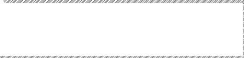
AVANT PROPOS
Dans le cadre de leur formation, les étudiants en cycle
d'ingénierie, doivent effectuer un stage ingénieur en fin de
formation. Ledit stage devant être couronné par la
rédaction d'un mémoire de fin d'études qui ferra l'objet
d'une soutenance. Ces stages en entreprise leur permettent en outre de mieux
affiner leur formation en confrontant les théories académiques
aux réalités professionnelles de sorte qu'au sortir du cycle de
formation ils soient directement opérationnels sur le terrain.
Ce document est le résultat d'un ensemble
d'études sur le processus de production des parquets menées sur
la base des formations en ingénierie à l'ESSET
de Douala et des formations ultérieures. L'objectif principal de ce
travail étant non seulement d'optimiser le rendement de la production du
parquet fabriqué à la FIP en sa base
d'ADZOPE en Côte d'ivoire, mais aussi de définir
le personnel requis pour le futur système dont le projet d'implantation
est en cours pour la représentation du Cameroun FIP-CAM.
Ce stage a été organisé en deux phases :
· Trois mois à ADZOPE en
Côte d'ivoire pour la prise de connaissance du système en place et
des différentes étapes de production des parquets.
· Deux mois à MFOU au Cameroun pour
finaliser les études et penser le futur système
amélioré.
Le travail à faire était notamment de concevoir
un système automatique de gestion d'une machine de rangement de
parquets.
Pour atteindre notre objectif, nous avons proposé une
solution technologique de logique programmée. Cette solution a
été mise en oeuvre à l'aide du microcontrôleur PIC
16F877.
INTRODUCTION GENERALE


Produire toujours plus et à moindre coûts. Tel
est l'objectif que poursuivent les chefs d'entreprise. Les solutions qu'ils
disposent sur le marché ne s'accordent pas souvent parfaitement avec
leur mode de travail. Ce fléau ouvre une autre porte source de solution
: celle de la conception. L'étude que nous présentons dans ce
document est consacrée à la conception d'un système de
rangement automatique de parquets pour la société FIPCAM.
La mission principale définit dans le cahier de charge
est d'automatiser le paquetage des parquets. Le bois des palettes
constituées après ce paquetage étant destiné
à aller suivre d'autres traitements, des contraintes de rangement
doivent être respectées.
Pour produire un travail final orienté vers le
même objectif que le cahier de charges, nous ferons recours à des
sources diverses telles que le catalogue LEROY SOMER
1998 pour le dimensionnement des moteurs électriques, les
schémas électroniques seront conçus dans le logiciel
PROTEUS.
La préoccupation première de ce projet sera de
mettre sur pied un ensemble de principes de fonctionnement, de définir
le type de rangement qu'effectuera le futur système et d'établir
un algorithme de fonctionnement. Ensuite, on s'attèlera à trouver
des formes mécaniques assurant les contraintes résultant des
principes précédents. La cinquième préoccupation
sera subdivisée en deux volets :
· Définition les montages électriques
des récepteurs et conception d'un schéma assurant la marche de
l'ensemble en mode manuel.
· Conception et réalisation de la carte
électronique à microcontrôleur pour le système,
rédaction sous Proton IDE du programme
informatique à transférer au microcontrôleur.
Nous ferons des tests de fonctionnement du prototype avant de
clôturer notre étude.

CHAPITRE 1 : PRESENTATION GENERALE
DE L'ENTREPRISE
1-1 FICHE D'IDENTITE
La FIP fabrique ivoirienne de parquets est une entreprise
créée en 1977 à ADZOPE en république de cote
d'ivoire. Elle connaitra plus tard des perturbations dans sa croissance
liées aux instabilités sociales du pays qui l'héberge.
Néanmoins, elle arrivera à braver plusieurs obstacles pour
survivre et poursuivre son extension si bien que de nos jours, la FIP est
reconnue comme première industrie ivoirienne de bois tant par la
diversité de ses actions sociales que dans ses produits.
A ce jour la FIP est une société anonyme (SA)
au capital de six cent millions de FCFA (600 000 000 FCFA). Elle compte sept
cent quatre vingt treize (793) employés permanents, une
société mère située à la Zone industrielle
à ADZOPE en cote d'ivoire, une petite unité de production
située à TANKESSE à l'EST sur la frontière entre la
cote d'ivoire et le GHANA un bureau de liaison à ABIDJAN et une branche
Camerounaise complètement autonome FIPCAM.
1-2 DIFFERENTS PRODUITS
La FIP est spécialisée dans la transformation du
bois. Les différents produits issus de cette exploitation de bois sont
:
- Les montants - Les lattes
- Les planches - Les parquets - Les débités
- Les panneaux lamellés et collés.
Le parquet est un produit spécial car pas assez connu
dans l'activité des industries forestières du Cameroun. C'est un
produit dont la matière première est très souvent
caractérisée par les restes de bois dérivant de la
fabrication des différents autres produits cités plus haut. En
effet, le parquet est très souvent destiné à la
décoration intérieure des murs et même du sol. Pour une
utilisation optimale, le parquet doit être suivi rigoureusement tel
qu'indiqué par le mode d'emploi livré avec le produit. Pour sa
fabrication, le produit fini a des dimensions en moyenne assimilables à
celles des carreaux en marbres communément vendus en quincaillerie. Leur
dimension varie entre quarante Cm (40 Cm) et cinquante Cm (50 Cm). Cet
état des choses fait en sorte que le bois destiné pour la
fabrication du parquet est utilisé jusqu'au morceau le plus petit
possible. Ceci est l'un des secrets de longévité et de
prospérité de la société car à ce moment,
pire que le Cameroun, le patrimoine forestier
ivoirien ne regorge plus ces grosses essences de grumes que
nous avons encore la chance de voir sur les engins des sociétés
implantées dans notre territoire national. Ceci étant, tandis que
certaines entreprises ferment les portes pour faillite causée par la
carence de matières premières, la FIP elle se contente de
différents restes ignorés ou simplement rejettes par d'autres
sociétés pour en faire sa matière première en plus
des produits qui lui viennent de TANKESSE, FIPCAM et les fournisseurs
divers.
L'organisation de la société plus
stratégique et simplifiée se dégage très
spécialement du style communément rencontré dans certaines
entreprises
1-3 ORGANIGRAMME
Comme toute société, la classification
hiérarchique et fonctionnelle du personnel de la FIPCAM est
représentée par un organigramme à la tête duquel se
trouve le directeur général. Dans la figure
1-1, nous avons une représentation descriptive
dudit organigramme fonctionnel.

Département administratif et financier
Département technique
Manoeuvres
Service d'entretient général
Techniciens
Directeur général adjoint
Directeur général
Service d'achats
Département de production
Gestion du materiel
Gestion du personnel
FIGURE 1-1 : ORGANIGRAMME DE
L'ENTREPRISE
Le parquet est le
premier produit sur lequel l'entreprise s'est
spécialisée en 1977. Au fil du temps et à mesure
que la société se
ait ses produits.
perfectionnait dans l'acquisition de matériel,
elle diversifi
Les différents produits dérivés on
permis au parquet de se maintenir
Le parquet est produit suivant un processus assez
simple et très rigoureux. Dans le processus
de production de parquet, malgré l'automatisatio
n des systèmes, on trouve différents types de
matériel et des ouvriers classés dans l'ordre
d'intervention comme l'indique la figure 1-2 suivante.
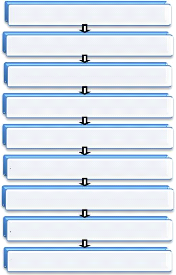
7: séchage(naturel ou artificiel)
3: Sciage industriel
4: coupure optimisée
5: Rangement 1 (empilage bois sur bois)
1: tronçonnage forestier
2: Transport de grumes
6: rangement 2 (avec aération)
8: contrôle de qualité
9: fabrication de parquets
FIGURE 1-2: DESCRIPTION DU PROCESSUS DE
PRODUCTION DES PARQUETS
Dans le souci d'optimiser la production
sur ce processus, nous avons
celles-
axé notre étude sur les
améliorations à apporter au système. Parmi ci
, le réaménagement de la section de
paquetage. Ce réaménagement nous a conduits vers la conception
d'un système de rangement automatique.
|
|
CHAPITRE 2 : MOTIVATIONS DU PROJET ET DEFINITION DES
PRINCIPES
|
2-1 INCIDENCE DU THEME SUR L'ACTIVITE DE L'ENTREPRISE
Le paquetage est un sous système capital dans le
système de production de parquets de la FIP mais jusqu'ici, les
méthodes employées et le nombre de manoeuvres requis sont source
d'inefficacité et de lenteur de travail. Ces différents maux
ayant pour manifestations communes le non respect des délais de
livraison souvent constaté, le coût élevé de la main
d'oeuvre qui entraine un coût de production élevé.
Comme toute entreprise, le souci capital est celui de faire du
profit. Cette réalité dans la branche de production de parquet
à elle seule étend son influence sur toute l'activité de
l'entreprise en général. Bien que n'ayant pas assez de
concurrence sur le parquet au niveau local, la dimension internationale de la
firme lui a permis d'avoir une clientèle du même. Or pour pouvoir
faire face à la concurrence à ce stade du marché, il faut
être extrêmement méticuleux sur tous les détails de
l'activité de l'entreprise car, tous d'une manière directe ou
indirecte ont leur part d'influence sur le bénéfice. D'un autre
coté, l'entreprise et toutes ses branches évoluant dans un
contexte africain a un ensemble d'activités sociales qu'elle s'est
engagé à entreprendre et ces activités font partie
intégrante des charges. C'est cet ensemble d'investissements qui ont
hissé la FIP aujourd'hui au sommet des entreprises du secteur du bois en
république de Cote d'ivoire. Elle arrive donc au Cameroun affichant
les
l'intérêt de l'entreprise de faire des
réformes sur les méthodes de production utilisées à
la maison mère. Ces méthodes pourront être testées
et évaluées sur place pour espérer implanter au Cameroun
un système assez compétitif. C'est par là qu'elle aura la
chance de croitre et de prétendre un jour atteindre les sommets qui pour
l'instant sont bien occupés pas d'autres entreprises locales toutes
aussi compétentes et innovatrices. La partie s'annonçant assez
rude, cette étude n'est qu'une manifestation de cette politique de
présence effective et efficace sur le terrain menée par la
FIPCAM.
2-2 PRINCIPES DE BASE DU SYSTEME
Apres plusieurs phases de conception, de critiques et de
modifications, le système arrêté pour notre étude
n'est pas un système extraordinaire. Par contre c'est juste un
assemblage de petites idées logiques qui nous ont menés vers ce
que nous avons nommé la palettiseuse A-g. Pour
mettre sur pied cet ensemble, il aura fallu prendre en compte plusieurs
paramètres électriques et mécaniques. Les dimensions
maximales et minimales du parquet que nous serons emmenés à
ranger ont permis le dimensionnement de la bâtisse mécanique. Les
palettes rangées sont destinées au séchage car le parquet
est fabriqué sur la base du bois séché. Le séchage
lui même est fait de deux manières :
· Un séchage naturel
Les palettes de parquet sont exposées en plein air sous
le soleil, la pluie et tous les changements atmosphérique de sorte
à permettre au bois qui, bien qu'étant déjà
scié, et loin de la forêt, de sécher sans contrainte et
naturellement.
Selon l'essence, l'épaisseur, et le type de produit
final, le niveau d'humidité est prélevé
périodiquement pour contrôler l'évolution du processus de
séchage.
· Un séchage artificiel
Toujours après le paquetage, les palettes de parquet
sont rangées dans des grandes enceintes où la température
et l'humidité sont contrôlées par ordinateur.
D'énormes brasseurs permettent la circulation d'air dans l'enceinte. Des
sondes permettent de vérifier chaque fois le niveau d'humidité
dans le bois et dans la chambre. L'ensemble est doté des vannes pour
permettre l'échappement de la chaleur en cas de chauffage excessif ne
respectant pas les consignes. La chaleur elle même est provoquée
par un radiateur qui reçoit de l'eau chaude venant de la
chaudière, la chaleur dégagée par l'eau dans les vaisseaux
du radiateur est refoulée dans l'enceinte du séchoir par un autre
ventilateur.
La réussite de tous ces processus de séchage est
conditionnée par le type de rangement de bois. Les palettes étant
déjà pleines et empilées les unes au dessus des autres,
pour une circulation normale de l'air et un séchage efficace il faut des
voies d'aérations entre les différentes pièces de parquet
rangées constituant la palette entière. C'est une des raisons de
la double équipe de paquetage présente au système actuel.
Cette double
présence est représentée sur
le
schéma synoptique de la figure
1-2. Différents modes de rangement ont
été mis sur pied pour respecter toutes les contraintes de
séchage. Parmi to
us ces modes, celui de la figure 2-1
est
palettiseuse
celui arrêté pour le paquetage automatique
à effectuer par la
A-g.
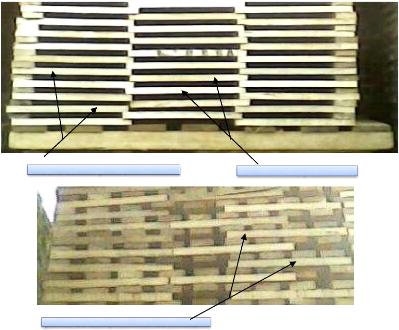
couche double pièces couche
mono pièce
pièces de compensation de niveau
FIGURE 2-1 : IMAGE D'UNE PALETTE EN COURS DE
RANGEMENT
2-3 METHODE DE RANGEMENT
Les différents paramètres à prendre en
compte pour le rangement d'une palette sont :
- Longueur de pièce
- Nombre de couches par palette - Nombre de lignes par couche
Une palette pleine est une alternance de deux types de couches
à savoir les couches à double pièces et les couches mono
pièce.
Une couche à double pièce est constituée
de lignes de deux pièces chacune placées aux
extrémités de la palette et les couches mono pièces comme
leur nom l'indique sont constituées de lignes d'une pièce
rangées au centre de la palette. Pour rétablir l'équilibre
des hauteurs sur les couches mono pièces, des morceaux de parquets
supplémentaires ou tout simplement des morceaux de bois prévus
à cet effet sont insérés sur les bords de la palette. Dans
notre système, cette insertion se fera manuellement.
Pour faciliter la superposition lors du séchage, les
palettes sont toujours constituées d'un nombre de couches impair car :
le rangement commence par les couches de deux pièces avec l'alternance
des couches, un nombre de couches pair permettra de terminer la palette par une
couche mono pièce. Cette couche mono pièce rangée au
centre de la palette imposerait un autre stratagème pour permettre une
superposition équilibrée d'une autre palette c'est pourquoi nous
avons pensé vérifier chaque fois que le nombre de couches est
impaire garantissant ainsi que
toute palette dont le rangement aura commencé en
respectant le principe de la couche double pièces en premier se
terminera par une couche de même type.
Le système étant appelé à
fonctionner automatiquement, des sous programmes de calcul en cours de
fonctionnement ont été insérés dans le code source
de sorte à pouvoir évaluer avec une très petite marge
d'erreur le volume de travail effectué à partir de la
dernière remise à zéro des mémoires.
Pour l'évaluation automatique du volume d'une palette,
le microcontrôleur se servira des données entrées lors du
paramétrage du rangement. Ainsi, il tiendra compte de l'épaisseur
e d'une pièce, de sa longueur L et de
sa largeur l. Ces trois dimensions assurant
premièrement le calcul du volume v d'une pièce
utilisée pour le rangement. Après ce calcul, la donnée
résultante sera stockée en mémoire vive pour attendre
l'évaluation du nombre de pièces requis pour une couche.
Ce calcul à son tour prendra à son compte le
nombre de lignes et le nombre de couches programmé par l'utilisateur.
Cela signifie à titre d'exemple que pour un nombre de lignes
X et un nombre de couches Y, le nombre de
pièces pour chaque palette pleine sera évalué de la
manière suivante :
Y est un nombre impair représentant le
nombre de couches total que comptera la palette entière ; ce nombre sera
subdivisé de la manière suivante :
· 1/2(Y-1) en couches mono pièce
· 1/2(Y-1) +1 en couches double
pièces
En étudiant le rangement de notre palettiseuse tel que
redéfinit Sur le schéma de la figure 2-2, nous
avons écrit un mini programme MATLAB pour nous
générer la formule à programmer sous PROTON
IDE pour que ledit calcul soit entièrement pris en charge par
l'automatisme.
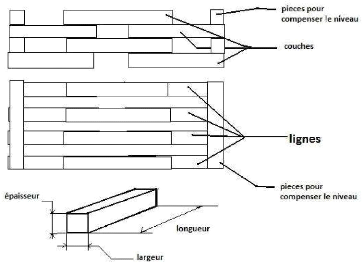
FIGURE 2-2 : DESCRIPTION DETAILLEE DES
PARAMETRES DE RANGEMENT
Le calcul du nombre total de pièces de la palette
pleine se fera en additionnant le nombre de pièces constitué par
les différents types de couches. Le volume V de la
palette s'obtiendra par produit des valeurs N et
v. Le sous programme de calcul de volume présent dans
notre code source tient compte de la formule générée par
le logiciel MATLAB après exécution du code ci
après.
%L= longueur, l=largeur,
e= épaisseur, v= volume d'une
pièce
%V=volume d'une palette pleine, X= nombre de lignes, Y=
Nombre de couches
syms Y l L e X; v=l*L*e;
N1=0.5*X*(Y-1) ; N2=X*[(Y-1)+2] ; N=N1+N2 ;
V=N*v
L'exécution de ce programme matlab nous
délivre la formule de calcul suivante que le
microcontrôleur se chargera de
résoudre.
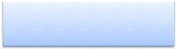
V =(1/2*X*(Y- 1)+X*(Y+1))*l*L*e
Les différentes parties du
système ont chacune été
conçues séparément et des ajustements pour un
assemblage optimal on été
opérés sur chacune d'elles en tenant compte des contraintes de
fonctionnement . Parmi ces contraintes, on note
les mouvements, le type de matériau à
manipuler, les différentes charges susceptibles d'êtres
transportées. Les renseignements sur la hauteur utile de l'ensemble ne
sont pas donnés car leur influence est quasi nulle dans la conception.
Il
n de ses
reviendra à l'utilisateur de se donner une
hauteur utile en fonctio
réalités d'exploitation. Pour notre cas
particulièrement, pour accoupler la palettiseuse A-g
à la DIMTER OPTICUT 704
de la FIP, il faudra la monter 1.4m
du sol
sur une hauteur utile équivalente soit . Le
schéma de principe
semble est représenté à la
général résultant de l'en FIGURE
2-3.
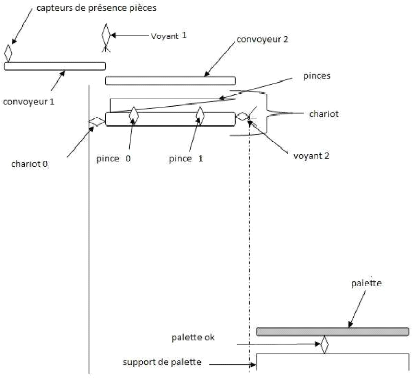
FIGURE 2-3 : SCHEMA DE PRINCIPE
GENERAL
NB : Les noms donnés dans la
Figure 2-3 sont les images des expressions
utilisées dans la suite du travail et dans le programme du
microcontrôleur. Pour plus de détails, consulter la fiche
détaillée des matériels utilisés.
N'ayant pour souci que la description simple du
système dont les précisions seront données au fil de la
progression, les formes et symboles ont été dessinés sans
tenir compte de normes quelconques.

CHAPITRE 3 : CONCEPTION DU
SYSTEME MECANIQUE
NB : les dessins mécaniques
présents dans ce chapitre sont l'oeuvre de GOLI KOUAKOU Raoul.ils sont
illustrés dans l'unique but de donner une image plus concrète du
projet. Le propriétaire se réserve le droit d'en faire un usage
complet.
3-1 INTRODUCTION
La palettiseuse A-g est un assemblage de quatre
(04) principales parties à savoir :
· Le convoyeur 1
· Le convoyeur 2
· Le chariot
· Le support de palette
Ces ensembles mécaniques distincts sont le fait des
contraintes rencontrées en vue du respect du type de rangement
présenté plus haut. L'entreprise se réservant la
propriété de cette partie, les détails sur les
différents schémas présentés dans ce chapitre ont
pour la plupart été retirés.
Représenté mécaniquement, la
palettiseuse est un système qui se range sur un espace minimal de cinq
(05) mètres de long sur trois (03) mètres de large. Sa hauteur
propre est de 2100 mm. Une articulation est prévue sur le tapis
d'admission au niveau des deux demi tapis de vitesse différente.
Celle-ci permet de proposer une première solution pour
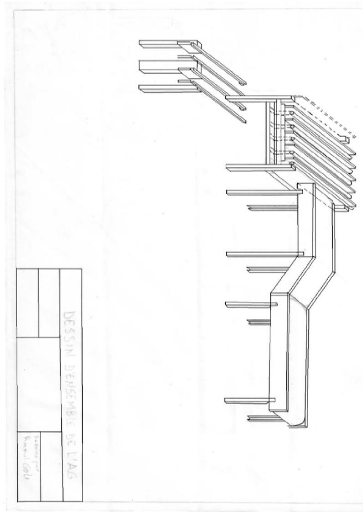
FIGURE 3-1 : DESSIN D'ENSEMBLE DE LA
PALETTISEUSE
3-2 LE CONVOYEUR 1
C'est un ensemble constitué de rouleaux de transport
et des chaînes. Les deux sous-ensembles permettent de changer le sens
d'admission des pièces de bois à un angle de 90°. En amont
du convoyeur 1 se trouve un tapis d'admission par lequel arrivent les
pièces de bois pour le rangement. Celui-ci est constitué de deux
demi tapis de transport entraînés par un même moteur
électrique. Les deux tapis tournent l'un à une vitesse double que
l'autre. Le plus rapide étant celui qui dépose directement ses
pièces dans le convoyeur 1. Cette stratégie est utilisée
dans l'industrie pour des systèmes sur lesquels un comptage est
effectué et où un bourrage pourrait advenir et causer des
défaillances de production. Arrivant en file, l'entrée dans le
convoyeur 1 est facilitée par les rouleaux de transport qui prennent le
relais une fois que les pièces ont atteint la fin du tapis. Deux
capteurs de présence pièce (piece1,
piece2) permettent de gérer le positionnement des
pièces pendant le fonctionnement.
Pour le changement de sens, entre chaque paire de rouleaux,
sont montées des chaînes munies de crochets
régulièrement disposés. Le choix porté sur
l'utilisation de ces chaines s'est imposé parce qu'il offrait la
possibilité de disposer les chaines à un niveau en dessous de
celui des rouleaux afin d'éviter de freiner les pièces de bois
par la présence de matériel fixe sur la trajectoire. Lesdites
chaînes entrainées par un moteur via un axe muni de pignons se
chargent de déplacer les pièces dès qu'elles sont
positionnées du convoyeur 1 vers le convoyeur 2 avant que d'autres
pièces ne soient admises.
3-3 LE CONVOYEUR 2
Moins complexe que le précédent, le convoyeur 2
a pour rôle principale d'assurer un espace entre les lignes de
pièces d'une même couche. Il est constitué de courroies
tendues entrainées par un moteur. Ici, pour le transport le choix a
été orienté vers une matière qui favorisera une
meilleure adhérence des pièces de bois sur les supports du
convoyeur 2 d'où l'utilisation des courroies. Chaque fois qu'une ligne
de pièces venant du convoyeur 1 est déposée sur le
convoyeur 2, celui-ci au moyen de ses courroies les déplace vers
l'avant. Ce déplacement d'une double importance permet d'abord d'assurer
l'espace d'aération requis entre les lignes des couches, puis
d'éviter que les pièces suivantes ne viennent se superposer sur
celles précédemment arrivées. Ce cycle de fonctionnement
du convoyeur 2 se répète jusqu'à ce que le nombre de
lignes pour une couche soit atteint.
3-4 LE CHARIOT
Il est constitué des pinces et leur support. Les
pinces sont des lames d'acier de taille très fines, elles sont
dissimulées à un niveau légèrement bas par rapport
aux courroies du convoyeur 2. Elles se chargent de débarrasser la
surface du convoyeur 2 pour décharger la couche ainsi constituée
sur la palette en cours de rangement. Ces pinces coulissent dans des rails en
forme de U au sein desquels une forme spéciale a
été taillée pour assurer le changement de niveau des
pinces au moment de
démarrage de leur course vers l'avant. Ce
déplacement permet de soulever la couche disposée sur le
convoyeur 2 avant que les pinces ne se mettent à leur course vers
l'avant. Cette étape est un peu délicate car il faut maintenir
les espaces d'aération entre les lignes de la couche. Pour cela, les
formes taillées dans le fer en U sont faites avec des
pentes douces pour éviter des secousses lors de la manutention. Les
pinces sont entrainées par un moteur fixé sur le chariot. Le
chariot lui même chargé du transport des pinces comporte un moteur
qui assure la descente des pinces pour la décharge et la montée
pour leur retour en position initiale. La décharge s'effectue dès
que l'ensemble descendant a atteint le niveau de la palette en cours de
rangement.
3-5 LE SUPPORT DE PALETTE
Toujours dans le but de respecter les contraintes de
rangement, le support de palette a été conçu avec un
degré de liberté car pendant le rangement, lors du passage entre
les deux types de couches, il y'a un décalage de la palette pour assurer
le positionnement de la couche suivante. Le mouvement de décalage ici
est assuré par un système de vis sans fin commandé lui
aussi par un moteur électrique.
Les schémas complémentaires sur les
différentes parties mécaniques se trouvent en annexe de ce
document.
CHAPITRE 4: CONCEPTION DES
SYSTEMES ELECTRIQUES
4-1 GENERALITES ET ALGORITHME
Cette phase de l'étude vient juste après
l'étude mécanique et tiendra compte de tous les mouvements
prévus dans le comportement dynamique de la palettiseuse A-g.
comme notifié dans les premières lignes de ce travail,
le fonctionnement global avant d'être mis sur pied a premièrement
été étudié de manière individuelle sur
chaque sous système de la partie mécanique. Cela aura permis de
faire une étude assez détaillée des récepteurs
électriques, des types de capteurs et de conducteurs. Ce n'est
qu'après ces évaluations individuelles que sera implantée
une installation électrique générale en tenant compte de
l'algorithme de fonctionnement.
En outre, pour le système, le câblage
électrique va permettre d'assurer la marche par à coups de
certains moteurs afin de donner une possibilité d'effectuer des
réglages d'initialisation ou de réinitialisation en cas de
dysfonctionnement.
Tous les montages électriques et commande, le code source
sont établis sur la base de l'algorithme de la figure
4-1
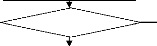
Initialisations ok
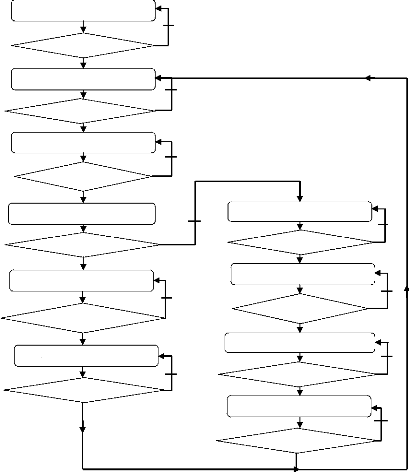
Décharge couche et mémorisations
Rangement double pièces
Attente nouvelle palette
Palette déchargée
Mémorisations ok
Nouvelle palette en place
NB couches atteint
Décharge palette
Paramétrage ok
NB lignes atteint
Mémorisations
Paramétrage
Décharge couche et mémorisations
Rangement mono pièce
Palette sur double
NB couches atteint
Palette sur mono
Décalage palette
Décalage palette
NB lignes atteint
FIGURE 4-1 : ALGORITHME GENERAL DE MARCHE
AUTOMATIQUE
Il est à noter que le manque des étapes et
conditions de marche/arrêt du système dans la figure
4-1 précédente n'est pas le fait d'un oubli mais un
souci de clarté, la figure a été restreinte à son
fonctionnement automatique. La marche manuelle ne comportant que des modes de
marche par à coups des différents récepteurs
commandés individuellement.
4-2 CIRCUIT ELECTRIQUE
Pour ce qui est du câblage électrique du
système, il est établi de manière plus explicite de sorte
à pouvoir mieux détailler cette marche par à coups.
La gestion des deux types de marche manuelle et automatique
est faite au moyen d'un commutateur double position sur lequel
l'opérateur pourra agir pour sélectionner le type de marche
souhaité.
Pour s'assurer de la bonne marche du système, ce
commutateur ne doit pas être actionné lorsque le système
est en marche. Son utilisation ne se faisant qu'au moment ou le système
est à l'arrêt permet uniquement d'effectuer des réglages
avant la mise en marche automatique de la machine laquelle marche constitue son
fonctionnement normal.
Le montage est alimenté sous une tension de 230V 50hz,
cette plage de tension est spécialement dictée par le type de
tension supporté par les bobines des contacteurs utilisés dans la
commande des moteurs. Il faut noter la présence d'une tension de 5 V
dans le même montage au niveau du commutateur de mode de fonctionnement.
Cette tension est
utilisée pour transmettre l'ordre émis par
l'opérateur au microcontrôleur afin de le mettre dans le mode
souhaité.
Pour éviter d'éventuels désagréments
dus à des
dysfonctionnements qui pourraient intervenir pendant que le
système se trouve dans l'un des deux modes de marche, un double
verrouillage logiciel et matériel est mis en place afin d'assurer la
protection du matériel, de l'opérateur et de l'environnement
immédiat de la palettiseuse A-g.
Le schéma de la figure 4-2
illustre en détail l'ensemble des commandes et les différentes
connexions entre les éléments du pupitre de marche manuelle
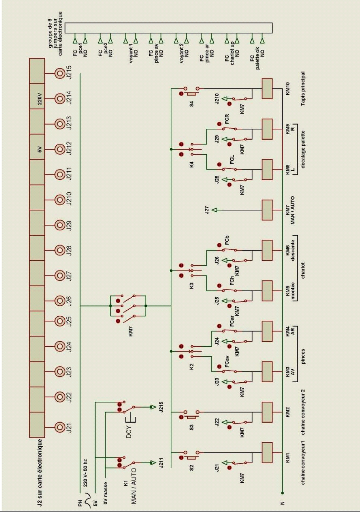
FIGURE 4-2 : SCHEMA
ELECTRIQUE
La figure 4-2
précédente laisse découvrir deux interfaces
d'intercommunication entre les parties mécaniques, la partie
électronique et la partie câblage électrique. Ainsi, le
bloc de 8 jumpers présent sur la carte électronique est l'endroit
par lequel le système en marche recueille des informations sur les
différents états des capteurs afin de prendre des
décisions de fonctionnement.
Les décisions de fonctionnement elles mêmes sont
traduites par des changements d'états des broches
J2x du connecteur J2. Par
ailleurs certaines broches de J2 sont
utilisées sous forme d'entrées de fonctionnement jouant le
même rôle que les huit (8) jumpers.
Ce schéma est interconnecté à la carte
électronique qui en ellemême intègre plus d'un ensemble de
mini montages assemblés de sorte à donner au système un
fonctionnement assez simple et autonome.
5-1 INTRODUCTION
Ici, le travail effectué s'articule essentiellement
autour du
microcontrôleur PIC 16F877 de
MICROCHIP qui est un microcontrôleur 16 bit
caractérisé par :
· Un jeu de 35 instructions
· Une plage de fréquences de fonctionnement de 4Mhz
à 20 Mhz
· 200 nano instructions / cycle
· 8K x 14 mots de mémoire flash programmable
· 368 x 8 Byte de mémoire de données (RAM)
· 256 x 5 Byte de mémoire EEPREOM
· Une apparence physique sous un boitier noir duquel
émergent 40 broches.
· Courant maximal débité par une broche
=25mA
D'amples détails sur ce composant et certains autres
des composants présents sur cette carte électronique ont leur
documentation technique en annexe de ce document. Les fiches techniques dans
lesquelles ces informations ont été recueillies ont
été téléchargées à partir d'un site
internet de téléchargement.
5-2 INTERFACE DE SORTIE :
Ici, il est question de trouver une méthode pour
commander les relais sur la carte avec une tension acceptable à un
courant débité par les broches du microcontrôleur
relativement bas de sorte à ne pas l'endommager et assurer la
longévité de la carte.
En effet, l'exécution du code source du programme en
mémoire du microcontrôleur est manifestée par des
changement d'état de ses broches dont certaines sont destinées
à commander, à piloter ou à verrouiller selon le cas.
Comme partout dans ce travail de conception il a fallu tester des prototypes
divers avant de se figer sur le model de la figure 4-3
cidessous.les broches du microcontrôleur chargées de
commander les différents relais sont directement connectées
à un ULN 2004A. Le circuit équivalent de notre
interface de sortie résulte des caractéristiques internes
fournies sur la fiche technique par le fabricant. Le souci de protéger
la sortie de chaque broche des forts courants ne s'est pas imposé ici du
fait de la présence d'une résistance incorporée sur chaque
entrée de l'ULN2004A.
Sur la figure 4-3 ci-dessous nous avons
la représentation d'une ligne d'amplification de
l'ULN2004A
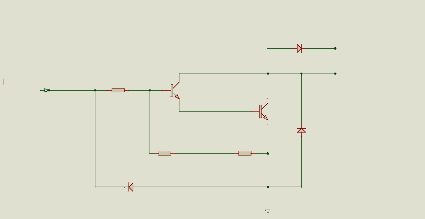
broches du microcontrôleur
commandant les relais
10.5 K
7.2K 3K
Bobine de relais
com
FIGURE 4-3 : SCHEMA DE L'INTERFACE UTILISEE
:
5-3 ALIMENTATON
L'alimentation générale de la carte peut provenir
de deux sources selon le choix :
Tous les niveaux de tension sont fournis de l'extérieur et
raccordés à la carte par les broches d'alimentation
répertoriées sur le connecteur J2
La tension secteur est directement raccordée au
transformateur incorporé à la carte qui par
l'intermédiaire des différents régulateurs de tension et
les montage de redressement, vont fournir à l'ensemble des circuits les
différentes tensions d'alimentation et de marche nécessaires. Le
redressement utilisé ici tel que représenté sur la
figure 5-1 est le redressement deux alternance
constitué de diodes 1N4007.
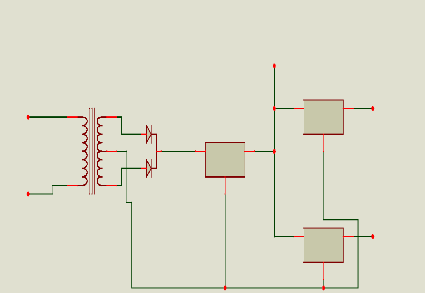
SECTEUR
TR1
TRAN-2P3S
D1
FMMD2838
1
U1
7812
VI
2
GND
VO
3
BOBIN ES DES RELAIS
1
1
U3
7805 VDD MICROCONTROLEUR
7805
U2
VI
VI
2
2
GND
GND
VO
VO
3
3
CAPTEURS ET LCD
FIGURE 5-1 : SCHEMA DU CIRCUIT
D'ALIMENTATION
5-4 CONNEXION CLAVIER ET ECRAN
Le clavier utilisé ici est un clavier 12 touches
matriciel soit quatre (04) lignes et trois (03) colonnes. L'écran est de
type alphanumérique de deux lignes utilisé avec une interface de
4 lignes de données. Ci-dessous, la figure 5-2
nous représente les connexions du clavier et de l'écran.
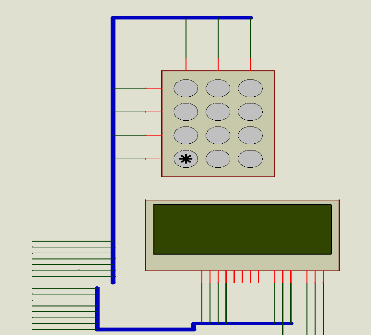
RB1
RC0
RC1
R
RC3
RC4
RC5
RC6
RC7
RB2
RB3
RB4
RB5
RB6
RB7
RB5
RB4
RB7
RB6
LCD1
LM044L
A1 2 3
B4 5 6 C7 8 9 D 0
#
FB1
FC7
14
D7
R=13
13
C8
F
R=5
12
2
C6
Rat
11
Di.
10
D3
9
FB3
8
3
D I
7
CO
R=3
8
E
5
RN
R=2
4
FS
3
NEE
2
VCD
VES
FIGURE 5-2 : CONNEXION CLAVIER SUR PORT B ET
ECRAN SUR PORT C
5-5 ENTREE DES CAPTEURS
Pour ce qui est des capteurs du système, leur action
est transmise à la carte par mise au niveau bas de la broche
correspondante. En d'autres termes, les capteurs utilisés sont actifs au
niveau bas. En fonctionnement normal, les broches sont maintenues à 5V.
Pour éviter de créer un court circuit lors d'une action sur un
des capteurs, des résistances ont été prévues sur
le montage. Celles-ci assurent le contrôle du courant
débité par le régulateur de 5V alimentant le contact au
moment où actionné il met mettant à la masse une broche
précise du microcontrôleur. Ce stratagème est plus
explicité dans la figure 5-3.
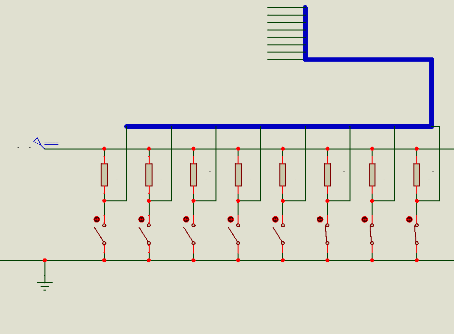
R1(2) VALUE=5
pcel
SW1
SW-SPST-MOM
R1
10
RDO
pce2
SW2
SW-SPST-MOM
R2
10
RD1
voyl
SW3 SW4
SW-SPST-MOMSW-SPST-MOM
R3
10
RD2
pincel
10
R4
RD3
voy2
RD0
RD1
RD2
RD3
RD4
RD5
RD6
RD7
SW5 SW6 SW7
SW-SPST-MOMSW-SPST-MOMSW-SPST-MOM
10
R5
RD4
pince0
10
R6
RD5
chart)
R7
10
RD6
paletteok
SW8
SW-SPST-M
R8
10
RD7
FIGURE 5-3 : CABLAGES DES CONTACTS DES
DIFFERENTS CAPTEURS
5-6 COMMANDE DU TAPIS D'ADMISSION
L'accent mis sur ce niveau est aussi important pour la
stabilité générale du système et son fonctionnement
bien que ce ne fut pas une exigence du cahier de charges. Ici, il est notamment
question de contrôler la mise en marche du tapis d'admission. Celui-ci ne
devra se mettre en marche qu'au moment requis pour envoyer les pièces de
bois au
convoyeur 1 ; c'est à dire uniquement quand le
système en a besoin afin d'éviter les bourrages.
Pour parvenir à gérer ce problème, il
aura fallu faire recours à un circuit fonctionnant à la fois avec
une logique combinatoire et une logique séquentielle.
En fonction du type de couche en cours de rangement, le tapis
d'admission se mettra chaque fois en marche si les deux capteurs de
pièces de bois sont ouverts pour le cas des couches double pièces
et pour le cas des couches mono-pièce, chaque fois que le capteur 1 du
convoyeur 1 sera fermé marquant l'arrivée d'une pièce, le
tapis devra s'arrêter de tourner et attendra à chaque fois la
libération du contact dudit capteur par les chaines du convoyeur 1.
Pour s'informer du type de couche en cours de rangement, on se
servira de la broche de commande du relais de décalage de la palette.
Le montage mis sur pied dans notre cas assure le
contrôle de la réinitialisions d'une bascule JK
dont les entrées J et K sont
connectées au aux capteurs de présence de pièce.
L'entrée d'horloge H est raccordée à la
fois au bouton poussoir DCY (départ cycle) et à
la broche RA0 commandant le relais des chaînes du
convoyeur 1. Une diode permet d'éviter la diffusion du signal
envoyé par action de DCY dans le microcontrôleur
la sortie Q utilisée alimente directement la bobine du
relais. La sortie complémentée pourra être raccordée
à la masse par l'intermédiaire d'une forte résistance.
Pour l'analyse combinatoire de ce sous ensemble, nous avons en entrées
trois (03) variables et une variable de sortie. Ce qui nous permet
d'établir la table de vérité du tableau
5-1
A
|
B
|
C
|
S
|
0
|
0
|
0
|
1
|
0
|
0
|
1
|
0
|
0
|
1
|
0
|
0
|
0
|
1
|
1
|
0
|
1
|
0
|
0
|
1
|
1
|
0
|
1
|
1
|
1
|
1
|
0
|
0
|
1
|
1
|
1
|
0
|
TABLEAU 5-1 :
TABLE DE VERITE DE LA COMMANDE DE
L'ADMISSION
A= RE2 : broche du microcontrôleur perme ttant
d'alimenter l'ensemble commandant le relais de décalage
de la palette.
B = RD0 : broche du microcontrôleur
connectée au capteur de présence de
pièce1.
C= RD1 : broche du microcontrôleur connectée
au capteur de présence de pièce 2.
De la précédente table de
vérité,
au moyen de l'algèbre de BOOLE, ation de
KARNAUGH suivante :
nous obtenons l'équ
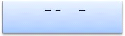
S = B C + A B C
Pour réaliser cette fonction (S
) nous avons opté pour l'utilisation
des portes
logiques NAND, ET,
OU.
Au moment de passer à la réalisation de
ce schéma, nous avons pris le soin de n'utiliser que des
composants d'une même te chnologie ; à
savoir 74HC00, 74HC11,
74CH112, 74HC4071.
Malheureusement, le marché ne nous a pas
aidés à ce point et la fonction
est restée non opérationnelle. Le diagramme
correspondant est donné sur la Figure 5-4.
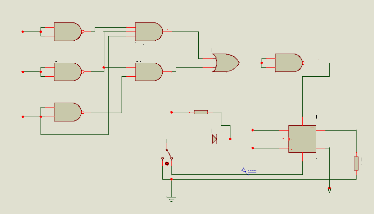
A
C
B
U1
NAND
U2
NAND
U3
NAND
2
13
1
AND
74HC11
U4:A
U5
DCY
RA0
12
R1
10k
2
1
74ALS32
DIODE
U6:A
D1
PCE2
PCE1
5 V
3
U7
NAND
6
9
7
J
K
C
4
R
5
bobine relais tapis d'admission
Q 3
Q
U8:A
10135
S
2
R2
10k
FIGURE 5-4 : MONTAGE GERANT LE FONCTIONNEMENT
DU TAPIS D'ADMISSION
5-7 SCHEMA ELECTRONIQUE GLOBAL
Nous sommes finalement rendus à la phase terminale de
la conception du circuit électronique. Basé essentiellement sur
les schémas illustrés précédemment, le circuit
final est en plus constitué de connecteurs et autres artifices assurant
la bonne tenue de la carte en fonctionnement réel. Le montage
présenté à la figure 5-5 a
été capturé dans l'écran de travail lors des
simulations sous le logiciel PROTEUS
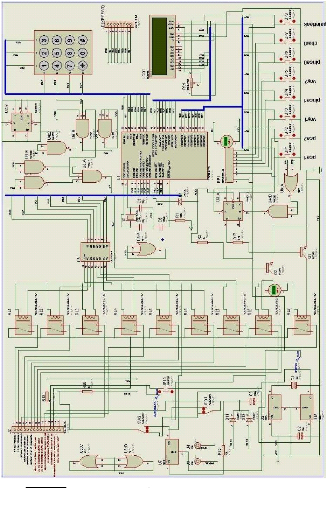
FIGURE 5-5: SCHEMA ELECTRONIQUE
GLOBAL
39
5-8 CONCEPTION DU PROGRAMME DE FONCTIONNEMENT
Cette dernière étape est entièrement
caractérisée par l'écriture en langage BASIC d'un code
source sur la base de l'algorithme de fonctionnement de la figure
4-1 afin de permettre au microcontrôleur d'assurer
fidèlement la marche du système. Le code source est écrit
avec le logiciel PROTON IDE et le transfert vers le
microcontrôleur se fait à l'aide du programmateur PROPIC
2. L'organigramme du processus de commande numérique par PIC
16F877 de notre code source est définit dans la figure
5-6 ci-après.
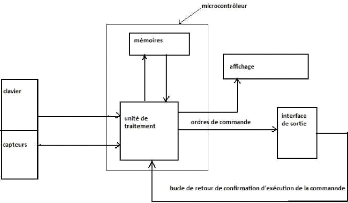
FIGURE 5-6 : ORGANIGRAMME DU PROCESSUS DE
COMMANDE
Ce programme classifié en annexe est destiné
à un montage dont l'afficheur LCD alphanumérique comporte 2
lignes et 16 colonnes. Pour pouvoir l'adapter à un montage ayant un LCD
différent il faudra opérer les ajustements nécessaires
dans le code source. D'autres parts, il intègre dans son fonctionnement
des sous programmes qui permettront à
l'ensemble d'effectuer les calculs internes et des
mémorisations pendant le fonctionnement. Lesdites mémorisations
sont faites par écriture à des adresses précises dans
l'EEPROM.
5-9 DESCRIPTION DE PROTON IDE
Le logiciel PROTON IDE est un
produit du groupe POSEK. Les versions d'évaluation sont disponibles
gratuitement sur le site internet du concepteur la version 1.0.0.1 est celle
utilisée dans notre projet.
PROTON IDE est un environnement de programmation en basic.
Pour programmer un microcontrôleur avec ce logiciel avec l'assurance que
celui-ci exécute en fidèlement le code source, il faut au
préalable définir tous les paramètres du
microcontrôleur dans la partie configuration du code programme.
L'interface utilisateur et les différentes configurations
de notre code source apparaissent dans la figure 5-7
ci après.
Proton IDE intègre un compilateur qui permet de
créer les fichiers utilisés par plus d'un type de compilateurs et
programmateurs. Dans notre cas, les fichiers portant les extensions .HEX, .ASM
et .Bas sont ceux utilisés par le Logiciel ICPROG que nous utilisons
pour piloter notre programmateur sous Windows XP pour le transfert du code
source vers la mémoire du microcontrôleur.
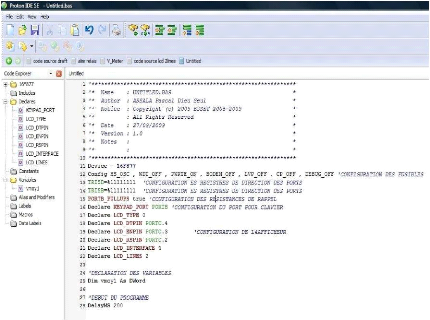
FIGURE 5-7 : PRESENTATION DE L'INTERFACE
UTILISATEUR DE PROTON IDE
5-10 PROGRAMMATEUR DE PIC16F877 SOUS ICPROG
Pour pouvoir actualiser le programme de pilotage du pic chaque
fois que des imperfections devaient survenir pendant la phase de
réglages et des différents tests, la phase de réalisation
a débuté par la réalisation d'un programmateur dont le
prototype a été téléchargé à partir
du site internet du propriétaire . C'est un programmateur permettant de
programmer une large gamme de PIC récents (12C508, 12C509, 16F84,
16F877...) mais aussi la plupart des mémoires EEPROM série
à protocole I2C de type 24Cxx, ou 24LCxx. Il se connecte simplement
à l'interface parallèle d'un PC. En effet, celui-ci est
distribué selon la loi du "freeware" (libre de droits), nous
remercions vivement son auteur, monsieur Bonny
GIJZEN. Le cout de réalisation de cette carte est
évalué en fonction des composants utilisés listés
ci-après.
Résistances 5%:
R1 à R6 ; R17: 1 k? (marron, noir, rouge)
R7 à R9: 2,2 k? (rouge, rouge, rouge)
R10 à R14: 10 k? (marron, noir, orange)
R15; R16: 330 ? (orange, orange, marron) Condensateurs:
C1: 1000 uF 25 volts (électrochimique à sorties
radiales)
; C3: 10 à 22 uF 25 volts (électrochimique à
sorties radiales) C4; C6; C7: 100 nF (mylar)
C5: 330 pF (céramique)
Semi-conducteurs:
D1; D2: 1N4007
D2 à D7: 1N4148
L1: Led 5mm. verte
L2: Led 5mm. orange
L3: Led 5mm. rouge
T1 à T3: BC557
CI1: 7407
CI2: 7812
CI3: 7805 Divers:
1 Prise DB25 mâle coudée pour circuit
imprimé
2x5 broches de barrette sécable femelle
2 Supports de circuits intégrés à 8 broches
1 Support de circuit intégré à 14 broches 1 Support de
circuit intégré à 18 broches
1 Support de circuit intégré à 28 broches
étroit 1 Support de circuit intégré à 40 broches
1 Bornier à 2 vis au pas de 5,08
1 transformateur moulé 2x12 volts 2VA Visserie et
entretoises de 3 mm.
En se référant à la grille des prix
utilisée pour la réalisation de la carte de contrôle, le
cout de revient de cette carte est de 60750 FCFA.
Le tableau 5-2 suivant donne une idée plus
détaillée des prix.
DEVIS MATERIELS
Désignation
|
Valeurs
|
Quantité
|
P.U
|
Total
|
Resistor
|
xx
|
17
|
500
|
8500
|
Led 5mm
|
verte
|
1
|
350
|
350
|
Led 5mm
|
orange
|
1
|
350
|
350
|
Led 5mm
|
rouge
|
1
|
350
|
350
|
Prise
|
Db25 male
|
1
|
5000
|
5000
|
Support de CI
|
8 broches
|
2
|
300
|
300
|
Support de CI
|
14 broches
|
1
|
300
|
300
|
Support de CI
|
18 broches
|
1
|
300
|
300
|
Support de CI
|
28 broches etroit
|
1
|
500
|
500
|
Support de CI
|
40 broches
|
1
|
800
|
800
|
Transformateur
|
moule 2x15 V
|
1
|
5000
|
5000
|
Plaque cuivrée
|
Presensibilisée
|
1
|
16000
|
16000
|
Frais
|
developpement
|
1
|
5000
|
5000
|
Frais
|
perçage
|
1
|
3000
|
3000
|
DIVERS
|
|
|
|
15000
|
TOTAL
|
|
|
|
60750
|
TABLEAU 5-2 : MATERIEL POUR LA FABRICATION DU
PROGRAMMATEUR
CHAPITRE 6 : REALISATIONS ET ESSAIS
6-1 REALISATIONS
6-1-1 REALISATION DU PROGRAMMATEUR
De nombreux montages font, aujourd'hui, appel à des
microcontrôleurs PIC et à des mémoires série. Parmi
tous les prototypes disponibles, nous avons choisi de réaliser celui
représenté par les figures 6-1, 6-2,
6-3 ci après.
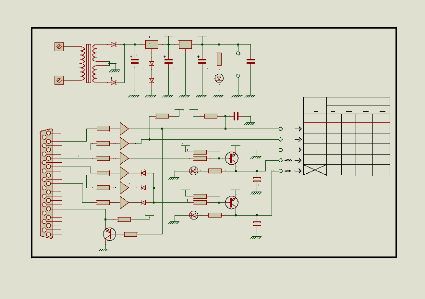
PC
PORT PARALLELE
1
14
2
15
3
16
4
17
5
18
6
19
7
20
8
21
9
22
10
23
11
24
12
25
13
D0 (DATA) Ecriture
D 1 (CLK)
D2 (+VDD)
D3 (+VPP1)
D4 (+VPP2)
D5 (+VPP3)
ACK (DATA ) Lecture
TRANSFORMATEUR
D1
2x15V 3,2VA
1N4007
BC557C
T1
1K
R1
1K
R2
1K
R3
1K
R4
1K
R5
1K
R6
CI1 = N1 à N6 = 7407
R14 10K
D2
1N4007
11
13
9
3
5
1
R9 2,2K
N1
N2
N3
N4
N5
N6
8
2 D5
4 D6
1N4148
D7
6
1N4148
10
12
C1
1000uF
1N4148
+5V
CI2
7812
D3 1N4148
D4 1N4148
R10 10K
+13V +5V
10uF
+5V
+13V
+5V
CI3
7805
L2
ORANGE
L3
ROUGE
R7 2,2K
R13 10K
10K
R12
R8 2,2K
+5V
R11 10K
C3
10uF
R16 330
R17 1K
L1 VERTE
R15 330
+13V
+5V
CI1
14
7
T2 BC557C
T3 BC55C
C5 330pF
C4
100nF
C7
C6
100nF
100nF
DATA
CLK
GND
EEPROM 24LCxx 8b
|
MICROCONTROLEURS
|
8b 18b 28b 40b
|
SUP1
|
SUP2 SUP3 SUP4 SUP5
|
5
|
7
|
13
|
28
|
40
|
6
|
6
|
12
|
27
|
39
|
1-2-3-4-7
|
8
|
5
|
8 - 19
|
12 - 31
|
8
|
1
|
14
|
20
|
11 - 32
|
|
4
|
4
|
1
|
1
|
FIGURE 6-1 : SCHEMA ISIS DU PROGRAMMATEUR
PROPIC 2
Ce montage, grâce à sa simplicité va
pouvoir être réalisé sur une petite carte pré
sensibilisée simple face selon le typon de la figure
6-2 réalisé avec le logiciel ARES de PROTEUS. Ce
schéma n'a pas été modifié et les connexions
demeurent telles que l'auteur les a conçues.
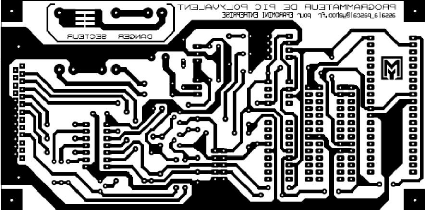
FIGURE 6-2 : TYPON POUR PROGRAMMATEUR
PROPI
Suivant ce typon nous avons réalisé la carte
représentée à la
figure 6-3.
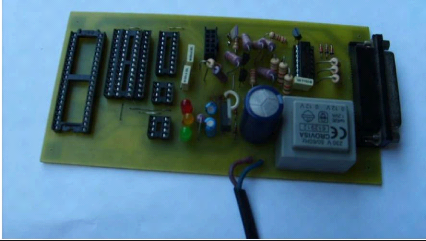
FIGURE 6-3 : PROGRAMMATEUR DE PIC
REALISE
6-1-2 REALISATION DE LA CARTE DE
CONTROLE
La mise en oeuvre de ce travail requiert l'utilisation de
ressources diverses. Les études mécaniques faites ici ne sont pas
à même de produire après réalisation un
résultat fiable. Elles ont été menées dans le seul
but de donner une image de la représentation réelle de la
bâtisse mécanique afin qu'ayant par la suite fait une
évaluation des différents mouvements nous déterminions les
différents mécanismes d'entrainement et appareil de
détection.
La carte de contrôle à microcontrôleur dont
le schéma a été présenté plus haut est
entièrement réalisée avec le logiciel proteus
de LABCENTER dont les versions d'évaluation sont
téléchargeables gratuitement sur le site du fabricant. Elle tient
sur une plaque pré- sensibilisée double face de 20 cm x 13 cm. Le
type de relais doit répondre à la disposition du perçage
sur le typon. En effet, sur cette carte, seul le relais R8 a ses deux contacts
NO (Normally open, ouvert au repos) et NC
(Normally Closed, fermé au repos) utilisés. Les
autres relais notamment R1 à R6 et R9 n'ont que le contact NO
utilisé. Pour ce qui est de l'alimentation, bien s'assurer que
tous les relais utilisés supportent la même tension
d'alimentation. Pour le cas d'une alimentation par transformateur,
prévoir un transformateur de 2 x 15 V. Cette carte utilise en tout 3
tensions différentes à savoir :
· 5V pour l'alimentation des circuits
intégrés
· 12V pour l'alimentation des relais
· 220V pour l'alimentation des bobines des contacteurs
externes
Il est conseillé de prendre toutes les dispositions
nécessaires pour éviter tout contact avec les parties actives
sous tensions ou même après la mise sous tension du fait de la
charge rémanente qui pourrait rester existante aux bornes des
condensateurs de filtrage.
Cette carte a les capacités de fonctionner dans des
applications diverses par juste changement du code source en mémoire du
microcontrôleur par un autre adéquat. Il est plus indiqué
de prévoir dans le matériel un support de circuit
intégré de 40 pattes sur lequel on pourra à volonté
embrocher le microcontrôleur. Cela permettra de s'épargner les
multiples soudures chaque fois ou le microcontrôleur devra être
reprogrammé.
Les figures 6-4, 6-5, 6-6
représentent le typon, et l'implantation des
composants.
Pour ce qui est des difficultés de fabrication, en
fabricant la carte électronique avec les typons des deux faces du
schéma, les pistes réalisées étaient d'une
très mauvaise qualité pour celles qui sont apparues constituant
pour la plupart des court circuits. D'autres par contre avait simplement
été effacées.
Pour pouvoir réaliser une carte assez
présentable et assurant un minimum de risque de court circuit entre les
pistes, le moyen utilisé était de modifier le schéma
donnant ainsi la possibilité de tracer des pistes un peu plus grandes
avec un espace assez sécurisant entre elles et réduisant le
risque de coupure ou de court circuit après les procédés
chimiques de réalisation.
La figure 6-4 est celle qui
représente la face supérieure de la carte électronique
double face. C'est sur cette face que sont montés les
composants. Le nombre de pistes sur cette face a
été réduit au minimum pour diminuer le nombre de vias et
pour minimiser les imperfections de gravure.
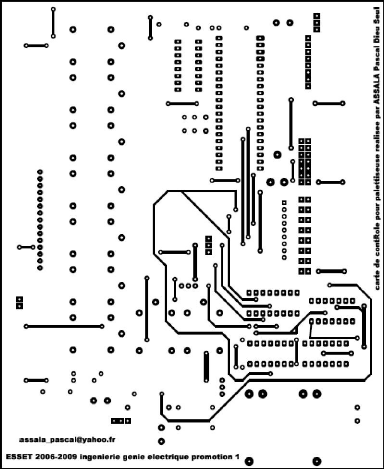
FIGURE 6-4 : FACE SUPERIEURE COTE
COMPOSANTS
La figure 6-5 ci-après
représente le typon coté soudure. Cette face est le lieu
principal des différentes connexions du montage. Du fait de sa
complexité, l'image a perdu ses propriétés d'origine et
tout contrairement à la précédente, elle ne pourrait pas
être utilisée comme typon de réalisation.
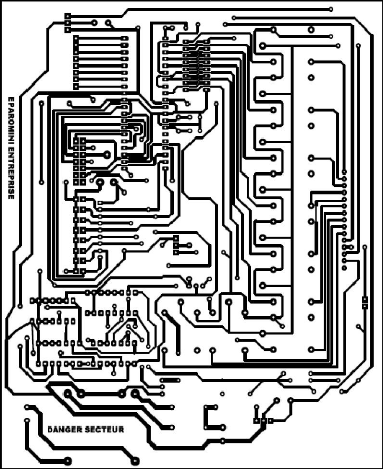
FIGURE 6-5 : FACE INFERIEURE
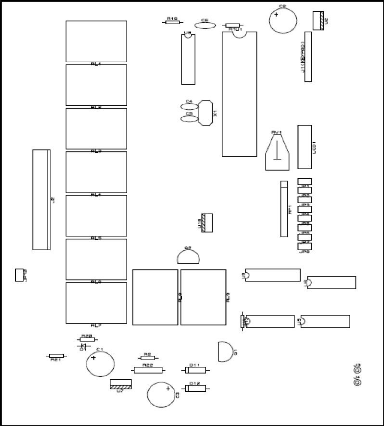
Pendant la disposition des composants de la carte de commande,
le souci principal était de les placer tel que les relais qui pourraient
véhiculer des courants importants assez loin du microcontrôleur.
Cela permet d'éviter des dysfonctionnements qui pourraient
résulter des effets dus à l'incompatibilité
électromagnétique de ces différents composants avec le
microcontrôleur au regard des niveaux de courants d'usage.
FIGURE 6-6 : IMPLANTATION DES
COMPOSANTS
6-1-3 LE CLAVIER
La majeure partie du travail de conception
électronique de ce projet est faite avec le logiciel proteus. Dans sa
bibliothèque de composants intégrée, on trouve deux
claviers de même type. Un clavier de 15 touches et un autre de 12
touches. La configuration ici est du type matriciel. Ce type de clavier est
aussi meilleur dans la réalisation électronique à cause de
son nombre de broches de sorties réduit. En effet, un clavier matriciel
de 12 touches comporte 4 lignes et 3 colonnes. Cette configuration permet de
gérer plusieurs états externes avec le moins possible
d'entrées du microcontrôleur utilisées. Par contre, il
existe des types différents mais aucun dans sa configuration n'offre le
même avantage.
Sur le marché local il n'a pas été
possible de trouver le clavier de type matriciel. Celui que nous avons pu avoir
est du type à sortie commune réalisé sur une logique selon
laquelle chaque bouton poussoir du clavier a une de ses bornes raccordée
à un point commun et l'autre borne représentant la touche
correspondante. Cette configuration est assimilable à un montage en
étoile. Il offre pour un nombre total de touches d'entrées
N, un nombre de sorties S=N+1. Pour avoir un
maximum de broches d'ENTREE/SORTIES configurables sur le microcontrôleur,
il suffira juste de supprimer certaines lignes de la carte du clavier et de
refaire certaines nouvelles connexions nécessaires pour avoir notre
clavier matriciel. Les deux types de clavier cités dans cette section se
présentent sous les schémas électriques de la
figure6-7.

com
#
1
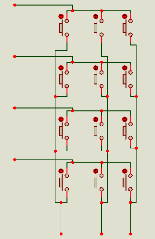
FIGURE 6-7: CLAVIER A POINT COMMUN ET CLAVIER
MATRICIEL
Les valeurs des autres composants utilisés sont
spécifiées sur la liste des composants de la page suivante. Pour
ce qui est des résistances, pour un souci de taille physique, celles
utilisées sont des résistances de 0.25Watt.
6-1-4 IMAGES DE LA CARTE DE CONTROLE
Apres avoir réalisé le circuit imprimé,
soudé les différent composants, la carte qui résulte de
notre étude se présente comme l'illustrent les
figures 6-8, 6-9 et les compléments
placés en annexe.
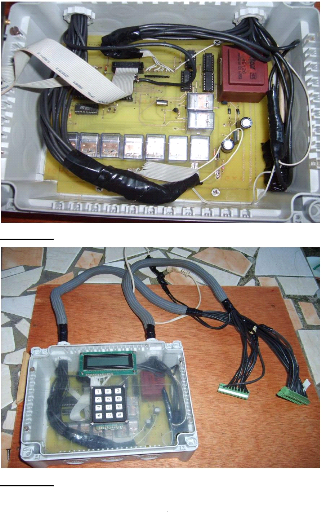
FIGURE 6-8 : CARTE DE CONTROLE MONTEE DANS UN
BOITIER
FIGURE 6-9 : VUE COMPLETE DE LA
CARTE
54
6-2 ESSAIS DU PROTOTYPE
La carte de contrôle conçue ne pourra
normalement fonctionner que si elle est raccordée au système
à piloter. Pour pouvoir réaliser des essais, nous avons mis sur
pied un banc d'essai constitué principalement de deux types de
matériel.
· les interrupteurs jouant le rôle des
différents capteurs de la palettiseuse et le commutateur pour la
sélection des deux modes de fonctionnement.
· Les lampes qui matérialisent la commande
envoyée par le microcontrôleur sur les différents
récepteurs électriques du système.
Les figures 6-10 et 6-11
représentent la face avant du banc d'essai et le point de
raccordement respectivement.
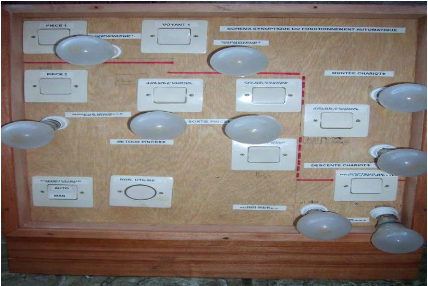
FIGURE 6-10 : BANC D'ESSAI REALISE POUR TEST
DU PROTOTYPE
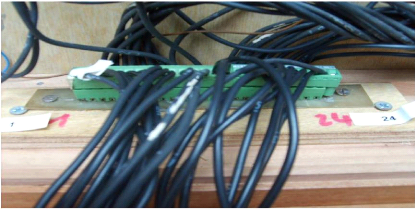
FIGURE 6-11 : POINT DE CONNEXION ENTRE LA CARTE ET
LE BANC
D'ESSAI
Avant mettre la carte en marche, nous nous servons du
programmateur de pic pour transférer le code source dans la
mémoire du microcontrôleur. Ce transfert se fait après un
paramétrage préalable du logiciel ICPROG que nous utilisons pour
communiquer avec le programmateur et ainsi transmettre les instructions de
fonctionnement au microcontrôleur. Ce logiciel peut être
utilisé gratuitement, et même être diffusé. Il ne
doit pas être modifié, tous ses fichiers doivent être
distribués ensemble, et il ne doit servir qu'à des fins
légales; telles sont les conditions de l'auteur.
Sur la figure 6-12 sont
indiqués les différents paramétrages à effectuer
dans ICPROG.
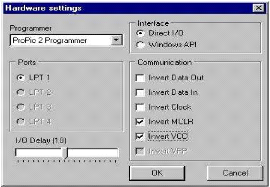
FIGURE 6-12 : PARAMETRAGE DE ICPROG POUR
PROPIG 2
Après avoir ainsi paramétré le logiciel
ICPROG, le programmateur branché sur le port LPT1 de
l'ordinateur, la seconde étape consiste à indiquer la source du
fichier programme à transférer au microcontrôleur. Ce
fichier doit avoir l'une des extensions des fichiers pris en charge par ICPROG.
Dans la suite nous indiquerons au logiciel le type de composant présent
sur le programmateur et que nous voulons programmer. Sur l'onglet
SETTINGS de l'interface utilisateur de ICPROG, on va choisir
le PIC16F877 selon la figure 6-13.
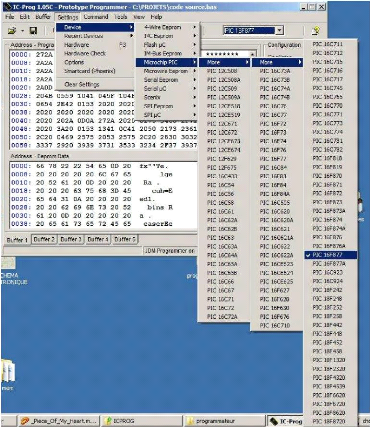
FIGURE 6-13 : CHOIX DU COMPOSANT A PROGRAMMER
SOUS ICPROG
Une fois le composant à programmer choisi, il ne reste
plus qu'à vérifier que le programmateur est connecté au
secteur. Si c'est le cas, démarrer le transfert en cliquant sur
l'icône de programmation du composant.
Lorsque le transfert du code source est terminé sans
erreur, le logiciel affiche un message de confirmation à la suite
duquel, on peut fermer l'interface, débrancher le programmateur du
secteur, le
déconnecter de l'ordinateur puis enlever le
microcontrôleur et le monter sur la carte de contrôle. La
figure 6-14 présente le programmateur
connecté sur le port LPT1 d'un ordinateur de bureau
pendant la mise en oeuvre.
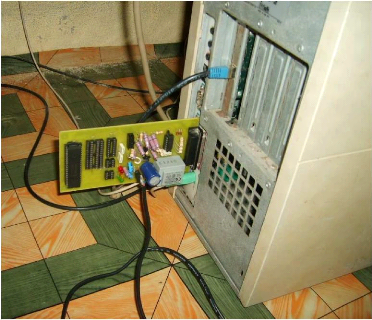
FIGURE 6-14 : PROGRAMMATEUR SUR PORT
LPT1
C'est au bout de toutes ces étapes
préliminaires et indispensables que nous pouvons procéder aux
essais proprement dits du prototype. Une fois le microcontrôleur
entièrement programmé et démonté du support du
programmateur, il est monté sur le support circuit intégré
prévu à cet effet sur la carte de contrôle.
Avant la mise en marche, il faut s'assurer que les
connexions entre la carte et le banc d'essai dans notre cas sont toutes
établies. Lorsque tout cela est fait, alimenter le banc
d'essai en premier puis la carte. A partir de ce
moment, le fonctionnement et les vérifications
sont tous pris en charge par le microcontrôleur.
Dans l'impossibilité de joindre une vidéo
à ce document, nous avons
figure 6-
pris des images de l'ensemble fonctionnant. La
15 représente une
étape de fon ctionne
ment au bout de laquelle l'utilisateur pourra
choisir de restaurer les données en mémoire
après les avoir consultées ou de
.
rentrer des nouvelles données de
fonctionnement
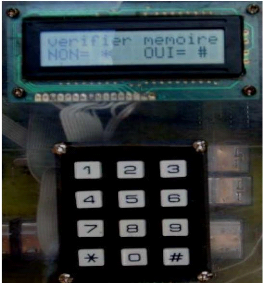
FIGURE 6-15 :
SYSTEME ATTENDANT LA COMMANDE DE
L'OPERATEUR
6-3 DEVIS DE REALISATION
6-3-1 DEVIS DE LA CARTE DE COMMANDE
Le tableau 6-1 suivant
récapitule le matériel utilisé pour la réalisation
de la carte électronique.
DEVIS MATERIELS
|
Désignation
|
Valeurs
|
Quantité
|
P.U
|
Total
|
Résistor
|
270
|
18
|
500
|
9000
|
Résistor
|
2k
|
3
|
500
|
1500
|
Condensateur
|
10u
|
2
|
500
|
500
|
Condensateur
|
100u
|
1
|
1200
|
1200
|
Circuit Intégré
|
PIC16F877A
|
1
|
29800
|
29800
|
Circuit Intégré
|
7805
|
2
|
2000
|
4000
|
Circuit Intégré
|
74HC112
|
1
|
1500
|
1500
|
Circuit Intégré
|
74HC00
|
1
|
1500
|
1500
|
Circuit Intégré
|
74HC112
|
1
|
1500
|
1500
|
Circuit Intégré
|
74HC4072
|
1
|
1500
|
1500
|
Circuit Intégré
|
7812
|
1
|
1500
|
1500
|
Diodes
|
1N4007
|
12
|
500
|
6000
|
Connecteur
|
CONN-SIL8
|
1
|
|
DIVERS
|
Connecteur
|
SIL-100-15
|
1
|
|
DIVERS
|
Jumper
|
JUMPER
|
8
|
|
DIVERS
|
Jumper
|
JUMPER2
|
1
|
|
DIVERS
|
Afficheur
alphanumérique
|
LMO44L
|
1
|
39000
|
39000
|
Relais
|
G5Q-14-DC12
|
9
|
5000
|
45000
|
Clavier
|
4x3 touches
|
1
|
11000
|
11000
|
Support de CI
|
40 broches
|
1
|
800
|
800
|
Transformateur
|
moule 2x15 V
|
1
|
5000
|
5000
|
Plaque cuivrée
|
Pré sensibilisée
|
1
|
20000
|
20000
|
Frais
|
développement
|
1
|
20000
|
20000
|
Frais
|
perçage
|
1
|
3000
|
3000
|
DIVERS
|
|
|
|
15000
|
TOTAL
|
|
|
|
218300
|
|
TABLEAU 6-1: MATERIEL UTILISE POUR LA REALISATION DE
LA CARTE DE
CONTROLE.
NB : Outre les divers, l'ensemble de
matériel présent dans le tableau 6-1
précédent est facturé selon la grille des
prix de MEGATEC ELECTRONIQUE situé
à la montée aurore à Yaoundé-Cameroun.
6-3-2 DEVIS POUR ENSEMBLE ELECTRIQUE
Le tableau 6-2 suivant représente le
matériel électrique à installer sur la machine pour une
prise en charge complète par la carte de contrôle.
Repères
|
Désignation
|
Caractéristiques
|
quantité
|
observations
|
Admission
|
Moteur électrique
|
1.5KW - 1495Trs/MIN- 3A 2 Ex: LS 80 L
|
1
|
Sur l'arbre de ce
moteur tournant dans un seul sens
Seront montés deux pignons dont le rapport des dents
d'engrenage est de 2
|
Convoyeurl
|
Moteur électrique
|
1.5KW -
1495Trs/MIN- 3A
2 Ex: LS 80 L
|
1
|
Moteur frein pour
assure le bon positionnement des chaines du convoyeur1. 1
sens de rotation
|
|
Interrupteur de position
3 ex : XCK-P110
ou XCK-M110
|
2
|
Ces deux capteurs
montés dans le convoyeur 1 assurent la transmission au
système de l'information sur la présence des pièces.
|
|
Détecteur de proximité
1 Photo
interrupteur de
positionnement ex :
OPKBKTIR0111S
3 détecteurs de
position inductif XS ou photoélectrique XUE
|
1
|
Détecteur à rayon
lumineux comportant un contact à fermeture. Il servira
notamment à renseigner le système sur le passage du bois des
chaines du convoyeur 1 vers les courroies du convoyeur 2
|
Convoyeur2
|
Moteur électrique
avec réducteur
|
Moteur électrique:1.5KW - 1495Trs/MIN- 3A
2 Ex: LS 80 L Réducteur:
2 orthobloc 2000
|
1
|
Le fonctionnement
intermittent de ce moteur freiné impose l'utilisation
d'un réducteur de faible rapport à défaut d'utiliser un
moteur pas à pas. En plus, pour le respect scrupuleux des intervalles
pour l'aération.
|
Chariot
|
Moteur électrique
|
1.5KW -
1495Trs/MIN- 3A
2 Ex: LS 80 L
|
1
|
Utilisé pour
l'entrainement des pinces, ce moteur doit être
freiné pour maintenir une stabilité des pinces pendant les
opérations de descente du chariot.
|
|
Interrupteur de
position
3 ex : XCK-P110
|
1
|
De même type que ceux du convoyeur1, celui-ci est
chargé de transmettre au
|
|
|
|
ou XCK-M110
|
|
système l'information sur la
position haute du chariot.
|
|
1.5KW -
1495Trs/MIN- 3A
2 Ex: LS 80 L
|
1
|
Ce moteur frein
supporte de grandes charges
dans l'ensemble car il est appelé à soulever et
décharger le chariot. Pour cela il a deux sens de marche
|
|
Détecteur de proximité, 1 Photo interrupteur de
positionnement ex : OPKBKTIR0111S
3 détecteurs de position inductif XS ou
photoélectrique XUE
|
1
|
Même type que le
voyant 1
|
Support de palette
|
Moteur électrique
|
1.5KW -
1495Trs/MIN- 3A
2 Ex: LS 80 L
|
1
|
Pour effectuer un
décalage chaque fois lors du rangement, ce moteur sera
chargé de mettre en rotation la vis sans fin. Ce système
intégrant un embrayage pour éviter de secouer la palette
pendant les multiples démarrages et arrêts.
|
|
Interrupteur de
position
3 ex : XCK-P110
ou XCK-M110
|
1
|
De même type que ceux du convoyeur1, celui-ci est
chargé de transmettre au système l'information sur la
Présence de la palette.
|
divers
|
contacteurs
|
3 LC1-K06
|
2
|
Pour moteur des
convoyeurs 2 et 2
|
|
Pour moteur du
support de palette.
|
|
Moteurs de Tapis
d'admission, pinces et chariot.
|
|
Contacteur de
marche manuelle
|
|
3 Bouton à
voyant XB5-AA31
|
3
|
NO avec rappel
automatique. Pour la marche par à coups de moteurs
à un sen de rotation
|
|
3 commutateur
de type CMB ou Bouton à voyant XB5-AA31
|
1
|
Deux contacts et
deux positions avec retour
automatique à la position
initiale. mise en marche du système. DCY
|
|
3
|
Trois contacts et
trois positions stables. Pour la
marche par à coups des
moteurs à deux sens de
rotation.
|
|
1
|
Deux positions NC et NO stables. Permet le choix du type de
fonctionnement MAN/AUTO
|
|
TABLEAU 6-2: LISTE DE MATERIEL
ELECTRIQUE
6-4 COMPARAISON DES CHARGES DE PERSONNEL
Actuellement, dans la figure 1-2
qui décrit le processus de production des parquets, le double service de
rangement présenté aux étapes 5 et 6 utilise seize (16)
personnes à la fois soit huit directement à la sortie de la
machine de coupe et huit autres pour le rangement assurant la circulation de
l'air pour les séchoirs. La seule idée de réduire ces deux
services en un seul constitué d'un personnel réduit de
moitié est un facteur avantageux pour opérer un choix
technologique.
L'usage du système de la palettiseuse devra imposer la
mobilisation d'un nombre inférieur d'ouvriers en permanence ; c'est
ainsi que dans le cadre le plus simple du fonctionnement du système, le
personnel requis pourra être caractérisé par un conducteur
assisté par deux manoeuvres. En effet pour effectuer des corrections au
moment où surviennent des défauts, le conducteur au moyen de son
pupitre de marche manuelle se charge de faire mouvoir les différentes
parties individuelles de la machine. Le mode de commande manuel ne comportant
pas d'auto maintient de l'organe commandé, la commande est valide et le
reste tant que le conducteur maintient son action sur l'organe de commande. Ce
qui oblige l'opérateur à rester uniquement devant son pupitre.
Parmi les charges générées par le mode
de rangement manuel, on note celles liées à la superficie de
l'entreprise et à l'éloignement des différents services.
Pour une palette pleine placée au séchoir, il faut au
préalable avoir rangé le bois à la sortie de l'OPTICUT,
puis transporter la palette vers le second service de rangement par un manitou,
après ce second rangement, la palette est enfin transportée dans
un séchoir. Par
contre, avec le rangement automatique, les palettes
rangées à la sortie de l'OPTICUT sont directement
destinées au séchoir. On note ici deux des avantages que
possède l'automatisation du système par rapport à la
marche manuelle à savoir.
· Un seul service destiné au rangement.
· Effectif réduit au quart de l'effectif de la
marche manuelle.
Par ailleurs ce système automatique mis en place sera
cause de mise au chômage d'un certain nombre d'employés ; à
première vue le caractère social de l'entreprise conduirait au
rejet de l'automatisation pour assurer un minimum de revenu à un maximum
de citoyens mais la perpétuelle recherche du gain viendra dominer les
conditions de choix et obligera la réduction du personnel.
6-5 PERSPECTIVES
Arrivés au terme de ce travail, nous sommes encore
très loin de déclarer avoir mis sur pied un prototype parfait.
L'étude menée jusqu'ici vient juste poser les jalons. En tenant
compte de toutes ces bases déjà mises sur pied, des études
plus poussées visant l'amélioration tant sur le plan
électrique que mécanique devront être menées afin de
mettre sur pied une machine répondant aux standards internationaux de
l'industrie. L'autre aspect incomplet dans notre travail concerne le programme
:
Les paramétrages de fréquence de fonctionnement
du microcontrôleur dans le code source peuvent être revus pour
assurer une fréquence de fonctionnement plus élevée et
adaptée à une ligne de
production plus accélérée. Cet autre
volet des améliorations provoquera un total réaménagement
dans les différentes temporisations. Le dernier des aspects modifiables
en vue de l'amélioration est la partie de commande de l'admission. Une
stratégie différente peut être mise au point pour aboutir
à la solution proposée. La liste des améliorations
citées ici n'est pas exhaustive. Toutes les contributions en vue de la
production d'un système plus performant seront source d'une progression
significative dans ce projet.
CONCLUSION GENERALE
Finaliser un projet demeure encore une affaire très
difficile dans notre pays. Cela d'autant plus que pour un étudiant, il
faut pouvoir passer de la théorie des simulations logicielles à
la pratique et affronter les coûts de matériel électronique
qui demeurent très élevés. D'autres parts, les domaines de
la conception en général et de l'électronique en
particulier restent une affaire d'une minorité tant dans les
réalisations que dans la vente de matériel ; ceci étant,
il est conseillé de se rassurer de la présence effective sur le
marché du composant à utiliser pendant la conception. Il faut
aussi noter que même si certaines réalisations sont possibles, il
demeure quasiment impossible de réaliser des travaux de haute
précision. Au regard de l'expérience vécue dans ce projet
où il a fallu reprendre deux fois le schéma électronique
et le typon, il n'est pas certain de nos jours de pouvoir réaliser une
carte électronique avec des pistes d'un-demi millimètre (0.5 mm)
de large. Nous en sommes encore loin. C'est là que vient l'occasion pour
nous d'interpeller les uns et les autres.
Le monde aujourd'hui doit son développement à
l'avancée des nouvelles technologies de l'information et de la
communication (NTIC). Comme un véhicule ne servira
à rien à son propriétaire si il n'y a pas de route, la
maitrise des NTIC et le développement chez nous n'auront un sens
réel qu'à partir du moment où nous aurons assez
repoussé les frontières des sciences et de la conception.
Le potentiel y est, il y'en a même qui à
très petite échelle le font déjà, nous avons eu
l'occasion de rencontrer une société qui en a fait sa
spécialité mais beaucoup reste à faire pour pouvoir entrer
dans la course au développement.
|