RESUME
La présente étude porte sur
l'amélioration du rendement de récupération du cobalt en
fractionnant le booster et le tall-oil comme activant, étude se
rapportant au concentrateur de Kolwezi, l'un des sièges de la
Générale des carrières et des mines. Les issues des
opérations dans ce concentrateur sont telles que les rejets usines
contiennent encore les métaux valorisables en taux considérables
par le simple fait que le tall-oil est rarement d'usage au finissage du
concentré de l'ébauchage secondaire.
Cela étant, nous avons tenu en compte une distribution
séquentielle du booster et de tall-oil en simple ébauchage. Pour
ce besoin, l'étude théorique traite les
généralités sur la fragmentation, les
considérations théoriques sur la flottation tout en se
référant aux actuelles pratiques du concentrateur de Kolwezi.
La partie expérimentale consiste en une
caractérisation chimique, minéralogique et granulochimique de
l'alimentation de la flottation du concentrateur de Kolwezi, en une mise en
oeuvre des tests de flottation qui se subdivisent en quatre grandes
catégories qui sont : les essais de flottation dans les conditions du
concentrateur de Kolwezi, les essais de flottation avec le booster
fractionné, les essais de flottation avec le tall-oil fractionné,
enfin les essais des flottation avec les deux activants fractionnés. Et
une brève étude des rejets de différentes
catégories d'essais de flottation ; avec une tentative d'analyse des
résultats dans les différents cas.
Après différents travaux aux laboratoires, la
présente étude nous réserve ce qui
suit :
? En ce qui concerne l'alimentation de la flottation, la
granulométrie est loin de celle retenue théoriquement par la
division du contrôle d'exploitation et ceci nous pousse à dire que
le broyage humide produit en grande quantité les grossiers.
? Les essais de flottation avec le booster fractionné
ne donnent pas de meilleurs résultats.
? Les essais de flottation avec le tall-oil fractionné
nous fournissent de bons résultats, un épuisement sensible du
rejet mais avec un problème de
concentration du manganèse qui va jusqu'autour de 1,5 %
dans le concentré ébauché et un rendement d'environ
61%.
? Quelques essais dans la catégorie du booster et du
tall-oil fractionnés ont été retenus pour une combinaison
de fractions dans le but d'améliorer le rendement de
récupération du cobalt. La combinaison de 25-75-0% du booster et
de 30-0-70% du tall-oil fournit les meilleurs résultats pour cette
étude. Respectivement pour le cobalt et le cuivre, nous avons un
concentré de tête titrant 2,05 et 23,43%, un concentré
ébauché ayant pour teneur 0,77 et 5,06%, un rendement de
récupération en tête de 23,74 et 47% ; en ébauchage,
nous avons obtenu un rendement de 79,16 et 89,8%. En ce qui concerne les rejets
de flottation, nous avons enregistré une teneur de 0,24 % pour le cobalt
et 0,68 % pour le cuivre.

EPIGRAPHE
II
DEDICACES
A vous mes parents Isaac BULAMBO et Hélène
Pétronie MALOBA pour le grand amour, leur éducation et tous les
sacrifices qu'ils ne cessent de consentir pour moi.
A vous mes frères et soeurs Joël BANGA, Elie
KASONGO, Michée KAZADI, Evodie MBUYU, Syntiche SAMBIABO, Léopold
MUTAMBA, Paulin KATSHONGO, Chrysostome MUTOMBO, Bienvenu SANGA, Miradie
Hélène MALOBA ; ce présent travail est pour vous le fruit
de votre compréhension, votre soutien et amour que vous n'aviez
cessé de témoigner à notre égard.
A vous mes nerveux et nièces, voici pour vous le chemin
à emprunter pour arriver à un bonheur et que ceci soit pour vous
un exemple à suivre.
A la famille KABAMBA TSHINGAMBO, soyez rassuré que nos
mots sont sans valeurs pour exprimer notre gratitude envers vous.
A vous mes oncles et tantes.
A vous mes chers amis Nathan KALOMBO et John KAMWENZE pour vos
conseils d'une grande valeur et votre soutien incontestable envers notre
personne.
A vous tous dont les noms ne se trouvent pas cités,
nous vous rassurons que la liste n'est pas exhaustive en vous remerciant pour
toutes les actions engagées à notre faveur.
III
AVANT-PROPOS
Initialement à l'Eternel Dieu des armées, nous
lui rendons grâce, car il ne cesse de nous offrir sans prix le souffle de
vie, lui en qui repose notre prospérité.
Nous adressons nos sincères remerciements à
l'endroit de l'assistant Ingénieur civil Guédally BWEREVU qui en
dépit de ses multiples occupations, a donné le meilleur de
lui-même pour la réussite du présent travail. Nous
rassurons notre estime pour les fructueuses remarques qu'il n'a cessé de
formuler à notre personne. Nos remerciements sont également
adressés par l'intermédiaire du Docteur Ingénieur Civil
Moise MUKEPE, Doyen de la faculté, à tout le corps
académique et enseignant de la faculté polytechnique de
l'Université de Kolwezi pour la formation qu'il ne cesse de mettre
à notre profit.
Aux responsables de la Gécamines, nous
réitérons nos remerciements et particulièrement à
ceux du concentrateur de Kolwezi pour nous avoir accepté de mener nos
études au sein de leur siège.
Dans le même ordre d'idée, nos remerciements vont
tout droit vers l'ingénieur Civil RAMAZANI, Directeur de siège ;
les ingénieurs civils KALENGA MWENZE, et Trésor MIMPIYA pour
leurs encadrements tout au long de la période de recherches, sans devoir
oublier Messieurs MWAMBA KALENGA, David TSHOTA, Patrick MUPENDA, NSENGA MUYOMBO
ainsi que Madame Brigitte.
Au terme de notre formation de gradué en sciences
appliquées et par ce travail de fin de cycle qui est le couronnement de
plusieurs années de labeur, qu'il nous soit permis de nous acquitter de
cet agréable devoir. Celui de remercier un nombre important des
personnes qui méritent notre profonde gratitude pour leurs contributions
non seulement dans l'élaboration de ce présent travail mais
surtout à l'édification de la formation reçue.
Que nos ainés scientifiques ingénieurs civils :
Richard KATONGE, Gabriel MWANASAYI, Gloire KAMANDA, Guellord NGAMBA,
connaissances et compagnons de lutte : Joël MAYAVA, Christian TSHAKAMBOWA,
Ophélie MWENDO, Hugues KANDA, Francie FATUMA, Grace SHIMBA, Gentil
MUFINDA, Yves MULONGA, Jacques KABUSU, trouvent l'expression de notre gratitude
eu égard à leur soutien incontestable.
IV
TABLE DES MATIERES
RESUME 1
EPIGRAPHE I
DEDICACES II
AVANT-PROPOS III
TABLE DES MATIERES IV
LISTE DES AVREVIATIONS ET ACRONYMES VII
LISTE DES FIGURES VIII
LISTE DES TABLEAUX IX
LISTE DES ANNEXES X
INTRODUCTION 1
CHAPITRE I. GENERALITES SUR LA FRAGMENTATION 3
I.1. INTRODUCTION 3
I.2. OBJECTIFS ET PROCESSUS DE LA FRAGMENTATION 4
I.2.1. OBJECTIFS DE LA FRAGMENTATION 4
I.2.2. PROCESSUS DE LA FRAGMENTATION 5
I.3. PROBLEME DE LA FRAGMENTATION 5
I.4. APPROCHE DU PROCESSUS DE FRAGMENTATION 6
I.5. EVALUATION DU RENDEMENT D'UN CIRCUIT BROYAGE-
CLASSIFICATION 7
I.6. OBJECTIFS ET APPAREILLAGE DE LA CLASSIFICATION 8
I.6.1. OBJECTIFS DE LA CLASSIFICATION 8
I.6.2. APPAREILLAGE DE LA CLASSIFICATION 8
I.7. LOIS DE LA DISTRIBUTION GRANULOMETRIQUE DES PRODUITS BROYES
... 10
CHAPITRE II. CONSIDERATIONS THEORIQUE SUR LA FLOTTATION 12
II.1. GENERALITES 12
II.2. TYPES DE FLOTTATION 13
II.2.1. FLOTTATION A L'HUILE 13
II.2.2. FLOTTATION PELLICULAIRE 13
II.2.3. FLOTTATION A LA MOUSSE 13
II.3. MECANISME DE FLOTTATION 13
II 3.1. LA POLARITE DES MINERAUX 13
V
II.3.2. LES INTERFACES 14
II.3.2.1. INTERFACE SOLIDE-LIQUIDE S-L 15
II.3.2.2. INTERFACE LIQUIDE-GAZ 15
II.3.2.3. LE SYSTEME SOLIDE-LIQUIDE-GAZ 16
II.3.2.4. ANGLE DE CONTACT 16
II.4. LES REACTIFS DE FLOTTATION 17
II.4.1. LES COLLECTEURS 17
II.4.2. LES ACTIVANTS ET LES DEPRIMANTS 18
II.4.3. LES MOUSSANTS 19
II.4.4. LE MODIFICATEUR DU MILIEU 19
II.5. ADSORPTION ET ABSORPTION DES COLLECTEURS 20
II.5.1. TYPE D'ADSORPTION 20
II.5.2. THEORIE SUR LA THERMODYNAMIQUE DE L'ADSORPTION 20
II.6. CINETIQUE DE LA FLOTTATION 21
II.7. DOSAGE ET DISTRIBUTION DES REACTIFS 22
II.7.1. STRATEGIE D'AJOUT DES REACTIFS 22
II.7.2. LE DOSAGE DES REACTIFS 22
II.7.3. LA DISTRIBUTION DES REACTIFS 22
II.8. PARAMETRES DE LA FLOTTATION 22
II.9. EVALUATION D'UNE OPERATION DE FLOTTATION 24
II.10. COMPROMIS ENTRE RENDEMENT DE RECUPERATION ET TAUX DE
CONCENTRATION 25
CHAPITRE III. APPROCHE EXPERIMENTALE 26
III.1. INTRODUCTION 26
III.2. ECHANTILLONNAGE 26
III.2.1. PRELEVEMENT D'ECHANTILLON 26
III.2.2. PREPARATION DE L'ECHANTILLON 26
III.3. CARACTERISATION DE L'ECHANTILLON 27
III.3.1. CARACTERISTIQUE CHIMIQUE 27
III.3.2. CARACTERISATION MINERALOGIQUE 27
III.4. MATERIELS UTILISES 27
III.5. MODE OPERATOIRE 28
III.6. DOSAGES DES REACTIFS UTILISES 29
CHAPITRE IV. PRESENTATION ET ANALYSE DES RESULTATS 30
IV.1. INTRODUCTION 30
VI
IV.2. ANALYSE GRANULOCHIMIQUE DE L'ALIMENTATION FLOTTATION 30
IV.3. TESTS DE FLOTTATION 31
IV.3.1. OBJECTIFS DES ESSAIS DE FLOTTATION 31
IV.3.2. APPRECIATION DE L'EFFICACITE DES ESSAIS DE FLOTTATION
31
IV.3.3. CONDUITE DES ESSAIS DE FLOTTATION AU LABORATOIRE 32
IV.4. RESULTATS DES ESSAIS DE FLOTTATION AVEC EBAUCHAGE 32
IV.4.1. ESSAIS DE FLOTTATION DANS LES CONDITIONS DE REFERENCE
32
IV.4.2. ESSAIS DE FLOTTATION AVEC LE BOOSTER FRACTIONNE 33
IV.4.3. ESSAIS DE FLOTTATION AVEC LE TALL OIL FRACTIONNE 36
IV.4.4. ESSAI DE FLOTTATION AVEC LE BOOSTER ET LE TALL- OIL
FRACTIONNES 38
IV.5. DISCUSSIONS 40
IV.6. ANALYSES GRANULOMETRIQUES DES REJETS 41
CONCLUSION 43
PERSPECTIVES 44
REFERENCES BIBLIOGRAPHIQUES 45
VII
LISTE DES AVREVIATIONS ET ACRONYMES
RDC : République Démocratique du Congo
GCM : Générale des carrières et des
mines
KZC : Concentrateur de Kolwezi
UCK : Usine à cuivre de Kolwezi
EMT : Etudes métallurgiques
DCE : Division de contrôle d'exploitation
OF: Over-flow
UF: Under-flow
BO: Booster
TO: Tall-Oil
VIII
LISTE DES FIGURES
Figure 1. Le système solide -liquide -gaz 15
Figure 2. Angle de contact du système S-L-G 16
Figure 3. Dispositif expérimental des essais de
flottation 28
Figure 4. Schéma de flottation avec un simple
ébauchage des concentrés 32
Figure 5. Evolution du rendement de récupération
du Cobalt en référence 33
Figure 6. Evolution du rendement de récupération
du Cobalt en présence du Booster 35
Figure 7. Evolution du rendement de récupération
en présence du Tall-oil fractionné 37
Figure 8. Evolution du rendement de récupération
du cobalt en présence du Booster et Tall- oil
fractionnés. 39
Figure 9. Variation de la teneur du Cobalt dans les
différentes tranches des rejets 42
IX
LISTE DES TABLEAUX
Tableau 1. Classification des minéraux en fonction de
leur degré de polarité 14
Tableau 2. Classification générale des
collecteurs 18
Tableau 3. Analyse chimique de l'échantillon 27
Tableau 4. Doses des réactifs au concentrateur de
Kolwezi 29
Tableau 5. Analyse granulochimique du composite alimentant la
flottation. 31
Tableau 6. Résultats synthétiques de flottation
en référence 33
Tableau 7. Résultats synthétiques de flottation
avec le Booster fractionné 34
Tableau 8. Résultats synthétiques de flottation
avec le Tall-oil fractionné 37
Tableau 9. Résultats synthétiques de flottation
avec le Booster et Tall- oil fractionnés 39
Tableau 10. Résultats synthétiques comparatifs
41
Tableau 11. Analyses granulochimiques des rejets de flottation
41
X
LISTE DES ANNEXES
Annexe A : Essai de flottation dans les conditions de KZC A
Annexe B : Essais de flottation avec le Booster
fractionné ...B
Annexe C : Essais de flottation avec le Tall-oil
fractionné .C
Annexe D : Essais de flottation avec le Booster et le Tall
-oil fractionnés E
Annexe E : Analyses granulochimiques de rejets de flottation
en utilisant le Booster, le Tall-
oil, le Booster et le Tall -oil fractionnés F
Annexe F : Flow-sheet général du concentrateur
de Kolwezi H
1
INTRODUCTION
Le concentrateur de Kolwezi (KZC), un des sièges de la
Générale des carrières et des mines (GCM), débute
ses opérations par un concassage suivi respectivement d'un broyage
humide, d'une séparation de la gangue du minéral utile, d'une
décantation et termine par une filtration avec l'obtention d'un
gâteau appelé concentré titrant 15 à 20% cuivre, 2
à 3% cobalt avec quelques impuretés telles que le
manganèse et le fer ayant comme teneur en moyenne respectivement 2 et 9
%.
La division de contrôle d'exploitation (DCE) de ce
siège mène depuis un temps une série d'études pour
la bonne marche du dit concentrateur et surtout en particulier celle de la
section de flottation. La granulométrie, le temps de flottation, la dose
et la distribution des réactifs sont quelques paramètres qui font
l'objet de ces études.
Dans ce Concentrateur, le booster et le tall- oil sont
utilisés comme activant du cobalt et sont ajoutés respectivement
au conditionnement en amont de l'ébauchage primaire et à la ligne
de finissage du concentré de l'ébauchage secondaire, laquelle
ligne n'est pas régulièrement opérationnelle suite
à un problème technique, ce qui concomitamment, diminue la
récupération du cobalt par le simple fait que le tall- oil ne se
trouve plus en circuit. Ainsi, une distribution séquentielle du booster
et du tall- oil comme celle du sulfudrate de sodium se laisse voir donc
importante pour contribuer à l'amélioration de la
récupération de ce métal qui se trouve en une marge
importante dans le rejet global. D'où l'intitulé du
présent travail de fin de cycle : Amélioration du rendement de
récupération du cobalt en fractionnant le booster et le tall- oil
comme activant.
Plusieurs paramètres peuvent entrer en jeu pour
l'amélioration de la récupération de cuivre et cobalt
comme minéraux de valeur, mais dans notre cas, nous nous limitons
objectivement à la distribution fractionnée du booster et du
tall-oil sur la ligne d'ébauchage.
Pour y arriver, la présente étude est
subdivisée en deux grandes parties : La première traite les
généralités sur la fragmentation et les
considérations théoriques sur la flottation. La seconde partie,
purement pratique, s'attèle sur les approches expérimentales, la
présentation et l'analyse des résultats.
2
Enfin une conclusion et des perspectives seront
formulées pour mieux améliorer le rendement de
récupération du cobalt et sans oublier celui du cuivre car le
cuivre et le cobalt sont souvent ensembles.
3
CHAPITRE I. GENERALITES SUR LA FRAGMENTATION
I.1. INTRODUCTION
La matière abattue au cours de l'exploitation du
gisement est constituée de blocs plus ou moins volumineux en fonction
des caractéristiques du gisement (nature de la minéralisation,
compacité, fracturation naturelle...) et du mode d'abattage
utilisé.
Pour différentes raisons, il est
généralement important de poursuivre la réduction
dimensionnelle des blocs :
? permettre la manutention, le stockage et le transport plus
aisé du minerai abattu ;
? les matériaux utilisés en génie civil
(granulats pour bétons,...) doivent avoir des caractéristiques
granulométriques bien déterminées.
? les minerais métalliques font l'objet de traitements
chimiques (pyro et hydro) et certaines substances minérales sont
utilisées dans des processus chimiques. Une augmentation de la surface
spécifique permet d'accroitre la cinétique des réactions
chimiques ou de donner accès aux phases minérales à mettre
en solution (Hydro métallurgie). (NDOLWA.C ; 2014)
Le terme fragmentation définit toute opération
conduisant à la réduction dimensionnelle des grains d'un
matériau. Elle se fait souvent en deux grandes opérations : le
concassage et le broyage.
- Le concassage
On utilise souvent le terme concassage lorsque
l'opération de fragmentation des minéraux de roches s'effectue
sur de dimensions métriques aux centimétriques. Ce type de
fragmentation qui constitue la première partie du processus de
fragmentation d'un matériau après l'extraction du gisement, est
généralement obtenu par la compression et flexion de la
matière entre les surfaces rigides ou bien encore par l'impact de
celle-ci sur de telles surfaces. Le concassage se fait souvent dans un milieu
sec. (Corneille EK et Al. Masson ; 1973)
4
- Le broyage
Le broyage est utilisé lorsque l'opération
concerne des particules dont la taille maximale est située aux alentours
du centimètre. Le broyage est obtenu par impact ou par abrasion entre la
matière à fragmenter et des corps broyant libres dans l'appareil
(boulet, barres...). Le broyage est souvent réalisé en deux
grandes étapes et avec un appoint d'eau pour palier à des
problèmes environnementaux et à des pertes des particules.
Un circuit de fragmentation peut comporter 3 à 6 stades
et ceci est lié à la granulométrie recherchée du
minerai. Dans le cas du concentrateur de Kolwezi, nous avons cinq stades qui
sont dans plusieurs usines de concentration ; on distingue :
- le concassage primaire : il fait la réduction
jusqu'à des dimensions de l'ordre de 100 à 150 mm. A ce niveau le
concentrateur de Kolwezi utilise un concasseur à mâchoires du type
Arbed ;
- le concassage secondaire : à ce niveau nous avons la
réduction de 150 mm jusqu'à une dimension de 50 mm ;
- le concassage tertiaire : il fait aussi office d'une
granulation, à ce stade, au Concentrateur de Kolwezi on a une dimension
de d80 qui vaut 19mm. Les moins de 19 mm sont envoyés au stockage et le
plus forment un circuit fermé au concassage ;
- le broyage grossier : depuis environ 12 à 25 mm
jusqu'à des dimensions de l'ordre de 1mm. A ce stade, le concentrateur
de Kolwezi utilise le broyeur à barres (Road-Mill 45) ;
- le broyage fin : depuis environ 1mm jusqu'à des
dimensions de l'ordre de 200 microns. Le broyage fin appelé aussi
broyage secondaire ; est l'étape finale de la fragmentation au
concentrateur de Kolwezi.
I.2. OBJECTIFS ET PROCESSUS DE LA
FRAGMENTATION
I.2.1. OBJECTIFS DE LA FRAGMENTATION
La fragmentation a pour objectif la conduite à un
état granulométrique acceptable à une utilisation
spécifique et à un traitement ultérieur à
appliquer. En traitement des minerais, la fragmentation a aussi comme objectif
la conduite à une libération satisfaite des différents
minéraux pour mieux exécuter l'opération de
séparation.
5
En métallurgie, la fragmentation est d'une importance
capitale car elle conditionne la cinétique des opérations pour
lesquelles une finesse de minerai est souvent requise. (Corneille EK et Al.
Masson ; 1973).
I.2.2. PROCESSUS DE LA FRAGMENTATION
La fragmentation résulte des chocs, des impacts des
corps broyant, des frottements sur les grains de minerais. Un meilleur
rendement énergétique, la suppression des poussières sont
les principaux avantages qui poussent le broyage qui est souvent l'étape
qui précède la concentration par flottation à se faire en
voie humide sur une pulpe.
Pour sa réalisation, la fragmentation fait intervenir
un équipement et un appareillage qui exécutent différentes
tâches spécifiques et arrivent à fournir un résultat
meilleur en cas de contrôle parfait des paramètres fixés.
Il est important en préparation des minerais de limiter au maximum le
surbroyage qui est un problème sérieux car il conduit souvent
à l'utilisation des broyeurs courts en circuit fermé avec un
recyclage trop élevé de la charge circulante par les
classificateurs. (Corneille EK et Al .Masson ; 1973)
I.3. PROBLEME DE LA FRAGMENTATION
La fragmentation ne sait pas fournir des matériaux
ayant une même dimension ainsi qu'une même forme. Souvent elle
donne des particules de toutes formes dont les dimensions s'échellent
entre la dimension voulue et la dimension non désirée.
Les fines particules formées lors de la fragmentation
peuvent varier largement et dépasser le minimum inévitable quand
les contraintes appliquées au matériau pour le fragmenter sont
très énormes ou s'exercent sur des particules déjà
fragmentée ou quand les particules subissent une abrasion par
frottement. Ce phénomène de production excessive des fins est
appelé surbroyage. (Blazy P ; 1970)
En préparation des minerais, quelques raisons nous
montrent que le surbroyage
est très nocif :
- Une grande consommation inutile d'énergie : le
concentrateur dépense une quantité importante d'énergie
pour la production de fines particules ;
- avec des fines particules, les opérations de
concentration ne sont pas bien assurées.
6
Une usine de préparation des minerais peut fonctionner
à perte par un surbroyage surtout si cette dernière traite les
minerais pauvres. On peut avoir un surbroyage considérable lorsque la
fragmentation s'effectuerait de telle sorte qu'à la sortie de l'appareil
utilisé tous les grains du matériau soient réduits en
dessous de la limite fixée. (Corneille EK et Al. Masson ; 1973)
Pour éviter ces problèmes de surbroyage, il
convient :
- D'opérer la fragmentation non pas un une seule
étape mais plutôt en plusieurs étapes dès que la
réduction volumétrique à obtenir est importante. Chaque
appareil pourra ainsi être bien adapté aux dimensions des grains
qu'il doit réduire ;
- A chacune des étapes préliminaires, de ne
laisser entrer dans l'appareil que les morceaux qui doivent y être
broyés et d'éliminer préalablement par une série de
tamisage les particules dont les dimensions sont déjà
inférieures à celle que l'on se propose avoir à cette
étape ;
- Laisser sortir du broyeur une quantité des grains
trop gros, non encore réduits à la dimension voulue puis de les
séparer des autres et de les rebroyer soit dans un autre broyeur.
La marche avec retour dans le même appareil s'appelle
circuit fermé et la proportion de matière recyclée est la
charge circulante. Celle-ci est d'une importance capitale que la
quantité d'alimentation nouvelle ; le rapport entre les deux peut
atteindre et même dépasser 400%.
Le problème fondamental de la fragmentation consiste
dès lors dans le choix du circuit opératoire qui permettra de
réduire économiquement la matière à la dimension
voulue sans un surbroyage excessif.
I.4. APPROCHE DU PROCESSUS DE FRAGMENTATION
L'impact économique de la fragmentation est très
considérable. Le coût des opérations est
élevé et la matière qu'il faut fragmenter est de nature
variée. En minéralurgie il faut en outre fragmenter toute la
gangue qui accompagne les utiles. Dans ces conditions, l'étude
scientifique du processus de fragmentation présente un
intérêt de grande importance car il n'est pas douteux qu'une
connaissance plus approfondie du phénomène permettrait
d'améliorer les méthodes et d'obtenir des rendements meilleurs
à moindres frais.
7
Cette étude se révèle forte complexe et
difficile, elle est loin d'être terminée car l'évolution
scientifique fait toujours des merveilles chaque jour.
De ce fait, quelques horizons s'ouvrent aux chercheurs :
- La recherche d'un modèle mathématique de la
fragmentation par l'étude de la cinétique de l'opération
;
- La recherche d'une relation entre l'énergie
nécessaire à la fragmentation et la réduction
volumétrique obtenue ;
- L'étude de la structure de la matière, de la
thermodynamique de la fragmentation et de la propagation des fractures.
I.5. EVALUATION DU RENDEMENT D'UN CIRCUIT
BROYAGE-CLASSIFICATION
Fixer un schéma type universel des opérations de
fragmentation n'a jamais été possible. Chaque traitement des
matières minérales est un cas particulier et les schémas
varient suivant la nature des matériaux, les tonnages à
alimenter, les opérations de concentration envisagées. Il est
fréquent par ailleurs que les circuits de fragmentation et de
concentration se fusionnent l'un en l'autre.
La nécessité de la marche en circuit
fermé au stade ultime du broyage a été longuement
explicitée. Il subsiste cependant encore une controverse auprès
des théoriciens et praticiens du broyage quant à la proportion
optimale de charge circulante, à savoir celle qui rend la
capacité maximale et la dépense énergétique
minimale. D'aucuns sont partisans d'une forte charge circulante (400% et plus),
d'autres d'une faible charge circulante (100 à 200%).
Une étude basée sur la transposition des
résultats obtenus dans un circuit ouvert au circuit fermé partant
des courbes de débits d'alimentation et de charges circulantes pour les
différents tonnage de production d'un broyeur laisse voir qu'à
une augmentation de la charge circulante correspond une alimentation
parallèle du rendement de classification, si bien qu'au-dessus de 200%
de charge circulante, l'avantage devient insignifiant. Cette étude qui
tente d'apporter une solution au problème de la charge circulante est
dite ? étude de HUKKI ?. (Corneille EK et Al. Masson ; 1973).
8
I.6. OBJECTIFS ET APPAREILLAGE DE LA
CLASSIFICATION
I.6.1. OBJECTIFS DE LA CLASSIFICATION
La classification est réalisée pour une
séparation des particules ayant une dimension inférieure à
une dimension de référence par une voie indirecte sur le plan
industriel. La sédimentation, l'élutriation différentielle
suivant la dimension des particules sont les propriétés sur
lesquelles la classification est basée.
La classification donne un classement par équivalence
de vitesse de dépôt où interviennent concurrentiellement la
dimension mais aussi la forme et la masse spécifique. Dans les
classificateurs, les particules fines à vitesse de sédimentation
lente sont entrainées par le débordement de la pulpe ; ce produit
s'appelle la surverse (OF). Au contraire les particules de grande dimension
sédimentent vers le fond dans un produit dénommé sous
verse (UF).
I.6.2. APPAREILLAGE DE LA CLASSIFICATION
Il existe plusieurs catégories d'appareil pour
effectuer une classification en voie humide ou voie sèche. Lors d'une
préparation des minerais, nous faisons recours aux classificateurs en
pulpes à savoir :
? Classificateurs hydrauliques à sédimentation ;
? Classificateurs mécaniques ;
? Les classificateurs hydrauliques à élutriation
;
? Les classificateurs hydrauliques à centrifugation :
deux grandes types d'appareils appartiennent à cette classe de
classificateurs, il s'agit des centrifuges et des hydrocyclones.
Au concentrateur de Kolwezi, l'hydrocyclone est l'appareil de
classification utilisé. I.6.2.1. LES HYDROCYCLONES
L'hydrocyclone est constitué d'un cylindre court
plongé vers le bas par un cône. Le produit à classer est
injecté en pulpe sous une pression tangentielle à la partie
supérieure de l'appareil et suit une trajectoire en spirale. (NDOLWA C ;
2014)
9
I.6.2.2. MECANISME FONCTIONNEL D'UN HYDROCYCLONE
Sous le fait d'une alimentation tangentielle, il y a naissance
des forces centrifuges dans l'appareil créant deux flux en spirale
à contre -courant. Une des spirales est descendante jusqu'à la
pointe terminale du cône l'autre est montante vers le diaphragme de
vortex. Entre les deux flux, il y a donc une zone où la vitesse
verticale est nulle, un filet d'air dont l'importance dépend des
caractéristiques de fonctionnement se forme alors au coeur de l'appareil
le long de l'axe central.
Dans un hydro cyclone, l'eau et les particules constitutives
de la pulpe sont soumises à des forces qui leur confèrent un
mouvement ayant trois composante : une composante verticale suivant l'axe de
l'appareil une composante tangentielle de rotation et une composante radiale
perpendiculaire à l'axe. (BANKA, 2015)
Pour ce qui concerne l'eau de la pulpe, le diamètre
décroissant du cône lui confère une composante radiale
centripète. Alors une particule sera centrifugée si sa vitesse
radiale est supérieure à la vitesse centripète radiale de
l'eau, elle ira se placer dans la spirale descendant vers l'apex. Si la vitesse
radiale est inférieure à celle de l'eau ; elle sera
entravée vers l'axe du cyclone et prise dans la spirale montant vers le
vortex.
I.6.2.3. PARAMETRES D'HYDROCYCLONAGE
1. Paramètres de marche de l'hydro
cyclone
· partie cylindrique : diamètre DC et la hauteur
HC
· injection : diamètre Di et éventuellement
l'angle du cône
· diaphragme du vortex : diamètre Dv et la hauteur
Hv
· partie conique : angle du Cône
· diamètre de l'apex : Da
2. Paramètres définissant la
pulpe
· le débit ;
· la masse spécifique apparente
· concentration en solide
· granulométrie des solides
· la pression d'injection.
(3)
10
I.7. LOIS DE LA DISTRIBUTION GRANULOMETRIQUE DES PRODUITS
BROYES
En observant à des stades différents d'une
opération de fragmentation les courbes granulométriques d'un
matériau, on remarque une certaine similitude et même un certain
parallélisme entre les différentes courbes obtenues. Cette
similitude laisse présager l'existence d'une loi entre les proportions
pondérales et les dimensions granulométriques des grains.
Plusieurs chercheurs scientifiques ont proposé
différentes lois pour l'interprétation d'une opération
granulométrique. Parmi ces lois existantes nous pouvons distinguer ce
qui suit :
? Loi de GAUDIN SCHUHMANN
GAUDIN SCHUHMANN, a formulé une relation la plus
utilisée en préparation des minerais des métaux non
ferreux et qui s'énonce comme suit :
(1)
Où P est la proportion cumulée de passant
à la maille de dimension d et où a et k100 et
sont deux paramètres indépendantes.
Les courbes granulométriques pour lesquelles cette
relation est observée sont figurées par une droite sur le
diagramme bi-logarithmique. Dans ce cas a est la pente de la droite et
k100, la dimension du point de rencontre de la droite avec
l'ordonnée 100%. On observe en général que de nombreuses
courbes granulométriques sont assimilables à une droite, puis
s'incurvent au-dessus de K80 , c'est ce qui justifie une autre forme de la
relation de GAUDIN SCHUHMANN :
(2)
? Loi de ROSIN-RAMMLER
C'est aussi une loi fortement utilisée et s'annonce comme
suit :
11
Où R est la proportion cumulée de retenu
à la maille de dimension d et où , k sont deux paramètres
indépendants. Parfois la relation de ROSIN-RAMMLER est meilleure que
celle de GAUDIN SCHUHMANN pour les produits fins, pour le charbon et certains
minerais de fer.
12
CHAPITRE II. CONSIDERATIONS THEORIQUE SUR
LA FLOTTATION
II.1. GENERALITES
La flottation est une méthode de séparation de
matières solides en pulpe qui consiste à former avec certains
minéraux un complexe plus léger que l'ensemble restant sur lequel
ce complexe peut flotter et dont il peut facilement être
séparé. (Corneille EK et Al .Masson ; 1973)
Le principe de la flottation est basé sur les
propriétés hydrophobes et aérophiles des surfaces solides.
Ces propriétés peuvent être naturelles dans la pulpe
lorsque de l'air est injecté sous forme de petites bulles dans un tel
milieu, et se produit un transport très sélectif des particules
hydrophobes. Les particules présentant des surfaces hydrophobes se
fixent aux bulles d'air, une fois en contact avec ces dernières. Ce
phénomène est dû à la grande affinité des
surfaces hydrophobes pour l'air dont la nature est non polaire. Les bulles
d'air entrainent ces particules jusqu'à la surface de la pulpe où
elles forment une mousse chargée. Par contre, les particules
présentant des surfaces hydrophiles ne se lient pas aux bulles d'air et
restent en suspension dans la pulpe. Les produits de la flottation sont le
concentré et le rejet.
La pulpe doit être préparée en fonction
des substances à concentrer et cette préparation repose
principalement sur la granulométrie des particules, l'ajout de
différents réactifs dont les moussants, les collecteurs, les
déprimants et les activant.
La stabilité de la mousse est assurée par les
moussants. Les collecteurs ont pour rôle d'adhérer aux surfaces
des particules désirées afin de les rendre hydrophobes et
aérophiles. Les activants altèrent les surfaces des particules
afin de les rendre plus susceptibles à l'action d'un collecteur. En
flottation, le pH est généralement utilisé pour modifier
l'activité de plusieurs réactifs. Il est donc important de
corriger la valeur du pH en fonction de réactifs utilisés.
(Gosselin A ,1999)
13
II.2. TYPES DE FLOTTATION II.2.1. FLOTTATION A
L'HUILE
L'huile utilisée en grande quantité
empêche certains minéraux d'être mouillés par l'eau
et les maintient ainsi dans un complexe léger recueilli à la
surface du liquide. (Corneille EK et Al .Masson ; 1973)
II.2.2. FLOTTATION PELLICULAIRE
Cette forme de flottation consiste à amener les
minéraux au contact de l'eau et sont mouillés à des
vitesses variables. Le phénomène peut être vrai si les
minéraux sont entourés d'une fine pellicule d'huile qui se fixe
préférentiellement sur des minéraux comme des sulfures par
exemple. (BOUCHARD S ; 2001)
II.2.3. FLOTTATION A LA MOUSSE
La flottation à la mousse est une forme de flottation
qui est appliquée dans une pulpe où les particules ont une
dimension de 74 um. Dans cette pulpe, il y est injecté de l'air qui
forme des bulles d'air, une fois le contact entre les bulles d'air et les
particules finement broyés est réalisé par
l'intermédiaire des réactifs chimiques tel que les collecteurs,
les moussants ; Il se forme une mousse chargée qui par le trop plein
arrive à déborder et à être recueilli dans un
chenal. Ce type de flottation est le plus utilisé dans de grands
concentrateurs et particulièrement au concentrateur de Kolwezi où
nous avons pu mener nous investigations.
II.3. MECANISME DE FLOTTATION
II 3.1. LA POLARITE DES MINERAUX
Lorsqu'on concentre les minéraux par des
méthodes physiques, leur nature chimique a peu d'importance. Les
propriétés d'intérêt sont plutôt
macroscopiques, telle la masse volumique.
Par contre, lorsqu'on concentre les minerais par flottation,
la nature chimique revêt une importance majeure pour la
compréhension des mécanismes de flottation. Ainsi une
classification des minéraux en oxydes, silicates, sulfures, carbonates,
etc. devient un préalable à la compréhension des
mécanismes en cause.
14
De façon générale les minéraux
sont aussi classés selon leur degré de polarité comme
présenté dans le tableau ci-dessus.
Tableau 1. Classification des minéraux en
fonction de leur degré de polarité
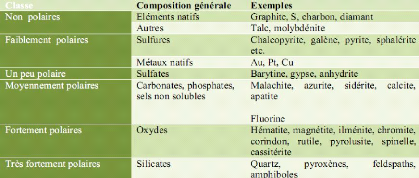
Un minéral est considéré être
polaire lorsqu'il comporte des sites éparpillés sur sa surface
dont la charge électrique résiduelle est majoritairement
positive, adjacents à des sites dont la charge électrique
résiduelle est plutôt négative. Ces sites positifs et
négatifs sur la surface des minéraux proviennent de la rupture de
leur réseau cristallin lors des opérations de fragmentation, les
minéraux non polaires n'en possèdent pas, ou très peu sur
sa surface.
Les surfaces de minéraux polaires réagissent
fortement avec les molécules d'eau, avec les ions, et les
molécules hétéro polaires. Ces surfaces sont dites
hydrophiles ou aérophobes. Au contraire, les surfaces de minéraux
non polaires n'attirent pas les molécules d'eau, ni des ions, ni les
composés hétéro polaires et ne sont pas très
actives. Ce sont des surfaces hydrophobes ou aérophiles.
II.3.2. LES INTERFACES
En flottation, lorsqu'une particule du minéral utile,
en suspension dans une solution aqueuse, est naturellement hydrophobe ou bien
rendue hydrophobe par l'adsorption d'un collecteur, elle peut adhérer
à une bulle d'air provenant de l'injection d'air dans la pulpe. Dans le
système obtenu, il y a trois phases en présence et, au contact
entre différentes phases, on trouve trois interfaces :
? L'interface solide-liquide (S-L) ? L'interface liquide-gaz
(L-G)
15
? L'interface solide-gaz (S-G)
Au contact entres les interfaces L-G, S-L, S-G, il existe une
ligne courbe appelée système SL-G.
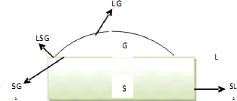
Figure 1. Le système solide -liquide
-gaz
II.3.2.1. INTERFACE SOLIDE-LIQUIDE S-L
L'interface S-L est l'interface la plus importante en
flottation. Elle est caractérisée à la fois par des
prénommes électriques et d'absorption.
a) Le phénomènes électrique : Ce
phénomène est caractérisé par le potentiel
zêta (æ) qui est un paramètre important pour la flottation
et la flottabilité des minéraux car il définit la
densité d`adsorption d'un collecteur à la surface d'un
minéral. Il est influencé par : le pH (pH acide æ>0, pH
basique æ<0 et pour æ=0 on a le pH de point de charge
zéro), le minéral, l'élément de substitution dans
le minéral, l'ions déterminant du potentiel zêta, l'ion
commun, les ions activant, la concentration des électrolytes
indifférents, du collecteurs, de la longueur de la chaine
carbonée.
b) L'adsorption : Ce phénomène probablement
très important se produit à l'interface S-L. Elle dépend
de la concentration de réactifs, de la longueur de la chaine
carbonée, de la température, du pH d'adsorption chimique, et de
la présence d'oxygène.
II.3.2.2. INTERFACE LIQUIDE-GAZ
L'interface liquide- gaz met en relation la solution aqueuse
avec la bulle d'air utilisée pour entrainer les particules hydrophobes
au concentré. Les propriétés de cet interface sont
influencées majoritairement par un composé tensio-actif
appelé moussant ou agent moussant.
16
En flottation les agents moussant les plus importants sont
ceux qui font baisser de façon importante la tension superficielle
lorsqu'ils sont utilisés en faible quantité en solution. Du point
de vue chimique, les moussants sont des molécules hétéro
polaires.
II.3.2.3. LE SYSTEME SOLIDE-LIQUIDE-GAZ
Les interfaces telles qu'étudiées
précédemment n'existent pas en réalité, mais
plutôt une relation étroite entre elles. Lorsqu'une bulle d'air et
une particule solide, toutes les deux en suspension dans une solution aqueuse,
entrent en contact l'une avec l''autre, la courbe délimitée aux
frontières des trois interfaces s'appelle système triple ou
système solide-liquide-gaz. Les propriétés de ce
système, soit l'angle de contact et l'adhésion, sont très
important en flottation et c'est le comportement de ce système qui
permet de déterminer la flottabilité d'une espèce
minérale.
II.3.2.4. ANGLE DE CONTACT
Les caractéristiques du système S-L-G sont
décrites par l'angle de contact mesuré dans la phase aqueuse,
entre l'interface solide-liquide et l'interface liquide-gaz. Le sommet de
l'angle est situé en un point sur la courbe du système triple.
L'expression angle de contact indique à quel point le contact
donné est réussi entre une bulle d'air et un minéral.
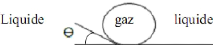
Figure 2. Angle de contact du système
S-L-G
Lorsque O=0, ou très petit, le minéral est
hydrophile et on dit que la solution mouille le solide. Par contre un angle O
très élevé, signifie que la particule est hydrophobe, donc
qu'elle est apte à être attachée solidement à la
bulle d'air, donc flottable. Ainsi, les minéraux dont l'angle de contact
naturel est de plus de 80° sont naturellement hydrophobes et pourraient
généralement être flottés facilement, sans
collecteur. Les autres minéraux sont hydrophiles et nécessitent
l'ajout d'un collecteur pour accroitre l'angle de contact et leur permettre de
flotter.
17
II.4. LES REACTIFS DE FLOTTATION
Les réactifs de flottation représentent une
partie importante des coûts du processus de traitement et sont
utilisés à différentes étapes du
procédé pour assurer la séparation. Selon la composition
du minerai à traiter, les stratégies d'addition des
réactifs peuvent être très différentes.
La flottation fait appel à cinq types de
réactifs : le collecteur, l'activant, le déprimant, le
régulateur du pH qui agit à la surface des minéraux, et le
moussant agit sur l'hydrodynamique du système pulpe-écume.
II.4.1. LES COLLECTEURS
Les collecteurs confèrent l'hydrophobicité
à la surface des particules à récupérer de
façon à permettre leur séparation des minéraux de
gangue. Les collecteurs sont des produits chimiques aux molécules
complexes. Ils comportent un premier composant responsable de l'accrochage du
produit à la surface de la particule soit par réaction chimique
ou par attraction électrostatique. La deuxième partie est une
chaine organique immixible dans l'eau qui induit l'hydrophobicité
à la particule.
Les collecteurs sont regroupés en 3 grandes
catégories à savoir : les collecteurs anioniques, les collecteurs
cationiques et ceux non ioniques.
II.4.1.1. LES COLLECTEURS ANIONIQUES
Ce type de collecteurs est utilisé pour les sulfures,
les métaux natifs et les minéraux oxydés ayant subi une
sulfuration (traitement préalable à l'aide d'une solution de NaSH
par exemple au concentrateur de Kolwezi) et possèdent très
généralement dans leurs groupes polaires un ou plusieurs atomes
de soufre qui assurent la liaison avec le minéral. Ce sont
principalement :
- Les xanthates (alkyl di thiocarbonates) ;
- Les aérofloats (aryl-alkyl-dithiophosphates) ;
- Et d'autres dont l'emploi est moins souvent dont les
mercaptans, le mercapto-benzothiazote,...
Les oxydes ont pour principaux deux classes de collecteurs :
18
a. Les acides gras et leurs savons : De
formule générale RCOOH. Ils sont peu solubles dans l'eau. Les
acides gras et leurs savons les plus employés contiennent un nombre
total d'atomes de carbone variant de 12 à 18. Ces acides ne sont pas
toujours saturés, ils contiennent parfois une ou plusieurs liaisons
double. (Corneille EK et Al. Masson ; 1973)
b. Les sulfonâtes d'alkyl : les
sulfates et les sulfonâtes d'acide dérivés du
pétrole (NDOLWA C ; 2014)
II.4.1.2. LES COLLECTEURS CATIONIQUES
A part quelques composés cycliques comme la pyridine et
la quinoléine, les collecteurs cationiques contiennent toujours d'azote
dans le groupe polaire. Les collecteurs cationiques les plus employés
sont les amines d'alkyl et leurs sels (Corneille EK et Al. Masson ; 1973).
II.4.1.3. LES COLLECTEURS NON IONIQUES
Ces collecteurs non ioniques sont des dérivés du
pétrole et sont employés soit seuls pour aider les flottants
naturels comme le soufre et le carbone, soit en mélange avec des
collecteurs ioniques pour flotter des oxydes de fer (NDOLWA C ; 2014)
Tableau 2. Classification générale des
collecteurs
|
|
|
|
Non ionisés,non polaires
|
|
|
COLLECTEURS
anioniques
|
|
|
|
|
|
|
|
|
carboxylates
|
|
RCOONa
|
L
Kerozène,Mazout, sulfates
RSO4Na sulfonates RSO3Na II.4.2. LES
ACTIVANTS ET LES DEPRIMANTS
cationiques
xanthates
AMINES:RNH2
RCOS2Na
Dithiophosphate
R2PO2S2Na
SLFYDYL
Y lD
S
XHDYL
Les activants et les déprimants sont utilisés
pour modifier la réactivité de la particule à la surface
vis-à-vis du collecteur. Lorsque le collecteur ne réagit plus
avec la surface des minéraux ciblés, la séparation devient
quasiment impossible. Un activant permet de modifier la nature chimique de la
surface de ce minéral favorisant l'adsorption du collecteur. (Horace H,
1952)
19
Contrairement à un activant, le déprimant
empêche le collecteur de réagir avec la surface d'une particule de
gangue qui conserve ainsi son caractère hydrophile.
Les activants sont choisis parmi les composés chimiques
dont l'ion actif est de signe opposé à celui de lion effectif
tandis que les déprimants sont choisis parmi les composés
chimiques dont l'ion actif a le même signe que l'ion effectif du
collecteur. Au Concentrateur de Kolwezi, le tall-oil et le booster sont
utilisés comme activant du cobalt et comme déprimant, le silicate
sodique.
II.4.3. LES MOUSSANTS
Après la collection d'un des constituants du minerai,
on injecte de l'air sous forme de bulles dans la pulpe pour accrocher le
minéral collecté et le récupérer. Or les bulles
d'air montent rapidement jusqu'à la surface de la pulpe et disparaissent
au même moment car les liquides purs ne moussent pas. Pour que les
particules du minéral collecté puissent être
séparées de la pulpe, il faut que les bulles d'air auxquelles
elles adhèrent soient stabilisées.
D'où la présence d'un moussant pour pouvoir
réaliser cette opération. Un moussant est un réactif, peu
soluble dans l'eau, possédant une chaine organique assez longue qui
permet de diminuer la tension de surface de l'eau, l'addition d'un moussant
favorise la production des bulles d'air fines et d'une écume stable.
Idéalement, le moussant ne doit pas réagir avec la surface des
particules. Certains réactifs peuvent combiner des
propriétés de moussant et de collecteur comme l'Aeroflot 241
(Wills ; 2001).
Au concentrateur de Kolwezi, le G41 est utilisé comme
agent moussant. Il est préparé à une concentration de 900
g/l.
II.4.4. LE MODIFICATEUR DU MILIEU
Les modificateurs ou régulateurs du pH font partie des
produits utilisés pour modifier les interactions
minéraux/collecteur. Selon l'alcalinité ou l'acidité de la
pulpe, de nouveaux composés se forment à la surface des
minéraux et réduisent ou activent l'adsorption des
collecteurs.
En général la flottation des sulfures est
effectuée en milieu alcalin car la plupart des collecteurs y sont plus
stables et en plus minimise les problèmes de corrosion des
équipements. (EVRARD ; 1971)
20
La chaux, le carbonate sodique et l'acide sulfurique sont les
réactifs les plus utilisés pour cette opération et sont
souvent appelés régulateurs du pH. Au concentrateur de Kolwezi,
le carbonate sodique est utilisé comme régulateur du pH.
II.5. ADSORPTION ET ABSORPTION DES
COLLECTEURS
La fixation du collecteur à la surface des minéraux
est bien expliquée par la théorie du potentiel
électrocinétique : les cations sont adsorbés par les
surfaces de charge négatives et les anions par les surfaces de charge
positive.
Lorsque l'adsorption est principalement électrostatique il
faut employer des collecteurs anioniques quand la surface est chargée
positivement, et des collecteurs cationiques quand la surface et chargée
négativement. (Corneille EK et Al Masson ; 1973)
II.5.1. TYPE D'ADSORPTION
Il existe deux modes d'adsorption des collecteurs à la
surface des minéraux.
a. L'adsorption physique
C'est une forme d'adsorption qui est surtout due à des
forces électrostatiques et le potentiel électrocinétique,
elle est caractérisée par une faible chaleur de
réaction.
b. L'adsorption chimique
Elle suppose l'affinité chimique de certains ions ou
atomes de surfaces solides pour les ions des collecteurs, elle est
caractérisée par une réaction chimique de surface, avec un
composé nouveau et donc spécifique et une forte chaleur de
réaction. (Corneille EK et Al. Masson, 1973)
II.5.2. THEORIE SUR LA THERMODYNAMIQUE DE
L'ADSORPTION
Une solution renfermant le soluté à adsorber est
mise en contact avec une masse connue d'un solide adsorbant. L'adsorption du
soluté se traduit par des variations simultanées de sa
concentration en solution et de celle à la surface du solide.
En clair, soit un volume (V) d'une solution contenant un
soluté i à la concentration initiale Ci° (mol/L) mise en
contact avec une masse ms (Kg) de solide adsorbant. A un temps t, si la
concentration en i de la solution est Ci (mol/L), alors la
21
quantité de soluté passant de la phase liquide
vers la surface du solide, est donnée par la différence : V
(Ci° - Ci) (mol). La quantité par unité d'adsorbant à
l'instant t est alors :
(4) (Mol/Kg)
L'aspect énergétique de l'adsorption est en lien
avec les propriétés thermodynamiques. En effet l'énergie
d'une molécule de soluté varie quand elle s'approche de la
surface pour atteindre un minimum à une certaine distance, près
d'un site d'adsorption.(Maather et al ; 2007).
II.6. CINETIQUE DE LA FLOTTATION
La cinétique de flottation est fonction de la
granulométrie, des interactions, de la taille des bulles d'air et bien
d'autres facteurs tels que la coagulation des fines particules et l'action de
la turbulence sur les agrégats.
Deux types de modèles sont mis sur pied pour la
détermination de la cinétique de flottation. L'un
considère la variation temporelle de la concentration des particules
flottés et l'autre tient compte la variation du temps de la
récupération des particules flottées. (Blazy P ; 1970)
En considérant constants les paramètres de
flottation (densité, pH, ajout des réactifs...) et en assimilant
la flottation à une réaction chimique, nous pouvons admettre que
la quantité de minerai qui passent dans la mousse ou la diminution de la
concentration du minerai dans la pulpe est une fonction directe de la
concentration :
(5)
Plusieurs recherches ont été menées sur
la cinétique de flottation et ont révélé que n=1.
D'où l'établissement de l'équation :
(6)
Où Cr est la concentration résiduelle en
minéral flottable après flottation prolongée.
22
II.7. DOSAGE ET DISTRIBUTION DES REACTIFS II.7.1.
STRATEGIE D'AJOUT DES REACTIFS
Une bonne stratégie d'ajout des réactifs
caractérise la quantité et la façon dont les
réactifs sont ajoutés dans un circuit de flottation. Les
variantes résident dans le choix des réactifs, du dosage et de la
distribution. La dernière composante est stratégique pour notre
étude.
II.7.2. LE DOSAGE DES REACTIFS
L'ajout d'un réactif dans une unité de
flottation est basé sur la quantité de minerai alimenté au
circuit et est souvent exprimé en grammes de réactifs par tonne
des minerais. Lorsque le rendement métallurgique est à la baisse,
il peut arriver qu'on augmente le dosage du collecteur ou du moussant.
Cependant le surplus du collecteur peut favoriser la flottation des
espèces non désirées réduisant ainsi la
sélectivité du procédé et de la même
façon, une quantité; insuffisante de collecteur réduit la
capacité de la flottation et l'utilisation restreinte du moussant peut
causer une instabilité de l'écume et une diminution du rendement
de récupération des minéraux utiles.
II.7.3. LA DISTRIBUTION DES REACTIFS
A différents endroits du circuit de flottation, les
réactifs peuvent y être ajoutés. On trouve parfois des
points d'injection pour le collecteur et du modificateur du milieu au broyage
permettant ainsi de maximiser le temps de conditionnement. Cependant la majeure
partie du collecteur et du moussant est ajoutée dès la
première étape de l'ébauchage et une faible
quantité est distribuée dans les bancs des cellules restantes.
II.8. PARAMETRES DE LA FLOTTATION
Pour la bonne marche d'un procédé de flottation,
il est d'une idée très capitale de prendre en
considération un nombre important de paramètres. Parmi ces
derniers nous pouvons retenons :
a) La granulométrie
La flottation met en jeu des phénomènes de
surface, dont l'action est d'autant plus intense que la surface
spécifique des particules est grande c'est-à-dire que leur
dimension est petite (Corneille EK et Al Masson ; 1973)
23
En fait, on constate que lorsque l'on flotte un minéral
pur, que le rendement de la flottation varie en fonction de la dimension des
particules et que, surtout dans un ensemble de granulométrie
hétérogène. Ce sont les grosses particules et les
très fines qui flottent le moins bien. D'où le respect d'une
fourchette de dimension de particules pour une bonne opération.
Au concentrateur de Kolwezi, la tranche granulométrique
nous révèle que :
- Les + 48 : 1 à 3%
- Les + 200# : 28-32%
- Le d70 (200#) varie de 60 à 110um, plus souvent 74um.
b) La température
La température n'influe pas trop sur la flottation des
minerais et cela va de pair avec les régions et les saisons. La
flottation est souvent faite à une température ambiante. Avec la
flottation aux acides gras, il est toujours recommandé de chauffer les
pulpes soit pour augmenter le rendement, soit pour rendre les réactifs
moins visqueux. (HORACE H. ; 1952)
c) Densité de la pulpe
La densité de la pulpe, pour une alimentation de la
flottation, varie d'une installation de concentration à une autre. Le
pourcentage en poids, des matières solides à une importance
considérable. L'emploi des pulpes peu diluées permet des
économies d'eau et de réactifs, ainsi qu'une augmentation de
récupération du minéral flotté. Il existe une
fourchette de densité bien précise pour une opération de
flottation.
Au concentrateur de Kolwezi, 1,28 -1,3 est la gamme de la
densité recommandée pour la bonne conduite de la flottation.
d) Conditionnement
Les réactions chimiques peuvent être
instantanées dans certaines conditions. Quant aux réactions de
flottation, l'exigence d'un temps avant qu'elle soit effective et
complète est d'une importance capitale. Cette période de temps
est appelée conditionnement et varie suivant la nature de
réactifs. (NTUMBA JM ; 2012) Le conditionnement est souvent
réalisé dans des cuves à agitation mécanique ou
directement dans les cellules de flottation. (EVRARD ; 1971).
24
II.9. EVALUATION D'UNE OPERATION DE
FLOTTATION
Pour se rendre compte de l'efficacité d'une
opération de flottation, quelques critères sont pris en
considération.
Il s'agit de :
- Le rendement de récupération du métal ; -
Le rendement pondéral du concentré ;
- Le taux de concentration du métal utile.
1. Le rendement de
récupération
Le rendement de récupération est le rapport en
pourcentage de la masse du métal utile récupéré
dans le concentré à la masse du métal contenu dans
l'alimentation. Améliorer ce critère d'évaluation fera
l'objet de notre étude. Il est déterminé de la
manière suivante :
(7)
2. Le rendement pondéral du
concentré
C'est le rapport exprimé en pourcentage du poids du
concentré obtenu au poids de l'alimentation. Il est donné par la
relation suivante :
3. Le taux de concentration
C'est le rapport de la teneur du métal utile dans le
concentré à celle de l'alimentation. La formule ci-dessous nous
permet d'exprimer le taux de concentration.
Avec :
- a : teneur du métal dans l'alimentation ; - r : teneur
du métal dans le rejet ;
- c : teneur du métal dans le concentré ;
25
- C : masse du concentré ;
- A : masse du minerai alimenté ;
- R : masse du rejet.
II.10. COMPROMIS ENTRE RENDEMENT DE RECUPERATION ET TAUX
DE CONCENTRATION
Une bonne opération de flottation est celle qui se
conclut par un concentré d'une bonne teneur et d'un rendement de
récupération élevée. Cependant comme ces deux
concepts sont en opposition, il convient donc de se donner un compromis entre
la teneur en élément utile et la récupération que
l'on désire avoir. Ceci découle de la loi de contamination
réciproque. Celle-ci a était fondée sur bases des
constatations :
? Si l'on désire atteindre de récupération
élevée du minéral valorisable, le
concentré sera contaminé par une grande
quantité de la gangue ;
? Si on désire obtenir un concentré trop riche
en élément de valeur, il faudra se limiter à recueillir
les grains qui flottent mieux et cela entraine un faible rendement de
récupération.
C'est ainsi que dans les industries où la flottation se
fait en continu dans plusieurs cellules de flottation (ébauchage,
pré-finissage-finissage), on se base également sur
l'évolution des teneurs en éléments utiles en fonction de
leurs rendements de récupération des concentrés
cumulés tout au long du circuit de flottation (NDOLWA C ; 2014).
26
CHAPITRE III. APPROCHE EXPERIMENTALE III.1.
INTRODUCTION
Dans le but d'améliorer le rendement de
récupération du cobalt en fractionnant le booster et le tall-oil,
nous avons mené nos études en procédant par des essais de
flottation sur la pulpe de décharge de l'hydro cyclone qui était
prête pour l'alimentation de la flottation. Ces essais de flottation ont
pour but de rechercher une bonne condition de flottabilité et visent
également la détermination d'une bonne distribution et de bons
ratios des réactifs pour parvenir à résoudre le
problème de notre travail.
III.2. ECHANTILLONNAGE
L'échantillonnage est la première et l'une des
étapes importantes d'une analyse. Il permet de réduire la taille
de la fraction d'un pot à étudier ainsi que la procédure
à suivre pour effectuer le prélèvement de manière
à garantir la représentativité. (ZEKA M ; 2015)
III.2.1. PRELEVEMENT D'ECHANTILLON
Les échantillons qui nous ont permis de bien
réaliser nos études ont été prélevés
dans une caisse de décharge de l'hydro cyclone. Le
prélèvement a été fait de manière suivante :
prendre la pulpe dans un seau de 10 l, laisser décanter la pulpe,
siphonner de l'eau ; répéter cette opération plusieurs
fois pour avoir la quantité suffisante des solides.
III.2.2. PREPARATION DE L'ECHANTILLON
La quantité des solides étant suffisante, nous
avons procédé à un mélange fidèle
jusqu'à une homogénéisation parfaite pour avoir un
échantillon caractérisé par les mêmes
propriétés en tout point de l'ensemble.
Cette homogénéisation a été rendue
possible grâce à l'utilisation d'une bêche et d'une
diviseuse. Nous avons laissé l'échantillon à
l'étuve pendant 24 heures pour éliminer l'humidité. Un
kilogramme de l'échantillon a été pulvérisé
pendant 4 à 6 minutes. La poudre qui en ressort a été
amenée au Laboratoire EMT/UCK et EMT/KZC pour une analyse chimique et
à EMT/LIKASI pour une analyse minéralogique.
27
III.3. CARACTERISATION DE L'ECHANTILLON
III.3.1. CARACTERISTIQUE CHIMIQUE
L'échantillon mené au labo, EMT/UCK et au Labo
EMT/KZC a été analysé respectivement au
spectromètre d'adsorption atomique et au metorex. Voici comment se
présente la répartition des quelques éléments
considérées dans l'échantillon.
Tableau 3. Analyse chimique de
l'échantillon
Eléments
|
Cuivre
|
Cobalt
|
Manganèse
|
Fer
|
%
|
3,37
|
0,56
|
0,32
|
9,04
|
III.3.2. CARACTERISATION MINERALOGIQUE
Il a été révélé que
l'échantillon sur lequel nous avons menés nos investigations a en
son sein le cuivre sous forme de la malachite et les traces de la chrysocolle,
le cobalt sous forme de l'heterogenite, le fer sous forme d'hématite
ainsi que le manganèse sous forme d'oxyde
III.4. MATERIELS UTILISES
Pour la réussite de nos travaux, voici les
matériels et appareils utilisés :
- machine de flottation du type DENVER ;
- Cellule de flottation
- balance électronique ;
- étuve ;
- chronomètre ;
- métorex ;
- calculatrice ;
- pans ;
- pissettes ;
- pipettes ;
- palette ;
- sachets ;
- seau.
28
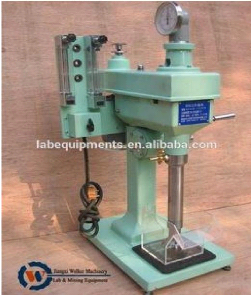
Figure 3. Dispositif expérimental des essais de
flottation
III.5. MODE OPERATOIRE
Le mode opératoire au cours des essais de flottation a
été le suivant :
> Déterminer la teneur en cuivre et en cobalt ;
> Faire le calcul de dose jusqu'au ml (C.C) ;
> Diluer à l'aide de l'eau la pulpe recueillie
jusqu'à ce qu'elle atteigne la densité
voulue et consulter le tableau de volume de pulpe pour les essais
de flottation au
laboratoire
> Placer la cellule sur le support de la machine de flottation
;
> Rabaisser la tige du rotor dans la pulpe contenue dans une
cellule de 2,5 litres ;
> Actionner la machine pour agiter la pulpe ;
> Ajouter le silicate, deux minutes après la mixture
dolomitique, le booster, le
collecteur (T3Y) et enfin la première fraction du
sulfhydrate de sodium ;
> Laisser la pulpe en agitation pendant un temps de
conditionnement de 5 minutes ;
> Ajouter quelques gouttes de G41 (agent moussant) puis
conditionner pendant une
trentaine de secondes ;
29
> Ouvrir le robinet d'admission d'air dans la pulpe et
recueillir, pendent 30 Secondes,
la première fraction de la mousse qui se fait au moyen
de la palette ;
> Recueillir pendent une minute et trente secondes la
deuxième fraction de la mousse
après les trente premières secondes ;
> Ajouter la seconde fraction du NaSH ;
> Recueillir pendant deux minutes la moitié de la
troisième fraction de la mousse
> Ajouter la troisième fraction du NaSH ;
> Recueillir pendant deux minutes la seconde partie de la
troisième fraction ;
> Sécher les concentrés ainsi que le rejet
dans une étuve pendant 24heures à 105 °C ;
> Peser les solides secs contenus dans les pans ;
> Mettre les fractions (A, B, C, et R) dans les sachets
biens étiquetés ;
> Faire analyser les concentrés et le rejet au
laboratoire d'EMT pour
déterminer les teneurs du cuivre et du cobalt.
III.6. DOSAGES DES REACTIFS UTILISES
Les dosages des réactifs sont fixés par le
laboratoire EMT/LIKASI et le concentrateur de Kolwezi n'en fait qu'une bonne
application, voici comment se fait les dosages de ces réactifs à
la GCM.
Tableau 4. Doses des réactifs au concentrateur
de Kolwezi
Réactifs
|
g/t
|
Concentration g/l
|
Volume CC
|
NaSH
|
3144
|
240
|
13,1
|
T3Y
|
393
|
55
|
7,14
|
MD
|
196,5
|
860
|
0,23
|
G41
|
98,25
|
900
|
0,11
|
Na2SiO3
|
200
|
300
|
0,66
|
BOOSTER
|
40
|
50
|
0,8
|
Tall-oil
|
22,5
|
900
|
0,025
|
30
CHAPITRE IV. PRESENTATION ET ANALYSE
DES RESULTATS
IV.1. INTRODUCTION
Dans le but de flotter sélectivement certains
minéraux, qui normalement flottent difficilement ou presque pas
lorsqu'on utilise uniquement les collecteurs et les moussants, il est d'une
nécessité capitale d'utiliser les activant afin d'assurer une
bonne sélectivité des minéraux qu'on veut flotter.
Pour le cas de l'étude ici présente, le booster
et le tall-oil sont les activants envisagés pour mener nos essais de
flottation à un bon rendement de récupération du cobalt.
Dans le présent chapitre, nous aurons à présenter les
résultats des analyses granulochimiques de l'échantillon
d'alimentation de la flottation du concentrateur de Kolwezi, des rejets de
différentes séries d'essais de flottation et des résultats
métallurgiques des essais effectués dans les conditions du
concentrateur de Kolwezi, suivis respectivement de ceux du booster, du
tall-oil, du booster et tall-oil fractionnés.
IV.2. ANALYSE GRANULOCHIMIQUE DE L'ALIMENTATION DE LA
FLOTTATION
L'analyse granulochimique consiste à diviser en
tranches granulométriques un échantillon d'un minerai, elle donne
une répartition pondérale suivant une succession d'intervalles
dimensionnelles, généralement reconnus standards, couvrant les
domaines granulométriques.
Du tableau 5 nous avons retenu ce qui suit :
- Environ 3% du cobalt sont renfermés dans la tranche
supérieure à 48 mesh ; - Plus de 90% de cobalt sont
renfermés dans la tranche supérieure à 200 mesh.
L'attente au concentrateur de Kolwezi sur le broyage humide
est telle que : la tranche supérieure à 48 mesh doit avoir 1
à 3% et celle supérieure à 200 mesh 28 à 32 %. Vu
ce qui précède, nous pouvons conclure que le broyage humide du
dit concentrateur produit des grossiers.
31
Tableau 5. Analyse granulochimique du composite
alimentant la flottation.
Tranches
|
Répartition granulometrique
|
|
Répartition Cobalt
|
|
Mesh
|
Microns
|
Poids
|
%Poids
|
% Rc
|
% Pc
|
% Co
|
PdS
|
% PdS
|
% Rc
|
% Pc
|
48
|
300
|
55
|
5.5
|
5.5
|
94.47
|
0.3
|
0.19
|
3.33
|
3.33
|
96.67
|
65
|
208
|
435
|
43.7
|
49.2
|
50.75
|
0.6
|
2.39
|
42.56
|
45.88
|
54.12
|
100
|
149
|
150
|
15.1
|
64.3
|
35.68
|
0.5
|
0.81
|
14.41
|
60.29
|
39.71
|
150
|
104
|
190
|
19.1
|
83.4
|
16.58
|
0.7
|
1.24
|
21.97
|
82.26
|
17.74
|
200
|
75
|
130
|
13.1
|
96.5
|
3.52
|
0.6
|
0.77
|
13.64
|
95.90
|
4.10
|
270
|
55
|
20
|
2.0
|
98.5
|
1.51
|
0.7
|
0.13
|
2.31
|
98.21
|
1.79
|
325
|
48
|
10
|
1.0
|
99.5
|
0.5
|
0.7
|
0.07
|
1.16
|
99.37
|
0.63
|
-325
|
-48
|
5
|
0.5
|
100
|
-
|
0.7
|
0.04
|
0.63
|
100
|
-
|
Alimentation
|
995
|
100
|
-
|
-
|
0.6
|
5.62
|
100
|
-
|
-
|
IV.3. TESTS DE FLOTTATION
IV.3.1. OBJECTIFS DES ESSAIS DE FLOTTATION
L'objectif de notre étude est d'améliorer le
rendement de récupération du cobalt par l'usage séquentiel
du booster et du tall-oil par rapport aux conditions présentes au
Concentrateur de Kolwezi dont les exigences sont les suivantes :
? Alimentation ou teneur du minerai : 2 à 3,5% Cu et 0,54%
Co
? Teneur du concentré fini 15 à 20% Cu, 2 à
3% Co
? Rendement de récupération : 80% Cuivre et 42%
Cobalt ? Teneur du rejet final : 1,2% Cuivre et 0,4 % Cobalt
(Source : Résultats métallurgiques DCE/KZC, le
09/03/2015)
IV.3.2. APPRECIATION DE L'EFFICACITE DES ESSAIS DE
FLOTTATION
Pratiquement l'appréciation des essais de flottation se
fera sur base des éléments suivants :
- Les concentrés de tête ;
- Les récupérations en tête ;
- Les récupérations globales des concentrés
ébauchés ; - Les teneurs dans les différents rejets.
32
IV.3.3. CONDUITE DES ESSAIS DE FLOTTATION AU LABORATOIRE
Signalons par la présente occasion que tous les essais
que nous avons réalisés tout le long de notre étude n'ont
été faits que par un simple ébauchage et cela se faisait
de la manière suivante :
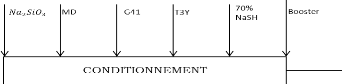

références :
Figure 4. Schéma de flottation avec un simple
ébauchage des concentrés
IV.4. RESULTATS DES ESSAIS DE FLOTTATION AVEC
EBAUCHAGE
Pour arriver à mieux effectuer ces essais de
flottation, et conformément à notre cadre d'étude, nous
avons subdivisé nos essais de flottation en quatre grandes
catégories à savoir :
- Essai de flottation dans les conditions de
référence (KZC) ; - Essai de flottation avec le booster
fractionné ;
- Essai de flottation avec le tall-oil fraction ;
- Essai de flottation avec le booster et le tall-oil
fractionnés.
IV.4.1. ESSAIS DE FLOTTATION DANS LES CONDITIONS DE
REFERENCE
Une série d'essais a été
réalisée dans les conditions du concentrateur de Kolwezi
où le booster est ajouté totalement au conditionnement pour avoir
des résultats que nous allons considérer tout au long de notre
étude comme résultats de référence.
Le tableau 6 et la figure 5 ci-dessous nous présentent
les résultats de
33
Tableau 6. Résultats synthétiques de
flottation en référence
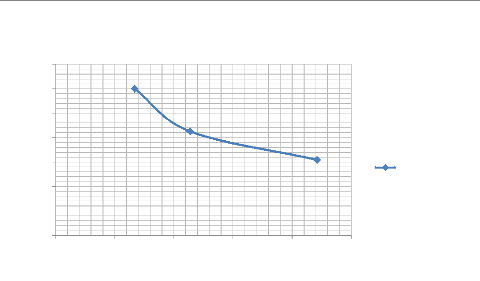
Téneur Cobalt(%)
0,80
0,60
0,40
0,20
0,00
1,40
1,20
1,00
0,0 10,0 20,0 30,0 40,0 50,0
Rendement de récupération
Cobalt(%)
REFERENCE
FRACTION
POIDS
COBALT
%
%
Rdt
Taux
C tête
5,71
1,2
13,4
2,35
C ébauché
36,57
0,62
44,2
1,21
1
Rejet
63,43
0,45
55,8
Alim
100
0,51
100
Evolution du rendement de
récupération du Cobalt
Conditions de KZC
Figure 5. Evolution du rendement de
récupération du Cobalt en référence
Une analyse objective a été faite sur ces
résultats et le constat fait nous révèle
ce qui suit :
- Le concentré de tête a une teneur de cobalt de
1,20% et un rendement de récupération de 13,4%
- Le concentré ébauché quant à lui
a une teneur cobalt de 0,62% et un rendement de récupération de
44,2%
- La teneur cobalt dans le rejet est de 0,45%.
IV.4.2. ESSAIS DE FLOTTATION AVEC LE BOOSTER
FRACTIONNE
34
Dans cette catégorie d'essais de flottation, neuf
essais ont étaient effectués avec le sulfudrate de sodium et le
booster fractionnés. Les résultats de ces essais sont
présentés synthétiquement dans le tableau 7 et des essais
jugés bons pour cette catégorie sont traduits par la figue 6. Les
annexes nous fournissent les détails possibles.
Tableau 7. Résultats synthétiques de
flottation avec le Booster fractionné
|
|
|
|
|
|
|
|
|
|
|
|
|
|
|
|
|
|
|
|
|
|
|
|
POIDS
|
|
COBALT
|
BOOSTER
|
FRACTION
|
%
|
%
|
Rdt(%)
|
Taux
|
C tête
|
6,63
|
1,38
|
18,08
|
2,73
1,69
|
C ébauché
|
26,52
|
0,86
|
44,81
|
R
|
73,48
|
0,38
|
55,19
|
0-0-0%
|
Alim
|
100
|
0,51
|
100,00
|
1,00
|
C tête
|
6,97
|
1,25
|
16,55
|
2,37
1,23
|
C ébauché
|
38,63
|
0,65
|
47,56
|
R
|
61,37
|
0,45
|
52,44
|
50-50-0%
|
Alim
|
100
|
0,53
|
100,00
|
1,00
|
C tête
|
6,45
|
1,49
|
16,86
|
2,61
1,27
|
C ébauché
|
41,94
|
0,72
|
53,14
|
R
|
58,06
|
0,46
|
46,86
|
25-25-50%
|
Alim
|
100
|
0,57
|
100,00
|
1,00
|
C tête
|
7,78
|
1,33
|
22,32
|
2,87
1,69
|
C ébauché
|
38,89
|
0,78
|
65,71
|
R
|
61,11
|
0,26
|
34,29
|
75-25-0%
|
Alim
|
100
|
0,46
|
100,00
|
1,00
|
C tête
|
13,26
|
1,32
|
32,09
|
2,42
1,43
|
C ébauché
|
46,96
|
0,78
|
66,94
|
R
|
53,04
|
0,34
|
33,06
|
25-75-0%
|
Alim
|
100
|
0,55
|
100,00
|
1,00
|
C tête
|
6,42
|
1,27
|
14,18
|
2,21
1,23
|
C ébauché
|
46,52
|
0,71
|
57,21
|
R
|
53,48
|
0,46
|
42,79
|
0-0-100%
|
Alim
|
100
|
0,57
|
100,00
|
1,00
|
C tête
|
9,04
|
1,48
|
28,19
|
3,12
1,47
|
C ébauché
|
40,96
|
0,70
|
60,20
|
R
|
59,04
|
0,32
|
|
0-100-0%
|
Alim
|
100
|
0,47
|
100,00
|
|
C tête
|
8,62
|
1,27
|
22,73
|
|
C ébauché
|
42,53
|
0,78
|
68,97
|
R
|
57,47
|
0,26
|
|
35
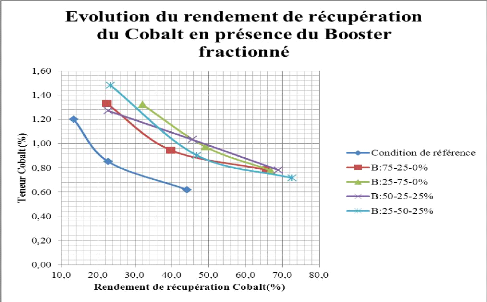
Figure 6. Evolution du rendement de
récupération du Cobalt en présence du Booster
Après survol du présent tableau nous avons
retenus quatre essais aux fractions différentes du booster qui nous
serviront d'essais d'amélioration du rendement de
récupération cobalt.
Ces essais nous laissent voir ce qui suit par rapport aux
conditions de
référence :
- A la fraction de 75-25-0% du booster, nous avons un
concentré de tête et ébauché titrant respectivement
1,33 et 0,78% cobalt avec un rendement de récupération de 22,32
et 65,71% ;
- A la fraction de 25-75-0% du booster, nous avons
remarqué presque une situation similaire du cas précédent
mais avec une nette variation du rendement de récupération dans
le concentré de tête ;
- A la fraction de 50-25-25% du booster, la teneur du
concentré de tête diminue et le rendement de
récupération en tête est quasiment similaire à celui
de la fraction 75-250% du booster, mais quant au concentré
ébauché nous avons noté une légère
amélioration du rendement de récupération du cobalt et la
teneur globale est équivalente à celles de deux cas
précédents ;
36
- Nous avons constaté une amélioration sensible
du rendement de récupération du cobalt dans le concentré
ébauché avec diminution de la teneur global, et un
concentré de tête qui a une teneur de 1,48 avec comme rendement de
récupération de 23,36% à la fraction de 25-50-25% du
booster
Notons également que dans les quatre essais retenus,
nous avons enregistré les teneurs de cobalt dans les différents
rejets respectivement de : 0,26 ; 0,34 ; 0,26 et 0,27%.
Les effets suivants ont été observés pendant
le déroulement de ces essais :
- Dans les fractions du milieu, des pétillements de la
mousse ont été observés à la surface de la pulpe,
dus normalement à un excès de NaSH ;
- La mousse a été chargée en
minéraux de cobalt dans la première fraction, puis un virement
brusque de la couleur qui passe du vert foncé vers une couleur presque
grise.
IV.4.3. ESSAIS DE FLOTTATION AVEC LE TALL OIL
FRACTIONNE
Sept essais de flottation ont été
effectués dans cette catégorie du tall-oil fractionné. La
présentation synthétique de ces résultats se fait dans le
tableau 8 et la traduction graphique des essais jugés bons et retenus se
fait à la figure 7. Comme nous l'avons dit précédemment,
les annexes fournissent beaucoup plus les détails.
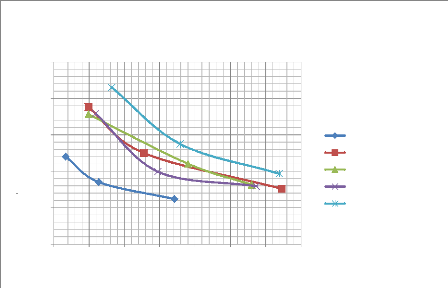
Teneur Cobalt (%)
70-0-30% 30-0-70% 30-70-0%
70-30-0%
2,50
2,00
0,50
0,00
1,50
1,00
10,0 20,0 30,0 40,0 50,0 60,0 70,0 80,0 Rendement de
récupération Cobalt(%)
COBALT
Taux
3,00
1,37
1,00
41,61
3,11
1,61
1,00
36,25
3,68
1,49
1,00
25,48
3,39
C ébauché
42,55
0,81
66,07
1,55
1,00
R
57,45
0,31
33,93
Alim
100,00
0,52
100,00
C tête
6,56
1,79
21,91
3,34
C ébauché
45,36
0,80
67,36
1,49
1,00
R
54,64
0,32
32,64
Alim
100,00
0,54
100,00
C tête
5,88
2,00
21,77
3,70
C ébauché
42,78
0,73
57,64
1,35
1,00
R
57,22
0,40
42,36
Alim
100,00
0,54
100,00
C tête
7,65
2,15
26,45
3,46
C ébauché
47,54
0,97
73,85
1,55
1,00
R
52,46
0,31
26,15
Alim
100,00
0,62
100,00
Evolution du rendement de récupération
du
Cobalt en présence du Tall Oil
fractionné
Condition de référence T:0-0-100% T:70-0-30%
T:30-0-70% T:70-30-0%
Figure 7. Evolution du rendement de
récupération en présence du Tall-oil
fractionné
37
Tableau 8. Résultats synthétiques de
flottation avec le Tall-oil fractionné
|
|
|
|
|
|
|
|
|
|
|
|
|
|
|
|
|
|
|
|
|
|
|
|
|
|
|
|
|
|
|
|
|
|
|
|
|
|
|
|
|
|
|
|
|
|
|
|
|
|
|
|
|
|
|
|
|
|
|
|
|
|
|
|
|
TALL OIL
|
|
|
|
|
|
|
POIDS
|
|
|
|
FRACTION
|
%
|
%
|
Rdt(%)
|
C tête
|
5,85
|
1,78
|
17,54
|
100-0-0%
|
C ébauché
|
42,55
|
0,81
|
58,39
|
|
R
|
57,45
|
0,43
|
|
|
Alim
|
100,00
|
0,59
|
100,00
|
C tête
|
7,32
|
1,45
|
22,76
|
0-100-0%
|
C ébauché
|
39,63
|
0,75
|
63,75
|
|
R
|
60,37
|
0,28
|
|
|
Alim
|
100,00
|
0,47
|
100,00
|
C tête
|
5,38
|
1,88
|
19,81
|
0-0-100%
|
C ébauché
|
50,00
|
0,76
|
74,52
|
|
R
|
50,00
|
0,26
|
|
|
Alim
|
100,00
|
0,51
|
100,00
|
C tête
|
5,85
|
1,78
|
19,85
|
38
Il ressort de l'examen des résultats obtenus, quatre
essais ont été retenus et nous fournissent les informations
suivantes :
- Le tall-oil fractionné comme suit 0-0-100% nous donne
un concentré de tête et un concentré ébauché
titrant respectivement 1,88 et 0,76 % cobalt, un rendement de
récupération de tête et celui du concentré
ébauché de : 19,81 et 74,52% pour le cobalt. Un rejet titrant
0,26% cobalt ;
- A une fractionné de 30-0-70%, nous avons
remarqué une augmentation négligeable du rendement de
récupération de tête par rapport à la fraction de
0-0-100 % tall- oil, une teneur cobalt en tête de 1,79 tandis que
l'ébauché diminue en rendement de récupération et
augmente en teneur global ;
- Enfin, par rapport au second essai retenu dans cette
catégorie, il y a eu une augmentation d'environ 6% du rendement de
récupération global et 0,17% de la teneur globale du cobalt
à la fraction de 70-30-0% et un rejet de 0,31% cobalt.
Les effets suivants ont été observés
pendant la réalisation de cette catégorie
d'essais :
- Les pétillements exagérés de la mousse
;
- Une couche noire brillante apparaissait chaque fois à la
surface de la mousse dès la
première fraction et disparaissait progressivement dans
les fractions suivantes ;
- En plus d'activer le cobalt, le tall- oil active aussi le
manganèse jusqu'aller à 1,5% dans la teneur globale avec un
rendement de récupération de 61 % à l'ébauchage.
IV.4.4. ESSAI DE FLOTTATION AVEC LE BOOSTER ET LE
TALL-OIL
FRACTIONNES
Dans le but d'améliorer le rendement de
récupération du cobalt, nous sommes arrivé à
utiliser le booster ainsi que le tall- oil tous fractionnés. Une
combinaison de différentes fractions du booster et du tall -oil retenue
dans les deux catégories a été réalisée dans
la présente catégorie. Ainsi, nous avons écarté
tous les essais qui nous ont fourni un rendement de récupération
global en cobalt inférieur à 50% et nous avons retenu quatre
essais dont la présentation synthétique se fait dans le tableau 9
et traduit graphiquement à la figure 8.
39
Tableau 9. Résultats synthétiques de
flottation avec le Booster et Tall- oil fractionnés
|
|
|
|
|
|
|
|
|
|
|
|
|
|
|
|
|
|
|
|
|
|
|
|
|
|
|
|
|
|
|
|
|
|
|
|
|
|
|
|
|
|
|
|
|
|
|
|
|
BOOSTER
|
TALL OIL
|
|
|
|
|
|
|
|
|
|
|
|
POIDS
|
|
|
FRACTION
|
%
|
%
|
Rdt(%)
|
25-50-25%
|
70-30-0%
|
C tête
|
6,38
|
2,05
|
23,47
|
|
C ébauché
|
59,57
|
0,71
|
75,34
|
|
R
|
40,43
|
0,34
|
|
Alim
|
100,00
|
0,56
|
100,00
|
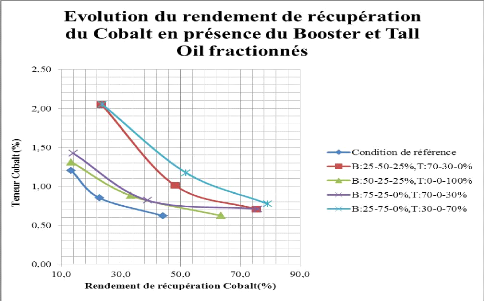
COBALT
Taux
3,7
1,3
1,0
24,66
2,4
1,2
1,0
36,45
2,6
1,3
1,0
24,13
25-75-0%
30-0-70%
3,9
1,5
1,0
20,84
Alim
100,00
0,53
100,00
Figure 8. Evolution du rendement de
récupération du cobalt en présence du Booster
et
Tall- oil fractionnés.
Par la même occasion, signalons qu'à cet essai
qui donne un bon résultat, nous avons observé une concentration
en cuivre dont les renseignements sont les suivants :
40
L'examen des résultats du tableau 9 laisse voir ce qui
suit :
- Le booster fractionné en 25-50-25% et le tall-oil en
70-30-0% conduit à un concentré de tête et un
concentré ébauché titrant respectivement 2,05 et 0,71 %
cobalt, un rendement de récupération en cobalt de 23,47 et
75,34%, la teneur du cobalt dans le rejet est de 0,34% ;
- Par rapport au premier cas de la catégorie d'essais,
à la fraction du booster de 50-2525% et celle du tall-oil de 0-0-100%,
on constate une diminution sensible de rendement de récupération
et de la teneur respectivement pour le concentré de tête et le
concentré ébauché. Le rejet possède une teneur en
cobalt de 0,44% ;
- 75-25-0% du booster et 70-0-30% du tall-oil laissent voir
sans équivoque que le concentré de tête titre 1,42% cobalt
en ayant un rendement de récupération de 14,09%, un
ébauchage du concentré titrant 0,71% cobalt et un rendement de
récupération de 75,87% ;
- Une amélioration nette a été
observée en fractionnant le booster et le tall-oil de la manière
suivante : 25-75-0% et 30-0-70%. Dans ce cas, on observe un concentré de
tête et un concentré ébauché titrant respectivement
2,05% et 0,77% cobalt, possédant comme rendement de
récupération en tête et global de 23,74% et 79,16% avec un
rejet de flottation titrant 0,24%.
IV.5. DISCUSSIONS
Nous notons une amélioration des résultats
entre, d'une part, nos meilleurs résultats trouvés au laboratoire
à ceux dans les conditions de référence et d'autre part,
à ceux rencontré au niveau de l'usine dans ses conditions
standards. Ceci, étant nous avons retenu l'essai de flottation en
fractionnant le booster et le tall- oil respectivement de la manière
suivante : 25-75-0% et 30-0-70% comme bon résultat dans la
catégorie des combinaisons de ces différents activant.
Comparativement à l'essai de référence
dont les résultats sont représentés synthétiquement
dans le tableau 10 et l'essai de la combinaison de booster et tall-oil
respectivement en fraction de 25-75-0% et 30-0-70%, nous pouvons juger cette
combinaison meilleure car elle a amélioré sensiblement le
rendement de récupération du cobalt.
41
- Le concentré de tête et le concentré
ébauché titrent respectivement : 23,43% et 5,06% cuivre ;
- Le rendement de récupération de tête et
celle récupération global de : 47% et 89,8% de cuivre ;
- Un rejet titrant 0,68% cuivre.
Tableau 10. Résultats synthétiques
comparatifs
EFFICACITE
|
REFERENCE
|
BO+TO
|
Concentré de tete
|
1.20
|
2.05
|
Concentré ébauché
|
0.62
|
0.77
|
Rendement de tete
|
13.4
|
23.47
|
Rendement ébauché
|
44.2
|
79.2
|
Rejet de flottation
|
0.51
|
0.24
|
IV.6. ANALYSES GRANULOMETRIQUES DES REJETS
Dans ce paragraphe, nous présentons une synthèse
des analyses granulochimiques effectuées sur les rejets d'essais de
flottation que nous avons jugé meilleurs dans les différentes
catégories, puis une comparaison et une brève explication sur
l'analyse des rejets de flottation dans les conditions standards et le rejet de
flottation avec le booster et le tall- oil fractionnés.
Tableau 11. Analyses granulochimiques des rejets de
flottation
|
|
|
|
|
|
|
|
|
|
|
|
|
BOOSTER
|
|
|
|
|
TALL OIL
|
|
|
BOOSTER+TALL OIL
|
|
|
|
Tranches
|
|
Poids
|
Cobalt
|
|
|
Poids
|
Cobalt
|
|
Poids
|
|
Cobalt
|
|
Mesh
|
Microns
|
g
|
%
|
%
|
%Pc
|
g
|
%
|
%
|
%Pc
|
g
|
%
|
%
|
%Pc
|
48
|
300
|
86
|
14,48
|
0,39
|
76,18
|
53
|
11,3
|
0,34
|
81,23
|
45
|
9,62
|
0,41
|
81,8
|
65
|
208
|
173
|
29,12
|
0,24
|
46,7
|
145
|
30,92
|
0,32
|
32,89
|
164
|
35
|
0,24
|
42,9
|
100
|
149
|
122
|
20,54
|
0,29
|
21,58
|
32
|
6,823
|
0,01
|
32,56
|
78
|
16,7
|
0,32
|
18,3
|
150
|
104
|
90
|
15,15
|
0,17
|
10,72
|
86
|
18,34
|
0,2
|
14,64
|
72
|
15,4
|
0,01
|
17,5
|
200
|
75
|
75
|
12,63
|
0,15
|
2,727
|
86
|
18,34
|
0,02
|
12,85
|
55
|
11,8
|
0,2
|
6,68
|
270
|
55
|
30
|
5,05
|
0,11
0,383
45
|
9,595
|
0,19
3,938
36
|
7,69
|
0,15
|
325
48
|
12
|
2,02
|
0,04
0,043
6
|
1,279
|
0,15
3
10
|
2,14
|
0,12
|
42
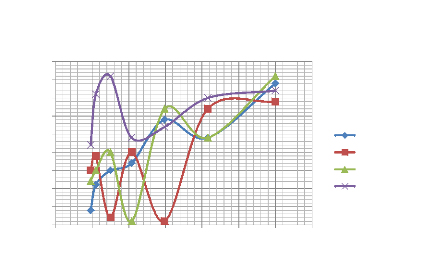
Teneur Cobalt(%)
0,45
0,35
0,25
0,15
0,05
0,4
0,3
0,2
0,1
0
Variation de la teneur du Cobalt dans les rejets de
flottation
0 50 100 150 200 250 300 350
Ouvertures des tamis en microns
Booster
Tall oil
Booster et Tall oil Conditions de KZC
Figure 9. Variation de la teneur du Cobalt dans les
différentes tranches des rejets
43
CONCLUSION
La présente étude s'inscrit dans l'ensemble des
voies susceptibles d'améliorer le rendement de
récupération du cobalt au Concentrateur de Kolwezi en faisant une
combinaison des différentes fractions du booster et du tall- oil.
Après caractérisation granulométrique de
l'alimentation de la flottation dudit Concentrateur, les résultats ont
révélés qu'environ 3% de cobalt sont renfermés dans
la tranche de plus de 48 mesh et plus de 90% dans la tranche supérieure
à 200 mesh, proportion qui n'est pas la bienvenue à la
flottation. Ceci étant, nous n'avons pas tenu compte de cet aspect
granulométrique, mais nous nous sommes attelés sur l'aspect
distribution des réactifs comme un des paramètres pour
améliorer le rendement de récupération de cobalt.
A l'issue de nos essais de flottation aux laboratoires, dans
la catégorie du tall-oil fractionné, nous avons constaté
avec amertume la concentration du manganèse qui est pour nous une
impureté.
Dans la catégorie du booster et du tall-oil
fractionnés, la combinaison de 2575-0% du booster et de 30-0-70% du
tall-oil, fournit des résultats jugés meilleurs pour cette
étude. Respectivement pour le cobalt et le cuivre, nous avons un
concentré de tête titrant 2,05 et 23,43%, un concentré
ébauché ayant pour teneur 0,77 et 5,06%, un rendement de
récupération en tête de 23,74 et 47% ; en ébauchage,
nous avons obtenu un rendement de 79,16 et 89,8%. En ce qui concerne les rejets
de flottation, nous avons enregistré une teneur de 0,24 % pour le cobalt
et 0,68 % pour le cuivre.
44
PERSPECTIVES
Au regard des résultats de cette étude, il
convient à la direction du contrôle d'exploitation du
concentrateur de Kolwezi d'orienter la suite de l'étude de la
manière suivante :
- Poursuivre la même étude en multipliant les
essais de combinaisons des fractions des activants et en révisant le
dosage du sulfudrate de sodium ;
- Tenir compte de la granulométrie ou déterminer
la courbe de broyabilité et se ramener dans les meilleures conditions
;
- Lors des essais de flottation avec le tall-oil, chercher
comment ne pas récupérer le manganèse car plusieurs
études du genre, élimination du manganèse par
précipitation dans le circuit cobalt (cas des usines hydro
métallurgiques de la Gécamines) traitant déjà ce
problème de manganèse.
En plus du point technique, il faudra établir une
caractérisation environnementale des rejets issus de la flottation dans
les cas de la combinaison du booster et tall- oil.
45
REFERENCES BIBLIOGRAPHIQUES
1. Anne GOSSELIN, DENN BLACKBURN, MARIO BERGERON, Mars 1999.
Protocole d'évaluation de la traitabilité des sédiments de
sels et des boues à l'aide des techniques métallurgiques.
2. Christian KATWIKA NDOLWA ,2014. Bases fondamentales de
préparation des minerais. UNIKOL Inédit.
3. NGENDA BANKA Richard ,2015. Génie métallurgique
I, UNIKOL inédit.
4. Serge BOUCHARD ,2005. Traitement du minerai, Edition le
Griffon d'Argile.
5. Corneille EK et Al Masson, 1973. Cours de minéralurgie
et préparation des minerais. Edition DERROUX Liège.
6. Pierre Blazy, 1970. La valorisation des minerais, Presse
universitaire de France.
7. Paris Barry A. Wills et Tim Napier-Munn, 2006. Mineral
Processing Technology,
8. Jean Marie KANDA NTUMBA, Décembre 2012. Etude de la
flottabilité de la malachite à l'aide de l'Amylxanthate de
potassium et acides gras. thèse de doctorat, Université de
Liège
9. ZEKA MUJINGA, 2015. Chimie analytique, UNIKOL
Inédit.
10. Notes de service DCE/KZC
,\NN IXES
A
ANNEXE A : ESSAI DE FLOTTATION DANS LES CONDITIONS DE
KZC
RATIO
COBALT
CUIVRE
CONDITION
FRACT
POIDS%POIDS
%
PdS
Rdt
taux
%
PdS
Rdt
taux
NaSH
A
50,0
5,7
1,20
0,60
13,4
2,35
26,81
13,41
57,6
10,1
70 -10 -20%
100 -0 -0%
ANNEXE B : ESSAIS DE FLOTTATION AVEC LE BOOSTER
FRACTIONNE
B
70,0
8,0
|
0,60
0,42
9,4
1,17
|
4,92
3,44
14,8
1,9
|
MD
|
A+B
|
120,0
|
13,7
|
0,85
|
1,02
|
22,8
|
1,66
|
14,04
|
16,85
|
72,4
|
5,3
|
Na2SiO3
|
|
C
|
200,0
|
22,9
|
0,48
|
0,96
|
21,4
|
0,94
|
1,40
|
2,80
|
12,0
|
0,5
|
G41
|
A+B+C
|
320,0
|
36,6
|
0,62
|
1,98
|
44,2
|
1,21
|
6,14
|
19,65
|
84,5
|
2,3
|
T3Y
|
|
R
|
555,0
|
63,4
|
0,45
|
2,50
|
55,8
|
|
0,65
|
3,61
|
15,5
|
|
BO
|
|
ALIM
|
875,0
|
100,0
|
0,51
|
4,48
|
|
|
2,66
|
23,26
|
|
|
|
|
|
|
|
|
|
|
|
|
|
|
|
|
|
|
RATIO
|
|
|
COBALT
|
|
|
|
CUIVRE
|
|
|
|
|
FRACT
|
|
POIDS%POIDS
|
%
|
PdS
|
Rdt
|
taux
|
%
|
PdS
|
Rdt
|
taux
|
NaHS
|
|
|
|
|
A+B
|
160
|
17,68
|
0,99
|
1,59
|
34,68
|
1,96
|
10,60
|
16,95
|
72,15
|
4,08
|
Na2SiO3
|
|
C
|
80
|
8,84
|
0,58
|
0,46
|
10,13
|
1,15
|
2,03
|
1,62
|
6,91
|
0,78
|
G41
|
A+B+C
|
240
|
26,52
|
0,86
|
2,05
|
44,81
|
1,69
|
7,74
|
18,58
|
79,06
|
2,98
|
T3Y
|
|
R
ALIM
|
665
905 RATIO
|
73,48
100,00
|
0,38
0,51
|
2,53
4,58 COBALT
|
55,19
|
|
0,74
2,60
|
4,92
23,50 CUIVRE
|
20,94
|
|
BO
CONDITION
|
|
FRACT
|
|
POIDS%POIDS
|
%
|
PdS
|
Rdt
|
taux
|
%
|
PdS
|
Rdt
|
taux
|
NaHS
|
|
A
|
65
|
6,97
|
1,25
|
0,81
|
16,55
|
2,37
|
21,35
|
13,88
|
54,41
|
7,80
|
|
|
B
|
75
|
8,05
|
0,68
|
0,51
|
10,39
|
1,29
|
6,22
|
4,67
|
18,29
|
2,27
|
MD
|
|
A+B
|
140
|
15,02
|
0,94
|
1,32
|
26,94
|
1,79
|
13,24
|
18,54
|
72,69
|
4,84
|
Na2SiO3
|
A+B+C
360
38,63
|
0,65
2,33
47,56
1,23
|
5,88
21,16
82,96
2,15
|
T3Y
|
R
|
572
|
61,37
|
0,45
|
2,57
|
52,44
|
|
0,76
|
4,35
|
17,04
|
|
BO
|
|
ALIM
|
932 RATIO
|
100,00
|
0,53
|
4,91 COBALT
|
|
|
2,74
|
25,51 CUIVRE
|
|
|
CONDITION
|
FRACT
|
|
POIDS%POIDS
|
%
|
PdS
|
Rdt
|
taux
|
%
|
PdS
|
Rdt
|
taux
|
NaHS
|
3144
|
A
|
60
|
6,45
|
1,49
|
0,89
|
16,86
|
2,61
|
21,21
|
12,73
|
47,70
|
7,39
|
70 -10 -20%
|
|
B
|
135
|
14,52
|
0,76
|
1,03
|
19,35
|
1,33
|
4,81
|
6,49
|
24,34
|
1,68
|
MD
|
19605
|
A+B
|
195
|
20,97
|
0,98
|
1,92
|
36,22
|
1,73
|
9,86
|
19,22
|
72,03
|
3,44
|
Na2SiO3
|
200
|
C
|
195
|
20,97
|
0,46
|
0,90
|
16,92
|
0,81
|
1,39
|
2,71
|
10,16
|
0,48
|
G41
|
98,25
|
A+B+C
|
390
|
41,94
|
0,72
|
2,82
|
53,14
|
1,27
|
5,62
|
21,93
|
82,19
|
1,96
|
T3Y
|
B
|
|
|
|
|
|
|
|
|
|
|
|
|
|
|
|
|
|
|
|
|
|
|
|
|
|
|
|
|
|
|
|
|
|
|
|
|
|
|
|
|
|
|
|
|
|
|
|
|
|
|
|
|
|
|
|
|
|
|
|
|
|
|
|
|
|
|
|
|
|
|
|
|
|
|
|
|
|
|
|
|
|
|
|
|
|
|
|
|
|
|
|
|
|
|
|
|
|
|
|
|
|
|
|
|
|
RATIO
|
COBALT
|
CUIVRE
|
|
FRACT
|
|
POIDS%POIDS
|
%
|
PdS
|
Rdt
|
taux
|
%
|
PdS
|
Rdt
|
taux
|
NaHS
|
|
A
|
70
|
7,78
|
1,33
|
0,93
|
22,32
|
2,87
|
21,62
|
15,13
|
58,41
|
7,51
|
|
B
|
105
|
11,67
|
0,69
|
0,72
|
17,37
|
1,49
|
3,62
|
3,80
|
14,67
|
1,26
|
MD
|
|
A+B
|
175
|
19,44
|
0,95
|
1,66
|
39,70
|
2,04
|
10,82
|
18,94
|
73,08
|
3,76
|
Na2SiO3
|
|
C
|
175
|
19,44
|
0,62
|
1,09
|
26,02
|
1,34
|
1,88
|
3,29
|
12,70
|
0,65
|
G41
|
|
A+B+C
|
350
|
38,89
|
0,78
|
2,74
|
65,71
|
1,69
|
6,35
|
22,23
|
85,78
|
2,21
|
T3Y
|
|
R
|
550
|
61,11
|
0,26
|
1,43
|
34,29
|
|
0,67
|
3,69
|
14,22
|
|
BO
|
|
ALIM
|
900 RATIO
|
100,00
|
0,46
|
4,17 COBALT
|
|
|
2,88
|
25,91 CUIVRE
|
|
|
|
B
130
14,36
|
0,65
0,85
17,12
1,19
|
3,04
3,95
14,74
1,03
|
MD
|
A+B
|
250
|
27,62
|
0,97
|
2,43
|
49,21
|
1,78
|
8,06
|
20,14
|
75,10
|
2,72
|
|
|
|
|
|
|
|
|
|
|
|
|
|
Na2SiO3
|
C
|
175
|
19,34
|
0,50
|
0,88
|
17,73
|
0,92
|
1,54
|
2,70
|
10,05
|
0,52
|
G41
|
|
A+B+C
|
425
|
46,96
|
0,78
|
3,30
|
66,94
|
1,43
|
5,37
|
22,84
|
85,14
|
1,81
|
T3Y
|
|
R
|
480 RATIO
|
53,04
|
0,34
|
1,63
RECUPERATION COBALT
|
33,06
|
|
0,83
|
3,98
RECUPERATION CUIVRE
|
14,86
|
|
BO
|
|
ALIM FRACT
|
905
|
100,00
POIDS%POIDS
|
0,55
%
|
4,94 PdS
|
Rdt
|
taux
|
2,96
%
|
26,82 PdS
|
Rdt
|
taux
|
NaSH
|
|
A
|
60
|
6,42
|
1,27
|
0,76
|
14,18
|
2,21
|
22,08
|
13,25
|
43,18
|
6,73
|
|
|
B
|
170
|
18,18
|
0,77
|
1,31
|
24,35
|
1,34
|
5,35
|
9,10
|
29,65
|
1,63
|
MD
|
C
205
21,93
|
0,49
1,00
18,69
0,85
|
1,70
3,49
11,36
0,52
|
G41
|
A+B+C
|
435
|
46,52
|
0,71
|
3,08
|
57,21
|
1,23
|
5,94
|
25,83
|
84,19
|
1,81
|
T3Y
|
|
R
|
500
|
53,48
|
0,46
|
2,30
|
42,79
|
|
0,97
|
4,85
|
15,81
|
|
BO
|
ALIM
|
935 RATIO
|
100,00
|
0,57
|
5,38 COBALT
|
|
|
3,28
|
30,68 CUIVRE
|
|
|
CONDITION
|
|
FRACT
|
|
POIDS%POIDS
|
%
|
PdS
|
Rdt
|
taux
|
%
|
PdS
|
Rdt
|
taux
|
NaHS
|
3144
|
A
|
85
|
9,04
|
1,48
|
1,26
|
28,19
|
3,12
|
16,94
|
14,40
|
60,50
|
6,69
|
70 -10 -20%
|
|
B
|
105
|
11,17
|
0,71
|
0,75
|
16,71
|
1,50
|
3,05
|
3,20
|
13,46
|
1,20
|
MD
|
196,5
|
A+B
|
190
|
20,21
|
1,05
|
2,00
|
44,90
|
2,22
|
9,26
|
17,60
|
73,95
|
3,66
|
Na2SiO3
|
|
C
|
195
|
20,74
|
0,35
|
0,68
|
15,30
|
0,74
|
1,13
|
2,20
|
9,26
|
0,45
|
G41
|
C
|
|
|
|
|
|
|
|
|
|
|
|
|
|
|
|
|
|
|
|
|
|
|
|
|
|
|
|
|
|
|
|
|
|
|
|
|
|
|
|
|
|
|
|
|
|
|
|
|
|
|
|
|
|
|
|
|
|
|
|
|
|
|
|
|
|
|
|
|
|
|
|
|
|
|
|
|
|
|
|
|
|
|
|
|
|
|
|
|
|
|
|
|
|
|
|
|
|
|
|
|
|
|
|
|
|
RATIO
|
COBALT
|
CUIVRE
|
|
FRACT
|
|
POIDS%POIDS
|
%
|
PdS
|
Rdt
|
taux
|
%
|
PdS
|
Rdt
|
taux
|
NaHS
|
|
A
|
75
|
8,62
|
1,27
|
0,95
|
22,73
|
2,64
|
21,44
|
16,08
|
55,59
|
6,45
|
|
B
|
110
|
12,64
|
0,87
|
0,96
|
22,84
|
1,81
|
5,44
|
5,98
|
20,69
|
1,64
|
MD
|
|
A+B
|
185
|
21,26
|
1,03
|
1,91
|
45,57
|
2,14
|
11,93
|
22,06
|
76,27
|
3,59
|
Na2SiO3
|
|
C
|
185
|
21,26
|
0,53
|
0,98
|
23,40
|
1,10
|
1,71
|
3,16
|
10,94
|
0,51
|
G41
|
|
A+B+C
|
370
|
42,53
|
0,78
|
2,89
|
68,97
|
1,62
|
6,82
|
25,23
|
87,21
|
2,05
|
T3Y
|
|
R
|
500
|
57,47
|
0,26
|
1,30
|
31,03
|
|
0,74
|
3,70
|
12,79
|
|
BO
|
|
ALIM
|
870 RATIO
|
100,00
|
0,48
|
4,19 COBALT
|
|
|
3,33
|
28,93 CUIVRE
|
|
|
|
CONDITION
70 -10 -20%
50 -25-25%
CONDITION
FRACT
POIDS%POIDS
%
PdS
Rdt
taux
%
PdS
Rdt
taux
NaHS
A
70
7,78
1,48
1,04
23,36
3,00
16,20
11,34
40,95
5,26
70 -10 -20%
B
160
17,78
0,65
1,04
23,45
1,32
4,93
7,89
28,48
1,60
MD
A+B
230
25,56
0,90
2,08
46,81
1,83
8,36
19,23
69,43
2,72
25-50 -25%
ANNEXE C : ESSAIS DE FLOTTATION AVEC LE TALL-OIL
TRACTIONNE
|
|
|
Na2SiO3
|
C
|
220
|
24,44
|
0,52
|
1,14
|
25,79
|
1,06
|
3,03
|
6,67
|
24,07
|
0,98
|
G41
|
|
A+B+C
|
450
|
50,00
|
0,72
|
3,22
|
72,60
|
1,45
|
5,75
|
25,89
|
93,50
|
1,87
|
T3Y
|
R
|
450
|
50,00
|
0,27
|
1,22
|
27,40
|
|
0,40
|
1,80
|
6,50
|
|
BO
|
|
ALIM
|
900
|
100,00
|
0,49
|
4,44
|
|
|
3,08
|
27,69
|
|
|
|
|
|
RATIO
|
|
|
COBALT
|
|
|
|
CUIVRE
|
|
|
|
|
FRACT
|
|
POIDS%POIDS
|
%
|
PdS
|
Rdt
|
taux
|
%
|
PdS
|
Rdt
|
taux
|
NaHS
|
|
A
|
55
|
5,9
|
1,78
|
0,98
|
17,5
|
3,00
|
24,02
|
13,21
|
38,7
|
6,61
|
|
|
B
|
160
|
17,0
|
0,87
|
1,39
|
24,9
|
1,47
|
7,09
|
11,34
|
33,2
|
1,95
|
MD
|
C
185
19,7
|
0,48
0,89
15,9
0,81
|
2,21
4,09
12,0
0,61
|
T3Y
|
A+B+C
|
400
|
42,6
|
0,81
|
3,26
|
58,4
|
1,37
|
7,16
|
28,64
|
83,9
|
1,97
|
G41
|
|
R
|
540 RATIO
|
57,4
|
0,43
|
2,32 COBALT
|
41,6
|
0,72
|
1,02
|
5,51 CUIVRE
|
16,1
|
0,28
|
T O
CONDITION
|
ALIM FRACT
|
940
|
100,0
POIDS%POIDS
|
0,59
%
|
5,58 PdS
|
100,0 Rdt
|
1,00 taux
|
3,63
%
|
34,15 PdS
|
100,0 Rdt
|
1,00 taux
|
NaHS
|
3144
|
A
|
60
|
7,32
|
1,45
|
0,87
|
22,8
|
3,11
|
12,64
|
7,58
|
38,7
|
5,28
|
70 -10 -20%
|
|
B
|
120
|
14,63
|
0,75
|
0,90
|
23,5
|
1,61
|
5,48
|
6,58
|
33,5
|
2,29
|
MD
|
196,5
|
A+B
|
180
|
21,95
|
0,98
|
1,77
|
46,3
|
2,11
|
7,87
|
14,16
|
72,2
|
3,29
|
Na2SiO3
|
200
|
C
|
145
|
17,68
|
0,46
|
0,67
|
17,4
|
0,99
|
1,20
|
1,74
|
8,9
|
0,50
|
T3Y
|
|
A+B+C
|
325
|
39,63
|
0,75
|
2,44
|
63,7
|
1,61
|
4,89
|
15,90
|
81,1
|
2,05
|
G41
|
D
|
|
|
|
|
|
|
|
|
|
|
|
|
|
|
|
|
|
|
|
|
|
|
|
|
|
|
|
|
|
|
|
|
|
|
|
|
|
|
|
|
|
|
|
|
|
|
|
|
|
|
|
|
|
|
|
|
|
|
|
|
|
|
|
|
|
|
|
|
|
|
|
|
|
|
|
|
|
|
|
|
|
|
|
|
|
|
|
|
|
|
|
|
|
|
|
|
|
|
|
|
|
|
|
|
|
RATIO
|
COBALT
|
CUIVRE
|
|
FRACT
|
|
POIDS%POIDS
|
%
|
PdS
|
Rdt
|
taux
|
%
|
PdS
|
Rdt
|
taux
|
NaHS
|
|
A
|
50
|
5,38
|
1,88
|
0,94
|
19,8
|
3,68
|
25,67
|
12,84
|
50,4
|
9,38
|
|
B
|
85
|
9,14
|
0,88
|
0,75
|
15,8
|
1,72
|
5,10
|
4,34
|
17,0
|
1,86
|
MD
|
|
A+B
|
135
|
14,52
|
1,25
|
1,69
|
35,6
|
2,45
|
12,72
|
17,17
|
67,5
|
|
4,65Na2SiO3
|
|
C
|
330
|
35,48
|
0,56
|
1,85
|
38,9
|
1,10
|
1,86
|
6,14
|
24,1
|
0,68
|
T3Y
|
|
A+B+C
|
465
|
50,00
|
0,76
|
3,54
|
74,5
|
1,49
|
5,01
|
23,31
|
91,6
|
1,83
|
G41
|
|
R
|
465
|
50,00
|
0,26
|
1,21
|
25,5
|
0,51
|
0,46
|
2,14
|
8,4
|
0,17
|
TO
|
|
ALIM
|
930 RATIO
|
100,00
|
0,51
|
4,75 COBALT
|
100,0
|
1,00
|
2,74
|
25,45 CUIVRE
|
100,0
|
1,00
|
|
A
55
5,85
|
1,78
0,98
19,8
3,39
|
24,02
13,21
38,7
6,61
|
|
B
A+B
|
160
215
|
17,02
22,87
|
0,87
1,10
|
1,39
2,37
|
28,2
48,1
|
1,66
2,10
|
7,09
11,42
|
11,34
24,56
|
33,2
71,9
|
1,95
|
MD
3,14Na2SiO3
|
|
|
185
|
19,68
|
0,48
|
0,89
|
18,0
|
0,91
|
2,21
|
4,09
|
12,0
|
0,61
|
T3Y
|
C
A+B+C
|
400
|
42,55
|
0,81
|
3,26
|
66,1
|
1,55
|
7,16
|
28,64
|
83,9
|
1,97
|
G41
|
|
|
|
|
|
|
|
|
|
|
|
|
|
|
R
ALIM
|
540
940 RATIO
|
57,45
100,00
|
0,31
0,52
|
1,67
4,93 COBALT
|
33,9
100,0
|
0,59
1,00
|
1,02
3,63
|
5,51
34,15 CUIVRE
|
16,1
100,0
|
0,28
1,00
|
TO
|
|
FRACT
|
|
POIDS%POIDS
|
%
|
PdS
|
Rdt
|
taux
|
%
|
PdS
|
Rdt
|
taux
|
NaHS
|
|
A
|
55
|
5,88
|
2,00
|
1,10
|
21,8
|
3,70
|
29,37
|
16,15
|
54,6
|
9,29
|
|
|
B
|
150
|
16,04
|
0,61
|
0,92
|
18,1
|
1,13
|
3,12
|
4,68
|
15,8
|
0,99
|
MD
|
C
195
20,86
|
0,46
0,90
17,8
0,85
|
1,57
3,06
10,4
0,50
|
T3Y
|
A+B+C
|
400
|
42,78
|
0,73
|
2,91
|
57,6
|
1,35
|
5,97
|
23,90
|
80,8
|
1,89
|
G41
|
|
R
|
535
|
57,22
|
0,40
|
2,14
|
42,4
|
0,74
|
1,06
|
5,67
|
19,2
|
0,34
|
TO
|
ALIM
|
935 RATIO
|
100,00
|
0,54
|
5,05 COBALT
|
100,0
|
1,00
|
3,16
|
29,57 CUIVRE
|
100,0
|
1,00
|
CONDITION
|
|
FRACT
|
|
POIDS%POIDS
|
%
|
PdS
|
Rdt
|
taux
|
%
|
PdS
|
Rdt
|
taux
|
NaHS
|
3144
|
A
|
60
|
6,56
|
1,79
|
1,07
|
21,9
|
3,34
|
26,04
|
15,62
|
51,8
|
7,89
|
70 -10 -20%
|
|
B
|
135
|
14,75
|
0,64
|
0,86
|
17,6
|
1,19
|
3,95
|
5,33
|
17,7
|
1,20
|
MD
|
196,5
|
A+B
|
195
|
21,31
|
0,99
|
1,94
|
39,5
|
1,86
|
10,75
|
20,96
|
69,4
|
|
3,26Na2SiO3
|
|
C
|
220
|
24,04
|
0,62
|
1,36
|
27,8
|
1,49
|
1,58
|
3,48
|
11,5
|
0,48
|
T3Y
|
E
RATIO
COBALT
CUIVRE
CONDITION
FRACT
POIDS%POIDS
%
PdS
Rdt
taux
%
PdS
Rdt
taux
NaHS
3144
70
7,7
2,15
1,51
26,5
3,46
24,01
16,81
58,7
7,67
70 -10 -20%
196,5
200
393
98,25
22,5
70 -30 - 0%
ANNEXE D : ESSAIS DE FLOTTATION AVEC LE BOOSTER ET
TALL-OIL
FRACTIONNES
B
120
13,1
A+B
190
20,8
|
0,92
1,10
19,4
1,48
1,37
2,61
45,9
2,21
|
4,23
5,08
17,7
1,35
11,52
21,88
76,4
|
MD
3,68Na2SiO3
|
C
|
245
|
26,8
|
0,65
|
1,59
|
28,0
|
1,05
|
1,02
|
2,50
|
8,7
|
0,33
|
T3Y
|
|
A+B+C
|
435
|
47,5
|
0,97
|
4,20
|
73,8
|
1,55
|
5,61
|
24,38
|
85,1
|
1,79
|
G41
|
R
|
480
|
52,5
|
0,31
|
1,49
|
26,2
|
0,50
|
0,89
|
4,27
|
14,9
|
0,28
|
TO
|
|
ALIM
|
915
|
100,0
|
0,62
|
5,69
|
100,0
|
1,00
|
3,13
|
28,65
|
100,0
|
1,00
|
|
|
|
|
|
|
|
|
|
|
|
|
|
|
|
|
|
|
|
|
|
|
|
|
|
|
|
RATIO
|
|
|
COBALT
|
|
|
|
CUIVRE
|
|
|
|
|
FRACT
|
|
POIDS%POIDS
|
%
|
PdS
|
Rdt
|
taux
|
%
|
PdS
|
Rdt
|
taux
|
NaHS
|
|
B
190
20,2
|
0,68
1,29
24,7
1,22
|
3,6
6,76
22,0
1,09
|
TO
|
A+B
|
250
|
26,6
|
1,01
|
2,52
|
48,1
|
1,81
|
9,0
|
22,54
|
73,2
|
2,75
|
|
|
C
|
310
|
33,0
|
0,46
|
1,43
|
27,2
|
0,83
|
1,6
|
4,99
|
16,2
|
0,49
|
BO
|
A+B+C
|
560
|
59,6
|
0,71
|
3,95
|
75,3
|
1,26
|
4,9
|
27,54
|
89,4
|
1,50
|
|
|
R
|
380 RATIO
|
40,4
|
0,34
|
1,29 COBALT
|
24,7
|
0,61
|
0,9
|
3,27
|
10,6
|
|
|
ALIM
|
940
|
100,0
POIDS%POIDS
|
0,56
%
|
5,24 PdS
|
100,0 Rdt
|
1,00
|
3,3
%
|
30,80 CUIVRE
PdS
|
100,0 Rdt
|
|
NaHS
|
|
FRACT
|
50
|
|
1,31
|
0,66
|
13,4
|
taux
2,4
|
25,5
|
12,74
|
|
taux
8,34
|
|
A
|
135
|
5,5
14,9
|
0,72
|
0,97
|
19,9
|
1,3
|
|
5,49
|
46,1
19,9
|
1,33
|
TO
|
|
B
A+B
|
185
|
20,4
|
0,88
|
1,63
|
33,3
|
1,6
|
4,1
9,9
|
18,23
|
66,0
|
3,23
|
|
|
A+B+C
500
55,2
|
0,62
3,11
63,6
1,2
|
4,5
22,74
82,3
1,49
|
|
R
|
405
|
44,8
|
0,44
|
1,78
|
36,4
|
0,8
|
1,2
|
4,90
|
17,7
|
|
|
|
ALIM
|
905 RATIO
|
100,0
|
0,54
|
4,89 COBALT
|
100,0
|
1,0
|
3,1
|
27,64 CUIVRE
|
100,0
|
|
CONDITION
|
FRACT
|
|
POIDS%POIDS
|
%
|
PdS
|
Rdt
|
taux
|
%
|
PdS
|
Rdt
|
taux
|
NaHS
|
3144
|
A
|
50
|
5,4
|
1,42
|
0,71
|
14,1
|
2,6
|
20,3
|
10,2
|
38,7
|
7,1
|
70 -10 -20%
|
B
|
190
|
20,7
|
0,66
|
1,25
|
24,9
|
1,2
|
3,8
|
7,2
|
27,5
|
1,3
|
TO
|
22,5
|
A+B
|
240
|
26,1
|
0,82
|
1,96
|
39,0
|
1,5
|
7,2
|
17,4
|
66,2
|
2,5
|
70 -0 -30%
|
C
|
300
|
32,6
|
0,62
|
1,86
|
36,9
|
1,1
|
2,1
|
6,4
|
24,2
|
0,7
|
BO
|
|
A+B+C
|
540
|
58,7
|
0,71
|
3,82
|
75,9
|
1,3
|
4,4
|
23,7
|
90,4
|
1,5
|
|
|
F
RATIO
COBALT
CUIVRE
CONDITION
FRACT
POIDS%POIDS
%
PdS
Rdt
taux
%
PdS
Rdt
taux
NaHS
3144
A
60
6,1
2,05
1,23
23,7
3,88
23,43
14,06
47,0
7,68
70 -10 -20%
22,5
30 -0 -70%
40
25 -75-0%
0,22
1,00
ANNEXE E : ANALYSES GRANULOCHIMIQUES DES REJETS EN
UTILISANT LE
BOOSTER, LE TALL-OIL, BOOSTER ET TALL-OIL FRACTIONNES
B
170
A+B
230
|
17,3
0,86
1,46
23,5
1,17
2,69
|
28,2
1,63
4,89
8,31
51,9
2,21
9,73
22,37
|
27,8
1,60
TO
74,8
3,19
|
C
|
300
|
|
30,6
|
0,47
|
1,41
|
|
27,2
|
0,89
|
1,49
|
4,47
|
14,9
|
0,49
|
BO
|
|
|
A+B+C
|
530
|
|
54,1
|
0,77
|
4,10
|
|
79,2
|
1,46
|
5,06
|
26,84
|
89,8
|
1,66
|
|
|
|
R
|
450
|
|
45,9
|
0,24
|
1,08
|
|
20,8
|
0,45
|
0,68
|
3,06
|
10,2
|
|
|
|
|
ALIM
|
980
|
|
100,0
|
0,53
|
5,18
|
|
100,0
|
1,00
|
3,05
|
29,90
|
100,0
|
|
|
|
|
|
|
|
|
|
|
|
|
|
|
|
|
|
|
|
|
|
|
|
|
|
|
|
|
|
|
|
|
|
|
|
|
|
|
|
|
|
|
|
|
|
|
|
|
|
|
|
|
|
|
|
|
|
|
|
|
|
|
|
|
|
|
|
|
|
Tranches
|
|
|
Répartition granulo
|
|
Répartition cuivre
|
|
|
|
%Rc
|
Mesh
|
MicronsPoids%Poids
|
%Rc
%Pc
%Cu
|
PdS
|
%PdS
%Rc
%Pc
%Co
|
PdS
|
%PdS
|
65
208
100
149
|
173
29,12
43,603
56,4
122
20,54
64,141
35,86
|
0,56
0,969
26,992
46,64
53,36
0,72
0,878
24,473
71,113
28,89
|
0,24
0,415
29,48
53,3
0,29
0,354
25,12
78,42
|
150
|
104
|
90
|
15,15
|
79,293
|
20,71
|
0,54
|
0,486
|
13,541
|
84,654
|
15,35
|
0,17
|
0,153
|
10,86
|
89,28
|
|
200
|
75
|
75
|
12,63
|
91,919
|
8,081
|
0,46
|
0,345
|
9,6122
|
94,266
|
5,734
|
0,15
|
0,113
|
7,988
|
97,27
|
|
270
|
55
|
30
|
5,051
|
96,97
|
3,03
|
0,43
|
0,129
|
3,5941
|
97,86
|
2,14
|
0,11
|
0,033
|
2,343
|
99,62
|
|
325
|
48
|
12
|
2,02
|
98,99
|
1,01
|
0,4
|
0,048
|
1,3373
|
99,198
|
0,802
|
0,04
|
0,005
|
0,341
|
99,96
|
|
-325
|
-48
Tranches
|
6
|
1,01
|
Répartition granulo
|
100 0,48
|
|
0,029
|
0,8024
Répartition cuivre
|
|
100 0,01
|
|
6E-04
|
0,043
Répartition cobalt
|
100
|
|
Mesh
|
Alimentation
|
594
MicronsPoids%Poids
|
|
100 0,6
%Rc
|
%Pc
|
%Cu
|
3,589 PdS
|
%PdS
|
100 0,24
%Rc
|
%Pc
|
%Co
|
1,408 PdS
|
%PdS
|
%Rc
|
|
48
|
300
|
53
|
11,3
|
11,301
|
88,7
|
0,76
|
0,403
|
15,011
|
15,011
|
84,99
|
0,34
|
0,18
|
18,77
|
18,77
|
|
65
|
208
|
145
|
30,92
|
42,217
|
57,78
|
0,42
|
0,609
|
22,696
|
37,707
|
62,29
|
0,32
|
0,464
|
48,34
|
67,11
|
|
100
|
149
|
32
|
6,823
|
49,041
50,96
0,72
|
0,23
|
8,5864
|
46,294
53,71
0,01
|
0,003
|
0,333
|
67,44
85,36
|
150
104
|
86
|
18,34
67,377
32,62
0,66
|
0,568
|
21,153
67,447
32,55
0,2
|
0,172
|
17,92
|
G
A
FLOW SHEET GENERAL DU CONCENTRATEUR DE KOLWELI
Dislributeur
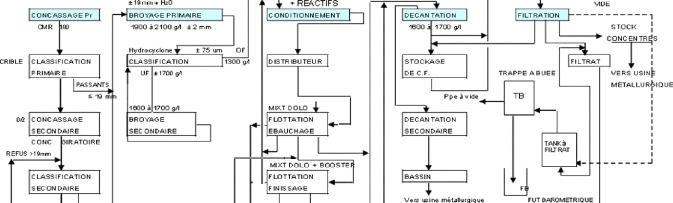
Mu&T DOLO FLOTTATION E19AUG11At3E
4 _' i_
NEXT DOLO * E OOSTE
FLOTTATION F RI'S SAeE
.I1-
19 rm. Hz0
+ REACTIF$
7
CONDITIONNEMENT
OR MAO PRIMAIRE
1g00S2100yA #2 mm
Kydroryelone
3 76 um OF
130Ci .
D ISTR IBU TE LI P.
C LASSIF I CATI O N
1 UF #177; 1700 grl
CRIS LE C LASS IFICATIplI
P Fi IhWIRE
PASSANTS i 19 rtr
TRAPP E A 611E E
FUT BAROFJIETF5 IQUE
IDECA1I TAMN j 11500 â 1
71X1 +I
V
STOCKAGE DE C.F.
Ppe Ivi ·s
D E CAN TA.TI0 N
SECONDAIRE
'BASSIN
T
Ve rs int rM1 t. Ik.lgiq ue
1
STOCK
CONCENTRIS
11
'
1
VE RS USI4 METALLU414 U
J
F ILT RATION
FILTRAT
16]0 â
1700 g/I
C LASS IFICATIOH SEG ON DAIRE
Où CO*ICAS SAG E
S EC ON DAME
C Ot1C RATOIRE
RERI '19mn
E R OYAG E
SEC OHDAIRE
PASSANTS s 19 mn
|
T
|
|
|
3!T
|
CONCASSAGE TERT1AJRE
|
|
|
|
CONE CARAT01R E
|
t
Rmet
Fig_1: Flaw-sheet géneral du concentrateur de Kolwezi
|
|
|