimale, collection techniques de
l'ingénieur, traité Génie énergétique.
[2]: Naima ELOUADI. Approche économique du secteur
énergétique, ministère de l'Economie, des Finances et de
la Privatisation (Maroc)
[3]: American Petroleum Institute, Mécanismes
d'endommagement affectant les équipements statiques dans l'Industrie du
raffinage.
[4]: Claude, LÉVY. Les techniques de
cogénération, collection techniques de l'ingénieur,
traité Génie énergétique.
[5]: Oran EST, Turbine à Gaz MS 6001 B, Cours
Maintenance, société General Electrique, Energy Learning Centre
-- Europe (documentation de la SAMIR).
[6]: LITWIN France, Analyse fonctionnelle de l'unité de
cogénération de la SAMIR.
[7]: Gilbert RUELLE. Turboalternateurs, collection techniques de
l'ingénieur, traité Génie énergétique.
[8]: Eric Gonéalvés et Jean Paul Thibault. Cycles
thermodynamiques des Machines Thermiques.
[9]: Sanae DEHBI, Mémoire de fin d'étude, Etude
de rentabilité du projet de cogénération et l'optimisation
du processus de production de la vapeur moyenne pression par la mise en place
d'une turbine à vapeur.
[10] : J. RENARD, Note sur le calcul de la
répartition de puissances souscrites entre tarif d'appoint et tarif de
secours.
[11] : Union européen, Guide d'audit
énergétique 1999, Gestion de l'énergie
électrique.
[12] : SENHAJI Saliha, ENSA Agadir, Cours de
dimensionnement des échangeurs de chaleur.
[13] : A. BENALLOU, ENIM Rabat, Cours de
conception et calcul des échangeurs de chaleur.
Webographie :
Site officiel de la SAMIR, http://www.samir.ma/ Site
officiel de l'ONE, http://www.one.org.ma/
Annexes
Annexe 1 : Vue générale de l'unité
de cogénération
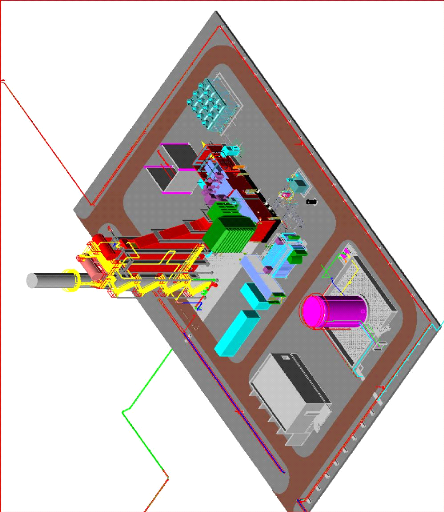
Annexe 2 : Caractéristiques des moteurs de la
cogénération
Moteurs
|
Sigle
|
Tension (V)
|
Puissance (kW)
|
Amperage (A)
|
Cos ö
|
Pompe alimentaire
|
110MP006A/B
|
5500
|
460
|
55
|
0,91
|
ompes d'appoint
|
110MP003A/B
|
400
|
37
|
65
|
0,89
|
Pompes gaz-oil
|
110MP002A/B
|
400
|
18,5
|
32,5
|
0,90
|
Injection O2 scavenger
|
110MP004
|
400
|
0,37
|
0,94
|
0,81
|
Injection phosphate
|
110MP005
|
400
|
0,37
|
0,94
|
0,81
|
Injection ammoniac
|
110MP007
|
400
|
0,37
|
0,94
|
0,81
|
Pompe d'eau de lavage
|
110MP121
|
400
|
15
|
27,2
|
0,89
|
Skid injection eau
|
88WN-1
|
400
|
22
|
37,2
|
0,92
|
Moteur de lancement
|
88CR
|
5500
|
450
|
55,5
|
0,90
|
Pompe auxiliaire
|
88QA
|
400
|
30
|
52
|
0,91
|
Pompe HP
|
88HQ1
|
400
|
15
|
30,1
|
0,85
|
Extracteur vap-huille
|
88QV-1
|
400
|
7,5
|
13,8
|
0,9
|
Pompe de vidange du fût
|
88W-1
|
400
|
0,55
|
1,50
|
0,79
|
huile-gaz-oi Ventillteur 1
|
88TK1
|
400
|
30
|
52
|
0,90
|
refoidissemen Vntillatur 2
|
88TK2
|
400
|
30
|
52
|
0,90
|
refroisissement
t Aé-réfrégéran
|
110GT188FC1
|
400
|
15
|
31,3
|
0,78
|
Aéro-réfrégérant
|
110GT188F
|
400
|
15
|
31,3
|
0,78
|
Aéro-réfrégérant
|
110GT188FC3
|
400
|
15
|
31,3
|
0,78
|
Aéro-réfrégérant
|
110GT188FC4
|
400
|
15
|
31,3
|
0,78
|
Aéro-réfrégérant
|
110GT188FC5
|
400
|
15
|
31,3
|
0,78
|
Aéro-réfrégérant
|
110GT188FC6
|
400
|
15
|
31,3
|
0,78
|
Aéro-réfrégérant
|
110GT188FC7
|
400
|
15
|
31,3
|
0,78
|
Aéro-réfrégérant
|
110GT188FC8
|
400
|
15
|
31,3
|
0,78
|
Aéro-réfrégérant
|
110GT188FC9
|
400
|
15
|
31,3
|
0,78
|
Aéro-réfrégérant
|
110GT188FC10
|
400
|
15
|
31,3
|
0,78
|
Aéro-réfrégérant
|
110GT188FC11
|
400
|
15
|
31,3
|
0,78
|
Aéro-réfrégérant
|
110GT188FC12
|
400
|
15
|
31,3
|
0,78
|
Extracteur air chaude compartiment turbine
|
88BT1
|
400
|
18,5
|
34,5
|
0,83
|
Extracteur air chaude compartiment turbine
|
88BT2
|
400
|
18,5
|
34,5
|
0,83
|
Extracteur air chaude échappement acoustique
|
88EF1
|
400
|
7,5
|
15,2
|
0,82
|
Extracteur air chaude côté turbine
|
88EF2
|
400
|
7,5
|
15,2
|
0,82
|
Dépoussiéreur admission filtre air
|
|
400
|
1,50
|
4,2
|
0 ,74
|
Dépoussiéreur admission filtre air
|
|
400
|
1,50
|
4,2
|
0 ,74
|
Dépoussiéreur admission filtre air
|
|
400
|
1,50
|
4,2
|
0 ,74
|
Extracteur air chaude skid d'injection d'eau
|
88JS1
|
400
|
0,37
|
1
|
0,82
|
|
Projet de Fin d'Etudes
|
|
|
Annexe 3 : les unités de la SAMIR.
Des unités de fabrication des grands produits.
+ Unités de raffinage zone I qui comprend :
- Deux colonnes de distillation atmosphérique (topping I
et II) - Unité de désulfuration du kérosène.
- Unité du lavage des GPL
- Unité de reforming catalytique
- Unités MEROX (GPL -essences légères et
kérosène).
+ Unités de raffinage zone II comprenant :
- Distillation atmosphérique (topping III) - Unité d
hydrotraitement du naphta.
- Unité MEROX GPL et essences légères. -
Unité de séparation C3/C4.
- Reforming catalytique.
- Unité d c des gasoils et du kérosène. -
Unité de lavage aux amines.
+ Un complexe de fabrication des huiles, bitumes et
paraffines. - Distillation sous vide (unite10).
- Unité de desasphaltages au propane (unite11).
- Unité d extraction au furfural (unite12).
- Unité de déparaffinage (unite13).
- Unité d hydrofining (unite14).
- Unité de traitement des paraffines (unité 15).
- Unité d oxydation des bitumes (unité 16).
+ Des installations off sites comprenant:
- parc de stockage de pétrole brut, des produits finis et
semi-fini.
- Deux centrales thermoélectriques pour produire les
différentes utilités : vapeur, électricité, eau
déminéralisé, air comprime, eau tempérée.
- Unité de traitement des eaux résiduaires.
Projet UPGRADE
+ Process Units :
- Unité 31 de distillation sous vide 31 : Vacuum
Distillation VDU
- Unité 33 d'hydrotraitement Gasoil : Distillates
Hydrotreater DHU - Unité 34 d'hydrocrackage: Hydrocraker (fiouls) HCU
- Unité 36 de production d'hydrogène: Hydrogen
Production HPU - Unité 37 de régénération d'amine:
Amine Regeneration ARU
- Unité 38 de Stripping des Eaux Acides: Sour Water
Stripper SWS
- Unité 39 de Récupération du Soufre:
Sulphur Recovery (trains 1 and 2) SRU
+ Utilities and Off sites :
- Unités 60, 61 & 62: Eau de Ville/ Eau de Service/
Eau Déminéralisée
- Unités 63, 64 & 65: Eau de Chaudière/
Système Vapeur/ Système Condensats - Unité 66 - Air
Instrument et Air de Service
- Unité 67 - Système Azote
- Unités 68 & 69 - Systèmes Fioul gas et Fioul
oil
- Unité 70 - Eau de Refroidissement
- Unité 71 - Système de Torche
- Unité 73 - Traitement des Effluents
- Unité 79 - Huile de flash
Annexe 4 : Diagnostique des chaudières A,B,C et
D de la centrale II
Eléments
|
Problèmes rencontrés
|
causes probables
|
Conséquences possibles
|
Action
|
Dégazeur A
|
mise en service le 30/03/2010 Démarrage avec une
T°C inférieur a spec
|
dégradation interne au niveau des chicanes
|
désaération thermique incomplet
|
|
Dégazeur B
|
débordement de l'eau vers l'extérieur (point
d'engorgement) débit de VBB supérieur au débit de l'eau
entré dégazeur
|
Pb au niveau des chicanes
|
Chut de la Température au niveau de paroi externe
de dégazeur
|
|
Corrosion externe au niveau des conduites
|
présence des traces d'eau sous calorifuge
|
Corrosion externe
sous calorifuge démunissions d'épaisseur fuite
de vapeur& fuite d'eau
|
|
Température de l'eau sortie dégazeur
inférieur a l'aspect
|
mauvais contacte entre l'eau et VBB
|
Condensation des fumes
sur l'économiseur dégradation a cause de corrosion
acide
|
Economiseur
|
Chaudière A/C Eco non opérationnelle
|
Ecrasement a cause de condensation des fumes entre les
tubes et les ailettes
|
pas d'échange thermiques entre les fumes et l'eau
circulé a l'intérieur des Eco
perte d'énergie (augmentation de la consommation du fuel
|
|
les Ramoneurs
|
Chaudière C Ramoneur 7 coûté Eco. non
opérationnelle
|
Blocage de l'axe de ramoneur a cause de l'encrassement
|
Accumulation de dépôt &
dégradation
|
|
Les tubes de la chaudière
|
la partie inférieur fuit d'eau arrêt de la
chaudière A le 2/4/2010
|
dépôts des fumes et les imbrulés
|
corrosion localisé dégradation de
tube écran
|
Isolation de Tube a Pb par débauchage
|
les tubes de la partie Ramonage arrêt le 03/04/2010
|
condensation de VM & présence des traces
de SO3
|
Formation et attaque par acide sulfurique
|
Changement des Tubes a Pb
|
Calorifuge
|
Economiseur de la chaudière C Pb de calorifuge
|
|
Chut de T°C de fumes a l'intérieur de l'Eco
|
|
|
Projet de Fin d'Etudes
|
|
|
Annexe 5 : méthodologie de dimensionnement de
l'échangeur de chaleur
> Calcul du flux de chaleur échangé Q :
> Calcul du débit de fluide chaud :
Avec :
Tfe : température d'entrée du fluide froid.
Tfs : température de sortie du fluide froid. Tce :
température d'entrée du fluide chaud. Tcs :
température de sortie du fluide chaud. Cpc : capacité
calorifique du fluide chaud. Cpf : capacité calorifique du
fluide froid. Df : débit du fluide froid.
Dc : débit du fluide chaud.
> Choix des fluides à l'intérieur du faisceau
et dans la calandre :
- - L'eau déminéralisée (fluide froid) dans
la calandre.
- - Vapeur (fluide chaud) à
l'intérieur des tubes.
- 2éme cas pour le fluide chaud l'eau
déminéralisée sortie économiseur avec une
température de 220°C à l'intérieur des
tubes.
>
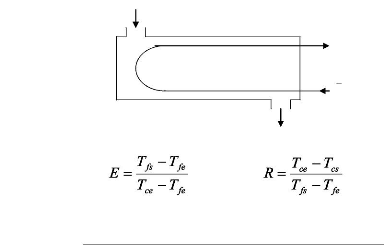
des abaques.
Tfe
Tcs
Tce
Les paramètres E et R
sont donnés par :
Tfs
On calcul les paramètres E et
R et on déduit la valeur du facteur de correction
F à partir
Calcul de la différence de température moyenne
?TLM :
|
|
|
|
|
|
|
|
|
|
|
|
|
|
|
|
|
|
|
|
|
|
|
|
|
|
|
|
|
>
On estime une valeur du coefficient de transfert global
U's d'après la littérature.
> On calcul l'aire d'echange A' de l'apparei
l :
> On choisit une longueur L de l'appareil ;
> On choisit la disposition des tubes dans l'appareil ;
> On choisit un diamètre externe des tubes (on
commence par le plus grand) et on calcul le nombre de tubes totale
Ntt' par la relation :
> On calcul le nombre de tubes par passe N'tp en divisant le
nombre de tubes total par le nombre de passe coté tubes nt :
On vérifie si la valeur trouvée
N'tp appartient à l'intervalle de valeurs dans la
colonne correspondante à la fois au diamètre externe qu'on a
choisit et au nombre de passe coté tubes ; s'elle appartient en prend la
valeur qui la suit directement dans la colonne soit Ntp cette
valeur, si non on reprend le calcul avec la valeur du diamètre le plus
petit qui suit. ?
> On choisit un diamètre interne di
parmi ceux disponibles pour chaque diamètre externe à condition
qu'il assure une vitesse convenable du fluide,
Avec V : vitesse de fluide à l'interieur des tubes ;
S : la section droite du tube ;
et avec
> On corrige la valeur de la surface et la valeur de
Us :
> On calcul la valeur du coefficient global d'échange
propre Up :
Avec hi : coefficient d'échange convectif du film
interne. he : coefficient d'échange convectif du film
externe. > Calcul de hi :
Re : nombre de Reynolds. Pr : nombre de Prandtl.

Et
Pour un faisceau à N nappes (N?10) :
Et la valeur de á donné en fonction du nombre de
nappes

Calcul de he :
On utilisera la corrélation de Donohue :
D
R

Et
Deq : diamètre équivalent du faisceau et Re est
défini par :
Avec
GT : vitesse massique transversale ;
GL : vitesse massique longitudinale :
Df : débit massique du fluide froid
afT : l'aire de passage entre deux chicanes.
Pour un pas carré on a :
B : l'espacement entre deux chicanes et est donné par :
p

et P le pas (pour chaque diamètre externe on a un pas
correspondant).[1]
Avec Dc le diamètre de la calandre et x le rapport de
l'aire du segment libre à la section intérieure de la calandre
(des essais de normalisation tendent à imposer une hauteur de segment
libre égale à 25%).
|
Vérification de la résistance d'encrassement R :
[1]
|
On calcul R et on la compare à la résistance
d'encrassement admissible Rad, le tableau [2]
? ?
P ? ? ? 4 N ? 1 . 5 ?
i p
d
donne certaines valeurs de Rad selon la température, la
vitesse et la nature du fluide utilisé.
? ? i ? ?
> Calcul des pertes de charge :
Les pertes de charge à l'intérieur des tubes
sont données par la relation
[2]
Avec :
ÄP : perte de charge (Pa) .
V : la vitesse du fluide dans les tubes. ñ :
la masse volumique dans les tubes. Np : le nombre de passes cote
tube.
L : la longueur des tubes.
di : diamètre intérieur des tubes.
ë' : le facteur de frottement de MOODY : ë' = 4f [2]
.
[2]
Pertes de charge à l'extérieur des tubes :
[2]
Ou
ÄPt et ÄPl : représentent les pertes de charges
transversales et longitudinales. N : le nombre de chicanes.
Perte de charge transversale (écoulement entre deux
chicanes) :
Avec [2]
[2]
Avec h est la hauteur libre sur les chicanes.
Perte de charge transversale (écoulement a travers les
chicanes) :
[2]
La perte de charge admissible 1 Kg/cm2.
Annexe 6 : cycle thermodynamique de HIRN.
Dans le cycle de HIRN, la détente de la vapeur dans la
turbine s'effectue en zone surchauffée de la vapeur:
Le cycle de HIRN contient :
AA' : compression adiabatique du liquide par la pompe
d'aspiration, A'B : Chauffage du liquide,
BC : vaporisation à pression constante,
CD : surchauffe de la vapeur,
DE : détente dans la turbine,
EA : refroidissement et condensation.
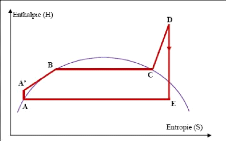
Cycle de HIRN
Le rendement de ce cycle est :
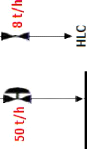








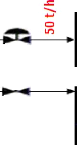








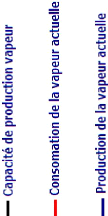

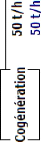



Annexe 7 : capacités de production et
consommation de la vapeur dans la raffinerie.
Biographie des auteurs
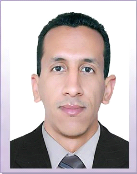
Yassine AIT SI HAMMOU.
Il est né en 1984 à Mohammedia, il a fait ses
études supérieures à la faculté des sciences et
techniques de Mohammedia pour obtenir le Diplôme des Etudes Universitaire
Général DEUG en physique, deux ans après, il a obtenu son
diplôme Maîtrise en génie des procédés et
environnement, il a été major de la promotion. En 2008 il a
intégré l'école nationale des sciences appliquées
d'Agadir pour préparer son diplôme d'Ingénieur
d'État en génie des procédés de l'énergie et
de l'environnement.
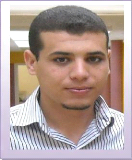
Adil EL ABDLI.
Né en 1986 à Casablanca, Adil El ABDLI a suivi
ses études supérieures à l'Ecole Supérieure de
Technologie (ESTC) de Casablanca, pour obtenir le Diplôme Universitaire
Technologique (DUT) en Génie des procèdes option, industrie
chimiques. Puis en 2007 il a poursuivi sa formation d'Ingénieur
d'État à l'école nationale des sciences appliquées
d'Agadir pour préparer son diplôme en génie des
procédés de l'énergie et de l'environnement.
|