II.7.1.1.Diagramme d'Ishikawa
Encore appelé la méthode 5M, Ce diagramme permet
de déterminer l'ensemble des causes qui produisent un effet
étudié. Souvent, l'étape de recherche des causes est
négligé ce qui engendre des erreurs de diagnostic qui a un impact
direct sur le délai, la qualité, et sur les coûts
engagés pour résoudre le problème.
Il est souvent utilisé dans le cadre d'une
résolution de problème. Il sera utile pour déterminer de
façon pertinente sur quels composants on doit agir pour améliorer
la situation.
Ce diagramme, est composé d'un tronc principal au bout
duquel est indiqué l'effet étudié et de 5 branches
correspondant à 5 familles de causes [3] :
? Main d'oeuvre : (Connaissances, compétences,
comportement, organisation de l'équipe de travail...)
? Milieu (Environnement de réalisation de la tâche :
température, luminosité...) ? Matière (Matière
première ou matière utilisée)
? Méthode : (Méthode de réalisation de la
tâche : Systématique de travail, Marche à suivre, document
de description de la tâche)
? Moyens (Outils utilisés pour la réalisation de la
tâche : Machines, outils)
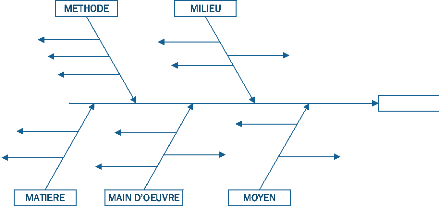
EFFET
10
Figure 9: diagramme d'Ishikawa
II.7.1.2.Diagramme de Pareto
Le diagramme de Pareto permet de hiérarchiser les
problèmes en fonction du nombre
d'occurrences et ainsi de définir des priorités
dans le traitement des problèmes.
Cet outil est basé sur la loi de 80/20. Autrement dit
il met en évidence les 20% de causes sur lesquelles il faut agir pour
résoudre 80 % du problème. Il sera utile pour déterminer
sur
11
quelles parties du groupe turbo-alternateur on doit agir en
priorité pour améliorer de façon significative la
situation (rendement).
Le diagramme de PARETO est composé de deux axes : L'axe
des abscisses représente les causes, l'axe des ordonnées
représente les effets sur le problème.
Il nous sera utile dans notre travail pour déterminer
les groupes qui engendre le plus de défaillance et qui ont un impact
important sur la baisse de production. Nous allons également l'exploiter
pour voir les groupes responsables du plus grand coût de maintenance.
L'analyse des résultats trouvés va permettre de proposer la
méthode efficace appropriée pour la maintenance
II.8.Processus d'élaboration du plan de maintenance
et Méthodes d'optimisation des rendements
La mise en oeuvre d'un plan de maintenance préventive
systématique comporte deux phases : ? L'élaboration du
plan : Consiste à analyser les actions préventives
proposées suivant la Criticité de chaque équipement ainsi
que d'établir un programme selon un processus structuré.
? L'exécution du plan : Consiste à
lancer les opérations et réaliser des visites afin de Collecter
les informations nécessaires pour l'évaluation du plan. [7]
? Méthodes d'optimisation des rendements
La notion d'optimisation des rendements des machines dans une
chaine de production au sein d'une entreprise dépend tout d'abord des
besoins annuels de l'entreprise et aussi de la demande des consommateurs
(clients).ainsi, à la centrale hydroélectrique d'Edéa on
dispose de plusieurs méthodes pour optimiser le rendement des groupes
turbo-alternateurs :
? Augmenter le débit d'eau entrant dans l'enceinte
turbine
? Isoler certaines charges (demande en énergie)
présentes sur le réseau de distribution ? Assurer l'entretien
permanent et régulier du groupe et de ses auxiliaires
? Respecter la politique de fonctionnement des appareils
présent dans l'usine
CONCLUSION
Dans cette partie, il était question de ressortir les
généralités sur les groupes TA et sur la maintenance
.ainsi, nous avions présentés d'une part le type de turbine
utilisé à la centrale(Kaplan), nous avions
présentés quelques outils de la maintenance (Ishikawa, Pareto) et
définir ce qu'on entend par maintenance tout en citant, expliquant
quelques concepts clé de celle-ci pour une bonne compréhension de
notre travail.
12
|