CHAPITRE II : DETERMINATION DU VOLUME A MINER ET
LA MAILLE DE FORAGE
II.1 NOTIONS GÉNÉRALES SUR LA
FRAGMENTATION
II.1.1 Définition
La fragmentation en exploitation minière est un terme
général qui décrit la taille Individuelle de chaque bloc
après le tir.
Cette notion révèle le détachement de la
roche du massif rocheux. Selon la nature de terrain, il y a des terrains que
les engins de chargements excavent sans difficultés même si ces
terrains n'ont pas été ébranlés au
préalable, d'autres terrains demandent un tir d'abattage c'est à
dire fragmentés avec une charge explosive. Deux opérations sont
indispensables pour réaliser la fragmentation en exploitation
minière à savoir : le forage et le minage.
II.1.2 Forage
C'est une opération au cours de laquelle un trou
cylindrique est exécuté jusqu'à une profondeur
donnée dans la roche. Plusieurs engins sont utilisés pour le
forage (la sondeuse, le perforateur, etc.) et se distinguent les unes des
autres tant par leur mode de forage que par le type d'énergie
utilisée.
Le choix d'un engin de forage peut être guidé par
:
> Le diamètre et la profondeur des trous de mine ;
> Le type et la constitution des roches in situ ;
> Le type d'énergie à utiliser.
Actuellement l'outil pneumatique est le plus utilisé,
à cause de ses multiples avantages qu'il présente : la
maniabilité, la souplesse, la puissance et la rapidité. Quant
à la mine à ciel ouvert de Kingamyambo, elle utilise pour le
forage des trous de mine, des sondeuses PANTERA 1500 avec marteau perforateur
hors du trou et des sondeuses ROC L8 avec marteau perforateur fond trou
utilisant de l'énergie hydropneumatique.
II.1.2.1 Méthodes de forages
Pour le choix de la méthode de forage convenant le mieux,
on doit tenir
compte des facteurs suivant :
> Topographie du lieu de travail ;
> Production demandée en tonnes/heure ou mètres
- cubes/heure ;
21
> Blocométrie ou granulométrie demandée
;
> Type de la roche (dure, tendre, compacte ou
fissurée) ;
> Coût par tonne commercialisée.
En plus, il faut évaluer le diamètre du trou, la
profondeur du trou, le type d'explosif à utilisé ainsi que
l'aptitude du foreur. Généralement trois méthodes de
forage sont à relever :
II.1.2.1.1 Forage au marteau perforateur hors du
trou
Le forage au marteau perforateur hors du trou utilise des
perforateurs pneumatiques et hydrauliques secondaires d'une glissière et
fonctionnant hors du trou. Le piston du marteau perforateur transmet son
énergie à la roche au travers d'une tige d'emmanchement, de
manchons d'accouplements, des tiges et du taillant.
L'énergie transmise permet un broyage facile de la
roche en petits sédiments de
forage.
Le moteur de rotation du marteau perforateur fait tourner le
taillant de façon à ce qu'il retrouve la roche non broyée
et en même temps écrase les sédiments de forage les plus
gros pour en réduire les dimensions. Puis, les sédiments sont
remontés par l'air comprimé jusqu'à leur évacuation
du trou.
Un système d'avance maintient une poussée
constante sur le perforateur, et donc à la surface de la roche, de
façon à utiliser le maximum d'énergie produite par le
marteau perforateur. L'ajout des tiges et manchons se traduit par une
dissipation d'énergie de foration.
En conséquence, la vitesse de foration
décroît avec la profondeur. La foration au marteau perforateur
hors du trou est généralement utilisée dans les roches
compactes ou partiellement fissurées.
II.1.2.1.2 Forage au marteau fond de trou
Le marteau fond de trou est, comme son nom l'indique,
installé à l'extrémité du train de tiges de forage.
Le piston du marteau est directement au contact du taillant. Puisque le piston
du marteau transmet directement son énergie au taillant, il n'y a pas
théoriquement dissipation de celle - ci dans le train de tiges alors que
la profondeur du trou augmente. Une tête de rotation hydraulique ou
pneumatique, située à l'extérieur du trou, fournit la
rotation. Les tiges de forage assurent le passage de l'air comprimé vers
le marteau fond de trou. C'est ce même air qui remonte les
sédiments de forage pour les évacuer du trou.
22
Bien qu'aucune énergie ne soit perdue lorsque la
profondeur du trou augmente, les frictions entre les tiges de forages et la
paroi du trou réduisent la vitesse du forage.
L'augmentation de la pression de l'air de fonctionnement
accroît l'énergie développée par le piston et donne
une pénétration plus rapide. La méthode de foration au
marteau fond de trou est normalement utilisée dans les roches
fissurées ou pour des trous dont la profondeur dépasse 20
mètres. Elle a généralement comme avantage de minimiser la
déviation du trou.
II.1.2.1.3 Forage Rotary
La foration rotary est généralement
utilisée pour les trous de grand diamètre ou pour le forage des
trous profonds. Cette foration utilise une pression très
élevée de poussée sur le tricône et une rotation de
celui - ci dont l'entraînement est situé en dehors du trou. Une
tête de rotation hydraulique, ou une tige d'entraînement fournit
cette rotation. La pression d'avance et la rotation du tricône broient et
écrasent la roche. L'air comprimé, la boue ou la mousse
transportent les sédiments en dehors du trou.
La relation entre pression d'avance et vitesse de rotation
détermine la vitesse de foration et le rendement :
> La roche tendre demande une pression d'avance réduite
et une vitesse de rotation plus rapide,
> La roche dure demande une pression d'avance importante et
une vitesse de rotation plus lente.
L'utilisation des tricônes de modèles
répondant très exactement aux conditions de travail maximalise la
vitesse de pénétration et leur durée de vie.
II.1.2.2 Constitution des roches & Types
(Classification des terrains) L'expérience de forage a
conduit à classifier les terrains les plus fréquemment
rencontrés en quatre catégories de dureté à savoir
: 2, 2D, 3 et 3D.
23
Tableau 2 : Types et Constitution des roches
CATEGORIES
|
COMPOSITIONS
|
CARACTERISTIQUES D'ABATTAGE
|
2
|
- Terres rouges, RGS
friables
- RDS très altèrés, RAT très
altèrés .
|
Tendre pas de minage.
|
2D
|
- CMN, RGS durs,
SDS croissant
- SDB altèrés, RAT altérée
compacte.
|
Ebranlement a faible charge explosive.
|
3D
|
- RSC altèrés, RAT
dolomitiques
- SDB, SDS, RSF
dolomitiques, RGS, CMN.
|
Tirs d'abattage avec charge
d'explosifs plus conséquente.
|
3D*
|
- RSC dolomitiques
- RGS dolomitiques très durs.
|
Fragmentation avec charge
explosive plus brisante.
|
II.1.2.3 Paramètres de forage a) Le
diamètre des trous de mine:
C'est l'un des paramètres de base à tout calcul
de fragmentation. Il dépend essentiellement de l'équipement de
forage dont on dispose. Les dimensions de la maille de forage augmentent avec
les diamètres du trou de mine. Dans la mine de kingamyambo, le
diamètre des trous de mine est de 101,6 mm.
b) Profondeur et surforage :
> La profondeur des trous de mine peut être
définie par :
Hg +
P = (1)
sina a
Avec Hg : La hauteur du gradin en mètre; á :
L'angle d'inclinaison des trous par rapport à la verticale; V :
L'écartement entre différentes rangées des trous;
24
a : Le coefficient dont le résultat de l'expérience
attesté pour les différentes catégories de terrains des
valeurs figurant dans le tableau ci-dessous :
Tableau 3: Les valeurs de a dans les différents
terrains
Terrains
|
D
|
D2
|
D3
|
D3*
|
A
|
8
|
V
|
3
|
2,5
|
> Le surforage (SF) :
Les trous de mine sont généralement forés
plus bas que le niveau désiré du gradin pour être certain
que les effets du tir donneront une fragmentation aux dimensions
désirées. La valeur du surforage (surprofondeur) est
généralement comprise entre 0,2 et 0,4 fois la banquette.
La longueur de la surprofondeur varie en fonction des
caractéristiques de la roche et de l'inclinaison.
SF = 10 d (2)
Avec d : diamètre des trous de mine
c) Maille de forage
La maille de forage est définie par l'expression suivante
:
Sm = 1T (3)
Avec Sm : La surface de la maille de forage en
mètre carré.
V : L'écartement entre différentes rangées
des trous de mine parallèles
au frond d'abattage, il est aussi appelé ligne de moindre
résistance;
E : La distance entre deux trous voisins de mine d'une même
rangée.
E = Kr x W~ ( 4)
Avec Wp : ligne de résistance au pied du gradin;
Kr : le coefficient de rapprochement de trou de mine.
Nous rencontrons trois sortes des mailles : La maille
carrée lorsque E = V (5)
25
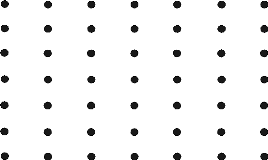
Figure 1 : Maille carrée
La maille rectangulaire lorsque E > V (6)
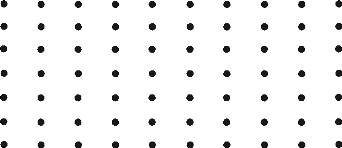
Figure 2 : Maille rectangulaire
La maille en quinconce : E = V sin 60 (7)
26
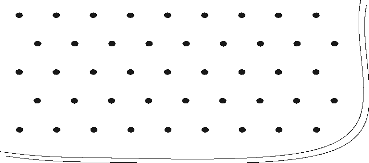
Figure 3 : Maille en quinconce
La ligne de résistance au pied du gradin en fonction du
diamètre d se traduit par les expressions empiriques suivantes :
1) Pour les roches fracturées faciles à
fragmenter
l4Çmax < 50 d
(8)
2) Dans les roches fracturées assez résistantes
lors de la fragmentation par le tir :
l4Çmax < 40 d
(9)
3) Dans les roches massives, tenaces et difficiles à
fragmenter par le tir
l4Çmax < 30 d
(10)
Dans les conditions répondant aux formules ci- dessus,
il est supposé qu'il ne restera de massifs résiduels à la
base du gradin qui nécessiteraient un minage secondaire.
En plus, la valeur minimale de Wp doit satisfaire la condition
de sécurité exprimée par l'expression suivante :
27
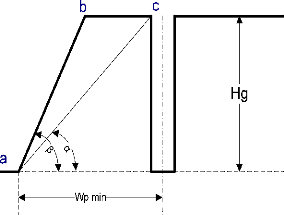
Figure 4 : La valeur minimale la ligne de moindre
résistance
Wp min = Hg 1230 4 + 56 56 = Hg (1230 7 - 1230 4
)
Wp min = Hg 1230 7 (11)
'56 : Prisme d'éboulement
La comparaison des valeurs Wp max et Wp min permet de choisir
l'angle d'inclinaison des trous de mine. Lorsque Wp min > Wp max, on recourt
à l'utilisation des trous inclinés.
Une fois le choix sur l'inclinaison est fait, on
détermine la ligne de résistance au pied du gradin compte tenu
des conditions géologiques, technologiques et techniques.
|