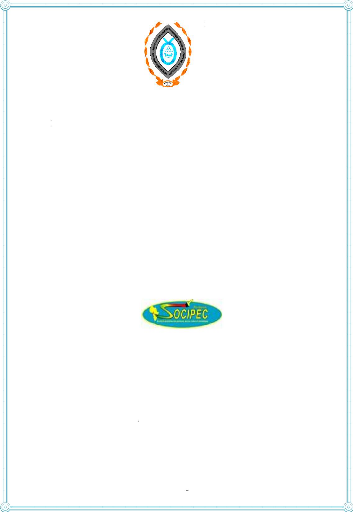
UNIVERSITE DE DSCHANG
REPUBLIQUE DU CAMEROUN Paix-Travail-Patrie
UNIVERSITY OF DSCHANG
INSTITUT UNIVERSITAIRE DE TECHNOLOGIE FOTSO VICTOR
REPUBLIC OF
CAMEROON Peace-Work-Fatherland
DEPARTEMENT DE GENIE MECANIQUE ET PRODUCTIQUE
MISE EN PLACE D'UNE POLITIQUE DE MAINTENANCE SUR
LES EQUIPEMENTS PERIPHERIQUES A LA PRODUCTION (GROUPE ELECTROGENE, GROUPE
DE PRODUCTION D'AIR COMPRIME, GROUPE DE FROID) EN VUE DE L'OPTIMISATION DE
LEUR DISPONIBILITE.
Projet de fin d'études effectué à la
Société Industrielle des Peintures, Encres, Colles et
Cosmétiques (SOCIPEC) de Douala du 10 novembre au 23 décembre
2011.
Par : TAMWO Francis
En vue de l'obtention de la Licence de Technologie
Mention Maintenance Industrielle et Productique
Sous l'encadrement de :
M. TATCHI Benoît
Responsable de production de SOCIPEC
- Dr. MTOPI FOTSO Blaise
Chargé de cours, IUT-FV de BANDJOUN
Année académique 2010-2011
Projet de fin d'études 2011
|
|
Projet de fin d'études 2011
|
|
DEDICACE
A ma tante SIKALI Elisabeth, mes soeurs GAMOGNE TAMWOUO
Gwladys et KAMNING TAMWOUO Edwige, qui m'aident tous les jours à donner
un sens à ma vie...
A TSEWOUO MAMBOU G, qui me donne l'énergie d'avancer
dans la bonne direction...
Projet de fin d'études 2011
|
|
REMERCIEMENTS
A l'issue de ce travail, je voudrais témoigner ma
gratitude à tous ceux qui de près ou de loin m'ont apporté
leur soutien. Plus particulièrement :
- Au Seigneur Dieu Tout Puissant pour toutes ses grâces
;
- A Prof. FOGUE Médard, Directeur de l'IUT FOTSO Victor de
Bandjoun;
- A notre Chef de département Dr. SOH FOTSING et notre
Enseignant Responsable Dr. MTOPI FOTSO, pour le sacrifice et les efforts
déployés pour le bon déroulement de nos enseignements,
afin que ces derniers soient de qualité ;
- A tous les Enseignants de l'IUT FOTSO Victor et
particulièrement ceux du Département du Génie
Mécanique et Productique ;
- A Monsieur TAGNE Chrétien, Directeur de SOCIPEC, pour
m'avoir donné l'opportunité d'effectuer un stage au sein de son
entreprise dans le cadre de notre projet de fin d'études, une fois de
plus merci ;
- A mon Encadreur professionnel Monsieur TATCHI Benoît,
pour son expertise, ses conseils et son encadrement ;
- A Madame ENANO Madeleine et Monsieur KAMGA NONO, pour leur
soutien ;
- A l'ensemble du Personnel de SOCIPEC pour son accueil
chaleureux et ses conseils ;
- A ma Tante Maman SIKALI Elisabeth, pour tout le sacrifice
qu'elle fait pour moi afin que
ma vie ait un sens ; merci infiniment maman ;
- A mes Soeurs jumelles GAMOGNE TAMWOUO Gwladys et KAMNING
TAMWOUO
Edwige pour leur soutien multidimensionnel et pour leur
compagnie, merci infiniment ; - A Mlle TSEWOUO MAMBOU G, pour tout son soutien
; merci infiniment ;
- A mes petits frères FOTSO KAMMOGNE, SIMO ARNAUD, SILA
ARNAUD, pour
l'accueil, l'hébergement et leur soutien durant mon stage;
merci beaucoup de courage !
- A toute ma famille et particulièrement à
Monsieur TAMO Christophe, Monsieur TAFFO
Blaise, Monsieur KENMOGNE Jacques, Monsieur KAM Michel ;
- Aux Mamans NEUKAM Delphine, FOKA Lucienne, TAMWOUO Madeleine,
pour leur soutien ;
- A ma bailleresse Maman Suzanne et à tous les habitants
de la Cité E (Chancelle, Carlos, Blaise, Georges, William) pour leur
compagnie et leur soutien;
- A mes amis FOTSO KAMBU, SADEU TAKAM, MBAH Kingsley, NDEMGNE
NGATCHESSI, FEUNIN Hugues ;
- A tous mes camarades de première promotion Licence MIP
particulièrement à Monsieur KAMDEM FOKOUA Blaise.
Projet de fin d'études 2011
|
|
AVANT-PROPOS
L'Institut Universitaire de Technologie FOTSO VICTOR de
BANDJOUN est l'un des établissements de
l'Université de DSCHANG né de la reforme
universitaire de 1993.
C'est une école qui forme en son sein des Techniciens
supérieurs en cycle de DUT et de BTS, et des agents de maîtrise en
cycle de Licence de technologie et de Licence Professionnelle. Elle regorge les
filières ci-après :
· En Cycle DUT :
- Maintenance Industrielle et Productique (MIP) ;
- Génie Informatique (GI) ;
- Génie Civil (GC) ;
- Génie de Télécommunications et
Réseaux (GTR) ;
- Génie Electrique option Electronique (EN) ;
- Génie Electrique option Electrotechnique (EL).
· En cycle BTS :
- Banque (BQ) ;
- Comptabilité et Gestion des Entreprises (CGE) ;
- Action Commerciale (AC) ;
- Secrétariat de Direction (SD) ;
- Génie Civil (GC) ;
- Génie Electrique option Electronique (EN) ;
- Génie Electrique option Electrotechnique (EL).
· En cycle de Licence de Technologie :
- Maintenance Industrielle et Productique (MIP) ;
- Génie Civil (GC) ;
- Génie Electrique (GE) ;
- Informatique et Réseaux (IR) ;
- Ingénierie des Réseaux et
Télécommunication (IRT).
· En cycle de Licence Professionnelle :
- Marketing Manager Opérationnel (MMO) ;
- Gestion Comptable et Financière (GCF) ;
- Banque et Gestionnaire des Relations Clientèles (BGRC)
;
- Gestion Administrative et Management des Organisations
(GAMO).
Projet de fin d'études 2011
|
|
En fin de cycle de Licence en maintenance industrielle et
productique, chaque étudiant doit effectuer un stage dans le cadre du
projet de fin d'études ; ce dernier permet d'une part à
l'étudiant de faire valoir ses acquis théoriques et pratiques
d'au moins 3 années d'études pour résoudre un ou plusieurs
problèmes posés par les industriels, et d'autre part à ces
derniers de bénéficier de ces résultats de recherche pour
la recherche du profit. C'est ainsi que nous avons effectué le notre
à la Société Industrielle des Peintures, Encres, Colles et
Cosmétiques (SOCIPEC) de Douala pendant la période allant du 10
novembre au 22 décembre 2011 sous le thème « Mise en
place d'une politique de maintenance sur les équipements
périphériques entrant dans le processus de production (Groupe
électrogène, groupe de froid et système de production et
de conditionnement de l'air comprimé) en vue de l'optimisation de leur
disponibilité ».
Projet de fin d'études 2011
|
|
Table des matières
DEDICACE i
REMERCIEMENTS ii
AVANT-PROPOS iii
RESUME vii
LISTE DES ABREVIATIONS viii
CAHIER DE CHARGES DU PROJET ix
INTRODUCTION 1
CHAPITRE I : PRESENTATION GENERALE DE L'ENTREPRISE 2
I- Historique 2
II- Missions 3
CHAPITRE II : PRESENTATION DES ASPECTS HUMAINS ET RELATIONNELS DU
CADRE DE TRAVAIL 4
I- Organigramme 4
II- Présentation des équipements
périphériques entrant dans le processus de production 5
CHAPITRE III : GENERALITES SUR LA MAINTENANCE [1] 6
Introduction : 6
3.1 Définition et Rôle de la maintenance 6
3.2 Place de la maintenance au sein de l'entreprise 7
3.3 Les différentes formes de maintenance 7
3.3.1 Les Concepts : 7
3.3.2 Les Méthodes 8
3.3.2.1 La maintenance corrective : 8
3.3.2.2 La maintenance préventive 9
a) Buts de la maintenance préventive 9
La maintenance préventive systématique : 9
La maintenance préventive conditionnelle : 10
La maintenance préventive prévisionnelle : 10
CHAPITRE IV : ETUDE ET MAINTENANCE DU SYSTEME DE PRODUCTION ET DE
CONDITIONNEMENT DE L'AIR COMPRIME 11
I- Système de production de l'énergie pneumatique
11
II- Système de conditionnement de l'air 12
1- Unité FRL 12
2- Sectionneur 12
III- Analyse fonctionnelle du système de production et de
conditionnement de l'air comprimé 13
IV- Analyse des modes de défaillances du système
14
Projet de fin d'études 2011
|
|
V- Plan de maintenance 15
1- Principales actions de maintenance 15
2- Plan de maintenance 16
3- Protocole de mise en marche, de contrôle et
d'arrêt des compresseurs [5] 17
CHAPITRE V : ETUDE ET MAINTENANCE DU GROUPE ELECTROGENE 18
I- Description fonctionnelle du groupe électrogène
18
1- Processus de transformation du groupe
électrogène 18
2- Description fonctionnelle 18
a) Problématique 18
b) L'analyse fonctionnelle 19
Le besoin : 19
Diagramme de pieuvre 19
L'analyse descendante SADT 20
Recherche des solutions technologiques méthodes FAST 20
II- Analyse des modes de défaillance type AMDEC 21
III- Procédure de maintenance curative. [4] 25
IV- Plan de maintenance du groupe électrogène [4]
28
1- Protocole de mise en marche et d'arrêt du groupe
électrogène 28
2- Planning de maintenance préventive du groupe
électrogène 28
3- Check-list 36 CHAPITRE VI : ETUDE ET MAINTENANCE DU GROUPE
DE PRODUCTION DE L'EAU
GLACEE 37
I- Découpage fonctionnel du système 37
II- Analyse des modes de défaillance du système
[3] 39
III- PLAN DE MAINTENANCE PREVENTIVE (INDICATIF) DU GROUPE DE
FROID 46
CHAPITRE VII : PERSPECTIVES ET SUGGESTIONS 47
I- Résultats 47
II- Remarques et suggestions 49
1- Remarques 49
2- Suggestions 51
CONCLUSION 52
BIBLIOGRAPHIE 53
ANNEXES 54
Projet de fin d'études 2011
|
|
RESUME
Ce projet de fin d'étude traite le problème
d'optimisation de la fonction maintenance par « l'élaboration d'un
plan de maintenance ». Il a pour objectif de cerner les différents
composants du processus de fabrication tout en cherchant celles qui
présentent les défaillances les plus critiques. Par la suite, il
consiste à identifier les organes élémentaires de ces
composantes qui portent préjudice au fonctionnement normal du
processus.
Les méthodes proposées ont pour but de focaliser
les efforts sur les défaillances des équipements qui causent la
majorité des effets nuisibles à la maintenance, à la
production et à la qualité. Elles reposent essentiellement sur
l'étude de la fiabilité des équipements et sur une analyse
type AMDEC. Ces techniques consistent non seulement à identifier les
anomalies et le dysfonctionnement du processus mais elles remontent
jusqu'à leurs causes profondes d'origine, puis suggèrent des
actions préventives et correctives appropriées.
La maintenance basée sur la fiabilité (MBF)
apparaît au premier abord comme principalement destinée à
élaborer un programme de maintenance préventive optimisé,
ayant pour but la sûreté de fonctionnement et la
sécurité des moyens de production en tenant compte des aspects
économiques. La suite de l'étude est de déterminer les
défaillances, les dysfonctionnements critiques et les périodes
d'intervention. La méthode a pour but non seulement de déterminer
les périodes des interventions et les causes d'origine, mais aussi de
chercher les solutions et engager les actions préventives et correctives
appropriées pour les éliminer et enfin généraliser
et standardiser les résultats à toutes les composantes similaires
des équipements périphériques que sont : le groupe
électrogène, le groupe de froid et le système de
production et de conditionnement de l'air comprimé.
Projet de fin d'études 2011
|
|
LISTE DES ABREVIATIONS
DUT : Diplôme Universitaire de Technologie
BTS : Brevet de Techniciens Supérieurs
AMDEC : Analyse des Modes de Défaillances, de leurs Effets
et de leurs Criticités SADT : Structured Analysis and Design Technic
FAST: Function Analysis System Technic
MIP: Maintenance Industrielle et Productique
ENSAI : Ecole Nationale des Sciences Agro-Industrielles
IUT : Institut Universitaire de Technologie
FRL : Filtre, Régulateur et Lubrificateur
FF : fluide frigorigène
SOCIPEC : Société Industrielle des Peintures,
Encres, Colles et Cosmétiques SABC : Société Anonyme des
Brasseries du Cameroun
FF HP : fluide frigorigène Haute pression
FF BP : fluide frigorigène Basse pression
Projet de fin d'études 2011
|
|
CAHIER DE CHARGES DU PROJET
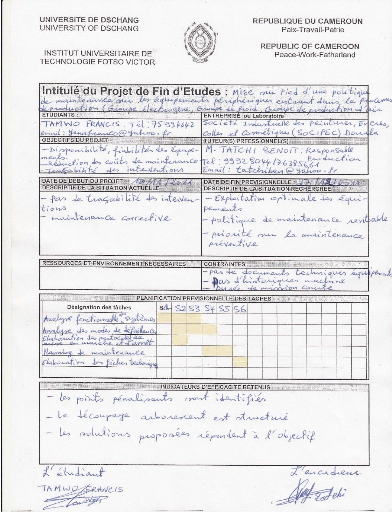
Projet de fin d'études 2011
|
|
INTRODUCTION
La maintenance industrielle, qui a pour vocation d'assurer le
bon fonctionnement des outils de production, est une fonction
stratégique dans les entreprises. Intimement liée à
l'incessant développement technologique, à l'apparition de
nouveaux modes de gestion, à la nécessité de
réduire les coûts de production, elle est en constante
évolution. Elle n'a plus aujourd'hui comme seul objectif de
réparer l'outil de travail mais aussi de prévoir et éviter
les dysfonctionnements. Ainsi la recherche des performances des systèmes
de production devenus complexes mène la fonction maintenance à
être responsable de la garantie de la disponibilité de tels
système. Cette garantie doit être assurée dans des
conditions financières optimales. En effet la concurrence est devenue de
plus en plus rude voire farouche, toutes les entreprises sont tenues à
appliquer la maintenance grâce aux objectifs qu'elle présente :
- Assurer la production prévue ;
- Maintenir le niveau de la qualité du produit
fabriqué ;
- Respecter les délais ;
- Respecter les objectifs humains : conditions de travail et de
sécurité ;
- Préserver l'environnement.
Dans ce contexte, l'élaboration d'un plan de
maintenance s'impose pour atteindre les objectifs prescrits avec des
coûts optimaux. Cette politique de maintenance exige la maîtrise et
l'optimisation des processus et des activités de production.
Le département production de la SOCIPEC a bien compris
cette politique. En effet, avant de proposer l'élaboration d'un plan de
maintenance, il a été question de faire une mise à jour
des fiches techniques de chaque machine. Comme l'outil de production comporte
plusieurs processus et activités, on ne peut pas leurs réserver
tous la même attention. Il convient donc d'identifier ceux qui sont
critique sur lesquels il faut agir en priorité. C'est ainsi que cette
priorité a été réservée aux
équipements périphériques à savoir : le groupe
électrogène, le groupe de froid et le système de
production et de conditionnement de l'air comprimé. Dans ce projet de
fin d'études, nous proposons une méthode d'élaboration
d'un plan de maintenance basée sur la théorie de la
fiabilité et une analyse typiquement AMDEC.
Ainsi, notre travail sera divisé en sept chapitres et
reparti comme suit :
- Les Chapitres I et II traiterons de la connaissance sur
l'entreprise;
- Le Chapitre III traitera des Généralités
sur la maintenance ;
- Les Chapitres IV, V et VI traiterons de l'Etude et la
maintenance du système de production et de conditionnement de l'air
comprimé, du groupe électrogène et du groupe de froid;
- et le dernier traitera des perspectives et suggestions.
Projet de fin d'études 2011
|
|
CHAPITRE I : PRESENTATION GENERALE DE
L'ENTREPRISE
I- Historique
Situé dans la zone industrielle de Bonamoussadi en face
du collège polyvalent BAHO, l'entreprise SOCIPEC
(Société Industrielle des Peintures, Encres et Colles)
voit le jour en juillet 2000 sous l'instigation de son promoteur M.TAGNE
CHRETIEN. En janvier 2005, elle absorbe TACICAM (Technique
Appliquée à la Chimie Industrielle au Cameroun),
entreprise spécialisée dans la fabrication et la
commercialisation des produits cosmétiques ; par cette opération,
elle devient Société industrielle des Peintures, Encres,
colles et cosmétiques (SOCIPEC). Initialement dotée d'un
capital de 100.000.000 de francs CFA, l'absorption entraîne le passage du
nouveau capital à 200.000.000 de francs CFA. Ceci étant,
l'entreprise a su rester fidèle à ses objectifs initiaux ;
notamment conquérir les 10% du marché sous régional et
améliorer constamment la qualité de ses produits. La
Société retient le slogan LA PEINTURE QUI DONNE DE
L'ECLAT PARTOUT

FICHE D'INDENTIFICATION
Raison sociale
|
Société Industrielle des Peintures, Encres, Colles
et Cosmétiques
|
Sigle
|
SOCIPEC
|
Siège social
|
Bonamoussadi-Douala
|
Capital
|
200.000.000 FCFA
|
Téléphone
|
(+237)33741133
|
Fax
|
(+237)33471967
|
Année de création
|
Janvier 2005
|
Registre de commerce
|
024886
|
Numéro de contribuable
|
MO70000010351U
|
Activités
|
Fabrication des produits cosmétiques et de peintures
|
Type
|
Société industrielle
|
Régime juridique
|
SARL
|
Régime d'imposition
|
Réel (IS)
|
Effectifs
|
65
|
Directeur Général
|
M.TAGNE CHRETIEN
|
Site
|
ZI de Bonamoussadi
|
Projet de fin d'études 2011
|
|
II- Missions
L'entreprise SOCIPEC a pour rôle principal la
fabrication des produits cosmétiques (eau de Cologne, savons de
toilette, glycérine, poudre, lait de toilette, produits capillaires),
des peintures, encres et colles (peinture bâtiment, carrosserie, colle
blanche, vernis, solvant et autre) ; la distribution-vente de ces produits.
Toutefois, l'entreprise peut aussi sous-traiter la fabrication d'emballages
plastiques et métalliques pour d'autres sociétés
industrielles. Les tableaux ci-dessous présentent quelques clients et
fournisseurs de l'entreprise :
FOURNISSEURS CLIENTS
FOURNISSEURS
|
matière livrée
|
Cameroun Continu
|
Entête de facture
|
Batoula
|
Sachets
|
Ecoquitance
|
Etiquettes
|
3TCAMEROUN
|
Transitaire
|
RN Graphic
|
Encre
|
PRODUITS
|
CLIENTS
|
Colle industrielle
|
MAYA ; CAMLAIT, etc.
|
Produits cosmétiques
|
supermarchés ; parfumeries
et instituts de beauté
|
Encres et Vernis
|
SAFCA ; MOONGA ; SOGEDI, etc.
|
Peinture
|
SHELL GABON ; CCF ;
SOQUICAM ; COGENI, etc.
|
Projet de fin d'études 2011
|
|
CHAPITRE II : PRESENTATION DES ASPECTS HUMAINS
ET RELATIONNELS DU CADRE DE TRAVAIL
I- Organigramme
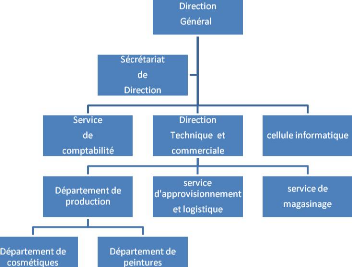
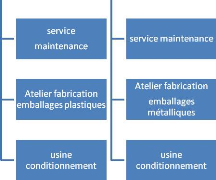
Fig1 : Organigramme de SOCIPEC
Projet de fin d'études 2011
|
|
II- Présentation des équipements
périphériques entrant dans le processus de
production
Ces équipements sont essentiellement critiques dans le
processus de production de SOCIPEC. Il s'agit entre autre :
- Du compresseur à air de marque Hydrovane 178 de
puissance 30kW, qui a pour rôle de produire
de l'énergie pneumatique, utilisée pour le
soufflage, le pompage et le nettoyage des pièces ;
- Du groupe électrogène de marque SDMO avec une
puissance apparente de 80kVA, qui a pour
rôle d'assurer la continuité de service en cas
d'interruption du réseau électrique ;
- De deux groupes de froid de marque CIAT mis en
parallèle de puissances 25 et 32 kW, qui ont pour rôle de produire
de l'eau glacée (à 5°C) pour le refroidissement des moules
montés sur les extrudeuses et presses à injection, et aussi pour
le refroidissement des zones de chauffe. Il est à noter qu'actuellement
il un seul groupe en état de fonctionnement.
Projet de fin d'études 2011
|
|
CHAPITRE III : GENERALITES SUR LA MAINTENANCE [1]
Introduction :
Pour être et demeurer compétitive, une entreprise
doit produire toujours mieux (qualité) et au coût le plus bas.
Pour minimiser ce coût, on fabrique plus vite et sans interruption des
produits, sans défaut afin d'atteindre la production maximale par
unité de temps. L'automatisation et l'informatique ont permis
d'accroître considérablement cette rapidité de production.
Cependant, les limitations technologiques des moyens de production ne
permettent pas d'augmenter les cadences.
De plus, produire plus sous-entend produire sans ralentissements,
ni arrêts. Pour cela, le système de production ne doit subir qu'un
nombre minimum de temps de non production. Exceptés les arrêts
inévitables dus à la production elle-même (changement de
production, montées en température, etc.), les machines ne
doivent jamais (ou presque) connaître de défaillances tout en
fonctionnant à un régime permettant le rendement maximal.
Cet objectif est un des buts de la fonction maintenance d'une
entreprise. Il s'agit de maintenir un bien dans un état lui permettant
de répondre de façon optimale à sa fonction.
3.1 Définition et Rôle de la
maintenance
L'AFNOR, par la norme NFX60-010, définit la maintenance
comme : « l'ensembles des actions permettant de maintenir ou de
rétablir un bien dans un état spécifié ou en mesure
d'assurer un service déterminé ».
La définition de la maintenance fait donc apparaître
3 notions :
- Maintenir qui suppose un suivi et une surveillance ;
- Rétablir qui sous-entendant l'idée d'une
correction de défaut ;
- Etat qui précise le niveau de compétences et les
objectifs attendus de la maintenance.
Dans une entreprise, quelque soit son type et son secteur
d'activité, le rôle de la fonction maintenance est donc de
garantie la plus grande disponibilité des équipements au
rendement meilleur tout en respectant le budget alloué.
Le service maintenance doit mettre en oeuvre la politique de
maintenance définie par la direction de l'entreprise ; cette politique
devant permettre d'atteindre le rendement maximal des systèmes de
production.
Projet de fin d'études 2011
|
|
3.2 Place de la maintenance au sein de l'entreprise
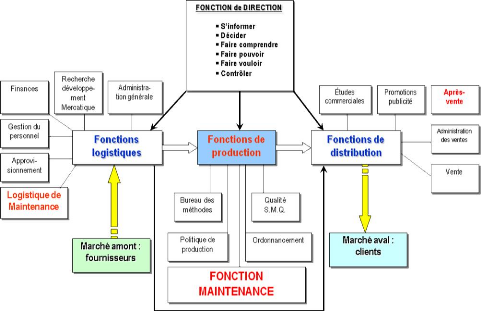
Projet de fin d'études 2011
|
|
3.3.2 Les Méthodes :
Le choix entre les méthodes de maintenance s'effectue dans
le cadre de la politique de la maintenance et doit s'opérer en accord
avec la direction de l'entreprise.
Pour choisir, il faut donc être informé des
objectifs de la direction, des directions politiques de maintenance, mais il
faut connaître le fonctionnement et les caractéristiques des
matériels, le comportement du matériel en exploitation, les
conditions d'application de chaque méthode, les coûts de
maintenance et les coûts de perte de production.
Le diagramme suivant synthétise selon la norme NF EN 13306
les méthodes de maintenance.
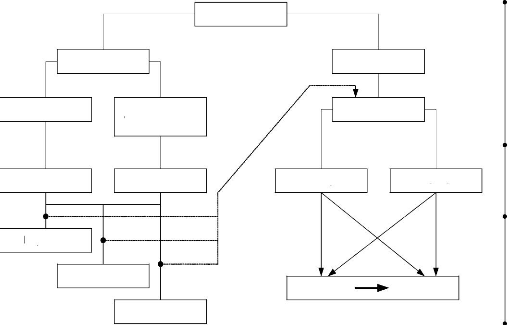
Methodes de maintenance
Evenements
Operations de
maintenance
MAINTENANCE
Visite
ECHEANCIER
Maintenance systématique
Inspection
Maintenance préventive
Contrôle
Maintenance conditionnelle ou prévisionnelle
ETAT DU BIEN
Défaillance partielle
Dépannage Réparation
DEFAILLANCE
Maintenance corrective
Panne
Fig 3 : les différents types de maintenance
3.3.2.1 La maintenance corrective :
Maintenance effectuée après apparition de la
panne.
Les défauts, pannes ou avaries diverses exigeant une
maintenance corrective entraînent une indisponibilité
immédiate ou à très brève échéance
des matériels affectés et/ou une dépréciation en
quantité et/ou qualité des services rendus.
Projet de fin d'études 2011
|
|
3.3.2.2 La maintenance préventive :
Maintenance exécutée à des intervalles
prédétermines ou selon des critères prescrits et
destinée à réduire la probabilité de
défaillance ou la dégradation du fonctionnement d'un bien
Elle doit permettre d'éviter les défaillances des
matériels en cours d'utilisation. L'analyse des coûts doit mettre
en évidence un gain par rapport aux défaillances qu'elle permet
d'éviter.
a) Buts de la maintenance préventive :
~ Augmenter la durée de vie des matériels
~ Diminuer la probabilité des défaillances en
service
~ Diminuer les temps d'arrêt en cas de révision ou
de panne
~ Prévenir et aussi prévoir les interventions
coûteuses de maintenance corrective
~ Permettre de décider la maintenance corrective dans de
bonnes conditions
~ Eviter les consommations anormales d'énergie, de
lubrifiant, etc.
~ Améliorer les conditions de travail du personnel de
production
~ Diminuer le budget de maintenance
~ Supprimer les causes d'accidents graves
La maintenance préventive systématique
:
Maintenance préventive exécutée à des
intervalles de temps préétablis ou selon un nombre défini
d'unités d'usage mais sans contrôle préalable de
l'état du bien.
Cette périodicité d'intervention est
déterminée à partir de la mise en service ou après
une révision complète ou partielle.
Remarque : de plus en plus, les
interventions de la maintenance systématique se font par échanges
standards.
Cas d'application :
o Equipements soumis à une législation en vigueur
(sécurité réglementée) : appareils de levage,
extincteurs, réservoirs sous pression, convoyeurs, ascenseurs,
monte-charge, etc.
o Equipements dont la panne risque de provoquer des accidents
graves : tous les matériels assurant le transport en commun des
personnes, avions, trains, etc.
o Equipement ayant un coût de défaillance
élevé : éléments d'une chaîne de production
automatisée, processus fonctionnant en continu (industries chimiques ou
métallurgiques).
o Equipements dont les dépenses de fonctionnement
deviennent anormalement élevées au cours de leur temps de service
: consommation excessive d'énergie, éclairage par lampes
usagées, allumage et carburation déréglés (moteurs
thermiques), etc.
Projet de fin d'études 2011
|
|
La maintenance préventive conditionnelle
:
Maintenance préventive basée sur une
surveillance du fonctionnement du bien et/ou des paramètres
significatifs de ce fonctionnement intégrant les actions qui en
découlent. La surveillance du fonctionnement et des paramètres
peut être exécutée selon un calendrier, ou à la
demande, ou de façon continue.
Remarque : la maintenance conditionnelle est donc une maintenance
dépendante de l'expérience et faisant intervenir des informations
recueillies en temps réel.
La maintenance préventive conditionnelle se
caractérise par la mise en évidence des points faibles. Suivant
le cas, il est souhaitable de les mettre sous surveillance et, à partir
de là, de décider d'une intervention lorsqu'un certain seuil est
atteint. Mais les contrôles demeurent systématiques et font partie
des moyens de contrôle non destructifs.
Tous les matériels sont concernés. Cette
maintenance préventive conditionnelle se fait par des mesures
pertinentes sur le matériel en fonctionnement.
Les paramètres mesurés peuvent porter sur :
o Le niveau et la qualité de l'huile
o Les températures et les pressions
o La tension et l'intensité des matériels
électriques o Les vibrations et les jeux mécaniques...
La surveillance est soit périodique, soit
continue.
Avantage : la connaissance du comportement se
fait en temps réel à condition de savoir interpréter les
résultats. A ce niveau, l'informatique prend une place primordiale.
Le matériel nécessaire pour assurer la maintenance
préventive conditionnelle devra être fiable pour ne pas perdre sa
raison d'être. Il est souvent onéreux, mais pour des cas bien
choisis il est rentabilisé rapidement.
Cette méthode de maintenance, pour être efficace,
doit dans tous cas être comprise et admise par les responsables de
production et avoir l'adhésion de tout le personnel.
Ces méthodes doivent être dans la mesure du possible
standardisées entre les différents secteurs (production et
périphériques) ; ce qui n'exclut pas l'adaptation essentielle de
la méthode au matériel.
Avec l'évolution actuelle des matériels et leurs
tendances à être de plus en plus fiables, la proportion des pannes
accidentelles sera mieux maîtrisée. La maintenance
préventive diminuera quantitativement d'une façon
systématique mais s'améliorera qualitativement par la maintenance
conditionnelle.
La maintenance préventive prévisionnelle
:
Maintenance conditionnelle exécutée en suivant les
prévisions extrapolées de l'analyse et de l'évaluation de
paramètres significatifs de la dégradation du bien.
Projet de fin d'études 2011
|
|
CHAPITRE IV : ETUDE ET MAINTENANCE DU SYSTEME
DE PRODUCTION ET DE CONDITIONNEMENT DE L'AIR
COMPRIME
I- Système de production de l'énergie
pneumatique
Elle est assurée par un compresseur de marque
HYDROVANNE178 de puissance 30 kW, animé par un moteur électrique.
Ce compresseur intégré est constitué d'un filtre, du
système de compression de l'air, d'un refroidisseur-assècheur et
d'un dernier filtre. La pression de sortie est de l'ordre de 10 bars. Un
réservoir permet de réguler la consommation.
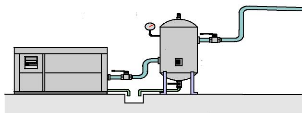
Compresseur intégré
Manomètre
Soupape de sécurité
SWP 10bar
Vanne de purge
Vanne d'isolement
Réservoir d'air
Conduite de distribution
Fig4 : système de production de l'air
comprimé [2]
Il est à noter que cet air, produit par ce compresseur
joue plusieurs rôles dans le processus de production de SOCIPEC. C'est
ainsi qu'on peut citer entre autre :
- Utilisé pour le soufflage des flacons et capsule (sur
les extrudeuses et presses à injection), les sérigrapheuses de
l'atelier de fabrication des emballages plastiques;
- Utilisé pour le pompage de la peinture, la colle
à l'atelier de peinture ;
- Utilisé aussi pour le conditionnement du lait de
toilette et le soufflage des pièces en atelier cosmétique.
Filtre Compresseur Refroidisseur Filtre
M
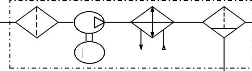
Air ambiant
Air comprime
Fig5 : Synoptique du compresseur intégré
[2]
Nous avons ci-dessous une vue détaillée de notre
compresseur intégré
Projet de fin d'études 2011
|
|
II- Système de conditionnement de l'air
Il est constitué d'une unité FRL (Filtre,
mano-Régulateur et Lubrificateur) et d'un sectionneur.
1- Unité FRL
Avant d'utiliser l'air, il faut le filtrer, l'assécher,
le graisser et réguler sa pression. Ainsi, avant chaque SAP
(Système Automatisé de Production), on place une unité de
conditionnement FRL (appelées aussi « Tête de ligne »)
qui adapte l'énergie pneumatique au système.Cette unité
FRL est constituée d'un Filtre, d'un
mano-Régulateur et d'un
Lubrificateur.
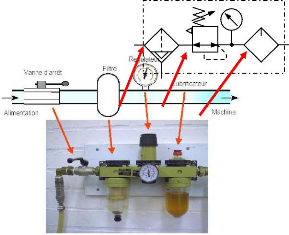
Fig6 : photo unité FRL[2] Le filtre sert à
assécher l'air et filtrer les poussières.
Le mano-régulateur sert à régler et
réguler la pression de l'air.
Le lubrificateur sert à éviter la corrosion et
à améliorer le glissement.
|
|
2- Sectionneur
Afin de mettre le système en ou hors énergie, on
utilise un sectionneur pneumatique. C'est une vanne de type 3/2, qui peut
être manoeuvrée manuellement ou électriquement. Son
rôle est d'isoler le circuit pneumatique du système par rapport
à la source, et de vider ce circuit lors de la mise hors
énergie.

Projet de fin d'études 2011
|
|
III- Analyse fonctionnelle du système de
production et de conditionnement de l'air comprimé
L'alimentation en air comprimé se fait en 2 temps :
produire de l'air comprimé pour l'entreprise (un compresseur
intégré marque Hydrovanne178) puis adapter cet air
comprimé à chaque machine.
Diagramme FAST de l'alimentation pneumatique
:
Alimenter
en énergie pneumatique
Produire de l'air comprimé
Adapter
l'air comprimé au système
|
Filtrer l'air
Comprimer l'air
Refroidir l'air
Assécher l'air
Stocker de l'air
Protéger le système
contre les
|
Filtrer l'air
Réguler la pression
Filtre
Compresseur
Refroidisseur
Sécheur
Réservoir
Pressostat

Filtre
Régulateur
Bloquer l'alimentation générale
Sectionneur ou vanne 3/2
Fig7 : Diagramme FAST du système de production et de
conditionnement de l'air comprimé
Projet de fin d'études 2011
|
|
IV- Analyse des modes de défaillances du
système
Dénomination
|
Défaillance
|
Cause de la défaillance
|
Intervention
|
Mesure préventive
|
Compresseur
|
Compresseur ne démarre pas
|
* pas de courant
* circuit de commande défectueux
* fusible détérioré
|
* mettre le courant
* changer le circuit de commande * changer le fusible
|
Prévoir un circuit de commande en stock. Prévoir
des fusibles en stock.
|
Défaut thermique moteur
|
Déclenchement de la protection thermique du moteur
électrique
|
* tension d'alimentation insuffisante
* surcharge du moteur *réglage de la protection
thermique
* roulement moteur
|
* vérifier la tension
* vérifier son branchement et la pression d'air
* vérifier la plage de réglage * vérifier
les roulements ou le graissage
* vérifier l'isolement
|
Prévoir la graisse en stock
|
Défaut température d'air
|
température finale inacceptable
|
* manque d'huile
* température ambiante trop élevée
* circuit d'huile obstrué
* vanne thermostatique bloquée * débit trop
faible
* colmatage de système de refroidissement.
|
* vérifier le niveau d'huile
* faire des ouvertures ou le
canalisation pour évacuer l'air chaud * vérifier le
circuit d'huile
* vérifier et nettoyer la vanne
* vérifier le débit
*examiner le système de refroidissement
|
|
Débit d'air
|
Débit d'air comprimé trop faible ou nul
|
* filtre à air obstrué
* le débit demandé est supérieur à
celui de compresseur
* l'électrovanne de régulation ne fonctionne pas
*manomètre mal régler
|
*nettoyer le filtre
* vérifier la consommation et fuites éventuelles
* vérifier la plage de réglage
* régler le manomètre
|
|
Pression de refoulement
|
Pression de refoulement trop faible
|
* manomètre mal régler
* le débit demandé est supérieur à
celui de compresseur
* clapet d'aspiration fermé
|
* régler le manomètre
* vérifier la consommation et fuites éventuelles
* vérifier l'électrovanne, manomètre,
clapet, vérifier la plage de réglage
|
|
Tableau1 : Analyse des défaillances du système
de production et de conditionnement de l'air comprimé
Projet de fin d'études 2011
|
|
V- Plan de maintenance
L'air comprimé est une des sources d'énergie
importantes d'un site industriel.
Tout arrêt de la production ou de la distribution d'air
comprimé entraîne l'immobilisation de tous les systèmes qui
y sont raccordés.
La durée de vie des systèmes dépend
essentiellement du respect de la qualité de l'air employé.
La production et la distribution font l'objet de plans de
maintenance fournis par le constructeur ou/et élaborés à
partir d'une analyse des modes de défaillance et de leur
criticité.
1- Principales actions de maintenance
systèmes
|
systématique
|
conditionnelle
|
observations
|
Les compresseurs
|
Changement:
-de pièces d'usure
-de soupapes de sécurité
|
Contrôle de la pression, de la température, de la
teneur en eau.
|
Les analyses vibratoires sont utiles suivant le type de
motocompresseur.
|
Les filtres
|
Remplacement en fonction des conditions d'utilisation.
|
Alarme de colmatage
|
Les filtres peuvent être équipés en by pass
en maintenance conditionnelle
|
La distribution
|
Vidange des purges manuelles
Contrôle des purges automatiques
|
Contrôle visuel des purges Contrôle de la teneur en
eau
|
Les purges automatiques sont des éléments
critiques.
|
Tableau2 : Actions de maintenance à effectuer sur
système de production et de conditionnement de
l'air comprimé
Consignes de sécurité [6]
Avant de travailler sur le compresseur :
- Couper l'alimentation secteur du compresseur.
- S'assurer qu'il n'ya pas de pression dans le compresseur ou la
tuyauterie.
- Ne jamais déposer le bouchon de remplissage d'huile
quand le compresseur est sous
pression.
Projet de fin d'études 2011
|
|
2- Plan de maintenance
Plan de maintenance préventive
|
|
Opération exécutable en
fonctionnement
|
Fréquence
|
Opérations
|
J
|
H
|
M
|
T
|
S
|
Purger la cuve du réservoir
|
x
|
|
|
|
|
Vérifier le niveau d'huile du compresseur
|
x
|
|
|
|
|
Contrôler la cartouche de filtre d'air
|
|
x
|
|
|
|
Nettoyer la cartouche de filtre d'air
|
|
x
|
|
|
|
Remplacer la cartouche de filtre d'air
|
|
|
x
|
|
|
Changer la cartouche de filtre d'huile
|
|
|
x
|
|
|
Nettoyer le filtre de retour d'huile
|
|
|
x
|
|
|
Contrôler l'étanchéité des raccords
|
|
|
x
|
|
|
Vérifier l'état des canalisations
|
|
|
|
x
|
|
Contrôler le système de refroidissement
|
|
x
|
|
|
|
Contrôler la soupape de sécurité
|
|
|
|
x
|
|
Graisser le palier du moteur
|
|
|
|
x
|
|
Vérifier le clapet d'aspiration
|
|
|
|
|
x
|
Vérifier l'état de l'accouplement
|
|
|
|
|
x
|
Nettoyer le dispositif de commande
|
|
|
x
|
|
|
Surveiller le bruit compresseur
|
x
|
|
|
|
|
Vérifier le robinet de vidange
|
x
|
|
|
|
|
Vérifier les fuites d'air
|
|
x
|
|
|
|
Vidanger l'huile
|
|
|
x
|
|
|
Nettoyer entre les ailettes du radiateur de refroidissement
d'huile
|
|
x
|
|
|
|
Tableau3 : planning de maintenance du système de
production et de conditionnement de l'air comprimé[6]
Remarque : J : opération à
réaliser chaque jour avant le démarrage
M : opérations à réaliser chaque mois (la
première semaine) T : opérations à réaliser chaque
trimestre
S : opérations à réaliser chaque semestre
;
H : opérations à réaliser chaque semaine.
Projet de fin d'études 2011
|
|
3- Protocole de mise en marche, de contrôle et
d'arrêt des compresseurs [5]
Procédure de démarrage :
Avant de procéder au démarrage d'un compresseur,
certaines mesures doivent être respectées afin d'éviter les
risques d'accident ou de bris d'équipement. Ces mesures sont les
suivantes :
Avant d'effectuer les vérifications suivantes, il faut
s'assurer que l'alimentation électrique du compresseur est interrompue
et cadenassée. On ne doit jamais tenir pour acquis qu'il est
sécuritaire de travail sur un compresseur qui n'est pas en
fonctionnement. En effet, un compresseur peut avoir un mode de
régulation intermittent et redémarrer à tout instant.
- Purger le récipient d'air de service ou bombonne
à l'aide du purgeur
- Fermer la vanne de sortie de la bombonne
- Ouvrir les vannes d'entrée de l'air
- s'assurer qu'il n'ya aucune pression à
l'intérieur du réservoir et du compresseur.
- vérifier le niveau d'huile.
- vérifier le bon état des raccords et conduits
pneumatiques.
- vérifier le bon état des soupapes de
sûreté en tirant l'anneau de ces dernières ou en actionnant
le levier.
Les soupapes de sûreté protègent les
différents composants d'un compresseur d'une surpression qui pourrait
leur être néfaste.
Les différents points à vérifier durant le
fonctionnement d'un compresseur sont :
- le fonctionnement adéquat de son mode de
régulation ;
- la présence de fuites d'huile ;
- la présence de fuites d'air.
Une fois les mesures et vérifications
complétées, on peut arrêter le compresseur en respectant la
procédure d'arrêt.
Procédure d'arrêt
Lors de l'arrêt d'un compresseur, afin d'éviter les
risques d'accident ou de bris d'équipement, il faut respecter les
mesures suivantes :
- Interrompre et cadenasser l'alimentation électrique du
compresseur ;
- Fermer le robinet d'isolement entre le compresseur et le
circuit pneumatique afin de prévenir un retour de pression vers le
compresseur ;
- Ouvrir la soupape de décharge afin de
dépressuriser le réservoir.
Projet de fin d'études 2011
|
|
CHAPITRE V : ETUDE ET MAINTENANCE DU GROUPE
ELECTROGENE
I- Description fonctionnelle du groupe
électrogène
Le groupe électrogène est un équipement
qui fournit de l'énergie électrique. En effet il transforme
l'énergie thermique du moteur en énergie électrique. Celui
objet de notre étude est de marque SDMO de puissance 80kVA. Elle est
constituée principalement d'un moteur thermique et d'un alternateur.

énergie électrique
Carburant
Moteur thermique
Energie mécanique
Alternateur
1- Processus de transformation du groupe
électrogène
2- Description fonctionnelle
a) Problématique
Etant donné :
- La coupure du courant électrique causée par la
maintenance des centrales, les tempêtes, surcharges ou autres
accidents...
- L'exigence de la continuité du courant
électrique
- Proposer des solutions susceptibles de mettre à la
disposition du client, l'énergie électrique, pendant la
coupure du courant électrique du réseau, en utilisant :
- L'outil de l'analyse fonctionnelle
- Les pré-requis sur la production d'énergie
électrique
- Les notions physiques.
Projet de fin d'études 2011
|
|
b) L'analyse fonctionnelle
Le besoin :
L'entreprise veut que l'énergie électrique soit
disponible dans tout le temps.
a) Diagramme de bête à cornes
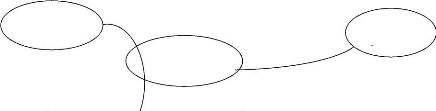
A qui rend- Sur quoi
t-il service ? agit-il ?
Le produit
Dans quel but le produit existe-t-il ?
Diagramme de pieuvre
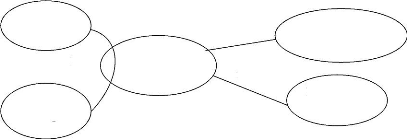
Energie électrique
SOCIPEC
FP1
Groupe électrogène
FC1
F
L'environnement
Réseau AES SONEL
Fig8 : Diagramme de Pieuvre du groupe
électrogène
Liste des fonctions de service
FP1
|
Produire l'énergie électrique
|
F
|
Etre adaptable au réseau électrique
|
FC1
|
Etre silencieux et non polluant
|
Projet de fin d'études 2011
|
|
L'analyse descendante SADT
Régler la tension
|
Régler la fréquence
|
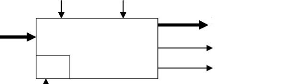
A-0
Produire
l'énergie électrique
Energie électrique
Echauffement Bruit, fumée
Carburant
Groupe électrogène
Fig9 : Diagramme SADT du groupe électrogène
Recherche des solutions technologiques méthodes
FAST
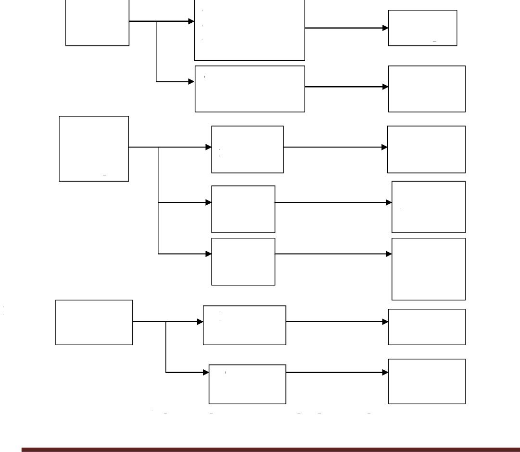
Convertir le carburant en
énergie mécanique (rotation)
Convertir l'énergie mécanique
en énergie électrique
Etre adaptable au réseau électrique
Fournir une puissance P suffisante
Alternateur de puissance suffisante
Avoir une tension U ajustable
Alternateur à excitation réglable
Avoir une fréquence f=50Hz
Moteur thermique à vitesse réglable
Etre silencieux et non polluant
Réduire le bruit
Traiter la fumée
Système silencieux
Système de traitement de fumée
Fig10 : Diagramme FAST du groupe électrogène
FC1
F
Produire l'énergie électrique
FP1
Moteur thermique
Machine synchrone Alternateur
Fonction de service
|
|
Fonction technologique
|
|
Solutions technologiques
|
|
|
|
|
Projet de fin d'études 2011
|
|
II- Analyse des modes de défaillance type
AMDEC
L'AMDEC est une méthode d'analyse de la fiabilité
qui permet de recenser les défaillances dont les conséquences
affectent le fonctionnement du système, dans le cadre d'une application
donné. La mise en oeuvre de l'AMDEC comporte :
> Une phase préliminaire, pour définir les
limites de l'étude et constituer le groupe de travail ;
> L'analyse des défaillances : qui se fait par la
détermination des modes de défaillances, la recherche des causes
et l'inventaire des effets.
> Le calcul de la criticité.
La gravité des conséquences d'une
défaillance se mesure par la prise en compte de la fréquence
d'apparition des défaillances caractérisé par un taux de
défaillance, de la probabilité de non détection des causes
de défaillances et enfin de la gravité des effets de la
défaillance par rapport à la sécurité des personnes
et des biens, ou par rapport à l'importance des couts de
défaillance.
A chaque critère est associé un coefficient dans
une échelle de valeurs préalablement établie : +
Fréquence : coefficient F
+ Non détection coefficient D
+ Gravité : coefficient G
FREQUENCE : F
|
1
|
1 défaillance maxi par an
|
2
|
1 défaillance maxi par trimestre
|
3
|
1 défaillance maxi par mois
|
4
|
1 défaillance maxi par semaine
|
NON DETECTION : D
|
1
|
Visible par l'opérateur
|
2
|
Détection aisée par un agent de maintenance
|
3
|
Détection difficile
|
4
|
Indécelable
|
GRAVITE (INDISPONIBILITE) : G
|
1
|
Pas d'arrêt de production
|
2
|
Arrêt =1 heure
|
3
|
1 heure < arrêt <1jour
|
4
|
Arrêt >1 jour
|
La criticité s'exprime par leur produit Criticité :
C = F*D*G
La valeur relative des criticités des différentes
défaillances permet de planifier les recherches d'amélioration en
commençant par celles qui ont la criticité la plus
élevée.
Projet de fin d'études 2011
|
|
Tableau4 : Analyse AMDEC
du groupe électrogène
Analyse des Modes de Défaillance et de leurs
Effets Critiques : AMDEC
|
Equipement : Groupe électrogène Marque
: SDMO
|
Système d'alimentation en
carburant
|
fonction
|
Mode de défaillance
|
Cause de la défaillance
|
Effet de la défaillance
|
Actions correctives
|
F
|
D
|
G
|
C
|
Pompe à injection
|
Alimentation des injecteurs
|
Le moteur ne démarre pas
|
Pompe d'injection défectueuse
|
Pompe ne débite pas
|
Réglage de la pompe d'injection
|
2
|
3
|
4
|
24
|
Excès de fumée noire
|
Débit d'injection trop grand,
|
Mauvaise combustion
|
3
|
3
|
4
|
36
|
Le moteur fume
|
Avance à l'injection
|
Compression faible
|
3
|
4
|
3
|
36
|
Injecteurs
|
Injection de carburant dans la pompe
|
Le moteur manque de puissance
|
Injecteur défectueux
|
Compression faible
|
Déposer l'injecteur, régler ou changer
l'injecteur
|
3
|
3
|
3
|
27
|
Le moteur ne démarre pas et fume noir
|
Mauvaise combustion
|
3
|
3
|
3
|
9
|
Projet de fin d'études 2011
|
|
Analyse des Modes de Défaillance et de leurs
Effets Critiques : AMDEC
|
Equipement : Groupe électrogène
Marque : SDMO
|
Système de lubrification
|
Fonction
|
Mode de défaillance
|
Cause de la défaillance
|
Effet de la défaillance
|
Actions correctives
|
F
|
D
|
G
|
C
|
Huile moteur
|
Lubrification, refroidissement, étanchéité
des composants
|
Consommation d'huile trop élevée
|
Viscosité de l'huile inappropriée
|
Remontée d'huile dans le cylindre
|
Vidangez, utiliser une huile dont l'indice de
viscosité est préconisé par le constructeur
|
2
|
3
|
1
|
8
|
Excès d'huile dans le moteur
|
Vidange jusqu'au niveau requis
|
2
|
1
|
1
|
2
|
Le moteur n'atteint pas son régime max
|
Niveau d'huile trop élevé,
|
Rétablissez le niveau
|
2
|
1
|
1
|
2
|
Le moteur chauffe
|
Huile usée
|
Mauvaise lubrification
|
Vidange, remplacement de l'huile
|
3
|
2
|
2
|
12
|
Crépine
|
Amorçage de la pompe à huile
|
La pompe n'aspire pas
|
Crépine colmatée
|
Débit et pression d'huile très faible
|
Nettoyage de la crépine
|
3
|
3
|
2
|
18
|
Projet de fin d'études 2011
|
|
Analyse des Modes de Défaillance et de leurs
Effets Critiques : AMDEC
|
Equipement : Groupe électrogène
Marque : SDMO
|
Système de démarrage et de
charge
|
Fonction
|
Mode de défaillance
|
Cause de la défaillance
|
Effet de la défaillance
|
Actions correctives
|
F
|
D
|
G
|
C
|
Alternateur
|
Générateur d'énergie
électrique, charge la batterie en permanence
|
Batterie déchargée
|
Alternateur défectueux
|
Démarrage impossible après arrêt
|
Remplacement de l'alternateur
|
3
|
2
|
3
|
18
|
Batterie
|
Stockage de l'énergie électrique pour le
démarrage
|
Batterie déchargée et ne se charge plus
|
Batterie défectueuse
|
Remplacement de la batterie
|
3
|
2
|
3
|
18
|
Démarreur
|
Entrainement du moteur en rotation
|
Le démarreur n'entraine pas le moteur
|
Démarreur défectueux
|
Remise en état de fonctionnement ou remplacement du
démarreur
|
2
|
3
|
2
|
12
|
Le démarreur ne s'arrête pas quand le moteur
est lancé
|
Remise en état de fonctionnement ou remplacement du
démarreur
|
3
|
3
|
3
|
27
|
Cosse
|
Raccordement des circuits électriques
|
Le démarreur n'entraine pas le moteur
|
Cosse de batterie sale ou desserré
|
Nettoyer les bornes et les cosses de la batterie. serrez
|
2
|
2
|
2
|
8
|
Projet de fin d'études 2011
|
|
III- Procédure de maintenance curative. [4]
- Groupe électrogène
Organes
|
Interventions à effectuer
|
Voyant de pression d'huile.
|
Ce voyant s'allume en cas de baisse anormale de la pression
d'huile. Il indique un incident de fonctionnement tel qu'un manque d'huile, une
défaillance du système de lubrification, ce défaut
arrête le GE.
|
Voyant de température du
système de refroidissement.
|
Ce voyant s'allume en cas d'élévation anormale
de la température du moteur. Il indique un incident de fonctionnement
tel qu'une perturbation du circuit d'air de refroidissement, une
température ambiante excessive, une charge excessive, d'où
arrêt instantané du GE
|
Voyant niveau du carburant.
|
|
Ce voyant s'allume lorsque le carburant atteint le niveau bas
du réservoir, il indique un manque de carburant mais ce défaut
n'arrête pas le GE.
|
Voyant charge batterie.
|
|
Ce voyant s'allume en cas d'incident de charge de(s)
batterie(s) pendant le fonctionnement du GE. Il met en évidence un
défaut du système de charge batterie. Ce défaut
n'arrête pas le GE. Allumé lors du démarrage du GE, ce
voyant d'éteint dès que l'alternateur a atteint sa vitesse
nominale.
|
Voyant de non démarrage.
|
|
Ce voyant s'allume après 3 à 6 tentatives de
démarrage non réussies.
|
Voyant de surcharge
Disjoncteur déclenché.
|
et
|
Ce voyant s'allume en cas de dépassement de la charge
nominale ou en cas de contrainte le disjoncteur déclenche
libérant ainsi le GE de sa charge. Lorsque le défaut
apparaît il convient de limiter la charge en débranchant quelques
appareils ou de supprimer le court-circuit puis réenclencher le
disjoncteur.
|
- Moteur
Symptôme
|
Problème
|
Solution
|
|
Démarrage incorrect.
|
Revoir la procédure de démarrage.
|
|
Pas de carburant.
|
S'assurer qu'il a du carburant dans le réservoir et que
le robinet d'arrêt manuel est ouvert.
|
|
Echappement obstrué.
|
Vérifier l'échappement et dégager
l'obstruction.
|
Le moteur tourne mais
|
Filtre à carburant colmaté ou plein
|
Remplacer le filtre ou vider l'eau.
|
ne démarre pas.
|
d'eau.
|
|
|
La pompe d'injection ne reçoit ni
|
Vérifier le débit de la pompe
|
|
carburant, ni air du circuit.
|
d'alimentation ou purger le circuit de carburant.
|
|
Pompe d'injection ou injecteurs
|
|
|
défectueux.
|
Réparer.
|
|
Démarrage incorrect.
|
Revoir la procédure de démarrage.
|
|
Pas de carburant.
|
Vérifier le réservoir.
|
|
Air dans les conduites de
|
Purge la conduite de carburant.
|
|
carburant.
|
Utiliser les dispositifs d'aide au
|
|
Temps froid.
|
démarrage par temps froid.
|
|
|
Voir si le démarreur ne tourne pas
|
|
Démarrage lent.
|
lentement.
|
|
|
Utiliser une huile de viscosité correcte.
|
|
Huile du carter moteur trop épais.
|
Consulter le fournisseur et changer de
|
|
Carburant de type incorrect.
|
carburant.
|
Le moteur démarre
|
|
Vidanger, rincer, remplir et purger le
|
Projet de fin d'études 2011
|
|
difficilement ou pas du tout.
|
Eau, saletés ou air dans le circuit de carburant.
Filtre à carburant colmaté. Injecteurs
encrassés ou
défectueux.
Le dispositif d'arrêt de la pompe d'injection ne se
réinitialise pas.
|
circuit.
Remplacer l'élément de filtre
Faire examiner soigneusement et
réparer.
Tourner le contact d'allumage sur
ARRET, puis sur MARCHE.
|
Cognements du moteur.
|
Niveau d'huile moteur insuffisant. Pompe d'injection
décalée.
Basse température de liquide de refroidissement.
Surchauffe du moteur.
|
Ajouter de l'huile dans le carter moteur. Examiner et
réparer.
Enlever et vérifier le thermostat.
Voir surchauffe du moteur.
|
Le moteur ne tourne pas régulièrement ou cale
fréquemment.
|
Basse température de liquide de refroidissement.
Filtre à carburant colmaté.
Eau, saletés ou air dans le circuit de carburant.
Injecteurs encrassés ou
défectueux.
|
Enlever et vérifier le thermostat.
Remplacer l'élément de filtre.
Vidanger, rincer, remplir et purger le circuit.
Faire examiner soigneusement et réparer.
|
Température du
moteur au-dessous de la normale
|
Thermostat défectueux
Thermostat ou transmetteur défectueux
|
Enlever et vérifier le thermostat.
Vérifier le thermomètre, le capteur et les
branchements.
|
Manque de puissance.
|
Moteur surchargé.
Obstruction de l'admission d'air. Filtre à carburant
colmaté. Carburant de type incorrect. Moteur surchauffé.
Température du moteur au-dessus de la normale.
Jeu des soupapes incorrect. Injecteurs encrassés ou
défectueux.
Pompe d'injection décalée. Fuite au joint du
collecteur d'échappement.
Flexible de carburant obstrué
|
Réduire la charge.
Effectuer l'entretien du filtre à air. Remplacer les
éléments du filtre à air. Utiliser le type de carburant
correct. Voir surchauffe moteur.
Enlever et vérifier le thermostat.
Démonter et régler selon le constructeur.
Démonter et régler selon le constructeur. Démonter et
régler selon le constructeur. Démonter et régler selon le
constructeur.
Le nettoyer ou le remplacer.
|
Basse pression d'huile.
|
Niveau du moteur insuffisant. Huile de type incorrect.
|
Ajouter de l'huile.
Vidanger le carter moteur et le remplir d'huile de
viscosité et de qualité correctes.
|
Consommation excessive d'huile
|
Huile du carter moteur trop fluide. Fuite d'huile.
Tube d'aération du carter moteur obstrué.
|
Utiliser de l'huile de viscosité correcte. Vérifier
les conduites, les joints et le bouchon de vidange.
Le nettoyer.
|
Le moteur émet de la fumée blanche.
|
Carburant de type incorrect. Température du moteur
insuffisante.
Thermostat défectueux.
|
Utiliser le type de carburant correct. Réchauffer le
moteur à la température normale de fonctionnement.
Enlever et vérifier le thermostat. Démonter et
régler selon le constructeur.
|
Projet de fin d'études 2011
|
|
|
Injecteurs défectueux. Moteur décalé.
|
Démonter et régler selon le constructeur
|
Le moteur émet de la
|
Carburant de type incorrect.
|
Utiliser le type de carburant correct.
|
fumée d'échappement
|
Filtre à air colmaté ou sale.
|
Effectuer l'entretien du filtre à air.
|
noire ou grise.
|
Moteur surchargé
|
Réduire la charge.
|
|
Injecteurs encrassés.
|
Démonter et régler selon le constructeur.
|
|
Moteur décalé.
|
Démonter et régler selon le constructeur
|
|
Moteur surchargé
|
Réduire la charge.
|
|
Niveau de liquide de
|
Remplir le radiateur jusqu'au niveau
|
|
refroidissement.
|
correct, vérifier que les connexions du radiateur et
des flexibles sont serrées et qu'elles ne fuient pas.
|
|
|
Faire vérifier par un technicien.
|
|
Bouchon du radiateur défectueux.
|
Vérifier le tendeur automatique et
|
|
Courroie trapézoïdale étirée ou
|
s'assurer que les courroies ne sont pas
|
Le moteur surchauffe.
|
tendeur de courroie défectueux.
|
étirées et les remplacer si nécessaire.
|
|
|
Vérifier le niveau d'huile. Ajouter de
|
|
Niveau d'huile moteur insuffisant.
|
l'huile selon le besoin.
|
|
|
Rincer le circuit de refroidissement.
|
|
Le circuit de refroidissement a
|
|
|
besoin d'être rincé.
|
Enlever et vérifier le thermostat.
|
|
Thermostat défectueux.
|
Vérifier la température de l'eau avec le
|
|
Thermomètre ou transmetteur
|
thermomètre et le remplacer si
|
|
défectueux.
|
nécessaire.
|
|
Carburant de type incorrect
|
Utiliser le type de carburant correct
|
- Batterie de démarrage
Défauts
|
Cause
|
Intervention
|
Batterie démarrage déchargé.
|
Niveau de l'électrolyte trop bas.
|
Refaire un appoint d'eau déminéralisée et
recharger
|
Câbles défectueux.
|
Nettoyer ou remplacer le câble et recharger la batterie.
|
Courroie du ventilateur détendue.
|
Retendre ou changer de courroie et recharger la batterie.
|
Batterie défectueuse.
|
Changer la batterie et recharger.
|
Régulateur de charge défectueux.
|
Remplacer l'alternateur et recharger la batterie.
|
Alternateur de charge défectueux.
|
Remplacer l'alternateur et recharger la batterie.
|
La batterie consomme trop d'eau.
|
Bac de batterie fendu.
|
Vérifier si le bac est humide et le remplacer selon le
besoin.
|
Batterie défectueuse.
|
Tester la batterie.
|
Taux de charge de la batterie trop élevé.
|
Tester le circuit de charge.
|
La batterie ne peut pas charger.
|
Connexions desserrées.
|
Nettoyer et resserrer les connexions.
|
Batterie sulfatée ou complètement usée.
|
Changer.
|
Courroie étirée ou tendeur de
courroie défectueux.
|
Régler la tension ou remplacer.
|
Tableau5 : procédure de maintenance curative du groupe
électrogène[5]
Projet de fin d'études 2011
|
|
IV- Plan de maintenance du groupe
électrogène [4]
1- Protocole de mise en marche et d'arrêt du groupe
électrogène
· Procédure de mise en marche.
- Remplir la fiche d'entretien journalier et
s'assurer que toutes les conditions sont réunies
- Vérifier la position du commutateur de
démarrage et du disjoncteur principal (celui de démarrage
à 0 et le disjoncteur désenclenché).
- Vérifier que le secteur AES SONEL est
isolé par la mise hors service de son disjoncteur.
- Mettre le groupe en marche en s'assurant
pendant quelques minutes (moins de 5 minutes) du bon fonctionnement par la
lecture des indicateurs.
- Mettre le disjoncteur du groupe en
service.
- Mettre le disjoncteur de l'arrivée
à l'armoire principal en marche.
- La ligne de transmission peut être
alimentée.
· Procédure de contrôle.
- Vérifier le comportement du groupe
après sa mise en marche en lui appliquant une charge. -
Vérifier la couleur de la fumée.
- Inspecter régulièrement afin de
s'assurer de la présence d'aucune anomalie.
- S'assurer que le groupe ne fonctionne pas
à vide, en dessous ou en dessus de la charge nominale pendant
longtemps.
· Procédure d'arrêt.
Ici on distingue deux types d'arrêt :
1. Arrêt d'urgence,
2. Arrêt normal.
Arrêt
Arrêt normal
Arrêt immédiat

+ Appuyer sur l'arrêt d'urgence.
+ Fin.
|
|
+ Délester le groupe.
+ Ouvrir le disjoncteur et appuyer sur le bouton arrêt
contacteur.
+ Laisser tourner le moteur à vide quelques minutes pour
le refroidissement et le ralentissement.
+ Arrêt moteur clé position 0.
+ Retirer la clé de contact.
+ Remettre le disjoncteur à l'arrêt
+ Fin.
|
|
|
2- Planning de maintenance préventive du groupe
électrogène
Projet de fin d'études 2011
|
|
Projet de fin d'études 2011
|
|
PLAN DE MAINTENANCE DU GROUPE ELECTROGENE
SDMO
|
PERIODICITE
|
module: moteur perkins et alternateur Leroy
somer
|
travail à effectuer
|
avant de d6marrer
|
durant le fonctionnement
|
chaque semaine
|
50 heures
|
100 heures
|
150 heures
|
200 heures
|
250 heures
|
300 heures
|
350 heures
|
400 heures
|
450 heures
|
500 heures
|
550 heures
|
600 heures
|
650 heures
|
700 heures
|
750 heures
|
800 heures
|
850 heures
|
900 heures
|
950 heures
|
1000 heures
|
visites
|
relevé compteur horaire
|
×
|
|
|
|
|
|
|
|
|
|
|
|
|
|
|
|
|
|
|
|
|
|
|
relevé appoint d'eau
|
×
|
|
|
|
|
|
|
|
|
|
|
|
|
|
|
|
|
|
|
|
|
|
|
relevé appoint d'huile
|
×
|
|
|
|
|
|
|
|
|
|
|
|
|
|
|
|
|
|
|
|
|
|
|
relevé couleur fumée
|
|
×
|
|
|
|
|
|
|
|
|
|
|
|
|
|
|
|
|
|
|
|
|
|
tours d'inspection
|
|
|
×
|
|
|
|
|
|
|
|
|
|
|
|
|
|
|
|
|
|
|
|
|
vérification chauffage moteur et alternateur
|
|
×
|
|
|
|
|
|
|
|
|
|
|
|
|
|
|
|
|
|
|
|
|
|
contrôle indication pression d'huile
|
|
×
|
|
|
|
|
|
|
|
|
|
|
|
|
|
|
|
|
|
|
|
|
|
vérification bruit moteur et alternateur
|
|
×
|
|
|
|
|
|
|
|
|
|
|
|
|
|
|
|
|
|
|
|
|
|
inspection fuites éventuelles
|
|
×
|
|
|
|
|
|
|
|
|
|
|
|
|
|
|
|
|
|
|
|
|
|
mesure tensions à vide
|
|
×
|
|
|
|
|
|
|
|
|
|
|
|
|
|
|
|
|
|
|
|
|
|
mesure fréquence à vide
|
|
×
|
|
|
|
|
|
|
|
|
|
|
|
|
|
|
|
|
|
|
|
|
|
chauffage du moteur
|
|
|
×
|
|
|
|
|
|
|
|
|
|
|
|
|
|
|
|
|
|
|
|
|
Tableau6 :Planning des visites du groupe
électrogène[4]
Projet de fin d'études 2011
|
|
PLAN DE MAINTENANCE DU GROUPE ELECTROGENE
SDMO
|
PERIODICITE
|
Module moteur perkins
|
travail à effectuer
|
avant de d6marrer
|
durant le fonctionnement
|
chaque semaine
|
50 heures
|
100 heures
|
150 heures
|
200 heures
|
250 heures
|
300 heures
|
350 heures
|
400 heures
|
450 heures
|
500 heures
|
550 heures
|
600 heures
|
650 heures
|
700 heures
|
750 heures
|
800 heures
|
850 heures
|
900 heures
|
950 heures
|
1000 heures
|
module: circuit d'alimentation
|
contrôle des fuites éventuelles de carburant
|
|
×
|
|
|
|
|
|
|
|
|
|
|
|
|
|
|
|
|
|
|
|
|
|
remplacement du filtre de carburant
|
|
|
|
|
|
|
|
|
|
|
|
|
×
|
|
|
|
|
|
|
|
|
|
×
|
vidange de l'eau et sédiments du réservoir
|
|
|
|
×
|
×
|
×
|
×
|
×
|
×
|
×
|
×
|
×
|
×
|
×
|
×
|
×
|
×
|
×
|
×
|
×
|
×
|
×
|
×
|
réglage du point d'injection
|
|
|
|
|
|
|
|
|
|
|
|
|
×
|
|
|
|
|
|
|
|
|
|
×
|
réglage de la pression d'injection
|
|
|
|
|
|
|
|
|
|
|
|
|
×
|
|
|
|
|
|
|
|
|
|
×
|
remplacement du préfiltre carburant
|
|
|
|
|
|
|
|
|
|
|
|
|
×
|
|
|
|
|
|
|
|
|
|
×
|
entretien de la pompe à carburant
|
|
|
|
|
|
|
|
|
|
|
|
|
|
|
|
|
|
|
|
|
|
|
|
nettoyage du filtre à carburant
|
|
|
|
|
×
|
|
×
|
|
×
|
|
×
|
|
×
|
|
×
|
|
×
|
|
×
|
|
×
|
|
×
|
|
|
|
|
|
|
|
|
|
|
|
|
|
|
|
|
|
|
|
|
|
|
|
|
|
|
|
|
|
|
|
|
|
|
|
|
|
|
|
|
|
|
|
|
|
|
|
|
Tableau 7 : Planning module alimentation du groupe
électrogène[4]
Projet de fin d'études 2011
|
|
PLAN DE MAINTENANCE DU GROUPE ELECTROGENE
SDMO
|
PERIODICITE
|
module: circuit d'huile
|
travail à effectuer
|
avant de d6marrer
|
durant le fonctionnement
|
chaque semaine
|
50 heures
|
100 heures
|
150 heures
|
200 heures
|
250 heures
|
300 heures
|
350 heures
|
400 heures
|
450 heures
|
500 heures
|
550 heures
|
600 heures
|
650 heures
|
700 heures
|
750 heures
|
800 heures
|
850 heures
|
900 heures
|
950 heures
|
1000 heures
|
changement de l'huile moteur
|
|
|
|
|
×
|
|
×
|
|
×
|
|
×
|
|
×
|
|
×
|
|
×
|
|
×
|
|
×
|
|
×
|
changement du filtre à huile
|
|
|
|
|
×
|
|
×
|
|
×
|
|
×
|
|
×
|
|
×
|
|
×
|
|
×
|
|
×
|
|
×
|
nettoyage du carter d'huile
|
|
|
|
|
×
|
|
×
|
|
×
|
|
×
|
|
×
|
|
×
|
|
×
|
|
×
|
|
×
|
|
×
|
entretien pompe à huile
|
|
|
|
|
×
|
|
×
|
|
×
|
|
×
|
|
×
|
|
×
|
|
×
|
|
×
|
|
×
|
|
×
|
contrôle des fuites éventuelles d'huile
|
|
×
|
|
|
×
|
|
×
|
|
×
|
|
×
|
|
×
|
|
×
|
|
×
|
|
×
|
|
×
|
|
×
|
contrôle du mano-contact pression d'huile
|
|
|
|
|
|
|
×
|
|
|
|
×
|
|
|
|
×
|
|
|
|
×
|
|
|
|
×
|
Tableau8 : Planning module circuit d'huile du groupe
électrogène[4]
Projet de fin d'études 2011
|
|
PLAN DE MAINTENANCE DU GROUPE ELECTROGENE
SDMO
|
PERIODICITE
|
module: moteur perkins
|
travail à effectuer
|
avant de d6marrer
|
durant le fonctionnement
|
chaque semaine
|
50 heures
|
100 heures
|
150 heures
|
200 heures
|
250 heures
|
300 heures
|
350 heures
|
400 heures
|
450 heures
|
500 heures
|
550 heures
|
600 heures
|
650 heures
|
700 heures
|
750 heures
|
800 heures
|
850 heures
|
900 heures
|
950 heures
|
1000 heures
|
organes électriques
|
entretien du démarreur
|
|
|
|
|
|
|
|
|
|
|
|
|
|
|
|
|
|
|
|
|
|
|
×
|
entretien de l'alternateur
|
|
|
|
|
|
|
|
|
|
|
|
|
|
|
|
|
|
|
|
|
|
|
×
|
vérification des serrages des
connexions électriques
|
|
|
|
|
|
|
×
|
|
|
|
×
|
|
|
|
×
|
|
|
|
×
|
|
|
|
×
|
vérification du niveau de l'électrolyte
|
|
|
|
×
|
×
|
×
|
×
|
×
|
×
|
×
|
×
|
×
|
×
|
×
|
×
|
×
|
×
|
×
|
×
|
×
|
×
|
×
|
×
|
Tableau 9: Planning module organes électriques du
groupe électrogène[4]
Projet de fin d'études 2011
|
|
PLAN DE MAINTENANCE DU GROUPE ELECTROGENE
SDMO
|
PERIODICITE
|
module: moteur perkins
|
travail à effectuer
|
avant de d6marrer
|
durant le fonctionnement
|
chaque semaine
|
50 heures
|
100 heures
|
150 heures
|
200 heures
|
250 heures
|
300 heures
|
350 heures
|
400 heures
|
450 heures
|
500 heures
|
550 heures
|
600 heures
|
650 heures
|
700 heures
|
750 heures
|
800 heures
|
850 heures
|
900 heures
|
950 heures
|
1000 heures
|
circuit de refroidissement
|
nettoyage des lamelles du radiateur
|
|
|
|
|
×
|
|
×
|
|
×
|
|
×
|
|
×
|
|
×
|
|
×
|
|
×
|
|
×
|
|
×
|
contrôle du thermostat
|
|
|
|
|
|
|
|
|
|
|
|
|
|
|
|
|
|
|
|
|
|
|
×
|
entretien pompe à eau
|
|
|
|
|
|
|
|
|
|
|
|
|
|
|
|
|
|
|
|
|
|
|
×
|
vidange et rinçage du circuit d'eau
|
|
|
|
|
|
|
|
|
|
|
|
|
|
|
|
|
|
|
|
|
|
|
×
|
contrôle tension courroie du ventilateur
|
|
|
|
|
|
|
|
|
|
|
|
|
|
|
|
|
|
|
|
|
|
|
×
|
remplacement de la courroie du ventilateur
|
|
|
|
|
|
|
|
|
|
|
|
|
×
|
|
|
|
|
|
|
|
|
|
×
|
contrôle du mano-contact température moteur
|
|
|
|
|
|
|
|
|
|
|
|
|
|
|
|
|
|
|
|
|
|
|
×
|
|
|
|
|
|
|
|
|
|
|
|
|
|
|
|
|
|
|
|
|
|
|
|
|
|
|
|
|
|
|
|
|
|
|
|
|
|
|
|
|
|
|
|
|
|
|
|
|
|
|
|
|
|
|
|
|
|
|
|
|
|
|
|
|
|
|
|
|
|
|
|
|
Tableau 10 : Planning module circuit de refroidissement du
groupe électrogène[4]
Projet de fin d'études 2011
|
|
module: moteur perkins
|
travail à effectuer
|
avant de d6marrer
|
durant le fonctionnement
|
chaque semaine
|
50 heures
|
100 heures
|
150 heures
|
200 heures
|
250 heures
|
300 heures
|
350 heures
|
400 heures
|
450 heures
|
500 heures
|
550 heures
|
600 heures
|
650 heures
|
700 heures
|
750 heures
|
800 heures
|
850 heures
|
900 heures
|
950 heures
|
1000 heures
|
bloc moteur et système
de distribution
|
contrôle et réglage du jeu des soupapes
|
|
|
|
|
|
|
|
|
|
|
|
|
×
|
|
|
|
|
|
|
|
|
|
×
|
contrôle du joint de culasse
|
|
|
|
|
|
|
|
|
|
|
|
|
×
|
|
|
|
|
|
|
|
|
|
|
vérification de la ligne d'échappement
|
|
|
|
|
|
|
×
|
|
|
|
×
|
|
|
|
×
|
|
|
|
×
|
|
|
|
×
|
nettoyage du filtre à air
|
|
|
|
|
×
|
|
×
|
|
×
|
|
×
|
|
×
|
|
×
|
|
×
|
|
×
|
|
×
|
|
×
|
resserrage des écrous et boulons du moteur
|
|
|
|
|
|
|
|
|
|
|
|
|
|
|
|
|
|
|
|
|
|
|
×
|
lavage du moteur
|
|
|
|
|
|
|
×
|
|
|
|
×
|
|
|
|
×
|
|
|
|
×
|
|
|
|
×
|
Tableau11 : Planning module système de distribution
du groupe électrogène[4]
Projet de fin d'études 2011
|
|
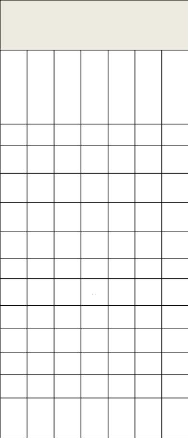
Périodicité
×
×
×
×
×
×
×
×
×
×
×
×
40000 heures
200 heures
4000 heures
30000 heures
1000 heures
8000 heures
chaque semaine
PLAN DE MAINTENANCE DU GROUPE
ELECTROGENE SDMO
module: alternateur Leroy Somer
tous les composants de l'alternateur
travail à effectuer
mesure de l'isolement du moteur
nettoyage des enroulements du stator
nettoyage des enroulements de la roue polaire
nettoyage des enroulements de l'excitatrice (stator et
rotor)
remplacement du roulement arrière
nettoyage du pont de diode
nettoyage du module de régulation
nettoyage externe de l'alternateur
nettoyage de la boite à borne
vérification de l'accouplement
vérification de l'amortisseur de vibration
vérification mécanique de tous les boulons de
fixation et des connections électrique
Tableau 12 : Planning composants de l'alternateur du groupe
électrogène[4]
Projet de fin d'études 2011
|
|
3- Check-list
Ce sont des tableaux qui découlent du planning dans
lesquels sont regroupées les opérations de mêmes
périodicités. Cela permet à l'exécutant d'avoir la
liste des tâches pour une intervention donnés une fiche de visite
et de contrôle devant être régulièrement remplie est
également établi. Voici ci-contre un exemple.
CHECK-LIST DE MAINTENANCE PREVENTIVE
NOM EQUIPEMENT
|
GROUPE ELECTROGENE SDMO MOTEUR PERKINS
|
FREQUENCE INTERVENTION
|
50 heures d'exploitation
|
DATE INTERVENTION
|
|
HEURE DEBUT ET FIN
|
|
Indication compteur horaire de la
prochaine intervention
|
|
FAIT
N°
|
DESCRIPTION DES TRAVAUX
|
OUI
|
NON
|
OBSERVATION
|
1
|
vérification du niveau de l'électrolyte
|
|
|
|
2
|
vidange d'eau et sédiments du réservoir de
carburant
|
|
|
|
3
|
|
|
|
|
4
|
|
|
|
|
pièces de rechange
N°
|
désignation
|
constructeur
|
références
|
code SOCIPEC
|
qté utilisée
|
observations
|
1
|
eau distillée
ou déminéralisée
|
|
|
|
1 litre
|
|
2
|
|
|
|
|
|
|
noms et visa opérateur
|
observations générales
|
visa contremaître
|
Tableau 13: Check-list de 50 heures d'exploitation du groupe
électrogène
Projet de fin d'études 2011
|
|
CHAPITRE VI : ETUDE ET MAINTENANCE DU GROUPE
DE PRODUCTION DE L'EAU GLACEE
I- Découpage fonctionnel du système
Le système a pour rôle de produire de l'eau
glacée pour le refroidissement des parois du moule des extrudeuses et
des presses à injection, et surtout les zones de chauffe. Cette eau est
généralement produite à 5°C. Ce système fait partir
des équipements critiques du processus de production de SOCIPEC ; car
sans eau glacée on ne peut pas avoir des flacons (produits par les
extrudeuses), ni de capsules (produites par presses à injection) pour le
conditionnement du lait de toilette et d'autres produits cosmétiques.
Ce système fonctionnement sur le principe des
installations frigorifiques dont le fonctionnement et les
éléments de base sont donnés sur la figure ci-contre, et
dont le fonctionnement est le suivant :
Le compresseur aspire les vapeurs froides venant de
l'évaporateur (celles-ci sont à basses pressions et à
basses températures) ; ensuite, il les comprime et les refoule vers le
condenseur, à haute pression et à haute température, qui
va liquéfier ces gaz chauds en rejetant de la chaleur à
l'extérieur. Les vapeurs liquéfiées vont ensuite
être envoyées vers le détendeur en passant par le filtre
déshydrateur qui va sécher de l'eau contenue dans ces vapeurs. Le
détendeur à son tour va faire chuter la pression,
entraînant ainsi une diminution de la température du fluide qui au
passage vers l'évaporateur sera gazeux. On constate un rejet des vapeurs
froides à ce niveau par aspiration de la chaleur sur les aliments et
autres. Et le cycle continue.
Il est à noter que ce groupe est de marque CIAT, de
puissance 32kW avec pour fluide frigorigène (FF) le Fréon R22, de
pression maximale 25 bars.
Projet de fin d'études 2011
|
|
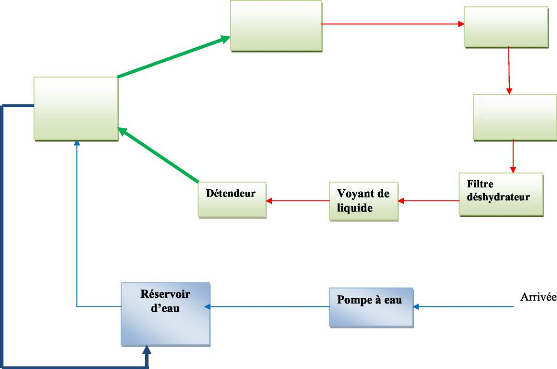
Evaporateur
Compresseur
Condenseur
Réservoir de
fluide liquide
Fig11 : synoptique du groupe de froid
|
|

Projet de fin d'études 2011
|
|
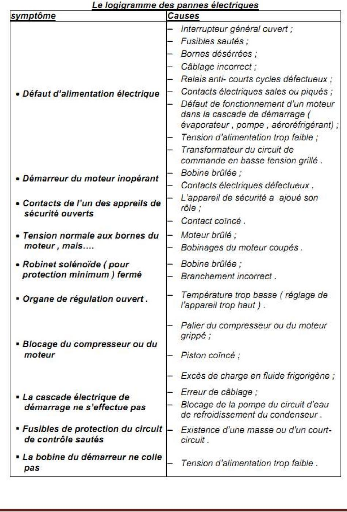
Tableau14 : logigramme des pannes électriques du
groupe de froid
II- Analyse des modes de défaillance du
système [3]
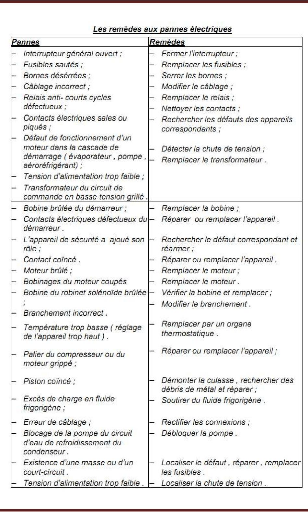
Tableau 15: remèdes aux pannes électriques du
groupe de froid
Projet de fin d'études 2011
|
|
Projet de fin d'études 2011
|
|
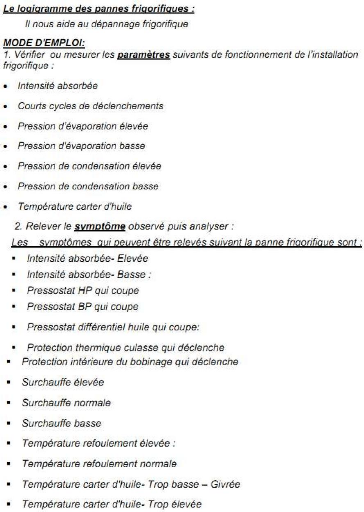
Projet de fin d'études 2011
|
|
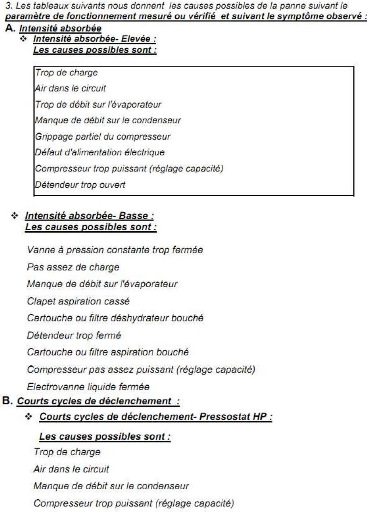
Projet de fin d'études 2011
|
|
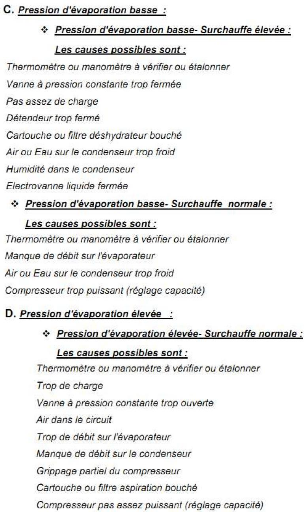
Projet de fin d'études 2011
|
|
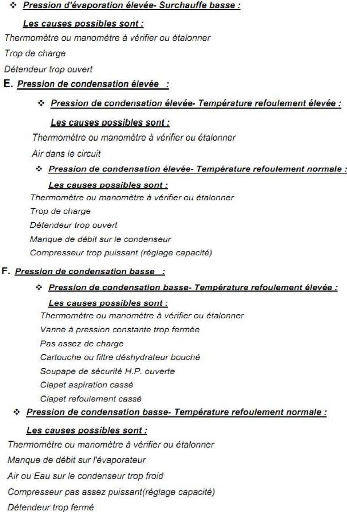
Projet de fin d'études 2011
|
|
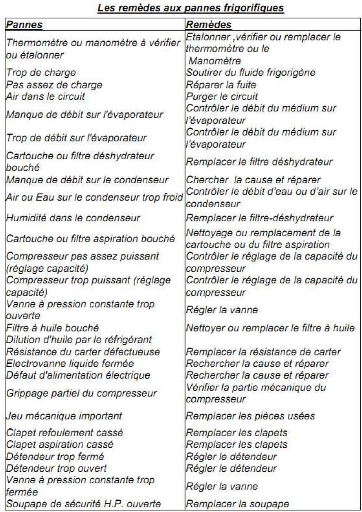
Tableau16: remèdes aux pannes frigorifiques du
groupe de froid
Projet de fin d'études 2011
|
|
III- PLAN DE MAINTENANCE PREVENTIVE (INDICATIF) DU
GROUPE DE FROID
INTERVENTIONS
|
Chaque jour
|
Chaque semaine
|
Chaque mois
|
Chaque trimestre
|
Vérifier la pression de refoulement et d'aspiration du
compresseur
|
x
|
|
|
|
Vérifier les fuites de gaz
|
|
x
|
|
|
Vérifier l'état du fluide : un manque de fluide
ou de sous-refroidissement se signale par des bulles dans le liquide en
circulation.
|
x
|
|
|
|
Vérifier l'humidité du fluide frigorifique : cette
vérification se fait en observant la couleur du voyant de liquide
placé après le déshydrateur ; la couleur verte signale que
la quantité d'eau contenue dans le fluide est inférieure à
la quantité d'eau maximale admissible, la couleur jaune signale les
effets nuisibles provenant de l'humidité. Remplacer le filtre
déshydrateur dès l'apparition de la couleur jaune
|
|
x
|
|
|
Contrôler la température de l'eau
|
x
|
|
|
|
Contrôler le niveau d'huile du carter du compresseur
|
|
|
x
|
|
Remplacer le filtre déshydrateur
|
|
|
|
X
|
Vérifier la température de refoulement et
d'aspiration
|
|
|
x
|
|
Nettoyer et contrôler l'état du détendeur
|
|
x
|
|
|
Contrôler l'état de la pompe (bruit,
débit...)
|
|
x
|
|
|
Tableau17 : plan de maintenance préventive (indicatif)
du groupe de froid
Projet de fin d'études 2011
|
|
CHAPITRE VII : PERSPECTIVES ET SUGGESTIONS
I- Résultats
En plus des plannings de maintenance et des protocoles de marche
et d'arrêt de ces équipements que nous avons proposé dans
les chapitres précédents, nous avons eu à établir
la fiche de suivi hebdomadaire du groupe électrogène (voir
annexe) , des fiches de compte rendu d'intervention et d'inspection machine,
également la fiche historique à rempli à base de fiche de
compte rendu, et aussi la fiche des commandements de l'agent de maintenance
(voir annexe). Nous avons ci-dessous un exemple de fiche de compte rendu que
nous avons établi après un
dépannage du groupe de froid qui est la suivante :
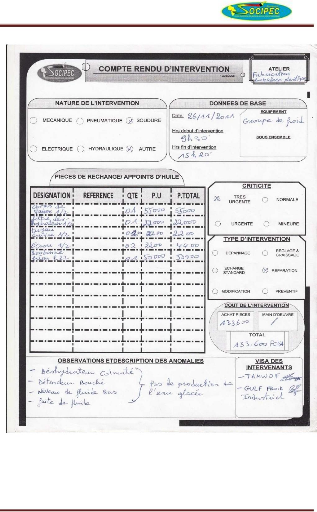
Projet de fin d'études 2011
Fig12 : Exemple rempli de compte rendu d'intervention
Projet de fin d'études 2011
|
|
II- Remarques et suggestions
1- Remarques
Ce stage a montré de nombreux manques et besoins sur
plusieurs aspects.
Premièrement, on voit une absence de flux communicationnel
entre les services. En effet, la scission entre les commerciaux et la
production est palpable.
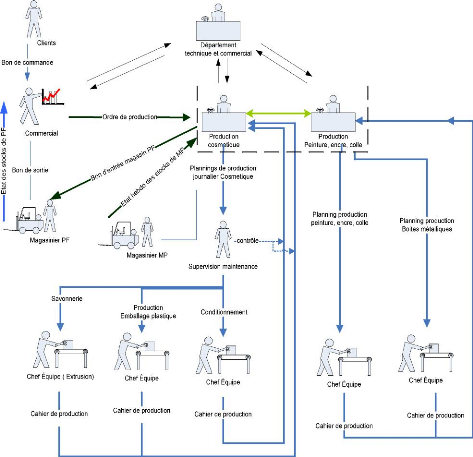
Fig13 : circulation des flux informationnel de SOCIPEC
La communication entre ces deux entités n'est pas
franche. Cependant, en observant le flux informationnel de SOCIPEC ci-dessus,
on se rend compte que la communication continuelle entre la production et les
commerciaux devrait exister. En effet, les commerciaux assurent l'interface
entre le produit de la production et le client.
Projet de fin d'études 2011
|
|
A SOCIPEC, les échanges ont
révélés une méconnaissance du rôle du
commercial par les opérateurs de production, pour qui,
l'objectif au quotidien c'est de produire à la demande du chef
directement supérieure dans l'organisation hiérarchique.
Certes une réunion hebdomadaire est quelques fois
organisée entre les commerciaux et la production, mais la diffusion des
informations ne se fait pas. Les ordres de production sont
lancés à toute heure.
Cette absence considérable de communication crée
des tares dans l'organisation de la production ; ce qui n'améliore pas
la productivité.
Le second problème majeur qui en est ressortit est la
gestion de la maintenance. En effet, l'operateur de production
se plaint du constant arrêt de défaillance des
machines, ce qui entraine un frein dans l'exécution du
programme de production. A ce problème, les techniciens affirment que
qu'il ne leurs est pas donnés les moyens de mettre en oeuvre leurs
compétences. En effet, ils se plaignent des dépannages
provisoires qui deviennent permanents. Les pièces de rechange ne sont
pas disponibles à temps. Tout ceci laisse voir l'absence d'une
planification des activités de maintenance et le manque
de suivi des équipements. On note aussi le manque d'outillage
de travail pour les techniciens. L'absence de traçabilité des
interventions.
L'aspect sécuritaire au sein de
l'entreprise est à très bas niveau. La
connaissance de la sécurité en entreprise est floue. Les gestes
de sécurité, les risques et mesures ne sont pas connu. On note
une présence de moyens de prévention à l'instar des
extincteurs installés dans les ateliers, des panneaux de signalisation ;
ce qui est déjà à saluer. Mais le véritable
problème ici est le non respect de ces consignes, car
les techniciens et opérateurs n'ont pas d'Equipements de Protection
Individuelle (EPI).
Toujours dans le sens de la productivité, on note les
retards constants d'approvisionnement des matières
premières, ce qui influence sur la qualité de production, car le
client n'est pas livré à temps. Ceci laisse voir la
mauvaise gestion des stocks dans l'entreprise.
Projet de fin d'études 2011
|
|
2- Suggestions
Tenant compte des paramètres sur-cités, nous
pouvons apporter notre pierre pour la reconstruction de cet édifice
industriel, en recommandant la prise en compte des éléments
suivants : - Mettre la priorité sur les équipements de
protections individuelles et collectives, car ceci garanti la santé et
la sécurité du travailleur ;
- Instaurer les réunions périodiques, afin
d'accentuer les relations interpersonnelles entre le personnel et
d'améliorer le dialogue et la communication dans l'entreprise ;
- Mettre sur pied une boîte à pharmacie ;
- Instaurer une journée de propreté chaque mois
pour le nettoyage général de l'entreprise avec la participation
de tous (maximum deux heures de temps et surtout un jeudi matin entre 8h et
10h) ;
- Mise sur pied d'une journée de maintenance
général pour l'inspection des machines, chaque mois et
souhaitable le samedi afin de ne pas freiner la production ;
- Faire des réunions périodiques entre le service
de production et les commerciaux afin de planifier et organiser la production
;
- Favoriser la traçabilité des interventions, en
remplissant les fiches de demande d'intervention (par l'opérateur
machine) et la fiche de rapport ou de compte rendu d'intervention (par le
technicien) ; car ces dernières constituent l'historique machine qui
facilitera les interventions une prochaine fois et orientera les nouveaux
techniciens ;
- Mettre chaque chose à sa place en définissant
« qui fait quoi ? » et « quand ? ».
Projet de fin d'études 2011
|
|
CONCLUSION
« Un plan de maintenance » est décrit selon
la norme NFX60-010 comme « un document énonçant les modes
opératoires, les ressources et la séquences des activités
liées à la maintenance d'un bien ». Le plan de maintenance
d'un bien doit permettre l'organisation de la maintenance du bien et concourir
à sa réalisation.
Ce projet de fin d'étude nous a permis de confectionner
ce document dans une phase d'analyse et de conception de la maintenance
à effectuer sur un matériel. Il rentre totalement dans une
démarche de mise en place d'une politique de maintenance dans chaque
atelier de l'entreprise et constitue le coeur du dossier des interventions. Les
résultats obtenus permettront à partir d'une fiche d'intervention
ou de visite de se focaliser sur les périodes des interventions et sur
les actions à faire face à un problème. Ceci permettra
également d'avoir un dossier de l'historique des interventions et de
renseigner le personnel du magasin de stock de pièces sur les
pièces de rechanges.
Ce projet nous a permis, d'une part d'approfondir nos
connaissances sur les méthodes de maintenance et d'autre part de
renforcer notre esprit d'organisation et de gestion du patrimoine technique des
entreprises mais aussi de profiter de l'expérience professionnelle de
notre encadreur.
Cependant quelques difficultés ont été
rencontrées dans la collecte des données et la cotation des
défaillances. Ceci s'explique par le manque de données techniques
et historiques sur les équipements de production, notamment les
équipements périphériques objet de notre étude.
Toutefois, le département de production, par sa nouvelle politique de
maintenance, est aujourd'hui en mesure de rectifier le tir pour atteindre son
objectif principal : réduire le coût de production.
Projet de fin d'études 2011
|
|
BIBLIOGRAPHIE
[1] MONCHY F, La fonction maintenance.
Edition Masson, Paris, 1996.
[2] Circuit puissance pneumatique, PowerPoint de
Jean-Louis Hû, téléchargeable à l'adresse
suivante :
http://perso.wanadoo.fr/hu.jean-louis/ressourc/auto/telecha/puispneu.zip
[3] J.P.Rapin, Installation frigorifique Tome2,
PYC-Edition
[4]FOUKA HALIDOU, Mise en place d'une politique de maintenance
préventive du groupe électrogène de secours de la SABC du
Nord, Mémoire de fin d'études ENSAI de
Ngaoundéré2007/2008
[5] La Pneumatique dans les Systèmes
Automatisés de Production, par S. Moreno et E.Peulot, Editions
Educalivre.
http://perso.wanadoo.fr/edmond.peulot
[6] Manuel compresseur Hydrovane 128/178
Projet de fin d'études 2011
|
|
ANNEXES
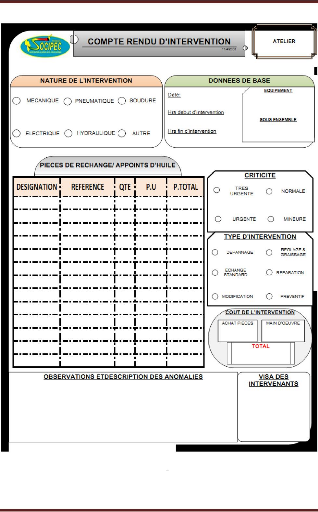
Annexe1 : fiche de compte rendu d'intervention
Projet de fin d'études 2011
|
|
Projet de fin d'études 2011
|
|
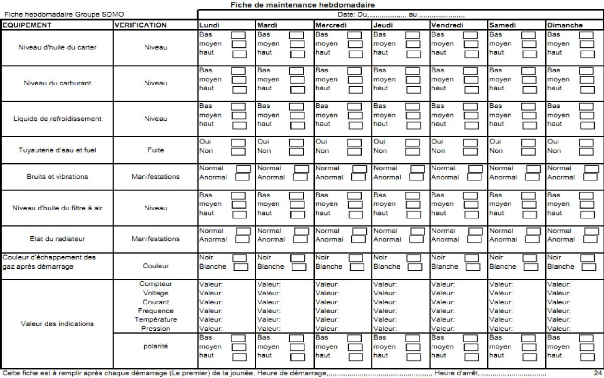
Annexe2 : fiche de suivi hebdomadaire du groupe
électrogène [4]
Projet de fin d'études 2011
|
|
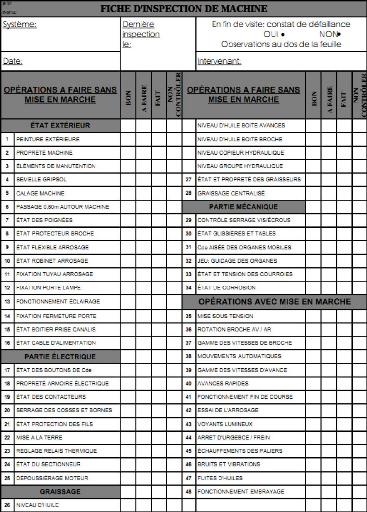
Annexe3 : fiche d'inspection machine
Projet de fin d'études 2011
|
|
|
Système
: ~~~~~~~~~~~~~~~~~~~~~~~~~~~~~~~~~~~
|
FICHIER HISTORIQUE
|
N° de
|
machine : ~~~~~~~~~
|
N° fichier : ~~~~~~
|
|
|
|
Marque
: ~~~~~~~~~~~~~~~~~~~~~~~~~~~~Type :
~~~~~~~~~~~~~~~~~~Date de la 1° Mise en Service
|
: ~~~~/ ~~~~/ ~~~~Ener ies :
|
|
~~~~~~~~~~~~~~~~~~~~~~~~~~~
|
|
N°
|
Date
|
N° R.I.
|
N° compteur
|
Degré d'urgence
|
Type d'Intervention
|
Désignation de ('intervention
|
nature
|
Temps passé
|
Coat en FCFA
|
Documents émis
|
1
|
|
|
|
|
|
|
|
|
|
|
2
|
|
|
|
|
|
|
|
|
|
|
3
|
|
|
|
|
|
|
|
|
|
|
4
|
|
|
|
|
|
|
|
|
|
|
Type d'intervention :Dp = dépannage - Rp =
réparation - Rg = réglage - Rn = rénovation - Rc =
reconstruction Nature : M = mécanique - E = électrique - P =
pneumatique - H = hydraulique - S = sécurité - A = autres
raisons
|
Annexe4 : fiche de l'historique des pannes d'une
machine
Projet de fin d'études 2011
|
|
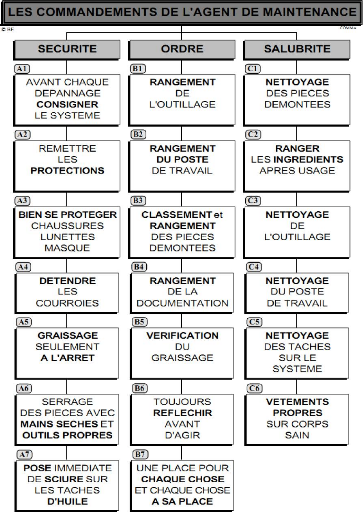
Annexe5 : les commandements de l'agent de
maintenance
|