RESUME
Le présent travail vise à améliorer les
caractéristiques mécaniques du concasseur à cône
SYMONS qui sert à la fragmentation des minerais de Kafundwa. Le but
poursuivi est de prolonger la durée de vie de la nuance A3SS qui est un
acier faiblement allié au nickel utilisé comme matière de
base de fabrication du Lower Mantle.
Plusieurs études ont été menées
pour résoudre le problème lié à la rupture fragile
en cours d'utilisation de ce matériau. Dans notre travail, nous avons
d'abord réalisé les tests de l'influence de la température
sur l'adoucissement du Lower Mantle dans la gamme de températures de
890, 910, 940 et 960°C pour un temps de maintien de 30 minutes dans les
conditions de refroidissement d'un four. A l'issu de ces tests, nous avons
retenu 940°C comme température optimale d'adoucissement qui offre
une dureté Brinell de 212 HB et une résilience de 11,25
J/cm2 contre 280 HB et 5 J/cm2 ; lesquelles
caractéristiques qu'on obtient à l'état brut de
coulée.
Pour que le matériau puisse mieux répondre aux
conditions sévères d'utilisation, les essais de traitement
thermique de trempe suivi d'un revenu ont été effectués.
Les principaux facteurs étudiés au cours de ces essais sont
notamment, le milieu de refroidissement et le temps de maintien. Force est de
constater que la trempe à l'eau accompagnée d'un revenu à
500°C offrent les meilleurs résultats de dureté et de
résilience à savoir 328 HB et 19 J/cm2 à
l'état trempé contre 240 HB et 18,83 J/cm2 pour un
refroidissement dans le four et 303 HB et 12,54 J/cm2 pour
refroidissement à l'air. Le résultat final après revenu
donne 307 HB et 24,13 J/cm2. Les analyses micrographiques ont chaque
fois été effectuées par microscopie électronique
à balayage pour mieux interpréter les résultats.
Les résultats ci-haut révèlent que pour
prolonger la durée de vie de cette nuance d'acier, il faudra faire un
adoucissement et une trempe accompagnée d'un revenu dans les conditions
précitées.
EPIGRAPHE
I
Il y a deux façons de voir la vie, l'une comme si
rien n'était un miracle, l'autre comme si tout était
miraculeux.
Albert Einstein
L'imprévisible est dans la nature même de
l'entreprise scientifique. Si ce qu'on va trouver est vraiment nouveau, alors
c'est par définition quelque chose d'inconnu à l'avance
».
François Jacob
II
DEDICACE
A vous mon père Daniel KASONGO SALUMU et ma bien
aimée mère Claudette UMBA NGOY, pour les sacrifices et efforts
conjugués.
A vous mes frères et soeurs : Agathe MULEZI, Garcia
UMBA, André MULOKO, Patricia MAILA, Isabelle ZUGU, Benjamin MONGOLI,
Gauthier BULUNGO, Polac ILUNGA, KEN MAYUKI merci pour vos prières et que
ce travail soit un exemple à suivre pour vous tous.
A vous mes cousins et cousines, ayez du courage et de la
persévérance dans
vos études.
A vous mes oncles et tantes pour vos prières familiales et
votre soutien.
A vous et vos familles respectives Serge MITONGA BULUNGO,
Valery SASHI, vous avez été pour moi des amis, frère,
oncle, père, merci de m'avoir accompagné durant tout mon parcours
académique.
Aux familles Simplice ILUNGA MONGA, Mbarsso KAMBA, John
MONGOLI pour votre soutien matériel, financier et moral.
A vous feux Grands-pères : Jean UMBA, Hyacinthe FATAKI
et John MONGOLI que la mort a arraché inopinément de la nature
pendant qu'on avait encore besoin de vous. Votre disparition est une grande
blessure dans notre coeur. Que vos âmes reposent en paix.
A vous tous, dont les noms ne figurent pas, trouvez dans ce
travail l'expression de ma très haute considération.
III
REMERCIEMENTS
Ce travail dont nous sommes auteur est le fruit de plusieurs
personnes qui de près ou de loin ont participé à son
élaboration. Que toutes ces personnes trouvent ici notre
reconnaissance.
Nous remercions le Doyen de la faculté polytechnique le
Professeur Guy NKULU WA NGOIE qui malgré ses multiples occupations a
accepté d'assurer la direction de ce travail.
Notre reconnaissance s'adresse également à
l'Assistant Ingénieur Abelard CHOLA pour avoir encadré ce
présent travail, ainsi qu'à l'ingénieur Dieudonné
KYUNGU MUTUMBA chef de service Fonderie/ACP pour nous avoir guidé durant
toute la période de nos expérimentations aux ACP.
Que l'ingénieur KING ZUABISALA chef de service d'appui
à la production/Fonderie/ACP, de même que les agents
affectés à la fonderie trouvent une marque de reconnaissance pour
leur serviabilité lors de nos expériences.
Nos remerciements s'adressent également au corps
académique et scientifique de la faculté de polytechnique de
l'Université de Likasi qui s'est donné la peine pour nous
puissions devenir ce que nous sommes aujourd'hui, finaliste du deuxième
cycle.
Nous ne pouvons terminer ce remerciement sans exprimer notre
gratitude envers nos amis et condisciples avec qui nous avons compati dans la
joie et dans la détresse; nous citons : Prince MUTITI, Merline MAUWA,
Gloria MWAYUMA, Rodrigue BASHALE, Helena ZWAO, Maben KAZADI, Junior TSHITAMBA,
Eloge KITENGE, Joe KAPEND, Jimmy MWEMEDI, Paul KASONGO.
Tous ceux dont leurs noms ne figurent pas dans ce travail,
trouvent notre profonde gratitude.
Jean Claude FATAKI NYEMBO
IV
TABLE DES MATIERES
RESUME
EPIGRAPHE I
DEDICACE II
REMERCIEMENTS III
TABLE DES MATIERES IV
LISTE DES ABREVIATIONS VII
LISTE DES FIGURES VIII
LISTE DES TABLEAUX X
INTRODUCTION 1
CHAPITRE I : GENERALITES SUR LES ACIERS 3
I.1 Définition 3
I.2 Type 3
I.3 Structure et phases de l'acier 3
a) Structure 3
b) Phase 5
I.4 Différentes familles des aciers 7
a) Aciers non alliés 7
b) Aciers faiblement alliés 7
c) Aciers fortement alliés 8
I.5 Propriétés et caractéristiques 9
CHAPITRE II INFLUENCE DES ELEMENTS D'ADDITION SUR LES
PROPRIETES
MECANIQUES DE L'ACIER 11
II.1. L'aluminium 11
II.2. Le carbone 11
II.3. Le chrome 12
II.4. Le cobalt 13
II.5. Le manganèse 13
II.6. Le molybdène 14
II.7. Le Nickel 16
II.8. Le silicium : 17
CHAPITRE III : TRAITEMENT THERMIQUE APPLIQUE AUX ACIERS 18
III.1. Définition 18
III.2. But 18
III.3. Eléments d'un traitement thermique 18
V
III.4. Types de traitements thermiques 19
1. Le recuit 19
2. La trempe 20
3. Le revenu 21
4. La normalisation 22
III.5. Transformation des phases au cours du traitement
thermique 22
a) Mécanisme de la transformation lors de
l'austénitisation 22
b) Constituant intermédiaire 23
c) La transformation martensitique 23
III.6. Influence des éléments d'alliage sur le
traitement thermique 24
a) Influence sur l'austénitisation 24
b) Influence sur la martensite 25
III.7. INFLUENCE DE LA GROSSEUR DES GRAINS D'AUSTENITE SUR
LES
PROPRIETES MECANIQUES 28
CHAPITRE IV : TRAVAUX ANTERIEURS SUR L'A3SS 29
IV.1. Amélioration de la nuance par les ACP
(Inédit) 29
a) Composition 29
b) Caractéristiques mécaniques 29
c) Conditions de traitement thermique 30
IV.2. Amélioration par substitution (mémoire) de
fin d'études 30
CHAPITRE V : MATERIEL ET PROCEDURE EXPERIMENTALE 31
V.1. Matériel 31
V.1.1. Caractérisation des échantillons 31
V.1.2. Essais mécaniques 33
V.1.3. Traitement thermique 37
V.1.4. Micrographie 39
V.2. Procédure expérimentale 42
V.2.1. Fusion 42
V.2.2. Traitement thermique 45
CHAPITRE VI : PRESENTATION ET INTERPRETATION DES RESULTATS 47
VI.1. Caractérisation des échantillons 47
a) HB et KCV 48
b) Traction 48
VI.2. Essais mécaniques 49
VI.2.1. Influence de la température d'adoucissement 49
VI.2.2. Influence du milieu de refroidissement 52
VI
VI.2.3. Influence du temps de maintien 56
VI.2.4. Influence de la température de revenu 57
CONCLUSION 61
BIBLIOGRAPHIE 63
a) Ouvrage 63
b) Articles et publications 63
c) Mémoires 63
d) Notes de cours 63
VII
LISTE DES ABREVIATIONS
F e y : Fer austénite
F e a : Ferrite
Fe3C : Cémentite ou carbure de fer
a : Ferrite magnétique formée à basse
température à structure cubique centré
a' : Martensite quadratique
y : Austénite d'équilibre formée à
haute température à structure cubique à faces
centrées
R e : Limite élastique
R m : Résistance mécanique
R r : Charge de rupture
H B : Dureté Brinell
KCV : Résilience sur éprouvette avec entaille en
V
A3SS : Acier d'amélioration faiblement allié au
Ni-Cr-Mo-Mn
ACP : Ateliers Centraux de Panda
TRC : Transformation en refroidissement continu
TTH : Traitement thermique d'hypertrempe
TTT : transformation temps température
VIII
LISTE DES FIGURES
Figure I.1 : structure cristalline des aciers à
l'état recuit 4
Figure I.2 : germination des phases de l'acier à partir
des grains d'austénite au cours de
refroidissement d'un acier hypoeutectoïde et
hypereutectoïde 5
Figure II.1 : Diagramme fer-carbone 12
Figure III.1 : Cycle d'un traitement thermique 19
Figure III.2 : Zones des températures les plus favorables
pour les différents recuits 20
Figure III.3 : Courbe TTT (acier faiblement allié 0,35%) :
ce diagramme se lit en suivant un isotherme
21
Figure III.4 : Premiers stades de la formation de la phase
austénitique 23
Figure III.5 : Position des atomes de carbone dans la maille
quadratique de la martensite 24
Figure III.6 : Influence des éléments d'alliage sur
le diagramme de phase FeC a) Présence d'un élément
alphagène, le molybdène- b) Présence d'un
élément gammagène, le manganèse
25
Figure III.7 : Diagramme de SCHAEFFLER ; A = austénite, F
= ferrite, M = martensite, les lignes de
pourcentage indiquent la proportion de ferrite dans
l'austénite 27
Figure V.1 : photographie montrant (a) un Analyseur NITON XLT et
(b) sulfo-carbomettre ELTRA
CS800 31
Figure VI.2 principe de l'essai de dureté 34
Figure V.3 : Photographie d'un mouton pendule de Charpy de 300 J
35
Figure V.4 : Photographie d'un four de traitement thermique de
type BENET 37
Figure V. 5 - photographie d'un microscope optique de type
Euromex équipé d'une caméra RD 39
Figure V.6 : Photographie d'une poliseuse fine du type METASERV
41
Figure VI.1 : structure cristallographique de l'alliage à
l'état brut de coulée 49
Figure VI.2 micrographie de l'acier A3SS chauffé à
AC3+30°C et refroidi dans le four 51
Figure VI.3 micrographie de l'acier A3SS chauffé à
AC3+50°C et refroidi dans le four 52
Figure VI.4 : Micrographie de l'acier A3SS chauffé
à AC3+80°C et refroidi dans le four 52
Figures VI.5 : structure de l'A3SS après
austénitisation à 910°C et refroidissement à l'air
55
Figures VI.6 : structure de l'A3SS après
austénitisation à 910°C et refroidissement à l'eau
55
Figures VI.7 : structure de l'A3SS après
austénitisation à 910°C pendant 30 minutes et
refroidissement
à l'eau 57
Figures VI.8 : structure de l'A3SS après
austénitisation à 910°C pendant 15 minutes et
refroidissement
à l'eau 57
Figure VI.9 : Micrographie de l'A3SS après revenu à
600°C 59
IX
Figure VI.9 : Micrographie de l'A3SS après revenu
à 400°C 60
Graphique VI.1 : l'Influence de la température
d'adoucissement sur HB et K 50
Graphique VI.2 : Histogramme des valeurs moyennes de
résilience et dureté après austénitisation
à
910°C et refroidissement selon les milieux 54
Graphique VI.3 : Evolution de la dureté et
résilience en fonction du temps 56
Graphique VI.4 : courbes de dureté et résilience
après revenu 58
X
LISTE DES TABLEAUX
Tableau I.1 : valeurs typique des caractéristiques
mécaniques 9
Tableau IV.1 : Composition en fourchette de la nuance A3SS 29
Tableau IV.2 : Marge des propriétés
mécanique de l'A3SS attendues après revenu à 600°C
29
Tableau VI.1 : Caractérisation chimique de la nuance A3SS
47
Tableau VI.2 : propriétés mécaniques
à l'état brut de coulée 48
Tableau VI.3 : Essais de traction 48
Tableau VI.4 : Essais de résilience de l'A3SS après
traitement d'adoucissement 50
Tableau VI.5 : moyenne de valeur de résilience et de
dureté aux températures d'adoucissement 50
Tableau VI.6 : Essais de dureté et résilience de
l'A3SS après austénitisation à 910°C pendant 30
minutes 53
Tableau VI.7 valeurs moyennes de dureté et
résilience après austénitisation à 910°C 53
Tableau VI.8 : Evolution des propriétés en fonction
du temps de maintien 54
Tableau VI.9 : Valeurs moyennes de dureté et
résilience en fonction du temps 54
Tableau VI.10 : résultat du revenu à
différentes températures pendant 30 minutes de maintien 58
Tableau VI.11 : Valeurs moyennes de dureté et
résilience après revenu pendant 30 minutes 58
1
INTRODUCTION
De tous les alliages métalliques, les aciers sont parmi
ceux les plus couramment employés dans les applications industrielles.
La grande diversité de leurs nuances et la possibilité de
réaliser les traitements thermomécaniques conditionnant les
propriétés mécaniques de ces aciers permettent de couvrir
une gamme d'applications extrêmement large. Leurs
propriétés mécaniques sont étroitement liées
à la microstructure de l'alliage, donc à sa composition et aux
traitements thermiques appliqués. Enfin, leurs faibles coûts
présentent un grand intérêt pour leurs utilisations.
Les éléments d'alliages, entrant en solution
solide interstitielle ou substitutionnelle, jouent un rôle
prépondérant dans les différentes transformations de
phases des aciers. L'étude de leur rôle, de leur influence et des
conditions dans lesquelles elles surviennent constitue donc une étape
incontournable dans la compréhension des différentes
propriétés d'un alliage. Ces éléments influent sur
les différentes propriétés en modifiant les
transformations, leur cinétique, et par conséquent, les
microstructures obtenues.
L'objectif de ce travail consiste à donner une longue
durée de vie d'une nuance d'acier (A3SS) devant être
utilisé pour la fabrication du lower mantle (pièce du concasseur
à cône fabriquée en acier faiblement allié). L'acier
doit présenter des caractéristiques mécaniques
élevées après un cycle des traitements thermiques :
l'obtention d'un optimum entre la résilience (K), la dureté (HB)
et d'une bonne résistance mécanique sera visée.
Ainsi, notre travail va s'orienter vers différents
essais mécaniques et traitements thermiques appliqués conduisant
à l'obtention des bonnes propriétés mécaniques.
Notre étude se penchera aussi sur l'influence d'éléments
d'alliage, de la température de chauffage et du milieu de
refroidissement pour le traitement thermique considéré. Une
compréhension approfondie de leurs effets séparés et
conjoints nous amènera logiquement à la proposition d'un cycle
qui comprend la température de chauffage, le temps de maintien et le
milieu de refroidissement, dont les propriétés correspondront au
mieux à celles recherchées.
2
Ce présent travail est divisé en deux grandes
parties à savoir :
- La première partie bibliographique donne un
aperçu général sur les aciers, les différents
éléments d'alliage et leur influence sur les
propriétés mécaniques, ainsi que les différents
modes de traitement thermique. Cette partie fait aussi référence
à quelques travaux antérieurs sur la nuance A3SS tout en
dégagent les conclusions de chacun.
- La deuxième partie expérimentale est
consacrée au matériel et procédure expérimentale
ainsi qu'à la représentation et analyse des résultats.
3
CHAPITRE I
GENERALITES SUR LES ACIERS
I.1 Définition
Les aciers sont les métaux les plus répandus
dans l'industrie et la construction mécanique d'une manière
générale, on les désigne ainsi par Fer + Carbone se
trouvant dans une proportion allant de 0,02 à 2% en masse (Air Formation
édition octobre 2007). Pour résister à ces sollicitations,
des éléments chimiques peuvent être ajoutés à
sa composition en plus du carbone. Ces éléments sont
appelés éléments d'additions, les principaux sont le
manganèse (Mn), le chrome (Cr), le nickel (Ni), le molybdène
(Mo).
I.2 Type
On distingue plusieurs types d'aciers selon le pourcentage
massique de carbone
qu'ils contiennent :
- les aciers hypoeutectoïdes de 0,0101 à 0,77 % de
carbone qui sont les plus
malléables; ils sont durcis par des
précipités de cémentite en faible quantité ;
- les aciers perlitiques ou eutectoïdes contenant du fer
á et la cémentite
- les aciers hypereutectoïdes : de 0,77 à 2,11 % de
carbone qui sont les plus durs
- il existe toutefois des aciers lédéburitiques
(Matériaux Métalliques).
I.3 Structure et phases de l'acier
a) Structure
À l'état stable, dit « recuit », la
structure de l'acier dépend de la composition :
? en dessous de 0,008 % de carbone en masse, le carbone est
entièrement dissout dans la maille de fer á ; on parle de «
fer » ;
? entre 0,008 et 0,022 %C, on a dépassé la
limite de solubilité du carbone dans le fer ; le carbone forme du
carbure de fer Fe3 C appelé « cémentite
» ; ce sont des aciers extra-doux, qui ont une limite élastique Re
faible ;
? entre 0,022 et 0,77 %C, on a une structure biphasée
ferrite/perlite (la perlite est un eutectoïde lamellaire) ; les grains de
ferrite peuvent être de forme régulière, ou bien
aciculaires (en forme d'aiguille), cette structure est fragile et a une
mauvaise résistance à la corrosion, raison pour laquelle on
l'évite ; pour 0,77 % C, on a uniquement de la perlite ;
? entre 0,77 et 2,1 %C, on a une structure biphasée
cémentite/perlite.
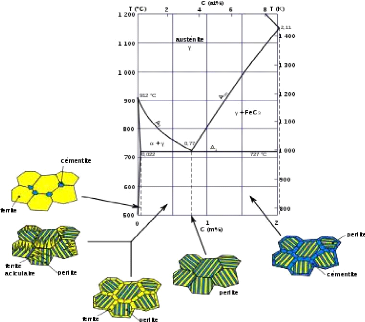
4
Figure I.1 : structure cristalline des aciers
à l'état recuit
Pour un acier hypoeutectoïde, on passe d'abord par une
zone á + ã entre les températures A3 et A1, on a donc
d'abord formation de ferrite dite « proeutectoïde » (qui se
forme avant l'eutectoïde) qui « prend la place des joints de grain
». Puis, la perlite se forme à la température A1. On se
retrouve fréquemment avec des grains de perlite entourés de
ferrite.
Pour un acier hypereutectoïde, on passe d'abord par une
zone cémentite + ã entre les températures Acm et A1, on a
donc d'abord formation de cémentite proeutectoïde qui « prend
la place des joints de grain ». Puis, la perlite se forme à la
température A1 (les aciers I théorie/Métallurgie
générale).
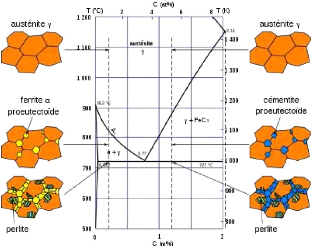
5
Figure I.2 : germination des phases de l'acier
à partir des grains d'austénite au cours de refroidissement d'un
acier hypoeutectoïde et hypereutectoïde
b) Phase
b.1) Austénite
l'austénite (fer ) est une phase du fer stable entre
910°c et 1394°c. Elle a une structure cristallographique cubique
à faces centrées et amagnétique. Cette structure permet
une grande solubilité du carbone (jusqu'à 2,1% massique à
1147°c).
Certains éléments d'alliage comme le
manganèse, nickel, azote augmentent la plage de stabilité de
l'austénite, ils sont dits « gammagènes ». Avec un
dosage suffisant, ils permettent, grâce à une trempe, d'obtenir de
l'austénite à température ambiante à l'état
métastable. D'autres éléments (silicium, molybdène
ou chrome par exemple) tendent à déstabiliser l'austénite.
On appelle ces éléments « alphagènes »
b.2) Ferrite
La ferrite (fer ) est une phase de l'acier, sous la forme
d'une structure cubique centrée. Cette phase est observable lorsque la
température est inférieure à 912°c ou
supérieure à 1394°c. Si la teneur en carbone est très
faible, le passage de la structure cubique à faces centrées
(austénite) du fer à la structure cubique centrée
(ferrite), lorsque la température descend en dessous de 912°c,
résulte de l'apparition progressive du ferromagnétisme dans la
structure cubique centrée. En effet, pour des raisons liées
à
6
l'arrangement cristallin, l'alignement des spins responsable
du ferromagnétisme tend à stabiliser la structure cubique
centrée.
b.3) Cémentite
La cémentite ou carbure de fer est un composé
chimique dont la formule est Fe3C
et ayant la structure orthorhombique. Elle contient 6,67% de
C. c'est un composé très dur (Dureté Vickers HV = 700
à 800) mais très fragile
(A = 0%, Rm = 700 N/ ).
mm2
Elle forme avec la ferrite un composé appelé
perlite.
b.4) Perlite
Agrégat eutectoïde ayant une structure de lamelles
alternées de ferrite et de
cémentite, provient de la décomposition de
l'austénite. Ce constituant contient 0.8%C, il offre une dureté
usinable et une bonne résistance. La perlite est dure (HB200),
résistante (Rm850 MPa) et assez ductile (A%10).
b.5) Martensite
En ce qui concerne les aciers, la martensite (fer a)
est une phase métastable
Cette phase cristallise dans le système quadratique.
On peut la considérer comme une solution solide de carbone dans le
réseau distordu de la ferrite. Cette distorsion est
caractéristique d'un acier refroidi rapidement depuis la
température d'austénitisation, et elle coexiste souvent avec la
bainite et la troostite. La martensite possède une grande dureté
(HV = 700 - 900), mais présente l'inconvénient d'être
très fragile. Elle est ferromagnétique comme la ferrite. Elle
peut martensite se présenter sous différentes morphologies :
massive ou aciculaire. Cette dernière forme est de loin la plus
répandue dans le cas des aciers faiblement alliés (S.BENSAADA
2010).
b.6) Bainite
La bainite est le nom d'une microstructure de l'acier
découverte en 1930 par E.S. Davenport et Edgar Bain lors de leurs
études de la décomposition isotherme de l'austénite. Cette
phase se présente sous la forme d'un agrégat de plaquettes (ou
lattes) de ferrite et de particules de cémentite. Elle se forme lorsque
le refroidissement de l'acier est trop rapide pour obtenir la formation de
perlite mais trop lent pour obtenir la formation de martensite.
7
C'est un constituant qui présente les mêmes
phases que la perlite mais possède une structure particulière
fine, souvent en aiguilles, ce qui lui confère de bonnes
propriétés mécaniques. Elle est dure et assez facile
à usiner.
I.4 Différentes familles des aciers
a) Aciers non alliés
? Aciers non alliés à usage
général
Ils sont destinés à la construction soudée,
à l'usinage, au pliage etc. On distingue :
- le type S qui correspond à un usage
général de base (construction de bâtiment...) ;
- le type P pour usage des appareils à pression ;
- le type L pour les tubes de conduites ;
- le type E pour la construction mécanique ;
- le type R pour les rails.
La désignation de ces aciers comprend la lettre
indiquant le type d'acier, suivie de la valeur de la limite élastique
(Re) exprimée en méga pascals (MPa).
S'il s'agit d'un acier moulé, la désignation est
précédée de la lettre G. La désignation peut
être complétée par des indications supplémentaires
(pureté, application dédiée, etc.). ? aciers non
alliés spéciaux (du type c)
La teneur en manganèse est inférieure à
1 %, et aucun élément d'addition ne dépasse 5 % en masse.
Leur composition est plus précise et plus pure et correspond à
des usages définis à l'avance.
Leurs applications courantes sont les foreuses (perceuses),
ressorts, arbres de transmission, matrices (moules), etc.
Leur désignation comprend la lettre C suivie de la
teneur en carbone multipliée par 100. S'il s'agit d'un acier
moulé, on précède la désignation de la lettre G.
b) Aciers faiblement alliés
La teneur en manganèse est supérieure à 1
% et aucun élément d'addition ne doit dépasser 5 % en
masse. Ils sont utilisés pour des applications nécessitant une
haute résistance.
Il existe aussi les aciers à résistance
améliorée à la corrosion sont des aciers faiblement
alliés appelés également aciers patinables ou aciers auto
protecteurs, car dans certaines
8
conditions d'exposition, ils ont la faculté de se
couvrir d'une couche protectrice appelée « patine ».
c) Aciers fortement alliés
Au moins un élément d'addition dépasse
les 5 % en masse, destinés à des usages bien spécifiques,
on y trouve des aciers à outils, réfractaires, maraging
(très haute résistance, utilisés dans
l'aéronautique et pour la fabrication de coque de sous-marins),
Hadfields (très grande résistance à l'usure),
Invar (faible coefficient de dilatation).
? Les aciers inoxydables
Les aciers inoxydables sont classés en quatre familles:
ferritique, austénitique, martensitique et austéno-ferritique.
Ils sont une des grandes familles des aciers qui présentent une grande
résistance à la corrosion, à l'oxydation à chaud et
au fluage (déformation irréversible). C'est un acier fortement
allié, ses applications sont multiples : chimie, nucléaire, mais
aussi couteux et équipements ménagers. Ces aciers au moins 12% de
chrome (Myriam Olivier, 2006).
? Les aciers multiphasés
Ces aciers sont conçus suivant les principes des
composites : par des traitements thermiques et mécaniques, on parvient
à enrichir localement la matière de certains
éléments d'alliage. On obtient alors un mélange de phases
dures et de phases ductiles, dont la combinaison permet l'obtention de
meilleures caractéristiques mécaniques. On citera, par exemple
:
- les aciers Dual Phase qui sont la
déclinaison moderne de l'acier damassé, mais où la
distinction entre phase dure (la martensite) et phase ductile (la ferrite), se
fait plus finement, au niveau du grain ;
- les aciers duplex formés de ferrite et
d'austénite dans des proportions sensiblement identiques ; les aciers
TRIP (Transformation Induced Plasticity), où l'austénite
se transforme partiellement en martensite après une sollicitation
mécanique. On débute donc avec un acier ductile, pour aboutir
à un acier de type Dual Phase ;
- les aciers damassés où des couches blanches
ductiles pauvres en carbone absorbent les chocs, et les noires, plus riches en
carbone, garantissent un bon tranchant.
9
I.5 Propriétés et
caractéristiques
L'acier est un alliage essentiellement composé de fer,
sa densité varie donc autour de celle du fer (7,32 à 7,86),
suivant sa composition chimique et ses traitements thermiques. Les aciers ont
un module de Young d'environ 200 GPa (200 milliards de pascals),
indépendamment de leur composition. Les autres propriétés
varient énormément en fonction de leur composition, du traitement
thermomécanique et des traitements de surface auxquels ils ont
été soumis.
Le coefficient de dilatation thermique de l'acier vaut
11,7×10 °C-1.
Les aciers ont quasiment tous le même module de YOUNG : E ?
200 GPa.
L'austénite a un module de YOUNG plus faible que la
ferrite :
E ferrite = 207 GPa ; E austénite = 193 GPa.
La ferrite a une masse volumique ñ de 7 874 kg/m3, celle
de l'austénite vaut 8679 kg/m3. On utilise en général des
aciers hypoeutectoïdes (moins de 0 ,77 % de carbone). De manière
globale (ARFAOUI Ali, CHAKER Med Amir) :
- les aciers austénitiques sont très ductiles
mais ont une limite élastique très basse, en effet, leur
structure cubique à face centrée permet de nombreux glissements
faciles entre les plans cristallins ; ils sont facilement formables à
température ambiante ;
- les aciers martensitiques ou bainitiques (aciers
trempés) ont une haute limite élastique mais une faible
ductilité (voir ci-dessus) ;
- les aciers ferritiques sont entre les deux.
Voici à titre indicatif des valeurs typiques.
Acier
|
Limite élastique Re (MPa)
|
Allongement à la rupture
A %
|
Acier extra-doux (ferritique très bas carbone)
|
150
|
35
|
Acier austénitique (hypertrempe)
|
200
|
25 - 50
|
Acier ferritique
|
200 - 400
|
20 - 25
|
Acier martensitique (trempe)
|
400 - 1000
|
10 - 20
|
Tableau I.1 : valeurs typique des
caractéristiques mécaniques
10
La ferrite et la martensite sont ferromagnétiques ;
l'austénite est paramagnétique. Un aimant adhère donc
moins bien à l'austénite qu'à la ferrite ou à la
martensite ; on utilise souvent le « test de l'aimant » pour
reconnaître un acier austénitique. L'austénite est souvent
qualifiée à tort « d'amagnétique » (ce terme n'a
pas de sens physique). Au-delà de 770 °C (point de CURIE), la
ferrite devient paramagnétique, elle perd son aimantation.
On augmente les propriétés magnétiques
(perméabilité magnétique) des aciers ferritiques par
addition de silicium à moins de 4 % : de trop fortes teneurs fragilisent
l'acier. On utilise naturellement des aciers bas carbone (<0 ,01 %),
celui-ci étant gammagène.
En conclusion les propriétés de l'acier
dépendent, en général, des éléments
d'addition ou défauts inclus dans l'acier.
11
CHAPITRE II
INFLUEN E DES ELEMENTS D' DDITION SUR LES
PROPRIETES ME NIQUES DE L' IER
On peut modifier les caractéristiques mécaniques
et aptitudes technologiques des aciers par addition d'autres métaux en
dehors de la variation du pourcentage de carbone. L'association de plusieurs
éléments d'addition entre eux permet de pondérer les
effets de chacun. Les métaux principaux, avec leurs principales
influences, sont :
II.1. L'aluminium
La solubilité de l'aluminium dans le fer est de 35%
à 1232°C et de 32% à la
température ambiante. Les additions d'aluminium
réduisent la région gamma du diagramme d'équilibre,
accroissant la phase alpha et formant finalement une région alpha et
gamma continue. La plupart des aciers moulés sont
désoxydés à l'aide de petites additions (0.5 à 1 kg
par tonne), qui changent l'oxyde de fer en en alumine insoluble,
dispersée sous la forme de particules ultra-microscopiques, infusibles
et dures, qui sont généralement moins gênantes au cours de
la fabrication que les inclusions existant dans les aciers calmés au
silicium. En empêchant la formation de gaz, des additions de ce genre
évitent la formation de piqûres et de ségrégation A
condition d'éviter la surchauffe, une forte désoxydant par
l'aluminium représente un moyen d'élever la température
à partir de laquelle le grain du métal grossit rapidement, et
l'on peut par la suite agir sur la finesse du grain. Les très petites
inclusions d'alumine agissent probablement en gênant mécaniquement
le grossissement des grains sur les bords de ceux-ci. Les aciers
désoxydés de cette façon ont une résilience
accrue.
II.2. Le carbone
Les propriétés de l'acier dépendent, de
façon fondamentale, de la teneur en
carbone. Le fer liquide dissout très facilement le
carbone dans des proportions très supérieures aux 2.08% qui
marquent la délimitation entre les aciers et les fontes. En
quantités allant jusqu'à cette limite de classification, le
carbone se dissout dans le fer Ó pour donner de l'austénite, mais
la solubilité dans le fer Ó est très faible (de 0.01
à 0.04%). Les additions de carbone introduisent le point A2 (695°C
formation de perlite) élèvent le point A4 (1400°C) et
peuvent abaisser le point A3 (910°C) jusqu'à 695°C.
12
De tous les constituants de l'acier, le carbone exerce de loin
l'influence la plus grande sur les propriétés du métal.
Dans les aciers au carbone, il se trouve presque exclusivement sous la forme de
carbure Fe3C dur et fragile, mais également sous la
forme de "carbone de trempe" dissous, et quelquefois sous la forme de graphite
(Métallurgie générale/les aciers I théorie).
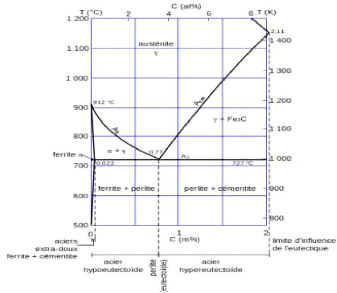
Figure II.1 : Diagramme
fer-carbone
II.3. Le chrome
Des additions de chrome améliorent les
propriétés mécaniques et la résistance à
la
corrosion, et cet élément est très
employé, en teneur variant de 0.25 à 30%, suivant l'application
précise que l'on veut faire. Il se combine de préférence
avec le carbone, et le carbure qui en résulte,
(généralement le carbure orthorhombique Cr3
C2 lorsque la teneur est modérée, ou le carbure
cubique Cr4C quand la teneur est forte) se dissout dans le
Fe3C restant pour former un carbure double, dur et stable.
Par suite, le chrome diminue la décarburation et corrige la tendance
graphitisante dans les aciers à forte teneur en carbone. Les
quantités en excès par rapport à celle nécessaire
à la formation des carbures se dissolvent librement et facilement dans
le fer liquide, et restent en solution dans le fer y, et, dans une
plus grande mesure encore dans le fer a. Le chrome en solution tend
à
13
retarder la transformation de l'austénite, ce qui
produit de la trempe à l'air, tendance qui est favorisée par des
températures initiales élevées ou par des vitesses de
refroidissement dépassant la vitesse d'équilibre, ces deux
conditions abaissant les points A3 et A1. Une teneur aussi faible que 0.5%
suffit pour donner une structure aciculaire dans de l'acier au carbone à
0.35% refroidi à l'air (ARFAOUI Ali, CHAKER Med Amir).
Le plus souvent, on emploie en même temps que d'autres
éléments d'addition, spécialement le nickel, le
molybdène, le vanadium et le titane, qui améliorent en plus la
ductilité et la ténacité, réduisant en outre la
fragilité due au grossissement du grain. Des additions
simultanées de chrome (0.5 à 1.5%) et de nickel (1.5 à
4.5%) donnent une association excellente de résistance à l'usure
et d'aptitude à la trempe, avec une résistance à la
rupture élevée, de la ductilité, de la
ténacité, le métal obtenu convenant bien aux fortes
épaisseurs, et n'étant que relativement peu sujet au
grossissement du grain.
II.4. Le cobalt
Le cobalt élargit la région á, en
relevant la température du solidus et abaissant le point de
transformation a - y. Ajouté à l'acier, il n'a pas
d'effet durcissant appréciable sur l'austénite. En ce qui
concerne les propriétés mécaniques à froid, il
élève graduellement la charge de rupture à la traction et
la limite élastique, avec réduction correspondante de
l'allongement et de la striction. La résistance à la corrosion
est améliorée. Le cobalt est le seul élément qui
n'agisse pas directement pour augmenter la dureté produite par la trempe
et il faut recourir à un refroidissement plus rapide. Cet
élément fait que l'acier résiste à l'action du
revenu après trempe.
Le cobalt existe dans les aciers surtout sous forme de
carbure Co3 C. L'instabilité de celui-ci tend
à produire de la décarburation pendant le travail à chaud.
Étant donné que le chrome exerce un effet stabilisant par suite
de la formation de carbures complexes, contrecarre la fragilité et
diminue partiellement les difficultés de forgeage. Il en résulte
qu'on l'ajoute souvent aux aciers au cobalt, surtout dans ceux qui sont
à haute teneur en carbone. Toute la proportion du cobalt qui n'est pas
combinée avec le carbone, forme un composé intermétallique
Fe2 Co, qui donne avec le fer une série de solutions
solides.
II.5. Le manganèse
Le manganèse a une influence si favorable qu'il est un
constituant essentiel de n'importe quel acier industriel. Le seul
élément qui ait une importance plus grande est le
14
carbone. Le manganèse forme avec le fer gamma ( ), le
fer á et la cémentite, une série continue de solutions
solides. Les points Ar3 (correspondant à la transformation ->
á) et Ar1 (changement eutectoïde) sont notablement abaissés
par la présence du manganèse. Avec une teneur en manganèse
de 2%, les points critiques se confondent, même quand la teneur en
carbone est modérée. Des additions de manganèse
améliorent la fluidité, mais augmentent le retrait. La
conductibilité électrique est réduite.
Le manganèse est présent dans les aciers, en
partie sous forme d'impuretés résiduelles, en partie comme
résultat d'une désoxydation. Une partie du manganèse
constitue un élément d'addition intentionnelle pour
contrebalancer la mauvaise influence du sulfure de fer, en produisant du
sulfure de manganèse relativement moins nocif. Le manganèse
améliore les propriétés mécaniques et les
possibilités de travail à chaud. En tant que désoxydant,
le manganèse a une très grande efficacité et il est
employé pour obtenir de l'acier sain, sans défaut interne, tels
que les soufflures. Si la teneur en manganèse est inférieure
à 0.2% l'acier sera vraisemblablement ruché (soufflures
superficielles en nid d'abeilles) et donc non sain. Son action sur le sulfure
de fer est utilisée dans tous les aciers. Elle est
particulièrement importante dans les aciers de décolletage
à haute teneur en soufre. Des quantités de manganèse,
supérieures à 0.30%, augmentent la résistance à la
traction et à moindre degré, diminuent l'allongement et la
striction. L'amélioration de ténacité due au
manganèse varie directement avec la teneur en carbone. Une teneur en
manganèse de 1% augmente la résistance d'un acier à 0.10%
de carbone d'environ de 25%, alors que, dans le cas d'un acier à 0.50%
de carbone, l'augmentation de résistance est d'environ 50%. Avec 2% de
manganèse, l'effet de trempe à l'air devient si prononcé
que la résistance au choc n'est plus que le cinquième de ce
qu'elle était avec 1.40% de manganèse. Une teneur très
favorable en manganèse, pour avoir un acier à haute
résistance et ductile, est de 1.2% à 1.6% avec 0.25 à
0.30% de carbone (BOUTARFIF Fatma et GUELAI Noussaida).
II.6. Le molybdène
Les aciers au molybdène ont pris une importance
croissante pour la fabrication d'organes de machines. Le molybdène
améliore les propriétés de résistance aux chocs des
aciers trempés. Les recherches étendues et les résultats
constatés font que le molybdène est maintenant le plus largement
employé dans les aciers à haute résistance, en vue de leur
maintenir une bonne résistance aux chocs et une bonne résistance
aux températures élevées. Le succès des additions
de molybdène est dû à plusieurs causes. L'une d'entre
15
elles est d'éliminer pratiquement toutes tendances
à la fragilité de revenu, après trempe, dans les aciers au
chrome-nickel et dans d'autres aciers spéciaux. Le molybdène est
donc un élément d'addition qu'on emploie habituellement en
même temps que d'autres. Sauf dans les aciers pour outils, où la
teneur en molybdène peut atteindre 10%, en remplaçant du
tungstène, les additions de molybdène ont rarement besoin de
dépasser 1% pour produire leur maximum d'effet utile et souvent, elles
sont beaucoup plus faibles. Ainsi, de nombreuses variétés
d'aciers spéciaux contiennent seulement de 0.15 à 0.40% de
molybdène.
Cet élément se dissout facilement dans l'acier
fondu et, dans de certaines limites, il est retenu sous forme de solution
solide dans le fer á et la ferrite y. Sa solubilité à
1440° C'est de 24%. A la température ordinaire, elle est de 4%. A
400°C, elle est de 6%. Le molybdène est susceptible de former le
composé Fe3Mo2. L'acier chauffé pour être amené
à l'état de solution solide est soumis à une trempe,
présente un précipité de Fe3Mo2 très finement
dispersé (Philipe Berger).
Cependant le molybdène est un puissant formateur de
carbure et il existe en forte proportion dans l'acier, sous forme de carbures
complexes de molybdène et de fer, plus stable de beaucoup que le simple
carbure du fer. Ces carbures lentement solubles, donnent à la
présence au molybdène beaucoup de son effet trempant, qui vient
tout de suite après celui du carbone. Une caractéristique des
additions de molybdène (0.5 à 1%) est de permettre un traitement
thermique efficace des aciers au nickel-chrome, des aciers à hautes
teneur en manganèse..., en supprimant largement leur
susceptibilité à la fragilité de revenu. Celle-ci consiste
en une précipitation durcissant entraînant une diminution
considérable de la résistance aux chocs. Cela ne résulte
pas d'un adoucissement de l'acier. Mais en fait le molybdène est
favorable à un durcissement par revenu. Il se crée alors des
petites particules de Fe3Mo2. Par suite de la solubilité lente des
carbures, il faut des températures de revenu élevées pour
produire l'adoucissement.
Le molybdène agit d'une façon semblable à
celle du chrome, pour augmenter la résistance, l'aptitude à la
trempe et la résistance à l'usure, tout en gardant une bonne
ténacité. Il a donc divers effets favorables, analogues à
ceux du nickel. Les aciers au nickel-molybdène ont une limite
élastique élevée, mais ils ont une faible
résistance aux chocs, et une médiocre usinabilité. Ils
sont employés comme aciers de cémentation.
16
II.7. Le Nickel
Le nickel est le premier de tous les éléments
alliés employé à l'échelle industrielle. Il
confère aux aciers un ensemble de propriétés remarquables,
de sorte qu'il se trouve un emploi étendu pour toutes sortes
d'applications, notamment aux teneurs jusqu'à 5% dans les aciers devant
subir un traitement thermique ou une cémentation et pour des
pièces forgées au pilon. Le plein effet du nickel se produit
seulement quand on l'emploie en même temps que d'autres
éléments alliés.
Cet élément a une structure atomique du type
cubique à faces centrées, comme celle du fer gamma, avec lequel
il peut s'allier complètement en formant une série continue de
solutions solides. Il est aussi complètement soluble dans la ferrite et
sauf pour une petite proportion où il existe comme carbure de nickel
instable, associé avec le carbure de fer, il existe dans les aciers pour
pièces de construction, sous forme de solution solide dans la ferrite.
Le nickel a un comportement semblable au manganèse. Son
intérêt fondamental est qu'il abaisse notablement la
température des points critiques. Les points critiques Ac3 et Ac1 sont,
tous les deux, abaissés d'environ 10°C pour chaque 1% de nickel
ajouté.
Le nickel a une vitesse de diffusion assez faible. Il est
très utile pour retarder le grossissement du grain par chauffage
à hautes températures. Il contrebalance les effets pernicieux
d'un surchauffage. La perlite devient plus fines, sa teneur en carbone est
diminuée et ramenée, par exemple, à 0.75%, quand la teneur
en nickel est de 3% et à 0.45%, quand la teneur en nickel est de 10%.
Le carbure de nickel est très instable. L'effet
graphitisant du nickel est intermédiaire entre celui du cuivre et celui
du silicium. Cet effet est habituellement contrecarré en élevant
le manganèse jusqu'à une teneur de 0.6 à 0.9% (BOUTARFIF
Fatma et GUELAI Noussaida).
Le nickel n'a qu'un effet modéré sur la
trempabilité des aciers. En abaissant la température des points
critiques et la vitesse critique du refroidissement, il permet une plus grande
latitude dans les conditions du traitement thermique. On peut abaisser la
température de trempe, en réduisant ainsi les possibilités
de décarburation superficielle et de déformation. On peut avoir
une trempe moins brutale que celle exigée par des cahiers au carbone
seul. En faisant un revenu après trempe vers des températures de
550° à 650°C. Les aciers au nickel présentent les
meilleurs ensembles de caractéristiques mécaniques.
17
Avec de faibles teneurs en carbone, la présence de 2%
de nickel donne un acier très ductile, résistant aux chocs et
à la fatigue aux basses températures et avec des teneurs moyennes
en carbone, il améliore les propriétés
élastiques.
Comme le nickel élargit le domaine gamma, des teneurs
intermédiaires en nickel produisent la structure martensitique,
même avec un refroidissement lent, mais des teneurs encore plus
élevées donneraient à l'acier une structure
austénitique permanente.
II.8. Le silicium :
De même que le carbone, l'élément silicium
est toujours présent dans les aciers industriels. Il forme facilement
des solutions solides avec le fer, aux états delta, gamma ou alpha et
aussi avec la cémentite, en diminuant la solubilité de celle-ci.
Alors qu'il est surtout présent à l'état de solution
solide dans la ferrite, il y en a une petite proportion sous forme
combinée, c'est la silice SiO2, formant dans le métal des
inclusions non métalliques.
Les aciers à hautes teneur en carbone et en silicium
peuvent contenir du carbure de silicium (SiC). Celui-ci, en solution solide,
contribue à produire un grain grossier dans les aciers, alors que sous
la forme d'inclusions dispersées, il a un certain effet pour gêner
le grossissement du grain. Le silicium à l'état allié au
fer, élargit le domaine de la phase alpha du diagramme
d'équilibre, et quand il est présent en quantité
suffisante, les alliages restent constamment ferritiques. En élevant
ainsi le point de transformation, il demande des températures de trempe
plus élevées. Une tendance très dommageable, surtout
lorsque sa teneur 0.50%, est celle qui contribue à décomposer la
cémentite en fer et graphite. On contrecarre cet effet par un apport de
manganèse.
Le silicium améliore la résistance de l'acier
aux températures élevées. Les pellicules d'oxyde
superficiel formées les premières sont adhérentes et
inertes et elles empêchent rapidement une oxydation ultérieure.
Certains des aciers à haute teneur en chrome résistant à
la chaleur contiennent de 1 à 3% de silicium (Philipe Berger).
Néanmoins tous ces éléments jouent un
rôle alphagènes ou gammagènes ou encore
carburigène.
18
CHAPITRE III
TRAITEMENT THERMIQUE APPLIQUE AUX ACIERS
III.1. Définition
Traitement thermique est une succession d'opérations au
cours desquelles
un produit ferreux solide est soumis en totalité ou
partiellement à des cycles thermiques pour obtenir un changement de ses
propriétés et/ou de sa structure.
III.2. But
On recherche un compromis entre les caractéristiques
suivantes :
- ductilité (capacité de déformation)
- résilience, ou ténacité (résistance
au choc)
- résistance (limite d'élasticité,
résistance à la traction)
- dureté
Certaines structures sont favorables à la dureté,
certaines caractéristiques (taille de grains)
en conjonction avec d'autres paramètres agissent sur la
ductilité.
Cette approche simplifiée ne reflète pas, bien
entendu, toute la complexité de la
métallurgie et de sa mise en oeuvre au travers des
traitements que nous décrivons.
III.3. Eléments d'un traitement
thermique
Les éléments d'un traitement thermique sont :
? Un traitement thermique consiste à jouer sur trois
éléments :
- la température
- le temps
- et le milieu de séjour durant le maintien en
température (neutre ou réactif)
? lors de trois phases différentes :
- la montée en température
- le maintien à température
- et le refroidissement.
En général, la phase déterminante et
critique est le refroidissement. La vitesse appropriée
pour obtenir les caractéristiques voulues amène
à choisir un milieu de refroidissement (par
exemple air, eau, bain de sel, huile, gaz ou mélanges
gazeux sous pression) en fonction de
la dimension de la pièce à traiter et la
trempabilité.
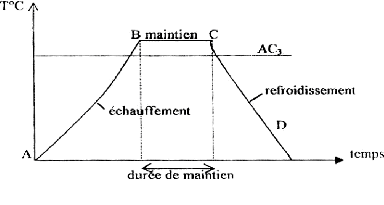
19
Figure III.1 : Cycle d'un traitement
thermique
Un acier peut présenter plusieurs types de structures
cristallines liées :
- aux phases
- aux types de précipités
- à l'organisation entre ces deux
éléments.
L'ensemble des traitements thermiques pour emploi final et
intermédiaires jouent sur ces aspects avec notamment les transformations
de phases au chauffage et au refroidissement, les mises en solution ou
apparition des précipités et la diffusion des
éléments divers au chauffage. La taille des grains et leur
grossissement interviennent. Cela agit sur le résultat final de la
structure et par ailleurs dépend également des conditions des
traitements thermiques et éventuellement des éléments
d'addition.
III.4. Types de traitements thermiques
1. Le recuit
Le recuit consiste à :
- chauffer la pièce à une température
déterminée dite température de recuit (le choix de la
température dépend des objectifs, elle peut aller de 450 et
1100°C)
- maintenir cette pièce à cette température
pendant un temps donné
- refroidir à la vitesse adéquate afin d'obtenir
après retour à la température ambiante un état
structural du métal proche de l'état d'équilibre
stable.
20
Cette définition très générale est
habituellement complétée par une formulation précisant le
but du traitement.
Le recuit permet notamment :
- d'éliminer ou réduire les contraintes
résiduelles du métal liées à une action
antérieure (déformation, soudure, etc.) ou un traitement
thermique antérieur
- ou d'obtenir la formation d'une structure favorable à
une action ultérieure (déformation, usinage, etc.) ou un
traitement thermique ultérieur.
|
A : Recuit de normalisation et recristallisation.
B : Recuits
d'adoucissement.
C : Recuits de détente.
D : Recuits
d'homogénéisation
ou de diffusion
|
Figure III.2 : Zones des températures les
plus favorables pour les différents recuits
|
|
2. La trempe
La trempe (ou durcissement par trempe) consiste à :
- chauffer la pièce à une température
appropriée (austénitisation ou mise en solution) - refroidir
à une vitesse adéquate la pièce en la plongeant par
exemple dans de l'eau (trempe à l'eau) ou de l'huile (trempe à
l'huile) ou par insufflation d'un gaz tel que l'air. Une trempe a pour objet de
durcir le métal. Elle permet d'obtenir des aciers très durs mais
dans la plupart des cas peu ductiles. Elle est donc généralement
suivie d'un revenu.
Les éléments ajoutés au Fer modifient
profondément la cinétique de la transformation á - y. Pour
mettre en évidence cette cinétique, on se sert des diagrammes TTT
(diagramme
21
de transformation de l'austénite en conditions
isothermes, Température - Temps - taux de Transformation, fig. 3)
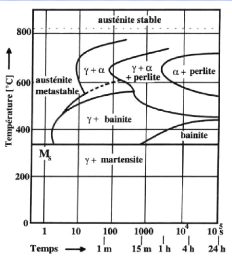
Figure III.3 : Courbe TTT (acier faiblement
allié 0,35%) : ce diagramme se lit en suivant un isotherme 3. Le
revenu
Le revenu consiste :
- en un ou plusieurs chauffages de la pièce à
une température déterminée (inférieure à la
température de début de transformation de phase de l'acier ~
700°C)
- un maintien de la pièce à cette
température pendant un temps donné
- un refroidissement approprié.
Un revenu permet d'atténuer les effets de la trempe en
rendant la pièce plus ductile et plus tenace. Il peut dans des cas
particuliers, cas des aciers faiblement alliés, permettre un
durcissement secondaire. L'emploi du terme revenu sous-entend que le traitement
est réalisé sur un état préalablement
trempé. [Un traitement à 500°C sur un acier trempé
est un revenu, sur un acier non traité est un recuit].
En fonction du résultat attendu, on distingue plusieurs
types de revenu :
- Revenu de relaxation ou de détente :
s'effectue entre 180°C et 220°C -250°C Il ne provoque aucune
modification de structure mais une relaxation des contraintes multiples dues au
refroidissement brusque de la trempe et au changement de structure
austénite martensite.
22
- Revenu de structure ou classique :
s'effectue entre 500°C et Ac1 On observe une augmentation des
caractéristiques K, A et Z et une diminution plus importante de H, Rm et
Re.
Revenu de durcissement : s'effectue entre 450 et 600°C
4. La normalisation
Le traitement de normalisation (équivalent d'un recuit
à haute température suivi d'un refroidissement à l'air)
est un traitement d'affinage structural permettant un adoucissement et
l'élimination des contraintes apparues avec les opérations
précédentes. Outre l'obtention de structures homogènes
recherchées dans certaines applications mécaniques il conduit
à un état reproductible idéal pour la trempe.
L'état dit "normalisé" est un état de livraison des
produits sidérurgiques.
III.5. Transformation des phases au cours du traitement
thermique
a) Mécanisme de la transformation lors de
l'austénitisation
Lors du traitement thermique d'austénitisation, les
structures martensitiques, bainitiques et ferrito-perlitiques se transforment
en phase austénitique. La croissance de l'austénite est
contrôlée par diffusion. Comme le traitement
d'austénitisation se fait à haute température, cette
diffusion est rapide, un traitement de 30 min permettant a priori une
redissolution complète de la perlite, pour des températures
suffisamment élevées. Pour les structures perlitiques, le
mécanisme de germination de l'austénite dépend de la
morphologie de la perlite initialement présente.
Dans le cas d'une perlite globulaire, la formation de
l'austénite se fait par étapes successives au cours de la
montée en température.
La diffusion du carbone se faisant
préférentiellement aux joints de grains, c'est sur ces derniers
que la germination de la phase austénitique se produit. Le carbone
nécessaire à cette étape provient de la dissolution des
carbures. La première apparition d'austénite peut aussi
être localisée à l'interface entre les colonies de perlite.
La croissance de l'austénite se poursuit ensuite sous formes de lattes.
Du fait que l'on se trouve à haute température, il y a ensuite
coalescence de ces lattes à l'arrière du front de croissance,
jusqu'à ce que celle-ci soit bloquée par des globules de perlite
encore présents. La phase austénitique croît alors de
façon isotrope à partir du joint de grains ou elle s'est
formée, parallèlement à la dissolution des carbures.
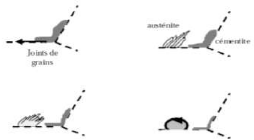
23
Figure III.4 : Premiers stades de la formation de
la phase austénitique
Si la structure perlitique initiale est lamellaire,
le mécanisme de formation de la phase austénitique est
différent de celui décrit précédemment.
L'austénite va germer sur les interfaces ferrite/cémentite de la
perlite. Une rapide croissance fait suite à une germination
instantanée de l'austénite. Au fur et à mesure que
l'austénite croît, la proportion de ferrite diminue et les
lamelles de cémentite deviennent de moins en moins épaisses
jusqu'à se dissoudre complètement (Hantcherli Muriel 2010).
b) Constituant intermédiaire
Si la trempe est plus lente, ou bien si on l'arrête
à une température intermédiaire (trempe
étagée), on peut former de la bainite : il se forme des lamelles
de ferrite (ferrite aciculaire), et de la cémentite vient se former soit
entre ces lamelles, on parle de bainite supérieure, ou bien à
l'intérieur des aiguilles, bainite inférieure. La bainite est un
peu moins dure que la martensite, mais plus ductile ; la bainite
inférieure a une meilleure résilience (métallurgie
générale/ les aciers I théorie).
c) La transformation martensitique
Au cours d'une trempe, en revanche, le carbone ne peut plus
diffuser. La phase martensitique possède donc la même teneur en
carbone que la phase austénitique dont elle est issue et on parle ici de
transformations displacives. Ce terme vient du fait que la croissance
rapide de la martensite se fait via un mouvement coordonné des atomes.
Il est cependant important de souligner que durant la transformation, ce
mouvement coordonné d'atomes est tel que le déplacement d'un
atome par rapport à ses voisins reste inférieur à la
distance inter-atomique (Hantcherli Muriel 2010).
Lors du refroidissement à partir de la phase
austénitique, il y a apparition de la phase martensitique. Elle se fait
instantanément, du moment qu'une certaine température Ms,
appelée température de début de transformation
martensitique est atteinte. Elle fait
24
apparaitre deux types de martensite : la martensite en latte
et la martensite en plaquette dépendant de la teneur en carbone.
Le paramètre c de la maille augmente avec la teneur en
carbone, tandis que le paramètre a décroît. Ainsi, plus la
maille est riche en carbone, plus elle est tétragonale. Ceci s'explique
par le fait que les atomes de carbone sont situés au centre des
arêtes, dans les sites octaédriques. La Figure I.5 résume
la position des atomes de carbones dans la maille.
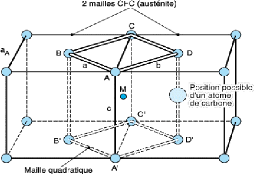
Figure III.5 : Position des atomes de carbone dans
la maille quadratique de la martensite
III.6. Influence des éléments d'alliage sur
le traitement thermique
a) Influence sur l'austénitisation
Les éléments d'alliage ont un rôle
prépondérant dans le traitement d'austénitisation. La
germination de l'austénite est instantanée dans le cas des aciers
au carbone mais la présence de certains éléments d'alliage
peut ralentir la croissance gouvernée essentiellement par la diffusion,
du fait de leur faible diffusivité, modifiant la position des points
caractéristiques de début et de fin de la transformation Ac1 et
Ac3. Les formules empiriques d'Andrews peuvent être utilisées pour
estimer les températures de transformation en fonction de la composition
chimique des aciers faiblement alliés. Elles sont valables pour des
aciers contenant moins de 0,6% de carbone. Ces formules sont données
ci-après en fonction de la teneur massique en éléments
d'alliages.
Ac1=723-10,7Mn-16,9Ni+29,1Si+16,9Cr+6,38W+290As
Ac3=912-203
C-15,2Ni+44,7Si+104V+31,5Mo+13,1W-30Mn
25
La Figure III.6 présente les changements
occasionnés par la présence des éléments d'alliages
alphagènes ou gammagènes sur le diagramme d'équilibre des
phases de l'alliage Fe-C (Hantcherli Muriel 2010).
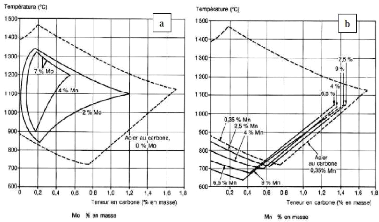
Figure III.6 : Influence des éléments
d'alliage sur le diagramme de phase FeC a) Présence d'un
élément alphagène, le molybdène- b)
Présence d'un élément gammagène, le
manganèse
Les éléments alphagènes les plus souvent
utilisés dans les aciers alliés sont le Si, Al, Cr, Mo, Ti, V, W.
Le nickel et le manganèse sont quant à eux des
éléments gammagènes. Ces considérations expliquent
l'effet de ces éléments sur l'abaissement ou l'augmentation des
températures Ac1 et Ac3 dans les formules d'Andrews et d'Eldis
précédemment citées.
Un autre aspect est à prendre en compte pour comprendre
l'effet de ces éléments. En effet, certains
éléments, dits carburigènes, ont une affinité plus
grande pour le carbone que celle du fer. Même présents en faible
quantité, ils peuvent se substituer partiellement aux atomes de fer de
la cémentite, formant ainsi des carbures notés de manière
générale M3C. Lorsque la teneur en ces éléments est
suffisante, la formation de différents carbures autres que la
cémentite, peut être observée. Notons ici quelques exemples
pour l'ajout de chrome ou de vanadium : (Cr,
Fe)23C6, (Cr, Fe)3C, (Cr,
Fe)7C3 ou (V, Fe)3C et (V,
Fe)4C3. Parmi les éléments
carburigènes on trouve Cr, V, Mo, Ti, W, Nb et Mn. Des
éléments comme le silicium où le nickel, n'étant
pas carburigènes, se retrouvent en solution solide dans la ferrite
(Hantcherli Miriel).
b) Influence sur la martensite
Les éléments d'alliages jouent un rôle
important dans la formation de la martensite, et ce, à trois niveaux.
Ils influent en effet sur la vitesse critique de trempe
26
nécessaire pour former cette phase, sur la
température de début de la transformation martensitique Ms, mais
également sur la morphologie de la martensite obtenue.
b.1) Influence sur la vitesse critique de
trempe
Les éléments d'additions altèrent la
cinétique des transformations de phases en modifiant la stabilité
de l'austénite pour des températures inférieures à
son domaine d'existence. De manière générale, ces derniers
stabilisent l'austénite instable et les courbes TRC sont ainsi
décalées vers la droite : les vitesses de transformations sont
diminuées. Dans certains cas, les éléments d'alliage
peuvent également modifier la forme des courbes de transformation. Cela
a une conséquence pratique sur la vitesse critique de trempe qui sera
moins élevée, les transformations bainitique et
ferrito-perlitique se produisant pour des vitesses plus faibles que dans le cas
d'un acier non allié. La trempabilité des aciers s'en trouve donc
améliorée (ARFAOUI Ali, CHAKER Med Amir).
b.2) Influence sur la température
MS
Différentes formules pour estimer la température
Ms (en °C), en fonction de la
teneur massique en éléments d'alliage sont
disponibles dans la littérature.
Les principales approximations sont les suivantes :
- Nehrenberg
Ms=500-300C-33Mn-17Ni-22Cr-11Mo-11Si
- Steven et Haynes
Ms=561-474C-33Mn-17Ni-17Cr-21Mo
- Andrews
Ms=539-423C-30,4Mn-17,7Ni-12,1Cr-7,5Mo
La relation d'Andrews est généralement
utilisée pour des aciers dont la teneur en carbone
ne dépasse pas les 0,6 % massique. Pour
l'établissement de ces formules, il est
communément admis que l'influence de chaque
élément est indépendante de la présence
ou de la teneur des autres éléments d'alliage.
En pratique, les éléments d'alliage en solution
solide dans l'austénite abaissent la
température Ms. Il est cependant important de souligner
que c'est la teneur en carbone qui
influe le plus sur le déplacement de cette
température. Pour cette même raison, la
dissolution totale des carbures dans la phase austénitique
joue un rôle prépondérant sur
27
Ms. En effet, il est aisé de constater via ces
formules, qu'une variation de 0,1% de carbone en solution solide peut conduire
à une variation de presque 40°C sur la température Ms. Pour
déterminer les phases que l'on obtient à température
ambiante, on détermine l'influence des éléments
alphagènes en calculant la teneur en « chrome équivalent
», on détermine l'influence des éléments
gammagènes en calculant la teneur en « nickel équivalent
»
alphagènes : (Cr)eq = (%Cr) + 1,5(Si%) +
(%Mo) + 0,5(%Nb)
gammagènes : (Ni)eq = (%Ni) + 0,5(%Mn) +
30(%C)
Et l'on reporte le point sur un diagramme, le plus couramment
utilisé dans le cadre de la soudure étant le diagramme de
SCHAEFFLER.
La zone dans laquelle se trouve le point indique les phases en
présence. Dans la zone biphasée austénite + ferrite (y +
á), on trace des droites indiquant la proportion des phases ; ces
droites sont appelées droites de conjugaison, ou conodes
(Métallurgie générale/ les aciers I théorie)
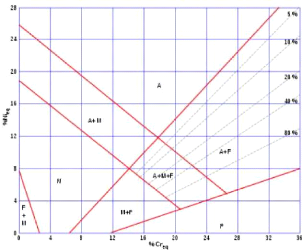
Figure III.7 : Diagramme de SCHAEFFLER ; A =
austénite, F = ferrite, M = martensite, les lignes de pourcentage
indiquent la proportion de ferrite dans l'austénite
Le diagramme de SCHAEFFLER est pertinent pour les
pièces brutes de solidification ; pour les pièces
laminées, on utilise un diagramme légèrement
différent, le diagramme de PRYCE et ANDREWS.
28
III.7. INFLUENCE DE LA GROSSEUR DES GRAINS D'AUSTENITE
SUR LES PROPRIETES MECANIQUES
D'une manière générale l'influence de la
grosseur du grain sur les propriétés mécaniques à
peu d'importance, sauf sur la résilience qui chute notablement surtout
dans le cas de dureté élevée et le seuil de
fragilité à froid qui s'élève. Plus le grain est
gros, plus l'acier est apte aux tapures et aux déformations de trempe.
La présence de la sorbite et de la troostite augmente de 10-15% la
résistance mécanique et la dureté de l'acier
normalisé.
Lorsque la température est portée au-dessus de
A1, il se forme à l'interface de la ferrite cémentite, des germes
de l'austénite qui croissent jusqu'au moment où toute la
structure se transforme en austénite.
En élevant la température ou en prolongeant la
durée de séjour à la température donnée, on
déclenche une cristallisation qui grossit le grain austénitique.
Cette croissance spontanée car le système à tendance
à diminuer l'énergie libre en réduisant la surface des
grains. Les gros grains se développent aux
dépend des petits grains thermodynamiquement stables. Les dimensions
des grains formés lors du chauffage jusqu'à une
température donnée ne changent naturellement pas au
refroidissement ultérieur. L'aptitude du grain austénitique
à la croissance varie suivant les conditions de fusion même pour
les aciers de composition identique. Et le grossissement des grains
d'austénite n'intervient qu'à des températures de plus en
plus élevées. La surchauffe durant la trempe produit une grande
quantité d'austénite résiduelle avec augmentation de la
quantité d'austénite effectivement, ce qui provoque une
diminution de la dureté de l'acier (Paul Kasongo 2018).
CHAPITRE IV
TRAVAUX ANTERIEURS SUR L' A3SS
Dans ce chapitre nous ferons un court aperçu sur les
travaux publiés par les ACP et quelques chercheurs sur l'A3SS.
IV.1. Amélioration de la nuance par les ACP
(Inédit)
Aux ACP l'amélioration de la nuance a été
faite par l'ajout du nickel. Le Lower
Mantle fabriqué en A3SS est une pièce devant
travailler sous sollicitations aux chocs, à l'usure et à la
fatigue. La présence associée du nickel, chrome, molybdène
et autres éléments apporte la résistance à la
corrosion et a une influence favorable sur la ténacité et la
tenue aux chocs en jouant sur la stabilité. Etant auto trempant, il
permet à l'état recuit une bonne usinabilité.
Nous vous présentons ci bas les attentes des ACP
concernant les propriétés mécaniques après
coulée et traitement thermique.
a) Composition
La composition est donnée dans la marge suivante :
Eléments
|
C
|
Mn
|
Ni
|
Cr
|
Mo
|
Si
|
P
|
S
|
Teneurs
|
0,280,5
~0 ,32
|
~0 ,6
|
3,25
~3 ,75
|
1
' 1 ,2
|
0,25
~0 ,45
|
max
0,28
|
max
0,03
|
< 0,03
|
|
Tableau IV.1 : Composition en fourchette de la
nuance A3SS
b) Caractéristiques mécaniques
Les propriétés mécaniques sont
données pour un revenu à 600°C
Propriétés
|
Résistance à la rupture
|
Limite élastique
|
Allongement
|
Résilience (kgm/cm2)
|
Dureté
|
Marge
|
90 -- 95
|
80 -- 85
|
>>-- 12
|
< 20
|
260 -- 280
|
29
Tableau IV.2 : Marge des propriétés
mécanique de l'A3SS attendues après revenu à
600°C
30
c) Conditions de traitement thermique
Près coulée la pièce est soumise à
un traitement thermique d'adoucissement (recuit d'adoucissement) pendant 6
à 10 heures à 680°C et pour la ramener aux conditions
d'utilisation, l'on fait une trempe à l'air à partir de
850°C. Le revenu suivant les caractéristiques
désirées se fait de 200 à 650°C (André Lebond,
1989).
Remarque : Eviter la maladie de Krupp autour
de 700 ou un séjour prolongé à la température
voisine de 500°C ; si possible arrêter le revenu à l'eau.
Le molybdène accroit la faculté de trempe,
à résistance égale la résistance est
augmentée de même la résistance à la fatigue.
IV.2. Amélioration par substitution
(mémoire de fin d'études)
Le travail présenté et défendu par
l'ingénieur MUTEBA KIBAMBE a porté sur la substitution faiblement
allié au manganèse par un acier fortement allié au
manganèse et traitement thermique. Les conclusions de ce travail ont
conduit à dire que l'acier Hadfield présentait une dureté
relativement faible à celle de l'acier faiblement allié, soit
160,67 HB contre 249 HB. Toutefois, la pièce originale a donné,
en fin de vie, une dureté d'environ 237 HB, ce qui implique que la
dureté avant utilisation devrait être relativement
inférieure (durcissement par écrouissage). Contrairement, la
résilience de l'acier Hadfield est de loin supérieure à
celle de l'acier faiblement allié, soit 299,79 J/Cm2 contre 51,67 J/Cm2
; toutefois, la nuance faiblement alliée présente une bonne
usinabilité que l'acier Hadfield, cependant, cet aspect ne devrait pas
être perçu comme un avantage d'autant plus qu'une
très bonne usinabilité est la conséquence
inéluctable de la perte considérable de matière par
frottement, par conséquent une faible résistance à l'usure
(MUTEBA KIBAMBE, 2017).
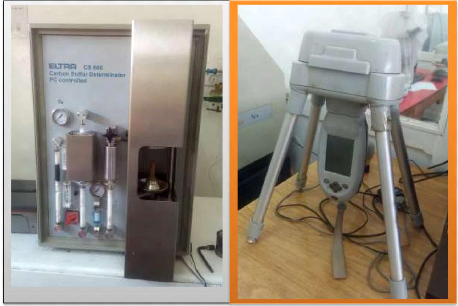
31
CHAPITRE V
MATERIEL ET PROCEDURE EXPERIMENTALE
V.1. Matériel
Dans l'hypothèse de notre étude, nous avons
réalisé nos essais sur des éprouvettes
coulées en barreaux dans les moules adaptés aux
dimensions prévues et mis en forme selon les normes.
V.1.1. Caractérisation des
échantillons
Nous avons fait la caractérisation des
échantillons chimiquement au laboratoire
des ateliers centraux de panda par la méthode de
fluorescence X au NITON XLT et par infrarouge au sulfo-carbomettre ELTRA CS800
pour l'analyse du soufre et du carbone. ci-dessous nous présentons la
photographie des appareils servant à la caractérisation chimique
des échantillons.
Figure V.1 : photographie montrant (a) un Analyseur
NITON XLT et (b) sulfo-carbomettre ELTRA CS800 a) Analyseur NITON
XLT
a.1) Principe d'analyse
L'analyse se fait par différence de longueurs d'onde et
d'énergie émise par chaque
élément contenu dans l'échantillon.
Lorsqu'on bombarde l'échantillon par les rayons X,
32
les atomes de l'échantillon acquièrent une grande
énergie et émettent des rayonnements qui sont quantifiés
en valeur électrique et convertis en teneur en élément.
Cet appareil est connecté à un ordinateur qui affiche les
résultats d'analyse.
a.2) Mode opératoire
- Allumer l'appareil sur le bouton marche/arrêt ;
- Mettre l'échantillon dans la boite
d'échantillonnage, munie d'une fenêtre par laquelle passe les
rayonnements incidents ;
- Appuyer sur la gâchette pour déclencher le
bombardement ;
- Lire les résultats d'analyse.
b) Analyseur ELTRA CS800
b.1) Principe
Celui-ci n'analyse que le soufre et le carbone, à la
seule différence avec le précédent ici on
utilise les infrarouges à la place des rayons X pour
l'analyse.
L'analyseur ELTRA CS800 comporte 4 cellules à infrarouges
dont la cellule HS (haut soufre), BS (bas soufre), HC (haut carbone) et BC (bas
Carbone).
Il est constitué aussi d'un petit four à induction
et d'un piédestal sur lequel on place l'éprouvette.
L'analyse est basée sur l'absorption des gaz issus des
réactions de combustion du carbone et du soufre dans le four
porté à 2000°C, selon les réactions suivantes :
S+02=S02
C+02= C02
Ces deux gaz seront absorbés par les infrarouges ou
l'énergie des gaz absorbés sera transformé à un
signal électrique convertit en pourcentage du carbone ou en pourcentage
du soufre.
L'analyseur ELTRA CS800 est aussi connecté à un
ordinateur qui affiche les résultats d'analyse.
b.2) Mode opératoire
? Peser l'échantillon sur la balance électronique
ELTRA 84 (figure IV.7 Ci-dessous)
;
? Prélever 0,3 g à 0,5g de l'échantillon
ainsi que les fondants (0,3g de fer à 1,2g de tungstène) et
mettre les tous dans une éprouvette ;
? Ouvrir de l'oxygène pur ;
? Démarrer l'appareil et attendre 30 à 45 minutes
pour commencer l'opération ;
33
? Placer l'éprouvette sur le piédestal dès
que le four atteint une température de 2000°C, le piédestal
monte à l'intérieur du le four ;
? L'écran commence à afficher l'évolution de
l'analyse et montrant les résultats ;
? Une fois que l'analyse sera terminé, le piédestal
va descendre avec l'éprouvette brulé et l'échantillon sera
fondu ;
? Lire les résultats finals sur l'écran.
V.1.2. Essais mécaniques
Les essais mécaniques ont pour but de déterminer
les caractéristiques mécaniques des
aciers. Les différents essais réalisés dans
ce travail sont :
- L'essai de dureté ;
- L'essai de résilience ; - L'essai de traction.
a) Essai de dureté
La dureté correspond à la mesure d'une
résistance à la pénétration locale du
matériau considéré. La dureté est
aussi une propriété physique qui dépend non seulement des
caractéristiques de ce matériau, mais aussi de la nature et de la
forme du pénétrateur et du mode de pénétration.
Dans le cadre de ce travail, la mesure de la dureté a
été faite par mesure de la dureté brinell.
1. Essai de dureté Brinell
Les essais selon Brinell s'appliquent au fer et à l'acier
d'une résistance de 1000 à 1500
N/mm2 et à tous les métaux
non-ferreux. Le tableau suivant indique les charges d'essai à utiliser
pour les matériaux et les différents diamètres de billes.
Il indique également le diamètre de billes à choisir pour
une épaisseur de paroi minimum déterminée.
2. Principe
L'essai consiste à appliquer à la surface d'un
matériau préalablement préparé (surface
plane, polie et dépourvue d'écrouissage), une
charge prédéfinie, à l'aide d'un
pénétrateur. Le pénétrateur est une bille en acier
ou en carbure de diamètre compris entre 10 et 1mm, la charge doit
être telle que l'empreinte obtenue soit comprise entre deux rapport
basés sur le diamètre de la bille : 0.24 x Diamètre de la
bille < diamètre de l'empreinte < 0.6 x Diamètre de la
bille.
34
Pour notre étude les essais sont
réalisés, à l'aide d'un duromètre à rebond
portatif de marque EQUOTIP 3, sur des éprouvettes à l'état
brut de coulée et celles ayant subi des traitements thermiques.
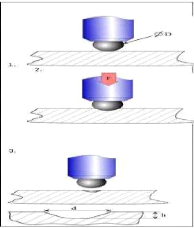
Figure VI.2 principe de l'essai de
dureté
3. Mode opératoire
> Démarrer l'appareil en appuyant sur le bouton
marche et arrêt pendant environ 2 seconde ;
> Sélectionner le groupe de matériau applicable
à l'échantillon ; > Sélectionner le nombre d'impact n
par série des mesures > Préparer l'échantillon à
la meule
> Armer la sonde en glissant simplement le tube vers l'avant
;
> L'instrument de frappe est fermement maintenu avec une main
et le tube de chargement est actionné avec l'autre main jusqu'à
ce que le contact soit ressenti ;
> Appuyer sur le bouton de déclenchement pour
libérer le corps de frappe ;
> Répéter ce cycle pour effectuer une autre
mesure à un autre endroit, selon le nombre de série de mesures
;
> Après la dernière mesure n, la moyenne de la
dureté sera affichée dans l'écran.
b) Essai de résilience
Les essais de résilience permettent de
caractériser la fragilisation d'un matériau
sous l'action d'un choc, soit de mesurer les
propriétés du métal à l'ambiance, soit alors de
déterminer la température de transition ductile-fragile sous
contraintes triaxiales. Cet essai est très ancien et sa vulgarisation
par Charpy date du XXe siècle.
1. Principe
La résilience est l'énergie nécessaire
pour produire la rupture d'une éprouvette placée sur deux appuis.
Cette énergie est fournie par la chute d'un mouton-pendule de Charpy
qui, dans les conditions normalisées, possède une énergie
de 300 j et est animé, au moment du choc, d'une vitesse de
déplacement de 5 à 5,5 m/s. l'énergie consommée par
la rupture de l'éprouvette se déduit de la lecture des angles de
chute et de remontée du pendule. Elle est rapportée à la
section à fond d'entaille pour calculer la résilience.
L'énergie consommée pour rompre le barreau est
mesurée en faisant la différence d'énergie potentielle
entre la hauteur de chute du « mouton » et celle à laquelle il
remonte
après avoir rompu le barreau[ ]. Si ce dernier
était complètement fragile, le « mouton »
remonterait à la même hauteur que celle d'où il a
chuté ; s'il était au contraire extrêmement tenace, il ne
serait pas rompu et le pendule ne remonterait pas du tout. L'énergie de
rupture ainsi déterminée s'appelle la résilience. Plus
elle est élevée, plus le matériau est tenace.
Ainsi la résilience, généralement
notée KCV se calcule comme suit :
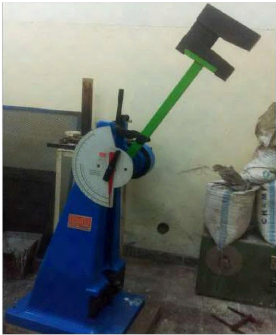
35
Figure V.3 : Photographie d'un mouton pendule de
Charpy de 300 J
36
L'éprouvette utilisée est un barreau à
section carrée de 10 mm de côté et de 55 mm de long avec
une entaille en V, qui a un rayon de 2,5 mm, une profondeur de 2 mm et un angle
de 45°.
2. Mode opératoire
> Mettre le « mouton » à son niveau de haut
énergie ;
> Régler l'aiguille de mesure ;
> Placer la pièce de sorte que la surface de l'entaille
soit contre la surface de contact
du « mouton » ;
> Lâcher le « mouton » de façon qu'il
frappe la pièce ;
> Lire la différence d'énergie
> Appuis sur un contre poids enfin de réduire la
vitesse du balance du « mouton »
pour arriver à le freiner.
a) Essai de traction
L'essai de traction est le moyen le plus fondamental
employé pour caractériser le
comportement mécanique d'un matériau sous une
sollicitation progressive à vitesse de chargement faible ou
modérée.
Les essais de traction ont été faits à
LATRECA
Principe
Les éprouvettes du matériau
considéré sont fixées dans une machine de traction
qui impose un allongement croissant à
l'éprouvette, et enregistre simultanément l'effort de traction
appliqué et allongement de l'éprouvette sur un diagramme
appelé courbe de traction, et dont l'exploitation permet de
dégager les caractéristiques du matériau testé.
Au cours de l'essai, il apparait les phases suivantes :
1ère phase : le domaine
élastique
Dans le domaine élastique, la déformation
crée par le phénomène de traction n'est pas constante, de
ce fait si l'on retire cet effet, l'éprouvette retrouve sa dimension
originale.
2ème phase : le domaine plastique
Lorsque l'allongement est tel, que l'éprouvette ne
retrouve plus sa dimension original et que l'allongement persiste si l'on
annule l'effet de traction, on considère que l'on se trouve dans le
domaine plastique.
37
3ème phase : la striction
La striction est l'apparition d'une diminution
localisée de la section. Un matériau cassant ne peut être
déformé, la rupture ce produit avant la striction.
L'allongement est exprimé en pour-cent, c'est
l'allongement permanent de l'éprouvette rompue. Il est
déterminé par la formule :
=[(Lu -- Lo)/Lo] x 100
Résistance élastique :
Re=Fe/ (avec Re en MPa ;
Fe en Newton et So en mm)
S
0
Résistance à la rupture :
Rr=Fe/ (avec Rr en MPa ;
Fe en Newton et So en mm) S
0
V.1.3. Traitement thermique
a) Introduction
Dans le cadre de ce travail, nous avons appliqué un cycle
de traitement thermique
à des différentes températures choisies
pour étude. Ainsi nous avons traité à 890, 910 et
940°c et refroidi dans le four afin d'adoucir l'acier. Les
températures choisies avaient pour but d'obtenir les différentes
phases pour permettre à la pièce d'être facilement
usinable. Puisqu'elle doit être ramenée une autre valeur de
dureté, un autre cycle de traitement thermique comprenant le chauffage
et le refroidissement selon le milieu sera étudié.
Le laboratoire des ACP nous a permis à procéder
ces différents traitements dans le four à résistance du
type BENET dont sa photographie est donnée ci-dessous.
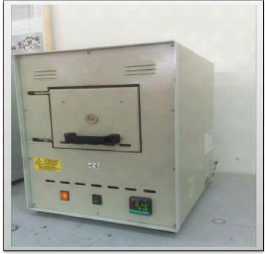
Figure V.4 : Photographie d'un four de traitement
thermique de type BENET
38
Caractéristiques du four
Les caractéristiques du four de traitement
thermique des ACP sont :
> Type forme ZE (parallélépipédique) ;
> Température maximale : 1100°C ;
> Puissance maximale : 2,3 KW ;
> Tension : 220V ;
> Fréquence : 50-60HZ ;
b) Mode opératoire
Les étapes suivies pour l'utilisation de ce four sont
:
> démarrer le four ;
> Placer les échantillons sur la sole du four ;
> Fermer la porte du four ;
> Régler la température de chauffage ;
> Après autorégulation automatique,
passé au palier en chronométrant le temps
de maintien de 30 minutes ;
> Refroidir dans le four, à l'air et dans l'eau.
c) Paramètre du traitement
thermique
Nous avons réalisés trois types de traitement
thermique comprenant le traitement
d'adoucissement, la trempe et le revenu.
- Pour le traitement d'adoucissement les paramètres
fixés sont :
> Température de chauffage : 890, 910, 940°C et
960°C;
> Temps de maintien : 30 minutes ;
> Milieu de refroidissement : four
- Les paramètres concernant la trempe sont :
> Température de chauffage : 910°C
> Temps de maintien : 15, 30 et 45 minutes
> Milieu de refroidissement : Air et Eau
- Le revenu a été fait selon les paramètres
suivants :
> Températures de chauffage : 400, 500 et 600°C
> Temps de maintien : 30 minutes
> Milieu de refroidissement : Air
39
V.1.4. Micrographie
a) Introduction
La micrographie nous permet d'observer les différentes
structures ou phases
présentes dans les échantillons
considérés pour l'étude. L'examen de la micrographie se
fera sur des échantillons traités et non traités. Les
échantillons sont attaqués avant analyses.
Ces observations ont été réalisés
au laboratoire de la fonderie des ACP l'aide d'un microscope optique de type
EUROMEX raccordé à une camera HD servant au transfert des images
sur un ordinateur dont la figure est représentée ci-dessous :
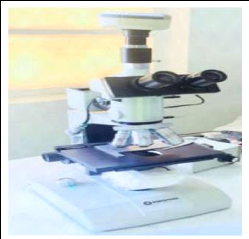
Figure V. 5 - photographie d'un microscope optique
de type Euromex équipé d'une caméra HD
b) Principe de fonctionnement du
microscope
Le principe du microscope est tel qu'il est alimenté par
l'énergie électrique où
une source lumineuse émise qui envoie la
lumière sur l'échantillon à travers un dispositif optique.
Les rayonnements réfléchis par l'échantillon sont repris
par l'objectif qui donne une première image intermédiaire ;
grâce à un miroir semi-réfléchissant, l'image est
renvoyée vers l'oeil de l'observateur à travers une lentille
oculaire qui permet de visualiser les différentes structures
micrographiques de l'échantillon.
c) Matériels utilisés
Le matériel ci-dessous nous a permis de réaliser
des observations micrographiques :
? une tronçonneuse METASERV ;
40
> une surfaceuse GLIA ;
> une polisseuse à disque tournant du type METASERV
;
> un microscope optique du type Euromex;
> des papiers abrasifs successifs de 120 à 1200
> un feutre fin ;
> une pâte d'alumine;
> une solution de Nital à 3% ;
> de l'eau distillée.
d) Mode opératoire
La mise en oeuvre de la micrographie de l'échantillon se
réalise en quatre étapes à savoir :
> Sa découpe à la tronçonneuse avec
un lubrifiant pour éviter l'échauffement exagéré de
l'échantillon ;
> Son enrobage de l'échantillon pour une bonne
manipulation ;
> Son polissage qui se fait sur différents papiers
abrasifs de granulométries différentes (P120 -P240-P350- P400 -
P600 - P800 - P1000-P1200) et sur la toile où l'on utilise l'eau
distillée, la patte d'Alumine ou de diamant ;
> L'attaque par un réactif approprié dans le
cas d'espèce, on a utilisé le Nital comme réactif. Ce
Nital a été préparé à 4% : on
prélève 4ml de HNO3 dans un ballon de 100ml que l'on remplit avec
l'alcool éthylique (alcool dénaturé) ;
> Son observation micrographique ;
> Le compte rendu ou interprétation.
e) Préparation des
échantillons
Nous avons utilisé la tronçonneuse du type
METASERV, équipée d'un système de
refroidissement pour éviter d'altérer les
structures afin de découper les échantillons sur les
éprouvettes brutes de coulée et ayant subi un traitement
thermique spécifique.
J) Le polissage des
échantillons
Cette opération se fait en trois phases : le dressage, le
dégrossissage et le polissage fin.
> Le dressage : cette opération se fait sur une
surfaceuse du type GLIA (figure
IV.10) pour avoir une surface bien plane.
> Le dégrossissage : il se fait à l'aide
d'une polisseuse du type METASERV, en se servant d'une série de disques
en papiers abrasifs de granulométries différentes
(P120, P200, P320, P400, P600, P800 et P1200), du plus grossier
au plus fin ;
41
> Le polissage fin de finition : il se fait à l'aide
d'une pâte d'alumine (0,03ìm) et de l'eau distillée
aspergées sur un feutre fin fixé sur la polisseuse du type
METASERV.
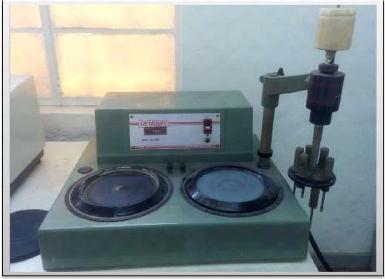
Figure V. 6 - photographie d'une polisseuse fine du
type METASERV g) Attaque chimique de l'échantillon
Les échantillons polis ont été
attaqués avec du Nital préparé avec un mélange
de
HNO3 (4%) et d'alcool pendant un temps d'environ 15 secondes
avant l'observation au
microscope ; cela en vue de révéler la structure
des grains et joints de grains présente.
Le mode opératoire pour la préparation de la
solution de Nital consiste à :
> Prendre un ballon de 100ml ;
> Y verser 4CC d'acide nitrique dans le ballon ;
> Remplir ce ballon avec de l'éthanol jusqu'au trait de
jauge ;
> Agiter le mélange pendant 3 à 5 minutes ;
> Prendre un verre de montre et y verser un peu de Nital ;
> Y tremper l'échantillon pendant 15 à 25
secondes, selon le type de nuance de
l'échantillon à analyser ;
> Rincer l'échantillon avec de l'eau distillé
;
> Passer à l'examen au microscope.
42
h) Observation au microscope
Cette observation a été faite au microscope optique
du type Euromex, elle a consisté :
? A Allumer le microscope ;
? A Placer l'échantillon sur le porte échantillon
;
? A Régler les lentilles de l'objectif et de l'oculaire en
vue d'avoir un grossissement
adéquat ;
? A Ajuster l'échantillon au moyen des boutons de
positionnement ;
? A Passer à la capture des clichés.
V.2. Procédure expérimentale
La procédure expérimentale consiste à
donner un aperçu sur la fusion de la
nuance A3SS afin d'optimiser les différents
paramètres du traitement thermique comme la température
conduisant à l'adoucissement de la pièce, le milieu de
refroidissement, le temps de maintien et la température de revenu. Cela
pour permettre à la pièce qui est à l'état brute de
coulée d'être usinée, dans le but de diminuer la
dureté jusqu'au seuil de l'usinabilité comprise entre 190 et 210
HB. En fin la conformer à l'état de fonctionnement exigé
par le client par l'élévation de la dureté entre 300-400
HB.
V.2.1. Fusion
La fusion des métaux ferreux s'est faite au four
électrique à arc triphasé de type
STEIN d'une capacité de 5 tonnes dont l'alimentation en
matière première est assurée par le parc à
mitraille et les ferro-alliages (ferromanganèses, des ferrochromes,
ferromolybdènes et des Ferro-silicium) ces derniers servent
essentiellement à la mise en nuance de l'acier. Les grandes
opérations nécessaires à la bonne conduite d'une
élaboration d'aciers sont :
a) Le chargement
L'enfournement de la mitraille au four électrique s'est
fait de la manière
suivante :
- Une quantité des pièces de refusions, soit 2600
kg - D'une quantité des mitrailles, soit 1300 kg
- De la fonte pour quantité de 70 kg
43
b) La fusion proprement dite
La fusion proprement dite a été faite selon le mode
opératoire suivant :
a) Démarrer le four avec ajout d'un peu de
ferromanganèse pour accélérer l'amorçage ;
b) Introduire plus ou moins 60% de la quantité totale
de chaux vive dans la charge. La mitraille passe de l'état solide
à l'état liquide, c'est au cours de cette fusion qui a lieu
à basse température que la déphosphoration
s'opère.
La charge enfournée est fondue par les arcs
électriques jaillissant lorsque les électrodes sont en contact
avec la masse du métal. Cette charge présente une composition
chimique préalablement connue. Celle-ci est obtenue après un
calcul de la proportion en poids de tous les composants de l'acier
proposé, on parle ainsi du « calcul des charges »
La quantité totale de chaux vive à introduire
dans le four doit être scrupuleusement respectée
c'est-à-dire plus ou moins 45Kg par tonne de métal.
c) L'oxydation
Lorsque le métal est complètement fondu, insuffler
de l'oxygène suivant les
proportions requises dans le bain liquide et chaud pour
d'avantage oxyder les impuretés. Par manque d'oxygène, on peut
introduire l'oxyde de fer (Fe203) dans le bain liquide et chaud. Cette
opération augmente la température du bain liquide et provoque un
grand brassage dans le bain au fond du four (laboratoire du four). A la fin de
cette opération, tous les éléments oxydés remontent
dans la scorie (prélever l'échantillon en nappe) du métal
pour essai de pliabilité.
d) Le décrassage
- Arrêter le four, le basculer du côté porte
de travail jusqu'à déversement d'un peu
de scorie dans la fosse de décrassage ;
- Mettre le sable tout venant mélangé à
l'eau sur toute la plate-forme de la porte de travail
- Placer les fer-rond de plus ou moins 25mm de diamètre
sur l'une des paires des cales conçues pour la cause
- Racler la scorie se trouvant aux alentours de la porte de
travail à l'aide d'un ringard et la déverser dans la fosse de
décrassage Toute la scorie se trouvant au fond du four sera
entrainée par gravité vers la porte de travail et devra
être aussi déversée
44
dans la fosse de décrassage Le métal doit rester nu
c'est à dire exempte de scorie cette dernière doit être de
couleur noire brillante (mauvaise qualité de la scorie)
NB. Pendant l'opération de décrassage le
fondeur-décrasseur évite que la scorie ne se colmate pas sur le
pavé, un deuxième fondeur jettera le sable mélangé
à l'eau sur le pavé de la porte de travail enfin un
troisième fondeur enlèvera les différentes croutes
formées sur le pavé à l'aide d'une barre a mines.
Ne pas plonger le ringard dans le bain au risque de corroder
leurs plaques (le ringard sera sans plaque, l'opération sera interrompue
et le décrassage sera incomplet) où moins d'amasser inutilement
le métal sur la plaque du ringard (le ringard pèsera lourd et
fatiguera le fondeur avec risque de ne pas terminer l'opération
délicate de décrassage)
e) La réduction ;
- Remettre le four en position de travail
- Introduire plus ou moins 2Kg d'aluminium dans le bain nu
- Introduire plus ou moins 30% de la quantité totale de
chaux vive dans le bain
- Redémarrer le four
- Laisser travailler le four pendant plus ou moins 15 minutes
- Introduire le mélange réducteur
préalablement préparer (10% de chaux vive restantes, coke fin,
FeSi, SiCu, spath- fluor, terre rouge...). C'est pendant cette phase à
haute température qu'a lieu la désulfuration et la couleur de la
scorie doit être brune tendant au kaki passant par le vert, elle sentira
l'odeur du carbure de calcium (Ca2C) au contact de l'eau H20.
J) La mise au point ;
a) Mise au point des éléments d'addition (les
ferroalliages et le nickel pur)
On ajoute les éléments d'alliage pour permettre
l'obtention de la composition contenue dans la fourchette
représentée dans le tableau ici-bas
b) Analyse des éléments au laboratoire
c) Mise au point de la température
45
g) La coulée
a) Mesurer la température
b) Couler dans la poche de coulée chauffée
préalablement, intervient lorsqu'on atteint la température, qui
varie de 1580 à 1600°C. Donc le métal liquide est
basculé dans la poche de coulée ; ensuite, dans le moule.
On ajoute de l'aluminium dans la poche de coulée sous
forme des lingots, pour la désoxydation définitive de l'acier
(acier calmé) et pour régler la grosseur des grains
d'austénite (dispersion des fines d'alumine). Il en est de même
pour le silicium, sous forme de ferro-alliage.
Après refroidissement, on décoche et on
débarrasse la pièce de tous les artifices de coulée
(masselottes, descente, chenal, ...) au chalumeau, .... Pour passer au
contrôle qualitatif et quantitatif.
V.2.2. Traitement thermique
L'optimisation du traitement thermique se fera de façon
à donner en premier lieu
une température qui permettra de diminuer la
dureté pour atteindre des valeurs de 190 à 210 HB, valeurs qui
permettront à la pièce d'être usinée, mais aussi
garder une bonne
valeur de la résilience. En deuxième lieu,
puisqu'il faut remonter la dureté aux conditions d'utilisation, on
étudiera le milieu de refroidissement qui donnera le meilleur compromis
entre la dureté et la résilience à l'acier
étudié.
a) Optimisation de la température
d'adoucissement
Dans cette nous étude, nous soumettrons la pièce
à des différentes températures
pour voir comment évoluera la dureté ainsi que
la résilience des éprouvettes prises pour étude. Les
températures choisies sont AC3+30°C, AC3+50°C, AC3+80°C
et AC3+100°C tout en gardant le milieu de refroidissement et le temps de
maintien constants. La température qui donnera le meilleur
résultat entre la dureté et la résilience sera retenue
pour adoucir la pièce pour usinage.
b) Optimisation du milieu de
refroidissement
Par milieu de refroidissement on voit le four, l'air et l'eau.
Ces milieux nous
permettront à voir comment évoluer la
dureté et la résilience. La température qui a donné
précédemment un bon compromis entre la dureté et la
résilience sera prise pour étude du
46
milieu tout en gardant le même temps de maintien qui est de
30 minutes. S'il y a lieu, il sera question d'optimiser la température
de revenu (dans le cas d'une trempe).
c) Optimisation du temps de
refroidissement
Pour cette étape les éprouvettes seront soumises
à des temps de maintien de 15,
30 et 45 minutes. Tout en gardant la température
(AC3+50°C) et le milieu de refroidissement constants.
Au bout de nos essais nous ressortirons des résultats qui
donneront une température d'adoucissement, le milieu de refroidissement,
la température de revenu (s'il y a lieu) et le temps de maintien,
valeurs qui donneront un bon compromis de la résilience et
dureté.
47
CHAPITRE VI
PRESENTATION ET INTERPRETATION DES
RESULTATS
Pour ce chapitre nous nous sommes limités aux essais de
traction à l'état brut de coulée ainsi que les essais
dureté et de résilience à l'état de coulée
et à l'état trempé.
Nous étudierons l'influence du traitement thermique sur
les propriétés mécaniques. Cette étude comprend
l'influence de la température, l'influence du milieu de refroidissement,
l'influence du temps de maintien pour arriver à trouver un meilleur
compris entre la dureté et la résilience de la nuance d'acier qui
fait l'objet de notre étude.
VI.1. Caractérisation des échantillons
La nuance A3SS 30NiCrD13 est une composition locale que les
ACP utilisent pour la fabrication du lower Mantle (pièce à
cône utilisée dans le concasseur à cône). C'est acier
faiblement allié au nickel auquel on ajoute des petites quantités
de chrome, molybdène et manganèse.
Ci-dessous nous donnons dans le tableau V.1. la
caractérisation chimique de la nuance A3SS.
Eléments
|
C
|
Mn
|
Ni
|
Cr
|
Mo
|
Ti
|
Pb
|
Cu
|
Teneurs
|
0,30
|
0,89
|
3,26
|
1,22
|
0,22
|
0,28
|
0,01
|
0,76
|
Tableau VI.1 : Caractérisation chimique de
la nuance A3SS
Le Nickel est un élément gammagène et
graphitisant, 3 fois moins énergique que le silicium. Dans les aciers
à bas carbone et à des teneurs inférieures à 6% en
Nickel, il augmente la résistance mécanique, la limite
élastique mais diminue la dureté et de l'allongement à la
rupture. Au-delà de 1%, il diminue le grossissement du grain lors de
l'austénitisation et conduit à l'augmentation de la
résilience.
Le manganèse, à la teneur de 0,89%, bloque
l'effet graphitisant du nickel. Le chrome améliore l'aptitude à
la trempe, accroit la résistance à la rupture sans diminuer la
ductilité de façon appréciable. Le molybdène quant
à lui améliore les propriétés de résistance
aux chocs des aciers trempés.
Ci-dessous nous donnons les propriétés
mécaniques et la microstructure obtenues après coulée.
48
HB et KCV
|
(HB)
|
W (J)
|
S
(cm2)
|
KVC (J/cm2)
|
Etat brut de coulée (A3SS)
|
284
|
3,4
|
0,8
|
4,3
|
|
4
|
0,8
|
5,0
|
|
3,8
|
0,8
|
4,8
|
|
3,5
|
0,8
|
4,4
|
|
4,5
|
0,8
|
5,6
|
Moyenne
|
280
|
|
|
4,8
|
|
Tableau VI.2 : propriétés
mécaniques à l'état brut de coulée
b) Traction
N° ECH
|
Diamètre (mm)
|
section (mm2)
|
Force (kg)
|
contrainte (kgf/mm2)
|
Allongement
|
Longueur utile (cm)
|
mm
|
%
|
1
|
13,48
|
142,64
|
3345
|
23,45
|
0
|
-
|
19,5
|
2
|
11,6
|
105,63
|
3150
|
29,82
|
0
|
-
|
19
|
3
|
10,16
|
81,03
|
2505
|
30,91
|
0
|
-
|
14
|
4
|
9,6
|
72,35
|
3010
|
41,61
|
0
|
-
|
12,5
|
Tableau VI.3 : Essais de traction
L'analyse du tableau VI.3 montre que le matériau a
connu une rupture fragile qui est traduite par la valeur nulle de l'allongement
cela est dû par les défauts d'homogénéisation que
présentent les échantillons. Nous pouvons aussi le constater sur
le tableau VI.2 par les valeurs de dureté et résilience. Le
matériau est dure et moins ductile ce qui explique sa rupture
fragile.
Dans la micrographique ci-dessous représentant la
structure du matériau à l'état brut de coulée, l'on
remarque la présence de ferrite, perlite et carbures reparties d'une
façon homogène.
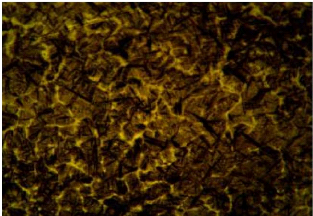
49
Figure VI.1 : structure cristallographique de
l'alliage à l'état brut de coulée
VI.2. Essais mécaniques
Les différents essais réalisés ont eu
comme objectif spécifique de donner un aperçu sur les
propriétés mécaniques tel que la dureté, la
résistance mécanique et la résilience. Par la suite nous
étudierons l'influence de la température de traitement, du temps
de maintien, du milieu de refroidissement ainsi que l'influence des
éléments d'addition.
VI.2.1. Influence de la température
d'adoucissement a) Présentation des
résultats
Dans cette série d'essais, il a été
question d'étudier l'impact de la température
d'austénitisation du traitement thermique sur les
propriétés comme la dureté et la résilience. Les
températures ont été variées dans les gammes
suivantes : AC3+30°C, AC3+50°C, AC3+80°C et AC3+100°C. Le
choix de la température a été opéré en
raison de la teneur en carbone de la nuance étudiée puisque
l'austénitisation se fait à AC3 + X°C et ce point se situe
pratiquement à environ 860°C, température à laquelle
nous sommes allés, pour cas d'étude. Les paramètres
constants que nous nous sommes fixés sont le milieu de refroidissement
(four) et le temps de maintien qui est de 30 minutes.
Les résultats obtenus sont repris dans le tableau V.2
qui représente la variation de la dureté et de la
résilience en fonction de la température.
Ainsi nous retiendrons une température qui nous
fournira le meilleur compris entre la dureté et la résilience.
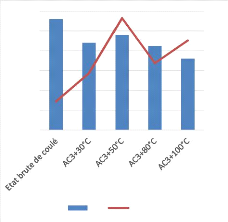
300
250
200
150
100
50
0
HB K (J/cm2)
4
8
6
0
20
2
18
16
14
12
10
|
890°C
|
910°C
|
940°C
|
960°C
|
W (J)
|
S (cm2)
|
KCV (J/cm2)
|
W (J)
|
S (cm2)
|
KCV (J/cm2)
|
W (J)
|
S (cm2)
|
KCV (J/cm2)
|
W (J)
|
S (cm2)
|
KCV (J/cm2)
|
Adoucissement (A3SS)
|
7,5
|
0,8
|
9,375
|
15
|
0,8
|
18,75
|
8,7
|
0,8
|
10,875
|
12
|
0,8
|
15,00
|
8,2
|
0,8
|
10,25
|
15,7
|
0,8
|
19,63
|
9
|
0,8
|
11,25
|
12,6
|
0,8
|
15,75
|
7,2
|
0,8
|
9
|
14,5
|
0,8
|
18,13
|
9,3
|
0,8
|
11,625
|
11,5
|
0,8
|
14,38
|
Moyenne
|
|
|
9,54
|
|
|
18,83
|
|
|
11,25
|
|
|
15,04
|
Tableau VI.4 : Essais de résilience de
l'A3SS après traitement d'adoucissement
HB
|
K (J/cm2)
|
Etat brute de coulé
|
280
|
4,8
|
AC3+30°C
|
220
|
9,54
|
AC3+50°C
|
240
|
18,83
|
AC3+80°C
|
212
|
11,25
|
AC3+100°C
|
180
|
15,05
|
Tableau VI.5 : moyenne de valeur de
résilience et de dureté aux températures
d'adoucissement
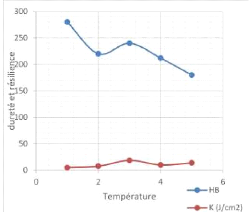
50
Graphique VI.1 : l'Influence de la
température d'adoucissement sur HB et K
b) Interprétation
L'analyse du tableau VI.5 (qui donne la moyenne à
différentes températures) et
du graphique VI.I, montre que les éléments
d'alliage n'agissent pas sur la dureté à l'état brut de
coulée parce qu'à l'état brut de coulée la hausse
de la dureté est due à la
51
ségrégation lors de la solidification et
à la présence des carbures. Nous remarquons qu'en chauffant
l'éprouvette sur le palier de températures données
ci-haut, la dureté baisse de moins en moins pour les températures
élevées ; cela est dû à la dissociation des carbures
qui sont témoins de la dureté dans les aciers. Les hautes
températures peuvent également données lieu à un
grossissement des grains austénitiques. A la température de
AC3+80°C et avec un refroidissement trop lent, nous constatons une
diminution de la dureté à environ la valeur que nous nous sommes
assignés comme objectif, néanmoins la résilience du
matériau n'augmente pas comparativement aux températures de 910
et 960°C.
c) Microstructure
Les figures VI.2, VI.3 et VI.4 donnent l'évolution de la
structure de la nuance selon les
températures considérées.
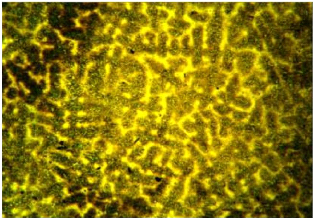
Figure VI.2 micrographie de l'acier A3SS
chauffé à AC3+30°C et refroidi dans le four
Constatons une présence de ferrite en
prépondérance, une faible quantité d'austénite et
de la perlite avec mise en évidence des défauts ponctuels. Cette
structure est due au refroidissement très lent qui donne les structures
d'équilibre avec diffusion du carbone, témoin la chute de la
dureté et la remontée de la résilience.
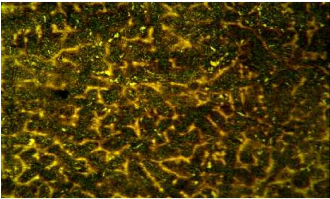
52
Figure VI.3 micrographie de l'acier A3SS
chauffé à AC3+50°C et refroidi dans le four
Nous remarquons une présence de la ferrite,
cémentite et de l'austénite résiduelle. Avec le
refroidissement lent, étant donné que nous avons un acier
faiblement allié, il y a lieu de retrouver de l'austénite
résiduelle dans la pièce. Cette structure nous donne une bonne
résilience puisqu'il y a dissociation des carbures et présence de
l'austénite et le nickel présent dans l'alliage diminue le
grossissement des grains ce qui conduit à l'augmentation de la
résilience.
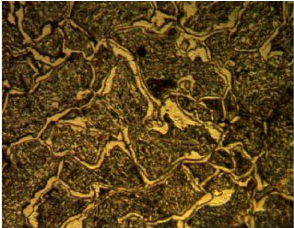
Figure VI.4 : Micrographie de l'acier A3SS
chauffé à AC3+80°C et refroidi dans le four
VI.2.2. Influence du milieu de
refroidissement
a) Présentation des
résultats
Etant donné que dans les conditions d'utilisation de la
pièce (Lower Mantle) qui
est sollicitée aux chocs, dans cette série
d'essais, il a été question de remonter la dureté
aux contions d'utilisations qui sont 300-400 HB. Pour cela
nous avons étudié différents milieu de refroidissement et
voir lequel nous donnera les caractéristiques voulues tout en gardant la
température de maintien de 910°C, température qui nous a
dégager un optimum entre la dureté et la résilience, et le
temps de maintien 30 minutes. Les milieux étudiés sont le four
(qui donne des faibles vitesses de refroidissement), l'air (vitesses moyennes)
et l'eau (vitesses assez rapides).
Dans le tableau VI.5 sont reprises les valeurs de
dureté et de résilience selon les différents milieux.
|
refroidissement dans le
four
|
refroidissement dans
l'air
|
refroidissement dans l'eau (trempe)
|
HB
|
W (J)
|
S (cm2)
|
KCV (J/cm2)
|
HB
|
W (J)
|
S (cm2)
|
KCV (J/cm2)
|
HB
|
W (J)
|
S (cm2)
|
KCV (J/cm2)
|
Austénitisation à
910°C/30'
|
243
|
15
|
0,8
|
18,75
|
302
|
9,6
|
0,8
|
12
|
327
|
15,2
|
0,8
|
19
|
238
|
15,7
|
0,8
|
19,63
|
305
|
10,5
|
0,8
|
13,13
|
330
|
15,3
|
0,8
|
19,1
|
240
|
14,5
|
0,8
|
18,13
|
303
|
10
|
0,8
|
12,5
|
326
|
15
|
0,8
|
18,8
|
Moyenne
|
240
|
|
|
18,83
|
303
|
|
|
12,54
|
328
|
|
|
19
|
Tableau VI.6 : Essais de dureté et
résilience de l'A3SS après austénitisation à
910°C pendant 30 minutes
La figure ci-dessous représente les valeurs de
dureté et de résilience selon les différents milieux de
refroidissement
HB
|
K (J/cm2)
|
Four
|
240
|
18,83
|
Air
|
303
|
12,54
|
Eau
|
328
|
19
|
53
Tableau VI.7 : valeurs moyennes de dureté et
résilience après austénitisation à
910°C
Four Air Eau
HB K (J/cm2)
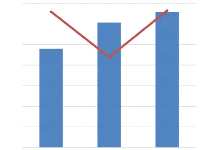
20
18
16
14
12
10
8
6
4
2
0
350
300
250
200
150
100
50
0
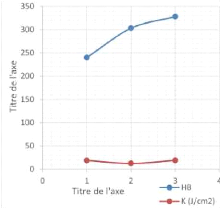
54
Graphique VI.2 : Histogramme des valeurs moyennes
de résilience et dureté après austénitisation
à 910°C et refroidissement selon les milieux
b) Interprétation
L'analyse de l'histogramme montre que pour un refroidissement
dans l'eau
(trempe), la dureté augmente avec la résilience
et un optimum se dégage vu qu'à cette température
l'austénitisation s'est faite totalement et les carbures ont eu le temps
de se dissoudre. Cela s'expliquerai par le fait qu'en étant à
910°C, on obtient l'austénite qui dissout un grand pourcentage en
carbone (témoins de la dureté dans les aciers) par rapport
à la ferrite et en faisant un refroidissement à une grande
vitesse, cette austénite est gardée à basse
température sans diffusion du carbone. Ceci a directement un impact sur
la dureté et le nickel qui se trouve en solution solide minimise le
grossissement des grains lors de l'austénitisation pour donner lieu
à une bonne résilience.
55
c) Micrographie
Les figures VI.5 et VI.6 représentent
l'évolution de la structure selon les différents milieux de
refroidissement.
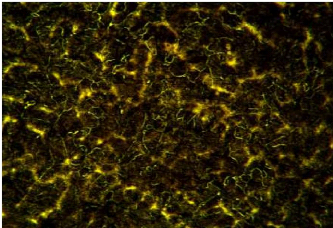
Figures VI.5 : structure de l'A3SS après
austénitisation à 910°C et refroidissement à
l'air
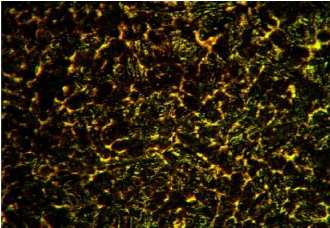
Figures VI.6 : structure de l'A3SS après
austénitisation à 910°C et refroidissement à
l'eau
La figure VI.4 fait apparaitre une structure
austéno-ferritique avec une grande proportion d'austénite,
présence des carbures et de ferrite repartis de façon
homogène tandis que la figure VI.5 quant à elle présente
une structure avec une grande prépondérance en austénite.
Ces structures sont témoins des valeurs de dureté et
résilience obtenues.
VI.2.3. Influence du temps de maintien
Dans cette catégorie d'essais, il a été
question de varier le maintien pour voir
comment la dureté et la résilience
évoluent tout en procédant par une austénitisation
à 910°C suivie d'une trempe à l'eau. Les résultats
des essais sont donnés dans le tableau ci-dessous :
a) Présentation des
résultats
|
15 minutes
|
30 minutes
|
45 minutes
|
HB
|
W (J)
|
S (cm2)
|
KCV (J/cm2)
|
HB
|
W (J)
|
S (cm2)
|
KCV (J/cm2)
|
HB
|
W (J)
|
S (cm2)
|
KCV (J/cm2)
|
Austénitisation à 910°C suivie d'une
trempe à l'eau
|
297
|
18,2
|
0,8
|
22,75
|
327
|
15,2
|
0,8
|
19
|
287
|
11
|
0,8
|
13,8
|
303
|
18,4
|
0,8
|
23
|
330
|
15,3
|
0,8
|
19,13
|
293
|
12
|
0,8
|
15
|
290
|
18
|
0,8
|
22,5
|
326
|
15
|
0,8
|
18,75
|
288
|
10
|
0,8
|
12,5
|
Moyenne
|
297
|
|
|
22,75
|
328
|
|
|
18,96
|
290
|
|
|
13,8
|
Tableau VI.8 : Evolution des propriétés
en fonction du temps de maintien
Temps de maintien
|
HB
|
K (J/cm2)
|
15
|
297
|
22,75
|
30
|
328
|
18,96
|
45
|
290
|
13,8
|
Tableau VI.9 : Valeurs moyennes de dureté et
résilience en fonction du temps
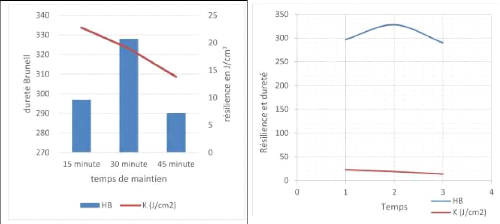
56
Graphique VI.3 : Evolution de la dureté et
résilience en fonction du temps
b) Interprétation
Le résultat montre qu'en faisant varier le temps de
maintien, tel que le montre le
graphique VI.3, il revient à dire que c'est autour de
30 minutes que l'on enregistre des bonnes valeurs de résilience et de
dureté qu'au-delà et que celles-ci diminuent au fur et à
mesure que l'on prolonge le maintien. Ceci peut être dû au fait que
plus le matériau est exposé pendant longtemps à une
température, plus la coalescence des grains est importante et influe sur
les propriétés mécaniques de l'acier tel que nous montre
le graphique.
c) Micrographie
L'analyse micrographique est représentée par les
figures VI.7 et VI.8 qui donnent
l'évolution de la structure pour 15 et 30 minutes.
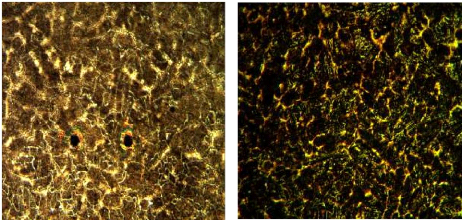
Figures VI.7 : structure de l'A3SS
après austénitisation à 910°C pendant
15 minutes et refroidissement à l'eau
Figures VI.8 : structure de l'A3SS
après austénitisation à 910°C pendant
30 minutes et refroidissement à l'eau
57
VI.2.4. Influence de la température de
revenu
Une opération de trempe à l'eau engendre des
grandes contraintes dans la pièce.
Cette opération est toujours suivie d'un revenu pour
éliminer les différentes contraintes induites dans la
pièce. Le Lower Mantle fonctionnera sous choc et avec une trempe seule,
sa durée ne sera que affectée, il est impérieux de
diminuer les contraintes pour lui permettre une durée de vie assez
acceptable par un revenu dans une gamme de température de 400, 500 et
600°C. Les résultats des essais mécaniques à ces
différentes températures sont donnés dans le tableau
VI.9.
a) Présentation des
résultats
|
400°C
|
500°C
|
600°C
|
HB
|
W (J)
|
S (cm2)
|
KCV (J/cm2)
|
HB
|
W (J)
|
S (cm2)
|
KCV (J/cm2)
|
HB
|
W (J)
|
S (cm2)
|
KCV (J/cm2)
|
Revenu à 30
minutes de maintien
|
333
|
5
|
0,8
|
6,25
|
308
|
19,5
|
0,8
|
24,4
|
283
|
21
|
0,8
|
26,3
|
337
|
5,6
|
0,8
|
7
|
312
|
20
|
0,8
|
25
|
288
|
21,5
|
0,8
|
26,9
|
320
|
5,2
|
0,8
|
6,5
|
300
|
18,4
|
0,8
|
23
|
284
|
19,8
|
0,8
|
24,8
|
Moyenne
|
330
|
|
|
6,6
|
307
|
|
|
24,13
|
285
|
|
|
25,8
|
Tableau VI.10 : résultat du revenu à
différentes températures pendant 30 minutes de
maintien
|
HB
|
K (J/cm2)
|
400°C
|
330
|
6,6
|
500°C
|
307
|
24,13
|
600°C
|
285
|
25,8
|
Tableau VI.11 : Valeurs moyennes de dureté
et résilience après revenu pendant 30 minutes
340
|
|
30
|
|
dureté
|
330 320 310 300 290 280 270 260
|
|
25 20 15 10 5 0
|
résilience
|
|
|
|
|
400°C 500°C 600°C
température
HB K (J/cm2)
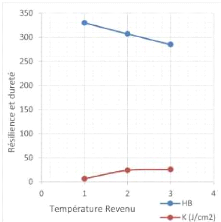
58
Graphique VI.4 : courbes de dureté et
résilience après revenu
b) 59
Interprétation
L'analyse du tableau VI.10 donnant les valeurs moyennes de
dureté et résilience après revenu à
différentes températures pendant 30 minutes de maintien montre
que l'élévation de la température de revenu nous rapproche
de plus en plus vers l'état d'équilibre ce qui a pour
conséquence la diminution de la dureté et l'augmentation de la
résilience rendant le métal ductile et tenace. Toutefois les
températures autour de 400°C ne sont pas à envisager puisque
les éléments d'addition font apparaitre une nouvelle
évolution dont la manifestation la plus sensible est l'augmentation de
la dureté ; c'est le phénomène de durcissement secondaire.
Ces effet est dû qu'à ces températures, la diffusion des
éléments carburigènes devient possible et la très
grande affinité de ces atomes pour le carbone entre la cémentite
disparait laissant place à des carbures plus stables et beaucoup plus
durs. Pour les aciers alliés lorsque l'on refroidit rapidement depuis la
température de revenu, la résilience conserve sa valeur normale,
en cas de refroidissement lent, la résilience finale à
température ambiante chute.
c) Micrographie
Nous pouvons constater sur les figures suivantes qui donnent
les structures de la nuance après revenu à 400 et 600°C.
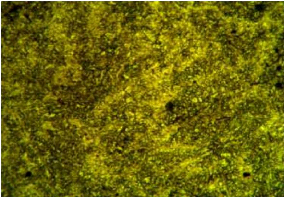
Figure VI.9 : Micrographie de l'A3SS après
revenu à 600°C
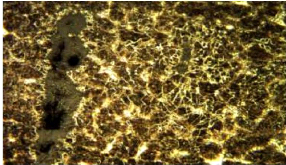
60
Figure VI.10 : Micrographie de l'A3SS après
revenu à 400°C
61
CONCLUSION
L'objet de ce travail a été de prolonger la
durée de vie d'un acier faiblement allié au nickel servant
à la fabrication du Lower Mantle par la proposition d'un mode de
traitement thermique de l'alliage qui satisferait au mieux aux exigences de
mise en forme et d'utilisation c'est-à-dire grande résistance
à l'usure par abrasion, ainsi qu'un bon compromis entre la dureté
et la résilience.
Pour arriver au bout de nos objectifs, nous avons
effectué une étude sur le traitement thermique à
appliquer, traitement conduisant à l'adoucissement de la pièce
tout en ressortissant les différentes propriétés
mécaniques concernant la dureté, la dureté et les
caractéristiques structurales. Vu que le matériau doit
fonctionner sous chocs répétés, il a été
aussi question de le conformer aux contions d'utilisation par ces
différentes caractéristiques.
A l'issu du travail, selon les résultats obtenus, nous
avons opté pour un traitement thermique de recuit tout en observant son
influence sur la résilience, la dureté et la microstructure. Les
conditions du traitement étaient la température
d'austénitisation, le temps de maintien et le milieu de refroidissement
qui ont eu un impact considérable sur les propriétés
mécaniques. Les résultats des propriétés
mécaniques après recuit ont conduit à première
approche à dire que le matériau présente à
940°C une dureté de 212 HB et 11,25 J/cm2 de
résilience contre 280 HB et 4,8 J/cm2 à l'état
brut de coulée et en deuxième approche le matériau donne
après trempe à l'eau une dureté de 380 HB et 19
J/cm2 par rapport aux autres milieux de refroidissement qui donnent
240 HB et 18,83 J/cm2 pour un refroidissement dans le four et 303 HB
et 12,54 J/cm2 pour refroidissement à l'air. Toutefois, la
pièce qui devra sous chocs, donc moins de contraintes internes, il lui a
fallu un revenu dont le résultat a conduit à opter pour une
température de 500°C et un temps de maintien de 30 minutes qui
donnent 307 HB de dureté et une résilience de 24,13 J/cm2 par
contre les températures de 400°C seront à éviter pour
le revenu puisque fragilisant la pièce par un phénomène de
durcissement secondaire.
Etant donné que le matériau présente les
caractéristiques attendues pour son adoucissement et sa mise aux
conditions d'utilisation, il revient de choisir les températures, le
temps de maintien et le milieu de refroidissement présentés
ci-haut tout
62
en espérant qu'il donne un bon comportement en service
avec une durée de vie relativement prolongée. Néanmoins,
des études poussées sur la composition de la nuance et les
combinaisons entre la température d'austénitisation, le milieu de
refroidissement et le temps de maintien conduisant à une meilleure
approche des différentes propriétés seraient à
envisager.
Toujours dit-on un travail humain n'est nullement parfait,
nous nous sommes efforcés à vous présenter le meilleur de
nos efforts. Ce travail n'étant qu'une étude scientifique parmi
tant d'autres, nous restons ouverts à vos questions, remarques et
suggestions qui contribueront à son amélioration.
63
BIBLIOGRAPHIE
a) Ouvrage
1. MURIEL HANTCHERLI, 2010 : Thèse de doctorat de
l'Ecole Nationale Supérieure des Mines : Influence
d'éléments d'addition sur les transformations de la martensite
revenue dans les aciers faiblement alliés.
2. André LEBOND, Notes de cours de métallurgie
destinées au personnel des ACP, GCM/ACP, 1989, inédit.
3. AIR FORMATION, Matériaux - les aciers,
édition 2007
4. Myriam Olivier, 2006, les métaux dans la
construction
5. Philipe Berger, 2012, Influence des éléments
d'addition
b) Articles et Publications
1. BENSAADA Said ; traitement thermique, classification et
désignation des aciers et fontes, presses universitaires, Tunisie
2. ARFAOUI Ali, CHAKER Med Amir ; Matériaux
Métalliques, ISET Kasserine, 2010
3. BOUTARFIF Fatma et GUELAI Noussaida, Comportements
mécaniques des aciers faiblement alliés avant et après
cémentation, 2016.
4.
Fr.m.wikiversy.org/wiki/Métallurgie
générale/les aciers_I_théorie
c) Mémoires
1. Paul KASONGO, 2018, Possibilité de substitution
d'une nuance d'acier fortement allié au manganèse A7 par un acier
de désignation GX 130MnNiCr13-3-2, Université de Likasi
2. MUTEBA KIBAMBE, 2017, Substitution d'un acier faiblement
allié au manganèse par un acier fortement allié au
manganèse et traitement thermique, Université de Likasi
d) Notes de cours
1. MWEPU WA NZOVU, traitement thermique, deuxième
grade métallurgie, Université de Likasi, Faculté
Polytechnique 2018, Inédit
2. MWEPU WA NZOVU, matériaux Métalliques,
premier grade métallurgie, Université de Likasi, Faculté
Polytechnique 2017, Inédit
3.
64
Guy NKULU W., métallographie, troisième graduat
métallurgie, Université de Likasi, Faculté Polytechnique
2016, Inédit
4. Richard NGENDA, Technique de fonderie, troisième
graduat métallurgie, Université de Likasi, Faculté
Polytechnique 2017, Inédit
5. Trésor BULEMBE, Métallurgie
Mécanique, troisième graduat métallurgie,
Université de Likasi, Faculté Polytechnique 2016,
Inédit
|