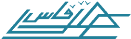
UNIVERSITÉ SIDI MOHAMED BEN
ABDELLAH
ÉCOLE SUPÉRIEURE DE
TÉCHNOLOGIE DE FÉS
DEPARTEMENT DU GÉNIE DES
PROCÉDÉS
OPTION INDUSTRIES CHIMIQUES
RAPPORT DE STAGE TÉCHNIQUE
Effectué au sein la CBGN sous le
thème :
Étude du système Qualité
Sécurité et Environnement au sein de la CBGN
PAR :
HAMMANI Othmane (Etudiant à
l'ESTF)
A.U 2008/2009
Dédicace
Je dédie ce travail avec le plus grand plaisir
à
Mes Parents
Mon frère et ma soeur
Mes professeurs et mes encadrants
Mes amis
Remerciements
J'adresse tout d'abord mes remerciements les plus
sincères, à mon professeur Monsieur Abdellatif LOUKILI, et
à Madame Hafida BENRAFAHALIA, qui ont très volontiers
acceptés d'être mes encadrants pendant mon stage.
* * * * *
Mes remerciements s'adressent également au
Directeur de l'ESTF, Monsieur Abdellatif SAFOUANE ainsi qu'au responsable de la
filière génie des procédés Monsieur Abdelhak
KHERBECHE.
* * * * *
Je me sentirais coupable d'ingratitude si je ne remerciais
pas tous mes professeurs et tous le personnel de la CBGN.
* * * * *
SOMMAIRE
Dédicaces.......................................................................2
Remerciements.................................................................3
Sommaire.......................................................................4
Introduction
.....................................................................5
Première partie : Présentation de
la CBGN..............................6
I.
Historique ..........................................................6
II. Activités de la
CBGN ...........................................7
III. Organisation de la
CBGN .......................................7
IV. Description de
l'usine ...........................................8
Deuxième partie : Procédé de
fabrication................................9
I. Traitement de
l'eau ...............................................9
II. Production de la boisson
gazeuse.............................15
III.
Conditionnement................................................19
Troisième partie : Etude du
système qualité sécurité et environnement au sein
de la CBGN.................................................26
I.
Généralités.......................................................26
II.
Qualité............................................................28
III.
Sécurité...........................................................33
IV.
Environnement..................................................51
Conclusion....................................................................54
Introduction
Avant d'obtenir le DUT Génies des
procédés option industries chimiques, l'étudiant doit
effectuer un stage de deux mois au sein d'une entreprise ou d'une institution,
le but est de permettre à l'étudiant de mettre en application les
connaissances acquises durant ses études.
Mon stage s'est déroulé du 27/04/2009 au
12/06/2009 : soit une période de sept semaines au sein de la
Compagnie des Boissons Gazeuses du Nord CBGN situé à
Fès.
A l'issue d'une discussion que j'ai effectué avec mon
professeur encadrant, nous avons déterminé un sujet qui
représente un besoin pour toute entreprise, le choix s'est porté
sur l'étude du système qualité sécurité et
environnement sur la chaîne de production de la CBGN.
Pour cela, j'ai été impliqué sur trois
phases :
1. Bref présentation de la CBGN.
2. Suivie des procédés de production.
3. Etude du système QSE dans la CBGN.
* * * * * * * * * * * *
Présentation de la
CBGN
I. Historique
La CBGN (Compagnie des Boissons Gazeuses du Nord) est une
société qui a pour activité principale la fabrication et
le conditionnement des boissons gazeuses.
Voila un bref historique de la CBGN :
Ø En 1952 : C'est la mise en place de la
CBGN : embouteilleur franchisé de
la compagnie coca-cola, elle a été située
à la place actuelle de l'hôtel Sofia.
Ø En 1971 : une nouvelle unité construite
au quartier industriel Sidi Brahim.
Ø De 1952 à 1987 : La CBGN ne fabriquait
que Coca-Cola et Fanta orange,
mais après, et pour augmenter sa part de marché,
la compagnie a décidé la diversification de ses produits, elle a
commencée de produire Fanta Florida, Fanta Lemon, Hawaï et Sprite,
elle a lancée en 1992 les bouteilles plastique PET, elle a même
achetée une nouvelle machine avec une grande capacité (plus de
6000 bouteilles par heure, rapide et qui effectue plusieurs taches au
même temps (soufflage, rinçage, soutirage, bouchage et datage).
Ø En 1997 : elle acquiert la SIM
(Société industrielle marocaine) ;
principal concurrent lui permettent ainsi d'augmenter sa
capacité de production et d'élargir sa gamme de produits.
Ø En 2002 : la CBGN devient filiale de l'ECCBC et
par la suite de Coca-
Cola Holding.
La CBGN reste parmi les anciens embouteilleurs qui existent au
MAROC.
II. Activités de la
CBGN
L'activité de la société est autant
industrielle que commerciale, elle se charge de la production des boissons
gazeuses du nord et de la distribution dans son territoire assigné.
Elle fabrique des boissons gazeuses de différents types
(Coca-Cola, Fanta, Hawaï... etc.), formes (PET et verre), et de
différents volumes (20, 25, 35, 35.5, 100, 150 et 200cl).
En plus da la commercialisation de ses propres produits, la
CBGN commercialise aussi les eaux de table (CIEL et BONAQUA), Coca-Cola light,
Coca-Cola zéro et d'autres boissons gazeuses de formes PET et canettes,
Miami, ces produits sont achetés des autres embouteilleurs appartenant
au même groupe NABC.
III. Organisation de la
CBGN
L'organigramme de la CBGN se présente de la
façon suivante :
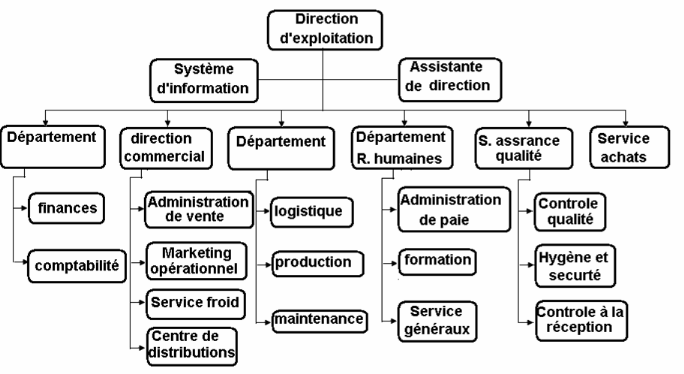
IV. Description de l'usine
L'usine de Fès est située au quartier industriel
Sidi Brahim, elle couvre une superficie globale d'environ un hectare.
L'usine dispose de :
Ø Une station pour le traitement des eaux.
Ø Une ligne de production (siroperie).
Ø Trois chaudières pour la production de la
vapeur.
Ø Ligne 1 et 2 des bouteilles en verre.
Ø Ligne 3 et 4 des bouteilles soufflées
« PET ».
Procédé de
fabrication
I. Traitement de l'eau
I.1. Nécessité du traitement de
l'eau
L'eau constitue l'élément majoritaire dans la
boisson gazeuse, donc il peut influencer son goût, son odeur ainsi que
son apparence, c'est pour cela qu'il faut traiter l'eau de ville avant son
utilisation pendant la production du sirop, cette eau contient pas mal de
substance qui peut influencer la boisson :
Ø MES (matière en
suspension) : De nombreuses particules peuvent
constituer les impuretés d'une eau. Les techniques
analytiques nécessaires à leurs déterminations
dépendent des dimensions de ces particules, les impuretés
présentes dans l'eau ont pour origine soit des substances
minérales, végétales ou animales.
Les matières décantables sont les
matières de grandes tailles, entre 40 micromètres et 5
millimètres et qui se déposent sans traitement physique ou
chimique.
Ø Les matières
colloïdales : ce sont des matières de même
origine que les
MES, leurs diamètres est généralement
inférieure à 5 micromètres. La duré
décantation naturelle de ces matières a été
estimé entre 2 et 200 ans pour sédimenter dans une colonne de 1
mètre d'eau, il faudra donc les précipiter pour contribuer
à leur décantation, c'est l'objectif de la
coagulation-floculation.
Ø Composés phosphorés :
Le phosphore est l'un des composants
essentiels de la matière vivante.
Ø L'alcalinité: les
bicarbonates, les carbonates ou les hydroxydes, peuvent
donner un goût anormal au produit fini.
Afin de transformé l'eau de ville en une eau convenable
à la production de la boisson, il faut la faire passé par
plusieurs étapes de traitement.
I.2. Procédé de traitement de l'eau
dans la CBGN
I.2.a. Traitement de l'eau de la
production
La CBGN dispose d'une installation importante qui est
destiné au traitement de l'eau, cette installation comprend :
Ø Des bassins de chloration.
Ø Des filtres à sable.
Ø Un décarbonateur.
Ø Des filtres à charbons.
Ø Des filtres polisseurs.
Ø Et des pompes pour la circulation de l'eau.
Flow sheet de cette installation.
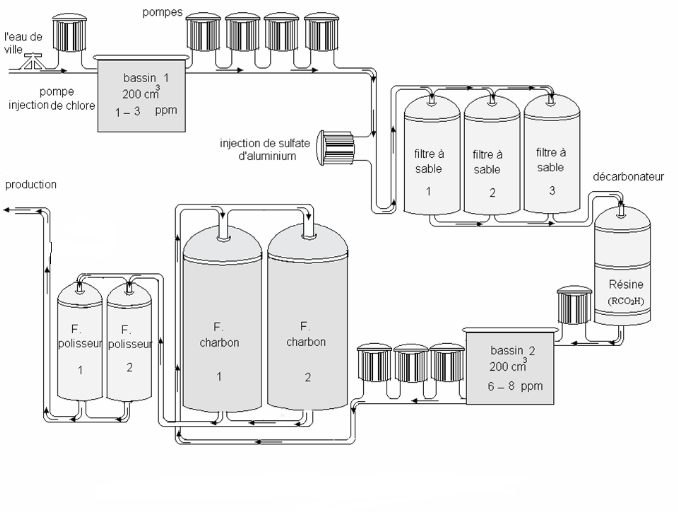
Mode de fonctionnement de
l'installation
Bassin 1 :
Ce bassin est destiné à la fois au stockage de
l'eau et à sa chloration par l'injection d'une quantité de chlore
comprise entre 1 et 3 ppm.
La capacité de ce bassin et d'environ 200
m3, le niveau d'eau à l'intérieur est
contrôlé au moyen des sondes de niveau.
A noter que la teneur en chlore et
les paramètres (goût, odorat et apparence) GOA, sont
analysés quotidiennement.
Filtre à
sable :
L'eau sortante du bassin 1 est transportée via des
pompes vers les filtres à sable après avoir reçue une dose
de sulfate d'aluminium qui représente l'agent coagulant, qui va
déstabiliser les particules colloïdales pour former des flocs qui
vont être éliminer au niveau de ces filtres.
Bien évidemment, après un certain temps
estimé à 3 jours, les filtres à sables vont être
chargés par les flocs, ce qui va déranger son bon fonctionnent,
pour les débarrassés de ces particules, il sera lavé tous
les 3 ou 4 jours par l'injection de l'eau à contre courrant.
L'efficacité de ces filtres est vérifiée
par l'analyse des GOA, et la turbidité, il faut aussi
vérifié l'état du sable, cette vérification peut
conduire au changement du sable si nécessaire.
Le
décarbonateur :
Il s'agit d'une grande cuve remplie par un lit de
résines cationiques, un solide organique insoluble qui au contacte de
l'eau échange les cations qui contient avec les cations provenant de la
solution.
Dans notre cas, la résine utilisée est de type
RCO2H, le but étant de réduire l'alcalinité de
l'eau, le mécanisme consiste à échanger les ions
Ca2+ et Mg2+ provenant du bicarbonate de sodium et de
magnésium avec la formation du gaz carbonique suivants les
réactions :
2RCO2H + Ca(HCO3)2
Ca(RCO2)2 + 2CO2 +
2H2O
2RCO2H + Mg(HCO3)2
Mg(RCO2)2 + 2CO2 +
2H2O
Il faut mesurer périodiquement l'efficacité de
la résine qui est caractérisée par la teneur de l'effluent
en carbonates et hydrogénocarbonates, lorsque cette quantité
dépasse les 85 mg/l, il faut régénéré la
résine par de l'acide chlorhydrique concentré qui va substituer
les ions Ca2+ et Mg2+ par des protons.
Après une certaine durée, la
régénération ne peut rénover les résines,
dans ce cas il faut changer carrément le remplissage.
Bassin 2 :
Le bassin 2 est un bassin qui reçoit l'eau sortante du
décarburateur, avec une capacité de 200 m3, une quantité
de chlore est ajouté de telle manier à obtenir une concentration
de 6 à 8 ppm afin de désinfecter l'eau.
Le niveau dans ce bassin doit être contrôlé
toutes les 4 heures, ainsi que la teneur du chlore dans l'eau sortante qui doit
rester dans l'intervalle de 6 à 8 ppm.
Filtre à
charbon :
Les filtres à charbon sont des cuves remplies par du
charbon actif qui représente un agent adsorbant visant à
éliminer le chlore et tous les substances pouvant donner un goût
ou une odeur anormal à la boisson, ainsi que les substances organiques
et les micro polluants.
A la sortie du filtre à charbon, plusieurs
paramètres doivent être vérifiés
Ø GOA
Ø Le titre alcalimétrique qui ne doit pas
dépasser les 2 mg/l.
Ø Le titre alcalimétrique complet qui ne doit pas
dépasser les 85 mg/l.
Ø La teneur en chlore doit être nul.
Ø Le pH doit être supérieure à 5.
Ø La TDS ne doit pas dépasser 500 ppm. (taux de
solide dissous)
Ø La turbidité doit rester dans la limite de 0.5
NTU.
Lorsque ces paramètres dépassent ces limites, le
charbon devient saturé, et nécessite d'être
changé.
Filtres polisseurs :
La station renferme deux filtres polisseur, chaque filtre se
compose d'un support pour filtre en papier ou cartouche en fibre chargé
d'éliminer les particules de charbon actif éventuellement
présentes dans l'eau à la sortie du filtre à charbon.
Les filtres polisseurs doivent être nettoyés avec
une solution chlorée à chaque changement de papier ou de
cartouche.
La stérilisation du filtre polisseur s'effectue deux
fois par semaine ou selon les résultats des analyses
microbiologiques.
I.2.b Traitement de l'eau utilisé pour le
lavage des bouteilles
Les laveuses des bouteilles et bien d'autres machines
consomment des quantités importantes d'eau sous des températures
relativement élevés, donc si on utilise l'eau de ville, ça
va provoquer du tartre qui va empêcher le bon fonctionnement de ces
équipements, pour cela il faut traités ces eaux afin
d'éviter la formation du tarte.
C'est l'opération d'adoucissement de l'eau, ça
consiste en une permutation des ions Mg2+ et Ca2+ par
Na+, pour ce faire, on fait circuler l'eau à travers des
résines cationiques de type Na2R selon les réactions
suivantes :
Ca(HCO3)2
NaHCO3 Mg(HCO3)
CaSO4 +
Na2R
NaSO4
MgSO4
CaCl2 MgCl2
NaCl
Après une certaine durée d'utilisation, la
résine se retrouve saturée, et nécessite par
conséquent une régénération par une solution
concentré de NaCl.
Remarque :
Ce même traitement est appliqué pour les eaux
utilisées dans les chaudières.
II. Production de la boisson
gazeuse
Après avoir traiter l'eau, il reste une deuxième
étape qui est la production de la boisson gazeuse, c'est la siroperie,
cette opération peut être subdivisé en deux grandes
parties, la préparation du sirop simple, puis du sirop fini.
II.1. Préparation du sirop
simple
Cette étape commence par l'injection du sucre
granulé, approvisionné par COSUMAR et contrôler dans le
laboratoire de la CBGN qui veille sur sa qualité et sur le respect des
normes prescrites.
L'opération à lieu au niveau d'un tamis
permettant d'arrêter les grands grains et de laisser passer les
particules ayant la granulométrie désirée, à l'aide
d'une vis, le sucre est ensuite transporter vers un silos de stockage qui
assure l'alimentation de circuit et évite toute rupture probable pendant
la fabrication.
En bas du silo, est installé une vanne munie de
vérins pneumatiques qui permettent un ajustement automatique de
l'alimentation du sucre selon les besoins en aval. Une deuxième vis sans
fin amène le sucre vers une cuve de dissolution qui contient de l'eau
traitée à la température de 60 °C.
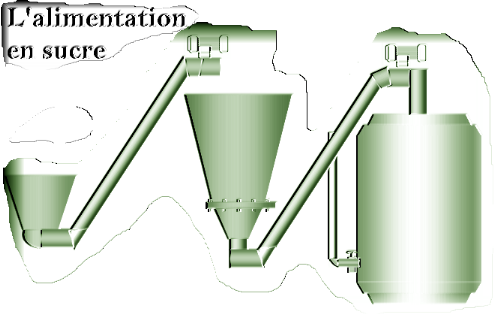
![]()
Alimentation du tamis et acheminement du sucre
vers la cuve de dissolution
A la sortie, on récupère une solution de sucre,
c'est le sirop qui va traverser dans un premier temps un filtre horizontal
puis l'autre qui est vertical au sein duquel s'effectue l'agitation de la
solution, les particules non dissoutes précipitent et sont
recyclées dans la cuve de dissolution, le brix de la solution se fait
à la sortie du filtre à l'aide du visio brix.
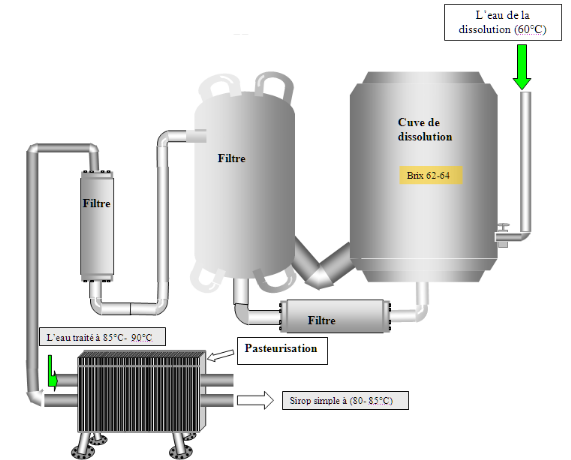
![]()
Traitement du sucre par des filtres et sa
pasteurisation au niveau de l'échangeur.
L'échangeur thermique est alimenté par la vapeur
d'eau provenant de l'atelier des chaudières. La vapeur permet le
chauffage de la solution à environ 85 °C, la température ne
dois pas dépasser ce degré, sinon on risque de caraméliser
le sucre, cette élévation de température permet la
pasteurisation qui consiste à enlevé les bactéries, les
germes ainsi que les autres micro-organismes existant dans la solution,
ensuite une partie du mélange est envoyée vers la cuve au
charbon actif, cette dernier est remplie de la solution du sucre à
laquelle vient s'ajouter le charbon actif en poudre, deux sonde
installées au niveau de la cuve, l'une en bas permet de contrôler
le niveau maximum de la solution, et ce en injectant du charbon et de la
solution du sucre via une pompe agitateur, une fois celle-ci atteint ce niveau,
l'autre sonde installée en haut bloc l'alimentation de la cuve une fois
le niveau maximum est atteint. Il est à noter que le sirop obtenu
à la sortie de l'échangeur ne traverse pas en entier la cuve du
charbon actif, mais juste une partie qui est à son tour injectée
dans la canalisation en provenance de l'échangeur et acheminée
vers la cuve de réaction.
Dans la cuve de réaction et au bout de 30 minutes
environ est effectuée la réaction entre le sirop et le charbon
actif, la réaction a pour but d'enlever la mauvaise odeur du sucre, de
virer son apparence du jaune au blanc et d'assurer un bon goût.
Pour éliminer les matières en suspension et les
impuretés qui restent dans le mélange, ce dernier subit une autre
phase de traitement, celle-ci commence par l'injection de la célite
(terre diatomée) sous forme de poudre au niveau d'une cuve adjuvant qui
va être déposée sur des plaques métalliques
horizontales installées au niveau d'une cuve formant ainsi un filtre dit
à gâteaux, le passage du sirop, à une température de
85 °C à travers ce filtre, permet sa purification.
La circulation du mélange entre l'entrée et la
sortie de la cuve est contrôlée par des manomètres qui
permettent le réglage de la pression dans les deux positons. Chaque fois
qu'il y a un colmatage du filtre on procède à l'évacuation
du gâteau.
Par ailleurs le mélange doit subir une succussion
d'étapes de refroidissement pour arriver à un sirop simple avec
une température convenable :
La première étape utilise l'eau
traitée à la température ambiante et permet de ramener la
température du sirop à 60 °C environ. Cette eau à une
telle température peut servir à dissoudre le sucre d'où
elle est recyclée vers la cuve de dissolution permettant ainsi une
économie d'énergie.
La deuxième exploite l'eau adoucie
en provenance de la tour de refroidissement à une température de
15°C afin de ramener le sirop, de l'étape précédente,
à une température de 50 °C, l'eau adoucie chaude est
renvoyée à la tour de refroidissement pour la porter à sa
température initiale.
La troisième étape se contente de l'eau
glycolée (eau à une température moins de 0 °C
mélangée avec une substance (glycol) pour éviter sa
congélation à cette température), ce qui permet d'abaisser
la température du sirop obtenu au niveau de la deuxième
étape à l'environ de 22°C, cela grâce à une
sonde qui ajuste le débit de l'eau glycolée et par la suite
contrôle son refroidissement. L'eau chaude est pompée à une
tour de refroidissement pour lui rendre sa température initiale. Le
sirop obtenu est envoyé à la cuve de sirop simple où
il repose pendant une heure pour qu'il soit désaéré.
A la fin de cette étape on obtient un mélange
appelé sirop simple.
II.2. Préparation du sirop
fini
Le sirop fini est un mélange de sirop simple et de
sirop concentré appelé aussi extrait de base, qui son tour un
mélange complexe d'arômes, d'acidifiants et de colorants, ce
dernier est reçu, sous licence, dans de grands flacons.
La préparation du sirop fini commence par le
contrôle des ingrédients du produit par un opérateur qui
les introduit dans un récipient où se fait le mixage avec l'eau
traitée, le mélange est ensuite envoyé à la cuve de
sirop fini dans lequel s'effectue le mixage avec le sirop simple à
l'aide d'une pompe qui maintient l'agitation pendant 30 min. le produit obtenu
repose dans les environs de 15 min afin d'assurer sa désaération
puis contrôlé par l'opérateur qui veille sur sa
conformité en réglant tous les paramètres en question
à savoir la température, les degré brix et bien d'autres
paramètres.
Le sirop fini va être envoyé vers le mixeur.
II.3. Mixage
Le mixage constitue la dernière phase de production de
la boisson, cette étape consiste à mélanger le sirop fini
avec l'eau traitée refroidie par l'eau glycolée et du gaz
carbonique dans des proportions bien définies.
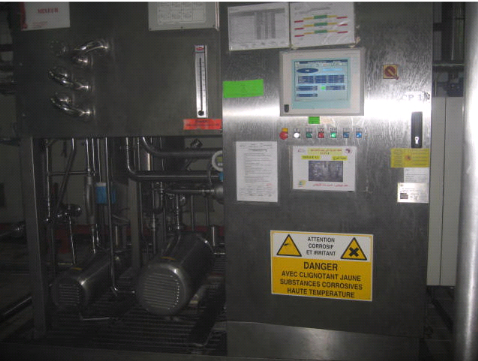
Mixeur
III. Conditionnement
Comme il a été déjà indiqué
dans le début de ce rapport, la compagnie contient quatre lignes, deux
pour les bouteilles en verre, les autres pour les bouteilles en plastique.
III.1. Bouteilles en verre
III.1.a. dépalettisation
Cette machine représente un système presque
automatisé concernant la mise en caisses sur convoyeurs, ces caissiers
sont placés les uns sur les autres sous forme d'un
parallélogramme de six caissiers sur quatre caissiers pour le volume de
1L et six caissiers pour le volume de 35 cl 20 cl, ce parallélogramme
est posé sur une planche appelée palette.
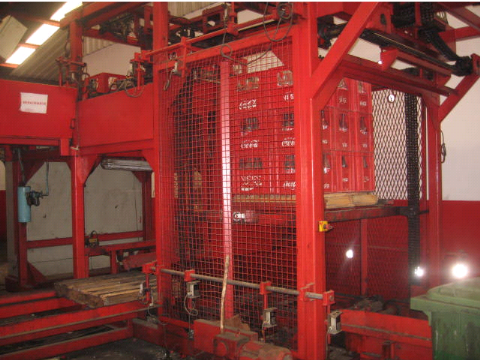
Dépalettiseur
III.1.b. décaisseuse
C'est une machine qui enlève les bouteilles vides des
caisses et les pose sur le convoyeur qui alimente la laveuse des bouteilles et
laisse échapper les caisses en destination de la laveuse des caisses.
La pose des bouteilles se fait à l'aide d'une ventouse
qui souffle de l'air et crée une force de pression.
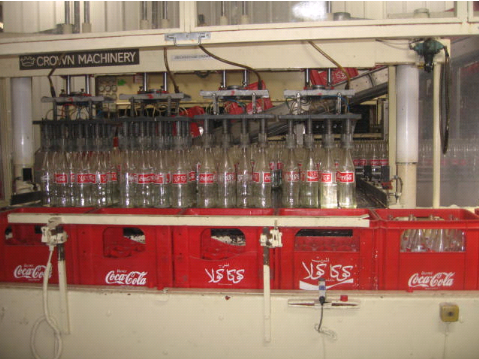
Décaisseuse
III.1.c. Lavage des bouteilles
Le lavage s'effectue selon plusieurs
étapes :
Ø La pré-inspection :
c'est l'opération qui consiste à la sélection des
bouteilles conformes, effectué par un
opérateur.
Ø Le prélavage : est
assurer par une eau adoucie tiède qui réchauffe
légèrement la bouteille, permettant par la suite
l'élimination des matières adhérant aux parois.
Ø Le lavage à la soude caustique :
s'effectue à une température de 82 °C
combiné au triphosphate de sodium dont le rôle
est d'empêcher le passage de la mousse en provenance de NaOH et de
permettre la brillance des bouteilles.
Ø Le pré-rinçage : est
une opération de rinçage des bouteilles afin
d'éliminer les traces de détergent, se fait dans
trois bains contenant une adoucie chaude, tiède et froide. Le
rinçage final est réalisé par l'eau froide chlorée
de 1 à 3 ppm pour éliminer les résidus caustiques et
refroidir les bouteilles jusqu'à la température ambiante.
Ø L'inspection visuelle par les mireurs :
à pour but d'éliminer les
bouteilles mal lavées et
ébréchées.
Ø L'inspection électronique :
s'effectue avant le soutirage, dans le but de
retirer les bouteilles contenant des matières
étrangères.
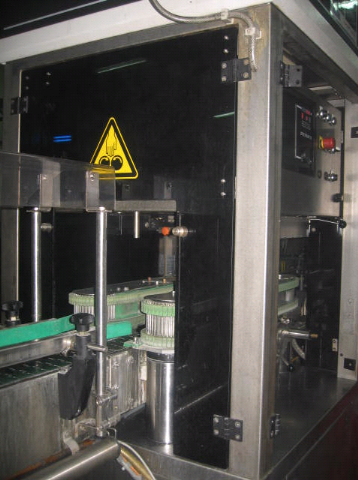
Laveuse des bouteilles
Inspectrice
III.1.d. Soutirage et bouchage
C'est le remplissage des bouteilles lavées par la
boisson à l'aide d'une soutireuse qui seront par la suite fermées
hermétiquement au niveau de la visseuse. Les bouteilles ainsi remplies
et fermées sont contrôlées visuellement par un appareil
électronique, afin de retirer les bouteilles mal remplies ou mal
bouchées.
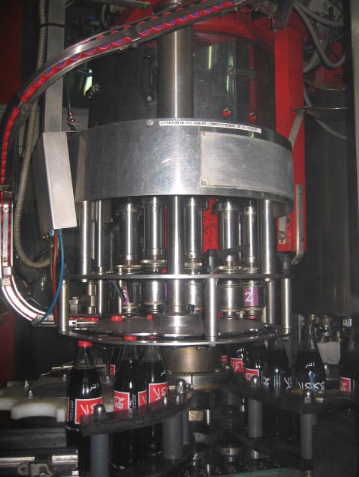
Soutireuse
Visseuse
III.1.e. étiquetage et
codage :
Après l'inspection visuelle, les bouteilles remplies
sont étiquetées et codées sur le bouchon, (date, heure et
lieu de production, date de péremption, ligne concernée).
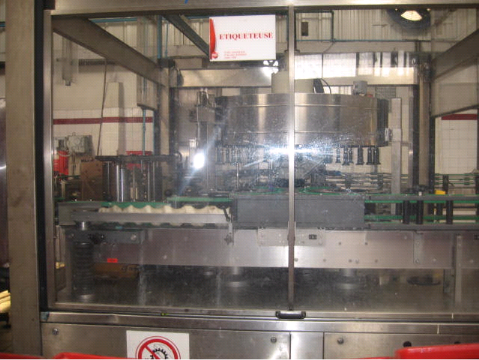
Etiqueteuse
III.1.f. Palettisation
C'est la mise en palettes des caisses pleines de bouteilles
remplies.
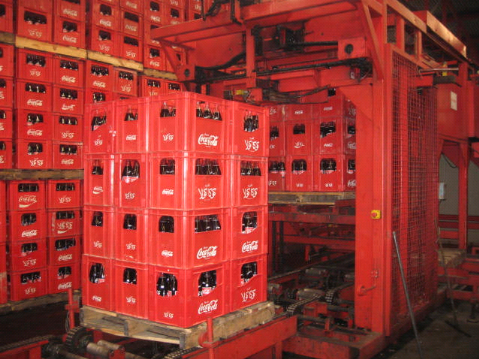
Palettiseur
III.2. Bouteilles en plastiques
III.2.a. Soufflage des
préformes
Les préformes sont conduites vers la machine de
fabrication par un élévateur en escalier, à
l'entrée de la machine, les préformes subissent un chauffage dans
un four qui contient des lampes à infrarouge, qui fixent les
préformes et les fait tournés tout au long du four, pour qu'elles
se ramollissent.
A la sortie du four, une pince attrape la tête de la
préforme et la conduit vers le moule muni d'une tige d'élongation
qui entre dans la préforme pour lui donner la hauteur prévue. La
préforme subit ensuite un pré-soufflage avec une pression de 7
bars, pour préparer la matière à subir une haute pression
(40 bars) lors du soufflage.
A la fin, les bouteilles sortent du moule et subissent un
dégazage à l'air libre, et une fois soufflées, elles
seront acheminées par un convoyeur vers la rinceuse.
III.2.b. Rinçage
Une fois les bouteilles soufflées PET sont obtenues,
elles sont acheminées par le convoyeur à l'air comprimé
vers la rinceuse ou elles subissent un rinçage par l'eau traité
chlorée.
III.2.c. Carbonatation et
refroidissement
III.2.d. Soutirage et bouchage
III.2.e. Etiquetage et codage
III.2.f. Mise en pack et stockage
Les bouteilles en PET étiquetés et codées
passent dans une fardeleuse qui les enveloppe d'un film rétractable pour
être stockées et distribuées sous forme de pack vers les
dépôts et les centres régionaux rattachés à
la CBGN.
III.3. Nettoyage et sanitation
Les opérations de sanitation des équipements de
mixage et de remplissage des produits sont des opérations de nettoyage
et de stérilisation qui consiste à débarrasser ces
équipements des traces de produits.
Ces opérations s'effectuent en des
étapes :
Nettoyage/ Sanitation 3 étapes eau chaud
:
-Prélavage
-Lavage à l'eau chaude.
-Rinçage à l'eau traitée.
Nettoyage 3 étapes à la soude
:
-Prélavage.
-Lavage à la soude.
-Rinçage à l'eau traitée.
Nettoyage 5 étapes à la soude
:
-Prélavage.
-Lavage à la soude.
-Rinçage à l'eau traitée.
-Lavage à l'eau chaude.
-Rinçage à l'eau traitée.
Nettoyage/ Sanitation 6étapes (à
chaque arrêt de 24h) :
-Prélavage.
-Lavage à la soude.
-Rinçage à l'eau traitée.
-Lavage à l'eau chaude.
-Rinçage à l'eau traitée.
-Utilisation de désinfectant (NaOH ou HCL).
Etude du système qualité
sécurité et environnement au sein de la CBGN
I. Généralités.
I.1. Les normes
Une norme (du latin `norma', « équerre,
règle ») désigne un état habituellement
répandu ou
moyen
considéré le plus souvent comme une règle à suivre.
Ce terme générique désigne un ensemble de
caractéristiques décrivant un objet, un être, qui peut
être
virtuel ou non. Tout ce qui
entre dans une norme est considéré comme
« normal », alors que ce qui en sort est
« anormal ». Ces termes peuvent sous-entendre ou non des
jugements de valeur.
Définition de l'ISO :
L'ISO est un réseau d'instituts nationaux de
normalisation de 156 pays, selon le principe d'un membre par pays, dont le
Secrétariat Central, situé à Genève, Suisse, assure
la coordination d'ensemble.
L'ISO est une organisation non gouvernementale : ses
membres ne sont pas, comme le système des Nations Unies, des
délégations des gouvernements nationaux. L'ISO occupe
néanmoins une position privilégiée entre les secteurs
public et privé. La raison à ce que l'ISO compte dans ses membres
de nombreux instituts faisant partie de la structure gouvernementale de leur
pays ou mandatés par leur gouvernement et d'autres organismes issus
exclusivement du secteur privé, établis par des partenariats
d'associations industrielles au niveau national.
L'ISO peut donc agir en tant qu'organisation de liaison
permettant d'établir un consensus sur des solutions répondant aux
exigences du monde économique et aux besoins de la
société, notamment ceux de parties prenantes comme les
consommateurs et les utilisateurs.
Remarque :
Parce que le nom de l'Organisation Internationale de
Normalisation donnerait lieu à des abréviations
différentes selon les langues (ISO anglais et OIN en français),
il a été décidé d'emblée d'adopter un mot
dérivé du grec isos, signifiant
"égal". La forme abrégée du nom
de l'organisation est par conséquent toujours ISO.
I.1.a. ISO 9001
La norme ISO 9001 fait partie de
la
série
des normes ISO 9000, relatives aux systèmes de
gestion de la
qualité, elle donne les exigences organisationnelles requises pour
l'existence d'un système de gestion de la qualité.
I.1.b. OHSAS 18001
Cette norme permet de mettre en
place un système de management de santé et de
sécurité au sein de l'entreprise pour assurer un
développement durable.
I.1.c. ISO 14001
La norme ISO 14001 est la plus
utilisée des normes de la série des normes ISO14000 qui
concernent le management environnemental.
I.2. La qualité
La qualité dans une
entreprise c'est l'ensemble des propriétés et
caractéristiques d'un produit ou d'un service qui lui confèrent
l'aptitude à satisfaire des besoins exprimés ou implicites.
Dans le cadre de la
gestion de la
qualité, plusieurs appellations avec leurs nuances se sont
succédées au fil des évolutions.
·
Démarche qualité : mise en oeuvre de la politique
qualité ;
· Cas particulier de la qualité total
· Le système qualité : description du
dispositif de la politique qualité.
·
Contrôle qualité : vérification des
conformités des produits.
Et les outils, dont :
· le
système
de management de la qualité ;
· Les
processus ;
· Un
cercle de
qualité est un groupe de réunion décisionnel.
II. La qualité dans la CBGN.
La CBGN veille principalement sur deux volets pour le
contrôle de la qualité à savoir le contrôle à
la réception et le contrôle au cours de la production.
II.1. Contrôle à la
réception
Chaque étapes du processus de fabrication de boisons
gazeuses subit un contrôle minutieux afin de s'assurer de sa
conformité selon les normes prédéfinis pour garantir la
sécurité du consommateur.
II.1.a. Contrôle des matières
premières
Ø Sucre : goût, odeur,
apparence et turbidité.
Ø Concentré, extrait de base et
additif.
Ø CO2 : Pureté,
odeur et goût.
II.1.b. Contrôle des matières
d'emballage et de conditionnement
Ø Préformes PET et bouteilles en
verre.
Ø Bouchons, étiquettes :
épaisseur, longueur, largeur, et impression.
Ø Films rétractable et
étirables.
Ø Palettes et casiers.
II.1.c. Contrôle des produits
chimiques
Ø La soude caustique utilisée pour
le nettoyage des bouteilles.
Ø Le chlore pour la désinfection
des bouteilles et le traitement des eaux.
Ø Le chlorure de sodium de
régénération des adoucisseurs.
Ø L'acide chlorhydrique pour la
régénération du décarbonateur.
II.2. Contrôle au cours de la
production
Plusieurs paramètres doit être
contrôlés au cours de la production de la boisson gazeuse, voila
un tableau qui résume ces différents contrôles :
Elément contrôlé
|
Paramètre
|
Sirop fini
|
Brix
|
Boissons gazeuses
|
G.O.A
Pression de CO2
Température de carbonatation
Volume de CO2
|
Bouchons
|
Codage
Torque
|
Etiquettes
|
Epaisseur, longueur et largeur.
Impressions.
|
Désignation des
abréviations :
Ø Brix : c'est le pourcentage
massique du saccharose dans la solution, est mesuré après
décarbonatation de l'échantillon pendant 3 min.
Ø GOA : goût, odeur,
apparence : c'est tout simplement un test qui consiste à
goûter la boisson et la sentir et essayai de détecter une anomalie
au goût à l'odeur ou à l'apparence.
Ø Torque mètre : c'est un
appareil qui sert à contrôler la pression d'ouverture du
bouchon.
Ø Codage : Vérification du
bon établissement du jet d'encre ainsi de sa clarté.
Ø Etiquetage : c'est voir si les
étiquettes sont bien appliqués sur les Bouteilles.
II.3. Amélioration de la
qualité
La qualité de tous les paramètres
contrôlés qu'on vient de citer dépend directement de la
qualité et de la méthode de manipulation des différents
outils et machines utilisés dans la chaîne de la production. C'est
pour cela qu'il faut bien former les opérateurs pour qu'ils atteignent
le niveau désiré afin d'utiliser correctement les machines et
d'éviter les petits fautes qui ont des influences sur la qualité
du produit fini ainsi qu'ils peuvent provoquer des pertes au niveau de
l'entreprise.
Dans ce paragraphe, on va donner quelques instructions de
travail relatif à certaines machines dans le but d'améliorer leur
efficacité.
II.3.a. La souffleuses des bouteilles
PET
L'opérateur de la souffleuse
doit :
Ø Respecter les procédures et exigences QSE.
Ø Assurer le réglage du convoyer lors des
changements de taille.
Ø Assurer l'arrêt du convoyeur à air
à chaque arrêt prolongé de la production.
Ø Assurer l'arrêt du convoyeur à air
à chaque fin de production.
Ø Veuillez au bon fonctionnement du convoyeur à
air.
L'opérateur de nettoyage doit :
Ø Assurer le nettoyage du convoyeur à air suivant
les prescriptions préalables.
Ø Assurer le nettoyage et les changements des filtres
d'air.
Ø Assurer le nettoyage des trémies des
préformes.
Ø Respecter les instructions de sécurité des
produits de nettoyage.
Ø Informer le responsable
hiérarchique
de toutes les anomalies constatées et veillez à leur
élimination.
Ø Nettoyer immédiatement des fuites d'huile.
Ø Poser les chiffons souillés dans les poubelles
destinées à cet effet.
II.3.b. Laveuses des bouteilles
L'opérateur de la laveuse
doit :
Ø Respecter les procédures et exigences QSE.
Ø Contrôler les niveaux des bains de soude le
chef d'équipe en cas de problème.
Ø Contrôler le niveau des bains de
rinçage.
Ø Au cours de la production contrôler le
fonctionnement et l'alignement des injections à travers les
fenêtres de la laveuse.
Ø Contrôler la pression de l'eau de
rinçage le long de l'opération.
Ø Contrôler l'état de l'eau au niveau des
bains de rinçage ; changer cette eau si nécessaire.
Ø Veuillez à l'élimination des
bouteilles trop sales, ébréchés et étrangers avant
l'entré à la laveuse.
Ø Mettre les lunettes de protection et les gants
antiacides lors du nettoyage des bains de soude.
Ø Porter ses EPI (les équipements de protection
individuels)
Ø Actionner les arrêts d'urgence avant chaque
intervention.
Ø Respecter les instructions de sécurité
liées aux produits chimiques utilisés (soude caustique, eau de
javel, synergique).
Ø Veuillez à la chasse des fuites, d'eau et de
soude.
Ø Optimiser la consommation de l'eau de la laveuse des
bouteilles.
Ø Contrôler l'alimentation de l'eau
recyclée à l'entrée de la laveuse.
Ø Vérifier le bon fonctionnement de glisseurs de
rinçage.
Ø Informer le responsable
hiérarchique
de toutes les anomalies constatées et veillez à leur
élimination.
II.3.c. Rinceuse
L'opérateur de la rinceuse doit :
Ø Enlever tout corps étranger éventuel
à l'intérieur.
Ø Nettoyer le tapis de caisse avec une brosse afin
d'enlever les matières telles que des éclats de verre ou autre,
qui peuvent provoquer une usure prématuré de la chaîne
plate à charrier.
Ø Nettoyer le dispositif et retirer des obturations
éventuelles existantes.
Ø Vérifier les circuits pneumatiques, des bruits
sifflants signalent une défectuosité.
Ø Arrêter la machine en cas des défauts
qui mettent en danger la sécurité de fonctionnement.
Ø Ne porter pas de bijoux, bague chaîne ou autre
avec le quels vous pouvez accrocher à la machine.
Ø Porter ses EPI.
Ø Informer le responsable
hiérarchique
de toutes les anomalies constatées et veillez à leur
élimination.
II.3.d. Mixeur starblend
Ø Respecter les procédures et exigences QSE.
Ø S'assurer que le branchement sur le panneau de
distribution du starblend est correct.
Ø S'assurer que la pression du CO2 à
l'entré du starblend est correct.
Ø Faites entré la recette du produit a soutirer en
respectant de démarrages affichés.
Ø S'assurer que la réfrigération est
adéquate.
Ø S'assurer après lancement de l'opération
drainage que le starblend est complètement vide.
Ø Suivre le déroulement de la première
production et apporter la correction des paramètres si
nécessaires.
Ø Contrôler le fonctionnement des flotteurs des
réservoirs d'eau du sirop et du mélange.
Ø Fermer les vannes d'eau, de sirop et de CO2
lors de tout arrêt prolongé.
Ø Actionner les arrêts d'urgence avent chaque
intervention.
Ø Surveiller et agir en cas de fuite d'eau glycolée
ou de produit.
Ø Informer le responsable
hiérarchique
de toutes les anomalies constatées et veillez à leur
élimination.
II.3.e. La siroperie.
L'opérateur de la siroperie doit respecter les
points suivant avant toute opération :
Ø Veillez au respect des règles
d'hygiènes QSE.
Ø Vérifiez l'état des vannes au niveau
des circuits de préparation du sirop.
Ø Vérifiez l'état des vannes au niveau
des panneaux de distribution.
Ø Vérifiez l'état des commandes au niveau
des postes de commandes.
Ø Mettre le sectionneur de courant des postes de
commande en position I.
Ø Démarrer les pompes d'agitation du sirop 30
min avant le démarrage.
Ø Préparer les sirops à brancher pour les
mesures de brix.
Ø Préparer les circuits de branchement des
sirops selon le besoin.
Ø Remettre les compteurs de sirop à la sortie
des pompes de refoulement à zéro.
Ø Respecter les procédures, les instructions de
travail et les instructions de préparation du sirop.
Ø Respecter les fréquences et les protocoles des
opérations d'entretient des équipements.
Ø Respecter la tenue de tous les enregistrements.
Ø Veuillez à porter les EPI
systématiquement prescrits.
Ø Veuillez à ce que la tenue de travail soit
correcte et propre.
Ø Ne pas déverser les produits dans les
égouts.
Ø Ne pas déverser le gâteau de filtration
dans les égouts.
Ø Garder son poste de travail.
Ø Respecter les instructions de sécurité
liées aux produits utilisés.
Ø Informer le responsable hiérarchique de toutes
les anomalies observées, veiller à leur limitation et à
l'enregistrement d'accès à la siroperie.
Remarque :
Les instructions de travail qu'on vient de citer contiennent au
fur et à mesure des mesures de sécurité que
l'opérateur doit respecter.
III. La sécurité dans la
CBGN
Les différentes opérations de production des
boissons gazeuses comme il est déjà cité dans la
deuxième partie de ce travail, utilisent souvent des machines et des
équipements présentant divers risques. En effet, la
sécurité des opérateurs et l'une des priorités
visées par la compagnie.
III.1. Notion d'accident du
travail
III.1.a. Définition
La notion d'accident de travail désigne un
événement violent et soudain qui cause un dommage corporel. Le
droit du travail désigne comme accident du travail « tout
accident survenu par le fait ou à l'occasion du travail quelle qu'en
soit la cause, à tout travailleur soumis aux dispositions du code du
travail. Sont également considérés comme accident de
travail, l'accident survenu à un travailleur pendant le trajet de sa
résidence au lieu de travail et vice versa, dans la mesure où le
parcours n'a pas été interrompu ou détourné pour un
motif dicté par l'intérêt personnel ou indépendant
de son emploi, et l'accident survenu pendant les voyages dont les frais sont
mis à la charge de l'employeur. »
III.1.b. Classification des accidents de
travail
L'extrême diversité des accidents de travail rend
difficile l'élaboration d'une méthode de classification et
d'enregistrement qui permette, sans être trop compliquée, de
réunir les renseignements essentiels pour la prévention. La
10ème conférence internationale des statisticiens du
travail en 1962 réunie au BIT a recommandé 4 formes de
classification :
Ø la classification selon la forme de
l'accident.
Cette forme de classification est basée sur la
manière dont s'est produit l'accident. Elle permet de déterminer
l'événement dont la lésion de la victime est la
conséquence directe ; elle indique comment l'objet ou la substance
qui a provoqué la lésion est entré en contact avec la
victime. Ainsi les différents types d'accidents sont :
§ Les chutes de personnes
§ Les chutes d'objets
§ Marche sur, choc contre, heurt par, des objets
§ Coincement dans un objet ou entre des objets
§ Effort excessif ou faux mouvements
§ Exposition à ou contact avec des
températures extrêmes
§ Exposition ou contact avec le courant électrique
§ Exposition ou contact avec des substances nocives ou des
radiations
§ Autres formes d'accidents non classés ailleurs
Ø la classification d'après l'agent
matériel.
L'agent matériel est l'objet qui a occasionné la
lésion. Cette forme de classification se fait en fonction de cet objet.
Elle peut être appliquée soit en relation avec la lésion,
soit en relation avec l'accident lui-même.
On distingue les accidents causés par les objets
suivants :
§ Machines
§ Moyens de transport et de manutention
§ Matériaux substances et radiations
§ Autres matériels
Ø la classification selon la nature de la
lésion.
Cette classification se fonde sur la nature du dommage
corporel dont est victime le travailleur : les fractures, luxations ;
entorses et foulures, les commotions et autres traumatismes internes, les
amputations et énucléations etc.
Ø la classification selon le siège de la
lésion.
Elle se fait selon la partie du corps où est
localisée le dommage corporel :
§ Tête
§ Cou
§ Tronc
§ Membres inférieurs et membres supérieurs
§ Sièges multiples
§ Lésions générales
§ Siège non précisé
III.2. Coûts des accidents du
travail
III.2.a. Coûts directs et coûts
indirects
Une manière fréquemment utilisée pour
classer les coûts des accidents du travail est de distinguer les
coûts selon qu'ils sont directs ou indirects. Trois typologies les plus
connues seront évoquées dans cette section.
Les coûts directs représentent
généralement les frais qui sont enregistrés dans le
système comptable de l'entreprise, c'est-à-dire les sommes qui
doivent être engagées à la suite d'accidents alors que les
coûts indirects décrivent les pertes subies par l'entreprise
à la suite d'un accident de travail, mais qui ne sont pas
nécessairement comptabilisées comme telles.
Bon nombre d'auteurs ont évalué ces coûts
en adoptant cette distinction sans toutefois utiliser une définition
commune des termes coûts directs et coûts indirects. HEINRICH
(1931) a été l'un des premiers à mettre en évidence
la présence de coûts cachés non comptabilisés par
l'employeur. Il a identifié les événements entourant un
accident et ayant des répercussions économiques permettant ainsi
d'identifier et de comparer les coûts directs et indirects. Les
composantes de ces deux types de coûts figurent au tableau 1. Heinrich
parvient à la conclusion que les coûts indirectement
générés par les accidents de travail sont quatre fois plus
élevés que les coûts directs.
Mais, ce ratio coûts indirects/directs de 4 / 1 n'est
qu'une moyenne de sommes (des coûts directs et indirects) sans aucune
autre analyse statistique ce qui ne permet pas de vérifier la
stabilité du ratio par exemple, selon le secteur de l'entreprise ou le
type d'accidents.
Typologie des coûts de Heinrich :
Coûts directs
|
Coûts indirects
|
§ Indemnisations
§ Hospitalisation
§ Soins médicaux dispensés à la
victime
|
§ Temps rémunéré et non
travaillé par l'accidenté et les autres employés
§ Temps perdu des intervenants dans l'accident
§ ·Dommages causés
§ Interruption de production
§ Avantages sociaux payés sans production
§ Perte de profits
§ Salaire versé à l'accidenté avec
production réduire
§ Perte de moral et de motivation
§ Charges d'électricité
§ Chauffage et location
|
LaBelle (2000) distingue lui aussi les coûts directs des
coûts indirects comme l'illustre le tableau suivant. Selon lui, les
coûts directs sont des charges monétaires actuelles attribuables
aux accidents alors que les coûts indirects représentent des
coûts en termes de temps et de ressources non monétaires. Tous les
éléments figurant dans ce tableau entrent en ligne de compte pour
déterminer le coût total des accidents de travail.
Coûts directs
|
Coûts indirects
|
§ Indemnisations des travailleurs
§ Traitements médicaux
§ Services d'ambulance
§ Tests de médicaments
§ Adaptation du travail
§ Achats d'équipements neufs
§ Matériels pour les soins médicaux sur le
lieu de travail
|
§ Soins de santé professionnelle
§ Blessures des travailleurs
§ Suivi des victimes
§ Retour au travail
§ Perte de productivité
§ Compte rendu des incidents
§ Ressources humaines
§ Coût d'embauche
§ Suivi du manager
§ Retards de production
§ Sécurité
§ Formation
§ Aspect légal
|
III.2.b. Coûts
économiques et sociaux
Les accidents de travail présentent plusieurs
coûts économiques et sociaux, que regroupe le tableau
ci-dessous.
Coût pour l'employeur
|
Coûts pour l'état
|
Coût pour la communauté
|
§ Paiement pour maladie en vertu du contrat de travail
§ Indemnités versées en vertu des obligations
légales
§ Coût de remplacement pour un nouvel
employé
§ Pertes pour l'usine suite à l'accident
§ Coût supplémentaire d'assurance des
travailleurs
§ Coût provenant d'une baisse de moral des
travailleurs
|
§ Indemnités versées dans le cade des
accidents
§ Montant d'éventuelles indemnités
supplémentaires
§ Coût de l'hôpital et des autres traitements
médicaux
§ Perte de taxes future de la victime
§ Perte de taxe due à une baisse de la
profitabilité de l'employeur
|
§ Coûts des enquêtes et des plaintes dans la
mesure où elles sont subies par l'employeur
§ Perte nette sur les biens et services fournis par la
victime
§ Coût subis par la victime, les amis, la famille, les
compagnies d'assurance et autres acteurs économiques
|
III.3.Panneaux de signalisation de santé et
de sécurité au travail
En fonction du risque relatif à chaque machine et
chaque produit chimique existant dans la CBGN, des panneaux de signalisation
doivent être placé pour que les opérateurs prennent leurs
précautions nécessaires.
III.3.a. signalisations
d'obligations.
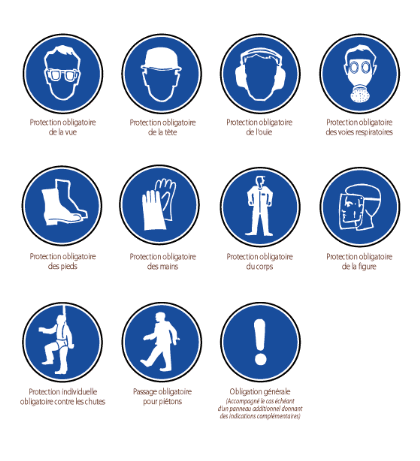
III.3.b. Signalisations
d'interdictions
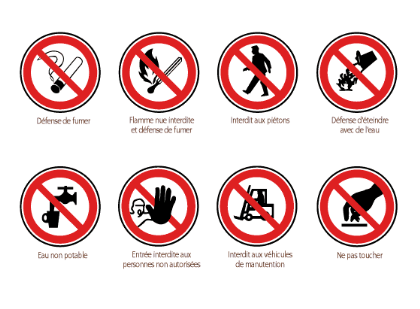
III.3.c. signalisation matériel
incendie
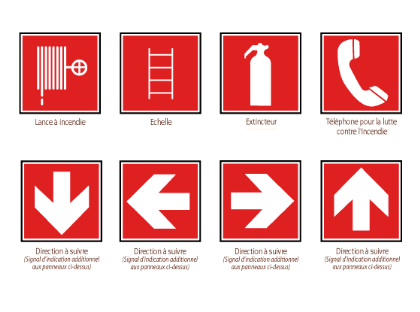
III.3.d. Sauvetage et Secours
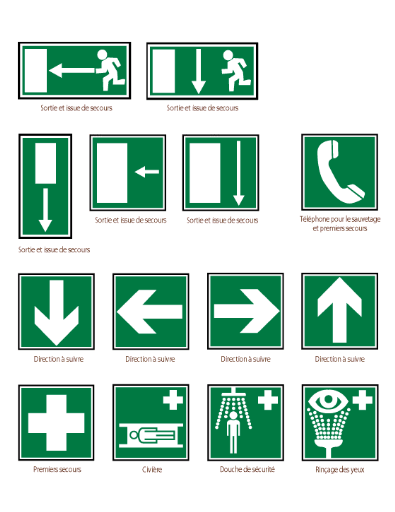
III.3.e. signalisation
avertissement
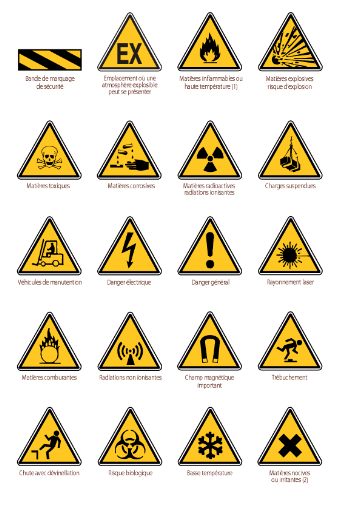
III.3.f. signalisation risques produits
chimiques
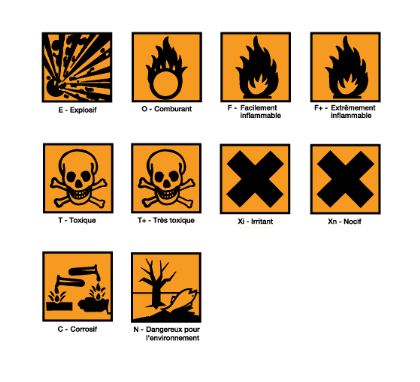
III.3.g. Phrases R et S
La caractérisation des risques se fait également
par l'indication des symboles de danger avec des désignations de danger,
des phrases de risque (phrases R) et des conseils de prudence (phrases S).
Phrases R
|
Phrases S
|
R 1 Explosif à l'état sec. R 2 Risque
d'explosion par le choc, la friction, le feu ou d'autres sources
d'ignition. R 3 Grand risque d'explosion par le choc, la friction, le feu ou
d'autres sources d'ignition. R 4 Forme des composés
métalliques explosifs très sensibles. R 5 Danger d'explosion
sous l'action de la chaleur. R 6 Danger d'explosion en contact ou sans
contact avec l'air. R 7 Peut provoquer un incendie. R 8 Favorise
l'inflammation des matières combustibles. R 9 Peut exploser en
mélange avec des matières combustibles. R 10 Inflammable. R
11 Facilement inflammable. R 12 Extrêmement inflammable. R 14
Réagit violemment au contact de l'eau. R 15 Au contact de l'eau,
dégage des gaz extrêmement inflammables R 16 Peut exploser en
mélange avec des substances comburantes. R 17 Spontanément
inflammable à l'air. R 18 Lors de l'utilisation, formation possible
de mélange vapeur-air inflammable/explosif. R 19 Peut former des
peroxydes explosifs. R 20 Nocif par inhalation. R 21 Nocif par contact
avec la peau. R 22 Nocif en cas d'ingestion. R 23 Toxique par
inhalation. R 24 Toxique par contact avec la peau. R 25 Toxique en cas
d'ingestion. R 26 Très toxique par inhalation. R 27 Très
toxique par contact avec la peau. R 28 Très toxique en cas
d'ingestion. R 29 Au contact de l'eau, dégage des gaz toxiques. R
30 Peut devenir facilement inflammable pendant l'utilisation. R 31 Au
contact d'un acide, dégage un gaz toxique. R 32 Au contact d'un
acide, dégage un gaz très toxique. R 33 Danger d'effets
cumulatifs. R 34 Provoque des brûlures. R 35 Provoque de graves
brûlures. R 36 Irritant pour les yeux. R 37 Irritant pour les voies
respiratoires. R 38 Irritant pour la peau. R 39 Danger d'effets
irréversibles très graves. R 40 Possibilité d'effets
irréversibles. R 41 Risque de lésions oculaires graves. R
42 Peut entraîner une sensibilisation par inhalation. R 43 Peut
entraîner une sensibilisation par contact avec la peau. R 44 Risque
d'explosion si chauffé en ambiance confinée. R 45 Peut causer
le cancer. R 46 Peut causer des altérations génétiques
héréditaires. R 47 Peut causer des malformations
congénitales R 48 Risque d'effets graves pour la santé en cas
d'exposition prolongée. R 49 Peut causer le cancer par
inhalation. R 50 Très toxique pour les organismes aquatiques. R 51
Toxique pour les organismes aquatiques. R 52 Nocif pour les organismes
aquatiques. R 53 Peut entraîner des effets néfastes à
long terme pour l'environnement aquatique R 54 Toxique pour la flore. R
55 Toxique pour la faune. R 56 Toxique pour les organismes du sol. R 57
Toxique pour les abeilles. R 58 Peut entraîner des effets
néfastes à long terme pour l'environnement. R 59 Dangereux
pour la couche d'ozone. R 60 Peut altérer la fertilité. R
61 Risque pendant la grossesse d'effets néfastes pour l'enfant. R 62
Risque possible d'altération de la fertilité. R 63 Risque
possible pendant la grossesse d'effets néfastes pour l'enfant. R 64
Risque possible pour les bébés nourris au lait maternel. R 65
Nocif : peut provoquer une atteinte des poumons en cas d'ingestion. R 66
L'exposition répétée peut provoquer dessèchement ou
gerçures de la peau. R 67 L'inhalation de vapeurs peut provoquer
somnolence et vertiges. R 68 Possibilité d'effets
irréversibles
|
S 1 Conserver sous clé. S 2 Conserver hors de la
portée des enfants. S 3 Conserver dans un endroit frais. S4
Conserver à l'écart de tout local d'habitation. S 5 Conserver
sous ... (liquide approprié à spécifier par le
fabricant). S 6 Conserver sous ... (gaz inerte à spécifier par
le fabricant). S 7 Conserver le récipient bien fermé. S 8
Conserver le récipient à l'abri de l'humidité. S 9
Conserver le récipient dans un endroit bien ventilé. S 12 Ne
pas fermer hermétiquement le récipient. S 13 Conserver
à l'écart des aliments et boissons y compris ceux pour
animaux. S 14 Conserver à l'écart des ... (matière(s)
incompatible(s) à indiquer par le fabricant). S 15 Conserver à
l'écart de la chaleur. S 16 Conserver à l'écart de
toute flamme ou source d'étincelles - Ne pas fumer. S 17 Tenir
à l'écart des matières combustibles. S 18 Manipuler et
ouvrir le récipient avec prudence. S 20 Ne pas manger et ne pas boire
pendant l'utilisation. S 21 Ne pas fumer pendant l'utilisation. S 22 Ne
pas respirer les poussières. S 23 Ne pas respirer les gaz/vapeurs/
fumées/aérosols (terme(s) approprié(s) à indiquer
par le fabricant). S 24 Eviter le contact avec la peau. S 25 Eviter le
contact avec les yeux. S 26 En cas de contact avec les yeux, laver
immédiatement et abondamment avec de l'eau et consulter un
spécialiste. S 27 Enlever immédiatement tout vêtement
souillé ou éclaboussé. S 28 Après contact avec
la peau, se laver immédiatement et abondamment avec ... (produits
appropriés à indiquer par le fabricant). S 29 Ne pas jeter les
résidus à l'égout. S 30 Ne jamais verser de l'eau dans
ce produit. S 33 Eviter l'accumulation de charges
électrostatiques. S 35 Ne se débarrasser de ce produit et de
son récipient qu'en prenant toute précaution d'usage. S 36
Porter un vêtement de protection approprié. S 37 Porter des
gants appropriés. S 38 En cas de ventilation insuffisante, porter un
appareil respiratoire approprié. S 39 Porter un appareil de
protection des yeux/du visage. S 40 Pour nettoyer le sol ou les objets,
souillés par ce produit, utiliser ... (à préciser par le
fabricant). S 41 En cas d'incendie et/ou d'explosion ne pas respirer les
fumées. S 42 Pendant les fumigations/pulvérisations porter un
appareil respiratoire approprié (terme(s) approprié(s) à
indiquer par le fabricant). S 43 En cas d'incendie utiliser... (moyens
d'extinction à préciser par le fabricant. Si l'eau augmente les
risques, ajouter "Ne jamais utiliser d'eau "). S 44 En cas de malaise,
consulter un médecin (si possible lui montrer l'étiquette) S
45 En cas d'accident ou de malaise consulter immédiatement un
médecin (si possible lui montrer l'étiquette). S 46 En cas
d'ingestion consulter immédiatement un médecin et lui montrer
l'emballage ou l'étiquette. S 47 Conserver à une
température ne dépassant pas ... °C (à
préciser par le fabricant). S 48 Maintenir humide avec... (moyen
approprié à préciser par le fabricant). S 49 Conserver
uniquement dans le récipient d'origine. S 50 Ne pas mélanger
avec ... (à spécifier par le fabricant). S 51 Utiliser
seulement dans des zones bien ventilées. S 52 Ne pas utiliser sur de
grandes surfaces dans les locaux habités. S 53 Eviter l'exposition,
se procurer des instructions spéciales avant l'utilisation. S 56
Eliminer ce produit et son récipient dans un centre de collecte des
déchets dangereux ou spéciaux. S 57 Utiliser un
récipient approprié pour éviter toute contamination du
milieu ambiant. S 59 Consulter le fabricant ou le fournisseur pour des
informations relatives à la récupération ou au
recyclage. S 60 Eliminer le produit et son récipient comme un
déchet dangereux. S 61 Eviter le rejet dans l'environnement.
Consulter les instructions spéciales/la fiche de données de
sécurité. S 62 En cas d'ingestion, ne pas faire vomir :
consulter immédiatement un médecin et lui montrer l'emballage ou
l'étiquette. S 63 En cas d'accident par inhalation, transporter la
victime hors de la zone contaminée et la garder au repos. S 64 En cas
d'ingestion, rincer la bouche avec de l'eau (seulement si la personne est
consciente).
|
III.4. Les équipements de
protection
III.4.a. Protection
collectives
Les protections collectives sont
votre meilleure assurance contre les accidents du travail et les maladies
professionnelles.
Assurez-vous toujours :
Ø De leur mise en place correcte, en
particulier de celle des écrans prévus sur les machines
(souffleuses, laveuses...etc.) pour vous protéger des pièces en
mouvement et du bruit ;
Ø De leur bon fonctionnement, en
particulier de celui des installations d'aspiration, de pulvérisation et
d'humidification qui réduisant le taux d'empoussièrement.
III.4.b. Les équipements de protection
individuelle
GANTS
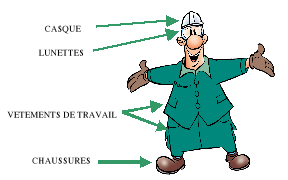
Un équipement de protection individuelle (EPI) est une
protection concernant un individu contre un risque donné, et selon
l'activité qu'il sera amené à exercer. D'une
manière générale, l'ensemble du corps peut et doit
être protégé, l'opérateur dans la CBGN doit porter
ces EPI relatives à la tache qu'il exécute.
Les opérateurs dans la CBGN doivent
être protégés en portant :
Ø Un casque et des chaussures de sécurité
toujours et partout ;
Ø Des lunettes de protection ;
Ø Des gants ;
Ø Un casque antibruit ou des bouchons d'oreille
à tous les postes bruyants ;
Ø Un masque antipoussières pour intervenir dans
les atmosphères empoussiérées ;
Ø Un harnais de sécurité pour certains
travaux en hauteur, en observant les conditions d'utilisation définies
par leur responsable ;
Ø Un gilet de sauvetage pour les travaux sur l'eau.
Les opérateurs dans la CBGN doivent
être protéger en portant :
Ø Un casque et des chaussures de sécurité
toujours et partout.
Ø Des lunettes de protection.
Ø Des gants.
Ø Un casque antibruit ou des bouchons d'oreille
à tous les postes bruyants :
Ø Un masque antipoussières pour intervenir dans
les atmosphères empoussiérées.
Ø Un harnais de sécurité pour certains
travaux en hauteur, en observant les conditions d'utilisation définies
par votre responsable.
Ø Un gilet de sauvetage pour les travaux sur l'eau.
III.5. Précautions d'utilisation de
certains produits chimiques utilisés au niveau de la
CBGN.
III.5.a. Eau de javel
Avertissement :
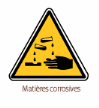
Stockage et manutention :
Ø Stocker le récipient bien fermé à
l'abri de la lumière.
Ø Température de stockage moins de 15 °C,
risque de décomposition avec formation de produits gazeux, surtout en
cas de stockage prolongé.
Ø Fermer les récipients de façon à
permettre à la pression intérieure de s'échapper (par
exemple valve de suppression).
Ø Pas de récipient en métal.
Protection individuelle :
En cas normale :
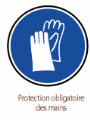
En cas de déversement :
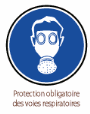
Premiers secours :
Ø En cas d'inhalation, faire respirer l'air frais,
consulter un médecin.
Ø En cas de contacte avec la peau, laver abondamment avec
l'eau, tomponner au polyéthylène glycol 400, enlevé
immédiatement tous vêtements souillé.
Ø En cas de contacte avec les yeux, rincer abondamment
avec de l'eau durant au moins 10 min, en maintenant les paupières
écartées, consulter immédiatement un ophtalmologiste.
Ø En cas d'injection, faire boire du jus de citron, du
vinaigre ou des oeufs crus mélangés avec du lait, puis beaucoup
d'eau, ne pas tenter de faire vomir.
III.5.b. charbon actif
Avertissement :
Produit non considéré comme dangereux.
Stockage et manutention :
Ø Bien fermé à l'abri de
l'humidité, température de stockage sans limites.
Ø N.B : lors du changement du filtre s'assurer est
aérée et la personne de deux personnes est obligatoire.
Protection individuelle :
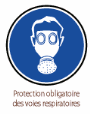
Premiers secours :
Ø Eviter la formation de poussière, ne pas
inhaler les poussières.
Ø Lors du nettoyage, récupérer à
l'état sec, acheminer vers l'alimentation, nettoyer.
III.5.c. hyflo supercel (la
celite)
Avertissement :
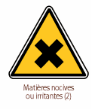
Protection individuelle :
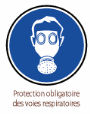
Premiers secours :
Ø En cas de contacte avec le peau, laver avec de l'eau
et du savon et laver soigneusement.
Ø En cas de contacte avec les yeux laver abondamment et
longuement à l'eau courante, si des spytrômes persistant,
consulter un médecin.
Ø En cas d'ingestion, rincer la bouche puis boire de
l'eau.
Ø En cas d'inhalation, amener le sujet à l'air
libre, boire de l'eau et se moucher pour évacuer la poussière.
Ø En cas de déversement éviter la
formation des poussières et utiliser les aspirateurs ou balayer
après humidification.
III.6. Précaution d'emploie de certaines
machines
Voir paragraphe (II.3. Amélioration de la
qualité)
Remarques :
Ø Les ouvriers dans la CBGN ne sont pas bien
formés au niveau de la sécurité.
Ø Les accès limité dans l'entreprise ne
sont pas vraiment inaccessibles.
Ø Les stagiaires ne sont pas bien
protégés contre les risques et ne reçoivent pas des EPI
suffisants.
IV. Environnement
Notre environnement a énormément changé
depuis la révolution industrielle. La technologie a
amélioré la vie de l'homme de plusieurs façons, mais elle
a causé d'autres problèmes dont les effets ne furent apparents
qu'après bien des années. La disparition d'espèces
animales, la pollution...etc.
La protection de l'environnement occupe une place de choix
dans la stratégie de la CBGN. Cette préoccupation majeure a
conduit l'entreprise à mettre en place une politique volontariste
destinée à maîtriser l'impact de son activité
industrielle sur le milieu naturel, à mettre en oeuvre des conditions
d'exploitation sans risque pour le personnel et la population, et à se
mettre en conformité avec les standards nationaux et internationaux.
IV.1. quelques problèmes
environnementaux
IV.1.a. Effet de serre.
L'effet de serre est un processus naturel de
réchauffement de l'atmosphère, sur terre il intervient dans le
bilan radiatif, il est du aux gaz à effet de serre (GES) contenus dans
l'atmosphère.
IV.1.b. pollution de l'eau
La pollution de l'eau peut se présenter sous
différentes formes : chimique, bactériologique,
thermique, et
les eaux ou masses d'eau concernées peuvent être douces,
saumâtres ou salées, souterraines ou superficielles. Il peut
même s'agir de la pluie ou des rosées.
IV.1.c. Couche d'ozone
La couche d'ozone protège l'homme et la
planète, des ultraviolets nuisibles venant des rayons solaires. L'homme
est pourtant le premier ennemi de la couche d'ozone et il se met ainsi en
danger lui même, souvent sans le savoir réellement. Nous avons
tous une part de responsabilité dans cette menace. Il est ainsi
nécessaire de prendre en compte plus sérieusement les
problèmes liés à la couche d'ozone pour éviter aux
générations futures de subir les conséquences de nos actes
présents.
IV.1. Pollution provoqué par la
CBGN
Les activités de la CBGN représentes des
nuisances importantes à l'environnement, les déchets de
l'entreprises peut être classé comme suit :
IV.1.a.Dechets solides
Ø Les éclats de verre.
Ø Bouchons métalliques et plastiques.
Ø Les étiquette enlevés des bouteilles
lavées.
Ø Bouteilles en plastique mal soufflées.
Ø Préformes non soufflées.
IV.2.b. Déchets liquides
Ø Soude caustique.
Ø Eau de javel.
Ø Eau sale.
Ø Eau chaude.
Ø Effluent de régénération des
résines.
Ø Effluent de lavage des filtres.
IV.3.c.Dechets gazeux
Ø Fumés de chaudières.
Ø Vapeurs.
IV.2.lutte contre la pollution
IV.2.a. La pollution des eaux
Comme il est déjà indiqué, les effluents
de la CBGN présente des compositions diverses, la compagnie est en cours
d'étudier le projet de construction d'une installation de traitement
des effluents par les boues activés, c'est un traitement biologique
adéquat pour ce genre d'effluent.
IV.2.b. Les déchets
solides
D'après l'inventaire des
déchets solides, on peut classés ces déchets en trois
catégories :
Ø Les déchets métalliques comme les
bouchons.
Ø déchets en plastiques.
Ø Déchets en cartons.
Ø Déchets en verre.
Les déchets doivent d'être trié au niveau
de l'entreprise avant d'être envoyé suivant leurs natures vers les
centres de recyclage pour les déchets métalliques, plastiques et
cartons, et verre les décharges appropriées pour les
déchets en verre.
IV.2.c. les déchets
gazeux
Pour les émissions gazeuses provenant des
chaudières et de certaines machines, ils doivent être traiter dans
des filtres approprié pour diminué leur teneur en gaz toxiques et
à effet de serre.
Conclusion
Un stage dans une entreprise pour un
étudient est primordiale, puisque, le savoir acquit dans l'école
supérieure de technologie de Fès est accomplie avec un savoir
faire dans lequel intervient, le savoir étudié, la technologie,
l'organisation, la qualité, le milieu sociale, l'économie et la
communication.
Le résumé c'est une étape que
doit faire un étudiant désirant entrer dans la vis active avec
une vue claire sur le travail.
* * * * * * * * * * * *
Fin

|