Sommaire
1. Remerciements 2/59
2. Objectif de stage
a. Réalisation de la supervision d'une maquette de
démonstration 3/59
3. Présentation générale de SIMTRONICS
SAS
a. Présentation globale & historique 4,5/59
b. Secteurs d'activités & clients 6/59
c. Organigramme des différents départements
7/59
4. Connaissances nécessaires d'avant projet
a. Les produits et les gaz détectables 8,9,10/59
b. La norme ATEX : (ATmosphères EXplosives)
11,12/59
c. Quelle place pour la supervision dans le domaine de la
détection ? 13/59
d. Le système SYNTEL / SYNTEL XXI 14,15,16,17/59
e. Le configurateur SYNTEL 18,19/59
5. Stage 08/09 chez SIMTRONICS SAS
a. La maquette de démonstration 20/59
· PcVue : une alternative ? 21/59
· Etude des travaux antérieurs 22...27/59
· Méthodologie de développement de la
supervision 28...44/59
b. Les critères importants d'une supervision industrielle
45/59
· L'aspect esthétique 46,47/59
· L'aspect pratique 48/59
c. Le protocole OPC
· OPC : OLE for Process Control 49/59
· Structures des variables OPC chez SIMTRONICS SAS
50...54/59
d. Optimisation 55/59
· Méthode de travail en mode OPC réel
56...58/59
6. Conclusion 59/59
Remerciements
Je tiens à remercier dans un premier temps, toute
l'équipe pédagogique de la faculté de St
Jérôme et celle du lycée du Rempart, responsables de la
licence professionnelle d'automatique et d'informatique industrielle, pour
avoir assuré la partie théorique de celle-ci. Je tiens
à remercier tout particulièrement et à témoigner
toute ma reconnaissance aux personnes suivantes, pour l'expérience
enrichissante et pleine d'intérêt qu'elles m'ont fait vivre durant
ces trois mois au sein de l'entreprise Simtronics SAS :
Monsieur LA
PIANA, Manager général de Simtronics SAS, pour son accueil et la
confiance qu'il m'a accordé dès mon arrivée dans
l'entreprise.
Monsieur CACCIAGUERRA, chef de projet et chargé
d'affaires chez Simtronics SAS, mon tuteur, pour m'avoir intégré
rapidement au sein de l'entreprise et m'avoir accordé toute sa
confiance; pour le temps qu'il m'a consacré tout au long de cette
période, sachant répondre à toutes mes interrogations ;
sans oublier sa participation au cheminement de ce rapport.
Messieurs
PASCOU, BOUDOUDA, DE GENNARO ainsi que l'ensemble du personnel de Simtronics
SAS pour leur accueil sympathique et leur coopération professionnelle
tout au long de ces trois mois.
Objectif de stage
Réalisation de la supervision d'une maquette de
démonstration
L'objectif du stage de fin d'études de la licence
professionnelle chez SIMTRONICS SAS
sera le développement complet de la supervision de la
maquette comprenant :
Ø Trois détecteurs :
v Un explosimètre
v Un toximètre
v Un détecteur de flamme
Ø Deux éléments divers :
v Une alimentation / contrôleur réseau
v Un relais
De ce fait, les axes principaux de difficultés à
appréhender seront :
v La création des modèles
§ En effet, pour pouvoir permettre à SIMTRONICS
SAS de réaliser
ses supervisions simplement après mon passage, le but
sera de créer des modèles informatiques des différents
produits
v Le protocole de communication utilisé
§ Pour qu'une supervision soit réussie et
fonctionnelle, la partie communication doit fonctionner correctement et
répondre aux attentes de l'utilisateur de l'interface homme machine.
Dans tous les cas, le système fonctionnant
déjà correctement, l'enjeu sera de proposer une interface de
qualité permettant d'exploiter en profondeur le système complexe
SYNTEL.
Présentation générale de SIMTRONICS
SAS
Présentation globale
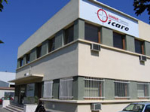
SIMTRONICS SAS
ZI Les Paluds
792, avenue de la Fleuride
BP 11 061
13781 Aubagne Cedex
France
Date de création : 1948
Forme juridique : société par actions
simplifiée
Capital social : 1.000.000,00 €
Chiffre d'affaires : 4.500.000 €
Effectif : 30 à 35 personnes
SIMTRONICS SAS est une société
spécialisée dans la conception, la fabrication, la
commercialisation et la maintenance de produits de détection de gaz et
de flammes.
Afin de renforcer sa position sur le marché mondial et
de répondre de façon globale aux marchés du monde de
l'offshore, l'entreprise a intégré le groupe Norvégien
SIMRAD Optronics.
Sur ses sites de production situés à Aubagne et
à Oslo, en Norvège, SIMTRONICS conçoit et réalise
une gamme complète de produits destinés à couvrir
l'ensemble des risques gaz et flamme.
Autour de son métier, la détection et l'analyse
des gaz explosifs et toxiques, la supervision et les systèmes
intégrés apportent une offre globale qui assure performances et
homogénéité. Grâce à la qualité de ses
produits et à son savoir-faire, SIMTRONICS réalise des projets
importants, en France et à l'export, qui a contribué à son
expansion et à l'évolution de sa structure.
Présentation générale de SIMTRONICS
SAS
Historique
1948 : Fondation de la
Société ICARE (Industrie de
Construction d'Appareils
Radio Electriques) pour répondre
à une demande de la Marine Nationale.
1954 : Homologation OTAN et
jusqu'à aujourd'hui équipement de tous les sous-marins construits
sous code OTAN et des sous-marins nucléaires Français.
1960 : ICARE équipe toutes les
installations militaires ou paramilitaires.
1969 : Ouverture des produits ICARE vers
le monde industriel (maritime, pétrole, chimie...)
1971 : ICARE commence à fournir
des ensembles de détection / analyse de Gaz au travers des
Sociétés d'Ingénieries.
1978 : ICARE commence à fournir
des ensembles de détection / analyse de Gaz dans les centrales
nucléaires civiles.
1980 : Création du concept
Compact Capteur avec électronique embarquée :
Explosimètres, Oxygénomètres et Toximètres.
1993 : Création du Concept
Télécapteur.
1994 : L'actionnaire principal de la
Société ICARE devient le Groupe CS (Compagnie des Signaux).
1995 : Création du Concept
d'Intelligence Distribuée (Réseau SYNTEL) dans la
détection de gaz et de flamme. Introduction du Microprocesseur dans
chaque capteur.
2000 : ICARE innove encore avec la
sortie d'un détecteur optique de flamme triple spectre, une
détection dans l'ultra violet combinée à une double
détection dans l'infra rouge.
2002 : ICARE intègre le groupe
français TAURUS Invest.
Sortie de la ligne de produits ECHO destinée
prioritairement aux sites semi industriels et tertiaires.
2004 : Evolution du Système
Syntel avec la sortie de la version Syntel 21.
Afin de renforcer sa position sur le marché mondial et
de répondre de façon globale aux marchés du monde de
l'offshore, l'entreprise intègre le groupe Norvégien SIMRAD
Optronics.
2007 : Séparation des deux
départements du groupe SIMRAD Optronics : Militaire et Fire &
Gas.
La division Fire&Gas devient Simtronics Fire & Gas.
Présentation générale de SIMTRONICS
SAS
Secteurs d'activités et clients

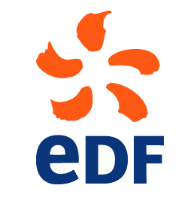
SIMTRONICS SAS travaille aujourd'hui sur plusieurs secteurs
d'activités et avec des clients tels que :
v NUCLEAIRE
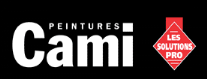
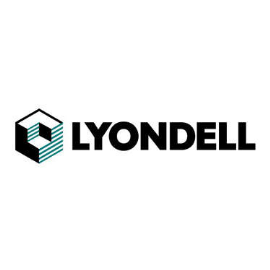
v CHIMIE

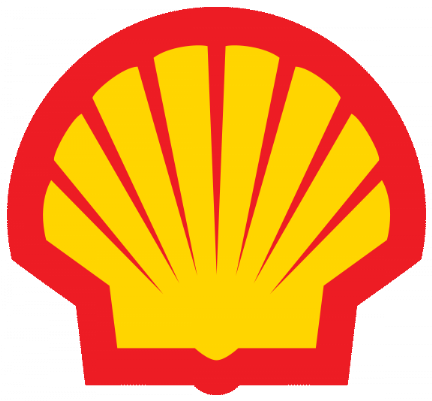
v PETROCHIMIE
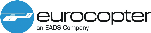
v AERONAUTIQUE - SPATIAL
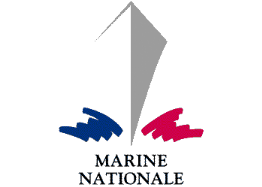
v MILITAIRE
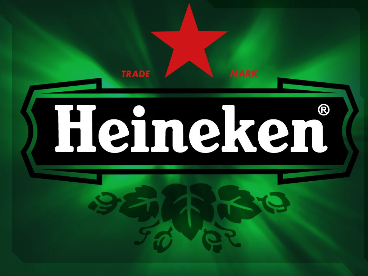
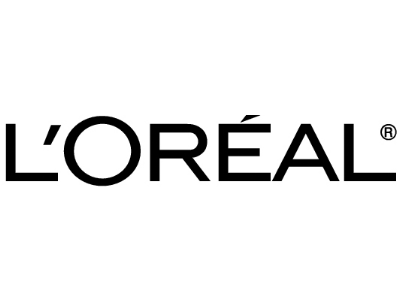
v COSMETIQUE
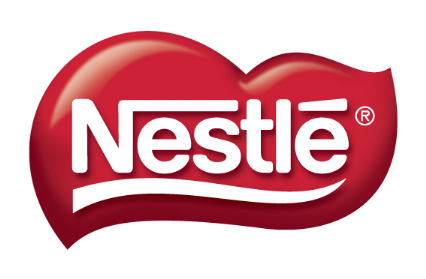
v AGRO-ALIMENTAIRE

v AUTOMOBILE
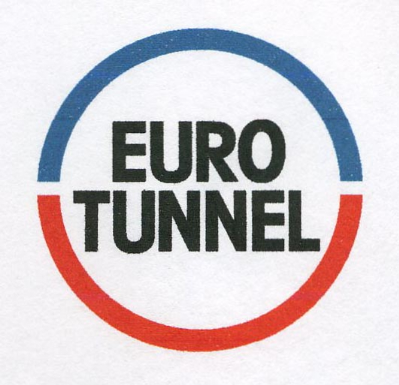
v TRANSPORTS
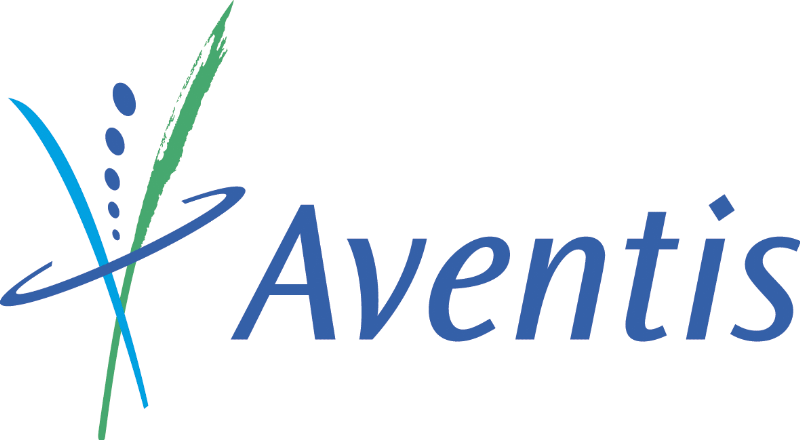
v PHARMACEUTIQUE
v PLATEFORMES PETROLIERES des sites de forage et
d'exploitation tels que North Alwyn (Mer du Nord), ou Frigg
(Norvège)...
Présentation générale de SIMTRONICS
SAS
Organigramme des différents départements
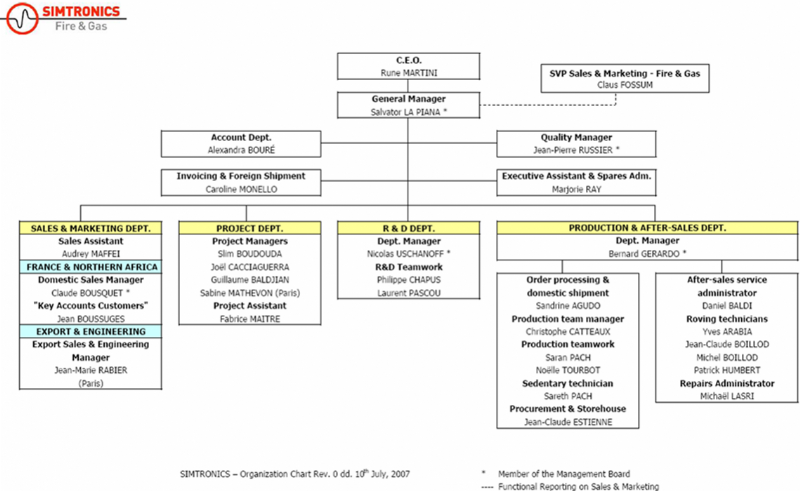
Connaissances nécessaires d'avant
projet
Les produits et les gaz détectables
Tous les produits fabriqués par SIMTRONICS SAS sont
certifiés ATEX, ils sont donc
parfaitement adaptés aux atmosphères
dangereuses.
Avant même de penser à l'étude du
développement de l'interface homme machine,
la logique m'a poussé à m'imprégner des
différents gaz détectables par les différents
détecteurs.
Dans le cas spécifique de mon travail, j'ai
étudié les explosimètres, les toximètres et les
détecteurs de flamme.
L'explosimètre :
Les explosimètres et catharomètres sont des
appareils destinés à la mesure du risque d'explosion
engendré par la présence de gaz ou de vapeurs inflammables.
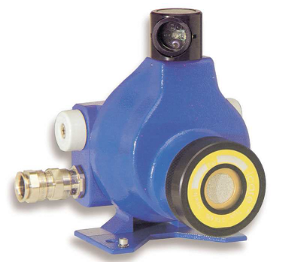
v Explosimètre
o Détecte les hydrocarbures saturés
(Méthane, propane, Heptane..)
o Les hydrocarbures cycliques (Cyclohexane...)
o Hydrogène
o Les alcènes, aromatiques, cétone,
aldéhydes...
o Les acides, alcools....
Le toximètre :
Les toximètres sont destinés à la mesure du
risque toxique engendré par la présence de gaz ou vapeurs
toxiques.
v Toximètre
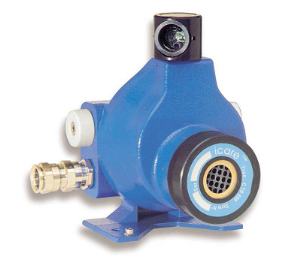
o Permet d'établir une surveillance constante et stable
du risque d'asphyxie par manque d'oxygène.
o Permet d'assurer d'autre part la sécurité des
personnes en contrôlant la déficience du taux d'oxygène
entraînée par des fuites de gaz tel que l
l'azote(N2) par exemple
Le détecteur de flamme :
Les détecteurs optiques de flamme sont
équipés d'une cartouche intelligente et débrochable
assurant la détection et le traitement du signal.
Afin de mieux répondre aux exigences du marché,
le détecteur fonctionne sur les différents principes suivants
:
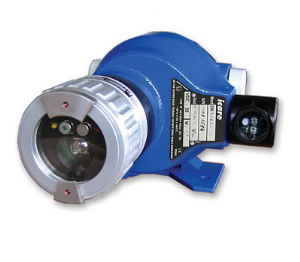
V00 : UV / IR² La triple
détection est basée sur le rayonnement de flamme dans l'Ultra
Violet et dans deux bandes infra rouges.
W00 : UV configuration Ultra
violet seul.
D00 : IR² configuration
voies infra rouges seuls.
T00 : IR3 La triple
détection est basée sur le rayonnement de flamme dans trois
bandes infra rouges distinctes.
Le V00 :
Conçu pour atteindre une grande portée de
détection tout en garantissant une excellente immunité contre les
fausses alarmes, il est le détecteur le plus performant de sa
catégorie. Du point de vue des fausses alarmes, l'exploitation de deux
mesures en infra rouge par un algorithme original rend le V00,
insensible aux conditions environnementales difficiles telles que pluie et vent
combinés, les variations rapides d'ensoleillement, ainsi que les sources
chaudes modulées, les éclairages industriels, ... L'utilisation
d'une confirmation de détection au travers d'une voie de mesure en
Ultraviolet permet de réduire encore le risque résiduel de
fausses alarmes tout en disposant d'une information de mesure très
rapide.
Le W00 :
Cette configuration en UV seul de la cartouche
de détection permet, principalement, d'exploiter l'appareil sur des feux
non hydrocarbonés, du type feux d'hydrogène, d'ammoniac, ... Elle
permet, par ailleurs, d'obtenir des temps de réponse extrêmement
intéressants.
Le D00 :
Cette déclinaison de la cartouche V00 en IR² seul
permet de fonctionner dans des environnements pénalisant la propagation
du rayonnement UV, du fait d'émanation de très fortes
fumées en milieu confiné, par exemple.
Le T00 :
La version de cartouche IR est la
dernière née de cette gamme d'appareil. Un effort particulier a
été fait sur l'algorithme de traitement du signal de
manière à donner à cette version des performances uniques
tout en maintenant un taux de fausses alarmes extrêmement faible. Pour
parvenir à ce résultat, l'appareil exploite trois bandes
infrarouges distinctes et un traitement mathématique complexe.
Connaissances nécessaires d'avant projet
La norme ATEX (Atmosphères Explosives)
SIMTRONICS SAS crée ses produits dans le but de
sécuriser les installations de ses clients.
De ce fait, quand un événement dangereux peut se
déclencher, le système de détection de gaz doit être
la plus fiable possible.
La réglementation ATEX
(ATmosphères EXplosibles) est issue de deux directives
européennes (en 1994 pour les machines et en 1999 pour les
utilisateurs).
La réglementation dite ATEX demande à tous les
chefs d'établissement de maîtriser les risques relatifs à
l'explosion de ces atmosphères au même titre que tous les autres
risques professionnels.
Une ATEX, c'est une « Atmosphère Explosible »
qui pourrait devenir explosive en raison des conditions locales ou/et
opérationnelles. C'est un mélange d'air et de substances
inflammables sous forme de gaz, vapeurs, brouillards ou poussières, dans
lequel, après inflammation, la combustion se propage à l'ensemble
du mélange non brûlé.
Quelles sont les conditions pour que l'on devienne en
présence d'une atmosphère explosive ?
Il faut deux conditions :
v Condition n°1 : Il faut la
présence d'un comburant et d'un combustible. Dans un
mélange formant une ATEX, l'oxygène de l'air est le
comburant, les substances inflammables sous forme de gaz, de
vapeurs ou de poussières sont le combustible. Voici
quelques exemples de combustibles pouvant former une ATEX dans un
mélange avec l'air :
Gaz
|
Vapeurs
|
Poussières
|
Méthane Butane Propane Hydrogène
|
Sulfure de carbone Alcool éthylique Oxyde
d'éthylène Acétone
|
Aluminium Amidon Céréales Charbon
|
v Condition n°2 : Le mélange doit
être explosif. Une ATEX explose par l'apport d'une
source d'inflammation, qui peut être une source
d'énergie suffisamment importante (par exemple une
étincelle d'origine mécanique ou électrique) ou une
température suffisamment élevée (par
exemple une surface chaude).
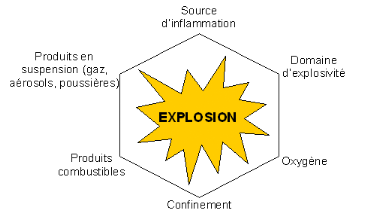
Où trouves t'on les ATEX ?
Toutes les entreprises utilisant des substances inflammables
ont un risque d'explosion et sont concernées par la
réglementation ATEX. Quelques exemples :

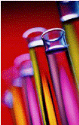
Pétrochimie Chimie


Agroalimentaire Recyclage
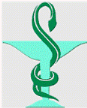
Industrie pharmaceutique
Connaissances nécessaires d'avant
projet
Quelle place pour la supervision dans le domaine de la
détection ?
SIMTRONICS SAS est spécialisée dans la
détection de gaz. Depuis plus de 50 ans, SIMTRONICS SAS a acquis et
développé son expérience dans le domaine de la
sécurité.
Les produits de SIMTRONICS SAS permettent de détecter
efficacement tout risque de toxicité, explosivité mais aussi les
départs de flamme.
Depuis peu, l'entreprise a crée un système de
réseau, nommé SYNTEL, permettant de
garantir la surveillance de chaque site de client
efficacement.
Ce réseau, développé en interne,
possède sa propre supervision, appelée SYNTEL CLASSIQUE.
Le logiciel Syntel Classique assure la gestion sur plate-forme
PC de l'ensemble des informations. Il présente un IHM graphique
permettant de visualiser l'ensemble de l'état de la détection en
global, par zone ou par détecteur ainsi que l'état du
système en terme de communication, d'alimentation et de
disponibilité.
Il délivre sur demande des diagnostics complets sous
forme de synoptiques animés.
Il archive les événements et les mesures dont
plusieurs critères de tri permettent l'exploitation de ces historiques.
La mesure de chaque détecteur est disponible sous forme de courbe temps
réel. Et plusieurs niveaux d'accès permettent de gérer
l'accès aux commandes de maintenance.
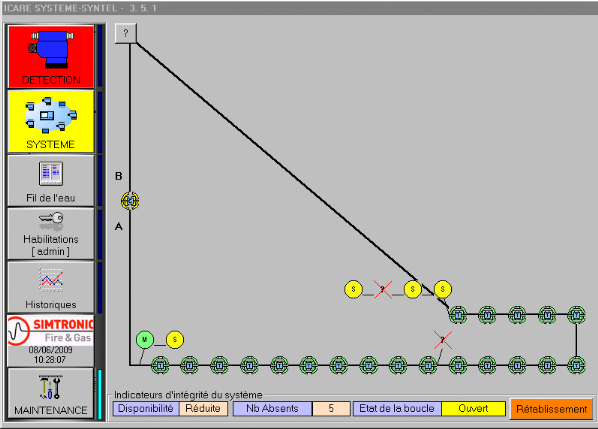
Logiciel
Syntel
Classique
Connaissances nécessaires d'avant
projet
Le système Syntel/SyntelXXI
LE SYSTEME SYNTEL (CLASSIQUE)
Description :
Le SYSTEME-SYNTEL® est un système en réseau
de terrain sécurisé à intelligence
distribuée où chaque détecteur interagit
directement sur les modules d'asservissement.
Une topologie en anneau où un câble unique permet
d'alimenter les équipements et de constituer le média de
communication. Les équipements peuvent être placés
n'importe où sur le câble, sans aucune contrainte
particulière.
Le système est résistant à une agression
du câble, en terme d'ouverture ou de court-circuit. Il réalise la
localisation de l'incident et le rétablissement automatique des
communications et des alimentations. De par son architecture à
intelligence distribuée, il n'existe pas de mode commun. Les
alimentations du système sont redondées. Le câble est
bouclé sur lui même via la SafeBox. Cet équipement
rétabli les communications en cas d'ouverture du média
(système breveté Simtronics). Le système est donc capable
de maintenir sa disponibilité en cas de rupture ou court-circuit du
média, de l'alimentation ou des deux à la fois.
Mode de fonctionnement de la communication
:
Les abonnés du SYSTEME-SYNTEL® communiquent entre
eux d'une manière spontanée grâce aux liens logiques
définis par l'outil de configuration.
Ce principe repose sur le service producteur/consommateur du
protocole Lonworks. Il permet de définir deux classes
d'abonnés. Celle qui regroupe tous les abonnés « produisant
» des informations (capteurs). Celle qui regroupe les abonnés
« consommant » ces informations (relais, superviseur Syntel, coupleur
...).
Lors de la configuration du réseau, des liens
implicites au mode producteur/ consommateur sont ainsi créés
entre les abonnés. Ainsi configuré, le producteur lors d'un
changement d'état de sa détection, envoie spontanément un
message au groupe consommateurs.
Chaque producteur d'informations possède deux
accès au réseau : A et B totalement indépendants.
A l'émission d'un message, le producteur émet
à la fois sur A et sur B.
De même les messages peuvent lui parvenir par A ou B.
Quel que soit le message circulant sur le réseau, les
producteurs fonctionnent en répéteur A vers B, ou B vers A.
Les messages transitent ainsi d'abonné en
abonné. La boucle est refermée sur un équipement
appelé Safebox. Cet équipement en mode nominal maintien la boucle
ouverte (en ne répétant pas les messages de A vers B et de B vers
A). La Safebox évite ainsi que les messages tournent inutilement
à l'infini. Ce principe est breveté par SIMTRONICS. La Safebox,
en cas de détection d'une rupture du média, assure la
continuité de celui-ci en répétant les messages à
travers elle.
Mécanisme automatique de reprise des
messages en cas de rupture du média.
Fonctionnement en mode nominal
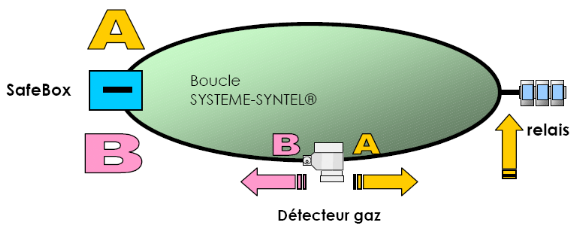
En mode nominal, la SafeBox ouvre la boucle entre A et B. Le
message envoyé par le capteur côtés A et B, parvient au
relais par A.
Fonctionnement en mode
dégradé
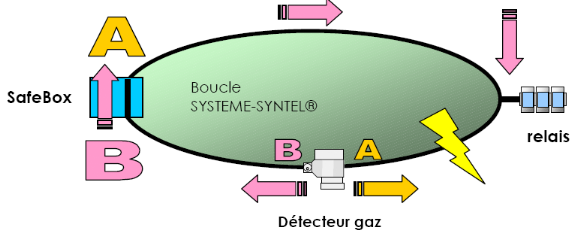
En mode dégradé, la Safebox ferme la boucle
entre A et B. Le message envoyé par le capteur côtés A et
B, parvient au relais par B.
La Safebox garantit une disponibilité de 100% du
système en cas de :
· Ouverture du média en un point.
· Court-circuit du média en un point.
La Safebox est un équipement passif du réseau en
mode nominal.
LE SYSTEME SYNTEL XXI
Aujourd'hui, le système SYNTEL a évolué et
se nomme maintenant SYNTEL XXI.
SIMTRONICS SAS a développé une supervision
nouvelle, permettant de tirer profits de la puissance de SYNTEL XXI. La
supervision a été développée à l'aide du
logiciel KEP INFILINK.
Cet IHM intègre maintenant les dernières
versions des composants (détecteurs, relais, etc.) sortis depuis la
création du système SYNTEL classique.
Cette application permet d'aller beaucoup plus loin que
précédemment dans l'interaction homme machine car elle permet
d'intégrer du code SCADA BASIC mais aussi le protocole OPC (Ole for
Process Control).
Les variables OPC permettent de faire remonter et de signaler
efficacement les informations propres au capteurs.
Grâce au configurateur SYNTEL développé en
interne chez SIMTRONICS SAS, on régit une génération de
capteurs et variables associées, et dans un second temps il ne reste
qu'à les placer
sur les plans d'usines dessinés sur AUTOCAD.
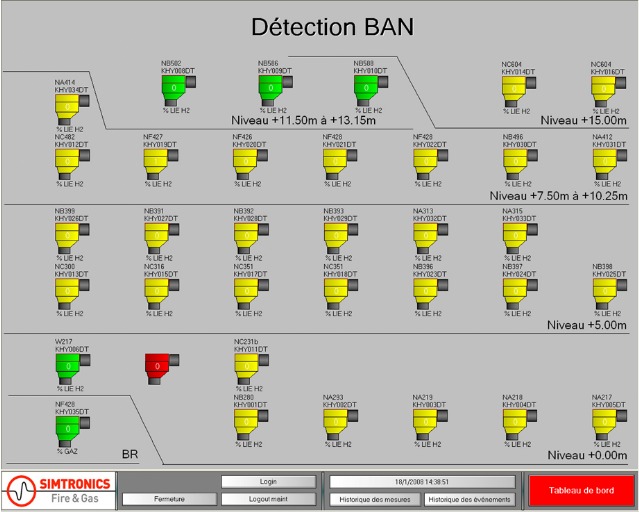
Supervision
KEP INFILINK
Système
SYNTEL XXI
Connaissances nécessaires d'avant
projet
Le configurateur Syntel
Dans le but de permettre de générer du code SCADA
BASIC facilement et donc de faciliter la création d'interfaces homme
machines grâce au logiciel KEP INFILINK, SIMTRONICS SAS a
développé le configurateur Syntel.
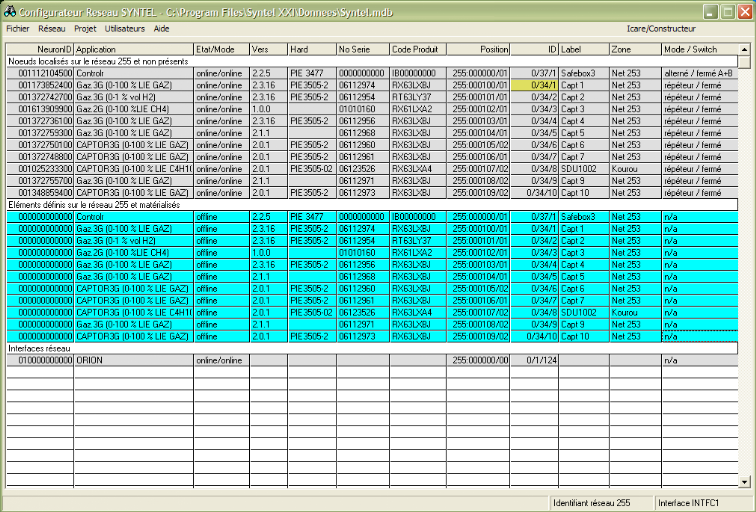
Le configurateur réseau SYNTEL permet de définir
une base de données de type Access, regroupant tous les
éléments réseau du système. Après avoir
renseigné à la base de données le nombre
d'éléments que l'on désire pour notre supervision, on
génère les fichiers SCADA utilisables directement par les
superviseurs compatibles. (KEP INFILINK et PcVue par exemple)
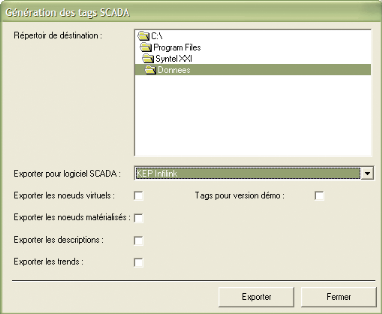
Génération de tags SCADA...
Stage 08/09 chez SIMTRONICS SAS
La maquette de démonstration
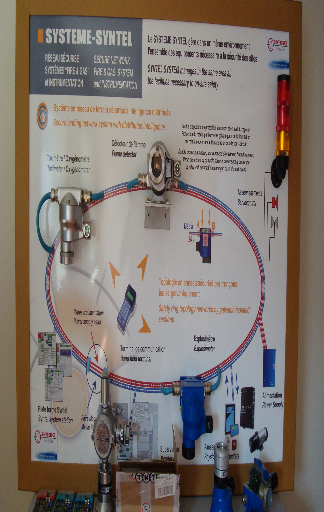
Cette maquette a pour but de présenter les produits
qui existent chez Simtronics.
Stage 08/09 chez SIMTRONICS SAS
Pcvue : une alternative ?
L'objectif de mon stage de mars à juin fut de proposer une
alternative à la solution de supervision déjà existante,
KEP INFILINK.
En effet, SIMTRONICS SAS, en proposant ce stage, cherche à
proposer une autre interface pour leurs clients.
Le but est de proposer de nouvelles idées, essentiellement
esthétiques, qui pourraient améliorer le travail qui existe
déjà.
Pour m'aider dans ma démarche, SIMTRONICS SAS m'a
proposé de participer au WONDERWARE TOUR, qui s'est
présenté à Aix-En-Provence, dans le but de me permettre
d'aborder au mieux les supervisions actuelles.
KEP INFILINK propose aujourd'hui une interface de
démonstration, et le passage du mode démonstration vers le mode
OPC réel se fait via une relance du logiciel.
De ce fait, j'ai du organiser ma stratégie de
réflexion afin de répondre à mes besoins.
Cette stratégie s'articule autour de quelques axes, tels
que :
v L'étude en détails de la supervision existante
v L'étude du projet réalisé par le stagiaire
de l'année précédente
v Acquérir les connaissances nécessaires afin de
réaliser une supervision stable
Cette étape préliminaire est importante pour
pouvoir aborder le projet avec aisance.
Les étapes importantes du projet :
v Travailler l'aspect esthétique
v Proposer de nouvelles solutions pratiques
Après avoir reconnu le degré de difficulté
de la réalisation du projet, je me suis donc lancé dans le
développement de la supervision sous PcVue en gardant à l'esprit
que l'esthétique était la partie dans laquelle je devrai
m'investir le plus possible.
Pour le développement, le choix s'est orienté vers
PcVue car le stagiaire précédent avait déjà
entrepris des réalisations pour SIMTRONICS SAS, notamment du capteur de
type explosimètre.
Stage 08/09 chez SIMTRONICS SAS
Etude des travaux antérieurs
Le stagiaire précèdent avait pour objectif de stage
de réaliser un modèle d'explosimètre, le plus proche de la
réalité possible, en laissant libre court à son esprit
esthétique.
Pour m'imprégner de son travail, il m'a été
suggéré de faire quelques propositions d'améliorations
concernant son projet.
Vue générale du projet
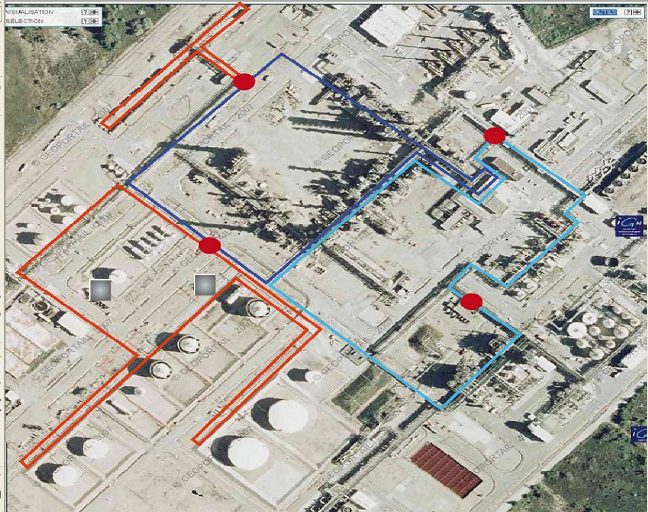
On remarque que sur la vue générale, les
détecteurs sont représentés par des carrés, ce qui
n'est pas envisageable lorsque l'on prend en compte l'aspect esthétique
de la supervision.
La solution que j'ai alors proposé dans le but d'une
possible amélioration de l'interface était de remplacer les
carrés par une miniature de capteur de manière à
comprendre directement que la zone concernée possède deux
détecteurs.
Message d'erreur se présentant en cas de clic sur
une zone ne comprenant pas de détecteurs
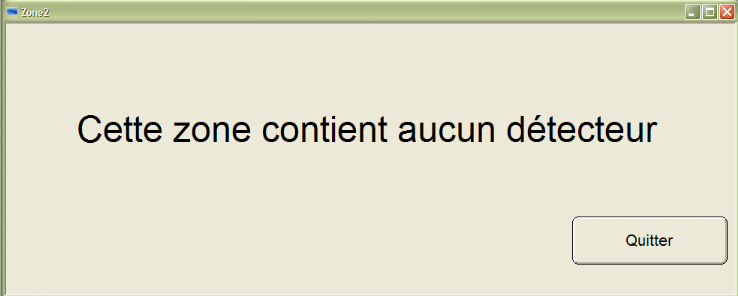
Les autres zones du premier écran ne sont pas judicieuses,
car elles ne contiennent qu'un message d'erreur qui nous renvoie sur la page
principale de plus, la phrase n'est pas correcte grammaticalement, il aurait
été judicieux d'écrire : « Cette zone ne
contient aucun détecteur actuellement ».
Solution proposée : ne pas supprimer les zones, mais
insister sur un encadrement en surbrillance grisâtre (ou autre code
couleur) pour insister sur le fait que l'endroit pointé n'est pas
pertinent.
Un point étant à souligner par ailleurs, la
résolution de la supervision étant assez faible (800*600),
sachant que les supervisions modernes doivent s'afficher sur un
écran haute définition, configurer l'espace de travail en
1920*1080 de façon à être exploitable.
Focus sur zone comprenant des
détecteurs
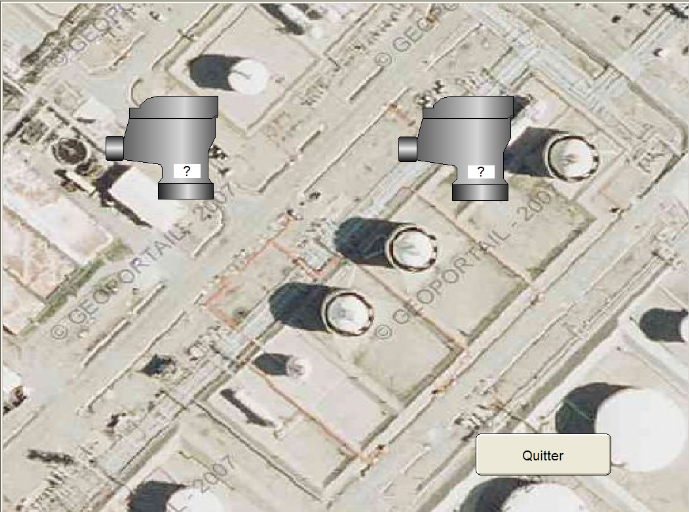
Le bouton quitter qui réalise une fonction de
chaînage fermeture ne porte pas un nom pertinent, surtout dans le cas
d'une supervision démonstrative.
Solution envisagée : proposer un autre label, comme
par exemple : « Revenir à l'écran
précèdent »,
« Précédent », « Revenir à
la vue générale ».
L'ombre portée de part et d'autre du détecteur
donne un effet d'amplitude de relief au capteur, ce qui est un excellent point
pour une représentation de qualité. Le synoptique est globalement
bien réalisé et correspond à un niveau passable de
représentation. Le seul point impertinent du détecteur est la
partie haute.
Solution envisagée : après avoir
étudié et regardé sous différents angles de vue un
détecteur lambda, prendre le temps d'élaborer un synoptique
modèle qui respecte les critères suivants :
ESTHETIQUE, SIMPLE, REUTILISABLE, AISEMENT SUPERVISABLE,
PERTINENT, REALISTE, BIEN PROPORTIONNE.
Dans le cas où plusieurs détecteurs seraient mis en
jeu, une appellation pour chaque détecteur serai judicieuse.
Proposition d'amélioration : nommer les capteurs de
façon à bien les différencier (classification par zone,
type, position sur écran) par exemple pour un explosimètre
placé dans la première zone d'une usine et placé en haut
de l'écran du superviseur :
Z1-EX-N avec Z1 pour Zone 1, EX pour Explosimètre et N
pour Nord.
Globalement, pour un travail de qualité, il est
nécessaire d'utiliser tous les outils mis à disposition par le
superviseur durant le développement de la supervision.
Le but est de développer une console de supervision simple
et intuitive pour être utilisée sans difficultés par un
opérateur, même sans culture informatique.
Vue de détails du détecteur
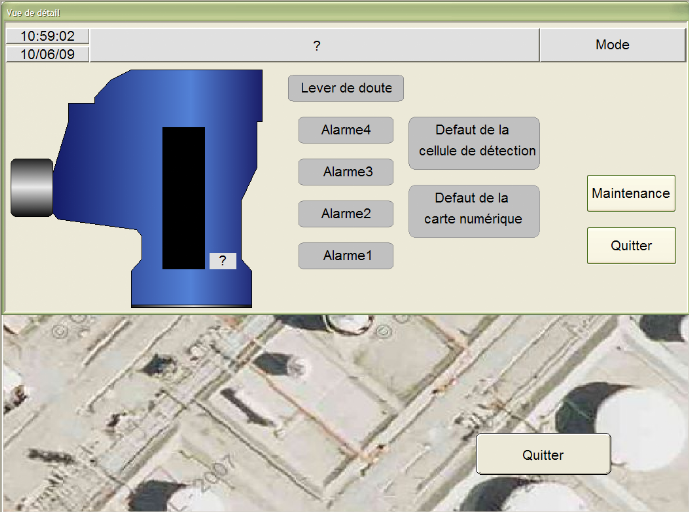
L'heure et la date sont gadgets, la logique de
développement propose plutôt de mettre ces informations dans un
panel commun aux différentes vues, ou bien sur la vue
générale.
La taille de la fenêtre de détails est trop
importante, on ne peut pas voir si le deuxième capteur change de couleur
(synonyme de défaut).
Le synoptique « Vue de détails » ne
donne pas l'espace optimum aux différents composants (boutons, symbole
détecteur).
Proposition : créer un synoptique de taille
suffisante pour une vue de détails claire et intuitive. En outre, la
disposition des éléments est une condition essentielle à
une interface homme machine réussie.
Exemple : symbole de détecteur placé à
gauche, attributs à droite.
Comme dans l'écran de focus détecteur, le bouton
Quitter n'est pas judicieux.
Proposition d'amélioration : Un label comme
« Revenir à la vue de zone » ou « Revenir
à l'écran précèdent » serai plus
intéressant.
A partir de ce moment là, le seul moyen de rentrer dans la
vue de maintenance est de passer par la vue de détails.
Proposition de changement de structure : cet aspect n'est
pas intuitif, il faut pouvoir accéder à l'écran de
maintenance à tout moment, quelque soit la fenêtre active.
Je tiens à signaler par ailleurs que les variables de
défauts sont les même sur les deux détecteurs, donc les
défauts forcés se répercutent sur les deux
détecteurs, il n'y a donc pas de supervision autonome pour les deux
détecteurs.
Vue de maintenance du détecteur
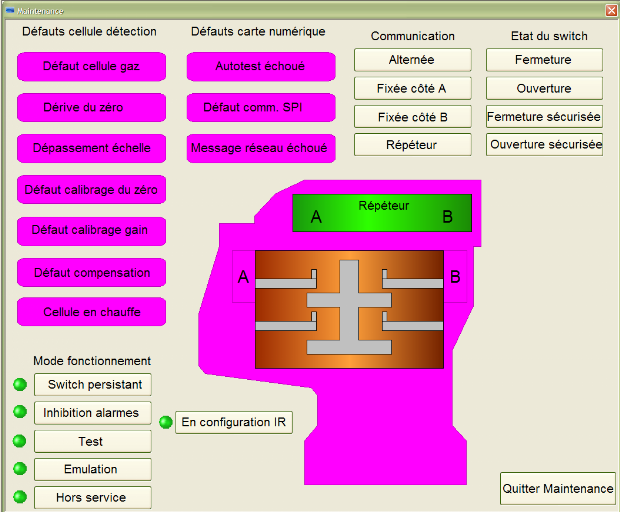
On retrouve le même problème que
précédemment, à savoir cette fois la vue de maintenance
occupe tout l'écran, il est donc impossible d'observer un défaut
sur un autre capteur.
Le bouton « Quitter Maintenance » est
essentiel, mais mal fini.
Proposition d'amélioration : Changer le nom du
bouton, il serai préférable de l'appeler « Quitter le
menu de maintenance » ou bien « Annuler ».
Il faudrait aussi créer un bouton permettant de revenir
à la vue générale sans repasser par la vue de
détail. On pourra le placer par exemple à proximité du
bouton actuel « Quitter Maintenance » qui permettra de
revenir directement à l'écran principal.
Le switch électrique est mal représenté, il
vaut mieux utiliser le symbole normalisé.
Stage 08/09 chez SIMTRONICS SAS
Méthodologie de développement de la
supervision
L'étape d'imprégnation du travail
précédent mon arrivée m'a permis de me concentrer sur la
réalisation en gardant des objectifs clairs et des erreurs à ne
pas commettre.
Le choix d'utilisation du superviseur PcVue m'a été
imposé, du fait d'être en adéquation avec les travaux
précédents.
Fin mars, j'ai donc entrepris le développement de la
supervision de la maquette.
Je me suis concentré premièrement à
l'élaboration des différent modèles que propose SIMTRONICS
SAS.
Pour l'explosimètre et le toximètre, je me suis
servi de ce qui existait déjà avec KEP INFILINK avant mon
arrivée, ainsi que le modèle élaboré des travaux
antécédents.
Version KEP Version du stage
précédent
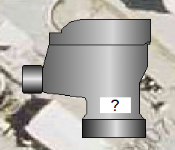

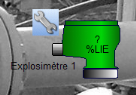
Ma version
De part l'étude de KEP qui m'a été
confiée, j'ai essayé de récupérer les points les
plus pertinents à mon goût, de façon a créer le
modèle le plus proche de la réalité possible, mais aussi
de pouvoir permettre aux développeurs qui me succèderont de faire
remonter l'information de défaut.
La particularité de PcVue est de pouvoir créer un
modèle lambda en y intégrant directement les variables
associées au modèle en question.
De ce fait, les variables pertinentes sont liées, ce qui
évite de renseigner le logiciel sur les variables accouplées au
modèle.
Le détecteur modélisé par KEP fonctionne
parfaitement, et se base sur trois zones d'animations.
Partie réseau

Corps du détecteur
Cartouche
Par analogie, j'ai reproduit ce système de zone sur ma
modélisation du capteur :
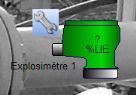
Partie haute (partie réseau)
Corps du détecteur
Cartouche
Ces zones d'animations permettent une meilleure précision
quant à la visualisation de l'endroit du défaut...
Pendant mon stage, j'ai appris que certains défauts
peuvent se répercuter sur des points particuliers du
détecteurs.
Par exemple, si un défaut apparaît sur la carte
réseau :
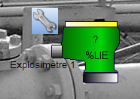
On distingue à ce moment là que la partie
réseau vire au dégradé jaune, ce qui indique qu'elle est
en défaut.
Il était très important de solutionner la
supervision de la partie réseau,
car elle est en elle-même l'interface qui régit
la communication entre le détecteur et le réseau SYNTEL.
Si un défaut apparaît autour du corps du
détecteur :
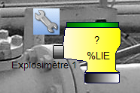
Cette fois, c'est le corps entier du détecteur qui
vire au dégradé jaune.
De manière générale, l'opérateur
doit savoir immédiatement que le système est en défaut, de
manière à contacter le service de maintenance du réseau
SYNTEL.
Dans le cas d'un défaut cartouche :
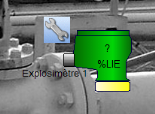
Dans ce cas là, la cartouche entière
elle-même vire au jaune.
Ce défaut est très important et doit
être réglé rapidement, car la cartouche est
l'élément permettant la mesure du gaz concerné.
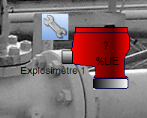
Dans le cas d'une alarme ou d'un lever de doute, le
détecteur prend la couleur rouge avec un dégradé
excentré.
La couleur rouge a été choisie car elle attire
l'oeil, et une alarme sur un détecteur signifie un danger imminent,
c'est-à-dire que soit l'alarme de niveau 1 s'est
déclenchée, soit celle de niveau 2, soit il faut pratiquer un
lever de doute sur le détecteur.
En ce qui concerne le détecteur de flamme, j'ai pris le
soin de recréer entièrement un modèle
indépendant.

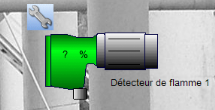
Après avoir demandé quelques conseils aux
différentes personnes pouvant m'aider, il s'est avéré que
le détecteur de flamme ne devait être placé cartouche vers
le bas, mais dans une direction choisie.
De plus, le détecteur de flamme doit être dans une
position haute.
Comme pour les détecteurs explosimètres et
toximètres, le détecteur possède trois zones d'animation,
pour plus de précision.
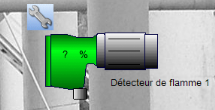
Partie réseau Corps du détecteur Cartouche
du détecteur
Il s'anime aussi de la même façon :
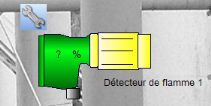
Pour un défaut cartouche
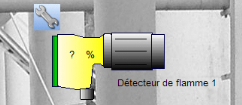
Pour un autotest par exemple
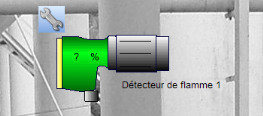
Défaut réseau
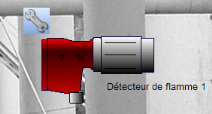
Dans le cas d'une pré alarme ou d'une alarme, le corps
et la partie haute du détecteur devienne rouge.
La méthodologie de développement de la supervision
que j'ai utilisée est d'utiliser les mêmes codes couleurs pour
tous les éléments du réseau SYNTEL. (Explosimètre,
Toximètre, Détecteur de flamme, Safebox, Relais...)
Pour les vues de détails, l'objectif était de
s'inspirer de KEP, de garder le même esprit, en apportant une touche de
nouveauté, et en tenant compte des travaux de mon
prédécesseur dans le même temps.
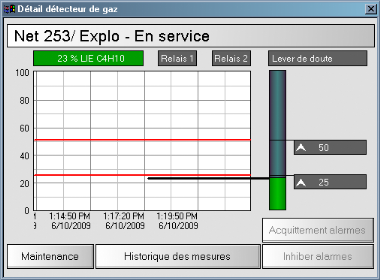
Vue de détails de l'explosimètre par KEP
INFILINK
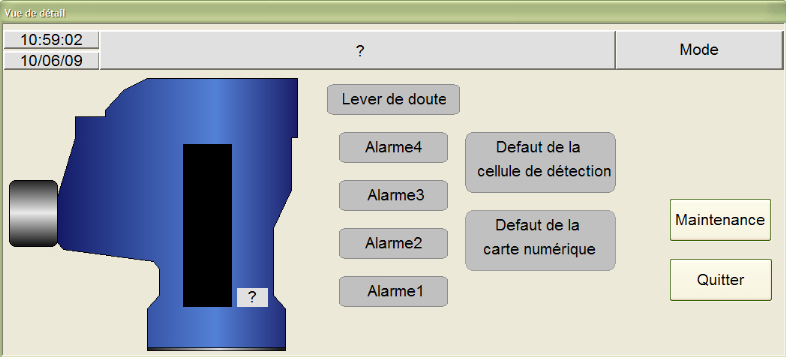
Vue de détails de l'explosimètre
réalisée par le stagiaire précédent
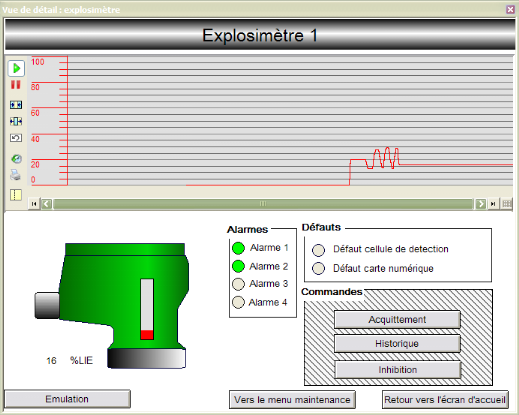
Voici donc la vue que j'ai proposée.
Tout d'abord, j'ai réuni pour moi les
éléments les plus pertinents qui devaient figurer sur une vue de
détail.
J'ai opté pour une vue de détails compacte et
structurée, avec plusieurs types d'espaces permettant de faire remonter
l'information à l'opérateur sous plusieurs formes.
Plusieurs espaces ont été mis en jeu pour
permettre à l'opérateur de voir, d'un simple clic de souris les
détails de son détecteur.
v L'espace courbe, sur la partie haute de la vue, qui permet
de voir évoluer les mesures en temps réel.
v Une autre représentation du détecteur, avec un
barre graphe incrusté qui varie en temps réel via la mesure du
détecteur.
v La signalisation est représentée par des
voyants encadrés ce qui permet de les différencier des commandes
qui elles, sont hachurées.
v Les commandes, représentées par des boutons,
sont encadrées et l'espace qui leur est dédié est
hachuré.
Le bouton « émulation » permet de
lancer une boite à boutons permettant de tester les défauts et de
les simuler.
Le bouton « Vers le menu maintenance »
permet de naviguer dans la maintenance du produit.
Le bouton « Vers l'écran
d'accueil » permet de fermer la vue de détails et de revenir
sur l'écran d'accueil.
Dans un second temps, j'ai dû aussi m'occuper des
alarmes.
Dans la supervision KEP INFILINK, les alarmes
déclenchent de la manière suivante :
v L'alarme de niveau 1 se déclenche quand le
détecteur dépasse les 25% LIE
v L'alarme de niveau 2 se déclenche quand le
détecteur dépasse les 50% LIE
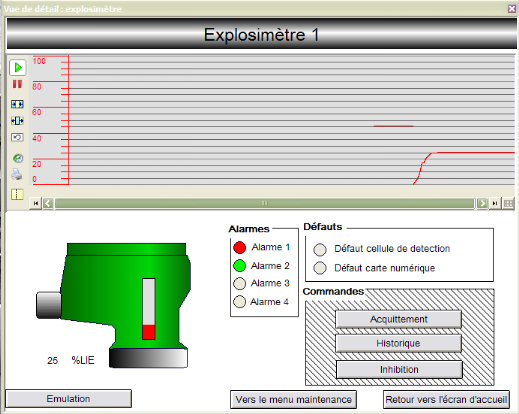
Dans ce cas, la variable interne de mesure signale qu'il faut
déclencher l'alarme de premier niveau
car on atteint 25% LIE.
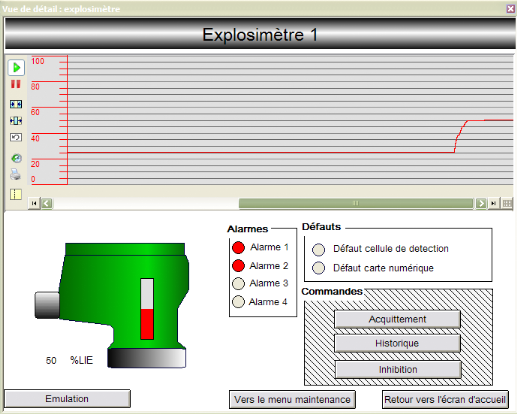
Maintenant, étant donné que la mesure a atteint
50%, l'alarme 2 doit être déclenchée
En ce qui concerne la vue de maintenance, j'ai essayé,
comme jusqu'à maintenant, de retenir les aspects positifs de KEP et des
travaux antécédents.
J'ai donc réuni, et réutilisé les points
que j'ai trouvés intéressants, à savoir :
v Les commandes à la volée
v La signalisation par zone pour mieux cibler les
défauts.
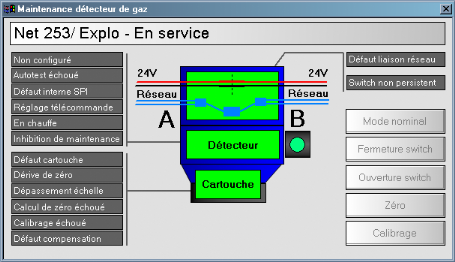
Sur cette vue de maintenance developpée sous Kep, on
distingue bien les commandes des voyants, c'est un aspect que j'ai voulu
reproduire.
Il était important pour moi de bien analyser la taille
des voyants, des boutons, de la représentation de capteur car cet
interface homme machine a été contrôlée et
critiquée par des personnes compétentes dans le métier de
l'automation.
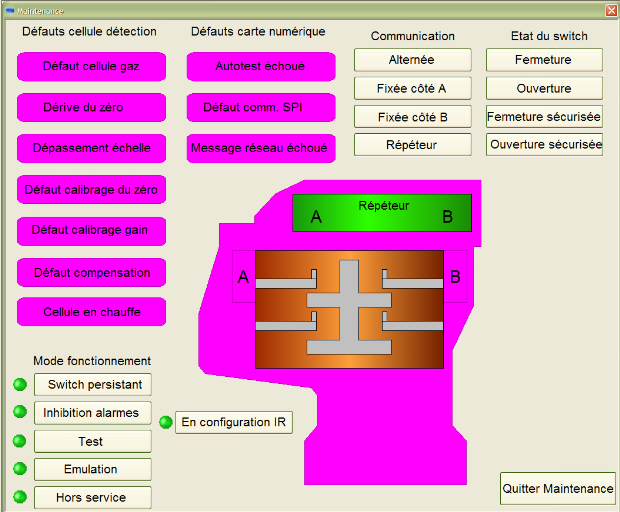
Cette vue m'a donné une idée quant à
la représentation de ma vue pour les différentes commandes
à créer, ainsi que les différentes signalisations.
Par analyse de ces anciens travaux, j'ai pu rapidement avoir
une vue globale sur ma vue de maintenance et les idées me sont venues.
Sur cette vue, il était impossible de revenir à
l'écran d'accueil, et par ailleurs, elle prenait entièrement
l'écran du superviseur.
La couleur (ici violet) est mal choisie pour
l'inactivité.
C'est avec de l'aide et des conseils, en lisant les rapports
de critiques que j'ai pu savoir que la couleur normalisée était
verte.
La couleur verte se justifie par le fait de la
normalité, du bon fonctionnement du système.
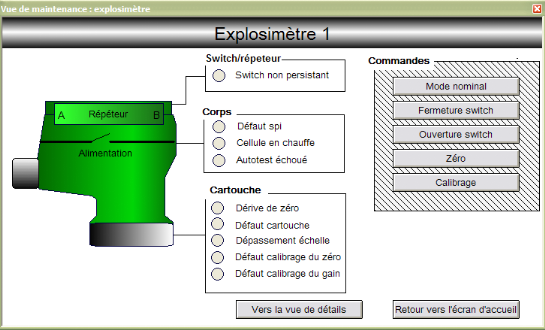
Voici donc la vue que j'ai proposée pour l'alternative
de KEP
Chaque défaut possède son voyant de
signalisation, et l'opérateur possède des commandes à la
volée.
De la vue de maintenance, on peut revenir via un clic vers la
vue de détails ou bien retourner sur la vue générale via
un clic sur le bouton « Retour vers l'écran
d'accueil ».
Les parties sont distinctes (voyants encadrés,
commandes hachurées)
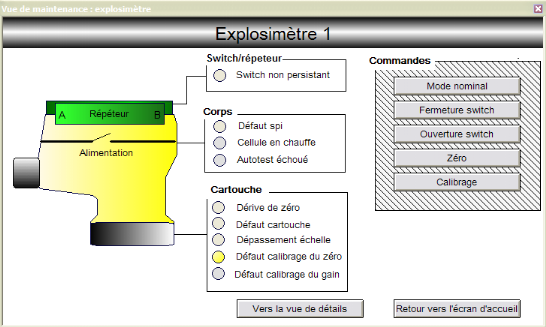
Si on déclenche un défaut
La partie concernée se met en défaut et le
voyant le signale.
J'ai élaboré la supervision de telle sorte que
l'on puisse revenir à l'écran d'accueil à partir de
n'importe quelle vue.
Chaque vue est indépendante, et il est possible de les
ouvrir et de les fermer sans interrompre le bon fonctionnement de la
supervision.
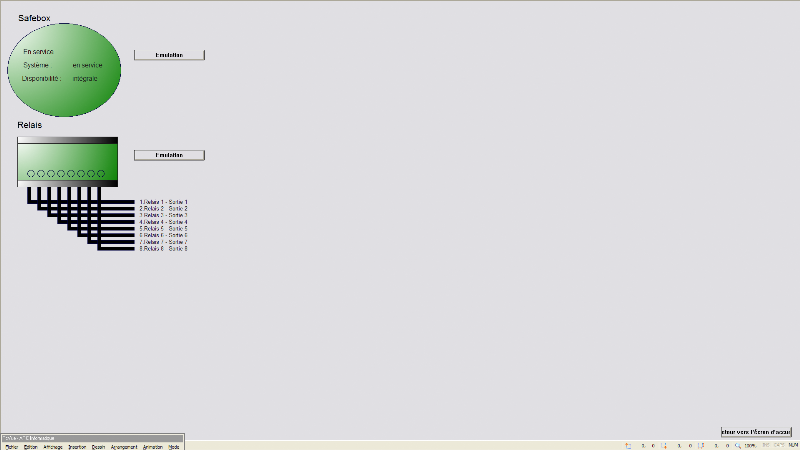
Pour les deux derniers éléments du
réseau, c'est-à-dire la safebox et le relais, il m'a
été conseillé de créer un autre espace de
maintenance, dans lesquels ils se situeront.
C'est dans cette espace que l'on pourra constater
l'état des safebox et relais.
Dans la supervision KEP INFILINK, la safebox était
représentée par un modèle rectangulaire.
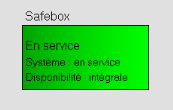
Dans le cas d'un défaut média
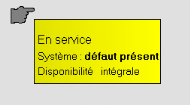
La safebox se colore en jaune, et
un libellé « défaut présent »
s'affiche.
Après étude de la safebox réelle, j'ai
opté pour un modèle rond, et qui donnera d'emblée une
précision supérieure au modèle KEP dans le cas d'un
défaut.
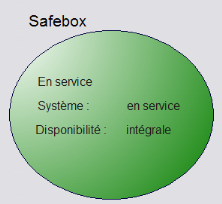
Dans le cadre d'un fonctionnement normal, la safebox
affiche Système : en service et une disponibilité
intégrale.
Dans le cas d'un défaut média :
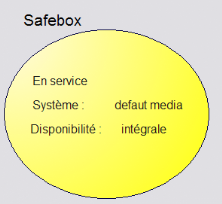
Cette fois, le système détecte un
défaut média et l'opérateur connaît directement la
nature de son défaut.
Plusieurs types de défauts peuvent apparaître sur
une safebox (défaut élément, défaut
détecteur, défaut alimentation, switch sécurisé...)
et dans tous les cas, la supervision remontera l'information directement en
affichant un libellé précis.
Dans le cas du relais, j'ai opté sur un modèle
équivalent à celui de KEP
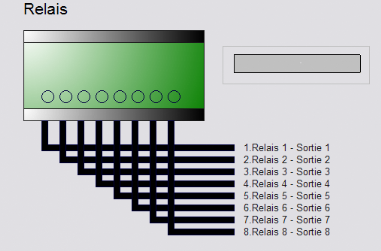
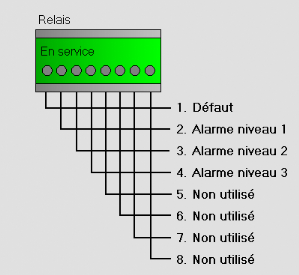
Représentation KEP INFILINK
Représentation PCVUE
Le but de la supervision est de faire remonter l'information
en cas de défaut sur une sortie.
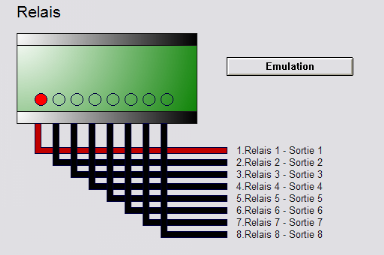
J'ai opté pour un défaut signalisé en
rouge pour chaque sortie défaillante.
Stage 08/09 chez SIMTRONICS SAS
Les critères importants d'une supervision
industrielle
Durant tout le développement de ma supervision, j'ai
tenu à garder une uniformité dans la différenciation des
commandes et des voyants.
J'ai opté pour un style sobre et clair, qui pour moi me
semblait le plus justifié pour une supervision de type industriel.
Le but de mon stage étant de proposer une alternative
à la solution déjà existante de KEP, il m'a fallu
travailler sur des idées d'amélioration de niveau
esthétique ainsi que pratique.
Je me suis donc concentré sur deux axes de
difficultés :
v ESTHETIQUE :
o Donner des critères importants à l'interface
homme machine dans le but de différencier le mode démonstration
du mode réel simplement.
v PRATIQUE :
o Pouvoir passer du mode démonstration (utilisant les
variables internes au superviseur PcVue) au mode réel (utilisant les
variables externes de type OPC)
Stage 08/09 chez SIMTRONICS SAS
L'aspect esthétique
Pour satisfaire au critère esthétique, qui
représentait 50% de mon objectif pour ma réalisation de projet,
j'ai du élaborer et améliorer au fur et à mesure ma
supervision.
Tout d'abord, concernant les modèles, ceux-ci ont
suivis plusieurs passes.
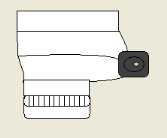
La version 1 du capteur, dessinée à mon
arrivée, a rapidement trouvé ses limites en terme
d'esthétique, il a donc fallu évolué sur la base du
travail précédent.
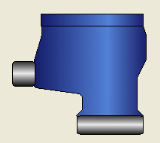
J'ai donc élaboré la version 2 du capteur,
en partie basée sur le travail du stagiaire qui m'a
précédé.
Ici, j'utilise une couleur bleue avec un
dégradé excentré.
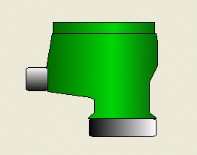
Pour ma version définitive, j'ai donné un
effet de dégradé sur la cartouche pour augmenter l'impression de
rondeur. J'ai aussi appliqué un dégradé. La couleur verte
m'a été imposée, synonyme de bon fonctionnement du
détecteur.
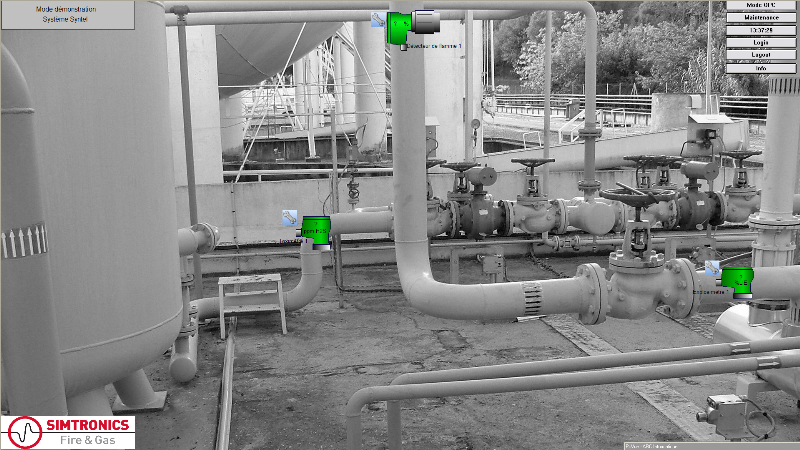
La version finale que j'ai proposée pour fournir
une alternative à KEP est celle-ci.
J'ai élaboré les différents menus
afin de proposer à l'opérateur une navigation
facile :
v MODE OPC : ce bouton permet de passer du mode
démonstration au mode OPC d'un seul clic
v Maintenance : ce bouton permet d'accéder
à la vue maintenance du système syntel
v L'heure
v Login : pour s'identifier
v Log out : pour clore une session
d'identification
v Info : pour avoir des informations sur
l'utilisateur courant
Stage 08/09 chez SIMTRONICS SAS
L'aspect pratique
Le problème qui a été rencontré
durant le développement sur KEP INFILINK était le passage du mode
démonstration au mode OPC réel.
J'ai donc du rechercher des solutions à ce
problème pour le proposer dans mon alternative sur PCVUE.
J'ai donc utilisé le système de branche sous
PCVUE, de façon à pouvoir passer du mode réel au mode
demonstration d'un seul clic.
Mode démonstration
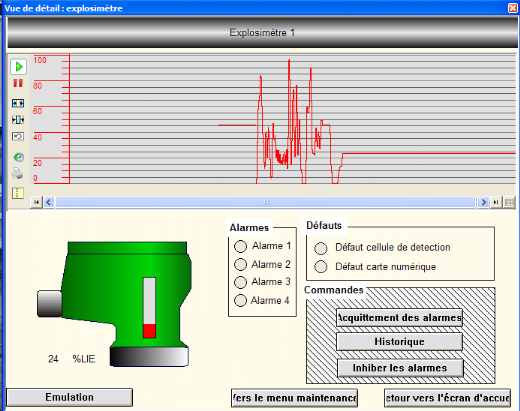
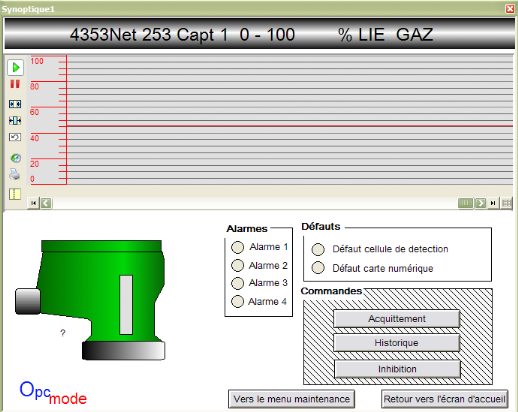
Clic sur
mode OPC
Mode réel
Stage 08/09 chez SIMTRONICS SAS
Le protocole OPC : OLE for Process Control
La technologie OPC est apparue en 1995. Cette technologie
dédiée à l'interopérabilité des
systèmes industriels signifiait initialement OLE for Process Control.
OPC n'est pas un protocole de communication mais une technologie basée
sur les technologies
OLE,
COM, et
DCOM développées
par
Microsoft pour sa famille
de
systèmes
d'exploitation.
OPC a été conçu pour relier les applications
Windows et les matériels et logiciels du contrôle de processus. La
norme définit une méthode cohérente pour accéder
aux données de terrain de dispositifs d'usine. Cette méthode
reste la même quel que soit le type et la source de données.
Les serveurs OPC fournissent une méthode permettant
à différents logiciels d'accéder aux données de
dispositifs de contrôle de processus, comme par exemple un automate.
Traditionnellement, chaque fois qu'un programme nécessitait
l'accès aux données d'un périphérique, une
interface personnalisée, un pilote ou driver, devait être
écrit. L'objectif de l'OPC est de définir une interface commune
écrite une fois puis réutilisées par n'importe quel
logiciel d'entreprise, SCADA,
IHM.
Une fois qu'un serveur OPC est écrit pour un périphérique
particulier, il peut être réutilisé par n'importe quelle
application qui est capable d'agir en tant que client OPC. Un serveur OPC
utilise la technologie Microsoft OLE (aussi connu sous le nom de Component
Object Model ou COM) pour communiquer avec les clients
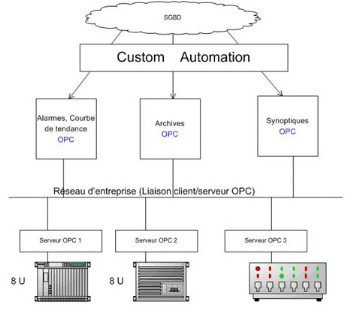
Stage 08/09 chez SIMTRONICS SAS
STRUCTURES DES VARIABLES OPC CHEZ SIMTRONICS SAS
Les items du serveur OPC d'ICARE se construisent comme suit :
net[<netID>].node[<nodeID>].<netvar>.<SNVT_type>!<SNVT_comp> :
...
Dans laquelle <netID> est l'identifiant du réseau,
<nodeID> celui du noeud, <netvar> le nom donné à la
variable réseau dans l'application du noeud, <SNVT_type> est le
type de la variable réseau, <SNVT_comp> est le nom pour un type
structuré sur plusieurs niveaux.
Les types de données des détecteurs sur le
serveur OPC sont décomposés en deux familles :
- ICARE_GAS, comprenant l'ensemble des détecteurs
liés aux gaz.
- ICARE_UV2IR comprenant l'ensemble des détecteurs
liés aux flammes.
Dans chacune des deux familles, on retrouve les données
sous plusieurs formes : en Bits et en Bytes.
Un bit contient une information.
Un byte contient huit informations.
Liste des données communes aux deux
familles :
|
COMMUN
|
|
Suffixe spécifique de l'item OPC
|
Bytes
|
Bits
|
Commandes
|
CommCmd
|
0 : Commande mode alterné
|
commande communication
|
1 : Commande mode fixé côté A
|
|
2 : Commande mode fixé côté B
|
|
3 : Commande mode répéteur
|
SwitchCmd
|
0 : Commande fermeture switch
|
commande du switch
|
1 : Commande ouverture switch
|
|
4 : Commande fermeture switch sécurisée
|
|
5 : Commande ouverture switch sécurisée
|
TransModeCmd
|
Bit 0 : inhibition alarmes
|
TransAlarmsInhibit : 1
|
commande mode de fonctionnement
|
Bit 1 : mode test liens réseau
|
NetTest : 1
|
|
Bit 2 : mode hors service
|
NetDisable : 1
|
|
Bit 5 : switch persistant
|
NetSwitchPersistent : 1
|
|
Bit 6 : mode émulation
|
NetEmultateDetector : 1
|
Défauts
|
TransFailure
|
Bit 0 : autotest carte échoué
|
TransTestFailure:Value : 1
|
défauts de la carte numérique
|
Bit 2 : Défaut comm SPI
|
TransSPIFailure:Value : 1
|
|
Bit 3 : message réseau échoué
|
NetMessageFailed:Value : 1
|
|
Bit 5.7 : cause du reset carte
|
NetResetInfo:Value
|
|
0 : inconnu
|
0 : inconnu
|
|
1 : power up
|
1 : power up
|
|
2 : pint reset Neuron Chip
|
2 : pint reset Neuron Chip
|
|
3 : software
|
3 : software
|
|
4 : watchdog
|
4 : watchdog
|
Informations
|
Quality
|
<>192 : Absent
|
présence du détecteur
|
= 192 : Présent
|
SwitchComm
|
Bit 0.2 : état du switch
|
Switch Value :
|
état du switch et de la communication
|
0 : fermé
|
0 : fermé
|
|
1 : ouvert
|
1 : ouvert
|
|
3 : ouvert sur incident
|
3 : ouvert sur incident
|
|
5 : ouvert en mode sécu
|
5 : ouvert en mode sécu
|
|
7 : inconnu
|
7 : inconnu
|
|
Bit 3 : comm mode repéteur
|
Repeater:Value : 1
|
|
Bit 4 : comm côté B
|
CommB:Value : 1
|
|
Bit 5 : comm côté A
|
CommA:Value : 1
|
|
Bit 6 : pas de tension côté B
|
PowerFailureB:Value : 1
|
|
Bit 7 : pas de tension côté A
|
PowerFailureA:Value 1
|
Liste des données propres à ICARE_GAS :
|
ICARE_GAS
|
|
Suffixe spécifique de l'item OPC
|
Bytes
|
Bits
|
Alarmes
|
Alarms
|
Bit 0 : alarme gaz niveau 1
|
Alarm1:Value : 1
|
alarmes du détecteur
|
Bit 1 : alarme gaz niveau 2
|
Alarm2:Value : 1
|
|
Bit 2 : alarme gaz niveau 3
|
Alarm3:Value : 1
|
|
Bit 3 : alarme gaz niveau 4
|
Alarm4:Value : 1
|
|
Bit 4 : protection sonde
|
SensorProtection:Value : 1
|
|
Bit 6 : alarme interne n1
|
LocalRelay1:Value : 1
|
|
Bit 7 : alarme interne n2
|
LocalRelay2 :Value : 1
|
Défauts
|
GasFailure
|
Bit 0 : défaut cellule gaz
|
SensorFailure:Value : 1
|
défauts de la cellule de détection
|
Bit 1 : dérive du zéro
|
ZeroShift:Value : 1
|
|
Bit 2 : dépassement échelle
|
ScaleLimitsExceeded:Value : 1
|
|
Bit 3 : défaut calibrage zéro
|
ZeroCalFailure:Value : 1
|
|
Bit 4 : défaut calibrage gain
|
GainCalFailure:Value : 1
|
|
Bit 5 : défaut compensation
|
CompensationFailure:Value : 1
|
Informations
|
|
Measure
|
Mesure du capteur sans facteur d'échelle
appliqué
|
mesure du capteur
|
|
|
Class
|
21 : capteur gaz 2G
|
modèle du capteur
|
23 capteur gaz 3G
|
TransMode
|
Bit 0 : alarmes gaz inhibées
|
TransAlarmsInhibited:Value : 1
|
mode de fonctionnement du capteur
|
Bit 1 : mode test
|
NetModeTestMode:Value : 1
|
|
Bit 2 : mode hors service
|
NetDisableMode:Value : 1
|
|
Bit 3 : en configuration IR
|
TransRemoteConfid:Value : 1
|
|
Bit 4 : cellule en chauffe
|
SensorWarmingUp:Value : 1
|
|
Bit 5 : switch persistant
|
NetPersistentSwitch:Value : 1
|
|
Bit 6 : mode émulation
|
NetEmulationMode:Value : 1
|
|
Bit 7 : en maintenance
|
TransMaintenanceMode:Value: 1
|
Liste des données propres à
ICARE_UV2IR :
|
ICARE_UV2IR
|
|
Suffixe spécifique de l'item OPC
|
Bytes
|
Bits
|
Alarmes
|
Alarms
|
Bit 0 : alarme flamme
|
Alarm:Value : 1
|
alarmes du détecteur
|
Bit 1 : préalarme flamme
|
Prealarm:Value : 1
|
|
Bit 6 : alarme interne n1
|
LocalRelay1:Value : 1
|
|
Bit 7 : alarme interne n2
|
LocalRelay2 :Value : 1
|
Défauts
|
FlameFailure
|
Bit 0 : défaut detection UV
|
UVFailure:Value : 1
|
défauts de la cellule de détection
|
Bit 1 : défaut detection IR
|
IRFailure:Value : 1
|
|
Bit 2 : défaut cellule detection
|
DetectorFailure:Value : 1
|
|
Bit 6 : mode simulation flamme
|
FlameSimulationMode:Value : 1
|
|
Bit 7 : mode test feu
|
FlameTestMode:Value : 1
|
Informations
|
Class
|
22 : uv2ir 3G
|
modèle du capteur
|
|
TransMode
|
Bit 0 : alarme flamme inhibée
|
TransAlarmsInhibited:Value : 1
|
mode de fonctionnement du capteur
|
Bit 1 : mode test
|
NetModeTestMode:Value : 1
|
|
Bit 2 : mode hors service
|
NetDisableMode:Value : 1
|
|
Bit 3 : en configuration IR
|
TransRemoteConfid:Value : 1
|
|
Bit 5 : switch persistant
|
NetPersistentSwitch:Value : 1
|
|
Bit 6 : mode émulation
|
NetEmulationMode:Value : 1
|
|
Bit 7 : en maintenance
|
TransMaintenanceMode:Value: 1
|
FlameIR
|
FlameIR:Value : 1
|
détection de flamme par infrarouge
|
|
|
FlameUV
|
FlameUV:Value : 1
|
détection de flamme par ultraviolet
|
|
|
Arborescence du serveur OPC :
Voici comment se présentent l'arborescence des
variables OPC :
Net[255]
Node[4354]
nvi_Activate
ICARE_CommCmd
nvi_ModeTrans
ICARE_TransModeCmd
Bits
NetDisable
NetEmulateDetector
NetSwitchPersistent
NetTest
TransAlarmsInhibit
Bytes
nvi_Relay
ICARE_SwitchCmd
nvo_Life_Signal
ICARE_Gas
Bits
Class
Measure
Switch
Repeater
CommB
CommA
PowerFailureB
PowerFailureA
Alarm1
Alarm2
Alarm3
Alarm4
SensorProtection
LocalRelay1
LocalRelay2
SensorFailure
ZeroShift
ScaleLimitsExceeded
ZeroCalFailure
GainCalFailure
CompensationFailure
TransUnconfigured
TransTestFailure
TransSPIFailure
NetMessageFailed
NetResetInfo
TransAlarmsInhibited
NetTestMode
NetDisabledMode
TransRemoteConfig
SensorWarmingUp
NetPersistentSwitch
NetEmulationMode
TransMaintenanceMode
Bytes
Class
Measure
SwitchComm
Alarms
GasFailure
TransFailure
TransMode
Description
Quality
Stage 08/09 chez SIMTRONICS SAS
Optimisation
Dans le but de pouvoir permettre à SIMTRONICS SAS
d'exploiter mon travail après la fin de mon stage, il m'a fallu,
après avoir complètement réalisé le mode de
démonstration, optimiser le mode OPC de façon à avoir le
moins de variables externes possibles.
En effet, les variables dites « externes »
sont en réalité les variables liées à des variables
OPC du serveur OPC.
Par ailleurs, dans le cas de PCVUE, le prix du logiciel
dépend du nombre de variables externes utilisées.
C'est pourquoi l'optimisation est une étape importante
dans le but de réduire au maximum le coût financier de la
supervision.
Pour le mode OPC de mon projet, nous avons donc
décidé de travailler uniquement en bytes, permettant dans un
premier temps de réduire le nombre de variables externes.
C'est pour cela qu'il m'a fallu établir une
méthode de travail rigoureuse.
Stage 08/09 chez SIMTRONICS SAS
Méthode de travail en mode OPC réel
La méthode de travail que j'ai utilisée est la
suivante :
1. Lancement du configurateur SYNTEL pour pouvoir
émuler un changement d'état sur le serveur OPC
2. Lancement du client OPC « SOFTING OPC TOOLBOX
DEMO CLIENT »
3. Lancement du superviseur PCVUE pour les procédures
de tests.
Par exemple, pour la variable qui permet de retourner la
valeur de la mesure du capteur.
On crée la variable Measure qui sera associée
à la variable externe OPC du serveur ICARE :
net[255].node[4353].nvo_LifeSignal!ICARE_Gas!Bytes!Measure
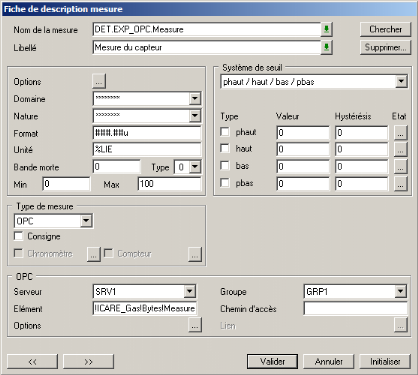
Via le configurateur, on émule une mesure qui va se
répercuter sur le serveur OPC
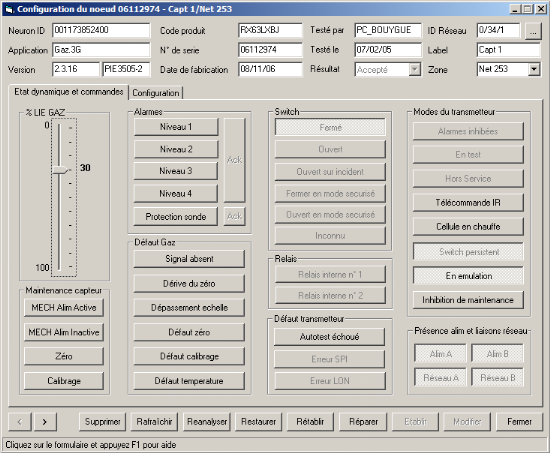
Ici, on a émulé une mesure du capteur de
30%LIE

La valeur est repercutée sur le client OPC qui nous
permet de vérifier si le serveur OPC a bien pris en compte la nouvelle
valeur :
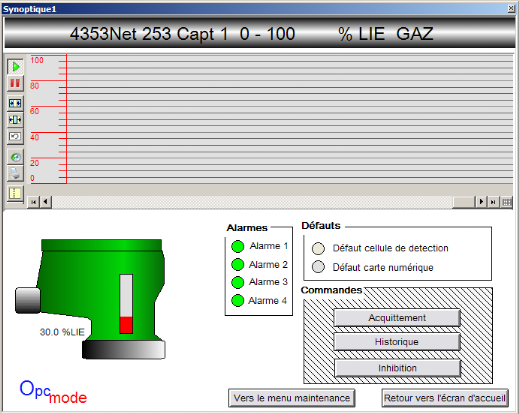
On a lié la variable measure au barre graphe sur la vue
de détails du capteur sur PCVUE
Le serveur OPC répond bien à la supervision, le
principe reste le même pour tout le reste du développement.
Conclusion
Ce stage pratique au sein de l'entreprise Simtronics SAS m'a
permit de mettre en pratique les connaissances acquises au cours de la
formation théorique à la faculté des sciences de St
Jérôme.
J'ai pu approfondir ces compétences et en
acquérir de nouvelles tant au niveau du développement sur
d'autres superviseurs que dans la méthodologie de réalisation.
Le stage m'a offert la possibilité d'intégrer
une équipe dynamique qui m'a guidé tout au long de la
réalisation de mon projet. J'ai pu vérifier mes
compétences au sein de cette équipe dans laquelle l'adaptation a
été aisée et où j'ai pu évoluer tout au long
de mon stage. Le développement des compétences a
été possible grâce a un partage de savoir entre les
différents membres de l'entreprise.
Le stage m'a offert une expérience intérressante
tant au point de vue technique (développement, réalisation) qu'au
point de vue humain (travail et coordination en équipe).
Les outils de développement convenaient parfaitement au
contenu du programme qui nous a été proposé par les
enseignants à la faculté des sciences de St Jérôme
ainsi qu'au lycée du Rempart.
|