|
Yassir RAMDANI
Tuteur : Fabien BRUNESEAUX
|
Rapport Bibliographique
Influence et Rôle du silicium dans la fonte
à graphite
sphéroïdale
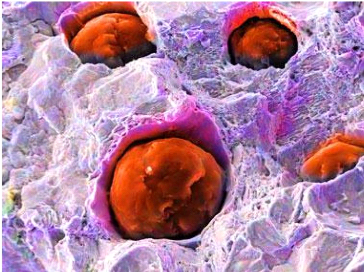
Stage de M2 SPM SIMM Effectué à Saint Gobain PAM 04
fev 2013 - 31 juil 2013

2
Table des matières
I. Rôle du Si dans la fonte 3
A. A la solidification 3
B. A la transformation à l'état solide. 3
II. Origine du Si dans la fonte 4
A. Résultant de la fonte des haut fourneau 4
B. Ajout de FeSi dans la fonte 5
III. Effets de l'ajout de FeSi dans la fonte 5
A. Aspect chimique de la réaction 5
B. Aspect thermique de la réaction 9
IV. Ajout combiné au magnésium 14
V. Inoculation de la fonte 16
A. Effet pré-conditionneur 16
B. La Pré-inoculation 16
C. Inoculation en poche 17
VI. Conclusion 17
3
I. Rôle du Si dans la fonte
Dans la fonte, le Si présente plusieurs
A. A la solidification
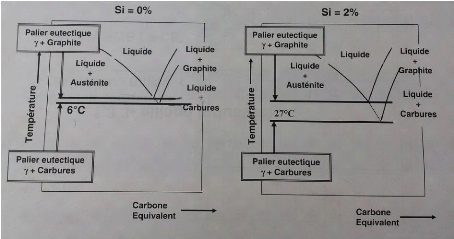
Figure 1 : Action du Si sur le diagramme Fe-C
[1]
Le silicium va augmenter l'écart de température
entre la transformation stable : L 4 graphite +
austénite et la transformation métastable : L 4
austénite + carbures. Cette augmentation d'écart de
température permet d'éviter la précipitation de fonte
blanche au cas où la surfusion est un peu trop profonde.
De plus, il est possible de refroidir le métal plus
vite car la plus grande différence de températures eutectiques,
stable et métastable, permet un cinétique de refroidissement plus
rapide.
B. A la transformation à l'état
solide.
De plus, les équilibres de transformation se font
à des taux de carbone plus bas qu'il s'agisse de la transformation
eutectique qu'eutectoïde.
La perlite, alors formée, a une fraction de
cémentite plus faible. Cette perlite est moins fragile et plus ductile
que celle formée à partir d'une fonte sans silicium.
4
II. Origine du Si dans la fonte
A. Résultant de la fonte des haut
fourneau
Les fontes sont composées principalement de 3
éléments :
? Fer
? Carbone ? Silicium
Ce sont les principaux constituants de cet alliage
La fonte est, à l'usine de Pont à Mousson,
produite à partir de hauts fourneaux. Celle-ci est obtenue à
partir d'une réaction de réduction de l'oxyde de fer a l'aide de
CO issu de la combustion du Coke [2] :
3 Fe2O3 + CO 4 2Fe3O4 + CO2 Fe3O4 + 4
CO 4 3Fe + 4 CO2
L'apport de carbone se fait au sein du haut fourneau,
où la fonte liquide qui perle sur les charges solides dont du coke. Au
contact de ce dernier la fonte absorbe du carbone jusqu'à saturation
Un premier apport en silicium se produit dans la zone de
combustion du haut fourneau par la réduction de la silice en oxyde de
silicium :
SiO2 + C 4 SiO + CO
Puis ce SiO gazeux va de nouveau réagir avec le coke
plus haut dans le ventre du haut fourneau pour libérer du silicium
monoatomique ainsi que du monoxyde de carbone :
SiO + C 4 Si + CO
Le silicium monoatomique et donc réactif va se lier
à la fonte en train d'être produite et le CO va monter vers le
gueulard afin de réduire de l'oxyde de fer. Le silicium apporté
de cette manière ne représente guère plus de 10% du taux
final de Si dans la fonte lorsqu'elle sera coulée.
5
B. Ajout de FeSi dans la fonte
Pour faire monter le taux de silicium, on incorpore des ajouts
tels que :
? Du ferro-Silicium d'une teneur de 45 à 95w% de Si
? Du carbure de Silicium SiC peut aussi être utilise. Ce
qui permet, en plus de corriger en Si, de faire varier le taux de carbone.
Etant donné que Saint-Gobain PaM utilise du FeSi 75
pour corriger ses fontes. Nous nous intéresserons aux effets du FeSi sur
la fonte lors de l'ajout de ce dernier ainsi que l'effet de certains
éléments ou paramètres sur le taux de silicium dans la
fonte.
III. Effets de l'ajout de FeSi dans la fonte
A. Aspect chimique de la réaction
Suite aux recherches de H. Fredriksson [3] On
observe ce qui se passe suite à l'ajout de FeSi dans un bain de fonte
dans une poche à 1300°C.
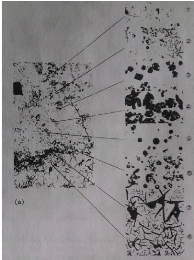
Figure 2 : Dissolution d'une particule de FeSi dans la
fonte. Observé au microscope optique (Grossissement : (a) 100x ; (b)
500x) [4].
La Figure 2 montre la microstructure qui entoure une particule
de FeSi lors de sa dissolution. La fonte a été trempée
juste après l'inoculation du FeSi dans le bain afin de figer le
processus de dissolution. Huit zones distinctes représentent des
microstructures différentes:
6
Zone 1 et 2 : On y trouve la particule originelle de FeSi avec en
zone 2 des cristaux de SiC sont mis en évidence, à la microsonde
de Castaing, sous forme de petit précipités à facettes.
Zone 3 : Des précipités plus grossiers de SiC
précipitent à la périphérie proche de la particule
de FeSi.
Zone 4 : On observe des nodules de graphite dans les SiC.
D'autres sont observables dans le liquide figé entre les SIC.
Zone 5 : Du graphite sphéroïdal est observable.
Zone 6 : Le graphite devient de moins en moins régulier au
fur et à mesure que l'on s'éloigne de la particule de FeSi.
Zone 7 : Apparait du graphite pro-eutectique. Zone 8 : On peut
voir du graphite lamellaire.
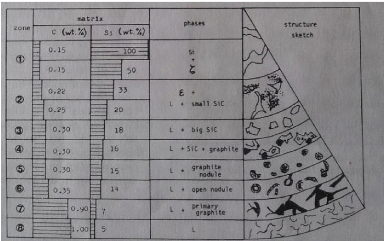
Figure 3 : composition des microstructures mises en
évidence dans la Figure 2 [4]
La figure 2 nous présente les structures
observées précédemment (Figure 2)
schématisées ainsi qu'un récapitulatif des phases en
présence. De plus des mesures à la microsonde ont
été effectuées afin de déterminer le taux de
Carbone et de Silicium dans le liquide figé.
Des tendances inverses d'évolution de concentration
sont observables pour le carbone et le silicium. Plus on s'éloigne de la
particule, plus le taux de carbone augmente alors que celui du silicium
décroit.
7
Ces évolutions s'expliquent très facilement, On
ajoute un alliage riche en Silicium dans un autre riche en Carbone. Les deux
vont attirer les éléments qui leur font défaut
jusqu'à obtenir un équilibre chimique.
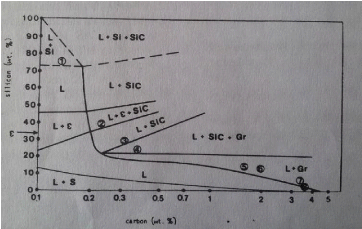
Figure 4 : Projection du liquidus pour un système
Fe-C-Si à 1300°C [4]
Dans ce diagramme, le FeSi est représenté par le
point 1 alors que la fonte liquide est représentée pas le point
8. Entre les deux points on peut voir qu'il y a différentes zones
où sont placés des points représentant les
différentes microstructures étudiées
précédemment.
La particule de FeSi va finir par se dissoudre, puis les
particules de SiC et de graphite formées vont se dissoudre aussi par
contre Fredriksson observe une dynamique de dissolution qui peut être
beaucoup plus lente que pour le FeSi car les distances de diffusion se trouvent
grandies.
Il va subsister une
hétérogénéité chimique au sein du liquide
que l'on recherche dans le cadre d'une inoculation. De plus, en fonction de la
taille de la particule de FeSi, le temps avant d'obtenir l'activité de
carbone initiale en tout point du liquide peut s'avérer assez long comme
nous le montrent Wang et Fredriksson [4]
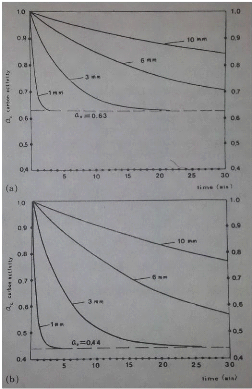
8
Figure 5 : Activité du carbone dans un bain de
fonte à 1400°C en fonction du temps pour différentes taille
de
particules de FeSi [4]
Plus la particule est grosse et plus le temps
nécessaire afin de rétablir de nouveau l'activité initiale
du carbone dans le bain. Dans le cadre d'une inoculation avant coulée,
cette tendance est plutôt bénéfique, le gradient
d'activité du carbone favorisera la diffusion de celui-ci et donc la
précipitation de graphite. Dans le cadre d'une correction où
seule l'augmentation du taux de Si est recherchée, une telle
durée d'homogénéisation est inacceptable. Un passage dans
un four à induction est donc nécessaire afin de brasser la fonte
mécaniquement à l'aide du mouvement convectif induit par les
bobines du four.
9
B. Aspect thermique de la réaction
S.A. Argyropoulos 5 a étudié l'effet
exothermique de l'ajout de FeSi dans un bain d'acier. Son expérience ce
déroulait de la manière suivante :
? Fusion d'une charge de 90kg ? Mise à température
1600°C
? Immersion du cylindre de FeSi relié à une
cellule de charger et à un thermocouple dans le bain d'acier
On obtient les courbes suivantes
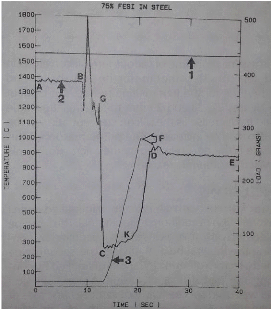
Figure 6 : Résultats expérimentaux du
transfert de masse durant l'immersion d'une barre de FeSi 75 dans un
bain
d'acier.
La courbe 1 représente la température du bain
d'acier. La courbe 2 illustre la mesure effectuée par la cellule de
charge et peut se diviser en six segments :
? A-B : Période avant l'immersion du cylindre de FeSi
dans l'acier
? B-G : Mesure chaotique due à la mise en branle de la
machine, les vibrations dues à la descente du cylindre donne des valeurs
mesurées confuses
? G-C : Immersion de la barre. La diminution de la charge
mesurée est due à la poussée d'Archimède
exercée par le métal en fusion.
? C-K : Représente la période où une
coquille d'acier solide se forme autour du barreau de FeSi (cf. Figure 2Figure
7). A l'interface entre le FeSi et l'acier solide ont lieu des
phénomènes micro-exothermiques dus à la combinaison d'une
part du FeSi et de l'acier solide en un eutectique FeSi.
? K-D : Suite à la refusion de la coque d'acier solide
préalablement formée d'abord à l'interface FeSi/Acier
solide par la formation d'un eutectique puis de l'extérieur par un
échange convectif avec le liquide. Le FeSi se dissout dans l'acier
liquide. Cette réaction est vivement exothermique.
? D-E : La partie immergée du cylindre a fondu il n'y a
plus de réaction.
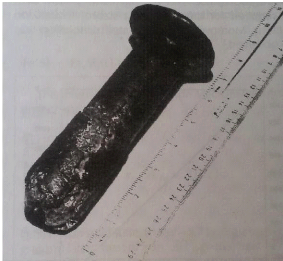
La courbe 3 représente la température au sein du
cylindre de FeSi et le point F indique le moment où la mesure
n'était plus pertinente. On remarque que ce dernier se situe peu de
temps après la transition réaction micro exothermique /
réaction macro exothermique.
10
Figure 7 : Cylindre de FeSi 75 immergé quelques
secondes dans un bain d'acier. Formation d'une coquille d'acier solide
autour du cylindre.
L'ajout de FeSi 50% dans l'acier provoque aussi une
réaction exothermique d'après les résultats publiés
par S.A. Argyropoulos [5-6] mais la cinétique est plus
lente.
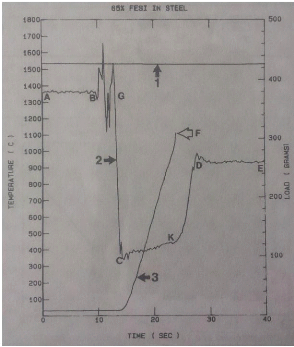
11
Figure 8 : Résultats expérimentaux du
transfert de masse durant l'immersion d'une barre de FeSi 50 dans un
bain
d'acier.
On observe sur cette courbe une cinétique plus lente
par rapport au FeSi 75 concernant la transition entre la phase de
réaction micro-exothermique et celle macro-exothermique. Ceci mis
à part l'allure des courbes reste là même.
Le point de perte de relevance de la prise de
température se situe 100°C plus haut. La réaction
étant moins exothermique, le cylindre fond de manière moins
turbulente et donc le thermocouple se retrouve moins vite au contact de la
fonte liquide.
Par contre c'est n'est pas le cas dans les fontes.
D'après Arthur F. Spengler [7], dans le cas des fontes.
Concernant les alliages de FeSi dont le taux de Si est inférieur
à 62%, la réaction est endothermique. Au-dessus de 62% de Si la
réaction est, elle, toujours exothermique.
Le caractère exothermique ou endothermique de la
réaction de dissolution d'un ferro-alliage dans un bain de fonte
provient de la manière dont il se dissout dans le bain en fusion.
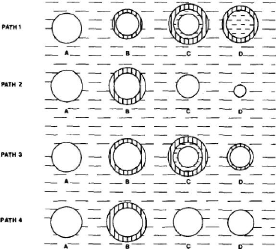
12
Figure 9 : Différentes tendances de fusion ou
dissolution des ferroalliages dans la fonte liquide [8].
J. R. Lampman [8] nous explique qu'il y a 4
tendances générales de dissolution et/ou fusion de l'additif dans
le bain en fusion. Universellement, l'addition de ferroalliage à
température ambiante dans le métal liquide, les grains vont se
retrouvés enrobé d'une carapace de fonte solidifiée.
Ensuite les tendances divergent :
? Tendance 1 : La particule fond dans sa carapace solide. La
fusion démarre à l'interface Ferroalliage/carapace puis
évolue vers le centre. La carapace refond ensuite par échange
convectif avec le bain. Le métal d'apport fondu se diluera à la
fusion de cette dernière.
? Tendance 2 : La carapace précédemment
formée fond par échange convectif avec le bain, puis la particule
se dissout dans le bain.
? Tendance 3 : Le métal d'apport et la fonte dans la
carapace se combinent pour former un alliage eutectique à bas point de
fusion. La carapace se dissout en faveur de l'eutectique ainsi formé.
Suite à la fusion totale de la carapace et à la dilution de
l'eutectique formé, la particule se trouve de nouveau en contact du bain
mais sa température n'a toujours pas atteint celle du bain. Une nouvelle
carapace se solidifie autour de la particule. C'est le cas de particules
à très faible conductivité thermique.
13
? Tendance 4 : La carapace refond par échange convectif
avec le bain. La particule ayant un point de fusion supérieur à
la température du métal en fusion, la particule restera en
suspension dans le bain si sa densité est proche de celle de l'alliage
corrigé sinon elle se décantera ou flottera.
Le FeSi 75 a une tendance de dissolution qui s'apparente aux
tendances 2 ou 4 en fonction de la température de fusion de la fonte et
du taux de Si dans le FeSi. Le caractère exothermique est dû
à la fusion de la carapace qui débute de l'interface avec la
particule vers le bain de fonte.
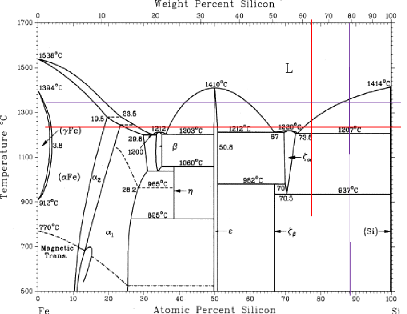
1340°C
1230°C
60 w%
75 w%
Figure 10 : Diagramme de phases binaire FeSi
[9]
Le FeSi 60 aussi communément utilisé a une
dissolution endothermique comme décrit par Spengler [7]. Sa
température de liquidus à 1230°C nous porte à
supposer que sa tendance de dissolution suit la tendance 1 de Lampman
[8] où les particules fondent totalement dans la carapace
solidifiée puis le liquide se dilue dans le bain lors de la refusion des
dites carapaces.
Alors qu'un FeSi 75, dont la température de liquidus
s'élève à 1340°C, suivra plutôt une
cinétique de dissolution proche de la tendance 2 avec une fusion de la
carapace solidifiée qui débutera à l'interface avec le
FeSi. Dans le cas d'une introduction du FeSi dans une fonte trop froide on
risque de se retrouver dans le cas n°4 où la particule ne fond pas
car sa température de liquidus est trop élevée par rapport
au liquide et donc elle se dissoudra lentement par diffusion chimique.
14
IV. Ajout combiné au magnésium
Le silicium n'est pas toujours ajouté seul (sous forme
de FeSi) dans le bain de fonte. Il peut être ajouté en combinaison
avec du magnésium (FeSiMg) afin de produire de la fonte à
graphite sphéroïdal.
Il est parfois préférable combiner l'ajout de
silicium (dans le cadre d'une inoculation et non d'une correction, ici le taux
de Si augmente de 0.05%) à celui du magnésium. De cette
manière on limite l'apport de Si qui dans le cas où son taux se
révèle trop élevé pourrait ne plus être
éligible pour un recyclage car le taux de silicium du bain avant
inoculation doit être très précis. De plus si le taux
dépasse les 2.5% on risque une transition Ductile/Fragile à la
température ambiante et perdre toute résilience [10].
M. Hecht [11] déclare que les ajouts de
magnésium pur ou d'alliage nickel magnésium dans une fonte
obligera le fondeur à inoculer la fonte au FeSi avant la coulée
et donc on risque de se retrouver dans les conditions citées ci-dessus
qui pourraient occasionner une impossibilité de recyclage de la fonte ou
un rebutage des pièces car les caractéristiques mécaniques
ne seraient pas conforme.
Le taux de magnésium résiduel, le
magnésium libre dans le bain de fonte qui n'a pas servi à
stabiliser l'oxygène ou le soufre, stabilise les oxydes et risque de
stabiliser les oxydes [1110] et d'entrer en compétition avec le
silicium. Le taux de ce dernier devra être gonflé et l'on risque
d'être confronté à une chute de résilience à
cause d'une fragilisation ai silicium.
Si le taux de soufre dans la fonte est trop important par
rapport au taux de magnésium introduit, on risque d'avoir des
sphéroïdes dégénérés voir de la fonte
vermiculaire. M. Bazdar [12] a étudié ce
phénomène.
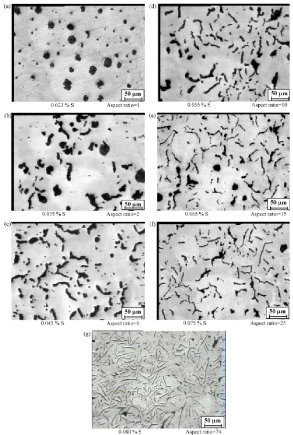
15
Figure 11 : Effet du Soufre sur l'allure du graphite
sphéroïdal obtenu suite à un traitement au magnésium
[12]
Toutes ces fontes ont été traitées avec
la même quantité de magnésium mais avaient un taux de
soufre initial différent. On peut observer la
dégénérescence des nodules de graphite de plus en plus
prononcée pour au final aboutir sur une structure où le
magnésium n'a eu aucun effet, il a totalement été
accaparé par le soufre.
Le taux de soufre avant l'ajout de FerroSilicoMagnésium
doit être connu et surtout contrôlé afin d'éviter de
devoir mettre trop d'additif de correction et de risque une fragilisation par
les éléments d'alliages.
Etant donné que le magnésium est très
friand de soufre comme nous l'exposent Gatellier et Olette13 c'est
d'ailleurs l'élément désulfurant optimal. On ajoute du
manganèse dans l'alliage de base afin qu'il fixe le soufre sous forme
que MnS. De cette manière, la quantité nécessaire de
magnésium à ajouter est moindre grâce au faible taux de
soufre libre.
16
V. Inoculation de la fonte
A. Effet pré-conditionneur
L'ajout de FeSi dans la fonte durant le circuit métal
permet de préparer l'arrivée des nodules de graphite par la
dissémination de centres de germination afin de favoriser au maximum la
précipitation du plus grand nombre de nodules possibles afin d'avoir une
microstructure la plus fine possible.
Pré-conditionner le métal, revient à
venir placer sur le bain décrassé une charge de FeSi afin
d'uniformiser le pouvoir le potentiel de nucléation du bain
[14]. Une granulométrie adéquate est requise pour
permettre une dissolution rapide.
Dans cette étape, l'ajout s'élève à
0.1% de Si.
B. La Pré-inoculation
L'ajout, en termes de Si, se situe entre 0.2 et 0.4%. La
charge ajoutée n'apporte pas forcément que du silicium. C'est
à cette étape où l'on ajoute le magnésium pour la
production de fonte ductile, par exemple.
L'effet recherché du magnésium, en plus
d'augmenter le nombre de germes, est de contrer l'effet carburigène du
magnésium et d'ajuster le taux de silicium voulu dans l'alliage final.
De plus le mélange de FeSiMg permet de limiter la violence de la
réaction de la sublimation du Mg et donc augmenter le temps que passent
les bulles de Mg dans le bain. Le rendement en magnésium.

Figure 12 : Comparaison de deux fontes l'une
inoculée correctement et l'autre non
17
C. Inoculation en poche
Suite à la violence du traitement de
sphéroïdisation. Une fraction non négligeable de germes
initialement présents dans le bain se retrouve dissoute ou
emprisonnés dans les crasses. On ajoute donc du FeSi dans la poche de
coulée afin de restaurer le potentiel de germination du bain avant
coulée.
VI. Conclusion
L'ajout de FeSi dans la fonte est une étape immuable du
cycle de production de l'alliage. La consommation de cet alliage en fonderie
est donc une grande source de dépenses. La maîtrise des rendements
des corrections en Silicium est donc une nécessité
pécuniaire due aux augmentations du prix à la tonne de
Ferro-alliage qui ne cesse d'augmenter.
En fonction de la réaction voulue, la nature du produit
à utiliser peut s'avérer très différent d'un cas
à l'autre. Un produit mal utilisé peut avoir une réaction
néfaste aussi bien financièrement que métallurgiquement
parlant.
Dans le cas où la seule finalité de l'ajout de
FeSi recherché est l'apport de silicium. Seront
préféré :
Un FeSi 75 pour une introduction en four. En poche, on risque
une diminution du rendement due à la décantation de particules de
FeSi infondues dans les crasses.
Pour une introduction en poche, on préfèrera un
FeSi 60 dont le point de fusion inférieur permet de diminuer le taux de
FeSi qui se retrouvera emprisonnés dans les crasses sur le bain.
Pour une inoculation avant coulée afin de favoriser la
précipitation de graphite. Ici le temps qui sépare l'inoculation
et la coulée est important car Ch. Wang et H. Fredriksson [4] nous
apprennent que l'inoculation donne lieu à la précipitation de
carbure de silicium et de graphite qui se redissoudront à la suite du
FeSi.
Pour éviter l'évanouissement total des
particules qui favoriseront la précipitation d'un graphite plus fin car
il y aura plus de centre de germination présents.
18
Dans le cas où l'on produit de la fonte à
graphite sphéroïdal où l'inoculation suivra où sera
simultanée à l'ajout de magnésium. Le Silicium et le
magnésium ont des effets contraires sur la microstructure.
Là où le silicium favorise la
précipitation du graphite et empêche la fragilisation de la fonte.
Le magnésium favorise la combinaison de fer avec le carbone, phase
très dure qui fragilise la microstructure.
Le taux de soufre libre devra donc être
contrôlé et limité par l'ajout de manganèse afin de
l'empêcher d'accaparer trop de magnésium. Ce qui pousserait
l'opérateur à forcer sur le taux de magnésium à
ajouter dans l'alliage et de ce fait booster aussi le taux de silicium. La
structure serait alors potentiellement fragilisée par un taux de
silicium trop important.
Pour conclure, Le silicium est un élément
indispensable dans la fonte quelle que soit son utilisation. Son taux doit
être suffisant pour apporter une contribution suffisamment efficace, tout
en restant sous les limites maximales où son effet risque de devenir
néfaste. Sans oublier de faire attention aux temps qui sépares
inoculation et coulée afin de prévenir tout effet
d'évanouissement d'autant plus vrai pour les traitements couplés
au magnésium.
19
1 Documents internes
2 Maurice BURTEAUX, Haut fourneau -
Théorie, DOSSIER Techniques De l'Ingénieur l'expertise
technique et scientifique de référence, m7400, 10/10/1991
3 H. Fredriksson, Inoculation of iron-base Alloys,
Materials Science and engineering 65, p 137 - 144,
1984
4 Ch. Wang et H. Fredriksson, On the mechanism
of inoculation of cast iron melts, Proc; 48th int. Foundry
Congress, Verna, 1981, 16pp
5 S.A. Argyropoulos, Exothermic phenomena in
liquid steel, Iron & steelmakerISSN 0275-8687, vol. 23, no7, 1996, pp.
65-80
6 S. A. Argyropoulos, R. I. L. Guthrie, The
Exothermic Dissolution of 50 wt.% Ferro-Silicon in Molten Steel, Canadian
Metallurgical Quarterly, Vol 18, 1979, pp 267-281
7 Arthur F. Spengler, Practical Methods for the
Control of the Inclusion Content in Ductile Iron, Ductile Iron
news Issue 1, 2002
8 J. R. Lampman, A. T. Peters, Ferroalloys and
Other Additives to Liquid Iron and Steel, ASTM International, 1 janv.
1981
9 W.J. Yuan, Characterization of the evaluation of
the solid solubility of Si in sintered Fe-Si alloys using DSC technique,
Materials Characterization Volume 58, Issue 4, April 2007, Pages 376-379
10 Fabrication de la fonte à graphite
sphéroïdal par les procédés au magnésium,
CTIF division des fontes, janvier 1969, indice de classification
idéologique : E04.00 B216
11 M. Hecht, Le traitement au magnésium en
vue de la sphéroïdisation du graphite, CTIF, Septembre
1990
12 M. Bazdar, H.R. Abbasi, A.H. Yaghtin, J.
Rassizadehghani, Effect of sulfur on graphite aspect ratio and tensile
properties in compacted graphite irons, Journal of Materials Processing
Technology 209, 2009, 1701-1705
13 C. Gatellier M. Olette, Aspects fondamentaux des
réactions entre éléments métalliques et
éléments non métalliques dans les aciers liquides,
Mémoires Techniques IRSID, juin 1979
14 P.-M. Cabanne et M. Gagné, Inoculer
une fonte GS : Pourquoi? Comment?, Services Techniques - Sorelmetal,
Suggestions pour la production de la fonte GS, Septembre 2010
|