
République Algérienne Démocratique et
Populaire
Ministre de l'Enseignement Supérieur et de la
Recherche Scientifique
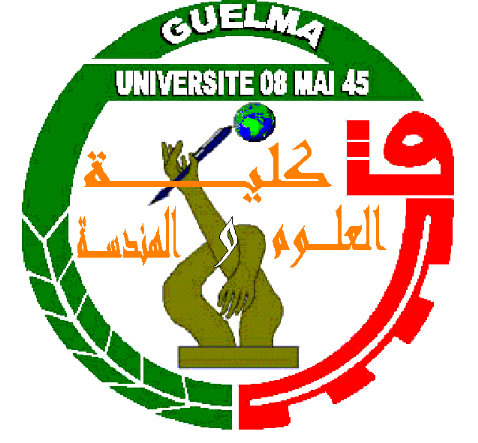
Université 08 Mai 1945
Département de Génie Mécanique
Mémoire de projet de fin d'étude licence
Etude des efforts de coupe et de la rugosité
lors de l'usinage du PE 80
Parcours : LICENCE C.F.A.O
Présenté par :
SELAIMIA Mossaab Et
HIMOUD Khaled
Encadré par :
Mr. BELHADI Salim
Mme. KADDECHE Mounia
JUIN 2009

Année: 2008 / 2009
Remerciement
Nous remercions Dieu qui nous a donné
la force et la patience nécessaire pour Mener le présent travail
à terme.
Nous remercions aussi, nos encadreurs Mr.BELHADI
SALIM
Et Mme.KADDECHE MOUNIA .
Nous remercions également tous les enseignants du
Département de mécanique, et
tout les étudiants promotion 2009
A touts ceux qui nous ont aidés à réaliser
ce travail.
Mercie à tous.........
Dédicace
Dédicace
On dédie ce modeste travail :
A NOS PARENTS
A nos chers frères
Très chers AMIS
pour leurs soutiens et leurs sacrifices.
A tous ceux qui nous ont aidé de prés ou
de loin pour la réalisation de ce Travail.
SELAIMIA MOSSAAB
HIMOUD KHALED
Une importante compétition sur les plans technique et
économique continue d'opposer les métaux aux matériaux
polymères pour la réalisation de pièces multiformes
destinées à être utilisées dans des domaines
variés comme le secteur de l'automobile, des prothèses
biomédicales, de l'aéronautique, des applications
électroménagères et autres. Les exigences des stylistes et
concepteurs imposent bien souvent des mises en forme très
compliquées ayant des cotes extrêmement précises
nécessitant, parfois, une fabrication de petites séries comme le
cas des coudes de diamètres importants.
Les polymères présentent l'avantage d'être
mis en oeuvre plus facilement lors de la production par moulage ou par
extrusion. Cependant, après moulage les pièces
polymériques peuvent encourir la probabilité de voir leur
structure se transformer par cristallisation en quelques jours, notamment en
surface, et les cotes peuvent ne plus être dans la tolérance
prévue par le design. Ainsi, les techniques de mise en forme et de
fabrication doivent être impérativement adaptées aux
comportements spécifiques du polymère pour l'application
désirée. Comme les polymères usuels ne sont
généralement pas conducteurs électriques, l'usinage par
électroérosion n'est donc plus possible. D'autre part, l'usinage
par ultrasons convient aux métaux durs, ce qui n'est pas le cas des
plastiques. Cela limite les procédés à l'usinage
conventionnel, souvent qualifié d'usinage par enlèvement de
copeaux et à la découpe par laser ou au jet d'eau.
Cette étude expérimentale est conçue dans
le but d'établir une loi de prédiction de la rugosité de
la surface obtenue en fonction des paramètres du régime de coupe
et d'étudier l'évolution des efforts de coupe lors de l'usinage
des tubes en HDPE-80.
I.1. Définitions :
Les polymères, appelés aussi matières
plastiques ou simplement plastiques, sont des matériaux organiques
composés essentiellement d'atomes de carbone et d'hydrogène. La
plupart des polymères sont élaborés à partir d'un
ou de deux types de monomères seulement. Les composés
macromoléculaires sont respectivement appelés homo ou
copolymères [1].
Une macromolécule correspond à un
enchaînement d'une multitude de monomères liés de
façon covalente. Le terme polymère est plutôt
réservé pour définir le matériau obtenue de
manière naturelle ou par synthèse organique. Le terme plastique
souligne plus fortement le caractère de matériau de
synthèse fini (à partir duquel des pièces sont produites
selon des technologies spécifiques) ; il définit moins la
structure du matériau et les réactions requises pour son
élaboration [2].
I.2. Classification des
polymères :
On peut classer les matériaux polymères suivant
différents critères. Le point de vue thermique conduit au
classement des matériaux polymères organiques en matériaux
thermoplastiques et matériaux thermodurcissables. Le point de vue
mécanique introduit les notions de solides viscoélastiques et
d'élastomères. On peut aussi examiner le matériau en
s'intéressant à sa structure physique ou à sa structure
chimique : dans le premier cas, les notion de matériau
semi-cristallins et de matériau amorphe sont introduites ; dans le
second, c'est la structure moléculaire en chaîne d'atome qui est
à prendre en considération [3].
I.2.1. Point de vue
thermomécanique :
* Les thermoplastiques :
Les thermoplastiques sont constitués de
macromolécules linéaires ou ramifiées, liées entre
elles par des liaisons physiques. Ces matières sont solides à
température ambiante. Elles se ramollissent à la chaleur
jusqu'à un état plastique dans lequel elles se laissent
comparativement plus facilement déformer. Ce processus est
réversible, c'est-à-dire que les thermoplastiques se rigidifient
de nouveau au refroidissement. Selon la régularité de leur
chaîne, ces polymères peuvent cristalliser (thermoplastiques
semi-cristallins) ou non (thermoplastiques amorphes) [2].
Ce qui caractérise un matériau thermoplastique
est la possibilité, après avoir subi une histoire
thermomécanique, d'être ramené par des moyens physiques
à l'état initiale. [3].
** Les thermodurcissables :
Les matières thermodurcissables diffèrent
nettement des matières thermoplastiques, non seulement du point de vue
de structure chimique, mais aussi des technologies de mise en forme requises.
Les principaux représentants de la famille des thermodurcissables sont
les polyesters insaturés (UP), les époxydes (EP), les
phénoplastes (phénol-formaldéhyde PF, notamment), les
aminoplastes, les acrylates et les silicones (SI). Ces matières trouvent
des applications, en particulier après renforcement par des fibres, pour
l'élaboration d'équipements industriels et sportifs, mais aussi
dans la construction aéronautique et d'engins spatiaux.
Les thermodurcissables sont stables même à des
températures relativement élevées et présentent en
générale une bonne tenue vis-à-vis des milieux agressifs.
Ils ne peuvent jamais revenir à l'état initiale quand leur
température a été augmentée.
***Les élastomères :
Les polymères de la 3éme famille, celle des
élastomères, se distinguent par les faibles valeurs des forces
d'attraction entre les chaînes et de leurs modules élastiques
(à température ambiante) et par leur capacité
élevée de déformation (quelque centaine de pour cent)
[4].
Les élastomères sont des composés
macromoléculaires dont les propriétés sont
étroitement liées à leur nature chimique et au
caractère aléatoire de la distribution des chaînes
moléculaires. Le caoutchouc naturel et les caoutchoucs
synthétiques appartiennent à cette famille.
I.2.2. Point de vue de la structure
physique :
* Polymère amorphe:
L'état amorphe des matériaux polymères
est caractérisé par l'absence d'ordre à grande distance.
Il n'y a pas de distance constante entre les macromolécules et aucune
régularité dans l'arrangement et l'orientation, et ceci en raison
de la structure et de la disposition aléatoire des chaînes
individuelles.
La structure des macromolécules dans les états
physiques solide (vitreux) et liquide étant très semblable pour
les matériaux amorphes. Pour une phase cristalline au contraire, un
nouvel arrangement ordonné des macromolécules les unes par
rapport aux autres est crée au refroidissement de la matière
fondue (cristallisation).
Les macromolécules dans la conformation de types pelote
statistique peuvent, selon les conditions auxquelles elles sont soumises,
s'entrelacer, s'enchevêtrer, mais aussi créer des noeuds chimiques
(réticulation) à certain endroits (figure 1) [2].
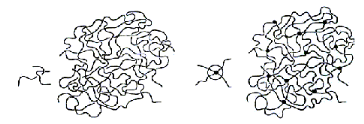
Exemple :PVC, PS,, PMMA, SAN Exemple :NR, SBR,
PUR
Figure1 : Interpénétration
de structure en pelote [2].
** Polymères
Semi-Cristallins :
Dans un polymère cristallisé les
molécules sont serrées les unes contre les autres et parfaitement
ordonnées dans des lamelles cristallines. Généralement les
polymères semi-cristallins présentent une alternance de
plaquettes de phase amorphe et de phase cristalline appelée structure
lamellaire.
Cependant certains matériaux polymères, tel que
le polyéthylène, peuvent présenter localement une
organisation macromoléculaire qui se répète sur une
distance telle qu'elle rappelle la structure cristalline des solides
métalliques.
A partir des études en laboratoire sur les monocristaux
de polyéthylène, la cristallisation résultait de
l'organisation en parallèle de segments de macromolécules. Elle
se replient sur elles-mêmes et peuvent ainsi participer à
l'édification de lamelles d'épaisseurs assez constante (quelques
dizaines de nanomètres).
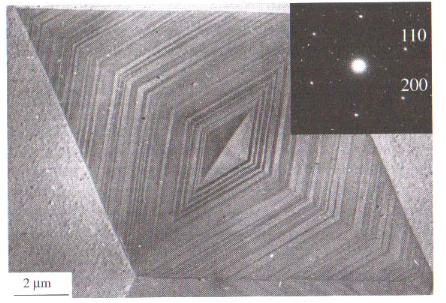
Figure 2 : Un monocristal de PE
à partir d'une solution de glycérol [4].
Les polymères semi-cristallins sont utilisés
à une température qui se situe entre la température de
transition vitreuse de leur phase amorphe et la température de fusion,
de leur phase cristalline. Ceci permet de profiter de la souplesse de la phase
amorphe et de la rigidité de la phase cristalline.
I. 3. Elaboration des polymères:
La nature des polymères conditionne leur mode
d'élaboration. Même si plusieurs voies sont chimiquement et
économiquement possibles, la liberté du choix de la
méthode de la mise en oeuvre est restreinte. Pour un objet
thermoplastique, il est rarement possible d'effectuer la polymérisation
dans le moule à partir des monomères, alors qu'un
thermodurcissable nécessite toujours que la chimie terminale soit faite
lors de la mise en forme. Ces contraintes font qu'entre le début des
opérations de synthèse et la mise en forme du matériau en
objet il va falloir passer par des étapes intermédiaires. Les
substances de base nécessaires à l'élaboration des
matières plastiques peuvent, à priori, être choisies dans
les trois origines de la nature (animale; végétale et
minérale) [5].
Actuellement les matières plastiques sont
essentiellement produites à partir de la pétrochimie (on pourrait
également utiliser la carbochimie, mais il est plus facile d'utiliser
directement un liquide ou un gaz). On opère suivant le cycle
représenté dans la figure 3.
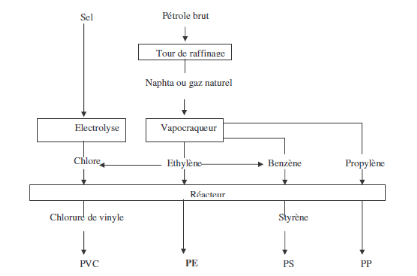
Figure 3: Grandes étapes de la
fabrication des plastiques [5].
A partir de naphta, le producteur de plastiques prépare
par vapocraquage (ou reformage) les rands intermédiaires de la
pétrochimie, dont les monomères qui, sous l'effet de pression,
température, catalyseurs... deviendront des polymères
(polycondensats), qui constituent les matières plastiques proprement
dites, que l'on utilisera dans la transformation. On passe du monomère
au polymère (combinaisons de monomères) de trois façons :
par polymérisation; par polycondensation et par polyaddition.
I.4. Le matériau polyéthylène:
I.4.1. Structure et
propriétés:
La polymérisation de l'éthylène produit
un hydrocarbure à chaîne essentiellement droite et à masse
molaire élevée. Les polyéthylènes (PE)
possèdent l'une des structures chimiques les plus simples de tous les
polymères. C'est des matériaux thermoplastiques semi cristallins
qui représentent un enchaînement de groupe
(CH2-CH2). Ils sont obtenus par polymérisation
d'éthylène gazeux. Ce dernier est polymérisé en
présence d'un comonomère (butène, pentène,
hexène, octène...etc.). Divers procédés sont
utilisables pour cette polymérisation, au nombre desquelles nous
citerons : la déshydratation de l'alcool éthylique sur l'alumine,
la hydrogénation de l'acétylène et le cracking des
hydrocarbures aliphatiques se trouvant dans le naphta (pétrole brut) et
les gaz naturels. Cette dernière s'effectue à haute
température, vers 800°C. L'éthylène doit être
soigneusement purifié, pour le débarrasser de diverses
impuretés gazeuses comme : CO, CO2, N2, NH3, S...qui pourraient jouer le
rôle d'inhibiteurs de polymérisation, en rompant les chaînes
de polymère, au fur et à mesure de leur formation.
D'après la norme américaine ASTM D1248, les
polyéthylènes sont classifiés comme suit : les PE qui ont
les densités comprises entre 0.910 g cm-1 et 0.925 g cm-1 sont de type I
; polyéthylène à basse densité. La rangée de
0.926 à 0.940 est le type II, polyéthylène moyenne
densité. Les rangées de 0.941 à 0.959 sont
classifiées sous le type III et +0.960 comme type IV, sont
appelées polyéthylène haute densité. Cette
classification est devenue fondamentale dans l'industrie des tubes [5].
Le polyéthylène à basse
densité (LDPE) possède un plus grand
nombre de ramifications, ce qui produit une structure moléculaire moins
compacte.
Le polyéthylène à haute
densité (HDPE) possède peu de
ramifications, ce que le rend plus rigide et moins perméable que le
LDPE.
Le polyéthylène à basse
densité linéaire (LLDPE) combine la
dureté du polyéthylène à basse densité avec
la rigidité du polyéthylène à haute
densité.
Le polyéthylène à haute
densité réticulé (XLPE) est une
forme de polyéthylène à haute densité dans lequel
les chaînes moléculaires individuelles sont liées les unes
aux autres pour former un polymère tridimensionnel à la masse
molaire extrêmement élevée.
Dans ce thème, on est intéressé par les
polyéthylènes de haute densité. Ces
polyéthylènes (PEHD) sont des polymères non ou très
peu branchés, courts ou longs, fabriqué surtout à basse et
moyenne pressions par amorçage ionique. Par rapport aux PEBD, les
matériaux au PEHD ont une rigidité, une résistance
mécanique et un point de fusion supérieurs, mais ils
présentent une résistance plus faible à la fissuration
provoquée par l'environnement. La formule chimique du PEHD est de la
forme [6] :
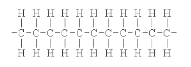
La Figure 4 représente le modèle d'un segment
macromoléculaire de polyéthylène de haute densité;
la chaîne est dans la réalité environ dix fois plus longue.
Les atomes d'hydrogène (blancs) sont liés latéralement aux
atomes de carbone (noirs), ce qui confère une allure en zigzag à
la macromolécule.
En l'absence de contraintes, le polyéthylène
haute densité peut supporter une température de 110 à
120°C, stérilisation par exemple, cette température
décroît sous charge et augmente avec la réticulation. Le
passage de la température de transition vitreuse est d'autant moins
sensible que le polyéthylène est plus cristallin. La fusion des
polyéthylènes est étalée. La température de
fusion augmente avec la masse volumique. Ils brûlent avec une flamme
bleutée et ils « gouttent ». La sensibilité
dimensionnelles est indépendante de la reprise d'humidité
très faibles <0.2% [5].
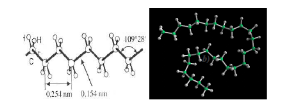
Figure 4 : Structure
macromoléculaire du polyéthylène linéaire (PE-HD)
[1].
a) Schéma de la structure d'une
chaîne et disposition spatiale des atomes.
b) Modèle d'un segment
macromoléculaire.
Les propriétés importantes de ces types sont
rassemblées dans le Tableau I.
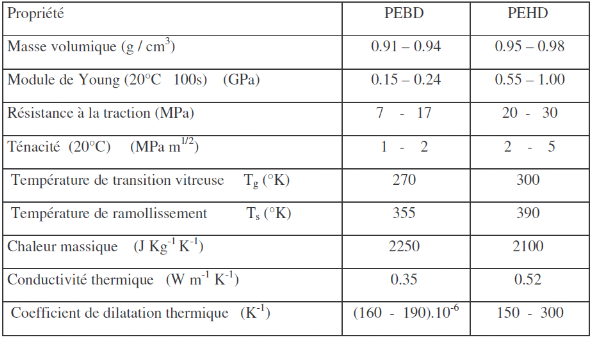
Tableau I: Propriétés
mécaniques et thermiques des polyéthylènes [7].
Les propriétés des polyéthylènes
dépendent des paramètres structuraux comme la
cristallinité, la masse volumique et la distribution des masses
molaires, de la conception de la pièce et des conditions d'utilisation
comme la durée des charges appliquées, la nature des contraintes
de sollicitation et la température. Le HDPE est un polymère
semi-cristallin. L'introduction de branchements courts dans la chaîne
carbonée, favorisant l'encombrement stérique, abaisse la masse
volumique du HDPE et sa cristallinité.
I.4.2.Mise en oeuvre du PE:
Pendant la mise en oeuvre, le polymère est
mélangé à différents produits (stabilisants,
lubrifiants, plastifiants, charges..) pour élaborer une formulation qui
se présente le plus souvent sous forme de poudre ou de granulés.
Cette formulation est ensuite fondue (cas des polymères
semi-cristallins) ou plastifiée (cas des polymères amorphes),
à la fois par conduction thermique depuis les parois de l'outillage de
mise en forme et par dissipation d'énergie mécanique. Cette
matière thermoplastique très visqueuse est ensuite forcée
dans un outillage qui va donner une première forme au produit (tube,
jonc, film...), elle est en suite mise en forme est alors refroidie, dans
certain cas étirée ou bi étirée, pour obtenir le
produit final.
Etant donné leur faible conductivité thermique
et leur viscosité élevée, les matériaux
polymères ne se laissent pas mettre en oeuvre comme des matériaux
traditionnels. Il faut en effet provoquer leur fusion, puis les mettre sous une
pression suffisante pour pouvoir les forcer au travers des outillages de mise
en forme.
Les machines d'extrusion (Figure 5) sont des
équipements de mise en oeuvre les plus utilisés et au travers
desquelles, la plus grande quantité de matières thermoplastiques
est mise et forme. Les éléments actifs de ces machines sont une
ou plusieurs vis enfermées dans un Foureau, dont la température
peut être contrôlée par des éléments
chauffants et refroidissant. Ces vis sont entraînées par un moteur
électrique (parfois hydraulique) à vitesses variables au travers
d'un réducteur et d'un dispositif d'accouplement [5].
Le PEHD peut être transformé par d'autres
techniques :
* Extrusion de films par technique ''Chill - Roll'';
* Production de fils et de fibres à partir de film
extrudé - soufflés (fibrillation) ;
* Production de fils par filage.
Pour plus d'informations le lecteur pourra consulter l'ouvrage
[7].
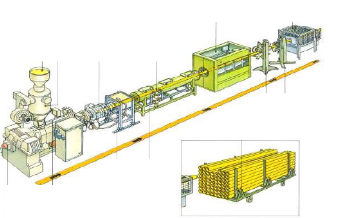
Figure 5: Représentation d'une
installation d'extrusion des tubes [5].
I.5. Application des plastiques en
tuyauterie:
Les tuyaux plastiques ont été utilisés
pour la première fois par les Allemands, au milieu des années
1930, dans des réseaux sanitaires d'évacuation. Leur emploi est
maintenant très diversifié et largement répandu dans les
pays industrialisés [6]. Le transport souterrain de l'eau et
d'égout a connu plutôt le béton, l'argile vitrifiée
et l'acier. Cependant, il y a une grande variété de tubes
plastiques souterrains comme le PVC et le polyéthylène à
haute densité. Une autre application concerne le transport d'eau chaude
est le (XPE). Ce dernier est un tube extrudé en
polyéthylène réticulé utilisé pour le
transport d'eau chaude.
Les plastiques sont les tubes de choix pour les lignes de
distribution de gaz à basse pression. Tandis que les composites et les
plastiques sont employés pour les lignes d'écoulement, de
collecte et de distribution. Actuellement, ils sont acceptés dans les
systèmes de transmission à haute pression de gaz naturel pour des
états d'étude. En raison de la facilité d'enroulement en
plus petits diamètres et de transport, les composites et les plastiques
sont un produit de substitution économique pour le tube d'acier.
Cependant il y a eu un essai limité d'un mélange
d'acier/composite dans une application de canalisation à transmission de
gaz naturel. Les résultats de cette recherche indiquent qu'il y a
quelques obstacles qui doivent être franchi pour fabriquer un tube de
composite à grand diamètre comme un choix permanent pour le
transport du gaz naturel à haute pression dans l'avenir [6]. Le Tableau
II donne les propriétés des plastiques et des matériaux
traditionnels employés en tuyauterie.
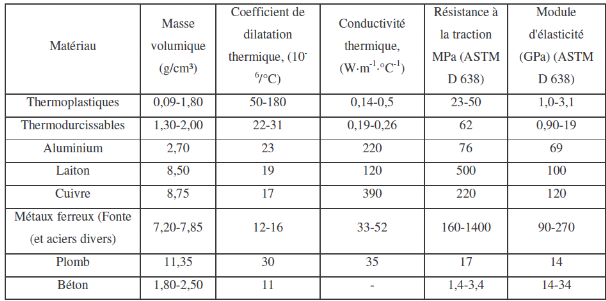
Tableau II : Propriétés des
plastiques et des matériaux traditionnels employés en transport
de fluides [5].
La discipline du développement technologique des
canalisations de gaz exige l'amélioration continue sur plusieurs fronts.
Les chercheurs prévoient un futur où les systèmes de gaz
sont plus fiables, et plus économiques que ceux d'aujourd'hui. Afin de
réduire le coût et d'améliorer l'efficacité du
contrôle de fuite de gaz naturel, GRI (Gas Research Institute) a
étudié l'utilisation de capteurs sensibles à distance, et
des techniques de formation d'image de fuite par laser qui tirent profit des
propriétés spectrales infrarouges d'absorption du gaz naturel.
Des systèmes prototypes ont été établis et ont
montré l'efficacité de ce procédé. D'autres
chercheurs ont réussi de fabriquer un matériau magnétique
pour des tubes de PE. Cette technologie facilite la localisation ainsi que
l'installation des canalisations. En ce qui concerne le contrôle des
réseaux, plusieurs méthodes de détection ont
été développées parmi lesquelles on cite
brièvement : techniques basées sur l'emploi de satellite afin de
détecter les éboulements potentiels qui sont dangereux ;
appareillage de contrôle de pression qui fournit une méthode
simple et beaucoup plus rapide pour surveiller et enregistrer
l'évolution de la pression, le temps et la température dans un
trancon de canalisation. Pour la préparation en "direct" des lignes de
gaz à l'intérieur du tube, un système robotique
automatisé est développé et manipulé à
distance économisant le temps et assurant la sécurité des
personnes [6].
I.5.1. Utilisations du polyéthylène dans
l'industrie de gaz:
A travers le monde et en Algérie, les résines de
polyéthylène de haute densité (HDPE) sont
transformées en grandes échelles en tubes et assemblages pour
construire des réseaux de transport et de distribution de gaz naturel.
Ces tubes se prêtent bien à l'usinage, on peut les couper,
raboter, tourner, etc....Ils sont antigelifs ce qui permet de les exploiter
dans un intervalle de température de +60 à -80°C.
Des statistiques récentes montrent que la
majorité des systèmes de gaz nouvellement installés dans
le monde sont exclusivement en polyéthylène en raison d'atouts
économiques et grâce aux avantages qu'ils offrent par rapport aux
systèmes à base de cuivre te d'acier. Le HDPE est employé
dans le transport du gaz naturel pour les lignes de distribution et
d'écoulement, aussi bien que dans quelques nouvelles applications comme
un composé avec les produits d'acier et de fibre. En Algérie ces
PE sont généralement importés par la SONELGAZ avec tous
les accessoires nécessaires pour la réalisation [8].
Les normes ISO 9080 et ASTM D2837 prévoient une vie
minimale de 50 ans à la pression de service pour les tubes de PE [5,6].
Cependant, on ne doit pas oublier même si le PE ne présente aucun
risque de corrosion, il est toujours un matériau qui vieillit et la vie
peut être affectée par divers facteurs tels que la contrainte
mécanique, la température, les conditions d'emploi et la
dégradation chimique de la structure. En conséquence, pour
obtenir des vies très longues, l'importance est accordée à
la qualité qui doit être strictement respectée de la
production de résine jusqu'au fonctionnement du réseau.
Cependant, il est important de souligner que tout matériau
destiné pour la production des tubes, devra poursuivre un programme de
stratégie d'essai afin d'examiner sa performance.
Le PEBD est transformé par extrusion en
profilés, mais surtout en tubes. Les tuyaux en PEBD (d'un
diamètre rarement supérieur à 100 mm), sont très
appréciés en agriculture, car, n'ayant pas la rigidité du
PVC, Ils peuvent être réceptionnés sur des tambours de
grand diamètre et transportés, enroulés, sur les lieux
d'utilisation. Là, ils sont déroulés en tranchée,
sur de grandes longueurs. Ce PEBD est, en général, coloré
en noir, par du noir de carbone fortement dispersé (2,3 %) [9], ceci
afin d'éviter un vieillissement prématuré. Le PEHD donne
des produits plus rigides. On peut, par mélange avec le PEBD obtenir des
tubes de rigidité intermédiaire entre les rigidités des
deux qualités de PE. Le mélange des granulés se fait en
toutes proportions et l'extrusion ne donne pas lieu à des
difficultés particulières. Les applications des
polyéthylènes sont : -Conduites de transport de pétrole,
fuel, gaz, eau salée.
-Conduites de ventilation et de dépoussiérage et
de transport de pâtes cellulosiques
-Irrigation (culture).et tubes de protection des câbles
téléphoniques.
I.5.2. Tubes récents en
polyéthylène:
À la fin des années quatre-vingt, le PE 80 a
été le matériau standard pour la distribution du gaz
naturel pour la gamme des bas diamètres et la pression moyenne (4
à 5 bar). L'introduction du PE 100, depuis une décade, a permis
le fonctionnement des tubes en PE dans des réseaux sous pression de 5
à 7 bars en toute sécurité sans risque de propagation
rapide de fissure [6]. Aujourd'hui, le PE 100 est employé pour des
pressions jusqu'à 10 bars dans la distribution de gaz naturel. Ce
matériau offre 25% de plus de la résistance à long terme,
en réduisant l'épaisseur du tube [5].
Les avancements dans les techniques associées ont pu
mener à l'utilisation de composites renforcés, un processus
certifié qui applique le renfort de verre-résine au tube d'acier
pour former une barrière protectrice externe avec une résistance
circonférentielle additionnelle. Le tube d'acier avec la sur-enveloppe
composée font ensemble un nouveau type de tube (CRLP) qui a des
caractéristiques exceptionnelles de résistance avec des avantages
positifs en termes de poids et de résistance à la corrosion. Deux
kilomètres de tubes CRLP avec un diamètre de 609,6 mm
développés par la "NCF industries" ont été
installés en hiver 2001. La compagnie "TransCanada Pipelines" du
nord-ouest du Canada suit régulièrement le comportement de ce
nouveau type de pipeline pour mesurer l'impact de son utilisation
étendue [7].
En mars 2001, la SDE (Steel Dragon Enterprise Co) a
établie le premier "Dragonpipe". Ce dernier est un tube ondulé en
HDPE, très résistant et fabriqué par extrusion. Il est
disponible en diamètres dans la gamme 300 mm à 1500 mm en
longueurs de 6 m. Il est destiné pour les applications de construction,
drains de route, drainage agricole et drains de bâtiment [10]. Il est
clair que les nouvelles applications de tubes en polymères sont
très larges et la combinaison avec d'autres matériaux offre des
solutions avantageuses à plusieurs problèmes techniques connus
par l'industrie.
II.1. Introduction:
La compétition oppose toujours les métaux aux
matériaux polymères pour la réalisation de pièces
multiformes destinées à être utilisées dans des
domaines variés comme le secteur de l'automobile, des prothèses
biomédicales, de l'aéronautique, les applications
électroménagères et autres. Les polymères
présentent l'avantage d'être mis en oeuvre plus facilement lors de
la production par moulage ou par extrusion (Figures 1 ; 2 et 3). Cependant,
après moulage les pièces polymériques peuvent encourir la
probabilité de voir leur structure se transformer par cristallisation en
quelques jours, notamment en surface, et les cotes peuvent ne plus être
dans la tolérance prévue par le design. Ainsi, les techniques de
mise en forme et de fabrication doivent être impérativement
adaptées aux comportements spécifiques du polymère pour
l'application désirée [5].
Les exigences des stylistes et concepteurs imposent bien
souvent des mises en forme très compliquées ayant des cotes
extrêmement précises nécessitant, parfois, une fabrication
de petites séries comme le cas des coudes de diamètres
importants. Néanmoins, il faut surveiller les dérives de
coût de fabrication, ce qui est rendu plus aisé par des
conceptions technologiques nouvelles qui permettent de regrouper plusieurs
fonctions dans la même pièce, avec pour conséquence une
réduction du nombre de pièces unitaires et du nombre
d'opérations de coupe, d'usinage et d'assemblage.
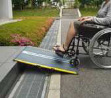
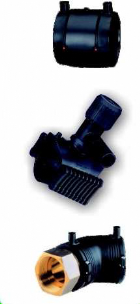
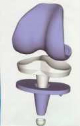
Figure 6: Prothèses
Figure 7: Un tapis en PE. Figure
8: Raccords
avec Insert en PE.
pour les tubes en PE.
Comme les polymères usuels ne sont
généralement pas conducteurs électriques, l'usinage par
électroérosion n'est donc plus possible. D'autre part, l'usinage
par ultrasons convient aux métaux durs, ce qui n'est pas le cas des
plastiques. Cela limite les procédés à l'usinage
conventionnel, souvent qualifié d'usinage par enlèvement de
copeaux et à la découpe par laser ou au jet d'eau [2,11].
Cette étude expérimentale est conçue dans
le but d'établir une loi de prédiction de la rugosité de
la surface obtenue en fonction des paramètres du régime de coupe
lors de l'usinage des tubes en HDPE-80.
II.2. Facteurs influençant la qualité de
surface en tournage:
Plusieurs facteurs affectent la qualité et
l'intégrité de la surface en tournage. Ces derniers peuvent
être classés en facteurs concernant le matériau de la
pièce à usiner (dureté, propriétés
métallurgique...), facteurs liés à l'outil de coupe
(composition chimique du matériau, géométrie...) et les
paramètres de coupe. La qualité de la surface est
influencée par la dureté et les propriétés du
matériau usiné. Il est prouver que la rugosité de la
surface diminue avec l'augmentation de la dureté de la pièce,
pour le matériau polyéthylène elle est très
inférieure à celle des matériaux coupant, ce qui n'influe
donc guère sur la duré de vie de l'outil de coupe [5].
Theile est al. [5] ont prouvé que la
géométrie de l'outil de coupe présente un impact important
sur la contrainte résiduelle et risque de provoquer des vibrations. Une
arête arrondie favorise l'apparition des contraintes compressives.
D'autre part le rayon du bec de l'outil a un effet considérable sur
l'intégrité de la surface en diminuant la hauteur des stries. En
effet la rugosité est inversement proportionnelle au rayon. Les
paramètres de coupe ont des effets considérables sur la
qualité de surface obtenue en tournage. L'augmentation de la vitesse de
coupe et la diminution de l'avance permettent la diminution de la
rugosité et améliorent la qualité de la surface. Du point
de vue théorique, la profondeur de passe a moins d'importance que
l'avance. Pour un outil correctement affûté, la rugosité
est directement liée à la valeur de l'avance par tour.
II.2.1 Influence des paramètres du régime
de coupe, en chariotage, sur l'état de surface
obtenue :
Dans le tournage la surface engendrée n'est pas
rigoureusement cylindrique, elle comporte des sillons hélicoïdaux
résultants de la forme plus ou moins pointue de l'outil de coupe et du
mouvement hélicoïdal outil/pièce. Ces sillons ont un profil
d'autant plus profond que le rayon du bec de l'outil est faible. Par ailleurs
ils sont d'autant plus larges que l'avance par tour est grande [16]. D'autre
part, la forme de la surface engendrée par l'outil peut être
affectée par les perturbations de la trajectoire de l'outil par rapport
à la pièce, occasionnées par des vibrations importantes de
l'un de ces éléments (ou des deux). Lorsque les conditions
dynamiques (flexibilité et inertie des éléments,
insuffisance d'amortissement mécanique) sont telles que les vibrations
oscillatoires de cette trajectoire deviennent autoentretenues il en
résulte des perturbations périodiques de la surface
découpée. Elles prennent la forme de marques ou de stries plus ou
moins accusées, qui peuvent modifier sensiblement la rugosité du
profil idéal défini par la trajectoire théorique de
l'outil [17].
La production de pièces en matières plastiques
doit prendre en compte, à part égale, les conditions de
fabrication, les caractéristiques propres du matériau, le type de
sollicitation et les conditions d'utilisation, ainsi que les interactions entre
ces différents critères. Les précautions essentielles
consistent à éviter toute déformation. Il faut penser
aussi que l'effort d'usinage est inférieur à celui
nécessaire pour usiner une pièce similaire en acier; il n'est
donc pas nécessaire de serrer la pièce plastique avec le
même effort. Les plastiques sont plus souples et fléchissent
d'avantage que les aciers; c'est pourquoi les profondeurs de passe et les
avances ne doivent pas être excessives. Par fois le refroidissement n'est
pas nécessaire, c'est le cas de certains usinages de matières
plastiques à faible coefficient de frottement tels que le
polyéthylène. Dans ce cas très particulier, il peut
être intéressant de prévoir quand même un soufflage
d'aire comprimé pour repousser le copeau et éviter qu'il ne
vienne s'enrouler autour de l'outil. Il est en effet fréquent que le
copeau ne se fragmente pas pendant l'usinage.
II.2.2 définition des critères de
Rugosité :
Les paramètres de la rugosité de surface sont
codifiés par les normes : ISO 468-1982, ISO 4287/1,2-1984 et
ANSI/ASME B46.1-1985. Cette normalisation porte sur des profils dans un espace
à deux dimensions. Les paramètres de la rugosité
définissent seulement les caractéristiques
micro-géométriques de la surface. Une valeur
déterminée de chaque paramètre peut correspondre à
plusieurs surfaces obtenues par différentes techniques
d'élaboration. Évidement les propriétés
mécaniques de chacune de ces surfaces peuvent être
différentes, c'est pourquoi pour caractériser exhaustivement une
surface, il faut souvent préciser plusieurs paramètres
accompagnés du mode d'élaboration de cette surface. Pour cette
étude la caractérisation de la qualité de la surface
usinée a été limitée aux trois critères de
rugosité (Ra, Rt et Rz) [18].
Selon les normes ISO 4287/1-1984 et ANSI/ASME B46.1-1985 [19]
les trois critères de rugosité, précédents, sont
définis comme suit :
La hauteur des irrégularités sur dix points
Rz : Moyenne des valeurs absolues des hauteurs, des cinq saillies du
profil les plus hautes et des profondeurs des cinq creux du profil les plus
bas, à l'intérieur de la longueur de base.
(1)
La hauteur maximale du profil Rt : Distance
entre la ligne des saillies et la ligne des creux à l'intérieur
de la longueur de base.
L'écart moyen arithmétique du profil
Ra : Moyenne arithmétique des valeurs absolues des
écarts du profil dans les limites de la longueur de base.
(2)
Figure 10 : Hauteur des
irrégularités sur dix points Rz [19]
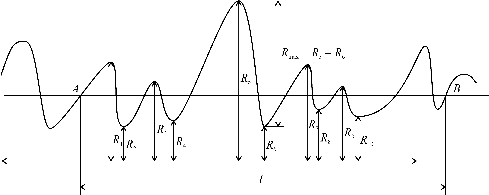
Figure 11 : Écart moyen
arithmétique du profil Ra [19]
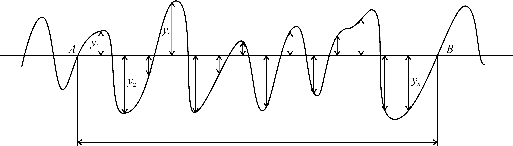
II.3. Comportement des polymères vis avis de
l'usinage:
Le point de fusion et la conductibilité thermique des
plastiques, en général, sont des valeurs inférieures
à celles des métaux et il est donc nécessaire de limiter
au minimum la chaleur engendrée en diminuant la friction. Des outils
émoussés ou bien des tranchants qui raclent plutôt qu'ils
ne coupent provoquent un dégagement de chaleur excessif, qui risque de
générer des contraintes internes préjudiciables à
géométrie et à la fiabilité de la pièce
finie. Les arrêtes des outils doivent donc être toujours
parfaitement affûtées et la dépouille doit être
suffisante pour garantir que seul l'arête de coupe soit en contact avec
la pièce usinée. On obtient généralement les
meilleurs résultats en travaillant à très grandes vitesses
avec une faible avance et des outils bien affûtés et lisses. Pour
les pièces de faibles sections, une passe trop profonde est susceptible
de provoquer son fléchissement. L'utilisation d'une lunette est
conseillée pour les pièces assez longues, et pour les plastiques
ayant un point de fusion bas, la lunette sera équipée de galets
car des sabots risqueraient de porter la pièce en fusion. L'emploi d'un
fluide de refroidissement est indispensable pour la réalisation de ces
pièces.
Lors du tournage de pièces de précision, il faut
éviter soigneusement toute surchauffe de la pièce tournée,
faute de quoi on s'expose à réaliser une passe excessive due
à la dilatation thermique de l'ébauche. Les mesures des
pièces doivent toujours être effectuées à
température ambiante, car le coefficient de dilatation dans le cas des
plastiques est parfois jusqu'à 10 fois supérieure à celui
de l'acier [12]. Dans ces cas, on peut également travailler avec
refroidissement par fluide, quoi que, par ailleurs certains plastiques se
travaillent aussi bien sans refroidissement.
Parmi les caractéristiques des polymères qui ont
une influence sur les opérations d'usinage on peut citer [13] :
II.3.1 La dilatation et la conductivité
thermique : Les matières plastique non chargées ont
des coefficients de dilatation thermique généralement compris
entre 50 et 200 m/m.k. ce sont des matériaux isolants, la combinaison de
ces deux caractéristiques, fait que la chaleur engendrée par
l'opération d'usinage reste concentrée sur la zone usinée
et entraîne une déformation thermique importante, voire un risque
de dégradation thermique.
II.3.2 Le module d'élasticité et la
dureté : Les plastiques sont très souples par
rapport aux aciers (modules compris entre 1000 et 2000 Mpa) et beaucoup moins
durs ce qui impose, par exemple, des précautions de serrage
particulières pour ne pas déformer la pièce ni en marquer
la surface.
II.3.3 Les contraintes internes: Les
pièces plastiques contiennent souvent des contraintes internes
après moulage, dues, en particulier, au retrait de la matière
passant de l'état liquide à l'état solide. Il arrive
fréquemment que l'usinage modifie la répartition de ces
contraintes. Dans l'étude [14] il a été prouvé que
le tournage préserve la rigidité mais perd beaucoup sur
óf et óy. Des précautions doivent
par conséquent être prises pour qu'il n y ait pas d'accumulation
de contraintes susceptibles d'entraîner des fissurations. Un des
remèdes peut être de pratiquer un requit des pièces
après moulage. La vitesse de refroidissement est un
élément essentiel pour réduire les contraintes internes.
Plus la température de recuit est élevée, plus la baisse
de température doit être lente. Parfois, l'usinage est
réalisé après dégrossissage d'une ébauche.
Dans ce cas, l'ébauche est généralement sans contraintes
internes car celles-ci sont libérée lors du
dégrossissage.
II.3.4 L'usure des outils: Une grande partie
des plastiques non chargés ont un comportement autolubrifiant et ne
créent pas d'usure importante des outils. Par contre, Ceux qui
comportent des charges minérales (verre) ont tendance à accentuer
l'usure des outils traditionnels d'usinage par enlèvement de copeaux.
II.3.5 L'hygrométrie: Certains
polymères absorbent un taux important d'humidité (polyamide, par
exemple). Les phénomènes d'absorption ne sont pas
instantanés mais se produisent au bout de quelques minutes, voire de
quelques heures. Cela modifie les caractéristiques mécaniques et
dimensionnelles. Cette évolution entre l'instant où on usine le
polymère (échauffement donc séchage) et celui où on
l'utilise (ambiance humide éventuellement donc dimensions
différentes). Il faut donc tenir compte du comportement du
polymère en présence d'humidité, de la présence ou
non d'un liquide de refroidissement, de l'ambiance hygrométrique de
l'atelier, du fait que l'échauffement dû à l'usinage va
sécher le matériau en surface, etc....
II.3.6 L'électrostatique: Certains
plastiques développent des charges électrostatiques
superficielles importantes par frottement, qui attire les copeaux ou la poudre
issus de l'usinage.
II.4. Conditions d'usinage du
polyéthylène de haute densité :
Les matériaux d'outils peuvent être en
acier rapide qui sont les moins chers à l'achat. Ils ont une
durée de vis moins longue, surtout avec les matériaux
renforcés de fibre de verre. Les carbures, qui ont une plus grande
résistance à l'abrasion que les aciers rapides et ils ont un bon
rapport prix/usure. Pendant l'usinage, Parfois le refroidissement n'est pas
nécessaire. C'est le cas de certains usinages de matières
plastique à faible coefficient de frottement, par exemple
polyéthylène. La précaution essentielle consiste à
éviter toute déformation. Il faut penser aussi que l'effort
d'usinage est inférieur à celui nécessaire pour usiner une
pièce similaire en acier ; il n'est donc pas nécessaire de serrer
la pièce avec le même effort. Ce qui nous à pousser
d'utiliser des montages spéciaux ; pour l'alésage en à
pénétrer notre tube dans tube en acier, pour éviter toute
déformation, pendant l'usinage et surtout à faible
épaisseur, par contre pour le chariotage en à utiliser un mandrin
en bois. Les mesures des cotes doivent toujours être effectuées
après retour de la pièce à la température ambiante.
Une tolérance de 0.1 à 0.2% de la cote nominale est accessible
sans précautions spéciales.
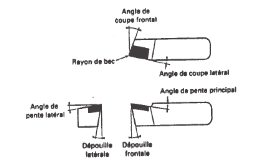
La Figure (9) définit différent angle d'un outil
de tour, les autres paramètres de coupes sont illustrés sur le
Tableau (III).
Figure 9 : Géométrie type d'un
outil de tournage [5].

Tableau III : Tournage du
polyéthylène [15].
II.5. Les efforts de la coupe :
Les efforts de coupe sont à l'origine des
déformations plastiques et donc des élévations de
température qui se produisent au cours de la coupe. Pour toutes autres
conditions de coupe égales, l'augmentation de la vitesse de coupe ne
s'accompagne pas d'une variation notable des efforts de coupe (10% de baisse
environ), alors que l'augmentation de la vitesse d'avance entraîne une
augmentation de la valeur de l'effort tangentiel (relation linéaire:
l'effort double environ quand la vitesse d'avance double).
II.5.1. Définition et intérêt de
leur mesure :
Le tournage longitudinal donne lieu à un effort de
coupe dont la décomposition dans trois directions
privilégiées peut servir de base à la définition
des efforts de coupe pour toutes les opérations d usinage [16].
Ø Fz : composante dans
le sens de la vitesse de coupe, appelée effort tangentiel ou effort
principal de coupe.
Ø Fx: composante dans le sens
de l avance, appelée effort d'avance ou effort axial en tournage, joue
un rôle fondamentale dans le processus de coupe.
Ø Fy : composante dans
le sens perpendiculaire aux deux autres, appelée effort de refoulement
ou effort radial, n'a qu'une importance secondaire est disparaît dans le
cas de coupe orthogonale pure.
Fz
Fy
Fx
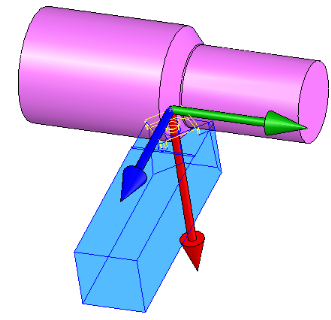
Figure 10 : Les composantes de l'effort de
coupe.
La connaissance des efforts de coupe est à la base de
puissance nécessaire à la coupe. Quand on veut connaître le
rendement mécanique d une machine outil, on a besoin de savoir quelle
est la puissance prise à l outil, et donc d avoir des renseignements sur
les efforts de coupe.
La valeur des efforts de coupe sert aussi à dimensionne
les organes de machine et à prévoir les déformations des
pièces. Elle intervient dans la précision d'usinage, dans les
conditions d'apparition des vibrations, au broutage, et indirectement dans la
formation de l'état de surface.
Enfin, les efforts de coupe, étant en relation avec les
propriétés mécaniques du métal, dans le processus
de formation du copeau.
Les formules empiriques les plus utilisées pour le
calcul pratique sont les suivantes [17]:
Fz = C1 PX
1. ay1. Vn 1. KV
(3)
Fy = C2
PX 2. ay 2 . Vn 2. KP
(4)
Fx = C3 PX
3. ay 3. Vn 3. Ka.
(5)
Avec:
Les coefficients C1, C2,
C3 sont des constantes qui dépendent des
propriétés mécaniques du métal à usiner et
conditions de son usinage.
Les coefficients KV, KP, Ka
se sont les coefficients correctif relatif aux conditions d'usinage
concrète.
Les coefficients X1,2,3 , y1,2,3
, n1,2,3 se sont des exposants qui caractérise le
degré d'influence des paramètres p,a , v sur les forces de coupes
Fz , Fx , Fy.
II.5.2. Influence des différents facteurs sur
les composantes de l'effort de coupe :
- Les propriétés mécaniques du
matériau à usiner :
La valeur de réaction Fz , Fx , Fy est
proportionnelle à la charge rupture à la traction Rt et à
la dureté HB du métal à usiner.
- Influence de la profondeur de passe et l'avance:
Avec l'augmentation des ces deux facteur, la section droit du
copeau s'accroît, de même que le volume du métal
déformé, il en résulte que le métal résiste
plus à la formation du coupeau et la valeur des composantes Fz ,
Fx et Fy nécessaire pour assurer la coupe est plus importante. En
chariotage, la profondeur de passe intervient d'une manière plus
accentuée sur les efforts de coupe que l'avance.
- Influence de la vitesse de
coupe : On peut distinguer 03 zones (Figure 11) ;
Ø Zone A : diminution de F avec
les vitesses bases due à une diminution de frottement copeau - outil.
Ø Zone B : l'apparition de
l'arrête rapportée provoque une augmentation des frottements et
par suite de l'effort tangentiel de coupe.
Ø Zone C : La VC
augmente arête rapportée diminue. L'effort tangentiel de
coupe F diminue et se stabilise vers 200m/min.
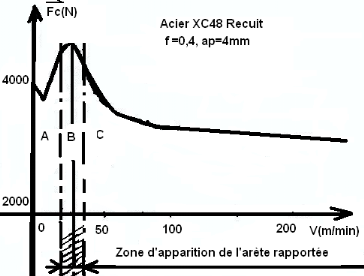
Figure 11 : Influence de la vitesse
de coupe sur l'effort de coupe.
- Influence de l'angle d'attaque (
) :
Lorsque () est négatif l'effort
tangentiel de coupe est important au fur et à mesure que augmente,
l'effort de coupe diminue et prend une valeur stable à partir de
30° (Figure 12) : Petit est grand la résistance
imposée à l'outil attaquant la pièce usiner est
importante.
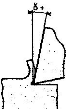
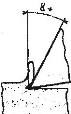
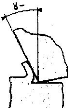
Figure 12 : Influence del'angle
d'attaque.
- Influence de l'angle de direction principale
(÷) :
Avec une avance inchangée, le copeau devient plus fin
au fur et à mesure que l'angle ÷r diminue. Ceci conduit
à une augmentation de l'effort de coupe, la réduction de l'angle
de position est limitée par les dégradations croissantes de la
stabilité (forte augmentation des efforts d'avances et de
pénétration tendance au broutage) figure 13.
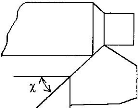
Figure 13 : Influence de l'angle de
direction principale.
Influence de matériau de
coupe :
Les matériaux de coupe revêtus, en particulier
ceux avec des revêtements TiN ou Ti (C,N), accusent un frottement moindre
et des efforts de coupe plus faible que les matériaux de coupe non
revêtus. Les faces d'attaque superfinies (rectifiées,
rodées, polies) et dotées d'une arête de coupe dure et
tranchante, réduisent les efforts de coupe (Figure 14).
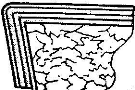
Figure 14 : Matériau de coupe.
III.1. Introduction:
En Algérie, le réseau de distribution de gaz
naturel compte plus de 22000Km construits en polyéthylène. Le
choix de ce dernier (en fait des copolymères d'éthylène
à faible proportion de butène ou d'hexène voir
d'octène) pour la fabrication des tubes de distribution du gaz
découle des nombreux avantages technico-économiques
procurés par ce matériau. Le PE est un matériau
léger, ce qui facilite les opérations de manutention et de mise
en oeuvre sur le terrain. Il possède une bonne résistance
à la corrosion, quelles que soient les conditions au sol, ce qui permet
d'éviter les surcoûts dus à l'application d'une protection
passive ou active. De plus, les systèmes en PE supportent les effets des
mouvements du sol dus aux instabilités et aux grandes variations de
température. Du fait de leur bonne résistance à la
fissuration, les canalisations en PE présentent un degré de
fiabilité élevé dans des conditions d'utilisations
normales. Dans ces conditions leur durée de vie est estimée
à plus de 50 ans sur la base de courbes de régression construites
à partir d'essais accélérés en pression hydraulique
[18].
En service, Ces tubes en polyéthylène subissent
des charges internes et des charges externes qui provoquent des
déformations et altères leurs propriétés
mécaniques.
Afin de mesurer ces propriétés
mécaniques, la préparation d'éprouvettes d'essais
mécaniques, directement extraites à partir du tube pour conserver
l'histoire thermomécanique intrinsèque et ayant un état de
surface comparable a celui des éprouvettes obtenues par moulage ou par
injection, s'impose.
C'est dans ce cadre que s'inscrit cette étude
expérimentale concernant le suivi des efforts de coupe
générés et de la rugosité de la surface
usinée, lors de l'usinage des tubes en HDPE-80, en fonction des
paramètres du régime de coupe.
III.2. Procédure expérimentale:
III.2.1. Planification des expériences et
équipements utilisés :
Cette série d'expérience concerne l'usinage d'un
tube en HDPE-80, par un outil en carbure métallique. Les variables
considérées sont la vitesse de coupe (Vc), l'avance par tour (f)
et la profondeur de passe (ap). Les paramètres de sortie sont les
composantes de l'effort de coupe et les critères de rugosité de
la surface usinée.
Les essais sont planifiés suivant la méthode
unifactorielle et multifactorielle.
III.2.1.1. Plan des essais unifactoriels :
Dans ces essais il est question d'étudier
l'évolution de la rugosité de la surface usinée et des
efforts de coupe en fonction de la vitesse de coupe (Tableau IV), de l'avance
par tour (Tableau V) et de la profondeur de passe (Tableau VI ) , suivant les
plans suivants :
f, [mm/tr]
|
0.14
|
0.24
|
0.36
|
0. 40
|
0.56
|
Vc, [m/min]
|
35
|
ap, [mm]
|
3
|
Tableau IV : Variation de l'avance
par tour.
f, [mm/tr]
|
0.14
|
Vc, [m/min]
|
30
|
65
|
90
|
125
|
180
|
ap, [mm]
|
3
|
Tableau V : Variation de la vitesse de
coupe.
f, [mm/tr]
|
0.14
|
Vc, [m/min]
|
35
|
ap, [mm]
|
2
|
3
|
4
|
Tableau VI : Variation de la profondeur
de passe.
III.2.1.2. Plan des essais multifactoriels :
Dans cette série d'essais nous avons
étudié la variation des efforts de coupe et de la rugosité
de la surface usinée en fonction de la vitesse de coupe (Vc), l'avance
par tour (f) et la profondeur de passe (ap), simultanément par la
méthode multifactorielle suivant les règles de construction du
plan de Taguchi [19]. Une série d'essais de 9 expériences suivant
la table orthogonale standard L9(3)3 est
réalisée.
N°
|
Vc, [m/min]
|
f, [mm/tr]
|
ap, [mm]
|
1
|
30
|
0.14
|
2
|
2
|
180
|
0.36
|
2
|
3
|
90
|
0.56
|
2
|
4
|
90
|
0.14
|
3
|
5
|
30
|
0.36
|
3
|
6
|
180
|
0.56
|
3
|
7
|
180
|
0.14
|
4
|
8
|
90
|
0.36
|
4
|
9
|
30
|
0.56
|
4
|
Tableau VII : Plan des essais
multifactoriels de TAGUCHY
III.2.2. Equipements
utilisés :
- Machine-outil :
L'usinage est réalisé sur un tour à
charioter et fileter de la société Tchèque
« TOS-TERENCIE »; modèle SN40 de puissance sur la
broche égale à 6,6 KW (figure 15).
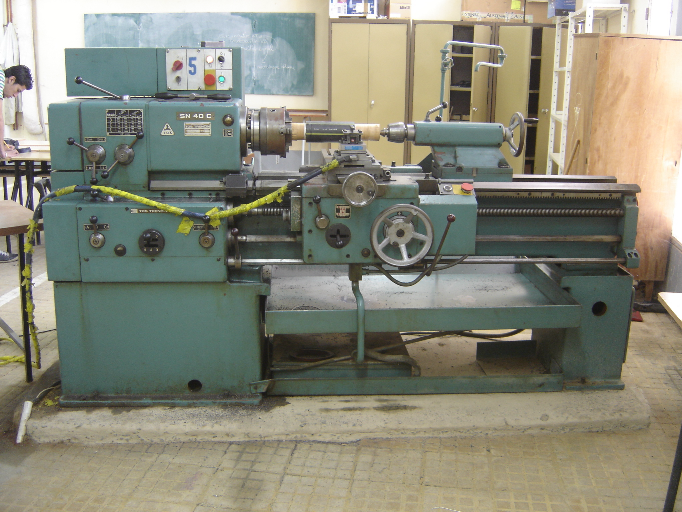
Figure 15 : Tour universel SN40C
- Matériau à usiner :
Nous avons utilisé comme matière usinée,
le polyéthylène de haute densité
« HDPE-80 », dont les caractéristiques chimiques et
mécaniques sont résumées dans le chapitre I.
La pièce est sous forme de tube de diamètre
extérieur D= 90 mm, d'épaisseur e= 10 mm et de longueur L = 200
mm.
- Outil de coupe utilisé:
La plaquette de coupe utilisée est de forme
carré en carbure de désignation GC3015(K10), fourni par Sandvik.
Le porte outil est de désignation CSBPR2525M12 avec une
géométrie de la partie active matérialisée par les
angles suivants: á= +5°; ÷r= 75°; ã= +7°,
ayant un rayon du bec de 0,8mm.
- Mesure des efforts de coupe:
Depuis plus de 35 ans, Kistler utilise le système de
mesure piézoélectrique des forces (Figure 16), au profit d'une
technique innovatrice, apportant une contribution exemplaire à la
sécurité et à la rentabilité, ce système de
mesure se distingue beaucoup des autres méthodes de mesure, les forces
agissant sur l'élément en quartz sont converties en charges
électriques proportionnelles.
Le chemin de mesure est de quelques millièmes de
millimètre.
En tournage la pièce à usinée est
animée d'un mouvement de rotation, l'outil de coupe doit être
solidement fixé au dynamomètre, qui est monté sur le
chariot de la machine-outil.
La force ainsi produite lors du processus de tournage est
alors directement exprimée par 3 composantes grâce au
dynamomètre multi-composantes à savoir:
- Force axial : Fx (Fa).
- Force radial : Fy (Fp).
- Force tangentiel : Fz (Fv).
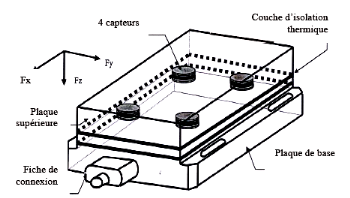 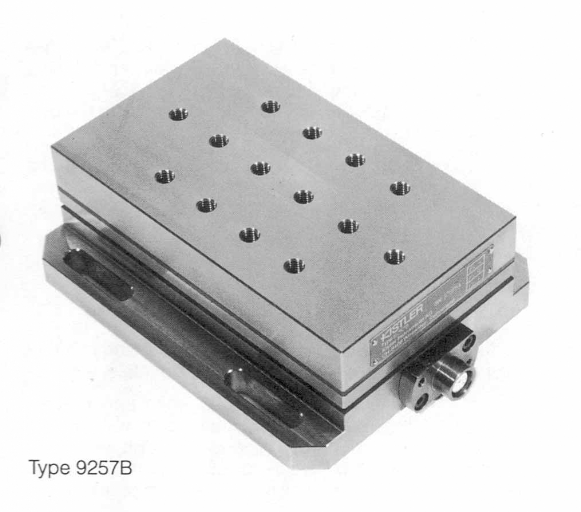 Figure 16 : Plate forme de mesure des
efforts « Kistler »
Chaîne de mesure :
Dynamomètre à 3 composantes (9257 B) : Le
porte outil type 9403 est employé pour des outils de tournage avec une
section maximum de 26x26 (figure17).
v Grande rigidité, fréquence propre très
élevée.
v Large gamme de mesure.
v Bonne linéarité, sans
hystérésis.
v Faible interaction (<1%).
v Utilisation simple (prêt à l'emploi).
v Construction compacte.
v Résistant au lubrifiant selon mode de protection IP
67.
v Câble spécial à haute isolation de la
connexion entre le dynamomètre et l'amplificateur (5 m de longueur; 8 mm
de diamètre).
v Amplificateur multi canaux; destiné aux mesures des
efforts de coupe.
v Oscilloscope.
v Ordinateur personnel PC.
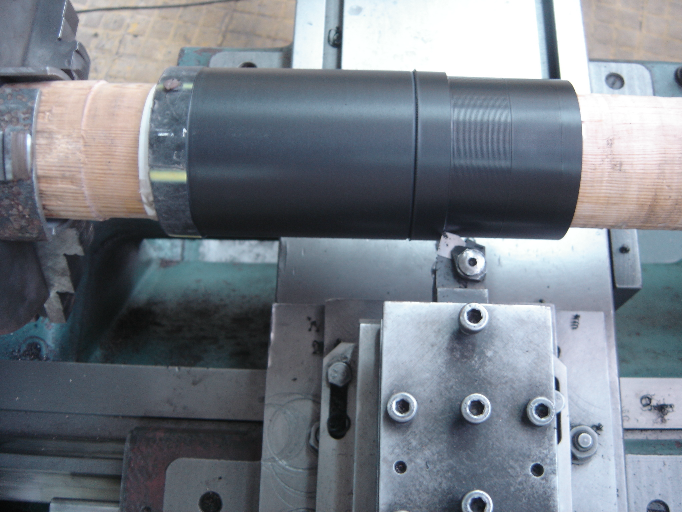
Figure 17 : Chaîne de mesure des
efforts de coupe.
- Rugosimètre :
Pour la mesure des différents critères de
rugosité (Ra, Rt et Rz), nous avons utilisé un rugosimètre
(2D) Surftest 301(Mitutoyo), équipé d'une imprimante de profil de
rugosité (fig18.). Ce dernier est
constitué d'une pointe en diamant (palpeur), avec un rayon de pointe de
5ìm se déplaçant linéairement sur la surface
mesurée. Afin d'éviter les erreurs de reprise et pour plus de
précision, la mesure de la rugosité a été
réalisée directement sur la machine et sans démontage de
la pièce.
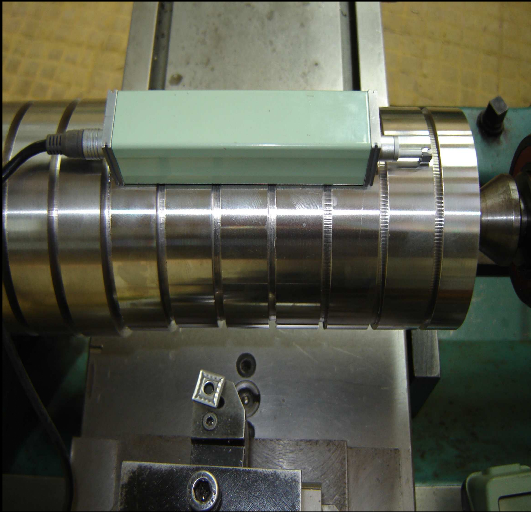 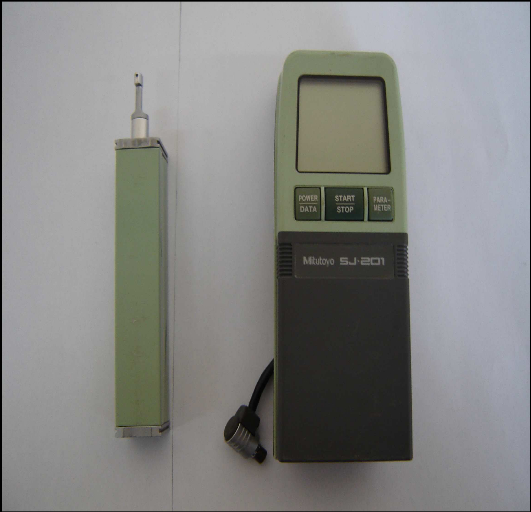
Fig18. Dispositif pour mesurer la
rugosité sans démonter la pièce
III.3. Résultats
expérimentaux :
III.3.1. Influence des paramètres du
régime de coupe, en chariotage, sur l'état de surface
obtenue :
Pour cette étude la caractérisation de la
qualité de la surface usinée a été limitée
aux trois critères de rugosité (Ra, Rt et Rz).
Les Figures 19,20 et 21 expriment l'influence des
éléments du régime de coupe (Vc, ap et f) sur la
rugosité obtenue.
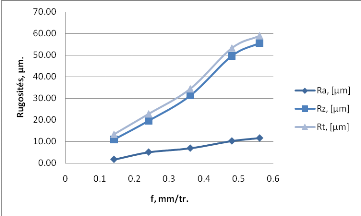
Figure 19 : Evolution de la
rugosité en fonction de l'avance (Vc=30m/min ; ap=3mm)
L'avance par tour possède l'effet le plus
significatif, en effet sur la courbe d'évolution de la rugosité
en fonction de l'avance (Figure 19), on constate une augmentation importante
des trois critères de rugosité avec l'augmentation de l'avance
dans le cas du polyéthylène HDPE comme dans le cas de plusieurs
autres matériaux tels que les aciers et les composites à base
polymérique,... etc. Ceci est principalement dû à la
cinématique de coupe. Les résultats des essais (Figure 20)
montrent que la profondeur de passe apporte une légère
augmentation des critères de rugosité. La vitesse de coupe
possède une influence significative sur la rugosité de surface,
les résultats obtenus (Figure 21) montrent, aussi, que l'état de
surface du tube s'améliore lorsque la vitesse de coupe augmente.
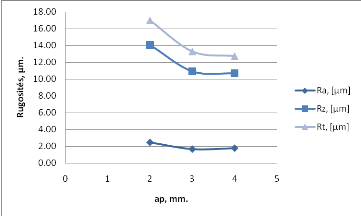
Figure 20 : Evolution de la
rugosité en fonction de la profondeur de passe
(Vc=30m/min ; f=0,14mm/tr)
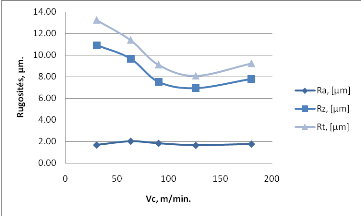
Figure 21 : Evolution de la
rugosité en fonction de la vitesse de coupe
(f=0,14mm/tr; ap=3mm).
Les résultats de la variation des composantes des
efforts de coupe pour les différentes combinaisons des
éléments du régime de coupe (Vc, f, ap), établis
selon les règles de construction du plan de Taguchi (la
table orthogonale standard L9(3)3), sont
représentés sur le tableau XIII :
N°
|
Vc, [m/min]
|
f, [mm/tr]
|
ap, [mm]
|
Ra, [um]
|
Rz, [um]
|
Rt, [um]
|
1
|
30
|
0.14
|
2
|
2.47
|
14.08
|
16.99
|
2
|
180
|
0.48
|
2
|
8.55
|
41.69
|
43.28
|
3
|
90
|
0.56
|
2
|
10.78
|
50.60
|
51.95
|
4
|
90
|
0.14
|
3
|
1.84
|
7.53
|
9.12
|
5
|
30
|
0.48
|
3
|
10.18
|
49.59
|
53.26
|
6
|
180
|
0.56
|
3
|
11.34
|
50.65
|
52.23
|
7
|
180
|
0.14
|
4
|
1.69
|
6.99
|
8.43
|
8
|
90
|
0.48
|
4
|
8.91
|
42.05
|
45.16
|
9
|
30
|
0.56
|
4
|
12.06
|
57.09
|
60.00
|
Tableau XIII : Résultats des
essais des rugosités.
III.3.2. Influence des paramètres du régime
de coupe, en chariotage, sur les composantes des efforts de coupe :
La chaine de mesure, figure 17, permet
d'obtenir les profils des efforts en fonction du temps de coupe tel que
présenté dans la figure 22. Le traitement de ces
résultats, par le logiciel Dynoware, permet l'obtention d'une valeur
moyenne des composantes de l'effort de coupe pour chaque essai.
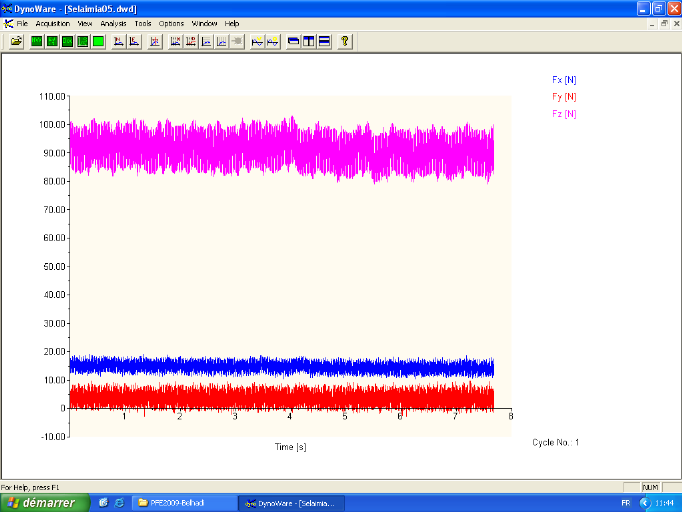
Figure 22 : Variation des composantes
de l'effort en fonction du temps.
Les résultats présentés sur les figures
23, 24 et 25 illustrent l'évolution des efforts de coupe en fonction des
paramètres d'usinage (Vc, f, ap). La figure 23 montre qu'une
augmentation de la vitesse de coupe conduit à une diminution des
composantes de l'effort de coupe, ceci est dû à
l'élévation de la température dans la zone de coupe qui
rend le métal travaillé plus plastique et par conséquent
l'effort nécessaire pour la coupe diminue. Il est à noter aussi
que pendant l'usinage du Polyéthylène il n'y a pas d'apparition
de l'arête rapportée, et les efforts mesurés sont beaucoup
moins importants que ceux mesurés lors de l'usinage des essais. Les
résultats montrent aussi que l'effort tangentiel est
prépondérant par rapport aux deux autres efforts (Fy et Fx) ce
qui n'est pas le cas lors de l'usinage des aciers, Ceci peut être
expliqué par la différence des géométries des
parties actives des outils d'usinage.
Les résultats de l'influence de l'avance sur les
efforts de coupe (figure 24), montrent une augmentation des efforts de coupe
avec l'augmentation de l'avance, puisque cette dernière fait
accroître la section du copeau cisaillée et le métal
résiste plus à la rupture et nécessite un effort plus
grand pour l'enlèvement du copeau. On remarque que l'effort tangentiel
est toujours prépondérant suivi par l'effort axial et en dernier
lieu par l'effort radial et cela pour toutes les avances testées.
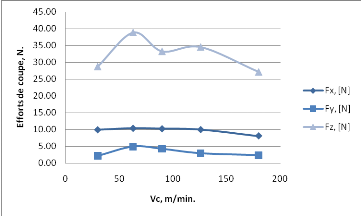
Figure 23 : Evolution des efforts de
coupe en fonction de la vitesse de coupe
(f=0,14mm/tr; ap=3mm).
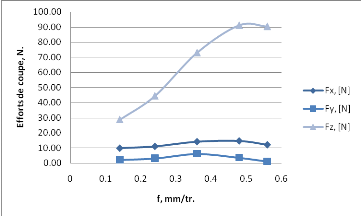
Figure 24 : Evolution des efforts de
coupe en fonction de l'avance
(Vc=30m/min ; ap=3mm)
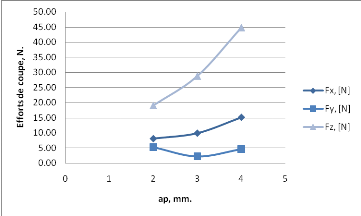
Figure 25 : Evolution des efforts de
coupe en fonction de la profondeur de passe
(Vc=30m/min ; f=0,14mm/tr)
La Figure 25 présente les
résultats de l'évolution des efforts de coupe en fonction de la
profondeur de passe. On remarque une augmentation des efforts de coupe avec
l'augmentation de la profondeur de passe à cause de l'augmentation de
l'épaisseur du copeau et par conséquent l'augmentation du volume
du matériau déformé, cette augmentation est presque
linéaire.
Les résultats de la variation des composantes des
efforts de coupe pour les différentes combinaisons des
éléments du régime de coupe (Vc, f, ap), établis
selon les règles de construction du plan de Taguchi (la
table orthogonale standard L9(3)3), sont
représentés sur le tableau IX :
N°
|
Vc, [m/min]
|
f, [mm/tr]
|
ap, [mm]
|
Fx, [N]
|
Fy, [N]
|
Fz, [N]
|
1
|
30
|
0.14
|
2
|
8.13
|
5.23
|
19.05
|
2
|
180
|
0.48
|
2
|
5.17
|
1.53
|
62.23
|
3
|
90
|
0.56
|
2
|
6.95
|
1.69
|
61.21
|
4
|
90
|
0.14
|
3
|
10.22
|
4.25
|
33.29
|
5
|
30
|
0.48
|
3
|
14.64
|
3.58
|
91.07
|
6
|
180
|
0.56
|
3
|
6.43
|
2.93
|
69.69
|
7
|
180
|
0.14
|
4
|
11.37
|
0.97
|
38.05
|
8
|
90
|
0.48
|
4
|
9.95
|
0.20
|
103.21
|
9
|
30
|
0.56
|
4
|
17.44
|
0.12
|
122.71
|
Tableau IX : Résultats des essais
des efforts de coupe.
III.4. Discussions:
III.4.1. Détermination des modèles de
rugosité:
Dans le but de maîtriser le tournage du
polyéthylène, il est nécessaire de mettre au point des
corrélations entre les critères de rugosité et les
paramètres d'usinage sous la forme:
(6)
Où C1, est une constante et k1,
k2 et k3 sont des exposants qui représentent les
degrés d'influence de chaque paramètre.
En appliquant les règles de construction du plan de
Taguchi [16] on a réaliser une série de 9 expériences
suivant la table orthogonale standard L9(3)3. Les
modèles de rugosité obtenus sont les suivants:
Ra = e3,78 . f1,26 .
ap-0,1. Vc-0,12
(7)
Rz = e5,86 . f1,28 .
ap-0,28. Vc-0,19
(8)
Rt = e5,84 . f1,28 .
ap-0,25. Vc-0,2
(9)
Les coefficients de détermination indiquent une bonne
corrélation entre les valeurs théoriques des critères de
rugosité, données par ces modèles, et les valeurs des
critères mesurés de rugosité (R2=0,96).
Ces résultats permettent de prédire, pour des
conditions d'usinage choisies dans les limites du modèle, la
rugosité avant même d'entreprendre des essais. Comme attendu,
l'avance reste toujours le facteur prépondérant sur les
critères de rugosité, puisqu'elle possède l'exposant le
plus important en valeur absolue.
III.4.2. Détermination des modèles des
efforts de coupe :
Les résultats expérimentaux des composantes des
efforts de coupe mesurés lors des essais précédents
(Tableau X), montre que l'effort tangentiel Fz est prépondérant
par rapport aux deux autres efforts (Fy et Fx), Ce qui nous a amené
à étudier l'influence des éléments du régime
de coupe sur l'effort tangentiel uniquement.
Le modèle mathématique, exprimant la relation
entre l'effort tangentiel Fz et les éléments du régime de
coupe (Vc, f, ap), est donné par :
Fz = e3,78 . f 1,26 .
ap-0,1. Vc-0,12
(10)
L'analyse du modèle mathématique
précédent (équation 10), permet de définir avec
plus de précision les tendances ainsi que les degrés d'influence
des différents facteurs du régime de coupe (Vc, f, ap), sur
l'effort tangentiel. A cet effet, l'analyse des exposants du modèle
montre que l'augmentation de la vitesse de coupe contribue à la
diminution des efforts de coupe, alors que l'augmentation de la section du
copeau (f x ap) contribue à l'accroissement des efforts. D'autre part,
le classement des exposants, en valeur absolue, exprime le degré
d'influence de chaque facteur des éléments du régime de
coupe sur les efforts. Par conséquent la plus grande influence est
réservée en général à l'avance suivie par la
profondeur de passe, par contre la vitesse de coupe a une influence
relativement faible. L'intérêt industriel des modèles
mathématiques trouvés est de taille car ils permettent la
détermination des conditions de coupe optimales et donnent des
renseignements précieux sur le processus de coupe.
Cette étude montre que l'usinage des tubes de
polyéthylène présente quelques spécificités
à prendre en compte lors de la conception ;
L'effet de l'avance est nettement important, sur
l'état de surface, par rapport aux autres paramètres de coupe.
La qualité de surface s'améliore avec la vitesse
mais il y a une élévation de température qui peut
provoquer une fusion locale du matériau.
L'effet de la profondeur de passe est très faible sur
l'état de surface obtenu.
L'analyse des exposants des différents modèles
trouvés fait sortir que l'augmentation de la vitesse de coupe contribue
à la diminution des efforts de coupe, alors que l'augmentation de la
section du copeau (f x ap) contribue à l'accroissement des
efforts.
D'autre part, le classement des exposants des
différents modèles trouvés en valeur absolue exprime le
degré d'influence de chaque facteur des éléments du
régime de coupe sur les efforts. Par conséquent la plus grande
influence est réservée en général à l'avance
suivie par la profondeur de passe, par contre la vitesse de coupe a une
influence relativement faible.
L'intérêt industriel des modèles
mathématiques trouvés est de taille, car ils permettent la
détermination des conditions de coupe optimales et donnent des
renseignements précieux sur le processus de coupe.
Bibliographie :
[1] R. Dekiouk, Etude et relation de
l'influence de la vitesse de déformation sur la dimension fractale et
sur la ténacité dans le cas d'un Polycarbonate, Thèse
de Doctorat, Université de Metz, France, juillet 1997.
[2] Gottfried W. Ehvenstein, Fabienne
Montagne, Matériaux polymères, Structure,
propriétés et application, Hermès, Paris 2000.
[3] Marc Carrega, les polymères de
la molécule à l'objet, EDP , Grenoble 1999.
[4] Hans-Henning Kausch, Nicole Heymans, Christopher
John Plummer et Pierre Decroly, Matériaux
polymères : Propriétés mécaniques et
physiques. Principe de mise en oeuvre, Lausanne 2001.
[5] M. Kaddeche et K. Chaoui, Etude
expérimentale des propriétés mécaniques et des
déformations résiduelles dans les tubes extrudés enHDPE-80
et HDPE-100, Mémoire de Magister, Guelma 2006.
[6] N. Kiass et K. Chaoui, Nouvelle
approche expérimentale des propriétés mécaniques
des tubes en PEHD-80, Thèse de Doctorat, Annaba 2005.
[7] J.Bost, Matières plastiques,
Chimie - Application, Dunod, Paris 1980.
[8] Gas Research Institute, Pipeline Statistics,
Distribution and Transmission, Annual
Mileage Totals, (www.gri.org/pub), Chicago (2002).
[9] Michel Colombié, Pratique des
matériaux industriels, propriétés, choix,
utilisations, Volume 5, DUNOD, paris, (7-2000).
[10] (
www.steel-dragon.com)
[11] M. Rahman, «Machinability study
of carbon fiber reinforced composite», J. Mater.
Proc. Technol., 89-90, (1999) 292-297.
[12] J. E. MARK, Polymer data
handbook, Oxford University Press, 1999.
[13] J.P.Trotignon, M.Piperaud; J.Verdu et A.Dobraczynski,
Précis de matières plastiques, Structure -
Propriétés, Mise en oeuvre et Normalisation, Afnor, Nathan,
1992.
[14] S.Mammeri & K. Chaoui,
Détermination des conditions d'usinage du PEHD, Thèse de
Magister, Université d'Annaba, 2003.
[15] A. Dessarthe, Usinage des
matières plastiques, Cétim. 2000.
[16] K. Palanikumar, L. Karunamoorthy, R.
Karthikeyan, Assessment of factors influencing surface roughness
on the machining of glass fiber-reinforced polymer composites, Materials
and Design 27 (2006) 862-871.
[17] M. A. Yallese, J.-F. Rigal, K. Chaoui et L.
Boulanouar, «The effects of cutting conditions on mixed
ceramic and cubic boron nitride tool wear on surface roughness during machining
of X200Cr12 steel (60 HRC)», IMechE, Part B: J. Engineering
Manufacture, Vol. 219, Nb. 1, (2005), 35-56.
[18] G. W. Ehrenstein et F. Montagne,
Matériaux polymères, structures, propriétés et
applications, Editions Hermes, Paris, 2000.
[19] M., VIGIER, Pratique des plans
d'expériences - Méthodologie Taguchi- les éditions
d'organisation, 1988.
|