III.5.la problématique de la
réactivité dans les systèmes industriels
Dans le contexte industriel actuel, les organisations ont
à faire face à la fois à :
1) un nombre croissant de perturbations et d'informations
perturbées qui obligent les systèmes de décision à
élaborer des solutions aux problèmes résultants en
exploitant des informations incertaines, incomplètes, voire
obsolètes au moment de leur utilisation ;
2) une complexification des produits et de leurs processus de
production, qui conduit à une complexification des systèmes
opérants : les moyens matériels (machines et outils) sont de plus
en plus sophistiqués, les moyens techniques (méthodes et
procédés de fabrication) sont de plus en plus compliqués.
Il devient essentiel de développer la conception des moyens
matériels et techniques en parfaite harmonie avec les besoins de la
production.
Face à ces contraintes, la réponse des
organisations se compose de deux axes qui contribuent à
l'amélioration de leur réactivité.
Modelisation du temps de reaction d'un systeme industriel :
Application aux centrales thermiques d'OYOMABANG I et II .
D'une part, pour répondre au point 1, elles s'attachent
à développer la capacité de leurs systèmes de
décision à répondre rapidement et efficacement aux
variations de l'environnement.
D'autre part, pour répondre au point 2, les
organisations tendent à favoriser l'intégration des fonctions de
production et de conception grâce à l'ingénierie
concourante. Leur but est de raccourcir le temps global de mise sur le
marché des produits en réduisant leur temps de
développement.
III.6.élaboration d'un reflexe : le transfert
réfléchi-reflexe
Nous nous intéresserons au fonctionnement de la
décision chez l'homme : il est capable de rendre réflexes des
actions qui nécessitent sa capacité d'attention et de
réflexion quand elles sont exécutées pour les
premières fois. Ce mécanisme lui permet d'alléger ses
activités cognitives au fur et à mesure de son apprentissage.
La génération de stratégie
effectuée par les fonctions réfléchies de la
décision permet de mettre en oeuvre un procédé semblable.
Dès qu'une stratégie est établie et validée par une
exécution satisfaisante, elle est intégrée dans l'ensemble
des connaissances du système de commande. Ce processus améliore
l'efficacité du système. Il s'enrichit d'éléments
de connaissance à chaque nouvelle intervention des fonctions
réfléchies de la décision. Par conséquent, le
niveau réfléchi ne sera plus sollicité pour les cas qu'il
aura déjà résolus. De plus, elle disposera de
connaissances évolutives pour mieux appliquer les différents
modes de raisonnement disponibles.
Supposons que ce processus puisse être exploité
complètement. Au bout d'un certain temps de fonctionnement du
système, la plupart des événements imprévus serait
apparu et aurait provoqué une réaction des fonctions
réfléchies de la décision, qui aurait été
mémorisée. Ces imprévus deviendraient des
événements prévus, c'est à dire reconnus comme
susceptibles de survenir pendant l'exécution de la tâche et pour
lesquels le système de décision disposerait d'une réponse
préétablie.
Ainsi, au cours de la vie du système de commande, le
travail des fonctions réfléchies sera progressivement
transféré vers les fonctions réflexes. Ce processus
accroît la capacité réflexe du système et donc son
efficacité à faire face aux événements. Il s'appuie
sur des mécanismes d'apprentissage tels que l'analogie ou
l'apprentissage par induction.
Modelisation du temps de reaction d'un systeme industriel :
Application aux centrales thermiques d'OYOMABANG I et II .
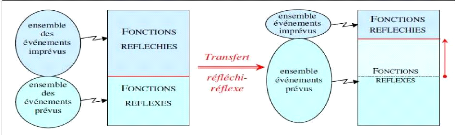
Figure 14 : Le transfert
`réfléchi-reflexe'
III.7.mise en oeuvre de la réactivité
industrielle par une démarche de pilotage Il s'agit des
sept étapes suivantes :
1. formulation d'un objectif global de référence
(ici, la réactivité industrielle) ;
2. déploiement de l'objectif global de
référence sur des processus (processus physiques,
informationnels, et de formation des opératrices) ;
3. analyse des causes de (non) réactivité et des
« leviers d'action » pour les pallier (un diagramme de type Ishikawa
est utilisé) ;
4. définition de plans d'action (ce que nous appelons la
« stabilisation » des processus, « l'amélioration
planifiée » ou « opportuniste ») ;
5. conception d'indicateurs de performance de
réactivité, de tableaux de bord à affichés;
6. conception d'un système d'information associé
;
7. mise en oeuvre d'un groupe de suivi et d'amélioration
de la réactivité.
Cette démarche procède à la fois d'une
logique de contrôle vertical (déploiement de l'objectif de
réactivité industrielle) et horizontal (implication des
différents processus et métiers concourant à l'objectif).
Elle a supposé une action simultanée sur différents
composants du système de production, à savoir :
ü le système de pilotage, avec l'optique
d'améliorer à terme son acuité ;
ü les ressources humaines, en élevant la polyvalence
des opérateurs, donc la flexibilité ;
ü les processus physiques et informationnels, en les
fluidifiants (réimplantation en cellules réactives,
informatisation de l'ordonnancement).
Modelisation du temps de reaction d'un systeme industriel :
Application aux centrales thermiques d'OYOMABANG I et II .
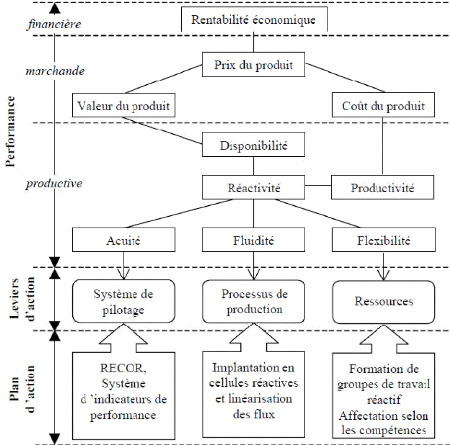
Figure 15 : Déploiement de la
réactivité industrielle [007]
Modelisation du temps de reaction d'un systeme industriel :
Application aux centrales thermiques d'OYOMABANG I et II .
CHAPITRE IV : MODELISATION DU TEMPS DE
REACTION D'UN SYSTEME HIERARCHISE
|
IV.1 définition du temps de
réaction.
Le temps de réaction d'un système industriel par
rapport à un Évènement Non Souhaité (ENS),
représente l'intervalle de temps qui s'écoule entre la date
d'occurrence de l'évènement sur un niveau et la date
d'application de la correction sur le même niveau. Ce temps doit
être le plus petit possible pour garantir une meilleure
réactivité. La réactivité d'un système
d'industriel est définie comme l'aptitude à répondre
(réagir) dans un temps requis aux changements de son environnement
interne ou externe (aléa, situation nouvelle, perturbation,
sollicitation, ...) par rapport au régime (fonctionnement) permanent
(stable).
IV.2 présentation des modèles de temps
de réaction existant. [003]
Cette modélisation qui est basée sur le
modèle GRAI du système industriel, repose sur un certain nombre
d'hypothèse :
> Propagation de l'événement :
l'événement apparait sur un niveau qui, n'arrivant pas à
le traiter localement après une tentative, le répercute au niveau
supérieur. Cette répercussion se répète ainsi de
niveau en niveau jusqu'à celui qui arrive à traiter
l'évènement. Cette phase ascendante (des niveaux bas vers les
niveaux hauts) est appelée phase amont. Elle a un dual : phase aval, qui
correspond à la répercussion de la réaction, du niveau
haut qui l'a élaborée vers le niveau bas qui doit la mettre en
oeuvre ;
> Fonctionnement périodique : la répercussion
d'un niveau à l'autre dans les deux phases amont (pour
l'évènement) et aval (pour la réaction) se fait en fin de
période.
> Existence d'un délai de transmission d'un niveau
à l'autre : la transmission d'un niveau à l'autre de
l'évènement ou de la réaction, selon la phase, n'est pas
instantanée. Il existe un délai de transmission amont et un
délai aval non nul entre deux niveaux consécutifs.
Modelisation du temps de reaction d'un systeme industriel :
Application aux centrales thermiques d'OYOMABANG I et II .
IV.2.1. Décomposition du temps de
réaction.
Pour mieux appréhender les différents temps
composant le temps de réaction ; dans les hypothèses ci-dessus,
on se place dans un cas simple ou un évènement arrivant sur un
niveau k est traité au niveau k+1, soit une répercussion sur deux
niveaux : Les différents temps rencontrés sont :
> Le temps du rendez-vous : c'est-à-dire, le temps
s'écoulant entre la date d'arrivée de l'évènement
ou de la réaction, selon la phase amont ou aval, sur le niveau
considéré et la prochaine fin de période de ce niveau. A
cette fin de période, en phase amont, l'évènement est
traité, si le niveau en est capable, ou alors répercuté au
niveau supérieur, sinon. En phase aval, la réaction est
transmisse au niveau inférieur, si ce n'est pas le niveau d'occurrence
de l'évènement, ou mise en oeuvre, sinon ;
> Le temps (délai) amont : c'est-à-dire le
temps que dure le transfert de l'évènement en phase amont (entre
les niveaux k et k+1) ;
> Le temps (délai) d'élaboration de a
réaction : c'est le temps mis pour élaborer la réaction au
niveau apte à traiter l'évènement ;
> Le temps aval : c'est le temps que dure la transmission de
la réaction, en phase aval, (entre les niveaux k+1 et k).


Figure 16 : Décomposition du temps de
réaction
Modelisation du temps de reaction d'un systeme industriel :
Application aux centrales thermiques d'OYOMABANG I et II .
IV.2.2. Modélisation du processus de
traitement.
Dans le cas ou le traitement de l'évènement
nécessite une succession de répercussion sur plusieurs niveaux,
la procédure étant la même entre deux niveaux
consécutifs, la schématisation du processus est obtenue en
superposant autant de fois qu'il le faut le modèle
précédent.
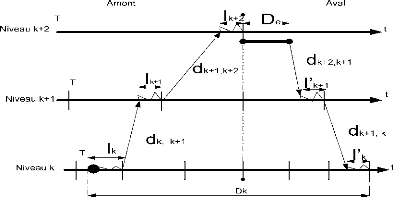
Figure 17 : procédure de réaction sur
trois niveaux
IV.2.3. Évaluation du temps de
réaction d'un Niveau : D.,
Considérons un ENS survenu au niveau n, quelconque, et
qui est finalement traité par un certain niveau m. La propagation dans
les deux phases amont et aval s'est donc déroulé entre ces deux
niveaux.
Pour un niveau quelconque k, entre les niveaux n et m, ayant
reçu l'évènement, on pose :
ü ~k: temps du au rendez vous au niveau k
en phase amont (pour l'évènement).
ü IIk: temps du au rendez vous
au niveau k en phase aval (pour la réaction).
· ( dk,k+i: temps
amont entre les niveaux k et k+1
· ( dk+i,k : temps
aval entre les niveaux k+1 et k
ü De: temps
d'élaboration de la réaction au niveau m, apte à traiter
l'évènement ;
ü Pk : temps limite de transmission ;
Modelisation du temps de reaction d'un systeme industriel :
Application aux centrales thermiques d'OYOMABANG I et II
.
Le temps de réaction s'écrit alors :
~~~
D ~ ? d, ~~~
~~~ ~ ? I
~~~ ~ D! ? I
~~~ ~ ? d, ~
~ ~~~ / (IV-1)
~~~ ~~~
IV.2.4. Expressions des valeurs minimales
(D,imin ) et maximales (Dnmax) de D.
Une expression du temps de réaction minimum, selon
cette modélisation, est proposée d'après l'auteur, elle
s'obtient lorsqu'il existe une parfaite synchronisation, à chaque
niveau, entre les instants de répercussion de la réaction et une
fin de période du niveau considéré. Ce qui se traduit par
:
4=0 et Pk=0, pour tout niveau k
du processus
Ainsi :
Diin -- ? d, ~~~
~~~ ~ D! ~ ? d, ~
~~~ (IV-2)
~~~ ~~~
De même, le temps de réaction serait maximum si l'on
a : 4=Pk et
rk=Pk, pour tout niveau k du processus.
On aura donc :
~~~
D#&' ~ ? d, ~~~
~~~ ~ ? P
~~~ ~ D! ? P
~~~ ~ ? d, ~
~ ~~~ / (IV-3)
~~~ ~~~
Dnmax = ? d, ~~~
~~~ ~~~ ~ P~~D! ~ ? d, ~
~~~
~ 2 ? P
~ (IV-4)
~~~ ~~~
Modelisation du temps de reaction d'un systeme industriel :
Application aux centrales thermiques d'OYOMABANG I et II .
IV. 3. Expression du modèle
adapté.
[002]. Cette étude se base sur une bonne structure
décisionnelle multi niveaux en fonctionnement périodique.
IV.3.1. procédure de traitement de
l'ENS.
Lorsqu'un ENS survient, la procédure de traitement est la
suivante :
Le niveau essaye d'abord de résorber
l'évènement localement : On parle de traitement «
sous contraintes ». S'il n'y arrive pas, il le
répercute ensuite au niveau supérieur : c'est le traitement
« sur contraintes ». Ce dernier à son tour
tente de le résorber, s'il n'y arrive pas aussi, il le répercute
au niveau au dessus. Ainsi de suite, jusqu'à ce qu'un niveau arrive
à résorber l'évènement. Cette procédure est
valable qu'on soit en conduite périodique ou
évènementielle. A la seule différence qu'en conduite
évènementiel, l'évènement est traité
aussitôt qu'il est détecté, sinon, répercuté
directement au niveau supérieur, alors qu'en conduite périodique,
le traitement de l'évènement a lieu en fin de période, sur
chaque niveau. Ce qui entraine des temps d'attente qui rallongent le temps de
réaction du système.
IV.3.2. hypothèses
d'étude
Pour l'étude nous faisons les hypothèses suivantes
:
> Le système fonctionne en régime
périodique, fonctionnement pour lequel les délais de
réaction sont plus long par rapport au fonctionnement
évènementiel ;
> Sur chaque niveau, il existe un décalage (pouvant
être nul) entre la date de référence, origine des temps
(to) et la date de début de la période de
référence, période suivant la
date de référence, Xin (o), du niveau m
considéré, ces décalages ne sont pas forcement
égaux pour tous les niveaux ;
> Nous supposons un classement en familles des
évènements Non Souhaités. Chaque famille étant
traitée, dans le cas le plus défavorable, par un niveau N ;
> Nous considérons, dans le cas la plus
défavorable d'une famille quelconque, un ENS qui apparait sur le niveau
0, et qui, n'arrivant pas à être traité, est
répercuté jusqu'au niveau
Modelisation du temps de reaction d'un systeme industriel :
Application aux centrales thermiques d'OYOMABANG I et II .
N ou il est finalement traité. Il va donc parcourir au
total N+1 niveaux. Ce cas particulier représente le temps de
réaction le plus long dans famille considérée.
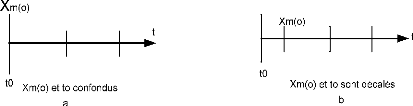
Figure 18 : positions relatives possibles entre to et
Xm (o) sur un niveau m
|