
Université François Rabelais de TOURS
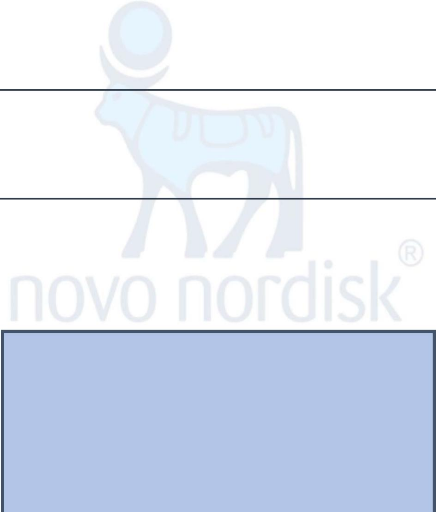
Démarche Lean Management et
respect des Bonnes Pratiques de
Fabrication
Cas d'une entreprise de production pharmaceutique
Novo Nordisk Production - Chartres (28)
Master 2 Management de la Qualité et des Projets Formation
par Apprentissage
Année universitaire 2018-2019 Mémoire
réalisé par Mlle Pauline BEZAULT
Mr Daniel LEROY
Responsable pédagogique: Directeur du Master 2
Mme Elodie DAHURON
Responsable d'entreprise: Ingénieure Assurance
Qualité
Institut d'Administration des Entreprises Mémoire
de fin d'études

« L'université n'entend donner aucune approbation
ni improbation aux opinions émises dans le mémoire : ces
émotions doivent être considérées comme propres
à leurs auteurs ».
I

Remerciements
Dans un premier temps, je tiens à remercier Novo
Nordisk Production, qui m'a permis d'effectuer cette année d'alternance
à Chartres, pour clôturer cette deuxième année de
Master en Management de la Qualité et des Projets.
Ma gratitude s'adresse tout particulièrement à
ma tutrice d'entreprise, Mme Elodie DAHURON, qui a su me faire confiance, m'a
confié des missions très intéressantes tout au long de
l'année, en rapport avec mon projet professionnel, mais aussi en
cohérence avec ma formation.
J'adresse mes remerciements à mon directeur de
mémoire Mr Daniel LEROY, également Directeur de la formation, qui
m'a suivi tout au long de cette année, et m'a guidé pour
rédiger ce mémoire.
Enfin, je remercie l'Université François
Rabelais de Tours, ainsi que l'Institut d'Administration des Entreprises, pour
m'avoir donné l'opportunité d'effectuer ce Master, et ainsi de
poursuivre mon projet professionnel.
II

III
Sommaire
Remerciements II
Sommaire III
Table des figures et tableaux IV
Glossaire V
Introduction 1
PARTIE 1 : Etat de l'art 3
I. Evolution du concept de la qualité et de sa
perception 3
II. Les réglementations en industrie pharmaceutique
8
III. Le Lean Management dans un environnement BPF 11
IV. L'intérêt économique d'une
stratégie Lean pour l'entreprise 17
V. Les travailleurs et le Lean 22
VI. Conclusion de l'état de l'art 25
PARTIE 2 : Enquête 27
I. Contexte de l'étude 27
II. Méthodologie de recherche 33
III. Questionnaire 35
IV. Observations 50
V. Conclusions de l'enquête 622
Conclusion 64
Apports et limites 66
Bibliographie Erreur ! Signet non
défini.
Table des matières Erreur ! Signet non
défini.
Résumé 73
Table des annexes 74

IV
Table des figures et tableaux
Figure 1 : Modèle de la performance en gestion de
projets 18
Figure 2 : Schéma représentant le modèle
de performance de Gibert (GILBERT & YALENIOS, 2017)
18
Figure 3: Bref historique du site de Chartres 27
Figure 4 : Evolution du site Novo Nordisk Chartres 28
Figure 5 : Représentation de la chaine de valeur de
Novo Nordisk. 29
Figure 6: Schéma du processus de production
simplifié 29
Figure 7 : Population source des personnes interrogées
36
Figure 8 : Poste occupé par les répondants 37
Figure 9 : Distribution des différentes formes
d'application du Lean (en %) 37
Figure 10 : Application du Lean en entreprise -
Répartition des réponses par population 38
Figure 11 : La place du Lean dans les BPF 39
Figure 12 : Comparaison des deux populations - Utiliser des
principes Lean facilite le respect des BPF
43
Figure 13 : Comparaison des deux populations - J'arrive
à respecter les BPF en utilisant le Lean 44
Figure 14 : Comparaison des deux populations - Je pense que le
Lean et les BPF sont contradictoires.
44
Figure 15 : Intérêt du Lean en industrie
pharmaceutique 45
Figure 16 : Principes Lean non appliqués en industrie
pharmaceutique 46
Figure 17 : Effets du Lean sur les travailleurs 47
Figure 18 : Processus simplifié de la
réalisation d'un APS 51
Figure 19 : Processus simplifié de la supervision des
APS par l'Assurance Qualité 51
Figure 20 : Processus détaillé de la supervision
des APS par l'Assurance Qualité, avec recherche du
point d'origine des problèmes. 52
Figure 21 : Graphique montrant l'évolution de la
conformité des indicateurs aux KPIs 57
Figure 22 : Représentation schématique du
principe Nécessaire et Suffisant 62
Tableau 1 : Comparaison Lean et BPF. Traduit de (GREEN &
O'ROURKE, 2006) 12
Tableau 2 : Prise de conscience des principaux aspects des BPF
par les industries pharmaceutiques.
Traduit de (JAIGANESH & SUDHAHAR, 2013) 15
Tableau 3: Postures de recherche, d'après Perret et
Girod-Séville (1999) et Giordano (2003) 34
Tableau 4 : La place du Lean dans les BPF- Score des
réponses pour tous les répondants 40
Tableau 5 : La place du Lean dans les BPF - Comparaison des
deux populations 41
Tableau 6 : Calcul des variances de scores obtenus aux
différentes questions, selon la population 42
Tableau 7 : Calcul du test de Fisher, selon la population
42
Tableau 8 : Tableau de statistiques sur les indicateurs de
délais et supervision des APS 56

Glossaire
ANSM Agence Nationale de Sûreté des
Médicaments et des produits de santé
A3 SPS Systematic Problem Solving - outil de
résolution de problème
API Activ Pharmaceutical Ingredient -
Ingrédient pharmaceutique actif
APS Aseptic Process Simulation - simulation de
procédé aseptique
AQ Assurance Qualité
Asepsie Absence de germes microbiens susceptibles de causer
une infection.
BPF Bonnes Pratiques de Fabrication
cLean current Lean - Lean actuel
FlexPen Stylo pré-rempli d'insuline
INRS Institut National de Recherche et de
Sécurité
ISO Internationale Standardisation Organisation -
Organisation internationale de
standardisation
Mediafill Technique de remplissage aseptique avec un milieu de
culture, dans la démarche de simulation de procédé
aseptique
PenFill Cartouche d'insuline de 1,5mL, assemblée dans les
FlexPen
R&D Recherche et Développement
TL Team Leader - Chef d'équipe
V

1
Introduction
Nous assistons, depuis les années 2000, à une
augmentation globale des coûts liés à la santé dans
le monde. En France par exemple, les dépenses liées à la
santé n'ont cessé d'augmenter : de 5.2% du PIB en 1970, ces
dépenses s'élèvent en 2000 à 9.6% du PIB
français et à 11.2% du PIB en 2018. Aux Etats-Unis, 16.9% du PIB
était consacré à la santé en 2018, contre 12.5% en
2000 et 6.2% en 19701.
Pour contrer ces hausses, une politique de
déremboursement et de diminution des prix des médicaments a
été menée en France, ce qui favorise les
médicaments à faible coût. Au contraire, aux Etats-Unis, le
prix de certains médicaments a explosé, ce qui pose des
problèmes aux patients pour avoir accès aux soins. En
réponse, l'industrie pharmaceutique a dû mener une
stratégie de réduction des coûts, afin de conserver sa
croissance et sa compétitivité d'une part, et de permettre un
meilleur accès aux soins à tous les patients d'autre part.
Les stratégies Lean, mises en place en premier lieu
dans les industries automobiles, puis aéronautiques, ont alors
gagnées le milieu pharmaceutique. « Lean » est un mot
anglais qui signifie, au sens littéral, maigre ou pauvre. En entreprise,
le Lean est une philosophie qui émane de l'entreprise japonaise Toyota,
et qui prend ses racines dans le Taylorisme et la recherche scientifique de la
performance dans le travail.
Ce concept a donné naissance notamment au Lean
Management, qui est, selon Michael Ballé, spécialiste du Lean
Management depuis plus de 25 ans, « une méthode de management
qui vise l'amélioration des performances de l'entreprise par le
développement de tous les employés » (BALLE, La
définition du Lean management, 2007).
Chez Novo Nordisk, une démarche Lean est menée
depuis plusieurs années, afin d'améliorer les performances de
l'entreprise. La place du Lean, dans cet environnement très
dépendant des réglementations, comme les Bonnes Pratiques de
Fabrication, peut être difficile. Cette étude a donc pour enjeu de
permettre une bonne mise en place du Lean Management à l'Assurance
1 Source : Issu de la base de données de
l'Organisation de Coopération et de Développement Economique
(OCDE). Consulté sur
https://stats.oecd.org/Index.aspx?DataSetCode=SHA
le 30/07/2019

Qualité, en identifiant les opportunités et les
limites d'une telle démarche, et en explorant l'intérêt
pour une entreprise, mais aussi pour un manager.
2

3
PARTIE 1 : Etat de l'art
I. Evolution du concept de la qualité et de sa
perception
La qualité, un concept général
Le mot qualité est utilisé dans
différents contextes. On parle ainsi de « qualité de
lumière » en photographie, ou encore de « qualité
morales » ou « qualités de coeur » pour un trait de
caractère. Le dictionnaire Larousse nous donne les définitions
suivantes : « Chacun des aspects positifs de quelque chose qui font
qu'il correspond au mieux à ce qu'on en attend ; Ce qui rend
quelque chose supérieur à la moyenne ». (Larousse,
2019)
L'Organisation Internationale de Normalisation
(International Standardization
Organization ou ISO), plus grand organisme de
normalisation au monde, caractérise quant à elle la
qualité comme étant « l'aptitude d'un ensemble de traits
distinctifs intrinsèques d'un objet à satisfaire des exigences
» (Editions ISO, 2015). La qualité d'un produit est donc sa
capacité à correspondre aux attentes de l'utilisateur, à
le satisfaire.
Dans le cas d'un produit pharmaceutique, on peut
définir deux types d'utilisateurs, ou clients : les médecins, qui
vont prescrire le produit, et les patients, qui vont l'utiliser. En marketing,
la satisfaction d'un client est « le sentiment de plaisir qui
naît de la comparaison entre des attentes préalables et une
expérience de consommation » (BAYNAST, LEVY, & LENDREVIE,
2017).
Les démarches qualités depuis les
révolutions industrielles
Après le XIXe siècle et la Révolution
Industrielle, le paysage économique est profondément
modifié. En effet, on passe d'une économie agraire et artisanale,
à une économie tournée vers l'industrie.
Avec le XXe siècle, ces changements économiques
conséquents aboutissent à l'apparition d'une consommation et une
production de masse. Cela entraîne bien sûr une modification
profonde de l'entreprise mais aussi du management dans son ensemble, et
notamment de la notion de qualité.
En effet, c'est dans les années 1880 que Frederik
Winslow Taylor met au point sa méthode d'organisation scientifique du
travail, qui prône une analyse rigoureuse des éléments de
travail,

4
en recherchant la « meilleure façon de faire
» comme référence. En 1908, Henry Ford reprend ces
principes et présente un nouveau modèle d'organisation du
travail, basé sur la simplification et la standardisation des
composants, afin de permettre une production en série.
C'est aussi à cette époque que des
découvertes capitales en médecine sont effectuées, en
particulier la pénicilline et l'insuline, respectivement en 1928 et
1921, qui commencent peu après à être produites en
quantité industrielle, et donnent le jour à l'industrie
pharmaceutique.
Dans la première partie du XXe siècle, la
démarche qualité est avant tout une méthode de
contrôle, destinée à améliorer la fiabilité
des produits fabriqués, et ainsi garantir le bon fonctionnement de
l'entreprise. Cette période est caractérisée par deux
phases, selon Caby et Jambart (CABY & JAMBART, 2000).
Apparue dès le début des années 1900, la
première phase est une phase d'inspection. En effet, la production de
masse induit le besoin d'établir des modèles de fabrication
standards, pour comparer tous les produits fabriqués à ce
standard. Le principal inconvénient de cette méthode est le
coût de contrôle rapidement prohibitif, avec l'augmentation des
quantités produites. L'année 1924 mène à la
deuxième phase, celle de la maîtrise statistique. Les
spécialistes de la qualité cherchent alors, en utilisant des
outils mathématiques et statistiques, à s'assurer de la
fiabilité d'un processus. Il n'y a plus alors de nécessité
de contrôler tous les produits créés, mais seulement des
échantillons, abaissant considérablement le coût de
contrôle.
Une démarche qualité pour rassurer les clients et
contrôler les produits
Walter A. Shewhart (1931), dans son livre Economic Control
of Quality of Manufactured Products, nous dit que « la
qualité maitrisée n'est pas la qualité constante »
(SHEWART, 1931). En effet, quand on mesure la fiabilité d'un
processus, la mesure obtenue variera, en fonction de différents
paramètres. Selon Shewhart, l'important n'est pas d'obtenir une mesure
qui ne variera pas, mais que cette mesure varie dans des limites acceptables.
Pour cela, il est nécessaire d'évaluer à quel moment il
n'est plus intéressant économiquement de produire : c'est une
limite à ne pas dépasser.

5
Edward Deming reprend les travaux de Shewhart, et
développe les outils statistiques d'un point de vue managérial,
dans son livre Out Of The Crisis. Il y développe les «
14 principes de fondamentaux du management » (DEMING, 1982).
L'Assurance Qualité a pris toute son importance pendant
la deuxième guerre mondiale. Il était alors vital de
contrôler la qualité de la production de masse pour l'industrie de
la défense. L'Assurance Qualité provient du mot anglais
insurance qui signifie inspirer confiance, rassurer. Elle a pour but
de garantir au client la qualité des produits proposés, et de
montrer l'aptitude d'une entreprise à acquérir et
pérenniser le niveau de qualité recherché.
Cette démarche a donc pour objectif de donner
l'assurance au client que l'on met en oeuvre des moyens pour proposer des
produits de qualité, afin de lui donner confiance. Le but est
d'atteindre et de maintenir les objectifs de qualité définis.
Le modèle de la Qualité totale
Après la 2e Guerre Mondiale, le Japon,
totalement détruit, cherche à relancer son économie. Les
dirigeants de Toyota mettent au point un système de gestion de
l'entreprise simple mais efficace, avec pour objectif de rattraper la
production américaine, qui était alors la première
puissance mondiale. Ils s'appuient sur cinq valeurs :
- Réduire les gaspillages
- Assurer une qualité optimale des produits, dès le
début de la production
- Produire à la demande des clients, pour réduire
les stocks
- Impliquer le personnel de production dans le diagnostic et la
résolution des problèmes
- Favoriser l'amélioration en continu, de façon
dynamique et en intégrant tous les acteurs
concernés
Cette méthode de management est aussi appelée
Total Production System, ou système de production totale.
L'objectif de cette méthode de management est d'impliquer la
totalité de l'entreprise dans la démarche qualité. Elle
permet une production plus efficace, et une implication des travailleurs, qui
sont directement investis dans la performance de l'entreprise.

6
En 1979, Philippe Crosby publie un livre intitulé
Quality is Free2. Il y définit le concept du zéro
défaut comme standard de la performance : le but d'une entreprise
étant de vendre ce qu'elle produit à des clients, il est
primordial de satisfaire ces clients. Pour cela, il lui faut livrer un produit
conforme aux attentes du client, à ce qu'on lui a promis. Une
dérogation à cette conformité est une entorse à la
parole donnée. L'entreprise perd alors de sa crédibilité
envers ses clients externes, mais aussi envers ses clients internes. Cela nuit
fortement à la capacité d'amélioration de l'entreprise,
car elle a perdu en considération, vis-à-vis des clients et des
employés.
L'AFNOR retient la définition suivante pour la
Qualité totale : « Mode de management d'un organisme,
centré sur la qualité, basé sur la participation de tous
ses membres et visant au succès à long terme par la satisfaction
du client et à des avantages pour les membres de l'organisation et pour
la société » (ERNOULT, 2010).
Cette définition place la satisfaction du client comme
objectif à long terme d'une démarche qualité, et comme
condition sine qua non du succès d'une entreprise. Le
management total de la qualité implique aussi la mise en valeur des
individus, à travers la valorisation du personnel ou la reconnaissance
des mérites. La qualité totale est ainsi une politique de
management, qui implique tous les membres de l'organisation, qu'ils soient
concernés directement ou non par le processus de production de
l'entreprise.
Dans les années 1990, le succès grandissant de
Toyota, attribué au Total Production System intrigue les
américains. Jim Womak, Daniel Ross et Daniel Jones publient en 1990 un
livre intitulé The Machine That Changed The World3,
où ils exposent le système de production japonais, comparé
aux méthodes de productions américaines ou européennes. Ce
livre va permettre la diffusion des méthodes japonaises en occident, qui
sera alors appelé Lean Manufacturing, littéralement
« production allégée ».
2 Source : Crosby P. (1979). Quality is Free :
the art of Making Quality Certain. New American Library (NewYork)
3 Source : Jones, D.T; Ross D. & Womak,J.P
(1991). The Machine that changed the World. Simon and Schuster (New York)

7
L'objectif de la méthode Lean est d'améliorer la
performance, en se basant sur les principes et techniques déjà
à la disposition des managers, et en suivant deux concepts principaux,
déclinés en principes de production :
- Le Juste-à-temps : défini comme «
La durée idéale de production d'un bien idéale, quand
elle correspond aux besoins du client » (BALLE & BEAUVALLET, Le
Management Lean, 2016)
o Nivelage de la production en fonction du volume et de la
période
o Le flux tiré : on produit pour honorer une commande et
pas avant
o Le changement rapide d'outils (SMED)
o L'intégration de la logistique
- L'Autonomation ou jidoka : défini par
« la responsabilisation des personnes chargées d'effectuer un
travail » (DELBALDO, 2009).
o La séparation de la machine et de l'Homme
o L'arrêt automatique de la chaine de production
dès le moindre défaut, sans devoir attendre une décision
de la hiérarchie
o Des détrompeurs pour éliminer les causes
d'erreur
o Analyser méthodiquement et systématiquement
les causes d'erreurs
Le Lean Management est une application des méthodes
Lean au management, c'est-à-dire au système d'organisation de
l'entreprise. Cette technique de gestion est décrite comme «
l'amélioration des performances de l'entreprise par le
développement de tous les employés » (BALLE, La
définition du Lean management, 2007). L'objectif est alors double :
permettre la satisfaction complète des clients, mais aussi le
succès et le développement de chacun des employés.
Pour résumer, la philosophie dérivant du Toyota
Production System, que l'on nomme « Lean », est un
état d'esprit appliqué au monde de l'entreprise, qui vise
à réduire toutes les formes de gaspillage, afin de créer
de la valeur pour les clients, internes ou externes. Il peut être
appliqué à la production, ou encore au management.

8
II. Les réglementations en industrie
pharmaceutique
Les réglementations applicables aux industries
pharmaceutiques sont très nombreuses, et souvent propres à chaque
pays. En Europe, les normes applicables sont les Good Manufacturing
Practicies for Pharmaceuticals qui sont très proches des Bonnes
Pratiques de Fabrication françaises. Aux Etats-Unis, ce sont les
réglementations éditées par la Food and Drugs
Administration (FDA). Au Japon, la réglementation à
respecter est la Pharmacopée japonaise. En France, nous pouvons lister
les Bonnes Pratiques de Fabrication, mais aussi la Pharmacopée ainsi que
le Code de Santé publique. Nous nous concentrerons sur les Bonnes
Pratiques de Fabrication dans cette étude.
L'ANSM
L'Agence Nationale de Sécurité du
Médicament et des produits de santé est un établissement
public, qui a pour mission principale d'évaluer les risques sanitaires
présentés par les médicaments et produits de santé,
destinés à l'être humain. Elle garantit, au travers de ses
missions de sécurité sanitaire, l'efficacité, la
qualité et le bon usage de tous les produits de santé
destinés à l'Homme.
Les missions de l'agence sont définies par une loi, et
quatre missions principales peuvent être dégagées :
- L'évaluation scientifique et
médico-économique
- Le contrôle en laboratoire et le contrôle de la
publicité
- L'inspection sur sites
- L'information des professionnels de santé et du
public
L'ANSM a aussi pour mission de contrôler la
communication publicitaire ou non faite autour des produits de santé
ainsi que de participer elle-même à des campagnes d'information
dans le domaine de la santé. Sa mission de contrôle de la
publicité l'amène à examiner le contenu des messages
promotionnels des firmes pharmaceutiques destinés aux professionnels ou
au grand public.

9
L'ANSM assure la gestion et l'évaluation des essais
cliniques portant sur les produits de santé mais aussi, depuis 2008, des
recherches biomédicales hors produits de santé. Elle s'assure en
particulier que ces recherches ne mettent pas en danger les personnes qui s'y
prêtent.
Un système d'Autorisation de Mise sur le Marché
(AMM) garantit que les médicaments commercialisés ont
été évalués par une autorité
compétente, assurant leur conformité avec les normes en vigueur
en matière de sécurité, d'efficacité et de
qualité. C'est l'ANSM qui accorde cette autorisation de mise sur le
marché au titulaire des droits d'exploitation du médicament.
Enfin, pour avoir le droit de produire et commercialiser des
médicaments, une entreprise pharmaceutique doit fournir une autorisation
d'ouverture, ainsi qu'un certificat de Bonnes Pratiques de Fabrication, qui
sont délivrés par l'ANSM.
Les Bonnes Pratiques de Fabrication
L'Organisation Mondiale de la Santé (OMS)
définit les Bonnes Pratiques de Fabrication (BPF) comme « un
des éléments de l'assurance de la qualité, garantissant
que les produits sont fabriqués et contrôlés de
façon uniforme et selon des normes de qualité adaptées
à leur utilisation et spécifiées dans l'autorisation de
mise sur le marché ». (Agence Nationale de Sûreté
des Médicaments, 2016)
Elles ont donc pour objectif de garantir que tous les
médicaments répondent aux normes de qualité et de
sécurité, ce qui leur permet de garantir une efficacité
constante. Les Bonnes Pratiques de Fabrication portent sur tous les aspects des
processus de production et de contrôle :
- Un processus de fabrication déterminé et des
étapes critiques validées ;
- Des locaux, un stockage et un transport adaptés ;
- Un personnel de production et de contrôle de la
qualité formé et qualifié ;
- Des installations suffisantes et qualifiées ;
- Des instructions et des modes opératoires écrits
approuvés ;
- La traçabilité complète d'un produit
grâce aux dossiers de lot ;
- Des systèmes d'enregistrement et d'examen des
réclamations ;
- Un système d'audit interne permettant la
vérification de la mise en application et le
monitoring des BPF.

10
Le principe directeur des BPF est que la qualité est
intégrée au produit tout au long de sa fabrication, et non pas
simplement testée dans un produit fini. Par conséquent,
l'assurance de la qualité signifie non seulement que le produit
répond aux spécifications définitives, mais aussi qu'il a
été obtenu par les mêmes méthodes et dans les
mêmes conditions chaque fois qu'un lot est fabriqué.
Il est important de noter que les Bonnes Pratiques de
Fabrication sont une réglementation avec obligation de résultat,
et non de moyens, même si les conditions de validation des processus sont
très clairement définies. Il s'agit donc d'obtenir les
résultats fixés par cette réglementation, en utilisant les
moyens qui semblent les plus pertinents pour l'entreprise. Cela peut entrainer
des interprétations multiples, et une multitude de possibilités
en termes d'outils ou de méthodes utilisées.
Département Assurance Qualité (AQ)
L'Agence Nationale de Sécurité des
Médicaments, nous donne la définition suivante, pour l'Assurance
Qualité : « L'ensemble de toutes les dispositions prises avec
les objectifs de s'assurer que toutes les substances actives sont de la
qualité requise pour leur usage prévu, et que des systèmes
qualité sont maintenus. » (Agence Nationale de
Sûreté des Médicaments, 2016)
La principale mission de ce service est d'assurer la bonne
conformité de la production vis-à-vis des directives externes,
comme les Bonnes Pratiques de Fabrication ou le Code de la Santé
Publique, et internes, comme les instructions (SOP : Standard Operating
Procedure ou Procédure d'Opération Standardisée).
Cela se traduit par le suivi et la validation des nouvelles instructions, des
modifications (CR : Change Request ou Requête de Changement), et
des déviations.
Ce service est indispensable dans le domaine pharmaceutique,
puisqu'il permet aussi d'assurer la libération des lots produits sur le
marché, et de conserver le droit de production auprès des
autorités telles que l'ANSM et la FDA (Food and Drugs
Administration).
Pour conclure, la principale réglementation en
industrie pharmaceutique est l'application des Bonnes Pratiques de Fabrication,
qui sont obligatoires pour produire des médicaments. Ces

11
bonnes pratiques sont éditées par l'Agence
Nationale de Sureté des Médicaments et des produits de
santé, qui s'assure aussi de leur respect et de leur bonne
application.
III. Le Lean Management dans un environnement BPF
Nous venons de constater que les Bonnes Pratiques de
Fabrication, réglementées par l'Agence Nationale du
Médicament et des produits de santé, sont une obligation en
industrie pharmaceutique. Cela permet de garantir la sécurité des
patients. Le bon suivi de ces BPF est obligatoire pour obtenir et maintenir
l'autorisation de produire et de vendre des produits pharmaceutiques.
On a aussi vu précédemment que le Lean est une
méthode, un état d'esprit visant à réduire les
gaspillages pour apporter de la valeur au client, et qui découle de
l'évolution de la notion de qualité en industrie. Nous allons
maintenant chercher à savoir s'il est possible d'utiliser les
méthodes Lean pour appliquer les BPF en industrie pharmaceutique.
Pour cela, nous allons répondre à la question de
recherche suivante :
Quelles sont les opportunités et limites d'une
démarche Lean Management dans un service d'Assurance Qualité,
qui doit respecter les Bonnes Pratiques de Fabrication ?
Comparaison du Lean et des BPF
En 2006, Anne Green et Dermot O'Rourke ont écrit un
article traitant de la place du Lean Manufacturing dans un
environnement BPF. Ils y proposent une comparaison du Lean et des BPF.
Pour eux, une comparaison stricte des BPF et du Lean peut
amener à penser que ce sont deux « familles en conflit
» (GREEN & O'ROURKE, 2006). En effet, on peut voir que les BPF et
le Lean ont des objectifs divergents, mais aussi des outils et méthodes
différents, ainsi qu'une approche de la production et de
l'amélioration distincts.
Ils proposent dans cet article une interprétation du
Lean, à travers une perspective BPF : « Le Lean Pharma consiste
essentiellement à déterminer comment modifier les
procédures opérationnelles en vigueur pour favoriser les
améliorations à court terme, tout en respectant

12
les normes techniques, afin de ne présenter aucun
risque pour le produit ». (GREEN & O'ROURKE, 2006).
BPF Lean
Objectif
|
Assurer l'efficacité du
produit
Prévenir les risques
|
Réduire les gaspillages Créer de la valeur
|
Focus
|
Développement du produit Production
Assurance Qualité
|
Chaine de valeur
|
Approche de la
production
|
La qualité avant tout
|
Qualité équilibrée à la
productivité
|
Amélioration
|
Régulée et prudente
|
Continue et simultanée
|
Principaux buts
|
Suivre les processus validés Eviter les
déviations
|
Réduire les coûts
Améliorer la qualité
Réduire les temps de cycle
Réduire les stocks
Améliorer la livraison des produits
|
Principaux outils
|
Système documentaire Personnel qualifié
Maîtrise de l'environnement Validation et qualification
Examen des réclamations Audits
|
Cartographie de la chaine de valeur
Amélioration Kaizen
Eviter les erreurs
Flux tirés
Flux simple
Entrainement, formation
Déploiement de la fonction qualité
|
Tableau 1 : Comparaison Lean et BPF. Traduit de (GREEN
& O'ROURKE, 2006)
Cet article propose donc 4 recommandations pour faciliter
l'usage du Lean dans une industrie pharmaceutique :
Recommandation 1 : « Travail standardisé »
Il faut standardiser les tâches, pour les
contrôler et les stabiliser, et ainsi pouvoir les améliorer. Il
est aussi plus facile d'identifier les variations ou les erreurs, en temps
réel. Le défi consiste à produire des instructions
conformes aux réglementations, mais aussi claires et
détaillées, pour éviter les différences de
pratiques selon les opérateurs par exemple, tout en favorisant
l'amélioration continue.
Recommandation 2 : « Des relations client-fournisseur
claires »

13
Il faut favoriser les échanges entre les clients et les
fournisseurs, mais aussi entre les départements de l'entreprise. Cela
favorise une meilleure production, et permet une prise de conscience de
l'impact de leurs problèmes sur le flux général. Il faut
aussi prioriser l'identification automatique des problèmes, par exemple
quand un processus prend plus de temps que le standard. Auparavant, il faut
mettre en place des temps de travail standardisés, et identifier les
responsabilités de chacun.
Recommandation 3 : « Un flux simple »
Un flux simple signifie sans boucle ou allers-retours, le flux
doit être unique et linéaire. Il doit aussi éviter les
zones de stock, ce qui ralenti le flux. Les BPF imposent une production en lot,
pour éviter la contamination croisée. Cependant, cela perturbe le
flux, et crée des stocks et des zones de ralentissement. Diminuer la
taille des lots produits permettrait d'être plus réactif face
à la demande des clients, et de bénéficier d'un effet
d'expérience pour les changements de lots.
Recommandation 4 : « Une amélioration basée
sur la science »
L'amélioration doit avoir lieu seulement quand le
processus est stabilisé : tenter d'améliorer un processus
comportant trop de variations ralentit souvent le processus ou réduit
l'effet de toute amélioration.
Les améliorations traditionnelles dans l'environnement
BPF résultent d'une réaction à une déviation,
plutôt que de la nécessité de réduire les
variations. La peur du changement et les systèmes de contrôle
actuels rendent l'amélioration continue très difficile. Selon les
auteurs, il serait intéressant de s'appuyer sur une approche
fondée sur les risques pour mettre en place cette amélioration
continue.
Ces conseils révèlent que les principes Lean
doivent être adaptés, pour faciliter le respect des Bonnes
Pratiques de Fabrication, et éviter les contresens. Ainsi, les
procédures de travail doivent à la fois être suffisamment
détaillées pour correspondre aux réglementations, et
éviter les différences entre opérateur, tout en
étant assez souples et adaptables, pour favoriser l'amélioration
continue.

14
Enfin, l'approche par les risques pour l'amélioration
continue permettrait de favoriser la stabilité des processus. Il ne
s'agirait plus de réagir à une non-conformité, mais de
l'anticiper et d'éviter qu'elle puisse se produire.
Suivre ces quatre règles permettrait d'appliquer les
principes Lean tout en respectant les Bonnes Pratiques de Fabrication,
obligatoires pour la production de médicaments par une industrie
pharmaceutique. Ces règles fixent donc les enjeux concernant l'adoption
et la mise en oeuvre d'une stratégie Lean au sein des entreprises
pharmaceutiques.
Principes de Lean Management cachés dans les BPF
Nous venons de voir que le Lean est compatible avec les BPF,
à condition d'appliquer certaines règles, pour adapter
l'environnement BPF à la philosophie Lean. Pour cela, Greene et O'Rourke
les ont comparés l'un à l'autre. Jaganesh et Sudhahar proposent
une autre méthodologie, en superposant les BPF et le Lean pour essayer
de trouver des similitudes et des synergies.
Dans leur étude parue en 2013, ils proposent un tableau,
qui regroupe deux questionnements :
- Les industries pharmaceutiques ont-elles conscience des
différents objectifs BPF ? - L'aspect Lean, qui peut être
relié à l'objectif BPF, est-il reconnu ?
Ce tableau nous renseigne sur deux choses : le taux de prise
de conscience des objectifs BPF par les industries pharmaceutiques d'une part,
et le lien éventuel des aspects Lean avec ces objectifs d'autre part.
Certains objectifs BPF ayant un but Lean similaire ont été
regroupés.
La première colonne reprend les objectifs
découlant des BPF. La deuxième colonne nous renseigne sur le taux
de reconnaissance de ce principe en tant qu'exigence des BPF. Par exemple,
« assurer une bonne efficacité du produit » est
identifiée par tous les répondants comme étant une
exigence des BPF. Au contraire, seulement 24% sont conscient que «
minimiser les stocks » est une exigence des BPF.
Les troisième et quatrième colonne rapprochent
les principes Lean des objectifs BPF, car l'application de ces principes
permettrait de respecter les objectifs BPF correspondants, de façon
directe ou indirecte.

15
Principe Lean caché
Objectif BPF
|
Prise de
conscience
|
Aspect Lean
|
Lien avec les BPF ?
|
Assurer une bonne efficacité du
produit
|
100%
|
Réduire les gaspillages Créer de la valeur
|
Direct
|
Eviter les dangers pour le patient
|
100%
|
Direct
|
Développement du produit Robustesse du
processus
Production régulée
et prudente
|
77%
|
Chaine de valeur
Qualité équilibrée avec la
productivité
|
Direct
|
Capacité de production
|
67%
|
Direct
|
Assurance Qualité Réduire les
réclamations Empêcher les déviations Réduire les
erreurs Processus validé
|
48%
|
Réduire les coûts Améliorer la qualité
Réduire les temps de cycle
Réduire les temps de livraison
|
Direct
|
Contrôle qualité Qualité avant
tout
|
55%
|
Améliorer la qualité
|
Direct
|
Minimiser les stocks
|
24%
|
Réduire les temps de cycle
|
Direct
|
Minimiser les erreurs
Gestion documentaire et formation du personnel
Validation et qualification
|
35%
|
Flux simple
Ne pas permettre les erreurs
Déploiement de la fonction qualité
|
Impact indirect
|
Stabilité du produit
|
64%
|
Créer de la valeur
|
Impact indirect
|
Tableau 2 : Prise de conscience des principaux aspects
des BPF par les industries pharmaceutiques. Traduit de (JAIGANESH &
SUDHAHAR, 2013)
Nous pouvons noter tout d'abord que certains principes BPF
sont peu reconnus par les industries pharmaceutiques. C'est le cas de la
réduction des stocks, car 24% des personnes interrogées le
reconnaissent en tant que principe BPF, ainsi que le groupe «
Minimiser les erreurs », « Gestion documentaire et
formation du personnel », et « Validation et qualification
», avec 35% des répondants.
Au contraire, certains objectifs BPF sont très
clairement identifiés, avec 100% des répondants. C'est le cas des
objectifs « Assurer une bonne efficacité du produit »
et « Eviter les risques pour le patient ».

16
Deuxièmement, nous pouvons remarquer que la plupart des
aspects Lean sont reliés aux objectifs BPF. Les auteurs identifient ces
aspects Lean comme étant « cachés derrière des
aspects BPF » (JAIGANESH & SUDHAHAR, 2013). Cependant, certains
aspects Lean n'ont qu'un impact indirect sur le respect des BPF, c'est le cas
des aspects « Flux simple », « Ne pas permettre les
erreurs », « Déploiement de la fonction
qualité » et « Créer de la valeur ».
Cet impact est cependant bien présent, même s'il ne peut pas
permettre de répondre aux principes BPF directement. Ils facilitent le
respect des BPF.
On peut penser que le Lean et les BPF sont liés, mais
que ce lien est indirect : les entreprises pharmaceutiques se concentrent sur
le respect des BPF, car c'est une condition obligatoire pour pouvoir produire
et vendre des médicaments. Elles mettent en place les principes Lean qui
y sont associés de façon indirecte.
Nous pouvons donc conclure que certains aspects Lean ne sont
pas seulement compatibles avec les objectifs BPF, mais peuvent être
confondus, et ont un objectif commun. D'autres n'ont qu'un impact indirect,
même s'ils favorisent le respect des BPF.
La Qualité au centre de la démarche de Lean
Management
Nous avons vu que la qualité du produit fabriqué
est primordiale pour une industrie pharmaceutique. Les Bonnes Pratiques de
Fabrication ont été mises en place pour garantir cette
qualité, en toutes circonstances.
Lorsqu'une stratégie Lean est mise en place sans
l'appui d'un système qualité, cette stratégie pourra avoir
des difficultés à pérenniser les bonnes pratiques. En
effet, lorsque cette démarche d'amélioration est menée par
des consultants ou des experts externes seulement, il y a un risque que «
l'ensemble de la démarche Lean peine à survivre au
départ des équipes » (BELLAÏCHE, BOUVARD, &
HARIVEL, 2015)
De même, lorsqu'une démarche qualité est
mise en place dans une entreprise sans stratégie Lean, cela aboutit
à « un système lourd et complexe, avec une
rentabilité compliquée à démontrer »
(BELLAÏCHE, BOUVARD, & HARIVEL, 2015). Cette vérité est
d'autant plus vraie dans les industries pharmaceutiques, qui doivent prouver
dès leur construction la sûreté des produits, et qui sont
soumises à de nombreux audits.

17
Les démarches Lean et le système de management
de la qualité sont complémentaires : un système de
management de la qualité apporte la stabilité et la
longévité à une démarche Lean souvent menée
en mode projet. A l'inverse, les stratégies Lean permettent une
meilleure agilité, une capacité d'adaptation et une culture
d'efficience à la Qualité.
Pour conclure, ces deux modes de fonctionnement sont
complémentaires, mais ils apparaissent aussi comme indissociable pour
une performance à long terme. Une stratégie Lean a donc un
intérêt particulier pour un service d'Assurance Qualité,
qui a pour but de faire appliquer ce système qualité, et de
veiller à son respect.
Après avoir détaillé
l'intérêt réglementaire à l'application du Lean en
industrie pharmaceutique, nous pouvons maintenant nous demander quels sont les
intérêts économiques d'une telle démarche, pour une
entreprise.
IV. L'intérêt économique d'une
stratégie Lean pour l'entreprise
Pour se protéger des crises financières, qui
affectent leur stabilité, toutes les entreprises cherchent à
améliorer leurs performances, afin de maximiser les profits et minimiser
les pertes. C'est particulièrement vrai depuis les années 2000,
avec la volonté des gouvernements de diminuer les dépenses de
santé.
Nous allons tout d'abord définir la performance de
façon générale. Ensuite, nous étudieront comment le
Lean peut influencer cette performance, à travers la chasse aux
gaspillages.
Qu'est-ce que la performance?
Nous pouvons décrire la performance grâce
à deux outils. Le premier est couramment utilisé dans le domaine
de la gestion de projet. La performance peut être décrite à
l'aide d'un triangle, dont les trois sommets sont une bonne qualité, un
coût maitrisé et des délais respectés :

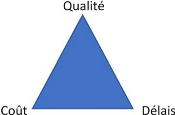
18
Figure 1 : Modèle de la performance en gestion de
projets
L'évaluation de la performance se fait alors en
analysant l'équilibre entre ces trois dimensions. Cet équilibre
doit correspondre aux besoins du client, et cela influencera sa
satisfaction.
Le deuxième est le modèle de performance de
Gilbert, qui décrit la performance comme « Un équilibre
entre les objectifs visés, les moyens matériels et
immatériels pour les réaliser, et les résultats obtenus
» (GILBERT & YALENIOS, 2017). On peut alors préciser trois
axes d'évaluation de la performance :
- La pertinence, qui est définie par le rapport entre
les objectifs initiaux et les ressources acquises pour les atteindre.
- L'efficience, qui est le rapport entre les résultats
obtenus et les ressources utilisées - L'efficacité, qui est le
rapport entre les résultats obtenus et les objectifs initiaux.
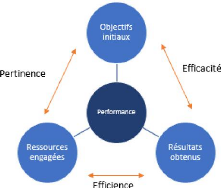
Figure 2 : Schéma représentant le
modèle de performance de Gibert (GILBERT & YALENIOS,
2017)

19
On peut développer la performance d'une organisation en
agissant sur ces trois axes. On cherchera alors à optimiser les
méthodes d'acquisition des ressources pour n'obtenir que ce qui est
nécessaire (pertinence), ou bien améliorer les méthodes de
production des résultats afin de diminuer la consommation des ressources
(efficience) ou encore fixer des objectifs au en tenant compte des
capacités réelles de l'organisation (efficacité).
Ces deux modèles peuvent être appliqués
à un service d'Assurance Qualité, qui agit alors comme une
organisation à l'intérieur de l'entreprise, en étant
à la fois un fournisseur de services, mais aussi un client,
vis-à-vis des autres départements de l'entreprise.
Les gaspillages nuisent à la performance
Nous avons vu précédemment cinq valeurs
appliquées par les japonais sur l'usine Toyota, pour redresser la
performance de l'entreprise :
- Réduire les gaspillages
- Assurer une qualité optimale des produits, dès le
début de la production
- Produire à la demande des clients, pour réduire
les stocks
- Impliquer le personnel de production dans le diagnostic et la
résolution des problèmes
- Favoriser l'amélioration en continu, de façon
dynamique et en intégrant tous les acteurs
concernés
Nous allons voir que la réduction des gaspillages
facilite l'adoption des quatre autres valeurs. Les gaspillages nuisent à
la performance, car ils ajoutent un coût supplémentaire et non
essentiel au cout de fabrication d'un produit. Michael BALLE et Godefroy
BEAUVALLET définissent dans leur ouvrage Le Management Lean
(2016) la marge d'une entreprise. C'est un facteur de rentabilité,
qui représente la différence entre le prix, c'est-à-dire
ce que le client donne pour un produit, et les couts engagés par
l'entreprise pour ce produit :
Marge = Prix - Coût
Selon ces deux auteurs, « toute activité
industrielle a un coût inévitable, auquel s'ajoute un
surcoût évitable : le coût de gaspillage (BALLE &
BEAUVALLET, Le Management Lean, 2016). On peut donc écrire :

20
Marge = Prix -- (Coût inévitable +
surcoût évitable)
En diminuant le surcout évitable, on diminue le
coût global de production, et on augmente donc la marge
engendrée.
Dans la philosophie Lean, le gaspillage est défini
comme « le coût de la non-valeur ajoutée » (
(BALLE & BEAUVALLET, Le Management Lean, 2016). Cela nous amène
à définir le terme de valeur ajoutée, qui peut être
traduit par « la valeur que le client est en droit d'attendre d'un
produit ou service, qui correspond à la satisfaction d'un besoin
» (DEMETRESCOUX, 2017).
Nous retrouvons ici la satisfaction du client, qui est au
coeur d'une démarche qualité. Le gaspillage serait alors
l'utilisation de ressources pour produire un produit ou un service, mais qui
n'ajouterait pas de valeur au produit, du point de vue du client.
Taiichi Ôhno, ingénieur chez Toyota, est le
premier à avoir étudié en détail cette non-valeur
ajoutée. Il montre dans son livre Toyota Production
System4 que la vraie valeur du travail ne représente
qu'une partie du temps des opérateurs, le reste pouvant être
qualifié de gaspillage. Il a ainsi détaillé sept
catégories de gaspillages, qu'il appelle Mudas (déchets
en japonais). Ils peuvent être rencontrés dans tous les domaines,
comme les zones de production ou les espaces de bureaux.
- Surproduction : produire plus que le besoin, ou bien
trop tôt par rapport au besoin. C'est le plus important des types de
gaspillages, car il peut entrainer d'autres types de gaspillages, comme les
stocks.
- Attente : toute ressource (machine, personnel,
matière) à l'arrêt, en attente. Cela entraine des stocks,
mais peut aussi altérer la ressource (péremption de
matière, désengagement du personnel)
- Transport : tout déplacement de ressource
(matériel, personnes, information), qui n'est pas nécessaire
à la production.
4 Source : Source : Taiichi Ôhno, Toyota
Production System : beyond large-scale production, Productivity Press,
(1988)

21
- Stocks : accumulation de plus de matière que
le minimum raisonnable pour la production. Cela engendre un cout très
important, car un stock nécessite de la place qui n'est plus disponible
pour la production, mais il faut aussi garantir de bonnes conditions pour
éviter d'altérer la matière. Enfin, d'un point de vue
comptable, les produits stockés sont une perte, car ils ont
consommé de la ressource, nais n'ont pas encore été
valorisés.
- Mouvement : tout mouvement superflu, qui est
dangereux ou pénible pour le personnel. - Défaut : toute
perte entrainée par une activité qui ne correspond pas à
l'exigence. Cela
concerne aussi les activités qui ne sont pas «
bonnes du premier coup », et qui nécessitent
une correction, ne réparation ou la mise au rebut de la
production.
- Processus excessif (ou sur-qualité) :
processus qui comporte des actions superflues, ou excessivement complexe. Cela
peut être la source d'erreurs, et donc paradoxalement, de
défauts.
Un huitième gaspillage a été
rajouté ultérieurement, et concerne une mauvaise utilisation du
potentiel humain des collaborateurs, par exemple, en ignorant le potentiel des
opérateurs dans les activités d'amélioration continue, qui
sont pourtant au contact de l'outil de production et ses dysfonctionnements.
Ces gaspillages peuvent être engendrés par deux
autres formes de gâchis, qui en sont donc des causes plus profondes. Le
premier est appelé Mura, ou variabilité et le
deuxième Muri, l'excès.
La variabilité et l'excès, des causes de
gaspillages
Le mot Mura désigne en japonais ce qui est
irrégulier, variable ou aléatoire. En pratique, cela se traduit
par des pics d'activités en fin de période, une
répartition inégale de la charge de travail, un manque de
standards conduisant à la variabilité des résultats, mais
aussi des pannes, l'absentéisme, ou encore des ruptures
d'approvisionnement.
Tout cela conduit à produire des gaspillages, qui ont
pour rôle de prévenir ces évènements
aléatoires. On peut penser aux stocks de matière première
ou d'en-cours, pour pallier des ruptures de la chaine de production, ou encore
à l'attente engendrée si ces stocks ne sont pas suffisants. Des
défauts sont aussi engendrés par la variabilité des
processus, qui ne sont alors plus conformes aux exigences.

22
Le mot Muri désigne tout ce qui est excessif
dans une organisation. Cela peut être l'achat d'un trop grand nombre de
machines pour les besoins de la production, une sur-utilisation d'un
équipement, ou bien la fixation de délais excessivement courts,
une surcharge de travail ou de pression sur les employés. Cela peut
entrainer des pannes, qui provoquent des attentes sur la chaine de production,
mais aussi de la fatigue et du stress pour le personnel.
Pour conclure, nous avons vu que l'ensemble des outils Lean
ont pour but de réduire ces gaspillages, en préservant les
ressources utilisées à mauvais escient, et en améliorant
les processus de production, ce qui permet d'augmenter la productivité
d'une entreprise.
Cependant, les Hommes sont au coeur du travail, et de la
performance d'une entreprise. En effet ils dirigent l'entreprise, prennent des
décisions et contrôlent l'outil de production. Quelle est leur
place dans une démarche Lean, et quels sont les apports d'une telle
démarche pour le management ?
V. Les travailleurs et le Lean
Nous avons vu que l'amélioration des performances d'une
entreprise est possible en faisant évoluer trois variables :
l'acquisition des ressources, la fixation des objectifs et la production des
résultats. Ces trois variables sont contrôlées par l'Homme.
Ils sont le socle du travail, et contrôlent l'outil de production, de
l'opérateur au directeur. Nous allons maintenant étudier la place
de l'Homme dans une démarche de Lean Management.
L'importance du développement humain
Dans une industrie, les outils de production ne sont que des
moyens censés simplifier le travail de l'homme et le rendre plus facile.
Selon Ballé et Beauvallet, « la formation est le socle
nécessaire au développement des personnes, et se fait au poste et
une personne à la fois ». (BALLE & BEAUVALLET, Le
Management Lean, 2016)
Le but est d'établir une organisation spécifique
de la formation, avec des standards, qui sont des références sur
la méthode de travail produisant le moins de non-valeur ajouté.
Les équipes sont coordonnées par un travailleur
expérimenté, qui fait appliquer les standards, les règles
de sécurité, etc. ... Les agents les plus
expérimentés dispensent les formations, qui ont pour but de

23
« développer la confiance que chacun a en son
jugement et dans chaque action de son travail » (BALLE &
BEAUVALLET, Le Management Lean, 2016).
La pratique régulière de la formation permet le
« développement des collaborateurs, dont la
finalité est d'accroitre leur autonomie » (BALLE &
BEAUVALLET, Le Management Lean, 2016). Cette autonomie est une source de
satisfaction au travail. Elle permet un meilleur engagement des
salariés, et augmente leurs compétences pour la résolution
des problèmes : l'amélioration continue est mieux
gérée dans les situations de crise, qui ne sont pas
décrites dans les standards mais nécessitent des prises de
décision efficaces. Les processus sont ainsi plus efficients, et la
performance de l'entreprise en est accrue.
Intérêt de la démarche pour un manager
Un manager a pour rôle d'accompagner une équipe,
pour l'amener à réaliser la stratégie fixée par
l'entreprise. Il est responsable de la productivité de ses
collaborateurs et des résultats finaux. L'application d'une
démarche Lean au sein de son équipe a plusieurs avantages.
Le premier point positif est qu'une stratégie Lean
permet de donner du sens au travail effectué. Les activités se
concentrent sur ce qui a réellement de la valeur pour le client, qui est
au centre de la démarche. Les activités qui n'ont pas de valeur
ajoutée sont améliorées ou optimisées.
De plus, la recherche de gaspillages dans les activités
réalisées permet aussi de réaliser des économies
d'énergie et de temps. Ces ressources économisées pourront
être utilisées pour d'autres activités plus valorisantes et
à forte valeur ajoutée, comme pour réaliser des projets
d'amélioration par exemple.
Enfin, les collaborateurs sont plus efficaces au quotidien. La
résolution des problèmes est facilitée par le gain
d'autonomie des individus. Cela est permis par la montée en
compétence des personnes, et la prise en compte des capacités et
des talents de chacun.
Effets sur la santé et la sécurité des
travailleurs (INRS, 2016)
La sécurité des travailleurs et leur
santé est au coeur de la démarche de Lean Management. En effet,
la stratégie Lean, visant à optimiser et simplifier les
tâches en supprimant le gaspillage,

24
ne prend pas seulement en compte l'environnement de travail et
l'outil de production, mais aussi l'homme et ses comportements.
L'ergonomie au poste de travail est importante dans
l'amélioration des processus. Des mouvements appropriés, et un
espace de travail pertinent et adapté permettent de réduire les
risques, d'une part pour le travailleur qui sera plus efficace et moins
fatigué, et d'autre part pour le produit, car cela réduit les
probabilités d'erreurs et donc de défauts.
De plus, l'amélioration de la performance, qui s'appuie
notamment sur huit gaspillages vus précédemment, doit aussi
être appliquée à l'homme. Par exemple, il est
préconisé d'étudier « les mouvements de pied, de
main et des yeux. Il faut voir les gestes répétitifs,
les efforts musculaires, les postures contraignantes, les surcharges cognitives
» (BALLE & BEAUVALLET, Le Management Lean, 2016).
L'implication de la hiérarchie dans l'ergonomie au
poste de travail des salariés a un autre effet : « l'ergonomie
est un excellent sujet pour déclencher l'implication » (BALLE
& BEAUVALLET, Le Management Lean, 2016). En s'intéressant au travail
des personnes, et à leur bien-être physique, la hiérarchie
montre aux salariés qu'ils ont de la valeur pour l'entreprise, et qu'ils
ne sont pas qu'un outil pour produire. Les chantiers d'ergonomie symbolisent
alors « le coeur du contrat social : les managers s'engagent à
améliorer les conditions d'emploi, et les employés contribuent
aux efforts de la société » (BALLE & BEAUVALLET, Le
Management Lean, 2016).
Cependant, l'INRS (Institut National de Recherche et de
Sécurité) propose un dossier sur les risques liés à
la mise en place d'une stratégie Lean dans une entreprise. Cette
étude (INRS, 2016) apporte un regard critique sur ces démarches,
et mets en avant les différences de mises en oeuvre selon les
entreprises.
Le premier point abordé concerne les changements
organisationnels induits par la mise en place d'une démarche
d'amélioration Lean. L'INRS constate « un manque de formations
adéquates, et d'évaluation des impacts potentiels sur le
personnel » (INRS, 2016). Nous avons pourtant mis en lumière
l'impact de la formation sur l'implication des travailleurs dans le Lean, et
constaté l'importance du développement des compétences. Il
est donc important de ne pas

25
négliger la dynamique d'apprentissage d'une
stratégie Lean, pour ne pas faire du déploiement et du maintien
de la démarche une finalité, mais un moyen de s'améliorer
continuellement.
De plus, l'INRS estime que « considérer les
actions à éliminer sur le seul critère de la valeur
ajoutée, du point de vue du client peut conduire à supprimer des
éléments essentiels à leur santé et à la
performance globale de l'entreprise » (INRS, 2016). La difficulté
réside donc dans l'évaluation de la valeur ajoutée
supposée des actions, pour le client. Dans le cas où un service
interne d'une entreprise peut être considérée comme une
organisation à part entière, on pourra prendre en compte le
client final, c'est-à-dire celui qui utilisera le produit ou qui
bénéficiera du service, mais aussi les clients
intermédiaires : le personnel de l'entreprise qui interagit ou est
impacté par un processus, ou bien une entreprise intermédiaire.
La valeur ajoutée d'une action doit alors être
évaluée en fonction de tous ces acteurs.
Pour conclure, nous avons pu voir que la place des
travailleurs dans le Lean est centrale. Le développement humain est une
condition nécessaire pour la viabilité des démarches
d'amélioration continue, mais aussi un moyen d'améliorer la
performance de l'entreprise. Il est aussi indispensable d'accompagner les
travailleurs dans le changement qu'implique une démarche Lean. Enfin, la
valeur ajoutée ne doit pas seulement être définie en
fonction du client final, mais aussi en fonction des intermédiaires.
VI. Conclusion de l'état de l'art
Tout d'abord, nous avons étudié
l'évolution du concept de la qualité en industrie, depuis les
révolutions industrielles au XIXe siècle, jusqu'à
l'apparition du Lean au Japon après la deuxième guerre mondiale,
qui est parvenu en occident sous l'appellation Qualité totale, dans les
années 70 et 80.
Ensuite, nous avons examiné l'importance des
réglementations, et plus précisément des Bonnes Pratiques
de Fabrication. Ce référentiel, édité par l'ANSM,
est une obligation en industrie pharmaceutique, pour pouvoir produire et vendre
des médicaments.
Alors, nous nous somme demandés si une démarche
de Lean Management est compatible avec le respect des Bonnes Pratiques de
Fabrication. La première question de recherche soulevée

26
concernait les opportunités et les limites d'une telle
démarche dans un service d`Assurance Qualité.
Premièrement, nous avons pu comprendre que les BPF et
le Lean sont compatibles et fonctionnent en synergie : le Lean apporte de
l'agilité et des capacités d'adaptation à un
système qualité, qui procure stabilité et
longévité aux démarches Lean. Il faut cependant adapter
l'environnement BPF à la philosophie Lean, et ajuster les principes Lean
aux obligations engendrées par le respect des BPF. Nous avons aussi vu
que la plupart des principes Lean sont retrouvés dans les BPF, et
peuvent avoir le même but.
Ensuite, nous avons étudié
l'intérêt économique du Lean Management, qui permet
d'améliorer les performances d'une entreprise. La stratégie Lean
vise à identifier et supprimer les sources de gaspillages, qui sont
consommateurs de ressources et n'apportent pas de valeur ajoutée au
produit.
Enfin, nous nous sommes intéressés à la
place du travailleur dans les stratégies Lean, et à son
intérêt managérial. Nous avons ainsi découvert
l'importance du développement humain dans cette philosophie Lean, et
avons expliqué les avantages procurés à un manager sur la
gestion d'une équipe. Enfin, nous avons étudié les effets
d'une mauvaise application de cette démarche sur la santé et la
sécurité des personnes.
Nous allons maintenant nous interroger sur la validité
des hypothèses soulevées pendant cet état de l'art, dans
une entreprise de production pharmaceutique comme Novo Nordisk. Pour cela, nous
allons tout d'abord présenter cette entreprise et définir le
contexte de l'étude, puis nous détaillerons la
méthodologie de recherche adoptée. Nous expliquerons ensuite les
résultats obtenus à travers cette enquête, et nous
tenterons de répondre à la question de recherche
soulevée.

27
PARTIE 2 : Enquête
I. Contexte de l'étude
1) Présentation de l'entreprise
Novo Nordisk est une entreprise de santé danoise. Elle
s'est spécialisée, depuis sa création en 1923, dans la
production d'insuline et de dispositifs d'injection. Aujourd'hui leader mondial
dans le traitement du diabète, le groupe occupe également une
place de premier plan dans le traitement de l'hémophilie et des
déficits en hormone de croissance.
Le groupe représente à ce jour plus de 43 000
employés à travers le monde et possède des filiales dans
80 pays, et leurs produits sont distribués dans plus de 170 pays. Il
totalise un chiffre d'affaire annuel à hauteur de 14,9 milliards
d'euros, et réinvestit en recherche et développement à
hauteur de 13% du CA. Il fournit plus de 50% de l'insuline mondiale,
utilisée par plus de 29 millions de personnes.
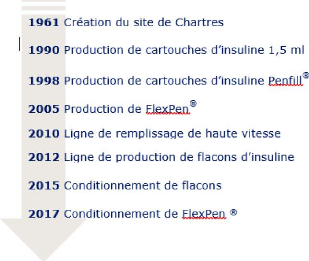
Figure 3: Bref historique du site de Chartres

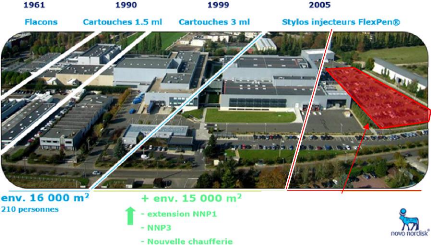
Extension FlexTouch
28
Figure 4 : Evolution du site Novo Nordisk
Chartres
Le diabète et l'insuline
Comme nous l'avons vu précédemment, Novo Nordisk
est une entreprise de production pharmaceutique spécialisée dans
la production d'insuline, à destination des humains. L'insuline est une
hormone, normalement sécrétée par des cellules
spécifiques du pancréas. Elle permet l'absorption du glucose dans
le sang par les cellules adipeuses et musculaires.
Chez les personnes diabétiques, le corps est incapable
de transporter le sucre du sang vers ces cellules, et cela entraine un
excès de sucre dans le sang. Les complications engendrées par le
diabète, qui est une maladie chronique, sont multiples et peuvent
être graves, affectant les yeux, les reins, les nerfs et les pieds. Cette
maladie favorise aussi les maladies cardiaques et l'hypertension
artérielle.
L'insuline produite par Novo Nordisk est une hormone de
synthèse. Comme les produits seront injectés dans les muscles des
patients, ils doivent être strictement stériles,
c'est-à-dire qu'ils ne doivent contenir aucun micro-organisme ou
particules. L'insuline étant une hormone sensible à la chaleur,
une stérilisation en fin de processus est impossible, car cela
détruirait ses propriétés. Le produit est formulé,
puis stérilise par filtration, et enfin rempli dans des

29
cartouches ou des flacons. Il est donc obligatoire d'assurer
la stérilité du produit depuis sa filtration jusqu'à la
fin du remplissage, où les contenants sont fermés.
L'organisation de Novo Nordisk

Figure 5 : Représentation de la chaine de valeur
de Novo Nordisk.
Novo Nordisk est organisé en plusieurs
départements. Le département « Product Supply (PS)
» (pour fourniture de produits) se concentre sur la fabrication de
produits pharmaceutiques, de la planification de l'approvisionnement à
la distribution aux patients.
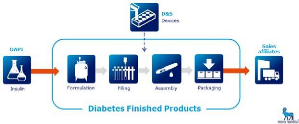
Figure 6: Schéma du processus de production
simplifié
Les matières premières vont être
fabriquées par le département « Diabetes API »
dont les sites sont principalement basés au Danemark. Elles sont ensuite
acheminées vers les sites de production de produits finis
diabétiques, comme celui de Chartres, afin de poursuivre les
étapes suivantes du processus de fabrication des médicaments.
Le premier process mis en oeuvre est le service Lavage et
Stérilisation, qui a pour objectif principal le lavage et la
stérilisation du matériel utile à la production.
Pendant le processus de formulation, l'insuline va tout
d'abord être préparée dans des cuves. Cette étape
permet la solubilisation des cristaux d'insuline provenant du Danemark afin
d'obtenir une formule liquide stable, de concentration suffisante, en fonction
du produit à formuler. Une fois cette étape effectuée,
l'ensemble préparé est stérilisé par filtration
stérilisante

30
à l'aide d'un filtre suffisamment fin pour ne pas
laisser passer les virus, bactéries ou autres particules.
L'étape suivante est celle du remplissage, où
les cuves de formulation vont être connectées aux lignes de
remplissage, via des filtres stérilisants. Ce processus permet le
remplissage aseptique de l'insuline stérile dans les cartouches ou
flacons. Le remplissage est une étape critique car le produit est
stérile et doit conserver ses propriétés, malgré la
manipulation humaine. Cela s'effectue sur des lignes automatisées, dans
une atmosphère strictement contrôlée afin de ne contenir
aucun micro-organisme ou poussière. Pour cela, le personnel de
production doit respecter un comportement aseptique très strict
Une fois remplies, les cartouches ou les flacons seront
inspectés par le process « Inspection », à l'aide
d'automates, et seront ensuite acheminés aux services suivants. Les
cartouches produites vont pouvoir être assemblées avec les 13
autres pièces composant un stylo insulinique appelé FlexPen
® et ainsi obtenir un stylo fonctionnel. Cette étape ne concerne
pas les flacons.
Et pour finir, les stylos et les flacons vont être
conditionnés et stockés en magasin. Les services Planification et
Chaine d'Approvisionnement géreront le transport des produits vers les
filiales.
2) Le Lean chez Novo Nordisk
Culture d'entreprise
Chez Novo Nordisk, la culture d'entreprise est très
centrée sur le Lean et l'amélioration des performances. Dix
valeurs essentielles permettent de résumer cette culture :
1. Nous créons de la valeur en centrant notre
activité sur les besoins du patient.
2. Nous nous fixons des objectifs ambitieux et aspirons à
l'excellence.
3. Nous sommes responsables de notre performance
financière, environnementale et sociale.
4. Nous innovons dans l'intérêt de nos
partenaires.
5. Nous construisons et entretenons de bonnes relations avec
nos principaux partenaires.
6. Nous traitons chacun avec respect.
7. Nous plaçons la performance individuelle et le
développement personnel au coeur de nos préoccupations.

8.
31
Nous proposons un environnement de travail sain et motivant.
9. Nous recherchons l'agilité et la simplicité
dans tout ce que nous entreprenons.
10. Nous ne transigeons jamais sur la qualité et
l'éthique professionnelle
Ces valeurs sont expliquées dès la
première journée sur le site, et font partie de la semaine
d'intégration. Elles sont affichées sur plusieurs salles de
production, et définissent également un comportement à
adopter au sein de l'entreprise, qui responsabilise au fait que les produits
sont pour des patients et non de simples clients.
Outils Lean appliqués chez Novo Nordisk
Résolution systématique des problèmes
Le SPS, ou Systematic Problem Solving
(résolution systématique des problèmes), aussi
appelé méthode 8D pour huit disciplines, est un outil sous forme
de tableau A3 qui est une manière systématique de gérer
les problèmes grâce à 8 étapes
complémentaires (Annexe 1) :
- Perception initiale du
problème : il faut décrire l'écart par
rapport à un objectif.
- Clarification du problème :
il est possible d'aller sur le terrain, poser des questions aux personnes
concernées pour mieux cerner le problème, prendre des photos,
prendre connaissance des standards et du mode opératoire, utiliser les
données disponibles et les mettre sous forme de graphique (Pareto,
graphique des tendances), établir la tendance et l'historique,
décomposer le problème en sous-problèmes, pour mieux le
clarifier
- Point d'apparition : on
remonte le processus à partir de l'endroit où le problème
a été observé.
- Actions provisoires : on
détermine les actions possibles pour maitriser et contenir rapidement le
problème avant d'en connaitre les causes racines.
- Causes et effets : on rappelle le
problème spécifique à traiter et son point d'apparition,
on invite les experts, et on réalise un brainstorming pour collecter
toutes les causes possibles. On définit ensuite les causes les plus
probables pour poursuivre les investigations.
- Investigations / causes :
Investigation sur les causes retenues à la suite du Brainstorming /
Ishikawa, on utilise les données retenues et on réalise des plans
de test. On définit précisément les conditions de test et
les résultats attendus. Ainsi cela permet

32
de déterminer la cause directe. Ensuite,
l'utilisation de la méthode « 5Pourquoi » permet d'aboutir
à la cause racine, qu'il faut traiter pour empêcher la
réapparition du problème.
- Actions définitives : on
détermine les actions correctives pour traiter la cause racine et
traiter les contributeurs identifiés pendant les investigations. On
contrôle l'efficacité de ces contremesures.
- Partage : on communique le document
en format A3 et les actions correctives afin de partager les connaissances
acquises et éviter l'apparition du problème sur d'autres
équipements, processus ou sites.
Performance Board (PB)
Le Performance Board (ou tableau de performances) est
un système de management visuel. Il consiste à détecter et
résoudre les problèmes le plus tôt possible avant qu'ils ne
deviennent plus complexes. Pour cela, on utilise des standards de performance
ou KPI (Key Performance Indicator, pour indicateur clé
de performance) pour mesurer les variations et les déviations.
Les tableaux de performance sont un élément
clé dans la façon de travailler chez Novo Nordisk. Ils expriment
le concept du management visuel selon lequel les problèmes doivent
être visibles le plus tôt possible.
Les Performance Board se font sous forme de réunions
quotidiennes de l'équipe. A la fin de la réunion, le responsable
du Board définit les priorités et les points de focalisation.
Cela permet de prendre des actions immédiates pour corriger le
problème, ou, le cas échéant, faire remonter les
problèmes détectés dans l'équipe jusqu'au niveau du
directeur du site, en moins d'une demi-journée. Ainsi, la succession des
Performance Boards permet une remontée rapide des décisions qui
doivent être prises à un niveau supérieur.
Service cLean
Un service dédié à l'application du Lean
dans l'entreprise, permet à chacun de bénéficier de
conseils et d'une aide pour appliquer les principes Lean au quotidien. Les
partenaires cLean (pour current Lean, Lean actuel) participent
à la résolution des problèmes en contribuant aux A3
notamment.

33
II. Méthodologie de recherche
Rappel de la problématique
En étudiant l'évolution du concept de la
qualité jusqu'à la stratégie Lean, puis en mettant en
lumière l'importance des Bonnes Pratiques de Fabrication au sein de
l'industrie pharmaceutique, nous avons pu soulever la question de recherche
suivante :
La démarche de Lean Management est-elle compatible avec
le respect des Bonnes Pratiques de Fabrication ?
Nous avons ensuite étudié le Lean Management
dans un environnement respectant les bonnes Pratiques de Fabrication, amenant
ainsi la question de recherche suivante :
Quelles sont les opportunités et limites d'une
démarche Lean Management dans un service d'Assurance Qualité, qui
doit respecter les Bonnes Pratiques de Fabrication ?
Grâce à la littérature, nous avons
proposé plusieurs hypothèses de réponse :
- Le Lean a tout d'abord un intérêt
réglementaire : les BPF et le Lean sont compatibles, à certaines
conditions. Des propositions sont émises pour pouvoir appliquer le Lean
dans un milieu respectant les BPF, fixant ainsi les enjeux du Lean dans
l'industrie pharmaceutique. Une adaptation de certains principes est toutefois
nécessaire.
- Le Lean a aussi un intérêt économique
pour les industries pharmaceutiques : il permet d'accroitre durablement la
performance de l'entreprise, en évitant les activités à
non-valeur ajoutée.
- Le Lean a enfin un intérêt humain et
managérial, car il permet le développement des personnes,
à travers l'autonomie et la prise en compte de la santé du
collaborateur.
Après avoir exposé la place du Lean dans
l'entreprise Novo Nordisk, nous allons tenter de valider ces
hypothèses.
Les différentes postures de recherche
Afin d'organiser les recherches sur le terrain, j'ai d'abord
choisi de comparer les différentes postures
épistémologiques afin de déterminer celle qui serait la
plus adaptée à ce projet.

34
D'après D. Leroy5, les postures de recherche,
adaptés de Perret et Girod-Séville (1999) et Giordano (2003),
peuvent être classifiés ainsi :
|
Positivisme
|
Interprétativisme
|
Constructivisme
|
Quelle est la
nature de la
connaissance ?
|
La réalité est une
donnée objective
indépendante des
sujets qui
l'observent
|
La réalité est
perçue/interprétée par des sujets
connaissants
|
La réalité est une
construction de sujets
connaissants qui
expérimentent le
monde
|
Comment la
connaissance est
engendrée ?
|
Indépendance :
Le chercheur n'agit
pas sur la réalité observée
|
Empathie :
Le chercheur interprète ce que les acteurs disent ou font,
qui eux-mêmes
interprètent l'objet de recherche
|
Interaction :
Le chercheur
coconstruit des
interprétations et/ou
des projets avec les acteurs
|
Quels sont la
valeur et le statut
de la connaissance ?
|
Expliquer, corroborer :
Fondé sur la
découverte de
régularités et de causalités
|
Comprendre :
Fondé sur la compréhension
empathique des représentations d'acteurs
|
Construire :
Fondé sur la
conception d'un projet
|
Tableau 3: Postures de recherche, d'après Perret
et Girod-Séville (1999) et Giordano (2003)
Dans le cadre de cette étude, j'ai choisi d'utiliser
les postures positivistes et interprétativistes, et donc de mener cette
recherche en deux étapes. La première étape utilisera la
posture positiviste, et consistera à l'élaboration puis
l'administration d'un questionnaire, pour identifier une corrélation
avec l'analyse théorique, menée en première partie. La
deuxième étape sera menée selon la posture
interprétativiste, et sera une analyse des différentes missions
d'amélioration Lean, exécutée durant cette année
d'alternance chez Novo Nordisk.
5 Source : Cours de Méthodologie de Recherche -
IAE de Tours, le 14 Novembre 2019.

35
III. Questionnaire
Objectifs et enjeux
L'objectif de cette première étape de recherche
est de valider ou non les hypothèses construites à partir de
l'Etat de l'Art, à l'aide d'un questionnaire. Il est destiné aux
professionnels, travaillant dans une entreprise pharmaceutique qui a mis en
place une démarche Lean et applique les Bonnes Pratiques de
Fabrication.
L'enjeu est d'apporter une réponse aux questions de
recherches, qui soit à la fois validée par l'Etat de l'Art, et
sur le terrain. Dans le cas où ces réponses seraient divergentes,
nous tenterons d'apporter une justification.
Ce questionnaire a été construit avec Google
Form, qui est un programme d'enquête de la suite bureautique de Google.
Cet outil a été choisi pour sa facilité d'utilisation et
de diffusion, et ses multiples possibilités pour la présentation
des questions. Il permet, entre autres, d'exporter les données
collectées sous forme d'une base de données.
Une fois construit, cette enquête a été
partagée au sein du service Assurance Qualité de Novo Nordisk,
mais aussi sur le réseau LinkedIn, pour obtenir des avis
extérieurs, et pouvoir établir des comparaisons. Le nombre de
réponses obtenues est de 29 au total. Les deux groupes de
répondants seront identifiés comme « Novo Nordisk » ou
« Extérieurs ».
Les données, recueillies via Google Forms, ont
été exportées sous la forme d'une base de données,
présentée en annexe (Annexe 2). Les deux
premières questions qui ont été posées ont pour but
de délimiter la population cible à des individus faisant partie
d'une entreprise respectant les BPF, et ayant mis en place une démarche
Lean.
Le traitement des données sera réalisé en
deux étapes. La première étape consistera à
étudier et interpréter les données recueillies pendant
cette enquête, et la deuxième étape consistera à
comparer les données recueillies lors de cette étude aux
données théoriques de l'état de l'art. Une étude de
l'échantillon sera menée dans un premier temps.
Nous étudierons quatre thématiques
différentes :

36
- L'application du Lean en entreprise
- La place du Lean au quotidien
- La performance et le Lean
- Le ressenti personnel à propos du Lean
Etude de l'échantillon interrogé
Nous allons tout d'abord étudier le profil des
répondants de ce questionnaire, à travers deux questions : la
population source, les postes occupés par les répondants.
Premièrement, nous pouvons voir que les deux groupes
sont plutôt équilibrés, malgré une plus grande
proportion de personnes travaillant chez Novo Nordisk (17 personnes sur 29).
Cela garantira un équilibre dans les réponses. De plus, la
comparaison entre les deux échantillons sera facilitée.
Population source des personnes
interrogées (en nombre de personnes)
Figure 7 : Population source des personnes
interrogées
Enfin, concernant les postes occupés, nous observons
une majorité d'ingénieur, pharmacien ou cadre non encadrant et de
technicien ou agent. L'échantillon est représentatif de la
distribution chez Novo Nordisk.

Poste occupé par les
répondants
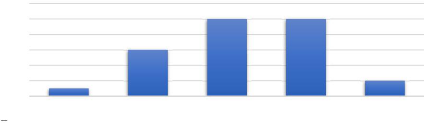
Cadre dirigeant Manager ou chef
d'équipe
Ingénieur, pharmacien, cadre non
encadrant
Technicien, agent Apprenti, stagiaire
Nombre de réponses
12
10 10
10
4
8
6
0
2
1
6
2
Type de poste
37
Figure 8 : Poste occupé par les
répondants
Nous allons maintenant analyser les réponses obtenues
à l'aide de ce questionnaire. Analyse des réponses
Application du Lean en entreprise
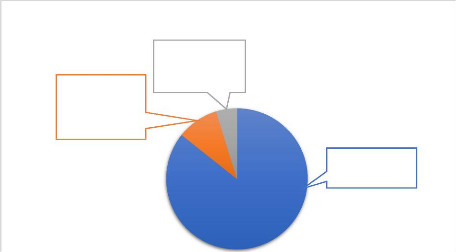
Distribution des différentes formes d'application
du Lean en entreprise (en pourcentage)
Le Lean est appliqué dans les
projets d'amélioration seulement 9%
Le Lean est un projet ou futur projet de mon
entreprise 5%
Le Lean est appliqué au quotidien
86%
Figure 9 : Distribution des différentes formes
d'application du Lean (en %)
Ce graphique nous permet de voir la distribution des
différentes formes d'application du Lean en entreprise. Nous pouvons
ainsi voir que la majorité des répondants appartiennent à
une entreprise où le Lean est appliqué au quotidien (86%).
Seulement 9% des répondants voient le

38
Lean appliqué dans des projets d'amélioration
seulement, et 5% des personnes considèrent le Lean comme un projet ou
futur projet de leur entreprise. Nous pouvons donc penser que le Lean est bien
intégré au quotidien.
Répartition des réponses par
population
18 16 14 12 10 8 6 4 2 0
|
|
|
|
|
|
7
|
|
|
|
|
|
4
|
|
1
|
|
|
Le Lean est appliqué au Le Lean est appliqué dans
Le Lean est un projet ou
quotidien les projets d'amélioration futur projet de
mon
seulement entreprise
ext
|
Nombre de réponses
17
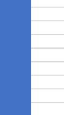
Le Lean est appliqué au quotidien
Novo
Figure 10 : Application du Lean en entreprise -
Répartition des réponses par population
En analysant les données, nous pouvons voir que seuls
les répondants extérieurs ont déclaré que le Lean
n'est pas appliqué au quotidien dans leur entreprise, mais sous forme
d'un projet d'amélioration (4 répondants) ou bien un projet ou
futur projet (1 répondant). Nous pouvons donc en conclure que le Lean
est perçu comme intégré au quotidien chez Novo Nordisk. Il
en est de même pour la majorité des répondants
extérieurs.
La place du Lean dans les BPF
Après avoir vu que le Lean est en majorité
appliqué au quotidien, nous allons maintenant nous interroger sur la
place du Lean.
Ce graphique nous permet de connaitre les réponses des
personnes interrogées à propos de cinq questions. Il est
important de noter que le code couleur a seulement un intérêt de
lisibilité du graphique. Nous pouvons noter que les deux
premières questions ont le même profil de réponses.

La place du Lean dans les BPF
|
|
|
|
|
|
|
|
10
|
|
|
|
|
|
2 2
|
|
|
|
0 0 0 0
|
|
|
|
Nombre de réponses
|
14 12 10 8 6 4 2 0
|
7
|
16
|
|
15
|
|
15
|
|
15
|
|
|
|
14 14
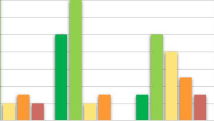
10
10
8
5
3
3
3
3
2
2
2
0
Le Lean est bien Utiliser des principes Les BPF encouragent
J'arrive à respecter Je pense que le Lean
intégré dans les BPF Lean facilite le l'utilisation
du Lean les BPF en utilisant le et les BPF sont
respect des BPF Lean contradictoires
Tout à fait d'accord Plutôt d'accord Je ne sais pas
Plutôt pas d'accord Pas du tout d'accord
Figure 11 : La place du Lean dans les BPF
Pour permettre le traitement statistique, des valeurs seront
attribuées aux réponses données :
- Tout à fait d'accord : 5
- Plutôt d'accord : 4
- Je ne sais pas : 3
- Plutôt pas d'accord : 2
- Pas du tout d'accord : 1
Nous obtenons le tableau de scores suivant. Le score obtenu est
la somme du nombre de réponses multiplié par la valeur de la
réponse, pour toutes les modalités de réponses.
Score = 1(nombre de réponses x valeur)
39

40
|
Q1 : Le Lean
est bien intégré dans les BPF
|
Q2 : Utiliser des principes Lean facilite
le respect des BPF
|
Q3 : Les
BPF encouragent l'utilisation du Lean
|
Q4 :
J'arrive à respecter les BPF en
utilisant le Lean
|
Q5 : Je pense
que le Lean et
les BPF sont contradictoires
|
Nombre de réponses
|
Tout à fait d'accord
|
7
|
10
|
3
|
15
|
0
|
Plutôt d'accord
|
15
|
14
|
10
|
14
|
2
|
Je ne sais pas
|
2
|
2
|
8
|
0
|
2
|
Plutôt pas
d'accord
|
3
|
3
|
5
|
0
|
10
|
Pas du tout d'accord
|
2
|
0
|
3
|
0
|
15
|
Score
|
22
|
31
|
5
|
44
|
-38
|
Tableau 4 : La place du Lean dans les BPF- Score des
réponses pour tous les répondants
Un score positif indique une réponse affirmative
à la question. Nous pouvons ainsi voir que la proposition la plus
vérifiée, c'est-à-dire celle qui remporte le plus haut
score concerne la capacité à respecter des BPF en utilisant le
Lean, avec 44 points. Nous pouvons proposer une explication à ce score
très haut : les Bonnes Pratiques de Fabrication étant très
profondément intégrées dans la culture de l'industrie
pharmaceutique, il est obligatoire de les respecter, quelles que soient les
méthodes utilisées au travail.
Deux phrases obtiennent un score proche : « Le Lean
est bien intégré dans les BPF » et « Utiliser
des principes Lean facilite le respect des BPF », avec 22 et 31
points. La méthode Lean est ainsi vue comme une méthode qui
permet le respect des BPF, les deux méthodes sont perçues comme
compatibles. Le score négatif de l'affirmation « Je pense que
les BPF et le Lean sont contradictoires » (-38 points), permet de
valider cette hypothèse.
On peut aussi noter un score plus faible pour l'affirmation
suivante : « les BPF encouragent l'utilisation du Lean »,
avec 5 points. En étudiant le Guide des Bonnes Pratiques de Fabrication,
on peut constater que le mot Lean n'apparait pas. Cependant,
l'amélioration continue est une notion très importante, et c'est
un des enjeux d'une démarche Lean. Une explication possible serait qu'il
y a une obligation de résultat pour le respect des BPF, pas de
méthode. Ce règlement n'encourage donc pas plus le Lean que
d'autres méthodes d'organisation.

41
Nous allons maintenant étudier la différence
entre les deux populations étudiées. Nous allons chercher si les
deux populations répondent de façon similaire à ces
questions, ou bien si l'on peut observer des différences.
Ce tableau a été réalisé en
différenciant les données des répondants extérieurs
de ceux travaillant chez Novo Nordisk. Il représente le nombre de
réponses obtenues pour chaque modalité.
|
Q1 : Le
Lean est
bien intégré
dans les BPF
|
Q2 : Utiliser des principes Lean facilite le respect des BPF
|
Q3 : Les
BPF encouragent l'utilisation du Lean
|
Q4 :
J'arrive à respecter
les BPF en utilisant le Lean
|
Q5 : Je pense que le Lean et les BPF sont contradictoires
|
Echantillon extérieur
|
Nombre de réponses
|
Tout à fait
d'accord
|
3
|
3
|
0
|
5
|
0
|
Plutôt d'accord
|
6
|
5
|
3
|
7
|
2
|
Je ne sais pas
|
0
|
2
|
3
|
0
|
2
|
Plutôt pas
d'accord
|
2
|
2
|
4
|
0
|
5
|
Pas du tout
d'accord
|
1
|
0
|
2
|
0
|
3
|
Score
|
8
|
9
|
-5
|
17
|
-9
|
Echantillon Novo Nordisk
|
Nombre de réponses
|
Tout à fait
d'accord
|
4
|
7
|
3
|
10
|
0
|
Plutôt d'accord
|
9
|
9
|
7
|
7
|
0
|
Je ne sais pas
|
2
|
0
|
5
|
0
|
0
|
Plutôt pas
d'accord
|
1
|
1
|
1
|
0
|
5
|
Pas du tout
d'accord
|
1
|
0
|
1
|
0
|
12
|
Score
|
14
|
22
|
10
|
27
|
-29
|
Tableau 5 : La place du Lean dans les BPF - Comparaison
des deux populations
Afin de vérifier si les différences
observées sont significatives d'un point de vue statistique, nous allons
réaliser un test de Fisher, qui permet de comparer les variances. Il est
utilisé pour

42
les petits échantillons, à la différence
d'un test de Chi2. Ici, nous étudierons donc la
différence entre les répondant travaillant chez Novo Nordisk
(Novo), et la population extérieure (Ext).
Soit l'hypothèses H0 = les variances des
échantillons sont homogènes.
On calcule les variances pour les réponses obtenues, pour
les deux échantillons. On obtient le résultat suivant :
|
Q1
|
Q2
|
Q3
|
Q4
|
Q5
|
Var (Ext)
|
16,8
|
12,2
|
9
|
22,8
|
12,2
|
Var (Novo)
|
27,7
|
45,3
|
17,5
|
75,8
|
108,2
|
Tableau 6 : Calcul des variances de scores obtenus aux
différentes questions, selon la population
Le test de Fisher s'effectue en comparant les valeurs
observées avec une valeur théorique présente dans une
table. Avec :
k ? (nombre d'individus dans l'échantillon d'où
provient la variance max) ? 1 ? 16 ?? ? (nombre d'individus dans
l'échantillon d'où provient la variance min) ? 1 ? 11
On trouve F théorique = 2.70
On calcule ensuite la valeur F observée :
V?????????????? ???? ???????? g??????????
????????é ?
V?????????????? ???? ???????? ????????????
On obtient les valeurs suivantes :
|
Q1
|
Q2
|
Q3
|
Q4
|
Q5
|
F observé
|
1,65
|
3,71
|
1,94
|
3,32
|
8,87
|
Tableau 7 : Calcul du test de Fisher, selon la
population
Lorsque F observé est supérieur à F
théorique, l'hypothèse H0 est rejetée, c'est-à-dire
que les variances des échantillons sont trop différentes pour
être considérées comme homogènes. Les

43
réponses des deux échantillons sont alors trop
différentes, et les répondants ont un comportement
différent.
Pour conclure, nous pouvons dire que les réponses des
deux populations sont similaires pour deux affirmations qui sont « Le
Lean est bien intégré dans les BPF » et « Les
BPF encouragent l'utilisation du Lean ». Pour les trois autres
affirmations, les réponses des deux populations sont différentes.
Nous allons étudier leur distribution en détails.
Comparaison entre les deux populations "Utiliser des
principes Lean facilite le respect des BPF"
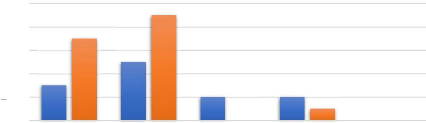
9
10
0
0
7
5
3
0
1
8
6
4
2
Nombre de réponses
0
2 2
Tout à fait d'accord Plutôt d'accord Je ne sais pas
Plutôt pas d'accord Pas du tout d'accord
Extérieur Novo Nordisk
Figure 12 : Comparaison des deux populations - Utiliser
des principes Lean facilite le respect des BPF
Nous pouvons voir que la distribution des réponses des
deux groupes est différente. L'échantillon « Novo Nordisk
» apparait plus tranché, les réponses sont en grande
majorité affirmatives. Au contraire, les réponses du groupe
« Extérieur » sont plus dispersées, avec quatre
réponses non affirmatives. Les employés de Novo Nordisk sont donc
plus convaincus de l'utilité du Lean pour le respect des BPF, et
seulement une personne interrogée n'est pas d'accord avec cette
affirmation.

44
Comparaison entre les deux populations "J'arrive
à respecter les BPF en utilisant le Lean"
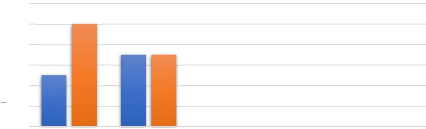
7
7
10
2
0 0 0 0 0 0
0
12
10
8
6
4
Nombre de réponses
5
Tout à fait d'accord Plutôt d'accord Je ne sais pas
Plutôt pas d'accord Pas du tout d'accord
Extérieur Novo Nordisk
Figure 13 : Comparaison des deux populations - J'arrive
à respecter les BPF en utilisant le Lean
Pour cette affirmation, les réponses des deux groupes
sont très similaires. Nous pouvons néanmoins noter que le groupe
« Novo Nordisk » a une proportion plus élevée de
réponse « tout à fait d'accord ». Là encore,
cela peut montrer un avis plus catégorique de cette population.
Comparaison entre les deux populations
"Je pense que le Lean et les BPF sont
contradictoires"
12
14
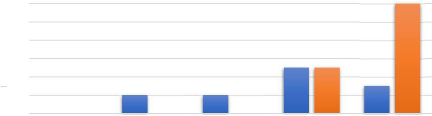
12
10
8
5
5
6
4
2 2
2
0
0
0
0
Nombre de réponses
0
3
Tout à fait d'accord Plutôt d'accord Je ne sais pas
Plutôt pas d'accord Pas du tout d'accord
Extérieur Novo Nordisk
Figure 14 : Comparaison des deux populations - Je pense
que le Lean et les BPF sont contradictoires.
Nous pouvons voir que la réponse des personnes
travaillant chez Novo Nordisk est de nouveau plus tranchée, ce qui peut
indiquer que les personnes sont convaincues du contraire de cette affirmation.
Au contraire, les réponses du groupe « Extérieur » sont
plus dispersés, avec quatre

45
réponses non-négatives. Nous observons un profil
de réponses très semblable à figure 12, mais
inversé.
Pour conclure, nous pouvons penser que le Lean est
perçu comme un outil plutôt bien intégré dans les
BPF. Ce sont deux méthodologies qui ne sont pas contradictoires, et qui
peuvent fonctionner en synergie : l'utilisation de l'un facilite l'emploi de
l'autre. Une orientation de la relation est possible : l'utilisation d'une
démarche Lean facilite le respect des BPF.
La performance et le Lean
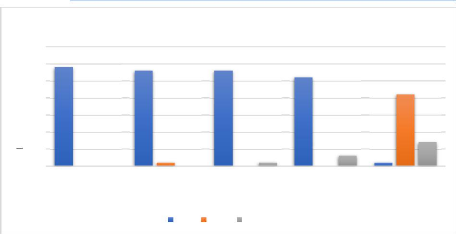
Le Lean me fait gagner du temps
Le Lean favorise le travail en équipe
Le Lean permet de gagner en performance
Appliquer les principes Lean coûte plus cher
Le Lean permet d'être plus compétitif
Intérêt du Lean en industrie
pharmaceutique
35
30
26
25
21
20
15
10
3
5
1
1
1
0
0
0
0
0
0
Nombre de réponses
29 28 28
7
VRAI FAUX Je ne sais pas
Figure 15 : Intérêt du Lean en industrie
pharmaceutique
Ce graphique permet de se rendre compte de l'avis des
personnes interrogées concernant l'intérêt du Lean en
industrie pharmaceutique. Nous pouvons voir que la majorité des
personnes reconnaissent que le Lean permet de gagner en performance,
d'être plus compétitif et de gagner du temps.
Nous pouvons observer une petite portion de réponses (3
sur 29 soit 10%) qui ne se prononce pas sur l'intérêt du Lean pour
le travail en équipe. La coopération est pourtant un
élément mis en avant dans la stratégie Lean. En effet,
deux des cinq valeurs du Lean concernent la coopération : impliquer le
personnel de production dans le diagnostic et la résolution des
problèmes et favoriser l'amélioration en continu, de façon
dynamique et en intégrant tous les acteurs concernés.

46
Enfin, concernant le coût d'une démarche Lean,
nous observons une majorité de réponses qui pense que cela ne
coûte pas plus cher. Un quart de l'échantillon ne sait pas si le
Lean coûte plus cher (7 sur 29 soit 24%). Nous pouvons tenter d'expliquer
cette proportion par le fait qu'il n'est pas précisé s'il faut
tenir compte du retour sur investissement, ou seulement de la mise en place de
la démarche Lean.
Les intérêts économiques
détaillés dans la première partie de cette étude
sont donc bien perçus par les répondants. Nous allons maintenant
étudier l'application de quelques principes Lean au quotidien.
Principes Lean non appliqués en
industrie pharmaceutique
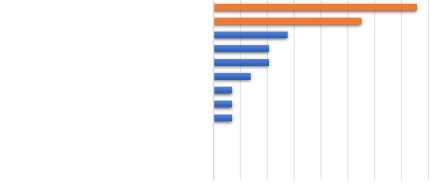
Philosophie long terme plutôt que court terme
Production constante et lissée
Respecter et motiver ses partenaires
Prendre des décisions en consensus
Aller toujours sur le terrain
S'améliorer continuellement
Qualité du premier coup
Faire monter en compétence les individus et les
équipes
Contrôles visuels pour détecter les
problèmes
Tâches standardisées
Résolution immédiate des problèmes
Flux tirés
Fluidité des processus
0% 5% 10% 15% 20% 25% 30% 35% 40%
38%
28%
14%
10%
10%
7%
3%
3%
3%
0%
0%
0%
0%
Nombre de réponses (en % de répondants)
Figure 16 : Principes Lean non appliqués en
industrie pharmaceutique
Ce graphique a été construit selon la
méthode de Pareto. Les répondants devaient se prononcer sur les
principes qui n'étaient pas appliqués dans leur entreprise. Les
modalités ont ensuite été triées par ordre
décroissant de réponses. Cette interrogation négative a
été utilisée pour inciter les répondants à
réfléchir, non pas sur ce qui est mis en place, mais sur ce qui
ne l'est pas, et ainsi avoir un regard critique sur leur organisation et leur
façon de travailler.

47
Nous pouvons observer que deux principes se distinguent des
autres et sont rarement appliqués en entreprise pharmaceutique, avec
plus de 15% des répondants qui les considèrent comme non
appliqués dans leur entreprise.
Le principe le moins appliqué en industrie
pharmaceutique, avec 38% des répondants ne l'appliquant pas, concerne
l'adoption d'une philosophie sur le long terme plutôt qu'à court
terme. Pour expliquer ce résultat, nous pouvons supposer que la
philosophie sur le long terme n'est pas communiquée aussi
fréquemment que la philosophie à long terme de l'entreprise.
Le deuxième point concerne la production constante et
lissée. Les BPF exigeant une production en lot, pour éviter les
risques de contamination croisée, il est en effet difficile de lisser la
production, qui connait de plus des ralentissements, du fait du vide de ligne
et des changements de lots par exemple.
Ces deux points ont été traités dans la
Partie 1.II, et les règles préconisées permettent de
trouver des solutions palliatives, permettant une bonne application du Lean,
malgré les contraintes engendrées par les BPF.
Ressenti personnel du Lean
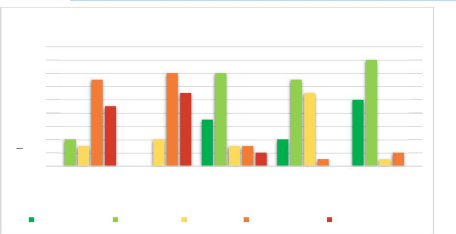
18
16
Met en avant le partage avec les autres]
Favorise ma sécurité
Augmente ma productivité
Augmente mon niveau de stress
Augmente mon niveau de fatigue
Effets du Lean sur les travailleurs
16
14
14
Nombre de réponses
13
14
11
12
9
10
7
8
6
4
4
3
4
2
0 0
0
0
3
3
2
4
13
11
1
0
10
1
2
0
Tout à fait d'accord Plutôt d'accord Je ne sais pas
Plutôt pas d'accord Pas du tout d'accord
Figure 17 : Effets du Lean sur les
travailleurs

48
Ce graphique représente l'avis des personnes
interrogées sur l'impact d'une démarche Lean sur le personnel.
Nous interpréterons chaque question indépendamment des autres.
Concernant le stress, la majorité des répondants
pense que le Lean n'augmente pas le niveau de stress (13 plutôt pas
d'accord et 9 pas du tout d'accord, soit 75% au total). Cependant, quatre
personnes pensent que cette démarche leur cause du stress. Nous pouvons
penser que ce stress est causé par le changement de méthode de
travail, qui peut être perçu négativement si l'entreprise
n'accompagne pas suffisamment ses employés pendant ce changement. Ce
stress peut aussi être causé par une recherche de performances
trop importante, et donc un changement de conditions de travail brutal.
Concernant la fatigue, la majorité des
répondants pense que le Lean n'augmente pas le niveau de fatigue (14
plutôt pas d'accord et 11 pas du tout d'accord, soit 86% au total). On
remarque une prise de position ferme, qui laisse penser que l'opinion est
franche. Une opinion aussi marquée peut faire penser que les
répondants ont un avis contraire à la réponse, et donc
qu'ils pensent que la démarche Lean leur cause moins de fatigue. La
stratégie Lean vise en effet à diminuer les gaspillages, comme
les déplacements ou gestes inutiles, qui peuvent être source de
fatigue pour les travailleurs.
Concernant la productivité, nous pouvons observer que
les répondants ont en majorité répondu « plutôt
d'accord » (14 sur 29 répondants soit 48%) pour l'augmentation de
la productivité par le Lean, et 25% (7 sur 29 réponses) «
tout à fait d'accord » et 17% des répondants ne sont pas
d'accord ou pas du tout d'accord avec cette affirmation. Nous pouvons expliquer
cette distribution par la différence entre la productivité, qui
est l'objet de cette question, et la performance, qui est l'enjeu du Lean. La
mesure de la productivité permet d'avoir un aperçu sur les
variations des résultats : c'est le rapport entre la quantité de
travail et le temps nécessaire à ce travail. La performance ne
concerne pas seulement les résultats, mais aussi les objectifs et les
ressources utilisées. La philosophie Lean met en avant
l'amélioration de la performance, qui peut donc être conduite via
une amélioration de la productivité, mais pas seulement.
Concernant la sécurité, la distribution des
réponses indique qu'une majorité des répondants pense que
le Lean favorise la sécurité des personnes (13 réponses
sur 29, soit 44%). Nous

49
pouvons noter aussi qu'une grande part des répondants
n'a pas su se positionner par rapport à cette affirmation : 11 personnes
sur 29 ne savent pas si le Lean favorise la sécurité, soit 38%.
La sécurité des personnes est pourtant un élément
important du Lean, qui cherche à travers différents outils
à favoriser la sécurité des personnes (ergonomie au poste
de travail, 5S, ...).
Enfin, concernant le partage avec les autres, une grande
majorité des répondants est convaincu que le Lean favorise le
partage avec les autres (26 réponses tout à fait d'accord ou
plutôt d'accord sur 29, soit 90%). Ce résultat confirme notre
constat concernant l'intérêt du Lean en industrie pharmaceutique
(Figure 8), concernant la coopération au sein des équipes, car
une majorité de personnes considèrent que le Lean favorise le
travail en équipe.
Pour conclure, l'intérêt humain est bien
perçu par les répondants, concernant la productivité, la
sécurité ou le partage avec les autres. De plus, les effets
négatifs, comme le stress ou la fatigue, remontés dans la Partie
1. IV par l'INRS, sont en majorité non perçus par les
répondants.
Conclusion
L'objectif de cette enquête était d'apporter une
validation empirique aux hypothèses soulevées lors de la revue de
l'Etat de l'art. Grâce aux résultats obtenus, nous avons pu en
premier lieu comprendre que le Lean est bien intégré au quotidien
dans les industries pharmaceutiques, et cela au quotidien.
L'intérêt réglementaire du Lean est
perçu, car cette méthodologie est bien intégrée
dans les BPF Les deux méthodologies ne sont pas contradictoires, et le
Lean permet même de faciliter l'application du référentiel.
Malgré cela, les BPF n'encouragent pas l'application du Lean. Cela est
expliqué par l'obligation de résultats et non de moyens du
référentiel. La comparaison des deux populations
interrogées a montré un résultat plutôt
homogène concernant les questions posées.
L'intérêt économique de l'application
d'une stratégie Lean est bien perçue par les répondants.
Deux principes sont peu appliqués en industrie pharmaceutique,
concernant l'adoption d'une philosophie à long terme et la production
constante et lissée. Cela confirme les difficultés
soulevées dans l'état de l'art.

50
Enfin, l'intérêt humain est bien perçu par
les répondants, concernant la productivité, la
sécurité ou le partage avec les autres. De plus, les effets
négatifs possibles ne sont pas rencontrés pour la majorité
des répondants.
Nous pouvons donc conclure que les hypothèses
soulevées sont bien vérifiées en entreprise. Nous allons
maintenant examiner les opportunités et limites soulevées par
l'adoption d'une méthodologie Lean, dans le cadre de missions
d'amélioration, menées durant cette année d'alternance
dans l'entreprise Novo Nordisk.
IV. Observations
Durant cette année de formation, plusieurs missions
m'ont été confiées. La première consistait à
suivre et améliorer le processus de supervision des APS (Aseptic
Process Simulation, ou Simulation de Procédé Aseptique). La
deuxième mission consistait à mettre en place une démarche
Nécessaire et Suffisant, pour les activités du service Assurance
Qualité.
Après avoir décrit le procédé de
simulation aseptique, nous allons analyser ces missions d'amélioration,
qui ont été menées en suivant une méthodologie
Lean. Nous tenterons de déterminer l'intérêt d'une telle
démarche pour ces cas pratiques, et en examinerons les avantages et les
limites.
Le processus de simulation de procédé aseptique
Comme nous l'avons vu auparavant, les médicaments
contenant de l'insuline doivent être produits de façon aseptique,
de leur filtration stérilisante à la fin du remplissage.
Les Bonnes Pratiques de Fabrication imposent des exigences
particulières aux industries pharmaceutiques produisant des
médicaments stériles, qui ne peuvent pas être
stérilisés à la fin du processus. Selon cette
réglementation, « la validation des procédés de
fabrication aseptique doit comprendre la simulation du procédé
à l'aide d'un milieu de culture », c'est-à-dire qu'on
exécute le processus de production aseptique en utilisant un milieu de
culture favorable à la croissance des micro-organismes. Cela permet
d'identifier d'éventuelles contaminations.

51
Chez Novo Nordisk, cette validation des procédés
de fabrication est évaluée par les APS, via un rapport de
validation. Le respect des critères de validation et la
non-contamination du média permettent d'approuver le rapport, et de
valider les procédés de fabrication de l'entreprise.
Ce processus est supervisé par l'Assurance
Qualité, qui assiste en direct ou en visionnant des enregistrements
à l'ensemble des activités du processus. Le rôle d'un
superviseur est de vérifier le bon comportement aseptique des
opérateurs de production et techniciens de maintenance, ainsi que de
s'assurer du respect des procédures applicables.
Production Contrôle qualité Assurance
Qualité

Lavage et Approbation
Formulation Remplissage Incubation Inspection
Stérilisation de l'APS
Figure 18 : Processus simplifié de la
réalisation d'un APS
En cas d'observation, un retour doit être
effectué à la personne concernée, sous forme d'une
remarque, ou d'une reformation. Ces retours, s'ils sont critiques, doivent
être faits avant l'approbation du rapport de validation.
Nous pouvons représenter ce processus ainsi :
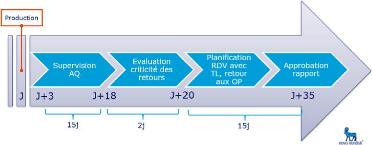
Figure 19 : Processus simplifié de la supervision
des APS par l'Assurance Qualité Etat des lieux
préalable
Ma mission a débuté avec une formation à
la supervision des APS, pour le processus de remplissage. Cette formation m'a
permis d'être habilitée à réaliser cette
activité. Cette

52
supervision s'effectue en zone de production, ou bien à
l'aide d'enregistrements vidéo. Cela m'a permis d'avoir un regard
interne sur ce processus, et d'en comprendre les dysfonctionnements.
La supervision des APS par l'Assurance Qualité est
suivie et pilotée grâce à un board de performance
hebdomadaire. Plusieurs indicateurs de performance y sont
évalués, concernant notamment l'état de la supervision en
cours, les délais de retours aux opérateurs ou bien l'approbation
de l'APS.
Nous avons pu nous rendre compte qu'un indicateur de
performance était souvent peu respecté. Cela concernait le temps
nécessaire pour réaliser les retours aux opérateurs, qui
dépassait parfois 60 jours après la réalisation des
activités, entrainant la perte des enregistrements vidéo
associés. Cela avait pour conséquence de ne pas avoir de support
pour effectuer les retours aux opérateurs. De plus, les
procédures du groupe exigent que les retours aux opérateurs
soient effectués le plus rapidement possible après
l'observation.
Il a donc été décidé de
réaliser un document A3, qui est un outil de résolution
systématique des problèmes, aussi appelée 8D pour 8
disciplines. Il est disponible en annexe (Annexe 3).
Amélioration du flux de retours APS
Résolution du problème
La clarification du problème montre que les retours
sont effectués trop longtemps après les activités. La
recherche du point d'origine pointe les étapes de gestion des retours
par l'Assurance Qualité, et de retour aux opérateurs, qui
s'effectuent en zone de production.
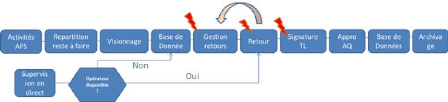
Figure 20 : Processus détaillé de la
supervision des APS par l'Assurance Qualité, avec recherche du point
d'origine des problèmes.

53
Après l'étape de clarification, nous nous sommes
aperçus qu'il y avait deux problèmes distincts à
résoudre, qui ont fait l'objet de deux recherches de causes :
- La gestion des retours commence trop tard après la
supervision,
- Il y a des difficultés pour faire les retours une fois
les observations faites.
Nous avons recherché toutes les causes possibles, en
utilisant un diagramme d'Ishikawa. En analysant ces retours d'un point de vue
Lean, nous pouvons identifier un grand nombre de gaspillages :
- Transport : Les retours aux opérateurs sont
effectués en zone à atmosphère contrôlée,
difficile d'accès. Des retours fréquents posent un
problème de sécurité, car il faut limiter l'accès
à ces zones pour éviter les contaminations par exemple. De plus,
cela allonge le temps de déplacement.
- Stock : A cause de ces déplacements
difficiles, les retours sont effectués seulement après
réception de tous les créneaux de supervision, et pas dès
la réception de chaque créneau. Cela crée un stock
d'informations.
- Retards : Ces stocks d'information créent des
retards pour les retours, qui ne sont pas effectués dès que cela
est possible.
- Sur-qualité : Les retours non-critiques sont
traités de la même manière que les retards critiques.
Après avoir effectué un diagramme d'Ishikawa
pour rechercher les causes possibles, nous avons mené des investigations
pour vérifier si ces causes avaient une réelle influence sur
notre problème ou non. La cause la plus probable est nommée cause
directe. Elle permet, en utilisant l'outil « 5 Pourquoi », de trouver
la cause racine.
Dans notre cas, nous avons abouti à deux causes directes
:
- Les rôles et responsabilités, définies
dans la procédure décrivant l'exécution de la supervision
des APS par l'Assurance Qualité, ne sont pas respectés : le suivi
des observations est effectué par les équipes d'Assurance
Qualité et non de la production.

54
- Des retards dans le flux de traitement des retours
entrainent un retard dans la prise en charge de ces retours.
L'équipe de l'Assurance Qualité doit donc
effectuer une activité qui ne lui est pas dédiée. Cela
entraine une charge supplémentaire, qui cause du retard dans le flux de
traitement des retours, principalement car cette activité n'est pas
prioritaire par rapport aux autres activités du service.
La première cause racine, concernant le non-respect des
rôles, pointe l'absence de formation pour le rôle de superviseur de
production, qui, de plus, n'est pas clairement défini. La supervision
n'est pas effectuée par la production, qui recense seulement les
activités effectuées en production. C'est donc l'Assurance
Qualité qui prend en charge cette activité.
L'investigation menée pour trouver la cause racine du
deuxième problème, concernant les retards dans le flux de
traitement des retours, met en cause les retards dans la supervision des APS
par l'Assurance Qualité. Ce problème sera détaillé
ultérieurement.
Afin de limiter les retards, plusieurs actions ont
été prises. Le board de performance, dédié
à l'APS, a été muté sous Trello, qui est un outil
de gestion de projet en ligne. L'utilisation d'un tel outil a permis une
meilleure visualisation des retours restant à faire, tout en regroupant
les informations nécessaires à la prise de rendez-vous avec
l'opérateur (équipe de rotation, date limite, date de retour
possible, commentaire associé, responsable du retour, ...)
De plus, afin de faciliter le suivi à plus long terme,
un graphique regroupant les délais de retour et de supervision a
été produit (Annexe 4). Il permet de visualiser le
délai de supervision, cumulé au délai de retour, pour
chaque opérateur à qui un retour a été fait depuis
le début de l'année 2019.
De plus, pour simplifier le flux de traitement des feuilles
d'observation, il a été décidé de séparer
physiquement les feuilles, selon leur stade de traitement :
- Les feuilles non traitées sont déposées
dans une pochette spécifique, avec le document de
traçabilité.

55
- Les feuilles traitées, c'est-à-dire pour
lesquelles les commentaires ont été entrés dans la base,
sont conservées dans un dossier identifié. Il est ajouté
un post-it sur la feuille, lorsqu'on identifie un retour nécessaire. De
plus, un suivi est assuré via Trello.
- Une fois les retours effectués, les feuilles pouvant
être archivées sont approuvées et rangées dans le
dossier identifié.
Enfin, pour permettre le respect des rôles et
responsabilités de chacun, deux propositions ont été
suggérées. La première consiste à mettre en place
un statut de superviseur de production, en construisant une formation
adaptée. Il faudra auparavant organiser un atelier de travail avec les
process de production, afin de définir le minimum attendu pour la
supervision.
Le processus de production des APS sera ainsi supervisé
d'une part par les équipes de production, et d'autre part par
l'Assurance Qualité. Les observations générées
pendant ces supervisions seront mises en commun, et feront l'objet de retours
aux opérateurs de production, effectués par les superviseurs de
production. Cela permettra un suivi plus efficace des actions sur le long
terme, et facilitera les retours aux opérateurs car ils seront
réalisés plus rapidement. De plus, une montée en
compétence des superviseurs de production sera réalisée.
Enfin, pour garantir un niveau de qualité suffisant, l'Assurance
Qualité réalisera les retours critiques, résultant de
gestes pouvant avoir une incidence sur le produit par exemple.
Concernant la mise en place d'un rôle de superviseur de
production, le gain de temps potentiel concernant l'équipe de
l'Assurance Qualité est conséquent. Sur l'année 2018, 16
APS ont été menés, aboutissant à 753 observations.
Cela a entrainé un retour à 35 équipes différentes
sur trois lignes de production. En arrondissant le temps moyen d'un retour
à 10 minutes, et en prenant en compte du temps d'accès à
la zone de production de 10 minutes en moyenne, cela aboutit à un total
de 251 heures de retours, pour l'année 2018. Après la mise en
place de l'amélioration proposée, la très grande
majorité de ces retours pourraient être effectués par le
superviseur de production, en collaboration avec l'Assurance Qualité.
Résultat obtenu

56
Les actions correctives menées, bien que provisoires et
non pérennes, ainsi qu'une vigilance accrue sur les délais, et
des rappels réguliers ont permis de diminuer sensiblement le temps
alloué à l'organisation des retours.
Le tableau suivant nous renseigne sur les délais moyens
de supervision et de remplissage, ainsi que les délais maximum et
minimum, pour tous les lots APS remplis depuis le début de
l'année 2019 :
|
Numéro de lot APS
|
JT6L180
|
JT6L294
|
JT6L572
|
JT96M005
|
JT6M189
|
JT6M287
|
JT6N304
|
JT6P157
|
Supervision
|
Moy
|
28
|
24
|
29
|
8
|
14
|
10
|
13
|
10
|
Max
|
34
|
41
|
35
|
31
|
18
|
27
|
24
|
24
|
Min
|
12
|
13
|
21
|
-
|
8
|
1
|
-
|
3
|
<18j
|
9%
|
36%
|
0%
|
89%
|
93%
|
88%
|
63%
|
77%
|
Retour
|
Moy
|
57
|
56
|
53
|
32
|
39
|
36
|
23
|
25
|
Max
|
94
|
77
|
80
|
84
|
78
|
64
|
43
|
36
|
Min
|
37
|
41
|
36
|
- 61
|
11
|
-
|
-
|
15
|
<60j
|
73%
|
73%
|
75%
|
92%
|
87%
|
94%
|
100%
|
100%
|
Tableau 8 : Tableau de statistiques sur les indicateurs
de délais et supervision des APS
Le délai de supervision est la différence entre
la date de l'activité et la validation de la supervision. Le
délai de retour est la différence entre la date de
l'activité, et la date du retour à l'opérateur.
Sur les derniers APS organisés, tous les rendez-vous
pour les retours ont été organisés avant l'approbation du
rapport, soit moins de 36 jours après les activités. Concernant
le premier APS réalisé en 2019, le délai moyen de
supervision était de 28 jours, pour un délai de retour global de
57 jours. Seulement 9% de la supervision était réalisée
dans les temps, et 73% des retours étaient effectués avant 60
jours. La différence est marquante avec le dernier APS organisé,
avec un délai moyen de supervision de 10 jours, avec 77% de la
supervision réalisée dans les temps.

57
Les retours ont été effectués en moyenne
après 25 jours, et 100% ont respecté les délais de 60
jours.
Nous pouvons visualiser l'évolution de la
conformité des délais de retour sur le graphique suivant :
JT6L180 JT6L294 JT6L572 JT96M005 JT6M189 JT6M287 JT6N304 JT6P157
Numéro de lot APS
Supervision conforme (%) Retours conformes (%)
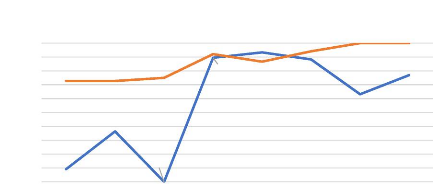
Taux de conformité (en %)
100%
40%
90%
80%
70%
60%
50%
30%
20%
10%
0%
94%
93%
92%
Evolution de la conformité des délais de
retour et de
supervision (en % de conformité)
100% 100%
75%
73% 73%
89%
87%
88%
63%
36%
9%
0%
77%
Figure 21 : Graphique montrant l'évolution de la
conformité des indicateurs aux KPIs
Nous pouvons noter l'influence de la conformité des
délais de supervision, sur les délais de retour. Lorsque la
supervision est réalisée en retard, il est plus difficile de
compenser lorsqu'il faut effectuer les retours. Il est donc important de
maintenir les efforts déployés à travers les actions
correctives mises en place, aussi bien pour respecter les délais de
supervision que de retours, et cela jusqu'à la mise en place d'une
solution durable et pérenne.
Analyse
Cette amélioration a permis de mettre en lumière
un manque de formation du personnel de production pour effectuer certaines
activités. Ces activités étaient réalisées
par d'autres personnes qui étaient formées, mais cela entrainait
une surcharge de travail. En conséquence, ces activités
étaient gérées après les autres activités de
routine, ce qui occasionnait des retards.

58
De plus, l'utilisation d'un outil Lean tel que l'outil de
résolution de problèmes A3 a permis de mettre en avant d'autres
sources de gaspillages, qui n'avaient pas été identifiées
au départ, et s'ajoutent à celles déjà
identifiées plus tôt :
- Un manque de formation du service de production
- Une surcharge de travail du service Assurance Qualité -
Des zones de stockage de l'information
- Des zones d'attente
Chez Novo Nordisk, le respect des BPF est primordial, et au
centre des activités de chacun. Les améliorations mises en place
respectent toujours ce référentiel. L'adoption d'une
démarche d'amélioration Lean, à travers une
résolution systématique des problèmes, a permis de se
rendre compte des sources de gaspillages cachées. Cela a pour effet
d'augmenter les compétences du personnel, d'optimiser la gestion du
temps du service d'Assurance Qualité, et de favoriser l'implication du
service de production dans les retours aux opérateurs.
Nous allons maintenant étudier la résolution du
deuxième problème, concernant l'organisation de la supervision
des APS par l'Assurance Qualité.
Optimisation de l'organisation pour l'observation AQ
Résolution du problème
La clarification du problème, concernant les
délais pour les retours aux opérateurs de productions, a mis un
deuxième problème à jour : la supervision de la production
par l'Assurance Qualité ne respecte pas les délais fixés.
Nous avons réalisé un deuxième A3 traitant de ce
problème.
La phase de clarification, effectuée sur trois APS
début 2019, permet de mettre en avant plusieurs problèmes :
- Les documents nécessaires à la supervision ne
sont pas toujours transmis rapidement à l'Assurance Qualité.
- La répartition des créneaux de supervision au
sein de l'équipe s'effectue trop tardivement après la
réception de ces documents

59
- Les dates limites pour la supervision des APS par
l'assurance Qualité ne sont pas toujours respectées. Tout cela
repousse les retours aux opérateurs, qui sont faits sur la base des
commentaires effectués pendant ces supervisions.
Cela a pour effet de retarder l'approbation des rapports
Mediafill, et donc de retarder la libération sur le marché des
lots insuliniques produit. A terme, des retards de livraisons peuvent avoir des
effets sur la santé des patients.
Des actions provisoires, pour apporter des solutions au plus
vite et éviter que la situation s'aggrave, ont été mises
en place. Le premier problème, concernant la transmission des documents,
contribue aux retards de supervision mais n'en est pas la cause principale. Il
a été résolu provisoirement en demandant les documents aux
processus supports dès que les activités étaient
réalisées, et non après l'écoulement du
délai imparti pour la transmission. De plus, la vigilance sur le
délai de répartition des vidéos a été
accrue, et les créneaux de supervision sont répartis dès
réception. Enfin, les délais fixés pour le visionnage des
activités est rappelé plus régulièrement.
L'utilisation du diagramme d'Ishikawa et l'investigation
menée a permis d'identifier la cause directe des retards : cette
activité n'est pas perçue comme une priorité. Les dates
limites sont alors oubliées ou ignorées, et les informations
nécessaires à la supervision ne sont pas cherchées.
L'emploi de l'outil « 5 Pourquoi » a permis de
comprendre qu'un sentiment de non expertise est à l'origine du
problème : toute l'équipe ne s'implique donc pas, par crainte de
ne pas avoir les capacités suffisantes. Seuls quelques membres de
l'équipe se sentent concernés. En conséquence, il n'y a
pas de communication sur l'importance de cette activité, et donc cela
n'est pas perçu comme urgent et prioritaire.
Il a été décidé de réaliser
un suivi poussé de cette activité. Dans un premier temps, ce
suivi s'est effectué en temps réel, via l'outil Trello. Une carte
été ajoutée au tableau de l'équipe, ce qui
permettait d'aborder de façon journalière cette
thématique, avec l'équipe entière. De plus, la mise en
place d'indicateurs, suivi à l'aide d'un graphique (Annexe 4),
a donné un point de vue macroscopique de l'évolution des
délais.

60
Le plan de formation de l'Assurance Qualité à la
supervision des APS a été revu et amélioré. L'enjeu
est d'augmenter l'efficacité de cette formation, afin d'une part de
gagner du temps et d'autre part de lutter contre le sentiment de non-expertise.
Pour cela, la première tâche a été d'identifier les
redondances entre les différents modules. Ensuite, les activités
sans valeur ajoutée ont été supprimées. La pratique
a été renforcée, avec la visualisation de vidéos
test pour évaluer les capacités des personnes à cette
activité. Enfin, les différentes sections de la formation ont
été pensées de façon à fonctionner
séparément les unes des autres, ce qui permet une meilleure
flexibilité pour la planification.
Résultat obtenu
Sur la dernière activité d'organisation des APS,
nous avons pu observer une réelle amélioration. Malgré une
période d'activité intense et une charge accrue à cause
des vacances d'été, tous les créneaux ont
été supervisés dans les temps. Le délai moyen entre
les activités de production et la fin de la supervision était de
28 jours avant les améliorations, et de 10 jours pour le dernier APS
supervisé. Les actions mises en place sont donc efficaces.
Il est cependant important de préciser que ces actions
ont pour but de contenir le problème, les résultats ne sont donc
pas permanents. Il est nécessaire de mettre en place des solutions
pérennes, qui assureront des effets à long terme.
Pour pérenniser les bonnes tendances, une communication
a été réalisée aux équipes en charge de la
supervision, pour rappeler l'importance d'une telle activité, qui est
une exigence réglementaire et qui conditionne la validation des
processus de production, au regard des réglementations. (Annexe
5)
L'activité de supervision des Mediafill est aujourd'hui
considérée comme une activité non prioritaire, car elle ne
concerne pas toute l'équipe, qui ne s'investit pas de la même
façon. Cette image nuit au respect des objectifs, car d'autres
activités sont considérées comme plus urgentes et plus
critiques. Ce manque d'investissement peut être dû à un
sentiment de non-expertise sur le sujet.
Pour diminuer ce ressenti, deux axes d'actions peuvent
être explorés, selon si le manque d'expertise est réel, ou
seulement ressenti. Dans le premier cas, il est important de garantir que

61
le personnel est suffisamment formé pour effectuer
cette activité. Dans le deuxième cas, un accompagnement sera
nécessaire, afin de permettre aux membres de l'équipe de prendre
confiance en leurs capacités.
Analyse
Encore une fois, l'adoption d'une démarche de
résolution de problème systématique a été
bénéfique. Cela a permis de prendre conscience de l'impact des
délais de supervision dans la gestion des retours aux
opérateurs.
Nous avons pu identifier plusieurs sources de gaspillages :
- Un manque de formation, réel ou ressenti, qui est la
cause racine du problème rencontré. - Des moments d'attente,
lorsqu'il faut attendre des documents non transmis.
- Des stocks d'information, lorsque les créneaux de
supervision ne sont pas répartis dès que cela est possible, ou
bien quand une personne ne transmet pas ses commentaires concernant la
supervision dans les temps.
- Une surcharge de travail, car cette activité n'est
pas régulière et cause des pics d'activité importants.
Nécessaire et Suffisant, communiquer et partager
La démarche Nécessaire et Suffisant a pour but
de faire réfléchir sur le niveau d'exigence attendu sur certaines
tâches, ce qui est nécessaire, pour la conformité avec les
réglementations par exemple, et ce qui est suffisant d'un point de vue
qualité. Elle est animée pendant la réunion
d'équipe quotidienne au board de performance. Le but est de
partager un questionnement rencontré pendant les activités
quotidiennes, et d'obtenir une réponse à la fois satisfaisante
d'un point de vue réglementaire, et qui n'engendre pas de
sur-qualité.
Cette réflexion permet donc de fixer une limite haute et
basse au niveau d'exigence requis :


Sur-qualité
Suffisant
Nécessaire et suffisant
Nécessaire
Sous-qualité

Niveau d'exigence
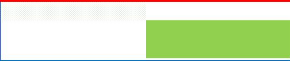
Figure 22 : Représentation schématique du
principe Nécessaire et Suffisant
62
Ma mission a consisté tout d'abord à mettre
cette pratique en commun avec plusieurs autres équipes de l'Assurance
Qualité.
Nous avons ensuite réalisé plusieurs
séances de travail avec un stagiaire d'une autre équipe, afin de
croiser les données obtenues par les deux équipes et les
réponses apportées aux différentes questions. Le but
était de garantir une homogénéité des
réponses apportées, et d'éviter de possibles
dérives, dans le temps mais aussi entre les différentes
équipes de l'Assurance Qualité.
Nous avons ensuite choisi de valider les réponses,
apportées pendant la discussion de l'équipe, auprès
d'experts, en fonction du sujet évoqué. Enfin, la parution
régulière d'une communication (Annexe 6),
diffusée à l'ensemble du service d'Assurance Qualité,
permet de transmettre l'avis des experts, et l'échange entre les
différentes équipes.
Cette activité permet d'éviter de nombreux
gaspillages. Les plus notables sont la sur-qualité et les
défauts, car il faut apporter une réponse qui soit
réellement nécessaire, d'un point de vue réglementaire,
mais aussi suffisante. Cela permet d'éviter une correction superflue par
exemple, ce qui aurait engendré de l'attente et des transports
d'information sans valeur ajoutée.
V. Conclusions de l'enquête
L'objectif de cette enquête était dans un premier
temps d'apporter une validation empirique aux hypothèses
soulevées lors de la revue de l'Etat de l'Art. Grâce aux
résultats obtenus, nous avons

pu valider les trois hypothèses proposées :
l'intérêt réglementaire, économique et humain, mais
aussi les limites de l'utilisation du Lean en industrie pharmaceutique, qui
sont bien perçues en entreprise.
L'analyse des missions menées durant cette année
d'alternance a pu mettre en lumière les bénéfices
possibles grâce à l'adoption d'une stratégie Lean dans un
milieu confronté aux Bonnes Pratiques de Fabrication. L'investigation
menée a permis de comprendre les causes multiples du premier
problème rencontré, c'est-à-dire des retards pour
effectuer les retours aux opérateurs, à la suite des
activités de supervision de la production aseptique. Un schéma
récapitulatif est disponible en annexe (Annexe 7), qui reprend
les causes directes identifiées, ainsi que les causes racines et
l'impact des différents retards sur le problème global.
63

64
Conclusion
Ce mémoire traite de la compatibilité d'une
démarche de Lean Management avec le respect des Bonnes Pratiques de
Fabrication, dans une industrie pharmaceutique. Cette problématique a
émergé d'un constat : les entreprises pharmaceutiques, pour
répondre à un besoin de rentabilité et de
pérennité, ont mis en place des démarches Lean. Ces
démarches ont pour principal enjeu de supprimer les activités
à non-valeur ajoutée des processus réalisés par
l'entreprise. Nous avons ainsi cherché à connaitre les
intérêts et les limites d'une telle démarche pour un
service d'Assurance Qualité.
Dans un premier temps, la littérature consultée
pendant la recherche documentaire nous a permis de voir que le Lean a tout
d'abord un intérêt réglementaire : les BPF et le Lean sont
compatibles, à certaines conditions. Des recommandations sont
émises pour pouvoir appliquer le Lean dans un milieu respectant les BPF,
fixant ainsi les enjeux du Lean dans l'industrie pharmaceutique.
Ensuite, nous nous sommes intéressés à
l'intérêt économique d'une telle démarche industries
pharmaceutiques : il permet d'accroitre durablement la performance de
l'entreprise, en évitant les activités à non-valeur
ajoutée, à travers la chasse aux gaspillages.
Enfin, nous avons compris l'importance du développement
des personnes, à travers l'autonomie et la prise en compte de la
santé du collaborateur. Des risques pour la santé et la
sécurité des travailleurs ont été soulevés,
notamment concernant la fatigue, le stress, ou bien les conséquences
d'une mauvaise gestion du changement de stratégie.
Dans un deuxième temps, nous avons
vérifié la véracité de ces hypothèses, en
administrant un questionnaire à des personnes travaillant dans une
industrie pharmaceutique qui applique le Lean, et qui travaille en Assurance
Qualité.
Nous avons ainsi pu constater que l'intérêt
réglementaire est bien perçu par les répondants : le Lean
permet de faciliter l'application des BPF, car les deux méthodes
partagent des objectifs communs. Par exemple, assurer l'efficacité du
médicament et supprimer les risques pour le patient sont un moyen de
garantir la valeur ajoutée du produit fabriqué.

Ensuite, nous avons vérifié que
l'amélioration des performances par l'application de principes Lean est
bien perçue par les répondants. Cela permet aux équipes
d'Assurance Qualité d'être plus compétitif et performant,
et de gagner du temps tout en favorisant le travail en équipe. Deux
principes Lean sont peu appliqués en industrie pharmaceutique,
concernant l'adoption d'une philosophie sur le long terme et la production
constante et lissée. Cette limite a été identifiée
dans la littérature, et l'enquête vient donc la valider.
Enfin, les risques pour les travailleurs, identifiés
à la suite de la mise en place de stratégies Lean, n'ont pas
été ressentis ou vécus par les répondants. Les
intérêts humains du Lean, comme le partage avec les autres ou les
bénéfices pour la sécurité, ont été
mis en avant.
Les démarches de Lean Management sont donc compatibles
avec les Bonnes Pratiques de Fabrication. L'application des principes Lean
apporte de réels intérêts réglementaires,
économiques mais aussi humains aux entreprises pharmaceutiques, et plus
particulièrement aux équipes d'Assurance Qualité.
Lors de cette année d'alternance, j'ai pu assister et
participer à la migration de plusieurs outils de management
d'équipe sur des supports informatiques. En effet, le board de
performance de l'équipe a été transféré sur
Trello, et tous les ordinateurs de l'entreprise ont changé de
système d'exploitation, et les collaborateurs ont adopté un mode
de stockage des données en ligne. Il pourrait être
intéressant par la suite de comprendre l'intérêt de la
digitalisation dans une démarche de Lean Management.
65

66
Apports et limites
Cette année d'apprentissage a été
très riche en enseignements, aussi bien professionnels que personnels.
Elle a représenté pour moi ma première expérience
longue dans le monde du travail, et m'a donné l'opportunité de
connaitre le domaine de l'industrie pharmaceutique, ainsi que le fonctionnement
d'un grand groupe international.
Cette année m'a permis d'appréhender le
management transversal, en gérant un processus qui mettait en relation
différents services de l'entreprise. Cette expérience m'a
également appris à gérer des activités à
court terme et à long terme, mais aussi à prioriser les
tâches, à court et moyen terme.
Lors de mon arrivée en entreprise, la peur de faire des
erreurs m'a parfois poussé à ne pas réaliser mes
activités de façon optimale. L'aide et le soutien de ma tutrice
m'a poussé à prendre confiance en mes capacités.
La pratique a représenté une partie importante
de mon expérience. Cela m'a permis d'une part de comprendre les axes
d'améliorations possibles, et les gaspillages en place, et d'autre part
de réaliser et d'apprécier les résultats obtenus.
Enfin, le contact régulier avec le personnel de
production, à travers la formation effectuée aux
opérateurs, a été très enrichissant, et m'a permis
de me rendre compte de l'importance d'aller sur le terrain.
Concernant l'administration de l'enquête, plusieurs
limites peuvent être soulevées. Le nombre réduit de
réponses au questionnaire ne permet pas d'être
représentatif de l'ensemble des industries pharmaceutiques
françaises. De plus, il aurait été intéressant
d'interroger des personnes travaillant dans des entreprises qui n'ont pas
adopté de stratégie Lean, afin d'effectuer des comparaisons.
De plus, connaitre le nombre d'entreprises extérieures
représentées dans l'échantillon de répondants
aurait permis d'apprécier la représentativité de notre
enquête, par rapport aux entreprises pharmaceutiques
françaises.

Il est important de noter que les BPF sont tellement
intégrées dans les industries pharmaceutiques que la
distanciation est difficile. En effet, ce référentiel est
présent avant même la construction d'une industrie, et conditionne
la production, sous tous ses aspects. Les idées d'amélioration
qui les remettraient en cause ne sont pas adoptables, et les stratégies
Lean qui tenteraient de les contourner pourraient rencontrer des risques
d'auto-censure, de la part de ceux qui les dirigent.
67

68
Bibliographie
Agence Nationale de Sûreté des Médicaments.
(2016). Guide des Bonnes Pratiques de Fabrication.
BALLE, M. (2007). La définition du Lean
management. Consulté le Mars 27, 2019, sur OperaPartners:
https://www.operaepartners.fr/la-definition-du-lean-management/
BALLE, M., & BEAUVALLET, G. (2016). Le Management Lean.
Tours: Pearson France.
BALLE, M., JONES, D., CHAIZE, J., & FIUME, O. (2018). La
stratégie Lean Créer un avantage compétitif,
libérer l'innovation, assurer une croissance durable en
développant les personnes. Paris: Groupe EYROLLES.
BAYNAST, LEVY, & LENDREVIE. (2017). Mercator. Paris:
DUNOD.
BAZIN, H. (2018). La Qualité du Management. La
Plaine Saint denis: AFNOR Editions.
BELLAÏCHE, M., BOUVARD, C., & HARIVEL, L. (2015).
Lean durable et qualité rentable. La-Plaine-Saint-Denis:
AFNOR.
CABY, F., & JAMBART, C. (2000). La Qualité dans
les services. Paris: Economica. DELBALDO, E. (2009). P-Lean. La
Plaine Saint Denis: AFNOR Editions . DEMETRESCOUX, R. (2017). Lean
Management, pour une performance solide et durable.
Malakoff: Dunod.
DEMING, W. (1982). Out of the Crisis. Economica.
E.AIZIER. (2012). Adaptation du Lean Manufacturing dans un
environnement GMP : ses opportunités et ses limites. Thèse
Diplôme d'Etat de Pharmacie.
Editions ISO. (2015). Principes essentiels et
vocabulaire. Récupéré sur Système de
Management de la Qualité:
https://www.iso.org/obp/ui#iso:std:iso:9000:ed-4:v2:fr

69
ERNOULT, R. (2010). Le grand livre de la Qualité.
La Plaine Saint Denis: AFNOR Editions.
FERNANDEZ, A. (2018, Juillet 3). Lean Management,
système d'organisation industrielle. Récupéré
sur
Piloter.org:
https://www.piloter.org/six-sigma/lean-management.htm
GILBERT, P., & YALENIOS, J. (2017). L'évaluation
de la performance individuelle. La Découverte.
GREEN, A., & O'ROURKE, D. (2006, Octobre 1). Lean
manufacturing practice in a cGMP environment. Pharmaceutical Technology
Europe, 18(10).
Guide des Bonnes Pratiques de Fabrication. (2016). ANSM.
HOHMANN, C. (2012). Lean Management. Paris: EYROLLES.
INRS. (2016, Décembre 15). Dossier Lean Management .
Récupéré sur INRS Santé et
Sécurité au travail:
http://www.inrs.fr/risques/lean-management/ce-qu-il-faut-retenir.html
JAIGANESH, V., & SUDHAHAR, J. C. (2013, Février).
Sketching out the Hidden Lean Management Principles in the Pharmaceutical
Manufacturing. (IJSRP, Éd.) Internationnal Journal of Scientific and
Research Publications, 3(2).
Larousse. (2019). Qualité.
Récupéré sur Dictionnaire de Français:
https://www.larousse.fr/dictionnaires/francais/qualité/65477?q=qualit%c3%a9#64734
NENNI, M. E., GIUSTINIANO, L., & PIROLO, L. (2014, August
04). Improvement of Manufacturing operations through a LEan Management Approach
: a Case study in the Pharmaceutical Industry. International Journal of
Engineering Business Management.
Novo Nordisk. (s.d.). A Propos de Novo Nordisk.
Récupéré sur Novo Nordisk France:
https://www.novonordisk.fr
SHEWART, W. A. (1931). Economic Control of Quality of
Manufactured Product. New York: Van Nostrand.

70
Table des matières
Remerciements II
Sommaire III
Table des figures et tableaux IV
Glossaire V
Introduction 1
PARTIE 1 : Etat de l'art 3
I. Evolution du concept de la qualité et de sa perception
3
La qualité, un concept général 3
Les démarches qualités depuis les
révolutions industrielles 3
Une démarche qualité pour rassurer les clients et
contrôler les produits 4
Le modèle de la Qualité totale 5
II. Les réglementations en industrie pharmaceutique 8
L'ANSM 8
Les Bonnes Pratiques de Fabrication 9
Département Assurance Qualité (AQ) 10
III. Le Lean Management dans un environnement BPF 11
Comparaison du Lean et des BPF 11
Principes de Lean Management cachés dans les BPF 14
La Qualité au centre de la démarche de Lean
Management 16
IV. L'intérêt économique d'une
stratégie Lean pour l'entreprise 17
Qu'est-ce que la performance ? 17
Les gaspillages nuisent à la performance 19
La variabilité et l'excès, des causes de
gaspillages 21
V. Les travailleurs et le Lean 22
L'importance du développement humain 22

71
Intérêt de la démarche pour un manager 23
Effets sur la santé et la sécurité des
travailleurs (INRS, 2016) 23
VI. Conclusion de l'état de l'art 25
PARTIE 2 : Enquête 27
I. Contexte de l'étude 27
1) Présentation de l'entreprise 27
2) Le Lean chez Novo Nordisk 30
II. Méthodologie de recherche 33
Rappel de la problématique 33
Les différentes postures de recherche 33
III. Questionnaire 35
Objectifs et enjeux 35
Etude de l'échantillon interrogé 36
Analyse des réponses 37
Conclusion 49
IV. Observations 50
Le processus de simulation de procédé aseptique
50
Etat des lieux préalable 51
Amélioration du flux de retours APS 52
Optimisation de l'organisation pour l'observation AQ 58
Nécessaire et Suffisant, communiquer et partager 61
V. Conclusions de l'enquête 62
Conclusion 64
Apports et limites 66
Bibliographie 68
Table des matières 70

Résumé 73
Table des annexes 74
Annexe 1 75
Annexe 2 76
Annexe 3 79
Annexe 4 81
Annexe 5 82
Annexe 6 85
Annexe 7 86
72

Résumé
L'augmentation régulière des dépenses de
santé constatée dans plusieurs pays a poussé les
gouvernements à prendre des mesures visant à les contrôler.
L'industrie pharmaceutique a donc cherché à mener une politique
de réduction des coûts, pour rester compétitif et permettre
à tous d'avoir accès aux soins. Des stratégies Lean ont
ainsi été adoptées par les entreprises.
En étudiant l'évolution du concept de la
qualité jusqu'à la stratégie Lean, tout en prenant en
compte l'importance des réglementations présentes au sein de
l'industrie pharmaceutique, nous avons pu soulever une question : La
démarche de Lean Management est-elle compatible avec le respect des
Bonnes Pratiques de Fabrication ?
L'étude de la place du Lean Management dans un
environnement respectant les bonnes Pratiques de Fabrication nous a
poussés à nous questionner sur les opportunités et limites
d'une démarche Lean Management dans un service d'Assurance
Qualité, qui doit respecter les Bonnes Pratiques de Fabrication.
L'enquête, menée à l'aide d'un
questionnaire administré en ligne, a permis de valider
l'intérêt à la fois économique, réglementaire
et humain du Lean pour une industrie pharmaceutique.
Enfin, l'analyse des différentes améliorations
menées dans le service d'Assurance Qualité de Novo Nordisk a
permis de comprendre les avantages d'une telle démarche, en pratique.
73

Table des annexes
Annexe 1 : A3 SPS - Trame 75
Annexe 2 : Base de données issue du questionnaire 78
Annexe 3 : A3-SPS - Retours effectués en retard 80
Annexe 4 : Graphique de suivi des délais - supervision
et retours. 81
Annexe 5 : Communication sur l'importance des APS 84
Annexe 6 : Communication Nécessaire et Suffisant,
diffusé le 9 Avril 2019 85
Annexe 7 : Schéma récapitulatif 86
74

82
Annexe 5
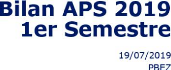

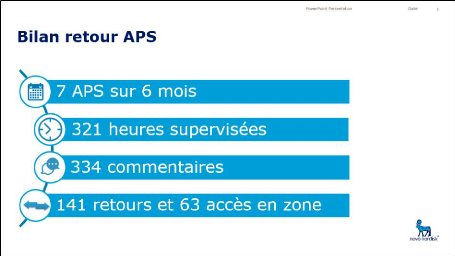
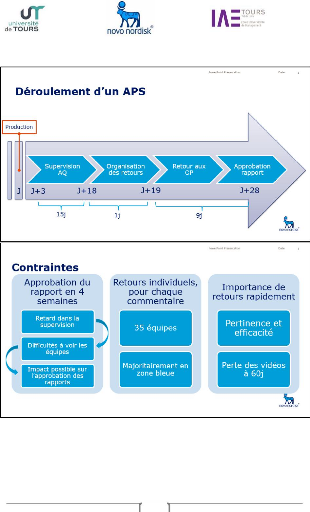
83

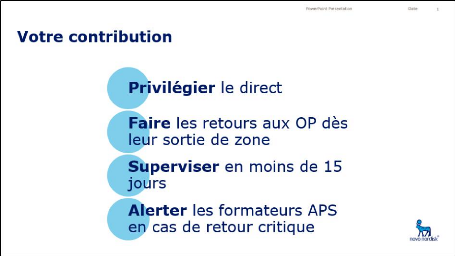
Annexe 5 : Communication sur l'importance des APS
84
|