Ministère de l'Enseignement Supérieur et
de la Recherche Scientifique
Université des Sciences et de la Technologie
MOHAMED BOUDIAF d'Oran
Faculté d'Architecture et de Génie
Civil
Département de Génie Civil
Projet de fin d'étude Pour l'Obtention du Diplôme
de Licence en Génie Civil
Réhabilitation des ouvrages en béton armé
Présenté par :
BENGUESMIA CHADLI MUSTAPHA AMINE
ABDELMALEK ABDEL NOUR
Dirigé par :
Melle BOUALLA N.
Promotion 2011-2012
mediatec
[Tapez le nom de la société]
Promotion 2011-2012
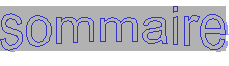
INTRODUCTION
5
CHAPITRE 01
8
1- DESCRIPTION DES PATHOLOGIES DU
BÉTON ARMÉ
9
1.1. LA FISSURATION
9
1.2. LA CARBONATATION DES
BÉTONS :
11
1.3. LA CORROSION DES ARMATURES :
12
1.3.1. LE PHÉNOMÈNE DE CORROSION
DANS LE BÉTON ARMÉ :
12
1.3.2. LES CAUSES DE LA CORROSION
12
1.3.3. LES CONSÉQUENCES DE LA
CORROSION :
13
1.4. Les autres causes de dégradation
des bétons
15
1.5. Classification général des
pathologies
16
2- LES PHASES DE
DÉGRADATION :
17
3- CONSÉQUENCES DES
DÉSORDRES :
17
3.1. L'aspect de
l'ouvrage :
17
3.2. La sécurité
vis-à-vis des usagers :
17
3.3. La stabilité de la
construction :
17
CHAPITRE 02
19
1- RÉALISATION D'UN DIAGNOSTIC :
20
1.1. CHOIX DES INVESTIGATIONS :
20
1.2. TYPES D'INVESTIGATIONS
22
1.2.1. INVESTIGATIONS NON DESTRUCTIVES
22
1.2.1.1. RELEVÉ VISUEL ;
23
1.2.1.2. L'ANALYSE DU FERRAILLAGE :
27
1.2.1.3. L'AUSCULTATION SONIQUE :
30
1.2.1.4. SCLÉROMÈTRE :
32
1.2.2. INVESTIGATIONS DESTRUCTIVES
33
1.2.2.1. CAROTTAGE D'ÉLÉMENTS EN
BÉTON ARMÉ
33
1.2.2.2. PRÉLÈVEMENTS
D'ACIERS :
35
1.2.2.3. POTENTIEL DE CORROSION :
36
1.2.2.4. TEST À LA
CARBONATATION :
38
1.3. CONCLUSION SUR LE DIAGNOSTIC :
40
2. RAPPORT DE DIAGNOSTIC :
41
3. CONTRAINTES ET EXIGENCES
41
3.1CONTRAINTES STRUCTURELLES
41
3.1.1.2. Pertes de section des armatures
42
3.1.1.3. Ancrage et entraînement des
armatures
43
3.1.1. Respect du
fonctionnement de la structure en l'état
43
3.1.1.1. Pertes de section du béton.
43
3.1.2. Respect des matériaux en place
44
3.1.2.1. Les actions irréversibles sur la
nature des matériaux
44
3.1.2.2. Les effets secondaires après
traitement
44
3.1.2.3. Les conséquence du choix des
matériaux de remplacement
45
3.2. EXIGENCES A PRENDRE EN COMPTE POUR LES
REPARATIONS
45
4. DURABILITE
46
4.1. Les contrôle du
résultat des traitements
46
4.2. Le contrôle des
revêtements de protection des bétons
46
CHAPITRE :03
47
1. RÉPARATION D'UN OUVRAGE EN BÉTON
ARMÉ
48
1.1. LE RAGRÉAGE
48
1.2. LE BÉTON PROJETÉ
50
1.2.1. HISTORIQUE DE LA MÉTHODE
51
1.2.2. TECHNIQUE DE PROJECTION
52
1.2.3. MODE OPÉRATOIRE
53
1.2.4 MATÉRIAUX UTILISÉS
54
1.3. TISSUS DE FIBRES DE CARBONE
56
1.4. CONCLUSION SUR LES RÉPARATIONS
57
2. PROTECTION DES OUVRAGES EN BÉTON
ARMÉ
58
2.1. LE REVÊTEMENT
IMPERMÉABILISANT
59
2.1.1. LES PEINTURES
59
2.1.2. LES LASURES
60
2.1.3. LES REVÊTEMENTS MINCES
60
2.1.4. LES ENDUITS DE FAÇADE
60
2.2. LES INHIBITEURS DE CORROSION
61
2.3. LA DÉCHLORURATION
63
2.4. LA RÉ-ALCALINISATION
66
2.5. LA PROTECTION CATHODIQUE
68
3. RECAPITULATIF
71
4- NORMES
75
CHAPITRE 04
77
1. CONTROLES DE LA MISE EN OEUVRE
78
1.1. PREPARATION DES TRAVAUX
78
1.1.1. Dossier de consultation des
entreprises
78
1.1.2. Mise au point du marché
79
1.1.3. Plan assurance qualité (PAQ)
79
1.2 .CONTROLE INTERIEUR DE L'ENTREPRISE
79
1.2.1. Epreuves
79
1.2.1.1. Epreuve d'étude
79
1.2.1.2. Epreuve de convenance
80
1.2.2. Réceptions
80
1.2.2.1. La réception des
matériaux
80
1.2.2.2. La réception du support
81
1.2.2.3. La réception des produits
81
1.2.3. Contrôle de la mise en
oeuvre
81
1.2.4. Contrôle des travaux finis
82
1.3. CONTROLE EXTERIEUR DU MAITRE D'OEUVRE
82
2. SUIVI D'UN OUVRAGE
83
2.1. LE SUIVI PONCTUEL
83
2.2. LE SUIVI CONTINU
83
CONCLUSION
85
Introduction
L
e béton est un matériau employé depuis
des millénaires, mais ce n'est qu'au XIX siècle qu'il connait un
grand essor notamment grâce au ciment de Portland et à Louis
Vicat. Il aura fallu attendre la fin de ce siècle pour voir apparaitre
les premières constructions en béton armé.
Depuis il est devenu un matériau composite
incontournable. Les éléments en béton armé sont
très présents dans notre vie.
Que ce soit dans un pont pour traverser une route, dans un
bâtiment pour abriter des personnes ou dans des activités, ou
autres ouvrages en béton armé, ils remplissent tous une ou
plusieurs fonctions bien précises.
Ces ouvrages sont nécessaires au bon fonctionnement de
notre société, car ce sont des éléments facilitant
ou améliorant la vie des usagers. Pour leur permettre de remplir leur
rôle, il est nécessaire de s'assurer de leur bonne santé et
dans le cas contraire les réparer.
C'est dans cette optique que s'inscrit le diagnostic
d'un ouvrage.
À partir du moment où une pathologie est
apparue, même si cela ne remet pas en cause la stabilité de
l'ouvrage, il est important de diagnostiquer d'une part d'où vient le
problème, mais à quel degré il affecte
l'édifice.
Dans un second temps, il est nécessaire de supprimer
le problème à la source et de réparer l'ouvrage.
Le diagnostic est un moment clé lorsqu'il y a
présence de pathologies.
En effet, si la source du problème est mal
diagnostiquée, les réparations préconisées ne
correspondront pas réellement à ce qui est nécessaire et
l'ouvrage sera toujours soumis aux mêmes attaques.
Pour effectuer un diagnostic, différents moyens
d'investigation sont disponibles. On a d'une part les méthodes
destructives, pour les structures pouvant être localement
dégradées et les méthodes non destructives pour les
ouvrages nécessitant d'être préservés tels que
les bâtiments classés monuments historiques.
Une fois les causes ainsi que les pathologies
diagnostiquées, il est nécessaire de prévoir des travaux
de réhabilitation afin de redonner à la structure ses
caractéristiques physiques et mécaniques initiales.
Afin de retarder ou de limiter de nouvelles pathologies
similaires, il est possible de protéger la structure. Il existe un grand
nombre de protections, elles sont à choisir selon les différentes
pathologies, mais aussi sur la durée de pérennisation
espérée. Elles vont du simple revêtement appliqué
sur le parement, aux traitements électrochimiques.
Ces expertises se développent de plus en plus
notamment du fait d'une volonté des pouvoirs politiques de
s'inscrire dans un schéma de développement durable, à
savoir, pérenniser l'existant.
Il est aussi possible de ne pas prévoir des travaux,
mais seulement s'intéresser à l'évolution des pathologies.
C'est le cas par exemple pour des fissures, il peut être
utile de vérifier si son ouverture est continuelle dans le temps, dans
ce cas il sera nécessaire de prévoir des travaux de confortement.
Ou bien si l'ouverture de la fissure dépend de l'évolution de la
température, auquel cas il est possible de laisser l'ouvrage en
l'état sans craindre une dégradation de l'ouvrage.
Chapitre 01
1- DESCRIPTION DES PATHOLOGIES DU
BÉTON ARMÉ
D
ans cette partie, nous nous intéresserons aux
principales pathologies apparaissant dans le béton armé durci.
Ces pathologies ont des causes et conséquences variables. Elles sont
décrites dans la suite.
1.1. LA FISSURATION
Il est important avant tout de souligner qu'il est impossible
aujourd'hui d'éviter la fissuration du béton armé, que ce
soit lors de la mise en oeuvre, due par exemple au retrait de dessiccation ou
sur le béton durci, dû au vieillissement du matériau. Les
causes de la fissuration sont multiples, mais peuvent être
répertoriées en quatre catégories :
· Les causes dues aux propriétés des
matériaux, avec par exemple le retrait suite à
l'évaporation de l'eau de gâchage, le gonflement engendré
par la réaction exothermique du liant ou encore à la
résistance mécanique de la cohésion du liant.
· Les causes directes externes, avec notamment les
déformations excessives sous l'action des charges ou encore des
déformations sous l'action des variations de température ou sous
l'action de l'humidité.
Ø Les causes externes indirectes, à savoir les
répercussions sur certaines structures d'actions provenant d'autres
éléments tels que les tassements différentiels des
fondations.
Ø Les causes dues à un phénomène
de corrosion des armatures, les armatures corrodées ayant un volume plus
important que les aciers en bon état, l'état de contrainte du
béton au droit d'une armature corrodée est plus important et la
fissuration s'enclenche.
Parmi les différents types de fissures, on distingue
principalement trois catégories :
Ø Le faïençage, c'est un réseau
caractéristique de microfissures qui affecte principalement la couche
superficielle du béton
Ø Les microfissures, ce sont des fissures très
fines dont la largeur est inférieure à 0,2 mm.
Ø Les fissures, ce sont des ouvertures linéaires
au tracé plus ou moins régulier dont la largeur est d'au moins
0,2 mm
Il est important lors du processus de réhabilitation
d'un ouvrage, de s'intéresser à l'évolution de la largeur
d'une fissure. Il est possible de classer les fissures en trois
catégories selon leur évolution :
Ø Les fissures passives ou mortes, pour les fissures
dont les ouvertures ne varient plus dans le temps, quelles que soient les
conditions de température, d'hygrométrie ou de sollicitation de
l'ouvrage. Cependant, elles sont rares, car les matériaux alentour
à la fissure varient selon la température, c'est le
phénomène de dilatation thermique.

Ø Les fissures stabilisées, lorsque leur
ouverture varie dans le temps en fonction de la température.
Fissure superficiel Fissure
profonde
Figure1 : représentant des fissures
relevées sur les parois
1.2. LA CARBONATATION DES
BÉTONS :
La carbonatation dans le béton armé correspond
à un phénomène chimique. Le CO2 contenu dans l'air
réagit avec l'hydrate de chaux présent dans le béton.
Cette réaction forme du carbonate de calcium et de l'eau.
L'écriture simplifiée de cette réaction est la suivante
:
Ca(OH)2 + CO2 -> CaCO3
+ H20
Cette réaction a pour conséquence que les
deux bases alcalines présentes dans le béton sont
consommées, il y a donc une diminution du pH du béton.
La valeur initiale du pH du béton de jeune âge
est aux environs de 13 à 13,5. Après carbonatation il est autour
de 9.
La carbonatation génère une modification lente
de la structure du matériau et un changement de son comportement. Certes
elle a un effet néfaste en réduisant la protection chimique des
armatures, mais elle est aussi bénéfique agressives en
améliorant la résistance mécanique et la
résistance aux eaux.
Le schéma de la carbonatation peut être
représenté de la manière suivante :

Figure 2 : Phénomène de carbonatation
1.3. LA CORROSION DES
ARMATURES :
1.3.1.
LE PHÉNOMÈNE DE CORROSION DANS LE BÉTON
ARMÉ :
Le béton sain ayant un pH de l'ordre de 13 correspond
à un milieu naturellement protecteur pour les armatures.
Autour des aciers se forme un film passif, une
solution solide de Fe3O4 -
Fe2O3 permettant de réduire voir d'arrêter la
vitesse de corrosion. La dépassivation de l'acier peut se faire dans les
cas où le béton d'enrobage est carbonaté ou si la teneur
en chlorure est élevée.
Après destruction du film passif, un
phénomène de pile électrochimique se met en place,
le milieu électrolytique étant constitué par la solution
interstitielle du béton. Au niveau de la zone correspondant
à l'anode, l'acier se dissout, entrainant une production
d'électrons qui seront consommés au niveau de la cathode par
réduction d'oxygène.
Cette réaction entraine la formation d'ions hydroxyle
OH- réagissant avec les ions ferreux produits au niveau de
l'anode.
En présence d'oxygène, il se forme à
l'anode des oxydes et hydroxydes de fer gonflants.

Figure 3 : Phénomène de corrosion
1.3.2. LES CAUSES DE LA
CORROSION
On distingue principalement deux facteurs favorisant
l'apparition de la corrosion dans le béton armé. Tout d'abord, il
y a la carbonatation du béton, lorsque le pH du béton descend en
dessous de 9 les armatures ne sont plus passivées.
Ce phénomène est occasionné par la
réaction entre les hydrates de la pâte de ciment et le CO2
atmosphérique.
L'autre facteur étant les chlorures, la dé
passivation s'opère lorsque la teneur en chlorures au niveau des
armatures dépasse un certain seuil. Il est admis que ce seuil correspond
à une teneur de 0,4% par rapport à la masse du ciment. le
schéma suivant décrit le principe de corrosion dans le
béton armé :

Figure 4 : Processus de corrosion
1.3.3. LES
CONSÉQUENCES DE LA CORROSION :
La formation de la corrosion s'effectue au dépens du
métal d'origine. Ce phénomène entraine à la fois
une augmentation importante de volume ainsi qu'une perte de la section efficace
de l'armature.
Cela a pour conséquences d'une part l'apparition de
différentes pathologies au niveau du parement suite à
l'augmentation de volume, mais aussi une perte de capacité portante due
à la diminution de la section efficace.
Ces pathologies peuvent être des fissures, des
épaufrures, des décollements, ...

Figure 5: Évolution de la dégradation d'une
structure en béton armé

Figure 6 : Dégradation due à la corrosion
1.4. Les autres causes de
dégradation des bétons
Nous avons vu que les bétons se dégradaient
à cause des milieux dans lesquels ils sont placés car ils y
subissent des agressions physiques et chimiques. Certaines causes,
essentiellement dues à une mauvaise mise en oeuvre, peuvent
également participer à la dégradation des
bétons.
Ø Mauvais positionnement des armatures : Les
armatures (généralement en acier) placées trop près
du parement béton lors du coulage provoquent à terme des
fissurations de surface.
Ø Mauvaise qualité des bétons
employés : Un béton trop faiblement dosé en ciment,
mal vibré, présentera un aspect défectueux : nids
d'abeilles, faïençage, fissures superficielles, trous laissant les
armatures apparentes.
Ø Vibration trop importante : Une vibration trop
longue peut entraîner une ségrégation du béton et
par conséquent une mauvaise répartition des constituants. Les
efforts mal répartis entraînent alors des fissurations et des
élancements du béton.
Ø Absence de cure du béton : La cure du
béton est indispensable par temps chaud venté. Sans protection de
surface, le béton se faïence en surface.
Ø Cycle humidité / sécheresse :
Les cycles répétés d'humidité/sécheresse
entraînent des variations dimensionnelles du béton pouvant
créer des fissures et par conséquent la corrasion des aciers.
1.5. Classification
général des pathologies
Famille
|
Lésions
|
Types
|
Physique
|
Humidité
|
Capillaire/De filtrage/De condensation/Accidentelle/De
travaux
|
Saleté
|
Par dépôt / Par nettoyage différentiel
|
Erosion
|
Météorologique
|
Mécanique
|
Déformations
|
Tassement/Effondrement/Flambement/Gauchissement/
Flèche
|
Fissures
|
Par charge / Par dilatation - contraction
|
Fissures superficielles
|
Par support / Par finition
|
Détachements
|
Finitions continues / Finitions par éléments
|
Erosion
|
Coups / Frottements
|
Chimique
|
Efflorescence
|
Sels solubles cristallisés/Réaction chimique
avec les sels
|
Oxydation
|
Oxydation superficielle
|
Corrosion
|
Oxydation préalable/Immersion/Aération
différentielle/Paire galvanique
|
Organismes
|
Présence et attaque d'animaux/Présence de
plante
|
Erosion
|
Pollution
|
Tableau 1. Classification
générale des pathologies liées au bâtiment. (Source
J. Monjo- Carrio, 2011).
Le tableau ci-dessus regroupe les différentes
pathologies qui peuvent atteindre un bâtiment.
Elles y sont classées en trois grandes
catégories ; physique, mécanique et chimique, avec en
complément le détail de leur typologie et de leur origine.
L'étude de ces pathologies constitue une étape
majeure dans le processus de la réhabilitation-que nous aborderons en
aval- notamment au stade de l'élaboration du diagnostic, étape
déterminante dans la définition des interventions à mener
sur le bâtiment.
2- Les phases de
dégradation :
La dégradation du béton armé comporte
deux phases successives :
Ø Une phase d'incubation ou de latence (dite parfois
d'amorçage) qui correspond à l'altération lente du
béton, sans qu'il ne se produise encore des effets visibles,
Ø Une phase de développement (dite parfois de
croissance) des dégradations du matériau.
La phase d'incubation s'arrête :
Ø Soit lorsque les produits formés par les
réactions internes du ciment atteignent un «volume critique »
provoquant un gonflement néfaste du béton (par exemple, par
réaction sulfatique),
Ø Soit lorsque l'enrobage de béton ne
protège plus les aciers contre la corrosion (par exemple, si l'enrobage
est carbonaté).
La phase de développement est celle où les
dégradations sont visibles.
A ce stade les réparations deviennent lourdes et
coûteuses.
3- CONSÉQUENCES DES
DÉSORDRES :
3.1.
L'aspect de l'ouvrage :
Les efflorescences et les taches de rouille conséquence
de la pénétration d'agents agressifs dans l'enrobage de
béton, altèrent l'aspect de l'ouvrage. Ce point est parfois
considéré comme étant de peu d'importance, par le
gestionnaire des ouvrages. Par contre, ce sont les fissurations et les
fracturations du béton qui commencent à inquiéter le
gestionnaire, car des éclats de béton peuvent se produire.
3.2. La sécurité
vis-à-vis des usagers :
Les éclats de béton présentent un
risque pour les personnes qui circulent près de l'ouvrage. Leur
prévention et leur élimination doivent donc être
traitées avec soin.
3.3. La stabilité de la
construction :
Des essais effectués sur des éprouvettes ont
permis d'estimer les valeurs des forces d'adhérence pour des
éléments en béton dont les armatures sont
corrodées.
Il est apparu que ni la qualité du béton, ni le
rapport enrobage/diamètre d'armature n'influent sur la force
résiduelle d'adhérence, même si l'enrobage est
fissuré par la corrosion de l'armature sans qu'il ne soit
détruit par éclatement.
En ce qui concerne les moments fléchissant et les
efforts tranchants, une recherche expérimentale a porté sur
l'effet de la corrosion sur ces grandeurs mécaniques. Elle a
montré que pour prévoir de façon conservatrice la tenue
des éléments en béton armé, il suffit d'appliquer
les modèles de calculs classiques, en considérant la section
réduite des armatures ainsi que la section réduite de
béton.
Ainsi, tant que les diminutions de section des armatures
restent faibles et que l'enrobage reste cohésif, la corrosion de ces
armatures ne modifie pas significativement la tenue au moment
fléchissant ou aux efforts tranchants.
Mais lorsque la corrosion a atteint un stade avancé,
des calculs plus précis doivent être faits pour évaluer la
tenue résiduelle de l'ouvrage.
Ce document ne traite que du matériau et laisse de
côté les problèmes de structures.
Chapitre 02
1- RÉALISATION D'UN
DIAGNOSTIC :
L
e diagnostic d'un ouvrage est une étape importante dans
le processus de sa réhabilitation. Il permet avant tout de se prononcer
son état de santé et de voir quelles sont les éventuelles
pathologies ainsi que leur ampleur.
Généralement lorsque l'on effectue un
diagnostic, c'est quand un client découvert quelque chose qui
n'allait pas dans le fonctionnement de l'ouvrage ou bien l'apparition de
désordres.
Le diagnostic peut avoir principalement deux finalités.
Dans un premier temps, il peut être demandé de
suivre l'évolution des différentes pathologies dans le temps, que
ce soit à court, moyen ou long terme. Cela permet d'évaluer le
comportement de l'ouvrage sous l'effet de ces troubles, de voir s'il y a une
stagnation du phénomène ou s'il y a une
dégénérescence, auquel cas il est important de
prévoir des réparations.
L'autre finalité d'un diagnostic c'est de
répertorier tous les désordres, mais aussi la constitution de
chaque élément, en vue d'un traitement immédiat.
1.1. CHOIX DES
INVESTIGATIONS :
Le choix des investigations dans un diagnostic d'ouvrage
dépend de plusieurs paramètres. Il est primordial de les
évaluer afin de mettre en oeuvre les moyens adaptés pour
répondre pleinement à la mission.
Ces différents paramètres sont les suivants :

Figure 7: Schéma du choix
d'investigation
En effet, le choix des investigations dans un diagnostic
d'ouvrage dépend :
- Du type de mission à réaliser ; selon ce que
souhaite le client, il est possible de réaliser différents types
de missions à savoir :
o Une inspection de l'ouvrage
o Un diagnostic
o Un diagnostic approfondi
o Un suivi d'ouvrage
Chacune de ces missions met en oeuvre différentes
méthodes de diagnostic, de plus ou moins grande ampleur, mais aussi une
interprétation des résultats plus ou moins poussée.
- De la nature des matériaux ; Le diagnostic d'un
ouvrage en béton armé ne fera pas appel aux mêmes
techniques d'investigation que pour un ouvrage en bois, en acier ou en
pierre.
De plus, chacun de ces matériaux a ses propres
pathologies types.
- Du type de structure ; Les moyens à mettre en oeuvre
seront différents selon qu'il s'agisse d'un ouvrage d'art ou bien
d'un bâtiment industriel ou un bâtiment d'habitations. La
géométrie et la taille de l'ouvrage rentrent aussi en compte dans
le choix des investigations.
- De l'environnement dans l'ouvrage ; Il est important
de prendre lequel se trouve l'ouvrage, car il peut être en
considération à l'origine de ces pathologies. C'est le cas
notamment pour les structures en milieu chimique ou pour le
bâtiment « La Saline » pour lequel sa structure se trouve dans
un milieu, avec beaucoup d'éléments de chlorures, directement
lié à l'activité se déroulant dans le
bâtiment.
- De l'état de l'ouvrage ; Les investigations
dépendent d'une part des désordres qui affectent l'ouvrage, le
matériel et le type d'investigation à mettre en oeuvre seront
différents pour des armatures corrodées ou pour des fissures.
Mais cela dépend aussi de la fragilité de l'ouvrage. S'il est
à la limite de la stabilité, on se dirigera plutôt vers des
méthodes non destructives afin de ne pas affecter plus la structure.
De plus, certaines parties de structures peuvent être
inaccessibles ou nécessitant la mise en place d'échafaudages ou
nacelle afin de pouvoir diagnostiquer ces éléments.
1.2. TYPES
D'INVESTIGATIONS
Il est possible de classer les différentes
investigations en deux catégories : soit les méthodes non
destructives, soit les méthodes destructives. Les principales
méthodes rencontrées lors de diagnostics sont
décrites dans la suite.
1.2.1. INVESTIGATIONS
NON DESTRUCTIVES
Le principe de ces méthodes de diagnostic réside
dans le fait que l'on analyse l'ouvrage ou une partie de l'ouvrage sans
porter atteinte à son intégrité.
Ceci est à privilégier dans
différents cas, par exemple les bâtiments classés
monuments historiques, pour lesquels il est difficile de faire accepter aux
architectes des bâtiments d'Algérie qu'il soit utile d'effectuer
des prélèvements de la structure pour pouvoir la
caractériser.
Ces méthodes sont à favoriser aussi dans le cas
d'ouvrage dont la structure est très atteinte et affaiblie.
Effectuer des prélèvements sur ce type de
structure risque de la fragiliser encore plus.
Pour les ouvrages en béton armé, il existe
différentes méthodes non destructives.

Figure 8 : Schéma des investigations non
destructives
1.2.1.1. RELEVÉ
VISUEL ;
Le diagnostic visuel consiste à aller sur site et
d'analyser chaque élément de la structure en détail.
Ainsi, cela permet dans un premier temps de connaitre les
caractéristiques géométriques de chaque
élément et aussi les matériaux constitutifs.
Cela permet d'évaluer le comportement global de
l'ouvrage, de connaitre les éléments porteurs ainsi que
l'acheminement des charges dans la structure.
Dans un second temps, il est nécessaire de
répertorier les différentes pathologies présentent sur la
structure.
Les principaux désordres rencontrés pour les
structures en béton armé sont les suivants :
o Les fissures, avec leur ouverture et leur longueur
o Les fractures, avec leur ouverture, décalage ou
rejet
o La présence de coulures de calcite
o Les zones d'altération superficielles et profondes
o Les zones humides
o Les zones de mousses ou de végétation
o Les zones de faïençage
o Les éclats de béton en formation ou
profonds
o Les aciers apparents
o Les zones de ségrégation
Il est nécessaire de répertorier tous ces
éléments sur des plans, soit existant soit à créer,
et de créer un dossier photographique des principaux désordres
afin de pouvoir les visualiser au mieux.
Dans tous les cas le diagnostic visuel doit permettre de
:
- Qualifier les désordres, car chaque type a une
origine et des conséquences particulières.
- Déterminer les caractéristiques d'une
pathologie permet de savoir quelle sorte de traitement sera nécessaire
afin de stopper le phénomène.
- Quantifier les désordres, car selon son ampleur, des
méthodes de réparation plus ou moins lourdes seront à
envisager.
- Localiser les désordres afin de pouvoir
déterminer son origine et ainsi agir à la source du
problème. S'il est seulement prévu de réparer
l'élément sans s'attaquer à ce qui engendre la pathologie,
la réparation risque de ne pas être pérenne et l'on verra
rapidement apparaitre de nouvelles pathologies similaires.


Les pathologies rencontrées lors du diagnostic visuel
sont généralement recensées dans un tableau 

de type :
Localisation
|
Description du désordre
|
Photo n°
|
Poutre A1-2
|
Face Est : Décollement avec aciers
apparents ; hauteur 12 cm, largeur 20 cm, profondeur 0 à 4 cm.
|
1
|
Poteau C3
|
Face Ouest : Fissure transversale ; épaisseur 0,5
à 2 mm, longueur 50 cm
|
8
|
Il est possible de classer les éléments selon la
gravité de leur pathologie :
-Indice A : Pas de défauts
apparents.
-Indice B : Défauts sans
conséquence importante autres qu'esthétique.
-Indice C : Défauts qui indiquent
qu'une évolution risque de se faire anormalement. Ces défauts
doivent être surveillés.
-Indice D : Défauts
révélateurs de dégradation, ils sont rangés en deux
classes:
O DA : Défauts qui indiquent un
début d'évolution. Ils doivent être
surveillés régulièrement et des mesures doivent être
prises en cas d'évolution.
O DB : Défauts qui indiquent une
évolution avancée. Des mesures de renforcement ou de remplacement
doivent être prises.
-Indice E : Défauts qui traduisent de
façon très nette une modification du comportement de la structure
et qui mettent en cause la durée de vie de l'ouvrage. Des mesures
doivent être prises dans les plus brefs délais.
-Indice F : Défauts indiquant la
proximité d'un état limite et nécessitant soit une
restriction d'utilisation, soit la mise hors service de l'ouvrage.
De même, il est possible de classer le site dans sa
globalité afin de donner une vision d'ensemble de l'état de la
structure au maître d'ouvrage. Il peut être classé de la
manière suivante:
-Indice 1 : Site en état neuf ou quasi
neuf, aucun travaux n'est à prévoir à moyen termes.
-Indice 2 : Site en très bon
état général, quelques points à surveiller.
-Indice 3 : Site en bon état, quelques
travaux à prévoir à moyen ou long termes.
-Indice 4 : Site en état moyen,
travaux à prévoir à moyen termes et surveillance
conseillée.
-Indice 5 : Site dégradé,
travaux à court termes à prévoir.
-Indice 6 : Site très
dégradé, travaux d'urgences à prévoir, site
prioritaire.
Les outils indispensables pour mener à bien une
inspection visuelle sont les suivants :
-Un appareil photo
-Un mètre
-Un distancemètre
-Un pied à coulisse
-Un fissuromètre (réglette en plastique
transparente munie de traits de largeurs calibrées que l'on place
successivement sur la fissure à observer pour estimer sa largeur)
-Le nécessaire pour prendre des notes

Figure 9 : Fissuromètre
Cette première étape permet de définir la
gravité des pathologies, mais aussi de classer les différents
éléments en fonction de la priorité auxquels ils doivent
être réparés.
L'investigation visuelle permet aussi de prévoir quels
sont les autres moyens de diagnostic les plus adaptés à mettre en
oeuvre afin de répondre pleinement à la problématique.
Ces investigations complémentaires on pour but de
préciser les désordres observés lors du
relevé visuel, mais aussi de recueillir des informations
complémentaires concernant leur constitution ainsi que leur
état.

Figure 10 : Mesure d'une fissure
1.2.1.2. L'ANALYSE DU
FERRAILLAGE :
Le relevé du ferraillage peut se faire à l'aide
d'un pachomètre de type Ferroscan.
Cet appareil est un système de détection
portable pour un examen d'armatures non destructif. Il permet de
déterminer le positon exact des barres d'armatures, de mesurer
l'enrobage et de donner une indication du diamètre de l'armature.
Le principe de fonctionnement repose sur l'émission
d'un flux magnétique par l'appareil.
Le pachomètre détecte la diffusion de ce champ
magnétique ainsi que les modifications de la résonance
magnétique induite par la présence d'aciers. Ainsi, l'appareil
mesure la variation électromagnétique due à la
présence d'éléments ferromagnétiques, les
armatures.
La détermination du diamètre et de l'enrobage
repose sur le fait que plus une armature a un diamètre important,
plus le signal reçu par l'appareil sera important. A contrario, plus
l'épaisseur d'enrobage sera importante, plus le signal sera faible.
Ainsi, la profondeur d'auscultation avec cet appareil est
limitée (généralement de l'ordre de 10 à 15
centimètres selon le type de bétons et le type d'armatures).
Le schéma ci-dessous montre la réponse obtenue
selon la densité d'armatures, avec à droite une seule armature,
au milieu trois armatures relativement espacées et à droite trois
armatures rapprochées.

Figure 11 : Réponse en fonction de la
densité d'armature
Concernant l'utilisation de l'appareil, il existe
principalement deux modes de mesures :
- La détection par lignes
- La détection par fenêtres
La première méthode consiste à
déplacer l'appareil perpendiculairement aux armatures que l'on souhaite
détecter.
Sens de la détection linéaire


Aciers détectés
Aciers non détectés
Figure 12 : Principe de la détection linéaire
La détection par lignes est très
intéressante pour les éléments longs sur lesquels on
souhaite avoir une vision globale du ferraillage. En effet, les
détections peuvent aller jusqu'à quarante mètres de
longueur. Ce type de mesure permet d'obtenir les variations d'espacement des
armatures ainsi que les enrobages correspondants.
La seconde méthode consiste à détecter
les aciers sur un carré de soixante centimètres de coté.
Cela par pallier de quinze centimètres, d'abord dans le sens transversal
puis dans le sens longitudinal.
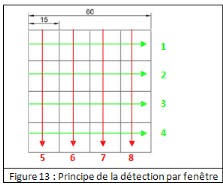
Cette méthode permet d'une part d'estimer le
diamètre des aciers ainsi que les enrobages, et d'autre part de voir
localement comment les aciers ont été assemblés. Cela
trouve toute son utilité pour voir
le clavetage d'une poutre à un poteau par exemple.
Le travail d'ingénierie consiste, après
extraction des données sur un ordinateur grâce à un
logiciel, à exploiter les mesures effectuées sur site. Cette
étape varie selon le type de mesures effectuées.
Pour la détection par ligne, l'exploitation des
données donne un résultat similaire au suivant :

Figure 14 : Résultat de la détection
linéaire
Pour la détection par image, on obtient des
résultats semblables aux suivants :

Figure 15 : Résultat de la détection par
fenêtre
Sur l'image ci-dessus on peut voir des aciers plus
foncés que d'autres, cela signifie qu'ils sont plus proches de
l'appareil, donc un enrobage moindre.
Il y a donc deux lits d'armatures, la nappe
supérieure (en foncée) et la nappe inférieure (en claire).
De plus, on peut voir l'espacement des armatures dans les deux
sens, leur diamètre ainsi que l'épaisseur d'enrobage des
aciers.

Figure 16 : Détection du ferraillage d'un balcon
1.2.1.3. L'AUSCULTATION
SONIQUE :
L'auscultation sonique permet de mesurer le temps de
propagation d'un train d'ondes sonores entre deux points. Une partie de
l'auscultateur, le transducteur, produit des ultrasons.
Grâce aux propriétés
piézoélectriques des matériaux, l'énergie
électrique émise est transformée en énergie
mécanique ultrasonore. L'appareil mesure le temps nécessaire
à l'onde pour atteindre le récepteur qui la convertit en
signal électrique. Connaissant la distance de l'émetteur
possible de connaitre la vitesse de propagation de l'onde dans le milieu.
Ce procédé permet de caractériser
l'homogénéité physique du béton ainsi que son
état d'altération. En effet, cette méthode de diagnostic
permet entre autres de localiser des défauts, des vides ou autres
malfaçons dans le béton.
Le principe est que les lames d'air emprisonnées dans
le matériau transmettent très peu l'énergie des ultrasons,
ainsi, la vitesse mesurée sur l'ensemble de l'élément sera
plus faible que pour un béton homogène.
Il existe principalement deux types de mesures à
effectuer sur site :
-Les mesures en transparence : cette méthode consiste
à déterminer le temps de propagation des ondes sonores
longitudinales à travers un élément. Pour procéder
à ce type de mesure, il faut placer l'émetteur et le
récepteur sur les deux faces opposées de l'élément
à ausculter.
-Les mesures de surface : cette méthode s'effectue
principalement lorsqu'une seule des faces de l'élément
est accessible lors des investigations.
Elle peut aussi être utilisée pour
déterminer la profondeur d'une fissure ou bien la présence de
couches multiples dans un même élément.
Pour réaliser cette mesure, il faut placer
l'émetteur et le récepteur sur la même face plane de
l'élément à ausculter.
L'émetteur reste sur un même point, tandis que le
récepteur se déplace en effectuant à chaque fois une
mesure.
Il est à noter qu'il existe une règle a
été conçue par le CEBTP afin d'avoir des espacements
donnés et ne pas faire des erreurs sur les distances mesurées.
Le tableau suivant donne les résultats d'essais obtenus
par le CEBTP sur l'auscultation sonique des bétons :
Vitesse de propagation du son
|
Qualité estimée du
béton
|
V > 4000 m/s
|
le béton est de bonne qualité
ethomogène
|
3500 < V < 4000 m/s
|
le béton est de qualité moyenne
|
3000 < V < 3500 m/s
|
le béton est de qualité
médiocre
|
V < 3000 m/s
|
le béton est de mauvaise qualité
|

Figure 17 : Mesure par transparence
1.2.1.4.
SCLÉROMÈTRE :
Le principe de l'essai sclérométrique repose sur
la corrélation entre la dureté d'un matériau et sa
résistance à la compression.
Pour déterminer la dureté du béton, une
bille d'acier est projetée sur une sonde en contact avec l'ouvrage
à inspecter. Lors de son rebond, la bille entraine un index coulissant
sur une règle de mesure. Plus le rebond sera important, plus le
matériau sera dur.
Il convient de réaliser un certain nombre d'essais sur
l'élément à ausculter, vingt-sept dans la norme actuelle,
afin d'obtenir un résultat cohérent.
L'indice sclérométrique Is de
l'élément diagnostiqué est la médiane de 27
mesures effectuées sur la zone d'ouvrage testé. Par report
de l'indice sclérométrique sur un abaque,
considéré. Il est important de savoir que différents
paramètres peuvent influer sur les résultats, tels que
l'on obtient la résistance à la compression estimée
de l'élément l'inclinaison du scléromètre ou
encore l'homogénéité du béton.
Il peut être intéressant de coupler ces
résultats avec des essais de résistance à la compression
sur des prélèvements de la zone étudiée.

Figure 18 : Scléromètre
1.2.2. INVESTIGATIONS
DESTRUCTIVES
Les investigations destructives dans les structures en
béton armé peuvent prendre plusieurs formes.
Soit on y a recours pour effectuer un
prélèvement de matériau pour connaitre ses
caractéristiques géométriques, mécaniques et
chimiques, soit c'est pour avoir accès à des
éléments interne ou sous- jacent à la structure.
Cela permet aussi de connaitre leur état
d'altération en profondeur ainsi que l'ampleur des pathologies.
Parmi les investigations destructives, on recense
principalement les techniques suivantes :

Figure 19 : Schéma des investigations destructives
1.2.2.1. CAROTTAGE
D'ÉLÉMENTS EN BÉTON ARMÉ
Le recours au carottage du béton armé peut avoir
plusieurs objectifs.
-Tout d'abord dans un dallage afin de permettre la
réalisation d'essais géotechniques sur le sol en place tel que
des pénétromètres dynamiques ou des tarières. Ceci
pour caractériser le sol sous la structure dans le cadre d'une
rénovation ou d'une restructuration de l'ouvrage.
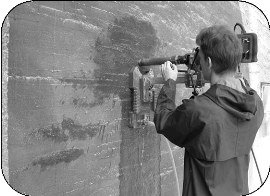
-Afin de pouvoir déterminer les
caractéristiques chimiques et mécaniques d'un
élément en béton de la structure, en effectuant des essais
de compressions sur les carottes prélevées, mais aussi des
analyses chimiques et microscopiques afin de déterminer les
différents constituants et leur quantité. Cela permet de
déterminer quel type de ciment a été utilisé ainsi
que le rapport E/C.
-Déterminer les caractéristiques des
couches constituantes de l'élément (épaisseur
du revêtement, de la chape, du béton,...) La norme NF EN
13791 de septembre 2007 indique deux méthodes pour «
l'évaluation de la résistance à la compression sur site
des structures et des éléments préfabriqués en
béton».
La méthode à utiliser varie selon le nombre
d'éléments carottés dans la structure concernée,
mais dans tous les cas, elle permet d'estimer la classe de résistance du
béton
Cette méthode nécessite le recours à une
carotteuse et il peut être nécessaire de déterminer
préalablement le ferraillage de l'élément afin
d'éviter d'avoir des aciers dans la carotte.
Ceci pour deux raisons : d'une part, cela fragilise plus la
structure si les aciers prélevés ont un rôle important,
d'autre part les résistances à la compression obtenue, sur une
carotte dans laquelle il y a présence d'acier, sont faussées.
Pour les mêmes raisons, il faut éviter de
carotter un élément sur une fissure.

Figure 20 : Carotte prélevée
1.2.2.2.
PRÉLÈVEMENTS D'ACIERS :
Le prélèvement d'acier peut s'avérer
utile notamment lorsqu'un recalcul d'une structure est demandé.
Dans ce cas, il est important de connaitre les aciers
présents dans un ouvrage. Ainsi, en prélevant des aciers, cela
permet de déterminer leur type, que ce soit des aciers Haute
Adhérence, lisse, TOR, etc. mais aussi leurs caractéristiques
mécaniques telle que la limite d'élasticité de l'armature.
Tous ces éléments sont nécessaires afin
de pouvoir déterminer quelles sont les charges pouvant s'appliquer sur
l'élément et s'il est nécessaire de prévoir de
renforcer la structure soit avec des tissus de fibre de carbone ou par ajout
d'armatures afin de pouvoir répondre aux besoins du client ou des
utilisateurs.

Figure 21 : Prélèvement d'aciers
Le prélèvement d'aciers peut se faire par
tronçonnage de l'armature, après l'avoir préalablement
dégagé du béton adjacent. Il est préférable
de le faire dans des zones saines pour ne pas risquer de fragiliser encore plus
la structure à cet endroit.
Il peut parfois s'avérer utile de prélever
localement des armatures dans des zones touchées par des pathologies,
telle que la corrosion des armatures afin de pouvoir déterminer son
avancement ainsi que la section restante d'acier pouvant être
exploité afin de déterminer les quantités d'armatures
nécessaires à rajouter pour redonner à
l'élément au minimum sa section d'acier initiale.
1.2.2.3. POTENTIEL DE
CORROSION :
La mesure du potentiel de corrosion ne peut se faire que si le
ferraillage est continu et s'il n'y a pas de revêtement de surface
pouvant agir comme isolant. Si le ferraillage est discontinu, il est toujours
possible de mettre en place des pontages électriques.
Le principe de la mesure du potentiel de corrosion est de
mettre à nu une armature puis de la connecter à une borne d'un
millivoltmètre à haute impédance. Une électrode de
référence est placée sur le parement, elle-même
reliée à une autre borne du millivoltmètre.
Elle est dite de référence, car elle a un
potentiel constant du à un équilibre électrochimique. Il
est important de veiller à ce que la jonction entre le béton et
l'électrode soit humide afin d'établir une conduction
électrique.
Cela permet de diminuer la résistance entre
l'électrode de référence et le béton ainsi que le
potentiel de jonction entre interstitielle du béton
l'électrolyte contenu dans l'électrode de
référence et la solution
Une fois les branchements faits, il faut réaliser les
mesures des potentiels des zones auscultées en déplaçant
l'électrode de référence.
La norme ASTM C876-91 fait une corrélation entre le
potentiel mesuré et la probabilité de corrosion. Ainsi, en
utilisant une électrode Cu/CuSO4 on a la relation suivante :
-Si E > - 200 mV alors la corrosion est peu probable
(probabilité inférieure à 10%)
-Si -350 < E < -200 mV alors la corrosion est possible
(probabilité de cinquante pour cent)
-Si E < - 350 mV alors la corrosion est très
probable (probabilité de 50 à 90%)

Figure 22 : Principe du potentiel de corrosion
Cependant, il est important de noter le fait que
différents paramètres peuvent influer sur les résultats
obtenus, tels que :
-L'hygrométrie de surface, il peut y avoir une
diminution de 100 mV entre une mesure sur surface humide et une mesure quand
c'est sec
-Pour des milieux agressifs comme la présence de
chlorures, la conductivité est augmentée et les potentiels
sont plus négatifs
-Lorsque le béton est carbonaté, les potentiels
sont plus positifs.
En effectuant ainsi des mesures en de nombreux points d'un
élément, il est possible d'effectuer une cartographie
complète de la probabilité de corrosion.

Figure 23 : Cartographie de potentiel de corrosion

Figure 24 : Mesure du potentiel de corrosion
1.2.2.4. TEST À
LA CARBONATATION :
Le principe du test à la carbonatation repose sur le
fait que le pH du béton carbonaté est plus faible que celui du
béton sain. Pour déterminer la zone carbonatée, il
est généralement utilisé un indicateur coloré
tel que la phénolphtaléine.
La phénolphtaléine est un composé
organique de formule C20H14O4. L'utilité de ce composé est qu'il
change de couleur selon le pH de l'élément avec lequel
il entre en contact.
Il fait partie des indicateurs de pH ou indicateur
coloré. Ce changement de couleur est dû à une modification
de la structure chimique de la molécule lors du passage de la forme
protonée (milieu acide) à la forme déprotonnée
(milieu basique).
La couleur que prend la phénolphtaléine
dépend du pH. Elle sera rose pour un pH compris entre 8,2 et 12 et
incolore au-delà et au-deçà de cette zone de virage.
Cet essai se réalise généralement sur une
coupe fraiche de béton. Il faut y pulvériser la solution de
phénolphtaléine, si la phénolphtaléine ne
réagit pas, il faut approfondir la coupe dans le béton par
paliers d'un centimètre et répéter les étapes
précédentes jusqu'à ce que la
phénolphtaléine vire au rose.
Puis il est nécessaire de mesurer l'épaisseur
entre le parement extérieur et la zone à laquelle commence la
coloration du béton. Cela nous donne la profondeur de carbonatation du
béton de cette zone.
Il peut être utile de réaliser cette mesure en
différents points d'un élément afin de pouvoir
cartographier les profondeurs de carbonatation associées.
Il peut s'avérer intéressant de coupler les
mesures de profondeur de carbonatation avec les mesures d'enrobages
données par exemple avec un pachomètre de type Ferroscan. En
effectuant un certain nombre de mesures, il est possible d'obtenir une courbe
du type :
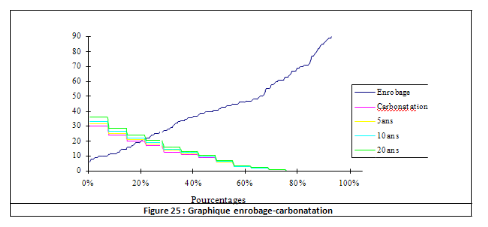
L'intersection de la courbe d'enrobage (courbe bleu
foncé) avec celle de carbonatation (courbe rose) donne le pourcentage
des armatures qui ne sont plus protégées.
Il est aussi possible de faire des prévisions sur les
évolutions pour les années à venir (courbes jaune, bleu
clair et verte). En effet, l'évolution de la carbonatation suit une
évolution en fonction du temps du type avt, avec « a » un
facteur propre à chaque béton. En connaissant l'âge du
bâtiment ainsi que la profondeur de carbonatation à l'instant t,
il est facile de déterminer le facteur « a ».
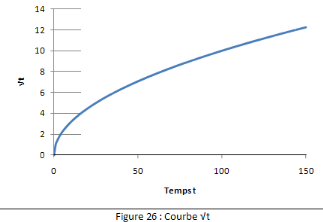

Figure 27 : Carbonatation sur carotte
1.3. CONCLUSION SUR LE
DIAGNOSTIC :
Dans cette partie nous avons vu l'importance du diagnostic
dans l'opération de réhabilitation d'un ouvrage ainsi que des
différents moyens disponibles pour le réaliser.
C'est l'étape clé qui permet de
déterminer les types de pathologies dont souffre l'ouvrage ainsi que
leur ampleur. Cela permet aussi de faire des prévisions quant à
l'évolution de ces troubles.
Mais c'est avant toute chose, l'étape qui va permettre
de mettre en oeuvre la méthode de réparation la plus
adaptée. Cela permet aussi d'évaluer la cause de ces
problèmes.
Cette cause peut être tout simplement le vieillissement
naturel de la structure, mais cela peut aussi être à cause de
l'environnement alentours. Afin de rendre les réparations
pérennes, il est nécessaire de mettre en oeuvre des
travaux de protection adaptées, mais aussi de travailler sur
l'origine du problème afin d'éviter l'apparition rapide de
nouvelles pathologies semblables
2. RAPPORT DE
DIAGNOSTIC :
Le rapport de diagnostic présente l'ensemble des
résultats et leur interprétation, mais doit être
compréhensible par un non initié.
Il comprend :
· l'identification de la structure, le nom du
demandeur,
· l'identification du laboratoire (ou de
l'ingénieur) chargé de l'étude, la date,
· une brève description de la structure,
· le rappel des objectifs de l'étude,
· la liste des documents consultés,
· les résultats de l'inspection
détaillée,
· les résultats des essais in situ et de
laboratoire,
· une discussion sur l'origine des désordres,
leur étendue, leur évolution probable, et leur incidence sur la
sécurité,
· des conclusions claires sur les désordres
constatés et des propositions éventuelles de complément
d'étude,
· une liste des priorités des
réparations et travaux à effectuer,
· des recommandations relatives aux méthodes
de réparation les plus adaptées.
3. CONTRAINTES ET
EXIGENCES
Ce chapitre dresse une liste non exhaustive de critères
pouvant guider l'ingénieur, qui doit préconiser une
réhabilitation du béton armé dégradé par la
corrosion. En effet, le choix de la méthode ou des produits de
réparation est soumis à des contraintes et exigences qui sont
liées au type de réhabilitation, ainsi qu'à la nature et
à l'environnement de l'ouvrage à réparer.
3.1CONTRAINTES
STRUCTURELLES
L'une des conséquences de la corrosion des armatures du
béton armé est un affaiblissement de la structure.
L'ingénieur chargé d'étudier la réparation doit
toujours avoir présent à l'esprit le respect de la
sécurité de service de l'ouvrage, donc de sa stabilité. Il
doit, avant même d'envisager des solutions de traitement de cette
corrosion, estimer l'état général de la structure et en
comprendre le fonctionnement.
Il doit prendre en compte, comme pour un projet nouveau, les
contraintes de service d'exploitation, de charges et d'environnement de la
structure.
Une visite approfondie de la structure, permettra de
déceler les indices révélateurs de la perte de
résistance de la structure, tels que les fissures, les écaillages
et écrasements locaux de béton etc.
Quelquefois cette inspection révélera que la
corrosion est d'abord due à un dysfonctionnement de la structure et
qu'elle n'est en fait qu'un facteur aggravant.
Les structures visitées sont en général
en service et soumises à des chargements, leur âge et leur
état général permettent à l'ingénieur
d'apprécier les qualités de la conception d'origine et leur
fonctionnement structurel.
Il ne convient pas de modifier systématiquement les
structures, quand leur comportement est satisfaisant. Mais le traitement de la
corrosion qui sera envisagé respectera en général le
projet, en lui redonnant ses caractéristiques originelles.
3.1.1.2. Pertes de section
des armatures
La corrosion métallique est une dissolution, donc une
perte de section des armatures. Le facteur de sécurité pris en
compte dans les calculs de dimensionnement, s'en trouve réduit.
L'ingénieur chargé de la réhabilitation de la structure
devra estimer ces pertes.
Cette tâche n'est pas facile ; l'estimation se fait
généralement de façon statistique après une
série de mesures des diamètres résiduels effectuées
dans des sondages.
Pour les visites d'évaluation, il est très rare
de disposer des moyens d'accès utilisés pour l'exécution
du chantier.
Les sondages d'évaluation sont
généralement réalisés dans des zones d'accès
faciles, où les sections ne sont pas toujours les plus
sollicitées. Il faut donc se garder la possibilité
financière de faire exécuter de nouveaux sondages dans les
sections les plus sollicitées, et prévoir un éventuel
renforcement d'armature.
Si la perte de section est supérieure à 10%, il
convient de renforcer les armatures. Il faut, bien entendu, s'assurer que les
charges de services n'ont pas évolué, et que
réglementairement les armatures en place correspondent aux
sollicitations.
L'apport de nouvelles armatures peut alors se faire dans la
masse, après démolition des zones et reconstitution du
béton, soit par un apport externe enrobé dans un
béton projeté connecté à la structure, soit par
des armatures additionnelles collées sous forme de plaques de tôle
ou de tissus de carbone.
3.1.1.3. Ancrage et
entraînement des armatures
Les oxydes de fer forment autour des armatures une gaine qui,
à partir d'une certaine importance, peut diminuer leur
adhérence au béton.
Cette perte d'entraînement des barres conduit alors
à une perte générale de la résistance de la
structure. La mobilisation des efforts par les barres en traction peut
être modifiée par un glissement relatif de l'ancrage lors de
sollicitations, la mobilisation des efforts se fait alors avec de plus grandes
déformations.
Il faut alors quelquefois dégarnir les enrobages de
béton altérés pour les reconstituer, ces opérations
libèrent totalement les ancrages de barres. Quand ils ne sont pas
accompagnés d'un étaiement soigné de la
structure avant le repiquage, ces dégarnissages modifient
profondément son fonctionnement, et peuvent présenter un
réel danger lors de l'exécution.
3.1.1. Respect du
fonctionnement de la structure en l'état
La corrosion des armatures du béton armé peut
entraîner un appauvrissement des capacités portantes de la
structure. Cette perte de résistance se manifeste par des
altérations des matériaux qui sont les suivantes.
3.1.1.1. Pertes de section
du béton.
Le foisonnement des oxydes de fer développe des
contraintes qui peuvent endommager le béton, allant jusqu'à
l'éclater. Il en résulte que les sections résistantes de
béton diminuent, les contraintes s'organisent, et transitent par les
zones adjacentes. La simple reconstitution de ces sections par un produit de
ragréage, n'est pas toujours suffisante pour retrouver le fonctionnement
originel de la structure.
Il faudra quelquefois avoir recours à des techniques de
vérinage pour soulager la structure, avant de reconstituer la section
altérée. Cela peut être le cas dans des zones
comprimées, la nature des produits de reconstitution devront alors tenir
compte de la composition du béton en place et de son module
d'élasticité.
La forme de la découpe pour curer les zones
altérées devra prendre en compte l'angle des joints de
bétonnage de la zone à reconstituer, pour que les contraintes
transitent correctement lors du rechargement.
3.1.2. Respect des
matériaux en place
Les traitements de corrosion des armatures du béton
armé sont réalisés soit par des apports de
matériaux en surface, soit par des reconstitutions de forme après
purge, soit par des procédés agissant en profondeur.
Le choix des techniques doit être fait en
considérant les matériaux constitutifs de la structure, tant sur
un plan physique que chimique. Ainsi, le traitement de la corrosion des
armatures ne doit pas entraîner une dégradation du béton en
place, qui serait due à l'incompatibilité de deux produits en
présence.
L'action des produits de protection des armatures ne doit pas
engendrer, vis-à- vis du béton, des actions secondaires
préjudiciables au bon fonctionnement de la structure.
Avant la préconisation du traitement,
l'ingénieur s'assurera que la solution choisie est en adéquation
avec les conditions de fonctionnement et le milieu ambiant de la structure.
Les effets d'un traitement peuvent être de trois
types.
3.1.2.1. Les actions
irréversibles sur la nature des matériaux
L'application de produits peut changer de façon
irréversible la structure interne ou superficielle des matériaux
traités. Certains produits de surface bloquent totalement les
porosités du béton et « piègent »
l'humidité dans les structures, ils les rendent ainsi plus sensibles aux
cycles gel / dégel.
Des produits d'imprégnations qui créent des
minéraux peuvent modifier l'équilibre chimique du béton en
place ou le module d'élasticité des zones fortement
imprégnées en surface.
D'autres produits peuvent empêcher à jamais la
pose de revêtements ultérieurs, etc.
3.1.2.2. Les effets
secondaires après traitement
Certains traitements peuvent avoir des effets secondaires,
après leur application sur certains bétons. Par exemple, les
traitements électrochimiques qui augmentent le pH du béton
d'enrobage, peuvent déclencher des réactions d'alcali-granulats.
De même, l'utilisation de produit à effet
gonflant (à long terme) peut créer des contraintes importantes,
pouvant aller jusqu'à des fissurations ou des éclatements.
3.1.2.3. Les
conséquence du choix des matériaux de remplacement
Le choix des matériaux de remplacement ou de
substitution des zones dégradées doit donc tenir compte de
l'état de vieillissement des matériaux en place. Si certaines
parties doivent être partiellement reconstruites, on devra s'assurer de
la bonne compatibilité des matériaux entre eux.
Certains produits, utilisés en ragréages,
faciles d'emploi, rapides, et compatibles avec les armatures, ne sont pas
toujours compatibles avec les bétons adjacents. Cela peut être le
cas des produits dont le liant est à base de ciment alumineux au contact
avec des bétons à base de ciment Portland CEM I.
3.2. EXIGENCES A PRENDRE EN
COMPTE POUR LES REPARATIONS
L'objet principal d'une réhabilitation est
d'arrêter ou d'éviter la corrosion des armatures du béton
armé.
Mais le traitement choisi doit aussi répondre aux
attentes du client qui peuvent être d'ordre fonctionnel ou
esthétique, avec le respect du caractère original ou historique
de la structure.
Ces exigences sont traitées au coup par coup. En
général, le cahier des clauses techniques particulières
fixera les critères de réalisation. Il est recommandé de
demander à l'entreprise chargée du chantier, des planches
d'essais pour valider les traitements à mettre en oeuvre.
Il peut aussi être demandé de réaliser in
situ, une partie de structure qui servira d'essai de convenance.
Cette dernière procédure offre l'avantage de
pouvoir valider en une seule fois le matériel, les matériaux et
la mise en oeuvre de la « planche » de convenance. Ces validations
peuvent concerner des exigences :
· de forme,
· de couleur,
· d'aspect,
· de respect de l'environnement.
4. DURABILITE
La durabilité d'une réhabilitation correspond au
fait qu'elle ne doit pas être renouvelée avant un certain
délai, qui est précisé dans une garantie. Cette
durabilité dépend de la pertinence du choix de la technique
retenue, de sa mise en oeuvre et des sollicitations après traitement.
La pérennité de l'ouvrage correspond à
son aptitude à remplir les fonctions prévues (mécaniques,
esthétiques, etc.). Elle peut être allongée, après
traitement de réhabilitation, quand les parements sont de plus
revêtus d'un écran protecteur contre les agents agressifs.
La notion de garantie est une notion contractuelle, dont la
durée est liée au traitement choisi, pour une structure dans des
conditions d'exploitation données. La garantie prend effet après
la réception des travaux.
La réception des travaux est un acte de fin de travaux
qui atteste que la réalisation est conforme au contrat. Avant cette
réception l'efficacité du traitement doit être
vérifiée.
4.1. Les contrôle du
résultat des traitements
Certaines vérifications sont simples, comme par exemple
les couleurs, les formes, la rugosité etc. D'autres demandent des
analyses beaucoup plus fines qui sont précisées dans le
chapitre 2. Il faut souvent faire appel à des laboratoires
spécialisés pour effectuer ces contrôles.
4.2. Le contrôle des
revêtements de protection des bétons
Les produits de protection du béton ne sont pas
toujours exigés, bien qu'ils constituent une barrière contre les
agents agressifs contenus dans le milieu environnant.
La vérification des revêtements se limite
généralement à des contrôles de leur
adhérence au support, de leur aspect et de leur épaisseur.
Chapitre :03
1. RÉPARATION D'UN
OUVRAGE EN BÉTON ARMÉ
La réparation d'un ouvrage est la deuxième
étape dans le processus de réhabilitation d'ouvrages en
béton armé. C'est l'étape nécessaire pour redonner
d'une part les sections d'origine de l'acier et du béton, mais aussi
pour rétablir les caractéristiques mécaniques des
différents éléments concernés. C'est-à-dire
de redonner la possibilité à la structure de reprendre au mieux
les efforts qui lui sont appliqués.
Il existe principalement deux méthodes de
réparation du béton armé. Il y a la méthode
traditionnelle du ragréage ainsi que la technique du béton
projeté.
Cependant, une troisième méthode, plus
récente, commence à se développer : l'utilisation des
Tissus de Fibres de Carbone (TFC).

Figure 28: Schéma de la réparation d'ouvrages en
béton armé
Ces différentes méthodes sont décrites
dans la suite.
1.1. LE RAGRÉAGE
La méthode de ragréage est
généralement utilisée lorsque la technique
traditionnelle de réparation des bétons. à reprendre
sont relativement faibles.
Ceci s'explique par le fait que ce type de réparation
n'a besoin que de très peu de matériel, mais est assez longue et
nécessite beaucoup de main-d'oeuvre.
Lorsque les surfaces à importantes, on
privilégiera plutôt le béton projeté, plus rapide,
mais nécessitant une part matériel. réparer sont plus
importantes, on privilégiera plutôt le béton
projeté, plus rapide, mais nécessitant une part plus importante
de matériel.
La préparation de surface est une étape
très importante pour la pérennité des réparations,
elle doit être effectuée avec soins. Il s'agit dans un premier
temps d'éliminer toutes les zones présentant une faible
cohésion sur l'élément à reprendre.
C'est-à-dire qu'il faut vérifier chaque zone,
afin de voir s'il n'y a pas de décollement du béton, de la
fissuration apparente, des épaufrures, etc. Les zones de
ségrégation doivent elles aussi être
éliminées.
S'il y a présence d'un phénomène de
corrosion des armatures, il est nécessaire de dégager les aciers
corrodés jusqu'à ce qu'une zone saine apparaisse. Pour être
sûr de pouvoir effectuer une bonne réparation, il est d'usage
d'obtenir un dégagement comme le montre le schéma suivant :

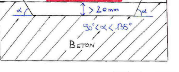
Figure 29 : Dégagement des armatures
Une fois les armatures corrodées
dégagées, il faut les nettoyer afin d'enlever toute trace
de corrosion.
Dans certains cas, la perte de section de l'acier peut
s'avérer être très élevée, il est alors
nécessaire de remplacer l'armature, soit par découpage de
la zone atteinte et soudage d'une armature équivalente, soit en
scellant une nouvelle armature dans le parement.
Il est important qu'après cette opération, la
section d'armatures soit au moins égale à celle présente
initialement dans l'élément de la structure concernée.
Afin de limiter les risques d'apparition de la corrosion, les
armatures doivent être passivées par application d'un produit
convenablement choisi. Cette application peut se méthodes (par
brossage, par application au pinceau, etc.)
Une fois les étapes précédentes
réalisées, il est possible de commencer le ragréage. Il
s'agit de reconstituer manuellement l'enrobage de béton à l'aide
d'un mortier de réparation convenablement choisi par une entreprise
possédant les compétences nécessaires. Il peut être
intéressant de choisir de mettre des inhibiteurs de corrosion
directement dans la formulation de ce mortier afin de limiter au maximum
l'apparition de corrosion dans les zones réparées.
Dans tous les cas le mortier utilisé doit avoir les
caractéristiques suivantes :
- Tenue verticale sans coffrage
- Montée en résistance rapide et de
résistance mécanique supérieure au béton support
- D'adhérence supérieure ou égale
à la cohésion du support
- D'imperméabilité à l'eau et aux agents
agressifs
- De coefficient de dilatation thermique et de module
d'élasticité équivalente au béton support
- De bonne protection des aciers
- Les produits doivent être conformes à la norme
NF P 18-840 ou être admis à la marque « NF Produits
spéciaux destinés aux constructions en béton hydraulique
».
1.2. LE BÉTON
PROJETÉ
La méthode du béton projeté est une
alternative au ragréage. Elle est généralement
utilisée lorsque les surfaces de béton à reprendre sont
assez importantes. Ceci s'explique par le fait que ce type de réparation
est relativement rapide à mettre en oeuvre, mais
nécessite du matériel particulier.
Lorsque les surfaces à réparer sont assez
faibles, on privilégiera plutôt le ragréage, plus
adapté aux petites surfaces.
1.2.1. HISTORIQUE DE LA
MÉTHODE
C'est en 1907 qu'apparut la première machine à
projeter, crée par l'américain Carl Akeley. Et c'est dès
1911 que son utilité s'est avérée dans le domaine du
génie civil, notamment pour la stabilisation des berges de la
tranchée « Culebra cut » du canal de Panama.

Figure 30 : Machine à sas de première
génération
En France, la méthode du béton projeté se
développa à la fin de la Première Guerre mondiale afin de
réparer les ouvrages d'art et des habitations endommagés par les
combats. Entre les deux guerres mondiales, le béton projeté
été couramment utilisé lors de gros projets.
Cependant, après la Deuxième Guerre mondiale
le savoir-faire des entreprises avait pratiquement disparu. Seules la SNCF et
EDF savaient que cette technique existait et continuaient de l'employer. Puis
EDF a entrepris des recherches afin d'améliorer la composition des
mélanges en notant les courbes granulaires de chaque
mélange afin de les comparer par la suite avec des essais sur
béton durci. Cela a permis à EDF de tracer des fuseaux optimaux
à l'intérieur desquels les courbes granulaires des
mélanges à projeter devaient se situer.
Ces fuseaux sont encore utilisés aujourd'hui.
1.2.2. TECHNIQUE DE
PROJECTION
Il existe principalement deux techniques de projection du
béton. Elles se différencient par rapport à l'emplacement
de l'introduction de l'eau de gâchage dans le matériau.
Il y a tout d'abord la méthode de projection par voie
humide, le béton gâché est transporté jusqu'à
la lance soit par pompage soit par de l'air comprimé. I
il y a ensuite la méthode de projection par voie
sèche pour laquelle le mélange de ciment et de granulats, non
additionné d'eau au moment du malaxage, est propulsé par de l'air
comprimé, l'eau étant ajoutée au dernier moment, en bout
de lance.
Le choix de la technique à utiliser dépend de
différents paramètres tels que la nature des matériaux
utilisés, de la nature des travaux à effectuer ou encore des
habitudes de l'entreprise.
|
|
Figure 31 : Béton projeté par voie
sèche
|
Figure 32 : Béton projeté par voie
humide
|
Le principe de la projection reste le même selon la
méthode employée. Il consiste à :
- Malaxer, homogénéiser les matériaux
à l'état sec ou humide
- Les transporter par canalisation, rigides ou souples,
grâce à des pompes mécaniques ou à de l'air
comprimé
- À projeter plus ou moins violemment, grâce
à de l'air comprimé ; le matériau sur les supports
à revêtir.
Cependant, selon la méthode utilisée les
résultats vont présenter quelques différences. Par voie
sèche, on obtiendra une résistance plus élevée que
par voie humide du fait du faible rapport E/C. Mais on aura une capacité
de production plus limitée, un dégagement de poussière
plus important, mais surtout un risque de détérioration d'un
support fragile.
Dans tous les cas, cette surépaisseur de béton
est moins poreuse, plus durable et peu sensible aux attaques chimiques. Le
béton projeté n'étant pas encore carbonaté, il
stoppe l'évolution de la carbonatation, le temps d'être
lui-même complètement carbonaté. Il empêche
également la pénétration d'humidité grâce
à sa faible porosité, ce qui protège les armatures de l
corrosion.
De plus, il est possible d'ajouter des inhibiteurs de
corrosion dans la formulation du béton, ce qui permet de rendre plus
pérennes les réparations effectuées.
1.2.3. MODE
OPÉRATOIRE
Tout comme pour la méthode de réparation par
ragréage, il est nécessaire d'effectuer une préparation de
la surface avec soins. Il s'agit dans un premier temps d'éliminer toutes
les zones présentant une faible cohésion sur
l'élément à reprendre. C'est-à-dire qu'il faut
vérifier chaque zone afin de voir s'il n'y a pas de décollement
du béton, de la fissuration du béton, des épaufrures, etc.
Les zones de ségrégation sont aussi à éliminer.
S'il y a présence de phénomène de
corrosion des armatures, il est nécessaire de dégager les aciers
corrodés jusqu'à ce qu'une zone saine apparaisse. Pour être
sûr de pouvoir effectuer une bonne réparation, il est d'usage
d'obtenir comme dans le cas du ragréage l'espacement suivant :








Figure 33 : Dégagement des armatures
Une fois les armatures corrodées
dégagées, il s'agit de les nettoyer afin d'enlever toute la
corrosion. Dans certains cas, la perte de section de l'acier étant
très élevée, il est nécessaire de remplacer
l'armature, soit par découpage de la zone atteinte et soudage d'une
armature équivalente, soit en scellant une nouvelle armature dans le
parement. Il est important qu'après cette opération, la
section d'armatures soit au moins égale à celle présente
initialement dans l'élément de la structure concernée
Dans le cadre de béton projeté par voie humide,
il est possible d'appliquer un passivant sur les armatures
réparées afin de limiter les risques d'apparition de la
corrosion.
Cette application peut se faire par différentes
méthodes (par brossage, par application au pinceau, etc.). Ceci
n'est pas possible lorsque l'on projette le béton par voie
sèche, car arrivant plus rapidement sur l'élément
concerné, la protection serait abimée et ne remplirait plus ses
fonctions.
1.2.4 MATÉRIAUX
UTILISÉS
Dans le cadre de la réparation d'ouvrages en
béton armé, le béton ou le mortier utilisé doit
avoir les caractéristiques suivantes :
- Tenue verticale sans coffrage
- Montée en résistance rapide et de
résistance mécanique supérieure au béton support
- D'adhérence supérieure ou égale
à la cohésion du support
- D'imperméabilité à l'eau et aux agents
agressifs
- De coefficient de dilatation thermique et de module
d'élasticité équivalente au béton support
- De bonne protection des aciers
- Les produits doivent être conformes à la norme
NF P 18-840 ou être admis à la marque « NF Produits
spéciaux destinés aux constructions en béton hydraulique
».

Figure 34 : Projection de béton
|
Remplacement du béton par ragréage avec
passivant
|
Remplacement du béton par béton
projeté
|
Avantages
|
Petites destructions localisées de béton, pas de
risque de déstabilisation de la structure.
Adapté aux petites surfaces.
|
Mise en place du mortier de réparation
plus rapide.
Béton moins poreux, donc moins sensible aux
chlorures.
Adapté aux surfaces importantes.
|
Inconvénients
|
Beaucoup de main d'oeuvre nécessaire pour purger,
passiver, ragréer.
Délais plus long.
Bien dégager tous les aciers corrodés et les
passiver sous peine de corrosion rapide.
Nécessite un revêtement
imperméabilisant.
|
Risque de déstabilisation suite à une
enlevée importante du béton.
Bien dégager tous les aciers corrodés et les
passiver sous peine de corrosion rapide.
Surcharges possibles => recalcul de la structure.
Pas adapté aux petites surfaces.
|
Contraintes phase travaux
|
Bien éliminer toutes les traces de corrosion des aciers
et bien les passiver sur l'ensemble de la zone de désordre et non pas
seulement au droit de l'épaufrure sous peine de corrosion
accentuée.
|
Bien éliminer toutes les traces de corrosion des aciers
et bien les passiver sur l'ensemble de la zone de désordre et non pas
seulement au droit de l'épaufrure sous peine de corrosion
accentuée.
|
Durée de vie estimée
|
Temps de carbonatation/détérioration du nouveau
béton.
Limité par rapport à la présence de
chlorures.
Améliorée si protection
complémentaire.
|
Temps de carbonatation/détérioration du nouveau
béton.
Limité par rapport à la présence de
chlorures.
Améliorée si protection
complémentaire.
|
1.3. TISSUS DE FIBRES DE
CARBONE
Le renforcement par tissus de fibres de carbone peut se faire
sur différents types de structures et sur les différents
matériaux usuels de la construction tels que le béton armé
ou non, le bois, ou les structures métalliques.
Ce matériau est dit composite, car il s'emploie
généralement avec une résine. Il présente beaucoup
d'avantages, notamment liés à ses fortes caractéristiques
mécaniques pour une masse volumique relativement faible.
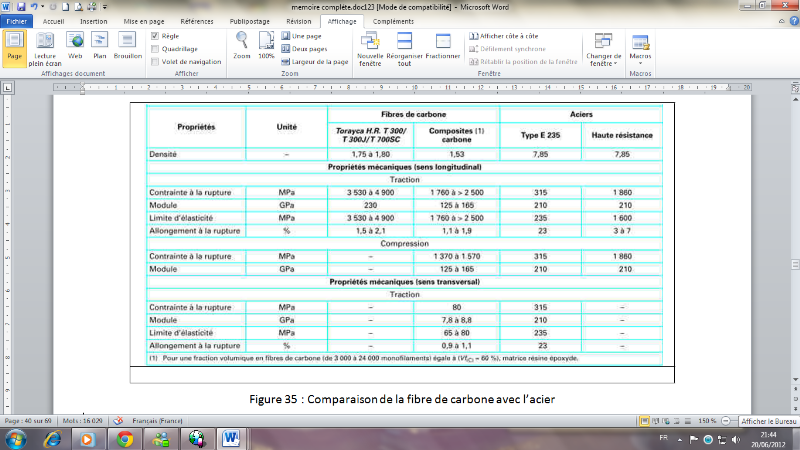
Le tableau suivant compare les différentes
caractéristiques mécaniques et physiques des construction :
fibres de carbone et celles des aciers usuellement
rencontrés.
L'intérêt des utilisations de la fibre de carbone
dans le génie civil se trouve essentiellement dans :
- sa faible densité
- ses propriétés mécaniques
longitudinales
- l'absence de corrosion
- sa très bonne tenue à la fatigue
- sa facilité de manipulation.
Cependant, comme tout matériau il a des
inconvénients. Les principaux sont les suivants :
- une anisotropie très marquée
- un comportement à la rupture de type fragile des
composites
- un prix de matière élevé comparé
à celui de l'acier.
Dans le cadre de la réhabilitation d'ouvrages en
béton armé, la qualité du support est primordiale. Il
convient d'effectuer un sablage à sec en vue d'obtenir un état de
surface rugueux et uniforme en tous points avec des reliefs d'impact compris
entre 0,5 et 1 mm. Les dépôts de poussières et les
particules non adhérentes sont éliminés par un brossage
énergique.
Cette technique peut être utilisée dans le
renforcement d'un ouvrage, soit dans le cas de perte de section d'acier
importante, soit lorsque la structure subit un ajout de charges par rapport
à ce qu'elle peut supporter. Ce procédé consiste à
placer des bandes de toile de fibres de carbone par collage aux endroits
déficients de l'élément concerné. Il est à
noter qu'une protection au feu est nécessaire afin de respecter la norme
en vigueur.

Figure36 : Tissus de fibre de carbone
1.4. CONCLUSION SUR LES
RÉPARATIONS
Dans ce chapitre nous avons vu les différentes
méthodes de réparation et de confortement d'un ouvrage en
béton armé.
Quelle que soit la méthode, le principe est de rendre
les sections d'acier et de béton initial ou de combler le manque de
section par ajout d'un autre matériau.
Dans tous les cas, le but est de faire en sorte que la
structure puisse reprendre à nouveau les charges qui lui sont
appliquées voir de pouvoir reprendre un supplément de charge si
cela s'avère nécessaire pour que l'ouvrage réponde aux
attentes et à l'évolution des besoins des utilisateurs ou des
propriétaires.
2. PROTECTION DES OUVRAGES
EN BÉTON ARMÉ
Après avoir diagnostiqué les différentes
pathologies, puis réparer la structure, il peut être utile de
prévoir une protection des ouvrages afin de rendre pérennes les
réparations afin d'éviter l'apparition rapide de nouvelles
pathologies semblables. Il existe un grand nombre de protections possible.
Elles sont à choisir selon ce contre quoi il est nécessaire de
protéger la structure.
Le schéma suivant recense les principales
méthodes existantes :

Figure 37 : Schéma de la protection d'un ouvrage en
béton armé
Chacune de ces méthodes permet soit de redonner au
béton de bonnes caractéristiques mécaniques et chimiques
soit de les protéger contre des attaques extérieures. Dans tous
les cas cela permet à la structure concernée de rallonger sa
durée de vie ainsi que ses capacités à absorber les
attaques de l'environnement extérieur et de la vieillesse.
2.1. LE REVÊTEMENT
IMPERMÉABILISANT
Les revêtements de surface, permettant de
protéger la structure contre les attaques, sont
décomposés en différentes catégories, elles sont
décrites dans la suite. Chaque type de revêtement a son propre
mode d'application.
Les revêtements imperméabilisants sont
généralement des systèmes multi couches appliqués
à titre curatif. Leur fonction principale est de pallier aux
désordres affectant la structure en ayant par exemple une fonction
d'imperméabilité à l'eau liquide.
Il est nécessaire qu'ils aient une
élasticité suffisante afin de pouvoir résister à la
fissuration du support.
Le DTU 42.1 définit le mode opératoire
d'application de ces revêtements.
Les produits utilisé doivent être choisis en
fonction des pathologies répertoriées lors du diagnostic. Les
produits doivent satisfaire à la norme NF 84-403 quant à leurs
caractéristiques (maintien de l'aspect, imperméabilité,
isolation thermique).
2.1.1. LES PEINTURES
La mise en peinture peut avoir différentes fonctions
:
- Elle permet d'améliorer l'esthétique de
l'ouvrage, par la mise en couleur ou la création de motifs
décoratifs, en vue de lui donner un aspect particulier, ou
d'homogénéiser, lorsque nécessaire, la teinte de ses
parements,
- Son but peut être d'augmenter le confort et la
sécurité des usagers, tout en facilitant le nettoyage
(exemple : revêtement des tunnels),
- Elle permet aussi de participer à la
sécurité de l'ouvrage (exemple : balisage des pylônes),
- Mais avant tout chose, elle permet de contribuer à la
protection du béton. En effet, la mise en place d'un système de
peinture en couche mince, dans la mesure où il apporte une
amélioration de l'imperméabilité du support peut
permettre de ralentir la pénétration de l'humidité
extérieure et d'améliorer ainsi la durabilité du
béton.
Il est à noter qu'il existe une procédure de
qualification concernant les systèmes de peinture pour béton de
génie civil. Elle donne des notions sur des critères
d'adhérence, d'aspect et plus généralement sur des
considérations d'ordre esthétique.
Cependant, elle ne se prononce pas sur des critères
visant à apprécier la capacité effective à remplir
une fonction de protection. L'ensemble de cette procédure est
décrit dans le guide « Mise en peinture des bétons de
génie civil » (LCPC, Juin 1999).
2.1.2. LES LASURES
Les lasures peuvent être utilisées pour conserver
ou mettre en valeur la texture du parement en béton. Il existe des
lasures incolores, mais aussi colorées. L'avantage par rapport aux
peintures c'est
2.1.3. LES
REVÊTEMENTS MINCES
Sont inclus dans cette catégorie :
- Les revêtements plastiques épais contenant
généralement des éléments à base de
résines acryliques ou polyuréthannes
- Les revêtements d'imperméabilité
à base de résine acrylique
- Les revêtements divers à base de
polyuréthane
2.1.4. LES ENDUITS DE
FAÇADE
On distingue deux catégories dans les enduits de
façade :
- Les enduits traditionnels, exécutés selon le
DTU 26.1 en trois couches distinctes
- Les enduits monocouche prêts à l'emploi.
Dans tous les cas ce sont des enduits à base de liants
hydrauliques et ou de chaux aérienne.

Figure 38 : Mise en place d'un revêtement de surface
2.2. LES INHIBITEURS DE
CORROSION
Les inhibiteurs de corrosion sont des éléments
chimiques permettant de ralentir, voire de stopper le processus de corrosion
des métaux sur lesquels ils sont appliqués.
Généralement ils sont ajoutés en faible concentration dans
le milieu corrosif.
Il est important de noter que ne sont pas inclus dans cette
catégorie de produit les éléments présents dans un
alliage de métaux tel que le chrome par exemple.
Il existe différents modes d'action des inhibiteurs de
corrosion selon leur catégorie. Chaque type réagira
différemment selon le milieu dans lequel il se situe. Par exemple,
l'inhibiteur peut recouvrir la surface du métal par adsorption et ainsi
réduire les surfaces de réaction élémentaires.
Dans un autre cas, il peut former des composés
avec le métal et le liquide environnant et modifier ainsi les
réactions d'interface. Dans tous les cas la vitesse de corrosion est
ainsi ralentie, voire annulée. Cependant pour généraliser,
la corrosion étant un processus électrochimique, l'action de
l'inhibiteur se ferra au niveau des étapes de réaction
électrochimique.
Les fonctions principales d'un inhibiteur de corrosion sont
les suivantes :
- Avoir une action rapide et vérifiable
- Être efficace durant de nombreuses années
- De pénétrer suffisamment les couches de
béton même dans le cas de béton très
hétérogène par nature
- D'abaisser la vitesse de corrosion du métal,
sans en affecter ses propriétés mécaniques et
chimiques ainsi que celles de son milieu environnant
- De prendre en considération le milieu (basique,
neutre dans le cas de la carbonatation, voir acide dans le cas de la
présence de chlorures) dans lequel il sera afin d'être compatible
avec celui-ci ainsi qu'à la température d'utilisation
- D'être en concentration suffisante pour être
efficace
- De ne pas être toxique
Comme il a été souligné plus haut, il
existe différentes catégories d'inhibiteurs de corrosion. Il est
possible de les classifier selon leur mode d'action, à savoir :
- Les inhibiteurs anodiques qui agissent en diminuant le
courant sur la partie anodique de la surface du métal. Cependant, il y a
un risque uniquement si son action n'est pas totale sur
l'élément, cela peut entrainer localement une augmentation de la
densité de courant et ainsi conduire à un processus localement
plus intense de corrosion qu'en l'absence d'inhibiteurs de corrosion.
- Les inhibiteurs cathodiques agissent en augmentant la
surtension au niveau de la cathode et ainsi réduisent le courant
de corrosion. Les inhibiteurs cathodiques ne stoppent jamais le processus de
corrosion, mais ils n'ont pas le désavantage des inhibiteurs
cathodiques, à savoir la corrosion localisée.
- Les inhibiteurs mixtes cathodiques. qui ont eux
à la fois les propriétés des inhibiteurs anodiques
et cathodiques.
Concernant la mise en oeuvre d'un inhibiteur de corrosion, il
est important avant de l'appliquer de préparer la surface du
béton, à savoir éliminer la peinture ou autre
revêtement. Une fois la surface prête à recevoir le produit,
l'application se fait directement sur la surface du béton à
l'aide d'un rouleau ou d'un pulvérisateur. Il faut veiller à ce
que les consommations mises en oeuvre soient conformes aux
préconisations. Pour les inhibiteurs de corrosion sous forme liquide,
l'application se fait en plusieurs passes.
Pour les inhibiteurs de corrosion sous forme
gélifiée, l'application se fait en une seule fois.
Il faudra par la suite vérifier que les
quantités minimales d'inhibiteurs de corrosion au niveau des armatures
soient atteintes. Cette vérification peut se faire par
prélèvement d'échantillons représentatifs de
l'ouvrage ou par le suivi des mesures de potentiel ou de courants de
corrosion.

Figure 39 : Application au rouleau d'inhibiteur de corrosion
Les zones devant recevoir ce type de produit sont les endroits
n'ayant pas été repris. En effet, généralement
lorsque les bétons sont dégradés par le processus de
corrosion, il est d'usage d'insérer un inhibiteur de corrosion dans la
formulation du béton de ragréage ou de béton
projeté.
Ainsi, les inhibiteurs de corrosion constituent un moyen de
lutte contre la corrosion des métaux. Ceci étant possible car le
traitement se fait par l'intermédiaire du milieu corrosif et non pas sur
le métal lui-même. Cela permet d'éviter de mettre
à nu les armatures pour l'application de ce type de produit.
2.3. LA
DÉCHLORURATION
Au fil du temps et selon l'environnement ambiant, des
éléments chlorures présents dans l'atmosphère
pénètrent dans le béton. Ces éléments
favorisent l'apparition et le développement de la corrosion des aciers
dans le béton armé. Ce phénomène est
amplifié lorsque la présence de chlorures est importante par
exemple pour les milieux salins, mais aussi dans le cadre de la
réfection des bétons du bâtiment « La Saline » de
la Compagnie des Salins du Midi et des Salines de l'Est. Cela étant
dû directement à l'activité qu'abrite ce bâtiment.
Le principe de la déchloruration est d'extraire ces
éléments chlorures du béton afin de limiter leur impact
sur les armatures présentent dans l'élément. Pour
ce faire, l'extraction des chlorures nécessite de polariser une
armature aux alentours du parement en utilisant une anode placée sur le
parement et enrobée d'un électrolyte. Ainsi peut circuler un
courant de polarisation, de l'anode vers la cathode (l'armature).
Pour l'heure, il existe principalement deux techniques
d'extraction des chlorures. Par courant imposé, lorsqu'un
générateur électrique est placé entre l'anode
et l'armature, ou par courant galvanique lorsqu'un alliage jouant le
rôle d'anode est directement relié à l'armature.
Cependant, cette méthode est réalisable
seulement dans les cas où il existe une continuité
électrique des armatures, il est toujours possible de relier
électriquement les armatures isolées à l'aide de pontages
électriques. Il est aussi nécessaire d'avoir
procédé à la réfection des parements avant
l'application de la ré-alcalinisation afin d'éviter toute forme
d'hétérogénéité.
L'action possible de ce traitement est limitée
à l'enrobage des armatures.
Il n'est pas possible d'extraire les chlorures
au-delà du premier lit d'armatures.
Dans le cas d'utilisation du système par courant
imposé, le principe de mise en oeuvre est le suivant :
- Projeter une couche de pâte (cellulose ou de laine de
roche) sur laquelle on appliquera une solution électrolytique (carbonata
alcalin)
- Mettre en place un treillis anodique métallique
sur des baguettes parement
- Connecter les fils de l'anode au treillis
- Projeter une deuxième couche de pâte
isolantes,
- Effectuer les raccordements électriques au
générateur de courant continu ayant une tension réglable
de 10 à 48 volts
- Humidifier périodiquement la pâte par
l'électrolyte
- Effectuer un suivi des tensions et courants ainsi que des
prélèvements d'échantillons en cours de traitement afin
d'effectuer des analyses sur l'efficacité du traitement
- Déposer l'ensemble de l'installation
- Rincer la structure à l'eau basse pression.
Dans le cas d'utilisation du système anodique, le
principe de mise en oeuvre est le suivant:
- Projeter une couche de pâte saturée en
électrolyte sur le béton
- Mettre en place l'anode métallique fixée d'une
part sur une baguette l'isolant du parement béton et d'autre part en
contact avec la pâte saturée en électrolyte
- Connecter l'anode au circuit électrique, c'est
à partir de la que le traitement se met en route
- Effectuer un suivi des tensions et courants ainsi que des
prélèvements d'échantillons de béton pour analyser
l'évolution du traitement
- Déposer l'ensemble de l'installation
- Rincer la structure à l'eau basse pression

Figure 40 : Traitement électrochimique en cours
Afin de vérifier si l'extraction des chlorures
est convenable, il est possible d'effectuer des
prélèvements d'échantillons avant et après
traitement pour pouvoir quantifier le résultat du traitement.

Figure 41 : Evolution de la teneur en chlorures avec le
traitement
2.4. LA
RÉ-ALCALINISATION
Le principe de base de la ré-alcalinisation est de
donner au béton un pH permettant de passiver les aciers. Initialement,
le béton lors de sa mise en oeuvre à un pH aux environs de 13.
Suite à sa carbonatation, le pH du béton diminue jusqu'aux
environs de 9, à ce moment-là, les armatures ne sont plus
protégées. Une ré-alcalinisation permet de redonner au
béton son pH d'origine. Ce traitement est dit temporaire, car il dure
généralement entre une et six semaines selon le degré
d'avancement de la carbonatation.
Pour effectuer une ré-alcalinisation, il est
nécessaire de polariser une armature aux alentours du parement en
utilisant une anode placée sur le parement et enrobée d'un
électrolyte. Ainsi peut circuler un courant de polarisation, de l'anode
vers la cathode (l'armature).
Tout comme pour la déchloruration, il existe
principalement deux techniques de ré-alcalinisation. Par l'armature, ou
par courant imposé, lorsqu'un générateur
électrique est placé entre l'anode et lecourant galvanique
lorsqu'un alliage jouant le rôle d'anode est directement relié
à l'armature.
Cependant, cette méthode est réalisable
seulement dans les cas où il existe une continuité
électrique des armatures, il est toujours possible de relier
électriquement les armatures isolées à l'aide de pontages
électriques. Il est aussi nécessaire d'avoir
procédé à la réfection des parements avant
l'application de la ré-alcalinisation afin d'éviter toute forme
d'hétérogénéité.
L'action possible de ce traitement est limitée à
l'enrobage des armatures. Il n'est pas possible de réalcaliniser
au-delà du premier lit d'armatures.
Dans le cas d'utilisation du système par courant
imposé, le principe de mise en oeuvre est le suivant :
- Projeter une couche de pâte (cellulose ou de laine de
roche) sur laquelle on appliquera une solution électrolytique (carbonata
alcalin)
- Mettre en place un treillis anodique métallique
sur des baguettes parement
- Connecter les fils de l'anode au
treillis-Projeter une deuxième couche de pâte
isolantes, fixées au parement.
- Effectuer les raccordements électriques au
générateur de courant continu ayant une tension réglable
de 10 à 48 volts
- Humidifier périodiquement la pâte par
l'électrolyte
- Effectuer un suivi des tensions et courants ainsi que des
prélèvements d'échantillons en cours de traitement afin
d'effectuer des analyses sur l'efficacité du traitement
- Déposer l'ensemble de l'installation
- Rincer la structure à l'eau basse pression.
Dans le cas d'utilisation du système anodique, le
principe de mise en oeuvre est le suivant:
- Projeter une couche de pâte saturée en
électrolyte sur le béton
- Mettre en place l'anode métallique fixée d'une
part sur une baguette l'isolant du parement béton et d'autre part en
contact avec la pâte saturée en électrolyte
- Connecter l'anode au circuit électrique, c'est
à partir de la que le traitement se met en route
- Effectuer un suivi des tensions et courants ainsi que des
prélèvements d'échantillons de béton pour analyser
l'évolution du traitement
- Déposer l'ensemble de l'installation
- Rincer la structure à l'eau basse pression
Afin de vérifier l'efficacité de la
ré-alcalinisation, il est possible de procéder à des tests
sur l'épaisseur de carbonatation avant et après traitement pour
pouvoir comparer les résultats. Ce test se fait
généralement à la phénolphtaléine.

Figure 42 : Evolution du pH avec la ré-alcalinisation
2.5. LA PROTECTION
CATHODIQUE
Pour le cas du béton armé, la protection
cathodique des armatures est un traitement, qui contrairement à
l'extraction des chlorures ou la ré-alcalinisation, appliqué de
façon permanente.
Il a pour but de ralentir, voire même d'arrêter la
corrosion. Le principe est d'abaisser le potentiel électrochimique de
l'armature jusqu'à une valeur seuil appelée potentiel de
protection.
Lorsque cette valeur est atteinte, on peut considérer
que la vitesse de corrosion dans l'acier est négligeable. Ceci peut se
faire en polarisant une armature présente dans le béton avec une
anode placée soit sur le parement soit dans l'enrobage. Puis il faut
appliquer un courant de polarisation, circulant de l'anode vers l'armature.
De même que pour la ré-alcalinisation et
l'extraction des chlorures, il existe principalement deux méthodes de
réalisation. Soit par courant imposé, avec un
générateur électrique placé entre l'anode et
l'armature, soit par courant galvanique avec une anode sacrificielle
directement reliée à l'armature.
Il est tout d'abord important d'effectuer des travaux
préalables avant l'application de la protection cathodique. En effet, il
est nécessaire d'éliminer le béton dégradé
ainsi que les bétons de réparations antérieurs, car ils
peuvent présenter une résistivité différente.
Il faut aussi enlever la rouille non adhérente sur les
armatures ainsi que de rétablir une continuité électrique
des aciers. Enfin, il est nécessaire de reconstituer l'enrobage tout
en veillant à avoir une distance millimètres entre
l'armature et le parement extérieur.
L'entreprise effectuant ces travaux doit procéder au
calcul de dimensionnement des anodes ainsi que de la capacité du
générateur. Cela a pour but de déterminer les
caractéristiques de l'installation à mettre en oeuvre telle que
le type et les quantités d'anodes à mettre en place, le courant
total nécessaire, etc. Ces paramètres sont directement fonction
de la dimension des armatures à traiter.
Une note de calcul doit indiquer le nombre et l'emplacement
des zones anodiques, la consommation en courant pour chaque zone, le type
d'anode choisi, le nombre et l'emplacement des capteurs de surveillance et de
contrôle.
Les étapes de la mise en oeuvre de la protection
cathodique sont les suivantes :
- Forer des trous dans le parement en béton
afin de mettre à nu des armatures et les connecter au
réseau électrique
- Les anodes sont soit plaquées à la surface du
parement soit enfouies dans le béton, il est nécessaire de les
enrober avec du mortier
- Installer des capteurs afin de pouvoir suivre
l'efficacité de l'installation
- Vérifier la continuité
- Mettre en service l'installation
|
Revêtement imperméabilisant
|
Ré-alcalinisation
Extraction des chlorures
|
Inhibiteur de corrosion
|
Protection cathodique
|
Avantages
|
Faible coût.
|
Passive à nouveau les aciers de manière
durable.
|
Possibilité
d'application seule sur béton afin de protéger
les aciers.
|
Empêche l'activité de corrosion.
|
Inconvénients
|
Nécessite un revêtement résistant à
la fissuration.
|
N'est efficace que
pour la partie située entre l'anode et la cathode.
Nécessite une purge du support et réparation des
épaufrures.
Les armatures doivent former un
réseau électrique.
|
Efficacité contestée.
Difficulté de contrôle de mise en oeuvre.
Nécessite une
purge du support et réparation des
épaufrures.
Les armatures doivent former un
réseau électrique si
forçage.
|
Nécessite une purge du support et réparation des
épaufrures.
Les armatures doivent former un réseau
électrique.
|
Contraintes phase travaux
|
Intempéries.
|
Installation conséquente. Réaliser des pontages
entre toutes les armatures.
|
Installation
importante si forçage. Renforcement des contrôles de
mise en place.
Réaliser des pontages entre toutes les armatures si
forçage.
|
Installation conséquente. Réaliser des pontages
entre toutes les armatures.
|
Durée de vie
estimée
|
10 ans.
|
10 ans.
|
10 ans si bonne
application.
|
30 ans.
|

Figure 43 : Raccordement de la protection cathodique
3. RECAPITULATIF
Plusieurs procédés existent pour
réhabiliter le béton armé dégradé par la
corrosion. Aucun d'eux n'est applicable dans tous les cas.
Leurs caractéristiques sont résumées dans
les tableaux ci-dessous.
Il est rappelé que chaque procédé ou
traitement doit comporter les étapes suivantes :
· Evaluation de la structure
· Nature et causes des éventuelles
dégradations
· Choix entre les solutions possibles sur le plan
technique
· Compatibilité entre les
procédés et les exigences diverses. En effet, la plupart du
temps, plusieurs options différentes sont possibles : la solution
retenue doit être compatible avec les exigences diverses, les
choix techniques et le coût supportable.
Béton projeté
Domaine d'action
|
Réparations, renforcements structurels
|
Mise en oeuvre
|
Projection sur la paroi à l'aide d'air comprimé
selon deux techniques : voie sèche et voie mouillée
|
Limites et précautions d'emploi
|
Respecter la norme NF 95102 pour la composition comme
pour les épaisseurs
|
Efficacité. Contrôle et durée
|
Réception des armatures, Contrôle
d'adhérence, Confection des caisses de convenance avec carottage
pour le contrôle des caractéristiques
|
Effets secondaires. Incidences sur l'ouvrage. Commentaires
|
Surcharges
|
Produits protecteurs : Inhibiteurs de
corrosion
Domaine d'action
|
Ralentissement du processus de corrosion des armatures
|
Mise en oeuvre
|
Par pulvérisation en plusieurs passes (forme liquide)
sur la surface du béton ou application directe sur la surface (forme
gélifiée) ou sur l'acier
|
Limites et précautions d'emploi
|
Incompatibilité avec les éléments
déjà traités par hydrofuges
Limites liées à des teneurs en chlorures trop
élevées
|
Efficacité. Contrôle et durée
|
Efficacité dépendante de la nature du produit et
de la quantité disponible au niveau des aciers (dosage de
l'inhibiteur)
Contrôle par mesures de potentiels ou de courants de
corrosion
|
Effets secondaires. Incidences sur l'ouvrage. Commentaires
|
Certains inhibiteurs minéraux interagissent avec le
béton
Risque d'apparition d'efflorescences devant être
nettoyées
|
Revêtements de surface : Peintures, lasures et
autres revêtements
Domaine d'action
|
Amélioration du parement : action esthétique,
limitation de l'encrassement, action protectrice du béton.
|
Mise en oeuvre
|
Application en plusieurs couches sur un support ne
présentant pas d'imperfections trop importantes
|
Limites et précautions d'emploi
|
Protection superficielle, non curative
L'état du support au moment de l'application a un
rôle déterminant
|
Efficacité. Contrôle et durée
|
L'efficacité est liée à la qualité
de l'adhérence entre le support et le revêtement, Risques de
cloquage, craquelage, écaillage.
Contrôle de la perméabilité de surface
|
Effets secondaires. Incidences sur l'ouvrage. Commentaires
|
Attention à la tenue aux rayons UV dans le choix des
produits
Risque d'incompatibilité avec certains traitements du
béton
|
Revêtements de surface : Enduits pour le
bâtiment
Domaine d'action
|
Amélioration de la surface du béton :
esthétique, correction des irrégularités de surface
(porosité, fissures), protection vis à vis de l'environnement
|
Mise en oeuvre
|
Selon la nature du produit
|
Limites et précautions d'emploi
|
Protection superficielle, non curative
|
Efficacité. Contrôle et durée
|
L'efficacité est liée à la qualité
de l'adhérence entre le support et le revêtement, Risques de
cloquage, craquelage, écaillage.
|
Effets secondaires. Incidences sur l'ouvrage. Commentaires
|
|
Traitements électrochimiques :
Ré-alcalinisation des bétons, extraction des
chlorures
Domaine d'action
|
Ré-alcalinisation pour les bétons
carbonatés
Extraction des chlorures pour les bétons pollués
en chlorures
|
Mise en oeuvre
|
Polarisation des armatures à l'aide d'une
électrode placée sur le parement et enrobée d'une
pâte saturée d'un électrolyte Durée : quelques
semaines
|
Limites et précautions d'emploi
|
Continuité électrique des armatures Béton
non susceptible à l'alcali-réaction Incompatibilité avec
les armatures revêtues Incompatibilité avec les
revêtements
|
Efficacité. Contrôle et durée
|
Vérification par indicateurs de pH
(ré-alcalinisation) ou détermination de la teneur en chlorures
(déchloruration). Traitement éventuellement à renouveler,
à terme.
|
Effets secondaires. Incidences sur l'ouvrage. Commentaires
|
Déséquilibre de la solution interstitielle du
béton
Risque d'apparition d'efflorescences devant être
nettoyées
|
Traitements électrochimiques : Protection
cathodique
Domaine d'action
|
Protection des aciers par abaissement de leur potentiel
électrochimique
|
Mise en oeuvre
|
Polarisation des aciers à l'aide d'une électrode
placée de façon permanente sur le parement ou dans l'enrobage
|
Limites et précautions d'emploi
|
Continuité électrique des armatures
Réparation éventuelle de la surface, Béton non susceptible
à l'alcali-réaction
Incompatibilité avec les armatures revêtues
Incompatibilité avec les revêtements
imperméabilisants.
|
Efficacité. Contrôle et durée
|
Efficace si le potentiel de l'acier est maintenu à la
valeur exigée
Remplacement des électrodes de
référence
|
Effets secondaires. Incidences sur l'ouvrage. Commentaires
|
Déséquilibre de la solution interstitielle du
béton
Risque de fragilisation dans le cas des aciers de
précontrainte. Modification de l'apparence du parement,
Suivi électrique indispensable durant la durée
de vie de l'ouvrage.
|
4- Normes
Les principales normes relatives aux produits de
réparation sont les suivantes :
Produits spéciaux destinés aux constructions en
béton hydraulique
|
N° de normes
|
Titre
|
Nature du liant
|
Année
|
NF P 18-800
|
Définitions, classification, conditionnement, marquage,
conditions de réception
|
H - R
|
1989
|
NF P 18-802
|
Contrôle sur chantier
|
H - R
|
1992
|
Produits ou systèmes de produits destinés aux
réparations de surface du béton durci
|
NF P 18-840
|
Caractères normalisés garantis- Normes d'essais
garantis - Normes
|
|
1993
|
NF P 18-852
|
Essais d'adhérence sur surfaces sciées
|
H - R
|
1993
|
NF P 18-853
|
Essai d'adhérence après cycles thermiques sur
surfaces sciées
|
H - R
|
1993
|
NF P 18-854
|
Essai de tenue aux chocs répétés sur
surfaces sciées
|
H - R
|
1993
|
NF P 18-855
|
Essai de perméabilité aux liquides avec surfaces
sciées
|
H - R
|
1992
|
NF P 18-856
|
Essai de tenue aux rayonnements U.V.
|
R
|
1993
|
NF P 18-857
|
Essai de tenue aux chocs
sur surfaces sciées après cycles
|
H - R
|
1993
|
NF P 18-858
|
Essai d'adhérence sur surfaces rugueuses
|
H
|
1993
|
NF P 18-859
|
Essai d'adhérence après cycles thermiques sur
surfaces rugueuses
|
H
|
1993
|
NF P 18-860
|
Essai de tenue aux chocs répétés sur
surfaces rugueuses
|
H
|
1993
|
NF P 18-861
|
Essai après cycles de gel-dégel, de tenue aux
chocs répétés sur éprouvettes à surface
rugueuse
|
H
|
1993
|
NF P 18-862
|
Essai de perméabilité aux liquides sur
éprouvette à surface rugueuse
|
H
|
1993
|
H : produits hydrauliques
R : résines de synthèse
Ouvrages d'art, Normes sur les techniques de
réparations
|
Année
|
NF P 95-101
|
Réparation et renforcement des ouvrages en béton
et en maçonnerie - Reprise du béton dégradé -
Spécifications relatives à la technique et aux matériaux
utilisés
|
1990
|
Chapitre 04
1. CONTROLES DE LA MISE EN
OEUVRE
La réhabilitation du béton armé
dégradé fait appel à différentes techniques, qui
ne sont pas encore toutes codifiées, ni du point de vue des
méthodes, ni du point de vue du contrôle.
L'objet de ce chapitre est de préciser ce qu'il y a
lieu de faire (c'est-à-dire faire figurer dans les pièces
contractuelles et exiger de l'entrepreneur), en matière de
contrôle interne, et préciser la nature du contrôle
extérieur, qui reste une prérogative du Maître d'oeuvre.
Il convient de rappeler les définitions suivantes :
· Point sensible : c'est un point de
l'exécution, qui doit particulièrement retenir l'attention.
· Point critique : c'est un point de
l'exécution, qui nécessite une matérialisation du
contrôle interne sur un document de suivi, ainsi qu'une information
préalable du contrôle extérieur pour que celui-ci puisse se
faire, le cas échéant. L'intervention du contrôle
extérieur n'est pas nécessaire à la poursuite de
l'exécution.
· Point d'arrêt : c'est un point critique,
pour lequel un accord formel du maître d'oeuvre ou d'un organisme
mandaté par lui, est nécessaire à la poursuite de
l'exécution. Les délais de préavis et les délais de
réponse du maître d'oeuvre sont fixés dans le Cahier des
Clauses Administratives Particulières (CCAP), qui doit préciser
les dispositions à prendre par l'entreprise, à l'issue du
délai de réponse, en l'absence de réaction du maître
d'oeuvre.
1.1. PREPARATION DES
TRAVAUX
1.1.1.
Dossier de consultation des entreprises
Lors de la rédaction du Dossier de
Consultation des Entreprises (DCE), il faut :
· indiquer que l'entrepreneur qui propose une
variante devra définir les contrôles internes correspondants,
· inclure une clause dans le Cahier des Clauses
Techniques Particulières (CCTP) portant sur l'Assurance de la
Qualité. Il est rappelé que "l'entrepreneur établit le
Plan d'Assurance Qualité (PAQ) dans lequel il décrit
l'organisation générale du chantier, les principaux moyens qu'il
compte y affecter et les dispositions de contrôle interne associés
à ces moyens". Le PAQ est soumis au visa du Maître d'oeuvre, ainsi
que le cadre des documents de suivi,
· indiquer, dans le CCTP, les sujétions que le
contrôle extérieur impliquera, à l'égard de
l'entreprise ; en particulier, cette pièce du marché devra
contenir la liste des points d'arrêt ainsi que les délais qui
s'attachent à la levée de ces derniers.
L'entrepreneur fait des essais et contrôles, au titre du
contrôle interne et les conserve à sa charge.
Le Maître d'oeuvre fait des essais et contrôles au
titre du contrôle extérieur et les rémunère sur
crédits du Maître d'ouvrage, qu'ils soient prévus ou non au
marché.
1.1.2. Mise au point du
marché
Lors de la mise au point du marché il y a lieu de :
· modifier le CCTP pour ce qui est relatif au
contrôle interne, en fonction des variantes (compléter si il y a
lieu la liste des contrôles internes prévus par
l'entrepreneur),
· mettre au point le cadre du PAQ qui comprendra les
principales dispositions du document d'organisation générale et
la liste des procédures d'exécution, et l'annexer au CCTP.
1.1.3. Plan assurance
qualité (PAQ)
Au cours de la période de la préparation et lors
de l'exécution, l'entrepreneur établit le
PAQ qui traite :
· des facteurs contribuant à
l'obtention de la qualité : affectation des taches, moyens en personnel
matériels et fournitures
Méthodes et points sensibles de l'exécution
· du contrôle interne.
Lors de l'examen du PAQ, le maître d'oeuvre devra
s'assurer que l'entrepreneur n'aura à se livrer à aucune
improvisation sur le chantier.
1.2 .CONTROLE INTERIEUR DE
L'ENTREPRISE
Le contrôle intérieur de l'entreprise porte sur
des épreuves, des réceptions et le contrôle des travaux
finis.
1.2.1. Epreuves
1.2.1.1. Epreuve d'étude
L'épreuve d'étude est un point
critique.
Lorsque le produit est un composite soumis à une
formulation explicite (par exemple, cas du béton projeté), un
dossier d'étude est fourni par l'entreprise. Ce document comporte les
résultats d'une épreuve d'étude.
1.2.1.2. Epreuve de
convenance
L'épreuve de convenance est un point
d'arrêt.
Elle a pour but de tester, dans les conditions de chantier,
l'aptitude de l'entreprise à réaliser les travaux avec les
matériaux et les moyens matériels et humains indiqués au
PAQ. A cette occasion, les points particuliers sont examinés. Pour
toutes les techniques, une attention particulière est portée
sur la préparation du support, pour qu'il soit compatible avec la
technique proposée.
La planche de convenance est généralement une
zone (de l'ordre du mètre-carré) de l'ouvrage à
réhabiliter. Elle doit être représentative de l'ensemble de
la réhabilitation, sur les plans techniques, difficulté
d'accès, sécurité etc.
Les matériaux, les moyens en matériel et la
compétence du personnel sont évalués, lors de
l'épreuve. Pour certaines techniques, la qualification de
l'équipe (exemples : porte lance, aide porte lance et machiniste en
béton projeté, ou électricien pour la composante
électrique de la protection cathodique) sera exigée.
1.2.2.
Réceptions
1.2.2.1. La réception des matériaux
La réception des matériaux est un point
critique.
La vérification de la conformité de la livraison
à la commande porte sur :
· le béton (cas du béton prêt
à l'emploi),
· les matériaux (ciment/granulats,
adjuvants/ajouts/eau ou les sacs pré-dosés dans le cas du
béton fabriqué sur place),
· les produits de ragréage et autres produits
de protection,
· les armatures et les produits de cure,
· les anodes, les autres fournitures
électriques et les capteurs de suivi des systèmes pour les
traitements électriques.
Des prélèvements conservatoires de
matériaux sont réalisés en vue d'analyses
éventuelles.
1.2.2.2. La
réception du support
La réception du support comprend :
· la vérification de la délimitation
des zones à réhabiliter,
· la vérification de l'état du support
et des surfaces de reprise entre couches (béton projeté
(point d'arrêt),
· la vérification de la mise en place du
ferraillage (point critique),
· la vérification de la mise en place du
système de traitement électrique (point critique).
1.2.2.3. La
réception des produits
La réception des produits comprend :
· la vérification du respect des dosages
(point critique).
· la caractérisation de l'ouvrabilité
du produit.
1.2.3. Contrôle de
la mise en oeuvre
Le contrôle de la mise en oeuvre comprend les points
suivants :
· contrôle du respect du phasage de la
réhabilitation (nombre de couches, délai d'application entre les
couches, épaisseur totale) (point critique),
· suivi de la consommation des produits,
· contrôle d'exécution et de la
qualité des produits mis en oeuvre (point critique),
· contrôle d'épaisseur du béton
projeté, des revêtements de surface (point critique),
· contrôle de finition (aspect,
planéité) (point critique),
· contrôle de cure (point
critique),
· contrôle de l'adhérence au support
(point d'arrêt),
· contrôle de mise en service (traitements
électriques) (point d'arrêt).
1.2.4. Contrôle des
travaux finis
Le contrôle des travaux finis est un point
d'arrêt. Il porte sur la vérification des
caractéristiques requises et de l'efficacité de la protection
et/ou de la réparation.
1.3. CONTROLE EXTERIEUR DU
MAITRE D'OEUVRE
Le « Contrôle extérieur » du
Maître d'oeuvre est un contrôle de conformité aux exigences
du CCTP, en ce qui concerne :
· le matériel de fabrication,
· la réception, le transport et la mise en
oeuvre des matériaux et matériels,
· le personnel d'exécution et de support
pour l'application des méthodes de réhabilitation.
L'entité "Contrôle extérieur" à
partir du Dossier de Consultation des Entreprises (DCE), du Schéma
Directeur de la Qualité (SDQ), du Plan d'Assurance Qualité (PAQ)
et des procédures des divers intervenants a les tâches suivantes
:
a- examiner et formuler un avis sur les propositions de
l'entreprise en matière de :
· moyens et qualification en personnel, moyens en
matériel de fabrication et mise en oeuvre,
· consistance des études,
· matériaux,
· contenu du contrôle intérieur.
b- proposer au Maître d'oeuvre un programme de
contrôle extérieur, en fonction du contrôle
intérieur.
c- réaliser le contrôle extérieur qui
porte sur :
· la vérification du PAQ Entreprise et des
sous-traitants et/ou fournisseurs,
· la validation de l'épreuve d'étude
(point d'arrêt),
· la validation de l'épreuve de convenance
(point d'arrêt),
· la vérification de l'application du PAQ
Entreprise concernant le contrôle interne lié à
l'exécution des travaux,
· le contrôle de réception du support
(point d'arrêt),
· le contrôle de qualité des
matériaux et matériels mis en oeuvre,
· le contrôle d'adhérence au support
(point d'arrêt),
· le contrôle de réception de l'ouvrage
(ou de l'élément d'ouvrage) (point d'arrêt).
2. SUIVI D'UN OUVRAGE
Le suivi d'un ouvrage a pour principale fonction de mesurer
l'évolution des pathologies dans le temps. Ce suivi peut se faire
notamment sur la fissuration d'un ouvrage, mais aussi sur l'avancement du front
de carbonatation ou encore l'évolution de la teneur en chlorures.
On distingue deux types de suivi d'ouvrages. Il y a le suivi
ponctuel et le suivi continu.
2.1. LE SUIVI PONCTUEL
Le principe de ce suivi est qu'une personne vient relever
l'évolution des pathologies à échéances
régulières, par exemple deux fois par an, afin d'effectuer des
prélèvements pour analyses ou faire des essais sur place. Cela se
fait principalement pour la teneur en chlorures, pour laquelle des poudres de
béton son prélevées en vue de déterminer la
quantité de chlorures présente.
Il est aussi possible de suivre l'avancement du front de
carbonatation, en effectuant des tests à la
phénolphtaléine sur un élément afin de
déterminer la vitesse à laquelle le béton le constituant
se carbonate. Il est aussi possible de procéder à ce type de
suivi pour l'ouverture de fissures.
Cela permet de déterminer si la fissure est passive,
stabilisée ou active. Par contre, la précision sera moindre que
pour un suivi continu.
2.2. LE SUIVI CONTINU
Le fonctionnement de ce suivi est de mettre en place des
capteurs afin de relever, l'évolution de la pathologie, plusieurs fois
par jour sur une période donnée. Cette méthode est
généralement employée pour le suivi de l'ouverture de
fissures.
Ainsi, il est possible de corréler la variation de
l'ouverture avec l'évolution des températures. Cela permet
là aussi de déterminer si la fissure est passive,
stabilisée ou active, mais avec plus de précision afin
d'être sûr que la fissure évolue avec les
températures ou non.
J'ai rencontré ce type de suivi sur l'instrumentation
et suivi microclimatique du barrage Vauban à Strasbourg. Le principe de
l'étude est de voir si les fissures du barrage ont un comportement
cyclique correspondant à l'évolution des températures sur
une année, ou si elles ont un caractère
dégénératif indépendant de la température.
Pour se faire, chaque fissure est équipée de
trois capteurs, l'un mesurant la composante perpendiculaire à la fissure
sur le plan horizontal, le deuxième mesurant la composante oblique
à la fissure sur le plan horizontal, et le dernier mesurant les
déformations sur le plan vertical.

Figure 44 Différents capteurs
Conclusion
L
es missions menées dans le cadre de ce Projet de Fin
d'Études ont permis de recenser les principales techniques
d'investigation d'ouvrages en béton armé utilisées. On a
pu voir qu'il existait deux types de diagnostic, l'un en utilisant des
méthodes destructives et l'autre avec des méthodes non
destructives. Il a été souligné l'importance du diagnostic
dans le processus de réhabilitation d'ouvrages en béton
armé, c'est à ce moment que l'on détermine les pathologies
présentes ainsi que leur ampleur. Cela est nécessaire afin de
prodiguer les réparations les plus adaptées ainsi que les
protections à mettre en oeuvre afin de donner les
défenses nécessaires à l'ouvrage
Concernant les différentes techniques de
réparation, nous nous somment appuyer sur des recherches menées
sur les projets de réhabilitation divers. Il en est ressorti trois
techniques particulières, le ragréage, le béton
projeté et l'utilisation de tissus de fibre de carbone. Ces trois
techniques ont pour buts principaux de redonner à chaque
élément ses caractéristiques géométriques et
également de redonner à la structure ses capacités
à reprendre les efforts qui lui sont appliqués.
Pour les différents modes de protections, la encore
nous avons effectué un travaille de recherche sur la réalisation
de dossier de consultation des entreprises et de dossier projet
bâtiment. On a pu voir les différents modes de protection, leurs
utilités, leur mode d'action ainsi que le principe de leur mise en
oeuvre. Cependant, il est nécessaire de souligner le fait que ce n'est
pas suffisant de simplement protéger l'ouvrage. Il faut avant tout
travailler sur l'origine des désordres, afin d'arrêter le
problème à la source.
La nécessité de réaliser des fiches, une
pour chaque technique, que ce soit de diagnostic, de réparation ou de
protection, était nécessaire pour l'entreprise. En effet,
certaines de ces techniques ne sont pas utilisées couramment dans
les agences et les détails du mode opératoire sont
rapidement omis. Pour les techniques qui sont plus couramment utilisées,
il est possible qu'elles soient mal appliquées. Dans les deux cas,
ce sont des sources d'erreurs et de mauvaise interprétation, ce
qui peut engendrer des problèmes lors de la réhabilitation d'un
ouvrage.
Ce Projet de Fin d'Études nous a permis de
découvrir de nouveaux aspects de l'ingénierie du génie
civil. Lors de notre formation, nous étudions principalement les
différents modes de construction et les matériaux utilisés
dans le neuf, mais très peu de connaissances ont été
acquises concernant la réhabilitation d'ouvrages existants. Pourtant, ce
domaine tend à se développer surtout dans le cadre du
développement durable.
|