1-Introduction :
Le verre a connu, ces dernières décennies, une
évolution technologique spectaculaire dans le secteur du bâtiment.
Il est ainsi passé de la simple vitre au vitrage possédant de
multiples propriétés tel la résistance mécanique,
sécurité, isolation thermique et acoustique, contrôle
solaire et décoration.
Les exigences du domaine de bâtiment au niveau de la
consommation énergétique de la construction, ses
résistances aux différents agents climatiques, son coté
esthétique et la commodité de son entretien, nous pousse à
bien choisir les bons matériaux pour la réaliser. Grace à
ses qualités obtenues lors de sa transformation, le verre se voit un
matériau de valeur qui pourra satisfaire aux exigences citées.
En effet, le dépôt de couche d'oxydes sur le
verre lui offre de des nouvelles propriétés, ainsi le verre
acquit des nouvelles fonctionnalités ; on cité l'autonettoyant
pour l'oxyde de titane, l'electrochrome pour l'oxyde de tungstène et
autre fonctionnalités.
De même le verre feuilleté, se
caractérisant par sa résistance mécanique
élavée, donne à la structure un aspect sécuritaire,
il est efficace contre les actes de vandalisme et en se brisant, le risque de
blessure et bien amorti.
Le vitrage isolant se distingue comme étant la solution
pour une consommation économique de l'énergie d'une maison ;
aussi, son isolation acoustique assure une sérénité
totale, ce qui lui ouvre le champ pour son utilisation dans des édifices
spéciaux comme les hôpitaux, écoles...etc.
Avec tous ses avantages, et les bénéfices qu'il
apporte au monde de la construction, le verre reste un matériau
indifférencié dans notre pays ; et pourtant, son utilisation chez
nous s'avère de plus en plus nécessaire.
2- Généralités sur le verre
2.1- définition du verre :
Plusieurs définitions peuvent être données
pour un verre. Par exemple, l'Encyclopedia Universalis (Reyches, 1989) rapporte
de nombreuses définitions du verre selon différents points de vue
:
> Définition courante : solide obtenu par le figeage
d'un liquide ;
> Définition structurale : un verre est un solide non
cristallin.
On peut aussi dire que le verre est formé par un
assemblage tridimensionnel désordonné de groupements structuraux
fondamentaux, semblables à ceux de l'état cristallin ;
> Définition thermodynamique : il s'agit d'un
matériau hors d'équilibre, dont l'énergie est
supérieure à celle des produits cristallisés
correspondants et dont le retour à une situation plus stable
(cristallisation) ne peut pas se faire qu'après des durées
considérables.
Selon l'American Society for Testing Materials (1945), le
verre est un matériau inorganique produit par fusion, qui a
été refroidi dans des conditions qui ont empêché sa
cristallisation. D'après Zarzycki (1982), un verre est un solide non
cristallin présentant une transition vitreuse. Et selon Sholze (1991),
le verre est un liquide surfondu figé.
La modalité de solidification d'un verre est
très différente de celle de la silice cristalline. Lorsqu'on
refroidit de la silice fondue, elle cristallise à une température
donnée (température de cristallisation : Tc). En revanche pour un
verre, pendant un intervalle dit de transformation (entre Tt et Tc), on assiste
à un passage progressif par des états de viscosité
différents, de l'état liquide vers l'état vitreux. Dans
cet intervalle, le verre se comporte comme un liquide surfondu. Tt est
définie comme la Température de transition ; pour un verre
silicaté il s'agit de la température à laquelle la
viscosité est voisine de 1013 poises (Zarzycky, 1982).
2.2- Structure et vitrification :
2.2.1- Critère de GOLDSCHMIDT :
En cherchant les conditions de vitrification pour les oxydes
simples de formule stoechiométrique AmOn, Goldschmidt a cru que le
critère pouvait être le rapport rA/r0 des rayons ionique du cation
et de 1 ' oxygène ; pour les oxydes formant des verres, ce rapport
devrait être compris entre 0,2 et O, 4. Or d'après les
considérations classiques de cristallochimie, pour des structures
ioniques, ce rapport est en relation directe avec le nombre de coordination du
cation central, d'où l'intervalle proposé implique donc une
coordination tétraédrique. [1]
2.2.2- Règles de ZACHARIASEN :
Un examen plus complet de différents cas montre que le
critère de Goldschmidt est insuffisant : l'oxyde de BeO par exemple qui
pourtant satisfait au critère étant impossible à
vitrifier. Zachariasen a repris le problème et, par un raisonnement
empirique, a établi un ensemble de règles qui ont eu un
retentissement considérable sur la recherche verrière. Son
analyse était fondée sur la considération suivante :
a) les forces de liaisons interatomiques dans le verre et dans
le cristal doivent être semblable, étant donné les
propriétés mécaniques voisines des deux types de
solides.
b) comme les cristaux, les verres doivent être
formés par un "réseau" tridimensionnel étendu, mais le
caractère diffus des spectres de diffraction X montre que ce
réseau n'est pas symétrique et périodique comme dans les
cristaux, c'est à dire qu'il n'y a pas d'ordre à longue
distance.
Le désordre du réseau introduirait une
distribution des forces de liaison ; leur rupture progressive au chauffage
expliquerait la décroissance graduelle de la viscosité. Le
désordre expliquerait de plus un contenu énergétique
supérieur à celui du cristal.
Zachariasen a montré qu'un oxyde formant un verre
devrait satisfaire à l'ensemble des règles suivantes :
1. - le nombre d'oxygènes entourant 1 'atome cation doit
être petit,
2.- aucun oxygène ne doit être lié à
plus de deux cation A.
3.- les polyèdres peuvent avoir des sommets communs mais
pas d'arrêtes ni de faces communes.
4. - au moins trois sommets de chaque polyèdre doivent
être partagés avec d'autres polyèdres.
Zachariasen a ensuite passé en revue les
possibilités de vitrification suivant la stoechiométrie de
l'oxyde. Les oxydes A2O ou AO ne peuvent satisfaire aux règles
précédentes et ne devraient donc pas former de verres. Et
effectivement, aucun des oxydes des éléments des groupes I et II
ne forme de verre.
Les règles 2, 3 et 4 sont satisfaites :
a) dans les oxydes A2O3 lorsque les oxygènes
formant des triangles autour des atomes A.
b) pour les oxydes AO2 et A2O5 lorsque les
oxygènes forment des tétraèdres.
c) pour les oxydes AO3, A2O7 lorsqu'ils forment des
octaèdres.
Ne connaissant pas d'exemple de formation de verre dans ce
groupe, Zachariasen a conclu que seuls les arrangements triangulaires et
tétraédriques satisfaisant aux conditions de la règle 1
qu'il a rendue plus spécifique : « le nombre des oxygène
entourant A doit être 3ou 4«.
En examinant systématiquement les
propriétés de coordinence des cations dans différentes
oxydes cristallisés ; zakariassen a conclu que seul B2O3,
SiO2, GeO2, P2O5, As2O5 et As2O3 ont été
réellement vérifiés. Ils satisfont tous aux règles.
La structure de SiO2 et GeO2 étant basée sur des
tétraèdres (AO4) et celle de B2O3 et
As2O3 sur des triangles (AO3) [1].
2.2.3- La transition vitreuse
Le phénomène de la transition vitreuse est bien
illustre par l'évolution du volume en fonction de la température.
La figure () montre schématiquement l'exemple d'un liquide suffisamment
visqueux à TL pour franchir cette température sans
cristalliser. On voit sur cette figure que le volume au-dessous de TL
se situe d'abord dans l'extrapolation des valeurs qu'il prend au-dessus de
TL.
Mais a la température TG ou la
viscosité atteint environ 1012 Pa.S., il y a une diminution
significative de la pente de la courbe de variation qui devient proche de celle
que présente le solide cristallise.
En revanche à cette température TG on
n'observe pas de changement brutal du volume comme c'est le cas lorsqu'il y a
passage de l'état liquide à l'état solide. Ceci montre
qu»il n'y a pas de variation structurale au passage de TG. La substance
obtenue au-dessous de TG, qui a la structure du liquide mais les
propriétés du solide, est le verre.
La transition vitreuse s'observe aussi en suivant les
variations, en fonction de la température, de diverses
propriétés comme l'indice de réfraction, l'enthalpie, la
conductivité électrique : on constate systématiquement a
TG un changement de la pente de la courbe représentative de la
propriété en fonction de T [2].
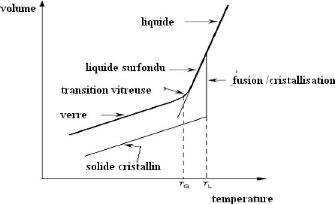
Figure 1. Genèse de l'état vitreux
2.3- Les propriétés du verre :
2.3.1- Propriétés rhéologiques
2.3.1.1- Viscosité :
La viscosité peut être définie comme le
frottement interne des liquides. Elle est mesurée en poise, le poise
étant la viscosité dynamique d'un liquide opposant une
résistance d'une dyne au glissement dans son plan d'une surface plane
d'un centimètre carré, avec un gradient de vitesse d'un
centimètre par seconde et par centimètre.
Elle est désignée, par la lettre grecque
ç. Son inverse, utilisé dans certains calculs,
y, est la fluidité. La viscosité est la caractéristique la
plus importante des verres. Sa connaissance est indispensable à leur
élaboration et à leur utilisation. Elle conditionne, en
particulier, tous les procédés de façonnage. Quelques
valeurs de viscosité exprimées en logarithme décimal et
les températures correspondantes.
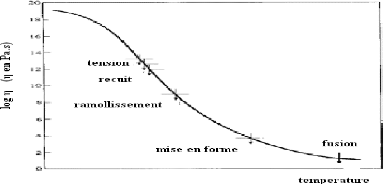

Figure 2.Variation de la viscosité en fonction de la
température. Tableau1 : Points fixes de viscosité.
Points Fixes
|
log ç
(ç en Pa.s)
|
Opération technique
|
Température de fusion
|
1
|
Fusion et affinage
|
Température de travail
|
3
|
Cueillage, moulage, étirage,
laminage, soudure
|
Température de ramollissement
|
6,65
|
Soufflage (Littleton)
|
Température de ramollissement
dilatométrique (point R)
|
10
|
Sortie de moule
|
Annealing point
|
12
|
Début de recuisson
|
Point S (transition vitreuse)
|
12
|
|
Strain point
|
13,5
|
Fin de recuisson
|
Point I
|
15
|
|
2.3.1.2- La tension superficielle :
Au sein d'un liquide ou d'un solide isotrope, l'ensemble des
forces de liaison auxquelles est soumis un atome ont une résultante
nulle alors que celles qui agissent sur un atome situe a la surface libre ont
une résultante f non nulle dirigée vers l'intérieur.
Par conséquent pour accroitre l'aire de la surface
libre il faut fournir un travail pour transférer les atomes de
l'intérieur vers la surface, en s'opposant à la force f. On admet
que si la surface libre d'un système thermodynamique augmente de dA, son
énergie libre augmente de :
dW = ó .dA.
Le facteur de proportionnalité ó
entre le travail dépense et l'accroissement de la surface se nomme
« énergie de surface « ou « tension superficielle «
et s'exprime en J.m-2.
2.3.2- Propriétés électriques
2.3.2.1- Conductibilité électrique :

Le passage du courant dans un matériau, ou
phénomène de conduction électrique est
caractérisé par la conductivité définie par la
relation :
P = ó E
Où P est la densité de courant et E le champ
électrique appliqué.
Dans le cas d'un matériau isotrope comme le verre,
ó est un scalaire, l'inverse de
ó est la résistivité
ò. Les unités et sont respectivement m et
(em) -1. La conductivité des verres dépend
essentiellement de leur nature .A la température ambiante, la plupart
des verres d'oxydes sont des isolants types, leur conductivité
étant de l'ordre de 10 - 17 à 10 - 5 (em) -
1.
2.3.3- Propriétés mécaniques
2.3.2.1- La dureté :
La dureté en général est la
résistance d'un solide à la pénétration d'une
pointe, d'une bille d'un outil, c'est à dire à la
déformation de la surface. Dans l'industrie verrière, la
dureté est une des propriétés les plus importantes, c'est
une grandeur qui nous détermine les verres durs et les verres
tendres.
Pour différencier les verres à faible
coefficient de dilatation qui se ramollissent à température
élevée (verres durs), des verres à coefficient de
dilatation élevée (supérieur à 50.10-7) qui se
ramollissent à température relativement basse (verres
tendres).
Le classement des verres, au point de vue de la dureté
dépend de la méthode d'essai. Ces différentes
méthodes : rayures, abrasion, empreinte reposent sur des principes
différents, elles conduisent donc à des résultats qui ne
sont pas comparables. D'autres essais tel que celui du
célérimètre ont été faits pour
établir un classement plus précis.
Ce classement se base soit sur la valeur de la force
nécessaire pour créer une rayure de dimension donnée, soit
sur les dimensions d'une rayure créé sous l'effet d'une
donnée.
2.3.2.2- Densité
La densité du verre est de 2,5, soit une masse de 2,5
kg par m2 et par mm d'épaisseur pour les vitrages plans. La masse
volumique, exprimée dans le système d'unités légal,
est de 2 500 kg/m3. Un m2 de verre 4mm a donc une masse de 10 kg
2.3.2.3 - Résistance à la compression
La résistance du verre à la compression est
très élevée : 1000 N/mm2 ou 1 000MPa. Ceci signifie que,
pour briser un cube de verre de 1 cm de côté, la charge
nécessaire est de l'ordre de 10 tonnes.
2.3.2.4 - Résistance à la flexion
Un vitrage soumis à la flexion a une face en
compression et une face en extension. La résistance à la rupture
en flexion est de l'ordre de : 40 MPa (N/mm2) pour un verre float recuit ; 120
à 200 MPa (N/mm2) pour un verre trempé (suivant épaisseur,
façonnage des bords et type d'ouvrage). La valeur élevée
de la résistance du verre trempé (SGG SECURIT) est due au fait
que son traitement met les faces du vitrage en forte compression.
2.3.2.5- Élasticité
Un corps solide subit une déformation sous l'action
d'une force de déformation, si cette déformation disparaît
par suppression de la force, le corps est appelé élastique. La
loi de HOOK exprime que la déformation D est proportionnelle à la
contrainte ó appliquée.
ó = E.D
Le verre est un matériau parfaitement élastique
: il ne présente jamais de déformation permanente. Il est
cependant fragile, c'est-à-dire que, soumis à une flexion
croissante, il casse sans présenter de signes précurseurs.
2.3.2.6- Module de Young, E
Ce module exprime la force de traction qu'il faudrait
théoriquement appliquer à une éprouvette de verre pour lui
communiquer un allongement égal à sa longueur initiale. Il
s'exprime en force par unité de surface. Pour le verre, selon les normes
européennes :
E = 7x1010 Pa= 70 GPa.
2.3.2.7- Coefficient de Poisson :
Lorsqu'une éprouvette subit un allongement sous
l'influence d'une contrainte mécanique, on constate un
rétrécissement de sa section. Le coefficient de Poisson Ó
est le rapport entre le rétrécissement unitaire sur une direction
perpendiculaire au sens de l'effort et l'allongement unitaire dans la direction
de l'effort. Pour les vitrages du bâtiment, la valeur du coefficient
Ó est de 0,2.
2.3.4- Les propriétés thermiques
Les propriétés thermiques sont directement
liées aux changements de température. Ce sont essentiellement :
la chaleur spécifique, le coefficient de dilatation thermique et la
conductivité thermique.
2.3.4.1- La chaleur massique
Dans la pratique, la grandeur la plus utile est la chaleur
massique c qui est la quantité de chaleur qu'il faut apporter a un
kilogramme de la Substance pour élever de un degré sa
température.
La chaleur massique c varie peu d'un verre a l'autre ; pour un
verre sodocalcique Au-dessous TG, c varie en fonction de la température
suivant l'équation empirique :
c = 909,81 + 0,34682 T - 1,7641.107
T-2 [6]
c étant exprime en
J.kg-1.K-1 et T en K. A 300 K on trouve c
= 818 J.kg-1.K-1.
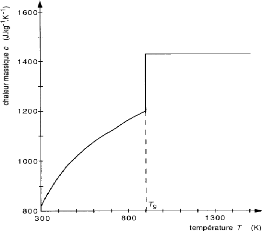
Figure3. La chaleur spécifique d'un verre sodo-calcique en
fonction de la température
2.3.4.2- La conductivité thermique :
La conductivité thermique mesure la capacité
d'un matériau conduire la chaleur. Elle définit comme le rapport
du flux de chaleur au gradient de température ; elle est mesurée
en joules par seconde par mètre carré de surface d'un corps pour
une différence de température de 1°C par 1
mètre d'épaisseur. [j/m.s.c].
La conductivité thermique d'un verre à la
température ambiante est relativement faible elle est d'environ :
2.926à 5.434 kJ/m.s.c.
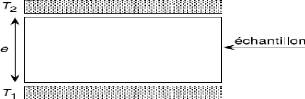
Figure 4.dispositif pour la mesure de la conductivité
thermique
2.3.4.3- La dilatation thermique :
La dilatation thermique d'un verre joue un grand rôle
dans sa résistance au changement de température. Elle
dépend beaucoup de la composition en oxydes, on peut en calculer
approximativement la valeur à partir de la composition chimique.
Actuellement elle est mesurée à l'aide de dilatomètre.
[4]
Tableau 2.dilatation thermique de quelques verres.
Type du verre
|
á °C 10-7
|
verre plat
|
80-90.
|
Verre borosilicate
|
80
|
vycore
|
8
|
2.3.5- Propriété optique :
2.3.5.1- Transparence :
La transparence d'un verre est une notion liée à la
transmission optique définie par la loi de Beer Lambert :

Avec I0 intensité d'un rayon entrant dans un
volume, défini à l'intérieur du verre, d'épaisseur
x, I intensité du rayon émergeant.
á est le coefficient d'absorption qui est relié
à l'indice d'absorption K par :

Si la transmission est mesurée au travers d'un volume de
matière, l'intensité transmise est plus faible en raison des
pertes par réflexion sur les faces d'entrée et de sortie. Dans le
cas où le rayon lumineux entrant est sous incidence normale.
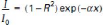
Où R exprime la réflexion :

n' : est le rapport entre l'indice de
réfraction du verre et celui du milieu environnant. Dans le domaine du
visible, K, qui a une très faible valeur, peut être
négligé.
n et K sont respectivement les grandeurs
réelles et imaginaires de l'indice de réfraction complexe

Ces grandeurs sont les manifestations de l'interaction d'une onde
électromagnétique avec des oscillateurs du réseau.
2.3.5.2- L'indice de réfraction du verre :
Il est calculé à partir de la formule
:

Où c est la vitesse de la lumière dans le vide,
v est la vitesse de la lumière dans le verre. Le verre étant un
matériau diélectrique, l'indice de réfraction complexe est
relié à la permittivité relative complexe.

À l'aide de cette expression et de l'équation du
mouvement pour un oscillateur harmonique simple, on peut calculer les
évolutions de n et K en fonction de la fréquence.
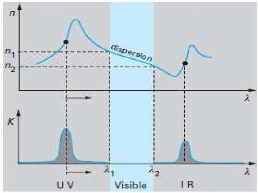
Figure 5.évolution de l'indice de réfraction et
de l'absorption du verre en fonction de la fréquence ou de la
longueur d'onde de la lumière incidente.
2.3.5.3- La transmission
La transmission est l'aptitude d'un verre à laisser
passer la lumière. Le coefficient de transmission d'un verre de lunettes
est le rapport entre la lumière émergente et la lumière
incidente. Le coefficient de transmission est plus élevé sur un
verre de lunettes traité contre les reflets que sur un verre non
traité.

L'indice de réfraction n varie brutalement lorsque la
fréquence de la lumière incidente devient proche de celle
correspondant à la résonance de l'oscillateur. Pour cette
fréquence, l'absorption est maximale. La transmission optique
décroît lorsque l'indice augmente en raison des réflexions
déjà mentionnées. La perte par réflexion est
particulièrement importante pour les verres de chalcogénures qui,
bien que transparents dans le domaine de l'infrarouge, ont un indice
élevé [5].
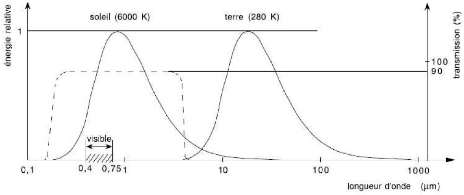
Figure 6.Situation du spectre de transmission du verre par
rapport aux spectres des rayonnements solaire et terrestre et à la
lumière visible
2.3.6- Propriétés chimiques :
Les verres sont généralement
considérés comme des matériaux résistants bien aux
différents agents chimiques. Pour cette raison, ils sont utilisés
à la fabrication des contenants destinés au stockage et au
transport des denrées alimentaires, des produits chimiques et
pharmaceutiques ; on les utilise généralement dans l'industrie,
en milieu corrosif sous forme de : verre de regard, canalisation, appareils
à distiller, ... etc.
Cependant, tous les verres n'ont pas la même
résistance aux agents chimiques et il est indispensable d'arrêter
un choix judicieux sur un verre, de bien connaître son comportement aux
différentes attaques possibles à l'eau, alcaline, acide [5].
2.3.6.1- Mécanisme de l'attaque :
L'eau est susceptible d'hydrolyser le verre, les ions
H+ prend la place des ions Na+ ou Ca2 + qui passent en
solution aqueuse. Il se forme à la surface du verre un gel de silice qui
peut retenir les ions alcalins et place le verre dans les conditions d'attaque
alcaline. Les solutions alcalines peuvent dissoudre la silice elle même,
de sorte que l'attaque est plus rapide que celle de l'eau. La vitesse d'attaque
est sensiblement constante et elle est une fonction exponentielle de la
température et du pH. L'acide fluorhydrique agit de la même
façon. Les acides ordinaires dissolvent seulement les alcalins et
alcalino-terreux, de sorte qu'ils ne peuvent attaquer le verre en profondeur
qu'après avoir diffusé à travers le réseau de
silice. Ce mécanisme explique le fait que la vitesse d'attaque
décroît en fonction du temps.
2.3.6.2- Essai d'altérabilité :
La vitesse de corrosion dépend d'un grand nombre de
facteurs de sorte qu'un seul essai d'utilisation réelle peut enseigner
exactement sur l'attaque, dans les conditions données. Toutefois, on
peut évaluer la résistance moyenne des verres et les classer en
les soumettant à des essais normalisés.
a-Attaque à l'eau :
L'eau attaque le verre après un temps très long
de contact. Il se produit un phénomène de dévitrification
et extraction. L'extraction est la conséquence du contact de l'eau avec
la surface du verre. L'attaque par l'eau est beaucoup plus forte aux
températures élevées.
La teneur en CaO et en SiO2 joue également un
rôle tel que la solubilité de ces corps à
température élevée est supérieure à celle
des alcalins. Les verres contenant B2O3 sont particulièrement
résistants, mais ce sont les verres quartzeux qui ont la
résistance la plus élevée.
b-L'attaque acide :
L'attaque du verre par les acides ne diffère pas de
celle par l'eau aux basses températures au début de contact mais
dans le cas général, après un certain temps on remarque
qu'il y a formation de couches de protection à la surface du verre, il
en résulte une diminution de l'attaque, c'est ainsi que l'acide
sulfurique forme des couches de protection de BaSO4 sur les verres contenants
du baryum ou plomb.
c-L'attaque alcaline :
L'eau et l'acide extraient les substances du verre, tandis que
les alcalis la dissolvent. Il n'y pas formation de couches protectrices tout le
verre est peu à peu désagrégé. L'action des
alcalines caractéristiques des carbonates et des solutions d'ammoniaque
est la plus forte, la dissolution de la surface du verre est 100 à 1
000fois plus grande que par l'eau. Les verres les plus sensibles aux alcalis
sont ceux qui contiennent beaucoup de B2O3 et
P2O5 ou ZnO et PbO mais peu de SiO2 et de CaO. Al2O3 augmente
généralement la résistance aux alcalins. Un alcalin
très faible agit comme l'eau.
3- La fabrication du verre plat
L'idée de produire un verre plat sur un substrat
métallique remonte au 19ème siècle. Le premier travail est
du à M. Henry Bessemer qui obtint un brevet pour un
procédé de production du verre sur un lit de métal fondu.
Il évoque la nécessité de travailler en atmosphère
réduite afin de prévenir l'oxydation de l'étain. Un
prototype plus intéressant, attribuable à la Pittisburg Plate
Glass Company, date des années 1920. Le système
expérimental prévoyait l'ajout d'un petit bain de métal
(étain ou Plomb) au four d'écrémage du verre (Edge,
1992).
Le verre devait être refroidi immergé dans le
bain métallique et retiré du bain au moyen d'une série de
rouleaux. Bien que construit ce système n'a jamais été
productif. Le système de production actuelle se base sur le dispositif
breveté par Sir Alastair Pilkington en 1959.
Ce procédé prévoit la production d'un
ruban de verre par laminage. Puis ce ruban est déposé sur un bain
d'étain fondu. La face en contact avec le métal épouse la
planéité de la surface du bain. La face supérieure devient
plate par l'action de la tension superficielle qui tend à étaler
le ruban. Des critères comme le coût, la toxicité, la
pression de vapeur, et l'indifférence chimique avec le verre, ont
été fondamentaux pour le choix de ce métal. Actuellement
le procédé « float » est le plus utilisé pour
produire du verre plat de haute qualité au niveau mondial.
3-1- Les procédés de fabrication du verre
plat :
3-1-1- Le procédé Fourcault :
L'étirage d'un ruban de verre par immersion et
extraction d'un peigne métallique vertical est simple dans son principe
mais présente l'inconvénient que sous l'action de la tension
superficielle le ruban vertical à tendance à se
rétrécir et de plus son pied n'est pas suffisamment stable. Le
procédé Fourcault qui fut exploite a partir de 1913
résolvait ces deux problèmes par l'emploi de la débiteuse
et de refroidisseurs [3].
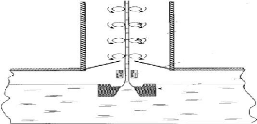
Figure 7. Procédé Fourcault pour le verre plat
La débiteuse est une pièce de réfractaire
de 3 m de longueur qui a la forme d'une auge dont le fond comporte une fente
longitudinale. Des tiges métalliques verticales permettent de
régler l'enfoncement de cette pièce dans le bain. Sous l'action
de la pression hydrostatique, le verre jaillit par la fente de la
débiteuse, ce qui définit la position du pied de feuille. Les
refroidisseurs sont des boites métalliques ou circule de l'eau et qui
sont situées au-dessus de la lèvre de la débiteuse.
Ils recueillent le rayonnement émis par les surfaces de
la feuille ce qui les refroidit fortement. Ces surfaces sont ainsi
figées, ce qui feuille dans un puits d'étirage d'une hauteur de 7
m environ.
Dans la partie supérieure du puits la feuille est
découpée en plateaux. Les largeurs de la feuille sont comprises
entre 2 m et 2,5 m et les épaisseurs entre 0,5 et 10 mm. La vitesse
d'étirage en 2 mm est d'environ 90 m/h [3].
3-1-2- Le procédé Pittsburgh
Les feuilles de verre produites par le procédé
Fourcault présentaient parfois des défauts de surface dus au
contact de la débiteuse. Le procédé développe a
partir de 1925 par la société PPG évite cet
inconvénient en utilisant, pour stabiliser la feuille, a la place de la
débiteuse, une barre d'étirage (draw bar), pièce
rectangulaire en réfractaire possédant une nervure longitudinale
et immergée sous environ 10 cm de verre. Des améliorations
successives ont permis de produire par ce procédé du verre de
bonne qualité pour le vitrage, en largeur de 4 m. La vitesse
d'étirage en 2 mm était de 150 m/h.
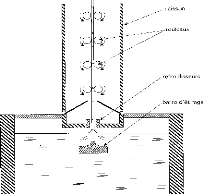
Figure 8.procédé Pittsburgh pour le verre
plat.
3-1-3- Le procédé Libbey-Owens :
Ce procédé, qui a été mis au point
par l'Américain Colburn chez Iibbey-Owens, opère d'après
une méthode un peu différente. La feuille de verre est
étirée hors de la surface du verre comme dans le
procédé de Pittsburgh. Elle est étirée
verticalement, mais à 65cm de hauteur elle est pliée à
l'horizontale sur un rouleau. Le verre est refroidi au-dessus de la
débiteuse par des refroidisseurs latéraux. Le rouleau plieur
saisit le verre à l'endroit où il est meure plastique au point de
pouvoir être plié sans casser, mais aussi de façon que la
surface ne puisse pas être endommagée par le rouleau plieur. La
bande de verre horizontale passe sur une série de rouleaux travers une
longue galerie de recuisson [3].
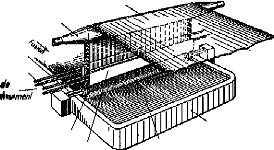
Figure 9.Procédé Libby_Owens 3-1-4- Le
procédé « Float glass »
Dans le procédé « float »
inventé par Sir Alastair Pilkington en 1952, un mélange de
matières premières est chargé en continu dans le four de
fusion. À la sortie du four le verre forme un ruban flottant à la
surface de l'étain fondu. La surface de l'étain fondu est
extrêmement lisse, donnant au verre une planéité de surface
parfaite. Le ruban de verre est ensuite lentement refroidi jusqu'à
complet durcissement et recuit. Le ruban ainsi obtenu est d'épaisseur
régulière et présente des surfaces parfaitement polies. Le
ruban est ensuite découpé en plaques pour livraison.
Ce procédé, que BSN utilisait en France, donnait
des carreaux de verre si « parfaits » que ce fabricant lança
en 1968 une OPA (ratée) sur son concurrent Saint-Gobain qui ne s'y
intéressait pas encore. Aujourd'hui, on ne trouve plus sur le
marché que des vitres en « float glass » et ce sont
paradoxalement les vitres imparfaites obtenues par les procédés
antérieurs qui semblent en gagner un certain charme.
3-1-4-1- Description de la ligne de production du "float
glass"
> Préparation de la composition
Ce système concerne les matières
premières déjà traitées, il est
équipés d'installations de levage, pesage et mélange.
L'extraction des poussières est située à l'endroit
où la poussière est habituellement produite. Des balances
électroniques avec différentes échelles sont
adaptées en fonction des quantités nécessaires de
matières premières, de calcin de l'usine ou extérieur.
L'atelier de composition est prévu pour fonctionner 24 heures sur 24.
Il est cependant dimensionné pour produire la
quantité de batch nécessaire en 16 heures, afin de permettre les
opérations de maintenance. Des alimentations séparées
seront prévues pour (a) le sable, (b) la soude, (c) la dolomie et le
calcaire pour empêcher que les matières premières ne se
contaminent entre elles.
Les matières premières seront stockées
dans les silos de l'atelier de composition et des installations de stockage qui
sont prévus pour une capacité de fonctionnement de 72 heures
minimum avec un stockage complémentaire au sol d'un mois pour la soude,
le sulfate et les autres matériaux.
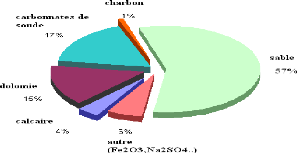
Figure 10. Dosage en matière première pour le verre
plat. > Traitement de sable
Ce poste en option peut être nécessaire en
fonction des caractéristiques réelles des matières
premières disponibles dans l'usine. Il comprendrait différentes
fonctions comme le broyage, le traitement, le séchage, la
séparation magnétique et l'homogénéisation du
sable. Dans tous les cas, l'installation de traitement de sable doit être
définie après analyse du sable et des matières
premières disponibles pour le projet.
> Le four de fusion
Construit en briques réfractaires, un four type
contient jusqu'à 2000 tonnes de verre fondu à 1550°C. La
température est contrôlée en permanence. Un des
systèmes les plus employés à ce jour est le
pyromètre. Exemple d'installation La fusion du verre pour la ligne
« float » sera assurée par un four à
régénérateurs à brûleurs transversaux. Le
verre fondu est affiné et homogénéisé. Le verre est
ensuite conditionné à température contrôlée
avant d'arriver au bain d'étain.
Pour assurer un bon fonctionnement, le four est
équipé de dispositifs automatiques de mesure, enregistrement et
régulation de pression et de niveau de verre, d'un système de
minuterie et d'inversion automatique de flamme, d'instruments de mesure,
enregistrement et régulation de température en différents
endroits du four et d'un dispositif de régulation de pression de gaz
naturel. Les fumées sont évacuées par tirage naturel par
une cheminée. Pour protéger l'environnement, les fumées
passeront par un équipement de dépollution à tirage
forcé conçu en fonction de la réglementation locale.
> Bain d'étain
Le processus de formage consiste à étirer ou
à comprimer mécaniquement la pâte de verre tout en la
solidifiant par refroidissement contrôlé.
En absence de toute contrainte extérieure, le verre
s'étalerait en formant sur l'étain liquide un ruban
d'épaisseur naturelle de 6,88 mm. Le verre, à une
température de 1100°C, se déverse
régulièrement sur l'étain en fusion grâce à
un système de régulation de débit appelé tweel. La
densité spécifique du verre lui permet de flotter sur
l'étain d'où la terminologie "float" couramment employé
pour décrire le procédé. Le verre et l'étain ne
réagissent pas entre eux et restent séparés, leur
résistance mutuelle à l'échelle moléculaire rendant
le verre parfaitement lisse.
Le bain est un système étanche avec une
atmosphère contrôlée composée d'azote et
d'hydrogène. Il se compose d'une structure en acier, d'une enveloppe
métallique supérieure, d'une enveloppe métallique
inférieure protégée de l'étain par des
réfractaires spéciaux et de systèmes de contrôle de
la température du ruban de verre et du formage. Le bain mesure environ
60 m de long sur 8m de large avec une vitesse de défilement pouvant
atteindre jusqu'à 25 m/min. Le bain contient près de 200 tonnes
d'étain pur, fondu à une température moyenne de 800 °
C.
Les dimensions du ruban de verre sont obtenues par
l'intermédiaire de forces de traction ou de compression
effectuées par des machines appelées top rolls, situées
sur chaque côté du bain.
Un programme de contrôle détermine les
réglages optimaux du process. L'épaisseur du verre peut varier de
0,55 à 25 mm.
Des résistances électriques, regroupées
en zones de chauffage, permettent une régulation fine de la
température du verre qui est progressivement réduite, lorsque le
verre a atteint les caractéristiques dimensionnelles
désirées. Le ruban est alors parfaitement plat et ses faces sont
parallèles.
A ce stade, les revêtements réflectifs, Low-E,
pour contrôle solaire, autonettoyants ou photovoltaïque peuvent
être déposés en utilisant le système de
dépôts chimiques en phase vapeur par pyrolyse. Le verre est
ensuite prêt à être refroidi.
> Étenderie :
Pour relâcher les contraintes physiques, le ruban est
soumis à un traitement thermique dans un long four de recuisson
appelé étenderie. Les températures sont étroitement
contrôlées dans le sens longitudinal et transversal du ruban.
L'étenderie sert à recuire et à refroidir
le verre. L'étenderie fermée est en construction
métallique, elle refroidit le verre par rayonnement et le recuit selon
les exigences de la spécification de production. Après recuisson,
le verre est refroidi rapidement de manière contrôlée par
un refroidissement adapté et un système de chauffage.
Le verre sera transporté dans l'étenderie sur un
convoyeur à rouleaux dont l'écartement permet le supportage du
ruban en toute sécurité. La commande est transmise
mécaniquement aux rouleaux par le système d'entraînement.
Un système d'entraînement de secours doit être disponible
pour prendre le relais en cas de panne électrique ou mécanique du
système de commande. Tous les rouleaux sont démontables pendant
le fonctionnement. Pour assurer un fonctionnement non-stop des rouleaux, une
commande de secours basse vitesse (pony) doit aussi être
intégrée au système de commande de l'étenderie de
même que le dispositif pour faire fonctionner l'entraînement
à la main.
> La découpe
Le ruban de verre ainsi produit est refroidi à l'air
libre, puis est contrôlé de manière permanente
(épaisseur, qualité optique, défauts, etc.), coupé
en plateaux de superficie standard et « débordé »
automatiquement (enlèvement des bords). Les plaques ainsi produites sont
placées verticalement sur des chevalets, grâce à des
releveuses à ventouses.
> Le lavage :
Après la découpe, les plaques de verre sont
généralement lavées afin d'éliminer les
impuretés organiques et inorganiques qui sont éventuellement
présentes à la surface. Les substances organiques se
déposent sur le verre par contact avec les différentes parties de
la chaîne de production (par exemple avec les ventouses en caoutchouc
utilisées pour leur déplacement). Ces substances altèrent
les propriétés de surface du verre en particulier la
mouillabilité.
> Le stockage :
La phase de stockage est la plus délicate de la
«vie» d'un float. Les différentes plaques de verre sont
séparées à l'aide de poudres intercalaires (ex. leucite)
puis emballées et laissées en attente avant la commercialisation.
Dans la majorité des cas les magasins ne sont pas pourvus d'un
système de contrôle de la température et de
l'humidité relative. Ainsi les verres sont soumis à des cycles de
condensation évaporation qui provoquent une détérioration
des deux plaques adjacentes sur les hydroxydes formés à partir de
Na+ et Ca2+). Parfois l'altération est très
importante car le rapport surface de verre/solution altérante est
élevée des piqûres se forment.
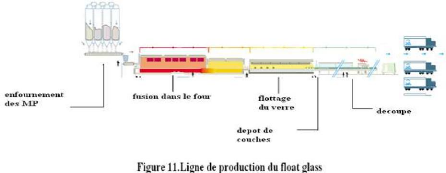
Description de l'unité MFG :
Mediterranean float glass , filiale du groupe CEVITAL
conçue pour la fabrication du verre plat, installée à
Larbaa à 30 km de Blida sur une surface de 10 hectares avec une ligne de
longueur de 630 m et une largeur de 39 m .375 travailleurs dont 95 cadres
veillent sur le bon déroulement de travail dans l'unité afin
d'assurer la production journalière de 600 t/j .
La première feuille du verre a vu le jour le
22/08/2007, depuis MFG maintient sa position de premier fournisseur du verre
plat en Algérie avec une réalisation dépassent 104% De
l'objectif visé, en laps de 3 mois, MFG a triplé ses exportation
en Europe avec 12220tonnes, contre 4428 tonnes au début 2008.
MFG adopte une système QHSE ce qui lui a permis
d'être certifiée en iso9001 version 2000, iso 14001et dans le
référentiel OHSAS18001, cela lui permet d'être
compétitive sur le marché international.
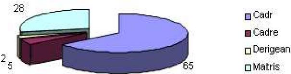
Figure13.Distribution de personnel formé en niveau MFG
2-Les différents ateliers de la ligne :
La ligne de la production du float glass comporte les ateliers
suivants :
2-1- Atelier de composition :
Cet atelier renferme les hangars de stockage des
matières premières, l'acheminement de ces dernières se
fait par des chargeurs et des transporteurs à godets vers les silos qui
assurent l'alimentation en continu des doseurs. Le mélange ainsi
dosé est envoyé vers le malaxeur ou ce fait la première
homogénéisation en présence d'eau .Le mélange
homogénéisé est transporté vers le four à
l'aide d'un transporteur à bondes.
Afin d'éliminer les éléments
minéraux non désirables, nuisibles pour la composition, la
matière première subit après le malaxage un contrôle
magnétique pour séparer les matériaux ferreux et à
l'aide d'un dispositif spécial pour les éléments non
ferreux.
La figure suivant représente le schéma
simplifié de l'atelier de composition :

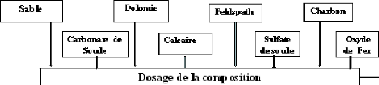
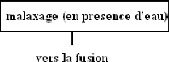
Figure 114.schématisation de l'atelier d'alimentation
Le mélange de matières premières est
pesé électroniquement avec une précision de 0,1%, puis
mélangé et humidifié. Il forme un mélange
vitrifiable auquel on ajoute du calcin avant de le charger directement dans le
four de fusion. L'ajout de calcin permet d'abaisser la température de
fusion du mélange.
La consommation journalière en tonne par jour des
matières premières au niveau de MFG est comme suite :
Tableau 3. Consommation journalière en matières
premières à MFG
MP
|
sable
|
Carbonates de soude
|
dolomie
|
calcaire
|
feldspath
|
Sulfates de soude
|
charbon
|
Oxyde de fer
|
calcin
|
Tonne/j
|
310
|
120
|
80
|
30
|
25
|
6
|
0.4
|
0.25
|
150
|
2-2- Atelier de fusion :
Comporte un four à 6 brûleurs transversaux
à chambre de régénération, long de 62.8 m et large
de 30m avec une quantité de verre en fusion de 2050 tonnes, la
température du four est de l'ordre de 1550°c .la consommation
énergétique est de 120000 m3 /j de gaz naturel.
L'alimentation des fours en mélange vitrifiable est
assurée par4 enfourneuses qui sont programmées de façon
à ce que le niveau du verre fondu soit toujours stable.
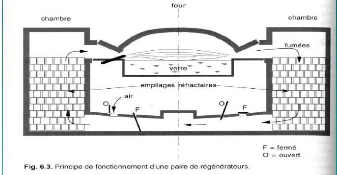
Figure15.Coupe latérale d'un four à
régénérateurs
Le four est constitué de 3 zones essentielles qui sont les
suivantes :
· l'élaboration :
Le mélange doit être transformé en un
liquide dépourvu d'inclusions cristallines. Au alentour de 1000°C,
les premières réactions de fusion et de décomposition
commencent à se produire mais il faut monter entre 1200 et 1500°C
pour s'assurer que les matières moins fusibles puissent réagir
avec les matières en fusion et être digérées par la
phase liquide.
· l'affinage :
Dans le mélange vitrifiable en fusion, il est
nécessaire d'expulser les bulles de gaz provenant des différentes
réactions chimiques mais également de l'air situé entre
les matières premières et de l'évaporation de l'eau.
Cette étape nécessite la présence
d'affinants dans le mélange de départ (voir page 2), une
élévation de la température (pour diminuer la
viscosité du verre fondu) et parfois une agitation mécanique ou
l'insufflation d'air.
· le conditionnement :
Après la fusion et l'affinage, le verre doit
être homogénéisé chimiquement et thermiquement. Les
variations de composition causent des défauts permanents lors de la
production tandis que les variations de températures occasionnent des
problèmes lors de l'étape de formage du verre.
Il existe plusieurs catégories de fours et il se peut
qu'une verrerie regroupe quelques-uns de ces systèmes de fusion
affectés à la production de différents produits
verriers.
Pour obtenir des températures suffisamment
élevées dans les fours, il est impératif de
préchauffer l'air de combustion. Pour réaliser des
économies d'énergie, les gaz chauds issus des fours passent par
des systèmes de régénération ou de
récupération thermique.
· Système de
régénération :
Les gaz brûlés passent dans une chambre
(régénérateur) dotée d'un garnissage
réfractaire absorbant la chaleur. Il y a deux
régénérateurs par four. Le chauffage des chambres n'a lieu
que d'un seul côté à la fois. Toutes les 20 minutes, la
combustion est inversée et l'air (comburant) est passé à
travers la chambre précédemment chauffée par les gaz
brûlés. Ce système permet d'obtenir des températures
de préchauffage de 1400°C.
· Système de récupération
:
Des échangeurs thermiques
(récupérateurs) assurent le préchauffage continu de l'air
(comburant) par la circulation des gaz brûlés. Les
températures de préchauffage atteintes sont limitées aux
alentours de 800°C. Ce système est principalement utilisé
lorsque la taille de l'exploitation est trop faible pour pouvoir rendre un
système de régénération économiquement
rentable. Les consommations énergétiques dépendent de la
capacité de production des fours et de la qualité du verre
à produire.
L'énergie nécessaire pour la fusion d'un
kilogramme de verre varie entre 3700 et 6000 kJ (pour des températures
de fusion qui varient entre 1200°C et 1500°C).
2-3- Bain d'étain :
Une installation de 60m de longueur et de 7,6m de largeur qui
contient environ 200t d'étain fondu pour une duré de vie
estimée de 10ans, l'atmosphère de bain est composée
essentiellement de l'azote et l'hydrogène avec des pressions bien
définies dont la consommation est respectivement 1600m3/h et
130m3/h.
Le verre affiné arrive du four par le canal et il est
déversé sur l'étain fondu dans le bain « float »
à une température variant de 1100°C pour du verre clair
à plus de 1170°C pour du verre teinté. Le débit est
régulé automatiquement de manière à maintenir la
largeur et l'épaisseur du ruban. Le bain « float » est
chauffé électriquement.
Le verre flotte sur un bain d'étain fondu. Des rouleaux
dentés, appelés « top-rollers », accrochent le verre
encore liquide sur les rives du ruban et font avancer le verre.
L'épaisseur naturelle du verre qui s'étale sur une table est de 5
à 6 mm. Si l'on veut obtenir un ruban d'une épaisseur
inférieure à 5 mm, on étire le verre et les top-rollers
ont un angle, dit « positif ». Si l'on veut une épaisseur
supérieure à 5 mm, et ce jusqu'à 12 mm, on repousse le
verre et les top-rollers ont un angle dit « négatif ». Plus on
s'écarte des 5 mm d'épaisseur, plus il faut ajouter de
top-rollers pour donner l'épaisseur souhaitée. Certains bains
d'étain possèdent plus de 20 top-rollers pour faire du verre de
0,5 mm d'épaisseur.
Un contrôle continu des paramètres du bain
d'étain tel que la pression des gaz à l'intérieur (N2,
H2), les températures d'entrée et de sortie du verre et une bonne
étanchéité est nécessaire pour la bonne
maîtrise du ruban du verre afin d'assurer un produit de qualité et
éviter tout incident probable.
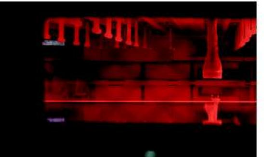
Figure 16. Vue intérieure du bain d'étain
2-4- Etenderie :
Afin d'éviter la formation de défauts
mécaniques dus aux tensions subies par le verre pendant le
refroidissement, le ruban de verre est soumis au processus d'annealing. Il
s'agit d'un traitement thermique effectué à l'intérieur
d'un tunnel long d'environ 100 m. Le verre est introduit à 600°C
ainsi, il refroidit sous contrôle jusqu'à la température
ambiante.
Plusieurs ventilateurs et équipements de chauffage ainsi
des moyens de mesures de températures sont installés pour le
contrôle strict de régime de refroidissement.
Pendant le temps de résidence du verre dans
l'étenderie on introduit, afin d'améliorer ses
caractéristiques, du SO2 gazeux. Ce procédé provoque un
échange ionique en sub-surface et conduit à la formation de
sulfates de sodium, selon les réactions suivantes :
· en présence de vapeur d'eau : 2Na+ (verre) + SO2 +
1/2 O2 + H2O ? 2H+ (verre) + Na2SO4
· en atmosphère sèche : Na2O + SO2 + 1/2 O2
? Na2SO4
Ce traitement sert à augmenter la durabilité du
verre en milieu acide ou neutre. Ceci crée à la surface du verre
une couche appauvrie en sodium et relativement enrichie en SiO2 et donc plus
résistante.
.
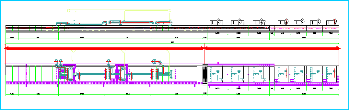
Convection non forcée Convection forcée
Figure17. Différentes zones de l'étenderie et les
régimes de recuisons
2-5- La découpe :
Après le travail dans le bout chaud on procède
au travail au bout froid au niveau de l'atelier de la découpe,
installation longue de159.78m et large de
4.80m.la largeur du ruban du verre peut
atteindre 4.5m max (la longueur nette est de 4.27m) ; le ruban se
déplace avec une vitesse maximale de 90m/min, il subit une inspection
automatique à laide des dispositifs spéciale pour :
* la détection des défauts du produit fini.
* la détection des contraintes dans le produit fini.
Des trémies et des broyeurs sont prévus pour le
broyage des rebus découpés et la récupération du
calcin, ce dernier et acheminé vers le silo de stockage ; il sera
réutilisé plus tard dans la composition du mélange
vitrifiable.
Le verre est découpé selon 3 formats qui sont les
suivants :
> PLF 3210x6000mm (international)
v' DLF 2250x 3210 (local)
v' DDLF: 1605x 2100 (local), 1605x 2400 (local).
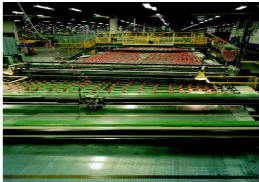
Figure18.Le verre passe sous des systèmes automatiques
de découpe. La largeur est ajustée avant que les plaques ne
soient découpées en différentes longueurs.
Les plaques de verre reçoivent un traitement leur
permettant d'être stockées sans dommage avant d'être
levées et puis empilées. Les plaques de verre
déposées sur des chevalets sont alors transférées
vers l'entrepôt de stockage ou pour expédition au client.
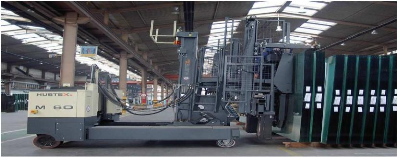
Figure 19. Moyen de manutention dans l'atelier de stockage
2-6- Atelier de contrôle de qualité :
On y effectue les différents tests afin de
détecter, classer et dimensionner les différents défauts,
on vérifie ainsi la conformité du verre aux normes de
consommation .au niveau de MFG, on effectue les tests suivants :
a) Le test zébra : pour
déterminer l'angle de déformation optique (la norme
internationale est de 45°).
b) Le test de la lumière latérale :
l'échantillon est latéralement traversé par une
lumière blanche, ça permet de bien visualiser les
défauts.
c) Le test de pupitre lumineux : la surface de
l'échantillon est exposée à la lumière blanche afin
de localisée les défauts.
Pour une vérification approfondie, une éxamination
de l'échantillon du verre est effectuée à l'aide de
microscope optique.
Des essais de découpage manuel sont effectués pour
contrôler le comportement du verre vis-à-vis l'outil coupant.
2-7- Installations annexes :
a) Station de traitement d'eau : l'eau
utilisée pour le refroidissement des équipements et installation
doit être traitée, afin d'éliminer le calcaire qui
après dépôt crée un étranglement de la
tuyauterie, ce qui nuis au bon fonctionnement de l'équipement.
b) Station d'énergie : assure
l'alimentation des différents équipements par leur besoin en
hydrogène, azote, gaz naturel et GPL.
Chapitre III le verre à couches
1. Les verres à couches
1.1 - Introduction
Par définition, les `verres à couches' sont des
produits verriers de types industriels (très généralement
des produits élaborés à partir de verre `float') qui sont
revêtus d'une couche mince, en général composée
d'oxydes métalliques. L'épaisseur de cette couche est de l'ordre
de 10 nanomètres à 800 nanomètres (0,8
jtm). Pour optimiser les performances, la couche peut
être constituée d'un empilement de plusieurs sous-couches.
Le rôle de cette couche est de modifier le comportement
optique (exemples : les vitrages antireflet, les vitrages
réfléchissants utilisés pour réduire le facteur
solaire), chimique (exemples : les vitrages `autonettoyants', vitres
hydrophobes), électrique (dépôts conducteur
électrique et transparent) ou encore mécanique (exemple : les
traitements contre les rayures).
Bien que ce travail concerne les verres à couches dont
la couche est inférieure à 1 micromètre, certains vitrages
fonctionnels comportant des couches plus épaisses comme les vitrages
anti-incendie, les vitrages électrochromes etc.... sont
présentés. Il est possible d'améliorer les
propriétés acoustique et mécanique du verre (exemple : les
vitrages feuilletés utilisés pour la sécurité,
l'anti vandalisme, la sécurité d'exploitation comme les planchers
en verre, les parois d'aquarium les hublots de piscine) [9].
1.2 - Les fonctions d'un verre à
couches
1.2.1-Les fonctions optiques
La couche modifie le comportement optique du verre, dans le
domaine visible et/ou dans le domaine de l'infrarouge. Les applications
optiques d'un verre à couche intéressent d'une part les vitrages
utilisés dans le domaine de l'architecture et d'autre part le traitement
du coefficient de réflexion.
A- Domaine de l'architecture
En architecture, il faut tenir compte de la répartition
énergétique (ou spectrale) de l'énergie solaire arrivant
sur terre. La puissance du rayonnement solaire sur terre est constituée
de 43% de rayonnement Infrarouge, de 3 % de rayonnement Ultraviolet, le reste
(54 %) étant de la lumière visible. Une application importante
est apportée par une modification du comportement vis-à-vis du
rayonnement solaire en contrôlant d'une part l'énergie solaire
transmise et d'autre part la luminosité, conduisant ainsi à une
économie de conditionnement d'air (en été) et de chauffage
(en hiver).
Les caractéristiques d'un vitrage sont principalement :
- le facteur solaire (noté g ou FS et variant de 0
à 1)
- la transmission lumineuse (notée TL et variant de 0
à 1)
- le facteur U qui caractérise les échanges
thermiques à travers le vitrage (W/m2. °C). -
l'émissivité (notée e et variant de 0
à1)
Des couches sont capables de modifier les quantités g,
e, TL et U, mais en général de façon non
indépendante. Le secteur de l'automobile fait aussi maintenant de plus
en plus appel au contrôle solaire, d'autant plus que dans ce domaine, les
vitrages ont des surfaces de plus en plus grandes et de moins en moins
verticales (exemple : les toits vitrés). Outre ces applications
pratiques, le traitement de surface peut présenter un
intérêt esthétique et de décoration (par exemple
coloration par effet de réflexion interférentielle
provoquée par un dépôt transparent d'indice
élevé comme l'oxyde de titane TiO2) [9].
B- Le traitement du coefficient de réflexion
Il est souvent intéressant de contrôler le
coefficient de réflexion sur un domaine spectral étendu, comme la
totalité du spectre visible par exemple. Des dépôts
multicouches diélectriques transparents d'indice de réfraction et
d'épaisseurs judicieusement choisis permettent d'obtenir des vitrages
anti-réfléchissant, semi-réfléchissant ou
super-réfléchissant. Les applications se trouvent dans le secteur
du bâtiment et de l'instrumentation optique.
1.2.2-Les fonctions chimiques
Il s'agit essentiellement de créer des vitres à
propriétés hydrophobes ou au contraire hydrophiles. Un exemple
est donné par des verres à couches autonettoyantes à base
d'oxyde de titane.
1.2.3-Les fonctions électriques
Le but est d'obtenir un dépôt transparent
à la lumière visible mais conducteur de
l'électricité. Les applications sont l'élimination de
charges électrostatiques, mais surtout concernent la réalisation
de vitrages `intelligents' de type électrochromes. Certains vitrages
`dégivrants' mettent à profit une fine couche transparente mais
conductrice de l'électricité. L'exemple typique d'une telle
couche est l'oxyde mixte d'indium et d'étain appelé ITO.
1.2.4-Les fonctions multiples
Souvent, une combinaison de ces différentes
propriétés est recherchée. Un exemple est donné par
les doubles vitrages autonettoyants et à isolation thermique
renforcée.
C'est le cas du vitrage `Cool-Lite SKN 154 BioClean' produit
par Saint-Gobain Glass : ce vitrage comporte une couche à faible
émissivité déposée en face 2 et un
dépôt autonettoyant en face 1.
1.3 - Structure d'un verre à couches
Pour assurer de bonnes propriétés et une bonne
durabilité, il est souvent indispensable de déposer :
- une sous-couche assurant l'adhérence sur le verre.
- une couche (mais plus généralement plusieurs
couches) pour donner au verre les caractéristiques fonctionnelles
recherchées.
- optionnellement, une couche de protection chimique et
mécanique (dans le cas de verres à faible
émissivité, cette dernière couche peut être du
nitrure de silicium) [9].
1.4 - Nature de couches, procédées de
dépôt
Diverses techniques existent pour apporter de la
matière sur une surface. Nous décrirons les principales
utilisées. On peut les classer de différentes manières
(e.g.physiques ou chimiques), mais nous préférons les classer
selon la phase par laquelle le matériau transite lors du
dépôt : soit par un gaz ionisé (plasma), soit en phase
vapeur, soit en phase liquide. Le choix d'un procédé
dépend de plusieurs facteurs : le matériau à
déposer, la nature du substrat, l'application désiré.
1.4.1- Pulvérisation cathodique
Ce procédé tend à se substituer
progressivement à l'évaporation dès lors que l'on souhaite
des dépôts de grande surface. En effet pour des raisons
strictement géométriques il est évident qu'une source
d'évaporation quasi ponctuelle peut être considérée
comme un centre de symétrie vis a vis des atomes évapores. En
d'autres termes le nombre d'atomes reçus à une distance
donnée de la source sera sensiblement inversement proportionnel à
la carre de la distance. II en résulte que le dépôt
présentera une épaisseur homogène s'il est effectue sur
une surface sphérique dont le centre est constitue par la source
d'évaporation. Comme en pratique les substrats sont
généralement plans, on ne pourra les assimiler qu'au plan tangent
a la sphère et de toute évidence l'épaisseur du
dépôt ne sera pas identique en tout point. On est donne contraint
à limiter fortement la surface utile du substrat, ou a le placer
très loin de la source ce qui entraine alors d'autres difficultés
(nécessite d'enceinte plus grande donne système de pompage
beaucoup plus cher, temps opératoire plus long...) [8].
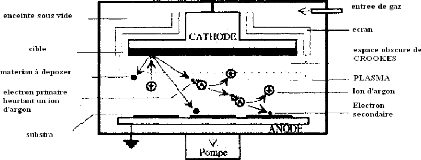
Figure 20. Principe de dépôt par
pulvérisation cathodique.
1.4.1.1- Mécanisme de la pulvérisation
On dispose a faible distance de deux plans parallèles,
1'un support de la source de matériau (cible), 1'autre du
réceptacle du dépôt. On procède au bombardement de
la source par des ions connus (argon le plus souvent) accélères
sous 1kV environ, ces ions vont arracher mécaniquement des atomes de la
source et ceux-ci vont être projetés vers le porte substrat
refroidi et s'y déposer. La source plane pouvant être de
très grande surface on peut théoriquement effectuer des
dépôts relativement homogènes sur une grande surface
[8].
Les dépôts métalliques sont aisés
à produire par pulvérisation cathodique, dans le cas de
matériaux diélectriques, et donc non conducteurs, il y a une
difficulté car les ions ne peuvent se décharger sur la cathode,
ce qui entraine la constitution d'une charge d'espace qui très vite
bloque la progression des ions vers la cathode et interrompt, de facto, le
processus de pulvérisation. On trouve une parade en interposant une
grille soumise a un potentiel module a haute fréquence (27 MHz) ce qui
augmente sensiblement la complexité et le cout du dispositif. La diode
plane représentée cidessus possède une cathode de
diamètre variant entre 10 et 30 cm tandis que la distance cathode anode
se situe entre 5 et 10 cm [8].
1.4.2-La pulvérisation magnétron :
1.4.2.1-Effet magnétron :
Une décharge diode DC est entretenue par les
électrons secondaires éjectés de la cathode sous l'effet
du bombardement ionique. Dans ce cas les électrons qui ne rencontrent
pas de molécules de gaz s'éloignent perpendiculairement à
la cathode et sont captés par l'anode.
Si on superpose au champ électrique un champ
magnétique B, perpendiculairement à celui ci, les trajectoires
électroniques s'enroulent autour des lignes de champ magnétique,
augmentant considérablement les chances d'ioniser une molécule de
gaz au voisinage de la cathode [9].
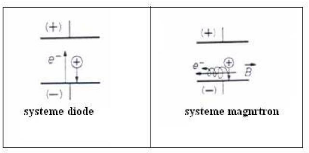
Figur21.Système diode et système
magnétron
1.4.2.2- Principe :
La décharge luminescente est concentrée dans la
zone ou le champ magnétique est le plus intense ; il se forme donc une
zone luminescente circulaire de forme annulaire. Ceci occasionne, après
plusieurs heures de fonctionnement, une profonde déflexion à
l'aplomb de l'anneau luminescent. La cathode magnétron existe sous deux
formes principales : planes (rectangulaires ou rondes) et cylindriques.
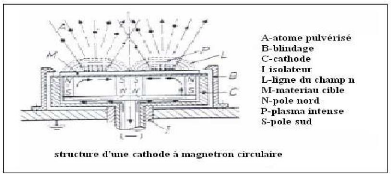
Figure 22. Cathode à magnétron circulaire
1.4.2.3- Propriétés des cathodes
magnétron :
La décharge magnétron se caractérise par
un degré d'ionisation élevé. En effet, les
électrons possèdent un mouvement cycloïdal autour des lignes
de champ, ceci augmente donc le taux de collisions entre ces électrons
et les molécules de gaz (Argon).
La pression de travail dans une enceinte équipée
d'une cathode magnétron peut aller de quelques 10-3 Torr
à quelques 10-4 Torr. Les particules
pulvérisées vont donc se déplacer en lignes droites avec
un minimum de collisions.
Dans des systèmes de pulvérisation
magnétron, le champ magnétique augmente la densité du
plasma ce qui a pour conséquences une augmentation de la densité
de courant sur la cathode. De grands taux de pulvérisation ainsi qu'une
diminution de la température du substrat peuvent être ainsi
obtenus [9].
Remarque :
L'unité de mesure légale de pression est le pascal
(Pa). Les unités pratiques en mesure du vide sont encore le torr (Torr)
et le millibar (mbar). On a la correspondance :
1 Torr = 1,33 mbar = 133 Pa.
1.4.3-Dépôt par évaporation
1.4.3.1- Principe de l'évaporation thermique :
La technique la plus courante consiste à
évaporer le matériau à déposer en le portant
à une température suffisante. Des que la température de
liquéfaction est dépassée, il se trouve que la pression de
vapeur du matériau est sensiblement supérieure a celle
résiduelle dans 1'enceinte. Alors des atomes du matériau
s'échappent et se propagent en ligne droite jusqu'a ce qu'ils
rencontrent un obstacle. Cette rencontre peut être le fait soit d'une
surface solide (substrat, paroi de 1'enceinte) soit d'un atome ou d'une
molécule se déplaçant dans l'espace. Dans le cas de
rencontre une surface, il y aura séjour de 1'atome sur la surface avec
échange d'énergie et si la surface est sensiblement plus froide
que l'atome il y a condensation définitive. La rencontre d'une
molécule résiduelle se traduit généralement par une
déviation de l'atome d'évaporant II apparait donc qu'il est
indispensable que la pression dans 1'enceinte soit suffisamment faible pour que
la probabilité de rencontre d'un atome résiduel soit quasi nulle.
Cela est réalise dans les systèmes courants des que la pression
est de 1'ordre de 10" Torr car alors le libre parcours moyen d'un atome dans
1'enceinte est statistiquement supérieur aux dimensions de celle-ci
[8].
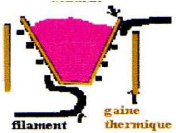
Figure 23. Creuset pour l'évaporation thermique.
La procédure de chauffage du matériau à
évaporer peut être réalisée de plusieurs
façons qui seront choisies en général en fonction de
critères de qualité du résultat attendu. On note
fréquemment l'emploi d'un Creuset chauffe par effet joule :
limité aux matériaux s'évaporant a relativement basse
température (et en tout cas très en dessous du point de fusion du
creuset qui sera souvent en alumine frittée, parfois en graphite ou en
oxyde de béryllium).
1.4.3.2- Principe de canon a électron
La seconde technique consiste à utiliser un canon
à électrons à déflexion
électromagnétique : permettant en théorie
1'évaporation de tout matériau (même très
réfractaire) sans risque de pollution par le support. Notons que le
faisceau d'électrons émis par un filament de tungstène est
focalise ponctuellement sur le sommet de l'échantillon à
évaporer.
On condense ainsi jusqu'a 2kW de puissance sur un volume
inferieur au mm3. Le matériau repose en pratique sur une nacelle de
cuivre refroidie par une circulation d'eau afin d'éviter qu'elle ne
s'évapore également. En jouant sur la tension
d'accélération des électrons et sur le champ
magnétique, il est aise de déplacer le point d'impact du faisceau
d'électrons. On dispose alors de la possibilité de déposer
plusieurs matériaux différents places dans des emplacements
sépares sur la nacelle [8].
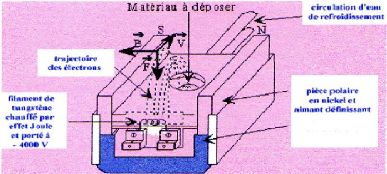
C'est un produit qui, sous un aspect assez neutre, aura une
plus forte TL. (Transmission Lumineuse) que les produits fabriqués en
phase liquide et avec un F.S. (Facteur Solaire) plus bas. Ces formes de
pyrolyse sont particulièrement adaptées à un
procédé en continu sur ligne de fabrication de verre
flotté. Au-delà de deux couches superposées, le
procédé devient difficile...
Par la pyrolyse, la couche s'intègre totalement
à la surface du verre (par osmose), lui conférant une grande
résistance et une stabilité dans le temps. De ce fait, ces
verres, classés A, sont utilisés en face
1 du vitrage.
1.4.4.2) Sur substrat froid
II est obtenu par enduction sur la surface du verre d'un liquide,
d'une pâte, d'un gel, puis chauffage. La matière se
décompose et laisse une couche mince sur le verre. Ce
procédé porte le nom de DIPPING ou SILICOAT DE GUARDIAN
(Sun-Guard Clear).
1.4.5) Procédé `sol-gel' :
Un composé organo-métallique est
déposé sur le substrat immergé dans une solution (`dip
coating'). Le composé est transformé en oxyde métallique
par traitement à haute température.
1.5- Tests, normalisation des verres à couches
pour l'architecture
Les verres traités utilisés pour les vitrages en
architecture doivent répondre à certains critères,
concernant en particulier :
v' la corrosion
v' l'abrasion et la résistance aux rayures
v' la résistance au brouillard salin
v' la résistance au rayonnement UV
v' la résistance à l'attaque chimique (solvants,
agents nettoyants, bases et acides) Une couche `dure' est conforme à
l'ensemble de ces tests.
2 - Classification des vitrages pour le
bâtiment
2.1 - Le rôle des couches
Les couches déposées sur les vitrages ont
plusieurs rôles : elles agissent sur la transmission lumineuse, le
contrôle solaire, le transfert thermique, l'émissivité. En
outre, certaines couches peuvent aussi avoir un rôle autonettoyant
efficace. Ces caractéristiques sont traitées en détail
dans des chapitres séparés.
a. Le coefficient de transparence, ou de transmission
lumineuse (TL ou t)
Ce coefficient de transparence caractérise la
proportion de lumière visible (spectre de longueurs d'onde comprises
entre 0,38 jim et 0,78 jim) traversant le
vitrage. Evidemment, le coefficient TL est compris entre 0 (opacité
complète) et 1 (transparence totale).
b. Le facteur solaire (FS ou g)
Le facteur solaire est la fraction de l'intensité du
rayonnement solaire (visible et non visible) traversant directement le vitrage
ainsi que la fraction absorbée par le vitrage puis réémis
vers l'intérieur sous forme chaleur (Infrarouge).
c. Le facteur gain solaire
Le facteur de gain solaire est le rapport TL/g. Il
définit la quantité de lumière visible transmise par un
vitrage sans apporter d'échauffement supplémentaire. Le choix de
ce facteur est important selon que le climat est froid ou chaud (voir vitrage
à faible émissivité et à contrôle
solaire).
d. L'émissivité e
La chaleur est transmise par conduction, convection et
radiation. Un vitrage simple non traité perd une grande partie de ses
propriétés d'isolation à cause de sa radiation
d'énergie élevée. Cette aptitude à rayonner la
chaleur est caractérisée par l'émissivité e.
L'émissivité la plus élevée est celle d'un `corps
noir' pour lequel elle est égale à 1 alors que celle de l'argent
métallique poli est 0,02.
L'émissivité d'un vitrage simple non
traité est comprise entre 0,89 et 0,87. Un vitrage revêtu d'une
couche métallique suffisamment mince pour rester transparente à
la lumière visible peut être réduite jusqu'à
0,04.
e. Le coefficient de transfert thermique U
Le coefficient U est la mesure de déperdition (ou de gain)
de chaleur à travers un vitrage provoquée par une
différence de température d'air entre l'extérieur et
l'intérieur.
La valeur du coefficient U est le résultat non seulement
de la nature des couches déposées sur les feuilles de verre, mais
aussi de la structure du vitrage.
Le coefficient U s'exprime en W/m2.K (watts par m2 et par
degré). Le coefficient U d'un vitrage simple est de l'ordre de 6 W/m2.K,
mais peut descendre à 1,1 pour un triple vitrage à isolation
renforcée [7].
Des valeurs encore plus faibles sont obtenues si ces triples
vitrages ont des espaces remplis non pas d'air mais de gaz moins conducteurs de
la chaleur comme l'argon ou encore mieux le xénon. Il faut noter que
l'inverse de U est la résistance thermique R=1/U.
Les coefficients TL, U, g et e ne peuvent pas toujours
être choisis séparément. Un compromis est souvent à
trouver. Par exemple, dans un pays froid, il vaut mieux avoir un contrôle
solaire g élevé pour profiter du chauffage par le rayonnement
solaire pendant la journée[7].
En outre, il existe des combinaisons plus ou moins complexe comme
des vitrages autonettoyants, à isolation thermique renforcée
(à faible émissivité) et à contrôle
solaire.
f. La couche autonettoyante
Un vitrage autonettoyant est un vitrage revêtu d'une
couche mince d'oxyde de titane (généralement pyrolytique) sous
forme cristalline anatase. Ce revêtement a des propriétés
semiconductrices et de superhydrophilicité. Ces deux
propriétés permettent au revêtement placé en
extérieur d'assurer la dégradation photo catalytique (sous
l'effet du rayonnement solaire) des salissures déposées sur la
vitre (car il est semi-conducteur) puis le lavage avec la pluie (car il est
super hydrophile).
2.2 - La classification des verres à couches
dans le bâtiment
Selon la méthode de dépôt des couches, la
durabilité et résistance mécanique de celles-ci seront
plus ou moins grandes. Par exemple, un dépôt pyrolytique CVD qui
présente une plus grande durabilité, pourra être
placé en face externe. Par contre une face traitée par un
dépôt obtenu par évaporation sous vide ou
pulvérisation cathodique PVD qui présente de meilleures
performances mais aussi une résistance moindre aux agressions devra
être placé en face interne d'un double vitrage. Un tel
dépôt demande aussi d'être manipulé avec
précaution. C'est pourquoi, en fonction de la nature des
dépôts, les vitrages pour bâtiments sont classés
suivant différentes catégories [7].
2.3 - La numérotation des faces d'un vitrage
simple ou multiple
Par convention, les faces d'un vitrage sont
repérées comme l'indique la figure (25) pour un vitrage simple et
double. La face extérieure est toujours numérotée 1.
Ainsi, pour un triple vitrage, les faces seront numérotées de 1
à 6.
Figure 25. Numérotation des faces d'un vitrage à
couches.
|
|
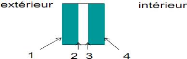
3 - Traitement de surface hydrophobe
3.1 - Surface hydrophobe :
Définition :
Une surface hydrophobe a tendance à repousser les
molécules d'eau. Ce caractère est l'opposé de celui
présenté par les surfaces hydrophiles (voir par exemple les
verres `autonettoyants' qui sont rendus `hyper-hydrophiles' grâce
à un dépôt d'oxyde de titane sous forme anatase).
Ainsi, une goutte d'eau à tendance à
s'étaler sur une surface hydrophile, alors qu'elle a tendance à
rester sous forme de gouttelette sphérique au contact d'une surface
hydrophobe comme indiqué sur la figure (26).
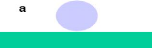


Figure 26. Étalement d'un liquide sur une surface.
a) sur une surface totalement hydrophobe : le liquide est
parfaitement non mouillant.
b) sur une surface totalement hydrophile : le liquide (l'eau)
est parfaitement mouillant. La nature nous donne des exemples de surfaces
hydrophobes comme cette feuille où l'eau reste sous forme de goutte sans
s'étaler (27) :
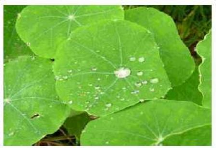
Figure 27. La surface de cette feuille est de nature
hydrophobe
La nature hydrophobe ou hydrophile d'une surface est
caractérisée par la valeur de l'angle de contact
è d'une goutte d'eau avec cette surface comme
indiqué sur la figure 4. Si cet angle è est
inférieur à 90°, il s'agit d'une surface hydrophile, tandis
que si cet angle est supérieur à 90°, il s'agit
d'une surface hydrophobe. Si l'angle de contact est
supérieur à 150°, la surface est qualifiée de
`super-hydrophobe.


Figure 28. Étalement d'une goutte d'eau sur une surface
hydrophobe ou hydrophile.
Une surface propre de verre est plutôt hydrophile :
l'eau au contact d'une vitre en verre a tendance à former des gouttes
qui s'étalent et adhérent au verre. Ceci pose un problème
car, d'une part la visibilité est réduite à travers la
vitre, et d'autre part des traces sont laissées sur la vitre
après séchage et évaporation. Si la nature
`super-hydrophile' apportée par un dépôt d'oxyde de titane
présente un intérêt dans le cas des vitrages
`autonettoyants', il peut être intéressant de rendre la surface du
verre hydrophobe.
3.2 - Réalisation de surfaces de verre
hydrophobes
Une surface peut être de nature hydrophobe et même
`super-hydrophobe' à cause de sa texture. C'est le cas de la surface des
feuilles de lotus. La nature hydrophobe et superhydrophobe peut aussi
être d'origine chimique. Nous traitons ici le cas des traitements
Hydrophobes d'origine chimique.
Une surface est hydrophobe si elle a tendance à
repousser les molécules d'eau plutôt que de les attirer. Les
molécules d'eau étant des molécules polaires, la surface
de nature hydrophobe doit être de nature non polaire. Les
molécules d'eau ont tendance à s'attirer entre elles alors
qu'elles sont peu attirées par le substrat. L'eau forme alors une
gouttelette qui ne s étale pas sur le substrat de nature hydrophobe.
Ainsi, pour que la surface d'un matériau soit rendue
hydrophobe, il faut déposer une couche de faible épaisseur d'un
matériau non polaire : typiquement des silanes fluorés. Un brevet
déposé par Saint-Gobain Vitrage (Courbevoie) décrit le
procédé (Brevet : United States Patent 5800918). Tout d'abord le
verre reçoit un premier dépôt appelé sous-couche. Ce
dépôt minéral pyrolytique à base d'oxydes (oxyde
d'aluminium, oxyde d'étain ...) de faible épaisseur (8 à
500 nanomètres, soit 0,008 à 0,500 millièmes de
millimètres) est transparent [7].
Enfin, un film très mince (1 à 5 nanomètres)
hydrophobe est déposé sur cette sous-couche : il s'agit d'un
fluorosilane La vitre en verre est ainsi rendue hydrophobe.
Si en outre la sous-couche est un oxyde dopé (oxyde
d'étain dopé au fluor ou oxyde d'indium dopé à
l'étain appelé ITO par exemple), alors le vitrage est hydrophobe,
antistatique et à faible émissivité.
De tels vitrages sont commercialisés pour le
bâtiment ainsi que pour les pare-brises automobiles. Dans ce cas, la
visibilité est très améliorée par temps de pluie
diluvienne (d'après documents Saint-Gobain) et on peut même
envisager d'éviter l'emploi d'essuie-glaces.
Si les vitrages sont déjà installés, il
est possible de les rendre hydrophobes en déposant un film par spray. De
tels produits sont commercialisés (exemple le produit de marque Rain-X),
essentiellement pour application sur pare-brises automobiles. La
durabilité n'est pas infinie, mais de plusieurs semaines. Là
encore, la surface rendue hydrophobe pourrait éviter l'utilisation
d'essuie- glaces, à condition que la vitesse du véhicule soit
suffisante (supérieure à 50 km/heure) pour chasser les
gouttelettes d'eau figure (29).
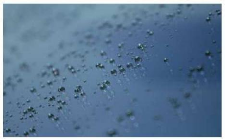
Figure 29. Gouttelettes d'eau sur un pare brise ayant
reçu un traitement par spray hydrophobe (selon un document
Rain-X).
3.3 - Aspects théoriques
Nous avons vu que la valeur de l'angle de contact
è entre une goutte d'eau et la surface du verre
caractérise la nature hydrophobe ou hydrophile. La valeur de cet angle
est calculée en écrivant l'équilibre au point triple de
contact entre le liquide (ici l'eau), l'atmosphère gazeuse environnante
(ici l'air) et la surface du solide (ici le verre) comme indiqué sur la
figure (30).
Figure 30.l'intersection des trois interfaces définit la
ligne de contact entre les trois phases (gaz/liquide/solide).
óSG, óLG,
et óSL sont les tensions inter faciales
solide/gaz, liquide/gaz et solide/liquide, respectivement.
|
|
L'équilibre des forces au point triple donne la valeur
de l'angle de contact (équation de Young). Soit aSL,
aSG et aLG les tensions interfaciales
solide/liquide, solide/gaz et liquide/gaz, respectivement.
L'unité de tension interfaciale est joule/m2 ou bien
newton/m. La condition d'équilibre de liquide à la surface du
solide donne l'équation dite équation de Young :

Dans le cas du système téflon/eau, nous avons :
aSG = a (téflon/air) =
0,019 N/m
aLG = a (eau/air) = 0,073
N/m
aSL = a (téflon/eau) =
0,050 N/m
L'application numérique de l'équation de Young
donne, pour le système eau/téflon un angle de contact voisin de
115°. Le téflon est bien un matériau hydrophobe.
Par contre, l'application numérique dans le cas du
système eau/verre donnerait un angle de contact très
inférieur à 90°. La surface d'un verre propre est bien de
tendance hydrophile.
4 - Dépôt transparent conducteur de
l'électricité
4.1 - Nature du dépôt : ITO (oxyde
d'étain et d'indium)
Le matériau ITO est un mélange d'oxydes d'indium
et d'étain. La composition typique en poids est 90% In2O3 et
10% SnO2. L'ITO est donc de l'oxyde d'indium où une faible fraction
d'atomes d'indium est remplacée par des atomes d'étain : on peut
dire qu'il s'agit d'oxyde d'indium dopé à l'étain.
Cet oxyde mixte est un semi conducteur de type n (la
conduction électrique a lieu par électrons) fortement
`dégénéré'. Ce matériau est faiblement
conducteur électronique, mais reste transparent à la
lumière visible à condition qu'il soit sous forme de couche
mince.
Cet oxyde est meilleur conducteur de
l'électricité que d'autres oxydes transparents comme ZnO etc. ...
L'augmentation de la conductivité électrique par dopage
entraîne une augmentation de l'absorption de la lumière et la
couche en ITO se colore en jaune [7].
Ce matériau est utilisé pour réaliser les
électrodes transparentes dans les dispositifs d'affichage à
écrans plats (exemple : les écrans LCD) et les vitrages
électrochromes.
4.2 - Elaboration du dépôt ITO
Les films en ITO sur plaques de verres sont obtenus par
différentes techniques de dépôts et
généralement par pulvérisation (PVD par exemple).
4.3 - Utilisations
Les films ITO sont essentiellement utilisés comme
électrodes transparentes pour les afficheurs à écrans
plats, écrans tactiles, cellules solaires, diodes
électroluminesentes (LED) organiques (OLED), certains revêtements
antistatiques et écrans contre les radiations
électromagnétiques mais transparents à la lumière
visible. Le développement des vitrages électrochromes est rendu
possible grâce à ce type d'électrodes transparentes
déposées sur verre.
Ce type de dépôt peut aussi être
utilisé comme système de dégivrage. Pour une application
pare brise en verre feuilleté, ce dépôt est placé
sur la face 2 ou 3 (naturellement, le dépôt est
réalisé avant assemblage des deux feuilles de verre).
Des feuilles de verres revêtues de films ITO transparents
conducteurs de l'électricité sont commercialisées.
5 - Verres à couches pour protection contre les
incendies
5.1 - Définition
Le rôle d'un vitrage de protection contre les incendies
est d'avoir une bonne transparence en période normale (c'est à
dire de se comporter comme un vitrage usuel) mais d'assurer automatiquement une
isolation thermique en cas d'incendie par action sur la conduction et le
rayonnement. Il existe plusieurs types de vitrages pour protection anti-feu
:
- certains verres trempés et à couches
réfléchissantes (surtout pour le rayonnement
Infrarouge).
- des verres à couches intumescentes.
Les verres dits `armés' peuvent aussi assurer, mais
dans une moindre mesure, un rôle de protection anti-feu car les
éclats de verre susceptibles de se former sous l'effet des flammes
restent reliés entre eux grâce aux fils métalliques. Ce
chapitre concerne seulement les verres à couches.
5.2 - Structure et fonctionnement d'un verre à
couches intumescentes
Un verre à couches de protection contre les incendies
est constitué d'un empilement de feuilles de verre (verre `float',
éventuellement trempé) séparées par des couches de
gel de silicate intumescent. L'épaisseur de ces couches de gel est de
l'ordre du millimètre. En période normale, le vitrage est aussi
transparent qu'un vitrage usuel. Si un incendie se déclare dans une
pièce d'un immeuble, la partie exposée du vitrage a tendance
à s'échauffer. La première couche de gel intumescent se
transforme en `mousse', assurant ainsi automatiquement une isolation thermique
en réduisant le transfert de chaleur par conduction et rayonnement (voir
figure 31). Si l'incendie persiste, une deuxième couche intumescente se
transforme, ce qui augmente l'efficacité de l'isolation et ainsi de
suite [7].
Figure 31. Structure et principe de fonctionnement d'un vitrage
anti-feu. Dans cet exemple, le vitrage, initialement transparent est
constitué de 4 feuilles de verre et de 3 couches intercalaires de gel de
silicate intumescent.
|
|
5.3 - Les verres à couches
réfléchissantes
Une autre technique de protection anti-feu consiste à
utiliser des vitrages de sécurité trempés et comportant
une couche réfléchissante (principalement dans l'Infrarouge).
L'avantage de ces vitrages est qu'ils restent transparents à la
lumière visible, même soumis à des températures
élevées. L'inconvénient est une efficacité
d'isolation thermique et de brise-feu moindre que les vitrages à couches
intumescentes.
5.4 - Les classes et normes pour vitrages de protection
anti-incendie
1) Les vitrages résistant au feu : sont classés en
trois catégories selon la norme EN13501-2. Le classement est
exprimé par une combinaison de lettres et de chiffres.
2) les vitrages de classe E : sont étanches aux flammes,
aux fumées et aux gaz chauds. Ces vitrages sont
généralement constitués de verres borosilicates
trempés.
3) les vitrages de classe EW : sont étanches aux
flammes, aux fumées et aux gaz chauds ils sont
généralement constitués de feuilles de verre trempé
revêtues de couches minces à faible émissivité qui
procurent une isolation thermique. Ce revêtement assure une limitation du
rayonnement thermique en dessous de la valeur nominative de 15 kW/m2.
4) les vitrages de classe EI : sont étanches aux
flammes, aux fumées et aux gaz chauds et en outre il constitue une
barrière thermique opaque aux rayonnements ; ces vitrages sont
constitués de feuilles de verre séparées par des couches
intumescentes (gels silicatés).
Les chiffres indiquent la durée en minutes pendant
laquelle le vitrage peut assurer la protection (exemples EI 30, EI 60, EW 120
...).
5.3 - Les verres à couches pour l'isolation
thermique renforcée et le contrôle solaire
5.3.1-Le verre et le rayonnement solaire
5.3.1.1- Introduction et définitions
L'énergie du rayonnement solaire reçu sur Terre
est constituée approximativement de 43% de lumière visible
(longueurs d'onde comprises entre 400nm et 800nm), de 52% de rayonnement
Infrarouge (longueurs d'onde supérieures à 800nm) et de 5%
d'Ultraviolet (longueurs d'onde inférieures à 400nm).
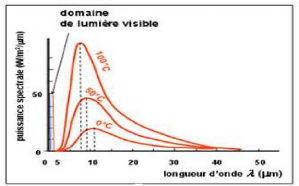
Figure32.puissance spectrale du rayonnement reçu sur
terre.
Pour réduire l'échauffement à
l'intérieur des locaux (et des véhicules) dû au rayonnement
solaire (surtout pendant les mois d'été) on utilise depuis
longtemps des vitrages absorbant préférentiellement le
rayonnement infrarouge (IR). C'est le cas des vitres `teintées'
utilisées dans le domaine du bâtiment mais aussi des transports.
L'absorption du rayonnement infrarouge par les verres teintés est due
aux ions Fe2+ dans la masse du verre, qui leur donne une coloration
verdâtre. L'inconvénient de cette méthode est que le verre
absorbant le rayonnement s'échauffe et, puisque sa température
s'élève, réémet un rayonnement IR vers
l'intérieur des locaux ce qui produit un échauffement
supplémentaire qui s'ajoute à celui produit par conduction et
convection dans l'air du local.
Une méthode plus efficace, qui a tendance à se
généraliser, pour contrôler le transfert d'énergie
par rayonnement à travers un vitrage est d'utiliser des verres
revêtus d'une couche à faible émissivité.
Les dépôts à faible
émissivité contribuent à l'isolation thermique
déjà obtenue grâce à la structure en doubles (et
éventuellement triples) vitrages (diminution de la conduction et de la
convection).
C'est l'isolation thermique `renforcée'. Les
caractéristiques d'un vitrage sont : - le coefficient de transmission
lumineuse (lumière visible) TL
- le facteur solaire g (ou FS)
- le coefficient de transmission énergétique U
- l'émissivité å
La valeur du coefficient U est essentiellement
déterminée par la structure du vitrage (double ou triple,
l'épaisseur des vitres et des espaces et la nature du gaz de
remplissage). Les couches à faible émissivité participent
à l'isolation thermique.
1.1.2 - Les vitrages à faible
émissivité (appelés aussi peu émissifs)
Dans le domaine du bâtiment, les couches à faible
émissivité (réfléchissant
préférentiellement l'IR mais transparents dans le domaine
visible) permettent d'éclairer une pièce par la lumière du
soleil tout en limitant l'échauffement en été ainsi que
les déperditions d'énergie en hiver.
Pour produire des vitres à faible
émissivité, on utilise généralement des verres
clairs (de type `float') qui sont revêtus d'un dépôt (soit
de type pyrolytique, soit par procédé PVD magnétron) d'un
métal ou d'un oxyde métallique qui réduit
l'émissivité du verre, ainsi :
v' dans les climats froids, la chaleur
générée par le rayonnement solaire et les appareils de
chauffage est gardée à l'intérieur.
v' dans les climats chauds, le transfert de chaleur depuis
l'extérieur est réduit.
En contribuant à la réduction de la valeur du
coefficient U (voir normes et standards), les dépôts à
faible émissivité participent aux économies
d'énergie en réduisant la consommation de chauffage en hiver et
de climatisation en été. Pour optimiser les économies
d'énergie, il faut tenir compte non seulement de
l'émissivité mais aussi du facteur solaire ainsi que du choix de
la face du vitrage (face 2 ou 3) qui doit recevoir la couche.
Les premiers vitrages à faible émissivité
ont été réalisés plutôt pour minimiser les
dépenses de chauffage. Ils présentaient un facteur solaire g et
un facteur de transmission lumineuse TL élevés. Ces vitrages des
vitrages à basse émissivité et haute transmission. Ils
devaient donc transmettre les longueurs d'onde du rayonnement solaire (visible
et proche Infrarouge, voir figure 25) mais arrêter le rayonnement
Infrarouge lointain à grandes longueurs d'onde produits par les
appareils de chauffage et autres corps terrestres (voir figure 25).
Actuellement, dans les immeubles dédiés au
secteur d'activité tertiaire (bureaux) on recherche à minimiser
les gains solaires, tout en gardant une bonne transmission lumineuse et une
bonne isolation.
Les vitrages correspondant doivent donc transmettre la
lumière visible, mais arrêter (donc réfléchir) les
Infrarouges du rayonnement solaire et les Infrarouges lointains (voir Figure
25). Il s'agit de vitrages à faible émissivité
sélectifs.
Si en outre la couche à faible émissivité
sélective est déposée sur une vitre teintée ou si
le coefficient de réflexion de la couche est augmenté, on obtient
un vitrage à basse émissivité sélectif et à
basse transmission.
1.1.3 - Mode de dépôt et
performance
Partie du spectre à grande longueur d'onde (IR). Le
dépôt à faible émissivité est un mince film
métallique ou d'oxyde métallique. Ce dépôt peut
être de type pyrolytique (CVD) ou obtenu par pulvérisation (PVD).
Le dépôt pyrolytique est plus résistant, plus commode
à manipuler et à fabriquer. Le dépôt obtenu par
pulvérisation est plus fragile mais présente de meilleures
performances. Le dépôt pyrolytique est appelé `couche dure'
et le dépôt PVD est appelé `couche tendre' ou encore
`couche douce'. Par dépôt, on obtient facilement des valeurs
d'émissivité faibles e = 0,2 (et même 0,04 pour des couches
`tendres') alors que l'émissivité d'un verre usuel non
traité est de l'ordre de 0,8 à 0,9 (typiquement 0,89).
1.1.4 - Les produits industriels
Il existe deux familles de vitrage à faible
émissivité (low-e glazing en anglais) : > Les verres
à couches classe C
La couche est déposée sous vide
(dépôt PVD magnétron). Il s'agit d'une couche dite
`tendre'. Pour obtenir un vitrage de sécurité à faible
émissivité, le verre est trempé mais la trempe doit avoir
lieu avant le dépôt de la couche afin de ne pas
détériorer celle-ci.
Ces couches sont plus performantes en termes d'isolation
thermique que les couches dites `dures' mais elles doivent être
utilisées uniquement en double vitrage car elles sont
délicates.
> Les verres à couches classe A
La couche est de type pyrolytique, déposée `en
ligne' à chaud pendant que la température du verre est encore au
voisinage de 600°C. Ce dépôt est appelé couche `dure'.
Le verre peut être trempé après le dépôt de la
couche.
La trempe thermique de ces verres classe A de type pyrolytique
est plus délicate que celle de verres classiques non traités. En
effet, la trempe thermique pose des problèmes engendrés par la
dissymétrie de rayonnement des deux faces (revêtue et non
revêtue).
La chauffe symétrique nécessaire pour éviter
une déformation du verre impose des consignes de chauffage
différenciées sur les deux faces.
De plus, pour ne pas dégrader la couche à faible
émissivité, la température atteinte avant refroidissement
ne doit pas dépasser 600°C (contre près de 650°C pour
la trempe thermique d'un verre clair classique). Il en résulte qu'un
refroidissement plus rapide s'impose pour obtenir un verre trempé.
Tableau5 : récapitulatif des propriétés
comparées des deux types de couches.
Revêtement `dur' (pyrolytique)
|
Revêtement `tendre' (dépôt PVD)
|
Avantages
|
Inconvénients
|
Avantages
|
Inconvénients
|
Bonne durabilité, manutention facile
|
valeur de U plus élevée.
|
transmission dans le visible élevée.
|
fragile à la manipulation, précautions
nécessaires pendant la fabrication du vitrage
|
la vitre traitée peut être trempée
|
diffusion optique légèrement plus visible.
|
bonne clarté, peu de diffusion.
|
doit être utilisé exclusivement en double
(ou triple)
|
NB : Si un vitrage est déjà en
place sur un immeuble, il est encore possible d'obtenir un vitrage à
faible émissivité et réflecteurs en appliquant sur ce
vitrage un film plastique mince revêtu d'une couche à faible
émissivité et à contrôle solaire. Ces films sont en
principe utilisés seulement pour la rénovation.
1.1.5 - Les économies d'énergie
Près de 25% de la facture énergétique
(chauffage et rafraîchissement) sont dus à la mauvaise
qualité des vitrages en termes d'isolation thermique.
L'efficacité des vitrages en ce qui concerne l'énergie est
caractérisée par le coefficient U et le coefficient g
(appelé SHGC pour `Solar Heat Gain Coefficient' en anglais).
Le coefficient g est exprimé par un nombre compris entre 0
et 1. Un faible coefficient g signifie moins d'apport de chaleur par le
rayonnement solaire et plus d'effet d'ombrage.
Les performances d'un vitrage isolant sont
caractérisées par sa valeur U. Le coefficient U, exprimé
en W/ (m2.K) (watts par m2 et par degré) représente le niveau de
déperdition de chaleur. Ainsi la valeur U d'un simple vitrage classique
est 5,8.
La valeur U est 2,8 pour un double vitrage ordinaire et 1,9 pour
un double vitrage avec couche isolante à faible émissivité
déposée sur la face 3 (figure 2).
La valeur de U est abaissée à 1,1 si la l'air
entre les feuilles de verre est remplacée par de l'azote.
L'épaisseur totale d'un tel double vitrage est 24mm. La valeur de U pour
un triple vitrage à faible émissivité et rempli d'azote
est aussi basse que 0,65 W/ (m2.K).
Figure 33. isolation thermique
comparées d'un simple vitrage,d'un double vitrage
ordinaire et d'un double vitrage avec couches à faible
emissivité
|
|
Dans un proche avenir, les vitrages isolants thermiques auront
des performances encore meilleures. Ainsi, un double vitrage isolant où
la lame d'air intermédiaire est remplacée par du `vide' pourrait
avoir une valeur de U aussi basse que 0,6 W/ (m2.K) pour une épaisseur
totale n'excédant pas 8mm. Rappelons qu'un mur sans isolation
particulière a une valeur de U typique de l'ordre de 0,5 W/ (m2.K). Les
meilleures performances actuelles en termes d'isolation thermique sont obtenues
avec des triples vitrages composés de feuilles de verre à
dépôts peu émissifs et dont les espaces sont remplis de gaz
xénon. Si dans tous les cas on a intérêt à avoir une
valeur de U la plus faible possible, la valeur du facteur solaire g optimale
dépend du climat. Pour les pays à climats chauds (où la
dépense d'énergie en climatisation est
prépondérante), g doit être faible. Au contraire, dans les
pays à climat froid (où les dépenses de chauffage sont
prépondérantes), une valeur de g est préférable
pour profiter de l'apport d'énergie solaire.
1.1.6 - La transmission spectrale
Pour caractériser de façon simple les
performances optiques d'un vitrage, il est commode de mesurer le coefficient de
transmission spectrale, c'est à dire la transmission en fonction de la
longueur d'onde du rayonnement. La couche à faible
émissivité permet de conserver une transmission lumineuse TL
élevée tout en réfléchissant sélectivement
le rayonnement Infrarouge (grandes longueurs d'onde). Le film plastique
métallisé abaisse le coefficient de transmission lumineuse TL
jusqu'à 20%, mais surtout abaisse fortement de coefficient g en
réfléchissant fortement le rayonnement Infrarouge. Ce type de
comportement est recherché pour les immeubles administratifs
(principalement pour les façades exposées au soleil).
- Aspects théoriques
- Notions sur les transferts thermiques
La distribution du rayonnement thermique sur une surface:
La puissance incidente, caractérisée par le flux G
est absorbée, réfléchie ou transmise, ce qui
s'écrit (figure 35):
G = áG +
ñG + ôG
Avec: a = absorbance ; p =
réflectivité ; t = coefficient de transmission.
Naturellement, a + p + t =
1.
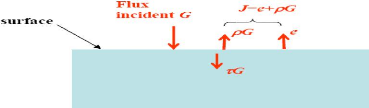
Figure 34. bilan énergétique (les fflux s'expriment
en W/m2 ).G est le flux de chaleur
incident en provenance de la source. J est le flux total
envoyé par la surface vers la source.
1.2.2 - Le problème du transfert de chaleur
à travers un vitrage
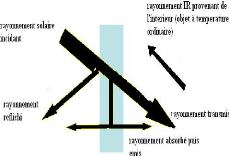
Soit à étudier le transfert de chaleur par
rayonnement à travers un vitrage (figure 36) :
Figure 35. interaction entre vitrage et rayonnement.
- venant de l'intérieur : le rayonnement infra rouge
émis par les objets présents et les appareils de chauffage. Il
s'agit d'optimiser les échanges pour avoir :
- en été : le minimum de chaleur provenant du
rayonnement extérieur
- en hiver : limiter au maximum les pertes vers
l'extérieur par rayonnement.
Des économies d'énergie sont
réalisées si on place une lame mince transparente dans le visible
et réfléchissante dans l'IR. En effet on optimise les transferts
radiatifs :
- en été, la lumière visible et surtout la
chaleur sous forme de rayonnement IR provient de l'extérieur (la
lumière solaire).
- en hiver, la source de rayonnement IR est essentiellement
située à l'intérieur.
Un vitrage à faible émissivité est donc
réalisé par un dépôt métallique de faible
épaisseur (de l'ordre de 4 nm), transparent dans le visible mais
réflecteur dans l'IR lointain.
2 - Les vitrages électrochromes
2.1 - Introduction
Les matériaux ou structures électrochromes ont la
particularité de changer de propriétés optiques (couleur
et/ou transparence lumineuse) sous l'effet d'un champ électrique
appliqué.
L'effet est réversible mais il peut être
rémanent ou non rémanent. Nous montrons ici deux exemples de
vitrages électrochromes. Ces vitrages électrochromes fonctionnent
sous basse tension et consomment une puissance électrique
extrêmement faible.
2.2 - Les vitrages `obturateurs' à cristaux
liquides
Description du fonctionnement
Le premier exemple est un vitrage apte à passer de
l'état diffusant à l'état transparent sous l'effet d'une
tension alternative de quelques dizaines de volts. Le film actif est
constitué d'une matrice polymère contenant de fines gouttelettes
de cristaux liquides (PDLC est l'acronyme de Polymer Dispersed Liquid
Crystal).
Ces vitrages, qui sont commercialisés, même avec
des dimensions importantes (plusieurs m2) sont plutôt utilisés
pour les bureaux, hôtels, hôpitaux ... Les applications domestiques
sont encore peu diffusées.
Au repos (lorsqu'aucune tension électrique n'est
appliquée) le vitrage est translucide. Le vitrage devient transparent si
la tension électrique est appliquée. Il n'y a pas d'effet
`mémoire' : le vitrage redevient translucide dès que la tension
électrique est supprimée. Le temps de réponse est
très court (inférieur au 1/10ème de seconde).
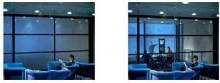
Figure 36. Vitrage électrochrome `obturateur' à
cristaux liquides.
A droite : le vitrage est opaque (pas de tension
électrique)
A gauche : le vitrage est transparent (tension électrique
appliquée)
Réalisation et structure du vitrage
obturateur
La réalisation est obtenue en plusieurs étapes.
Un liquide comprenant un mélange de molécules cristaux liquides,
de molécules polymérisables (appelées monomères) et
d'une petite quantité de billes de silice de très petit
diamètre (quelques dizaines de microns, en fait leur diamètre
correspond à l'épaisseur du film électrochrome à
former) et appelées à jouer le rôle d'espaceurs est
versée sur la face d'une vitre rendue conductrice par un
dépôt d'ITO (voir dépôt conducteur à base
d'oxyde d'étain et d'indium). Ensuite, une deuxième vitre dont la
face interne est elle aussi rendue conductrice par un dépôt d'ITO
est appliquée sur le film liquide. On obtient ainsi une structure
`sandwich' schématisée sur la figure 37.
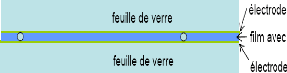
Figure 37. Structure d'un vitrage
obturateur. L'épaisseur du film est de quelques dizaines de
micromètres.
Les `espaceurs' (en silice) maintiennent l'épaisseur du
film constante et évitent tout court-circuit entre les deux
électrodes transparentes. Ces espaceurs occupent un très petit
volume du film et sont pratiquement Invisibles. L'épaisseur totale du
vitrage est de l'ordre de 3 millimètres. La morphologie de type
`microcomposite' composée d'un film mince polymère renfermant de
fines gouttelettes (dont le diamètre est de l'ordre de la dizaine de
micromètres) de cristaux liquides est formée au moment de la
polymérisation qui provoque une séparation de phase entre
molécules de cristaux liquides et molécules monomères
formant le film polymère.
A l'intérieur d'une gouttelette, les molécules de
cristaux liquides sont orientées les unes par rapport aux autres. Une
gouttelette est donc anisotrope du point de vue optique.
Cette anisotropie est caractérisée par la
présence d'un axe optique correspondant à la direction
d'alignement des molécules de cristaux liquides dans la gouttelette. Au
repos, les axes optiques des gouttelettes sont distribués au hasard et
la lumière est diffusée (le vitrage est opaque, ou plutôt
translucide) car le film PDLC n'est pas homogène (il diffuse la
lumière à l'instar du brouillard qui est constitué de
fines gouttelettes d'eau en suspension dans l'air).
Sous l'effet d'un champ électrique, les axes optiques
des gouttelettes sont alignés. Les molécules de cristaux liquides
sont choisies de telle façon que l'indice ordinaire no des
gouttelettes soit égal à l'indice de la matrice
polymère.
Le film apparaît `homogène' au rayonnement
incident et la lumière n'est plus diffusée (le vitrage devient
transparent) comme indiqué sur la figure 3. Rappelons que l'effet est
non rémanent : le vitrage redevient translucide si la tension
électrique est supprimée.
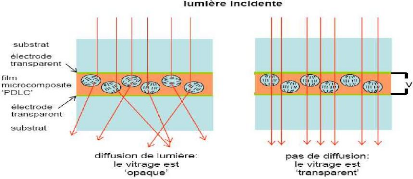
Figure 38. Principe de fonctionnement d'un vitrage
`obturateur'.Sous l'effet d'une tension électrique alternative de
quelques volts, les molécules de cristaux liquides s'orientent.
2.3 - Le vitrage électrochrome `assombrissant'
2.3.1- Description du fonctionnement
Le deuxième exemple de vitrage électrochrome est
basé sur le changement de transparence d'une fine couche
déposée entre deux feuilles de verres. Supposons le vitrage
initialement transparent.
L'application d'un courant électrique pendant un
certain temps (quelques secondes à une minute) rend le vitrage `sombre'.
Si le courant électrique est supprimé, le vitrage reste sombre.
Pour rendre le vitrage à nouveau transparent, il suffit d'appliquer un
courant électrique en sens inverse. Contrairement au cas
précédent, l'effet est rémanent. Le curant
électrique appliqué n'est pas alternatif mais continu.
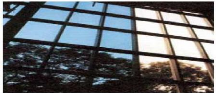
Figure 39. vitrage électrochrome pour le
bâtiment. (A gauche : état `sombre' A droite : état
`clair').
2.3.2- Applications
Ce type de vitrage trouve des applications dans le domaine du
bâtiment, comme en témoigne la figure (39), mais aussi dans le
domaine du transport automobile (haut de gamme). Par exemple, le toit en verre
rétractable et repliable qui équipe la Ferrari Superamerica a
été mis au point par Saint-Gobain. Une commande au tableau de
bord permet d'ajuster l'opacité sur 5 niveaux, depuis l'état
`clair' jusqu'à un état très `sombre'. Les
rétroviseurs électrochromes qui équipent certains
véhicules et sensés éviter l'éblouissement par les
véhicules suiveurs sont basés sur ce principe (ici, le changement
de transparence est commandé automatiquement par une cellule
photoélectrique).
2.3.3- Réalisation et structure du vitrage
assombrissant
La structure ressemble à la précédente :
le film mince électrochrome est placé entre deux feuilles de
verre. La face interne de chaque feuille de verre est rendue conductrice par un
dépôt d'ITO. Ces films d'ITO servent d'électrodes
transparentes. Le changement contrôlé de transparence est
basé sur le changement de composition d'un film mince (ici de l'oxyde de
tungstène WO3) entraînant un changement d'absorption optique
figure (41).
Ce système est commandé par un courant continu.
Initialement le film WO3 est transparent. L'application d'une tension
électrique entraîne la migration d'ions métalliques M+ vers
la couche d'oxyde de tungstène qui change de composition et devient
absorbante (bleu foncé).
Si la tension est supprimée, le vitrage reste sombre :
l'effet est rémanent. Pour revenir à l'état clair, il
suffit d'appliquer une tension électrique en sens opposé :
l'effet est donc rémanent mais réversible.
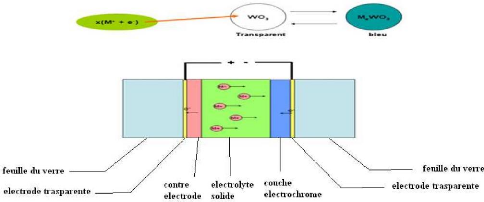
Figure 40.Principe de fonctionnement d'un verre electrechrome
à transparence controlée.
3- Les vitrages thermochromes : vers un contrôle
solaire `intelligent'
3.1 - Introduction : la thermochromie
Un matériau thermochrome, par définition, est un
matériau dont les propriétés optiques changent en fonction
de la température et ceci de façon réversible ou quasi
réversible.
Dans la vie courante, les matériaux thermochromes sont
de type organique, comme par exemple les cristaux liquides de type
cholestérique ou des molécules formant des pigments
appelés `leuco colorants'. Ces matériaux thermochromes sensibles
vers la température ordinaire trouvent des applications dans le domaine
grand public. Un exemple est donné par des encres pour étiquettes
collées sur des bouteilles pour vérifier si la température
optimale est atteinte ou encore des encres pour étiquettes de
boîtes de médicaments pour vérifier que la
température de conservation est suffisamment basse.
Une application en voie de développement des
matériaux thermochromes est l'application de peinture sur la
chaussée changeant de couleur vers 0°C (la peinture passe de
l'état `transparent' à haute température mais prend une
couleur rouge si la température devient inférieure à
+1°C) donnant ainsi l'alerte en cas de risque de verglas.Les applications
des matériaux thermochromes ne se limitent pas aux basses
températures.Citons l'indicateur de sécurité pour
température élevée d'appareil de chauffage, certaines
parties de moteurs ou encore l'indicateur de température optimale
atteinte pour cuisson (exemple : thermospot).
3.2 - Les dépôts et couches thermochromes
pour vitrages
L'effet thermochrome souhaité pour une application vitrage
est le passage réversible d'un état transparent vers un
état plutôt sombre ou réfléchissant au-dessus d'une
certaine température.
Certains verres contenant des nanoparticules de
composés métalliques (diamètres de l'ordre de quelques
millièmes de micromètres) sont susceptibles de présenter
cet effet. Ceci a été réalisé au niveau
expérimental. Cependant la température correspondant au
changement de comportement se situe vers quelques centaines de degrés,
ce qui n'est pas intéressant dans le cas d'une application pour
vitrages. Il faut donc trouver un matériau présentant l'effet
thermochrome au voisinage de la température ordinaire ou quelque peu
supérieure.
Il est possible de déposer un film thermochrome de
nature organique (un film de cristaux liquides par exemple) sur une vitre en
verre, ou plutôt entre deux feuilles de verres, l'ensemble
réalisant un vitrage appelé thermochrome. Une autre
méthode est un dépôt d'oxyde métallique
judicieusement choisi, qui présente un pouvoir réflecteur
sélectif pour la lumière visible et pour le rayonnement
Infrarouge.
Il existe des matériaux thermochromes minéraux,
qui se présentent généralement sous forme de
dépôts (les couches sont réalisées par PVD). Les
propriétés optiques sont affectées par suite de changement
de phase (passage de l'état semi-conducteur clair vers un comportement
de type métallique absorbant).
Un inconvénient est que les températures de
transformation sont plutôt élevées comme l'indique le
tableau :
Tableau 6 : Températures de transformation de quelque
oxyde.
Matériau
|
Tc (°C)
|
NbO2
|
800
|
BiVO4
|
300
|
AL2-xCrxO3
|
183...377
|
VO2
|
68
|
Parmi ces oxydes, l'oxyde de vanadium est le plus
intéressant pour l'application vitrage. L'effet thermochrome de l'oxyde
de vanadium est provoqué par le changement de phase accompagné
d'un changement de comportement semi-conducteur ? métal
rendant le matériau transparent à basse température et
absorbant à température élevée.
Cet effet est réversible :
Semi conducteur ? Tc (68°C)
? comportement métallique (transparent) (absorbant).
A la température de transition, la
résistivité électrique change de 4 ordres de grandeur. Le
matériau est mauvais conducteur de l'électricité à
basse température (résistivité de l'ordre de 100
~ .Cm) et meilleur conducteur à haute
température (résistivité de l'ordre de 0,01 .Cm). Ce
passage de l'état plutôt isolant vers un état plutôt
conducteur explique le changement des propriétés optiques.
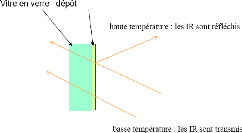
Lorsque la transition se produit, la transmission optique dans
l'Infrarouge (longueur d'onde ë égale ou
supérieure à 3jtm) passe de 70% à 30%,
alors que la transmission dans la partie visible du spectre est peu
affectée, ce qui est très intéressant pour le
contrôle `intelligent' de transfert thermique figure (42). Ce
revêtement est appelé `spectralement sélectif'.
Figure 41. Structure d'un vitrage `intelligent' thermochrome. Le
contrôle solaire s'ajuste automatiquement en fonction de la saison.
Par dopage de l'oxyde de vanadium VO2, il est possible de
modifier la température de transition Tc et obtenir une
température de transition de +10°C jusqu'à 70°C.
Par exemple, le dopage de l'oxyde de vanadium avec 1,9% de
tungstène abaisse la température de transition vers 29°C.
Ainsi, le dépôt sur un vitrage d'un couche mince
d'oxyde de vanadium convenablement dopé pour avoir une
température de transition vers 30°C, pourrait être
considéré comme une version `automatique' et `intelligente' de
vitrage à isolation thermique renforcée. Il s'agit d'un verre
fonctionnel `innovant'.
Un inconvénient pour sa commercialisation est un
abaissement de transparence pour la lumière visible et une
légère tendance à être coloré en jaune. De
grands progrès ont été réalisés
récemment, basés sur des dépôts de couches multiples
et un contrôle de l'épaisseur. Ces progrès permettent
d'envisager une application pratique prochaine.
Il faut aussi noter parmi ces progrès qu'un mode de
dépôt où l'oxyde de vanadium est formé de grains de
très petites tailles (quelques nanomètres) permet d'abaisser la
température de transformation de 68°C à près de
30°C, ce qui est appréciable pour une application vitrage.
3.3 - Autres variétés de vitrages
thermochromes
Il existe d'autres possibilités pour qu'un vitrage soit
thermochrome.
Première variété : la pose sur un vitrage
existant d'un film constitué par une solution de polymère et
d'eau prise en sandwich entre deux films très minces de polymère.
Ce film est pratiquement transparent à basse température mais
laisse passer peu la lumière si la température dépasse une
certaine valeur.
Une autre variété de vitrages thermochromes est
constituée non pas par des verres à couches minces mais par des
vitrages feuilletés thermochromes. La couche intermédiaire est un
polymère dopé avec des complexes de métaux de transition.
Les métaux dans ces complexes changent de coordination, modifiant ainsi
la transmission et la couleur du film polymère sous l'effet de la
température. Le vitrage s'adapte automatiquement en fonction des
conditions climatiques. Là encore il s'agit d'obtenir un vitrage
thermochrome `auto adaptatif' en fonction des conditions climatiques, mais
l'avantage du film VO2 est qu'il s'agit d'une version `tout minéral' de
bonne durabilité.
4 - Modification des propriétés optiques
du verre par dépôts multicouches diélectriques
(transparents)
4.1 - Introduction
Lorsque qu'une onde lumineuse qui se propage dans l'air arrive
sur la surface d'un verre, une fraction de l'intensité du rayonnement
lumineux est réfléchie. On appelle coefficient de
réflexion R le rapport entre l'intensité lumineuse
réfléchie et l'intensité lumineuse incidente.
Le coefficient de réflexion dépend de l'angle
d'incidence. Si les rayons lumineux arrivent perpendiculairement à la
surface du verre, environ 4% de l'intensité lumineuse est
réfléchie.
Ainsi, puisque la vitre a deux faces, c'est donc environ 8% de
l'intensité lumineuse qui est réfléchie. Ces reflets
peuvent être gênants. Dans ce cas, il faudrait trouver une
méthode pour réduire ces reflets. Au contraire, dans certaines
applications, il peut être intéressant d'avoir un facteur de
réflexion R très élevé.
De plus, pour des applications plus spécifiques, il est
souhaitable d'avoir un coefficient de réflexion dont la valeur est
contrôlée selon la `couleur' du rayonnement lumineux incident.
Il s'agit donc de modifier le coefficient de réflexion
du verre par des dépôts judicieusement choisis. Ce contrôle
sélectif du coefficient de réflexion R d'un verre est obtenu par
un dépôt, généralement multicouche, de films
diélectriques (c'est-à-dire transparents et donc non absorbants)
de très faible épaisseur. Les cas des dépôts
métalliques et à faible émissivité seront
traités dans d'autres chapitres.
4.2 - Applications pratiques des traitements
`anti-reflets'
4.2.1 - Dans le domaine du bâtiment et de
l'architecture
Les traitements anti-réfléchissants sont
utilisés pour les vitrines d'exposition (musées, vitrines de
magasins), rendant ainsi plus commode l'observation des objets sans reflets
parasites. Les cabines de presse dans les stades font appel aussi à des
vitres anti- réfléchissantes car l'intérieur est fortement
éclairé en comparaison avec l'extérieur. Le traitement
anti-réfléchissant n'est pas toujours souhaitable dans le domaine
du bâtiment. C'est le cas en particulier, des portes constituées
d'une feuille de verre (aéroports, halls d'accueil du public ...), des
abris bus urbains etc. ... Il est même recommandé dans cette
application illustrée par la figure (43) d'utiliser des verres
comportant une sérigraphie.
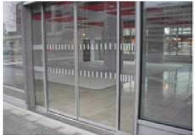
Figure 42. Il n'est pas souhaitable que les feuilles de
verre utilisées pour les portes de bâtiments avec accès
au public et le mobilier urbain soient traitées
anti-réfléchissantes. Au contraire, ces feuilles comportent
des sérigraphies afin d'être visibles !
4.2.2 - Dans le domaine de l'optique
Les traitements multicouches
anti-réfléchissants
sont très utilisés dans les instruments
d'optique et la lunetterie. Ces traitements sont très utiles pour
augmenter la luminosité des objectifs d'appareils photographiques et
éliminer les reflets parasites provoqués par des
réflexions multiples.
4.2.3 - Dans le domaine des énergies
renouvelables
Pour augmenter le rendement des cellules solaires
(photovoltaïques et thermiques), les verres de protections sont
revêtus de couches antiréfléchissantes.
4.3 - Applications pratiques des traitements
`semi-réfléchissants' et
`réfléchissants'
Ces traitements de surface du verre sont essentiellement
utilisés dans le domaine de l'instrumentation optique. Nous donnons ici
des exemples d'application.
Application 1 : le dépôt sur du
verre d'une couche transparente d'indice de réfraction
élevé, par exemple d'oxyde de titane, est utilisé pour
produire un effet décoratif par réflexion sélective. Ce
dépôt est obtenu en condition industrielle par
pulvérisation PVD magnétron.
Application 2 : La cavité
résonnante d'un LASER utilise un traitement réfléchissant
voisin de 1 pour une couleur (c'est-à-dire une longueur d'onde) bien
précise : celle du rayonnement émis par le LASER.
Application 3 : Les présentateurs de
journaux télévisés utilisent souvent un `prompteur'. Cet
appareil, qui met en oeuvre une glace semi-réfléchissante, permet
de lire un texte déroulant tout en fixant la caméra de prise de
vue.
Application 4 : il peut être
intéressant dans certains instruments d'optique scientifique de disposer
de deux faisceaux de même intensité lumineuse issus d'une seule
source. Ceci est obtenu en utilisant un `séparateur de faisceaux'
élaboré à partir d'un verre traité `semi
réfléchissant'.
4.4 - Applications pratiques des traitements
réfléchissants sélectifs
L'application la plus courante des miroirs sélectifs
est la réalisation de `miroirs froids'. Les miroirs `froids' permettent
un éclairage efficace et intense en lumière visible tout en
minimisant le chauffage indésirable par infrarouge et trouvent des
applications concrètes.
On peut citer comme exemples les spots d'éclairage de
vitrine de magasins, de vitrines d'exposition de musées, sans oublier
les miroirs utilisés en salles d'opérations chirurgicales etc.
... Ces dépôts sélectifs multicouches sont obtenus par
procédé PVD. (Voir aussi le chapitre verres à faible
émissivité et à contrôle solaire).
4.5 - Aspects théoriques : le coefficient de
réflexion d'une surface de verre
Un rayonnement lumineux incident sur la surface de
séparation air/verre subit d'une part une réflexion, alors que
d'autre part une partie de l'intensité lumineuse est transmise
(réfraction).
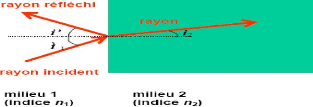
Figure 43.ondes incidente, réfléchie et transmise
à la surface du verre. Dans le cas qui nous intéresse, le
milieu 1 est l'air et le milieu 2 est le verre.
Considérons les lois de Descartes de réflexion et
de réfraction figure (44) portant sur les angles des rayons incident i1,
réfléchi i'1 et réfracté i2 :

Le coefficient de réflexion dépend de l'angle
d'incidence i1 et de l'état de polarisation de l'onde incidente. Dans ce
qui suit, on s'intéressera essentiellement au cas de l'incidence normale
(i1=0), ce qui correspond à la situation la plus courante.
Dans le cas de l'incidence normale, en supposant que le milieu
1 est le vide ou l'air (n1=1 ou 1,00293, respectivement), et que le milieu 2
est un verre courant (n2 voisin de 1,5), le coefficient de réflexion R
est :

D'après cette équation, il en résulte que le
coefficient de réflexion R de la surface du verre est égal
à 0,04 et donc que le coefficient de transmission T est égal
à 1-R, soit 0,96.
Figure 45. Les ondes multiples
(dépôt monocouche)
|
|
Dans certaines applications, il peut être
intéressant d'avoir R proche de 0 et dans d'autres applications R voisin
de 1, ou encore de l'ordre de 0,5. Pour ajuster le coefficient de
réflexion (et donc de transmission), pour un verre donné, il
convient de modifier sa surface. Ceci peut être obtenu par des
dépôts de couches minces diélectriques (c'est-à-dire
transparentes et non absorbantes).
4.6 - Aspects théoriques : les
dépôts simples `monocouches'
Soit une couche mince et transparente d'indice n0,
déposée sur du verre d'indice n2. Un calcul simplifié avec
2 ondes donne facilement les conditions pour avoir un coefficient de
réflexion fort ou faible, selon que les ondes réfléchies 1
et 2 figure (45) sont en phase ou en opposition de phase.
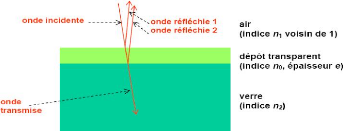
Figure 44. Ondes incidente, réfléchie et
transmise (verre à une seule couche).
La lumière réfléchie est composée
de deux ondes: une onde provenant de la réflexion sur la surface
air/dépôt et une onde réfléchie sur la surface
dépôt/verre. Les ondes étant cohérentes, il faut
additionner non pas les intensités mais les `vibrations' ou champs
électriques (interférences).
Le calcul plus rigoureux demande de prendre en
considération les réflexions multiples dans la couche dont les
coefficients de réflexion sont R1 et R2 figure (46). Après avoir
effectué la sommation des ondes multiples (il y en a une
infinité, et dont l'amplitude est décroissante), on peut calculer
les conditions et performances de traitements réfléchissants et
anti-réfléchissantes.
Deux cas sont à étudier : le revêtement
antireflet et le revêtement réfléchissant. Les
différents milieux sont supposés parfaits (donc non
absorbants).
Soit ë0 la longueur d'onde de la
lumière incidente.
4.6.1 - Traitement antireflet
Soit ë0 la longueur d'onde du rayonnement
incident. On peut montrer que le traitement antireflet est obtenu si les deux
conditions suivantes sont remplies :
a) l'indice de la couche n0 doit être inférieur
à celui du verre n2.n1<n0<n2
b) l'épaisseur e de la couche est donnée
par : n0 e = ë0/4 + k
ë0/2
Où k est un nombre entier.
Ce dépôt est donc une couche appelée lame
appelée `quart d'onde'. Le coefficient de réflexion minimum est
:

Le coefficient de réflexion est nul si :

Pour qu'une surface de verre d'indice n2=1,5 présente
un coefficient de réflexion nul, il faudrait un dépôt
d'indice 1,23. C'est une valeur très faible. Il faut en outre que le
dépôt soit réalisé avec un matériau de bonne
durabilité chimique et mécanique, adhérant au verre et
pouvant être déposé par un moyen commode industriel (PVD
par exemple). Les matériaux qui conviendraient le mieux seraient:
- le fluorure de magnésium MgF2 (indice 1,38)
- la cryolite Na3AlF6 (indice 1,35)
Si :

Alors le coefficient de réflexion sera minimum pour
ë = ë0.
Un traitement anti-réfléchissant par
dépôt de MgF2 abaisse le coefficient de réflexion de la
valeur initiale (verre sans dépôt) 4% à 1,2% (figure
47).
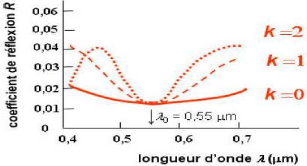
Figure 46. Réponse spectrale d'un dépôt
monocouche anti-réfléchissantes
Le dépôt est ajusté pour que le coefficient
de réflexion R soit minimum pour la longueur l'onde
ë 0=0,55 _m (centre du spectre visible).
A noter :
Si le dépôt est épais (k
élevé), alors l'intensité sera nulle pour plusieurs
valeurs de la longueur d'onde dans le domaine visible du spectre. Dans la
figure, on a représenté les cas k=0, k=1 et k=2.
La valeur de R en fonction de la longueur d'onde explique l'effet
décoratif obtenu par des couches minces d'oxyde de titane sur du
verre.
Mais il y a deux problèmes car :
1) le minimum n'est pas nul
2) le calcul suppose une lumière monochromatique de
longueur d'onde ë0
, alors qu'on souhaite en général une
réponse sur un spectre étendu (le spectre de lumière
visible, par exemple). Pour pallier ces inconvénients, il faut utiliser
des dépôts multicouches.
4.6.2 - Traitement réfléchissant
Pour obtenir un traitement à fort pouvoir
réflecteur, il faut que l'indice de réfraction de la couche soit
supérieur à celui du verre. C'est le cas par exemple de l'oxyde
de titane. Le coefficient de réflexion est maximum si l'épaisseur
e de la couche est donnée par :
n0 e = ë0/4 + k
ë0/2
Où k est un nombre entier.
Comme précédemment, il s'agit d'un
dépôt `quart d'onde'. Par exemple, si on souhaite obtenir des
reflets bleus (longueur d'onde 0,45 jtm) en éclairant
un objet en verre par de la lumière blanche il faut un
dépôt d'oxyde de titane (indice égal à 2,28)
d'épaisseur environ 0,05 JLm.
4.7 - Les dépôts `multicouches'
4.7.1 - Traitement anti-reflets
La figure 47 donne l'exemple d'un revêtement à 4
couches d'indices de réfraction et d'épaisseurs tels que :
n1e1 = n2e2 = n3e3 = n4e4 = 0,485 jim n1=1,38 ;
n2=2,2 ; n3=2,43 ; n4=1,887
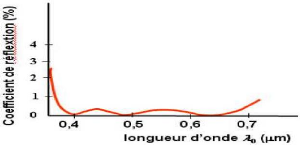
Figure 47. Exemple de réponse spectrale d'un traitement
anti-reflets à 4 couches : n1e1 = n2e2 = n3e3 = n4e4 = 0,485 mm
n1=1,38 ; n2=2,2 ; n3=2,43 ; n4=1,887
4.7.2 - Couches à fort coefficient de
réflexion :
Il existe deux solutions : soit un dépôt
métallique, soit un dépôt diélectrique non absorbant
(simple couche ou à couches multiples).
Dans le cas d'un dépôt métallique, les
coefficients de réflexion obtenus sont :
R=0,96 (argent)
R=0,92 (aluminium)
Si on utilise des dépôts diélectriques non
absorbants, on obtient un résultat médiocre avec un simple
dépôt monocouche d'indice élevé. Par exemple, avec
une couche de ZnS (indice 2,35) sur du verre d'indice 1,5 on a: R=0,3.
Pour atteindre des pouvoirs réflecteurs très
élevés, il est nécessaire d'avoir recours à des
systèmes multicouches constitués par des couches alternées
de faible indice et de fort indice et d'épaisseur optique e `'quart
d'onde» ë0/4 (rappelons que l'épaisseur
optique est égale à l'épaisseur de la couche
multipliée par l'indice de réfraction de la couche),
ë0 étant la longueur d'onde du rayonnement pour
laquelle on veut obtenir le pouvoir réflecteur maximal.
La figure (47) donne à titre d'exemple la variation du
coefficient réflecteur R en fonction de ë/
ë0 pour un dépôt constitué de 5
doublets de couches d'indices de réfraction respectif n1=1,38 et
n2=2,3.
Avec un système multicouche déposé sur du
verre d'indice n, constitué de 5 doublets comme indiqué sur la
figure (49), on a le dépôt des 5 doublets sur du verre d'indice
n=1,5 donne:
R=0,98 Il est possible avec des dépôts plus
élaborés d'obtenir R=0,999. Cette valeur, qui dépasse de
loin le coefficient de réflexion d'un métal, et qui de plus
correspond à une absorption nulle, est intéressante pour la
réalisation de LASERS.
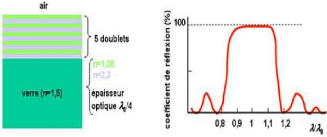
Figure 48. Exemple de traitement multicouche à fort
coefficient de réflexion constitué de 5 doublets et sa
réponse spectrale.
4.7.3 - Traitement pour réflexion
sélective
Il s'agit de réaliser des systèmes
présentant un coefficient de réflexion variable selon la longueur
d'onde, pour obtenir par exemple:
- des miroirs `froids' transparents pour l'Infrarouge (IR) et ne
réfléchissant que la lumière visible - des miroirs
`chauds' transparent pour le visible et réfléchissant
l'Infrarouge.
- des miroirs dichroïques permettant de séparer des
faisceaux `de couleurs différentes'. Exemple de `miroir froid'.
Cette application impose certaines conditions :
1) un coefficient de réflexion élevé (au
moins 95-98%) dans le spectre visible (longueurs d'onde: 400 à 700
nm).
2) une transmission élevée dans le proche IR (800
à 2500 nm).
3) une diffusion et absorption dans les couches du
dépôt faible (<1%)
4) une bonne reproductibilité de température de
couleur (en réflexion)
5) une bonne stabilité thermique des couches du
dépôt (>250-400°C)
6) une durée de vie supérieure à 5000
heures sous éclairage intense
Comme cela a été signalé, ces miroirs sont
constitués par un empilement alterné de matériaux
transparents d'indice élevé et faible.
Les matériaux utilisables dans la pratique sont :
- pour les indices faibles : MgF2 (1,35) ou SiO2 (1,46)
- pour les indices élevés : TiO2 (2,28) et ZnS
(2,4)
Les systèmes couramment utilisés sont :
a) MgF2 et ZnS (`réflecteur doux')
b) SiO2 et ZnS (`réflecteur semi dur')
c) SiO2 et TiO2 (`réflecteur dur')
Applications des miroirs `froids' :
Les miroirs `froids' qui permettent un éclairage efficace
et intense en lumière visible et en minimisant le chauffage
indésirable par infrarouge trouvent des applications
concrètes.
On peut citer comme exemples les spots d'éclairage de
vitrines de magasins, de vitrines d'exposition de musées, de salles
d'opérations chirurgicales etc. ... La figure (49) donne la
réponse spectrale d'un miroir froid constitué par un
dépôt de 23 couches et d'épaisseur totale égale
à 2 micromètre. Les couches successives ont été
produites par technique PVD.
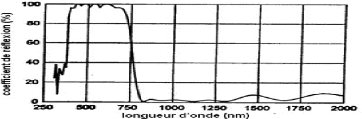
Figure 49. Réponse spectrale d'un miroir `froid'
composé de 23 couches diélectriques : 11 couches de faible
indice (silice) alternées avec 12 couches de fort indice (TiO2).
L'épaisseur totale du dépôt est égale à 2
JLm.
A noter que le coefficient de réflexion est presque
égal à l'unité dans la totalité du domaine visible
et pratiquement nul en dehors de ce domaine : le miroir est transparent dans
l'Infra-rouge et l'Ultra-violet.
5 - Le vitrage autonettoyant
5.1 - Introduction
Les architectes conçoivent des immeubles de grandes
dimensions (hauteurs). Ces façades de grandes surfaces et de grandes
hauteurs posent un problème car elles sont difficiles à atteindre
et donc difficiles à nettoyer. En 2001, la société
Pilkington a commencé à commercialiser le vitrage
`autonettoyant', suivie par Saint-Gobain ... et d'autres manufacturiers.
Le principe d'un vitrage autonettoyant est basé sur une
couche transparente déposée en face 1 et qui a la
particularité d'être photocatalytique (sous l'effet des UV A de la
lumière solaire) et hyper hydrophile. L'effet photocatalytique provoque
la destruction d'impuretés déposées sur la vitre tandis
que la propriété de superhydrophilicité favorise
l'élimination de ces impuretés avec la pluie.
5.2 - Principe d'un vitrage autonettoyant
Plusieurs composés sont capables de provoquer l'effet
photocatalytique favorisant la destruction de composés organiques comme
par exemple:
TiO2, SnO2, WO3, ZnO, CdS ... L'oxyde de titane TiO2 (sous forme
cristalline anatase) est le plus actif et de plus présente un aspect
d'hyperphilicité.
Le principe actif d'un vitrage autonettoyant est un mince film
d'oxyde de titane TiO2 déposé sur la face extérieure de la
vitre. Sous l'effet du rayonnement solaire, ce film provoque des
réactions d'oxydo-réduction qui détruisent les
composés organiques en formant du CO2 et de l'eau. Le nettoyage de la
surface de la vitre est obtenu par la pluie qui achève l'action par
lavage. L'effet hydrophile empêche la formation de gouttelettes d'eau qui
concentreraient les impuretés et laisseraient des traces après
séchage. En outre, l'eau formant un film mince sur la vitre est
évacuée rapidement par évaporation.
Un verre autonettoyant est donc efficace quand il est
exposé alternativement au soleil et à la pluie. Cette action
n'est pas efficace directement pour la destruction particules minérales,
mais diminue considérablement leur adhésion au vitrage par
élimination des salissures organiques. Les salissures minérales
sont donc aussi éliminées avec la pluie.
5.3 - Caractéristiques et techniques de
dépôt du film autonettoyant TiO2
a) le film doit être déposé en face 1 du
vitrage Il s'agit d'une couche mince transparente d'oxyde de titane TiO2 sous
forme anatase. Le dépôt est généralement est
appliqué `en ligne' à haute température pendant la
fabrication de la feuille de verre.
b) Il s'agit donc d'un dépôt de type pyrolytique
transparent d'oxyde de titane, dit `dépôt dur', est très
résistant chimiquement et mécaniquement, ce qui est indispensable
pour une
application en face1 (face extérieure). En outre, la
manipulation est plus facile et le délai de stockage `avant pose' n'est
pas limité.
c) l'épaisseur du dépôt est de quelques
dizaines de nm (quelques millièmes de micromètres).
d) les vitrages autonettoyants réduisent la transmission
des rayonnements UV (A et B) de 20 à 40 % ce qui est un avantage
certain.
d) la pollution possible par les ions sodium Na+ provenant du
verre pourrait poser un problème si l'épaisseur du
dépôt était trop faible.
e) outre le dépôt pyrolytique en ligne (qui est le
dépôt le plus courant), d'autres procédés de
dépôt sont possibles :
- l'enduction, non utilisée pour les vitrages (poudre de
TiO2 + liant)
- le dépôt par procédé sol-gel (`dip
coating'), suivi d'un recuit à haute température (300°C
à400°C) pendant lequel le composé organo-métallique
est transformé en oxyde de titane.
5.5 - Aspects théoriques des effets
photocatalytique et hyperhydrophile de l'oxyde de titane
L'oxyde de titane TiO2 est un matériau présent
dans de nombreux produits de la vie courante (pigments de peinture,
cosmétiques, denrées alimentaires). Il se présente sous
trois formes cristallines : rutile, anatase et brookite. La
photoactivité de TiO2 est connue depuis plus de soixante ans. C'est sous
sa forme anatase (densité 3,9) que l'oxyde de titane présente la
plus grande activité de photo catalyse et d'hydrophobicité
photo-induite. Les dépôts CVD sont sous forme anatase.
L'anatase est un semi-conducteur. L'énergie de sa bande
interdite est 3,2 eV, ce qui signifie que des photons d'énergie au moins
égale à cette valeur peuvent créer des porteurs de charge
libres. C'est le cas des UV A (de longueur d'onde égale ou
inférieure à 0,38 jtm) de la lumière
solaire. Ainsi, l'anatase est transparent à la lumière visible
(surtout sous forme de film mince) mais à tendance à absorber le
rayonnement UV.
La figure (50) montre le mécanisme photochimique
conduisant à la dégradation des salissures organiques
déposées sur la surface de l'oxyde de titane.
Tout d'abord un photon UV crée une paire de porteurs de
charges électriques mobiles (l'électron qui laisse une place
vacante appelée `trou'). Ces porteurs de charges migrent à la
surface et créent des radicaux par interaction avec des molécules
d'eau et d'oxygène de l'atmosphère.
Les radicaux ainsi créés .O2-
et .OH vont dégrader activement les salissures
organiques par suite de réactions d'oxydo-réduction. Les
salissures constituées de molécules organiques ainsi
dégradées vont être éliminées par l'eau de
pluie grâce à l'effet d'hyperphilicité de l'anatase.
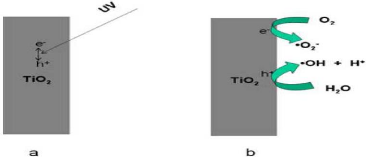
Figure 50. Réactions d'oxydo-réduction
photoinduites à la surface de l'oxyde de titane
A : formation photoinduite d'une paire de porteurs de charge
mobiles (électron + `trou')
B : formation de radicaux responsables des réactions
d'oxydo-réduction.
La figure (51) montre de façon schématique le
mécanisme d'hyperphilicité photoinduite oxyde de titane. Les
photons UV (de la lumière solaire) induisent la formation de lacunes
d'oxygène à la surface de l'oxyde de titane, ce qui favorise
l'adsorption de molécules d'eau est facilité. Les
molécules d'eau se dissocient et des groupes hydroxyles -OH se forment
surface, rendant ainsi la surface de l'oxyde de titane hyperhydrophile.

Figure 51.Mécanisme de l'hydraulicité
photoinduite de l'oxyde de titane
6-Le verre émaillé et le verre
sérigraphié
6.1-Définition
Le verre émaillé ou sérigraphié est
un produit trempé dont une face (ou les deux) est revêtue d'une
(ou plusieurs) couche d'émaux colorés, opaques, vitrifiés
au cours de la trempe thermique. Tous les verres trempables peuvent être
émaillés ou sérigraphié.
Le processus de l'émaillage et de la sérigraphie se
déroule de la façon suivante :

Dépôt de l'émail
Découpe du verre
Façonnage, lavage et séchage


- trempe
Chauffage du verre émaillé ou
sérigraphié
Séchage de l'émail
Figure52.Processus de l'émaillage et de la
sérigraphie des verres.
6.2-L'émaillage :
6.2.1-Définition d'un émail :
C'est un verre fusible à 600°C environ, auquel on
a ajouté un colorant appelé en terme technique "pigment". Pour
que l'émail soit plus fusible que le verre, on utilise des "frittes" de
verre de composition spéciale (plus fondant, à base de
borosilicate de plomb. Il existe également des émaux sans plomb.
Les pigments sont des oxydes minéraux qui donnent la couleur à
l'émail. Ils sont portés à haute température pour
rendre la teinte stable.
6.2.2-Techniques d'émaillage :
> Enduction au rideau
Cette technique est utilisée pour les grandes
séries. Elle assure une excellente opacité avec une consommation
d'émail réduite. Un convoyeur à vitesse variable
entraîne les volumes à émailler sous une tête
d'épandage. La tête est un bac suspendu possédant une fente
à sa base. Cette tête est remplis d'émail en suspension, un
film s'écoule par la fente, les volumes crèvent le film à
grande vitesse et entraînent une quantité d'émail sur leur
face supérieure. La quantité d'émail déposée
est fonction de la vitesse de passage sous la tête, la viscosité
de l'émail et l'ouverture de la fuite. L'émail provenant d'un bac
avec agitateur est sans cesse recyclé. Ce procédé
évite les taches d'émail sur la face inférieure.
> Enduction au pistolet
Le pistolet pulvérisateur est supporté par un
bras mécanique qui fait subir à celui-ci un mouvement
perpendiculaire de va-et-vient par rapport aux volumes qui avancent sur un
transporteur à rouleaux sous la pulvérisation.
La vitesse du pistolet est réglée par rapport
à la vitesse de défilement du volume. Ce procédé
pollue la face inférieure et les chants ; un nettoyage soigneux des
volumes avant trempe est impératif.
> Enduction par rouleau
L'enduction est réalisée par un rouleau,
lui-même enrobé par un rouleau imprégnateur baignant dans
le bac contenant les émaux. Cette technique est réservée
aux grandes séries. Elle est très économique quant
à la consommation d'émail. Elle assure une excellente
opacité, sans pollution des chants et de la face inférieure.
7-la sérigraphie :
La particularité de la sérigraphie par rapport
aux autres techniques d'impression est que l'on imprime à travers le
cliché sur le support et non pas comme dans les autres techniques, par
report du cliché sur le support. Pour ce faire, on utilise un
écran composé d'un tissu synthétique (polyester) tendu sur
un cadre métallique. Sous cet écran (dit cliché), on pose
le support (verre) destiné à recevoir l'impression.
Ce cliché est obtenu par une méthode photo
mécanique directe de telle façon que les mailles du tissu soient
obturées dans les endroits qui ne doivent pas être imprimés
et ouvertes dans les parties de dessin qui doivent être reproduites.
L'émail, déposé sur le dessus de l'écran à
l'intérieur du cadre, est pressé à travers les mailles
ouvertes de l'écran à l'aide de la raclette (lame de caoutchouc)
.Cette opération est suivie d'un séchage ou polymérisation
afin de faciliter les manutentions du produit imprimé ou de permettre
d'autres impressions. Cette polymérisation est indispensable pour
éviter le phénomène de craquelure lors de la trempe du
volume. Le cycle de sérigraphie avec émaux est achevé par
la trempe qui permet de cuire les émaux (environ 650°C).
8-Caractérisation des couches minces
La caractérisation d'une couche mince s'effectue par la
méthode suivante: mesure de 1'épaisseur, caractérisations
structurales et analyse de la composition
8.1-Mesure de I' épaisseur :
La caractéristique essentielle d'une couche mince
étant sa faible épaisseur, Deux grandes familiers de
méthodes de mesure de 1'épaisseur sont présentes sur le
marche : celles qui permettent la mesure en temps réel au moment de la
fabrication et celles qui font appel a des procèdes en temps
diffère. [8].
> Les méthodes par micropesée
:
Eu égard aux dimensions réduites, la masse d'une
couche mince est toujours exprimée en microgrammes et le matériel
de mesure doit donc être très spécifique. Dans les
années 60 deux techniques ont été
développées, 1'une, dite microbalance a fil de torsion est
quasiment abandonnée après avoir suscite beaucoup d'espoirs,
1'autre, microbalance a quartz vibrant, imaginée simultanément
par Gunther SAUERBREY en Allemagne et Pierre LOSTIS en France, constitue
actuellement le procède privilégie de mesure de
1'épaisseur d'une couche mince pendant sa formation.
> Procèdes optiques :
Le plus connu est plus employé comme moyen de
contrôle d'une microbalance quartz (étalonnage en cas de nouveau
type de dépôt ou déplacement de quartz) que
véritablement comme moyen de mesure de routine car il est en temps
diffère et de plus destructeur de la couche le plus souvent. Son
principe est base sur la génération de franges
d'interférence entre un faisceau lumineux monochromatique incident et
réfléchi par la couche, selon la méthode du coin d'air.
8.2-Détermination de la structure.
En métallurgie des poudres ou des monocristaux, on a
coutume d'analyser la structure des matériaux par le biais de la
diffraction des rayons X traversant ledit matériau. Avec les films, eu
égard a leur faible épaisseur, cette technique manque de
sensibilité, de plus la présence d'un substrat conduit
généralement a des interférences complémentaires du
type orientation préférentielle des grains, macro et micro
contraintes liées au processus de préparation.
II faudra donc prendre des précautions
particulières si on veut a 1'aide des RX obtenir des informations utiles
sur la structure (ainsi un substrat monocristallin typique d'une application
sur semiconducteurs, induit des angles de diffraction spécifiques qui se
superposent et dépassent en intensité le signal couche mince).
La solution dans ce cas consiste à orienter le substrat
par rapport au faisceau de telle sorte que la condition de Bragg ne puisse
être satisfaite pour le substrat, ce qui en général n'aura
pas d'incidence sur le film qui est le plus souvent polycristallin. II
n'empêche que si le film est trop mince (<200nm) on aura du mal
à voir quelque chose.
8.3-Morphologie d'une couche mince
Le microscope a balayage (MEB) peut être utilise pour
1'étude analytique des surfaces sous fort grossissement. Par rapport au
microscope optique il présente 1'avantage essentiel d'une
résolution accrue et d'une profondeur de champ importante, mais en plus
le bombardement d'une surface par des électrons peut induire tout un
ensemble de phénomènes exploitables pour 1'analyse.
8.4-Analyses des contraintes
La direction d'une contrainte dans un film peut être
déterminée parfois par simple examen à 1'oeil nu dans le
cas d'un substrat mince reconverti sur une seule face. Si la cote recouverte
est concave, la couche est en tension, elle est comprimée dans le cas
inverse. La mesure du rayon de courbure donne la contrainte :
S = (E/6(l-v) r} (ts 2/tf) relation dans
laquelle :
· E module d'Young du matériau, v coefficient de
Poisson du substrat, ts épaisseur du substrat.
· tf épaisseur du film, r rayon de courbure.
En fait la validité de cette relation nécessite
deux conditions principales : une liaison importante entre le film et le
substrat et pas de déformation plastique a I' interface. Cela signifie
que lors du dépôt, et tout particulièrement au
début, il n'y a pas eu de variation anormale de la température.
On devra donc prendre garde à ce problème thermique lors de la
réalisation [8].
8.5-Adhérences
On vient de signaler 1'importance de 1'adhérence dans
1'évaluation significative des contraintes. II apparait très
difficile de préciser quantitativement les interactions atomiques ou
moléculaires responsables de cette adhérence.
8.6- compositions
L'aspect le plus important d'une caractérisation de
couche mince est sans doute 1'analyse de sa composition. Les méthodes
analytiques, classiques avec les matériaux massifs, sont le plus souvent
utilisées [8].
Chapitre IV Le verre feuilleté

1- Généralités sur Le verre
feuilleté
1-1 Historique :
En 1909, un chimiste français, Edouard Benedictus, fit
tomber un jour, en rangeant son laboratoire, un flacon contenant une solution
de nitrocellulose. Il constata avec surprise qu'au lieu de voler en
éclats, le flacon, bien que fendillé en étoile ne
s'était pas brisé. Il invente alors ce qui deviendra le verre
feuilleté, auquel il donne le nom de Triplex. Le Triplex a sauvé
la vie de Georges Clemenceau lors de l'attentat manqué de 1919, en
démontrant l'utilité de ce verre qui n'éclatait pas en
morceaux dangereux, mais s'étoilait sous l'impact sans chuter ou
projeter d'éclats vulnérants. Cet attentat fit la
publicité et la popularité de ce produit alors
révolutionnaire. L'utilisation du verre feuilleté dans le
bâtiment fut plus tardive. La première grande réalisation
en verre feuilleté en France est la Pyramide du Louvre à
Paris.
Ce procédé, industrialisé à la fin
des années 1930, qui consiste à lier deux feuilles de verre par
un film intercalaire polymère transparent fait du verre un produit de
sécurité.
1.2- Définition
Le verre feuilleté est un assemblage de feuilles de
verres et d'intercalaires de nature plastique. Les intercalaires peuvent se
présenter sous forme de film, généralement
(Poly-VinyleButyral) ou EVA (Ethyle-Vinyle-Acétate), ou bien sous forme
liquide, coulée entre deux verres (résine). Le verre
feuilleté pour bâtiment fait l'objet de la norme EN ISO 12543.
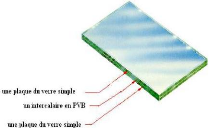
Figure 63. Composition d'un verre
feuilleté ordinaire
Le verre feuilleté résiste à 1'impact
(propriété très importante). Lors d'un choc avec un corps
étranger, le verre se fendille, la fracture est
localisée au point d'impact sans altérer la
visibilité. L'intercalaire PVB, maintient les morceaux de verre en
place, ce qui diminue le risque de coupure par 1'éclat de verre. II
garde 1'étanchéité de la paroi.
De plus, 1'énergie résiduelle du corps est
absorbée par cet intercalaire ; le vitrage empêche donc le passage
du corps si 1'impact n'est pas disproportionne.
2- Principe de fabrication du verre
feuilleté
Le verre de sécurité (feuilleté) est un
assemblage de deux ou plusieurs feuilles de verre (recuit ou trempe)
liée entre elles par un ou plusieurs films de polyvinyle butyral (PVB)
ou d'autres matériaux synthétiques, résines ou gels
peuvent être utilises.
Lors du processus de laminage, les verres sont places a
1'intérieur d'un autoclave puis soumise a une pression de 180 a 200
pascal combinée a une température oscillant entre 275 a
300C°. Ce précède assure aussi une parfaite adhérence
des différents éléments entre eux, ainsi le produit rend
transparent en éliminant 1'air emprisonne entre 1'intercalaire
synthétique et le verre.
Alors le verre feuilleté est un matériau composite
combinant les propriétés du verre aux propriétés de
1'intercalaire utilise (adhésion au verre, élasticité,
résistance a 1'impact).
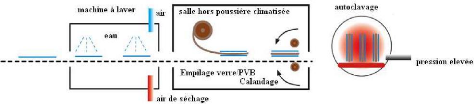
Figure 64.Chaine de fabrication du verre feuilleté
2.1- Films intercalaires
L'intercalaire, de par ses propriétés
mécaniques et adhésives, joue deux rôles. Il permet d'une
part de dégrader une partie de l'énergie d'impact par
déformation viscoplastique et d'éviter la projection de
fragments. D'autre part, après impact, il permet de conserver une tenue
résiduelle assurant le maintien du vitrage.
Les films intercalaires permettent d'améliorer les
performances du verre d'un point de vue mécanique mais aussi acoustique
(atténuation de certaines fréquences) tout en conservant la
propriété de transparence.
Son processus de fabrication lui permet aussi par adjonction
de colorant d'être utilisé comme élément de
décoration. Le type d'intercalaire peut varier suivant le niveau de
performance recherché (polyuréthane, polycarbonate,
résines bi-composants, polyéthylène, ...).
Nous nous intéresserons ici au seul cas du poly ([alcool
de vinyle] -co- [butyrate de vinyle]) ou « polyvinyle Butyral »
(PVB).
Ce polymère est le plus couramment utilisé pour
les applications vitrages feuilletés grâce à son forte
compatibilité avec le verre, liée à sa transparence et
à ses remarquables propriétés adhésives, ainsi
qu'à ses propriétés viscoélastiques garantissant
une déformation importante avant rupture et un amortissement maximal des
basses fréquences à température ambiante
viscoélastiques garantissant une déformation importante avant
rupture et un amortissement maximal des basses fréquences à
température ambiante [10].
2.1.1- Fabrication de résine de polyvinyle
Butyral :
Le film utilise pour la fabrication de verre feuilletés
est en polyvinyle Butyral (PVB) obtenu par la réaction du butyraldehyde
sur 1'alcool polyvinylique avec 1'addition d'un plastifiant.
Le polyvinyle Butyral s'obtient au cours d'un processus en trois
étapes :
Première étapes : consiste à obtenir le
poly acétate de vinyle a partir de la réaction
d'acétylène avec 1'acide acétique comme suite :
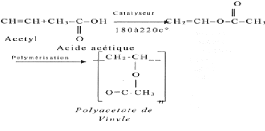
Deuxième étape : Etant que 1'alcool vinylique
monomère n'offre pas de résistance entant que compose libre et
qu'il n'est pas disponible pour la polymérisation, une conversion du
poly acétate de vinyle en alcool polyvinylique se fait par
saponification en présence [11].

La troisième étape : le polyvinyle est obtenu par
acétylisations de l'alcool polyvinylique avec du
butyraldéhyde.

La résine de PVB est une poudre blanche crème
qui se présente sous la forme d'un film et possède une
élasticité suffisante pour son utilisation comme film de verre
feuilleté de sécurité, la compatibilité avec les
plastifiants est déterminée par la part de groupes hydroxyle
libres et 1'humidité. Parmi les plastifiants appropries, alors par
exemple Tester du polyéthylène glycol et de 1'acide adipique.
La nature et la quantité déterminent les
propriétés du film (propriétés mécaniques,
1'adhérence sur le verre) [11].
Les produits obtenus à la fine preuve d'une
élasticité très élevée. Deux exemples de
plastifiants plus courants :
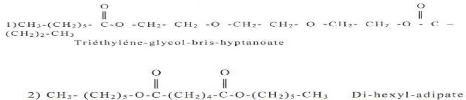
2.1.2- Caractéristiques
physico-chimiques
· Transparence entre les feuilles de verre.
· Indice optique 1.47 proche de celui de verre (1.56).
· Resistance a la traction 200 à 250 Kg/Cm2.
· Allongement a la rupture 300%.
· Dilatation 7.7 X 10 beaucoup plus grandes que celle de
verre (9X 10'6).
· Densité : 1.07.
· Aptitude au collage avec le verre en fonction de
1'état de surface du verre, de la teneur en eau du PVB.
· L'épaisseur existant des feuilles de PVB de 0.38,
0.76, 1.14 ou 1.54.
2.1.3- Trempe thermique
Le renforcement du verre par refroidissement rapide
était connu depuis le XVIIe siècle au moins. On savait
qu'une goutte de verre fondu tombant dans de l'eau peut former une larme solide
de très grande résistance mécanique. La surface en se
figeant forme une coque solide remplie de matière visqueuse, car encore
chaude, qui va se contracter en se refroidissant. Cette contraction produit une
forte compression permanente dans les couches superficielles de la goutte
à froid de sorte qu'il faut une force très grande pour produire
la contrainte d'extension nécessaire au départ d'une fracture.
Notons que la coque en se formant doit s'étirer pour envelopper son
contenu qui est plus chaud.
C'est à cause de cet étirage, qui n'est que
partiellement élastique, que la coque se trouve en compression
lorsqu'elle et son contenu, après refroidissement, sont de nouveau
à la même température. Le même principe s'applique
aux feuilles de verre, industriellement, le refroidissement s'effectue
maintenant par jets d'air (fig. 65).
Tous les autres moyens, tels que l'immersion dans de l'eau ou
dans de l'huile, les pulvérisations ou le contact avec plaques
métalliques, produisaient des casses intempestives ou, au mieux, des
états de surface nécessitant un polissage [6].
Notons enfin qu'à cause du refroidissement rapide la
température fictive du verre près de la surface est plus
élevée que celle de l'intérieur et cette différence
augmente les contraintes produites par la trempe thermique. Cette contribution
serait d'environ 24% dans le cas une trempe industrielle d'un verre
d'épaisseur 6 mm.La trempe d'une feuille de verre à l'aide de
jets d'air est issue du Laboratoire des Glaceries de Saint-Gobain dirigé
par Bernard Long, place des Saussaies, Paris. Comme d'autres, avant et
après lui, il a cherché une trempe par pulvérisation
d'eau. La découverte fut faite lorsque le débit d'air dans les
pulvérisateurs était fort et que l'arrivée d'eau
était restée fermée [6].
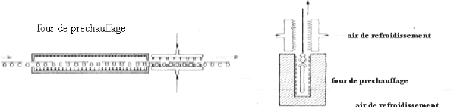
Figure 65. Principes d'installations industrielles de la trempe
thermique de verre plat.
2.1.4) Trempe chimique
Lorsqu'une feuille de verre sodocalcique est immergée
dans un bain de nitrate de potassium fondu, vers 400°C, des ions de sodium
près de la surface sont remplacés par des ions de potassium.
A cause de la plus grande taille de ces derniers, cet
«échange d'ions» donne lieu à une forte compression
superficielle. Typiquement de 400 MPa, la contrainte est environ quatre fois
celle obtenue par trempe thermique.
Il est important de noter que la contrainte diminue par
relaxation visqueuse pendant le traitement de sorte qu'à la surface
même la contrainte est au maximum dès les premiers instants de
l'échange. La durée du traitement sert à obtenir
l'épaisseur nécessaire pour la couche en compression.
Le niveau élevé du renforcement obtenu est
l'avantage principal du procédé. Il y en a deux autres : la
possibilité de renforcer du verre mince (ce qui n'est pas possible par
trempe.
L'inconvénient majeur est le temps de traitement qui se
chiffre en dizaines d'heures. Pour réduire cette durée (et
augmenter les contraintes), on fait appel aux formules particulières.
Le procédé trouve une application dans les vitrages
pour la construction aéronautique où une faible cadence de
production n'est pas un inconvénient rédhibitoire.
Il permet de fournir l'élément assurant la
résistance mécanique d'un pare-brise (résistance
normalisée en particulier relativement aux chocs avec des oiseaux) avec
une économie appréciable de poids [6].
2.1.5) Régime thermique de la trempe
:
Les températures du four approximatives sont
consignées par rapport aux épaisseurs du verre, plus
l'épaisseur augmente plus la température diminue mais le temps de
chauffage augmente de manière 40 sec/mm d'épaisseur.
Exemple : à une épaisseur du verre égale
3,5mrn, la température est de725°C - l'épaisseur
égale 12mm la température est de 710 C (voir la courbe de
régime thermique).
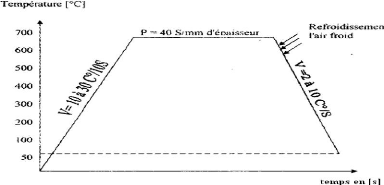
Figure 66.Schéma du régime thermique de la
trempe
3) Applications
Selon la nature des intercalaires, le verre feuilleté
peut être :
· Un bon isolant acoustique ;
· Résistant au vandalisme, à l'effraction ou
aux tirs d'armes à feu, voire aux ouragans ou aux explosions ;
· Utilisé pour protéger les personnes de
risques accidentels (pare-brise automobile, protection contre la chute dans le
vide en cas de bris du vitrage, etc.);
· Utilisé dans des parois pare-flammes ou coupe-feu
jusqu'à deux heures (verre feuilleté à intercalaire
intumescent);
· Décoratif (film intercalaire de couleur, à
motif, etc.);
· Opacifiant (film intercalaire à cristaux
liquides);
· Photovoltaïque (intégration de cellules
photovoltaïques dans le film intercalaire);
4) Types de verre feuilletéLes verres feuilletés se
chassent en quatre types différents :
1. Les verres anti-effraction.
2. Les verres de sécurité avec alarme.
3. Les verres pare-balles.
4. Les verres à haute résistance.
4.1) Les verres anti-effraction : >
Composition
Le verre de sécurité (anti-effraction) est
composé de deux ou plusieurs feuilles de verre reliées entre elle
par des feuilles de polyvinyle. Le nombre de feuilles peut atteindre jusqu'a 18
feuilles. Le type le plus mince étant : deux float de 2mm + Feuille de
PVB 0.38mm.
> Protection
On parle généralement de sécurité
simple lorsqu'on cherche à protéger les personnes centre les
blessures graves en cas de heurt accidentel centre un vitrage.
Dans le cas de sécurité simple, le verre
feuillète anti-effraction doit résister aux chocs d'un personne
tombant centre un vitrage, ou a une effraction simple, sans utilisation d'objet
lourd.
Si le verre se fissure, le PVB va maintenir les morceaux de verre
ensemble et empêcher leur dangereuse dispersion.
Lorsque les vitrages sont exposes au vide, il doit rester en
place et assurer une protection de chute au travers de ceux-ci.
Tableau8 : La résistance à l'impacte des verres
feuilletés.
classe
|
Nombre d'impacte avec marteau et hache
|
Energie accumulée
(joule)
|
Epaisseur totale (mm)
|
Poids Kg/m2
|
P6A
|
49
|
14850
|
14
|
30
|
P7A
|
64
|
17400
|
22
|
50
|
P7B
|
65
|
20950
|
23
|
50
|
P7B
|
72
|
25200
|
27
|
60
|
> Propriétés
mécaniques
Le verre Anti-effraction résiste à la destruction
d'un vitrage par le moyen d'un marteau et d'une hache réalisant une
ouverture de 400X400mm.

> Types d'utilisation :
Le verre feuilleté double ou triple de type
anti-effraction s'utilise pour :
· Les verres de fenêtres composés avec un
verre isolant.
· Séparation de locaux.
· Cage d'escaliers.
· Verre de balcon.
· Vitrage en toiture.
· Vitrines.
· Protection de locaux contre 1'émeute, 1'effraction
ou le vandalisme.
· Protection des biens.
· Protection centre l'explosion.
Tableau 9 : exemple de la composition de quelques verres
feuilleté double et triple, anti-effraction.
Nbr de verre
|
Epaisseur des verres
|
Nbr de PVB
|
Epaisseur de PVB
|
Epaisseur totale
|
Poids Kg/m2
|
Dimension maximum (cm)
|
2
|
2-2
|
1
|
0.38
|
4.3
|
10.4
|
120*280
|
2
|
3-3
|
1
|
0.38
|
6.3
|
15.5
|
250*600
|
2
|
4-4
|
1
|
0.76
|
9.7
|
21.0
|
250*600
|
2
|
5-5
|
1
|
1.52
|
11.5
|
26.7
|
250*600
|
2
|
6-6
|
1
|
2.28
|
14.3
|
32.5
|
250*600
|
2
|
6-6
|
1
|
4.56
|
16.5
|
34.7
|
250*600
|
3
|
3-3-3
|
2
|
0.76
|
10.5
|
24.0
|
250*600
|
3
|
4-4-4
|
2
|
0.76
|
13.5
|
31.5
|
250*600
|
3
|
5-5-5
|
2
|
1.52
|
18.5
|
40.7
|
250*600
|
3
|
5-5-5
|
2
|
2.28
|
19.5
|
42.0
|
250*600
|
3
|
6-6-6
|
2
|
3.80
|
26.0
|
53.0
|
250*600
|
3
|
6-6-6
|
2
|
4.56
|
28.0
|
56
|
250*600
|
|
4.2) Les verres de sécurité avec fil
d'alarme
Ce type du verre constitue de deux ou plusieurs feuilles de
verre généralement trempées, reliées par des
feuilles de polyvinyle Butyral avec insertion d'un réseau
électrique de fils de cuivre extrêmement minces et a peine
visibles, de 0.08mm de diamètre. Ce réseau est constitue d'un
trame quadrillée ou de fils longitudinaux distant antre eux de 20 a
60mm. En cas d'effraction le fil conducteur se sectionne et déclenche
automatiquement le dispositif d'alarme place a 1'endroit du verre ou relie au
poste de police.
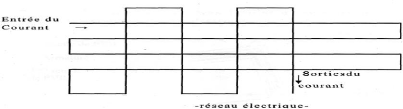
Figure 67. réseau electrique intercalé entre les
feuille de verre. > Types d'utilisation
· Devantures d'établissement bancaires.
· Bijouteries, horlogeries.
· Salle de musée ; Collection d'objets d'art.
· Salles d'ordinateurs.
Les verres feuilletés avec insertion de fils d'alarme
portent une grande résistance et signalisation en cas d'effraction.
Les verres de sécurité avec film d'alarme sont
exécutes selon les types de verres feuillètes et triple.
Exemple 1 : de 1'assemblage de deux feuilles du verre et une
feuille de PVB avec insertion de réseau électrique
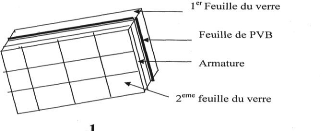
Figure 68. 1'assemblage de deux feuilles du verre et une feuille
de PVB avec insertion de réseau électrique
Exemple 2 : L'assemblage de deux feuilles du verre et deux
feuilles de PVB avec insertion de réseau électrique.
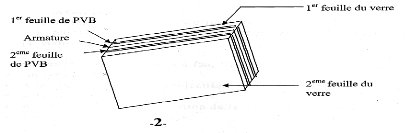
Figure 69. L'assemblage de deux feuilles du verre et deux
feuilles de PVB avec insertion de réseau électrique.
4.3) Les verres pare-balles (anti-balle) :
Composition :
Les verres feuilleté anti-balle est un produit compose
d'au moins trois couches de verre assemblées par plusieurs couches de
matière synthétique. Lors de la fabrication, les couches de
matière synthétique et les différentes couches de verre
sont soumises à des pressions et des températures telles que ces
couches adhérent d'une façon définitive.
> Protection
Le vitrage pare balles doivent établir une protection
efficace et sécurisante entre un agresseur arme et les personnes qu'il
menace. Us doivent résister a un nombre détermine de tirs de
balles.
Le verre anti-balle ne devrait pas être utilise comme
un verre anti-effraction : il a été con9u pour résister a
des d'impacts de projectiles a grande vitesse et non a des impacts prolonges
faits a 1'aide d'objets lourde (marteau, pierre, brique,.. .. etc.). Le verre
anti-balle est un verre de sécurité multi-feuilleté,
fabrique pour résister à la pénétration des
projectiles d'arme à feu. Lors de Pimpant, I' onde de choc produit par
le projectile fait en sorte que des éclats se détachent du cote
protège. La conception du vitrage blinde fait en sorte que
1'énergie du projectile engendre un nombre très minime de
particules. Les éléments à prendre en considération
pour sélectionner le type de verre sont :
> Le taux de risque propre à 1'établissement ou
au local à protéger, lie :
· Au type de bâtiment (établissements
financiers... etc.).
· A la nature de 1'activité (ambassade,
véhicule blinde).
· A la présence de personnel.
· A la rapidité et aux moyens d'intervention.
· A la puissance des armes a feu centre les quelles ou
souhaiterait se prémunir.
> La résistance aux tirs d'armes a feu, liée
:
· Au type d'armes.
· A la vitesse initiale du projectile.
· A la distance de tir.
· A la forme et a la composition de la balle et à la
température du vitrage.
Les verres pare-balles sont divisés en deux
catégories :
1- Les verres résistants aux armes de poing de
faible puissance : 2- Tableau 10 : armes de faible puissance [11].
Epaisseurs des verres (mm)
|
N° de feuille de PVB
|
Epaisseur de PVB
|
Epaisseur totale (mm)
|
Dimension max
|
6-6-6-6
|
3
|
0.76
|
26
|
254x449
|
4-12-4-4
|
3
|
0.76
|
28
|
254x449
|
6-6-6-6-6
|
4
|
0.76
|
32
|
254x449
|
8-8-6-8
|
3
|
1.52
|
33
|
254x449
|
2-Les résistants à toutes armes de poing
Tableau 11: toutes armes de poing [11]
Epaisseur de verre (mm)
|
N° de PVB
|
Epaisseur e PVB
|
Epaisseur totale (mm)
|
Dimension max
|
6-15-5-4
|
3
|
0.76
|
32
|
254x449
|
5-15-5-4-4
|
4
|
0.76
|
36
|
254x449
|
> Avantage du produit : Confort acoustique
:
Par sa composition, le verre feuilleté anti-balle augmente
la valeur acoustique par rapport au verre ordinaire de même
épaisseur. Confort thermique.
En simple et évidemment en double vitrage le verre
feuilleté anti-balle augmente le confort thermique.
Confort visuel.
En faisant usage d'un film colore au lieu d'un film clair, le
confort visuel est augmente.
Protection contre les rayons ultraviolets :
Le film de matière synthétique empêche
pratiquement la pénétration des rayons ultraviolets et
protège les objets exposes de la décoloration.
-Dimensions maximum de fabrication.
2500X3500mm avec un poids de 205Kg maximum par verre.
4.4) Les verres à haute résistance
:
Les verres feuillètes a haute résistance sont un
assemblage de deux verres trempes chimiquement et trois feuilles (deux feuilles
de polyvinyle butyrate et. D'une feuille de polycarbonate). Le verre a trempe
chimiquement offre une résistance mécanique d'environ cinq fois
supérieure a celle du flot et résiste bien aux chocs mous, a
1'abrasion, au transpercement et a la coupe au moyen de dament [11].
Ce type du verre résiste milieu a 1'abrasion et produit
chimique ainsi que Ce type du verre est considère comme un verre
anti-feu, qui résiste généralement environ de 700c°
pendant 4 heures. Ces avantages sont donnes par le film de polycarbonate qui
possède des propriétés remarquables.
-Dimensions maximales : 300X195Cm.
> L'utilisation :
v' Les ateliers de fondre.
v' Les pistes d'aéroport et tout Les endroit ou il ya le
risque de sante.
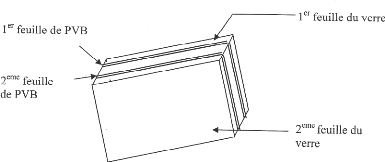
Figure 70.verre feuilleté à haute
résistance [11].
1- Le double vitrage
1-1 Définition :
Un double vitrage est une paroi vitrée
constituée de deux vitres séparées par une
épaisseur d'air immobile, dite « lame d'air ».
L'intérêt du double vitrage est de permettre une
amélioration thermique et phonique, la lame d'air constituant un bon
isolant, bien meilleur que le verre luimême. Le double vitrage permet
ainsi de réduire l'« effet de paroi froide » d'où une
diminution de la condensation en hiver et une diminution des pertes de chaleur
soit un gain de 10 % de la consommation en chauffage.
En pratique la lame d'air est parfois constituée de gaz
inertes (argon, krypton) afin d'améliorer l'isolation. Il existe aussi
des triples vitrages, conçus pour apporter une isolation encore
meilleure. Le triple vitrage, pour être intéressant,
nécessite une attention particulière sur l'isolation au niveau
des joints de menuiserie, car c'est en général par eux qu'a lieu
le gros des déperditions de chaleur. Le triple vitrage est par exemple
utilisé sur les trains à grande vitesse.
Un double vitrage standard a un indice uw d'environ 2,9
W/m2K, un double vitrage haute performance peut descendre
jusqu'à 1,1 W/m2K.
Les épaisseurs sont souvent désignées de
la façon suivante : A/B/C. Avec A, B, et C, les épaisseurs en
millimètres des éléments (vitre extérieure, lame
d'air, vitre intérieure). Des doubles vitrages courants sont en 4/16/4.
Les deux vitres ont souvent la même épaisseur. Sinon, on parle de
double vitrage asymétrique. Le double vitrage asymétrique permet
une meilleure isolation phonique car les fréquences de résonnance
des deux vitres sont différentes. En général, la vitre
extérieure est souvent la plus épaisse : 10/10/4. Cependant, le
sens n'a pas d'effet sur les performances d'affaiblissement acoustique. Seul
lors de l'utilisation d'un vitrage feuilleté, le sens de mise en place
sera conditionné par les contraintes de protection des personnes en
fonction de leur situation vis-à-vis le vitrage.
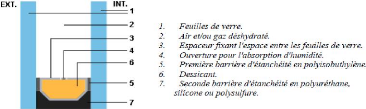
Figure 71 .Composition d'un double vitrage isolant
Le dessicatif introduit dans l'espaceurs est destiné
à assécher le gaz emprisonné à la fermeture du
vitrage et à absorber la vapeur d'eau éventuelle. Le bon
fonctionnement des barrières d'étanchéité et du
dessicatif conditionne la durée de vie du vitrage.
1-2 Les modes de transmission de chaleur
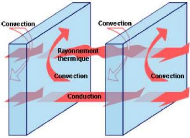
L'intérêt du dispositif est de
bénéficier du pouvoir isolant apporté par la lame d'air ou
de gaz, et de faire baisser de la sorte le coefficient de transmission
thermique U de l'ensemble du vitrage. Elle se fait par conduction et
rayonnement dans le verre. La présence de la lame d'air permet de
limiter les pertes de chaleur par conduction, la conductivité thermique
de l'air (0.025 W/mK (à 10°C)) étant nettement
inférieure à celle du verre (1 W/mK).
Figure72 .mode de transfert de chaleur à travers
un double vitrage.
1-3 Caractéristiques
énergétiques
Lorsque l'énergie solaire est interceptée par
une paroi, une partie est réfléchie vers l'extérieur, une
partie est absorbée par le matériau, une partie est transmise
à l'intérieur. La transmission solaire du double vitrage est
légèrement plus faible que celle du vitrage simple car la chaleur
qui traverse le vitrage est absorbée et réfléchie par deux
couches et non une seule.
Les schémas suivants donnent les coefficients de
transmission thermique U et le facteur solaire FS d'un double vitrage et d'un
simple vitrage :
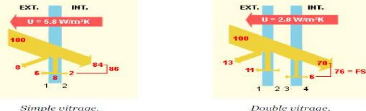
Figure73 .les coefficients de transmission thermique U et le
facteur solaire FS d'un double vitrage et d'un simple vitrage
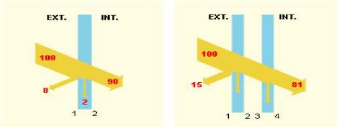
1-4 Caractéristique lumineuse
Le double vitrage assure un aspect neutre en réflexion
et une grande transparence. Il est caractérisé par un coefficient
de transmission lumineuse élevé mais néanmoins
inférieur à celui d'un simple vitrage.

Figure74. Coefficient de transmission lumineuse d'un simple et
double vitrage.
1-5 Caractéristique acoustique
Curieusement, l'isolation acoustique que procure le double
vitrage dans les basses (bruit de trafic lent) et moyennes fréquences
est légèrement inférieure à celle d'un simple
vitrage de la même épaisseur.
Il est caractérisé par un indice
pondéré d'affaiblissement acoustique :
Tableau 12 : indice pondéré d'affaiblissement
acoustique d'un double vitrage.
Rw
|
Rw + C
|
Rw + Ctr
|
30
|
29
|
26
|
Certaines dispositions peuvent être prises de
façon à assurer des performances acoustiques suffisantes. On se
référera aux vitrages acoustiques. A partir du double vitrage des
améliorations sont possibles afin d'augmenter encore les performances
énergétiques et solaires du vitrage : le vitrage basse
émissivité, absorbant, réfléchissant...
2- Le double vitrage "à basse
émissivité"
2-1 Principe
Ce vitrage est aussi appelé "vitrage à haut
rendement" ou "vitrage super isolant". En anglais, il se nomme vitrage "low-E"
et en France, on l'appelle "Vitrage à Isolation Renforcée" (VIR).
L'objectif est d'augmenter le pouvoir isolant du double vitrage, c.à.d.
de diminuer son coefficient de transmission thermique U (anciennement "k").
Vous avez dit : "émissivité" ?
Quand de la chaleur ou de l'énergie solaire est
absorbée par un vitrage, elle est réémise par le vitrage,
soit par convection d'air le long de sa surface, soit par radiation de la
surface du vitrage vers les autres surfaces plus froides. Par
conséquent, la réduction de la chaleur émise par les
fenêtres sous forme de radiation peut améliorer fortement ses
propriétés isolantes.
La capacité d'un matériau à
émettre de la chaleur de manière radiative est appelée son
émissivité. Ce coefficient d'émissivité varie en
fonction de la longueur d'onde du signal émis. Les fenêtres, ainsi
que les matériaux que l'on trouve à l'intérieur d'un
bâtiment, émettent typiquement des radiations sous forme
d'infrarouges de très grande longueur d'onde. A savoir enfin que pour
une longueur d'onde donnée, le coefficient d'absorption d'un
matériau est égal au coefficient d'émissivité. Les
vitrages standards ont une émissivité de 0.84 sur
l'entièreté du spectre. Cela signifie qu'ils émettent 84 %
de l'énergie possible pour un objet à cette
température.
Cela signifie également qu'en ce qui concerne les
rayonnements à grande longueur d'onde qui frappent la surface du verre,
84 % est absorbé et seulement 16 % est réfléchi.
Par comparaison, les couches basse-émissivité
ont un coefficient d'émissivité de 0.04. Les vitrages sur
lesquels on a déposé de telles couches émettront seulement
4 % de l'énergie possible à cette température, donc
absorberont seulement 4 % du rayonnement de grande longueur d'onde qui les
atteint. Autrement dit, ils réfléchiront 96 % du rayonnement
infrarouge de grande longueur d'onde. Application
Le rayonnement calorifique des objets terrestres est
émis à une longueur d'onde plus élevée que ceux qui
composent le spectre solaire. D'où l'astuce : il est tout à fait
possible de laisser pénétrer l'énergie solaire (à
courte longueur d'onde) à travers un vitrage tout en empêchant la
chaleur (à grande longueur d'onde) de quitter ce local !
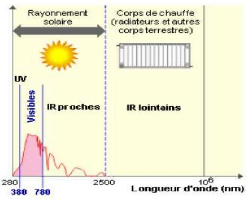
Figure75. Ondes électromagnétiques correspondant
au rayonnement solaire et au rayonnement des corps terrestres.
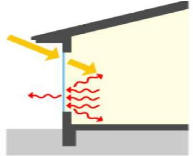
Figure76 .Principe de fonctionnement d'un double vitrage
à basse émissivité.
La couche "basse émissivité" est, en
général, une couche métallique, en argent par exemple,
déposée sous vide et qui doit être placée à
l'intérieur du double vitrage vu sa fragilité. Elle bloquera une
partie du transfert de chaleur par rayonnement, diminuant ainsi le flux total
de chaleur au travers de la fenêtre.
2-2 Importance de la position de la couche basse
émissivitéLa position de la couche basse émissivité
dans un double vitrage n'affecte en rien le facteur
U (ou k) de celui-ci. Donc, en ce qui concerne les pertes de
chaleur par transmission, il n'y a absolument aucune différence que la
couche basse émissivité soit placée en position 2 ou en
position
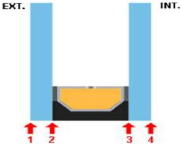
Figure77. Numérotation des faces d'un double vitrage.
La surface d'un vitrage, dans un double ou un triple vitrage,
est référencée par un nombre, commençant par le
numéro 1 pour la surface extérieure du vitrage extérieur
vers la surface intérieure du vitrage intérieur. La surface
intérieure d'un double vitrage porte donc le numéro 4.
Par contre, le facteur solaire FS du vitrage est
influencé par la position de la couche. En effet, en plus de sa
capacité à inhiber les transferts d'infrarouges à grande
longueur d'onde, une couche basse émissivité absorbe aussi une
certaine quantité de l'énergie solaire incidente. Cette
énergie absorbée est transformée en chaleur, provoquant
ainsi un échauffement du vitrage. Si l'on cherche à laisser
passer la chaleur solaire (FS élevé), la couche basse
émissivité sera placée sur le verre intérieur du
double vitrage (en face 3). La chaleur absorbée par la vitre sera
réémise vers l'intérieur.
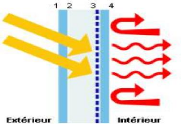
Figure78. Double vitrage avec une couche basse
émissivité déposée sur la vitre interne
Si l'on cherche au contraire à diminuer la chaleur
solaire entrante (FS faible), la couche basse émissivité sera
placée en face 2, la chaleur absorbée par le vitrage étant
alors essentiellement réémise vers l'extérieur. Dans ce
cas, on peut adjoindre une couche réfléchissante à la
couche basse émissivité pour diminuer encore FS.
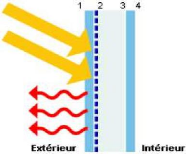
Figure79 .Double vitrage avec couche bas emissivité
deposée sur la vitre extene Et si on pose le châssis
à l'envers ?
Lorsque les châssis et les vitrages arrivent
séparément sur un chantier, on veillera à ce que la couche
basse émissivité se retrouve bien à la position
souhaitée pour tous les châssis du bâtiment
(généralement en face 3 dans le domestique et en face 2 dans le
tertiaire avec apports internes).
Si l'autocollant est absent, il est possible de repérer
la position de la couche au moyen de la flamme d'un briquet. En effet, 4 images
de la flamme seront réfléchies par les 4 faces. La couche basse
émissivité génèrera un reflet bleuté, les
autres étant plus orangées
2-3 Caractéristiques énergétiques
et lumineuses
Le double vitrage basse émissivité est
caractérisé par un faible coefficient de transmission thermique
U, variant de 1,1 à 1,9 W/m2.K selon le mode d'application de
la couche métallique ainsi que la nature du gaz présent entre les
feuilles de verres. Il existe une multitude de vitrages sur le marché.
Des combinaisons multiples sont proposées entre le facteur solaire FS et
le facteur de transmission lumineuse FL. Il est possible de trouver un vitrage
pour lequel la présence de la couche métallique ne provoque
qu'une très légère baisse des gains solaires et de la
transmission lumineuse par rapport à un double vitrage classique.
Autrement dit, la couche basse émissivité "ne se voit pas".
Tableau 13 : caractéristique énergétiques et
lumineuse des doubles vitrages.
Type de vitrage
|
Facteurs énergétiques
|
Facteur lumineux
|
U(K) W/m2K
|
FS %
|
TL %
|
Double vitrage ordinaire
|
2.8
|
76
|
81
|
Double vitrage à basse émissivité
|
1.3
|
60...75
|
74...80
|
2-4 Combinaison des couches basse
émissivité et de couches permettant le contrôle solaire
La couche à basse émissivité peut être
manipulée de manière à transmettre le rayonnement ayant
certaines longueurs d'onde et à réfléchir le rayonnement
ayant d'autres longueurs d'ondes.
On peut ainsi combiner les couches à basse
émissivité et les couches de contrôle solaire. Il s'agit
alors de couches déposées sous vide, combinant ces deux effets et
placées en position 2.
Les premiers vitrages à basse émissivité
ont été conçus de manière à maximiser les
gains solaires en hiver. Ils devraient donc avoir un grand facteur solaire, un
coefficient de transmission lumineuse important ainsi qu'un faible coefficient
de transmission thermique U (anciennement "k"). Ils devaient donc transmettre
les longueurs d'ondes du rayonnement solaire (rayonnements visibles et
infrarouges proches) mais arrêter les infrarouges lointains
(correspondant au rayonnement des corps terrestres). On appelle ces vitrages
"vitrages à basse émissivité et haute transmission".
Actuellement dans les bâtiments du secteur tertiaire, on
demande de plus en plus de minimiser les gains solaires tout en conservant une
bonne transmission lumineuse et une bonne isolation.
Ces vitrages doivent donc transmettre le rayonnement visible
tout en arrêtant le rayonnement solaire correspondant aux infrarouges
proches et le rayonnement des corps terrestres (les infrarouges lointains). Ces
vitrages sont appelés "vitrages à basse émissivité
sélectifs".
Exemple. On trouve actuellement des vitrages "haut rendement"
avec un facteur solaire limité à 40 % tout en atteignant une
transmission lumineuse de 70 %. Pour diminuer encore le facteur solaire, on
peut enfin placer une couche basse émissivité sur un vitrage
teinté foncé ou augmenter le coefficient de réflexion des
rayons lumineux de la couche elle-même, créant ainsi un produit
ayant les propriétés isolantes d'un vitrage "basse
émissivité", conjugué un rejet des gains solaires, perdant
de facto une certaine qualité de transmission lumineuse. Ces vitrages
sont appelés "vitrages à basse émissivité
sélectifs et à basse transmission".
Figure80 .Coefficient de transmission lumineuse de quelques
verres
1. Vitrage clair
2. Vitrage basse émissivité et haute
transmission
3. Vitrage basse émissivité spectralement
sélectif
4. Vitrage basse émissivité spectralement
sélectif et à basse transmission.
|
|
3-Le triple vitrage
Le vitrage est formé par trois feuilles de verre
séparant deux espaces d'air.
3-1 Caractéristiques énergétiques
et lumineuses
L'isolation thermique que procure un triple vitrage est
meilleure que celle d'un double vitrage. Le coefficient de transmission
thermique U d'un tel vitrage est de 1,9 W/m2K pour un triple vitrage
ordinaire. Par contre, les gains solaires et la transmission lumineuse sont
diminués par la présence du troisième verre. Le facteur
solaire (FS) est généralement de 68 % et le facteur de
transmission lumineuse (TL) sera de 74 %. Une variante Le triple vitrage est
rarement appliquée, car sa forte épaisseur et son poids
élevé ne s'adaptent pas aux menuiseries classiques.
Une variante consiste en un double vitrage avec un ou plusieurs
films plastiques tendus dans l'espace d'air, de façon à avoir
plusieurs lames d'air en série sans augmenter le poids du vitrage.
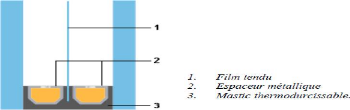
Figure81. Assemblage d'un triple vitrage.
4-Le vitrage isolant acoustique
Si l'on observe le spectre d'isolation acoustique d'un double
vitrage, on remarque que l'isolation acoustique que procure un double vitrage
est relativement mauvaise à la fréquence critique des feuilles de
verres (3 200 Hertz) et dans les basses et moyennes fréquences (bruit de
trafic lent).
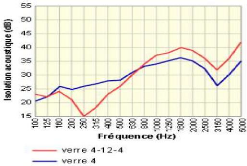
Figure82. Isolation acoustique d'un verre ordinaire et d'un
double vitrage
Ce deuxième puits de résonance s'explique par le
fait que le double vitrage se comporte comme un système acoustique du
type MASSE/RESSORT/MASSE. La lame d'air jouant le rôle de ressort, son
épaisseur est généralement trop faible pour créer
un ressort suffisamment souple et le système fait entrer le verre en
résonance. Pourtant l'acoustique s'améliore lors d'un
remplacement d'un châssis !
Des propos ci-dessus, on pourrait déduire que le
remplacement, en rénovation, du simple vitrage par du double vitrage
n'est pas intéressant du point de vue acoustique... Cette supposition
est cependant erronée car le remplacement du vitrage s'accompagne, en
général, du remplacement du châssis qui offre une meilleure
étanchéité à l'air et donc à une meilleure
isolation acoustique que l'ancien châssis; ce qui mène à
une amélioration de l'isolation acoustique de l'ensemble vitrage +
châssis. Certaines dispositions permettent aussi d'améliorer
l'isolation acoustique d'un double vitrage :
1' Les doubles vitrages dissymétriques
Chaque plaque d'un matériau d'une épaisseur
donnée a une fréquence critique pour laquelle elle se met
à vibrer plus facilement. A cette fréquence, le bruit se transmet
beaucoup mieux.
Le principe des vitrages dissymétriques est le suivant
:
On utilise au sein d'un même vitrage des verres
d'épaisseur suffisamment différente de sorte que chacun d'eux
puisse masquer les faiblesses de l'autre lorsqu'il atteint sa fréquence
critique.
La figure suivante compare les spectres d'isolation acoustique
d'un double vitrage classique et d'un double vitrage dissymétrique.
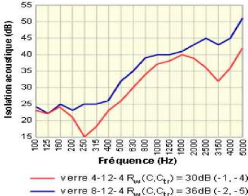
Figure83 .Isolation acoustique des doubles vitrages 4/12/4 et
8/12/4.
Tableau14 : performances acoustiques des doubles vitrages pour
différents types d'assemblages.
Composition (mm)
|
Rw + C (db)
|
Rw + Ctr (db)
|
6-15-4
|
33
|
31
|
8-12-5
|
35
|
32
|
8-20-5
|
35
|
32
|
10-12-6
|
36
|
34
|
10-15-6
|
37
|
34
|
10-12-8
|
36
|
34
|
1' Les vitrages avec gaz isolant
On remplace l'air d'un double vitrage par un gaz isolant
adapté (l'hexafluorure de carbone : SF6). Cela permet de réaliser
des gains appréciables dans les hautes et moyennes fréquences
(bruits de trafic rapide), mais les performances s'avèrent
défavorables dans les basses fréquences (bruit de trafic urbain
(315 Hertz)). La figure suivante comparant les spectres d'isolation acoustique
d'un double vitrage classique et d'un double vitrage avec gaz isolant.
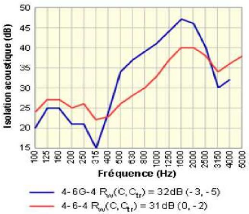
Figure84. Isolation acoustique d'un double vitrage classique et
d'un double vitrage avec gaz isolant.
Ce gaz présente le désavantage de diminuer
l'isolation thermique des doubles vitrages et cause des problèmes
à l'environnement. Les doubles vitrages avec SF6 sont donc à
déconseiller et sont, de toute façon, appelés à
disparaître.
v' Les verres feuilletés acoustiques
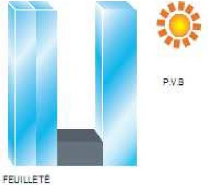
.
Figure 85. Association d'un verre feuilleté dans un
double vitrage.
L'utilisation d'un vitrage feuilleté dans le double
vitrage améliore d'avantages les performances de ce dernier, non
seulement au niveau de pouvoir acoustique mais également il assure une
bonne protection anti-vandalisme
Tableau 15: isolation acoustique de quelques vitrages
spéciaux comparée à celle d'un vitrage ordinaire.
Type de vitrage
|
Rw
|
Rw + C
|
Rw +Ctr
|
Vitrage double ordinaire (4/15 air/4)
|
30
|
29
|
26
|
Vitrage thermique dissymétrique (8/12 argon/5)
|
38
|
36
|
32
|
Vitrage thermique feuilleté (6/15air/55.2pvb)
|
38
|
37
|
35
|
Vitrage feuilleté (8/12air/44.2 pvb)
|
41
|
40
|
37
|
Vitrage avec pbv amélioré(12/20air/44.2 pvb)
|
44
|
43
|
40
|
Vitrage avec résine coulée
|
49
|
47
|
42
|
Conclusion
Le verre n'est plus le matériau fragile posé dans
de petites ouvertures aménagées dans une paroi afin de laisser
pénétrer un peu de lumière naturelle dans les
intérieurs.
Dans l'architecture actuelle, le verre est devenu
lui-même paroi, voire façade. Il doit donc en assumer toutes les
fonctions telles que la protection contre le froid, la chaleur, l'eau, le vent,
l'excès de lumière, parfois la transparence, le bruit, le feu,
les rayonnements nocifs, le vandalisme, l'effraction, etc. .... et ce de
manière économique, durable et esthétique.
Le verre est devenu un matériau d'architecture complet aux
fonctions sans cesse plus nombreuses, plus attractives et plus performantes
autorisant les réalisations les plus audacieuses.
Le développement de ce travail sera le fruit d'une
collaboration entre universitaires et industriels pour asseoir une politique de
recherche à l'échelle industrielle et universitaire, de cette
façon nous pourrions contribuer à l'extension de notre industrie
verrière qui recense un manque flagrant pour ce type de matériau
de construction, et acquérir une performance de développement
industriel.
L'ampleur de ce travail nous pouvons approfondir et mettre en
application nos connaissances scientifiques et technologiques pour
développer plus spécialement certains aspects des verres
spéciaux tels que :
1' Relations structure- composition- propriétés des
matériaux.
v' Mise en ouvre des matériaux, formulation,
élaboration. 1' Comportement en service.
1' Stratégie de choix d'un matériau pour une
application donnée. 1' Acquérir une performance de
développement industriel.
v' Développement d'une politique de recyclage du verre
(gain d'énergie, matières premières et
écologie).
Notre objectif aussi est de sensibiliser les industriels ayant
choisi l'option des matériaux pour l'importance de développement
de l'industrie verrière et de satisfaire le marché national vis
à vis des exigences auxquelles les produits obtenus de devraient se
soumettre.
Aujourd'hui, dans un monde de compétition industrielle,
où tout est plus difficile, le succès et la rentabilité
d'un produit passent par l'amélioration constante des techniques de
fabrication en termes de productivité, de qualité, de
consommation d'énergie, et de réduction de la pollution.
Sommaire
Chapitre I Généralités sur le
verre
1Introduction ... ... ...... ... ...... ...
...............1
2- Généralités sur le verre 2
2.1- définition du verre : 2
2.2- Structure et vitrification : 2
2.2.1- Critère de GOLDSCHMIDT : 2
2.2.2- Règles de ZACHARIASEN : 3
2.2.3- La transition vitreuse 4
2.3- Les propriétés du verre : 5
2.3.1- Propriétés rhéologiques 5
2.3.2- Propriétés électriques 7
2.3.3- Propriétés mécaniques 7
Chapitre II Description de l'unité MFG
Description de l'unité MFG : 23
2-Les différents ateliers de la ligne : 23
2-1- Atelier de composition : 23
2-2- Atelier de fusion : 25
2-3- Bain d'étain : 27
2-4- Etenderie : 28
2-5- La découpe : 29
2-6- Atelier de contrôle de qualité : 30
2-7- Installations annexes : 30
Chapitre III Les verres à couches
1. Les verres à couches 31
1.1 - Introduction 31
1.2 - Les fonctions d'un verre à couches 31
1.2.1-Les fonctions optiques 31
1.4.3.2- Principe de canon a électron 37
.4.4- Le dépôt de couche pyrolytique 38
1.4.4.1-Sur substrat chaud : 38
1.4.4.1.1) la pyrolyse en phase liquide : 38
1.4.4.1.2) la pyrolyse en phase solide : 38
1.4.4.1.3) la pyrolyse en phase gazeuse : 38
1.4.4.2) Sur substrat froid. 39
1.4.5) Procédé `sol-gel' : 39
1.5- Tests, normalisation des verres à couches pour
l'architecture 39
2 - Classification des vitrages pour le bâtiment 39
2.1 - Le rôle des couches 39
2.2 - La classification des verres à couches dans le
bâtiment 41
2.3 - La numérotation des faces d'un vitrage simple ou
multiple 41
3 - Traitement de surface hydrophobe 42
3.1 - Surface hydrophobe : 42
3.2 - Réalisation de surfaces de verre hydrophobes 43
3.3 - Aspects théoriques 44
4 - Dépôt transparent conducteur de
l'électricité 45
4.1 - Nature du dépôt : ITO (oxyde d'étain et
d'indium) 45
4.2 - Elaboration du dépôt ITO 45
4.3 - Utilisations 46
5 - Verres à couches pour protection contre les incendies
46
5.1 - Définition 46
5.2 - Structure et fonctionnement d'un verre à couches
intumescentes 46
5.3 - Les verres à couches réfléchissantes
47
5.4 - Les classes et normes pour vitrages de protection
anti-incendie 47
5.3 - Les verres à couches pour l'isolation thermique
renforcée et le contrôle solaire 48
5.3.1-Le verre et le rayonnement solaire 48
5.3.1.1- Introduction et définitions 48
1.1.2 - Les vitrages à faible émissivité
(appelés aussi peu émissifs) 49
1.1.3 - Mode de dépôt et performance 50
1.1.4 - Les produits industriels 50
1.1.5 - Les économies d'énergie 51
1.1.6 - La transmission spectrale 52
- Aspects théoriques 53
- Notions sur les transferts thermiques 53
1.2.2 - Le problème du transfert de chaleur à
travers un vitrage 53
2 - Les vitrages électrochromes 54
2.1 - Introduction 54
2.2 - Les vitrages `obturateurs' à cristaux liquides 54
2.3 - Le vitrage électrochrome `assombrissant' 56
2.3.1- Description du fonctionnement 56
2.3.2- Applications 57
2.3.3- Réalisation et structure du vitrage assombrissant
57
3- Les vitrages thermochromes : vers un contrôle solaire
`intelligent' 58
3.1 - Introduction : la thermochromie 58
3.2 - Les dépôts et couches thermochromes pour
vitrages 58
3.3 - Autres variétés de vitrages thermochromes
60
4 - Modification des propriétés optiques du verre
par dépôts multicouches diélectriques (transparents) 61
4.1 - Introduction 61
4.2 - Applications pratiques des traitements `anti-reflets' 61
4.2.1 - Dans le domaine du bâtiment et de l'architecture
61
4.2.2 - Dans le domaine de l'optique 62
4.2.3 - Dans le domaine des énergies renouvelables 62
4.3 - Applications pratiques des traitements
`semi-réfléchissants' et `réfléchissants' 62
4.4 - Applications pratiques des traitements
réfléchissants sélectifs 62
4.5 - Aspects théoriques : le coefficient de
réflexion d'une surface de verre 63
4.6 - Aspects théoriques : les dépôts simples
`monocouches' 64
4.6.1 - Traitement antireflet 65
4.6.2 - Traitement réfléchissant 66
4.7 - Les dépôts `multicouches' 67
4.7.1 - Traitement anti-reflets 67
4.7.2 - Couches à fort coefficient de réflexion :
67
4.7.3 - Traitement pour réflexion sélective 68
5 - Le vitrage autonettoyant 70
5.1 - Introduction 70
5.2 - Principe d'un vitrage autonettoyant 70
5.3 - Caractéristiques et techniques de dépôt
du film autonettoyant TiO2 70
6-Le verre émaillé et le verre
sérigraphié 73
6.1-Définition 73
6.2-L'émaillage : 73
6.2.1-Définition d'un émail : 73
6.2.2-Techniques d'émaillage : 73
7-la sérigraphie : 74
8-Caractérisation des couches minces 75
8.1-Mesure de I' épaisseur : 75
8.3-Morphologie d'une couche mince 76
8.4-Analyses des contraintes 76
8.5-Adhérences 76
8.6- compositions 76
Chapitre IV Le verre feuilleté
1- Généralités sur Le verre
feuilleté 77
1-1 Historique : 77
1.2- Définition 77
Figure 63. Composition d'un verre feuilleté ordinaire
77
2- Principe de fabrication du verre feuilleté 78
2.1- Films intercalaires 78
2.1.1- Fabrication de résine de polyvinyle Butyral :
79
2.1.3- Trempe thermique 81
2.1.4) Trempe chimique 82
2.1.5) Régime thermique de la trempe : 82
3) Applications 83
4) Types de verre feuilleté 83
4.1) Les verres anti-effraction : 84
4.2) Les verres de sécurité avec fil d'alarme 85
4.3) Les verres pare-balles (anti-balle) : 87
4.4) Les verres à haute résistance : 89
Chapitre V Le double vitrage
1- Le double vitrage 90
1-1 Définition : 90
1-2 Les modes de transmission de chaleur 91
1-3 Caractéristiques énergétiques 91
1-4 Caractéristique lumineuse 92
1-5 Caractéristique acoustique 92
2- Le double vitrage "à basse émissivité"
93
2-1 Principe 93
2-2 Importance de la position de la couche basse
émissivité 94
2-3 Caractéristiques énergétiques et
lumineuses 96
2-4 Combinaison des couches basse émissivité et de
couches permettant le contrôle solaire 97
3-Le triple vitrage 98
3-1 Caractéristiques énergétiques et
lumineuses 98
4-Le vitrage isolant acoustique 98
1 Les doubles vitrages dissymétriques 99
Conclusion 102
|